IDEC EB3N User manual

EB3N Safety Relay Barriers
Build a safety system in an explosive atmosphere.
• Ensures explosion protection safety and machine safety in an explosive
atmosphere.
• Machine safety system can be built in compliance with ISO13849-1 Category
4, Performance level e.
• Safety input devices applicable in any explosive gas and hazardous areas are
available.
• Available with auxiliary inputs (5 points) used to monitor the operating status
of safety input devices.
• A wide variety of Japan TIIS-rated emergency stop switches and interlock
switches are available.
• Global usage
Explosion protection: Global: PTB (IEC Ex), Europe: PTB (ATEX), USA: UL
Japan (TIIS), China (Ex-CCC)
Machine safety: TÜV Rheinland
• No grounding required.
Explosion
Protection
Safety relay barrier [Exia] II C
Switch (EB9Z-A) Exia II CT6
Switch (EB9Z-A1) Exia II BT6
Safety
Performance
Performance level e
Category 4
Safety Relay Barriers
Safety Input Points Safety Output
Points
Auxiliary Input Points
(Note 1)
Auxiliary Output Points
(Relay Output)
Reset (Start)
(Note 2, Note 3) Part No.
2 2NO Without Without Auto reset (Auto start) EB3N-A2ND
Manual reset (Manual start) EB3N-M2ND
2 2NO 5 (1 common) 5NO (1 common) Auto reset (Auto start) EB3N-A2R5D
Manual reset (Manual start) EB3N-M2R5D
Note 1: A maximum of ve monitor contacts from safety input devices can be connected to the auxiliary input terminals. In addition, non-safety input devices can also be connected to the
auxiliary input terminals.
Note 2: On auto reset (auto start) models, when the safety condition is met (two safety inputs are both on), safety outputs are turned on automatically.
Connect the reset (start) input terminals Y1 and Y2 together except for the following cases:
When connecting a contactor or force guided relay to the safety output of the EB3N, connect the NC contacts of the contactor or force guided relay to the reset (start) input terminals
Y1 and Y2 of the EB3N for use as a backcheck input signal.
Note 3: On manual reset (manual start) models, while the safety condition is met (two safety inputs are both on), safety outputs are turned on at the falling edge of the reset switch (start
switch) signal (OFF ON OFF) (start off check).
Manual reset (manual start) models have a monitoring function of reset switch contacts (detection of welded contacts). Use NO contacts of a momentary switch for the reset (start)
input. When connecting a contactor or force guided relay to the safety output of the EB3N, connect the NC contacts of the contactor or force guided relay to the reset (start) input
terminals Y1 and Y2 of the EB3N for use as a backcheck input signal.
Selection Guide
1. Selecting the reset (start) function
Auto reset (auto start): Select this model when connecting safety control devices, such as safety relay modules or safety controllers, to the EB3N safety outputs to set up a safety
system, using the reset (start) function of the safety control device.
Select this model when connecting contactors or force guided relays to the EB3N safety outputs to set up a safety system, and a risk assessment on the entire
system has not found any safety problem in using auto reset (auto start).
Manual reset (manual start): Select this model when connecting contactors or force guided relays to the EB3N safety outputs to set up a safety system, and a risk assessment on the entire
system has found that manual reset (manual start) is necessary.
2. Selecting the auxiliary outputs
Without auxiliary outputs: Select this model when the operating status of safety input devices are not monitored.
With auxiliary outputs: Select this model when the operating status of safety input devices are monitored or when non-safety input devices are also connected.
General Specifications
Rated Power Voltage 24V DC
Power Voltage Range 20.4 to 26.4V DC
Operating Temperature
–20 to +60°C (no freezing)
UL: –20 to +40°C
(no freezing)
Operating Humidity 45 to 85% RH
(no condensation)
Power
Consumption
Without auxiliary output 5.5W maximum
With auxiliary output 7.0W maximum
Safety
Output
Contacts 13-14,
23-24 2NO
Rated Load Resistive 30V DC, 1A
Inductive DC-13, 24V, 1A
Response
(rated voltage)
Turn on 100 ms maximum
Turn off 20 ms maximum
Auxiliary
Output
Contacts A* - C1 5NO/1 common
Rated Load Resistive 24V DC, 3A,
common terminal 5A max.
Response
(rated voltage)
Turn on 15 ms maximum
Turn off 10 ms maximum
Mounting DIN rail or panel mounting
*: Channel Nos. 1 to 5
Explosion-Protection Specifications
Explosion Protection [Exia] II C
Non-intrinsically Safe Circuit Maximum Voltage
(Um) 250V (UL: 125V)
Intrinsically Safe Circuit Maximum Voltage (Uo) 13.2V
Intrinsically Safe Circuit Maximum Current (Io) 227.2 mA
Intrinsically Safe Circuit Maximum Power (Po) 750 mW
Intrinsically Safe Circuit Allowable Capacitance (Co) 0.49 µF (TIIS: 0.28 μF)
Intrinsically Safe Circuit Allowable Inductance (Lo) 0.60 mH
(TIIS: 0.56 mH)
Intrinsically Safe Circuit
Wiring Resistance (Rw)
Safety circuit (Note 1)
Auxiliary circuit (Note 2)
Note 1: 10Ω maximum (500m maximum using a 1.25 mm2 cable)
Note 2: 600/(N+1)Ω maximum, where N = the number of common channels
Safety Specifications
Category 4
Performance Level (PL) e
Mean Time to Dangerous Failure (MTTFd) 100 years
Diagnostic Range 99% minimum
Calculation conditions for MTTFd
tcycle: Mean operation cycle = 1 hour
hop: Mean operation hours per day = 24 hours
dop: Mean operation days per year = 365 days
Note: When tcycle is shorter than 1 hour, MTTFd will decrease.
