Inovance Monarch MCTC-PEC-E1 User manual

User Guide
MCTC-PES-E1
Programmable Electronic System
Suzhou Inovance Technology Co., Ltd.
Add.: No. 16 Youxiang Road, Yuexi Town, Wuzhong District, Suzhou 215104, P.R. China
Tel: +86-512-6637 6666
Fax: +86-512-6285 6720
Service Hotline: 400-777-1260
http: //www.inovance.com
Shenzhen Inovance Technology Co., Ltd.
Add.: Building E, Hongwei Industry Park, Liuxian Road, Baocheng No. 70 Zone, Bao’an District, Shenzhen
Tel: +86-755-2979 9595
Fax: +86-755-2961 9897
Service Hotline: 400-777-1260
http: //www.inovance.com
MCTC-PES-E1 Programmable Electronic System User Guide
Copyright Shenzhen Inovance Technology Co., Ltd.
A02
Data code 19010187
User Guide

Preface
- 1-
Preface
Thank you for purchasing the MCTC-PES-E1 system.
MCTC-PES-E1, independently developed and produced by Suzhou Monarch Control
Technology Co., Ltd., is a programmable electronic system in safety related applications
for escalators and moving walkways (PESSRAE).
The MCTC-PES-E1 adopts dual-CPU control and provides multiple security monitoring
protections for escalators and moving walkways. The system satisfies the GB/16899-2011
Safety Rules for the Construction and Installation of Escalators and Moving Walks.
This manual describes the correct use of the MCTC-PES-E1 system. System installation,
commissioning and maintenance must be performed only by qualified personnel with
related experience.
It introduces the construction, features, security prompts, design & installation, operation &
maintenance, and faults & solutions of the MCTC-PES-E1 system. Read and understand
the manual before use, and keep it properly for future reference.
Notes
◆To describe product details, this manual provides diagrams showing the status without a
housing or safety cover. Before using this product, install the housing or safety cover as
required and refer to the instructions in this manual.
◆Diagrams in this document are used only for function description. The product structure
shown in the diagrams may be different from the structure of the product that you purchase.
◆When the product is upgraded or the specifications change, this manual will be updated in
a timely manner to improve its accessibility and accuracy.
◆If you need to purchase this manual in case that the original copy is damaged or lost,
contact our local agent or our customer service center.
◆If you have any questions regarding the usage of this product, contact our customer
service center.

Contents
- 2-
Contents
Preface ............................................................................................................................................ 1
Safety Instructions ................................................................................................................................ 4
Safety Disclaimer ..................................................................................................................... 4
Safety Levels and Definitions ................................................................................................. 4
Safety Instructions ................................................................................................................... 4
Service life ................................................................................................................................ 8
Chapter 1 Product Information .......................................................................................................... 9
1.1 Introduction ............................................................................................................................. 9
1.2 System Components .............................................................................................................. 9
1.3 System Functions ..................................................................................................................10
1.3.1 Working States .............................................................................................................. 11
1.3.2 Description of Security Functions .............................................................................. 11
1.3.3 Security Measures After Security Functions Enabled .............................................. 12
Chapter 2 Installation and Wiring ...................................................................................................13
2.1 Mechanical Installation ........................................................................................................13
2.1.1 Installation environment requirements ....................................................................13
2.1.2 Installation Dimensions ............................................................................................... 13
2.1.3 Installation Instructions ............................................................................................... 14
2.2 Installation of Sensors ..........................................................................................................14
2.2.1 Technical Data of Sensors ............................................................................................14
2.2.2 Installing the Speed Sensor and Running Direction Sensor for Escalator/Moving
Walkway ........................................................................................................................16
2.2.3 Installing the Handrail Speed Sensor ........................................................................ 17
2.2.4 Installing the Step/Pallet Loss Sensor........................................................................ 18
2.3 Wiring ......................................................................................................................................21
2.3.1 Description of System Terminals ................................................................................21
2.3.2 Wiring of the MCTC-PES-E1 .........................................................................................25
2.3.3 Connecting the Floor Plate Switches .........................................................................26
2.3.4 Connecting Brake Detection Switches in Dual-Motor Application .......................27
Chapter 3 Operation Panel ...............................................................................................................28
3.1 LED Operation Panel ............................................................................................................28
3.1.1 Button Description ........................................................................................................28
3.1.2 Indicators .......................................................................................................................29
3.1.3 Data Display ...................................................................................................................29

Contents
- 3-
3.2 Basic Operations ....................................................................................................................30
Chapter 4 Functional Parameters ....................................................................................................31
4.1 Parameter Description .........................................................................................................31
Group F0: Basic Parameters ..................................................................................................31
Group F1: State Parameters ..................................................................................................34
Group F2: Fault Information .................................................................................................37
Group FF: Factory Parameters ..............................................................................................39
Group FP: Management Parameters ...................................................................................39
4.2 Examples of Commissioning Applications ......................................................................40
Chapter 5 Troubleshooting ..............................................................................................................42
5.1 Fault Description ...................................................................................................................42
5.2 System Prompt Faults ..........................................................................................................44
Revision History ..................................................................................................................................45
Warranty Agreement .........................................................................................................................46

