iBOTZ TRIBOTZ MR-1005 User manual

iBOTZ Division
Instruments Direct Ltd.
Unit 14, Worton Court
Worton Road
Isleworth TW7 5ER
UK
iBOTZ Division
Instruments Direct Ltd.
10 Brent Drive
Hudson, MA 01749
USA
UKVER2
TRIBOTZ
Build your own robot
Model No: MR-1005
Manufactured by iBOTZ Div of Instruments Direct Ltd.
The Open University is based at Milton Keynes in the UK

1
Read this manual carefully before getting started on your robot. Ask
someone to help you read the instructions. Keep this manual for future
reference.
?Take care when using sharp tools such as, knives or screwdrivers.
?Keep the robotic parts away from small children. Don’t assemble
the robot where small children can reach it.
?Keep fingers out of the working parts such as the motors and gears.
?Do not force the robot to move/stop; this could cause the motors to
overheat.
?The Specification and anything contained within this manual are
subject to change without notice.
?When using batteries:
-Use the batteries in the correct polarity (+ -)
-Never short circuit, disassemble, heat, or dispose of batteries in a
fire.
-When the robot is not in use the batteries should be removed.
-If the batteries or robot become wet, remove the batteries from the
hold and dry the robot.
-Do not mix old and new batteries. Do not mix alkaline, standard
(carbon-zinc) or rechargeable (nickel-cadmium) batteries. We
recommend the use of alkaline batteries for extended life.
READ BEFORE PROCEEDING
2
Product Information
Tribotz
Model:MR-1005
About Tribotz
This robot reacts to sound impulses and walks for a few seconds and
then automatically stops. Tribotz will also follow a black line and avoid
dark coloured obstacles
Specification
Powervoltage: DC 3V (AA Battery x 2pcs and 9V x 1pc)
Height 110mm
Length 145mm
Width 150mm
TRIBOTZ MR-1005 robot

3
This iBOTZ kit is an ideal introduction for someone wanting to investigate the fascinating
world of robots and intelligent machines.
The kit introduces the fundamentals of sensor technology and shows how sensors, electronic
circuit boards, and motors can be combined with carefully designed mechanical gears and
shafts to produce a robot that walks and avoids obstacles.
Clap you hand and watch TRIBOTZ move away. Draw a black line on a white sheet of paper
and watch it follow along. Put some obstacles in front of TRIBOTZ and see it steer around
them. How does it do all that?
By reading this manual you will find out what the components in your iBOTZ HYDRAZOID
do, and how they work together to generate its behavior. In the process you will be introduced
to some basic electronics and aspects of engineering design.
We have iBOTZ robots in our laboratory at the Open University, and they are always a big hit
with visitors. When you have built and experimented with yours, you will be ready to move
on towards the more advanced robots that are used for research. Have fun!
Professor Jeffrey Johnson
Department of Design & Innovation
The Open University
http://technology.open.ac.uk
4
History of Robots
Definition of a Robot
According to The Robot Institute of America (1979) :
"A reprogrammable, multifunctional manipulator designed to move materials, parts, tools, or
specialized devices through various programmed motions for the performance of a variety of
tasks." According to the Webster dictionary: "An automatic device that performs functions
normally ascribed to humans or a machine in the form of a human (Webster, 1993)."
A brief review of robot development is important as it puts the current machines and interest
in them into an historical perspective. The following list highlights the growth of automated
machines that led to the development of the industrial robots currently available today.
250BC
One of the first robots was the clepsydra or water clock, which was made in 250 B.C. It was
created by Ctesibius of Alexandria, a Greek physicist and inventor.
1801
Joseph Jacquard invents a textile machine that is operated by punch cards. The machine is
called a programmable loom and goes into mass production.
1830
American Christopher Spencer designs a cam-operated lathe.
1892
In the United States, Seward Babbitt designs a motorised crane with gripper to remove ingots
from a furnace.
1921
The first reference to the word robot appears in a play opening in London. The play, written by
Czechoslovakian Karel Capek, introduces the word robot from the Czech robota, which means
a serf or one in subservient labour. From this beginning the concept of a robot takes hold.
1938
Americans Willard Pollard and Harold Roselund design a programmable paint-spraying
mechanism for the DeVilbiss Company.
1948

