horsch DrillManager User manual

Operating Instructions
Art.: 80660206 en
Read carefully prior to starting up!
Keep operating instructions in a safe place!
10/2012
DrillManager
Software 8.52


- Translation of the Original Operating Instructions -
Machine Identication
The corresponding data is to be entered into the list below upon
receiving the machine:
Serial number: .......................................
Machine type: .......................................
Year of construction: .......................................
Initial installation: .......................................
Fittings: .............................................................
..........................................................................
..........................................................................
..........................................................................
Publication date of Operation Manual: 10/2012
Latest change:
Address of Retailer: Name: ......................................................................
Road: ......................................................................
Town/City: ......................................................................
Tel.: ......................................................................
Customer No.:
Retailer: ......................................................................
Address of HORSCH: HORSCH Maschinen GmbH
92421 Schwandorf, Sitzenhof 1
92401 Schwandorf, Postbox 1038
Tel.: +49 (0) 9431 / 7143-0
Fax: +49 (0) 9431 / 41364
Customer No.:
HORSCH: ......................................................................
80660206 DrillManager en

2
Table of contents
DrillManager..................................................4
Description......................................................4
Wiring loom of machine ................................7
Installing the DrillManager..............................9
Installation on tractors with
ISOBUS equipment ......................................9
Installation on tractors without
ISOBUS equipment ......................................9
Terminal .......................................................10
Operation....................................................11
Terminal settings ........................................12
Menu overview .............................................14
Screen display work mask............................15
Adapting the work screen ...........................15
Function symbols..........................................16
Bout marker and hydraulic control..............17
Half width shut o .......................................18
Menu overview Calibration .........................20
Seed calibration............................................21
Rotor selection............................................24
Seed Check ................................................29
Performance data .......................................29
Input of machine data ................................30
Joining of hoppers ....................................34
Tram line rhythm.........................................39
Seed ow monitoring ...................................52
Entering sensor numbers for FGS..............52
Setting the sensitivity..................................53
Seed ow monitoring ..................................53
Alarm message...........................................54
Seed ow diagnose ....................................54
Diagnostics program.....................................55
Alarm overview...........................................57

3

4
DrillManager
The HORSCH DrillManager is an electronic
control unit for drills and their components.
It regulates, monitors and controls all connected
assemblies in the drill.
You should only start up the DrillManager
after you have read the operating
instructions and are familiar with the
operation.
Strict compliance with the applicable accident
prevention instructions and other established
regulations concerning technical and industrial
health and safety is mandatory when working
with the DrillManager.
Description
The HORSCH DrillManager is a complete
system in which the modules included in the
equipment must only be activated.
The complete system consists of the following
components:
¾Computer
¾Monitor
¾Modules, depending on machine type and
equipment, for:
one to three metering drives for seed, fertiliser
or liquid fertiliser
hydraulic control for raising, wings and bout
marker indicator control
half-side control
Seed ow monitoring
¾Sensors for:
fan
forward speed (radar)
hopper empty indicator (2 channels)
¾connection for work signal
¾switch for calibration
All components and sensors are connected to
computer and monitor by means of the wiring
loom.
The computer receives the information, evaluates
these and displays the operating status and data
on the monitor.
If entered or xed default values are exceeded
or fallen short of, or in case of malfunctions the
monitor display is interrupted and the fault is
indicated.
The monitor thereby identies the corresponding
component or the limit value that has been
exceeded.
Depending on the version the machine is
equipped with one or two computers.
Computer with one and two 16-pin plugs
Stickers on the computer inform about the
hardwar status, the software status is displayed
in the “Diagnose” menu.
Maintenance
The system is maintenance free. You should
keep an eye on the computer and the cable
connections when washing the machine.
Do not clean the computer, the plugs
and any of the electronic components
with high pressure cleaning equipment
or a direct water jet.

5
Description of the computer
Computers with black plastic end plates have
program “version 8.xx” installed.
These computers can be operated with HORSCH
terminals, external ISOBUS terminals and with
ISOBUS compatible tractor terminals.
Machines with two computers
On machines with two metering drives two
computers are installed in the machine and
tightly connected together with a cable.
On drills which are temporarily combined with
an additional metering drive, like DuoDrill or
Maistro, the computers of both machines are
connected with a 16-pin plug.
The socket of this connection has an integrated
ISO-Bus termination and can thus can only be
replaced by an original cable in case of a repair.
Computer version
The computer is available in three dierent
hardware versions, whereby two of these
versions look optically exactly the same. It is
therefore very important to look for the article
numbers when carrying out repair work.
No. 00345005 (standard computer)
¾Installed in all machines with just one
computer;
¾Is able to control two metering drives;
¾Is always programmed with the master
version 8.xx 49;
¾Cable inlet: One 16-pin plug;
No. 00345069 (dual computer)
¾Installed as master computer in all machines
with two computers;
¾In connection with the second computer this
computer is able to control three metering
drives or two metering drives and the Maistro;
¾Is always programmed with the master
version 8.xx 49;
¾Cable inlet: Two 16-pin plugs;
No. 00345091 (additional computer)
¾Is used a second computer in machines with
two computers
¾Supports the main computer in the control of
the third metering drive
¾Is always programmed with the slave version
8.xx 4a;
¾Cable inlet: One 16-pin plug
Programs
The programs can be identied by their ending,
e.g. 8.xx 49 for the master version and 8.xx 4a
in the slave version. This ending can only be
recognized during programming.
On machines with dual computers the new and
old computer versions must not be combined.
When replacing an old computer it may be
necessary to replace both computers.
The programs in both computers must also be of
the same version, e.g. 8.52 49 only with 8.52 4a.
In case of incorrectly combined program
versions errors and malfunctions may
occur.

