ITW Dynatec DYNAMINI Operation manual
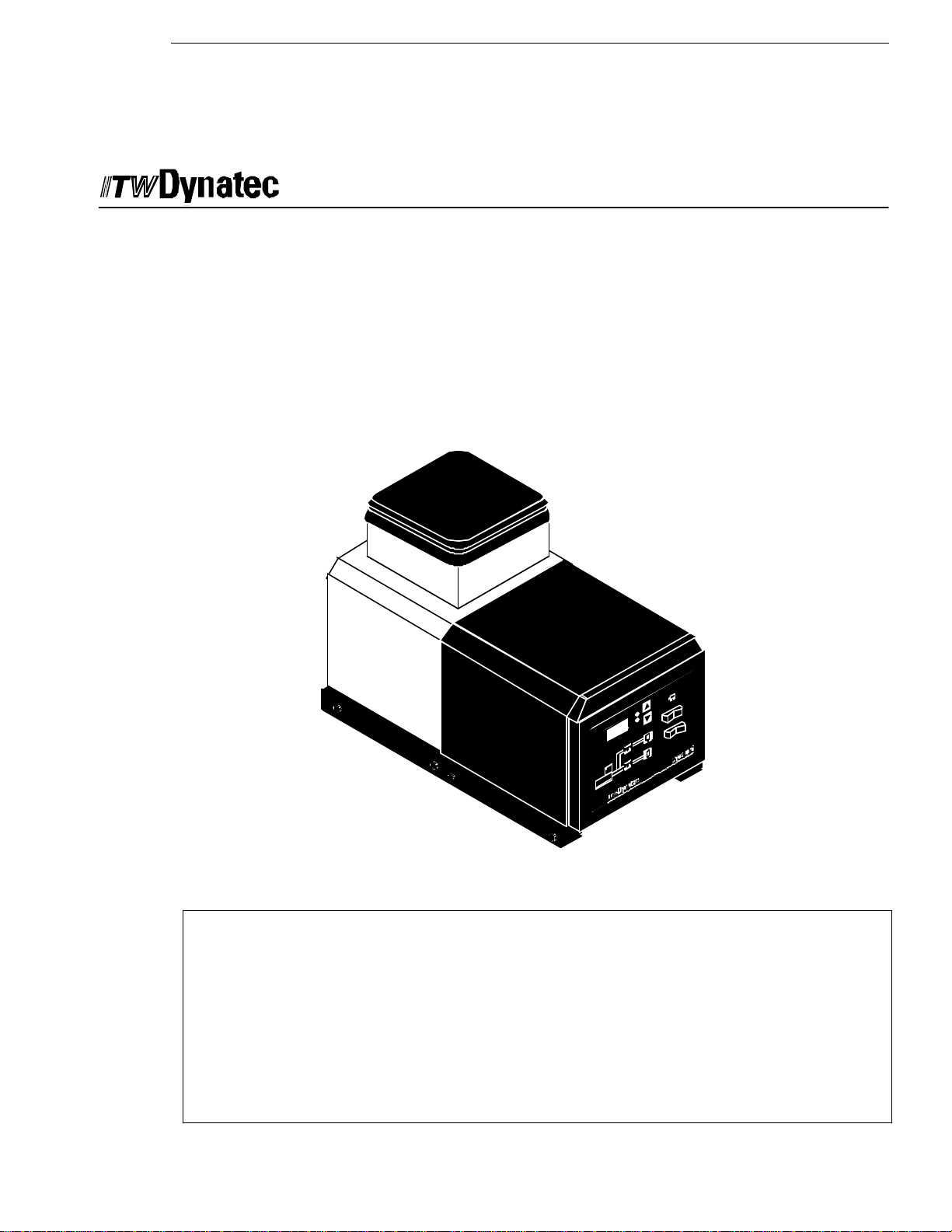
ITWDynatec
AnIllinoisToolWorks Company
31 VolunteerDrive
Hendersonville,TN37075 USA
Telephone 615.824.3634
FAX 615.264.5222
OPERATIONS & SERVICEMANUAL
Manual20-25
Revised 1/05
ITWDynatecGmbH
Industiestrasse 28
D-40822 Mettmann,Germany
Telephone 49.2104.915.0
FAX 49.210.2104.915.111
ITWDynatecK.K.
DaiwashinagawaBldg., 7-15 Konan,3-Chome
Minata-Ku,Tokoyo 108 Japan
Telephone 81.3.3450.5901
FAX 81.3.3450.8405
AdhesiveApplication Solutions·ISO9001 Certified
DYNAMINIäADHESIVE SUPPLYUNIT
OPERATIONS AND SERVICEMANUAL
withSoftwareVersion 2.00
IMPORTANT! -READ ALL INSTRUCTIONSBEFOREOPERATINGTHIS EQUIPMENT
It isthe customer’sresponsibilityto have all operatorsand service personnelread and understand
thisinformation.ContactyourITWDynatec customerservicerepresentativeforadditionalcopies.
NOTICE!Please be suretoincludethe serialnumberofyourapplication system
eachtime you order replacementparts and/orsupplies.Thiswill enableusto
send you the correctitemsthatyou need.
ITWDynatec Service PartsDirectDial:1-800-538-9540
ITWDynatec TechnicalService DirectDial:1-800-654-6711
Foran online copyof thismanual,go towww.itwdynatec.com/manuals.htm
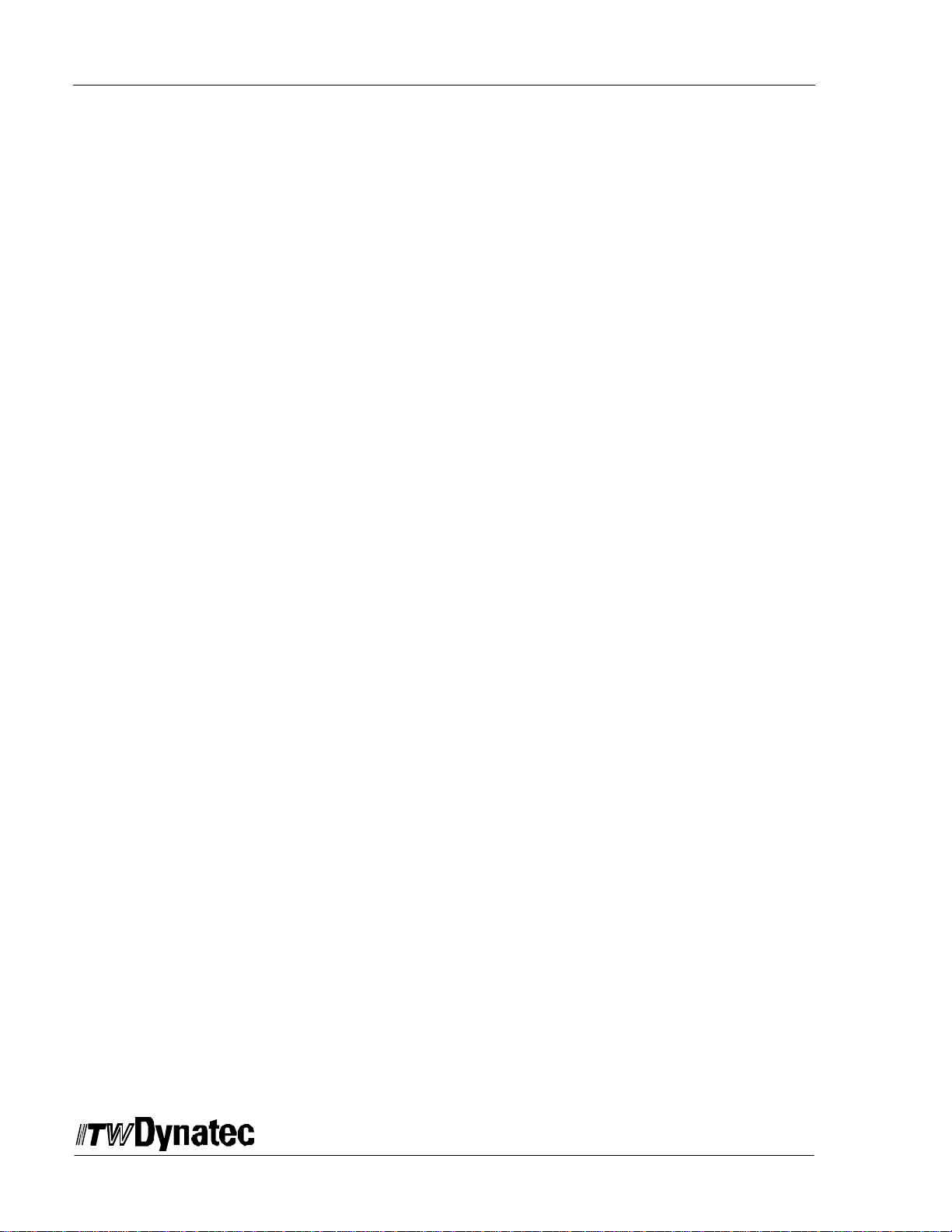
Page ii
Revised 1/05 ITWDynatec c.2004
DYNAMINIASUManual#20-25
ITWDynatec
AnIllinoisToolWorks Company
AdhesiveApplication Solutions
TheDynaminiASUismanufactured underoneormoreof thefollowing PATENTS:
UnitedStates:
D388,800 5,613,451
5,632,918 5,645,743
5,683,578 5,719,378
5,806,720
Europe:
97309164.8-2206
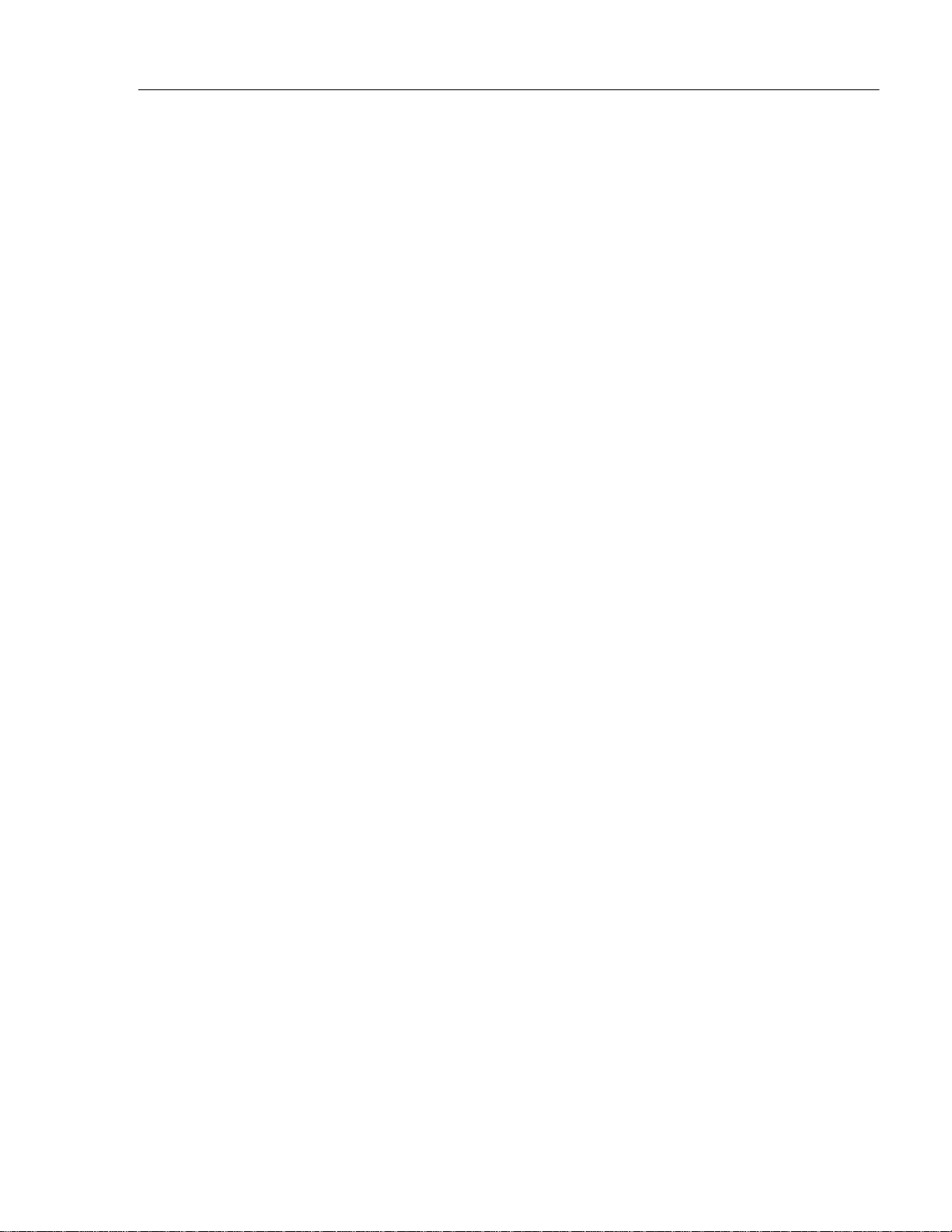
ITWDynatec c.2004
DYNAMINIASUManual#20-25 Page iii
Revised 1/05
TABLEOFCONTENTS
Chapter1SafetyPrecautionsChapter -Page #
Chapter2Specifications& Dimensions
ModelDescription Matrix 2-1.......................................................
