IMKO TRIME-GW Series User manual

Manual
TRIME®-GW Line
More information:
www.imko.de
Moisture Sensor Experts

2
Thank you for purchasing this IMKO product
This manual is an original operating manual of the manufacturer.
The described instructions for use and commissioning are part of the products described and must be kept for
future installation or use.
Important!
Please read these instructions carefully to accomplish optimum results with your moisture probe. Please contact
your authorized dealer, distributor or service center for troubleshooting, questions or suggestions on your new
moisture probe. You may contact IMKO directly, to after exploring your local contact.
We look forward to helping you!
For warranty claims, please contact your local dealer, distributor or service center. The warranty does not include
any kind of willful damage to the device or its accessories or an operation outside of the product specification. Ple-
ase refer to the information in this manual. If you have any questions, please contact IMKO service. Don’t open the
device and do not try to repair the device yourself- the guarantee expires when the device is opened or modified.
In the course of product improvements, we reserve the right to make technical and visual changes to the device.

Content
1 Functional Description ................................................................................................ 5
1.1 The patented TRIME® TDR-Measuring Method ....................................................................................................5
1.2 TRIME® compared to other Measuring Methods .................................................................................................5
1.3 Areas of Application with TRIME-GW Line and the 1-Rod Probe...........................................................................5
2 Mode of Operation ..................................................................................................... 6
2.1 Measurement value collection with pre-check, average value and filtering.........................................................6
2.2 Temperature Measurement ...................................................................................................................................6
2.3 Temperature compensation when working at high temperatures ........................................................................6
2.4 Analogue Outputs ..................................................................................................................................................6
2.5 The serial RS485 and IMP-Bus interface .................................................................................................................7
2.6 The IMP-Bus as a user friendly network system.....................................................................................................7
2.7 Error Reports and Error Messages .........................................................................................................................7
3 Connectivity to TRIME-GW Line .................................................................................. 8
3.1 How to configure SONO-probes to appropriate operating and calibration parameters? .....................................8
3.2 System Setup with several TRIME-GW Line............................................................................................................9
3.3 Connection Plug and Plug Pinning .........................................................................................................................9
3.4 Analogue Output 0..10V with a Shunt-Resistor....................................................................................................10
4 TRIME-GW Line Installation ...................................................................................... 11
4.1 Schematic Diagram with Carrier Plate U-Profile...................................................................................................12
4.2 Installation on a steel girder with HEA-profile .....................................................................................................12
4.3 Carrier plate dimensions for 120mm steel girder ................................................................................................13
4.4 Installation of two carrier plates very close to each other...................................................................................15
5 Initial operation and adjustments ............................................................................. 16
5.1 Adjustment Guidelines for Moisture Measurements ..........................................................................................16
5.2 How to use the Calibration Curves Cal1 to Cal15.................................................................................................16
5.3 Calibration Curves Cal1 to Cal15...........................................................................................................................17
5.4 Selection and application of the reference method.............................................................................................18
5.5 Recording measurement data in trial operation ..................................................................................................19
5.6 Setting the calibration curve (adjustment)...........................................................................................................19
5.7 Selection of the individual Calibration Curves......................................................................................................20
5.8 Creating a linear Calibration Curve for a specific Material ..................................................................................21
5.9 Calculation for a linear 2-point calibration curve ................................................................................................21
5.10 Calculation for a linear 1-point calibration curve ................................................................................................22
5.11 Calculation for a non-linear calibration curve .....................................................................................................22
5.12 Configuration of the Measuring Mode.................................................................................................................22
5.13 Operation Mode CA and CF at non-continuous Material Flow ...........................................................................24
5.14 Filtering at material gaps in mode CA and CF.......................................................................................................25
5.15 Mode CC – automatic summation of a moisture quantity during one batch process ........................................26
6 Serial Connection to the SM-USB Module ................................................................ 28
3

7 Quick Guide for the Commissioning Software SONO-CONFIG ................................... 30
7.1 Scan of connected SONO probes on the serial interface .....................................................................................30
7.2 Configuration of serial SONO-interface ................................................................................................................31
7.3 Set analogue outputs of the SONO probe............................................................................................................31
7.4 Configuration of Measure Mode .........................................................................................................................32
7.5 Setting the precision of a single value measurement cycle .................................................................................33
7.6 Test run in the respective Measurement Mode ..................................................................................................33
7.7 “Measure” Run in Datalogging-Operation............................................................................................................34
7.8 Offsetting the material temperature sensor ........................................................................................................35
7.9 Compensation of the electronic temperature......................................................................................................36
8 Technical Data TRIME-GW Line.................................................................................. 37
9 Safty Notes ............................................................................................................... 38
4

