Hukseflux TPSYS20 User manual

TPSYS20 manual v2202 2/75
Cautionary statements
Cautionary statements are subdivided into four categories: danger, warning, caution and
notice according to the severity of the risk.
DANGER
Failure to comply with a danger statement will lead to death or serious
physical injuries.
WARNING
Failure to comply with a warning statement may lead to risk of death or
serious physical injuries.
CAUTION
Failure to comply with a caution statement may lead to risk of minor or
moderate physical injuries.
NOTICE
Failure to comply with a notice may lead to damage to equipment or may
compromise reliable operation of the instrument.

TPSYS20 manual v2202 3/75
Contents
Cautionary statements 2
Contents 3
List of symbols 4
Introduction 5
Accessories 9
1Ordering and checking at delivery 10
Ordering TPSYS20 10
Included items 10
2Instrument principle and theory 12
Operating principle of thermal needle probes 12
Measurement and Control Unit 14
Measurement model and data analysis 15
3Specifications 18
Specifications of TPSYS20 18
Dimensions of TPSYS20 22
4Installation and connection 23
Hardware installation 23
Opening the graphical user interface 24
Setting the system clock 25
Setting the net frequency filter 26
Overview of the graphical user interface 26
5Making measurements 31
Setting the thermal needle probe parameters 31
Thermal needle probe calibration 32
Thermal conductivity measurements 35
Retrieving measurement data 40
6Data analysis 43
The tool 43
Data import 45
Analysis process 46
Analysis results 49
7Maintenance and trouble shooting 52
Recommended maintenance and quality assurance 52
Trouble shooting 53
8Appendices 55
Theory 55
Uncertainty assessment 58
Thermal properties of some common materials 60
Calibration 62
Using the external trigger input 65
TPSYS20 field use 66
Thermal needle probe wiring 70
LoggerLink app 71
Campbell Scientific Device Configuration Utility 72
EU declaration of conformity 74

TPSYS20 manual v2202 4/75
List of symbols
Quantities Symbol Unit
Heater current IA
Heater electrical resistance per unit length RL
Heater length Lm
Heater power QW/m
Heating time theat s
Specimen diameter Dspecimen m
Temperature T°C
Temperature difference
Δ
TK
Time ts
Thermal conductivity λ
Thermal diffusivity αm2/s
Thermocouple sensitivity SmV/K
Expanded uncertainty in a U(a) units of a
Standard uncertainty in a u(a) units of a
(Relative) expanded uncertainty in a U(a)/a%
(Relative) standard uncertainty in a u(a)/a %
Coverage factor of U(a) k -
Acronyms
GUI Graphical User Interface
KD Keyboard Display
MCU Measurement Control Unit
PC Personal Computer
PSU Power Supply Unit

TPSYS20 manual v2202 5/75
Introduction
TPSYS20 is an accurate and user friendly system for measuring thermal conductivity. Its main
components are the TP02 thermal needle probe (or its smaller equivalent, model TP08), the
MCU Measurement and Control Unit and software.
This user manual describes the use of the TPSYS20 system in combination with TP02 or TP08.
There are slight differences in requirements for heating time, specimen size and the use of
containers for the specimen. For more details about the TP02 and TP08 thermal needle probes
themselves, please consult the separate TP02 and TP08 user manuals. The general text of the
TPSYS20 user manual covers laboratory experiments. Field measurements are possible as
well, but are less common. These are treated in the appendix.
TP02 and TP08 are designed for measuring thermal conductivities in the range from 0.1 to
6.0
thermal conductivity of a specimen is determined from the step response of the specimen
temperature to heat from a linear heater. The MCU takes care of the measurement and control
process and provides a convenient graphical user interface in the form of a webpage. TPSYS20
is particularly suitable for thermal conductivity measurements in a laboratory environment. If
needed, TPSYS20 can be powered from a 12 V battery, so that it may be used in the field.
TPSYS20 is operated in conjunction with a PC. An intuitive and easy-to-use graphical user
interface allows the user to set measurement parameters, control measurements, view
measurement progress and view and download measurement data.
Figure 0.1 Application of the complete TPSYS20 measuring system in a laboratory
environment using a CRC01 calibration reference cylinder

TPSYS20 manual v2202 6/75
Figure 0.2 TPSYS20 standard configuration: Sample (1), Needle model TP02 or TP08 (2),
MCU Measurement and Control Unit (3), Adapter suitable for both 230 and 110 VAC (4), USB
or ethernet connection (5), PC (not included) (6)
TPSYS20 advantages
•Connection via Ethernet or USB. The MCU can be connected to a local area
network (LAN) via ethernet or directly to a PC via USB.
Intuitive and easy-to-use graphical user interface. The MCU acts as a server
that provides a graphical user interface in the form of a webpage. The graphical
user interface is accessible through a web browser. No software installation is
required.
High-accuracy thermal conductivity measurements. Thermal Needle Probes,
also known as Non-Steady-State Probes (NSSPs) and line-source probes are
designed for high-accuracy measurements. The transient-line source method is
sensitive to the thermal conductivity only. It is insensitive to other
specimen properties and there is no need to make assumptions about the
specimen heat capacity or thermal diffusivity. This makes it an ideal method for
measuring thermal conductivity.
Adjustable constant current source. The current source in the MCU provides a
stable heater current that can be adjusted such that a broad range of thermal
conductivities can be measured.
Measurement and analysis of heating and cooling phase. Users can choose
to measure heating phase only or to measure heating and cooling phase. The latter
reduces effect of specimen temperature drift on the measurement result.
Figure 0.3 TPSYS20 is delivered with either a TP02 Non-Steady-State Probe or its smaller
equivalent TP08.

TPSYS20 manual v2202 7/75
Suggested use
NSSPs are particularly suitable for measuring the thermal conductivity of fine granular
materials, powders, pastes, gels and highly viscous fluids in which a needle probe can be
easily inserted. Harder materials such as rocks may also be measured provided that a
hole can be drilled to insert the probe. Examples of typical specimen materials include
soils, thermal backfill materials, sediments, foodstuff, sludges, paints and glues.
Areas of application include measurement of soils for thermal management of high-
voltage electric cables, pipelines and ground heat exchangers; measurement of plastics
for the optimisation of material processing; material characterisation.
TPSYS20 can be used to measure thermal conductivities in the range from 0.1 to
6.0 W/(m·K). Recommended specimen dimensions are a diameter of 100 mm or more
and a length of at least 160 mm for TP02 (specimen volume ~1.3 L) or 80 mm for TP08
(specimen volume ~ 0.65 L). Use of smaller specimen may be possible depending on the
thermal properties of the specimen and the required accuracy.
Standards
The measurement with TPSYS20 complies with the IEEE Guide for Soil Thermal
Resistivity Measurements (IEEE 442-2017) as well as with ASTM D5334 - 14 Standard
Test Method for Determination of Thermal Conductivity of Soil and Soft Rock. TPSYS20 is
suitable for use by ISO certified laboratories.
Figure 0.4 Overview of TPSYS20: the system includes needle model TP08 (1) or TP02
(2) and the MCU (6). The thermal needle probe must be connected to the MCU (7). The
MCU is powered from a 12 VDC power source (3). Communication with the MCU can be
done via an Ethernet port (4) or a USB port (5).