Specifications2-2................................................................
Dimensions2-4..................................................................
Chapter3Installation &StartUp
Mounting theASU/Lifting theASU3-1...............................................
Installation 3-2..................................................................
WattageAvailabilityChart3-4......................................................
Adding to orChanging theAdhesiveFormula3-4........................................
AirControlFilterUnit/ RearCover:Head&HoseConnections3-5...........................
TypicalStartUpand ShutDownProcedures3-6.........................................
Storage and DisposaloftheApplication System3-7......................................
Chapter4DynaminiTemperatureControllerSet-Up
TemperatureControlFunctionsinGeneral4-1...........................................
Defining DynaminiTemperatureControlTerms4-1.......................................
Error Indication Messages4-2.......................................................
SoftwareChip(EPROM)and Checksum4-2............................................
SettingsforaTypicalOperation 4-3...................................................
SystemValues4-3................................................................
Default SettingsoftheController4-4.................................................
HelpfulTipsfortheUser4-4........................................................
Chapter5Programming of theDynaminiController
ControllerKeypad 5-1.............................................................
Programming 5-1................................................................
TurnOn 5-1.....................................................................
TemperatureSetpoints5-2..........................................................
Turning ZonesOn/Off 5-2..........................................................
Error Indication Messages5-2.......................................................
KeypadLocking 5-3..............................................................
Service Functions5-4.............................................................
DiagramoftheService FunctionsLoop 5-4.............................................
Standby 5-5.....................................................................
Tolerance 5-6....................................................................
SequentialStartup 5-6............................................................
TemperatureScale5-7.............................................................
Ready Delay 5-7.................................................................
ChangeAccess Code5-8...........................................................
Chapter6Preventive Maintenence
GeneralCleaning 6-1..............................................................
PreventiveMaintenanace 6-1.......................................................
OutputFilter6-1.................................................................
HoseFittingsand Fasteners6-1......................................................
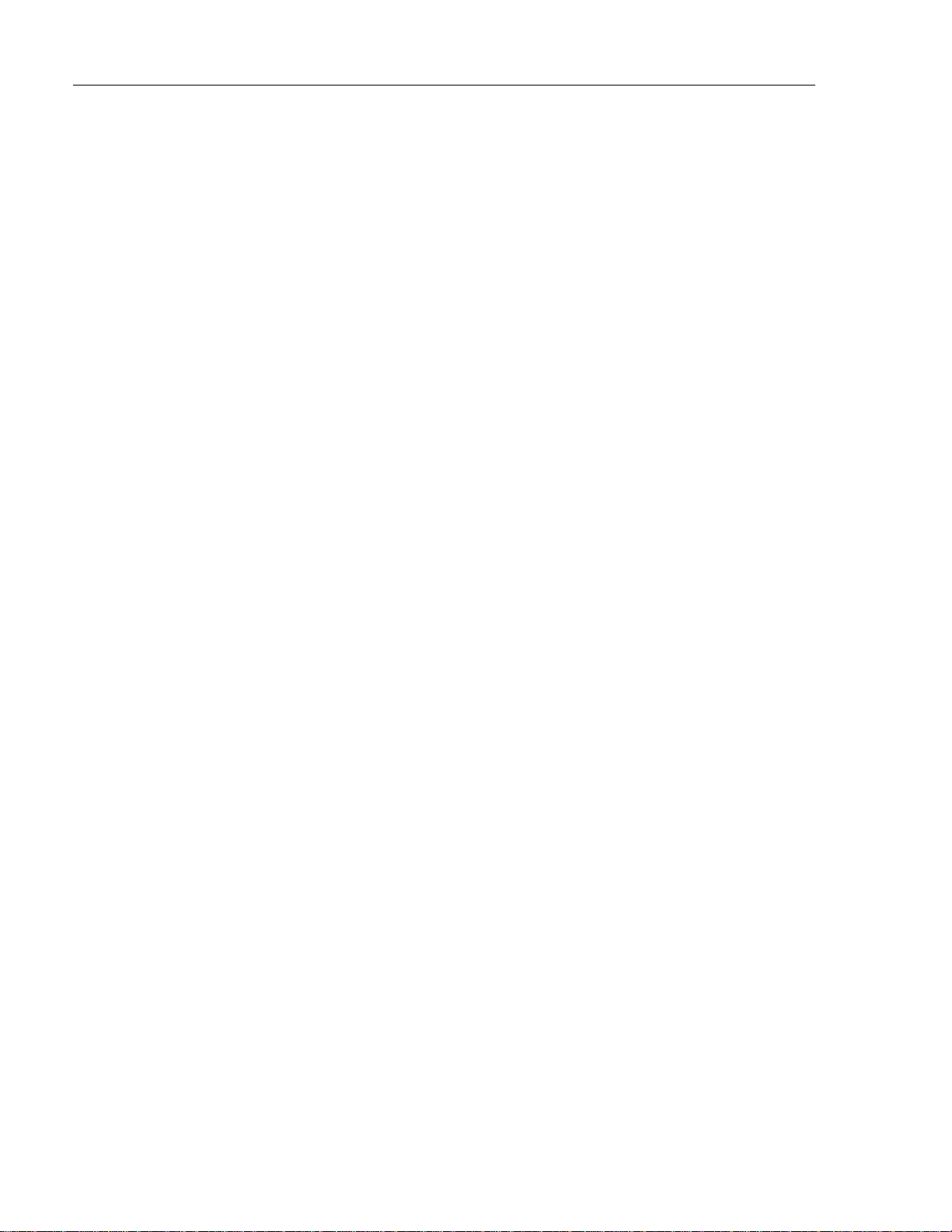
Page iv
Revised 1/05 ITWDynatec c.2004
DYNAMINIASUManual#20-25
HopperFilter Inspection and Cleaning 6-2.............................................
Purging theFilterManifold ofAdhesive and Pressure6-2..................................
Flushing theSystem6-3...........................................................
Chapter7Troubleshooting
Handling PrintedCircuit Boards7-1..................................................
PrintedCircuit Board&LayoutIllustration 7-2..........................................
OvertempThermostat7-3..........................................................
Location ofPCB &OvertempThermostatRe-set7-3.....................................
Resistance Tables7-4.............................................................
Troubleshooting Guide7-5.........................................................
PumpOperation &AdjustablePressureRelief7-9........................................
Piston PumpTroubleshooting Guide7-10...............................................
GearPumpTroubleshooting Guide7-14................................................
Chapter8Disassembly& Re-assemblyProcedures
ToRemovethePump&ElectronicsCover8-1..........................................
ToRemovetheHopperCover8-1....................................................
ToRemovetheHopperLid 8-2......................................................
ThermostatReplacement8-2........................................................
RTDSensorReplacement8-2.......................................................
ToAccess &Replace theElectricalComponents8-3......................................
ToAccess &Replace thePumpsorMotors8-5..........................................
Noteon Cast-inHeaters8-6.........................................................
Re-assemblyProcedures&Cautions8-7...............................................
Chapter9AvailableOptions& Accessories
PressureGaugeKit 9-1.............................................................
FilterOption 9-1.................................................................
PumpOptions&Accessories9-1.....................................................
Troubleshooting Job Aide9-2.......................................................
RecommendedService PartsList9-3..................................................
Chapter10 ComponentIllustrations& BillsofMaterial
ElectricalPanelAssembly 10-2.......................................................
Piston PumpAssembly 10-4.........................................................
CabinetAssembly 10-6.............................................................
DriveSection 10-8.................................................................
Filter&Melt Assembly 10-10.........................................................
PumpAssemblies10-12..............................................................
Chapter11 SystemSchematics &Engineering Drawings
HoseSchematic:all models11-2......................................................
HeadSchematic:all models11-3......................................................
Wiring Diagrams11-4..............................................................
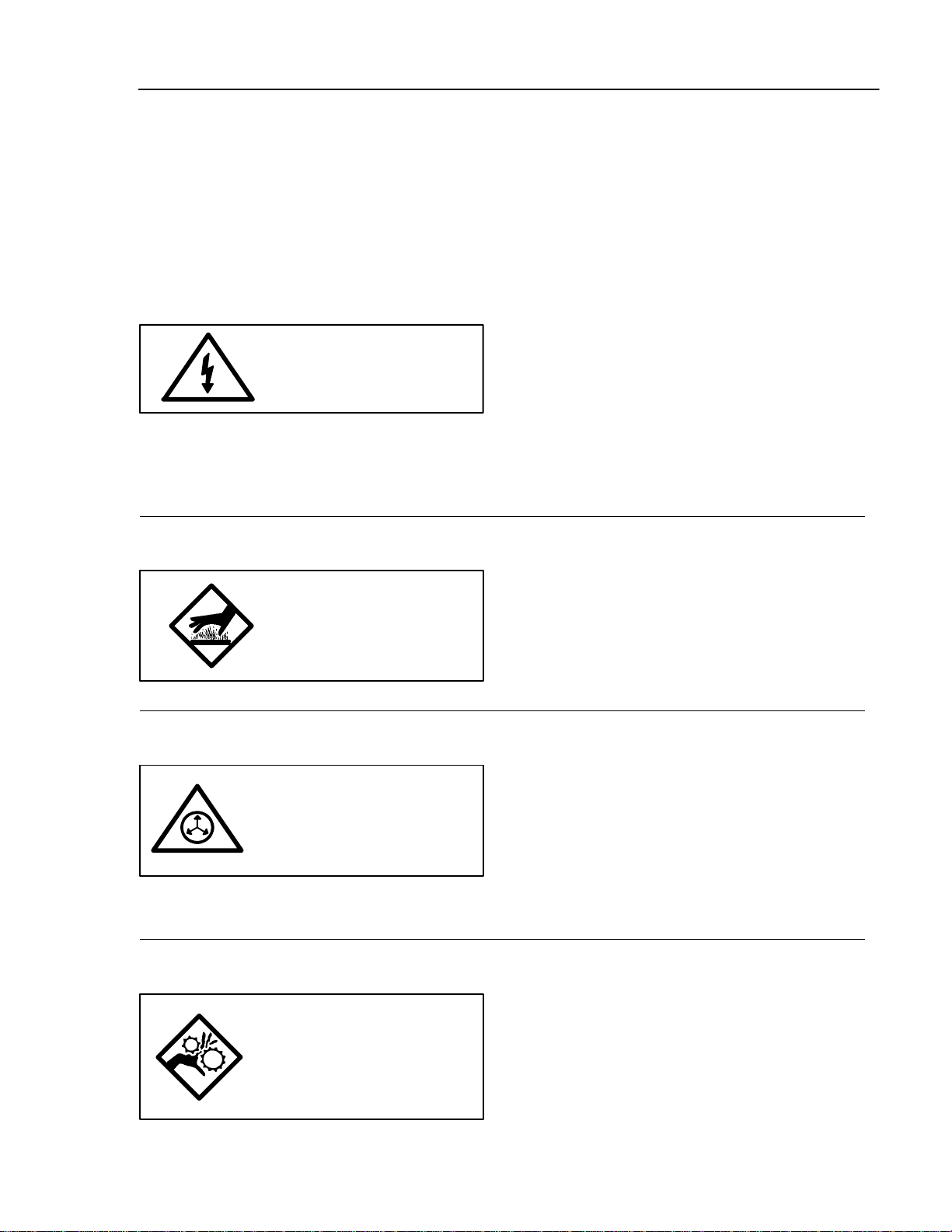
ITW Dynatec c. 2004
DYNAMINI ASU Manual #20-25 Page 1-1
Revised 9/98
Chapter 1
SAFETY PRECAUTIONS
All operators and service personnel must read
and understand this manual before operating
or servicing equipment.