5
1 Functional Description
1.1 The patented TRIME® TDR-Measuring Method
The TDR technology (Time-Domain-Reflectometry) is a radar-based dielectric measuring procedure at which the
transit times of electromagnetic pulses for the measurement of dielectric constants, respectively the moisture
content are determined.
TRIME-GW Line consists of the measurement transformer TRIME-GW casing and the 1-rod-probe head. An
integrated TRIME TDR measuring transducer of IMKO´s SONO-series is installed into the TRIME-GW Line casing.
A high frequency TDR pulse (1GHz), passes along wave guides and generates an electro-magnetic field around
these guides and herewith also in the material surrounding the probe. Using a patented measuring method, the
transit time of this pulse is determined with a resolution of <1 picosecond (1x10-12). Due to this high resolution
the moisture and the conductivity of the material is measured with a high precission.
The established moisture content, as well as the conductivity, respectively the temperature, can either be uploaded
directly into a PLC via two analogue outputs 0(4) ...20 mA or recalled via a serial RS485 interface.
1.2 TRIME® compared to other Measuring Methods
In contrary to conventional capacitive or microwave measuring methods, the TRIME® technology (Time-Domain-
Reflectometry with Intelligent Micromodule Elements) offers precise measurement results which means more
reliability at the production.
TRIME-TDR technology operates in the ideal frequency range between 600MHz and 1,2 GHz. Capacitive
measuring methods (also referred to as Frequency-Domain-Technology) , depending on the device, operate within
a frequency range between 5MHz and 40MHz and are therefore prone to interference due to disturbance such
as the temperature and the mineral contents of the measured material. Microwave measuring systems operate
with high frequencies >2GHz. At these frequencies, nonlinearities are generated which require very complex
compensation. For this reason, microwave measuring methods are more sensitive in regard to temperature
variation.
The modular TRIME technology enables a manifold of special applications without much effort due to the fact that
it can be variably adjusted to many applications.
1.3 Areas of Application with TRIME-GW Line and the 1-Rod Probe
The TRIME-GW Line with the 1-rod probe is suited for measuring in different materials directly inside a silo. The
1-rod probe requires a good flowability of the measured material in order to ensure that the material lies close to
the rods when the material is flowing.
The temperature of the measured material should not be higher than 60°C.