6
Pin
No.
Colour Function Colour
/ No. of
part
37 bl/rd Radar signal gn
38 br/wh Rotary speed 2 (right)
Metering unit 2 lling level
sensor
gn
39 gn/wh Fan signal gn
40 rd/ye Hopper 1 lling level sensor gn
41 bk/ye Metering unit 1 lling level
sensor
gn
42 bl Ground 0 V power
Ring ye Shielding (motor) ye 6
Cable assignment on on connecting cable
20 and 16 pin plug
Plug
20 pin on
tractor
Cable
No.
Function Plug
16 pin on
Computer
A 1 1 1
A 2 2 Can Low 2
A 3 3 Can GND 3
A 4 4 0 Volt electronics 4
A 5 5 0 Volt power 5
A 6 6 0 Volt power 6
A 7 7 0 Volt power 7
A 8 8 0 Volt power 8
A 9
A 10
B 1 9 9
B 2 10 Can High 10
B 3 11 Can EN 11
B 4 12 12 Volt
electronics
12
B 5 13 12 Volt power 13
B 6 14 12 Volt power 14
B 7 15 12 Volt power 15
B 8 16 12 Volt power 16
B 9
B 10
Cable assignment on the 42 pin plug
Pin
No.
Colour Function Colour
/ No. of
part
1 gr Motor 2 plus 12 V power rd
2 gn Half width signal right 3
3 ye Half width signal left 4
4 gr Rotary speed 1 (left)
Hopper 2 lling level sensor
gn
5 pu Hydr. boutmarker left 1
6 rd Hydr. boutmarker right 2
7 bk Tram line +/- right 1
8 vi Tram line -/+ right 2
9 or Tram line +/- left 3
10 br/gn Tram line -/+ left 4
11 wh/rd Pre-emergence marker right 5
12 gn/bl Pre-emergence marker left 6
13 - - -
14 - - -
15 gn Motor 1 minus power bl 1
16 rd/bl Work position signal br
17 ye/bk Motor 1 current
measurement
18 wh/bk Half width signal middle gn
19 rd/bk Hydr. "Lift" 3
20 br/ye Hydr. "Wings" and horn 4
21 rd/wh Liquid fertiliser ball valve +/-
Fan control +/-
br
22 rd/gn Liquid fertiliser ball valve -/+
Fan control -/+
bl
23 - - -
24 br/bk Liquid fertiliser solenoid
valve
25 bl/ye Half width motor +/- 1
26 bl/gn Half width motor -/+ 2
27 - - -
28 br Motor 2 minus power bl
29 rd Motor 1 plus 12 V power rd 2
30 gr/rd Calibration switch signal br
31 gn/gr Motor 2 current
measurement
32 br Sensors all 12 V plus br 4
33 wt Sensors all 0 V electr. wt 3
34 gn/pk Liquid fertiliser. Sensor /
signal coulter pressure
adjustment
gn
35 ye/bl Motor 2 signal gn
36 gn/bk Motor 1 signal gn 5

7
Wiring loom of machine
The wiring loom is adapted to match the
corresponding machine type and prefabricated
with plugs for all equipment variants.
In order to avoid malfunctions caused by dirt,
all open plugs must be closed with blind caps
or similar.
Wiring loom
Pin assignment in all 3 pin plugs
1 - ground cable, white
2 + plus cable, brown
3 signal cable, green
Plug designations:
A Work signal
B1 Bridging metering unit 1
B2 Bridging metering unit 2
D1 Speed monitoring, shaft 1
D2 Speed monitoring, shaft 2
G Fan
H Horn
R Radar - speed
S Signal middle position of half width
SV Coulter pressure adjustment
T1 Filling level monitoring seed hopper 1
T2 Filling level monitoring seed hopper 2
K Ball valve (liquid fertiliser)
D Flow sensor (liquid fertiliser)
2 pole at plug with diode - shut-o valve
Cable 8 pole automatic tram line control set
to "Magnet".
1 + Valves right
2 + Valves right
3 + valves left
4 + valves left
5 + Pre emergence markers right
6 + Pre-emergence markers left
7 - Ground all
8 - Ground all
Cable 8 pole automatic tram line control set
to "Motor".
1 + / - Motor right
2 - / + Motor right
3 + / - Motor left
4 - / + Motor left
5 + Pre emergence markers right
6 + Pre-emergence markers left
7 - Ground
8 - Ground
6 pole hydraulic control, "Lift", "Wings" and
"Bout marker".
1 + Bout marker left
2 + Bout marker right
3 + Lifting / lowering
4 + Wings
5 - Ground all
6 - Ground all
5-pin half width control
1 Adjustment motor + / -
2 Adjustment motor - / +
3 Signal right
4 Signal left
5 Signal output
7-pin Motor metering drive
1 - blue
2 + red
3 white
4 brown
5 green
6 yellow

