Ier Automatic Systems BL52 User manual

The information contained in this document is the property of Automatic Systems and is confidential. The recipient shall refrain from using it for any purpose other than the use of the products or the
execution of the project to which it refers, and from communicating it to third parties without Automatic Systems’ prior written agreement. Document subject to change without notice.
BL5x-MT-EN-13 page 1/56
BL 52 –BL 53
Electrical rising barrier
BL52 / BL53
This handbook is also valid for the customised equipment BLG76, which will be regarded as BL52 with netting.
OPERATING MANUAL
(translated from the French original notice)

The information contained in this document is the property of Automatic Systems and is confidential. The recipient shall refrain from using it for any purpose other than the use of the products or the
execution of the project to which it refers, and from communicating it to third parties without Automatic Systems’ prior written agreement. Document subject to change without notice.
BL5x-MT-EN-13 page 2/56
Revision page
Rev
Date
Written by
Checked by
Nature of the modification
02
Apr 05, 2007
MFy
SD + JB
- Replacement of D1 control board by AS1320
(version 3.6 of the program) => ch 3 added.
03
July 19, 2007
MFy
- Update of the balance table (ch. 5.5).
04
13 nov. 07
MFy
- Update the emergency operation (ch 2.5.2).
- Adapt to software version 4.1 of AS1320 control
board (ch 3).
- Update of the balance table (ch 5.5).
- Addition of balance spring fixing bolt inspection (ch 6).
- Update of the conformity certificates (ch 9).
05
June 09, 2008
MFy
- Adition of the note regarding BLG76 (p1).
- Control board: adapted to version 6.x of the program.
- Revision of the electric diagram & addition of
connector blocks assignment.
06
July 3, 2008
MFy
Ch. 7.1: adapt the detection loops pinning references
to electric drawings (X9-X11-X13-X14).
07
2009-08-03
MFy
Ch. 2.4: operation t° modification.
Ch. 9: EC certificate update.
08
2009-08-20
MFy
Ch. "Safety warnings" & "Installing the arm": add
warning.
09
2009-11-26
MFy
Ch.1: warning added regarding detection loops
installation.
Ch.3 adapted to control board v 6.2 (no functional
modification).
10
2010-01-04
MFy
EC certificate update.
11
2010-06-30
MFy
Electrical connections: add warning regarding
power network.
12
2010-11-04
MFy
AS1320 menus: translation corrected by RWK.
13
2011-01-05
MFy
Ch. 3.1: Download Chg Lvx parameters description
modified.

The information contained in this document is the property of Automatic Systems and is confidential. The recipient shall refrain from using it for any purpose other than the use of the products or the
execution of the project to which it refers, and from communicating it to third parties without Automatic Systems’ prior written agreement. Document subject to change without notice.
BL5x-MT-EN-13 page 3/56
Table of contents
1. SAFETY WARNINGS ...................................................................................................................................4
2. GENERAL.....................................................................................................................................................5
2.1. General view .................................................................................................................................................5
2.2. Access to internal components.....................................................................................................................6
2.3. Switching off the equipment..........................................................................................................................7
2.4. General conditions of use .............................................................................................................................8
2.5. Emergency operation....................................................................................................................................8
2.5.1. Opening or closing in case of power failure....................................................................................8
2.5.2. In case of breakdown......................................................................................................................9
3. AS1320 Control board...............................................................................................................................10
3.1. “PRDSTD – BL_xxx” Menu: Diagnosis and monitoring ...............................................................................12
3.2. "QUICK START" menu: quick configuration................................................................................................18
4. INSTALLATION..........................................................................................................................................26
4.1. Preliminary work on site..............................................................................................................................26
4.2. Handling and installing the unit...................................................................................................................27
4.3. Installing the round arm (BL52)...................................................................................................................28
4.4. Installing the oval arm (BL53) .....................................................................................................................29
4.5. Fixing the shrouds (BL52 only) ...................................................................................................................30
4.6. Dimensional views and arm segments........................................................................................................31
4.7. Levelling the barrier arm .............................................................................................................................33
4.7.1. Horizontal position "closed" ..........................................................................................................33
4.7.2. Vertical position "open".................................................................................................................34
4.8. Installing the tip support..............................................................................................................................35
4.8.1. Standard tip support......................................................................................................................35
4.8.2. Electromagnetic tip support ..........................................................................................................36
4.9. Electrical connections and initial power-up.................................................................................................37
4.10. Check-list ....................................................................................................................................................37
4.11. Scrapping the equipment............................................................................................................................37
5. ADJUSTMENTS AND TECHNICAL INTERVENTIONS.............................................................................38
5.1. Arm balance adjustment .............................................................................................................................38
5.1.1. Checking the arm balance adjustment..........................................................................................39
5.2. Belt tension adjustment...............................................................................................................................40
5.3. Safety torque limiter adjustment..................................................................................................................42
5.4. Limit switch adjustment...............................................................................................................................43
5.4.1. Electrical closing test ....................................................................................................................43
5.5. Changing the arm model.............................................................................................................................45
6. MAINTENANCE..........................................................................................................................................48
7. ELECTRICAL DRAWINGS.........................................................................................................................49
7.1. Control blocks assignment..........................................................................................................................50
8. INSTALLATION PLANS.............................................................................................................................53
9. EC CONFORMITY CERTIFICATES...........................................................................................................56

