ITT McDonnell & Miller FS8-W Series Maintenance and service guide

Series FS8-W
General Purpose
Liquid Flow Switch
OPERATION
This control is an independently mounted water flow
sensing device that makes or breaks an electrical
circuit when flow stops or starts.
• Before using product, read and understand instructions.
• Save these instructions for future reference.
• All work must be performed by qualified personnel trained in the proper application,
installation, and maintenance of plumbing, steam and electrical equipment and/or systems in
accordance with all applicable codes and ordinances.
• To prevent electrical shock, turn off the electrical power before making electrical
connections.
• To prevent an electrical fire or equipment damage, electrical wiring insulation must have a
rating of 167˚F (75˚C) if the liquid’s temperature exceeds 180˚F (82˚C).
• To prevent electrocution, when the electrical power is connected to the flow switch, do not
touch the terminals.
• Make sure flow switch electrical cover is secured before turning on electric power.
Failure to follow this warning could cause property damage, personal injury or death.
WARNING CAUTION
!
WARNING
Series FS8-W
Now
with
Stainless Steel
Paddles
McDonnell & Miller
Installation & Maintenance
Instructions
MM-600(G)

2
NOTE: Switch on ‘G’ models is rated for 300 watts @ 125VAC.
Maximum Liquid Pressure: 160 psi (11.3 kg/cm2)
Liquid Temperature Range (TL): 32 - 225˚F (0 - 107˚C)
Ambient Temperature Range (TS): 32 - 120˚F (0 - 49˚C)
Electrical Enclosure Rating: Nema Type 4X (IP 56)
Maximum Velocity: 10ft/sec (3M/sec)
Pipe Connection Thread Size: - 1" NPT
- All models
except “J”
- 1" BSPT
- “J” models
• This Control: is for continuous operations
is not electronic
has Type 1C action (micro
interruption on operation)
• LVD 73/23/EEC
• EMC 89/33/EEC
For applications with loads between 0.5 and 3.7 Amps,
power factors exceeding 0.65, an anticipated system
switch
operation rate of less than once per 2.5 minutes,
and any
one cycle greater than 3 seconds on and 3
seconds off.
For applications with loads 0.5 and 38mA, power
factors exceeding 0.65, an anticipated system switch
operation rate of less than once per 5 minutes, and any
one cycle greater than 3 seconds on and 3 seconds
off.
Additional suppression may be required for applica-
tions outside these ranges.
• Declaration of Conformity
Available on request.
SPECIFICATIONS
CE Circuit Rating
7.4 (7.4)/120~ 0.3/120=
3.7 (3.7)/240~ 0.15/240=
Motor Switch Rating (Amperes)
Voltage Full Load Locked Rotor Pilot Duty
120 VAC 7.4 44.4 125 VA at
240 VAC 3.7 22.2 120 or 240 VAC
50 or 60 cycles
ELECTRICAL RATINGS
Models that meet CE Conformance:
FS8-WJA-E

3
NOTE: DO NOT USE LIQUID FLOW SWITCHES ON SYSTEMS
WITH FLOW VELOCITY GREATER THAN 10 FEET
(3M) PER SECOND.
Pipe Mode of Operation
Size NPT Flow Velocity No Flow Velocity
in. (mm) Settings gpm (lpm) fps (mps) gpm (lpm) fps (mps)
Factory or
1 (25) Minimum 4.9 (18.5) 1.82 (.55) 3.4 (12.9) 1.25 (.38) 27
Maximum 17.6 (66.6) 6.53 (2.60) 15 (56.8) 5.56(1.69) (102)
Factory or
1
1⁄4
(32) Minimum 7.5 (28.4) 1.60 (.49) 5.3 (20.1) 1.14 (.35) 47
Maximum 29 (110) 6.23 (1.9) 24.6 (93.1) 5.28(1.61) (178)
Factory or
1
1⁄2
(40) Minimum 9.4 (35.6) 1.48 (.45) 6.7 (25.4) 1.05 (.32) 63
Maximum 37.8 (143) 5.95 (1.81) 32.2 (122) 5.07 (1.54) (239)
Factory or
2 (50) Minimum 13.7 (51.8) 1.31 (.4) 9.4 (35.6) .9 (.27) 105
Maximum 56.4 (214) 5.39 (1.64) 47.4 (179) 4.53 (1.38) (398)
Factory or
2
1⁄2
(65) Minimum 17.9 (67.8) 1.20 (.36) 12.1 (45.8) .81 (.25) 149
Maximum 71.3 (270) 4.78 (1.46) 59.2 (224) 3.97 (1.21) (565)
Factory or
3 (80) Minimum 24.2 (91.6) 1.05 (.32) 16.4 (62.1) .71 (.22) 230
Maximum 89 (337) 3.87 (1.18) 72.5 (274) 3.15 (.96) (872)
Factory or
4 (100) Minimum 35.3 (134) .89 (.27) 27 (102) .68 (.21) 397
Maximum 118 (446) 2.89 (.91) 105 (397) 2.64 (.8) (1505)
Factory or
5 (125) Minimum 48.6 (184) .78 (.24) 37.4 (142) .6 (.18) 654
Maximum 178 (674) 2.86 (.87) 160 (606) 2.57 (.78) (2479)
Factory or
6 (150) Minimum 60.3 (228) .67 (.20) 46.8 (177) .52 (.16) 900
Maximum 245 (927) 2.72 (.83) 225 (852) 2.5 (.76) (3411)
Values are ± 10%
Max. Flow
Rate gpm
(lpm) w/o
Paddle Damage
FLOW RATES
Flow rates required to activate flow switch are shown
in chart below. The values are calculated for sensing
water (potable, non-polluted) in a horizontal pipe.