TPSYS20 manual v2202 8/75
TP02 or TP08 probe
TPSYS20 is either delivered with a TP02 or a TP08 probe.
TP02 is equipped with a reference temperature junction, located in the tip of the needle.
This allows the temperature difference between the heated section of the needle and the
reference junction to be measured. The use of a reference junction makes the thermal
conductivity measurement much less sensitive to specimen temperature drift. For more
details see the TP02 brochure.
TP08 is a shorter needle, which makes it an excellent alternative when only small
amounts of sample material are available. TP08 does not have a reference temperature
junction. For more details see the TP08 brochure.
Alternative systems
TPSYS20 is primarily intended for laboratory use. For outdoor soil measurements
Hukseflux recommends consulting the brochures of the more robust albeit less accurate
FTN02, MTN02 and TNS02 systems designed for outdoor use.
User interface: MCU as a web server
TPSYS20 is controlled via a PC. The TPSYS20 MCU can be connected to a local area
network via ethernet or directly to a PC via USB. The graphical user interface is available
through a webpage and can be opened in any of the supported web browsers. No
installation of software is required. The graphical user interface allows the user to
configure measurement parameters, control measurements, view measurement progress
and to view and download measurement results.
Figure 0.5 TPSYS20 graphical user interface, accessible through a web browser

TPSYS20 manual v2202 9/75
TPSYS20 is a complete measuring system delivered with either probe TP02 or TP08.
Besides this option, there are several accessories. See Chapter 1 Ordering and checking
at delivery for a complete overview.
Accessories
For high accuracy calibration dedicated CRC01 Calibration Reference Cylinders are
available. For insertion into hard material types or for casting into plastics, cement and
backfill materials, GT Series Guiding tubes can be applied.
Figure 0.6 A CRC01 calibration reference cylinder containing a polymethylmethacrylate
reference material for calibrating TP02 and TP08
See also
our range of sensors, systems and services for thermal conductivity measurement
robust alternative systems: FTN02, MTN02
TP02 and TP08 thermal needle probes brochure and user manual

TPSYS20 manual v2202 10/75
1Ordering and checking at delivery
Ordering TPSYS20
The standard configuration of TPSYS20 includes either a TP02 or a TP08 thermal needle
probe.
•TPSYS20 with TP02 probe, order code TPSYS20-02
•TPSYS20 with TP08 probe, order code TPSYS20-08
Included items
Arriving at the customer, the TPSYS20 delivery should include:
•1 x TPSYS20 Measurement and control unit (MCU)
•1 x TP02 or TP08 thermal needle probe with connector and protective cover
•1 x 12 VDC Power supply unit (PSU), with 4 interchangeable AC plugs
•1 x USB-A to USB-B cable with Bulgin connector, 2 m
•1 x reference material container with polyester fibres
•5 x GT02 guiding tubes for TP02 or 5 x GT01 for TP08
•1 x USB flash drive containing manual and data analysis tool
•1 x carrying case
•1 x product certificate
Figure 1.2.1 TPSYS20 system with its main components: MCU, TP02/TP08 sensor,
carrying case, power supply, reference material container and a set of guiding tubes

TPSYS20 manual v2202 11/75
Common accessories are:
•CRC01 - a calibration reference cylinder
•CR1000KD- a Campbell Scientific CR1000KD Keyboard/Display
•TP02 - a spare TP02 thermal needle probe
•TP08 - a spare TP08 thermal needle probe
•GT01 a spare set of 5 guiding tubes for TP08
•GT02 a spare set of 5 guiding tubes for TP02
Figure 1.2.2 TPSYS20 is delivered with either a TP02 or TP08 thermal needle probe.
Spare probes can be ordered as an accessory.

TPSYS20 manual v2202 12/75
2Instrument principle and theory
thermal needle probe (also known as a non-steady
state probe or transient line-source probe) and a measurement and control unit (MCU).
TPSYS20 is intended for the measurement of the thermal conductivity of the medium into
which the thermal needle probe is inserted.
Operating principle of thermal needle probes
Thermal needle probes are used to determine the thermal conductivity by measuring the
temperature response of a specimen to heat generated by the probe.
On a coarse level a thermal needle probe consists of a needle, a base and a cable with a
connector used to connect the probe to the MCU. The needle contains a linear heater
sensors at least one of which is located in the heated section of the needle. The heater
and sensor connections to the cable are located in the base. Additionally, the base may
contain a temperature sensor.
As an example, consider the TP02 and TP08 thermal needle probes. TP02 and TP08
needles contain a thermocouple with a hot joint located in the middle of the heated
section of the needle. The base of TP02 and TP08 contains a reference junction with a
Pt1000 resistance thermometer. For TP08 the heater runs along the length of the needle.
For TP02 the heater runs along two-thirds the length of the needle, with the remaining
one-third of the needle being unheated. The tip of the TP02 needle contains a cold
junction. This allows TP02 to measure the temperature difference between the hot
junction and the cold junction. TP08 does not have a second thermocouple or a cold
junction. See Figure 2.1.1.
Figure 2.1.1 The main components of a thermal needle probe

TPSYS20 manual v2202 13/75
To measure the thermal conductivity the needle is inserted into the specimen. By running
a set current through the heater, the specimen will start to heat up. For a given amount
of heat Q(in W/m) generated by the probe, the temperature of a specimen with a small
thermal conductivity λwill increase more rapidly than the temperature of a specimen
with a large thermal conductivity, as illustrated in Figure 2.1.2. The thermal conductivity
is determined from the rate at which the temperature increases, or more precisely the
slope of temperature-versus-logarithm-of-time curve (see Section 2.3 for more details).
Similar arguments apply to the cooling of a specimen after the heater is switched off.
Figure 2.1.2 Thermal needle probes are used to determine the thermal conductivity λ
measuring the temperature response to heat generated by the probe. For specimen with a
lower thermal conductivity the temperature will increase more rapidly than for specimen
with a higher thermal conductivity for the same amount of heat generated by the probe.
In a typical experiment first the temperature stability is measured during a time twait. Next,
at time t= 0, the heater is switched on and the temperature response over a time interval
theat is measured. At time t= theat the heater is switched off. Optionally the temperature
response during the cooling phase is measured. See Figure 2.1.3. Data collection, timing
and switching of the heater is controlled by the MCU. See Section 2.2 for more details on
the MCU.