5
Norbert Wiener, a professor at M.I.T., publishes Cybernetics, a book which describes the
concept of communications and control in electronic, mechanical, and biological systems.
1954
After the invention of the transistor in 1948, many robots were used in conjunction with the
computer. The first patent for a computer controlled industrial robot was developed in 1954 by
George Devol. Devol created a computerized memory and control system called "universal
automation." Devol co-founded the Unimation industrial robot company, and "started the
industrial robot revolution" by selling designs of powerful assembly line arms to General
Motors.
1959
Planet Corporation markets the first commercially available robot.
1960
Unimation is purchased by Condec Corporation and development of Unimate Robot Systems
begins. American Machine and Foundry, later known as AMF Corporation, markets a robot,
1962
General Motors installs the first industrial robot on a production line.
1968
Stanford Research Institute at Palo Alto, California (SRI) builds and tests a mobile robot with
vision capability, called Shakey. It was a small unstable box on wheels that used memory and
logical reasoning to solve problems and navigate in its environment. Besides moving
between rooms and avoiding objects, Shakey II was able to stack wooden blocks according to
spoken instructions. It looked to see if the blocks were properly aligned, and if not, it adjusted
the stack. Shakey was once asked to push a box off a platform, but could not reach the box.
The robot found a rasmp, pushed the ramp against the platform, rolled up the ramp, and then
pushed the box onto the floor
1970
At Stanford University a robot arm is developed which becomes a standard for research
projects. The arm is electrically powered and becomes known as the Stanford Arm.
1973
The first commercially available minicomputer-controlled industrial robot is developed by
Richard Hohn for Cincinnati Milacron Corporation. The robot is called the T3, “The
Tomorrow Tool”.
1974
Professor Scheinman, the developer of the Stanford Arm, forms Vicarm Inc. to market a
6
version of the arm for industrial applications. The new arm is controlled by a minicomputer.
1976
Robot arms are used on Viking 1 and 2 space probes Vicarm Inc. incorporates a
microcomputer into the Vicarm design.
1977
ASEA, a European robot company, offers two sizes of electric powered industrial robots. Both
robots usea microcomputer controller for programming and operation. In the same year
Unimation purchases Vicarm Inc.
1978
The Puma (Programmable Universal Machine for Assembly) robot is developed by Unimation
from Vicarm techniques and with support from General Motors.
1980
The robot industry starts its rapid growth, with a new robot or company entering the market
every month.
A brief overview
The parts of many modern robots can be generalized into four categories: the base, object
manipulator, primary control system, and sensory system. The base is usually a metal or
plastic frame that supports the robot's components. Most industrial robot bases are stationary,
although the arms move about. Other bases move about by treads, wheels, or legs. Wheel
driven bases have various configurations. Some have two big rear wheels, and a small front
balancing wheel, while others have four equally sized wheels.
The second part of the modern robot is the object manipulator. Basic grasping and
manipulation requires a large amount of memory, due to the requirements of smoothness and
sensitivity during operation . The minimum number of fingers necessary to grasp an object,
hold it securely, and manipulate it smoothly was found to be three.
The third part of the modern robot is the control system. Primary systems include the remote
control, driver circuit, or computer. Quite often, the control system consists of a primary
control and secondary, application-specific controls. The primary control executes the main
program, calling individual functions or reading resultant data, while the secondary control
systems determine how those functions are processed.

7
The final part of the modern robot is the sensory system. The sense of touch is used for object
recognition or collision avoidance. For example, a robot hand, equipped with a rubber skin of
microswitches, can recognize objects such as screws, pins, and washers.
When, in 1954 George C. Devol filed a U.S. patent for a programmable method for
transferring articles between different parts of a factory, he wrote:
"The present invention makes available for the first time a more or less general purpose
machine that has universal application to a vast diversity of applications where cyclic control
is desired."
In 1956 Devol met Joseph F. Engelberger, a young engineer in the aerospace industry. With
others, they set up the world's first robot company, Unimation, Inc., and built their first
machine in 1958. Their initiative was a great deal ahead of its time; according to Engelberger,
Unimation did not show a profit until 1975.
The first industrial robot saw service in 1962 in a car factory run by General Motors in
Trenton, New Jersey. The robot lifted hot pieces of metal from a die-casting machine and
stacked them.
Japan, by comparison, imported its first industrial robot from AMF in 1967, at which time the
United States was a good 10 years ahead in robotics technology. By 1990, there were more
than 40 Japanese companies that were producing commercial robots. By comparison, there
were approximately one dozen U.S. firms, led by Cincinnati Milacron and Westinghouse's
Unimation.
The Future of Robots
Robots and the robotics industry will continue to grow at a rapid rate. As technology advances
so will the robots that rely so heavily upon these advances. Robots will become more technical
until one day they will become as powerful as we are.

8
Long-nose pliers Cutting pliers
Tools needed for assembly
Hammer
Used for
installing
gears
-Screwdriver+ Screwdriver
Helpful Hints prior to assembly
Removing parts from plastic frame, simply twist the plastic parts away from the frame or use
some cutting pliers, being careful not to snap any of the fragile parts.
Tapping screws
Tapping screws make threads like screws do in wood. The best way to screw a tapping screw is
to screw in a couple of turns and then unscrew half a turn, repeat this until the screw is in flush
to the surface.
Tightening of nuts and screws
Make sure nuts are tightened securely to the bolts; if not they may work loose and cause the
robot to malfunction. Also make sure the nuts are not too tight and cause the parts to function
incorrectly.
Screw sizing
The size of the screws is expressed by the thickness and length. A screw marked M3x10 is 3mm
thick and 10mm long. Nuts are measured in a similar way corresponding to the size of the
screw. A M3 nut is used on an M3bolt/screw.
9
Motor and gearbox
(3V) Tapping Screws
Screw A Ø 2.6x6 PB 9pcs 2pcs
Screw B Ø 2.8x8 PB 6pcs 2pcs
2 pcs
Partslist

10
Tire set
Tire
Tire
Plastic Parts Set
Battery
cover
Gear box
holder
Dome
Bottom case
CASTOR
CASTOR STOPPER
CASTOR TIRE
Castor SET
FRONT
APRON
REAR
APRON
WHEEL
GEAR BOX
HOLDER
WHEEL SET
Tyre (Tire) Set
Please Note:We have supplied extra castors and
caster stoppers than you need.

