IMV K2 User manual

Non-Gaussian Random Vibration Control System
K2/ NON-GAUSSIAN
K2Sprint/ NON-GAUSSIAN
Instruction Manual
IMV CORPORATION
ULimitation of K2Sprint/NON-GAUSSIAN
・Maximum numbers of usable input channel are ‘2’ channels.
・Option of LIMIT CONTROL can not be added.

Type of Document : Instruction Manual
System Applied : K2/K2Sprint
Software < NON-GAUSSIAN > Later than Version 14.6.0

Japanese Edition
Version Date Contents
10.0.0 2016.02.29 First edition
10.0.1 2016.03.02 Correction of a misprint
13.0.0 2016.04.28 Correction of a misprint
14.3.0 2019.04.19 Modified description of Data save condition, correction of misprints
14.6.0 2020.04.15 Correction of a misprint
English Edition
Version Date Contents
13.0.0 2016.04.28 First edition
13.0.1 2017.09.28 Correction of misprint
14.3.0 2019.04.19 Modified description of Data save condition, correction of misprints
14.6.0 2020.04.15 Correction of a misprint

CONTENS
Chapter 1 Outline of the System........................................................... 1-1
1.1 Outline ........................................................................... 1-1
1.1.1 Index indicating characteristics of random vibration ........................ 1-1
1.1.2 Amplitude probability density ............................................... 1-2
1.1.3 Kurtosis .................................................................... 1-3
1.1.4 Skewness .................................................................... 1-4
1.1.5 Non-Gaussian random control ................................................. 1-5
1.1.6 Non-Gaussian characteristic type ............................................ 1-6
1.2 Specifications .................................................................... 1-7
1.2.1 NON-GAUSSIAN ................................................................ 1-7
Chapter 2 Operation System of K2 Application .............................................. 2-1
2.1 Outline ........................................................................... 2-1
2.2 Test File ......................................................................... 2-2
Chapter 3 Basic Operation................................................................. 3-1
3.1 Break point PSD ................................................................... 3-1
3.2 Measured PSD ...................................................................... 3-24
3.3 Measured waveform ................................................................. 3-47
Chapter 4 Test Definition................................................................. 4-1
4.1 Outline ........................................................................... 4-1
4.2 Fundamental/Control Condition ..................................................... 4-2
4.2.1 Frequency range fmax ........................................................ 4-2
4.2.2 Control frequency lines ..................................................... 4-3
4.2.3 Max. Observation Frequency (Max. Observation Freq.) ......................... 4-3
4.2.4 Controlled variable ......................................................... 4-4
4.2.5 Averaging Parameters ........................................................ 4-4
4.2.6 Equalization Mode ........................................................... 4-5
4.2.7 Loop check .................................................................. 4-6
4.2.8 Test time ................................................................... 4-7
4.2.9 Initial output level ........................................................ 4-7
4.2.10 Level increment ............................................................ 4-8
4.2.11 Auto-start ................................................................. 4-8
4.2.12 Shutdown time .............................................................. 4-8
4.2.13 Level Scheduling ........................................................... 4-9
4.2.13.1 Level ................................................................ 4-10
4.2.13.2 Time ................................................................. 4-10
4.2.13.3 Tolerance enlarge .................................................... 4-10
4.3 Waveform control condition ........................................................ 4-11
4.3.1 Specify the time of XFR measurement excitation .............................. 4-11