Safety Instructions
- 4-
Safety Instructions
Safety Disclaimer
1)Read and comply with the safety instructions during installation, operation, and mainte-
nance on the equipment.
2)To ensure the safety of humans and the products, follow the marks on the products and
all the safety instructions in this document.
3)The “CAUTION”, “WARNING”, and “DANGER”are only supplements to the
safety instructions.
4)Use this equipment based on the designated environment requirements. Damages
caused by improper usage are not covered by warranty.
5)The company shall take no responsibility of any personal injuries or Operation damag-
es caused by improper usage.
Safety Levels and Definitions
Danger
The“Danger” sign indicates that failure to comply with the notice will
result in server personal injuries or even death.
Warning
The“Warning” sign indicates that failure to comply with the notice may
result in server personal injuries or even death.
Caution
The“Caution” sign indicates that failure to comply with the notice may
result in minor or moderate personal injuries or damage to the equipment.
Safety Instructions
Unpacking
Caution
◆Check whether the packing is intact and whether there is damage, water seepage, damp,
and deformation.
◆Unpack the package following the package sequence. Do not hit the package with force.
◆Check whether there are damages, rust, or injuries on the surface of the product or product
accessories.
◆Check whether the number of packing materials is consistent with the packing list.
Warning
◆Do not install the equipment if you find damages, corrosions, or indications of use on the
product or accessories.
◆Do not install the equipment if you find water seepage, component missing or damage
upon unpacking.
◆Do not install the equipment if you find the packing list does not conform to the equipment
you received.

Safety Instructions
- 5-
Storage and Transportation
Caution
◆Store this equipment based on the storage and transportation requirements on humidity
and temperature.
◆Avoid transporting the equipment in environment such as water splashing, rain, direct sun-
light, high voltage, strong magnetic field, and strong vibration.
◆Avoid storing the product for more than 3 months, long-term storage shall require stricter
protection and necessary inspections..
◆Pack the product strictly before you transport. Use a sealed box for long-distance transpor-
tation.
◆Never transport this product with products or materials that harm or have negative impacts
on this product.
Warning
◆Use professional loading and unloading equipment to carry large-scale or heavy products.
◆When carry this equipment with bear hand, hold the product casing firmly with care pre-
venting from parts falling, otherwise, it may result in personal jury or equipment damages.
◆Handle the products with care, mind your steps, otherwise, it may result in personal juries
or equipment damages.
◆Never stand or stay below the equipment when the equipment is lifted by hoisting equip-
ment.
Installation
Warning
◆Read and comply with the safety instructions before performing installation.
◆Do not modify this product.
◆Do not rotate the product components or the fixed bolts and red marked bolts on product
components.
◆Do not install this product in places where there is strong electric field or strong magnetic
field.
◆When this product is installed in a cabinet or terminal device, the cabinet or terminal device
must be equipped with protective shell. The proof class must comply with relevant IEC
standards and local regulations.
Danger
◆Do not allow non-professionals to perform product installation, wiring, maintenance, inspec-
tion or parts replacement.
◆The installation, wiring, maintenance, inspection and parts replacement are intended to be
performed by professional personnel only.
◆Installation personnel must be familiar with product installation requirements and relevant
technical materials.
◆If you need to install transformer or other strong electromagnetic interference equipment,
install shielding device at the same time to avoid product malfunction.

Safety Instructions
- 6-
Wiring
Danger
◆Do not allow non-professionals to perform product installation, wiring, maintenance, inspec-
tion or parts replacement.
◆Never perform wiring at power-on. Failure to comply may result in electric shock.
◆Cut off all power supplies before wiring. Wait at least 10 minutes after power-off so that re-
sidual voltage can discharge safely. Wait at least 10 minutes after power-off so that residual
voltage can discharge safely.
◆Make sure that the equipment is reliably grounded. Failure to comply may result in electric
shock.
◆Follow the proper electrostatic discharge (ESD) procedures, and wear an anti-static wrist
strap to perform wiring. Failure to comply may result in damage to the equipment or the
internal circuit the product.
Warning
◆Never connect the power cable with the product output terminals (U, V, W.). Failure to com-
ply may result in equipment damage or even fire.
◆When connecting driving equipment with the motor, make sure the phase sequence of the
drive and motor are consistent to prevent motor reverse rotation.
◆The cable used in wiring must conform to the wire diameter and shielding requirements,
the shielding layer of the shielded cable must be reliably grounded at one end.
◆After wiring, make sure there are no fallen screws or exposed wire inside the cabinet or
product.
Power-on
Danger
◆Before power-on, make sure that the equipment or products are intact, all wiring are safely
connected, and the motor device allows a restart.
◆Before power-on, check if the power supply meets the equipment requirements, avoid
equipment damage or fire.
◆At power-on, equipment or product may start running abruptly, keep away from mechanical
device.
◆After power-on, never open the cabinet door or the protective shell to avoid electric shock.
◆Never touch any terminals at power-on to avoid electric shock.
◆Never dismantle the equipment or remove any parts from the equipment at power-on to
avoid electric shock.
Operation
Danger
◆Never touch any terminals during operation. Failure to comply may result in electric shock.
◆Never dismantle the equipment or remove any parts from the equipment during operation.
Failure to comply may result in electric shock.
◆Never touch the equipment shell, fan or resistor for temperature detection. Failure to com-
ply may result in burn!
◆Do not allow non-professional technicians to detect signals during operation. Failure to
comply may result in equipment damage even personal injuries.