11
Castor stopper
Castor section Bottom case section
Push down the castor stopper and snap
the castor section.
Make sure to rotate free the castor section
and castor tire.
Completed
bottom case
and castor
section
Castor section
Castor stopper
Bottom case
Completed castor section
Castor tire
Castor
1. Assembling the castor
2.Assembling the castor and the bottom case
Please Note: This section is now
completed by the factory
12
Motor-gear
box
Bottom case
section
Motor-gear
box
Gear box
holder
Gear box
holder
Screws B (4pcs)
Motor wire
(4pcs)
Completed wheel section
Completed Bottom case and
motor (gear box) section
3. Assembly of motor-gear boxes and bottom case
4. Assembling the wheels (2 set)
Wheel
Wheel
Tire
Tire
.

13
Bottom case and
wheel section
PC board-B
Screw A (3 pcs)
10pin wire
Bottom case
section
Wheel section
Wheel section
Screw A
Screw A
Completed
bottom case and
wheel section
5. Assembling the wheel and the bottom case
6. Assembling PC board-B and bottom case section
14
Bottom case and PC
board-B section
PC board-A
Screw A (3 pcs)
10pin wire
First, insert 10pin wire
plug through the
rectangular opening
on PC board-A .
Then, lower the PC
board-A onto the
bottom case section
with screws-A (3pcs)
Completed bottom
case and PC board-A
section
Completed bottom
case and PC board-B
section
Slide the tab on the wire plug
into the slot in the wire socket.
Make sure to install in
correct direction.
7. Assembling PC board-A and bottom case section
Continuation of step 6

15
Insert the terminal pins from the PC board-C to
the socket on PC board-B
PC board-B
PC board-C
Bottom case and PC
board-A,B section
PC board-C
8. Assembling the PC board-C and the bottom case
16
Completed PC board-B and PC board-C
Continuation of step 8
9. Assembling the batteries and the bottom case
Completed bottom case
and PC board-A,B,C
section
3V battery holder
AA battery
AA battery
9V battery
9V battery snap
Bottom case
section
Make sure the switch is off.
Place two AA batteries in
the 3V battery holder in the
correct polarity.
The 9V battery snap push
to 9V battery with correct
polarity.
Insert 9V battery snap wire
through the rectangular
opening on bottom case .
Insert 3V battery holder
wire through the
rectangular opening on
bottom case.

17
Screw A
Battery cover
Bottom case
section
Insert the motor wires
(left and right) through
the hole of PC board-A.
Insert the 9V battery
snap wires and 3V
battery holder wires
through the hole of PC
board-A.
Completed bottom
case and battery
cover section
10. Assembling the battery cover
11. Connecting the wires connector to PC board pins
18
PC board A
9V battery
snap and 3V
battery holder
wires
Motor wires
(left and right)
If the connectors of
the wires are too loose,
pinch the connectors
lightly with a pair of
long nose pliers so
they will not come off.
Continuation of step 11
Completed connecting
the wires
Wiring table
Wire Marking on PCB
Right motor
Yellow MR+
Green MR-
Left motor
Yellow ML+
Green ML-
9V battery snap
Red 9V
Black
3V battery holder
Red 3V
Black
R H Motor

19
12. Assembling front/rear apron and bottom case
Completed body section
Rear apron
Front apron
Insert the pins of aprons to the
holes of bottom case section.
Bottom case
section
20
Body section
Screw-B
(2 pcs)
Insert the holes
of dome to the
pins of aprons.
And then
assembling the
dome and the
body section
with screw-B
Dome
13. Assembling dome and body section
Completed sketch

21
How to operation Tribotz
1. Install both the “AA” batteries and 9V battery in the battery holder.
2. Check that the motor runs when the Tribotz is switched on the
“T”, ”S”, and “A”.
3. Draw a line with the black marking pen on paper. (The line should
be 3 to 8 mm in thickness.)
4. When in line tracer mode, the red LED lights up. PlaceTribotzon
the paper positioning the centre of the sensor PC board right on the
black line. Check to make sure Tribotz moves forward and follows
the line.
5. When in sound mode, the yellow LED lights up. Tribotz will start
moving at random. When clap your hands near the sound sensor
(condenser microphone), Tribotz will turn to the left immediately
and then moves forward again.
6. When in avoid mode, the green LED lights up. If there is an
obstacle in front, Tribotz will avoid an obstacle and move will
forward continuously. (If an obstacle is too small, too close, or the
colour is too dark, Tribotz may not find it.)
22
Black line White paper
Reflection light
phototransistorphototransistor
Bend to toward or backward
LED
Bend to left or
right
Bend to left or
right
How to use the Tribotz in line tracer mode?
Bend the LED on the sensor PC board a little either way (toward the LED
or the other way) to adjust the sensitivity when the sensor does not catch the
black line well.
Tuning the sensor
Tribotz detects the line with two phototransistors (light sensor) sensing
the reflected light so that its movement depends on how the sensors receive
the light. If the Tribotz moves not follows the line, adjust the LED and
phototransistors properly. (See the illustration below)
Tribotz also comes with a Line Tracer Puzzle Game. The object of the game
is to see can you complete putting the line together before the robot catches
up with you! An ideal family of part game.
It is important that this is laid on a flat surface so thatthe joints are as
smooth as possible.

