HunterDouglas Luminette PowerGlide 2.1 User manual

Luminette®PowerGlide®2.1
with Platinum™Technology
Side, Split, and Offset Stacks
Installation •Operation •Care

CONTENTS
Questions?
Call the Hunter Douglas Customer Information Center at
1-888-501-8364.
© 2014 Hunter Douglas. All rights reserved. All trademarks used herein are the property of Hunter Douglas.
Getting Started:
Product View ............................................................................ 1
Tools and Fasteners Needed ...................................................... 2
Unpack the Components ........................................................... 2
Mounting Types and Window Terminology................................... 3
Installation:
Mount the Installation Brackets — Inside/Ceiling Mount.............. 4
Mount the Installation Brackets — Outside Mount ...................... 7
Bracket Locations — Corner and Bay Windows ........................ 12
Install the SofTrak™Headrail .................................................... 13
Side-by-Side (Abutted) Installations (Simulated Split Stack)........ 14
Attach PowerGlide®2.1 Components ....................................... 15
Test Headrail Operation .......................................................... 18
Attach the Fabric Panel(s)........................................................ 18
Modern Draperies Dressing .................................................... 22
Operation:
Operate the Window Covering.................................................. 23
Resetting the Window Covering................................................ 24
Troubleshooting ...................................................................... 25
Care:
Cleaning Procedures ............................................................... 28
Removing the Modular Motor (If Necessary) ............................. 31
Removing the Fabric (If Necessary)........................................... 31
Removing the Headrail (If Necessary)........................................ 32
Additional Product Enhancements ............................................ 32
Radio Frequency FCC Compliance:
This device complies with Part 15 of the FCC Rules. Operation is subject to the following two conditions:
(1) This device may not cause harmful interference, and
(2) This device must accept any interference received, including interference that may cause undesired operation.
This equipment has been tested and found to comply with the limits for a Class B digital device, pursuant to Part 15 of the FCC Rules. These limits are
designed to provide reasonable protection against harmful interference in a residential installation. This equipment generates, uses and can radiate radio
frequency energy and, if not installed and used in accordance with the instructions, may cause harmful interference to radio communications. However,
there is no guarantee that interference will not occur in a particular installation. If this equipment does cause harmful interference to radio or television
reception, which can be determined by turning the equipment off and on, the user is encouraged to try to correct the interference by one or more of the
following measures:
■Reorient or relocate the receiving antenna.
■Increase the separation between the equipment and receiver.
■Connect the equipment into an outlet on a circuit different from that to which the receiver is connected.
■Consult the dealer or an experienced radio/TV technician for help.
Any changes or modifications not expressly approved by the party responsible
for compliance could void the user’s authority to operate the equipment.

GETTING STARTED
1
Product View
Left Stack Right Stack Split Stack
Dual Panel
Split Stack
Dual Panel Offset Stack
(Left Stack Shown)
Dual Panel
Side Stack Left
Dual Panel
Side Stack Right
SofTrak™
Headrail
Swivel
Plate
Rivet
Swivel
Arm
Left Stack Shown
End
Treatment
Inside/Ceiling
Mount Bracket
Installation Bracket
Faceplate
DC Power
Supply
DC Power
Supply Cable
C-Clip
Modular Motor
Assembly
Platinum
™
Satellite Eye
Platinum
Remote Control
Drive Assembly
Spacer Block
with Bushings
Pinion
Clips
Swivel
Plate

2
GETTING STARTED
Thank you for purchasing Hunter Douglas Luminette®Privacy Sheers or Luminette Modern
Draperies. With proper installation, operation, and care, your new window fashions will provide
years of beauty and performance.
Please thoroughly review this instruction booklet and the packing list included with your order
before beginning the installation.
Tools and Fasteners Needed
■Flat blade and Phillips screwdriver ■Laser level
■Measuring tape and pencil ■Needlenose pliers
■Paper clip or push pin
■Utility knife and scissors
■Power drill,
3
/
32
" drill bit,
and
1
/
4
" hex driver
In addition, you will need fasteners designed to work with your specific mounting surface(s).
■#6 Hex Head Screws (Provided). Two screws are provided per installation bracket.
■Speed Nuts and Screws (Provided). Extension brackets come with screws and speed nuts.
■Drywall Anchors (Not Provided). Use drywall anchors when mounting into drywall.
Unpack the Components
■Make sure you have clean hands or wear disposable gloves when handling Luminette fabric.
To avoid wrinkling the fabric, do not fold it or drape it over furniture.
■One or more fabric panels may be packaged in a carton.
■The fabric panels are rolled around a cardboard tube. Do not remove the protective
wrapping until completing the “Attach the Fabric Panel(s)” procedure on page18.
■Remove the SofTrak™headrail system and installation hardware from inside the carton.
■Remove the foam supports from the tilt shaft inside
the headrail. Rotate the supports in either direction
until they can be pulled off.
Important: With wider fabrics, the SofTrak
headrail may be shipped separately.
Remove
Foam Supports
Speed Nut and Screw
(Two Provided with Each
Extension Bracket)
#6 x 1
1
/
2
" (Inside/Ceiling Mount)
#6 x 2" (Outside Mount)
Hex Head Screw
(Provided)

