Hussmann Proto-Aire EZ User manual

®
Æ
Proto-Aire EZ
Installation and
Operation Manual
P/N 3090249_E
October 2020
MANUAL- Proto-Aire EZ - IO
Le manuel en français est
disponible via le code QR

Environmental Concerns
Hussmann recommends responsible handling of refrige
-
rants that contain Chlorine, Fluorine and Carbon (CFCs)
and those that contain Hydrogen, Chlorine, Fluorine, and
Carbon (HCFCs). Only certied technicians may handle
these refrigerants. All technicians must be aware and
follow the requirements set forth by the Federal Clean Air
Act (Section 608) for any service procedure being perfor
-
med on this equipment that involves refrigerant. Additio
-
nally, some states have other requirements that must be
adhered to for responsible management of refrigerants.
Contractors shall strictly adhere to specifications
provided by the Engineer of Record (EOR), as
well as US Environmental Protection Agency reg-
ulations, OSHA regulations, and all other federal,
state and local codes. This work should only be
done by qualified, licensed contractors. There are
numerous hazards, not limited to, but including:
burns due to high temperatures, high pressures,
toxic substances, electrical arcs and shocks,
very heavy equipment with specific lift points and
structural constraints, food and product damage or
contamination, public safety, noise, and possible
environmental damage. Never leave operating
compressors unattended during the manual soft-
start process. Always power rocker switches off
when unattended.
PERSONAL PROTECTION EQUIPMENT (PPE)
Only qualified personnel should install and service
this equipment. Personal Protection Equipment
(PPE) is required whenever servicing this equipment.
Wear safety glasses, gloves, protective boots
or shoes, long pants, and a long-sleeve shirt as
required when working with this equipment. Ob-
serve all precautions on tags, stickers, labels and
literature attached to this equipment.
The precautions and use of the procedures described
herein are intended to use the product correctly and
safely. Comply with the precautions described below to
protect you and others from possible injuries. Relative to
their potential danger, the relevant matters are divided
into four parts as dened by ANSI Z535.5
ANSI Z535.5 DEFINITIONS
• DANGER – Indicate[s] a hazardous
situa-
tion which, if not avoided, will result in death
or serious injury.
• WARNING –Indicate[s] a hazardous
situation
which, if not avoided,
could result in death or
serious injury.
• CAUTION –Indicate[s] a hazardous
situation
which, if not avoided, could result in minor
or moderate injury.
• NOTICE – Not related to personal injury –Indicates[s]
situations, which if not avoided, could result in damage
to equipment.
* * * * * * * * * * * * * * * * * * * * * * * * * * * * * * * * * * *
BEFORE YOU BEGIN
Read the safety information completely and carefully.

— LOCK OUT / TAG OUT —
To avoid serious injury or death from electrical
shock, always disconnect the electrical power at
the main disconnect when servicing or replacing
any electrical component. This includes, but is
not limited to, such items as controllers, electrical
panels, condensers, lights, fans, and heaters.
This manual was written in accordance with
originally perscribed equipment that is subject
to change. Hussmann reserves the right to
change all or part of the equipment for future
stores such as, but not limited to, controllers,
valves and electrical specifications. It is the
installers responsibility to reference the refriger-
ation drawings supplied for each installation, as
directed by the Engineer of Record.
Proper Field Wiring and Grounding Required!
Failure to follow code could result in death or se-
rious injury. All field wiring MUST be performed
by qualified personnel. Improperly installed and
grounded field wiring poses FIRE and ELECTRO-
CUTION hazards. To avoid these hazards, you
MUST follow requirements for field wiring instal-
lation and grounding as described in NEC and
your local/state electrical codes.
This warning does not mean that Hussmann
products will cause cancer or reproductive harm,
or is in violation of any product-safety standards
or requirements. As clarified by the California
State government, Proposition 65 can be
considered more of a ‘right to know’ law than a
pure product safety law. When used as designed,
Hussmann believes that our products are not
harmful. We provide the Proposition 65 warning
to stay in compliance with California State law. It
is your responsibility to provide accurate
Proposition 65 warning labels to your customers
when necessary. For more information on
Proposition 65, please visit the California State
government website.
August 31, 2018
This equipment is prohibited from use in California
with any refrigerants on the “List of Prohibited
Substances” for that specific end-use, per Cal-
ifornia Code of Regulations, title 17, section
95374.
Use in other locations is limited to refrigerants
permitted by country, state, or local laws and is
the responsibility of the installer/end-user to ensure
only permitted refrigerants are used.
This disclosure statement has been reviewed and
approved by Hussmann and Hussmann attests,
under penalty of perjury, that these statements
are true and accurate.

