Johnson Controls EDA-8102 Assembly instructions
Other Johnson Controls Controllers manuals
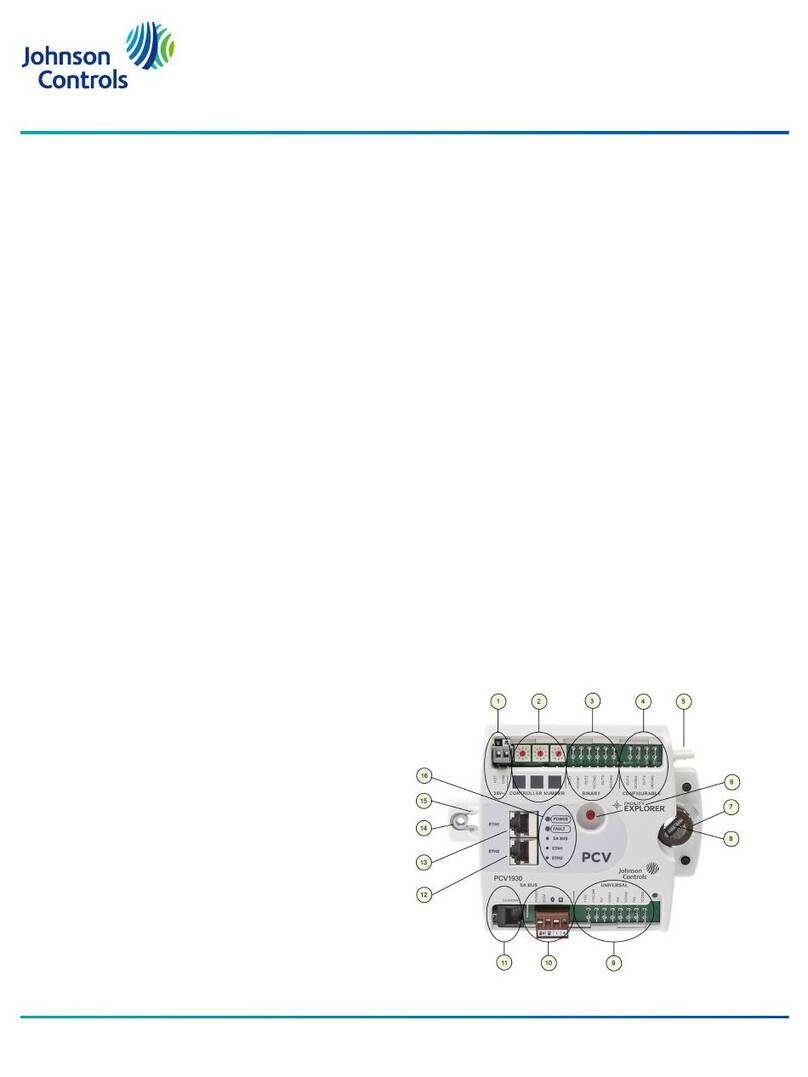
Johnson Controls
Johnson Controls FX-PCV1930 User manual
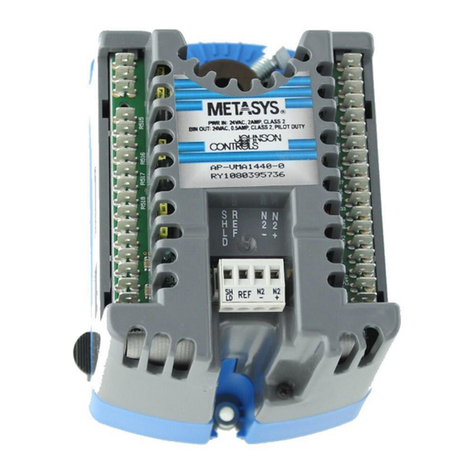
Johnson Controls
Johnson Controls VMA 1400 Series User manual

Johnson Controls
