Jema Autolifte JA3500T Operation instructions

Jema Autolifte –Denmark - WE ARE HERE TO SURPRISE!
JA3500T
Lifting capacity:3500KG
Floor Plate Two Post Lift
Electrical Release
Original Instruction

Jema Autolifte –Denmark - WE ARE HERE TO SURPRISE!
2
INDEX
1. Important safety instructions……………………………….…3~5
1.1 Important notices
1.2 Qualified personnel
1.3 Danger notices
1.4 Condition notices
1.5 Warning signs
1.6 Level of sound pressure
1.7 Training
2. Overview of the machine………………………………………5~6
2.1 Product introduction
2.2 Technical data
2.3 Construction of the lift
3. Installation instruction…………………………………………6~12
3.1 Preparation before installation
3.1.1 Tool and equipments needed
3.1.2 Parts check
3.1.3 Space required
3.2 Precautions during installation
3.3 Installation
3.4 Check list after installation
4. Operation instruction…………………………………………12~15
4.1 Precautions during operation
4.2 control box panel description
4.3 Flow chart for operation
4.4 Operation
4.5 Emergency lowing when the power is off
5. Trouble shooting………………….……………………………16~16
6. Maintenance…………………………………………………….17~18
7. Annex…………………………………………………….….……18~30
Annex1, Shipping sheet
Annex2, Overall diagram
Annex3, Space required
Annex4, Hydraulic connection
Annex5, Wiring diagram
Annex6, Exploded drawing parts
Annex7, Spare parts list
Annex8, Sizes and weight requirement for the vehicle and valve board diagram

Jema Autolifte –Denmark - WE ARE HERE TO SURPRISE!
3
1. Important safety instructions
1.1 Important notices
Jema Autolifte will give the user one-year warranty of quality for the machine. If something wrong with the machine within the
term of service, we will repair or replace the product according to the user’s demand. The manufacturer will not take any
responsibility for improper installation and operation, overload running, wrong concrete ground (that cannot meet the
requirements in the manual), normal mechanical abrasion and insufficient maintenance. The warranty will be carried out on the
basis of the type and serial number of the equipment. Therefore, the users shall provide them to the manufacturer when asking
service.
The 2-post lift is suitable for lifting motor vehicles having maximum weight as described, any other use is to be considered
improper and irrational and thus highly forbidden. The constructor cannot be held responsibilities for any damage or injuries
caused by an improper use or by the non-observance of the following instructions.
Read this guide carefully before using the machine and follow the instructions given by this guide to grant the machine a correct
function, efficiency and a long service life.
1.2 Qualified personnel
1.2.1 The lift may only be used by qualified staff, properly trained for the specific use of the machine.
1.2.2 The wiring must comply with local code and a certified electrician for electrical hook up.
1.2.3 Only authorized personnel are allowed in lifting area.
1.3 Danger notices
1.3.1 Do not install the lift on any asphalt surface
1.3.2 Read and understand all safety warning procedures before operating the lift.
1.3.3 The lift, in its standard version, is not designed for outdoor use.
1.3.4 Keep hands and feet away from any moving parts. Keep feet clear of lift when lowering.
1.3.5 The lift may only be used by qualified staff, properly trained for the specific use of the machine.
1.3.6 Do not wear unfit clothes such as large clothes with flounces, tires, etc, which could get caught by moving parts of the
machine.
1.3.7 The lift surrounding area must be free from people or objects which could be a danger for lifting operations.
1.3.8 The lift is only designed to lift the entire body of vehicle, having maximum weight not more than the lift capacity.
1.3.9 Always insure the safety devices are engaged before any attempt to work on or near vehicle.
1.3.10 The vehicle must be centered and positioned in a stable correct way with respect to the posts and following the
instructions given by manufacturer.
1.3.11 Make sure that the machine and its devices are working correctly, according to the specific instructions for maintenance
1.3.12 Lower the lift to its lowest position when service finishes.
1.3.13 Do not modify the machine without manufacturer’s advice.
1.3.14 If the machine is not to be used any more, owners is suggested to removing the power supply connections, emptying the
oil tank and disposing the liquids by right way.
1.3.15 If the lift is to be left unused for a long period, proceed as follows:
a. Disconnect the energy source
b. Empty the oil tank
c. Grease the moving parts which might be damaged by dust or drying out
1.4 Condition notices
Generally, this machine will be installed on the following conditions:
1.4.1 Supply voltage: 0.9 - 1.1 nominal supply voltage
1.4.2 Source frequency: 0.99 - 1.01 nominal frequency
1.4.3 Ambient temperature: 5°C - 40°C
1.4.4 Altitude: shall be at altitudes up to 1000m above mean sea level
1.4.5 Relative humidity: not exceed 50% at 40°C
1.4.6 Atmosphere: Free from excessive dust, acid fume, corrosive gases and salt.
1.4.7 Avoid exposing to direct sunlight or heat rays which can change the environmental temp.
1.4.8 Avoid exposing to abnormal vibration.
1.4.9 Electrical equipment shall withstand the effects of transportation and storage temperature within a range of -25°C to 55°C
and for short periods not exceeding 24 hours at up to +70°C.