Proto-Aire EZ I/O Manual
P/N 3090249_E
4
TABLE OF CONTENTS
INSTALLATION .............................................................................................................................................. 5
Overview.......................................................................................................................................................... 5
Shipping Damage ............................................................................................................................................ 5
Apparent Loss or Damage............................................................................................................................... 5
Concealed Loss or Damage ............................................................................................................................. 5
On Site Damage Control.................................................................................................................................. 5
Proto-Aire EZ Unit Nomenclature ................................................................................................................ 6
Moving the Unit ............................................................................................................................................. 7
Physical Drawings and Dimensions (Submittal Documents)............................................................................ 8
REFRIGERATION PIPING ........................................................................................................................ 12
Overview........................................................................................................................................................ 12
Refrigeration Line Piping............................................................................................................................... 12
Return Gas Superheat.................................................................................................................................... 12
Suction Line................................................................................................................................................... 12
Liquid Line.................................................................................................................................................... 13
Refrigeration Cycle ........................................................................................................................................ 13
Oil Cycle ........................................................................................................................................................ 14
ELECTRICAL................................................................................................................................................. 14
Field Wiring................................................................................................................................................... 14
Maximum & Minimum Field Wire Size ................................................................................................... 14
Sizing Wire and Overcurrent Protectors................................................................................................... 14
For 208-230/3/60 Compressor Units with Single Power Feed ................................................................... 14
For 208-230/3/60 Compressor Units with Dual Power Feed..................................................................... 15
For 208-230/1/60 Compressor Units with Single Power Feed .................................................................. 15
For 208-230/1/60 Compressor Units with Dual Power Feed .................................................................... 15
For 460/3/60 Compressor Units with Single Power Feed.......................................................................... 15
For 460/3/60 Compressor Units with Dual Power Feed ........................................................................... 15
Temperature Sensors & Defrost Termination Sensors & Thermostats...................................................... 16
120V GFCI Circuit Operation ................................................................................................................ 16
LED Lighting Operation (if applied) ...................................................................................................... 16
Electronic Oil Level Control .......................................................................................................................... 16
Generic Enclosure Layout ............................................................................................................................. 17
STARTUP
Startup........................................................................................................................................................... 18
Charging the Refrigeration Side..................................................................................................................... 18
Procedure – Triple Evacuation ....................................................................................................................... 19
Pre-charge Check List.................................................................................................................................... 19
Refrigerant Charge ........................................................................................................................................ 19
Oil Charge ..................................................................................................................................................... 20
Compressor Motor Rotation ......................................................................................................................... 20
Final Checks.................................................................................................................................................. 21
Control Settings............................................................................................................................................. 21
Electronic Oil Level Control .......................................................................................................................... 22
Auxiliary Systems .......................................................................................................................................... 22
Temperature Termination (Digital Mode)...................................................................................................... 22
Offtime Defrost.............................................................................................................................................. 23
Sensor Applications ....................................................................................................................................... 23
Suction Pressure Sensor ........................................................................................................................... 23
SERVICE
Service and Maintenance ............................................................................................................................... 24
Compressor Replacement ............................................................................................................................ 24
Replacing Drier.............................................................................................................................................. 25
Checklist........................................................................................................................................................ 26
Sequence of Operation................................................................................................................................... 28
Replacement Parts ......................................................................................................................................... 31
Warranty Information ................................................................................................................................... 32

Proto-Aire EZ I/O Manual
P/N 3090249_E
5
Installation
Overview
This section is limited to the information needed to setup the Proto-Aire EZ Unit.
Shipping Damage
All equipment should be thoroughly examined for shipping damage before and while unloading.
This equipment has been carefully inspected at our factory, and the carrier has assumed
responsibility for safe arrival. If damaged, either apparent or concealed, the claim must be made
to the carrier.
Apparent Loss or Damage
If there is an obvious loss or damage, it must be noted on the freight bill or receipt and signed
by the carrier’s agent; otherwise, carrier may refuse claim. The carrier will supply the necessary
claim forms.
Concealed Loss or Damage
When loss or damage is not apparent until after equipment is uncrated, a claim for concealed
damage is made. Upon discovering damage, make request in writing to carrier for inspection
within 15 days and retain all packing. The carrier will supply inspection report and required
claim forms.
On Site Damage Control
The Proto-Aire EZ Unit is shipped on skids with panels installed. Remove panels to access lifting
points on frame. Do not attempt to move the unit from the skids without rst removing the
panels.

Proto-Aire EZ I/O Manual
P/N 3090249_E
6
Proto-Aire EZ UNIT NOMENCLATURE
The model numbers for Proto-Aire EZ units are shown on the legend in modular
form. The nomenclature is interpreted as follows:
The unit nomenclature is part of the UL code requirements and must
be included on the legend as well as the data plate for each unit.
MR O Z 3 21 M T K
Voltage K = 208/3/60; D = 208/1/60
M = 460/3/60
M = Medium Temp. L = Low Temp.
D = Dual (Split Suction Temp.)
Sum of Compressor Horse Power
Total Number of Compressors
Z = Scroll
O = Outdoor
MR = Proto-Aire EZ
Refrigerant: F = 407F; Q = 407A;
R = 449A; S = 404A; T = 448A

Proto-Aire EZ I/O Manual
P/N 3090249_E
7
MOVING THE UNIT
It is the responsibility of the installer to ensure that the nal equipment installation meets all
applicable code requirements. Illustrations shown on the next pages are only for general representation.
Actual product will vary depending on application. Be sure that lifting cables/straps do not damage
piping stubs, coil surface, orventilation shroud. Full perimeter support foundation required.
N.E.C. and local electrical code restrictions must be followed for electrical clearances and all
other installation requirements.
50
57
119 MIN
90.5
A
DETAIL A
4X
ATTACH
LIFTING
SHACKLES
HERE.
119" MIN
SPREADER BARS
130" MIN
APPROX OVER ALL DIMENSION OF THE UNIT: 140.0" L X 61.2" W X 50.0" H.
COMPRESSORS: MAX 4 SCROLL COMPRESSORS.
WEIGHT DETAILS-
3 COMPRESSOR UNIT: 2437 SHIPPING WEIGHT / 2505 OPERATING WEIGHT.
4 COMPRESSOR UNIT: 2637 SHIPPING WEIGHT / 2737 OPERATING WEIGHT.
TYPE OF LIQUID DRIER: SEALED / REPLACEABLE CORE.
TYPE OF SUCTION FILTER : SEALED / REPLACEABLE CORE.
119" MIN
SPREADER BARS
130" MIN
APPROX OVER ALL DIMENSION OF THE UNIT: 140.0" L X 61.2" W X 50.0" H.
COMPRESSORS: MAX 4 SCROLL COMPRESSORS.
WEIGHT DETAILS-
3 COMPRESSOR UNIT: 2437 SHIPPING WEIGHT / 2505 OPERATING WEIGHT.
4 COMPRESSOR UNIT: 2637 SHIPPING WEIGHT / 2737 OPERATING WEIGHT.
TYPE OF LIQUID DRIER: SEALED / REPLACEABLE CORE.
TYPE OF SUCTION FILTER : SEALED / REPLACEABLE CORE.
121" MIN