4.3.2 (This section is left blank intentionally.) ............................... 4-12
4.3.3 Control strategy ............................................................ 4-12
4.3.4 Drive saving ................................................................ 4-13
4.3.5 Control speed ............................................................... 4-15
4.3.6 Control sharpness ........................................................... 4-16
4.3.7 Cross-talk control loop open ................................................ 4-17
4.3.8 Cross-talk information averaging times ...................................... 4-18
4.3.9(This section is left blank intentionally.) ................................ 4-18
4.4 Excitation System Setting ......................................................... 4-19
4.4.1 Initial output voltage ...................................................... 4-19
4.4.2 XFR Measure output voltage .................................................. 4-19
4.4.3 Clipping.................................................................... 4-20
4.4.3.1 Clipping of drive waveform............................................ 4-20
4.4.3.1.1 Clipping by crest factor ....................................... 4-20
4.4.3.1.2 Allowable voltage .............................................. 4-20
4.4.3.1.3 Allowance clipping ratio ....................................... 4-21
4.4.3.2 Clipping of control response waveform ................................. 4-21
4.4.4 High Pass Filter(HPF) ....................................................... 4-22
4.5 Control Reference ................................................................. 4-23
4.5.1 PSD definition .............................................................. 4-23
4.5.1.1 Non-Gaussian characteristic........................................... 4-23
4.5.2 PSD definition type ......................................................... 4-25
4.5.2.1 Break point PSD definition............................................ 4-26
4.5.2.1.1 Outline ........................................................ 4-26
4.5.2.1.2 Frequency ...................................................... 4-27
4.5.2.1.3 Level .......................................................... 4-27
4.5.2.1.4 Slope .......................................................... 4-27
4.5.2.1.5 rms change ..................................................... 4-28
4.5.2.1.6 Non-Gaussian control ........................................... 4-29
4.5.2.2 Measured PSD definition............................................... 4-30
4.5.2.2.1 Outline ........................................................ 4-30
4.5.2.2.2 PSD Data File loading .......................................... 4-32
4.5.2.2.3 Data edit ...................................................... 4-34
4.5.2.2.3.1 LPF (low pass filter) .................................... 4-34
4.5.2.2.3.2 HPF (high pass filter) ................................... 4-35
4.5.2.2.3.3 Level Change ............................................. 4-36
4.5.2.2.3.4 rms change ............................................... 4-37
4.5.2.2.4 Non-gaussian control ........................................... 4-37
4.5.2.2.5 CSV data file .................................................. 4-38
4.5.2.3 Measured Waveform definition.......................................... 4-39

4.5.2.3.1 Outline......................................................... 4-39
4.5.2.3.2 Waveform Data File loading ...................................... 4-40
4.5.2.3.3 Data edit....................................................... 4-43
4.5.2.3.3.1 Filtering................................................. 4-43
4.5.2.3.3.2 Edging ................................................... 4-45
4.5.2.3.3.3 Scalar calculation........................................ 4-48
4.5.2.3.3.4 Data length change........................................ 4-50
4.5.2.3.4 CSV data file................................................... 4-53
4.5.3 Tolerance Definition ........................................................ 4-54
4.5.3.1 Tolerance ............................................................. 4-55
4.5.3.2 Define the alarm line ................................................. 4-55
4.5.3.3 Use the lower limit line .............................................. 4-55
4.5.4 RMS Check ................................................................... 4-56
4.6 Input Channel ..................................................................... 4-57
4.6.1 Outline ..................................................................... 4-57
4.6.2 Input channel configuration ................................................. 4-58
4.6.3 Input channel element ....................................................... 4-59
4.6.3.1 (This section is left blank intentionally.) ......................... 4-60
4.6.3.2 Specify the abort level of XFR measurement ............................ 4-60
4.6.3.3 Averaging weighting factor ............................................ 4-60
4.6.3.4 Maximum Value Control ................................................. 4-61
4.6.3.5 Minimum Value Control ................................................. 4-62
4.6.3.6 Specify the averaging parameters to each ch. .......................... 4-63
4.6.3.7 Monitoring RMS observing .............................................. 4-64
4.6.3.7.1 Abort Check / Alarm Check ....................................... 4-64
4.6.3.8 Use the observation profile ........................................... 4-65
4.6.3.8.1 Profile definition .............................................. 4-66
4.6.3.8.2 Tolerance definition ............................................ 4-66
4.6.3.8.3 Limit by observation profile .................................... 4-67
4.7 Analysis condition ................................................................ 4-68
4.7.1 Outline ..................................................................... 4-68
4.7.2 Analysis condition .......................................................... 4-68
4.8 Data Save Condition ............................................................... 4-70
4.8.1 Outline ..................................................................... 4-70
4.8.2 Saving Condition ............................................................ 4-70
4.9 Operation Status .................................................................. 4-72
Chapter 5 Message and Meanings............................................................ 5-1
5.1 K2Non-Gaussian Error Message ...................................................... 5-1
Chapter 6 Supplemental Explanation........................................................ 6-1
6.1 Set Up ............................................................................ 6-1