Jema Autolifte –Denmark - WE ARE HERE TO SURPRISE!
4
Attention: Dispose the unused oil by a correct way to protect the surround environment.
1.5 Warning signs
All safety warning signs presented on the machine with the purpose to draw the operator’s attention from dangerous or unsafe
situations. The labels must be kept clean and they have to be replaced if detached or damaged. Read the meaning of the labels
carefully and memorize it.

Jema Autolifte –Denmark - WE ARE HERE TO SURPRISE!
5
1.6 Level of sound pressure
The sound pressure of the car lift does not exceed 75DB. For the sake of your healthy, we suggest you place a noise meter in
the operation area.
1.7 Training
Only qualified personnel can operate and use the lift. Contact the manufacturer to provide with trained courses and aid you in
becoming familiar with the car lift.
2. Overview of the machine
2.1 Product Introduction
The floor plate lift is composed of posts, carriages, lifting arms, cylinders and power unit, etc.
The lift is operated by an electric motor controlling a hydraulic system, which delivers the hydraulic fluid to cylinders inside the
columns for lifting two trolleys. The safety teeth block will bite with safety plate in the posts automatically. Therefore, the lift will
not lower when hydraulic system trouble happens.
Safety structure:
2.2 Technical data
Model
Lifting capacity
Lifting time
Lifting height
Height
Width
Width between posts
JA3500T
3500kg
50 Sec
1900mm
2850mm
3581mm
2780mm
Weight on JA3500T = 700 KG

Jema Autolifte –Denmark - WE ARE HERE TO SURPRISE!
6
2.3 Construction of the lift
3. Installation instruction
3.1 Preparation before installation
3.1.1 Tools and equipments needed
Appropriate lifting equipment
AW 32. 46 or other good quality garage hydraulic oil.
Rotary Hammer Drill with 3/4’’ drill bit.
Chalk line and tape measure.
Sockets and Open wrench set.
Hammer 4pounds
Ф2 tape measure
3.1.2 Parts check ---annex 1(shipping sheet)
Remove the packing material, identify the components and check for shortages as ANNEX 1(shipping sheet), Contact us
immediately if shortage discovered. If the buyer still installs the machine upon the shortage, the manufacturer and the dealer
will not hold any responsibility and will not solve the problems by free.
3.1.3 Space required
The lift should be located on a relatively level concrete floor, having minimum thickness of 18cm.
The lift should be fixed on a smooth and solid concrete ground with its strength more than 3000psi, tolerance of flatness less
than 5mm and minimum thickness of 200mm. In addition, newly built concrete ground must undergo more than 28days’ cure
and reinforcement.

Jema Autolifte –Denmark - WE ARE HERE TO SURPRISE!
7
3.2 Precautions during installation
3.2.1 Make sure the two posts are vertical to the floor.
3.2.2 Oil hose and wire rope connection should be correct, make sure the joints are tight.
3.2.3 All the bolts connection should be tight.
3.2.4 Do not place any vehicle when try running the lift.
3.3 Installation
Step one: Remove the packing materials, take out the parts carton and cover plate.
Step two:Remove the packing brackets and bolts holding the two columns together.
Attention:Be careful in this step, in case the posts fall down &the personnel or the parts are damaged.
Step three:Remove the first post and place a supporter under the second post, then remove the bolts.
Step four: Decide the installation position of the columns, erect the main and assistant post. Pay attention
that the width between posts is 2780MM
1. Determine which side will be the main post to mount the power unit and the other assistant post.
2. Once the location is selected, use a chalk line to layout a grid for the post locations and make an outline of the posts on the
floor at each location.
3. Before proceeding, double check measurements and make certain that the bases of each column are square and aligned
with the chalk line.
2780