Settings will vary when used to sense flow of other
fluids or if located in a vertical pipe.

4
a. If the paddle must be trimmed, measure the
paddle from the center of large hole (A) to the
length required. Using non-serrated tin snips,
trim the end (B) on a curve just like the paddle
was originally cut.
A
BRequired
Length
STEP 1 - Paddle Sizing
1" (25mm)
2" (51mm)
3" (76mm)
6" (152mm)
Determine the correct paddle length for your installation from the
chart below.
NOTE: All models include 4 paddles as shown.
Pipe Flow No-Flow
Size NPT Maximum Maximum
in. (mm) Adjustment Adjustment
2 (50) 118.5 99.5
3 (80) 278.0 227.0
4 (100) 442.0 391.0
5 (125) 847.0 762.0
6 (150) 1440.0 1325.0
Series FS8-W “K” Factor
b. If the flow rate in the pipe exceeds the
maximum adjustment on the Flow Switch
use the following formula to change the
paddle lengths.
Paddle Length = K
_______________
Flow Rate (GPM)
NOTE: If trimming the paddle for a no-flow action make sure
there is enough flow to activate switch.
Pipe Size Paddle Trim to Length
(Standard Length)
in. (mm) in. (mm) in. (mm)
1 (25) 1 (25) N/A
1 1/4 (32) 2 (25) 1 1/4 (32)
1 1/2 (40) 2 (51) 1 1/2 (38)
2 (50) 2 (51) 1 5/8 (41)
2 1/2 (65) 3 (76) 2 1/4 (57)
3 (80) 3 (76) 2 5/8 (67)
4 (100) 6 (152) 3 5/8 (92)
6 (150) 6 (152) 5 5/8 (143)
8+ (200+) 6 (152) N/A

5
D
FLUID FLOW
D= PIPE DIAMETER
1" PIPE
CONNECTION
5 x D
MINIMUM
5 x D
MINIMUM
a. The flow switch must be installed in the pipe using
a threaded tee connection or welding fitting of
minimum length such as a half coupling. Use a
face or hex bushing to reduce the tee outlet to 1"
pipe thread if a reduced tee outlet thread size fitting
is not available.
1" MAX
(25mm)
Paddle Arm
b. When installing brazed/soldered copper pipe,
size the threaded adapter to ensure the paddle
arm extends into the main run of the pipe.
• The flow switch
should be located in a horizontal
section of pipe
where there is a straight horizontal
run of at least 5 pipe diameters on each side of the
flow switch. The flow switch may be installed in a
vertical pipe if the flow is in the upward direction.
• The flow switch
must be installed in the upright
position
as shown with arrow mark on side of casting
in the same direction as fluid will flow.
•
Some system conditions that require more than 5 pipe
diameters are high viscosity fluid and high fluid velocity.
• The flow switch must be installed in the pump suction
piping when spring-loaded check valves and/or other
close coupled accessories are installed in the pump
discharge piping.
1" (25mm)
1"
(25mm)
1"
(25mm)
1" (25mm)
2"
(50mm)
11/4"
(32mm)
11/2"
(40mm)
11/4"
(32mm)
2"
(50mm)
11/2"
(40mm)
FACE OR HEX.
BUSHING
2" (50mm)
3" (80mm)
2" (50mm)
3" (80mm)
11/4" (32mm) 1
1/4" (32mm)
11/2" (40mm)11/2" (40mm)
21/2" (65mm) 21/2" (65mm)
2" (50mm)
3" (80mm)
1" MAX
(25mm)
1" (25mm)
4" (100mm)
6" (150mm)
2" (50mm)
3" (80mm)
4"(100mm)
6"(150mm)
21/2"(65mm) 21/2" (65mm)
Threaded
Pipe
Threaded
Pipe
CORRECT INCORRECT
Threaded
Pipe
Welded
Pipe
STEP 2 - Determine the Location of the Flow Switch
STEP 3 - Connecting the Flow Switch to Pipe
a. Insert the 8/32 x 5/16" screw through lock washer, new larger
washer and paddle. Attach screw to the paddle arm and tighten
to a torque of approximately 12-16 lb•in (1.36-1.81 N•m).
NOTE: If two paddles are being installed, they must be stacked one on top
of the other with the longer paddle first in line to the flow.

6
x 4
A
a. Cover Removal and Installation Procedure
• Using a flathead screwdriver, unscrew the four
cover screws and remove the electrical connec-
tion cover (A).
• Place electrical connection cover on the flow
switch and insert four cover screws. Tighten the
screws to 10 lb•in (1.13 N•m).
STEP 4 - Electric Wire Connections
• To prevent electrical shock, turn off the electrical power before making electrical connections.
• To prevent an electrical fire or equipment damage, electrical wiring insulation must have a rating of 167˚F
(75˚C) if the liquid’s temperature exceeds 180˚F (82˚C).
• To prevent electrocution, when the electrical power is connected to the flow switch, do not touch the
terminals.
• Make sure flow switch electrical cover is secured before turning on electric power.
Failure to follow this warning could cause property damage, personal injury or death.
!