Johnson Controls VA-8122 Service manual
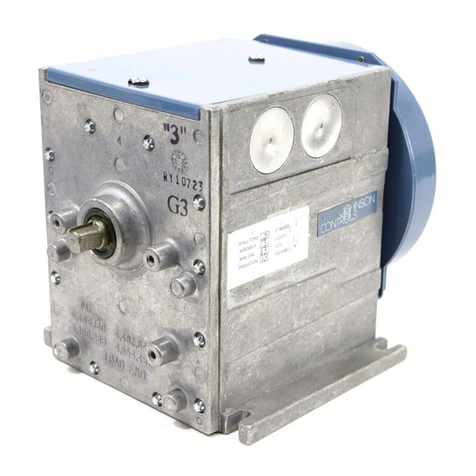
Johnson Controls
Johnson Controls M100G User manual
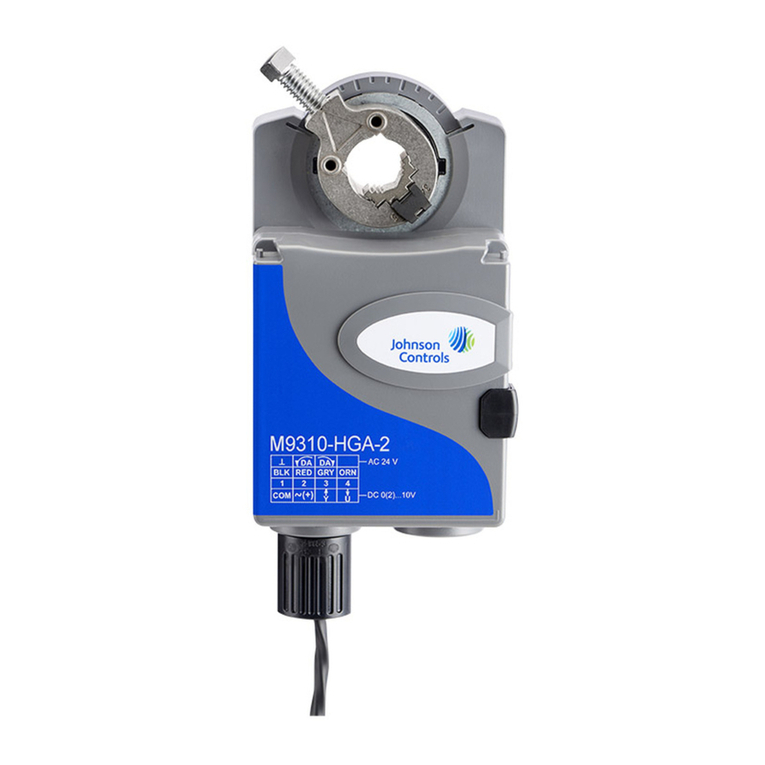
Johnson Controls
Johnson Controls M9310 Series User manual
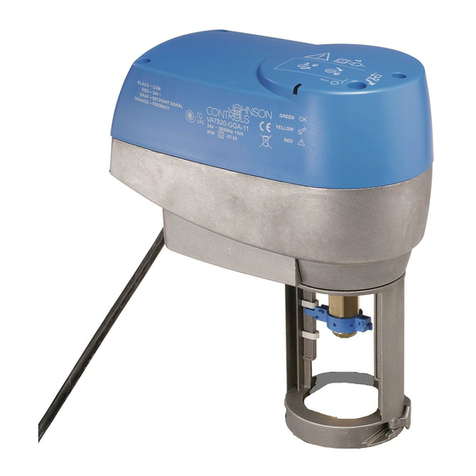
Johnson Controls
Johnson Controls VA7800 Series User manual