TPSYS20 manual v2202 14/75
Figure 2.1.3 Illustration of a typical experiment. First the temperature stability is
measured during a time twait. Next at time t = 0 the heater is switched on and the
temperature response is measured during a time theat. At time t = theat the heater is
switched off. Recording of the cooling phase data over a time interval equal to the
heating phase theat up to time t = 2∙theat is optional.
The thermal conductivity is determined by analysing the temperature response to the
applied heating. See Section 2.3 for details on the measurement model and analysis.
Measurement and Control Unit
MCU performs three tasks. Firstly, it performs measurements and collects
data, secondly it processes that data and finally it provides a graphical user interface:
•The MCU controls the measurement. The MCU contains an adjustable constant
current source that is used to heater. The MCU takes care of
measurement timing and will switch the heater on and off at the times set by the
user. The MCU contains a 24-bit ADC to measure the heater current and read the
temperature sensors. During an experiment the MCU will collect and store
data.
•The MCU processes the data to display a preliminary result. After an experiment is
complete the MCU will automatically perform a basic data analysis to obtain a
preliminary value for the thermal conductivity λ. Hukseflux recommends
downloading the data and performing a more sophisticated analysis to reach the final
result (see Chapter 6).
•The MCU provides a graphical user interface (GUI) in the form of a webpage.
acts as webserver. It can be connected to ethernet or USB. The GUI
can be accessed through a web browser. The GUI provides a convenient way to set
measurement parameters, start and monitor measurements and view preliminary
results. It also provides users a way to retrieve data from the MCU. The user is
referred to Chapter 4 for details on how to access the GUI from a PC.

TPSYS20 manual v2202 15/75
The MCU consists of a Campbell Scientific CR1000X datalogger plus additional
electronics. MCU has multiple drives: the CPU drive and the CRD drive. The
CPU drive contains the program that controls the measurement. The CRD drive contains
the graphical user interface files and the measurement data.
Figure 2.2.1 TPSYS20’s Measurement and Control Unit (MCU)
Measurement model and data analysis
When the heater is switched on at time t= 0 the temperature Twill start to increase.
After a brief transient period, the temperature during the heating phase is described by:
Where λis the thermal conductivity of the specimen, Q is the heater power per unit
length of the heater and ln denotes the natural logarithm function. Likewise, when the
heater is switched off at t= theat the temperature Twill start to decrease. During the
cooling phase, after a brief transient period, the temperature is described by:
The slope of the temperature-versus-ln(t) curve for the heating phase and similarly the
slope of the temperature-versus-ln[t/(t-theat)] curve for the cooling phase depends only
on the thermal conductivity λand the heater power Q. Therefore, by determining the
slope of the curve, one can evaluate the thermal conductivity of the specimen:

TPSYS20 manual v2202 16/75
Where the heater power Q
resistance-per-unit-length RL m) and the electrical current (in A) running through
the heater by
The slope can be determined using a linear regression analysis. Only the linear part of
the curve should be included in the analysis. An initial transient portion of the curve is
affected by factors other than the thermal conductivity λof the specimen, such as the
specimen thermal diffusivity and the diameter and heat capacity of the probe itself. This
initial transient portion of the curve for t< t1should be excluded from the analysis.
Depending on the duration of the measurement and the thermal diffusivity of the
specimen, for long times t> t2edge effects due to the finite diameter Dspecimen of the
specimen and end effects due to the finite length Lheater of the heater may start to affect
the measurement data. If this is the case, then the portion of the data affected by such
edge or end effects should also be excluded from the analysis. Only part of the data
between a certain time t1and a certain time t2should be included in the analysis as
illustrated in Figure 2.3.1.
Figure 2.3.1 Illustration of heating phase data used for analysis. Only data between
time t1and time t2is used in the analysis. The transient period for t <t1and the period
dominated by edge or end effects for t > t2are discarded. In the above illustration
t2 < theat, however this is not necessarily always the case.
If the cooling phase data is recorded in addition to the heating phase data, the heating
time theat must be adjusted such that edge or end effects only become relevant during
the cooling phase. If edge or end effects already dominate during the heating phase, the
cooling phase data must be discarded and only heating phase data can be used. Like the
heating phase, the cooling phase is initially dominated by transient effects. This initial
portion of the cooling phase data should likewise be discarded.

TPSYS20 manual v2202 17/75
Since the thermal conductivity is calculated from the slope it is important that the
temperature of the specimen is stable prior to the heating phase. Specimen temperature
drift will bias the thermal conductivity. Data from the prior phase can be used to estimate
the specimen temperature drift in °C/min. The absolute value of the temperature drift
should be small compared to the temperature increase during the heating phase or the
temperature decrease during the cooling phase.
If the temperature response during the cooling phase was measured the thermal
conductivity λhcalculated from the heating phase data and the thermal conductivity λc
calculated from the cooling phase data can be averaged:
The advantage of measuring the cooling phase in addition to the heating phase is that
specimen temperature drift affects the calculated thermal conductivity from the heating
phase and the cooling phase in the opposite direction, therefore by averaging the results,
the effect of specimen temperature drift is minimized.
More details about the theory of thermal needle probes can be found in Appendix 8.1.
TPSYS20 is provided with a data analysis tool in the form of an MS Excel sheet that aids
in the analysis of thermal conductivity data. The use of the data analysis tool is explained
in Chapter 6.