WARNING
c. Insert the flow switch into the pipe tee. Turn
the flow switch two (2) or three (3) revolutions
clockwise until tight. Do not put excessive
force on cover when turning.
FLOW
d. Place a 1 3/8" open end wrench on flow switch
body to tighten to final position. Final position
is with arrow on body aligned in the same
direction as liquid flow.
Teflon®
b. Apply pipe sealing compound or Teflon®tape to the
flow switch pipe threads.
NOTE: Do not apply sealant to first threads as this
switch is grounded (earthed) via the pipe mounting.

7
b. Electrical Conduit Connection
• Connect electric conduit to flow switch electrical enclosure.
• Follow accepted electrical practices when installing fittings
and making connections.
• Refer to and follow local codes and standards when
selecting the types of electrical fittings and conduit to
connect to flow switch.
c. Determine which switch action is required for the
flow switch.
• “Flow” means that the switch will close circuit
C.-N.O. and open circuit C.-N.C. when flow rate
is increased above setpoint of flow switch.
• “No Flow” means that the switch will open circuit
C.-N.O. and close circuit C.-N.C. when flow rate
is decreased below setpoint of flow switch.
d. Based upon the mode of operation (“Flow” or “No-
Flow”) required, complete the appropriate steps to
connect wires to flow switch. Use a Phillip’s head
screwdriver to loosen and tighten switch terminal
screws when attaching wires.
For “Flow” Mode of Operation (Fig. 1)
If the flow switch will be used to actuate a signal,
alarm or other device when
flow
occurs, connect
the wire from that device to the “N.O.” contact.
Connect the “Hot” power supply wire to “C” terminal.
For “No Flow” Mode of Operation (Fig. 2)
If the flow switch will be used to actuate a signal,
alarm or other device when
no flow
occurs, connect
the wire from that device to the “N.C.” contact.
Connect the “Hot” power supply wire to “C” terminal.
COMMON
NORMALLY
OPEN
NORMALLY
CLOSED
Flow
Opens
Circuit
Normally
closed
3
Common
1
Flow
Closes
Circuit
2
(
(
Normally
open
(
(
Common
(
(
FS8-W LINE
LOAD
Fig. 1
HOT
31
2
FS8-W LINE
LOAD
Fig. 2
HOT
31
2
a. Place cover on flow switch and turn on power. Initiate fluid
flow through the system. Observe the device being
activated by the flow switch to determine if device is
operating as required.
b. Turn off fluid flow to determine if device is operating
as required.
c. Repeat initiating and turning off fluid flow several times to
test flow switch and device for proper operation.
- If operating as required, put system into service.
- If not operating as required, Flow Switch may need
to be adjusted.
OFF
ON
STEP 5 - Testing
C. N.O.
FLOW
N.C. C. N.O.
NO FLOW
N.C.

MAINTENANCE
SCHEDULE:
• Inspect paddle annually. Turbulent or high
flow velocity conditions may require more
frequent inspection and/or replacement.
• Replace paddle if damaged or showing signs
of wear.
• Replace flow switch every 5 years or 100,000
cycles, whichever occurs first.
TROUBLESHOOTING
Problem:
1. Flow Switch Does Not Operate
Solution:
a. Make sure power has been turned on to device
and flow switch.
b. Verify that flow rate is high enough for flow switch
to activate. Measure flow rate and match with
velocities shown in flow rate chart.
c.
Check to see if paddle moves freely. Some system
piping disassembly may be required.
2. Flow Switch Operates Erratically
Solution:
a. Flow switch may be located in an area of high
turbulence causing paddles to flutter.
b. Adjustment screw may have been turned below
original factory setpoint. Verify that flow rate is high
enough for flow switch to activate. Measure flow
rate and match with velocities shown in flow
rate chart.
c.
Check to see if paddle moves freely. Some system
piping disassembly may be required.
3. Flow Switch Does Not Deactivate
Solution:
a.
Check to see if paddle moves freely. Some system
piping disassembly may be required.
b.
Measure flow rate and match with velocities shown
in flow rate chart. Flow switch must prove flow
before it can indicate no flow.
STEP 6 - Adjustment
COMMON
NORMALLY
OPEN
NORMALLY
CLOSED
ADJUSTMENT
SCREW
Adjustment is necessary only if required flow/no flow set-
points are above factory set minimum.
a. Turn off power. Remove electric enclosure cover.
b. Turn the adjusting screw clockwise to increase setpoint.
c. Place cover on flow switch and turn on power.
d. Test the operation of the flow switch after each
adjustment.
IMPORTANT: Do not attempt to lower flow switch
setpoint from original factory minimum setting.
Lowering (turning adjusting screw counterclock-
wise) the setpoint from original factory setting
may cause erratic flow switch operation.