1
EB3N Safety Relay Barriers

Certification No.
Certication
Organization Explosion Protection Certication No.
TIIS
Safety Relay Barriers [Exia] II C
Switch (EB9Z-A) [Exia] II CT6
Switch (EB9Z-A1) [Exia] II BT6
TC18753
TC15758
T15961
PTB
[Exia] II C, [Exia D] IEC Ex PTB 10.0015
II (1) G [Exia] II C
II (1) D [Exia D] PTB 09 ATEX 2046
CQST [Exia] II C CNEx 11.0038
UL Class I, Zone 0, [AExia] II C
Class I, II, III, Div. 1, Grps A, B, C, D, E, F and G E234997
Dimensions
EB3N-A2ND EB3N-A2R5D
EB3N-M2ND EB3N-M2R5D
Mounting Hole Layout
EB3N-A2ND EB3N-A2R5D
EB3N-M2ND EB3N-M2R5D
EB3N System Configuration Examples
EB3N-A2ND Safety Control Device
Safety Control Device
PLC
PLC
Safety Contactor
EB3N-M2ND Safety Contactor
Safety Contactor
Safety Contactor
Safety Input Device
Safety Input Device
Barrier Safety Output Safety Output
Barrier Safety Output
Backcheck Input
Safety Output
Backcheck Input
1:1 connection with a safety input device, compliant with Category 4
Connection with multiple safety input devices,
capable of monitoring up to 5 contact operations, compliant with Category 3
F
or monitoring operating statuses of safety input devices located in a non-hazardous area
EB3N-A2R5D
Monitor
Monitor
Barrier Safety Output
Auxiliary Output
(Monitor Output)
Reset (Start) Input
Auxiliary Output
(Monitor Output)
EB3N-M2R5D
Barrier Safety Output
Hazardous Area Non-hazardous Area
Hazardous Area Non-hazardous Area
• A safety relay module or safety controller is used
to set up a safety circuit, using the reset (start)
function of the safety relay module or safety
controller.
• The manual reset (manual start) function of the
EB3N is used to set up a safety circuit, without
using a safety control device.
• A safety relay module or safety controller is used
to set up a safety circuit, using the reset (start)
function of the safety relay module or safety
controller.
• The reset (start) function is used to set up a
safety circuit, without using a safety relay module
or safety controller.
Safety Input Devices
Connected in Series
…
Safety Input Devices
Connected in Series
…
Reset (Start) Input
Backcheck Input
Reset (Start) Input
Backcheck Input
Reset (Start) Input
65.0
M3
75.0
110.5 77.5
75.0
M3
Terminal Functions
24V DC Power
Y1-Y2 Reset input
(Start input)
11-12 Safety input 1
21-22 Safety input 2
N1, N2 Signal ground
P*-N3 Auxiliary input
13-14 Safety output 1
23-24 Safety output 2
A*-C1 Auxiliary output
*: 1 to 5
2-M4 tapped or
2-ø4.5 drilled holes
51
65
97
65
2-M4 tapped or
2-ø4.5 drilled holes
2
EBN Safety Relay Modules

Safety Control Device
Reset (Start) Switch
Other Input Device
PLC
PLC
Safety Contactor
Safety Contactor
Safety Output
Backcheck Input
Installing a reset switch in a hazardous area, using auxiliary input and output
Barrier Safety Output
Reset (Start) Output
Other Output
EB3N-A2R5D
EB3N-M2R5D
Barrier Safety Output
Backcheck Input
Reset (Start) Input
Other Output
Hazardous Area Non-hazardous Area
Safety Input Devices
…
Reset (Start) Switch
Other Input Device
Safety Input Devices
Safety Input Devices Connectable to Safety Input Terminals (Examples)
Emergency stop switch: (Non-illuminated) XW1E-BV402MFRH, XN4E-BL412MRH
Safety switch: HS6B-02B05, HS1B-02R
Operating Instructions
Notes for Operation
1. Do not disassemble, repair, or modify the EB3N safety relay barrier,
otherwise the safety characteristics may be impaired.
2. Use the EB3N within its specication values.
3. The EB3N can be mounted in any direction.
4. Mount the EB3N on a 35-mm-wide DIN rail or directly on a panel surface
using screws. When mounting on a DIN rail, push in the clamp and use end
clips to secure the EB3N. When mounting on a panel surface, tighten the
screws rmly.
5. Excessive noise may cause malfunction or damage to the EB3N. When the
internal voltage limiting circuit (thyristor) has shut down the power due to
noise, remove the cause of the noise before powering up again.
6. The internal power circuit contains an electronic fuse to suppress
overcurrents. When the electronic fuse has tripped, shut down the power,
remove the cause of the overcurrent before powering up again.
7. Use crimping terminals with insulation sheath for wiring. Tighten the terminal
screws, including unused terminal screws, to a recommended tightening
torque of 0.6 to N·m using a screwdriver of ø5.5 mm in diameter.
8. Before inspecting or replacing the EB3N, turn off the power.
Notes for Machine Safety
1. Operate the safety input device to check the EB3N functionality everyday.
2. For safety input devices, such as safety switches or emergency stop
switches, connected to the EB3N, use safety standard-compliant devices
with direct opening action and 2NC contacts.