TPSYS20 manual v2202 18/75
3Specifications
Specifications of TPSYS20
TPSYS20 is a high accuracy measuring system for measuring the thermal conductivity of
specimens. TPSYS20 specifications are listed in Table 3.1.1. TPSYS20 is delivered with
either a TP02 or TP08 thermal needle probe. TP02 and TP08 can also be ordered
separately. TP02 and TP08 specifications are listed in table 3.1.2.
Table 3.1.1 Specifications of TPSYS20 (continued on next page)
TPSYS20 SPECIFICATIONS
Description
thermal conductivity measuring system
Measurand
thermal conductivity
Measurand in base SI units
thermal conductivity in W
Rated measuring range
0.1 to 6.0
Measurand
specimen temperature
Measurand in base SI units
specimen temperature in °C
Optional measurand
thermal resistivity
Measurand in base SI units
Rated measuring range
0.16
Included items
•TPSYS20 Measurement and control unit (MCU)
•TP02 or TP08 thermal needle probe with connector
and protective cover
•12 VDC Power supply unit (PSU), with 4
interchangeable AC plugs
•USB-A to USB-B cable with Bulgin connector
•Reference material container with polyester fibres
•Carrying case
•USB flash drive containing manual and data
analysis tool
•Product certificate
Compatible test methods
•ASTM D5334 14 Standard Test Method for the
Determination of Thermal Conductivity of Soil and
Soft Rock by Thermal Needle Probe Procedure
•IEEE 442-2017 IEEE Guide for Thermal
Resistivity Measurements of Soils and Backfill
Materials
•ASTM D5930 17 Standard Test Method for
Thermal Conductivity of Plastics by Means of a
Transient Line-Source Technique
Storage and transport
Gross weight TPSYS20 system including
carrying case and packaging
approx. 10 kg
Net weight TPSYS20 system
including carrying case
approx. 9 kg
Carrying case TPSYS20 system
case of 480 mm x 385 mm x 190 mm
Limiting storage and transport
temperature
-20 to +80 °C
Storage
The thermal needle probe and MCU should be stored
in a dry place. The thermal needle probe should be
stored with protective cap in place. TPSYS20 MCU
should be stored with the dedicated dust caps placed
on connectors.
-

TPSYS20 manual v2202 19/75
Table 3.1.1 Specifications of TPSYS20 (continued from previous page)
TPSYS20 MCU SPECIFICATIONS
Compatible Thermal Needle Probes
•TP02
•TP08
Operating voltage
10 to 16 VDC
Recommended operating voltage
12 VDC
Typical current
100 to 500 × 10-3 A
Max. current
1 A
ON/OFF switch and Power ON LED
red Power ON LED is on when power is supplied to MCU
Sample rate
2 Samples / s
Data tables
RawData
Results
Net weight MCU
3.80 kg
IP rating MCU
IP54
MCU Datalogger
Campbell Scientific CR1000X Measurement and
Control Datalogger
Datalogger specifications
see CR1000X manual and specification sheet
available from https://www.campbellsci.com/cr1000x
Internal battery
Tadiran, TL-5903/S) for
battery-backed memory and clock only
Internal battery replacement interval
3 years
Internal memory card
ATP, 2 GB MicroSDHC Card Class 10, UHS-1 U1, SLC
User interface
Connection
MCU user interface
web page via a web browser
Web browser requirements
HTML 5 support
Supported web browsers
Chrome 10
Firefox 4
Internet Explorer 9
Opera 11
Safari 5
(and later)
12 VDC connector
Connector type on MCU
Bulgin Standard Buccaneer®, PX0735/P, 2 pole
connector with pins
Sensor connector
Connector type on MCU
Fischer, DEE 104 A055-130, 9 pin, female connector
Thermal fuse current limit
1800 x 10-3 A
Purpose
connecting a compatible thermal needle probe
USB connector
Connector type on MCU
female USB-B
Maximum USB cable length
3.0 m
Ethernet connector
Connector type on MCU
RJ45 (shielded)
Isolation/protection
magnetic isolation
TVS surge protection
Recommended ethernet cable type
CAT6A S/FTP
Maximum ethernet cable length
30 m
Trigger input connector
Connector type on MCU
female BNC connector
Input impedance
Pull-up resistance
Max. input voltage
10 V
Protection
TVS surge protection
Minimum trigger pulse width
5 ms
RS232 connector
Connector type on MCU
female DB9 connector
-

TPSYS20 manual v2202 20/75
Table 3.1.1 Specifications of TPSYS20 (continued from previous pages)
CS I/O connector
Connector type on MCU
female DB9 connector
Purpose
for connecting TPSYS20 MCU to optional Campbell
Scientific CR1000KD Keyboard/Display
(not included with TPSYS20)
POWER SUPPLY SPECIFICATIONS
Power supply model
Friwo, FOX30-X, 12V/2500mA, FW8030/12, 1898155
Input voltage
100 or 240 VAC
Frequency
50 Hz or 60 Hz
Input plug type
Type A/B (USA),
Type C/F (EU),
Type G (UK),
Type I (AU)
Output voltage
12 VDC
Output current
2.5 A
Output cable length
approx. 1.75 m
Output connector type
Bulgin Standard Buccaneer®, PX0736/S, 2 pole
connector with sockets
REFERENCE MATERIAL CONTAINER
Reference Material
glycerol, > 96% pure (not included)
Fibres to inhibit convection
polyester fibres
Weight (glycerol not included)
0.180 kg
Volume
1.0 L
Reference thermal conductivity
5 °C
Uncertainty
± 5 % (coverage factor k = 2)
Table 3.1.2 Specifications of TP02 and TP08 thermal needle probes (continued on next page)
THERMAL NEEDLE PROBE SPECIFICATIONS
Model
TP02
TP08
Cable and connector
Cable length
2.5 m
2.5 m
Connnector type
Fischer, S 104 A055-130, 9 pin, male connnector
with internal part E3 104.2/6.7 + B
Probe dimensions
Needle diameter
1.5 mm
1.2 mm
Needle length
150 mm
70 mm
Base diameter
10 mm
10 mm
Weight (including cable)
0.3 kg
0.3 kg
Heater
Heater resistance per unit length
specified for each instrument individually
Nominal heater resistance per unit length
Nominal heater resistance
(including lead wire resistance)
Heater length
100 ± 2 mm
70 ± 2 mm
Base temperature sensor
Type
resistance thermometer, Pt1000,
IEC 751:1983 class B
Accuracy
± (0.005 ×|T| + 0.30 °C)
T in °C
Needle temperature sensor
Type
thermocouple, type K,
IEC 60584-1:2013 class 2
-
Table of contents
Other Hukseflux Measuring Instrument manuals