GETTING STARTED
3
Mounting Types and Window Terminology
If the installation brackets are mounted correctly, the rest of the installation process follows very
easily. To prepare for this important first step, review the mounting types and basic window
terminology illustrated below.
■For proper operation, the fabric must clear all obstructions, including window cranks,
handles, and moldings.
➤Replace protruding window cranks with T-cranks, as needed.
■Refer to the appropriate page below based on your order:
➤Inside/Ceiling Mount — Page 4
➤Outside Mount — Page 7
Collectively, the sill and
jambs are called the
“window casement.”
Molding (or Wall)
Head Jamb
Sill (or Floor)
Jamb Jamb
Inside Mount
Sheer or drapery
fits within
window opening.
Outside Mount
Sheer or drapery
mounts outside
window opening.

INSTALLATION
4
Mount the Installation Brackets — Inside/Ceiling Mount
If you are mounting on corner or bay windows, refer to “Bracket Locations — Corner and Bay
Windows” on page12 for specific bracket locations. Return to this page after identifying
thelocations.
■Your order will include the appropriate number of inside/ceiling mount installation brackets.
The number of installation brackets required varies with headrail width, as shown below.
Measure and Mark Bracket Locations
■Measure for the bracket locations.
➤Mark 5" from each jamb on the mounting surface. These marks are for the outside edge
of the end installation brackets.
➤If more than two installation brackets are required (see table above), mark the locations
of additional bracket(s) spaced evenly between the two end brackets.
Important: For the most reliable operation, the motor side bracket needs to be close
(
3
/
4
" or less) to the motor.
CautIon: Installation brackets should be fastened into wood whenever possible.
Use drywall anchors when mounting into drywall. When attaching brackets into drywall,
additional brackets may be required to keep the headrail level after the fabric is attached.
Inside/Ceiling Mount
Installation Bracket
Headrail
Width
Brackets Required
Up to 40" 2
40
1
/
8
" – 70" 3
70
1
/
8
" – 96" 4
96
1
/
8
" – 155" 6
155
1
/
8
" – 192" 8
Top View
Bracket
Jamb
Jamb
SofTrak™Headrail
Space EvenlySpace Evenly5" 5"
5
/
8
" Gap Required
Motor

INSTALLATION
5
■Mark where to drill holes for the screws.
Important: The front edges of the brackets must be level and aligned to each other.
➤Align the outside edge of the
end brackets on your marks,
then mark each of the screw
holes. Center any additional
brackets on the marks to
mark their screw holes.
➤The minimum depth required
is 1" for the Classic 3
1
/
2
"
vane size and 2" for the
Quintette®4
3
/
4
" vane size.
➤To fully recess the fabric in the window casement, 6
1
/
4
" is needed for the Classic 3
1
/
2
"
vane size, and 8
1
/
4
" is needed for the Quintette 4
3
/
4
" vane size. See the illustration
below.
Minimum Inside Mount Depth:
Classic 3
1
/
2
" Vane Size = 1"
Quintette 4
3
/
4
" Vane Size = 2"
5"
SofTrak™Headrail
Bracket
Inside Mount
Fully Recessed Mounting Depth
Stacked
Classic Fabric
(Privacy Sheers
and Modern
Draperies)
Stacked
Quintette
Fabric
Classic Vane
Quintette
Vane
6
1
/
4
" Minimum for Classic 3
1
/
2
" Vane Size
8
1
/
4
" Minimum for Quintette 4
3
/
4
" Vane Size
Window
Side

INSTALLATION
6
Mount the Brackets
■Drill the screw holes using a
3
/
32
" drill bit.
Important: Use drywall anchors when
mounting into drywall.
■Attach the installation brackets using the
screwsprovided.
Important: For proper operation, the
SofTrak™headrail must be mounted level.
Use a laser level to check that the installation
brackets are level and aligned. Shim the
brackets if necessary. The brackets may also
need to be shimmed if the mounting surface
is heavilytextured.
To Shim the Brackets:
■Snap off the top of the shim for use with inside/ceiling mount
brackets.
■Use the shims, as needed, between the mounting
surface and the inside/ceiling mount brackets.
Use a laser level as reference.
■To make further adjustments, you may add
or remove shims by loosening the installation
bracket screws.
Proceed to “Install the SofTrak Headrail” on page13.
Level and Aligned
Snap Off
Shim
Loosen
screws
to add or
remove shims.