McDonnell & Miller
Table of contents
Other ITT Switch manuals
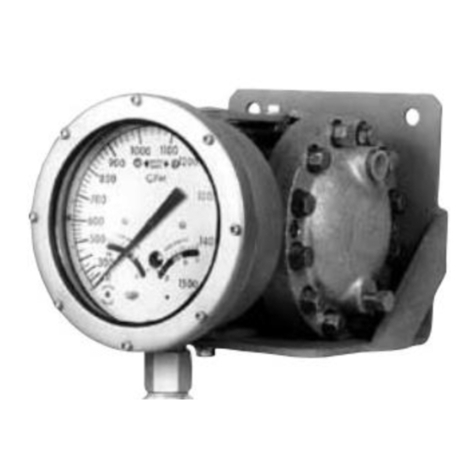
ITT
ITT BARTON 581A User manual
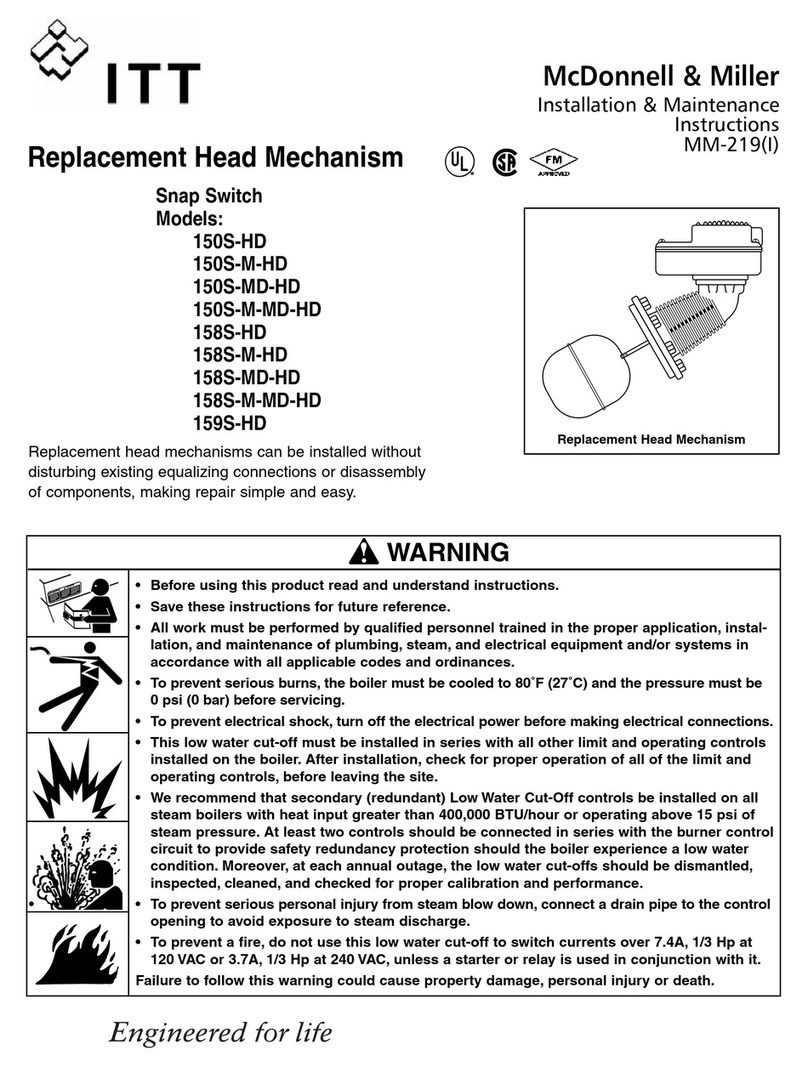
ITT
ITT 150S-HD Installation and operating instructions
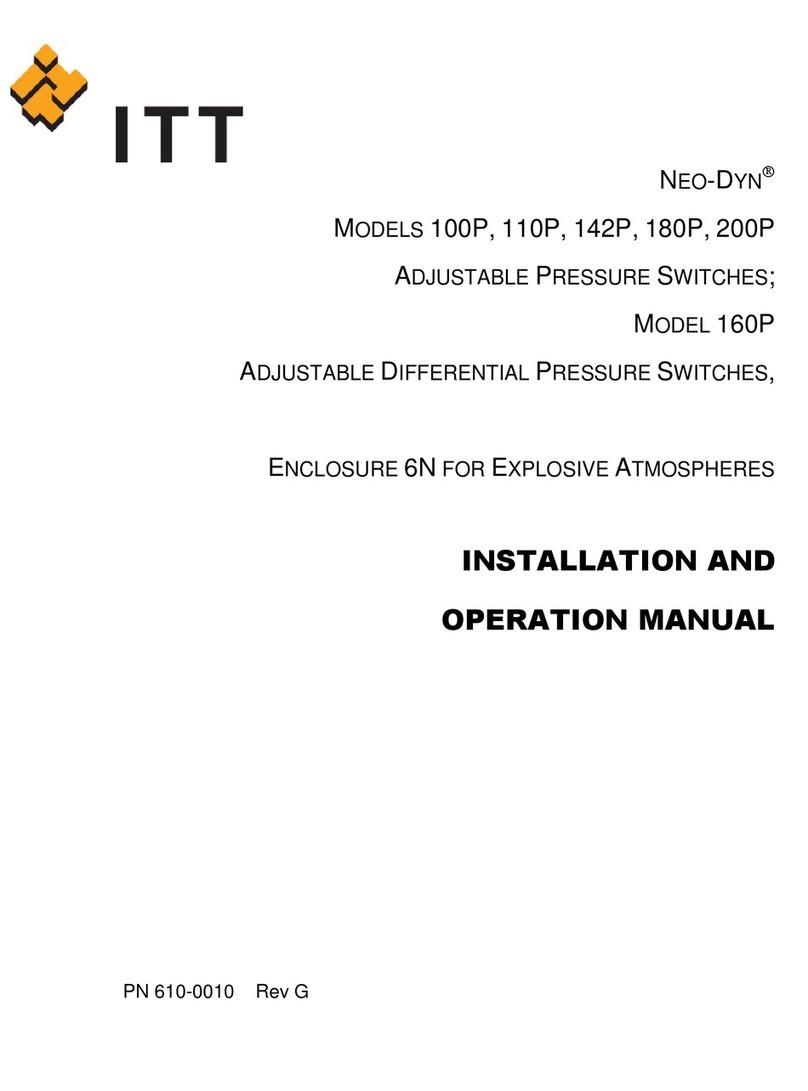
ITT