6.2 Manual Operation .................................................................. 6-2

1 - 1
Chapter 1 Outline of the System
1.1 Outline
K2/NON-GAUSSIAN is an option of K2/RANDOM.
Vibration test is conducted to verify that the designed performance and functions of a product can be
maintained until it is discarded by artificially giving it dynamic stress which is assumed to be given
during the life cycle of a product. The test result greatly depends on the type and method of artificial
stress to be given to the product. Therefore, vibration to be given artificially in the vibration test is
preferable to be similar to that in actual vibration environment. For these reasons, sinusoidal vibration
has been used for most of vibration tests for the last few decades. However, random vibration has
become mainstream recently, since it is closer to actual vibration.
In this random test, Gaussian random vibration in accordance with Gaussian distribution (normal
distribution) is used. However, analysis of measured vibration including vibration during transportation
often reveals the vibration to be non-Gaussian random vibrationwhich generates higher peaks, not
Gaussian random vibration.
Non-Gaussian random controller reproduces such non-Gaussian random vibrations more precisely. In
the non-Gaussian random test, higher peaks are generated than in the conventional random test.
Thoroughly understand the nature of non-Gaussian random test, review the protection of specimen and
vibration system, considering varied protective functions provided for this system, and conduct the test
carefully.
It should be noted that the reproduction of non-Gaussian random vibration having the same
characteristics as measured vibration is difficult in general. This is because there are many types of non-
Gaussian random vibration having varied characteristics while the characteristics of Gaussian random
vibration are uniquely defined.
1.1.1 Index indicating characteristics of random vibration
Following two types of indexes indicating characteristics of random vibration are used in normal
random test.
・Power spectral density (PSD)
・rms value
In non-Gaussian random test, following two parameters are added as indexes indicating non-
Gaussian.
・Kurtosis
・Skewness
‘Kurtosis and Skewness’, a kind of statistic, the same as rms value, is indicated by numerical
value as ‘5’. Although rms value is easy to understand immediately as a value to indicate
‘magnitude of vibration’, ‘Kurtosis and Skewness’ may be hard to be understood immediately. To
understand ‘Kurotosis and Skewness’, it is necessary to understand how characteristics of random
vibration are evaluated.

1 - 2
1.1.2 Amplitude probability density
Amplitude probability density (function) indicates the distribution states of random vibration
amplitude (magnitude) to evaluate the characteristics of random vibration.
In the graph below, normal waveform graph is turned clockwise by 90, and amplitude values are
on the horizontal axis, while time values are on the vertical axis.
Horizontal axis in this graph is divided into fixed intervals, like scales (grids), as shown below. In
the histogram shown below, the number of points counted on the waveform between the bins are
plotted for each amplitude level.
However, shape of histograms cannot be compared because the number of points is greater as the
waveform is longer (as the test time is longer). Amplitude probability density is the histogram that
the number of points at each amplitude level is normalized by using the total number of points. And
amplitude probability density facilitates the comparison of histograms.
-2 -1 0 1 2
Time [s]
Amplitude [m/s
2
]
0
-2 -1 0 1 2
Amplitude [m/s2]
0
Amplitude [m/s2]
Time [s]
Number of points
Number of points
between each bins
are counted.
Histogram
Waveform graph

1 - 3
1.1.3 Kurtosis
Kurtosis (peakedness) indicates the density extent of amplitude probability density in the vicinity
of zero (average value), and it also indicates the peakedness in the area close to zero.
As kurtosis is larger, the peakedness in the area close to zero is enhanced, and the tail is thicker.
As the tail is thicker, the peak of random vibration is higher. Kurtosis of Gaussian distribution is
“3”.
Amplitude probability density examples in the case of Gaussian distribution and, 6 and 10 of
kurtosis K are shown below.
Random vibration examples in the case of Gaussian distribution and, 6 and 10 of kurtosis K are
shown below. As kurtosis is larger, the peak of waveform is higher.
-4 -3 -2 -1 0 1 2 3 4
0
0.1
0.2
0.3
0.4
0.5
0.6
0.7
Amplitude [m/s2]
Amplitude probability density
0
K = 10
K = 6
K = 3
(Gaussian distribution)
2 2.5 3 3.5 4
0
0.05
Zoom
0 1 0 2 0 3 0
-5
0
-5
0
5
-5
0
5
[s]
[m/s2]
[s]
[s]
K = 10
K = 6
K = 3 (Gaussian distribution)