The information contained in this document is the property of Automatic Systems and is confidential. The recipient shall refrain from using it for any purpose other than the use of the products or the
execution of the project to which it refers, and from communicating it to third parties without Automatic Systems’ prior written agreement. Document subject to change without notice.
BL5x-MT-EN-13 page 4/56
1. SAFETY WARNINGS
WARNING:
YOUR RISING BARRIER TYPE BL52/BL53 COMPRISES A MECHANISM AND VARIOUS ELECTRICAL
COMPONENTS.ANY NEGLIGENCE DURING AN INTERVENTION IN THE MACHINE MAY SERIOUSLY
ENDANGER YOUR SAFETY.AS SOON AS YOU OPEN THE HOUSING,SWITCH OFF THE CIRCUIT BREAKER
(4:1)LOCATED BEHIND THE SIDE DOOR (1:2). BE CAREFUL IN HANDLING ANY INTERNAL ELEMENT
WHICH MIGHT BE UNDER POWER OR COULD BE SET IN MOTION.THE HOOD SHOULD BE REMOVED ONLY
IF YOU NEED TO REPLACE THE DRIVING SHAFT OR THE SPRING,ADJUST THE ARM BALANCE OR PROCEED
WITH THE MAINTENANCE.
WARNING: Never raise the arm brackets by means of the crank, without the boom arm fixed for
counterbalancing the spring: the arm brakets would swing violently, with serious injury
risks for the operators.
IMPORTANT INFORMATION CONCERNING HEALTH & SAFETY PROCEDURES
The introduction of a pedestrian or vehicle barrier product as manufactured by Automatic Systems places a
duty of responsibility for the safety and well-being of any user(s) or person(s) in close proximity to such
equipment. You are required therefore to observe and put in place appropriate safety measures, as deemed
necessary.
Pedestrian flow must be prohibited anywhere within a vehicle barrier passage-way, unless the movement of
the barrier system is clearly indicated, e.g. audible and/or visual signals, floor marking, notices, etc.
Access keys to any of the internal mechanisms can only be issued to authorised and qualified personnel,
aware of the relevant electrical and mechanical safety codes and regulations in force. All equipment
housing must be kept locked.
You have a legal obligation and responsibility to enforce good safety practices at all times. See also note below.
Note: In the countries of the European Union, the requirement 1.3.7.2 of the EC Machines Directive
prescribes that the pictogram for "Dangerous area* -- no entry for pedestrians" be affixed on both
sides of the equipment (* within 1 meter of the barrier arm in its closed position).
black
white
red
The installation of detection loops must be validated by qualified personnel who will determine their optimal
configuration (adapted to vehicle type and passageway).
WARNING: The risk of injury exists for people when using standard detection loops; they can incorrectly detect
trucks and (motor)bikes and close the gate on them!

The information contained in this document is the property of Automatic Systems and is confidential. The recipient shall refrain from using it for any purpose other than the use of the products or the
execution of the project to which it refers, and from communicating it to third parties without Automatic Systems’ prior written agreement. Document subject to change without notice.
BL5x-MT-EN-13 page 5/56
2. GENERAL
2.1. General view
1:12 Commercial identification plate
Legend:
1:2
1:11 Emergency crank handle
1:9 Stainless steel heater
1:8 Fixing brackets
1:7 Housing
1:6 Hood
1:5 Arm bracket (BL53)
1:4 Arm bracket (BL52)
1:3 Safety locks with keys
1:2 Right-hand door
1:4
1:5
1:8
1:12
1:1
1:3
1:6
1:7
1:9
1:1 Left-hand door
1:11
1:10
1:10 Emergency crank hole

The information contained in this document is the property of Automatic Systems and is confidential. The recipient shall refrain from using it for any purpose other than the use of the products or the
execution of the project to which it refers, and from communicating it to third parties without Automatic Systems’ prior written agreement. Document subject to change without notice.
BL5x-MT-EN-13 page 6/56
2.2. Access to internal components
2:1 Control board with cover
2:2 Control board guides
2:3 Driving belt
2:4 Spring
2:5 Limit switches
2:6 Serial plate
2:7 Crank switch
2:8 Motor
2:9 Gearbox
2:10 Driving rod
2:11 Heater
2:12 Fixing latches
2:13 Driving shaft
2:14 Abutment

The information contained in this document is the property of Automatic Systems and is confidential. The recipient shall refrain from using it for any purpose other than the use of the products or the
execution of the project to which it refers, and from communicating it to third parties without Automatic Systems’ prior written agreement. Document subject to change without notice.
BL5x-MT-EN-13 page 7/56
2.3. Switching off the equipment
As soon as you open the housing, switch off the power by switching off the magneto-thermal circuit breaker
(4:1) located behind the side door (1:1).
Fig. 4
4:1 Main circuit breaker
4:2 Ground terminal
4:2
4:1

The information contained in this document is the property of Automatic Systems and is confidential. The recipient shall refrain from using it for any purpose other than the use of the products or the
execution of the project to which it refers, and from communicating it to third parties without Automatic Systems’ prior written agreement. Document subject to change without notice.
BL5x-MT-EN-13 page 8/56
2.4. General conditions of use
Your rising barrier type BL52/BL53 has been designed to operate in any kind of climatic environment,
from -35°C to +50C (thanks to heating resistance), with up to 95% of relative humidity.
2.5. Emergency operation
The following instructions are to be given to the installation supervisor.
2.5.1. Opening or closing in case of power failure
-- Insert the emergency crank handle (1:11) into the crank hole (1:10). A safety device automatically
switches off the power supply, thus eliminating any risk of accident in case the power supply
returns.
-- Turn the crank clockwise to open the barrier and counter' clockwise to close the barrier
-- When the arm is in the horizontal or vertical position, keep turning the crank to lock the barrier
mechanically.

The information contained in this document is the property of Automatic Systems and is confidential. The recipient shall refrain from using it for any purpose other than the use of the products or the
execution of the project to which it refers, and from communicating it to third parties without Automatic Systems’ prior written agreement. Document subject to change without notice.
BL5x-MT-EN-13 page 9/56
2.5.2. In case of breakdown
The obstacle does
not move
Liquid crystal display is
off
Check the general power supply.
Check the voltage on the circuit breaker (4:1),
and check if this late is on.
Check the connection of the control wires
referring to the electrical diagram, as well as
their tightening.
Check the state of the fuses (5:1, p10) on the
electrical control board.
Check that the green LEDs are lit on the logic
control board (5:6, p10).
- If not, check the general fuses (5:1, p10).
- If so, check that the logic board is not in
programming mode (cable RJ45, plugged in
socket 5:5, p10).
Liquid crystal display is
on
Check that the red LEDs (other than the
analogue output ones) on the logic control
board are on (5:6, p10).
- If not, cut the supply voltage and remove the
control terminal blocks (5:6, p10) (on the
AS1320 and AS1321, if present). Turn the
power back on and then check whether the
red LEDs are on. If that is the case, there is
a short circuit in one of the control terminal
blocks (5:6, p10). In order to reactivate the
outputs, the logic board has to be turned on
again.
- If so, refer to the displayed breakdowns
(“PRDSTD – BL_xxx“ menu “Log”/”Close
Status”/”Open Status”).
Check the defects on the
frequency inverter
Refer to AS1320 control board manual.
The obstacle stops
during movement
OP, CL and STOP
commands have no
effect.
Opening and/or closing limit switch is defective or
badly connected.
Note: If the trouble persists after you carry out the checks above mentioned, call your local Automatic
Systems agent.