ITT NEO-DYN 142P User manual
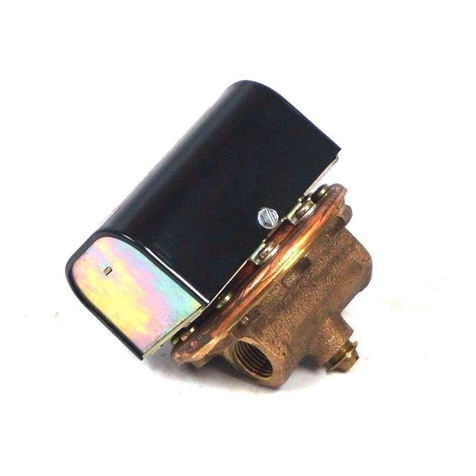
ITT
ITT McDonnell & Miller FS1 Series Installation and operating instructions
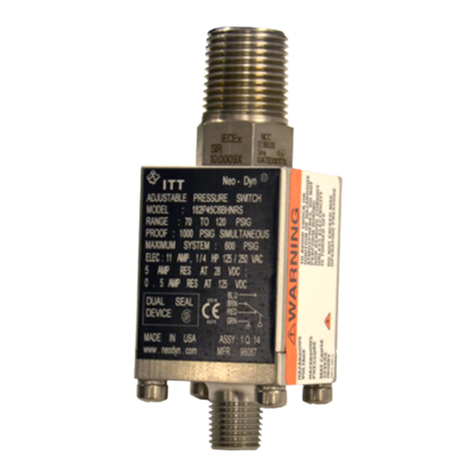
ITT
ITT NEO-DYN 182P User manual
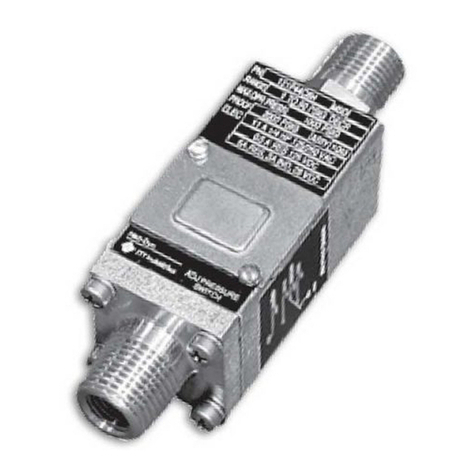
ITT
ITT NEO-DYN 122P Owner's manual
