Hukseflux TRSYS20 User manual

TRSYS20 manual v2301 2/39
Cautionary statements
Cautionary statements are subdivided into four categories: danger, warning, caution and
notice according to the severity of the risk.
DANGER
Failure to comply with a danger statement will lead to death or serious
physical injuries.
WARNING
Failure to comply with a warning statement may lead to risk of death or
serious physical injuries.
CAUTION
Failure to comply with a caution statement may lead to risk of minor or
moderate physical injuries.
NOTICE
Failure to comply with a notice may lead to damage to equipment or may
compromise reliable operation of the instrument.

TRSYS20 manual v2301 3/39
Contents
Cautionary statements 2
Contents 3
List of symbols 4
Introduction 5
1Ordering and checking at delivery 10
1.1 Ordering TRSYS20 10
1.2 Included items 10
2Instrument principle and theory 11
2.1 TRSYS20 measuring system 11
2.2 Theory 12
3Specifications of TRSYS20 17
3.1 Specifications of TRSYS20 17
3.2 Dimensions of TRSYS20 21
4Preparation of an experiment 22
4.1 Preparing the equipment 22
5TRSYS20 MCU system setup 23
5.1 Setting up connection 23
5.2 Setting the clock 24
5.3 Setting the net frequency filter 25
5.4 Verifying the programmed HFP01 sensitivity 25
6Installation of sensors: HFP01 and TC 26
6.1 Site selection and installation 26
7Performing measurements 29
7.1 Starting an experiment 29
7.2 Monitoring measurements 29
7.3 Retrieving measurement data 30
8Data analysis tool 31
8.1 Importing the data 31
8.2 Viewing results 31
9Uncertainty evaluation 32
9.1 Heat flux measurements 32
9.2 Temperature difference 32
9.3 Thermal resistance 32
10 Maintenance and trouble shooting 33
10.1 Recommended maintenance and quality assurance 33
10.2 Trouble shooting 34
10.3 Calibration and checks in the field 35
10.4 Storage 35
11 Appendices 36
11.1 TRSYS20 data table 36
11.2 EU declaration of conformity 37

TRSYS20 manual v2301 4/39
List of symbols
Quantities Symbol Unit
Heat flux ΦW/m²
Voltage output U V
Sensitivity S V/(W/m2)
Temperature T °C
Temperature difference ΔT °C, K
Time constant τs
Thermal resistance, from surface to surface R K/(W/m²)
Thermal resistance, from environment to environment RTK/(W/m²)
Λ-Value, thermal conductance ΛW/(m²·K)
Thermal resistance ambient air boundary layer for:
indoor layer Ramb., indoor K/(W/m²)
outdoor layer Ramb., outdoor K/(W/m²)
U-Value, thermal transmittance U W/(m²·K)
Time t s
Thermal conductivity λW/(m∙K)
Thermal resistivity r m∙K/W
Ambient air / wind speed v m/s
Volumetric heat capacity Cvolumetric J/(m³∙K)
Resistance R Ω
Heat transfer coefficient h W/(m²·K)
Convection heat transfer coefficient hcW/(m²·K)
Radiation heat transfer coefficient hrW/(m²·K)
Subscripts
Property of thermopile sensor sensor
Property of ambient air ambient
Property at indoor location indoor
Property at outdoor location outdoor
Acronyms
GUI Graphical User Interface
MCU Measurement Control Unit
PC Personal Computer
PSU Power Supply Unit
ISO International Organization for Standards
ASTM American Society for Testing and Materials
TC Thermocouple
HFM heat flow meter (ISO)
HFT heat flow transducer (ASTM)

TRSYS20 manual v2301 5/39
Introduction
TRSYS20 is a high-accuracy system for on-site measurement of thermal resistance (R-
value), and thermal transmittance (U-value), of building envelope components. TRSYS20
is mostly used for measurements according to standard practices of ISO 9869 and ASTM
C1155 / C1046. The system is equipped with high-accuracy electronics, two heat flux
sensors of model HFP01 as well as two pairs of matched thermocouples. The two
measurement locations provide redundancy, leading to a high level of confidence in the
measurement result. The high accuracy of the heat flux sensors and temperature
difference measurements ensures that TRSYS20 continues measuring when other
systems no longer perform; in particular at very low temperature differences across the
wall.
HFP01 is a versatile heat flux sensor that, amongst others, has been employed in soil
science applications for studying the heat balance of soils and in building physics
applications for determining the thermal resistances of walls and building envelope
components. For HFP01 specifications, see the HFP01 manual.
Figure 0.1 TRSYS20: the complete measuring system includes 2 HFP01 heat flux sensors
and 2 matched thermocouple pairs, TC, (in total 4 temperature sensors) and the MCU
measurement and control unit.
On-site measurements of thermal resistance, R, are often applied in studies of buildings.
Alternatives are to measure its inverse value, the thermal conductance which is called
the Λ-value, or the thermal transmittance which includes ambient air boundary layer
thermal resistance, the U-value.
The measurements of R are based on simultaneous time averaged measurement of heat
flux Φ and differential temperature, ΔT, (using two temperature sensors, each on a
different side of the wall).
R = ΔT / Φ
The ISO and ASTM standards give detailed directions concerning the measurement
method, sensor installation and data analysis.