Safety Instructions
- 7-
Warning
◆Prevent metal or other objects from falling into the device during operation, failure to com-
ply may result in equipment damage.
◆Never use contactors to start or stop the equipment. Failure to comply may result in dam-
age to the equipment!
Maintenance
Danger
◆Do not allow non-professionals to perform product installation, wiring, maintenance, inspec-
tion or parts replacement.
◆Never perform maintenance at power-on. Failure to comply may result in electric shock.
◆Before maintenance, wait at least 10 minutes after power-off so that residual voltage can
discharge safely.
Warning
◆Following the equipment repair and maintenance requirements to perform routine and
periodical inspection and maintenance, and keep a maintenance record.
Repair
Danger
◆Do not allow non-professionals to perform product installation, wiring, maintenance, inspec-
tion or parts replacement.
◆Never perform any inspection or maintenance operations at power-on. Failure to comply
may result in electric shock.
◆Before inspection or maintenance, wait at least 10 minutes so that residual voltage can
discharge safely.
Warning
◆Follow the terms defined in the warranty agreement to repair the product.
◆When the equipment has a fault or is damaged, follow the instructions of the professionals
to perform troubleshooting or maintenance, and keep a maintenance record.
◆Following the quick-wear parts instructions to replace the damaged parts.
◆Do not continue to use the damaged equipment. Failure to comply may result in worse
damages.
◆Following the equipment repair and maintenance requirements to perform routine and
periodical inspection and maintenance, and keep a maintenance record.
Disposal
Warning
◆Following the local regulations or standards to dispose the retired equipment or products.
Failure to comply may result in Operation damage or even death.
◆Following the industry waste disposal standards to recycle the scrapped equipment to
avoid environmental pollution.

Safety Instructions
- 8-
Service life
The service life of the MCTC-PES-E1 is 15 years. To ensure normal use and security, you
need to replace the product that has been used for approximately 10 years (calculated
from delivery) or return them to Monarch for repair and maintenance.

Chapter 1 Product Information
- 9-
Chapter 1 Product Information
1.1 Introduction
The MCTC-PES-E1 is designed to provide multiple security monitoring protections for
escalators and moving walkways. It adopts dual-CPU control and judges the signals
related to the escalator or moving walkway simultaneously. Once detecting a fault, the two
CPUs instruct the safety relays to act and output the fault signal.
Furthermore, the two CPUs monitor each other. If one CPU breaks down or is damaged,
the other instructs the safety circuits to act immediately and output the corresponding
fault signal. The MCTC-PES-E1 has an LED operation panel, on which you can perform
operations such as parameter modification and working status monitoring.
The following figure shows the physical appearance of the MCTC-PES-E1.
Figure 1-1 Physical appearance of the MCTC-PES-E1 (a control board fixed inside the
black housing)
1.2 System Components
The MCTC-PES-E1 is configured with a control board, a protective guard, and a switching-
mode power supply(the models are introduced in Table 1-1).
When installing the MCTC-PES-E1, six sensors and seven detection switches are required.
The sensor models are designated and sold by Monarch, while the detection switches are
decided by the customer. The recommended models of the sensors and detection switches
are introduced in Table 2-2.
Caution
◆The MCTC-PES-E1 system is installed in the machine room of the escalator or moving
walkway. The installation environment must satisfy the requirements described in Table 1-2.
Monarch will assume no risk or responsibility if a fault occurs in the system because the
installation environment requirements are not satisfied.
◆The switching-mode power supply provides power supply only to the components of the
MCTC-PES-E1 (including the control board and the connected sensors and detection
switches). It is prohibited to provide power supply to any other devices.