6
2 Mode of Operation
2.1 Measurement value collection with pre-check, average value and filtering
TRIME-GW Line measures internally at a very high rate of measurements per second and issues the resulting
measurement value at a cycle time of up to 200 milliseconds at the analogue output. Within this cycle time
of 200 milliseconds a probe-internal pre-check of the moisture values is included. Only plausible and physically
pre-averaged measurement values are used for the further data processing. This increases reliability and stability
of the measurement output at the interface of the probe.
In the Measurement Mode CS (Cyclic-Successive), an average value is not accumulated, and the cycle time here
is 200 milliseconds. In the Measurement Mode CA and CF (Average), not the momentarily measured individual
values are directly issued, but an average value is accumulated via a variable number of measurements in order
to filter out temporary variations. These variations can be caused by inhomogeneous moisture distribution of
the material. The delivery scope of TRIME-GW Line includes suited parameters for the averaging period and a
universally applicable filter function deployable for currently usual applications. The time for the average value
accumulation, as well as various filter functions, can be adjusted and customized for special applications.
2.2 Temperature Measurement
A temperature sensor is installed on one stay bar of the 1-rod probe which establishes the measurement of the
material temperature. The temperature can optionally be transmitted at the analogue output 2.
2.3 Temperature compensation when working at high temperatures
Because the TRIME-GW Line measurement transformer works in other temperature ranges as the 1-rod-probe
inside the dryer, it is necessary to compensate the electronic separately from the 1-rod-probe. TRIME-GW Line
offers two possibilities for temperature compensation.
A) Temperature compensation of the internal TRIME-electronic
Despite the TRIME-GW Line electronic shows a generally low temperature drift, it is necessary to compensate a
temperature drift in applications for measuring moisture inside a grain dryer. With this method of temperature
compensation, a possible temperature drift of the TRIME-electronic can be compensated. For standard applications
in grain drying the compensation parameter is pre-set to TempComp = 0.2. For special applications it could be
necessary to adjust this parameter. But it is to consider that it is necessary to make a Basic-Balancing of the
TRIME-GW Line in air and dry glass beads if the parameter TempComp is changed to another value. The parameter
TempComp can be changed with the software tool SONO-CONFIG, in the menu "Calibration" and the window
"Temperature-Compensation".
B) Temperature compensation for the measured material
Water and special materials like maize, wheat and others, show a dependency of the dielectric permittivity when
using TRIME-GW Line at high temperature ranges. The dielectric permittivity is the raw parameter for measuring
water content with TRIME-GW Line. If special materials show this temperature drift, it could be necessary to use
a more elaborate temperature compensation. TRIME-GW Line offers the possibility to set special temperature
compensation parameters for every calibration curve Cal1 of Cal15 (see chapter “Selection of the individual
calibration curve”).
2.4 Analogue Outputs
The measurement values are transmitted as a current signal via the analogue output. With the help of the service
program SONO-CONFIG, the TRIME-GW Line can be set to the two versions for 0..20mA or 4..20mA. Furthermore,
it is also possible to variably adjust the moisture dynamic range e.g. to 0-10%, 0-20% or 0-50%. For a 0-10V DC
voltage output, a 500R resistor can be installed in order to reach a 0..10V output.

7
Analogue Output 1: Moisture in % (0…50%, variable adjustable)
Analogue Output 2: Temperature 0….100°C, variable adjustable
F
For the analogue outputs 1 and 2 there are two adjustable options: Analog Output: (two possible selections)
0..20mA 4..20mA
Output Channel 1 and 2: (three possible selections)
Moisture Temperature: Analogue output 1 for moisture, output 2 for temperature.
For analogue output 1 and 2 the moisture dynamic range and temperature dynamic range can be variably adjusted.
The moisture dynamic range should not exceed 100%
Moisture Range: Temp. Range:
Maximum: e.g. 50 for maize (Set in %) Maximum: 60°C
Minimum: 0 Minimum: 0°C
2.5 The serial RS485 and IMP-Bus interface
TRIME-GW Line is equipped with a standard RS485 as well as the IMP-Bus interface to set and readout individual
parameters or measurement values. An easy to implement data transfer protocol enables the connection of several
sensors/probes at the RS485-Interface. In addition, the TRIME-GW Line can be directly connected via the module
SM-USB to the USB port of a PC, in order to adjust individual measuring parameters or conduct calibrations.
NOTE:
The initial default setting of the serial interface is pre-set for the IMP-Bus. To operate with the RS485 it is
necessary to switch and activate the RS485 interface with help of the modul SM-USB. The transmission
protocol of TRIME-GW Line can be requested via “Contact us” on www.imko.de.
2.6 The IMP-Bus as a user friendly network system
With external power supply on site for the SONO probes, a simple 2-wire cable can be used for the networking. By
use of 4-wire cables, several probes can be also supplied with power.
Standard RS485-interfaces cause very often problems! They are not galvanically isolated and therefore raises the
danger of mass grindings or interferences which can lead to considerably security problems. An RS485 network
needs shielded and twisted pair cables, especially for long distances. Depending on the topology of the network,
it is necessary to place 100Ohm termination resistors at sensitive locations. In practice this means considerable
specialist effort and insurmountable problems.
The robust IMP-Bus ensures security. SONO-probes have in parallel to the standard RS485 interface the robust
IMP-Bus which is galvanically isolated which means increased safety. The serial data line is isolated from the
probe´s power supply and the complete sensor network is therefore independent from single ground potentials
and different grid phases. Furthermore, the IMP-Bus transmit its data packets not as voltage signals, but rather as
current signals which also works at already existing longer lines. A special shielded cable is not necessary and also
stub lines are no problem.
2.7 Error Reports and Error Messages
TRIME-GW Line is very fault-tolerant. This enables failure-free operation. Error messages can be recalled via the
serial interface.