TRSYS20 manual v2301 6/39
The TRSYS20 system employs dedicated sensors and electronics. Their high sensitivity
and accuracy ensure that TRSYS20 will still measure under circumstances where
competing systems no longer perform reliable measurements; i.e. down to very low heat
fluxes and low temperature differences across the wall. The matched thermocouple pairs
in TRSYS20, measure temperature differences with an uncertainty of better than 0.1 °C
over the entire rated temperature range. TRSYS20 includes 2 x HFP01 heat flux plates.
HFP01 is the world’s most popular sensor for heat flux measurement in studies of
buildings.
The system generates a measurement file, including time, heat flux, temperature and
temperature difference for the two measurement locations. The measurement is stored in
the MCU and later downloaded to a PC. The user is responsible for data analysis,
calculating the R-value or U-value of the building envelope according to the ISO or ASTM
standards.
Equipped with heavy-duty components, TRSYS20 has proven to be very robust and
stable. It survives repeated installation necessary in this application where measuring
systems are typically used at multiple locations.
The measurements and the analyses that have to be performed are not straightforward;
although the measurements are standardised, this always involves a significant element
of expertise and a subjective data interpretation. Hukseflux helps to gain the necessary
experience by offering operator training.
Training vastly improves the level of service to the end user, the efficiency of working
with the equipment and reduces the uncertainty of the end result. Please contact us for
more information on training courses in thermal measurement at Hukseflux.
Figure 0.2 TRSYS20 consists of MCU Measurement and Control Unit (3), a 12 VDC
adapter to power the MCU (1), two pairs of matched thermocouples (4) to be placed on
both sides of a wall, and two model HFP01 heat flux plates (5) to be placed on the inside
side of a wall. The MCU measures and stores measurement data. The MCU can be

TRSYS20 manual v2301 7/39
connected to a PC (2, not included) via USB or ethernet. Graphical user interface is
accessible through a web browser.
Calibration of TRSYS20 components is traceable to international standards.
HFP01 and MCU are traceable to the international standards for voltage, current and
length, the thermocouples to ITS-90. TRSYS20 undergoes a functional test at the factory.
This conformity assessment includes temperature difference measurement accuracy.
Figure 0.3 TRSYS20 in its carrying case on the left and one HFP01 sensor on the right. 2
HFP01 heat flux sensors and 2 matched thermocouple pairs, TC, (in total 4 temperature
sensors) are included in TRSYS20.
TRSYS20 advantages
•Connection via ethernet or USB. The MCU can be connected to a local area network
(LAN) via ethernet or directly to a PC via USB.
•Intuitive and easy-to-use graphical user interface. The MCU acts as a server that
provides a graphical user interface in the form of a webpage. The graphical user interface
is accessible through a web browser. No software installation is required.
•Matched thermocouple pairs. Matched thermocouple pairs have a measurement
uncertainty of better than 0.1 °C over the entire rated temperature range. Their high
accuracy and sensitivity ensure that TRSYS20 will still measure under circumstances
where competing systems no longer perform reliable measurements; i.e. down to very
low heat fluxes and low temperature differences across the wall.

TRSYS20 manual v2301 8/39
Suggested use
On-site measurements of thermal resistance, R, are often applied in studies of buildings.
Alternatives are to measure its inverse value, the thermal conductance which is called
the Λ-value, or the thermal transmittance which includes ambient air boundary layer
thermal resistance, the U-value. The measurements of R are based on simultaneous time
averaged measurement of heat flux Φand differential temperature, ΔT, (using two
temperature sensors, each on a different side of the wall).
R = ΔT / Φ
Standards
TRSYS20 is mostly used for measurements according to standard practices of ISO 9869
and ASTM C1155 / C1046. TRSYS20 is suitable for use by ISO certified laboratories.
Figure 0.4 TRSYS20 measuring system with carrying case.

TRSYS20 manual v2301 9/39
User interface: MCU as a web server
TRSYS20 is controlled via a PC. The TPSYS20 MCU can be connected to a local area
network via ethernet or directly to a PC via USB. The graphical user interface is available
through a webpage and can be opened in any of the supported web browsers. No
installation of software is required. The graphical user interface allows the user to
configure measurement parameters, control measurements, view measurement progress
and to view and download measurement results.
Figure 0.5 TPSYS20 graphical user interface, accessible through a web browser.

TRSYS20 manual v2301 10/39
1Ordering and checking at delivery
1.1 Ordering TRSYS20
The standard configuration of TRSYS20 is with 2 x heat flux sensor, one with 10 and one
with 20 m cable, and 2 x matched thermocouple pairs, TC, one pair with 10 m cable and
one pair with 20 m cable.
1.2 Included items
Arriving at the customer, the TRSYS20 delivery should include:
•1 x carrying case
•1 x TRSYS20, consisting of
oa measurement and control unit (MCU)
o2 x HFP01 heat flux plates
o2 x matched thermocouple pairs
•1 x 12 VDC Power supply unit (PSU), with 4 interchangeable AC plugs
•1 x USB-A to USB-B cable
•1 x product certificate TRSYS20
Figure 1.2.1 Overview of TRSYS20: the system includes 2x HFP01 sensor (4), 2x
matched thermocouple pairs (5), and the MCU (6). The MCU is powered from a 12 VDC
power source (1). Communication with the MCU can be done via an ethernet port (2) or
a USB port (3).

TRSYS20 manual v2301 11/39
2Instrument principle and theory
TRSYS20 measuring system consists of multiple heat flux- and temperature sensors that
are used to measure heat fluxes through- and temperature difference across walls or
building envelope components. The data can be used to estimate the energy budget of
buildings and to determine thermal resistance of walls. The data analysis required to
determine thermal resistance, R, thermal conductance, Λ, or thermal transmittance, U,
from the data is the responsibility of the user and should be performed according to ISO
and ASTM recommended practices.
This chapter provides a brief introduction into the theory, the relevant standards and the
TRSYS20 operating principle.
Figure 2.1 HFP01 heat flux sensor and TC mounted on a wall.
2.1 TRSYS20 measuring system
2.1.1 HFP01 heat flux sensors
TRSYS20 uses HFP01 heat flux sensors to measure the heat flux through building
envelope components. Heat flux is the amount of heat flowing through a surface per unit
time per unit area and is expressed in SI units of W/m2.
HFP01 heat flux sensor contains a thermopile that generates an output voltage that is
proportional to the temperature difference across the heat flux sensor. From Fourier’s
law it follows that the temperature difference across the heat flux sensor is proportional
to the heat flux through the sensor. Hence output voltage U is proportional is
proportional to the heat flux Φ:

TRSYS20 manual v2301 12/39
Φ = U/S
Where S, a constant, is the sensitivity of the heat flux sensor. HFP01 is calibrated at the
factory.
Installation of a heat flux sensor generally perturbs the heat flows. To avoid perturbing
the heat flows, heat flux sensors should have a small thermal resistance while having a
sufficiently large sensitivity for their application. HFP01 is designed to minimize the
perturbation while having a high sensitivity.
For more details on the HFP01 heat flux sensors, the reader is referred to the HFP01
manual.
2.1.2 Matched thermocouple pairs
TRSYS20 uses matched thermocouple pairs to measure temperature differences across
building envelope components. While the absolute temperature measuring accuracy of
individual thermocouples is low, matched thermocouple pairs can be used to very
accurately measure temperature differences. Proper selection / pairing leads to
uncertainties better than 0.1 °C over the full rated measurement range.
2.1.3 Measurement and control unit (MCU)
The measurement and control unit (MCU) contains a Campbell Scientific CR1000X
datalogger. The MCU is used to measure the voltage signals from the heat flux sensors
and thermocouples, process the signals, store measurement data and to provide a user
interface.
The MCU uses high resolution AD converters to measure the voltage signals from the
heat flux sensors and thermocouples. A net-frequency filter is used to minimize cross talk
from power lines. The net-frequency filter must be set to net frequency (50 or 60 Hz) of
the region in which the system is used. The MCU measured voltages are then converted
to heat flux, temperature and temperature difference values. It has an on-board
temperature sensor that acts as a cold junction measurement for the thermocouples.
This is called the panel temperature.
MCU contains a clock and memory. 10 minute averages of heat flux, temperature and
temperature differences are stored along with appropriate time stamps. Once a
measurement has been completed, the measurement data can be downloaded from the
MCU.
The MCU provides a user interface that allows the user to view live measurement data as
well as preliminary results. The user interface is accessible via a PC or laptop using a web
browser. To access the user interface the MCU can be connected via USB or ethernet.
2.2 Theory
TRSYS20 is a system for in-situ (or field) measurements of the thermal resistance of
building envelope components as opposed to ex-situ (or laboratory) measurements.

TRSYS20 manual v2301 13/39
In-situ thermal resistance evaluations use long-term averages of temperature difference
across- and heat flux through the wall or building envelope component. Using the time-
averaged temperature difference ΔTavg and time-averaged heat flux Φavg the thermal
resistance can be evaluated using the thermal equivalent of Ohm’s law:
R = ΔTavg /Φavg (Formula 2.1.1)
For finite measuring times the evaluation of the thermal resistance is complicated by the
fact that walls have a non-zero heat capacity. A wall absorbs and releases heat during a
day. Measurement duration should be long enough to allow the R-value to stabilize.
Typical measurement times are on the order of one to two weeks, with a minimum of 3
days. The required measurement time ultimately depends on the thermal properties of
the wall or building envelope component as well as the measuring conditions.
There are several applicable standards for in-situ thermal resistance measurements. The
standards provide guidance on how to perform measurements as well as methods for
processing measurement data and obtaining thermal resistances or similar quantities of
interest. Specifically, the standards contain methods for determining whether sufficient
data has been collected, as well as corrections to formula 2.1.1 for finite time
measurements on walls with high thermal resistance and heat capacity. These standards
are discussed in more detail in section 2.2.1. The user is responsible for the data
analysis.
2.2.1 Applicable standards
Table 2.2.1.1 contains a listing of applicable standards. We recommend users to
purchase the latest version of the standard.
Table 2.2.1.1 Standards with recommendations for instrument use in building physics.
STANDARDS FOR INSTRUMENT USE FOR BUILDING ENVELOPE THERMAL RESISTANCE
MEASUREMENT
ISO STANDARD
EQUIVALENT
ASTM STANDARD
ISO 9869 Thermal insulation – Building
elements – In-situ measurement of thermal
resistance and thermal transmittance
ASTM C 1155-95 Standard Practice for
Determining Thermal Resistance of Building
Envelope Components from the In Situ Data
ASTM 1046-95 Standard Practice for In Situ
Measurement of Heat Flux and Temperature on
Building Envelope Components
2.2.2 ISO 9869-1:2014: thermal conductance (Λ-value) and transmittance (U-
value)
ISO 9869-1 makes a distinction between:
•thermal resistance R from surface to surface by conduction, in SI units of m2∙K/W,
calculated from heat flux and surface temperature difference Tsurface (or the inverse
value: thermal conductance Λ, in SI units of W/(m2∙K))
•thermal resistance RTfrom environment to environment by convection plus
conduction, calculated from heat flux and ambient air temperature difference Tambient
(or the inverse value: thermal transmittance U)
Typically, the wall thermal conductance Λ(or thermal resistance R) is measured using
surface temperatures on the wall:

TRSYS20 manual v2301 14/39
Λ = 1/R = Φ/(Tsurface, indoor – Tsurface, outdoor) (Formula 2.2.2.1)
The thermal resistance R of an old insulated wall is of the order of 2.5 K/(W/m2), a
modern insulated wall may attain 6.7 K/(W/m2).
The thermal transmittance U is a measure how effective a material is as an insulator. The
lower the U value, the less heat is lost and the more insulation the material provides. U-
value includes an ambient air boundary thermal layer at the inside and outside of the
wall. When measuring the thermal transmittance:
U = 1/RT= Φ/(Tambient, indoor – Tambient, outdoor) (Formula 2.2.2.2)
The U-value (or alternatively RT) includes Rambient, indoor and Rambient, outdoor, a thermal
boundary layer of air plus radiative transport resistance.
RT= R + Rambient, indoor + Rambient, outdoor (Formula 2.2.2.3)
Formula 2.2.2.4 shows a typical assumption for non-ventilated walls for 2 surfaces:
Rambient = Rambient, indoor + Rambient, outdoor = 0.25 K/(W/m2) (Formula 2.2.2.4)
The convective transport of heat from the wall to the ambient air, Φ, is a function of the
heat transfer coefficient, hc, and the temperature difference between ambient air and
sensor.
Φ= hc∙ ( Tambient – Tobject ) = ( Tambient – Tobject )/Rambient (Formula 2.2.2.5)
In buildings under indoor conditions we expect wind speeds of < 1 m/s. Indoor
environments such as office spaces will typically have wind speeds < 0.5 m/s. Outdoors,
wind speeds may reach 15 m/s under normal conditions, and up to 60 m/s in case of
heavy storm.
An approximation of the heat transfer coefficient at a single surface at moderate ambient
air speeds, v, and taking 5 W/(m2·K) for the radiative transfer coefficient, is given by:
h = hr+ hc= 5 W/(m2·K) + 4 J/(m3·K) ∙ v (Formula 2.2.2.6)
According to ISO 9869, A.3.1, a common value for the heat transfer coefficient by
convection, hc, for a single surface is 3.0 W/(m2·K); in the equation above this would
represent a wind speed of 0.75 m/s. The total heat transfer coefficient h for one surface
then is 8 W/(m2·K). For two surfaces Rambient then becomes 0.25 K/(W/m2) according to
formula 2.2.2.4.
The radiative heat transfer coefficient of 5 W/(m2·K) follows from the Stefan–Boltzmann
law, linearised around 20 °C.
In this standard the heat flux sensor name is heat flowmeter (HFM). Installation is
described in ISO 9869 paragraph 6.1.2. The user should verify the representativeness of
the area with a thermal camera. The installation should not be in the vicinity of potential
sources of error such as thermal bridges, cracks, heating or cooling devices and fans.
Sensors should not be exposed to rain, snow, and direct solar radiation. The standard
recommends use of thermal paste. Hukseflux discourages the use of thermal paste