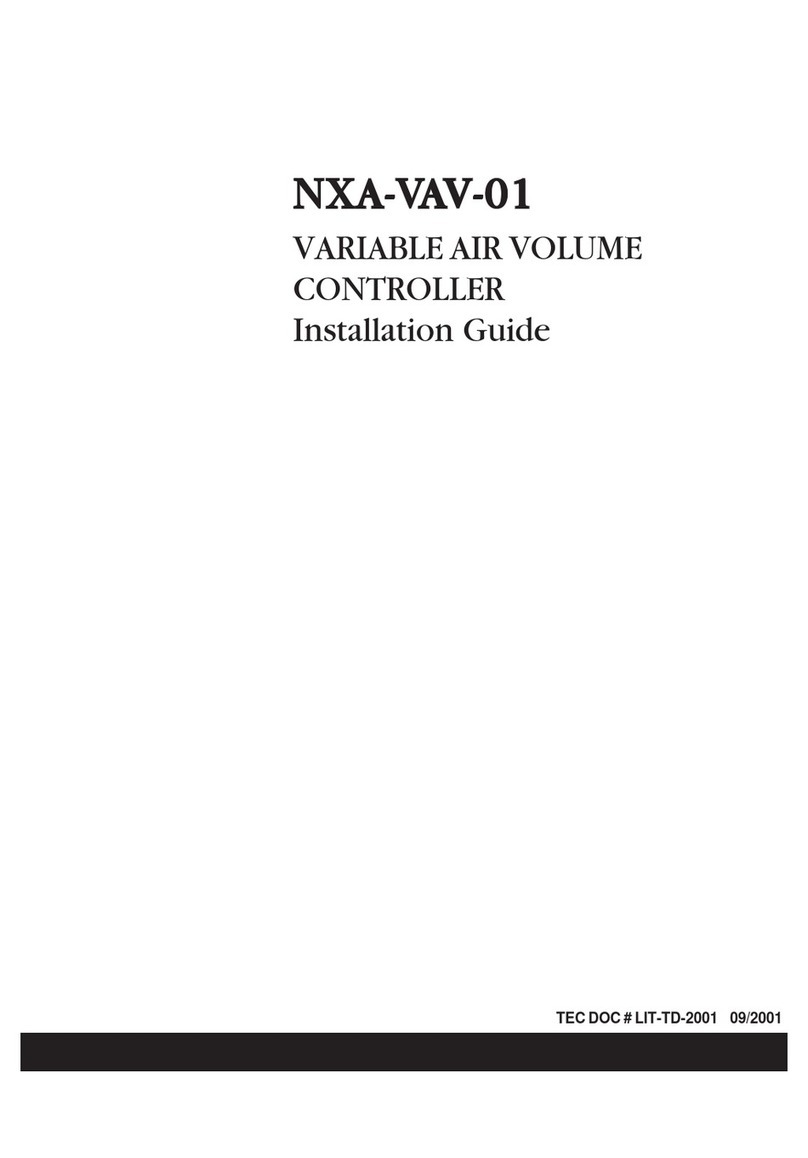
Johnson Controls
Johnson Controls NXA-VAV-01 User manual

Johnson Controls
Johnson Controls VA9104-AGA-1S User manual
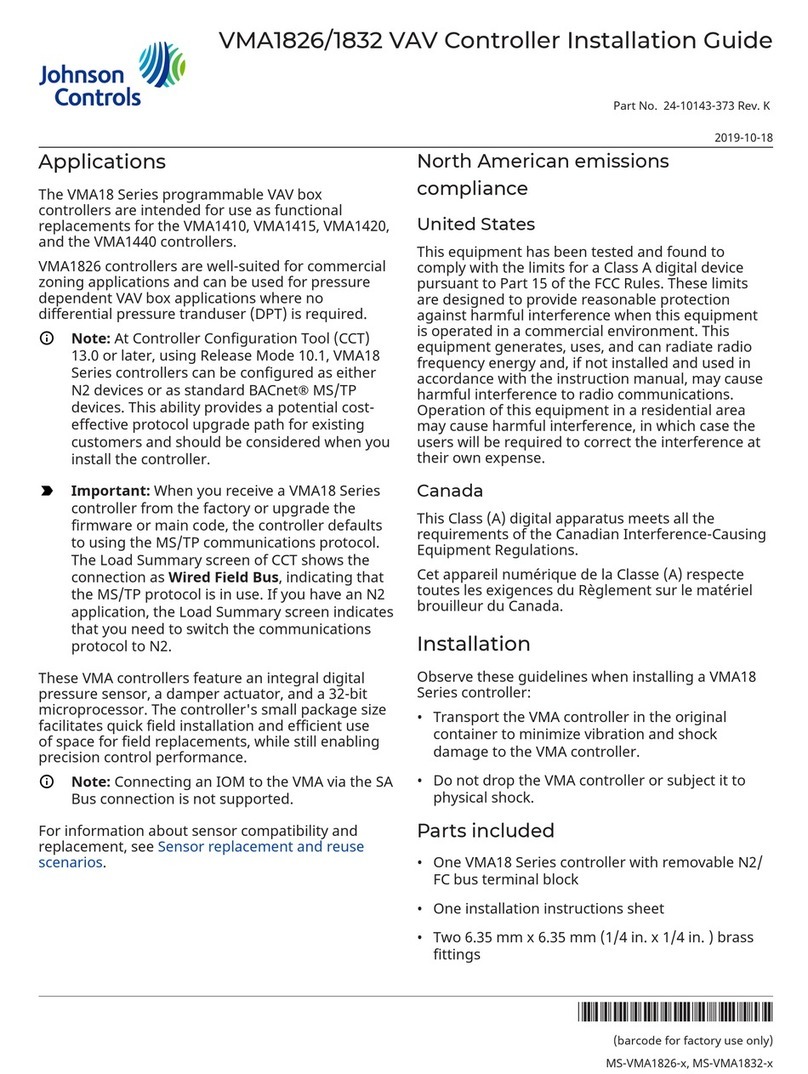
Johnson Controls
Johnson Controls VMA18 Series User manual
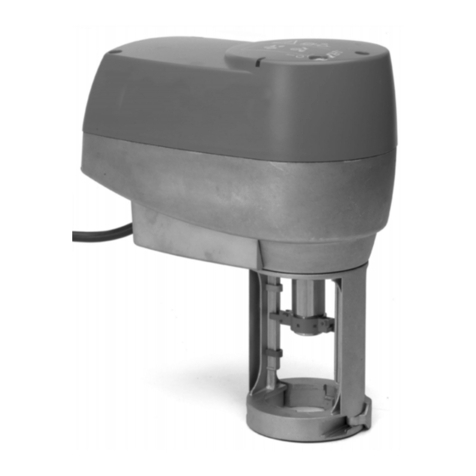
Johnson Controls