Chapter 1 Product Information
- 10 -
Table 1-1Models of switching-mode power supply
Component Quantity Adapted Model Remarks
Switching-
mode power
supply
1
ECU EPR-35-24
EPR-35-24
(35W,DC24V)
Schneider
ABL2REM24015H
(35W,DC24V)
Mean Well
LRS-35-24
(35W,DC24V)
The switching-
mode power
supply of
MCTC-
PES-E1 is
provided by
Monarch.
Table 1-2 Models of sensors and detection switches
Accessory Quantity Recommended Model Remarks
Sensor Schneider OMRON Specify the required
sensor models in
your order. Monarch
will deliver them
(except NBN40-L2-
E0-V1) together with
the MCTC-PES-E1.
Both low-level and
high-level signals
are supported.
Escalator/Moving
walkway speed
sensor
2 XS2 18BLNAL2C E2B-M18KN16-WP-C1-
MNK
Handrail speed
sensor 2 XS2 12BLNAL2C E2B-M12KN08-WP-C1-
MNK
Step loss
detection sensor 2 XS2 30BLNAL2C
E2B-M30KN20-WP-C1-
MNK、E2B-M30LN30-
WP-C1-MNK
Detection Switch Schmersal OMRON
Customer option
Motor brake
detection switch 2TS236-02Z
TS236-11Z
D4N-4132
D4NA-4131
Auxiliary brake
detection switch 1TS236-02Z
TS236-11Z D4N-4132
Floor plate
detection switch 4TS236-02Z
TS236-11Z
D4N-4132
D4N-2B64-E1
D4NA-412G
1.3 System Functions
The MCTC-PES-E1 is designed to ensure safe running of escalator and moving walkway
according to the security grading defined in the newest escalator security standard
GB16899-2011. It has the following security functions:
■Overspeed protection
■Unintentional reversal protection
■Handrail speed deviation protection
■Service brake and auxiliary brake monitoring protection
■Step or pallet loss protection
■Braking-to-stop distance detection and alarm
■Floor plate state monitoring

Chapter 1 Product Information
- 11 -
1.3.1 Working States
Table 1-3 States of the MCTC-PES-E1
State Description
Startup The system is powered on and then starts to run properly. In the startup
process, the system completes self-check and all relays are in the OFF state.
Setting
You can modify parameters and reset faults using the external operation panel.
This mode is active only when the system is in the stop state. When the system
is running, you can change nothing using the operation panel.
Stop The system is not powered on and all relays are in the OFF state.
Fault The system itself has abnormality, such as self-check failure. In such state, all
relays are cut off. You need to power on the system again.
Normal All functions are normal during running.
Inspection
The system enters the inspection state after the inspection signal becomes
active. In such state, the step loss detection function, motor braking detection
function and handrail speed detection function are disabled, while the other
functions are available.
Manual
reset
The system enters the manual reset state after the manual reset signal
becomes active. In such state, all securitiy functions are disabled and all relay
outputs are in the OFF state.
1.3.2 Description of Security Functions
The following table describes the security functions provided by the MCTC-PES-E1.
Table 1-4 Description of security functions
No. Security Function Description
1 Over-speed protection 1 Check the speed and acts before the speed exceeds
1.2 times of nominal speed.
2 Over-speed protection 2 Check the speed and act before the speed exceeds 1.4
times of nominal speed.
3Unintentional reversal
protection Check the unintentional reversal running.
4 Brake monitoring protection Check the action of the auxiliary brake.
5 Step or pallet loss protection Check whether the step or pallet is lost.
6 Brake monitoring protection Check whether the main brake is released.
7Handrail speed deviation
protection
Check the deviation between the handrail speed and
the actual step or pallet speed. If the speed deviation
is greater than -15% and continues for 15s, the system
performs protection.
8Braking-to-stop distance
detection and alarm
Check the braking-to-stop distance. If the distance
exceeds 1.2 times of the allowable maximum value,
the system performs protection.
9 Floor plate detection switch Check whether the floor plate is opened or removed.

Chapter 1 Product Information
- 12 -
1.3.3 Security Measures After Security Functions Enabled
The following table describes the security measures after the security functions become
enabled.
Table 1-5 Security measures after the security functions enabled
No. Description of Security Function Security
Circuit Open
Power off
the Supply of
Auxiliary Brake
Manual
Reset
1
Check the speed and acts before the
speed exceeds 1.2 times of nominal
speed.
Yes No Yes
2
Check the speed and acts before the
speed exceeds 1.4 times of nominal
speed.
Yes Yes Yes
3Check the unintentional reversal running. Yes Yes Yes
4 Check the action of the auxiliary brake. Yes No No
5 Check whether the step or pallet is lost. Yes No Yes
6Check whether the main brake is
released. Yes No Yes
7
Check the deviation between the
handrail speed and the actual step or
pallet speed. If the speed deviation is
greater than -15% and the duration
exceeds 15s, it performs protection.
Yes No No
8
Check the braking-to-stop distance. If
the distance exceeds 1.2 times of the
allowable maximum value, it performs
protection.
Yes No Yes
9Check whether the floor plate is opened/
removed.
Yes (see the
"Note" below.) No No
NOTE
◆The security circuit of the escalator or moving walkway is cut off after the
floor plate is opened or removed. After the system enters the inspection
state, the fault is reset automatically.