All maintenance and service on this equip-
ment must be performed by trained techni-
cians.
Electrical
DANGER
HIGH VOLTAGE
Dangerous voltages exist at several points in this
equipment. To avoid personal injury, do not touch
exposed connections and components while input
power is on. Disconnect, lockout and tag external
electrical power before removing protective panels.
A secure connection to a reliable earth ground is
essential for safe operation.
A disconnect switch with lockout capability must be
provided in the line ahead of the unit. Wiring used to
supply electrical power should be installed by a
qualified electrician.
High Temperatures
WARNING
HOT
SURFACE
Severe burns can occur if unprotected skin comes in
contact with molten adhesive or hot application system
parts.
Safety glasses, gloves and long- sleeved clothing must
be worn whenever working with or around adhesive
application systems.
High Pressure
WARNING
HIGH PRESSURE
PRESENT
To avoid personal injury, do not operate the equipment
without all covers, panels and safety guards properly
installed.
To prevent serious injury from molten adhesive under
pressure when servicing the equipment, disengage the
pumps and relieve the adhesive system’s hydraulic
pressure (e.g., trigger the heads, hand-held applicators,
and/or other application devices into a waste container)
before opening any hydraulic fittings or connections.
Protective Covers
WARNING
DO NOT OPERATE
WITHOUT GUARDS
IN PLACE
Keep all guards in place!
To avoid personal injury, do not operate the application
system without all covers, panels and safety guards
properly installed.
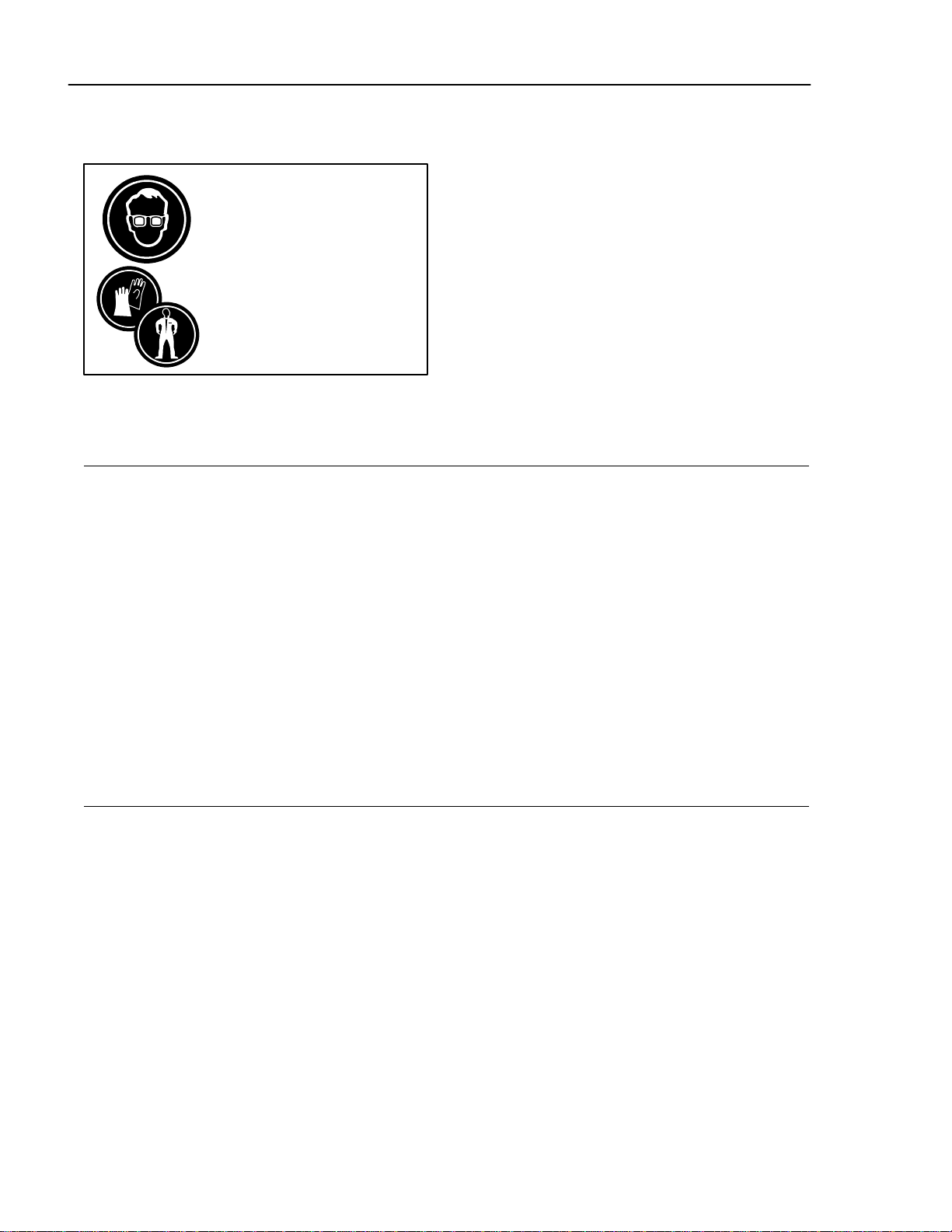
Page 1-2
Revised 3/97 ITW Dynatec c. 2004
DYNAMINI ASU Manual 20-25
Eye Protection & Protective Clothing
WARNING
EYE PROTECTION
REQUIRED
PROTECTIVE
CLOTHING
REQUIRED
It is very important that you PROTECT YOUR EYES
when working around hot melt adhesive equipment!
Wear safety glasses with side shields which conform to
ANSI Z87.1 or EN166.
Failure to wear safety glasses could result in severe eye
injury.
It is important to protect yourself from potential burns
when working around hot melt adhesive equipment.
Wear protective gloves and long-sleeved, protective
clothing to prevent burns that could result from contact
with hot material or hot components.
Always wear steel-reinforced safety shoes.
Safe Installation and Operation
To avoid possible failure of hoses, make sure all hoses
are routed to avoid kinking, tight radius turns (8” or
less) and abrasive contact. Hot-melt hoses should not
have prolonged contact with heat-absorbing surfaces
such as cold floors or metal troughs. These
heat-absorbing surfaces can alter adhesive flow and
cause incorrect calibration. Hoses should never be
covered with materials that prevent heat dissipation,
such as insulation or sheathing.
Read this manual before applying electrical power to
the equipment. Equipment may be damaged by
incorrect electrical connections.
Do not use adhesive that is dirty or that may be
chemically contaminated. Doing so can cause system
clogging and pump damage.
When adhesive hand-held applicators or other movable
applicators are used, never point them at yourself or at
any other person. Never leave a hand-held applicator’s
trigger unlocked when not actually in use.
Do not operate the hopper or other system components
without adhesive for more than 15 minutes if the
temperature is 150 degrees C (300 degrees F) or more.
To do so will cause charring of the residual adhesive.
Never activate the heads, hand-held applicators and/ or
other application devices until the adhesive’s
temperature is within the operating range. Severe
damage could result to internal parts and seals.
Treatment for Burns From Hot Melt Adhesives
Burns caused by hot melt adhesive must be treated at a
burn center.
Care should be used when working with hot melt
adhesives in the molten state. Because they rapidly
solidify, they present a unique hazard.
Even when first solidified, they are still hot and can
cause severe burns. When working near a hot melt
application system, always wear safety gloves, safety
glasses and long-sleeved, protective clothing.
Always have first-aid information and supplies
available.
Call a physician and/or an emergency medical
technician immediately.
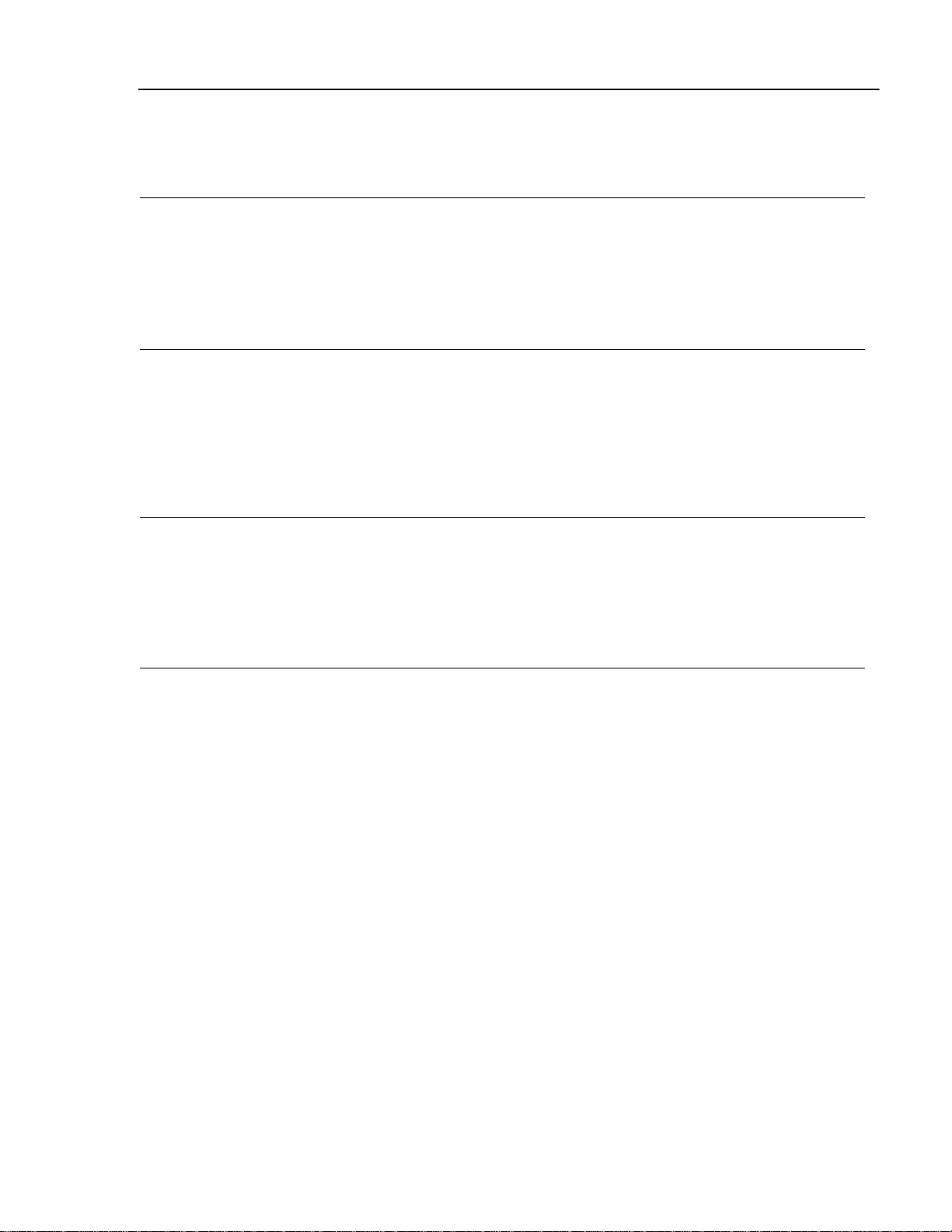
ITW Dynatec c. 2004
DYNAMINI ASU Manual #20-25 Page 1-3
Revised 9/98
Service
Refer all servicing to qualified personnel only.
Explosion/ Fire Hazard
Never operate this unit in an explosive environment.
Use cleaning compounds recommended by ITW
Dynatec or your adhesive supplier only. Flash points
of cleaning compounds vary according to their com-
position, so consult with your supplier to determine the
maximum heating temperatures and safety precautions.
Lockout/ Tagout
Follow OSHA 1910.147 (Lockout/ Tagout Regulation)
for equipment’s lockout procedures and other impor-
tant lockout/ tagout guidelines.