3. Do not use the auxiliary input as a safety input.
4. For safety control devices connected with the EB3N, use machine safety
standard-compliant devices with a disparity detection function.
5. Use safety inputs and safety outputs in a circuit conguration compliant
with safety requirements.
6. To calculate the safety distance, take into consideration the response time
of all devices comprising the system, such as the EB3N and safety devices
connected to the EB3N.
7. Separate the input and output wiring from power lines and motor lines.
8. When using multiple EB3N safety relay barriers, do not connect one switch
to more than one EB3N. Use separate switches for each EB3N.
9. To ensure EMC, use shielded cables for safety inputs and auxiliary inputs.
Connect the shield to the FG of the control panel on which the EB3N is
mounted.
10. For protection against overcurrents, connect an IEC60127-2-compliant 2A
fast-blow fuse (5 × 20 mm).
11. Evaluate the ISO 13849-1 category and performance level in consideration
of the entire system.
Notes for Explosion Protection Safety
1. Install the EB3N in an enclosure capable of protecting against mechanical
shocks at a hazardous location in accordance with intrinsic safety ratings
and parameters.
2. Install and wire the EB3N so that the EB3N is not subject to electromagnetic
and electrostatic induction and does not contact with other circuits.
For example, keep a minimum spacing of 50 mm between intrinsically safe
and non-intrinsically safe circuits, or provide a metallic separating board
between the intrinsically safe circuit and non-intrinsically safe circuit. When
providing a metallic separating board, make sure that the board ts closely
to the enclosure (top, bottom, and both sides). Allowable clearance between
the board and the enclosure is 1.5 mm at the maximum.
When a motor circuit or high-voltage circuit is installed nearby, keep a wider
spacing than 50 mm between intrinsically safe and non-intrinsically safe
circuits.
3. Keep a minimum spacing of 3 mm between the terminal or relay terminal
block of the intrinsically safe circuit and the grounded metal parts of the
metal enclosure.
4. Connect the terminals so that IP20 is ensured.
5. To prevent disengaged wires from contacting with other intrinsically safe
circuits, bind together the end of wires.
6. Make sure that the voltage of the power supply for the devices connected
to the non-intrinsically safe circuit or the internal voltage of such devices
does not exceed 250V AC/DC 50/60 Hz or 250V DC under any normal and
abnormal conditions.
7. Make sure that the wiring of intrinsically safe circuits does not contact
with other circuits or is not subject to electromagnetic and electrostatic
inductions, otherwise explosion protection is not ensured.
8. When identifying intrinsically safe circuits by color, use light blue terminal
blocks and cables.
9. When wiring the intrinsically safe circuit, determine the distance to satisfy
the wiring parameters shown below.
a) Wiring capacitance Cw ≤ Co – Ci
Co: Intrinsically safe circuit allowable capacitance
Ci: Internal capacitance of switches
b) Wiring inductance Lw ≤ Lo – Li
Lo: Intrinsically safe circuit allowable inductance
Li: Internal inductance of switches
c) Wiring resistance ≤ Rw
Rw: Allowable wiring resistance
Switches in the Hazardous Area
1. A switch contains the switch contact, enclosure, and internal wiring. A
switch contact refers to an ordinary switching device which consists of
contacts only.
2. When the switch has internal wiring or lead wire, make sure that the values
of internal capacitance (Ci) and inductance (Li) are within the certied
values.
3. Enclose the bare live part of the switch contact in an enclosure of IP20 or
higher protection.
4. Depending on the explosion-protection specications of TIIS, the exposed
area of plastic switch operator, when installed in Japan, is limited as
follows:
Certication Explosion Protection Exposed Area
TC15758 Exia II CT6 20 cm2maximum
TC15961 Exia II BT6 100 cm2maximum
BGLEN01A-Fa-EB3N July 2021
3
EBN Safety Relay Modules

1. Notes on contents of Catalogs
(1) Rated values, performance values, and specification values of IDEC products
listed in this Catalog are values acquired under respective conditions in
independent testing, and do not guarantee values gained in combined
conditions.
Also, durability varies depending on the usage environment and usage
conditions.
(2) Reference data and reference values listed in Catalogs are for reference
purposes only, and do not guarantee that the product will always operate
appropriately in that range.
(3) The specifications / appearance and accessories of IDEC products listed in
Catalogs are subject to change or termination of sales without notice, for
improvement or other reasons.
(4) The content of Catalogs is subject to change without notice.
2. Note on applications
(1) If using IDEC products in combination with other products, confirm the
applicable laws / regulations and standards.
Also, confirm that IDEC products are compatible with your systems, machines,
devices, and the like by using under the actual conditions. IDEC shall bear no
liability whatsoever regarding the compatibility with IDEC products.
(2) The usage examples and application examples listed in Catalogs are for
reference purposes only. Therefore, when introducing a product, confirm the
performance and safety of the instruments, devices, and the like before use.
Furthermore, regarding these examples, IDEC does not grant license to use
IDEC products to you, and IDEC offers no warranties regarding the ownership
of intellectual property rights or non-infringement upon the intellectual
property rights of third parties.
(3) When using IDEC products, be cautious when implementing the following.
i. Use of IDEC products with sufficient allowance for rating and
performance
ii. Safety design, including redundant design and malfunction prevention
design that prevents other danger and damage even in the event that an
IDEC product fails
iii. Wiring and installation that ensures the IDEC product used in your
system, machine, device, or the like can perform and function according
to its specifications
(4) Continuing to use an IDEC product even after the performance has
deteriorated can result in abnormal heat, smoke, fires, and the like due to
insulation deterioration or the like. Perform periodic maintenance for IDEC
products and the systems, machines, devices, and the like in which they are
used.