Chapter 2 Installation and Wiring
- 13 -
Chapter 2 Installation and Wiring
2.1 Mechanical Installation
2.1.1 Installation environment requirements
The MCTC-PES-E1 system is installed in the main control cabinet of the machine room of
the escalator or moving walkway. Keep the installation room clean, well ventilated and dust
& moisture proong. when only the control board without the protective guard is installed,
take other dust & moisture proong measures.The installation environment must satisfy the
requirements described in Table 2-1. Monarch will assume no risk or responsibility if a fault
occurs in the system because the installation environment requirements are not satisfied.
Table 2-1 Installation environment requirements
Item Requirements
Ambient temperature -20°C to +65°C
Humidity Less than 95% RH, without condensing
Mounting location Free from conducting materials, corrosive gas, combustible gas,
metal powder, oil dirt and dust
IP level
IP00 (no IP level requirement on board)
IP5X (with housing)
Note: The MCTC-PES-E1 system has the housing that satisfies
IP5X. If you purchase the board only, install the board in the control
cabinet or other housing satisfying IP5X.
2.1.2 Installation Dimensions
The following figure shows the dimensions of the MCTC-PES-E1 system.
260.0
245.0
4-5.5
4-8.0
150.0
187.0
42.8
78.8
Switching-mode
power supply
Figure 2-1 Dimensions of the MCTC-PES-E1 system (Unit:mm)
Only the control board (without the protective guard) is required in some applications. The
following figures show the physical appearance and installation dimensions of the control
board.

Chapter 2 Installation and Wiring
- 14 -
CN3 CN4 J3
CN1
101.0
148.0
162.0
7.0
88.0
201.0
178.0
6.0
Φ6.0
CN5
RJ45
Figure 2-2 Physical appearance of the control board (Unit:mm)
2.1.3 Installation Instructions
To install the MCTC-PES-E1 system, do as follows:
1) Process the installation side in the main control cabinet. For the processing dimensions,
refer to Figure 2-1.
2) Mount the MCTC-PES-E1 on the installation side and fix it with screws.
If only the control board (without the protective guard) is required, do as follows:
1) Process the installation side in the main control cabinet. For the processing dimensions,
refer to Figure 2-2.
2) Mount the control board on the installation side and fix it with screws.
Caution
◆The switching-mode power supply has been fixed on the protective guard of the MCTC-
PES-E1 system upon delivery.
◆The screws for fixing the protective guard are not delivered together with the MCTC-
PES-E1 and you need to prepare them yourself. When selecting screws, consider the plate
thickness of the installation side, the thickness of the protective guard and the dimension of
the hole in Figure2-1.
2.2 Installation of Sensors
2.2.1 Technical Data of Sensors
The following table describes the technical data of the sensors.

Chapter 2 Installation and Wiring
- 15 -
Table 2-1 Technical data of Schneider sensors
Brand Schneider
Sensor Escalator/Moving
walkway speed sensor Handrail speed sensor Step loss detection
sensor
Model XS2 18BLNAL2C
XS2 18BLPAL2C
XS2 12BLNAL2C
XS2 12BLPAL2C
XS2 30BLNAL2C
XS2 30BLPAL2C
Diameter 18mm 12mm 30mm
Sensing
Distance ≤ 8mm ≤ 4mm ≤ 15mm
Length 50.6mm 41.3mm 50.6mm
Power
Supply (DC) 12-24V 12-24V 12-24V
Output NPN、PNP NPN、PNP NPN、PNP
Definition of
Cables
Brown (BN): positive
Blue (BU): negative
Black (BK): output signal
Brown (BN): positive
Blue (BU): negative
Black (BK): output signal
Brown (BN): positive
Blue (BU): negative
Black (BK): output signal
Appearance
Dimension
a=50.6mm;b=40.4mm a=50.6mm;b=34.1mm a=50.6mm;b=35.4mm
Table 2-2 Technical data of OMRON sensors
Brand OMRON
Sensor
Escalator/Moving
walkway speed
sensor
Handrail speed
sensor Step loss detection sensor
Model E2B-M18KN16-
WP-C1-MNK
E2B-M12KN08-
WP-C1-MNK
E2B-M30KN20-
WP-C1-MNK
E2B-M30LN30
-WP-C1-MNK
Diameter 18mm 12mm 30mm 30mm
Sensing
Distance ≤ 16mm ≤ 8mm ≤ 20mm ≤ 30mm
Length 56mm 47mm 60mm 82mm
Power
Supply
(DC)
10-30V 10-30V 10-30V 10-30V
Output NPN NPN NPN NPN

Chapter 2 Installation and Wiring
- 16 -
Brand OMRON
Definition of
Cables
Brown (BN):
positive
Blue (BU): negative
Black (BK): output
signal
Brown (BN):
positive
Blue (BU):
negative
Black (BK): output
signal
Brown (BN):
positive
Blue (BU): negative
Black (BK): output
signal
Brown (BN): positive
Blue (BU): negative
Black (BK): output
signal
Appearance
Dimension
2.2.2 Installing the Speed Sensor and Running Direction Sensor for
Escalator/Moving Walkway
1 Installation
1) Installation position
Align the center of the sensing face of one sensor with the center of one tooth on the
driving chain sprocket and align the sensing edge of the other sensor with the center of the
neighboring tooth on the driving chain sprocket, as shown in the following figure.
2) Installation distance
3mm ≤ LA=LB ≤ 8mm
Speed measured
By the driving chain
sprocket
R
Sensor A
Sensor B
LB
LA
Sensor A
signal
Sensor B
signal
Figure 2-3 Installation of the escalator/moving walkway speed sensor and running direction
sensor