TRSYS20 manual v2301 15/39
because it tends to dry out. Silicone glue and double sided tape are more reliable. The
standard recommends the use of a passive guard ring. Annex D.3.2 states that “the
width of the guard ring should be at least 5 times the thickness of the heat flux meter”.
HFP01 is equipped with a guard ring fulfilling the requirement of the standard. The ISO
9869-1 standard provides three methods for obtaining the thermal resistance from
measurement data:
1. The average method (ISO 9869-1, paragraph 7.1).
2. The average method with a correction for storage effects (ISO 9869-1,
paragraph 7.2).
3. The dynamic method (ISO 9869-1, Annex B).
For the average method, when measuring the thermal resistance of a building element,
the duration of the test according to ISO 9869-1 should be at least 72 h (ISO 9869-1
paragraph 7.1). In some cases, only night time data may be included in the analysis. At
the end of a test the obtained R – value should not deviate by more than ± 5 % from the
value obtained 24 h before, i.e. the measurement should converge. Furthermore, the
thermal resistance value obtained by analysing the initial 2/3 of the test data should not
deviate from value obtained by analysing the final 2/3 of the test data by more than
± 5 %, i.e. the measurement should be consistent. Whenever the change in heat stored
by the wall is more than 5 % of the heat flow through the wall during the test period, the
first method is insufficient and either the second or the third method listed above should
be used.
Chapters 7 and 8 of the ISO standard describe corrections for storage effects (changes in
average wall temperature), added thermal resistance by the heat flux sensor, which we
call the resistance error, and errors caused by the finite dimensions of the sensor.
ISO 9869 chapter 9 shows examples of uncertainty evaluation, arriving at typical
uncertainties of the order of ± 20 % of on-site measurements of thermal resistances.
Sensors for measurement of temperature difference should be calibrated to an accuracy
of ± 0.1 °C, reference paragraph 9.2 of this manual.
2.2.3 ASTM C 1155 and ASTM 1046: thermal resistance R
ASTM C 1155 and ASTM 1046 focus on the measurement of thermal resistance R (from
surface to surface) only. This is the R-value of formula 2.2.2.1.ASTM 1155 defines a Heat
Flow Sensor or Heat Flux Transducer (HFT). Paragraph 5.8 of the standard specifies that
during the test the indoor temperature changes less than 3 °C, and specifies that the
density of the construction material is < 440 kg/m3. Areas with a high lateral heat flux
should be avoided. Time constants should be estimated according to ASTM 1046. The
duration of the test is at least 24 h, and a convergence test may be used to determine
total required timespan.
ASTM 1046 offers good practices for installation and site selection.
2.2.4 Measurements on glass windows

TRSYS20 manual v2301 16/39
TRSYS20 and HFP01 may be mounted on glass windows, however special care must be
taken when interpreting data from measurements on glass. When measuring glass
windows please observe the following:
•During daytime, the window material typically transmits solar radiation, while the
HFP01 heat flux sensors absorb this radiation. During daytime the measurement is not
representative of the heat flux through the window. It is recommended to use night-
time data only.
•For windows with low R-value (high Λ-value), especially single-layer glass windows,
the thermal resistance of HFP01 itself may be non-negligible. The user should review
their case and may correct for the resistance error.

TRSYS20 manual v2301 17/39
3Specifications of TRSYS20
3.1 Specifications of TRSYS20
TRSYS20 is a system used for on-site measurement of thermal resistance, R, thermal
conductance, the Λ-value, and thermal transmittance, the U-value, of building envelope
components. TRSYS20 is used for measurements according to standard practices of ISO
9869 and ASTM C1155 / C1046. The system is equipped with MCU electronics, two heat
flux sensors of model HFP01 as well as two pairs of matched thermocouples. The sensors
are used to measure at two locations. Data review and calculation of the thermal
resistance from heat flux and temperature difference is the responsibility of the user.
Table 3.1.1 Specifications of TRSYS20 (continued on next page).
TRSYS20 SPECIFICATIONS
Description
high-accuracy building thermal resistance measuring
system with two measurement locations
Measurand
heat flux (2 x)
Measurand in SI units
heat flux density in W/m²
Measurand
temperature (2 x)
Measurand in SI units
temperature in °C
Measurand
temperature difference (2 x)
Measurand in SI units
temperature difference in °C
Use
Required data analysis to determine
thermal resistance, R, thermal
conductance, the Λ-value, and thermal
transmittance, the U-value
to be performed by the user according to ISO and
ASTM recommended practices
Minimum measurement duration
> 3 days
Standards governing use of the
measuring system
•ISO 9869 Thermal insulation – Building elements
– In-situ measurement of thermal resistance and
thermal transmittance.
•ASTM C 1155-95 Standard Practice for
Determining Thermal Resistance of Building
Envelope Components from the In Situ Data.
•ASTM 1046-95 Standard Practice for In Situ
Measurement of Heat Flux and Temperature on
Building Envelope Components
Measurement locations and sensor labelling
Number of measurement locations
2
Cable length per location
location 1: 10 m
location 2: 20 m
Included sensors location 1
heat flux: 1 x HFP01-10 with 10 m cable
temperature and temperature difference:
1 x TC-10 matched thermocouple pair with 10 m cable
marking “TC-1 inside” and “TC-1 outside”
Included sensors location 2
heat flux: 1 x HFP01-20 with 20 m cable
temperature and temperature difference:
1 x TC-20 matched thermocouple pair with 20 m cable
marking “TC-2 inside” and “TC-2 outside”
Cable markers heat flux sensor
2 x sticker, 1 x at sensor and 1 x cable end, wrapped
around the heat flux sensor cable. Both stickers show
sensitivity and serial number.