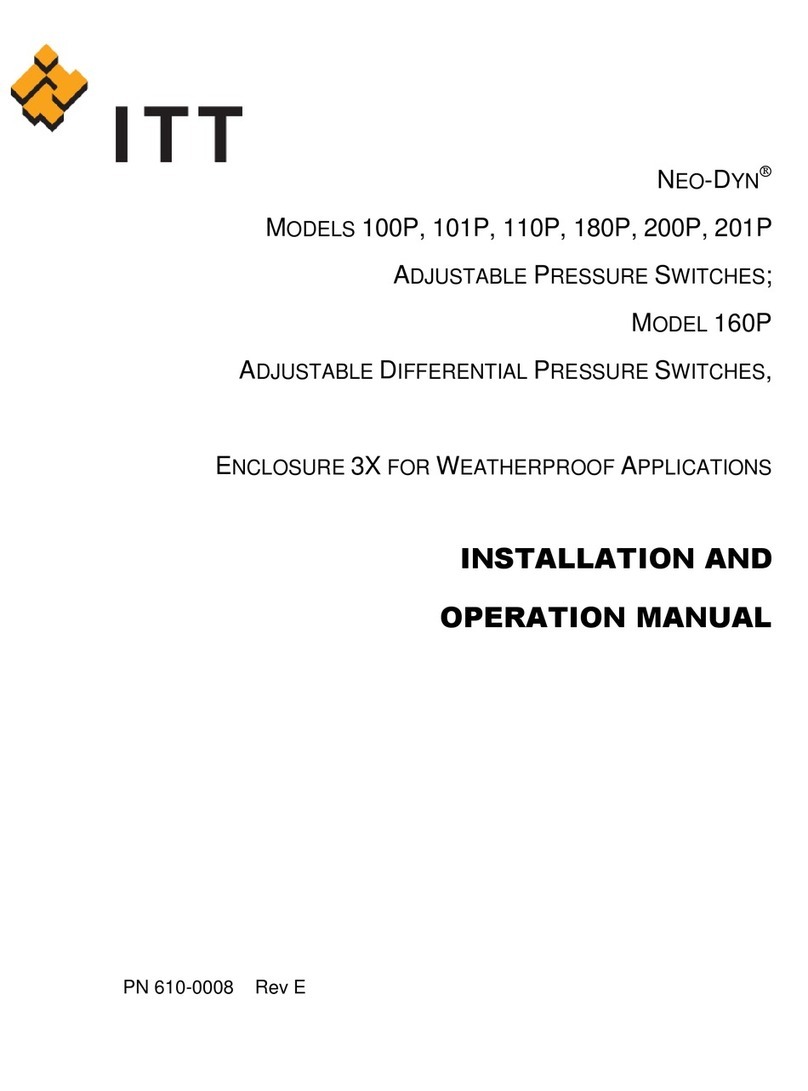
ITT
ITT neo-dyn 100p User manual
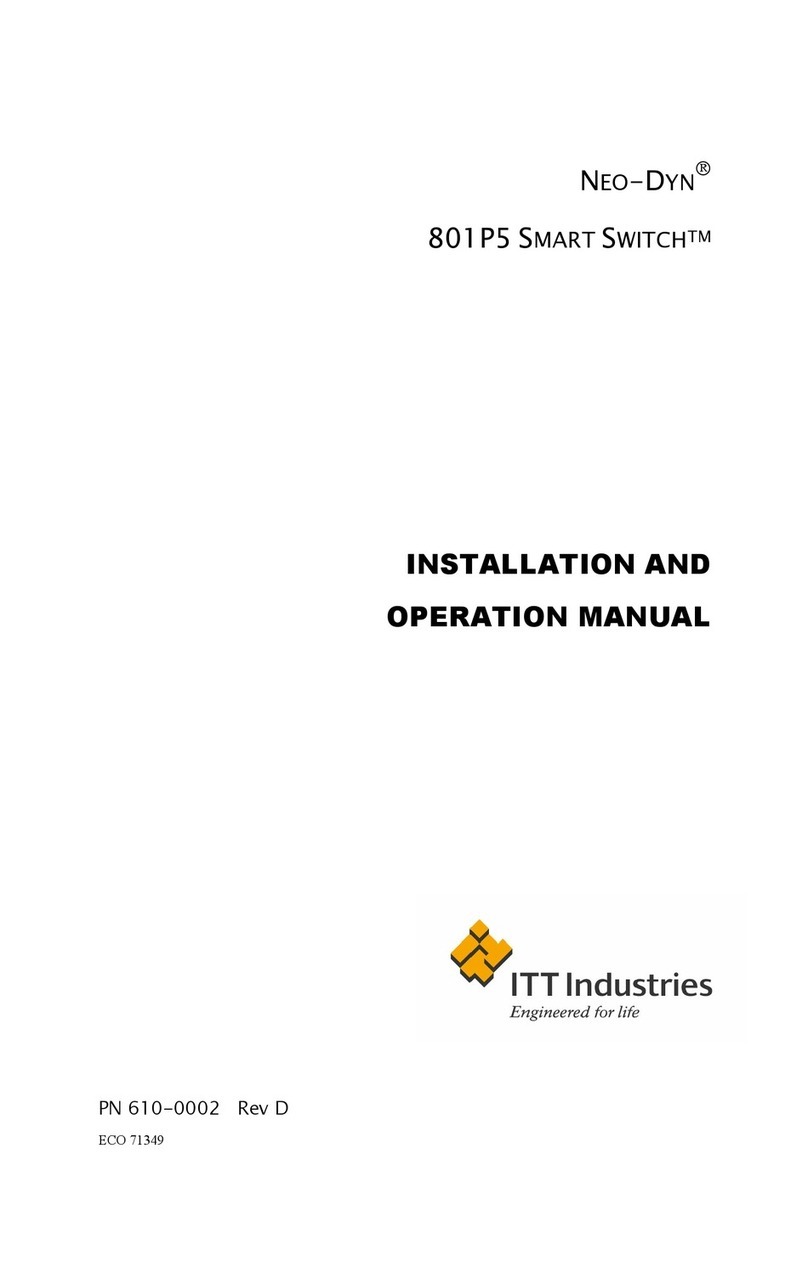
ITT
ITT Neo-Dyn 801P5 User manual
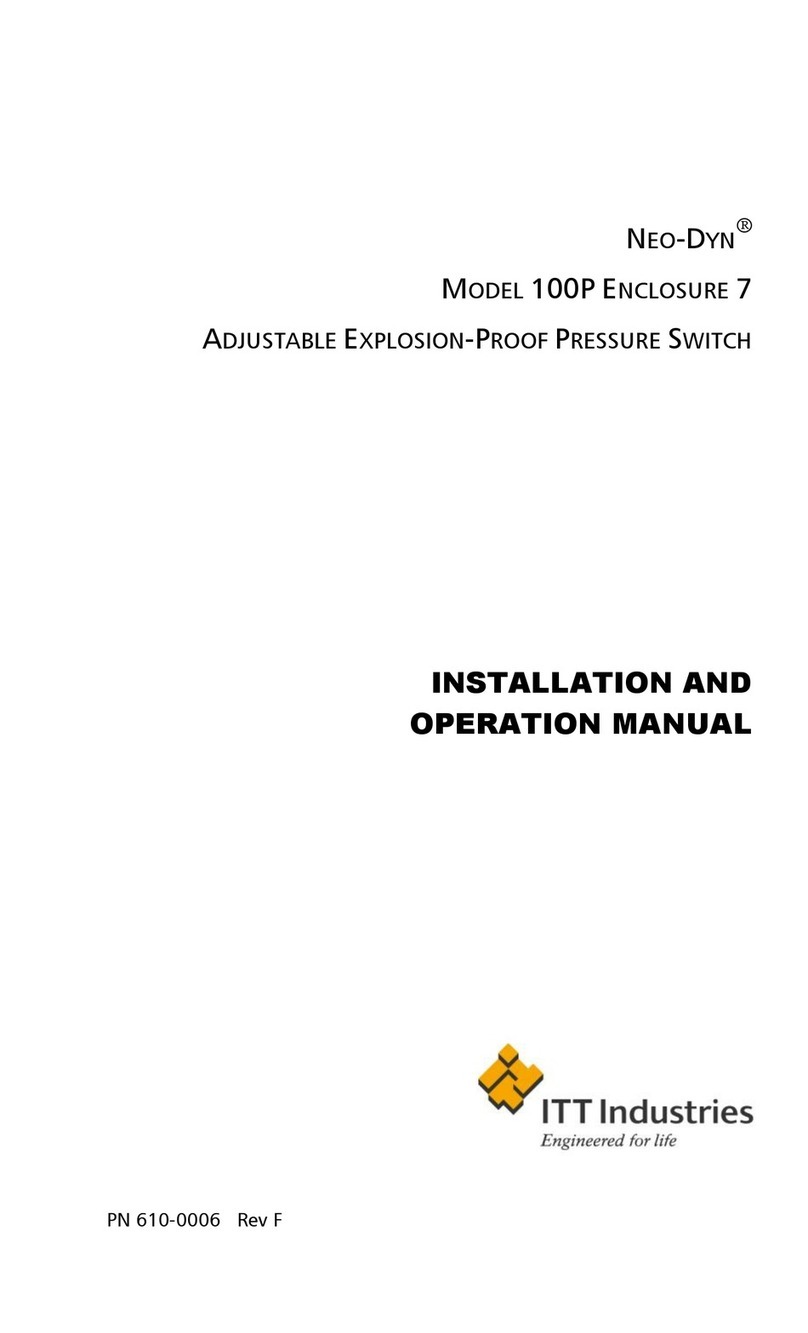
ITT
ITT NEO-DYN 100P ENCLOSURE 7 User manual
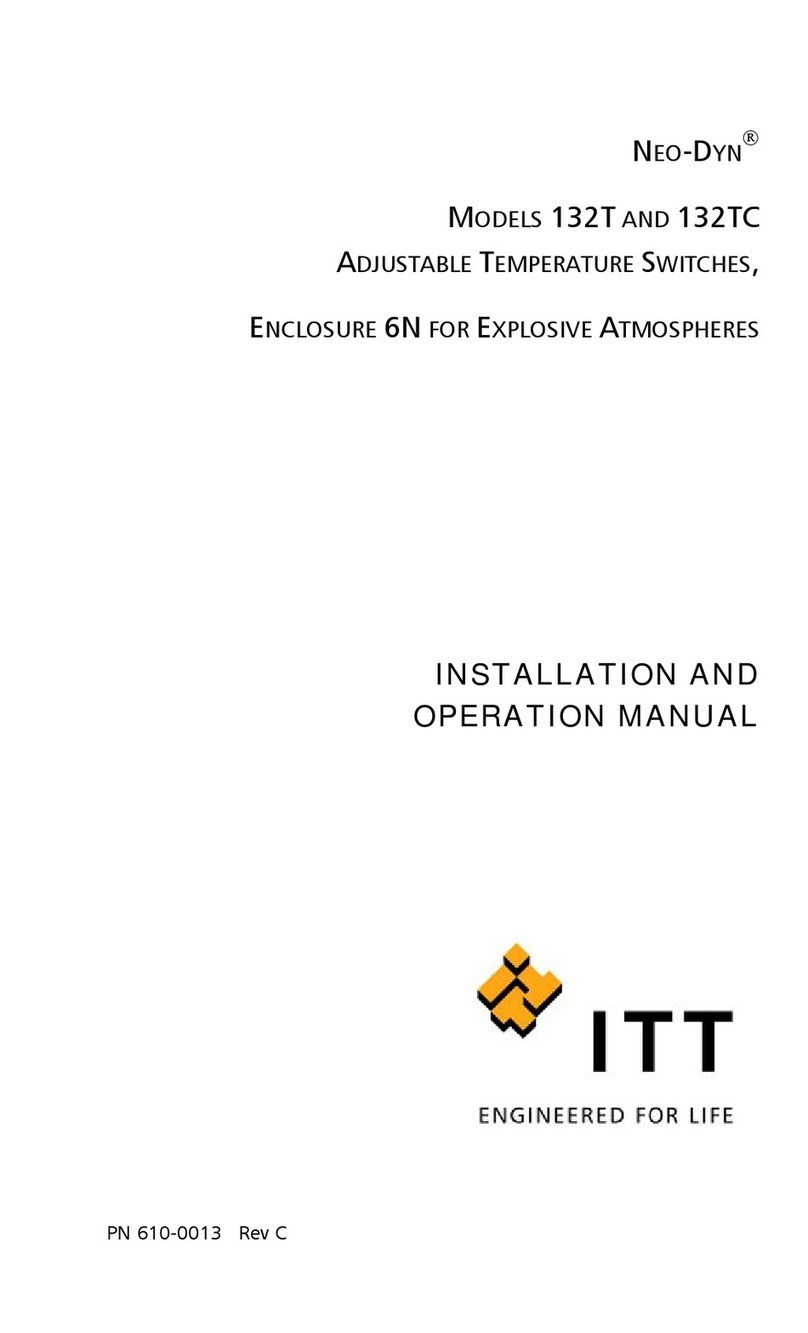
