HindlePower AT series User manual

AT SERIES
Operating Instructions
MICROPROCESSOR-CONTROLLED FLOAT BATTERY CHARGER
COMMUNICATIONS MODULE
(DNP3 Level 2 / Modbus Protocols)
JA5011-04

AT SERIES COMMUNICATIONS MODULE
DNP3 LEVEL 2 / MODBUS COMMUNICATIONS
FOR THE AT10.1 AND AT30 SERIES BATTERY CHARGERS
• The AT Communications Module allows the user to remotely monitor and control
the AT Series Battery Charger over a serial connection.
• Supports DNP3 Level 2 and Modbus protocols over RS-232 or RS-485 half-
duplex.
• The option can be used with a modem for telephone communications.
• All features of the AT Series front instrument panel are accessible remotely.
• SCADA (Supervisory Control And Data Acquisition) systems will be able to
control, monitor and log the events of the battery charger.
The AT Series Communications Module Option (EJ5037-xx) includes the AT Series
Communications PC Board (A12), external power supply resistor(s) (R29), an Operating
Instructions manual (JA5026-00), and a field-retrofit instruction sheet (JD5008-00). A
compatible industry-standard modem and modem cable are also available. Refer to the items
listed below for part information and check off which items were supplied.
STANDARD COMMUNICATION MODULES Part No.
¨Communications Module for 12 Vdc AT charger EJ5037-01
¨Communications Module for 24 Vdc AT charger EJ5037-02
¨Communications Module for 48 Vdc AT charger EJ5037-03
¨Communications Module for 130 Vdc AT charger EJ5037-04
OPTIONAL ACCESSORIES Part No.
¨Compatible Modem Option PM5005-00
¨10ft / 3.05m Modem Cable EH5026-00
¨25ft / 7.62m Modem Cable EH5026-01
¨50ft / 15.24m Modem Cable EH5026-02
¨100ft / 30.48m Modem Cable EH5026-03
SUPPLEMENTAL DOCUMENTATION
A number of supplemental online documents may be used in conjunction with this manual:
Doc. No. Online Hyperlink Description
JA0102-04 http://www.ATSeries.net/PDFs/JA0102-04.pdf AT Series Comm. Mod. Manual
JD5008-00 http://www.ATSeries.net/PDFs/JD5008-00.pdf AT Comm. Mod. Field Install.
JD5012-00 http://www.ATSeries.net/PDFs/JD5012-00.pdf Main Ctrl PCB A1 Replacement
JE5107-00 http://www.ATSeries.net/PDFs/JE5107-00.pdf AT Series Comm. Mod. Assy

TABLE OF CONTENTS
i
Section Page No.
1Introduction.........................................................................................................2
2Protocols .............................................................................................................2
2.1 Modbus..................................................................................................................2
2.2 DNP3.....................................................................................................................2
3Hardware .............................................................................................................3
3.1 Installation.............................................................................................................3
3.2 Serial Connections ................................................................................................5
3.2.1 RS-232........................................................................................................5
3.2.2 RS-485........................................................................................................8
3.3 Using a Modem ...................................................................................................12
4Configuration ....................................................................................................14
4.1 DIP Switch Settings.............................................................................................14
4.2 Setup Program ....................................................................................................15
4.3 Factory Defaults ..................................................................................................16
4.4 Status LED (D1) ..................................................................................................16
5DNP V3.00..........................................................................................................17
5.1 Introduction..........................................................................................................17
5.2 Device Profile ......................................................................................................17
5.3 Implementation Table..........................................................................................20
5.4 Point List..............................................................................................................23
5.4.1 Binary Inputs.............................................................................................23
5.4.2 Binary Output Status Points......................................................................24
5.4.3 Analog Inputs............................................................................................25
5.4.4 Analog Output Status Points.....................................................................26
5.4.5 Internal Indications....................................................................................27
6Modbus..............................................................................................................28
6.1 Introduction..........................................................................................................28
6.2 Supported Function Codes..................................................................................28
6.3 Register Definitions.............................................................................................29
6.3.1 Binary Outputs..........................................................................................29
6.3.2 Binary Inputs.............................................................................................29
6.3.3 Input Registers..........................................................................................30
6.3.4 Holding Registers......................................................................................30
6.3.5 Scaling Sample.........................................................................................30
7AT Series Charger Data Ranges......................................................................31
7.1 Voltage Ranges...................................................................................................31
7.2 Current Ranges...................................................................................................31
7.3 Equalize Time......................................................................................................31
APPENDIX A: Frequently Asked Questions (FAQ)..............................................32
APPENDIX B: Standard Drawings
AT Series Battery Charger Communications PC Board Assembly (JE5107-00) .........34
MANUAL SPECIFICATIONS (document control information).................................36