INSTALLATION
7
Mount the Installation Brackets — Outside Mount
If you are mounting on corner or bay windows, refer to “Bracket Locations — Corner and Bay
Windows” on page12 for specific bracket locations. Return to this page after identifying
thelocations.
■Your order will include installation bracket assemblies specific to your vane size. The number
of assemblies required varies with headrail width, as shown below.
Important: The spacer blocks have tabs that prevent the
brackets from being mounted too close to the ceiling. If the sheer
or drapery is not going to be mounted at ceiling level, the tabs
can be removed.
Adding Clearance
■Use spacer blocks to add additional clearance. Spacer blocks add clearance in
1
/
2
" increments.
➤Classic 3
1
/
2
" Vane Size: Requires one spacer block with faceplate for standard
installation. Three additional spacer blocks may be added for an extra 1
1
/
2
" clearance.
➤Quintette 4
3
/
4
" Vane Size: Requires three spacer blocks with faceplate for standard
installation. One additional spacer block may be added for an extra
1
/
2
" clearance.
■Use optional extension brackets to add more clearance.
➤Classic 3
1
/
2
" Vane Size: Standard extension brackets
can provide up to 3
1
/
2
" clearance; XLextension
brackets can provide up to 5
1
/
2
" clearance.
➤Quintette 4
3
/
4
" Vane Size: Standard extension
brackets can provide up to 2" clearance; XLextension
brackets can provide up to 4" clearance.
➤Indentations are stamped into the extension brackets between each set of holes. Using
the indentations as a guide, you may cut off any unneeded length before mounting the
extension brackets. Each two-hole section is
1
/
2
" in length.
Removable
Tabs
Standard Extension
Bracket
XL Extension
Bracket
Faceplate
Bracket Assembly
Classic 3
1
/
2
" Vanes
One
Spacer
Block
Three
Spacer
Blocks
Bracket Assembly
Quintette®4
3
/
4
" Vanes
Bushings
Headrail
Width
Bracket Assemblies
Required
Up to 40" 2
40
1
/
8
" – 70" 3
70
1
/
8
" – 96" 4
96
1
/
8
" – 155" 6
155
1
/
8
" – 192" 8

INSTALLATION
8
Measure and Mark Bracket Locations
■Position the SofTrak™headrail over the window or door opening at the ordered height, found
on the headrail label. Use a pencil to lightly mark each end of the headrail.
➤Alternatively, measure the width of the headrail and use that width to mark the headrail
end points over the opening.
Important: Typically, split stack designs are centered over the opening. However, side
stack designs may be offset to one side if the fabric was intended to stack partially or
completely off the window or door opening. The intended stackback must be taken into
account when marking the headrail end points.
■Mark 5" from each end of the headrail.
➤If more than two installation brackets are required (see table on previous page), mark the
locations of additional bracket(s) spaced evenly between the two end brackets.
CautIon: Installation brackets should be fastened into wood whenever possible.
Use drywall anchors when mounting into drywall. When attaching brackets into drywall,
additional brackets may be required to keep the headrail level.
■Mark the bracket mounting height to allow proper floor clearance for the fabric when
attached to the headrail. This method provides a minimum of
1
/
2
” floor clearance.
➤Locate the ordered height on the headrail label.
➤Spacer Blocks: Measure the
ordered height minus
1
/
4
” from
the floor surface. Mark this
height at each bracket location.
➤Extension Brackets: Measure
the ordered height plus
1
/
4
” from
the floor surface. Mark this
height at each bracket location.
(With XL brackets, measure and
mark the ordered height.)
Important: Mount the screws at the height indicated, or higher for additional floor
clearance. Be sure to clear all floor obstructions such as carpet, vents, rugs, etc.
Headrail End Marks
Window Opening
5"
Space EvenlySpace Evenly
5"
Floor Surface
Ordered
Height –
1
/
4
"
Ordered
Height +
1
/
4
"
(XL Brackets
= Ordered
Height)
Spacer
Block
Extension
Bracket

INSTALLATION
9
■Mark where to drill holes for the installation screws.
➤A minimum of 1
1
/
8
" flat vertical surface is required for spacer block installation and
1
3
/
8
" flat vertical surface is required for installation with extension brackets.
➤Align the spacer blocks or extension brackets on your height marks.
➤Align the outside edge of the end spacer blocks or extension brackets on your bracket
location marks, then mark each of the screw holes. Center any additional brackets on
the bracket location marks to mark their screw holes.
CautIon: The rear of the blocks/brackets must be flush against a flat mounting surface.
Do not mount brackets oncurved molding.
Mount the Spacer Blocks or Extension Brackets
■Drill the screw holes using a
3
/
32
" drill bit.
Important: Use drywall anchors when mounting into drywall.
■Attach the spacer blocks or extension brackets using the
screws provided.
➤For the spacer block installation, first insert the square end
of the bushings into the slots in the spacer block. Insert the
screws through bushings.
Important: With spacer blocks, place the screws in the
middle of the slots to make aligning the brackets easier.
Bushings
Bushings Inserted
Headrail
End Mark
Screw
Height Mark
Headrail
End Mark
5"
Screw
Height Mark
5"