TRSYS20 manual v2301 18/39
Heat flux sensor mounting and
orientation
recommended orientation is with the red face of the
heat flux sensors facing indoors, and the blue face
mounted at the indoor walls
Cable markers temperature sensors
location 1: TC-1 inside and TC-1 outside
location 2: TC-2 inside and TC-2 outside
Table 3.1.1 Specifications of TRSYS20 (started on previous page, continued on next page)
Rated operating conditions
Rated operating temperature range
HFP01 and TC: -30 to +70 °C
MCU: -20 to +50 °C
IP protection class
see individual components below.
Rated operating relative humidity range
0 to 100 %
Storage and transport
Storage
when not in use TRSYS20 should be stored inside its
carrying case in a dry place. TRSYS20 MCU should be
stored with the dedicated dust caps placed on
connectors.
Net weight total TRSYS20 including
carrying case
approx. 8 kg
Gross weight
approx. 11 kg
Carrying case
box of 480 x 390 x 190 × 10-3 m
MEASUREMENT AND CONTROL UNIT (MCU)
Rated operating voltage
10 – 16 VDC
Recommended operating voltage
12 VDC
Power consumption
< 1 W
12 VDC connector type on MCU
Bulgin Standard Buccaneer®, PX0735/P, 2 pole
connector with pins
Maximum power supply cable length
1.8 m
Sample rate
1 sample/s
Stored measurements
10 min averages of heat flux, temperature and
temperature differences; instantaneous values of
panel temperature, heat flux sensor 1 sensitivity, heat
flux sensor 2 sensitivity
Storage capacity
> 30 days
MCU datalogger
Campbell Scientific CR1000X Measurement and
Control datalogger
Ingress protection rating
IP54
Indicator LEDs
Power switch / LED
red LED is on when power is supplied to MCU
Running LED
green LED is on when measurement is running
Internal battery for battery-backed memory and clock
Internal system battery
AA, 2.4 A∙hr, 3.6 VDC (Tadiran, TL-5903/S)
Internal battery replacement interval
3 years, can be replaced by the user
USB connector
Connector type on MCU
USB-B socket
USB cable type
shielded
Maximum USB cable length
2.0 m
Ethernet connector
Connector type on MCU
RJ45 (shielded)
Isolation/protection
magnetic isolation
TVS surge protection
Ethernet cable type
shielded
Maximum ethernet cable length
30 m
User interface
Hardware connection to PC
USB or
ethernet (preferred for long-term use)
User interface on PC
web interface
Web browser requirement
HTML 5 support
Supported web browsers
Chrome 10

TRSYS20 manual v2301 19/39
Firefox 4
Internet Explorer 9
Opera 11
Safari 5
or later
POWER SUPPLY UNIT (PSU)
Power supply model
Mean Well, GEM60I12
(similar power supplies may be used)
Input voltage
100 - 260 VAC
Input frequency
50 / 60 Hz
Input plug type
Type A/B (USA)
Type C/F (EU)
Type G (UK)
Type I (AU)
Output voltage
12 VDC
Output current
4.5 A
Output cable length
approx. 1.0 m
Output connector type
Bulgin Standard Buccaneer®, PX0736/S, 2 pole
connector with sockets
Ingress protection rating
IP22
Table 3.1.1 Specifications of TRSYS20 (started on previous pages).
HFP01 HEAT FLUX SENSOR
Specifications
see HFP01 manual
Guard width to thickness ratio
5 (as required by ISO 9869 D.3.1)
Measurement function
Φ
1
= U
1
/S
1
Φ2= U2/S2
Calibration uncertainty HFP01 heat flux
sensors
± 3 % (k = 2)
Ingress protection rating
IP67
TC MATCHED THERMOCOUPLE PAIR
Thermocouple type
IEC 60584-3: 2007 type KX
Measurement function
ΔT
1
= T
1, indoor
– T
1, outdoor
ΔT2= T2, indoor – T2, outdoor
Acceptance interval temperature
difference measurement
< ± 0.1°C
(required by ISO 9869, paragraph 5.2)
Ingress protection rating
IP67
INSTALLATION AND USE
Performing a representative
measurement
see the chapter on standards and recommended
practices for use and the chapter on installation of
HFP01 and TC
Installation
see the chapter on standards and recommended
practices for use and the chapter on installation of
HFP01 and TC
Sensor mounting
for mounting sensors on walls, we recommend use of
double-sided “removable” carpet laying tape such as
TESA 4939, which has free removability up to 14 days
from the most common surfaces (needs to be tested
individually before usage)
CALIBRATION AND FUNCTIONAL TEST
Performance verification
via functional test