The information contained in this document is the property of Automatic Systems and is confidential. The recipient shall refrain from using it for any purpose other than the use of the products or the
execution of the project to which it refers, and from communicating it to third parties without Automatic Systems’ prior written agreement. Document subject to change without notice.
BL5x-MT-EN-13 page 10/56
3. AS1320 Control board
(Extract from AS1320 technician manual)
5:1. Fuses
5:2. Stabilised power supply indicator light
5:3. Menu display screen
5:4. Menu navigation keys
5:5. RJ45 communication connector
5:6. In/Out control connector blocks
5:7. 5 green LEDs (lit when the board is on)
5:8. Connectors for presence detectors (for inductive loops)
5:6
5:5
5:4
5:3
5:2
5:1
5:7
5:8

The information contained in this document is the property of Automatic Systems and is confidential. The recipient shall refrain from using it for any purpose other than the use of the products or the
execution of the project to which it refers, and from communicating it to third parties without Automatic Systems’ prior written agreement. Document subject to change without notice.
BL5x-MT-EN-13 page 11/56
The control board is the interface between the user and the barrier, which manages all the latter’s actions,
including any possible options.
Note: Hereinafter are presented only the functions accessible in Simplified mode and sufficient for daily
use of the equipment.
For a detailed description of all the functions, their parameter setting, etc, please refer to the manual
dedicated to the board (available on request)..
Navigation in the menus of the display screen is based on a pull-down menu architecture on 3 levels:
MENUS ↔ PARAMETERS ↔ VALUES.
Moving from one level to another is achieved via the ◄ ► keys and navigation inside those levels by means of
the ▲ ▼ keys (press for a few seconds to go from the at-rest screen to another menu).
Note: the second column in the tables below provides the parameter default values as they are entered during
manufacturing of the control board.
Nevertheless, as each equipment has been specifically adjusted in our workshops, the values actually present on
the board may differ slightly.
Menus are displayed in capital
letters on the top line, starting
with the first character of the
LCD.
Hold ▲ or ▼ for a few seconds to
leave the PRDSTD screen and
access the other menus.
Only the first letter of each word in
the parameters is a capital. They are
displayed on the top line starting with
the second character of the LCD (i.e.,
there is a space in front). At the end
of the top line, the parameter unit is
displayed if there is one.
A question mark (?) preceding the
parameter indicates that it is ready to be
modified.
The current value of the parameter appears
on the second line.
A star (*) below a parameter indicates that it
is the default value (set in the factory).
To validate a modification, press the OK
key.
Store the modifications to avoid
them being lost in the event of a
power outage ("QUICK START"
"MEMORY"
"Save")
Menus
Parameter
s
Arm Length
Barrier Type
Arm Type #
? Arm Length
* 3m00
? Arm Length
2m50
? Arm Length
2m00
? Arm Length
6m00
? Arm Length
3m50
? Arm Length
4m00
? Arm Length
4m50
? Arm Length
5m50
? Arm Length
5m00
CANCEL
VALIDATE
or
Values
QUICK START
DATE & TIME
CL REGULATION
PRDSTD - BL_xxx
TIMING
OUTPUT FUNCTION
SENSOR FUNCTION
OK

The information contained in this document is the property of Automatic Systems and is confidential. The recipient shall refrain from using it for any purpose other than the use of the products or the execution of the project to which
it refers, and from communicating it to third parties without Automatic Systems’ prior written agreement. Document subject to change without notice.
BL5x-MT-EN-13 page 12/56
3.1. “PRDSTD – BL_xxx” Menu: Diagnosis and monitoring
This screen appears when the unit is turned on and when there has not been any navigation through the menus in Simplified
mode for 100 seconds.
Parameter
Values
Description
OK key: (only within this menu (*) and when no other parameter
is selected): command for opening and closing the obstacle.
OK during opening: without effect.
OK during closing: inversion (= opening).
OK maintained: oscillating movement around the opening limit
switch: the obstacle opens, starts closing, opens again, etc.
(*) Warning: in QUICKSTART menu, validating passage from
Extended to Simplified menus through the OK key causes also
an opening or closing movement of the arm, even if a presence
is detected by the Presence sensors.
Note: When the operating mode is configured as 1 contact (see
the Exploitation parameter in the QUICK START menu), the
obstacle closes automatically when the opening limit switch is
detected.
Left key (◄): Change the menu display language with each
touch.
EN = English
FR = Français
NL = Nederlands
DE = Deutsch
ES = Español
IT = Italiano
SV = Svenska
Select the language using the OK key or allow it to change
automatically after a few seconds, following which all of the
preceding parameter modifications (including the language) will
be saved in MEM1.
Soft. Version
Display the software version used by the control unit, following
format type –evolution –version –revision –minor index of the
application.
The descriptions included in this chapter correspond to versions
00-00-06-rr-00.
Program name
Date (DD/MM)
Time (hh:mm)
Choose a language
using the ◄ button