Hukseflux
Hukseflux DR01 User manual
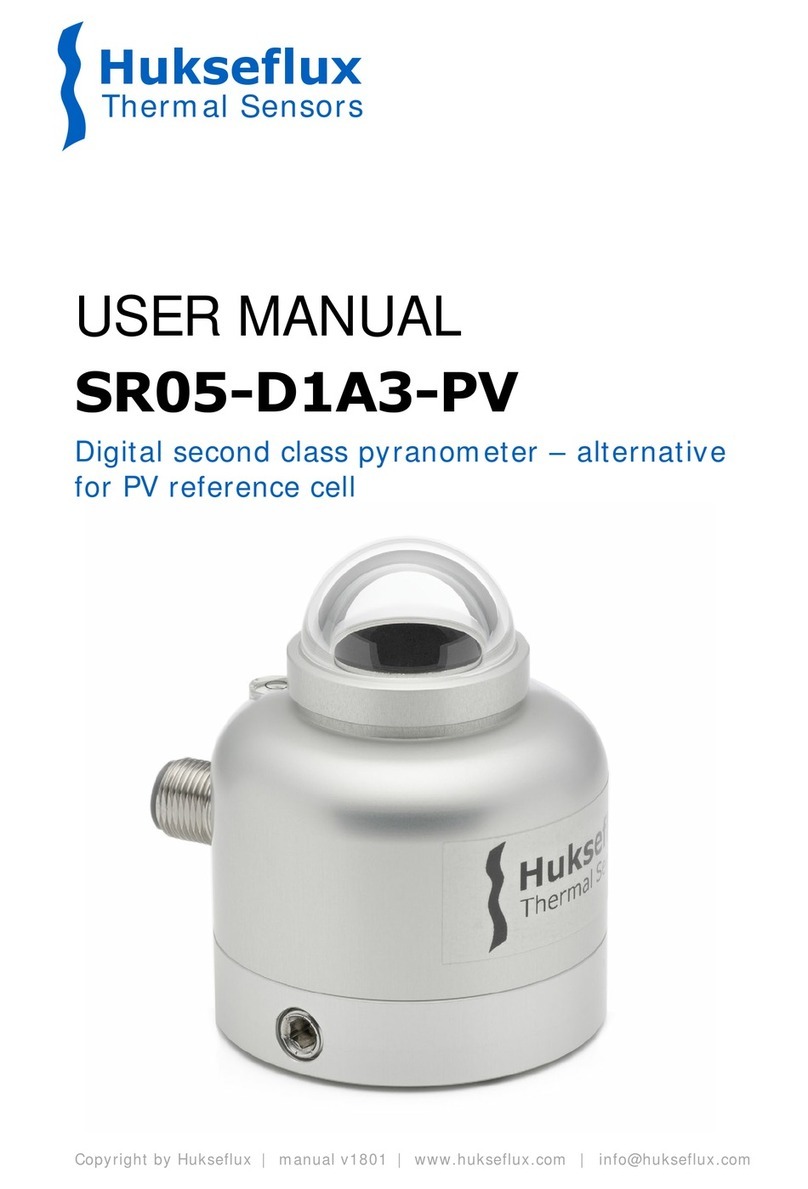
Hukseflux
Hukseflux SR05 series User manual
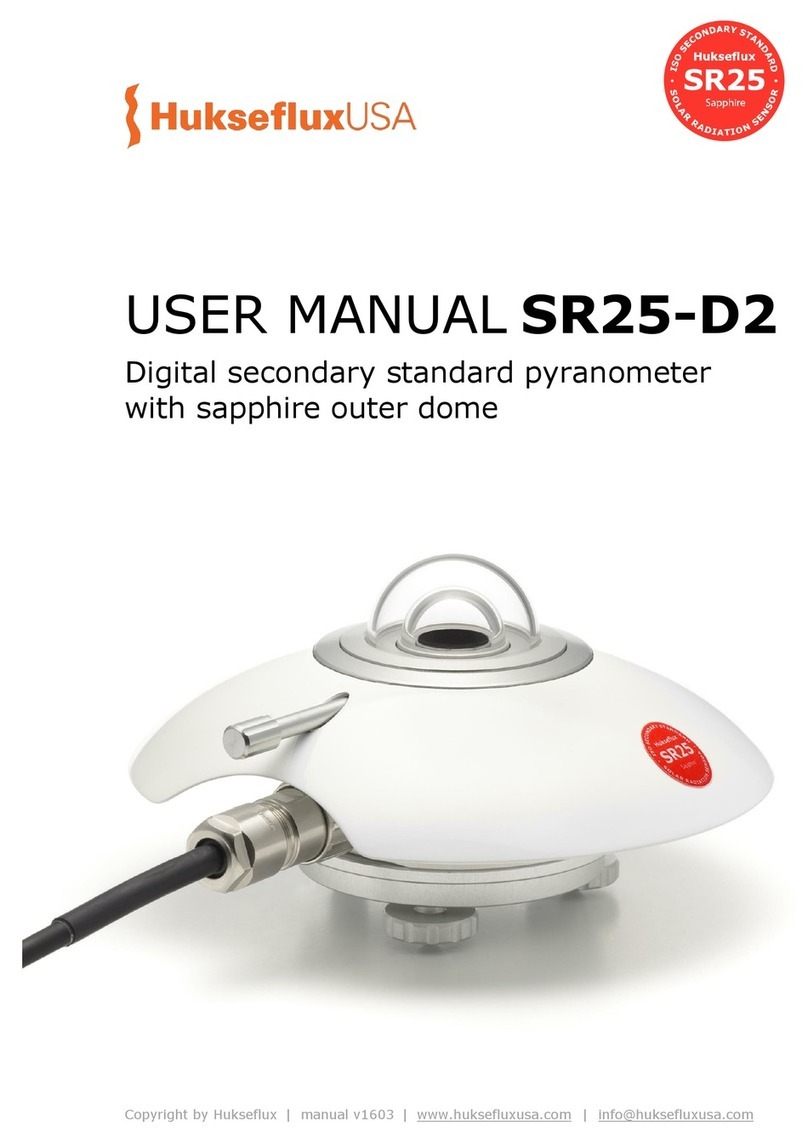
Hukseflux
Hukseflux SR25-D2 User manual