8
ed jul 11
DatumEntw.DateinameZeichnungsnummerMaschine Zeichnung
Stecker 42 pol saetech
-
+
sig
1
2
3
4
5
6
7
Motor -
Motor +
Sensor -
Sensor +
Sensor Signal
Abschirmung
-
+
sig
1
2
3
4
5
6
7
Motor -
Motor +
Sensor -
Sensor +
Sensor Signal
Abschirmung
1
2
4
5
6
7
gn/ge
Motor rechts +/-
Motor rechts -/+
Motor links +/-
Motor links -/+
Vorauflaufmarkierer rechts +
Vorauflaufmarkierer links +
Masse für 5 und6
Masse für 5 und6
3
-
+
sig
-
+
sig
-
+
sig
-
+
sig
-
+
sig
-
+
sig
FGS
Motor 1
Motor 2
Verteiler
-
+
sig
-
+
3
Masse Spuranz.
Heben
1
2
3
4
5
6
7
8
9
10
11
12
13
14
15
16
17
18
19
20
21
22
23
24
25
26
27
28
29
30
31
32
33
34
35
36
37
38
39
40
41
42
gn
ge
gr
rs
rt
sw
vi
or
br / gn
ws / rt
gn / bl
gn
rt / bl
ge / sw
ws / sw
rt / sw
br / ge
rt / ws
rt / gn
br / sw
bl / ge
bl / gn
br
rt
gr / rt
gn / gr
br
ws
gn / rs
ge / bl
gn / sw
bl / rt
br / ws
gn / ws
rt / ge
sw/ ge
bl
ge
Radar
Arbeitssig
Tank 1
Tank 2 /
Welle 1
Dosier 1
Abdrehen 1
Abdrehen 2
Dosier 2 /
Welle 2
Gebläse
Fl. Dünger sen /
Schardruckverst.
Halbs. Mittelst.
Kugelhahn /
Gebläseregelung
Abschaltvent.
Halbs. Mot u.
links u. rechts
Hydraulik
M1
M2
Spuranr. l
Spuranr. r
Klappen
Masse He. u. Kl.
rt
gn
123 123 123 123 123 123 123 123 123 12 4564512 12
+ / -
- / +
+ / -
- / +
sig r.
sig l.
sig
Platine Strommessung
gr
123
Hupe
123
mit Hupe u Radar Stecker in AMP 3 pol. Kabelfarben am42 pol geändert durch ME seit ca. 2008
Wiring loom - drill

9
Installing the DrillManager
The DrillManager is delivered with an ISOBUS
compatible software and and ISOBUS connecting
cable.
The ISOBUS functions can be utilized with the
HORSCH terminal, the Comfort terminal or the
tractor's ISOBUS terminal.
Installation on tractors with
ISOBUS equipment
In case of existing ISOBUS equipment on the
tractor, the drill can be controlled from the tractor
terminal or from an additional terminal.
Control with tractor terminal
¾Plug the machine connecting cable into the
ISOBUS socket on the tractor and switch on
the terminal.
¾When switching on, the control screens are
automatically loaded and the drill can be
controlled with the tractor terminal.
Control with an additional terminal
¾Plug the machine connecting cable into the
ISOBUS socket on the tractor.
¾Fasten the terminal at a suitable place in the
cabin. The vision on the road should not be
impaired.
¾Connect the terminal to the ISOBUS socket in
the cabin by using the supplied cable.
¾When switching on, the control screens are
loaded and the drill can be controlled with
the terminal.
Installation on tractors without
ISOBUS equipment
For all tractors without ISOBUS equipment the
basic equipment must be installed in the tractor
during the initial installation.
The cables for the basic equipment must be
directly connected to the tractor battery.
The cables must be protected against chang
and the insulation must not be damaged.
Basic equipment ISOBUS
The battery connections must have good con-
tact. Assembly faults will lead to voltage drop
and indenable error messages and failures.
¾Assemble the terminal bracket in a suitable
place within the view and the operating range
of the driver.
¾Fasten the ISOBUS socket in a suitable place
at the rear end of the tractor.
¾Route the thick cable to the battery, extend
it if necessary.
¾Connect both fuse holders tightly and durably
with the cable.
¾Connect the two red cables tightly with battery
plus and the two black cables with battery
negative.
¾Plug the connecting cable in at the bottom of
the terminal.