The information contained in this document is the property of Automatic Systems and is confidential. The recipient shall refrain from using it for any purpose other than the use of the products or the execution of the project to which
it refers, and from communicating it to third parties without Automatic Systems’ prior written agreement. Document subject to change without notice.
BL5x-MT-EN-13 page 13/56
Parameter
Values
Description
Log
Display of the last 100 events (use ► the ▲ and keys to view
preceding events).
For the first two seconds, the event number (00 for the last
event recorded (= most recent), 01 for the preceding event, and
so on), as well as the date (year-month-day) and time (hours-
minutes-seconds) of creation are displayed.
In the next two seconds, the event description is displayed.
For example:
2 s
Log
00 060324 235034
On 24 March 2006 at 23 hours
(11 p.m.) 50 minutes and 34
seconds…
2 s
Log
Out Of Service
…the apparatus was put out of
service.
2 s
Log
01 060324 235034
View the preceding message
(01) using the ►▲ keys…
2 s
Log
Open Time Out
…we observe that it was put out
of service due to a time out
while opening.
Note: If no error message is displayed when the machine fails,
refer to the Troubleshooting chapter.
Power Up
Power was turned on.
Power Down
Power was turned off.
Short Circuit
Short circuit of the control board outputs (connector blocks). The
short circuit is declared and the equipment put Out of Service
only after 3 unsuccessful reactivation tries within the 2.5
seconds following a voltage drop in the 24V power supply (this
is to avoid putting it out of service at inopportune moments, as
for example during a network changeover to an emergency
generator).
If one of the outputs short circuits, all of them become inactive
and the control board must be powered up again for the outputs
to be reactivated.
Open Time Out
Time out during opening: the time allocated for opening was
exceeded (TIMING menu, OpenTimeOut parameter).
Close Time Out
Time out during closing: the time allocated for closing was
exceeded (TIMING menu, CloseTimeOut parameter).
Close Retries
Allotted number of trials to close have been executed (as
defined in the TIMING menu).
Arm Swing Off
Arm detected out of its support jaw (see the Arm Swing Off
parameter in the OPTIONS menu).
If the message continues to be displayed after the arm is
rehinged, check the status of the SW arm presence sensor and
its fastening.
Out Of Service
Apparatus out of service. This may be caused by the following
events:
1) Time out during opening (see Open Time Out
message).
2) Time out during closing (see Close Time Out error) +
allotted number of tries to close have been executed
(see Close Retries message).
3) Arm is unhinged (see Arm Swing Off message).
4) Locking or unlocking failure of the BL4x (see Unlock
BL4x Er message).
5) Defect of the frequency inverter.

The information contained in this document is the property of Automatic Systems and is confidential. The recipient shall refrain from using it for any purpose other than the use of the products or the execution of the project to which
it refers, and from communicating it to third parties without Automatic Systems’ prior written agreement. Document subject to change without notice.
BL5x-MT-EN-13 page 14/56
Parameter
Values
Description
Time Adjust
Modification of the date and time.
Access Level Chg
Change to the access level.
OOS Restore
Apparatus put back in service (after it has been out of service)
=> see the RestartMode parameter under the OPTIONS menu.
Test Intensive
Activation of the intensive test.
Lock Open
The Lock Open command of the test mode has been activated.
Lock Close
The Lock Close command of the test mode has been activated.
Safety Arm
Safety arm (only with the rubber protection profile option:
Rubber strip that detects when the arm makes contact with a
vehicle).
Sw Manual
Frequency converter power cut-off in order to prevent any
movement of the obstacle in case of:
Crank presence sensor activation (available on some
equipment for manual handling of the obstacle),
Door/hood opening sensors activation (option on
some equipment).
Reset Sensor Init
Change of the positioning sensor type (cf. Positioning parameter
of QUICKSTART menu).
LS Fault
Both opening and closing limit switches are activated
simultaneously or badly connected during 100 ms, while
Positioning parameter of the QUICKSTART menu is set to Limit
Switches.
Reset LS Fault
Limit switch problem resolved (see LS Fault error).
Analog. Fault
The analogue sensor gives 0 or 1023 during minimum 100 ms.
This may result from a defective wiring, a wrong positioning of
the sensor in front of its cam, a defective sensor, etc.
OP Power Cut
Unlocking of the obstacle following an outage of the supply
voltage (if QUICK START ► Power Fail OP ►ON).
OP Power Blip
Unlocking of the obstacle following a micro-outage of the supply
voltage (the voltage drops to 0 V during a few milliseconds) (if
QUICK START ► Power Fail OP ►ON).
In this state, the obstacle is STOPPED but still operational,
because the supply voltage has returned. The apparatus waits
for the next command to execute a movement.
CoolingMotor ON
Start-up of the motor cooling fan.
Note: This message is only displayed if the Cooling –Log
(below) is ON.
CoolingMotor OFF
Stopping of the fan that cools the motor.
Note: This message is only displayed if the Cooling –Log
(below) is ON.
Stop Time Out
Elapse of the delay defined under the Max Stop parameter of
the TIMING menu for the regulation of the obstacle position with
regard to the Stop.
Download Chg Lv1
Downloading a version of the control board program that differs
from the one previously installed.
As the difference is of level 1 (minor index modification or
revision), the parameters continue operate with their value
saved in MEM1.

The information contained in this document is the property of Automatic Systems and is confidential. The recipient shall refrain from using it for any purpose other than the use of the products or the execution of the project to which
it refers, and from communicating it to third parties without Automatic Systems’ prior written agreement. Document subject to change without notice.
BL5x-MT-EN-13 page 15/56
Parameter
Values
Description
Download Chg Lv2
Downloading a version of the control board program that differs
from the one previously installed.
As the difference is of level 2 (modification of the version or the
evolution), all of the parameters are returned to their default
values.
WARNING: it is then necessary to set the parameters to the
actual configuration of the equipment and to save them in
MEM1.
Note: it would be wise to keep the parameters values before
changing the program version: Communication parameter
Extract Param (Technician level access).
Download Chg Lv3
Downloading a version of the control board program that differs
from the one previously installed.
As the difference is of level 3 (modification of the type), all of the
parameters are returned to their default values and the counters
are reset to 0.
WARNING: it is then necessary to set the parameters to the
actual configuration of the equipment and to save them in
MEM1.
Note: it would be wise to keep the parameters values before
changing the program version: Communication parameter
Extract Param (Technician level access).
Reset Counters
Counters reset to zero following the download of a different
program version of level 3 (see Download Chg Lv3).
Curve 229Std
Change in the type of barrier: selection of curve 229 standard
(Barrier Type parameter under the QUICK START menu).
Curve 229Highway
Change in the type of barrier: selection of curve 229 highway
(Barrier Type parameter under the QUICK START menu).
Curve 1x-2x-3x-5x
Change in the type of barrier: selection of curve for BL16, BL32,
BL33, BL52, BL53 (Barrier Type parameter under the QUICK
START menu).
Curve BLG77
Change in the type of barrier: Selection of curve BLG77 (Barrier
Type parameter under the QUICK START menu).
Curve Special
Change in the type of barrier: selection of the Special curve
(OPTIONS menu) for operation according to the OP
REGULATION and CL REGULATION menus.
Curve BL223
Change in the type of barrier: Selection of curve BL223 (Barrier
Type parameter under the QUICK START menu).
Curve BL40 AVR
Change in the type of barrier: Selection of curve BL40 AVR
(Barrier Type parameter under the QUICK START menu).
Curve BL40 SR
Change in the type of barrier: Selection of curve BL40SR
(Barrier Type parameter under the QUICK START menu).
Curve BL41 AVR
Change in the type of barrier: Selection of curve BL41AVR
(Barrier Type parameter under the QUICK START menu).
Curve BL41 SR
Change in the type of barrier: Selection of curve BL41SR
(Barrier Type parameter under the QUICK START menu).
Curve BL43 AVR
Change in the type of barrier: Selection of curve BL43AVR
(Barrier Type parameter under the QUICK START menu).
Curve BL43 SR
Change in the type of barrier: Selection of curve BL43SR
(Barrier Type parameter under the QUICK START menu).
Curve BL44 AVR
Change in the type of barrier: Selection of curve BL44AVR
(Barrier Type parameter under the QUICK START menu).
Curve BL44 SR
Change in the type of barrier: Selection of curve BL44SR
(Barrier Type parameter under the QUICK START menu).