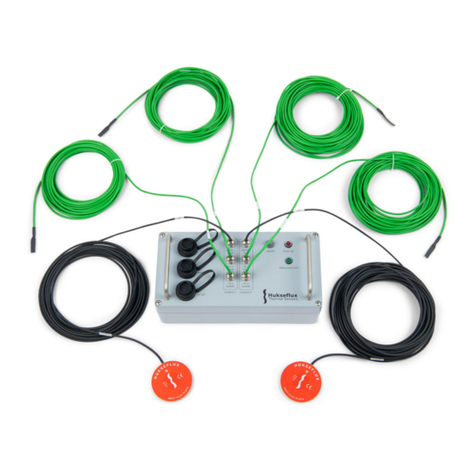
Hukseflux
Hukseflux TRSYS20 User manual
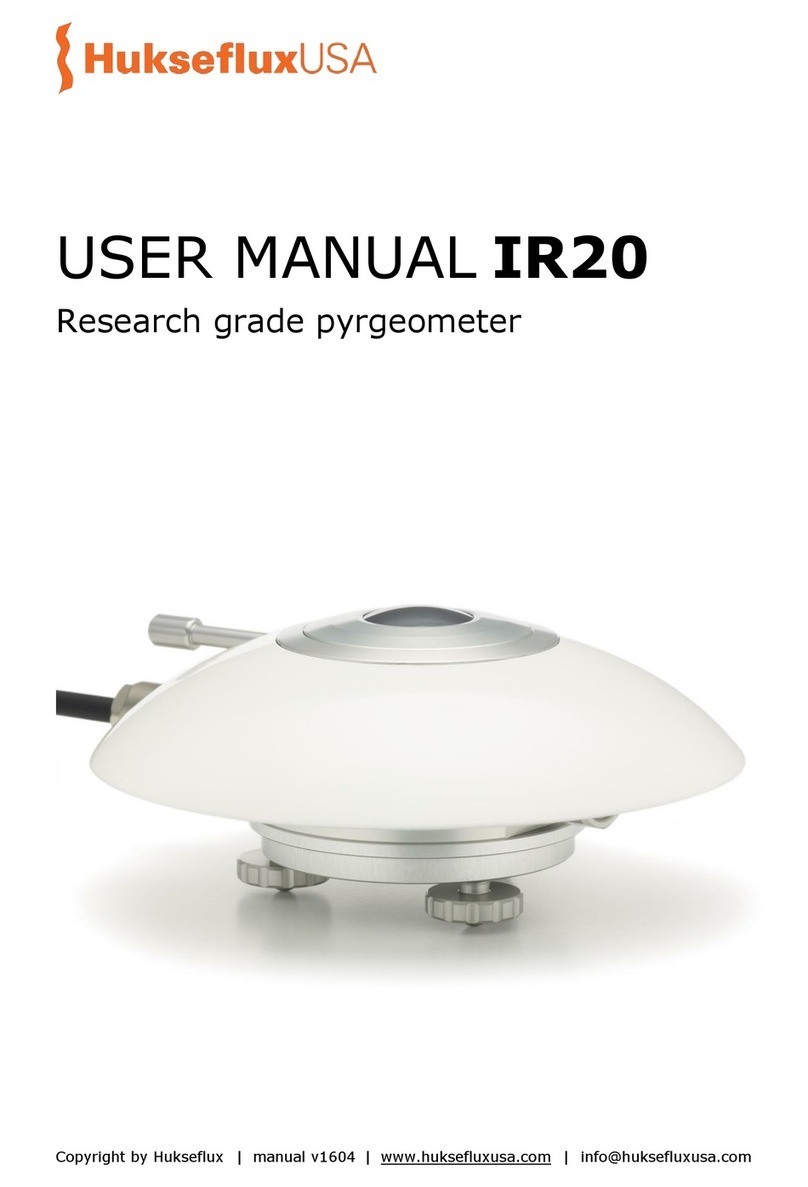
Hukseflux
Hukseflux IR20 User manual
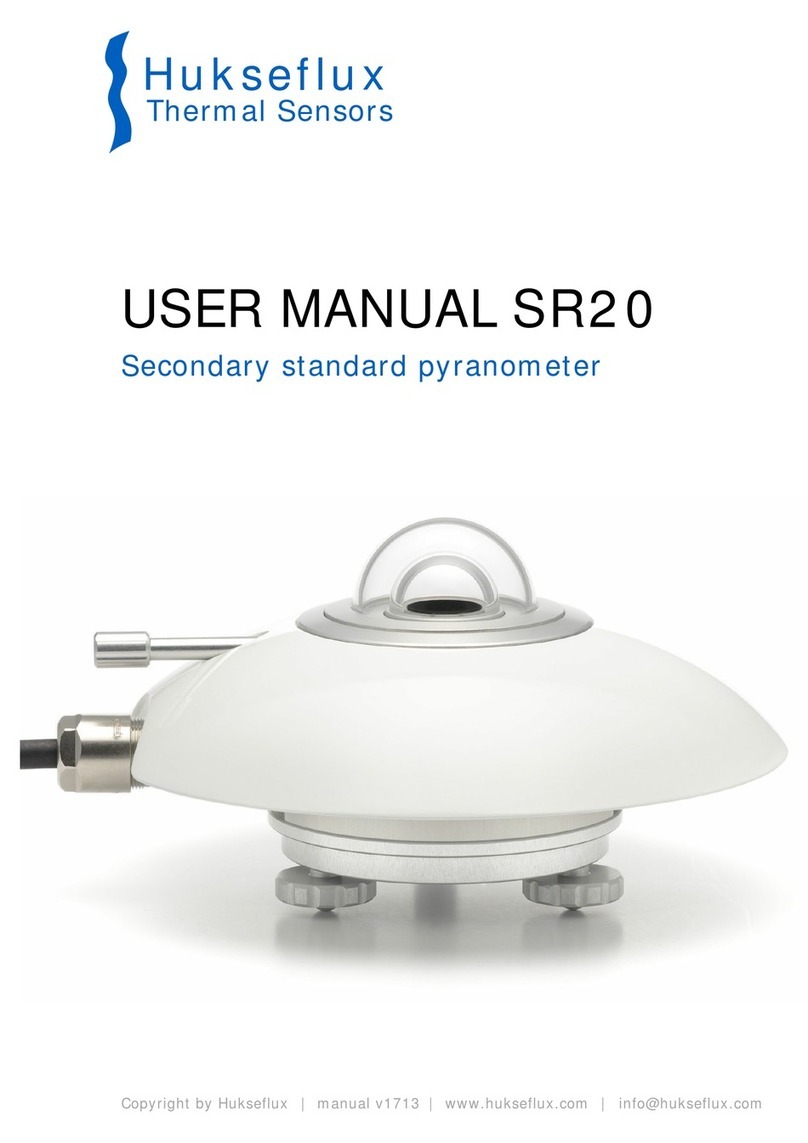
Hukseflux
Hukseflux SR20 User manual