INSTALLATION
10
➤For extension bracket installation, you may cut off any unneeded length (before
mounting) at indentations stamped into the brackets between each set of holes. Each
two-hole section is
1
/
2
" in length.
Important: For proper operation, the SofTrak™headrail must be mounted level. Use
a laser level to check that the spacer blocks or extension brackets are level and aligned.
Shim the brackets if necessary. The brackets may also need to be shimmed if the mounting
surface is heavily textured.
To Shim the Brackets:
■Loosen the installation screws securing
the spacer block or extension bracket.
■Insert one or more shims between the
spacer block or extension bracket and
the mounting surface. Tighten the
installation screws.
Level and Aligned
Level and Aligned
Loosen
Mounting
Screws
Insert
Shim(s)
1
2
1
2
To Shim
Installation Bracket
To Shim
Extension Bracket

INSTALLATION
11
Finish Bracket Assembly
Spacer Blocks:
■Add any additional spacer blocks required.
Important: A maximum of four spacer
blocks can be used per installation faceplate.
■Hook the top of the faceplate to the front
spacer block and snap it into place.
Extension Brackets:
■Slide the base covers onto each extension bracket.
■If necessary, use scissors to trim the flat bracket cover to length. Slide a cover onto
each bracket.
■Attach inside/ceiling mount installation brackets using the screws and speed nuts provided.
Proceed to “Install the SofTrak™Headrail” on page13.
Faceplate
Extension
Bracket
Cover
Extension
Bracket
Extension Bracket
Base Cover
Screws
Speed Nuts
Inside/Ceiling
Mount
Bracket

INSTALLATION
12
Bracket Locations — Corner and Bay Windows
■For bracket placement, mount the installation brackets 8" from the corner for the Classic
3
1
/
2
" vane size and 9" from the corner for the Quintette®4
3
/
4
" vane size.
Important: The ends of the headrails should be located 3" from the corner for the
Classic 3
1
/
2
” vane size and 4" from the corner for the Quintette 4
3
/
4
” vane size.
➤If additional spacer blocks or extension brackets are used, the installation brackets must
be moved further away from the corner by the amount of added clearance.
■For bay windows, treat the center system as a corner system on both ends of the headrail.
Important: For the most reliable operation, the motor-side bracket needs to be close
(
3
/
4
" or less) to the motor.
Classic 3½" Vane Size
8"
3"
Motor
End
Motor
End
Brackets
5"
(ends of headrails
located 3" from corner)
Quintette 4¾" Vane Size
(ends of headrails
located 4" from corner)
8" 5"
9"
4"
Motor
End
Motor
End
Brackets
5"
9" 5"

INSTALLATION
13
Install the SofTrak™Headrail
■Push up on the locking screws. This raises the locking
tab and makes the headrail easier to install.
■The grooves on the back of the headrail are designed
to snap into the locking tab on the faceplate and
inside/ceiling mount bracket.
➤Tilt the front of the headrail (the side with the
pinion clips) up so the top groove fits into the
locking tab on each installation bracket.
■With the top groove in place on all brackets, tilt
the headrail down so the bottom groove fits into
the bottom tabs on the installation brackets.
■Position/center the headrail and tighten the locking
screws with a screwdriver. Do not overtighten.
Inside Mount and Wall-To-Wall Outside Mount Installations
■After the SofTrak™headrail is installed into the installation brackets, check the clearance at
eachend and make any necessary adjustments.
Important: The recommended amount of clearance varies according to the motor end
and stack design, as shown below.
■Lock the headrail into place by tightening the locking screws on the bottom of the brackets
until they are snug. Do not overtighten.
Tilt Down
Pinion
Clip
Tighten
Tilt Up
Locking
Tab
SofTrak
Headrail
Locking
Screw
Split Stack and Dual Panel Design — Minimum Clearances*
5
/
8
"
Non-Motor End*
5
/
8
"
Right Stack Design — Minimum Clearances
7
/
8
"
Non-Motor End
5
/
8
"
Left Stack Design — Minimum Clearances
5
/
8
"
Non-Motor End
7
/
8
"
*Split Stack Design: Motor is on either the right or left as ordered.
Motor End*
Motor End
Motor End

INSTALLATION
14
Side-by-Side (Abutted) Installations (Simulated Split Stack)
A simulated split stack (the fabric opens in the
center) is two side stack systems installed with
the non-motor ends side-by-side.
■Adjust the SofTrak™headrails according
to the illustration for proper swivel arm
operation.
Important: Be sure to measure the
spacing from end cap to end cap, not from
the swivel arms.
Non-Motor
End Cap
Non-Motor
End Cap
1
1
/
2
"
Swivel
Plates
Swivel
Arm
Swivel
Arm
RTW
Swivel
Plates
RTW Not Recommended
Proper Installation
Simulated Split Stack