Proto-Aire EZ I/O Manual
P/N 3090249_E
8
57 60
AIR INTAKE
AIR DISCHARGE
CONDENSER
SUCTION FILTERS
OPTIONAL VERTICAL
ORIENTATION IS
AVAILABLE
LIQUID DRIER
OPTIONAL VERTICAL
ORIENTATION IS
AVAILABLE
SCROLL COMPRESSORS
OIL SEPARATOR
CONTROL PANEL
OIL FILTER
OIL MANIFOLD
61.15
49.85
57.00
HINGED
TOP
COVERS
33"
OUTER SPLIT
HINGED
EXTERIOR
DOORS
Small Unit Large Unit
Approximate Operating Weight (lbs.) 2180 2737
Shipping Weight 2080 2637
Refrigerant R448A/R449A/407A/407F/404A
Unit Charge (Summer) lbs 2 Row – 8; 5 Row – 15; 6 Row – 22 LAHB13412/10 – 15.4; LAHB13310 – 12.1
Unit Charge (Winter) 2 Row – 24; 5 Row – 56; 6 Row – 82 LAHB13412/10 – 61.6; LAHB13310 –
R448A/R449A/407A/407F/404A
45.4
Receiver Capacity at 80% 98 98
MINIMUM CLEARANCE REQUIREMENTS:
Provide clearances as shown on Pages 8 and 9 to ensure adequate airow, reduce the potential
for air recirculation, facilitate service accessibility, and to maintain compliance with electrical
code requirements. It is the responsibility of the installer to ensure that the nal equipment
installation meets all applicable code requirements. Suggested rigging setup is illustrated. Be sure
that lifting cables/straps do not damage piping stubs, coil surface, or rain guard. Full perimeter
support under unit rail foundation required.
Proto-Aire EZ — Physical Data

Proto-Aire EZ I/O Manual
P/N 3090249_E
9
48" MIN
48" MIN
48" MIN
54" MIN
EXTERIOR
HINGED
RH DOOR
CONTROL
PANEL
ACCESS
DOOR
EXTERIOR
HINGED
LH DOOR
14.0
2X
HEAT RCLM LINES
7.0
LIQ LINE
10.0
SUCT LINE 2
10.5
SUCT LINE 1
11.0
SUCT LINE 2
16.5
LIQ LINE
18.0
SUCT LINE 1
9.0
FROM
HEAT RCLM
15.5
TO
HEAT RCLM
Proto-Aire EZ — Stub Out Locations

Proto-Aire EZ I/O Manual
P/N 3090249_E
10
FRONT VIEW
REAR VIEW
TEMP SENSOR IS
FASTENED TO THE VERT
SUPPORT ON THE COND
SIDE WITH THE HELP OF
SELF TAPPING SCREW
#0700900.
REAR GRILLE IS
OPTIONAL SHOWN
HERE FOR
REFERENCE.
0427001
BRACKET-AMB
TEMP SENSOR
LARGE PTD SKIN
REAR VIEW
133.75
50.01
57.00
134.00
41.03
AMBIENT TEMP SENSOR MOUNTING.
REAR GRILLE IS
OPTIONAL
SHOWN HERE
FOR
REFERENCE.
55.00
3.98
61.15 55.25
LARGE PTD SKIN
NOTE
Dimensions shown in inches.

Proto-Aire EZ I/O Manual
P/N 3090249_E
11
SMALL PTD SKIN
106.25
55.00
57.00
61.15
50.01
55.25
3.98
REAR VIEW
41.03
AMBIENT TEMP SENSOR MOUNTING.
REAR GRILLE IS
OPTIONAL
SHOWN HERE
FOR
REFERENCE.
FRONT VIEW
REAR VIEW
TEMP SENSOR IS
FASTENED TO THE
VERTICAL SUPPORT ON
THE COND SIDE WITH THE
HELP OF
SELF TAPPING SCREW
#0700900.
REAR GRILLE IS
OPTIONAL
SHOWN HERE
FOR
REFERENCE.
0427001
BRACKET-
AMB TEMP
SENSOR
SMALL PTD SKIN
NOTE
Dimensions shown in inches.

Proto-Aire EZ I/O Manual
P/N 3090249_E
12
REFRIGERATION PIPING
Important: Since Hussmann has no direct control over the installation, providing
freeze-burst protection is the responsibility of the installing contractor.
Always use a pressure regulator with a nitrogen tank. Do not exceed 2 psig and vent lines
when brazing. Do not exceed 350 psig for leak testing high side. Do not exceed 150 psig for leak
testing low side.
Always recapture test charge in approved recovery vessel for recycling.
Overview
This section details the major refrigeration components and their locations in each piping
system.
Refrigeration Line Piping
Use only clean, dehydrated, sealed refrigeration grade copper tubing. Use dry nitrogen in the
tubing during brazing to prevent the formation of copper oxide. All joints should be made with
silver alloy brazing material, and use 35% silver solder for dissimilar metals.
Liquid and suction lines must be free to expand and contract independently of each other.
Do not clamp or solder them together. Run supports must allow tubing to expand and contract
freely. Do not exceed 100 feet without a change of direction or an offset. Plan proper pitching,
expansion allowance, and P-traps at the base of all suction risers. Use long radius elbows to
reduce ow resistance and breakage. Avoid completely the use of 45° elbows. Install service
valves at several locations for ease of maintenance and reduction of service costs. These must be
UL approved for 450 psig minimum working pressure.
Return Gas Superheat
Return gas superheat should be 20 to 30 °F on all units.
Suction Line
1. Install a downward slope in direction of ow. A P-trap is required for all vertical risers.
2. Line may be reduced by one size after rst third of case load and again after the second
third.
3. Suction returns from evaporators must enter at the top of the line.
4. A minimum pitch of 1/2” per 10 feet of horizontal run should be used.
5. To facilitate proper oil return from, a suction branch should enter the main suction
return on the top of the main suction return.