23
Tribotz has two battery holders, with two batteries in each. 2xAA batteries (3V) for
driving the motors, and 9V battery for circuits. As the power consumption differs, the
batteries used for the motors will run down faster than the ones used for the circuit. If
the motor batteries (3V) become weak, its running speed turns slower. And if the circuit
battery (9V) become weak, Tribotz does not function. In either case, change the weak
batteries.
Use this chart to diagnose problems:
Problem Solution
The motor is not spinning. ~ Check that the wiring is correct.
~ Check the polarity of the batteries.
~ Insert new batteries
The Tribotz off the line easily. ~ Tuning the LED and phototransistors.
~ Insert new 9V battery.
The Tribotz does not avoid an obstacle ~ Insert new 9V battery.
The Tribotz does not react to hand claps. ~ Insert new 9V battery.
Tribotz also comes with a Line Tracer Puzzle Game. The object of the game
is to see can you complete putting the line together before the robot catches
up with you! An ideal family of part game.
It is important that this is laid on a flat surface so that the joints are as
smooth as possible.

24
AMPLIFICATION AND DRIVING MOTOR
MODE CONDITION
DISPLAY
TRACER POWER
SUPPLY CONTROL
MEMORY
CIRCUIT
TRACER
SENSOR
AMPLIFICATION TIMER
SOUND
SENSOR
AVOIDANCE
SENSOR
FLICKER
CIRCUIT POWER SUPPLY
FILTER FILTER
RED
LED5
YELLOW
LED5
GREEN
LED5
LINE
TRACER
MODE
SOUND
MODE
AVOID
MODE
Schematic of electronic circuit
The schematic of electronic circuit is a kind of diagram showing how the
parts such as resistors and capacitors are connected to each other by
simplifiedmarkings.
25
Avoidance
sensor section
Tracer power
supply control
section
Power supply
(9V) section
Power supply
(3V) section
Sound sensor
section
Memory circuit
section
Tracer sensor
section
Amplification
time section Amplification
and driving
motor section
Right motor
Left motor
sw-A
sw-B
TSAOFF
Flicker circuit
section
Filter section
Filter section
Switch (SW)
ML
MR
Mode condition
dispaly section
Mode condition display
1.Linetracermode
Switch on the "T" and red led5
lightup.
2. Avoider mode
Switch on the "A" and green
led3 light up.
3. Sound mode
Switch on the "S" and yellow
led4 light up.
Block diagram
The block diagram is a simplified figure that shows each function of the
electric circuit.

Explanation of circuit
26
Explanation of the different modes of operation of Tribotz
Tribotz has three modes.
A. The line tracer mode -In this mode, if you draw a line with the black marking pen on
white paper. (The line should be 3 to 8 mm in thickness.), Tribotz will move forward
following the line.
B. The avoider mode -In this mode, if the infrared sensor perceives an obstacle, Tribotz
avoids the obstacle, and it will turn and change direction, and move forward once more.
C. The sound mode -In this mode, if it comes in contact with an object or hears a loud noise
(such as hand clapping), Tribotz will automatically reverse, then turn left before embarking on
a new course.
Explanation of how each mode of operation is handled in the electronics
A. Line tracer mode
Operation procedure: Turn the switch (sw) on to the position marked “T” on Tribotz–this
line tracer mode (You will find four switch positions on the lower half of the schematic
diagram states as OFF, A, Sand T. At this point a red LED (designated as LED5 in the
schematic diagram) will light up, indicating that you a selected the line tracer mode for
Tribotz. You will find this LED in the Mode condition display section.
1. Tracer sensor section
This Tribotz detects a black line using a redLED2 and two phototransistors (PD2, PD3). As
white colours (colors) reflects light and black colours (colors) absorbs it, Tribotz uses this
principle to detect where the black line might be. The phototransistors are able to detect the
reflection of the light reflected back of the white paper from LED2 and therefore determine
the precise position of the black line.
2. Memory circuit section
This section consists of transistors, resistors and capacitors designated by: TR11,TR12, R22,
R23, R26, R27, C7 and C8, and it is also called “bistable multi-vibrator”. When Tribotz
Explanation of circuit
27
wanders off the black line, it memorizes from which side it has strayed off and this part of the
circuit instructs the motors to direct Tribotz back to the black line. For example, when it goes
off to the right side of a black line, the reflected light is collected by the phototransistor PD2,
TR12 turns on andTR11 turns off. At the same time, TR13, TR3 and TR6 (in the
amplification and driving motor section) are turned on (we will explain how this happens
later!), which makes controls the right side motor and Tribotz returns to the black line.
However, when it goes off to left side of the black line, TR11 turns on and TR12 turns off.
Since the reflected light is collected by PD3, the transistors TR14, TR4, TR7 and TR9 are all
turned on and a left side motor is activated. When the black line is straight and both
phototransistors are on the line, all transistors are turned on, both of motors are activated and
Tribotz runs directly ahead on the straight line
3. Amplification and driving motor section
The electrical current generated from the memory circuit section is not enough to rotate the
motors. Since a large amount of current is necessary to turn a motor, the transistors TR13,
TR3 and TR6will amplify this current current. This will rotate the right motor (MR), and
transistors TR14, TR4, TR7 and TR9 amplify the current to rotate the left motor (ML).
4. Power supply section
The 9V battery provides the energy to operate the tracer power supply control section and
mode condition display section. The 2 x “AA” batteries (each AA batter is 1.5V) provide
energy tooperate the tracer sensor section, memory circuit section and power to spin the
motors.
B. Avoider mode
Operation procedure: Turn the switch (sw) to position “A” (This position can be found in
OFF, A, Sand Tare on the schematic of electronic circuit) and green LED3 will light
up.(Mode condition display section)
1. Flicker circuit section
The flicker circuit section consists of TR1, TR2, R2, R3, R4, R5and C3 and it is called a
“multi-vibrator”. When TR1 and TR2 are turned on, the voltage level “H” will be fed back