(5) IDEC products are developed and manufactured as general-purpose products
for general industrial products. They are not intended for use in the following
applications, and in the event that you use an IDEC product for these
applications, unless otherwise agreed upon between you and IDEC, IDEC shall
provide no guarantees whatsoever regarding IDEC products.
i. Use in applications that require a high degree of safety, including nuclear
power control equipment, transportation equipment (railroads / airplanes
/ ships / vehicles / vehicle instruments, etc.), equipment for use in outer
space, elevating equipment, medical instruments, safety devices, or
any other equipment, instruments, or the like that could endanger life or
human health
ii. Use in applications that require a high degree of reliability, such as
provision systems for gas / waterworks / electricity, etc., systems that
operate continuously for 24 hours, and settlement systems
iii. Use in applications where the product may be handled or used deviating
from the specifications or conditions / environment listed in the Catalogs,
such as equipment used outdoors or applications in environments
subject to chemical pollution or electromagnetic interference
If you would like to use IDEC products in the above applications, be sure
to consult with an IDEC sales representative.
3. Inspections
We ask that you implement inspections for IDEC products you purchase without
delay, as well as thoroughly keep in mind management/maintenance regarding
handling of the product before and during the inspection.
4. Warranty
(1) Warranty period
The warranty period for IDEC products shall be one (1) year after purchase or
delivery to the specified location. However, this shall not apply in cases where
there is a different specification in the Catalogs or there is another agreement
in place between you and IDEC.
(2) Warranty scope
Should a failure occur in an IDEC product during the above warranty period
for reasons attributable to IDEC, then IDEC shall replace or repair that
product, free of charge, at the purchase location / delivery location of the
product, or an IDEC service base. However, failures caused by the following
reasons shall be deemed outside the scope of this warranty.
i. The product was handled or used deviating from the conditions /
environment listed in the Catalogs
ii. The failure was caused by reasons other than an IDEC product
iii. Modification or repair was performed by a party other than IDEC
iv. The failure was caused by a software program of a party other than
IDEC
v. The product was used outside of its original purpose
vi. Replacement of maintenance parts, installation of accessories, or the like
was not performed properly in accordance with the user’s manual and
Catalogs
vii. The failure could not have been predicted with the scientific and
technical standards at the time when the product was shipped from
IDEC
viii. The failure was due to other causes not attributable to IDEC (including
cases of force majeure such as natural disasters and other disasters)
Furthermore, the warranty described here refers to a warranty on the IDEC
product as a unit, and damages induced by the failure of an IDEC product are
excluded from this warranty.
5. Limitation of liability
The warranty listed in this Agreement is the full and complete warranty for IDEC
products, and IDEC shall bear no liability whatsoever regarding special damages,
indirect damages, incidental damages, or passive damages that occurred due to an
IDEC product.
6. Service scope
The prices of IDEC products do not include the cost of services, such as dispatching
technicians. Therefore, separate fees are required in the following cases.
(1) Instructions for installation / adjustment and accompaniment at test operation
(including creating application software and testing operation, etc.)
(2) Maintenance inspections, adjustments, and repairs
(3) Technical instructions and technical training
(4) Product tests or inspections specified by you
The above content assumes transactions and usage within your region. Please
consult with an IDEC sales representative regarding transactions and usage outside
of your region. Also, IDEC provides no guarantees whatsoever regarding IDEC
products sold outside your region.
Ordering Terms and Conditions
Thank you for using IDEC Products.
By purchasing products listed in our catalogs, datasheets, and the like (hereinafter referred to as “Catalogs”) you agree to be bound by these terms and conditions. Please read
and agree to the terms and conditions before placing your order.
Specications and other descriptions in this brochure are subject to change without notice.
Information in this brochure is current as of June, 2021.
2021 IDEC Corporation, All Rights Reserved.
USA IDEC Corporation
EMEA
APEM SAS
China IDEC (Shanghai) Corporation
IDEC Izumi (H.K.) Co., Ltd.
Taiwan IDEC Taiwan Corporation
Singapore IDEC Izumi Asia Pte. Ltd.
Thailand IDEC Asia (Thailand) Co., Ltd.
India IDEC Controls India Private Ltd.