Be familiar with all lockout sources on the equipment.
Even after the equipment has been locked out, there
may be stored energy in the application system, partic-
ularly in the capacitors within the panel box. To ensure
that all stored energy is relieved, wait at least one min-
ute before servicing electrical capacitors.
In This Manual
WARNINGS and CAUTIONS are found throughout
this manual.
WARNINGS mean that failure to observe the specific
instructions may cause injury to personnel.
CAUTIONS mean that failure to observe the specific
instructions may damage the equipment.
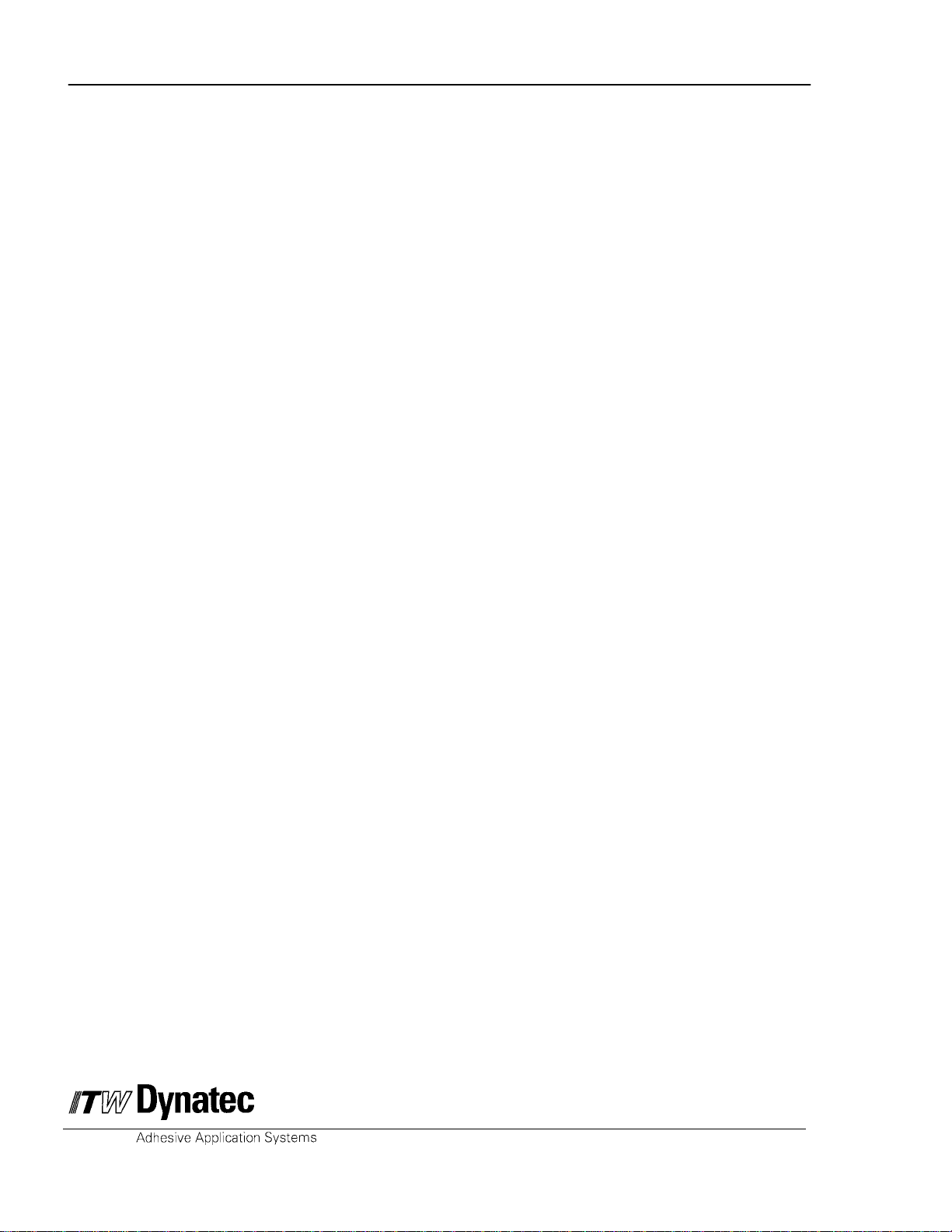
Page 1-4
Revised 3/97 ITW Dynatec c. 2004
DYNAMINI ASU Manual 20-25
ITW Dynatec
An Illinois Tool Works Company

ITWDynatec c.2004
DYNAMINIASUManual#20-25 Page 2-1
Revised 1/05
Chapter2
SPECIFICATIONSAND DIMENSIONS
NX2X X X X -XXXX
DYNAMINI
5=5kg/10 lb.
1=10 kg/20 lb.
HOSE:2-hosecapable
PUMPTYPE:
P12 =Piston Pump 12:1
GAS =GearPump 1.5cc
GBS =GearPump 3.2cc
GCS=GearPump 4.5cc
GDS=GearPump 0.55cc
GES =GearPump 10cc
VOLTAGE:
1=100 -120VAC,1 phase
2=200 -240VAC,1 phase
OPTIONS:
ACCESSORIES:
F=100 mesh/149 micron outlet filter(40 mesh/420 micron is standard)
G=Analog pressure gauge
V=Swirlkit, 1 hose
W=Swirlkit, 2 hose
CONFIGUREDSYSTEMOPTIONS:
C24 =2.4m/8ft. Abrasion resistanthose
C36 =3.6m/12 ft. Abrasion resistanthose
CHB=Hand Bead Applicator
CHS=Hand SwirlApplicator
STACKTITE SYSTEMOPTIONS:
SB =Bead applicator
SS =Swirlapplicator
EXAMPLE:
N52GAS2-F=Dynamini10 lb.hopperw/1.5cc gearpump,240 VAC/1 phase and 100 mesh outlet
filter.
DYNAMINIModel Designation Matrix
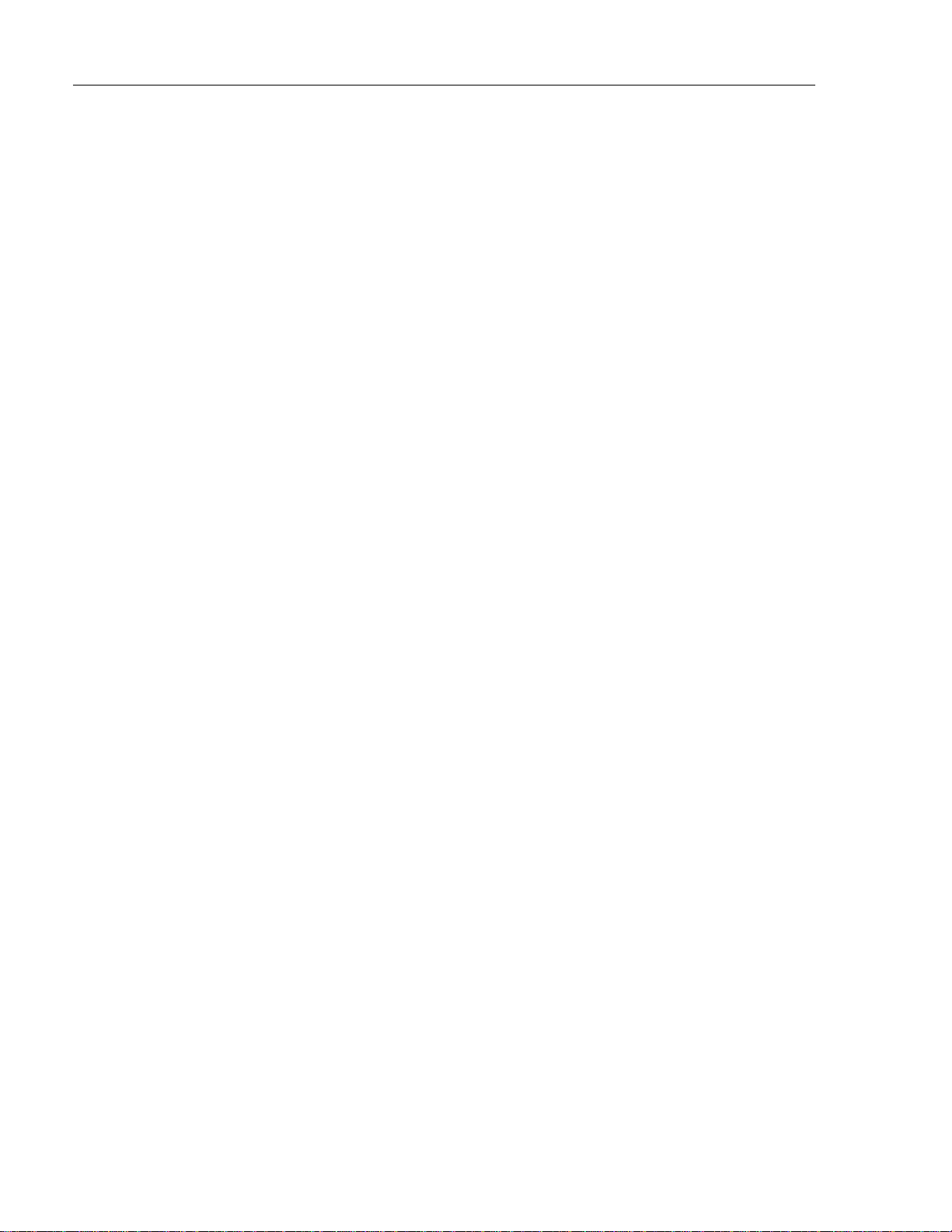
Page 2-2
Revised 1/05 ITWDynatec c.2004
DYNAMINIASUManual#20-25
Specifications
Environmental:
Storage/shipping temperature-40°Cto 70°C(-40°Fto 158°F)..............................
Ambientservice temperature-7°Cto 50°C(20°Fto 122°F)................................
Noise emission TBD<db(A)........................................................
Physical:
Dimensions see dimensional layoutson following pages....................................
Numberofheads/hoses2...........................................................
Numberofhoppertemperature zones1.................................................
Numberofpumps1................................................................
Piston pumpratio 12:1..............................................................
Gearpumpsee optionson page2-1...................................................
Enclosurestyled, durablemetaland high temp plastic, dustand splatter resistant.................
Hose connectionsElectrical: universal15-pinAmphenolconnectorsatasu,..................... Mechanical: wrench-securedfluidfittings(#6 JIC)
Hopper (tank)capacityModel05:5 kg/11 lb............................................Model10:10 kg/20 lb
Hopperconstruction cast-in heaters,TFE Teflon impregnated..............................
Filtration hopperbottomscreen, manifold basketfilter.....................................
Weight,emptytbd kg/ tbd lb..........................................................
Adhesiveformstandard grades(non-waterbased only)....................................
Electrical:
PowerSupplyRequired 100-120 VAC/1p/50-60 Hz/15 Ampere...........................
or200-240 VAC/1p/50-60 Hz/30 Ampere
Hopperheatertype cast-intubular.....................................................
Powerconsumption, system maximum100-120 VACsystem: 1800 watts......................
200-240 VACsystem: 6800 watts(w. piston pump)
200-240 VACsystem: 7200 watts(w. gearpump)
HopperPower100-120 VACsystem: 600 wattsat120 VAC...............................200-240 VACsystem: 1200 wattsat240 VAC
Temperature control microcontroller...................................................
Temperaturesensors100 OhmPlatinumRTDstandard....................................
GearpumpMotor1/4 hp, constantspeed, AC, directdrive, horizontalorientation................