8
3 Connectivity to TRIME-GW Line
Compatible to SONO probes
3.1 How to configure SONO-probes to appropriate operating and calibration parameters?
TRIME-GW Line is initially adjusted for the application for grain drying with the calibration curve Cal14, operation
mode CF and 3 seconds average time. The analogue outputs are adjusted to 4..20mA. With this pre-adjustment
TRIME-GW Line can be installed direct in the heating zone, without further adjustments. For operation at the
discharge hopper where an absolute moisture value is important, TRIME-GW Line has to be adjusted to a suitable
calibration curve Cal-x, depending on grain type and possibly to a zero-offset, depending on installation place.
There are two ways to configure and adjust a SONO-probe:
A: Online Configuration via SONO-VIEW
With the stand-alone device SONO-VIEW it is possible to configure SONO-probes online to an appropriate operating
mode, without the need to connect the SONO-probe to a PC. The operating mode depends on the application like
the moisture measurement under a silo flap, inside a dryer or mixer or on a conveyor belt. The SONO-probe can be
adapted via the SONO-VIEW to the appropriate operating mode like cyclic measurement, averaging, filtering, cu-
mulating and other powerful operating parameters. Furthermore, it is possible to select a calibration curve inside
a SONO-probe with zero-offset setting. All configuration parameters are stored in a non-volatile memory inside
the SONO-probe. This ensures that the analog output (e.g. 4-20mA) of the SONO-probe which could be connected
in parallel to a PLC, responds directly to the set configuration parameters.

9
B: Configuration via SM-USB
The SONO-probe is connected via the SM-USB and the RS485-interface to a PC. With help of the software tool
SONO-CONFIG it is possible to configurate SONO-probes to an appropriate operating mode. The operating mode
depends on the application like the moisture measurement under a silo flap, inside a mixer or on a conveyor belt.
The SONO-probe can be adapted to the appropriate operating mode like cyclic measurement, averaging, filtering,
cumulating and other powerful operating parameters. Furthermore, it is possible to select a calibration curve
inside a SONO-probe with zero-offset setting. All configuration parameters are stored in a non-volatile memory
inside the SONO-probe. So the analog output (e.g. 4-20mA) of the SONO-probe which could be connected in
parallel to a PLC, responds directly to the configuration parameters.
3.2 System Setup with several TRIME-GW Line
3.3 Connection Plug and Plug Pinning
TRIME-GW Line is supplied with a 10-pole MIL flange plug.

10
Plug-PIN Sensor Connections Lead Colour Lead Colour
A +12V….24V Power Supply Red Red
B 0V Power Supply Blue Blue
D 1. Analogue Positive (+) Moisture Green Green
E 1. Analogue Return Line (-) Moisture Yellow Yellow
F RS485 A Weiß White
G RS485 B Brown Brown
C (rt) IMP-Bus Grey/Pink Grey/Pink
J (com) IMP-Bus Blue/Red Blue/ed
K 2. Analogue Positive (+) Pink Pink
E 2. Analogue Return Line (-) Grey Grey
H
Screen
(is grounded at the sensor. The plant must
be properly grounded!)
Transparent Transparent
Assignment of the 10-pole MIL Plug and sensor cable connections:
3.4 Analogue Output 0..10V with a Shunt-Resistor
With the help of a shunt resistor with 500 ohm (included in the delivery) 0..10V can be generated from the current
signal 0..20mA, in case the local PLC does not handle the recommended 4..20mA. Therefore the 500 Ohm shunt
resistor should be placed at the end of the line respectively at the input of the PLC. Following drawing shows the
wire connection.
NOTE:
The analogue output of TRIME-GW Line must be set to 0 to 20mA!

11
4 TRIME-GW Line Installation

12
4.1 Schematic Diagram with Carrier Plate U-Profile
4.2 Installation on a steel girder with HEA-profile
TRIME-GW Line is delivered with a carrier plate as U-profile. This carrier plate can be mounted directly on a steel
girder which can be installed in silos or drying chambers.
IMKO offers the carrier plate in two possible steel girder
dimensions
A) With width a = 120mm
B) With width a = 4”

13
4.3 Carrier plate dimensions for 120mm steel girder

14
Carrier plate dimensions for 4” steel girder

15
4.4 Installation of two carrier plates very close to each other
Here it is very important that the two long rods have sufficient distance to one another. This can be achieved with
a spacer between the carrier plates.