Hukseflux
Hukseflux FTN02 User manual
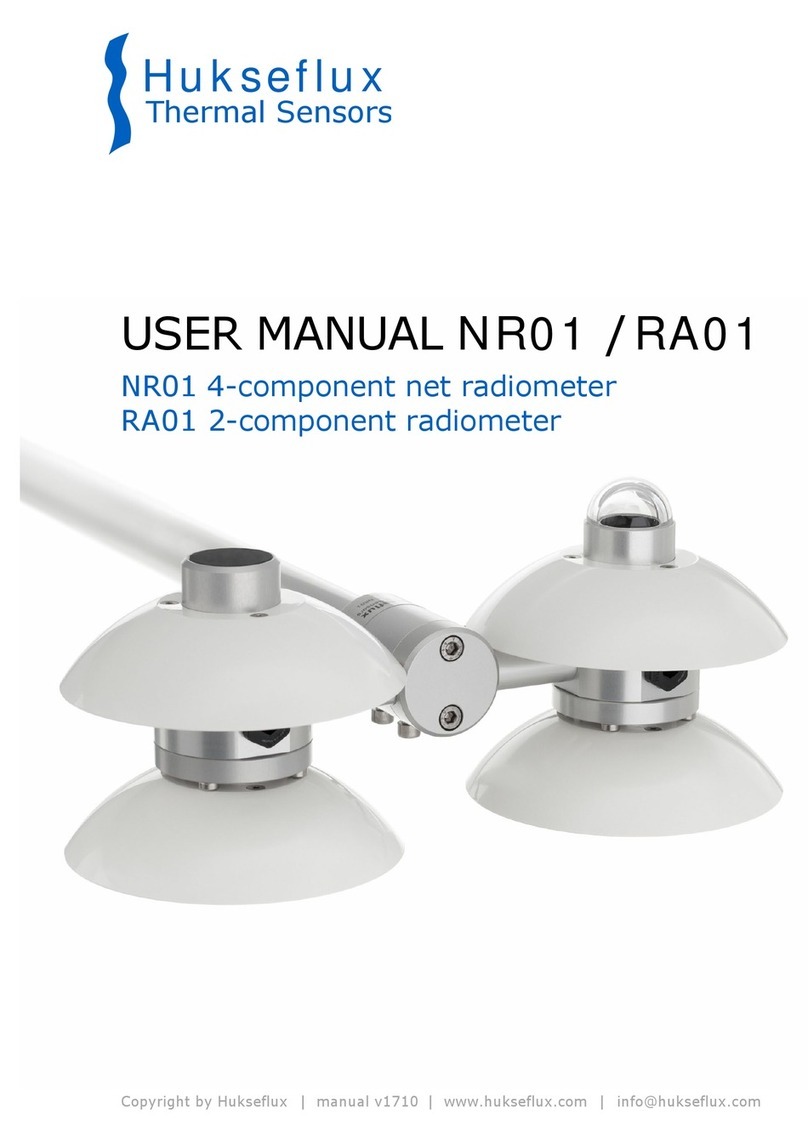
Hukseflux
Hukseflux NR01 User manual
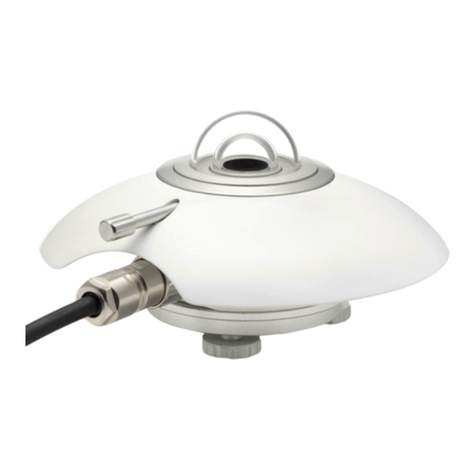
Hukseflux
Hukseflux SR20-D2 User manual
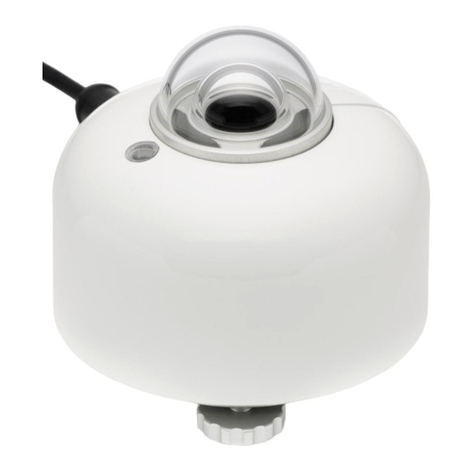
Hukseflux
Hukseflux SR30-D1 User manual
Popular Measuring Instrument manuals by other brands
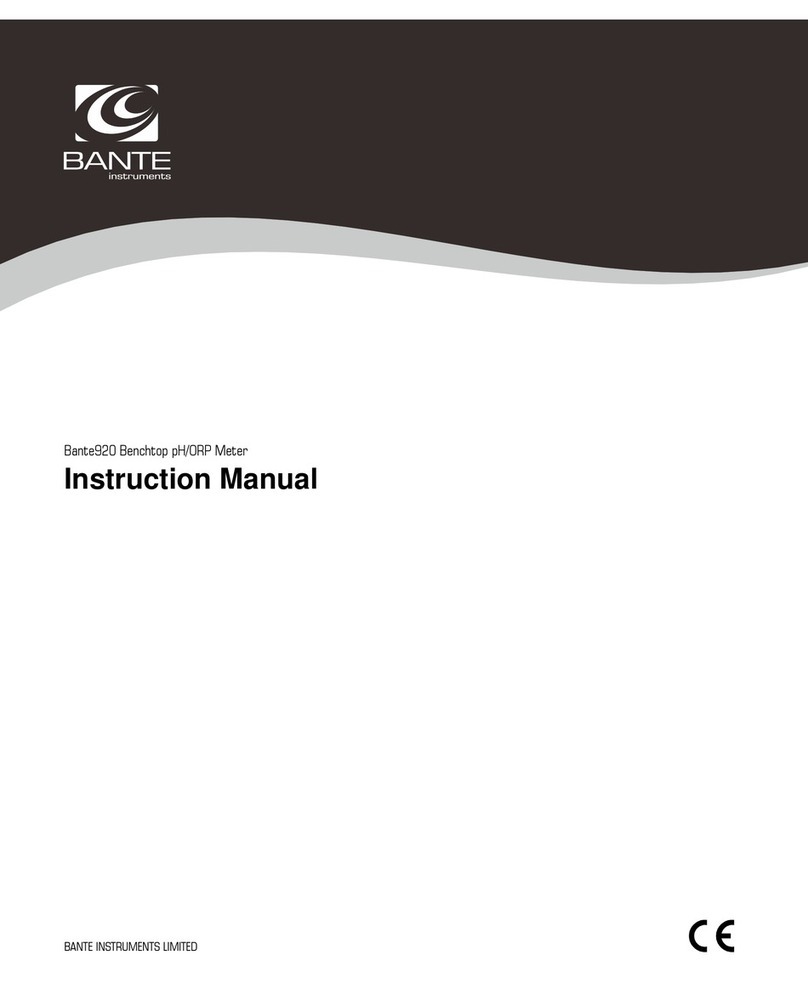
BANTE
BANTE Bante920 instruction manual
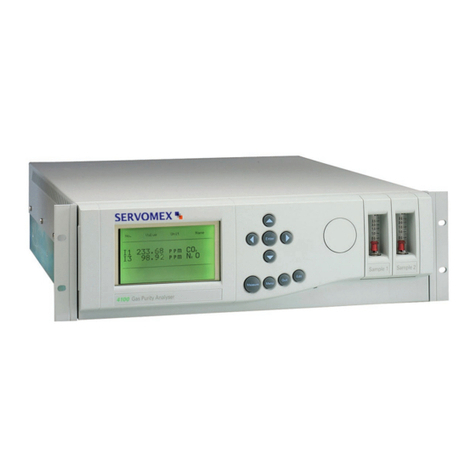