10
Terminal
The terminal is plugged on the pre-assembled
bracket in the tractor and connected to the
computer by means of a cable.
Terminal with colour display and keyboard
1. On/O button
2. Function keys
3. not assigned
4. not assigned
5. ESC-button
- Cancel input
- Exit mask
- Hide warning messages and alarms
6. Invoking / exiting selection menu
7. Rotary button
- Selection, input and conrmation
8. Connection of USB plug
The keys (2) on the display have no fixed
functions assigned to them. They will always
switch the function currently displayed.
The displayed screen contents may
vary from the illustration depending on
the respective program version.
4
3
1
2
7
6
8
5
The cables must under no circum-
stances be connected to any other
plugs in the cab.
The plugs are unable to transfer the
required current (A). Voltage losses
and drilling faults will occur.
The terminal should not obstruct the
eld of vision to the road.

11
Operation
Switching on
Press the "On/O" button momentarily.
After a new start and after changing or
reprogramming the computer the data will be
loaded from the computer.
Restart the system
Once the terminal has been connected to the
ISOBUS of the tractor, the computer is not
automatically restarted when the terminal is
switched o and on.
To restart the system you must
disconnect the connecting cable to the
machine for a short moment.
It is highly recommended to make a note of the
machine and adjustment data before running
an update.
In case of update of minor extent the data will
be maintained.
With extensive updates and if new graphics
have to be displayed, the old adjustment and
performance data may be lost.
With some system dependent faults it may be
necessary to delete the control masks from the
terminal and to upload these again from the
computer by restarting.
The pool will in this case saved again in the
terminal.
Deleting the pool
Choose the "Service" area. In the menu "File
management" select "Pools" and delete the rst
le for the drill and the second le for the single
grain metering.
The switch the terminal o for a moment. The
masks will be loaded new during a restart.

12
Terminal settings
The settings for the terminal:
¾brightness /display)
¾volume (alarm)
¾date / time
¾language selection
¾measuring units
¾keyboard illumination
are set in the "Service" menu option.
Press button (6) to open the selection menu.
Turn the rotary wheel to mark and confirm
"Service".
Turn the rotary wheel to mark and confirm
"Terminal setting".
Setting and changing inputs
Before initial start-up some settings must be
entered in to the system.
The selection, input and conrmation of text or
numericals is accomplished via the rotary button.
Use the rotary button to place the marking over
the numerical or the term and press the rotary
button to conrm.
For the terms / words all selectable possibilities
appear, for the numericals the table with the
numbers 1 - 10 with two arrows and OK.
Changing numerical values
If the number is not to be changed, press the
rotary button to conrm the number.
To change the number with the rotary button
select the desired number and press the rotary
button to conrm.
The system will automatically change to the
next number.
With the arrow keys the desired cipher can be
directly selected.
For the terms mark the new term / word with the
rotary button and press to conrm.

13
Place and conrm the marking with the rotary
wheel.
Turn the rotary wheel to change the value or
e.g. choose the country specic language and
conrm again.
e.g. language selection
Adapt the settings for brightness, contrast and
keyboard illumination to the light conditions and
your personal appreciation.
Set the volume as loud as possible. Alarm
messages should be audible in your tractor,
even when used in the eld.
Once the settings have been made the terminal
must be switched o and on again.
Depending on the changes, e.g. in language or
the measuring units, the terminal must rst load
the new language or measuring units from the
computer of the machine.
The following languages are currently available:
German de
English en
French fr
Danish da
Polish pl
Czech cs
Romanian ro
Spanish es
Swedish sv
Hungarian hu
Serbian sr
Russian ru
Estonian et
Lithuanian li
Latvian lv
Bulgarian bg
Croatian hr
Finnish
Italian it
Settings and activation for GPS functions like
- Task Manager
- TRACK Leader II
- Section Controll etc.
are described in a dedicated instruction manual.

14
ed sep 08
DatumEntw.DateinameZeichnungsnummer
Maschine Zeichnung
pfeil
ed sep 08
DatumEntw.DateinameZeichnungsnummerMaschine Zeichnung
pfeil
ed sep 08
DatumEntw.DateinameZeichnungsnummerMaschine Zeichnung
pfeil
ed sep 08
DatumEntw.DateinameZeichnungsnummerMaschine Zeichnung
pfeil
ed sep 08
DatumEntw.DateinameZeichnungsnummer
Maschine Zeichnung
pfeil
ed sep 08
DatumEntw.DateinameZeichnungsnummerMaschine Zeichnung
pfeil
ed sep 08
DatumEntw.DateinameZeichnungsnummerMaschine Zeichnung
pfeil
ed sep 08
DatumEntw.DateinameZeichnungsnummerMaschine Zeichnung
pfeil
ed sep 08
DatumEntw.DateinameZeichnungsnummer
Maschine Zeichnung
pfeil
ed sep 08
DatumEntw.DateinameZeichnungsnummer
Maschine Zeichnung
pfeil
ed sep 08
DatumEntw.DateinameZeichnungsnummer
Maschine Zeichnung
pfeil
ed sep 08
DatumEntw.DateinameZeichnungsnummer
Maschine Zeichnung
pfeil
ed sep 08
DatumEntw.DateinameZeichnungsnummerMaschine Zeichnung
pfeil
Menu overview
Start
Diagnostic
Work screens
Machine data
ed sep 08
DatumEntw.DateinameZeichnungsnummerMaschine Zeichnung
pfeil
for calibration
Performance data
Drive a distance of 100 m
Setting the tram lines
5 sec.