INTRODUCTION / PROTOCOLS
2
1Introduction
The AT Series Communications option allows the user to remotely monitor and control the
AT Series Battery Charger over a serial connection. Everything that the user can do at the
charger’s front panel display is accessible remotely. The communications option supports
DNP3 Level 2 and Modbus protocols over RS-232 or RS-485 serial communications.
Configuration is done by DIP switches and a setup program for additional parameters. The
communications board supports baud rates of 9600 bps and 19200 bps.
2Protocols
2.1 Modbus
The communications option can be setup to communicate on standard Modbus networks
using either of two transmission modes: ASCII (American Standard Code for Information
Interchange) or RTU (Remote Terminal Unit). The advantage of ASCII allows less strict
serial timing requirements without causing communication errors. The advantage of RTU
allows more data to be transmitted than ASCII mode for higher throughput.
Modbus ASCII mode supports the following serial settings:
• No parity, 7 data bits, 2 stop bits
• Even parity, 7 data bits, 1 stop bit
• Odd parity, 7 data bits, 1 stop bit
Modbus RTU mode supports the following serial settings:
• No parity, 8 data bits, 2 stop bits
• Even parity, 8 data bits, 1 stop bit
• Odd parity, 8 data bits, 1 stop bit
Refer to the Modbus section on page 28 for information on its implementation.
2.2 DNP3
The communications option supports DNP3 Level 2. This implementation of DNP3 meets
Level 2 conformance and supports change events with unsolicited messaging.
The DNP protocol supports the following serial settings:
• No parity, 8 data bits, 1 stop bit
• No parity, 8 data bits, 2 stop bits
• Even parity, 8 data bits, 1 stop bit
• Odd parity, 8 data bits, 1 stop bit
Refer to the DNP V3.00 section on page 17 for information on its implementation.

HARDWARE
3
3Hardware
3.1 Installation
WARNING
Disconnect and lock out all power to the battery charger before starting any maintenance
procedures. Turn the AC power off at the distribution panel upstream from the battery
charger. Disconnect the battery from the charger output terminals. This includes remote
sense wires if they were installed.
CAUTION
This part is susceptible to damage from static discharge. Please use the following
precautions:
• If you have a ground wrist strap, please use it to ground yourself to the charger
enclosure using the ground stud on the back of the door.
• Touch the ground stud on the back of the door before handling circuit boards or other
static sensitive parts.
• Handle circuit boards only by their edges.
• Ground yourself again before you replace any connectors or terminals on the new
part.
• If you are replacing a static sensitive circuit board parts, be sure you are grounded
before removing the new part from its anti-static carrier.
Installation Steps
Step 1 Turn off the AC and DC circuit breakers on the charger. Using a voltmeter, verify
that all potential voltages on the I/O panel are zero. This includes the DC Output
terminals TB1(+) and TB1(-), and the Remote Sense terminals (+) and (-).
Step 2 Locate the stand-offs that hold the main control card. Use a needle nose pliers to
pinch the retaining ear on the stand-offs, and gently pull the main control card back
off the stand-offs, roughly 0.25 inches. It is best to unlatch all stand-offs first with
the main control card still resting on them. Finally, remove the main control card in
one motion.
Step 3 The EN5004-xx communications module pc board (A12) mounts to the left of the
EN5002-xx main control pc board (A1), with connector (P13) plugged into J13.
Make sure that the pins on the connector line up. See Figure 1.
Step 4 Position the boards over the stand-offs. Firmly push both boards onto the stand-offs
until they are fully seated under the plastic clips. Minimize pc board flexing by
pushing directly on the areas surrounding stand-offs holes. Check the front panel
for proper alignment of indicating lights and push button switches.

HARDWARE
4
Figure 1
EN5004-00 AT Series Communications PC Board (A12)
Connected To EN5002-00 Main Control PC Board (A1)
Step 5 Connect the ballast resistor(s) (R29) to the power supply connection plug (J20). Pin
2 on J20 is +vdc and pin 4 is common. See Figure 2.
Step 6 Connect the serial connection to TB10 for RS-232 (see section 3.2.1 on page 5) or
TB11 for RS-485 (see section 3.2.2 on page 8).
Step 7 Check your work, read all the steps again and make sure that all the instructions
were performed.
Checks:
¨All stand-offs are fully latched.
¨All wire harness connectors are properly mated.
¨Indicator lights properly align with the front panel.
¨Push button switches work properly.