ITT
ITT NEO-DYN 132T User manual
Popular Switch manuals by other brands

Belden
Belden grass valley MASTERPIECE 12G-SDI installation manual
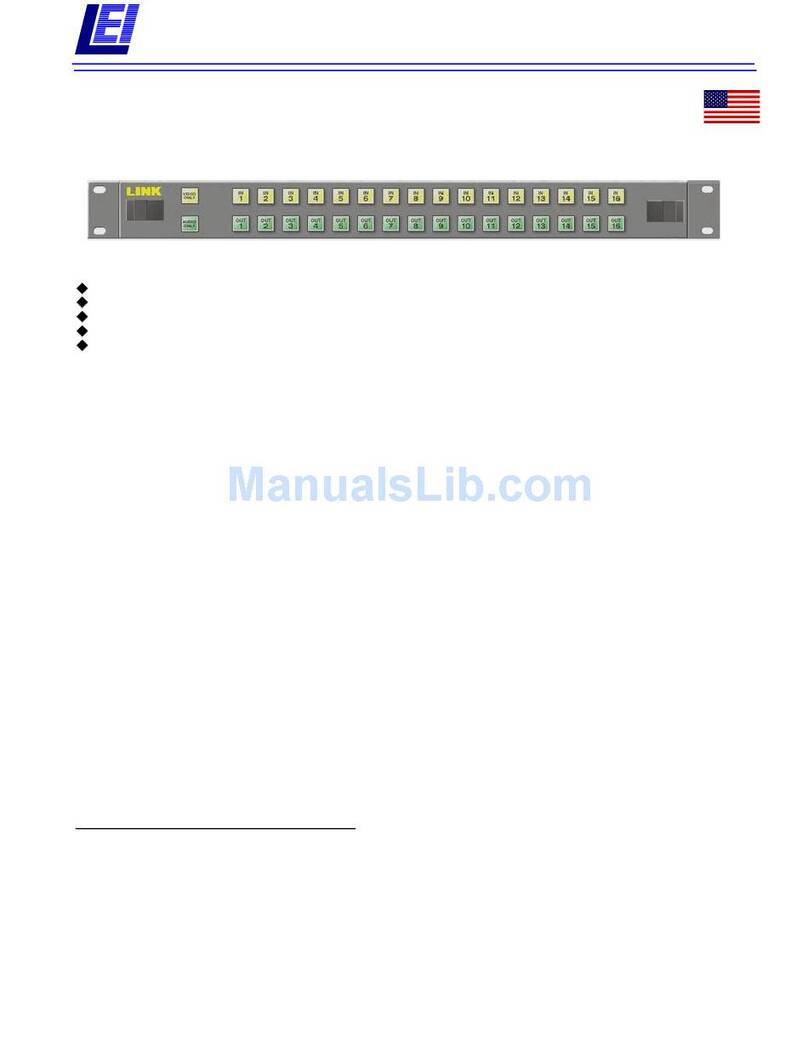
Link electronics
Link electronics 861-XL1616G Specification sheet

Velleman
Velleman WRS4 user manual