Proto-Aire EZ I/O Manual
P/N 3090249_E
13
Liquid Line
Take-offs to evaporators must exit the bottom of the liquid line.
Refrigeration Cycle
Beginning with Compressors, refrigerant vapor is compressed into the Discharge Header.
The oil separator effectively divides the refrigerant from the lubricant in the system. The
lubricant is then returned to the compressors. The Condenser dissipates the unwanted heat from
the refrigerant into an air-cooled condenser.
The receiver acts as a vapor trap and supplies the Liquid Line with quality liquid refrigerant.
A Liquid Line Filter/Drier removes water and other contaminants from the refrigerant.
The liquid branch line supplies liquid refrigerant to the Thermostatic Expansion Valve (TXV),
which in turn feed refrigerant to the cases (evaporator coils). These coils pick up heat from the
product stored in the cases. A Suction Filter removes system contaminants from return vapor,
which is factory supplied but eld installed. It is also a good idea to install isolation valves for
ease of service.
The mechanical ORI valve (Open on Rise of Inlet pressure) should be set to start opening at
70°F equivalent pressure from T/P chart. This will allow bypass after fans have been cycled off.
To set the valve, install pressure gauge on the inlet tap of the valve and articially lower the
pressure to when the valve starts to open. The valve comes factory set from Sporlan to open at
120 psi. For initial start-up, turning the adjustment screw IN approximately * turns should give a
starting point and make it easier to verify proper operation.
*ORI-6 = 1 turn = 27 lbs
*ORI-10 = 1 turn = 17 lbs
70° F equivalent pressure = (X) turns + 120 psi
The mechanical bypass CRO valve (Close on Rise of Outlet pressure) should be set to start
closing at 2 psi above the low temperature satellite compressor suction pressure set-point. This
will prevent the low temperature satellite compressor from short cycling. The valve comes
factory set from Sporlan to close at 15 psi. For initial start-up, turn the adjustment screw either
clockwise to increase the setting or counterclockwise to decrease the setting approximately *
turns. The valve has an adjustment range of 0 to 20 psi.
*CRO-4= 1 turn = 3.3 psi

Proto-Aire EZ I/O Manual
P/N 3090249_E
14
Electrical
Field Wiring
Maximum & Minimum Field Wire Size
Field wire size is based on the total load amperes, the largest connectable wire sizes for the
terminals. (Wire size is based on the serial plate minimum circuit ampacity.) Refer to National
Electric Code for correction and adjustment factors.
Sizing Wire and Overcurrent Protectors
Check the legend for Minimum Circuit Ampacity (MCA), Maximum Overcurrent Protective
Devices (MOPD), and total RLAs. Follow NEC guidelines.
Branch Circuit(s) must be built to the unit using information supplied on the unit data plate
for Minimum Current Ampacities (MCA) and Maximum Over Current Protective Device(s)
(MOPD).
Proto-Aire EZ components are wired as completely as possible at the factory with all work
completed in accordance with the National Electrical Code. All deviations required by governing
electrical codes will be the responsibility of the installer.
For 208-230/3/60 Compressor Units with Single Power Feed:
To each Proto-Aire EZ provide:
• One 208-230/3/60 branch circuit (neutral wire also required if low
ambient receiver heater utilized)
• One 120/1/60 dedicated GFI circuit if convenience receptacle is applied.
• One ground wire to earth ground
Oil Cycle
Discharge refrigerant carries droplets of oil from the compressor’s outlet. The Oil Separator
separates the oil from the refrigerant. The oil is stored in the Oil Separator until needed. The oil
returns to the system through the high-pressure line and oil lter.
The oil lter removes impurities from the oil. The high-pressure oil is distributed to the electronic
oil level control, which feeds oil into the compressor through a solenoid valve.
Electronic oil regulators monitor oil levels. The units are powered by a 208V power supply.
When the oil level in the compressor drops below ½ sightglass, the ll light comes on, and the oil
solenoid is energized. If after 90 seconds the oil level does not rise above ½ sightglass, the unit
opens the compressor control circuit. If oil becomes available, the electronic oil level control will
automatically re-set and the compressor will resume operation.

Proto-Aire EZ I/O Manual
P/N 3090249_E
15
For 208-230/3/60 Compressor Units with Dual Power Feed:
To each Proto-Aire EZ provide:
• One 208-230/3/60 branch circuit
• One ground wire to earth ground
• One 208-230/1/60 branch circuit (neutral wire also required if low ambient receiver
heater applied)
• One ground wire to earth ground
• One 120/1/60 dedicated GFI circuit if convenience receptacle is applied.
For 208-230/1/60 Compressor Units with Single Power Feed:
To each Proto-Aire EZ provide:
• One 208-230/1/60 Circuit (neutral wire also required if low ambient receiver heater applied)
• One ground wire to earth ground
• One 120/1/60 dedicated GFI circuit if convenience receptacle is applied.
For 208-230/1/60 Compressor Units with Dual Power Feed:
To each Proto-Aire EZ provide:
• One 208-230/1/60 Circuit (neutral wire also required if low ambient receiver heater
applied)
• One ground wire to earth ground
• One 208-230/1/60 branch circuit (neutral wire also required if low ambient receiver
heater applied)
• One ground wire to earth ground
• One 120/1/60 dedicated GFI circuit if convenience receptacle is applied.
For 460/3/60 Compressor Units with Single Power Feed:
To each Proto-Aire EZ provide:
• One 460/3/60 Circuit (neutral wire also required if low ambient receiver heater applied)
• One ground wire to earth ground
• One 120/1/60 dedicated GFI circuit if convenience receptacle is applied.
• If a eld installed single point transformer is applied, then additional wiring to and from
the transformer is required as required by application.
For 460/3/60 Compressor Units with Dual Power Feed:
To each Proto-Aire EZ provide:
• One 460/3/60 Circuit (neutral wire also required if low ambient receiver heater
applied)
• One ground wire to earth ground
• One 208-230/1/60 or 208-230/3/60 branch circuit as required by application
(neutral wire also required if low ambient receiver heater applied)
• One ground wire to earth ground
• One 120/1/60 dedicated GFI circuit if convenience receptacle is applied.

Proto-Aire EZ I/O Manual
P/N 3090249_E
16
120V GFCI Circuit Operation
The Proto-Aire EZ may include an optional GFCI convenience receptacle eld wired from
dedicated circuit. This circuit will be energized even when unit power is disconnected.
LED Lighting Operation (if applied)
The Proto-Aire EZ may include LED lighting within the electrical enclosure and within the unit.
The lighting is controlled via a toggle switch within the electrical enclosure. The lighting will not
function if power is removed from unit.
Electronic Oil Level Control
Standard oil level control is powered by 208V with matching control voltage. Wired to general
compressor alarm circuit or detected by a compressor proof alarm.
Important:
Shielded cable must be used. The shield wire must be attached to the panel liner that
contains the control board it is terminating to.
Temperature Sensors & Defrost Termination Sensors & Thermostats
Use a shielded and grounded Belden Cable #8762, or equivalent between control panel and case
sensors or thermostats.