INSTALLATION
15
Attach PowerGlide®2.1 Components
Attach the Motor Assembly
■Remove the orange pull tab from the drive
assembly.
■Align the pins with the holes in the drive
assembly. Press the motor up into the drive
assembly until it clicks into place.
Important: If snapping the motor onto
the drive assembly seems difficult, grasp
the lead carrier and pull the carriers slightly
away from the motor, as shown at right.
The motor should now snap in easily.
■If you remove the motor and need to reinstall it, check the drive assembly and make sure
the tilt gear aligns with the arrows.
➤If necessary, use a screwdriver to turn the tilt gear until it is aligned.
Aligned Tilt Gear

INSTALLATION
16
Connect the Platinum™Satellite Eye
CautIon: Connect the satellite eye before
connecting the DC power supply.
■Plug the 6-wire satellite eye connector into
the motor housing.
CautIon: The satellite eye can only
be inserted one way. Do not force the
connector into the motor housing.
Determine Platinum Satellite Eye Mounting Location
■A 20" wire is standard on the satellite eye. You
may have ordered a longer length.
■For infrared (IR) operation, choose a location for
the satellite eye where the signal from the remote
control will not be obstructed.
Important: For infrared operation, do not mount the satellite eye in direct sunlight or
in bright, focused light from halogen or fluorescent light fixtures, track lighting, spotlights
or neon lights. Do not mount behind the SofTrak™headrail unless you plan to operate the
system only in radio frequency mode.
For radio frequency operation, the satellite eye does not need to be visible and bright
lights do not affect operation. However, the satellite eye does need to be visible during
theprogramming process.
Mount the Platinum Satellite Eye
CautIon: Handle the satellite eye carefully to avoid damaging the
infrared eye. Do not touch, move, or push the infrared eye.
■Choose a location where the infrared signal from the remote is
not obstructed. Check that the wire is not caught or pinched in
the brackets or headrail.
Infrared
Eye

INSTALLATION
17
■Using a single screw, mount the hinged flange to the wall
through the center hole on the flange. The satellite eye
should face down, as shown in theillustration.
■After mounting the hinged flange, swivel the satellite eye
upward to the correct angle for receiving infrared signal
from the remote control.
Install the DC Power Supply
CautIon: Make sure the Platinum™satellite eye is plugged into the motor before connecting
the DC power supply.
■Plug the power cable with the barrel
connector from the motor into the
extensioncable.
■Plug the other end of the extension cable
into the DC power supply.
■Secure the DC power supply wire using
the C-clips provided. Hide the wire behind
the fabric, making sure it does not impede
operation.
■Space the C-clips approximately 15" apart along
the DC power supply wire, as shown.
■Plug the DC power supply into the power source.
WarnIng: Keep cables and small parts
out of the reach of children. They can wrap
cables around their necks and STRANGLE.
They can also put small parts in their
mouths and CHOKE.
WarnIng: Electric shock and/or afire
hazard may occur if not properlyinstalled.
Flange
Wall
Barrel
Connector
Extension
Cable
DC
Power
Supply
Extension
Cable
15" (Max)
18V
Power Supply
Wire Retainer
Extension Cable
Motor
Assembly

INSTALLATION
18
Test Headrail Operation
Use the manual control button on the satellite eye to test the operation of the headrail.
■Test the traverse function.
➤Press and release the button to traverse the
carriers across the full length of the headrail.
➤Press and release the button a second time to
traverse the carriers to the fully stacked position.
➤Pressing the button while the fabric carriers are
traversing will stop the traverse at that point.
■Test the tilt function.
➤When the carriers are fully traversed across the headrail, press and hold the button for
approximately 3 to 5 seconds to test the tilt function.
➤Press and hold the button a second time to tilt in the other direction.
➤To stop the tilt function, release the manual control button.
Attach the Fabric Panel(s)
Preparations
■Use the manual control button on the satellite eye to stack the carriers.
■Stand the tube on end on a clean surface with the header at the top. Position
the tube at the end of the headrail where the fabric stacks.
■If the tube is too long to stand on end, carefully and safely use a utility knife
to trim the tube to an appropriate length. Do not unroll the fabric until you
begin attaching the vanes to the pinion clips.
CautIon: Be very careful when trimming the tube to avoid damaging the
fabric in any way.
■Remove the protective wrapping from the fabric.
Manual Control Button
Tube
Fabric
Panel
Table of contents
Other HunterDouglas Accessories manuals
Popular Accessories manuals by other brands
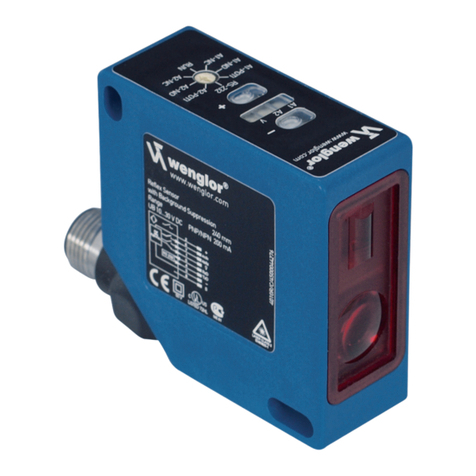
Wenglor
Wenglor CP25QXVT80 operating instructions