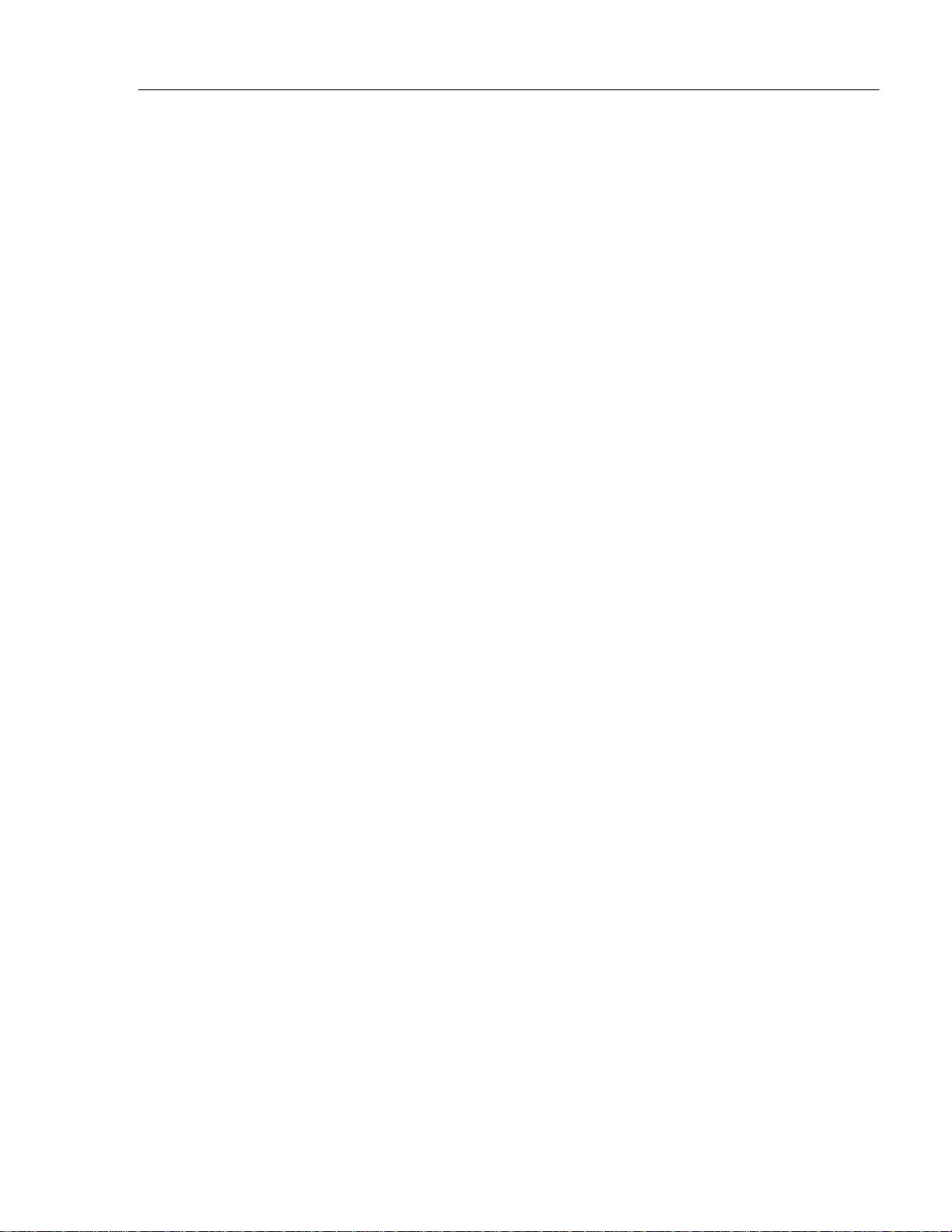
ITWDynatec c.2004
DYNAMINIASUManual#20-25 Page 2-3
Revised 1/05
PressurizedAir:
Airpressuresupply 1.4 to 6.8 bar (20 to 100 psig).........................................
Airconsumption at60 pumpcyclesperminute90 normal liters/ minute....................... (3.2 SCFMat100 psig)
Performance:
Adhesivetemperature controlrange40°Cto 218°C(100°Fto 425°F).........................
Adhesivetemperature controlaccuracy±1°C(±1°F).....................................
Over-temperature cutoff forhopper232°C(450°F).......................................
Adhesiveviscosity 500 to 50,000 centipoise.............................................
Warm-up time,full hopperapproximately .5 hour.........................................
Adhesivedeliveryrate, openline.91 kg/min(2lb/min)(12:1 piston pump).....................
Adhesivemelt rate(dependson adhesiveused)8 kg/hr (17.3 lb/hr)...........................
Adhesivepressureup to 68 bar (1000 psi)maximum.......................................
Maximumpumpspeed, piston pump 60 pumpcyclesperminute.............................
Maximumpumpspeed, gearpump 87 revolutionsperminute,60Hz,constantspeed..............73 revolutionsperminute,50Hz,constantspeed
DynaminiTemperatureControl:
Controllerboard 1 printedcircuit board.................................................
Displaytypelong-life,light-emitting diode(LED)........................................
Temperature controlzones5triac-output................................................
Other:
Operatorinterface digitaldisplaywithsimplified, all-icon keypad.............................
Temperatureoffsetno..............................................................
Sensoropenerrormessageyes.......................................................
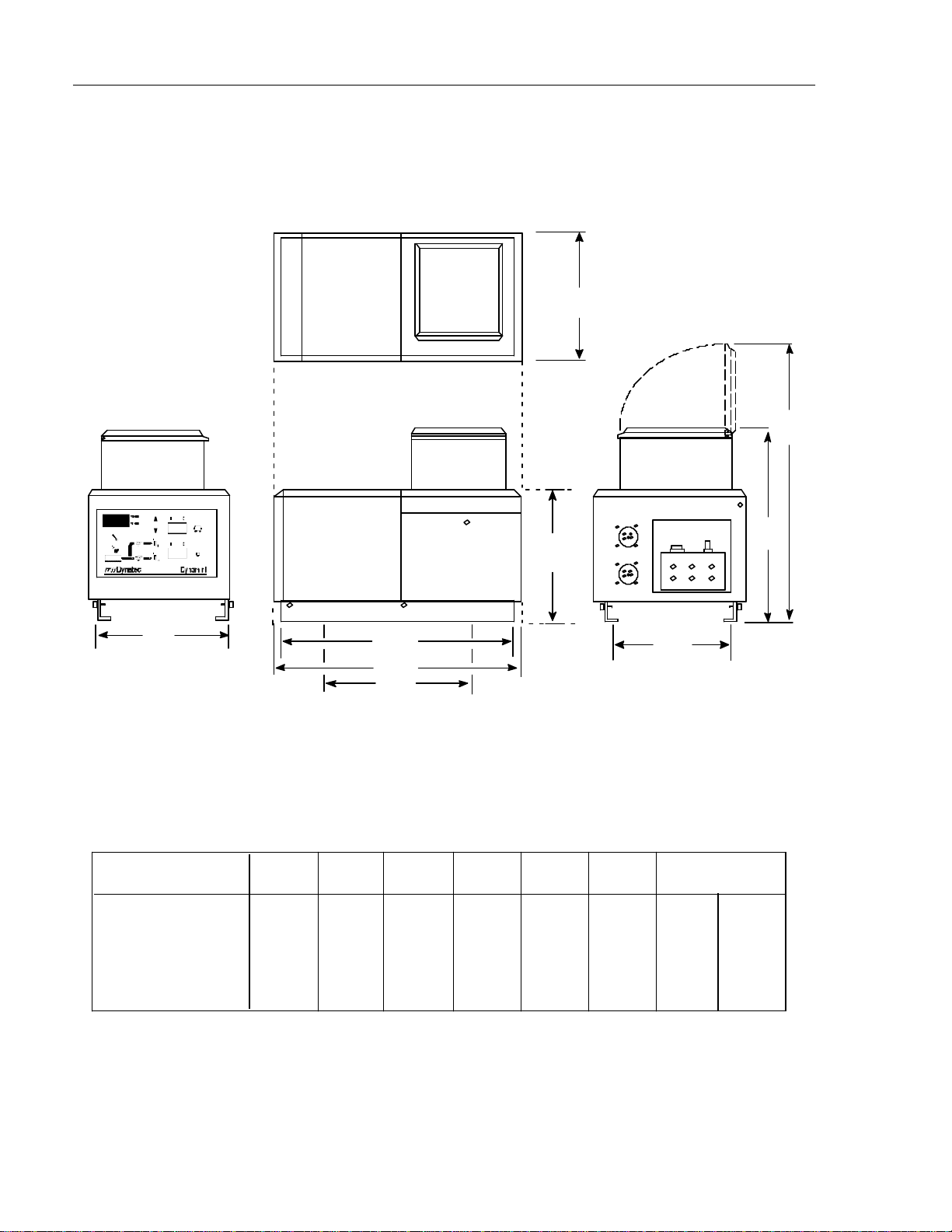
Page 2-4
Revised 1/05 ITWDynatec c.2004
DYNAMINIASUManual#20-25
AB
C
DE
A
F
G
DYNAMINI Installation Dimensions
H
DIMENSION A BC D EFG H
289 527 540 238 451 635 249 381
11.38 20.75 21.25 9.37 17.75 25.0 9.8 15.0
289 527 540 238 654 838 249 381
11.38 20.75 21.25 9.37 25.75 33.0 9.8 15.0
MODEL 05 (mm)
MODEL 05 (inches)
MODEL 10 (mm)
MODEL 10 (inches)
mounting holes*
*All Mounting holesare10mm diameter.
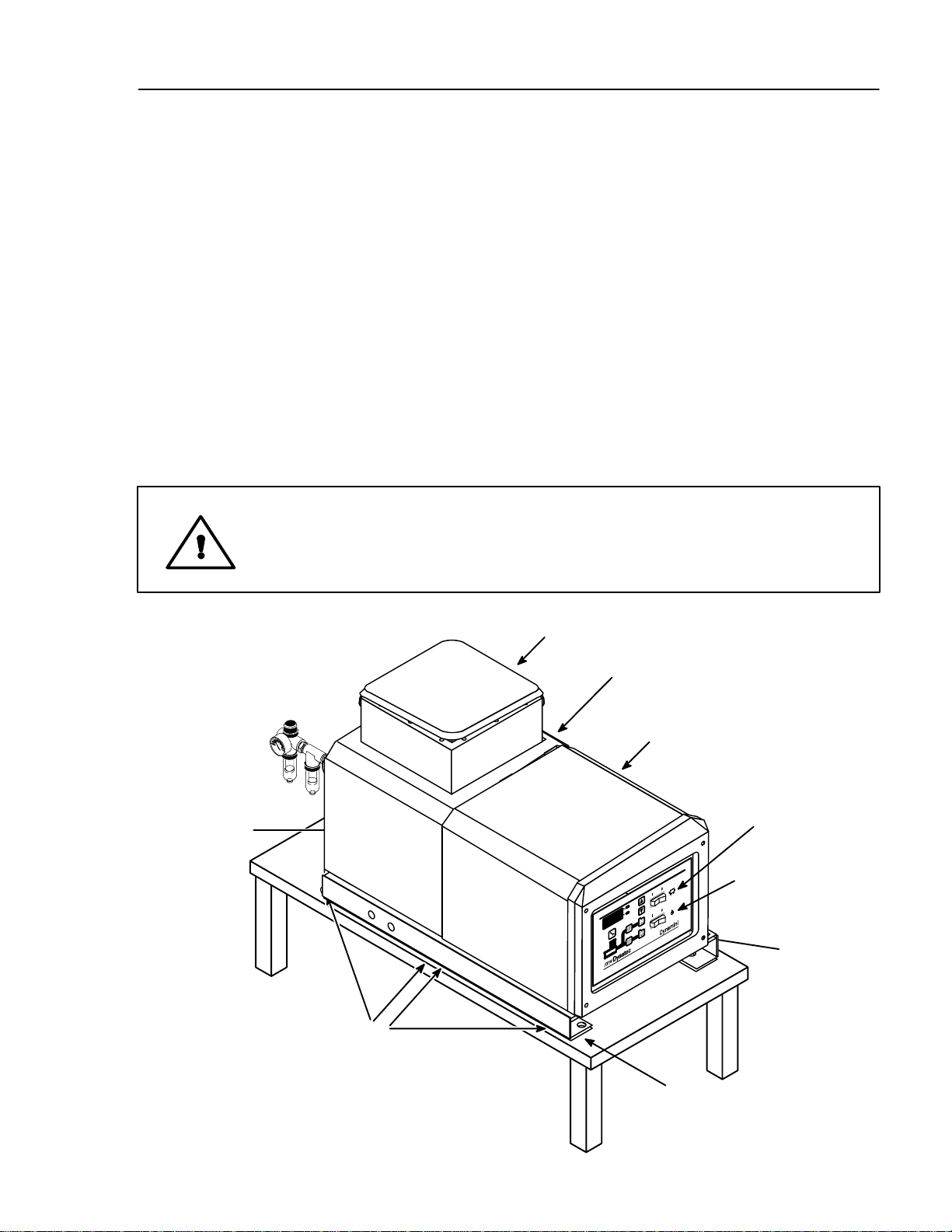
ITW Dynatec c. 2004
DYNAMINI ASU Manual 20-25 Page 3-1
Revised 1/05
Chapter 3
INSTALLATION & START-UP
Mounting the DYNAMINI ASU
The DYNAMINI ASU can be mounted on most flat surfaces, on either an open or a solid frame (as
shown below). The main electrical power and the serial communication connections come in from
below the unit and connect under the keypad. Access to the underside of the ASU is not a necessary
consideration in mounting the unit.