TRSYS20 manual v2301 20/39
Calibration traceability
HFP01, TC and MCU are traceable to SI units
Calibration uncertainty HFP01 heat flux
sensors
± 3 % (k = 2)
Acceptance interval temperature
difference measurement
< ± 0.1°C
(required by ISO 9869, paragraph 5.2)
Recommended recalibration interval
2 yr
Electromagnetic Compatibility (EMC)
Emission standards
EN-IEC 61326-1 (2013)
EN-IEC 61326-1 (2021)
EN-IEC 61000-3-2 (2014), Class A
EN-IEC 61000-3-2 (2019) + AC (2021), Class A
EN-IEC 61000-3-3 (2013) + A1 (2019) + A2 (2021) +
AC (2022)
Emission limits
Light industrial and domestic environments, Class B
Immunity
EN-IEC 61326-1 (2013)
EN-IEC 61326-1 (2021)
Immunity levels
Industrial
Table of contents
Other Hukseflux Measuring Instrument manuals
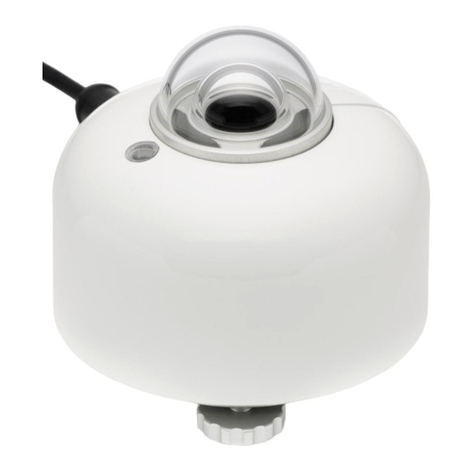
Hukseflux
Hukseflux SR30-D1 User manual
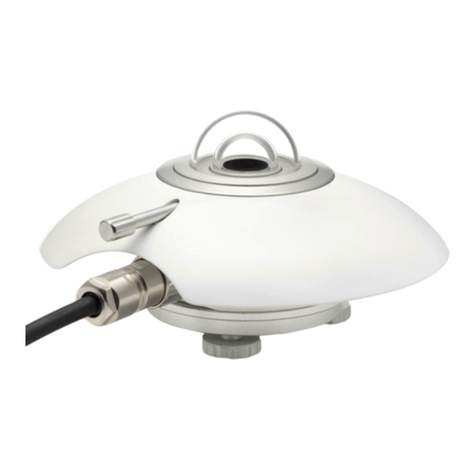
Hukseflux
Hukseflux SR20-D2 User manual
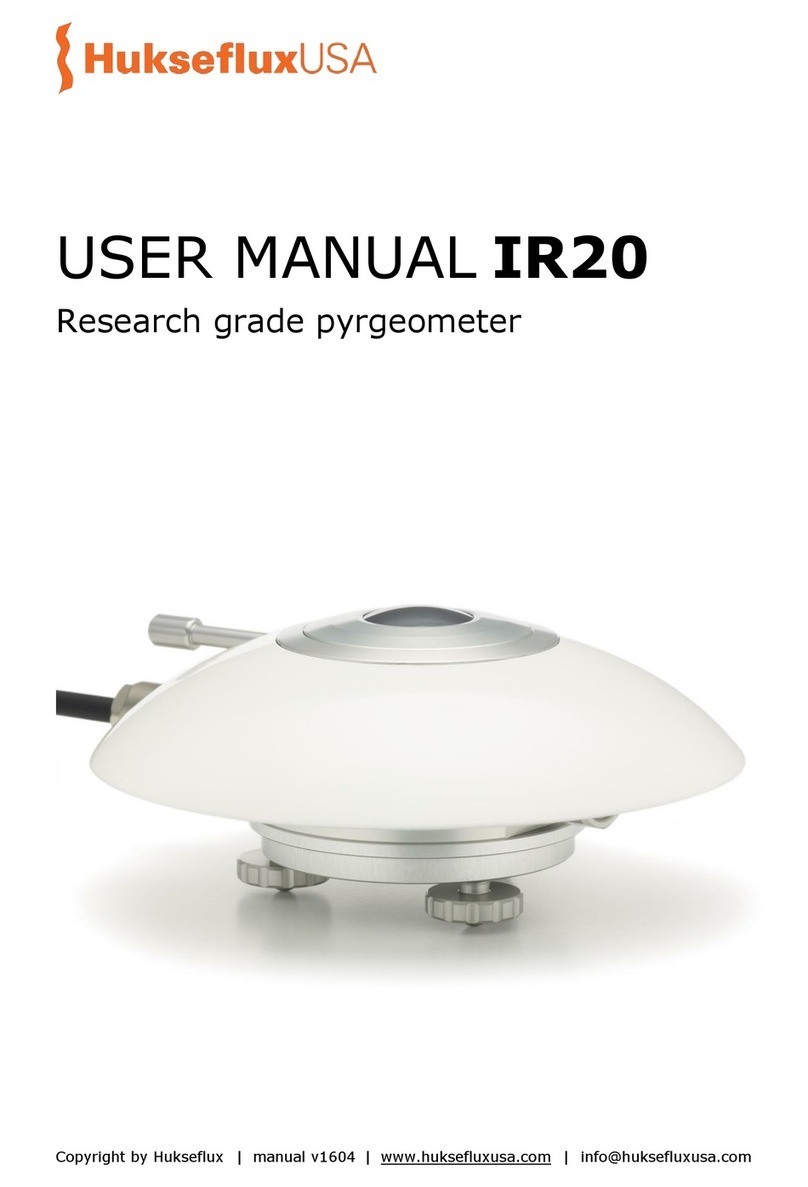
Hukseflux
Hukseflux IR20 User manual
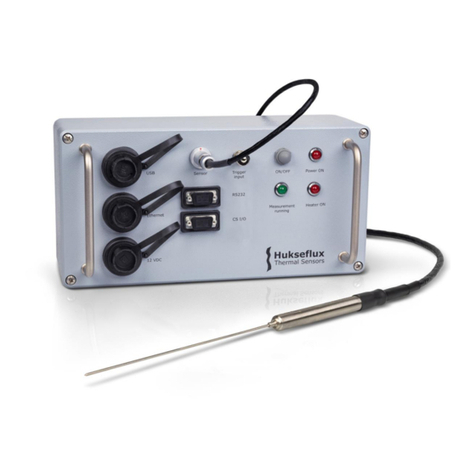
Hukseflux
Hukseflux TPSYS20 User manual
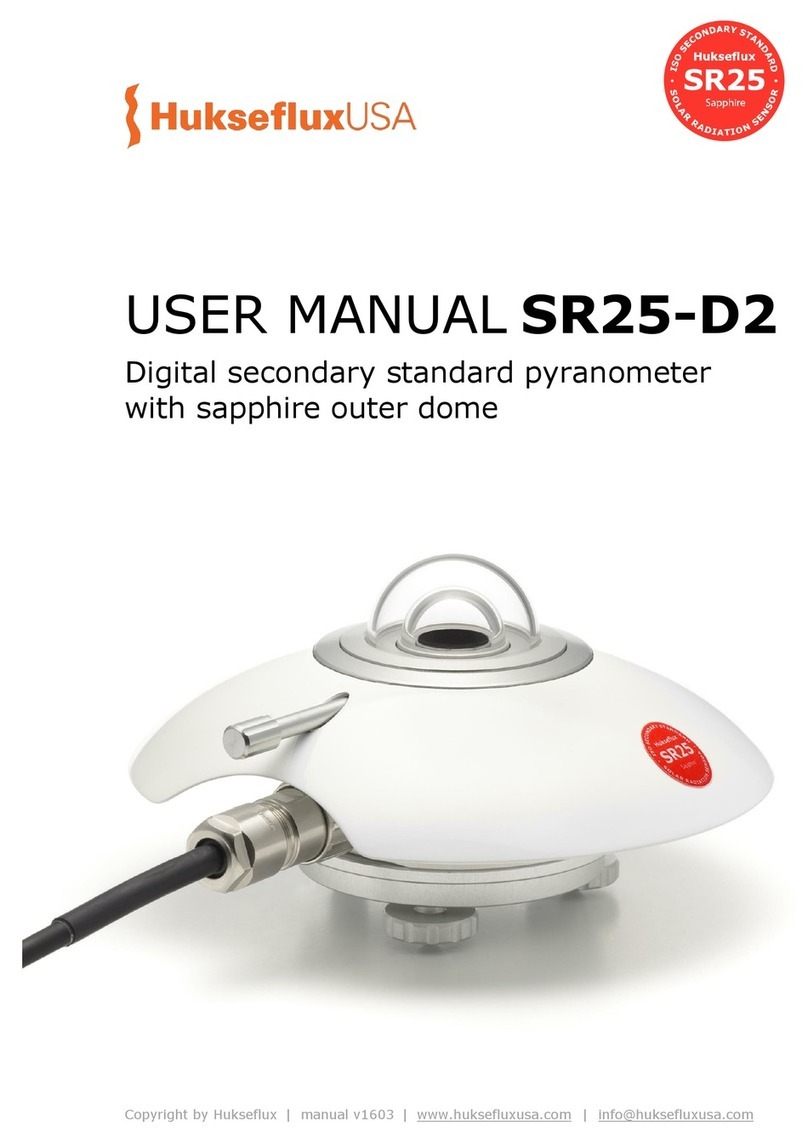
Hukseflux
Hukseflux SR25-D2 User manual
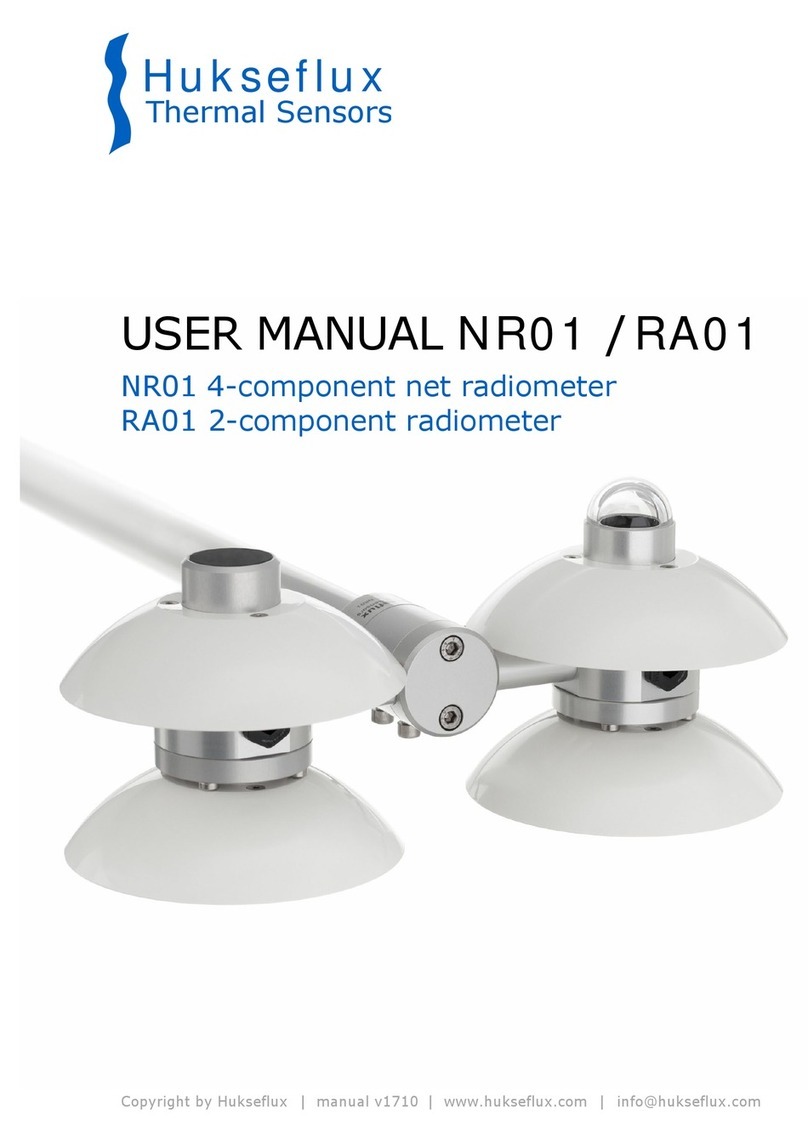
Hukseflux
Hukseflux NR01 User manual
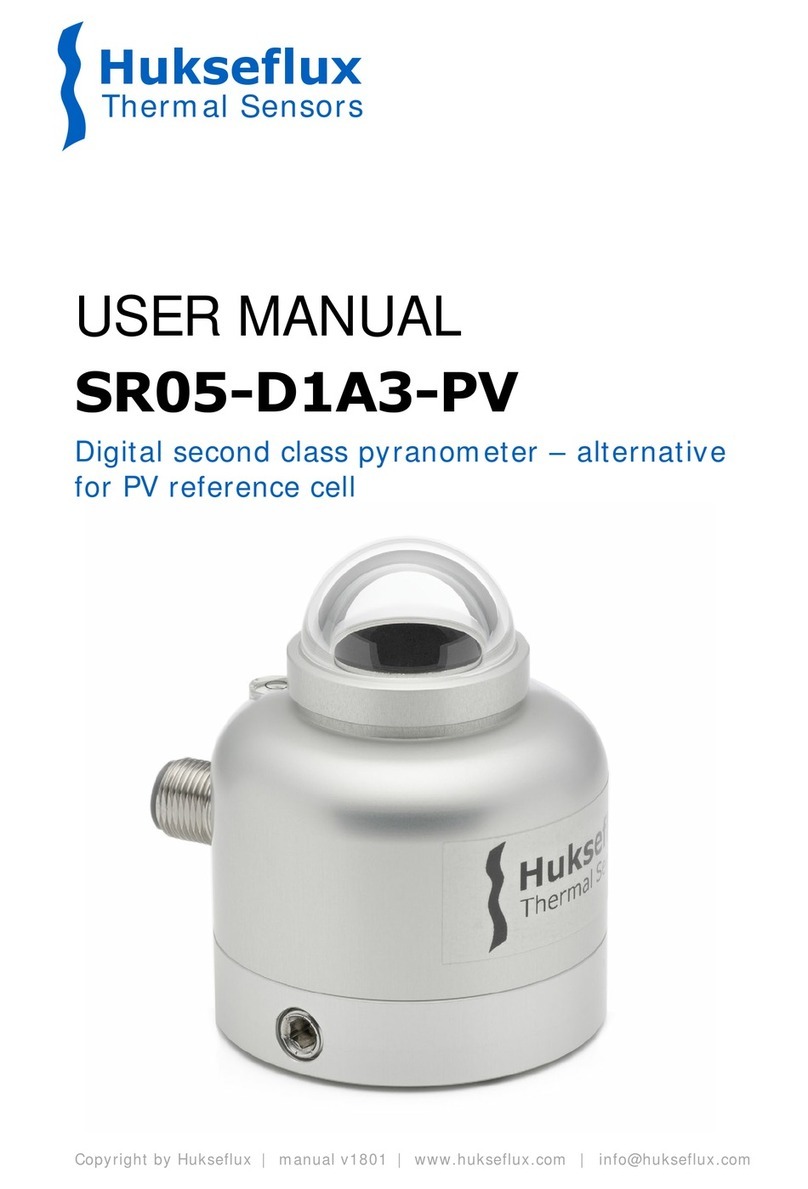
Hukseflux
Hukseflux SR05 series User manual