The information contained in this document is the property of Automatic Systems and is confidential. The recipient shall refrain from using it for any purpose other than the use of the products or the execution of the project to which
it refers, and from communicating it to third parties without Automatic Systems’ prior written agreement. Document subject to change without notice.
BL5x-MT-EN-13 page 16/56
Parameter
Values
Description
Curve BL46 AVR
Change in the type of barrier: Selection of curve BL46AVR
(Barrier Type parameter under the QUICK START menu).
Curve BL46 SR
Change in the type of barrier: Selection of curve BL46SR
(Barrier Type parameter under the QUICK START menu).
Curve RSB 70&71
Change in the type of equipment: Selection of curve RSB 70&71
(Barrier Type parameter under the QUICK START menu).
Unlock BL4x Er
Only with locking of the arm option for BL4x. The inductive
sensor has not detected the release of the lock within the 3
seconds following the open or close request: check whether the
locking pin is pressing on the locking clips, preventing them
form opening, or whether the sensor is defective.
Close Status
Cases when the obstacle is prevented from closing during a
close request:
OK
Normal closure.
PS1 Activated
A sensor (loop/cell) detects a presence or a fault in the
circuit. In the latter case:
Check whether the sensor is plugged into the
corresponding connector and whether it is functioning
properly.
Check whether the sensor is properly connected.
Check whether the sensors are programmed correctly
(SENSOR FUNCTION menu).
PS2 Activated
PS3 Activated
PS4 Activated
Lock OP Hold
Check why the Lock Open command is being maintained on the
control board connector block.
Safe Arm Activ
Activation of the Safety Arm sensor (only with the rubber
protection profile option: rubber strip that detects when the
arm makes contact with a vehicle):
Check whether the arm safety sensor is functioning
properly.
Check whether the Safety Arm parameter is
programmed correctly (Options menu).
PWF Open Activ
Setting of the PWF Open Activ parameter of the OPTIONS
menu to ON, that is to say that during activation the obstacle
opens and waits for the activation of a close or lock-close
command.
Note: the closure loops are not taken into account for closing in
this case.
Lock Open LCD
The Test Mode parameter of the TEST menu is not set to
Deactivated.
Delay Befor CL
Wait for the delay programmed under the Delay Befor. CL
parameter under the TIMING menu to elapse.
Open Cmd Hold
Check why the open command is being maintained on the
control board connector block.
Stop Cmd Hold
Check why the stop command is being maintained on
the control board connector block.
Check whether the Stop Cmd parameter is
programmed correctly (Options menu).
Reader A Hold
Check why the Reader A command is being maintained on the
control board connector block.

The information contained in this document is the property of Automatic Systems and is confidential. The recipient shall refrain from using it for any purpose other than the use of the products or the execution of the project to which
it refers, and from communicating it to third parties without Automatic Systems’ prior written agreement. Document subject to change without notice.
BL5x-MT-EN-13 page 17/56
Parameter
Values
Description
Reader B Hold
Check why the Reader B command is being maintained on the
control board connector block
Position Fail
The type of sensor selected is Analogue Sensor (QUICK START
► menu Positioning); nevertheless, the obstacle still has to be
activated (► Activate Motor? ► OK).
Counter CR
The reader counter (see the OPTIONS menu
Counter CR) is greater than zero.
Or the timing for no passage is other than zero (see
the TIMING menu No Passage).
Open Status
Cases when the obstacle is prevented from opening during a
request to open.
OK
Normal opening.
Lock CL Hold
Check why the Lock CL command is being maintained on the
control board connector block.
Lock Close LCD
The Test Mode parameter of the TEST menu is not set to
Deactivated.
Delay Befor OP
Wait for the time programmed under the Delay Bef. OP under
the TIMING menu to elapse.
Stop Cmd Hold
Check why the close order is being maintained on the
control board connector block.
Check whether the Stop CMD parameter is
programmed correctly (Options menu).
Arm ELV Locked
Check whether the detector of the unlocking of the
electrically locking (ELV) tip is functioning properly.
Check whether the Arm parameter in the OPTIONS
menu is programmed correctly.
Arm ELV Detect
Check whether the detector sensing the presence of the
arm is functioning properly on the control board connector
block.
Position Fail
The type of sensor selected is Analog. Sensor (QUICK START
menu ►Positioning); nevertheless, the obstacle still has to be
activated (► Activate Motor? ►OK).
Counter 1
0 to 99,000,000
(0 by default)
Total number of manoeuvres executed by the obstacle since it
was first put into service.
Counter 2
0 to 99,000,000
(0 by default)
Representation of counter 1, with the possibility of resetting it to
zero.
Reset counter 2
Counter 2 reset to zero.
OFF (by default)
No resetting.
ON
Request to reset to zero.
Done
Message is displayed for 1 second when the counter has been
reset to zero.