The Dynamini’s hinged hopper lid may be rotated 90 degrees in any direction.
For installation dimensions, see illustration on page 2-4.
Lifting the ASU
Captive Cover Screws
Hopper Lid
Hopper Cover
Pump & Electronics Cover
Controller
Keypad
Access Cover
Base
Plate
Pump ON/OFF
Switch
WARNING
The unit must be lifted by two persons, using proper lifting technique, one
person at either end. Securely hold it under its base plate. No belts or hooks
should be used. Never allow anyone to stand on the ASU.
Main ON/OFF
Power Switch
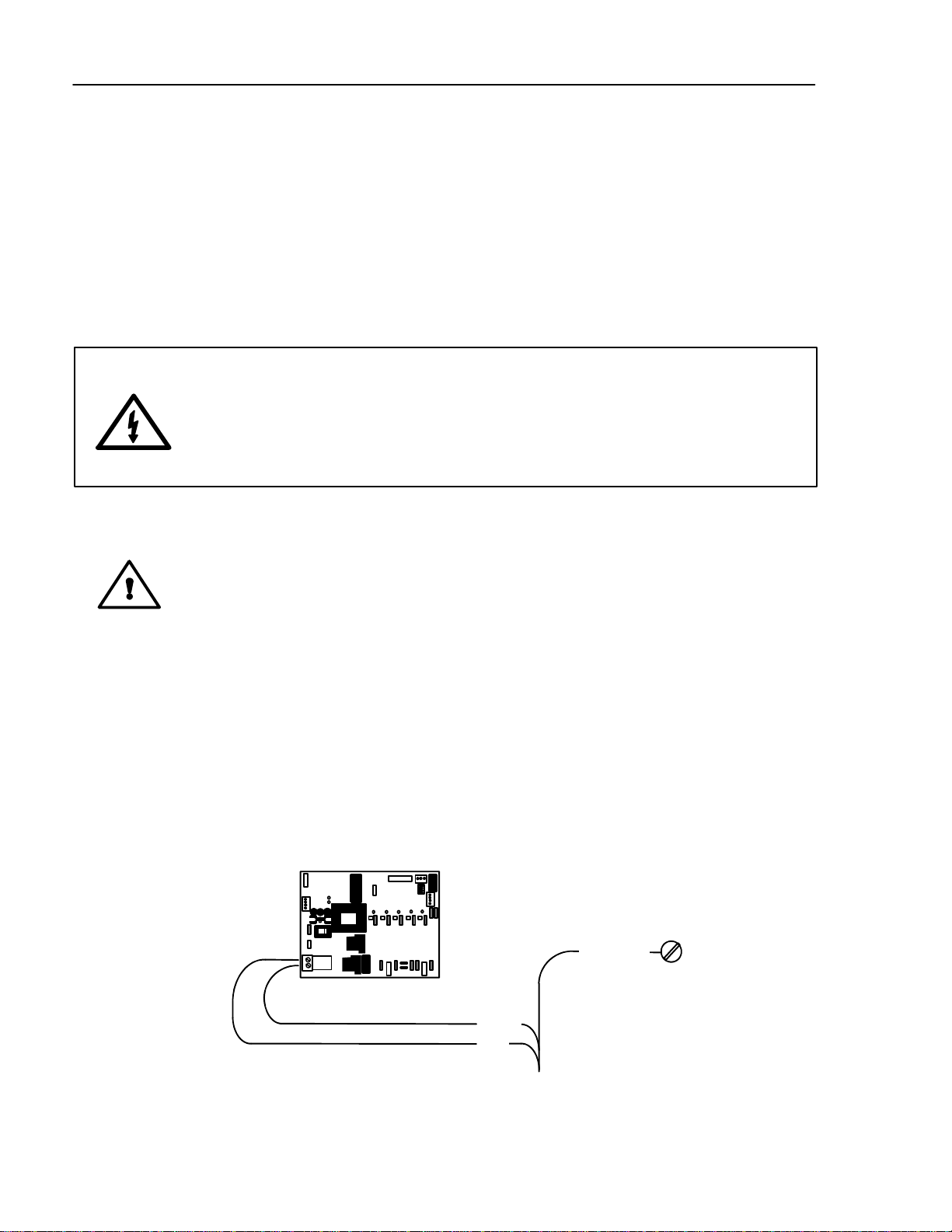
Page 3-2
Revised 1/05 ITW Dynatec c. 2004
DYNAMINI ASU Manual #20-25
Installation
NOTE: Re-read Chapter 1 “Safety Precautions” before performing any installation procedures. All
installation procedures must be performed by qualified, trained technicians.
After the DYNAMINI ASU has been properly mounted, the following general sequence should be
followed for installation:
1. Make sure that incoming line power to the ASU is turned OFF at a customer-provided circuit
breaker. Incoming line power must be overcurrent-protected.
2. For 200-240 VAC units, power supply wires should be rated for 30 Amperes service and
should include an earth ground conductor.
3. 100-120 VAC units are supplied with a line cord and a plug suitable for use in North America
on 15 AMP power supplies. For other types of 100-120 VAC power wiring, supply wires should
be rated for 1.5 Amp service and include an earth ground conductor.
4. Acceptable power supplies are either 100-120 VAC 1-Ph 50/60 Hz with a neutral wire, or
200-240 VAC 1-Ph 50/60 Hz with or without a neutral wire. The information plate on the ASU
(adhesive supply unit) will indicate the required power supply.
5. Power supply wires are to be connected to the removable plug at header X1 on the printed
circuit board,, as shown below.
CAUTION: Grounding conductors never carry electrical current. The use of a
neutral conducting wire as earth ground is incorrect and may cause damage to
the equipment.
DANGER HIGH VOLTAGE
Disconnect and lockout input power to the application system before start-
ing any installation procedures. Make sure there is no electrical power on the
leads you will be connecting. THE UNIT’S MAIN SWITCH DOES NOT SHUT OFF
ALL POWER WITHIN UNIT!! Make sure incoming line power is turned off at the
customer-provided circuit breaker before opening unit.
POWER IN
GROUND
L1
L2/ N
Supply Power Installation Diagram
Printed
Circuit
Board
X1
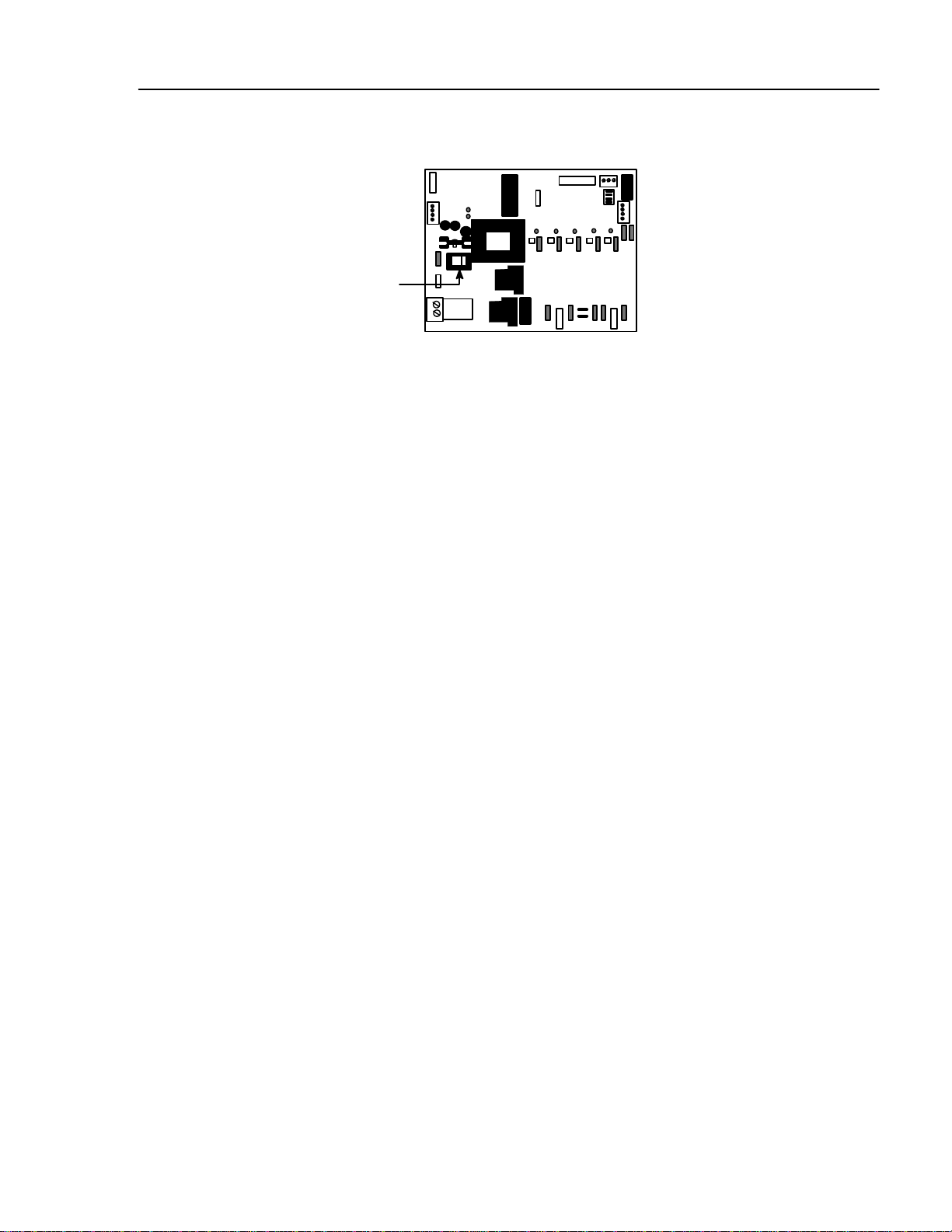
ITW Dynatec c. 2004
DYNAMINI ASU Manual 20-25 Page 3-3
Revised 1/05
6. Choose ASU Voltage:
Using the selection switch on the printed circuit board, set the controller for the appropriate
supply voltage.
7. Reassemble the pump and electronics cover to the ASU.
8. Gear Pump models: omit this step.
Piston Pump models: Install the Air Control/ Filter Unit (containing the air regulator, the
coalescing filter and pre-filter). See illustration on page 3-5. The air control/ filter unit is
mounted directly to the ASU via a threaded hole on the rear cover. Wrap Teflon tape around
the nipple fitting before installing in the ASU. The unit requires clean, dry air. NEVER use
lubricated oil.
For operator convenience, the air pressure gauge can be mounted to either side of the air
control regulator.
With the air pressure regulator, a clockwise turn increases pressure. A counter-clockwise
turn decreases pressure. The recommended pressure is 1.4 to 6.8 bar (20 to 100 psi).
9. Refer to the Wattage Availability Chart on the next page to determine the hose and head
power available for the various configurations of the Dynamini ASU.
10. The adhesive hoses are connected at the rear cover (see illustration on page 3-5). Make
your electrical hose connections at the two numbered connects on the left side of the cover.
Route hoses so that there is at least an eight-inch radius at any bend. Do not hang hoses
without proper support. Do not crimp, clamp, squeeze or tie hoses.
The hose adhesive ports are located at the bottom of the filter block, to the right of the
electrical connections. There are three ports for the use of up to two hoses and for the
(optional) adhesive pressure gauge.When making hose connections, use the numbered
guides shown on the illustration to coordinate; ie. when using one hose make your hookup
to electrical connection #1 and adhesive port #1. When using two heads/ hoses, hookup
hose/ head #1 to electrical connection #1 and adhesive port #1, then hookup hose/ head #2
to electrical connection #2 and adhesive port #2.