Japan IDEC Corporation
Head Office 6-64, Nishi-Miyahara-2-Chome, Yodogawa-ku, Osaka 532-0004, Japan www.idec.com
Other IDEC Relay manuals
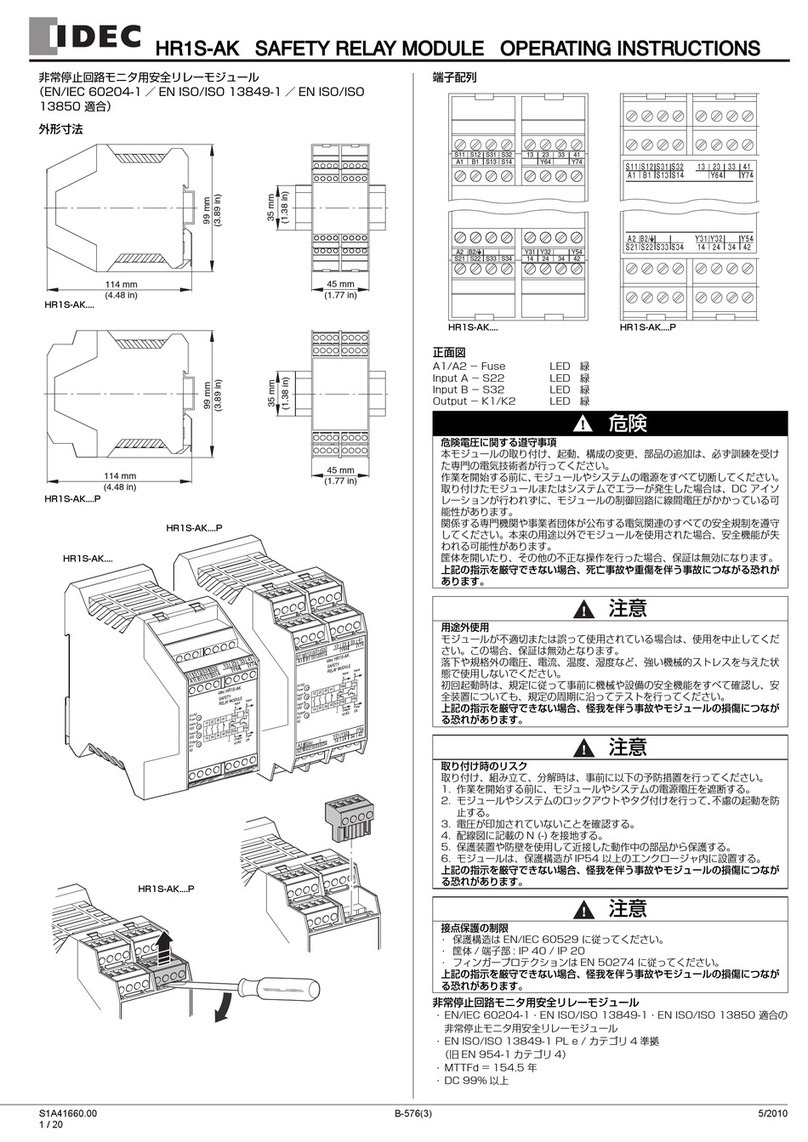
IDEC
IDEC HR1S-AK User manual