The information contained in this document is the property of Automatic Systems and is confidential. The recipient shall refrain from using it for any purpose other than the use of the products or the execution of the project to which
it refers, and from communicating it to third parties without Automatic Systems’ prior written agreement. Document subject to change without notice.
BL5x-MT-EN-13 page 18/56
3.2. "QUICK START" menu: quick configuration
This menu inspects the parameters that have to be configured before the equipment may be used.
Parameter
Values
Description
PS1 Function
0 (by default) to 7
Definition of the mode of operation of Presence
Sensor 1: see table below.
PS 2 Function:
0 (by default) to 7
Definition of the mode of operation of Presence
Sensor 2: see table below.
By default, the presence sensors are deactivated.
Therefore, in order to ensure that their safety functions are operational, it is
indispensable that the parameters for each of the presence sensors used be set.
closed obstacle
open obstacle
Closing obstacle
Sensor function
Action upon
arrival in the
sensor’s field
Action upon
leaving the
sensor’s field
Action upon
arrival in the
sensor’s field
+
Action upon
leaving the
sensor’s field
0
Deactivated
**
-
-
1
Opening
Opening**
Closing*
Opening
+
Closing*
2
CL_Stop+CL
**
Closing***
Stop
+
Closing
3
CL_OP+CL
**
Closing***
Opening
+
Closing
4
Nothin_Stop+CL
**
-
Stop
+
Closing
5
Nothing_OP+CL
**
-
Opening
+
Closing
6
Nothing_Stop
**
-
Stop
7
Nothing_OP
**
-
Opening
Incompatible
This message is displayed for 1 second if the selected operating mode for the sensor
is not compatible with the exploitation mode (parameter below). See the table of
incompatible modes here under.
*: Automatic closure only if the preceding opening was initiated by detection and not if presence is detected by another sensor.
Notably, if there is a power outage when the obstacle is open, the obstacle will not close automatically when the power is
brought back (a close command must be executed).
Warning: The presence sensor operating in “Open” mode may not be placed under the arm, because it is it is not secured, in
contrast to the other modes: a Lock Close command has priority for it (see the "Exploitation" parameter below) and could
cause the arm to close on a vehicle.
**: Opening is possible using the commands present on the control board's connector blocks: open command, reader command,
and Lock Open command.
***: If passage is detected while the obstacle is Locked Open, closure will take place when the Lock Open command is
deactivated.
: With regard to the underlined values, a close command must be executed to close the obstacle when it is open. The safety
function is only activated during the closing movement of the obstacle.
Note: the installation of 2 loops on PS1 and PS2 requires the use of a double detector since PS1 and PS2 are on the same
connector.
Note: 2 supplementary Presence Sensor (PS3 and PS4) are available through extended menu "SENSOR FUNCTION".
Note: the information regarding the sensor status (1/0) is always available (for each function mode) through extended menu
"OUTPUT FUNCTION".
Warning: When the power is turned on, the detectors (DP) measure the state of the loops and initialize the reference level with
regard to their environment. Hence, if a vehicle is present on the loop during activation, it will not be detected and the loop will
give the order to close (in modes 1, 2 and 3 only)!

The information contained in this document is the property of Automatic Systems and is confidential. The recipient shall refrain from using it for any purpose other than the use of the products or the
execution of the project to which it refers, and from communicating it to third parties without Automatic Systems’ prior written agreement. Document subject to change without notice.
BL5x-MT-EN-13 page 19/56
Parameter
Values
Description
Positioning
Definition of the type of sensor used to position the obstacle.
Limit Switches
(by default)
To be selected if the open/close position of the obstacle is
determined by limit switches.
Analog. Sensor
To be selected if the position of the obstacle is determined
by an analogue sensor.
The analogue position sensor measures the distance
separating it from a spiral cam located on the shaft that
transmits the movement of the obstacle’s motor, which
means that the angular position of the obstacle is known at
all times. Also, see the Min Sensor Max parameter below.
Manual Switch
This message is displayed if it is not possible to activate the
analogue sensor, as per one of these cases:
The crank presence detector (only present on some
equipments) is engaged.
=> Remove the crank so that the motor may be engaged.
If the equipment does not have a crank presence
detector, the circuit may have been cut.
=> link the corresponding connections.
Activate Motor?
Pushing the OK key within 5 seconds launches the analogue
sensor activation procedure (see below) and the movement
of the obstacle!
The Barrier Type and Arm characteristics
must be selected BEFORE initializing the
analogue sensor. Otherwise, rough
movements of the arm can occur with risk
of injury for the personnel and the equipment.
=> Navigate through the menus by means of the upper
key ().
Search LSO…
The obstacle opens to look
for its open limit position.
The obstacle is moving
during this phase!
Search LSC…
The obstacle closes to look
for its close limit position.
Init. Passed
This is displayed if the open and closed limit values have
been recorded.
The analogue sensor is then operational.
The message disappears after 5 seconds or if the OK key is
pushed.
IMPORTANT: Save the values in MEM1 or MEM2
(MEMORY menu).
Adjust Sensor
Activation failed because the analogue sensor was not
properly positioned => adjust it (closer or further away from
the cam) so the measurement is included in the working
range (= between the min. and the max. set in the Min
Sensor Max parameter below).