Refer to the hose and applicator manuals for further details on these items.
11. Install the hose manifold outlet cover by sliding it into place and attaching with the two M4
screws provided.
Printed Circuit Board
Voltage Selection Switch:
“230” for 200-240VAC
or
“115” for 100-120VAC
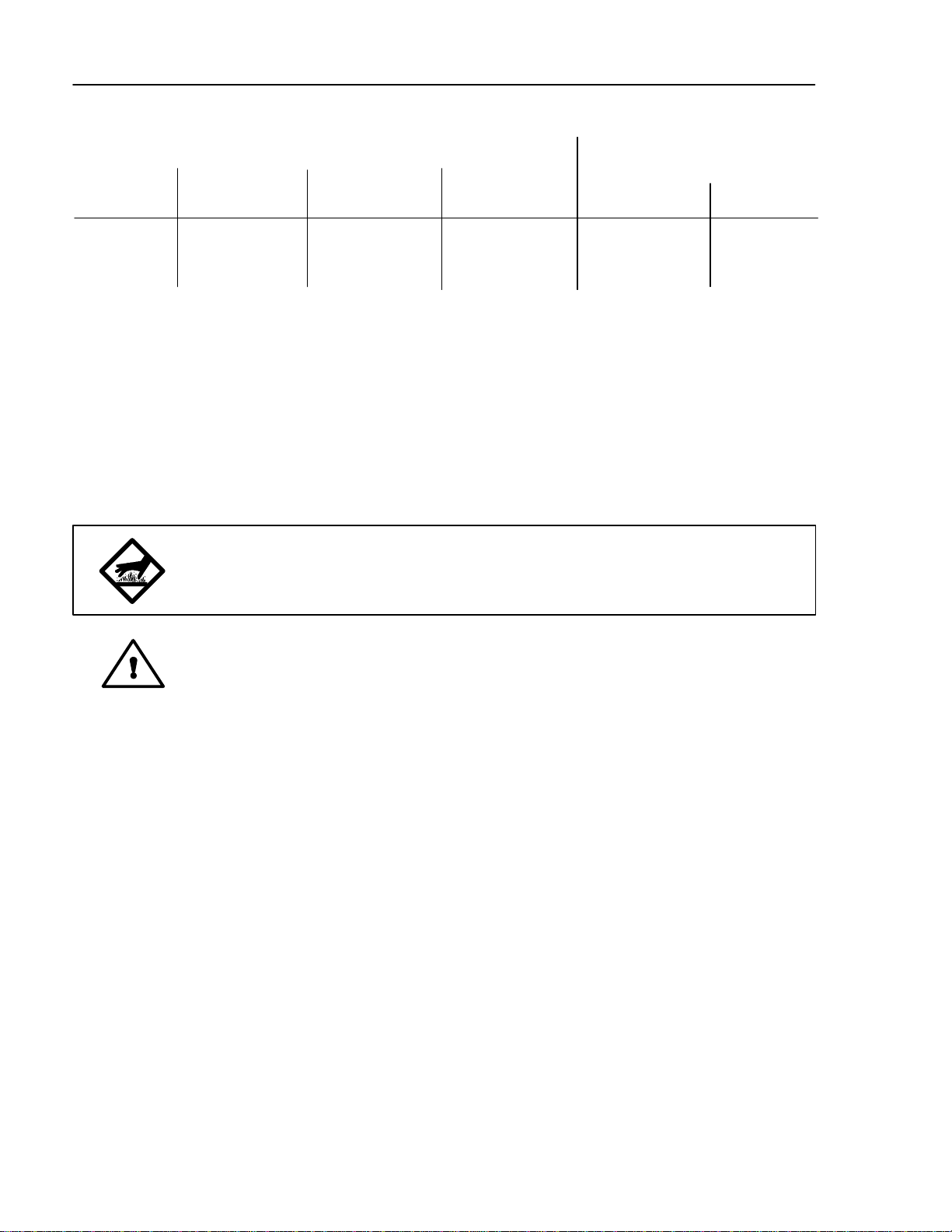
Page 3-4
Revised 1/05 ITW Dynatec c. 2004
DYNAMINI ASU Manual #20-25
Adding Adhesive
The adhesive level should be maintained at 13mm to 100mm (1/2” to 4”) from the top of the hop-
per. Where applications demand a high output volume of adhesive, add small amounts of adhesive
frequently. Adding large amounts of adhesive to an almost empty hopper will lower the temperature
of the adhesive in the hopper and may cause the ASU to fall below its READY setpoint.
Changing the Adhesive Formula
If a different adhesive formulation from the one being currently used is needed, the system will
have to be flushed if the two formulations are incompatible. See page 6-3 of this manual for the
proper flushing procedure. When in doubt about adhesive compatibility, flush your system.
WARNING HOT ADHESIVE
Do not overfill the hopper (melt tank) since adhesive generally expands as it
melts and a full hopper will overflow.
CAUTION: Using adhesive with viscosity over 50,000 centipoise could cause
motor stall and/ or pump failure.
Wattage Availability Chart
ASU Voltage Max. System Hopper Gear Pump Piston Pump Gear Pump
Wattage Wattage Motor Wattage
100-120 VAC 1800 @ 120VAC 600 @ 120VAC 370 @120VAC 1200 @ 120VAC 830 @ 120VAC
200-240 VAC 7200 @ 240VAC 1200 @ 240VAC 370 @ 240VAC 6000 @ 240VAC 5630 @ 240VAC
Wattage Available for
All Hoses and Heads
Notes:
1. Assume 33 Watts per foot of hose, #6 hose at 120VAC or 240VAC.
2. Assume 100 Watts per inch of head width, at 120VAC or 240VAC.
3. The power available for any one hose or head is 720 Watts at 120VAC or 1440 Watts at 240VAC.
4. At reduced voltage, less wattage is available. For example: 120 volt equipment operated on 100
volts or 240 volt equipment on 200 volts, will develop wattage 31% lower than the wattage available
at 120 or 240 volts.
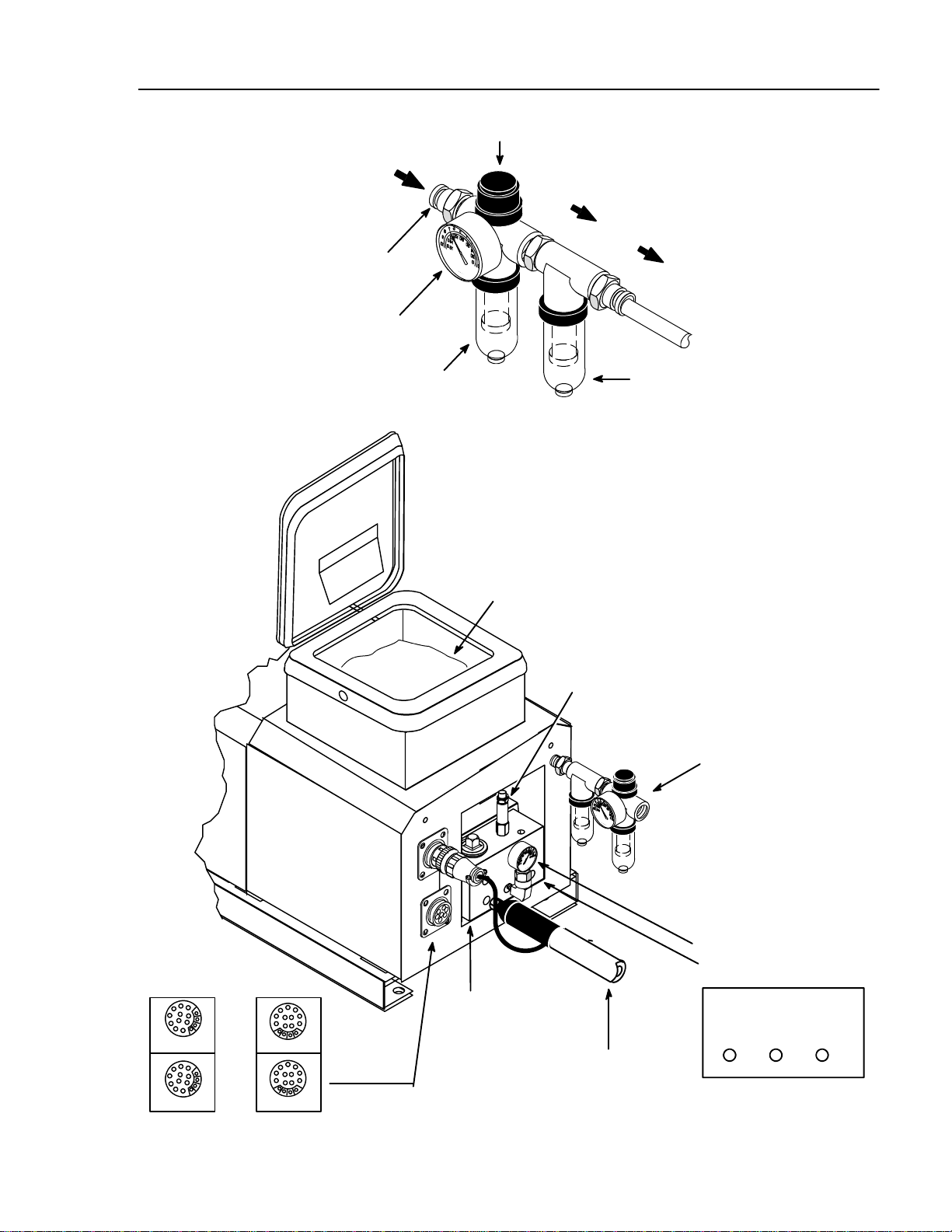
ITW Dynatec c. 2004
DYNAMINI ASU Manual 20-25 Page 3-5
Revised 1/05
Rear Cover: Hose and Head Electrical and Adhesive Connections
Air Pressure Regulator (clockwise increases)
Pressurized Air In
Air pressure gauge
Coalescing filter Pre-filter
1/4 NPT female
Air Flow
Air Control/ Filter Unit
Pressure Gauge (optional)
Hose/ Head Adhesive Ports
Output Filter Manifold
Hose/ Head
Electrical Connections
120v 240v
Adhesive Supply
Hose
Adjustable Pressure
Relief Valve
Electrical #1
Electrical #2
Adhesive Port Connections
#1 Gauge #2
Maintain adhesive level 13mm-100mm (1/2”-
4”) from top of hopper.