1 - 4
1.1.4 Skewness
Skewness (degree of skew) is an index indicating the asymmetry of amplitude probability density
distribution. When skewness is 0, distribution is symmetrical to zero (average value). When
skewness is a positive value, the amplitude of which probability is maximum is shifted to the
negative side, and the tail of distribution in the positive side is thicker. As the tail of distribution is
thicker, the peak of random vibration tends to be biased to the positive side. When skewness is
negative conversely, the peak of random waveform tends to be biased to the negative side.
Skewness of Gaussian distribution is ‘0’.
Amplitude probability density examples when skewness S is 0, 1, or -1 are shown below.
Random vibration examples when skewness S is 0, 1, or -1 are shown below. When skewness is
1, the peak in the positive side is higher, while the peak in the negative side is higher when
skewness is -1. The average value is also 0 even in this case.
-4 -3 -2 -1 0 1 2 3 4
0
0.1
0.2
0.3
0.4
0.5
Amplitude [m/s2]
Amplitude probability density
0
S = 1 S = -1
S = 0
-5
0
5
0
5
-5
0
5
[s]
[s]
[s]
S = -1
S = 1
S = 0
[m/s2]

1 - 5
1.1.5 Non-Gaussian random control
Non-Gaussian random controller, like a conventional random controller, controls ‘Power spectral
density (PSD) and rms value’ of the control channel to be coincided with the reference values. In
addition, it also controls the non-Gaussian parameters ‘Kurtosis and skewness*’ to be coincided
with the reference values.
In the non-Gaussian random test, the results of control channel power spectral density is the same
as those of the conventional random test. However, the generated peak of response wave of the
control channel is higher than that of the conventional random controller.
Because this system has adopted a waveform control function in order to reproduce non-Gaussian
parameters precisely, process of measuring the transfer function of controlled system is required
prior to the test.
Test procedures of this system are shown below.
1) Transfer function measurement
2) Initial equalization
Equalization is conducted so that ‘Power spectral density and rms value’ are
coincided with the reference values.
3) Initial equalization for Non-Gaussian
Equalization is conducted so that ‘Kurtosis and skewness*’ are coincided with the
reference values.
4) Test start
‘1) Transfer function measurement’ and ‘3) Non-Gaussian initial equalization’ are the processing
not conducted with conventional random controllers.
After ‘1) Transfer function measurement’ is finished, the system waits for command from an
operator in order to confirm the normality of measured transfer function. Subsequent serial
processes are conducted automatically.
* Definition of skewness is not mandatory.

1 - 6
1.1.6 Non-Gaussian characteristic type
Varied types of non-Gaussian random vibration generating methods are available, and the shape
of non-Gaussian random vibration cannot be defined uniquely even when kurtoses are identical.
This system enables the reproduction of two types of non-Gaussian random vibration having
characteristics different from each other.
・Sporadic peak type
This type of Non-Gaussian random vibration is accompanied with higher peaks
sporadically. In this type, only kurtosis can be defined.
・Stationary peak type
This type of Non-Gaussian random vibration is accompanied with higher peaks
constantly. In this type, kurtosis as well as skewness can be defined.
Random vibration examples of sporadic peak type and stationary peaktype are shown below.
(a) Sporadic peak type example
(b) Stationary peak type example