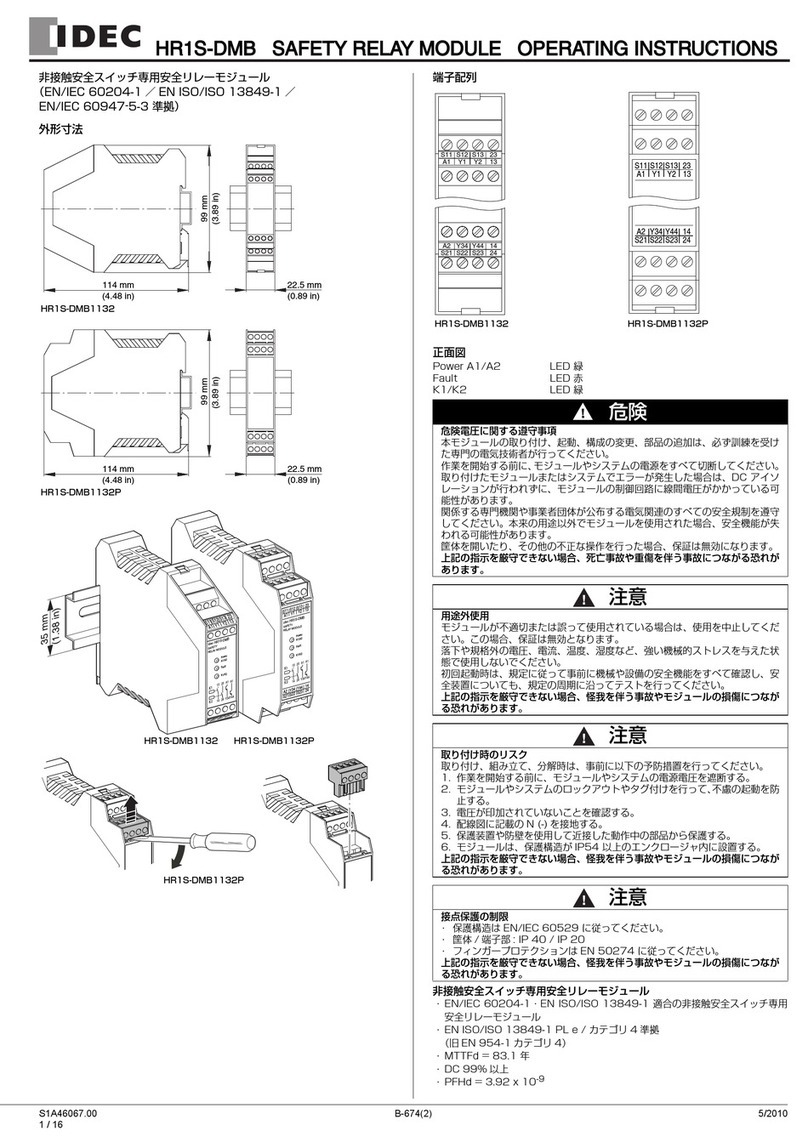
IDEC
IDEC HR1S-DMB Series User manual
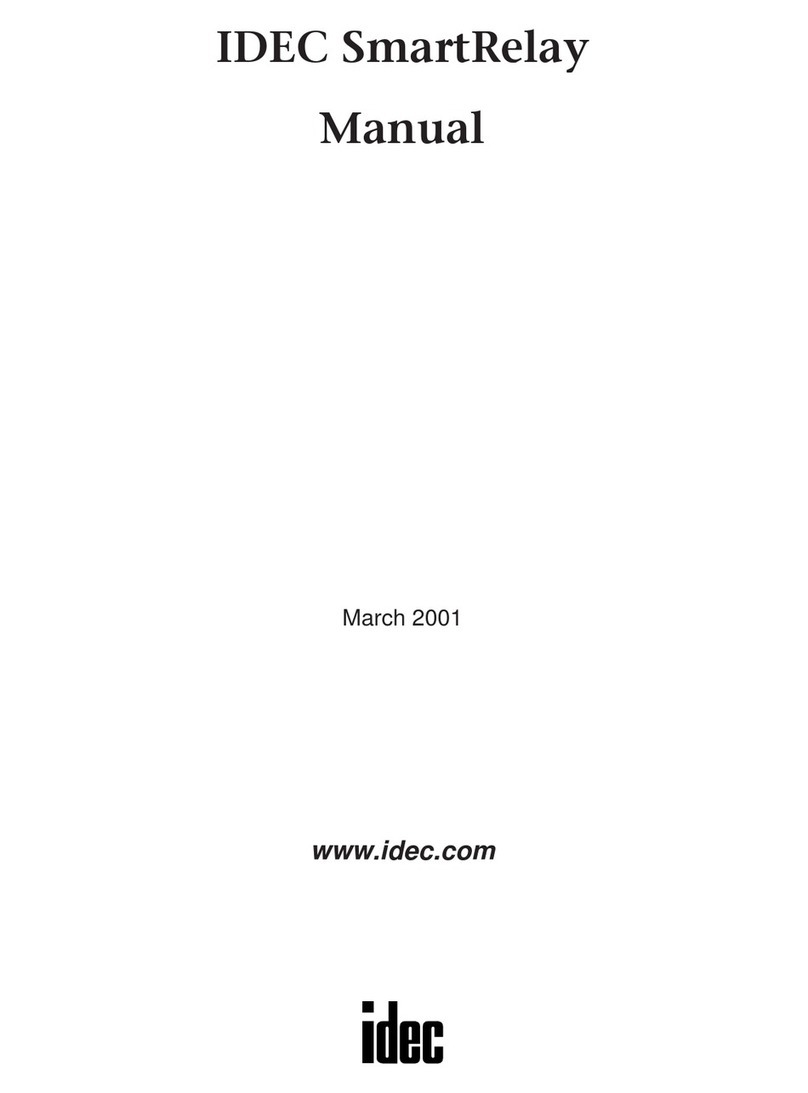
IDEC
IDEC SmartRelay FL1A-H12RCE User manual
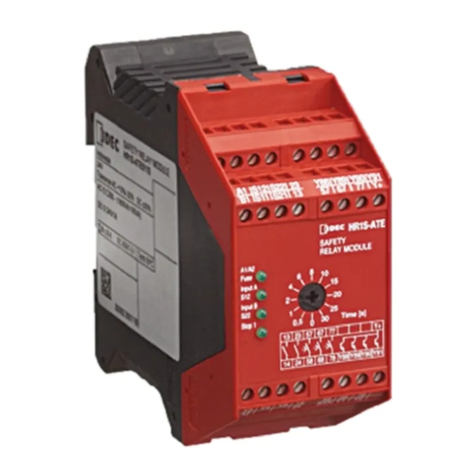
IDEC