Jema Autolifte –Denmark - WE ARE HERE TO SURPRISE!
8
Step five: erect the posts, main post first and then the assistant post
1. Drill each anchor hole in the concrete using a rotary hammer drill. To assure full holding power, do not ream the hole or
allow drill to wobble.
2. After drilling, remove dust thoroughly from each hole and make certain that the column remains aligned with the chalk line
during this process.
3. Position the main column at the designated chalk locations and follow the same procedures step 1, 2 to position the
assistant column.
Step six:Install the bottom trough plate
Step seven: connect the wire rope
1. Raise and lock each carriage approximately 800mm high above the ground.
2. Make sure that the safety locks on each column are fully engaged before attempting to route equalizer cables.
3. Carriages must be equal height from the floor before proceeding.
4. With the carriages in equal position from the floor, route the equalizer cables as shown.
5. After the equalizer cables have been routed, adjust each cable so that they are equal tension.
6. Grease the wire rope with butter.(this step must be carried out )
Bolt to adjust the tightness of
the wire rope

Jema Autolifte –Denmark - WE ARE HERE TO SURPRISE!
9
Step eight: connect the oil hose
Connect the oil hose as the following diagram.
Step nine: Install four safety plates, four electromagnets and the electromagnet covers
Safety plate

Jema Autolifte –Denmark - WE ARE HERE TO SURPRISE!
10
Step ten: mount the power unit and the control box
1. Mount the power unit on the main post
2. Connect the power unit with the control box as the wiring diagram
3. Connect the limit switch
Step eleven: Install the oil hose cover
Limit switch
Oil hose cover

Jema Autolifte –Denmark - WE ARE HERE TO SURPRISE!
11
Step twelve: Install the lifting arms
Connect the lifting arm and the carriage by pin. Install the swing arms on the carriages. Check to make sure the rack on the lock
should be fully engaged.
Step thirteen: fill the hydraulic oil
The volume of the oil tank is 10L,To insure the lift in a normal work condition, the oil should be over 80% of the oil tank volume;
Use AW 32# in winter/46# in summer or other good quality garage hydraulic oil.
Step fourteen: try running the lift
Do not place any vehicle in this step
Step fifteen: install the chain protection and the door-opening protection
Chain protection
Door-opening protection

Jema Autolifte –Denmark - WE ARE HERE TO SURPRISE!
12
Step sixteen: install the cover plate
3.4 Check list after installation
S/N
Check items
YES
NO
1
If the columns is vertical to the floor
2
If the two posts are horizontal
3
If the oil hose connection is correct
4
If the wire rope connection is correct
5
If the arm is fastening
6
If the wiring is correct
7
If the other joints are tightened
4. Operation instruction
4.1 Precautions during operation
Remark: Only authorized staff can adjust the system pressure on the power unit.
4.1.1 Check all the pipelines and joints before use. The machine only can be used after there is not any leakage.
4.1.2 The lift, if its safety device malfunctions, shall not be used.
4.1.3 The machine shall not lift or lower an automobile if the center of gravity of automobile is not within the supporting range of
the supporting device. Otherwise, the manufacturer will not bear any responsibility for the consequence resulted from the
operation above mentioned.
4.1.4 The staff or operators shall be in a safe position when the machine lift or lower.
4.1.5 When the lift with vehicle on reaches a desired height, first of all, the main switch must be turned off before the
automobile is repaired so as to prevent non-operator or unauthorized person from pressing the start switch.
4.1.6. Always lock the lift by pressing handle on power unit before going under the vehicle. Never allow anyone to go under the
lift when raising or lowering.