HARDWARE
5
COMPONENT LISTING
AT Series Communications PC Board (A12)
INDICATOR LIGHTS:
D1 Status LED
JUMPERS:
J20 Power Supply Connection
J21 Factory Connection
J22 RS-485 Terminating Resistor
(enable/disable)
CONNECTORS:
P13 Plug for Main Control PC Board (A1)
J13 Connection
SWITCHES:
S1 Configuration Switches
S2 MODBUS Address
TERMINAL BLOCKS:
TB10 RS-485 User Connection
TB11 RS-232 User Connection
Figure 2
EN5004-00 AT Series
Communications PC Board (A12)
3.2 Serial Connections
The communications option supports RS-232 and RS-485. RS-232 is a standard serial
communications used on personal computers. It has a limited cable distance and is
acceptable to electrical noise. RS-485 serial communications allow longer distances and
allow multiple devices to be connected to the same serial network. TB10 terminal block is
for the RS-485 connections and TB11 terminal block is for the RS-232 connections.
3.2.1 RS-232
Set configuration switch S1-5 to OFF to select RS-
232. Configuration switch S1-6 Enables or Disables
the RTS and CTS handshaking lines. Terminal block
TB11 User Connection
Pin 1 Pin 2 Pin 3 Pin 4 Pin 5
RDX TDX COM RTS CTS
TB11 is for the RS-232 user connections. In each section for RS-232 3-wire and 5-wire
installation, a typical connection diagram is shown. Each diagram shows the pinout used for
a standard personal computer (PC) for either a 25-pin or 9-pin serial connection.

HARDWARE
6
3.2.1 RS-232 3-Wire
For a RS-232 3-wire operation, the hardware handshaking lines are disabled. Disable the
hardware handshaking lines by setting configuration switch S1-6 to the OFF position.
Figure 3
RS-232 3-Wire Connection

HARDWARE
7
3.2.1 RS-232 5-Wire
For a RS-232 5-wire operation, the hardware handshaking lines are enabled. Enable the
hardware handshaking lines by setting configuration switch S1-6 to the ON position.
Figure 4
RS-232 5-Wire Connection

HARDWARE
8
3.2.2 RS-485
The communications board supports half-duplex RS-485 communications. Set configuration
switch S1-5 to ON to select RS-485. TB10 terminal block is for the RS-485 connections.
The next two sections describe a single connection and multi-drop connection.
Some RS-485 networks may require terminating resistors at both ends of the serial network.
The decision of whether or not to use termination resistors should be based on the BAUD
rate, the cable distance, and the type of cable being used to build the network. In most cases
for BAUD rates under 19.2K, terminating resistors are not required. If termination resistors
are used, the network must be designed with the appropriate biasing resistors to ensure
reliable communications.
The biasing resistors are responsible for ensuring that the network remains in the idle state
when all drivers are tri-stated. In order to guarantee that the receivers remain in a known
state, +/-200mV must always be maintained across the (+) and (-) or (A) and (B) RS-485
inputs. The use of termination resistors requires a significantly lower value of biasing
resistors which results in greater dc loading of the network.
Network design and biasing resistor calculations depend on the number of nodes on the
network, the type of drivers and receivers on the network, and any biasing already designed
into other devices sharing the network. As a result, whether or not use termination resistors
and biasing resistor calculation is beyond the scope of this manual. For more information on
biasing and termination details see the following references:
1) EIA/TIA-485 standard
Telecommunication Industry Association
http://www.tiaonline.org/standards/catalog/
2) RS422/485 Application Note
Copyright: B&B Electronics
http://www.bb-elec.com/tech_articles/rs422_485_app_note/table_of_contents.asp
The communications board has a termination resistor built in. Jumper J22 enables or
disables the terminating resistor. If the host computer is on one of the ends and does not
have a built in terminating resistor, add the resistor at the connection across the plus (+) and
minus (-). Each device needs to have a unique address number. Refer to Section 4for
configuration information for either Modbus or DNP protocols.
TB10 User Connection
Pin 1 Pin 2 Pin 3
(+) POS (-) NEG COM

HARDWARE
9
3.2.2 RS-485 Single Connection
When a single device is connected using RS-485, the terminating resistor is required. Move
the jumper on J22 to pins 1 and 2 to enable the terminating resistor. The device
communicating with the charger needs its own terminating resistor installed.
Figure 5
RS-485 Single Connection

HARDWARE
10
3.2.2 RS-485 Multi-Drop
When multiple chargers are connected using RS-485, the devices on the ends of the network
needs a terminating resistor installed or enabled. On the communications board, moving the
jumper on J22 between pins 1 and 2 enables the terminating resistor. The devices in the
middle of the network do not require the terminating resistor. Move jumper on J22 between
pins 2 and 3 to disable the terminating resistor. Figure 6 and Figure 7 show examples of
multiple chargers on a RS-485 serial network.
Figure 6
RS-485 Multi-Drop 2 Chargers