15
Page three of the work mask is mainly needed
for calibration, to adjust the sensitivity of seed
ow monitoring during operation and for trouble
shooting in case of blockage and with defective
sensors.
Page three of work mask
Pages two and three of the work masks
automatically return to the rst page after
10 seconds during drilling.
The arrow key can also be used to scroll back
to page one.
Adapting the work screen
The rst page of the work screen can be adapted
to your own wishes and practical use, whenever
required.
In this case a new display page is placed in front
of the rst standard page.
You can congure this page yourself in the
menu "Machine configuration" under menu
option "extra key selection" (see machine
conguration).
Screen display work mask
After switching on page one of the work mask
will always be displayed.
The displayed image will always depend on the
setting and the available equipment.
Page one of work mask
Work mask second page

16
Function symbols
The symbols in the display represent the
functions of the corresponding keys.
Stop button for tram line:
The button prevents the rhythm
being switched further after the
machine has been lifted out of
work. The function is indicated with
STOP between the tracks.
The tram line rhythm is increased
by one track with every operation
of the key.
The track number is displayed
between the tracks.
In case of a tram line track the
switched tracks are black under
laid.
In addition, the closed coulter rows
no longer appear in the display
during the sowing.
If the machine is equipped with the hydraulic bout
marker control, the symbol for the alternating
bout marker will appear instead of the
"Tram Line +" symbol when pressing "STOP
Tram Line".
This button can now be used to
change the side for the bout marker.
If stationary with the drill lowered
by pressing the meter fill drill
function, the metering unit will start
up over a specified time. If the
computer receives a speed signal
during this period, the computer will
take over the control.
Post mode:
The post mode disables the
hydraulic "Lifting" function.
When operating the control unit only
the bout marker will be hydraulically triggered.
The machine remains in working position. The
work signal is hydraulically blocked and the tram
line will not count on.
Seed quantity 100 %:
If the seed quantity had been
adjusted with the +% or -% keys,
pressing this key will switch back to
the default seed quantity in kg/ha.
With the adjustment keys +% or -%
the seed quantity can be set and
reset in several steps.
The seed quantity is displayed in % by the
display above the hopper. The percentage step
can be changed in the machine data. There you
can also select whether only the seed quantity
is to be changed, or also the fertiliser quantity.
Switching the drill function ON / OFF:
With the drill function switched o
the display will show STOP under
the drill.
If the drill function is switched on,
the drill is lowered to work position
and the computer receives a speed
signal,
the computer will start the control
process.
Continue to next page:
If the hydraulic bout marker control
or the half width control is activated,
the next page will show the menu
for bout marker control, lifting and
folding of the machine half width
switch o.

17
Bout marker and hydraulic
control
Menu image second work page - hydraulic functions
The enabled functions appear in the display
next to the drill.
Both bout markers are lifted out or
lowered together with the machine.
Only the left hand bout marker will
be operated.
Only the right hand bout marker will
be operated.
Alternating mode: Left and right
hand bout markers lift and lower
alternately.
This is the normal drill work mode.
When switching on this bout marker control also
always activates the hydraulic "Lifting" function.
Folding / unfolding the machine
With all foldable machines this key is used to
switch the hydraulic valve block over to "Folding".
The functions "Lifting / Lowering" and the drill
function are switched o.
Lifting and lowering the machine
The function "Lifting / Lowering" is automatically
activated when activating the bout marker
function. If the bout marker is switched on, the
rst actuation of the key will switch o the bout
marker and the second actuation will disable the
"Lifting / Lowering" function.
"Wet hole" function
In certain situations, e.g. if the machine sinks in
at very wet patches in the eld, this function can
be used to raise the machine. The work signal
is thereby not interrupted and the tram line will
not switch further.
Return to the normal drill function by pressing
the key again and by pressing the key for the
desired bout marker function.
Continue to next page