Explanation of circuit
28
from the collector terminal of TR2 to the base terminal of TR1 through R4 and C3 (called
positive feedback ). At this point TR1 and TR2 are turned off.
2. Avoidance sensor section
When TR2is turned on and off, the LED1 will blink on and off. If there is an obstacle in
Tribotz’s way, the light emitted from LED1 is reflected and the phototransistor PD1 receives
the signal. Tribotz will now avoid an obstacle and change direction of motion.
3. Amplification timer section
When the PD1 receives a signal, IC1 (8pin) keeps the voltage level “H”. Since the signal of
the IC1(8pin) will be fed back to the IC1(10pin) through R14 and C6 (called positive
feedback), the voltage level does not stay in “H” level but is sent back to “L” level.
When the PD1 is not have a signal, the IC1(7pin) keeps the voltage level “H” and the
IC1(8pin) keeps the voltage level “L”. You have probably guesses that H = High Voltage
level and L = Low Voltage Level !
4. Amplification and driving motor
As the electric signal sent from the amplification time section does not have enough current to
rotate the motors, the transistors marked TR5, TR10, TR8, TR4, TR7, TR9, TR3 and TR6
amplify the current to generate sufficient power. When the signal from the amplification
time section IC1(8pin) is at the “H” level, the TR5,TR10 and TR8 turn on and the electric
current flows into the left motor (ML) to make it spin to turn and avoid an obstacle.
When the signal from the amplification time section IC1(7pin)is “H” level, the TR3 and
TR6 turn on and the electric current flows into the right motor (MR) to make it spin; the
transistors TR4, TR7 and TR 9turn on and the electric current flows into the left motor (ML)
to make it spin. Tribotz will now move forward.
5. Filter section
When the motor spins, the electric noise (change of power supply voltage) will naturally be
generated. Since the noise may affect the sensor and the amplification timer section, leading to
the malfunction, a filter which consisting of R1, C2 and C1 is included to suppress the noise.
This is one of the tests for Toy Safety in the European Community and is known as the EMC
Explanation of circuit
29
Test.
6. Power supply section
The 9V battery provides the energy to operate the flicker circuit section, avoidance sensor
section, amplification timer section and mode condition display sections. The 2 pieces of
“AA” batteries (1.5V x 2 = 3V) provide energy to operate the amplification and driving
motor section and provide power to spin the motors.
C. Sound mode
Operation procedure: Turn the switch (sw) on the “S” on Tribotz. (The markings of OFF, A, S
and Tare on the electronic circuit section of the schematic) The yellow LED4 will light up
indicating we have selected the sound activation mode . (Mode condition display section)
1. Sound sensor section
A condenser microphone (MK1) used as a sound sensor, picks up the sounds such as a
handclap. It senses the vibration of air (sound) and converts it into an electric signal.
2. Amplification timer section
When the MK1 sensor receives a signal, the IC1(8pin) keeps the voltage level “H”. Since the
signal of the IC1(8pin) will be fed back to the IC1(10pin) throughR14 and C6 (called
positive feedback ) The voltage level does not stay in “H” level but is sent back to “L” level.
When the PD1 is not a signal, the IC1(7pin) keeps the voltage level “H” and the IC1(8pin)
keeps the voltage level “L”.
3. Amplification and driving motor
As the electric signal sent from the amplification time section does not have enough current
to rotate the motors, the transistors TR5, TR10, TR8, TR4, TR7, TR9, TR3 and TR6
amplify the current to generate the power needed. When the signal from the amplification
time sectionIC1(8pin) is “H” level, the TR5, TR10 and TR8turn on and the electric current
flows into the left motor (ML)to make it spin Also the signal from the amplification time
section IC1(7pin) is “L” level, the transistorsTR3 and TR6 turn off and the right motor (MR)
does not run. Tribotz will now turn to avoid the obstacle. When the signal from the