16
5 Initial operation and adjustments
5.1 Adjustment Guidelines for Moisture Measurements
Please read the detailed description first and subsequently use these guidelines as a checklist for adjustments.
1. Extract samples from as close as possible to the probe.
2. Select calibration curve with help of SONO-VIEW or via the module SM-USB.
3. Note: TRIME-GW Line is initially adjusted for the application for grain with the calibration curve Cal2. The
analogue outputs are adjusted to 4..20mA. With this pre-adjustment TRIME-GW Line can be installed direct
in the silo, without further adjustments.
4. Determine the difference between the target and the actual value and if necessary adjust the offset of the
selected calibration curve.
5. Repeat this procedure for different grain types.
5.2 How to use the Calibration Curves Cal1 to Cal15
Up to 15 different calibration curves (CAL1 ... Cal15) are stored inside the TRIME-GW Line. They can be activated
in two ways:
The calibration curve (Cal1. .15) can be activated with the module SONO-VIEW which is working offline or online
with a connection via a PC. In the menu "Calibration" and in the window “Material Property Calibration" by selecting
the desired calibration curve (Cal1...Cal15) and with using the button “Set Active Calib”. The finally desired and
possibly altered calibration curve (Cal1. .15) which is activated after switching on the probes power supply will be
adjusted with the button "Set Default Calib”.
The TRIME-GW Line can only be adjusted when installed in the plant as the location and the bulk density of the
grain have a significant influence on moisture measurement. Adjustment must be carried out separately for every
dried product. Moisture measurement is influenced by the following parameters:
• Location (e.g. metallic objects within the field of measurement)
• Bulk density of the grain (or material)
• Type of grain (material)
As soon as one of these parameters changes, another calibration curve and adjustment must be chosen. If all
possible grain types are adjusted, it is only necessary to select the right calibration curve when changing the grain
type in the plant.
The following charts (Cal.1 .. Cal15) show different selectable calibration curves which are stored inside the TRI-
ME-GW Line.
Plotted is on the y-axis the gravimetric moisture (MoistAve) and on the x-axis depending on the calibration curve
the associated radar time tpAve in picoseconds. With the software SONO-CONFIG the radar time tpAve is shown
on the screen parallel to the moisture value MoistAve (see "Quick Guide for the Software SONO-CONFIG).

17
5.3 Calibration Curves Cal1 to Cal15
Calibration functions with and without temperature compensation

18
Calibration
Curve
Recommended for
grain type
Bulk density
of grain type
Application
Cal1
Maize, without TC
(TC = Temperature
Compensation)
0,75
Installation at the discharge hopper. The outfeed is
batch by batch and it is not secured, that the 1-rod
probe is continually covered with grain.
Cal2 Maize with TC 0,75 Installation inside a silo where the 1-rod probe is
continually covered with grain.
Cal3 Wheat without TC 0,75 Pre-installed like Cal1
Cal4 Wheat with TC 0,75 Pre-installed like Cal2
Cal5 Rye without TC 0,72 Pre-installed like Cal1
Cal6 Rye with TC 0,72 Pre-installed like Cal2
Cal7 Barley without TC 0,63 Special calibration curve
Cal8 Barley with TC 0,63 Special calibration curve
Cal9 Rape and oilseeds
without TC 0.65 No temperature compensation necessary!
Cal10 Sunflower seeds wit-
hout TC 0,30 No temperature compensation necessary!
Cal11 Soya without TC 0,65 Special calibration curve
Cal12 Soya with TC 0,65 Special calibration curve
Cal13
Cal14
(pre-setted
after delivery)
Corn ear of maize 0,5 Special calibration curve
Cal15 1/10 tp Radar time and reference calibration for test
5.4 Selection and application of the reference method
In order to adjust the TRIME-GW Line for precise absolute measurements at the discharge, an off-line measurement
method must be available to serve as a reference. It must provide a high degree of absolute precision and function
with large sample volumes.
The TRIME-GW Line measures the average value continuously over a large measurement volume. In moving grain,
the results of multiple measurement volumes can be accumulated in respect to the chosen avereging time. It
therefore requires a lot of time and effort to verify this very representative value with a reference instrument
mostly using much more smallersample quantities. The most suitable method for determining the exact moisture
of the grain is to use a drying oven. The sample volume is of importance and should be at least 0.5 litres.
For sample extraction and making reference measurements please take the following best practice points into
account:

19
• The samples for the reference measurements should be extracted from as close as possible to the probe
→ The moisture distribution is often very inhomogienius inside the grain dryer
• When using a calibrated instrument with small sample volumes, several samples must be extracted and their
arithmetical average calculated
→ The smaller the sample volume, the larger the failures due to e.g. weight measurement
• Please note that calibrated instruments also have measurement faults, depending of the device between 2%
in the lower and even 5% in the upper moisture range.
→ An alignment between the TRIME GW Line and the reference measurements should be based on multiple
measurements if possible at different moistures.
5.5 Recording measurement data in trial operation
The selection of the calibration curve can only be done in real operation or in realistic trial operation. The following
description is based on the implementation of the TRIME-GW Line at the discharge, in the delivery or in the
storage area.
As a general rule, only the moisture range close to the reference input is of significance for trial operation, i.e.
when determining the switch position for maize at e.g. 15%, calibration should be done at about 15%. It is more
important that the TRIME-GW Line is exactly correct in range of the setpoint value, in this example in the lower
measurement range. It is of less importance whether TRIME-GW Line measures 26% instead of 28% in the upper
measurement range.
When extracting a sample or checking the lower reference input (e.g. 15% ), a single sample is of course insufficient.
Single samples, possibly even extracted from quite a different point than in the direct vicinity of the probe, are not
representative. Several samples must be taken directly at the probe and averaged.
At the start of trial operation, the suitable calibration curve can be set.
When all the preparations for extracting samples and reference measurmentshave been made, the grain dryer can
be started up. Now, samples of grain must be taken continuously, ideally every 15 minutes.
The TRIME-GW Line reading and the selected calibration curve are to be noted simultaneously with every extracted
sample. This is compared with the appropriate offline-determined reference value, which is also to be noted. As
soon as the moisture is near the target moisture, the calibration curve should be set to the best possible value,
which is the nearest to the reference value.
In the following you will find a ready-to-use form for entering the measurements.
• Where continuous-flow dryers are concerned, at least 10 to 20 measurements should be available in the
range between the minimum and maximum permissible moisture content after drying. The measurements
from the still very damp discharged grain during the charge phase should be noted but not used for the
purposes of adjustment.
• For rotary dryers, only the measurements taken towards the end of the drying process are of relevance
to adjustment. Here, too, at least 10 measurements are to have to be documented. Density and moisture
distribution effects in the grain can cause too low measurements during the first one to two hours. These
values should not be used for the adjustment.
5.6 Setting the calibration curve (adjustment)
The appropriate setting of the calibration curve should be determined on the adjustment protocol. Only the
measurements near the target moisture should be taken into account.
5.7 Selection of the individual Calibration Curves

20
In the menu "Calibration" and the window "Material Property Calibration" the calibration curves CAL1 to Cal15
which are stored in the SONO probe are loaded and displayed on the screen (takes max. 1 minute). With the
mouse pointer individual calibration curves can be activated and tested with the SONO-probe by activating the
button "Set Active Calib". Furthermore, the individual calibration curves CAL1 to Cal15 can be adapted or modified
with the calibration coefficients (see Chapter “Creating a linear calibration curve”).
The desired and possibly altered calibration curve (Cal1. .15) which is activated after switching on the probes
power supply can be adjusted with the button "Set Default Calib”.
The calibration name can be entered in the window “Calibration Name”.
The coefficients m0 to m1 (for linear curves) and m0 to m5 (for non-linear curves) can be entered and adjusted
directly by hand with the buttons “Set” and “Save”. Possible are non-linear calibration curves with polynomials
up to fifth order (m0-m5).
Attention:
Use “dot” as separator not comma, for coefficients m0 to m5!
Table of contents
Other IMKO Measuring Instrument manuals
Popular Measuring Instrument manuals by other brands