18
The signals for both end positions are transmitted
from the motor to the computer. The signal for
middle position is switched by the sensor on the
metering unit.
Continue to next page
Half width shut off
After selecting the half width shut
o in the machine conguration, the
two symbols for left and right hand
on the second work page.
As soon as a key for shutting down a half width
is pressed, the corresponding half width will ash
in the displayed graph, until the sensor sends
a signal to the computer when end position is
reached.
In end position the closed half width is hidden.
The seed quantity is reduced by half, the seed
quantity display in kg/ha remains unchanged,
because the working width has also been
halved.
After pressing the same key again the total
working width is available again and the display
shows the complete machine.
Table of contents
Other horsch Control Unit manuals
Popular Control Unit manuals by other brands
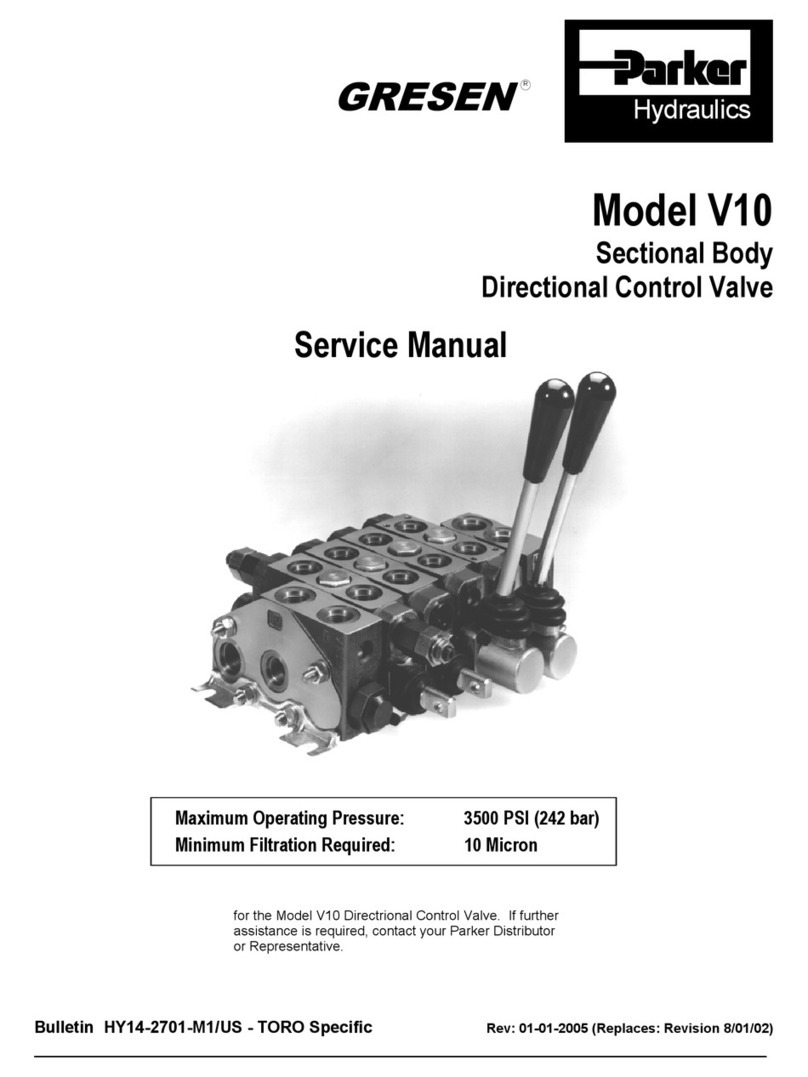
Parker Hydraulics
Parker Hydraulics GRESEN V10 Service manual
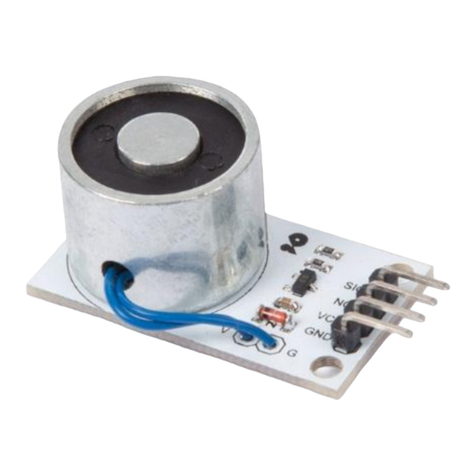
Velleman
Velleman VMA431 user manual