Jema Autolifte –Denmark - WE ARE HERE TO SURPRISE!
13
Start
Turn on the power switch
Press DOWN button
The lift is lowered
Start
Turn on the power switch
Press UP button
Motor drives the gear pump work
Cylinder piston drives the chain work
Chain drives the carriage to rise
The lift is raised
4.2 control box panel description
4.3 Flow chart for operation
Description
Function
Power switch
Connect the power
Power lamp
Show the power is on
UP button
Raise the lift
LOCK button
Make sure the security during repair work
DOWN button
Lower the lift
Raising
Lowering

Jema Autolifte –Denmark - WE ARE HERE TO SURPRISE!
14
4.4 Operation
Raise the lift
1. Make sure that you have read the operation manual before operation.
2. Position the vehicle between columns.
3. Adjust the swing lift arms so that the vehicle is positioned with the center of gravity of midway between pads
4. Turn on the Power Switch, the power indicating light is on, raise the lift by pressing the up button on control box until the
pads touch firmly the right points and recheck if the vehicle is secure.
5. Continue to press the UP button to raise the lift to the demanded height.
6. Press the handle of the manual unloading valve to lock the lift
7. Check the security of vehicle, and then turn off the power switch before performing maintenance or repair work.
Lower the lift
1. Turn on the power switch
2. Press the DOWN button on control box, the lift will raise about 5CM automatically to release the safety lock and then, the
lift lowers.
3. Before driving away the vehicle, clear all the obstacles.
4.5 Emergency lowering when the power is off
The carriage is not engaged:
a. Pull off the electromagnets on the two posts.
b. Loosen the electrical valve of the power unit to lower the carriage.

Jema Autolifte –Denmark - WE ARE HERE TO SURPRISE!
15
The carriage is engaged:
a. Screw off the fitting(opposite of the oil out-let) to connect the manual hydraulic pump
b. Press the handle of the hydraulic pump(optional) to supply oil to the cylinder to release the lock
c. Pull off the electromagnets on the two posts.
d. Loosen the electrical valve of the power unit to lower the carriage.

Jema Autolifte –Denmark - WE ARE HERE TO SURPRISE!
16
5. Trouble Shooting
ATTENTION: If you could not do the trouble shooting by your own, please contact us for help. You are requested to send us the
serial No. with detailed description of faulty machine or parts. We keep the right to ask for photos and pictures for diagnostics
TROUBLE
CAUSE
SOLUTION
Abnormal noise
There is abrasion in the post
Grease the inside of the post
There is trash in the post
Clear away the trash
Motor does not run and
will not rise
The wire connection is loose
Check it and make a good connection.
The motor is blown
Replace it.
The limit switch is damaged or the
wire connection is loose
Make a good connection, adjust or replace
the limit switch.
Motor runs but will not
raise
The motor reverse
Check the wire connection.
A piece of trash is under overflow
valve or the overflow valve is loose
Clean or adjusts the it
The gear pump is damaged
Replace it
Oil level too low
Oil level should be more than 2/3 oil tank
volume.
The oil absorbing pipe is loose
Tighten it
A piece of trash is under cushion valve
or the cushion valve is loose
Clean or adjusts it
Carriages go down
slowly after raising
Raising too slow
The oil hose leaks
Check or replace it
The seal of the cylinder is abrasion
Replace the seal
The single valve leaks
Clean or replace it
The overflow valve leaks
Clean or replace it
Manual unloading valve or electrical
unloading valve leaks
Clean or replace it.
The oil filter is jammed
Clean or replace it.
Lowering too slow
Oil level too low.
Oil level should be more than 2/3 oil tank
volume.
The overflow valve is loose
Adjust it.
The hydraulic oil is too hot ( above
45°)
Change the oil
The seal of the cylinder is abrasion
Replace the seal.
The post inside is rough
Grease the post inside
There is trash in the throttle valve
Clean or replace
The wire rope is abraded
The hydraulic oil is dirty
Change the oil
There is trash in the anti-surge valve
Replace it
There is trash in the oil hose
Replace it
Did not grease the wire rope with
grease in installation or the use time of
the wire rope is out of its service
lifetime
Replace it