Proto-Aire EZ I/O Manual
P/N 3090249_E
17
Generic Enclosure Layout
The below electrical enclosure layout is a generic layout that shows names
and locations of components within on the enclosure. The layout represents
a 208VAC/3/60Hz, 10kA SCCR, 3-compressor unit with a through the door
disconnect installed. As the product is congurable, the layout below will not
be representative of any one specic unit and should only be used as a generic
example.
More components maybe located on an additional liner on the door to the
electrical enclosure. These components will be specic to the controller and control
system selected for the individual units.

Proto-Aire EZ I/O Manual
P/N 3090249_E
18
Startup
Charging the Refrigeration Side
Leak Testing
Visually inspect all lines and joints for proper piping practices.
Open Power Supply
Compressors – Open circuit breakers to all compressors.
Isolate
Compressors – Front seat service valves on suction and discharge.
Pressure Transducers – Close angle valves
Liquid Injection Valves – Close Valves
Open
Valves, Receiver.
Verify
Refrigerant requirements for system, compressors, and TXV’s in merchandisers and coolers.
Electrical supply and component requirements.
Test Charge
Using properly regulated dry nitrogen and refrigerant mixture, pressurize the system with vapor
only. Bring the system pressure up to 150 psig. Use an electronic leak detector to inspect all
connections. If a leak is found, isolate, repair, and retest. Be sure system is a 150 psig and all
valves closed to repair the leak are re-opened. After the last leak is repaired and retested, the
system must stand unaltered for at least 12 hours with no pressure drop from 150 psig.
Evacuation
Nitrogen and moisture will remain in the system unless proper evacuation procedures are
followed. Nitrogen left in the system may cause excessive head pressure. Moisture causes TXV ice
blockage, wax build up, acid, oil, and sludge formation.
Do not simply purge the system because this procedure is illegal, expensive, harmful to the
environment, and may leave moisture and nitrogen. Do not run the compressor to evacuate
because this procedure introduces moisture into the compressors crankcase oil and does
not produce adequate vacuum to remove moisture from the rest of the system at normal
temperatures.
Setup
Using an 8 CFM or larger vacuum pump, connect to the access port on both the suction header
and liquid supply line of the Proto-Aire EZ Unit. Connect one micron vacuum gauge at the
pump, and one at the furthest point in the system from the compressor. Plan procedures so
breaking the vacuum with refrigerant will not introduce contaminates into the system. The
vacuum pump must be in good condition and lled with fresh oil to achieve desired results.

Proto-Aire EZ I/O Manual
P/N 3090249_E
19
Procedure – Triple Evacuation
Pull a vacuum to 1500 microns. If the vacuum fails to hold, determine the cause and correct.
Begin again and pull a vacuum to 1500 microns.
Break the vacuum with refrigerant vapor to a pressure of about 2 psig. Do not exceed the micron
gauge transducer’s maximum pressure surge to the transducer of the micron gauge.
Pull a second vacuum to 1500 microns.
Break the vacuum with refrigerant vapor to a pressure of about 2 psig. Prior to charging the
system, packing from all lter / drier shells should be removed if a sealed lter or drier is not
provided. Proper suction lters and liquid drier cores should be installed when applicable.
Pull a third vacuum to 500 microns. Close vacuum header valves and allow system to stand for
a minimum of 12 hours. If the 500 micron vacuum holds, charging may begin. If not, the cause
must be determined and corrected. Repeat the entire evacuation procedure from the rst step.
Pre-charge Check List
During any of the pull downs, check:
Merchandisers
Electrical requirements and power supply
Electrical connections tight and clean
Proper fan operation
Thermostat setting
Walk-in Coolers and Freezers
Electrical requirements and power supply
Electrical connections tight and clean
Proper fan operation
Thermostat setting
NOTES:
Refrigerant Charge
• Remember the condenser in the Proto-Aire EZ holds only a small amount of refrigerant. It is
therefore very easy to overcharge the Proto-Aire EZ unless care is taken during the charging
process.
• Charging until the liquid sight glass is clear of bubbles will often overcharge the system causing
head pressure alarms. However, if the condenser has a subcooling circuit there should be a solid
liquid sight glass the majority of the time.
• The initial / refrigerant charge should be through the liquid side of the system to prevent
liquid ood back to the compressors.