The information contained in this document is the property of Automatic Systems and is confidential. The recipient shall refrain from using it for any purpose other than the use of the products or the
execution of the project to which it refers, and from communicating it to third parties without Automatic Systems’ prior written agreement. Document subject to change without notice.
BL5x-MT-EN-13 page 20/56
Parameter
Values
Description
Value 0 Detect
Activation failed because the analogue sensor returned a
measurement of zero.
As this value is invalid, check:
the sensor’s wiring (in the sensor as well as on the
control board's connector blocks);
whether is sensor is too close to the cam;
whether the sensor is functioning: LED on the sensor is
illuminated and the value measured is displayed in the
Min Sensor Max parameter below.
Barrier Type
Definition of the equipment type; this allows the program to
automatically modify the opening and closing motor power
curves.
Note 1: The equipment type is stated on the reference plate,
inside the housing.
Note 2: to change from barrier solution 1 or 2 to solution 3 or
4 (illustration below), 2 phases of the motor have to be
inverted.
229 Standard
(by default)
Parameter to select for a BL229 Standard.
229 Highway
Parameter to select for a BL229 Highway.
1x –2x –3x –5x
Parameter to select for a BL16, BL32, BL33, BL52, BL53,
BP56.
BLG77
Parameter to select for a BLG77.
BL 223
Parameter to select for a BL223.
RSB 70 & 71
Parameter to select for a RSB 70 or RSB 71.
BL 40 SR
Parameter to select for a BL40 without automatic opening of
the arm in case of power cut.
BL40 AVR
Parameter to select for a BL40 with automatic opening of the
arm in case of power cut.
BL 41 SR
Parameter to select for a BL41 without automatic opening of
the arm in case of power cut.
BL 41 AVR
Parameter to select for a BL41 with automatic opening of the
arm in case of power cut.
BL 43 SR
Parameter to select for a BL43 without automatic opening of
the arm in case of power cut.
BL 43 AVR
Parameter to select for a BL43 with automatic opening of the
arm in case of power cut.
BL 44 SR
Parameter to select for a BL44 without automatic opening of
the arm in case of power cut.
BL44 AVR
Parameter to select for a BL44 with automatic opening of the
arm in case of power cut.
BL 46 SR
Parameter to select for a BL46 without automatic opening of
the arm in case of power cut.
solution 1 solution 2 solution 3 solution 4
door
door
door
door
This manual suits for next models
2
Table of contents
Popular Control System manuals by other brands
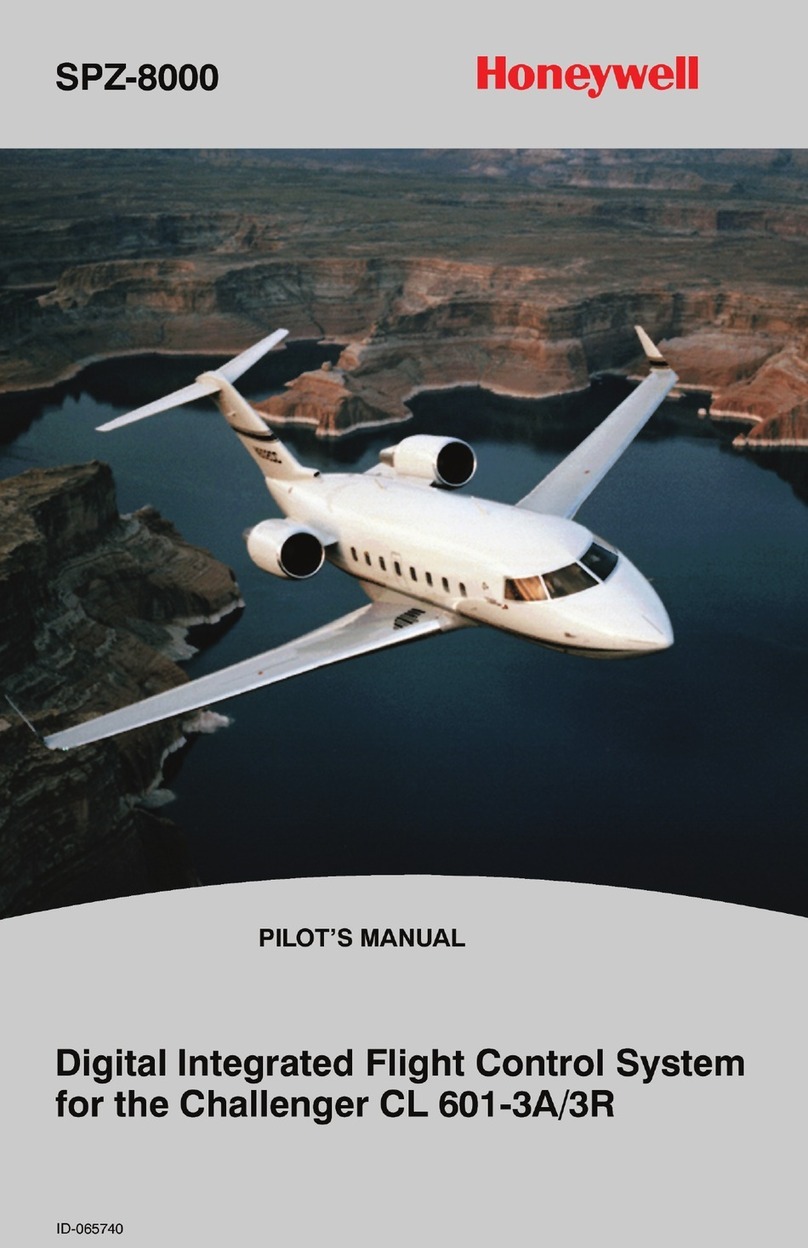
Honeywell
Honeywell SPZ-8000 Pilot's manual
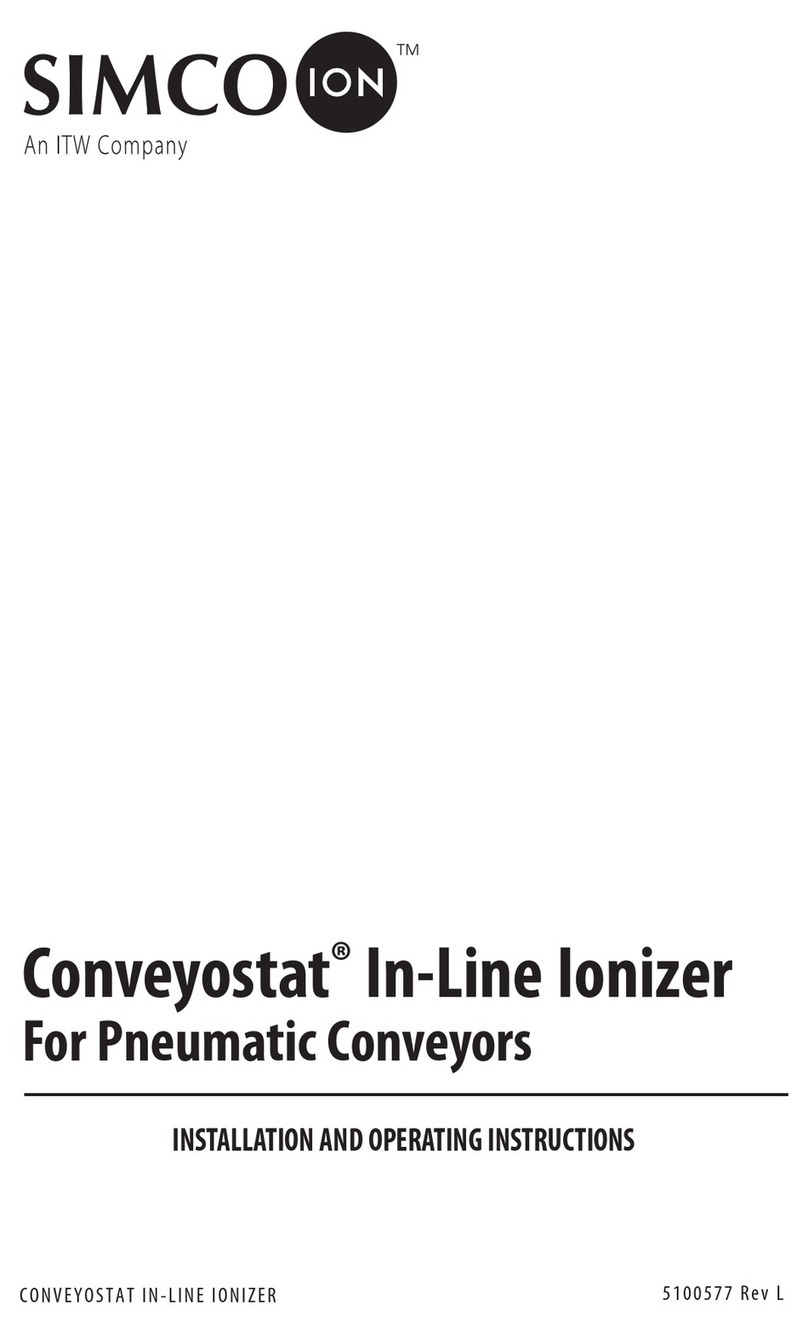
ITW
ITW Simco-Ion Conveyostat Installation and operating instructions