Burkert
Burkert 8030 HT instruction manual
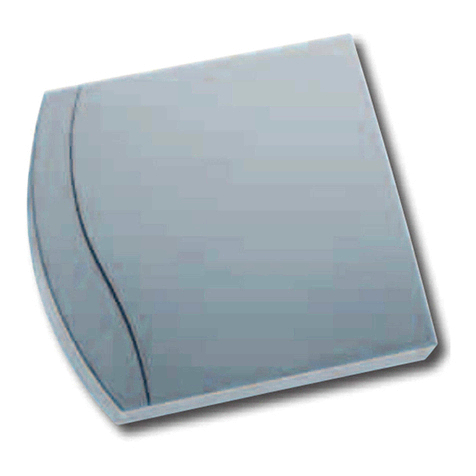
S+S Regeltechnik
S+S Regeltechnik AERASGARD RFTF-CO2 Operating Instructions, Mounting & Installation

Cuisinart
Cuisinart CEK-50 Quick reference guide

STEINEL
STEINEL IR Quattro HD-2 KNX manual
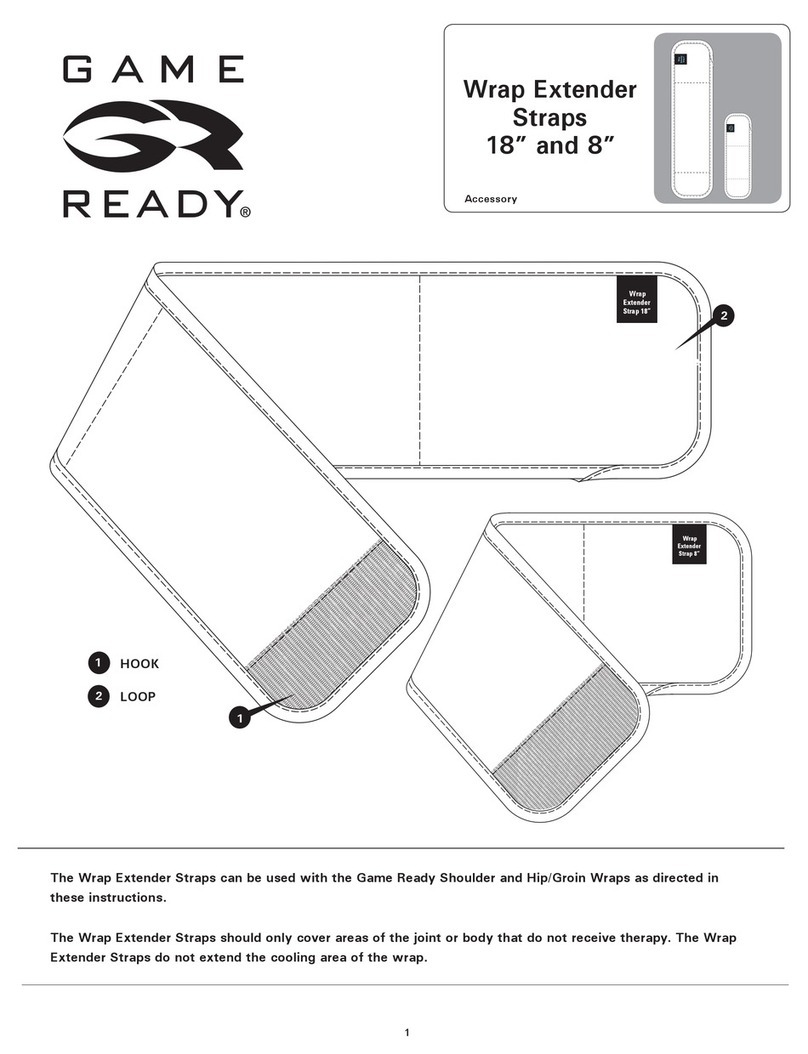
Game ready
Game ready Wrap Extender Strap 18" user manual
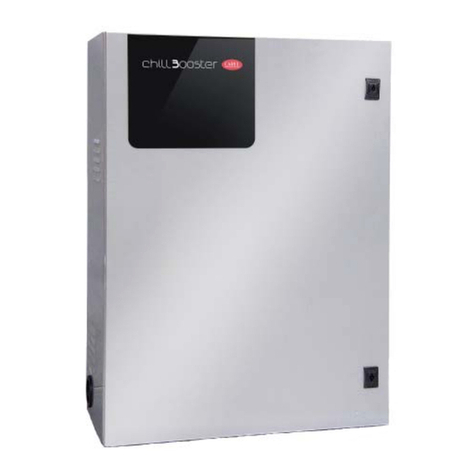
Carel
Carel ChillBooster AC010D0 Series user manual
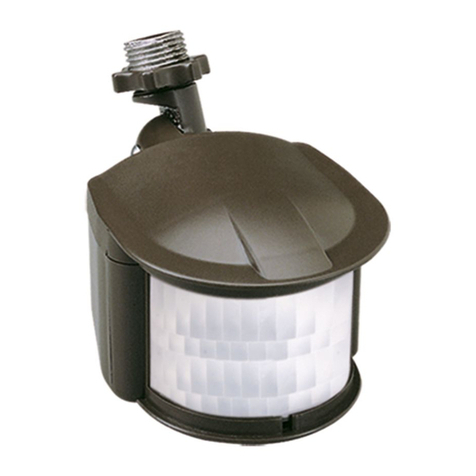
Cooper Lighting
Cooper Lighting MS180 instruction manual