Jema Autolifte –Denmark - WE ARE HERE TO SURPRISE!
17
6. Maintenance
The several pieces of maintenance operations to be carried out are described below. A low operating cost and a long life of the
machine are from routine observation of there operations.
The listed intervention times are given for information and they refer to normal operating conditions. They can change according
to the kind of service, environment, frequency of use, etc.
THE FOLLOW PARTSARE NEEDED TO BE LUBRICATED
6.1. DAILY PRE-OPERATION CHECK
The user should perform daily check. Daily check of safety latch system is very important –the discovery of device failure
before needed could save you from expensive property damage, lost production time, serious personal injury, even death.
Check safety lock audibly and visually while in operation.
Check safety latch for free movement and full engagement with rack.
Check hydraulic connections and hoses for leakage.
Check chain connections for bends, cracks and looseness.
Check cables connections for bends, cracks and looseness.
Check for frayed cables in both raised and lowered position.
Check snap rings at each roller and sheave.
Check bolts, nut and screws. Tighten if needed.
Check wiring and switches for damage.
Keep base plate free of dirt, grease or any other corrosive substances.
Check floor for stress cracks near anchor bolts.
6.2. WEEKLY MAINTENANCE
Check the cleanness of the mobile parts.
Check the safety device as previously described.
Check hydraulic fluid level as follow: let the trolleys go up completely and in case they do not reach maximum
height, add oil.
S/N
Description
1
Upper wheel
2
Wire rope
3
Chain wheel
4
Chain
5
Sliding block
6
Pin
7
Arm block
8
Lifting arm
9
Tray
10
Down wheel

Jema Autolifte –Denmark - WE ARE HERE TO SURPRISE!
18
Check and tighten bolts, nuts and screws
6.3. MONTHLY MAINTENANCE
Check the tightening of screws
Check the hydraulic system seal and tighten the loose unions, if necessary.
Check the greasing and wear condition of pins, rollers, bushes, of trolley structure as well as arms and relevant
extensions, if necessary, replace the damaged parts by original spare parts.
6.4. YEARLY MAINTENANCE
Lubricate chain.
Grease rub blocks and column surface contacting rub blocks.
Change the hydraulic fluid. Good maintenance procedure makes it mandatory to keep hydraulic fluid clean.
Due to operating temperature, type of service, contamination levels, filtrationand chemical composition of
fluid, the hydraulicfluid may need to be changed more or less frequently.
If the above maintenance operations are carried out, there will be an advantage for the user, who will find the
equipment in perfect condition each time he restarts work.
7. ANNEX
ANNEX1,Shipping Sheet
S/N
DESCRIPTION
PART NO
MATERIAL
Q’TY
1
Main and assistant post
JA3500T-C-A1
Component
2
2
Carriage
JA3500T-C -A2
Component
2
6
Power unit
JA3500T-C -B5-B6
Component
1
7
Assistant cylinder
JA3500T-C -A5-B4
Component
1
8
Main cylinder
JA3500T-C -A5-B5
Component
1
9
Electrical system
JA3500T-C -A5
Component
1
Control box
1
Electromagnet and its cover
1
10
Wire rope L=8785mm
JA3500T-C -A6
Component
2
11
Long arm
JA3500T-C -A7
Component
2
12
Short arm
JA3500T-C -A8
Component
2
13
Bottom trough plate
JA3500T-C -A9
Welding piece
1
14
Cover plate
JA3500T-C -A10
Q235A
1
15
Right packing frame
JA3500T-C -A30-B1
Topper plate cover
JA3500T-C -A16
ABS
2
16
Left packing frame
JA3500T-C -A30-B2
20
Carton(include the following parts)
22
Pin
A12
Component
4
23
Height adapter
JA3500T-C -A11
Q235A
4
24
Foot protector
A9-B3
Welding piece
2
25
Foot protector
JA3500T-C -A7-B5
Component
2
26
Tray
JA3500T-C -A7-B4
Component
4
27
Pulling rod
JA3500T-C -A2-B1
Component
4

Jema Autolifte –Denmark - WE ARE HERE TO SURPRISE!
19
28
Oil hose L=2550mm
JA3500T-C -B4-B1
Component
1
29
Oil hose L=2880mm
JA3500T-C -B4-B2
Component
1
30
Safety plate
JA3500T-C -A13
45
4
32
Electromagnet cover
JA3500T-C -A15
ABS
4
34
Positioning block
JA3500T-C E-A17
Q235A
4
35
Oil hose cover
JA3500T-C -A18
Q235A
6
36
Chain protection
JA3500T-C -A1-B5
2
37
Chain protection hook
JA3500T-C -A1-B6
Welding piece
4
38
Door-opening protection
JA3500T-C -A7-B10
Rubber
2
39
Bolt
M8*30
Standard piece
4
41
Screw
M8*12
Standard piece
8
42
Screw
M5*10
Standard piece
24
43
Screw
M5*20
Standard piece
12
44
Screw
M6*8
Standard piece
4
45
Screw
M6*16
Standard piece
4
46
Screw
M8*25
Standard piece
4
47
Flat washer
6
Standard piece
8
48
Flat washer
10
Standard piece
4
49
Spring washer
10
Standard piece
4
50
Nut
M6
Standard piece
8
51
Nut
M0
Standard piece
4
52
Circlip for shaft
50
Standard piece
4
53
Expansion bolt
M16*160
Standard piece
10