IDEC HR1S-ATE User manual
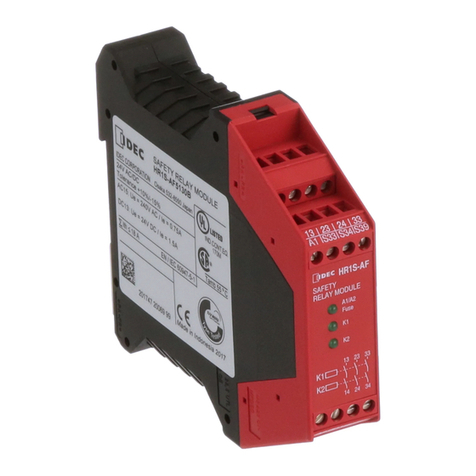
IDEC
IDEC HR1S-AF 5130B/PB User manual
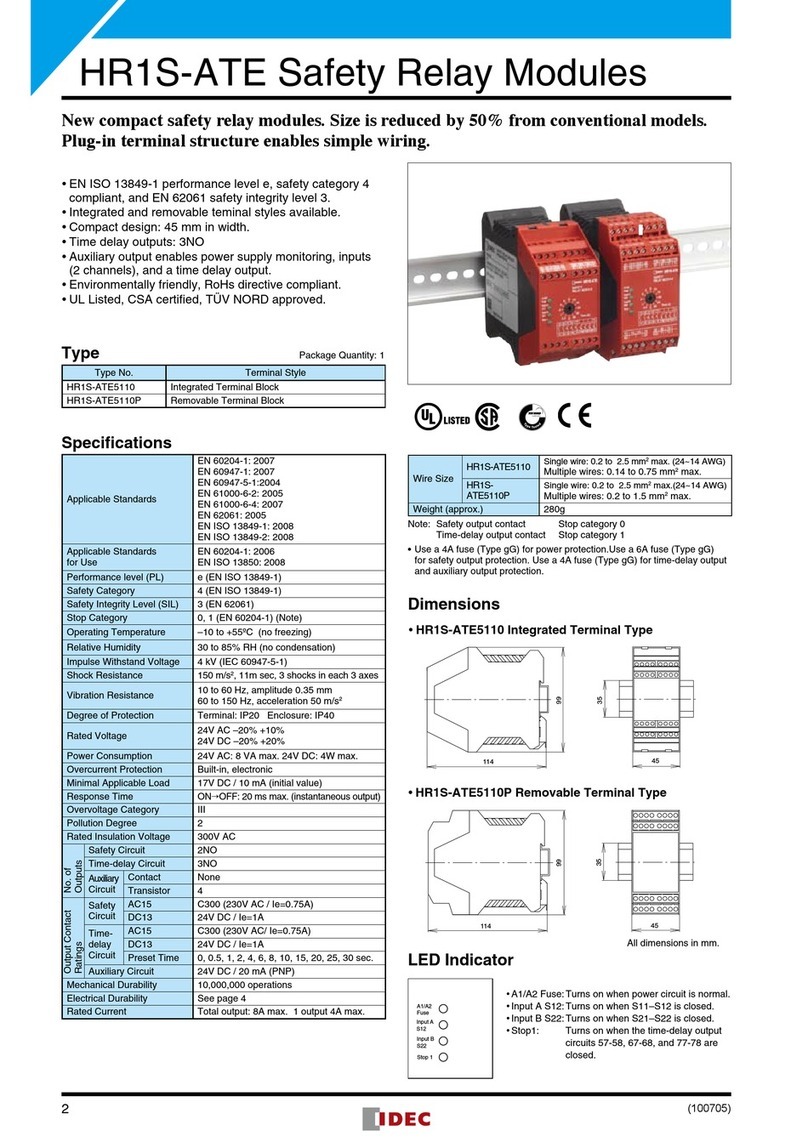
IDEC
IDEC HR1S-ATE User manual
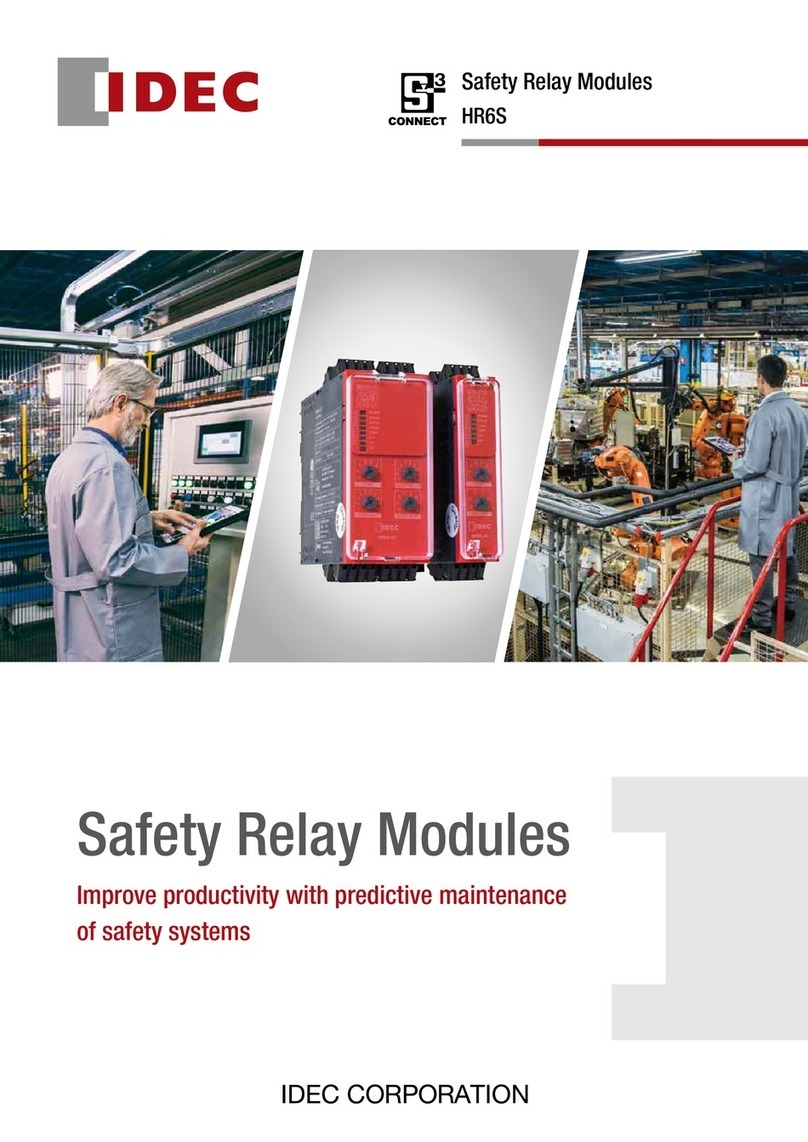