Proto-Aire EZ I/O Manual
P/N 3090249_E
20
Because the HFC refrigerants are less dense than the refrigerants they replace, they will tend to
“ash” or bubble more easily, even when the correct charge is in the system.
Oil Charge
Charge the oil separator with oil.
Use only Mobil EAL Arctic 22 CC, ICI Emkarate RL 32 CF, or Copeland Ultra 22 CC
Oil separator is shipped without oil charge.
Oil Levels
Compressor − top half of the sight glass
Oil separator − between the two sight glasses
Important Notice to the Installer
The compressors and oil separator must be closely monitored during startup, because the POE
oil does not return from the evaporators as quickly as mineral oil
Compressor Motor Rotation
To check compressor rotation on three phase units, use the following procedure:
1. Install gauges on suction and main discharge line. A momentary compressor run should
cause a drop in suction pressure and a rise in discharge pressure.
2. Switch OFF all breakers in the control panel EXCEPT the control circuit breaker.
3. Turn ON main power switch.
4. Look for the green light on the single-phase protector. If the light is red, turn OFF the
main power switch. All Proto-Aire EZ 3-phase wiring is connected L1 to T1, L2 to T2,
and L3 to T3. Have the eld connections corrected so the phase protector indicates phase
alignment. (The light is green.)
5. Installing contractor should re-check condenser fan rotation.
6. Turn ON main power switch.
7. Turn all compressors ON using the electronic controller.
Table of contents
Languages:
Popular Power Distribution Unit manuals by other brands
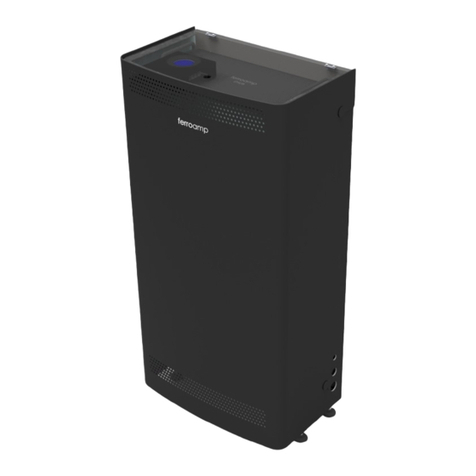
ferroamp
ferroamp EnergyHub XL Single 21 kW installation manual
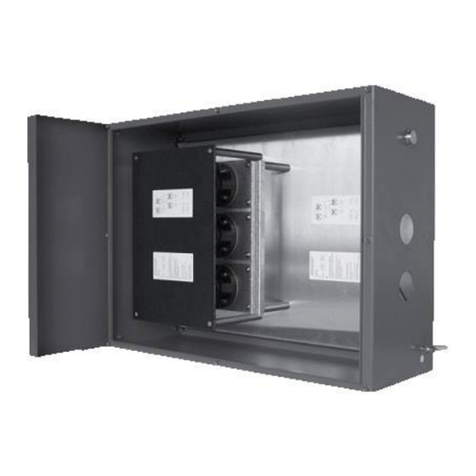
Bartec
Bartec 07-5184 Series Operational Instruction

DVIGear
DVIGear DVI-7520-PDU quick start guide
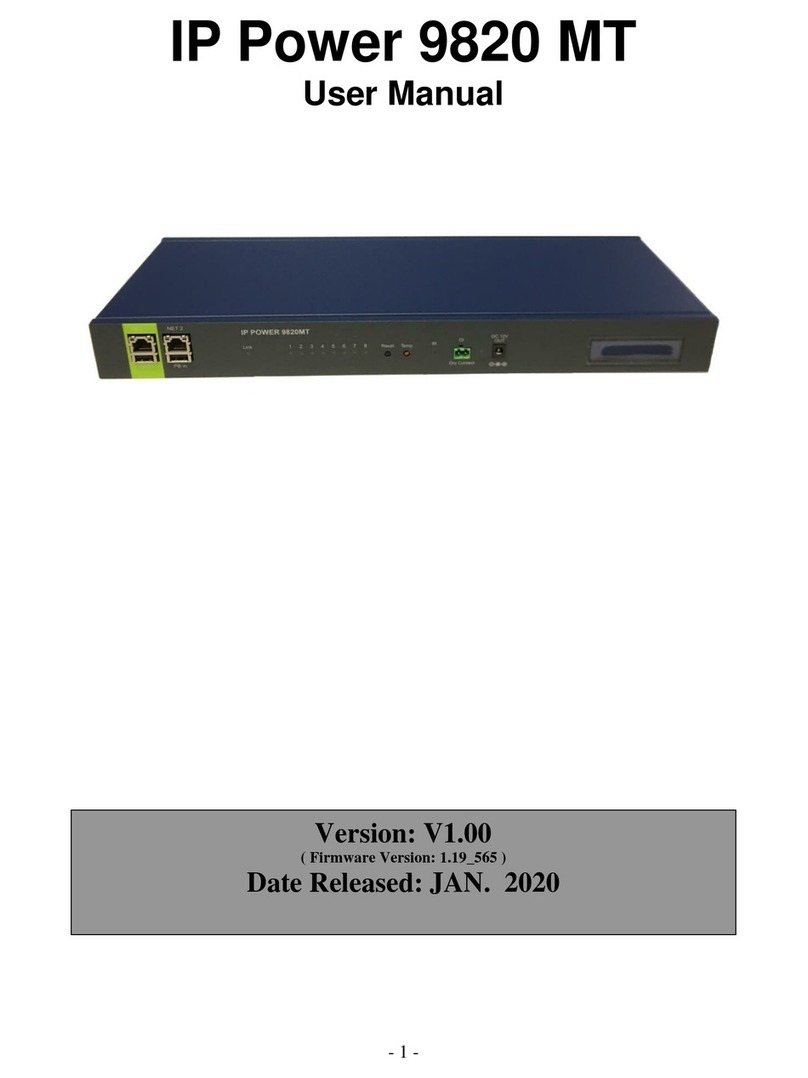
IP Power
IP Power 9820 MT Series user manual