1 - 7
1.2 Specifications
1.2.1 NON-GAUSSIAN
(1) Control Method:1) PSD control of the random waveform signal with the Non-Gaussian
nature by using the feed-forward method
2) Real time waveform control by using the feed-forward method
(2) Control frequency fmax:Maximum 10 kHz (However, it may be limited by conditions.)
(3) Number of control lines L : Maximum 3200 lines
(However, it may be limited by conditions.)
(4) Control dynamic range:More than 90 dB (Sporadic peak type, in the case of kurtosis 5)
(5) Loop Time :Within 450 ms (120 DOF, fmax = 2000 Hz, L = 200 line, waveform control
average = at 8times/a loop)
(6) Non-gaussian control
1) Non-Gaussian control: Kurtosis / Skewness (Stationary peak type only)
2) Non-Gaussian characteristic type: Sporadic peak type / Stationary peak
(7) Input channel (However, it may be limited by conditions.)
1) Number of channels:Maximum 64
(Non-Gaussian control channel: 1 ch)
2) Channel type::
Non-gaussian control channel / Control channel / Monitor channel(possible to duplicate)
3) Control response averaging method:
Average value control / Maximum value control / Minimum value control
4) Alarm / Abort:For each input channel, the maximum allowance spectrum data
(PSD) or RMS value can be specified for setting of Alarm / Abort.
5) Limit control function:Conforms to K2/RANDOM
(8) Output channel
1) Number of channels:1
2) Clipping:Voltage value (specifying by σcan also be added.)
Response of non-Gaussian control channel.
(9) Analysis / Display data:
1) Reference, Controlled response PSD and Tolerance
2) PSD and Waveform data of each input channel
3) Drive spectrum
4) Transmissibility: ・Controlled system transmissibility (control response / drive)
・Transmissibility between input channel and drive
・Transmissibility between input channels (amplitude, phase)
5) PSD for Monitoring, Limit control execution ratio
6) Amplitude probability density (Non-gaussian control channel, each control channel)
7) Trend Graph (rms value, Kurtosis and Skewness of non-Gaussian control channel)
8) System Data such as Transfer Function or Coherence between Non-Gaussian control
channel and Drive output channel

1 - 8
(10) Data save:Automatic / Manual
Display data save as CSV format
(11) Control operation information save and use
1) Storing of the test operation time information and continuing of test operation
(Partial execution of the test)
2) Storing the control information and continuing of the control
Example of NON-GAUSSIAN execution screen
Upper Control response PSD
Lower Drive PSD

2 - 1
Chapter 2 Operation System of K2 Application
2.1 Outline
In K2 application, operation after booting up is executed by using a keyboard and a mouse.
When this application is started, a window shown as below appears.
All the names of menu in this application are displayed in Menu bar. Each menu is to be opened by
clicking on its name and available commands appears as a list.
The commands used frequently are displayed as icons in each Tool bar. A command is executed or a
dialog box corresponding to the command is opened when the icon is clicked. Operation status of K2
Controller is displayed in Status bar. The state during the excitation operation is displayed in Operation
status panel.
K2 Application Window
Menu Bar
Operation Status Panel
File Tool Bar
Test Definition Tool Bar Manual Operation Tool Bar
Status Bar
Operation Tool Bar

2 - 2
2.2 Test File
In K2 application, necessary information to operate a test is saved in a specified file called ‘Test File’.
Following kinds of Test File are available in this system.
Necessary Test Files for test operation
・Test Definition File :K2NON-GAUSSIAN(*.ngaus2)
・Graph Data File :(*.vdf2)
・Environment setting File
(I/O Module Configuration Information, Excitation System Information, Input channel
Information ) :SystemInfo.dat2
Note 1) Saved in ‘¥IMV¥K2_2nd’ on System Drive. Deleting inhibited

3 - 1
Chapter 3 Basic Operation
3.1 Break point PSD
< Example >
An example of Break point PSD random test is described as below ;
[Reference pattern]
The PSD is specified to 10 [(m/s2)rms] having the shape as in the above between 10 [Hz] and 1000
[Hz].
Non-Gaussian characteristic is set to sporadic peak type, and kurtosis is set to 5.0 during the control.
[Test time]
10 minutes
[Information of sensors to be used]
Two acceleration pickups of piezoelectric is used for control and another for monitor.
Ch. 1 : for non-gaussian control, sensitivity 3pC/(m/s2), Break point PSD reference
Ch. 2 : for monitor, sensitivity 3pC/(m/s2)
However, these channels must be registered in Input channel information (in this example,
‘INPUT’).
Also, the rating information of excitation system has already been registered in Excitation system
information (in this example, ‘System’).
Frequency [Hz]
Level
[(m/s2)2/ Hz]
10
Slope:6[dB/oct]
100 1000

3 - 2
< Procedures >
< Step 1 >
Press the button of [New] to start ‘New definition’.
<Step 2>
Select an Excitation system from the list of ‘Excitation system information’.