Servomex
Servomex SERVOPRO 4000 Series installation manual
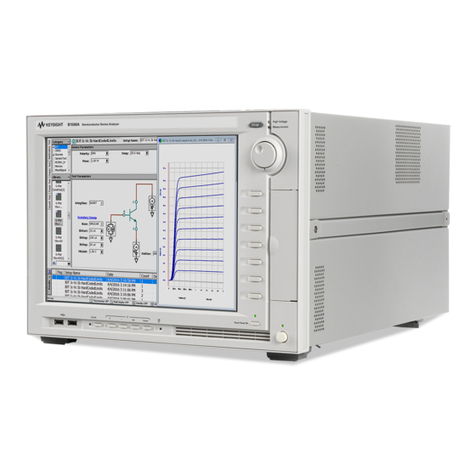
Keysight Technologies
Keysight Technologies B1500A Configuration guide
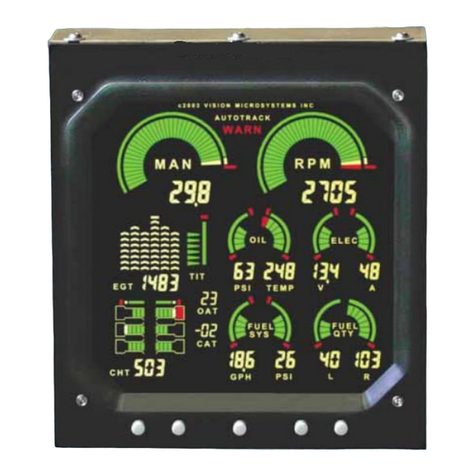
vision microsystems
vision microsystems VM1000C pilot's guide
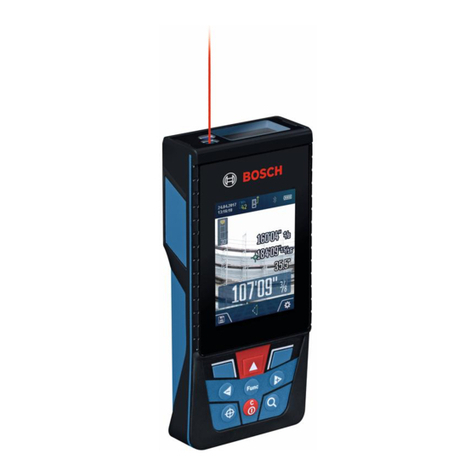
Bosch
Bosch GLM400C Operating/safety instructions
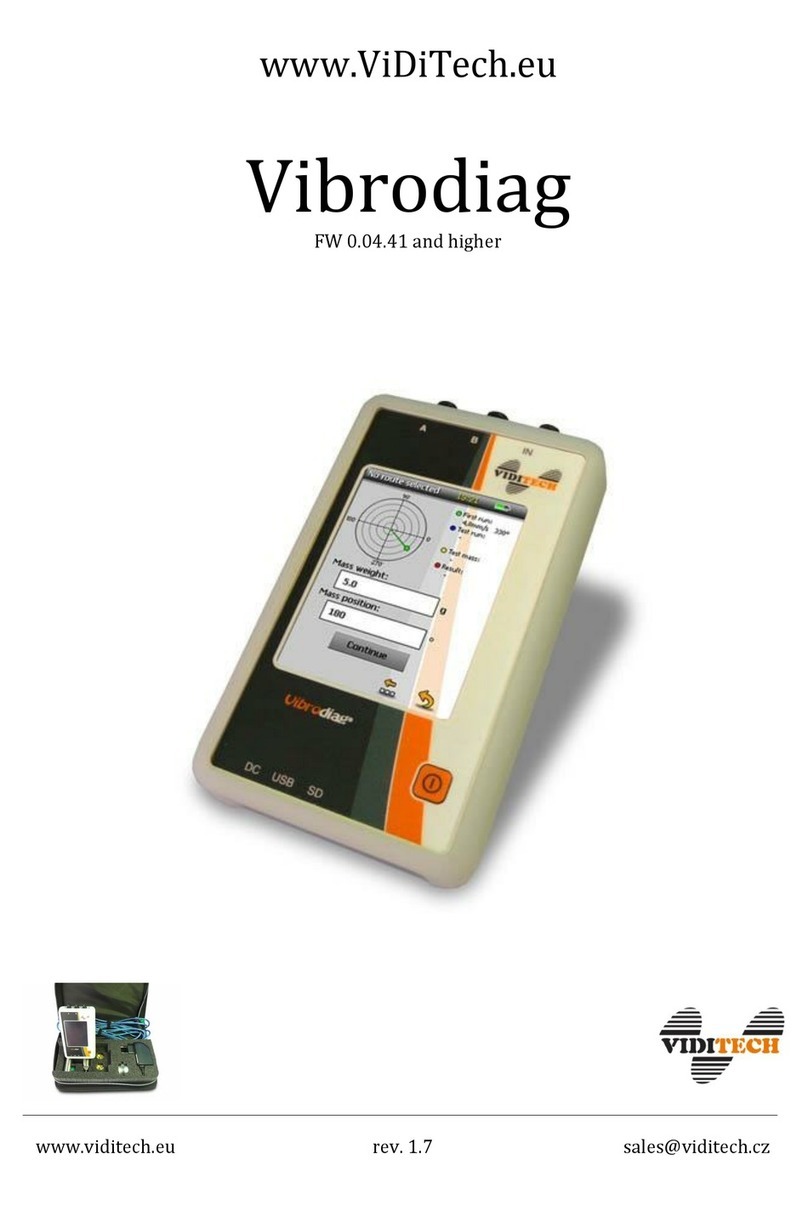
VIDITECH
VIDITECH Vibrodiag user manual