Belkin
Belkin P74978UKAP21000UK3M user manual
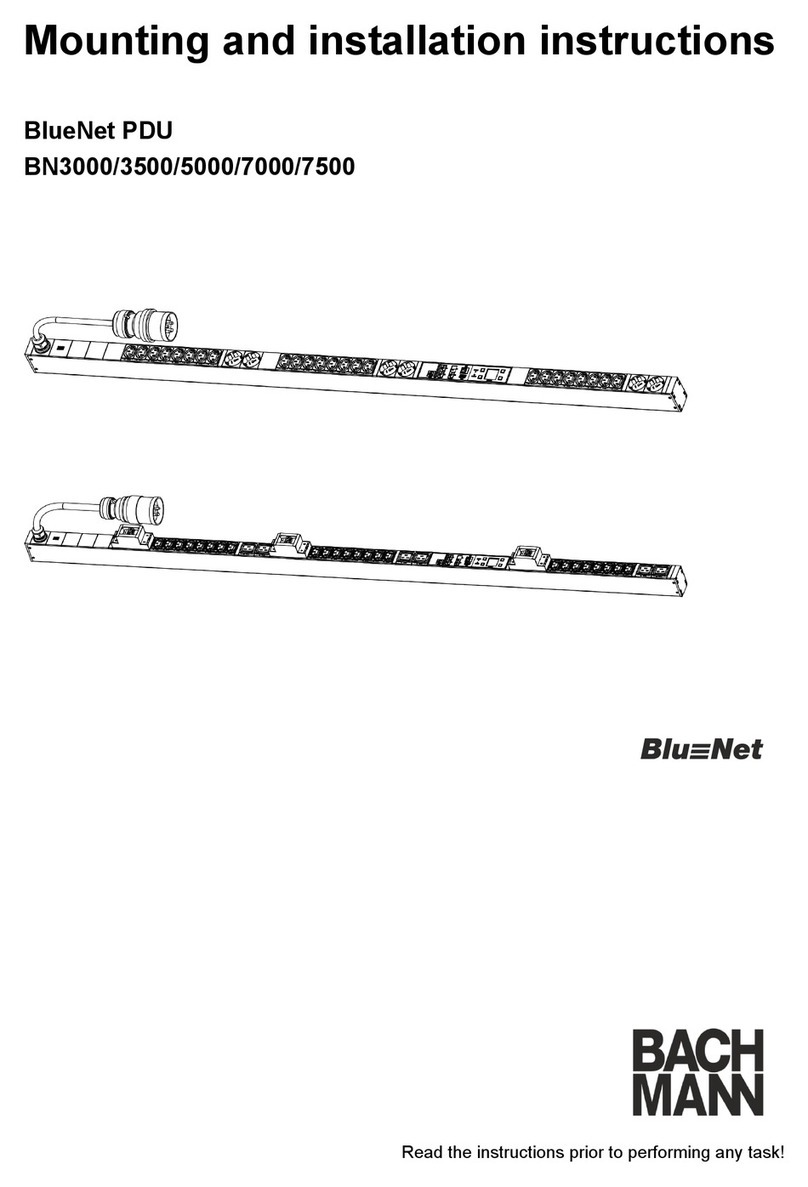
Bachmann
Bachmann BlueNet BN3000 Mounting and installation instructions
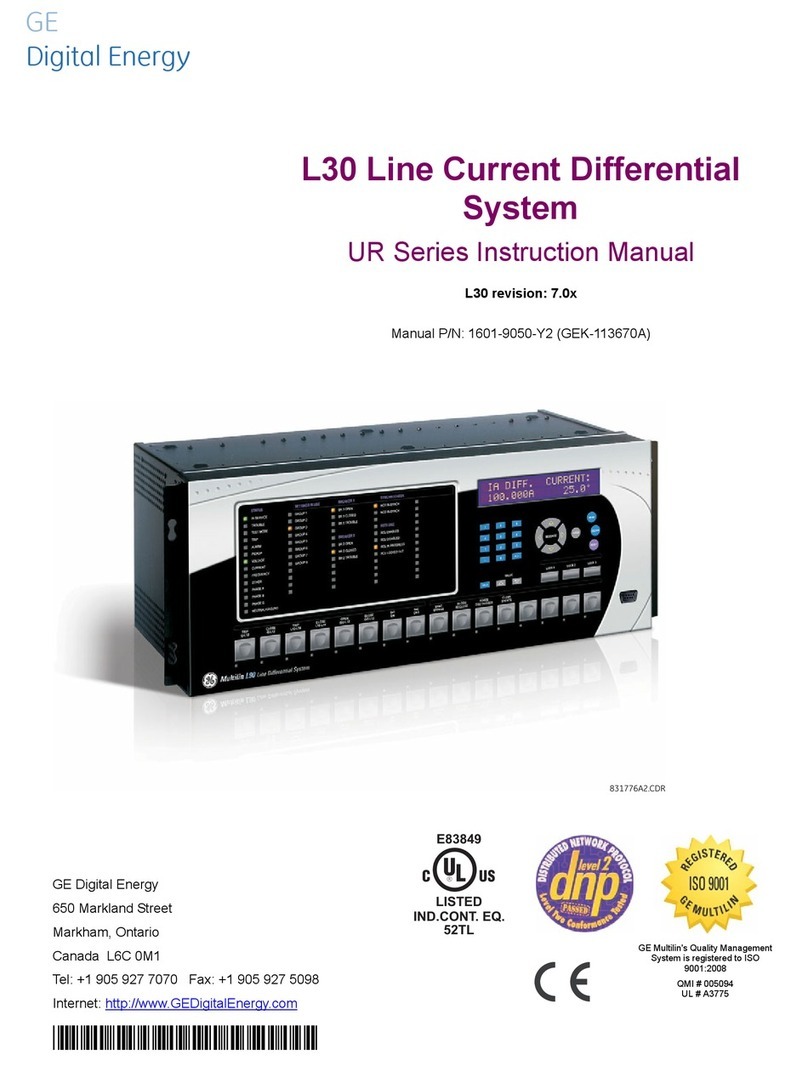
GE Digital Energy
GE Digital Energy L30 instruction manual
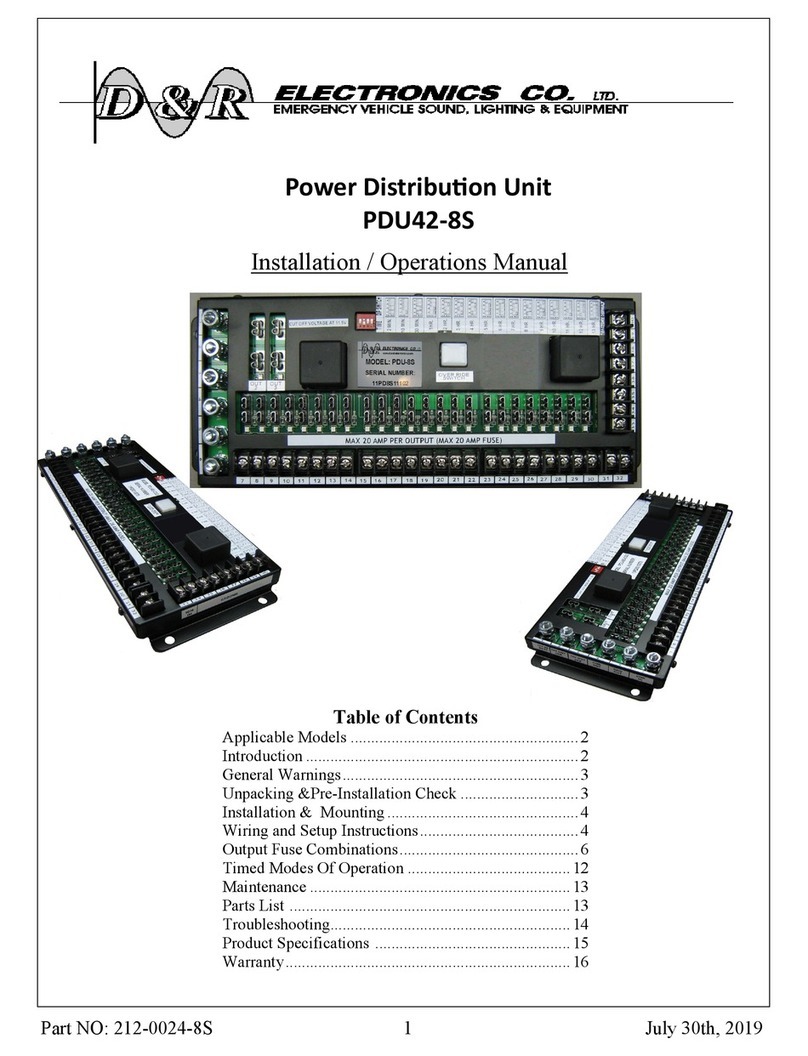
D&R ELECTRONICS
D&R ELECTRONICS PDU42-8S Installation & operation manual