Explanation of circuit
30
amplification time section IC1(7pin) is in “H” level, the transistors TR3 and
TR6turn on and the electric current flows into the right motor (MR) to make it spin. The
TR4, TR7 and TR9turn on and the electric current flows into the left motor (ML) to make it
spin. Tribotz will now move forward.
4. Filter section
When the motor spins, the electric noise (change of power supply voltage) will naturally be
generated. Since the noise may affect the sensor and the amplification timer section, leading to
the malfunction, a filter which consists of R1, C2 and C1 is included to restrict the noise.
5. Power supply section
The 9V battery provides energy to operate the flicker circuit section, avoidance sensor
section, amplification timer section and mode condition display section. The 2 pieces of the
“AA” batteries (1.5V x 2 = 3V) provide energy to operate the amplification and driving
motor section and provide power to spin the motors.
If you would like additional resource material please log on to www.iBOTZ.com , where we
will post further information about electronics and new products from time to time.

Learn all about the electronic parts used in robots
31
So what is electronics?
We all know that atoms are made up of protons, neutrons and electrons. The electrons are tiny
particles that orbit about the nucleus (made up of protons and neutrons) and have a special
electrical property of charge. The protons in the nucleus have a positive (+) charge whilst those
interesting electrons have a negative (-) one. This charge is what electronics is all about. When
electrons move together in a similar way we say there is a current flowing. The electrons are
actually moving all the time in materials like metals but they moving in all sorts of directions; it
is only when they all get together and move in the same direction we say that we have a current
flowing. However, electrons can't flow through every material. Materials that allow a current to
flow easily are called conductors. Materials that don't allow a current to flow are called non-
conductors or insulators. Metals are the most common conductors, whilst plastics are typical
insulators.
In order to get electrons toflow in a certain way they need to have an “energy” given to them.
Batteries are designed in such a way as to give that “energy” for electrons to flow between a
negative and a positive side (or electrode). This creates something like a pressure or force and
this is called the voltage. The bigger the voltage, the greater the pressure or force available to
the electrons. This force is sometimes called potential difference. A typical battery will give a
flow (or voltage) of 9 volts (9v). Before an electric current can go anywhere it needs to be given
a road or path to follow. This is what you see on our printed circuit board and it is called a
circuit. Therefore by connecting a battery to a circuit we can get a current to move and perform
the function we want. The battery will eventually run out of energy as it pushes the electrons out
from one side and collects them at the other. This will eventually result in the battery running
down.
Current & Amps
So how do we measure current? Currents are measured in amps, and voltages are measured in
volts (after the scientists Ampère and Volta). Voltages are sometimes called potential
differences, or electromotive forces. Current flows into a component and the same amount of
current always flows out of the component. As current flows through a component it will cause
a reaction of some kind, for example a bulb getting brighter.
Learn all about the electronic parts used in robots
32
Resistors & Resistance
Any material that hinders the movement of electrons is called a resistor. Electrons move more
easily through some materials than others when a voltage is applied. We measure how much
opposition there is to an electric current as resistance. Components that cause a resistance are
hence called resistors. The higher the resistance value, the more it restricts the flow. The
resistor will give the circuit a stable current thus giving protection to sensitive elements within a
circuit from damage
Resistance is measured in ohms after the discoverer of a law relating voltage to current. Ohms
are represented by the Greek letter omega. (Ù).
The main function of resistors in a circuit is to control the flow of current to other components.
Take an LED (light emitting diode) for example. If too much current flows through an LED it is
destroyed. So a resistor is used to limit the current.
What is Ohms Law?
The Law basically brings together the relationship between Voltage (V), Resistance (R) and
Current (I) as follows:
Potential Difference (V) in volts
Resistance(R) (ohm ΩΩ )
=Current (I) in amperes
Ohm discovered that if you double the voltage across the resistor then the current through it also
doubles. If you halve the voltage then the current is halved. This means that the current is
proportional to the voltage. Not surprisingly the opposite to this also happens! He also found
that if you double the value of the resistor then the current through it is halved. If the value of
the resistor is halved the current is doubled. Thus the current is inversely proportional to the
resistance.