Jema Autolifte –Denmark - WE ARE HERE TO SURPRISE!
20
ANNEX 2, Overall Diagram
Table of contents
Other Jema Autolifte Lifting System manuals
Popular Lifting System manuals by other brands

Challenger Lifts
Challenger Lifts EnviroLift EV1020QC Installation, operation & maintenance manual
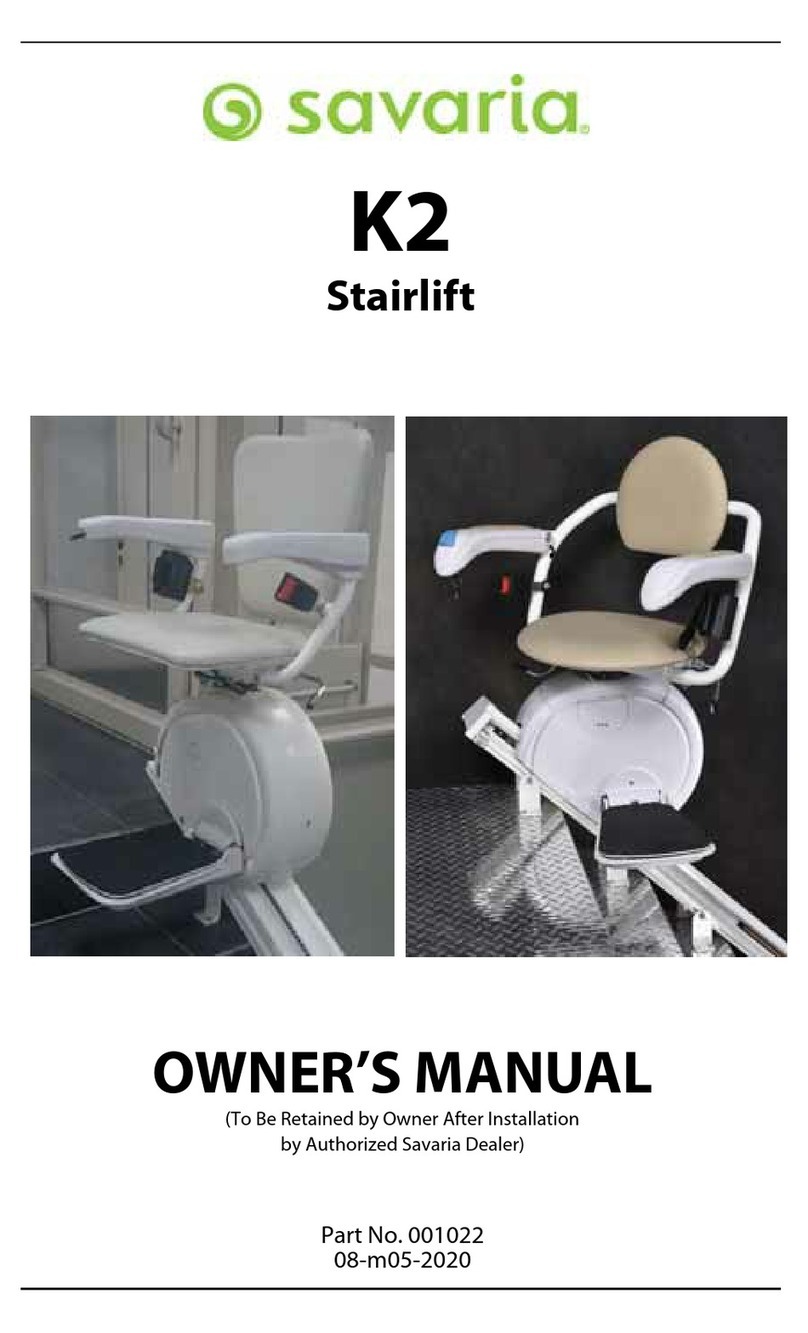