HARDWARE
11
Figure 7
RS-485 Multi-Drop 3 Chargers

HARDWARE
12
3.3 Using a Modem
These instructions are for a U.S. Robotics modem product # USR5686D or equivalent with
auto answer feature.
If using Modbus protocol, use ASCII mode. RTU mode has tighter timing requirements that
might prevent communications while using the modem. ASCII mode is enabled by
configuration switch S1-4 in the ON position. Enable the RS-232 handshaking lines by
setting the configuration switch S1-6 to the ON position. Connect the modem to TB11 as
detailed in Figure 8. Set the baud rate to 9600 bps by setting the configuration switch S1-7 to
the OFF position. Set the modem up for the settings listed below. The telephone cable plugs
into a standard analog phone line. This modem will not work with office digital phone
systems. The telephone line needs to be a dedicated analog phone line similar to most fax
machines. Plug in the AC power supply. The host software needs to have the same protocol
and serial parameters as the communications option.
Modem DIP Switch Settings
Switch Position Setting
1Down Data Terminal Ready override
2Up Verbal result codes
3Down Display result codes
4Up Echo offline commands
5Up Auto answer on
6Up Carrier detect normal
7Down Load factory defaults
8Down Smart mode

HARDWARE
13
Figure 8
Modem Connection

CONFIGURATION
14
4Configuration
All user configurable items are controlled by two groups of switches and a setup program to
modify additional configuration parameters. After changes have been made, the charger
must have both the AC and DC circuit breakers turned OFF then back ON again for any
changes to take affect.
S1 is used to configure the communications interface. S2 is used to set the device address for
Modbus. Setting S1-1 to enable the Setup Program, allows modification to additional
configuration parameters.
4.1 DIP Switch Settings
S1 Configuration
Position Description “ON” position “OFF” position
DIP S1-1Setup Program Enabled Disabled
DIP S1-2Configuration
Parameters* User Values Factory Default
Values
DIP S1-3Protocol DNP Modbus
DIP S1-4Modbus Protocol ASCII RTU
DIP S1-5Serial Port RS-485 RS-232
DIP S1-6RS-232 Handshaking Enabled Disabled
DIP S1-7Baud Rate 19200 bps 9600 bps
DIP S1-8Not Used
*Note: See Configuration Parameters Below
S2 Modbus Network Address Selection
Switch Position Address bit
DIP S2-1Net addr b7
DIP S2-2Net addr b6
DIP S2-3Net addr b5
DIP S2-4Net addr b4
DIP S2-5Net addr b3
DIP S2-6Net addr b2
DIP S2-7Net addr b1
DIP S2-8Net addr b0
Modbus Slave Address Table
DIP S2Slave
Address
12345678
100000001
200000010
300000011
400000100
500000101
600000110
…
…
…
…
…
…
…
…
…
255 11111111

CONFIGURATION
15
4.2 Setup Program
The setup program may only be used with an RS-232 serial connection. Use a terminal mode
program such as HyperTerminal with the baud rate set to 9600 bps, 8 data bits, no parity, 2
stop bits, and no hardware handshaking. Remove power to the charger by turning both AC
and DC circuit breakers off. To enable the setup program, set switch S1-1 to ON. To use the
user values for configuration parameters, set switch S1-2 to ON. Restore power to charger
by turning on the DC breaker first then the AC breaker. The following screen will appear:
-- EN5004 Setup --
1 DNP Device Address
2 DNP Unsol Destination Address
3 DNP Unsol Messaging Enabled
4 DNP Unsol Timeout
5 DNP Unsol Retries Amount
6 DNP Unsol Indefinite Retries
7 Comm Parity
8 Comm Stop Bits
To change a value, please select its item number:
To select an item to view and modify, enter the item number by typing the number and press
ENTER. The sample below shows item 1 DNP Device Address is selected. The current
value is set to 1. Entering a new value and pressing ENTER will accept the new value if it is
within the acceptable range. “Value written to memory” will be displayed if
accepted or “VALUE ENTERED IS OUT OF RANGE!” if not accepted. Pressing the
ESC key will cancel modifying the parameter and return to main menu.
To change a value, please select its item number: 1
DNP Device Address: 1 (Range 1 to 65,519),
Enter new value (ESC to cancel): 2
Value written to memory
If S1-2 is set to OFF for using factory default values, the parameters can be viewed. The
parameters can be modified but if S1-2 is still set to factory default values when power is
cycled, then all values will be changed back to factory defaults. Setting S1-2 ON will allow
USER values to be used. If S1-2 is OFF the screen will look like this:
-- EN5004 Setup --
USING DEFAULT VALUES (SWITCH S1-2 IS OFF)
CHANGED VALUES WILL NOT BE STORED
1 DNP Device Address
2 DNP Unsol Destination Address
3 DNP Unsol Messaging Enabled
4 DNP Unsol Timeout
5 DNP Unsol Retries Amount
6 DNP Unsol Indefinite Retries
7 Comm Parity
8 Comm Stop Bits
To change a value, please select its item number:

CONFIGURATION
16
After all parameters have been modified to the correct values, turn off the charger. Close
your terminal program and reconnect the charger to the communications network. Turn off
S1-1 to disable the setup program. Make sure all switch settings are set correctly. Turn on
the charger to initiate communications.
4.3 Factory Defaults
Configuration Parameter Factory Default Range
DNP Device Address: 11 to 65519
DNP Unsolicited Destination Address: 65519 1 to 65519
DNP Unsolicited Messaging Enabled: 0 (Off) 0 (Off), 1 (On)
DNP Unsolicited Timeout: 30 seconds 1 to 60 seconds
DNP Unsolicited Retries Amount: 20 to 255
DNP Unsolicited Indefinite Retries: 0 (Off) 0 (Limited), 1 (Indefinite)
Comm Parity: 0 (None) 0 (None), 1 (Odd), 2 (Even)
Comm Stop Bits: 1 for DNP 1 or 2
2 for Modbus RTU
1 for Modbus ASCII
4.4 Status LED (D1)
The EN5004-xx communications module pc board (A12) features a Status LED (D1) built
into the board, located to the left of the Configuration Switches (S1). See Figure 2 on page 5
for location. During normal operations the LED will flash very quickly to indicate
communications with the host computer. Use the following guide for LED troubleshooting:
4.4.1 Blinking LED
On power up the D1 will blink on and off at a steady rate of 1 sec. on and 1 sec. off to indicate that the
Modbus Address selected by the DIP switches S2 is invalid. The acceptable Modbus address range is 1-
247. For example, if all the switches for S2 are set to off for an address of 0, the LED will blink for an
invalid address.
4.4.2 LED Always Off
The LED will flash when the communications board receives and processes data from a host computer.
When the LED does not flash, then the communications board is not processing the data being sent to it by
the computer. Check the following items to al items can be the cause of no communications.
•Verify that the connection P13 is aligned properly with J13 on the main control card.
•Make sure the power supply connection J20 is plugged in.
•Measure the voltage of J20 pins 2(+) and 4(-) with J20 plugged in. It should be between 7-10vdc.
•Check the communications wiring from the host computer to the communications board.
•If the communications board is wired for RS-232 make sure RS-232 is selected in the DIP switches.
•If the communications board is wired for RS-485 make sure RS-485 is selected in the DIP switches.
•Check all the communication configuration settings.
•Verify the host computer's communications settings match the charger communications board settings
(protocol, address, baud rate, stop bits, data bits, etc.).
4.4.2 LED Always On
If the LED is always on then this indicates the communications board is not working. Check the
following:
•Verify that the connection P13 is aligned properly with J13 on the main control card.
•Make sure the power supply connection J20 is plugged in.
•Measure the voltage of J20 pins 2(+) and 4(-) with J20 plugged in. It should be between 7-10vdc.

DNP V3.00
17
5DNP V3.00
5.1 Introduction
The purpose of this section is to describe the specific implementation of the DNP3 within
EJ5037-xx Communications Interface.
This document, in conjunction with the DNP3 Basic 4 Document Set, and the DNP Subset
Definitions Document, provides complete information on how to communicate with
HindlePower, Inc. EJ5037 Communications Interface via the DNP3 protocol.
This implementation of DNP3 is fully compliant with DNP3 Subset Definition Level 2,
contains many Subset Level 3 features, and contains some functionality even beyond Subset
Level 3.
5.2 Device Profile
The following table provides a “Device Profile Document” in the standard format defined in
the DNP3 Subset Definitions Document. While it is referred to in the DNP3 Subset
Definitions as a “Document,” it is only a component of a total interoperability guide. This
table, in combination with the following should provide a complete interoperability/
configuration guide for the HindlePower AT Series Communications Interface:
• The Implementation Table provided in Section 5.3 (beginning on page 20),
• The Point List Tables provided in Section 5.4 (beginning on page 23)
DNP V3.00
DEVICE PROFILE DOCUMENT
(Also see the Implementation Table in Section 5.3, beginning on page 20.)
Vendor Name: HindlePower, Inc. -1075 Saint John Street -Easton, PA 18042
Device Name: EJ5037-XX Communications Interface
Highest DNP Level Supported:
For Requests: Level 2
For Responses: Level 2
Device Function:
£Master
TSlave
Notable objects, functions, and/or qualifiers supported in addition to the Highest DNP Levels Supported
(the complete list is described in the attached table):
Maximum Data Link Frame Size (octets):
Transmitted: 292
Received 292
Maximum Application Fragment Size (octets):
Transmitted: 2048
Received: 2048
Maximum Data Link Re-tries:
TNone
£Fixed at 3
£Configurable range 0 to 255
Maximum Application Layer Re-tries:
TNone
£Configurable
Requires Data Link Layer Confirmation:
TNever
£Always
£Sometimes
£Configurable