Air Control/ Filter Unit
Electrical #1
Electrical #2
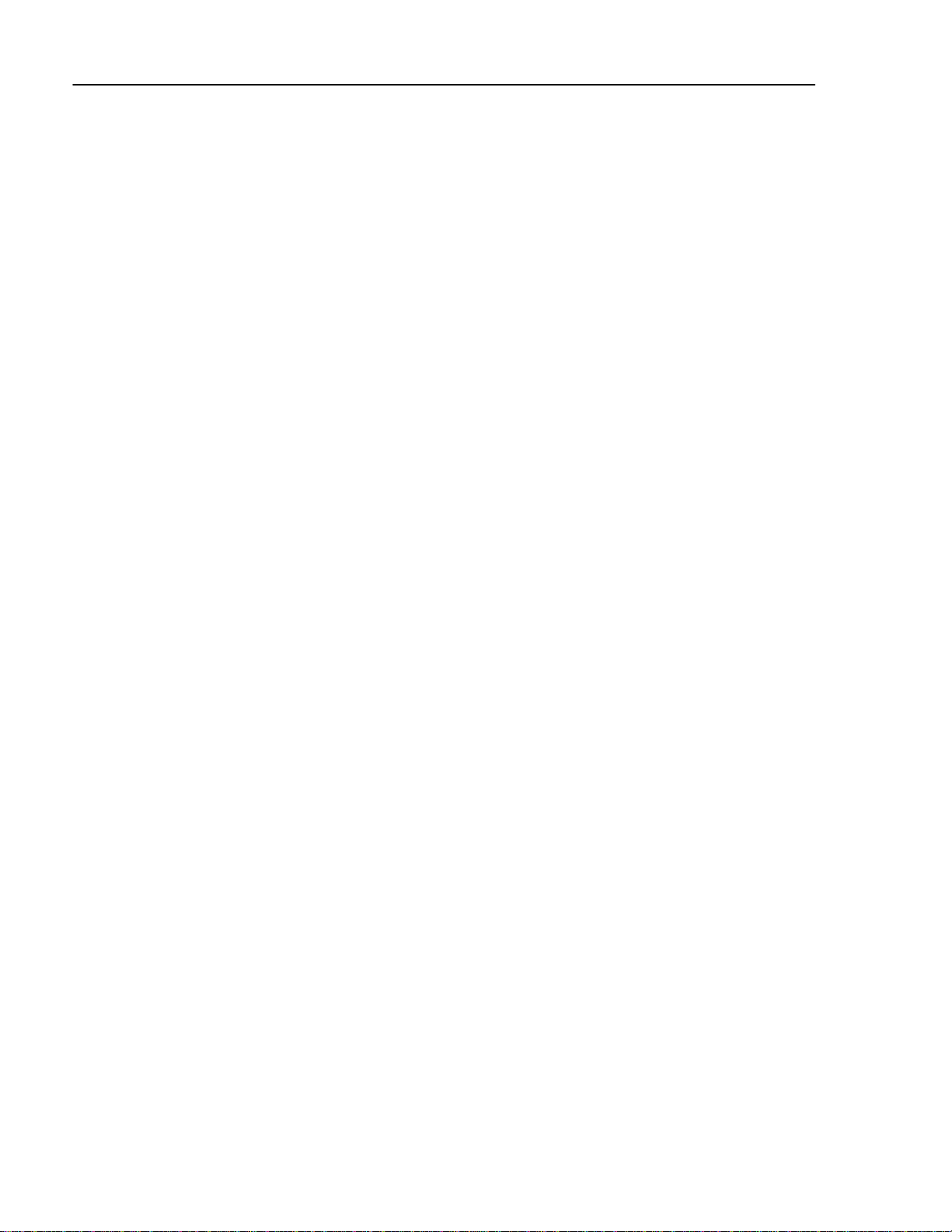
Page 3-6
Revised 1/05 ITW Dynatec c. 2004
DYNAMINI ASU Manual #20-25
Typical Start-Up and Shut Down of the DYNAMINI Application System
Start Up Procedures
1. Fill the ASU’s hopper with clean hot-melt adhesive as described on page 3-4. Close the
hopper lid immediately to prevent contaminants from falling in. (Cover your bulk supply of
adhesive to prevent contaminants also.)
2. At the control panel, turn ON the Main Power Switch. The controller will perform its initial
calibration cycle. The display will read “CAL”. Each of the five temperature zone’s LEDs will
flash as a lamp test.
3. Program your adhesive setpoints (see instructions on page 5-2) or use the factory settings listed
below. Allow adequate time (approximately 20-30 min.) for the adhesive to melt and the
temperatures of the temperature zones to stabilize.
Note: When the ASU leaves the ITW Dynatec factory, it is programmed with the following
factory settings (unless special factory settings were requested):
Hopper: 150°C (300°F)
Hose: 177°C (350°F)
Applicator: 177°C (350°F)
Sequential Startup: ON
4. Once the ASU has reached temperature, turn ON the Pump ON/ OFF Switch. The ASU will
begin to pump adhesive.
5. a. On piston pump units: use the air pressure regulator, located at the rear of the ASU, to
regulate adhesive output.
b. On gear pump units: use the pressure relief valve, located on the filter outlet manifold, to
regulate adhesive output.
Shut Down Procedures
1. Turn OFF the Pump Switch.
2.Turn OFF the Main Power Switch.
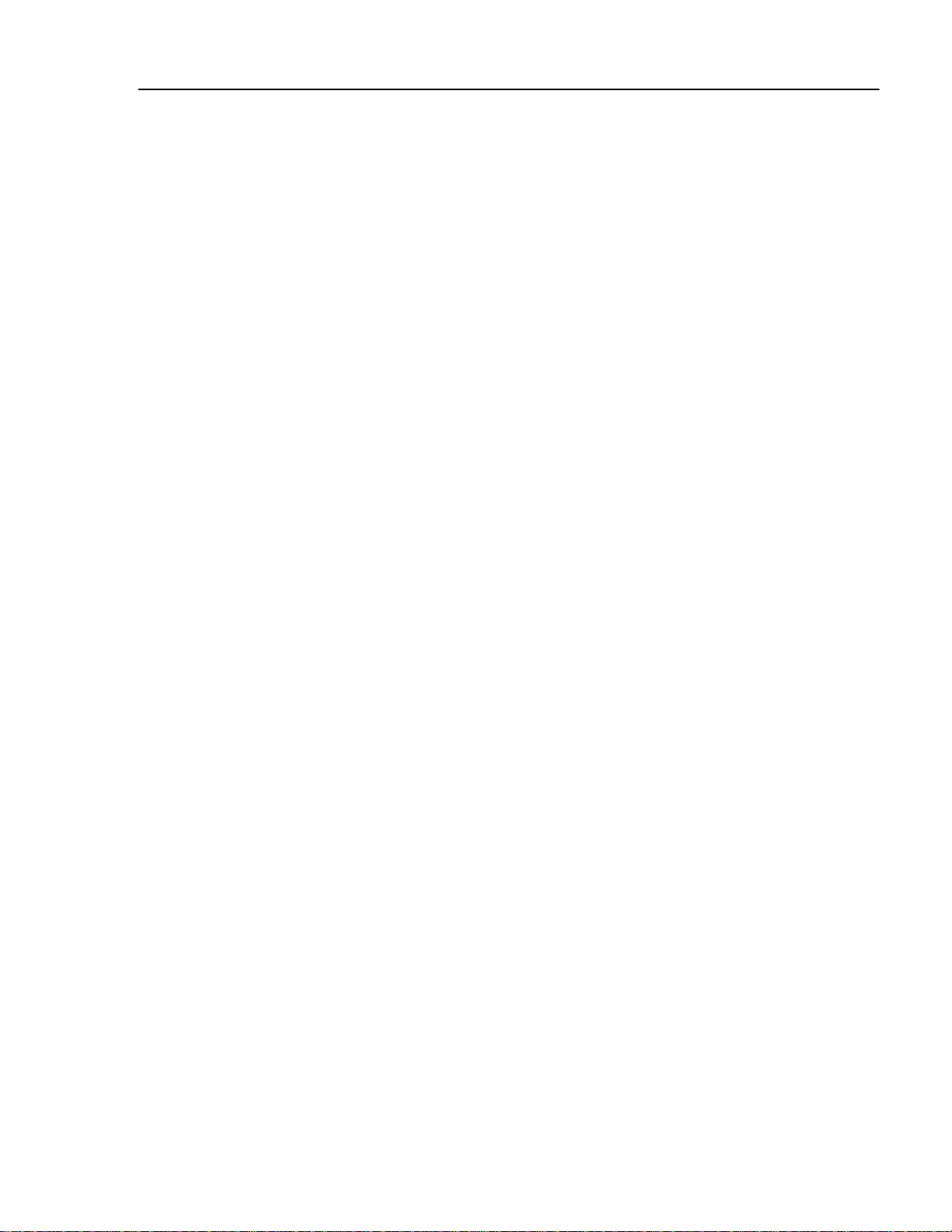
ITW Dynatec c. 2004
DYNAMINI ASU Manual 20-25 Page 3-7
Revised 1/05
Storage and Disposal of the DYNAMINI Application System
Temporary Storage of the Unit
1. Flush the adhesive application system with flushing fluid (PN L15653), following the
instructions detailed in chapter 6 of this manual.
2. Clean or replace both the output filter and the primary filter, following instructions detailed
in chapter 6.
3. Shut OFF all pressure and power sources.
4. Release residual air pressure.
5. Remove all residual adhesive and wipe components clean.
6. Remove all air lines and all power supply cables.
7. Pack the unit in a corrosion-proof manner.
8. Store the unit in such a way that it is protected from damage.
Disposal of the Unit
1. Shut OFF all pressure and power sources.
2. Release residual air pressure.
3. Remove all residual adhesive.
4. Remove all air and adhesive supply hoses and all power supply cables.
5. Dismantle all components and sort into mechanical and electrical components.
6. Arrange for all components to be recycled.
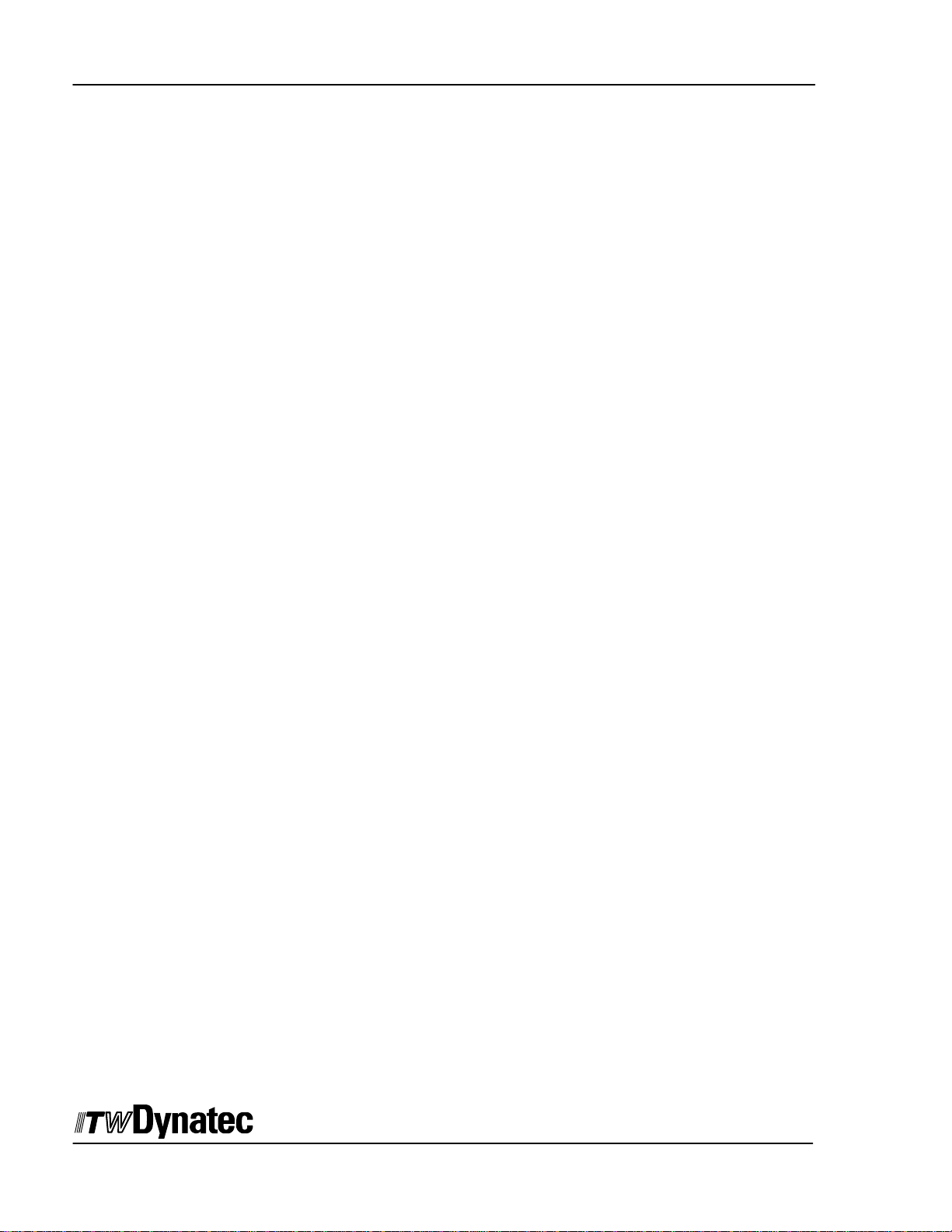
Page 3-8
Revised 1/05 ITW Dynatec c. 2004
DYNAMINI ASU Manual #20-25
ITW Dynatec
An Illinois Tool Works Company
Adhesive Application Solutions
Table of contents