IFM Electronic
IFM Electronic ecomot200 FR-2 operating instructions

Kobold
Kobold ZUB-MANS-KON1/2 operating instructions
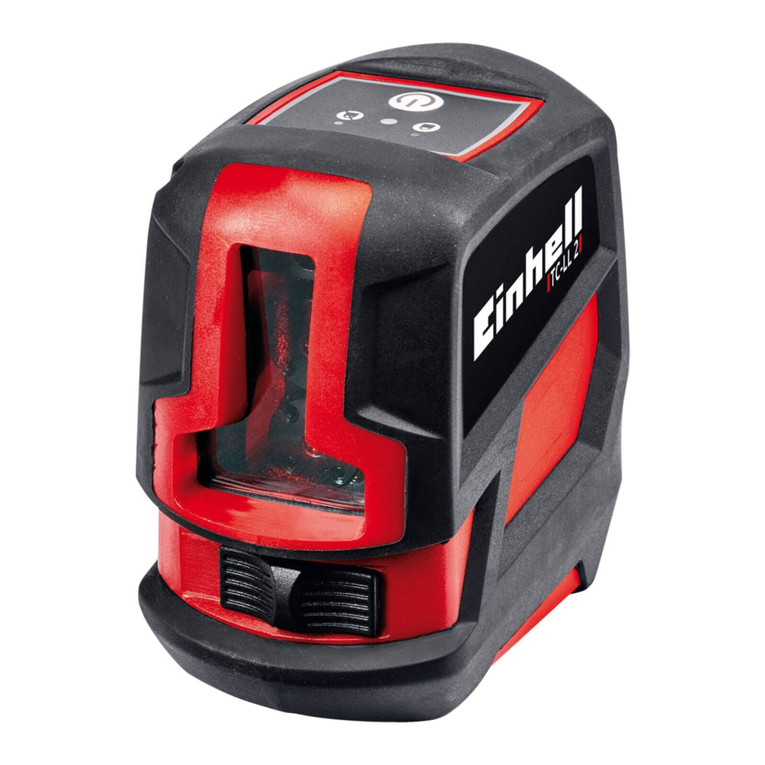
EINHELL
EINHELL TC-LL 2 Original operating instructions
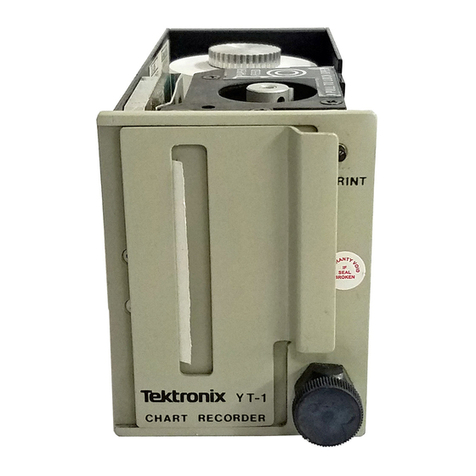
Tektronix
Tektronix YT-1 instruction manual
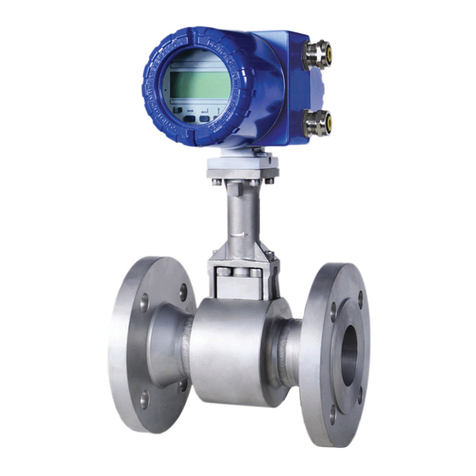
Onicon
Onicon F-2500 series Installation and operation guide
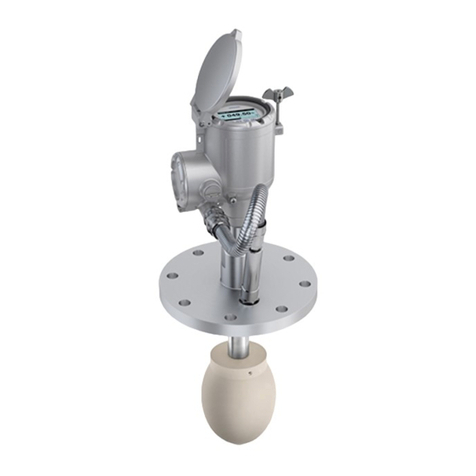
KROHNE
KROHNE OPTIWAVE-M 7400 C Short guide