Savaria
Savaria K2 owner's manual
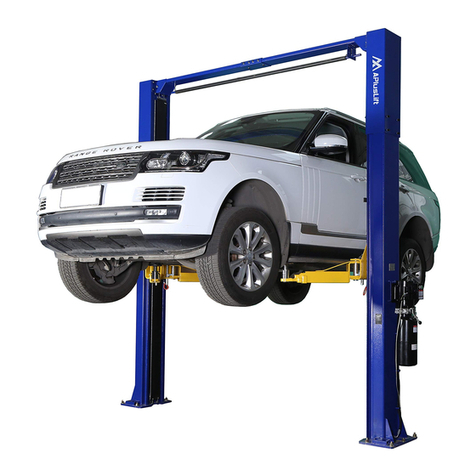
Atlas Equipment
Atlas Equipment OH-10X manual
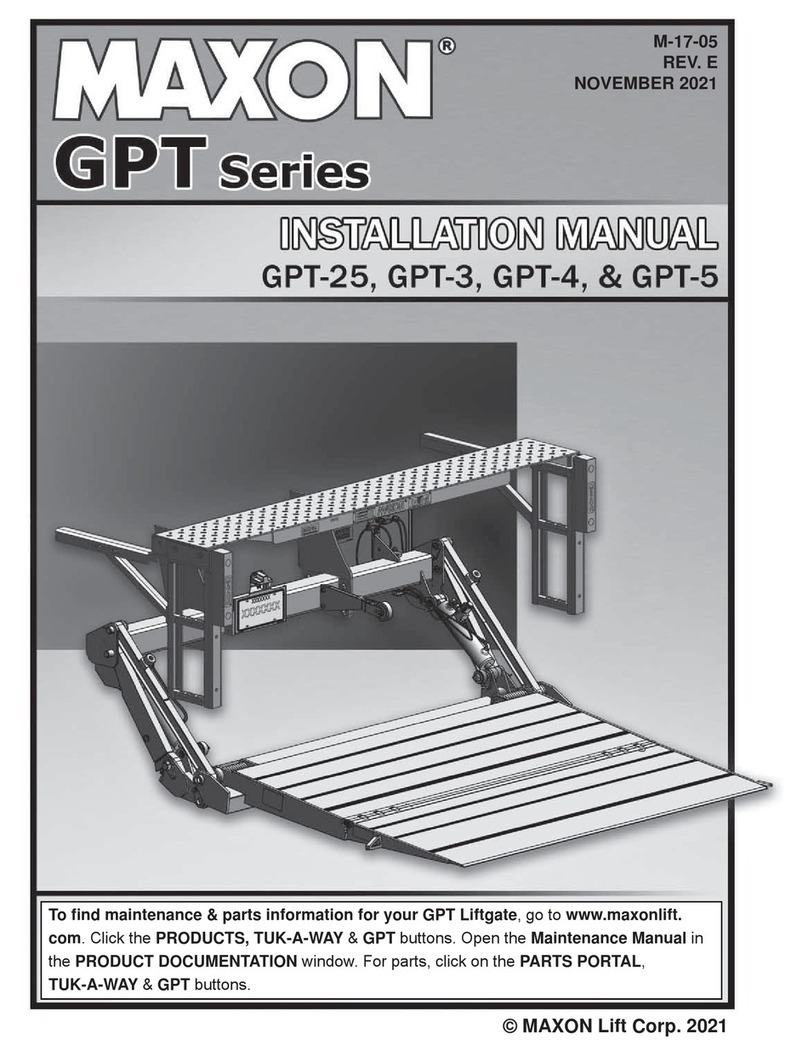
Maxon
Maxon Tuk-A-Way GPT Series installation manual
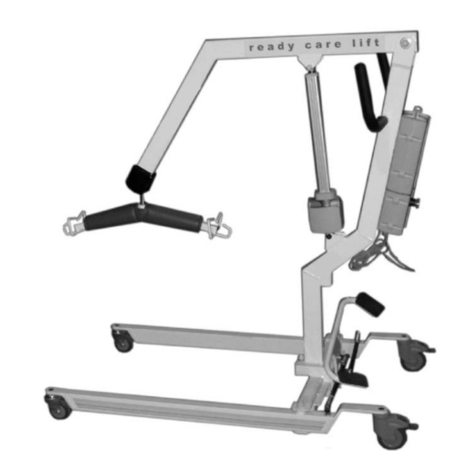
Barton
Barton RCL-4002 Operation manual

Strongway
Strongway 55833 owner's manual