Chapter 2 Installation and Wiring
- 17 -
2 DetectionPrinciple
1) Overspeed protection function
By measuring the speed of the driving chain sprocket through sensor A and sensor B, the
MCTC-PES-E1 system judges whether the running speed of the escalator/moving walkway
exceeds the allowable speed. If yes, the MCTC-PES-E1 system will perform overspeed
protection.
When the driving chain sprocket rotates, every time a sensor detects a tooth, the sensor
sends a pulse. The MCTC-PES-E1 system calculates the running speed of the escalator/
moving walkway based on the time interval of detected pulses.
Sensor A and sensor B are redundant speed measuring channels for each other. By setting
a certain pulse cycle or frequency threshold, 1.2 times or 1.4 times overspeed can be
detected.
2) Unintentional reversal protection
By fixing the relative positions of the two sensors correctly, make the phase of sensor A in
advance of the phase of sensor B and ensure that the two sensors have overlapping pulse
part. In this case, the MCTC-PES-E1 system detects the logic sequence of the two sensors
and judges the actual running direction of the escalator/moving walkway through the logic
sequence, preventing reversal running.
2.2.3 Installing the Handrail Speed Sensor
1 Installation
1) Installation position
Align the sensor with the inductive part on the tachometer wheel.
If the tachometer wheel is made of plastic, use a ferric device as the inductive part. If the
tachometer wheel is ferric, drill a hole as the inductive part in the wheel. The section size of
the inductive part should be approximate to that of the sensing face of the sensor.
2) Installation distance
1 mm ≤ L3 = L4 ≤ 4 mm
The following figure shows the installation position of the handrail speed sensor.
Sensor 3/4
L3/4
Sensor 3/4
Sensor 3/4 signal
Tachometer wheel Inductive part
Handrail
Figure 2-4 Installation position of the handrail speed sensor

Chapter 2 Installation and Wiring
- 18 -
2 DetectionPrinciple
Sensor 3/4 is used to measure the left/right handrail speed. The tachometer wheel is
driven by the handrail to rotate and its linear speed is basically consistent with the handrail
speed. An inductive part is set on the tachometer wheel to mount sensor 3/4 on a fixed
mechanical structure with the sensing face toward the inductive part.
When the tachometer wheel follows the handrail to rotate, sensor 3/4 outputs pulses, as
shown in Figure 3-5. A pulse is output every time the tachometer wheel rotates a revolution.
With the pulses and radius of the wheel, the system can measure the rotational speed of
the tachometer wheel. Then the system calculates the handrail speed and compares it
with the escalator/moving walkway speed. If the handrail speed is lower than 85% of the
corresponding escalator/moving walkway speed and the handrail underspeed continues
for 15s, the system cuts off the power supply to the safety circuit of the escalator/moving
walkway to stop the running, implementing protection.
2.2.4 Installing the Step/Pallet Loss Sensor
1 Installation
1) Installation position
For aluminum step or pallet, it is suggested to select NBN40-L2-E0-V1 (P+F), whose
detection distance is long and signal is reliable. Each step/pallet loss sensor is required for
the top and bottom machine rooms respectively. Install the sensor with the sensing face
toward the step beam to be detected.
2) Installation distance
5 mm ≤ L5 = L6 ≤ 15 mm
The following figure shows the installation position of sensor (5/6) for the escalator.
Step beam to be detected
L5/L6
Step/Pallet loss
sensor5/6
Step
Figure 2-5 Installation position of the step/pallet loss sensor