schmersal
schmersal EX-BNS 303-2187 operating instructions
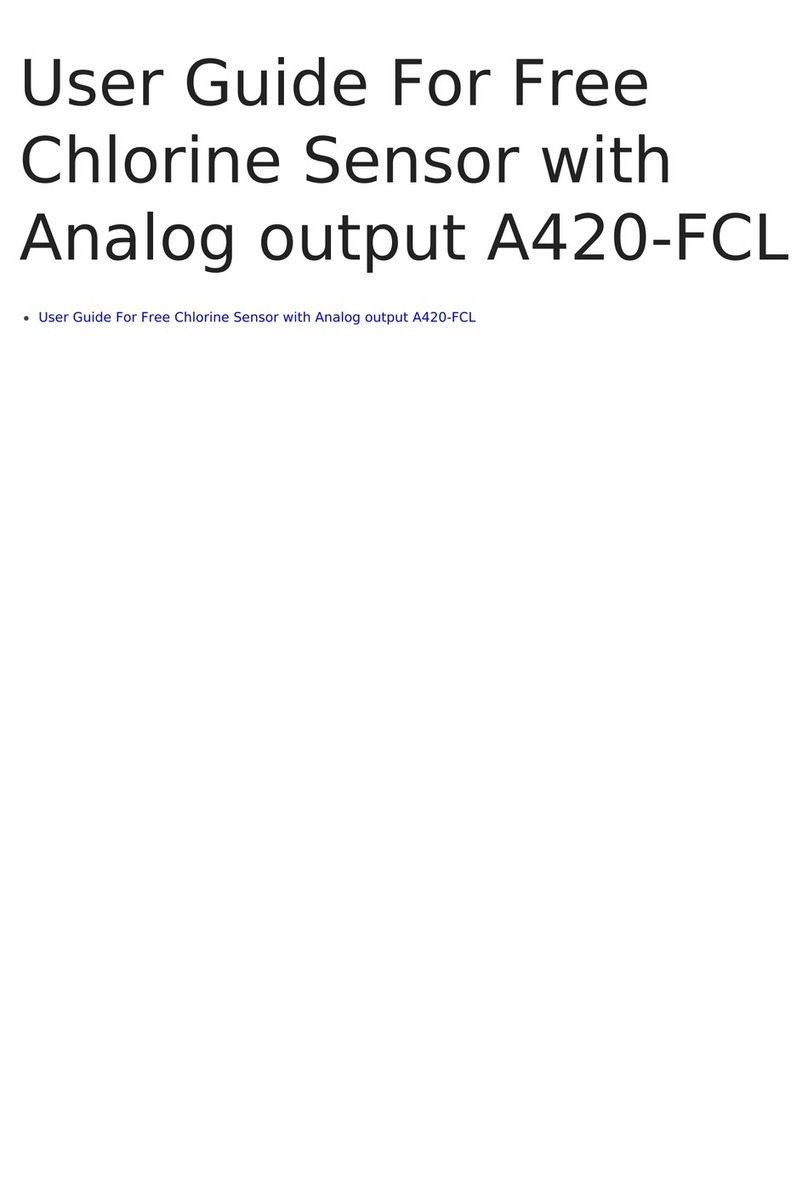
daviteq
daviteq A420-FCL user guide
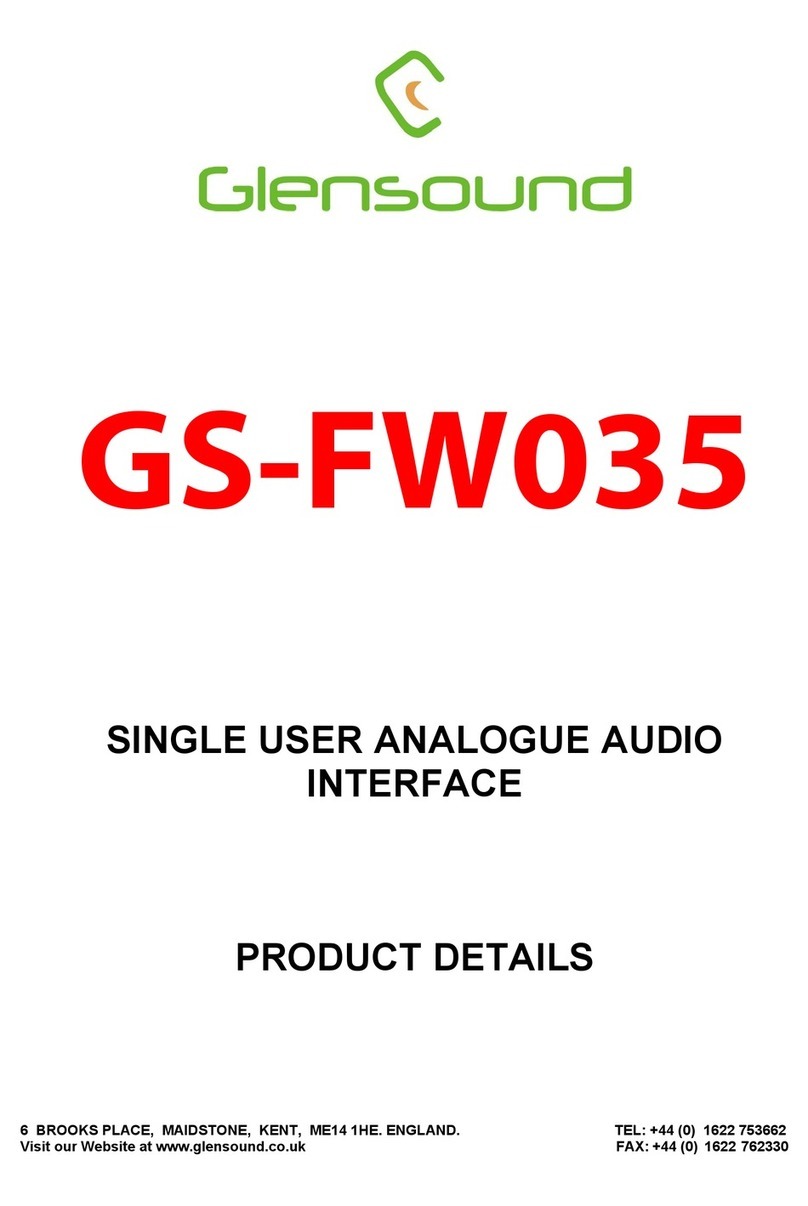