DNP V3.00
18
DNP V3.00
DEVICE PROFILE DOCUMENT
(Also see the Implementation Table in Section 5.3, beginning on page 20.)
Requires Application Layer Confirmation:
£Never
£Always
TWhen reporting Event Data
£When sending multi-fragment responses
£Sometimes
£Configurable
Timeouts while waiting for:
Data Link Confirm: £None TFixed at 2000 £Variable £Configurable.
Complete Appl. Fragment: TNone £Fixed at ____ £Variable £Configurable
Application Confirm: £None TFixed at 2000 £Variable £Configurable,.
Complete Appl. Response: TNone £Fixed at ____ £Variable £Configurable
Others:
Inter-character Timeout: TFixed at 50 ms.
Select/Operate Arm Timeout: TFixed at 5000 ms.
Binary input change scanning period: TFixed at 5000 ms.
Analog input change scanning period: TFixed at 5000 ms.
Unsolicited offline interval: TFixed at 30000 ms if unsolicited messages is off
Configurable if unsolicited messages is on. See setup.
Unsolicited response notification delay: TFixed at 15000 ms.
Delay Measurement: 100 ms.
Synchronization: 1000 ms.
Sends/Executes Control Operations:
WRITE Binary Outputs £Never TAlways £Sometimes £Configurable
SELECT/OPERATE £Never TAlways £Sometimes £Configurable
DIRECT OPERATE £Never TAlways £Sometimes £Configurable
DIRECT OPERATE –NO ACK £Never TAlways £Sometimes £Configurable
Count > 1 TNever £Always £Sometimes £Configurable
Pulse On TNever £Always £Sometimes £Configurable
Pulse Off TNever £Always £Sometimes £Configurable
Latch On £Never TAlways £Sometimes £Configurable
Latch Off £Never £Always TSometimes £Configurable
Queue TNever £Always £Sometimes £Configurable
Clear Queue TNever £Always £Sometimes £Configurable
Explanation of Sometimes: See the Binary Outputs point list in Section 5.4.2 starting on page 24 for a
description of which control operations are supported for each point.
Table of contents
Popular Control Unit manuals by other brands
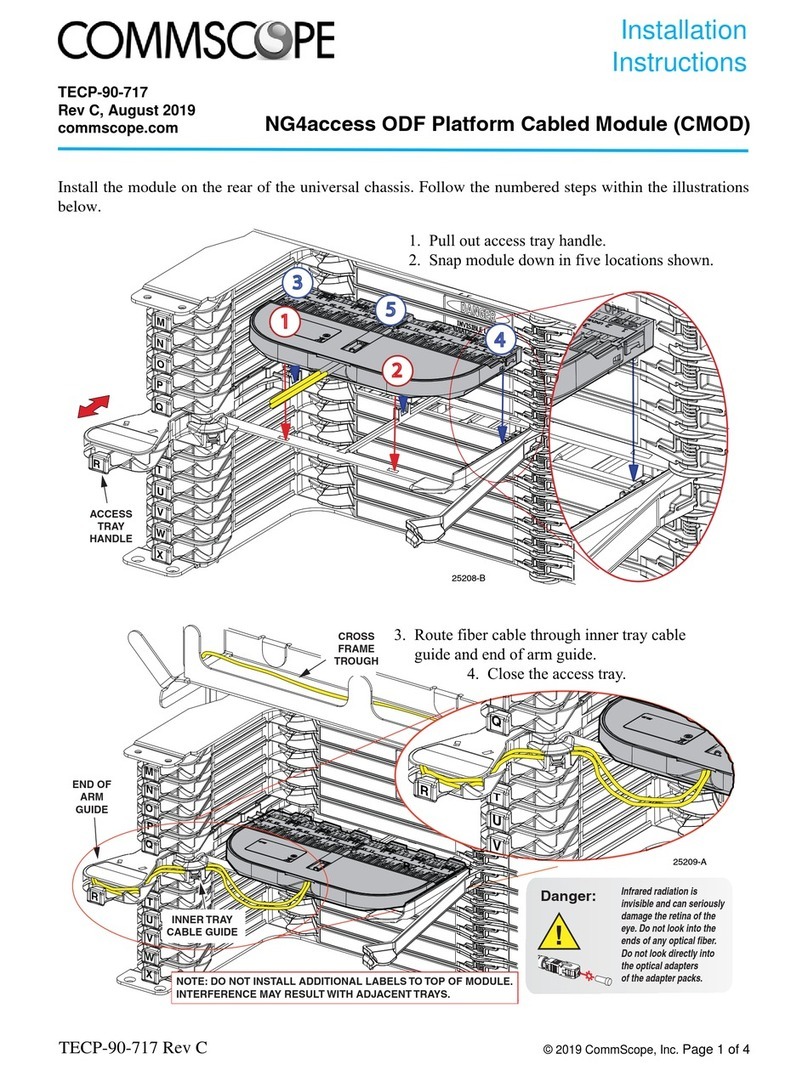
CommScope
CommScope CMOD installation instructions