3 - 3
<Step 3>
Click the checkbox of ‘Input channel information selection’ and select an input channel information
from the list.
<Step 4>
Press the [OK] button.
①
②
Other manuals for K2
5
This manual suits for next models
1
Table of contents
Other IMV Control System manuals
Popular Control System manuals by other brands
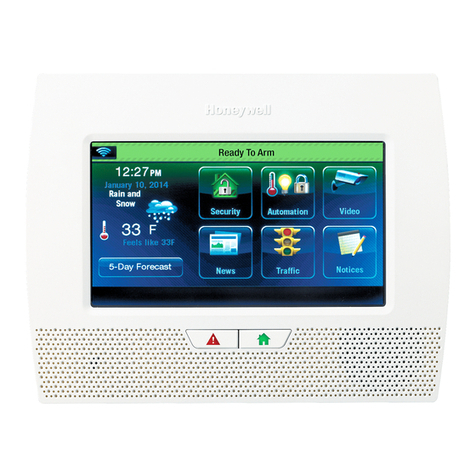
Honeywell
Honeywell LYNX Touch L7000 Series Quick installation guide
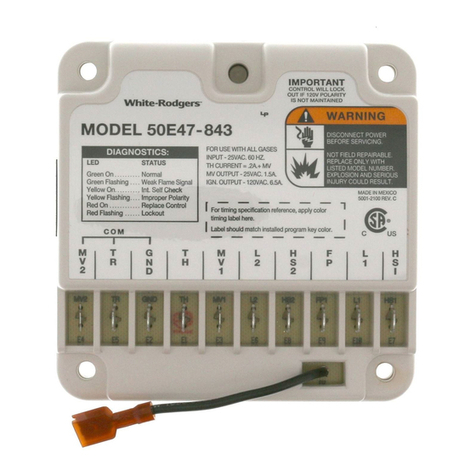
White Rodgers
White Rodgers 50E47-843 installation instructions
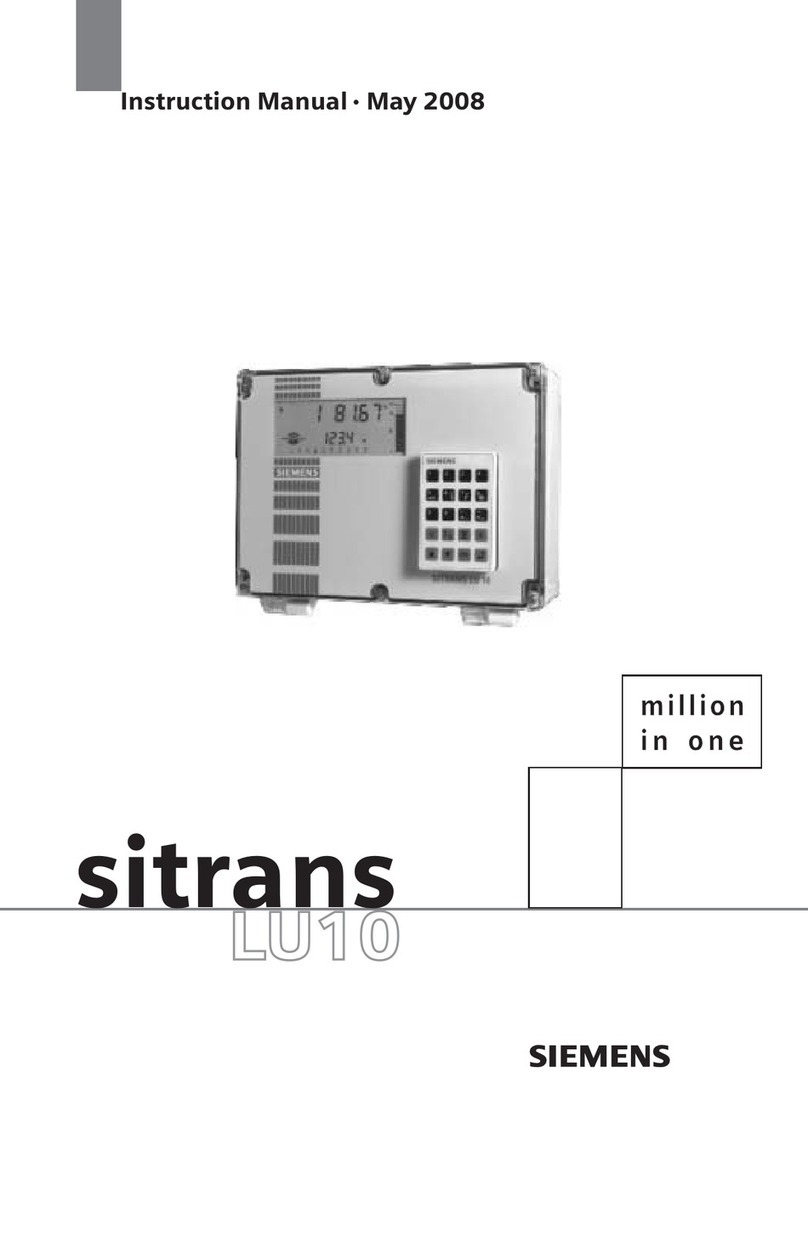
Siemens
Siemens sitrans LU10 instruction manual