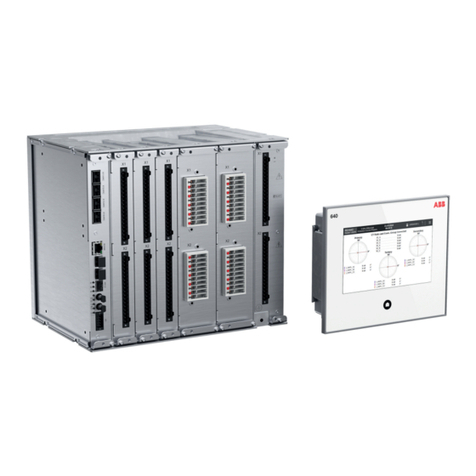
ABB
ABB RELION REX640 Engineering manual
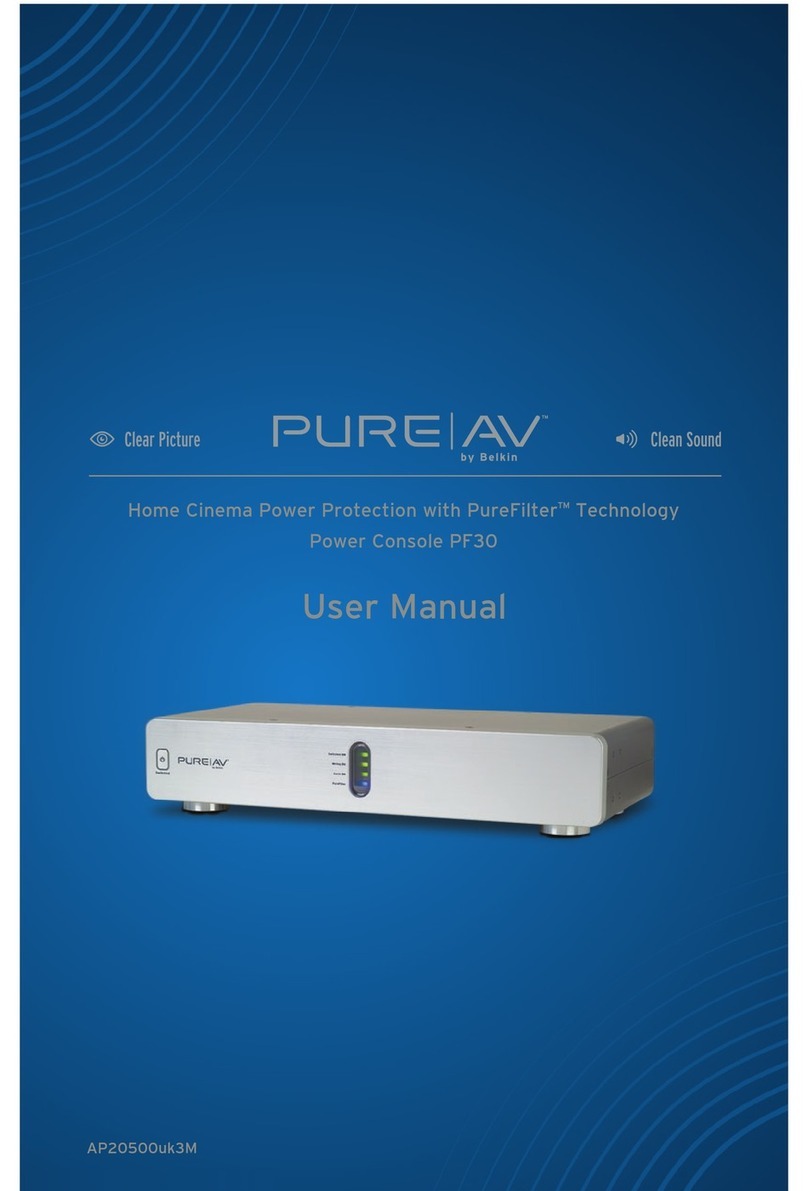
Belkin
Belkin P74977UKAP20500UK3M user manual

Avocent
Avocent Cyclades PM3000 brochure
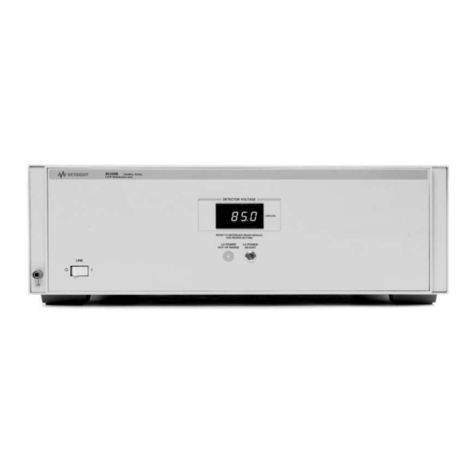
Keysight Technologies
Keysight Technologies 85309B LO/IF User's and service guide