IDEC
IDEC HR6S Series User manual

IDEC
IDEC SmartAXIS FT9Z-1A01 User manual
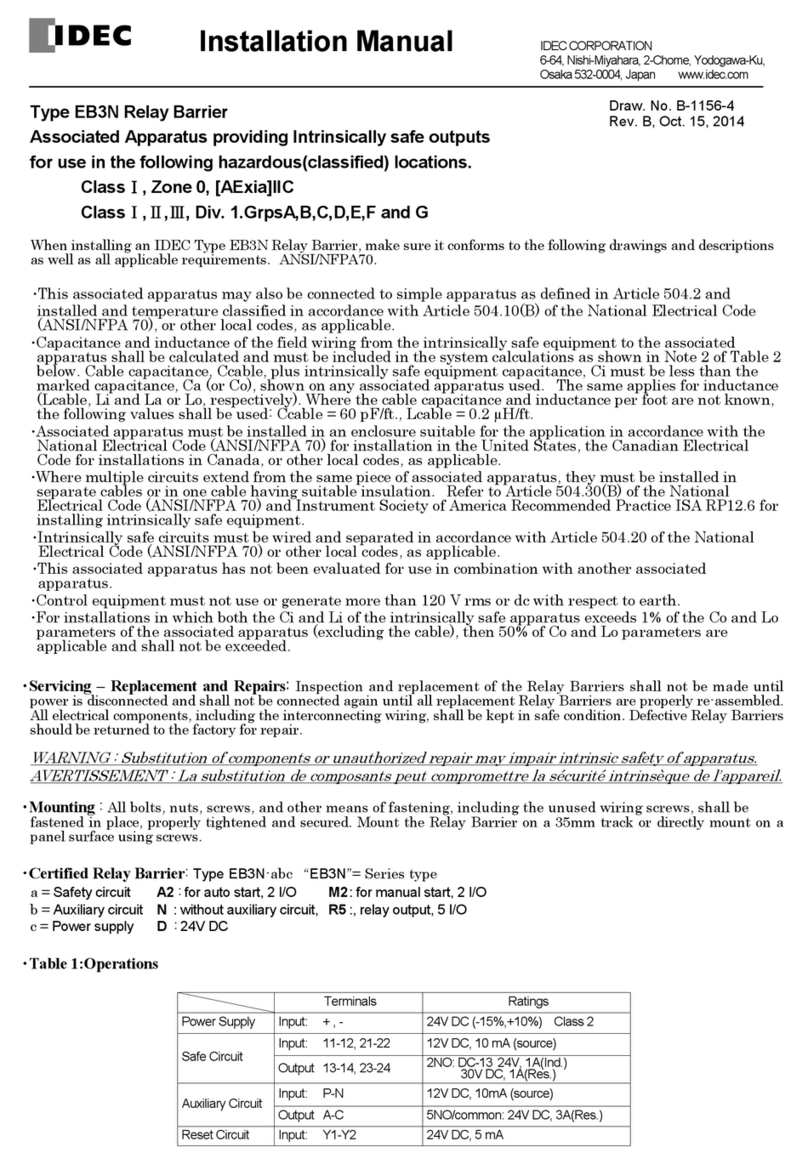
IDEC
IDEC EB3N User manual
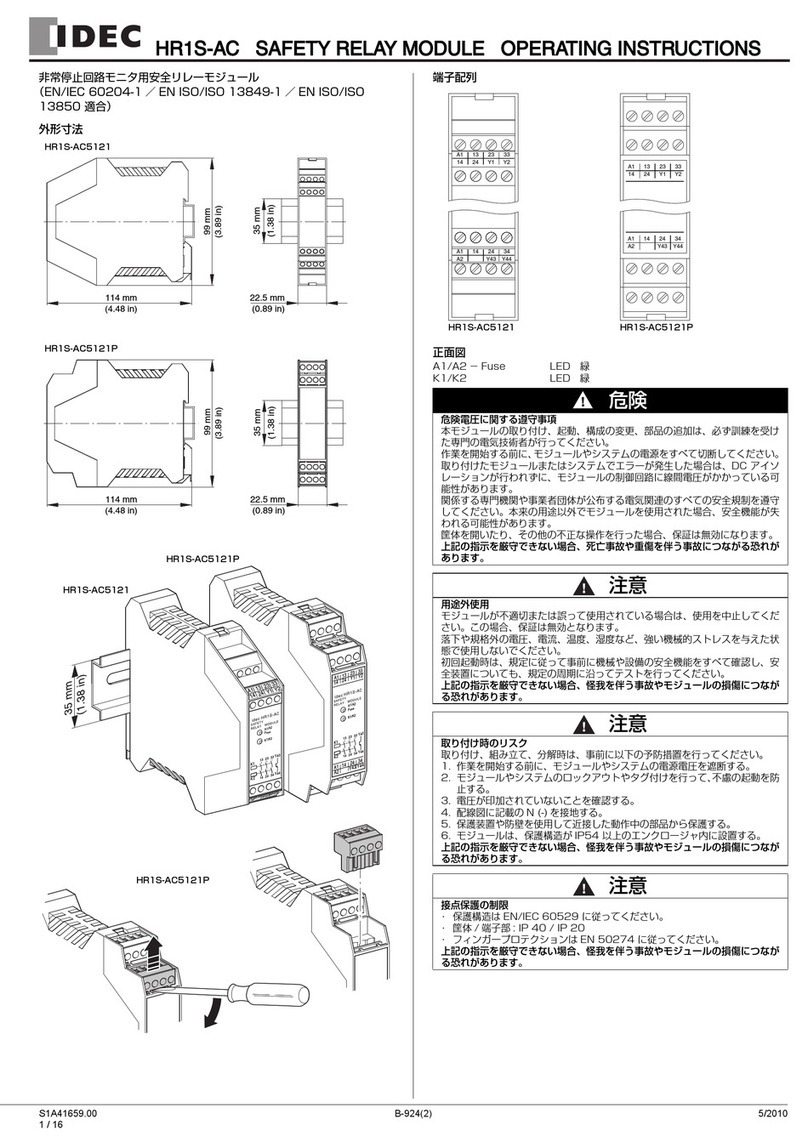
IDEC
IDEC HR1S-AC User manual