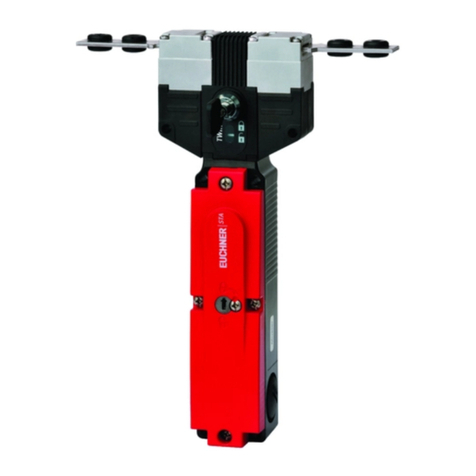
EUCHNER
EUCHNER STA-TW Series operating instructions
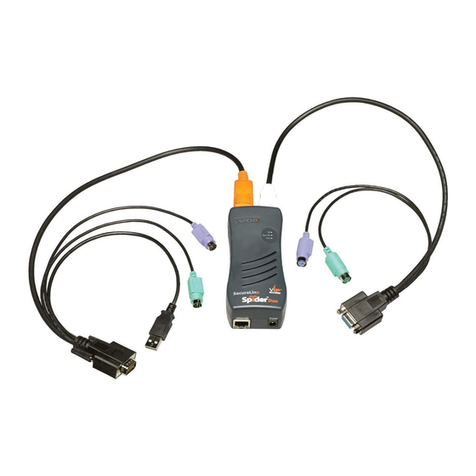
Lantronix
Lantronix Spider user guide
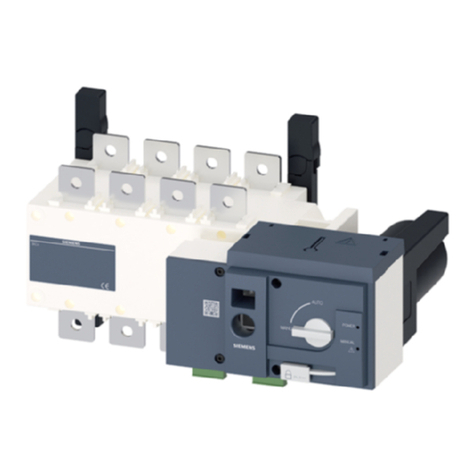
Siemens
Siemens 3KC4338-0CA21-0AA3 operating instructions