Honeywell
Honeywell Gamewell FCI Velociti Series Installation and maintenance instructions
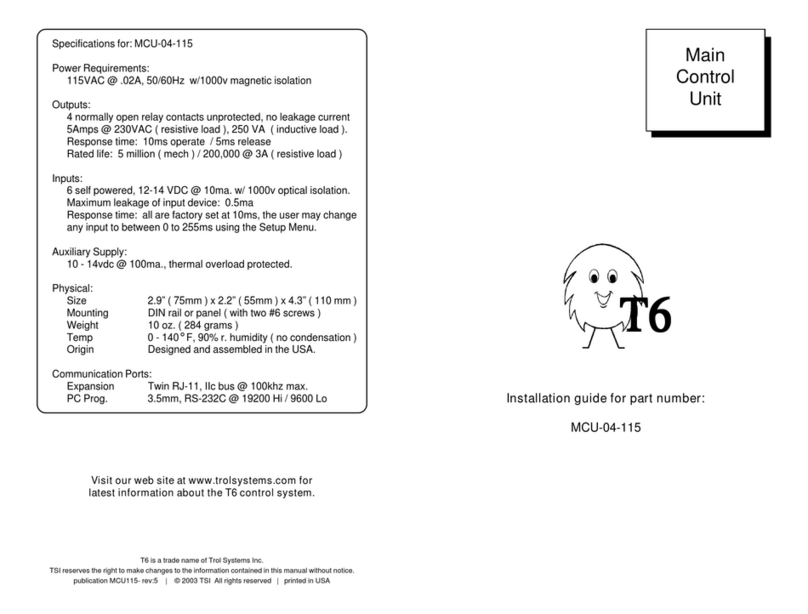
Trol Systems
Trol Systems MCU-04-115 installation guide
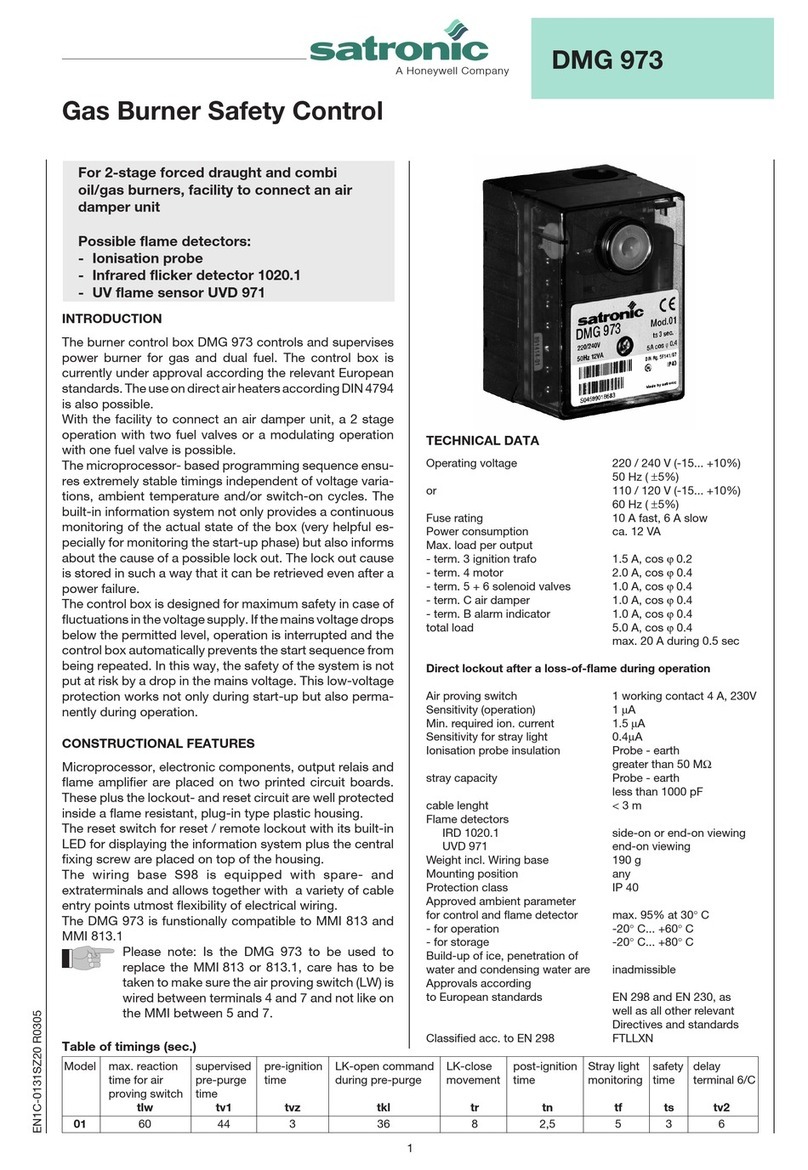
Honeywell
Honeywell Satronic DMG 973 manual