Hukseflux
Hukseflux FTN02 User manual
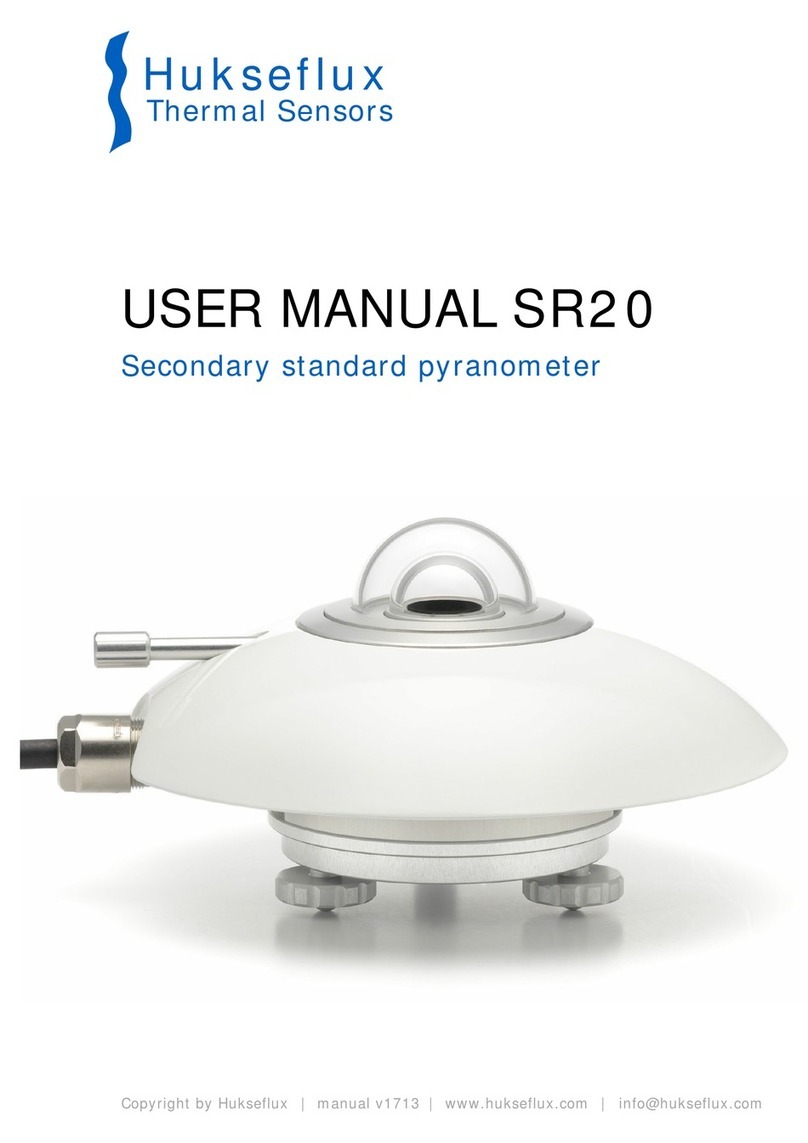
Hukseflux
Hukseflux SR20 User manual

Hukseflux
Hukseflux DR01 User manual