Chapter 2 Installation and Wiring
- 19 -
Step
Sensor 5/6
L5 / L6
Sensor 5/6
signal
Figure 2-6 Installation position of the step/pallet loss sensor for escalator
2 DetectionPrinciple
Each sensor (5/6) is installed in the return/driving station in the top/bottom machine room,
respectively to detect step loss. Based on signals of speed sensor A/B for the motor, the
system calculates the number of pulses of sensor A/B between two adjacent pulses of
sensor 5/6 to judge whether step/pallet loss occurs.
When a step passes, sensor 5/6 receives the signal and outputs a pulse. Set the time
interval between two adjacent pulses of sensor 5/6 as T and the pulse counting of sensor
A/B within T as X. In the case of no step loss, the X value is within a certain threshold
regardless of the escalator speed. If X exceeds the threshold, the system judges that step
loss occurs. Then the escalator stops running immediately and enters the safety state.
NOTE
◆If the detection principle is not suitable to the use habit of escalator
manufacturers, step loss can be monitored by using sensor 5/6 to detect the
step auxiliary wheel. The prerequisite is to ensure that the auxiliary wheel is
lost while the step gets lost in any way.
To detect whether a pallet of the moving walkway is lost, install sensor 5/6 in the machine
room, as shown in the following figure.
Table of contents
Other Inovance Control System manuals
Popular Control System manuals by other brands
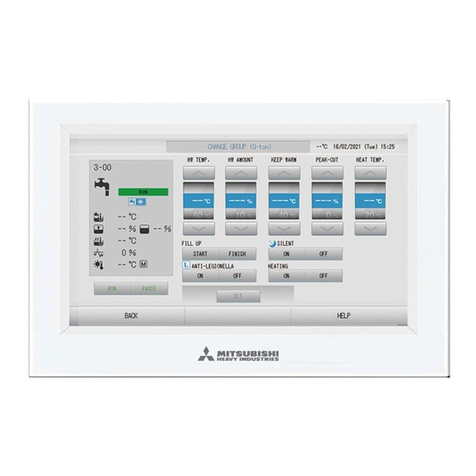
Mitsubishi Heavy Industries
Mitsubishi Heavy Industries SC-SL4-AE Technical manual
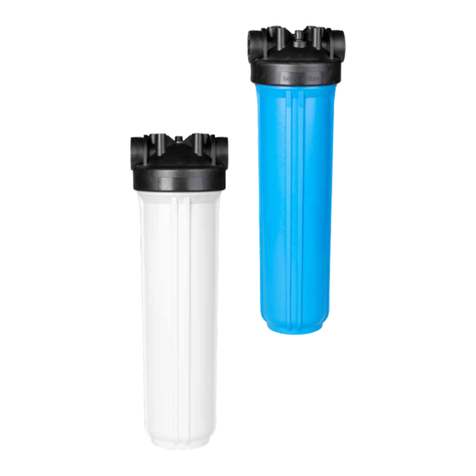
Watts
Watts OneFlow OFTWH-R Installation and operation manual
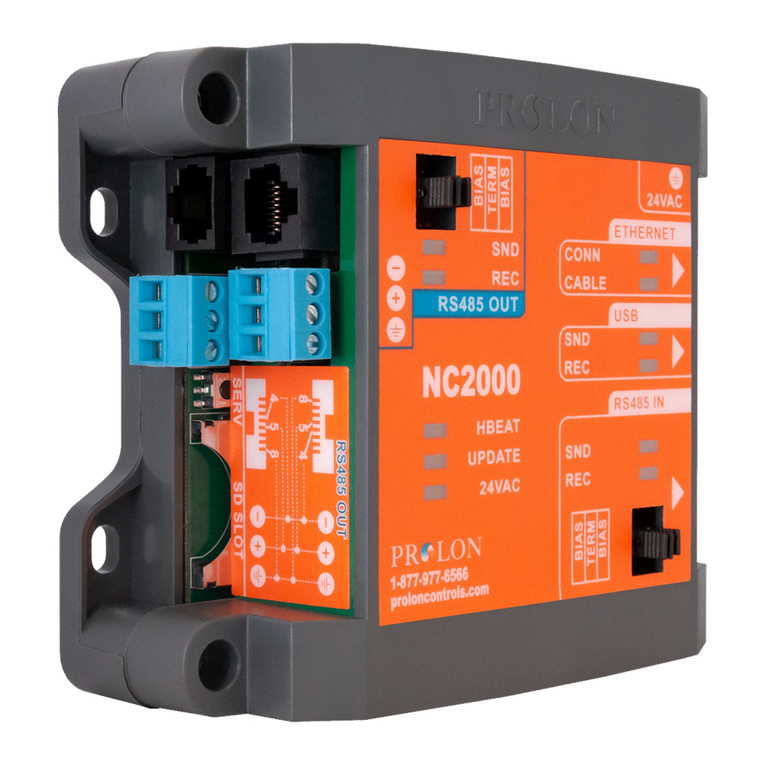
Prolon
Prolon NC2000 quick start guide
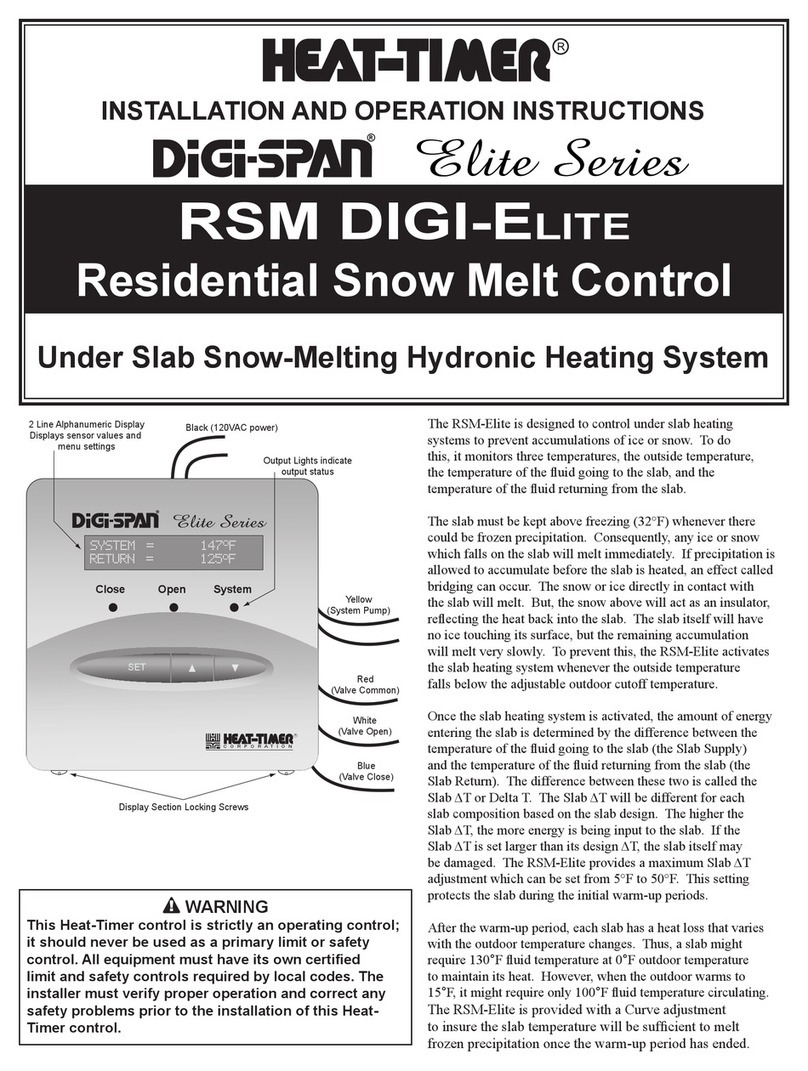
heat-timer
heat-timer DiGi-SPAN Elite Series Installation and operation instruction