ABB
ABB RBIP-01 user manual
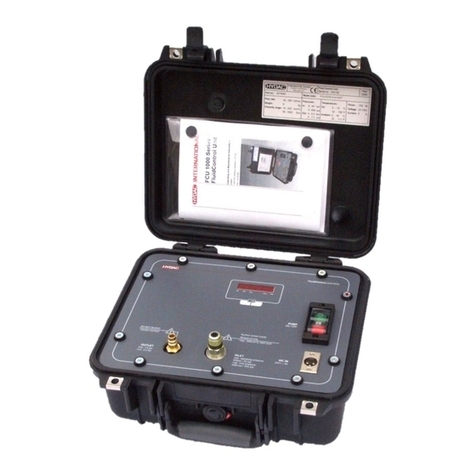
HYDAC FILTER SYSTEMS
HYDAC FILTER SYSTEMS FCU 1210 Operating and maintenance instructions
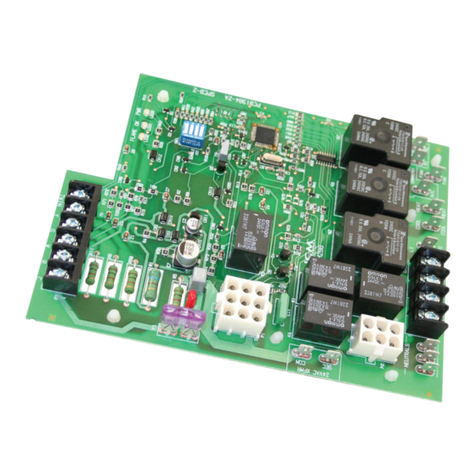
ICM Controls
ICM Controls ICM288 manual
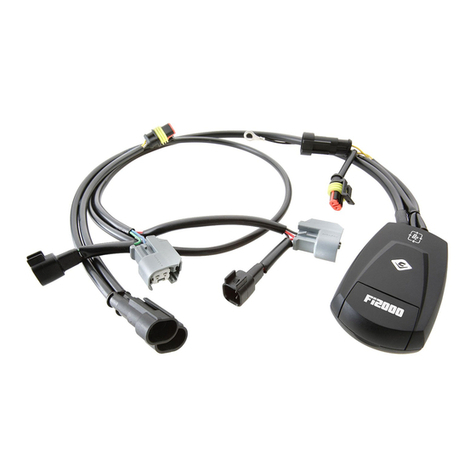
Cobra USA
Cobra USA Fi2000 quick start guide
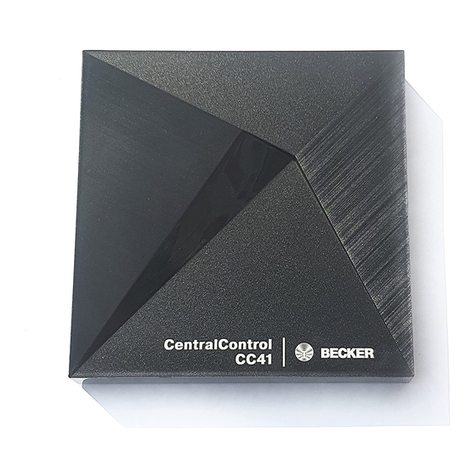
Becker
Becker CentralControl CC41 Commissioning Instruction
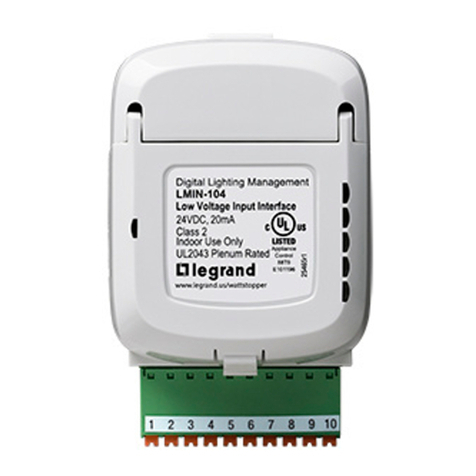
LEGRAND
LEGRAND Wattstopper LMIN-104 installation instructions
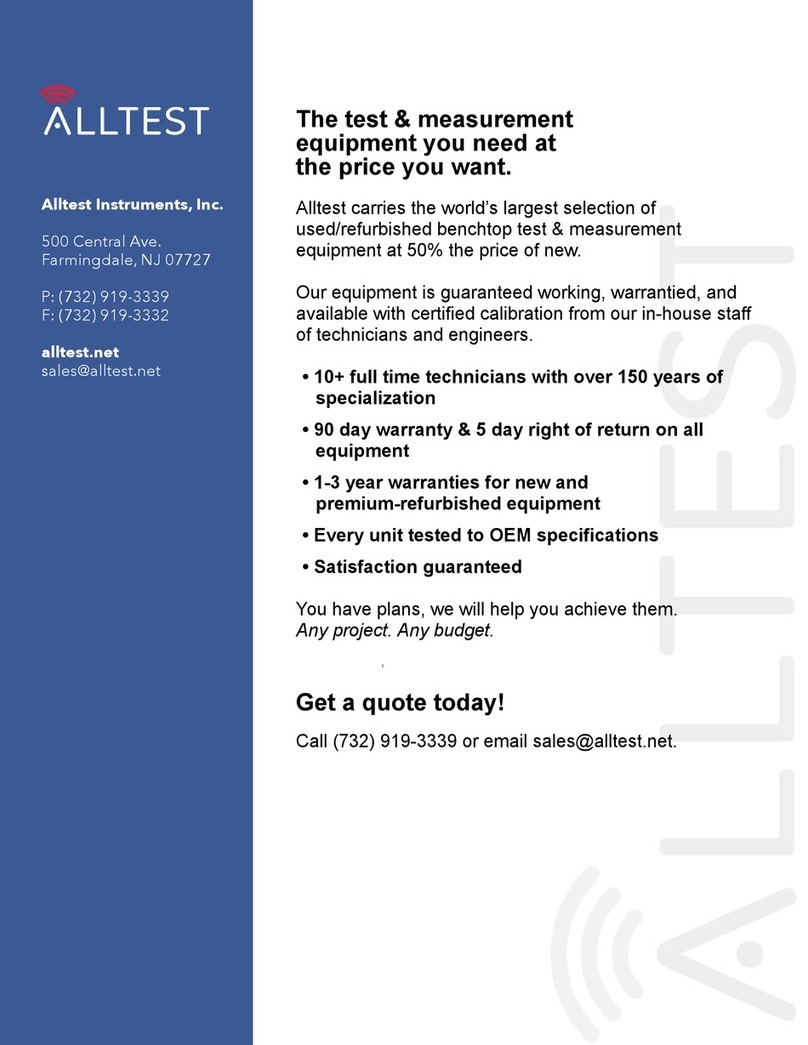
Tektronix
Tektronix 80C00 user manual