Viessmann
Viessmann VITOCROSSAL CI operating instructions
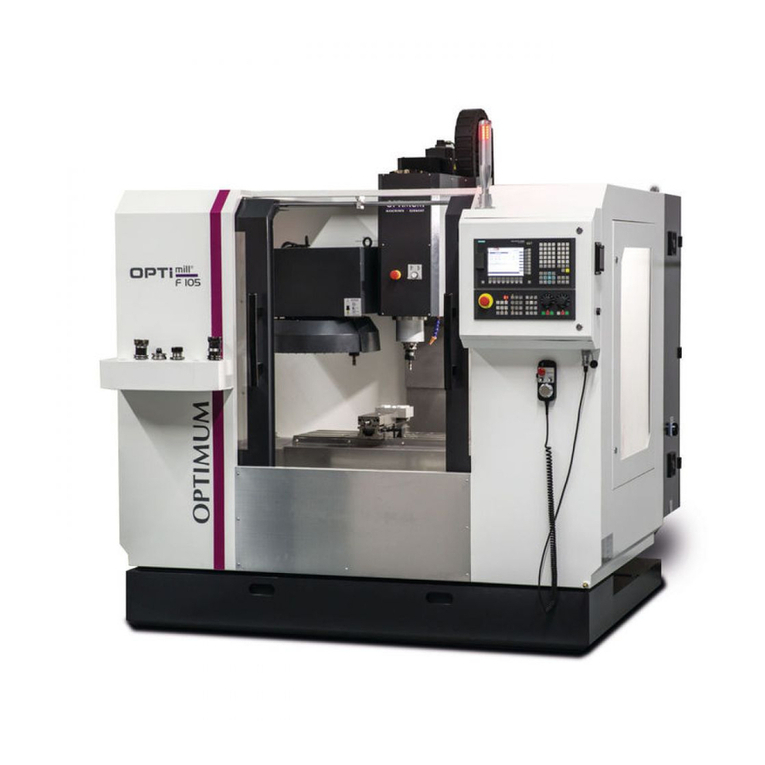
OPTIMUM Maschinen
OPTIMUM Maschinen OPTImill F 80 operating manual
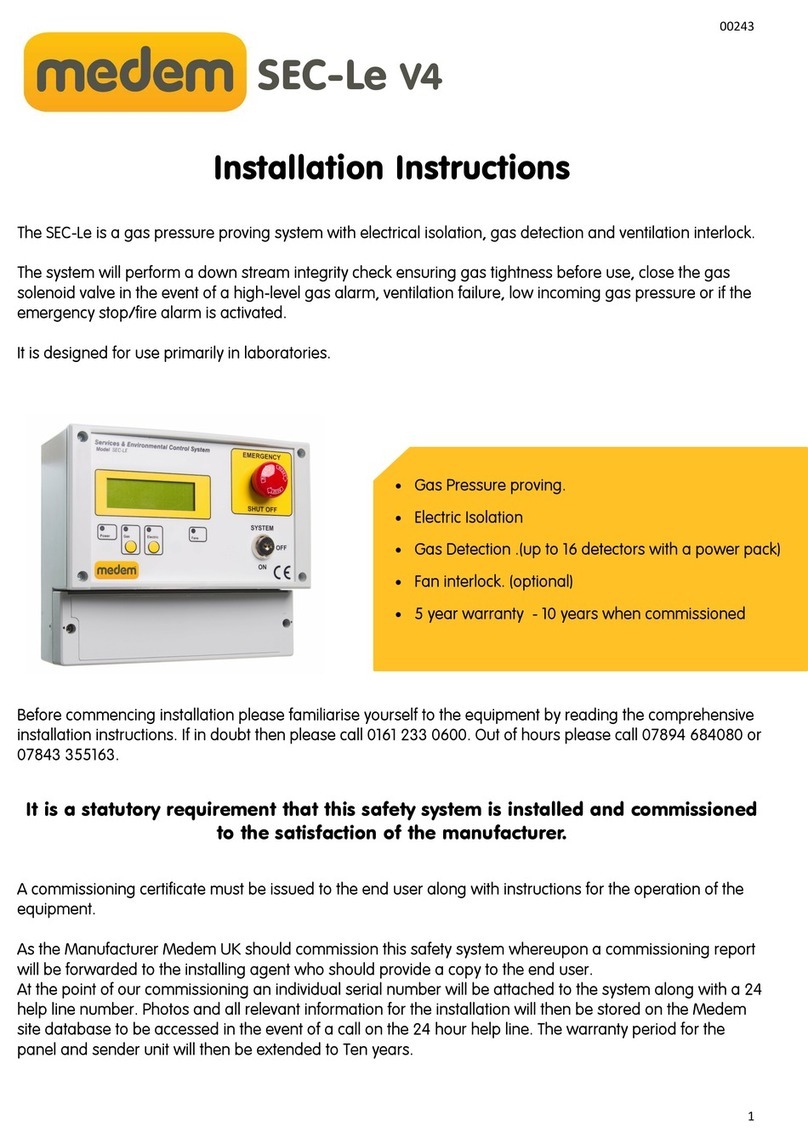
Medem
Medem SEC-Le V4 installation instructions

Vestil
Vestil PRAIL-102 quick start guide