Riello
Riello ricloud user manual
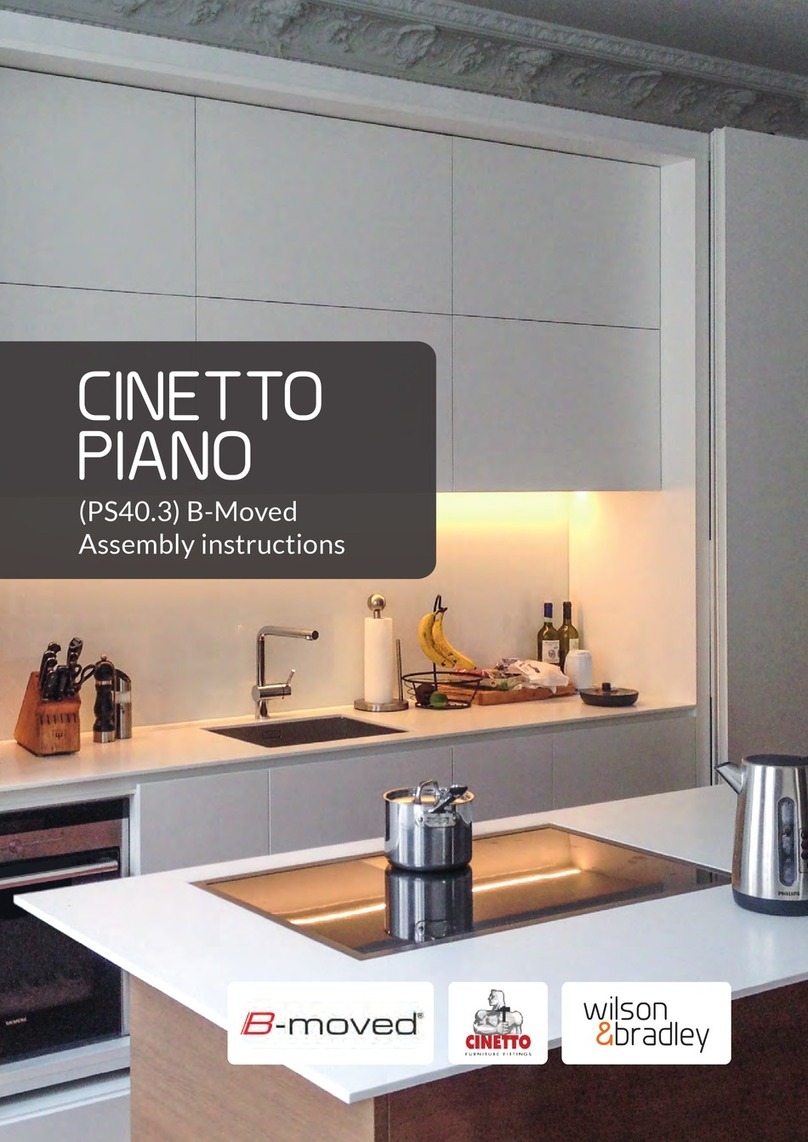
cinetto
cinetto Piano B-Moved Assembly instructions