GEM
GEM R639 operating instructions
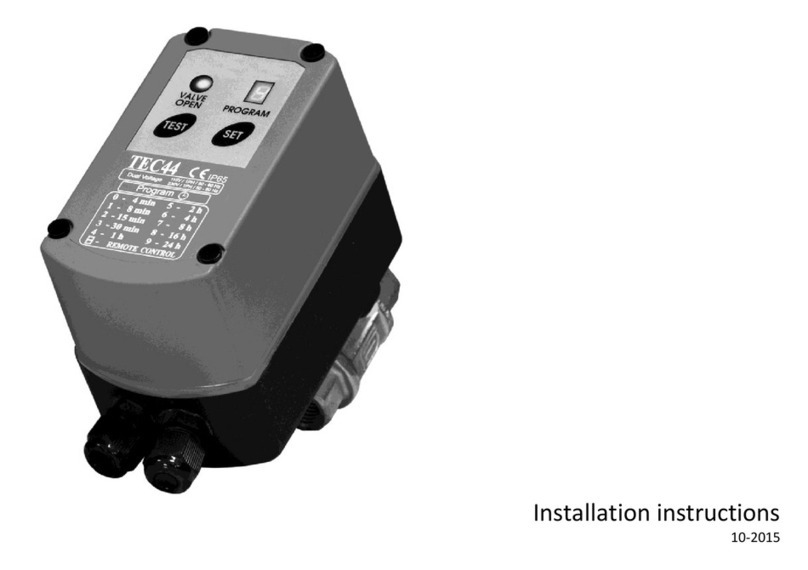
Jorc
Jorc TEC-44 installation instructions
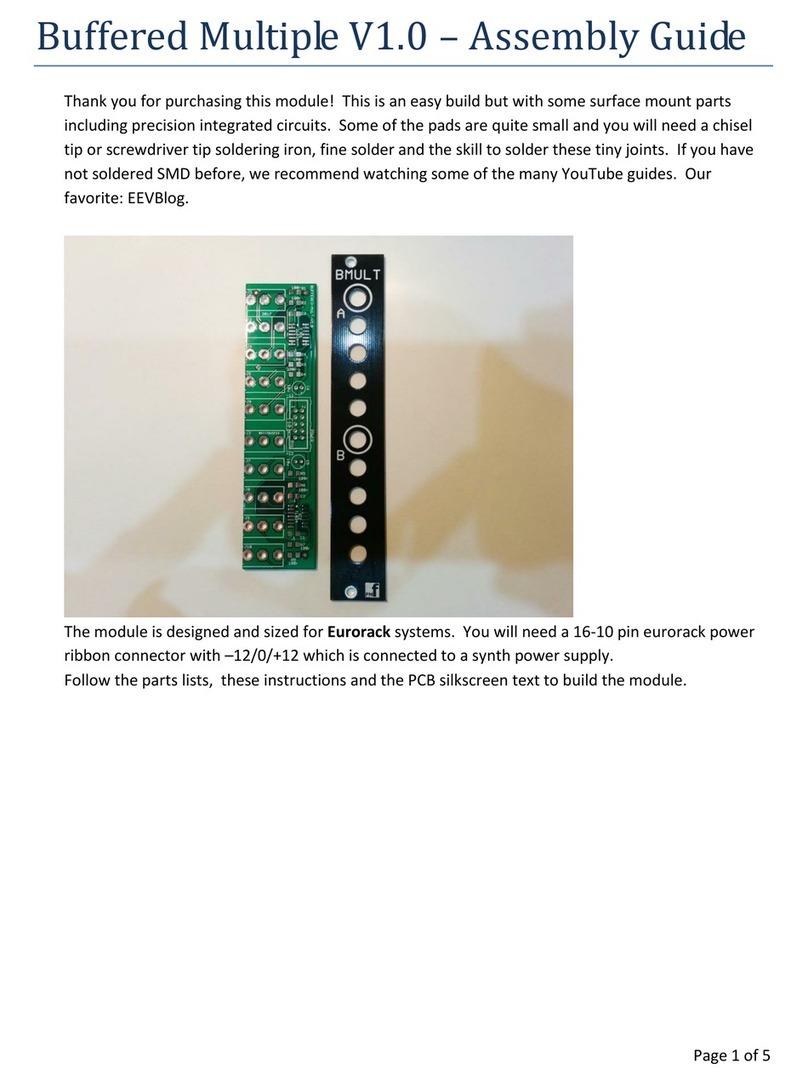
PMFoundations
PMFoundations Buffered Multipl Assembly guide