Glensound
Glensound GS-FW035 manual
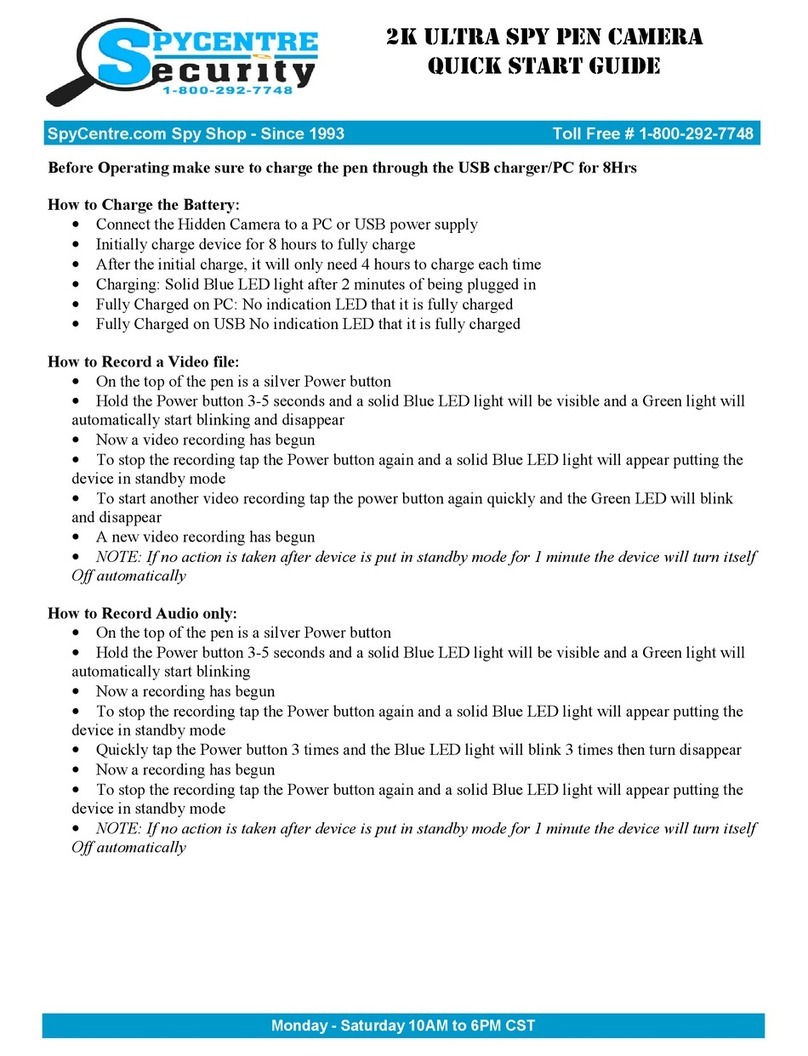
Spycentre Security
Spycentre Security 2K ULTRA SPY PEN CAMERA quick start guide