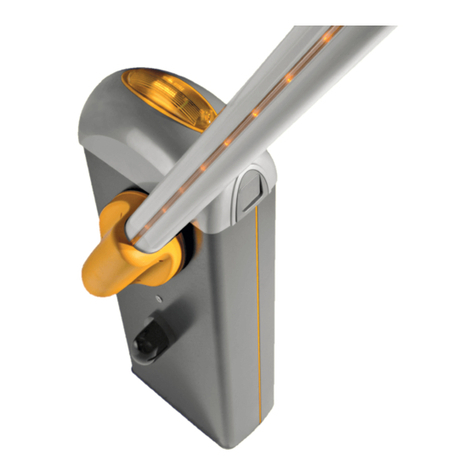
CAME
CAME Barriere GARD quick start guide
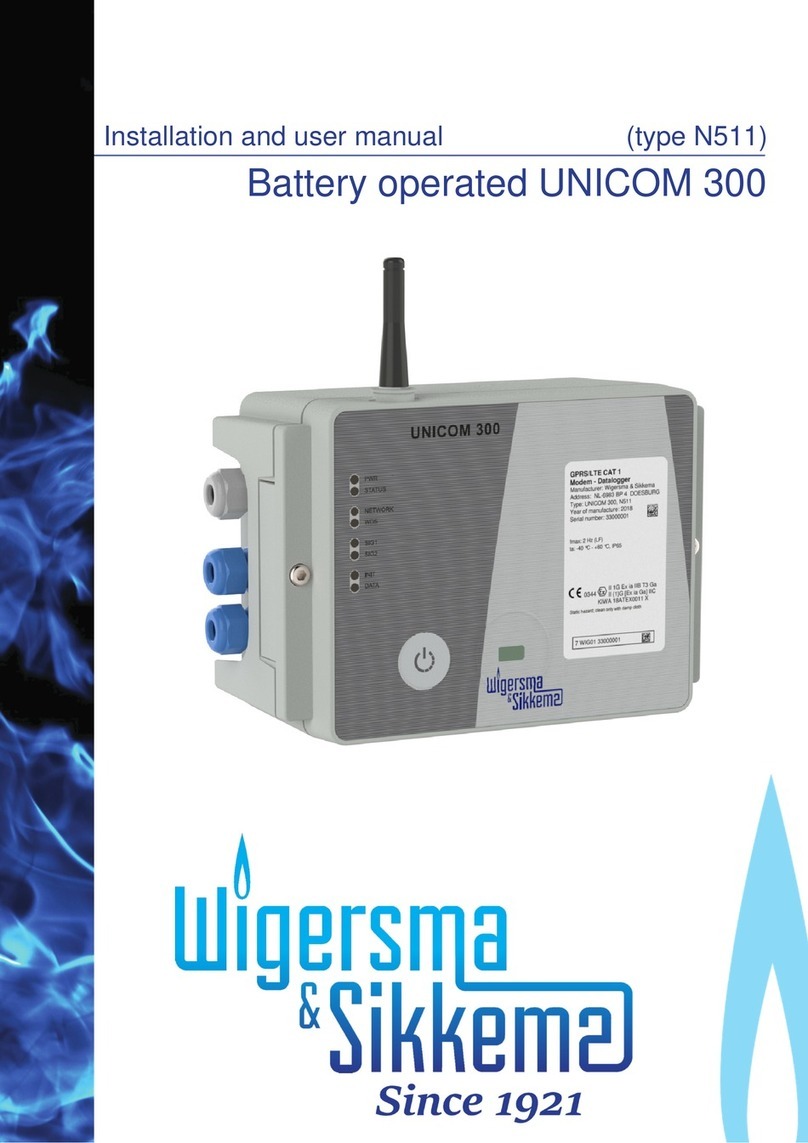
Wigersma & Sikkema
Wigersma & Sikkema UNICOM 300 Installation and user manual
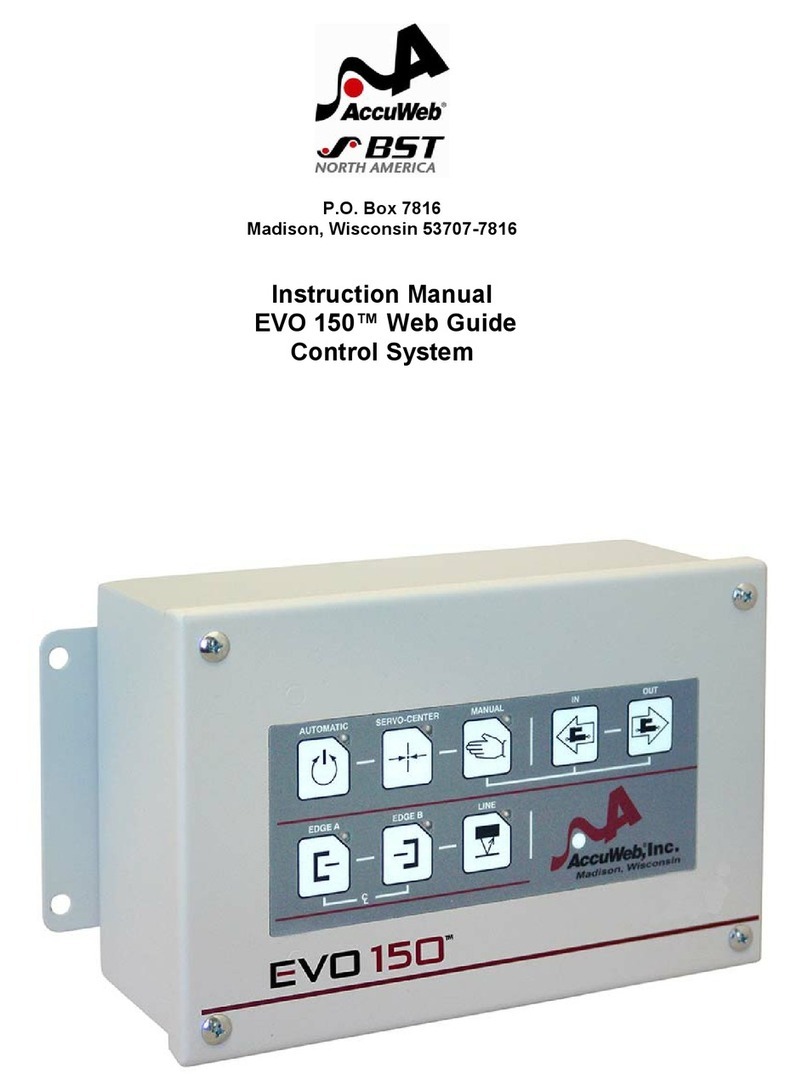
AccuWeb
AccuWeb EVO 150 instruction manual