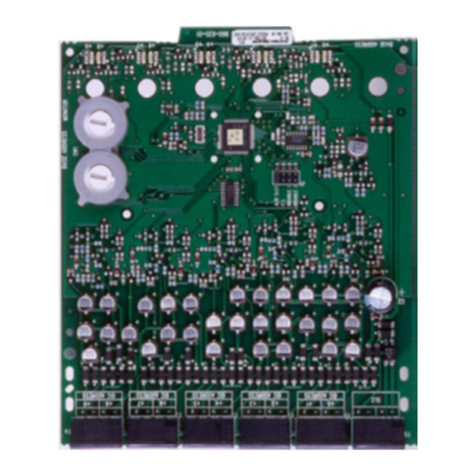
Fike
Fike FIK-IM-10 Installation and maintenance instructions
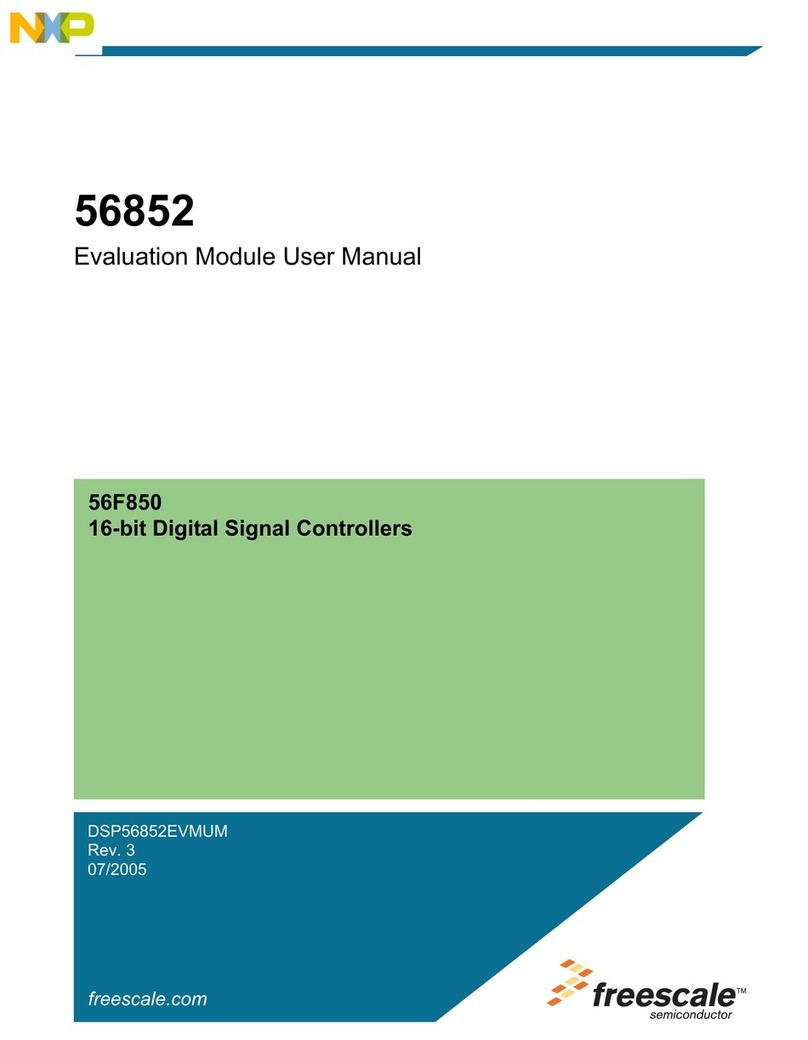
Freescale Semiconductor
Freescale Semiconductor 56852 user manual