Learn all about the electronic parts used in robots
33
If all this is a little hard to take in, here’s a handy way to remember Ohm’s Law
How do you determine the resistance of a resistor?
Resistors are colour coded for easy reading. To determine
the value of a given resistor look for the gold or silver
tolerance band and rotate the resistor as in the photo
above. (Tolerance band to the right). Look at the 1st
colour band and determine its colour. This maybe
difficult on small or oddly coloured resistors. Now look
at the chart and match the "1st & 2nd colour band" colour to the "Digit it represents". Write this
number down. Now look at the 2nd colour band and match that colour to the same chart. Write
this number next to the 1st Digit. The last colour band is the number you will multiply the result
by. Match the 3rd colour band with the chart under multiplier. This is the number you will
multiple the other 2 numbers by. Write it next to the other 2 numbers with a multiplication sign
before it. Example: 2 2 x 1,000.To pull it all together now, simply multiply the first 2 numbers
(1st number in the tens column and 2nd in the ones column) by the Multiplier
Common symbols used for resistors
Learn all about the electronic parts used in robots
34
Resistor Colour Code Chart
1st. & 2nd
Colour Band
Digit it
Represents -----Multiplier-----
BLACK 0×1
BROWN 1×10
RED 2×100
ORANGE 3×1000 or 1K
YELLOW 4×10000 or 10K
GREEN 5×100000 or 100K
BLUE 6×1000000 or 1M
VIOLET 7Silver is divide by 100
GREY 8Gold is divide by 10
WHITE 9
§Tolerances
§Gold = 5%
§Silver = 10%
§None = 20%
Capacitors & Capacitance
Capacitors are like tiny batteries in a circuit storing charge. Like tiny batteries they can cause a
current to flow in a circuit. But they can only do this for a short time -they cannot deliver a
sustained current. They can be charged up with energy from a battery, then return that energy
back later. The capacitance of a capacitor is a measure of how much energy or charge it can
hold.
Table of contents
Other iBOTZ Robotics manuals
Popular Robotics manuals by other brands
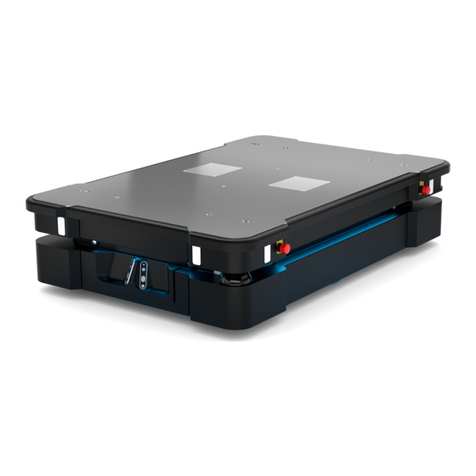
MIR
MIR MiR1000 operating guide
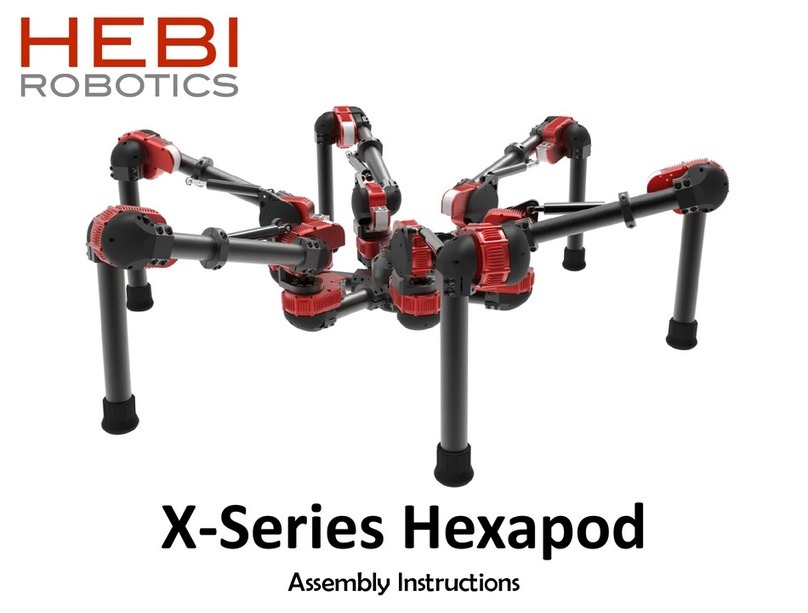
HEBI Robotics
HEBI Robotics X-Series Hexapod Assembly instructions
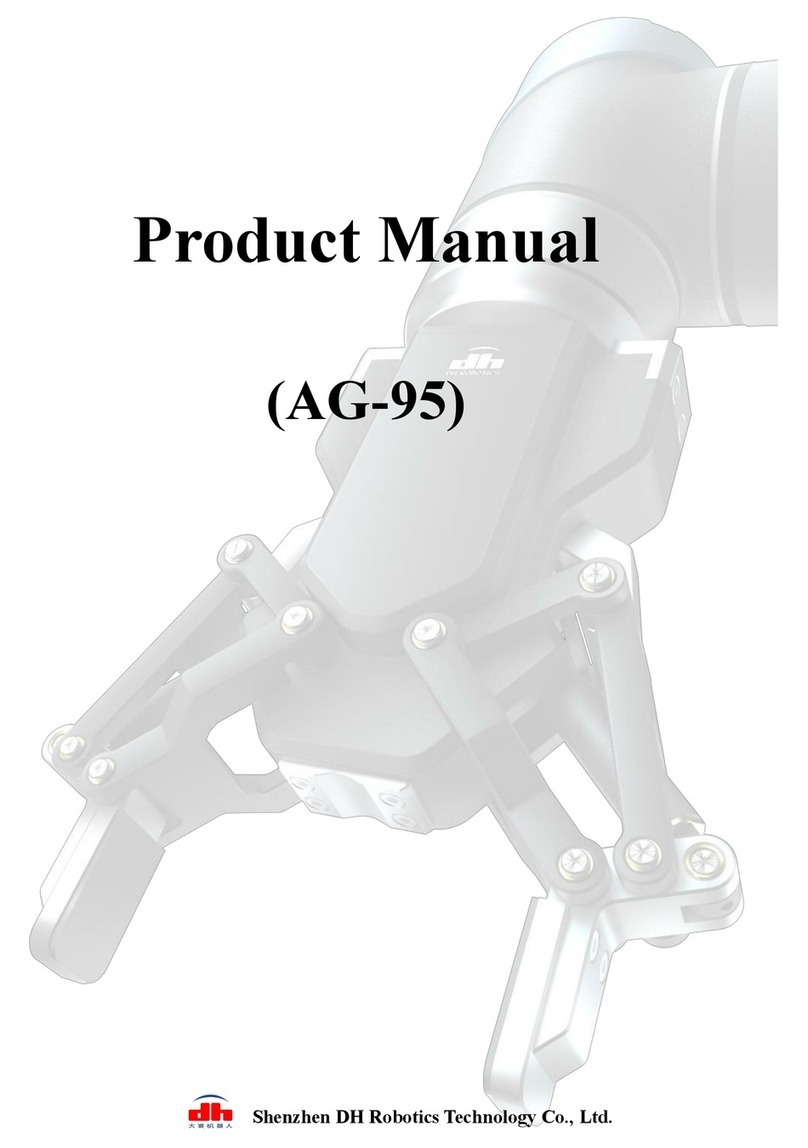
DH Robotics Technology
DH Robotics Technology AG-95 product manual
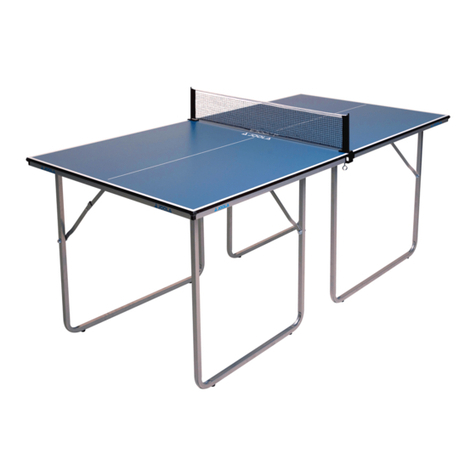
JOOLA
JOOLA Midsize Table instruction manual
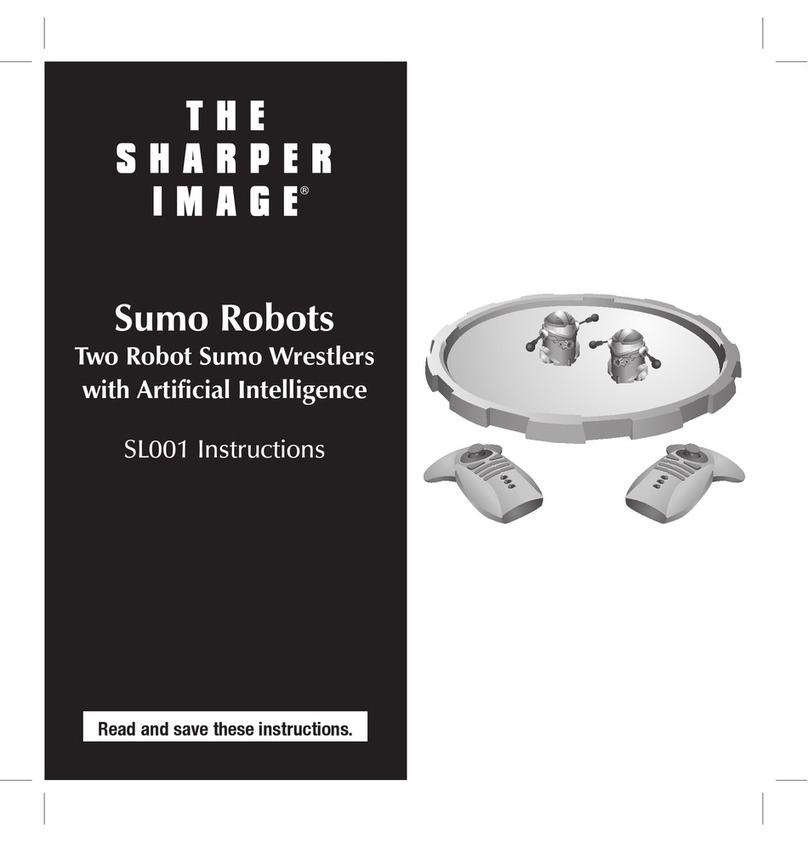
Sharper Image
Sharper Image SL001 instructions
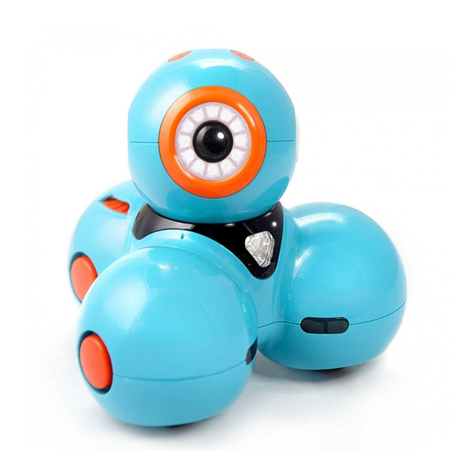
Wonder Workshop
Wonder Workshop Learning Robots Dash Getting started