Johnson Controls VA7820-GG-1 Series User manual
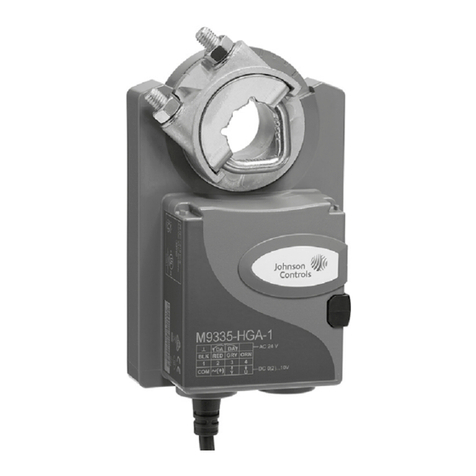
Johnson Controls
Johnson Controls M9316-A Z Series User manual
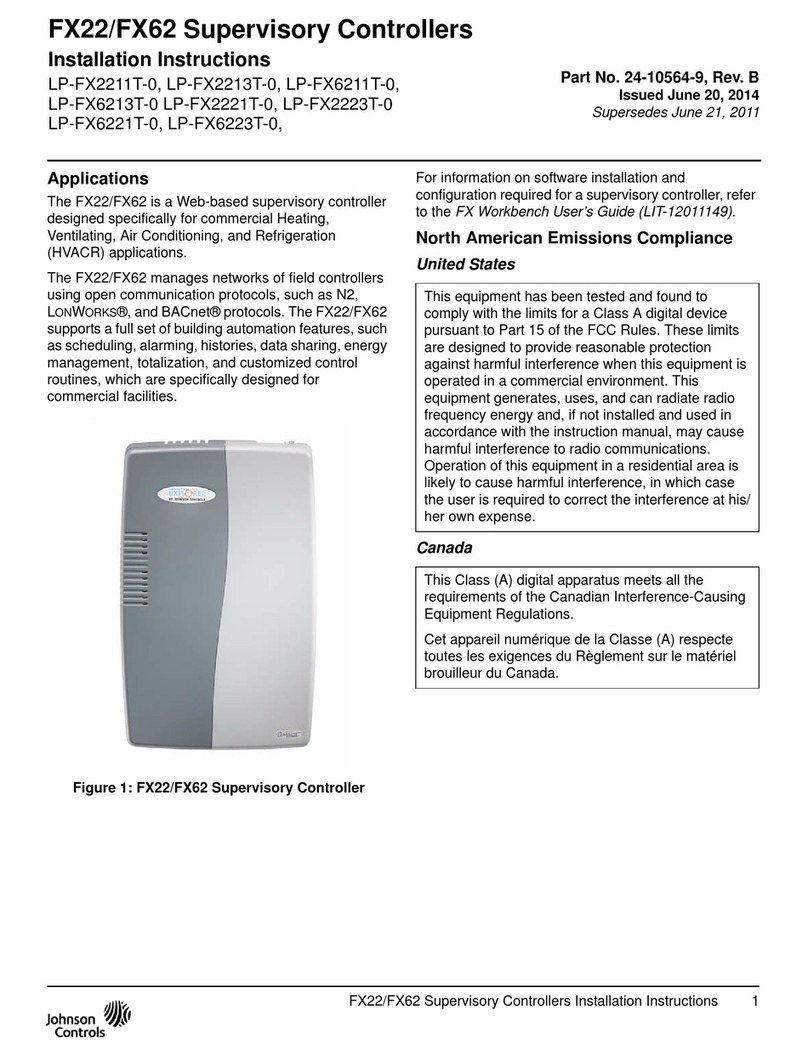
Johnson Controls
Johnson Controls LP-FX2211T-0 User manual
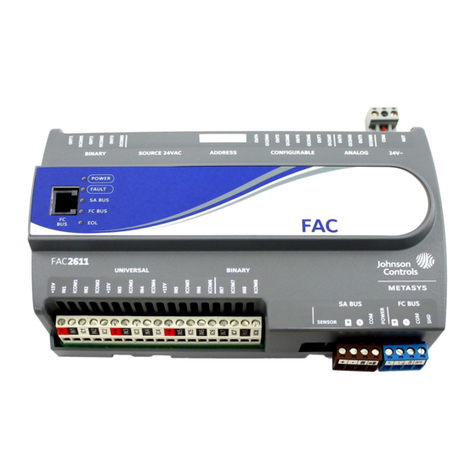
Johnson Controls
Johnson Controls FAC2611-0U User manual
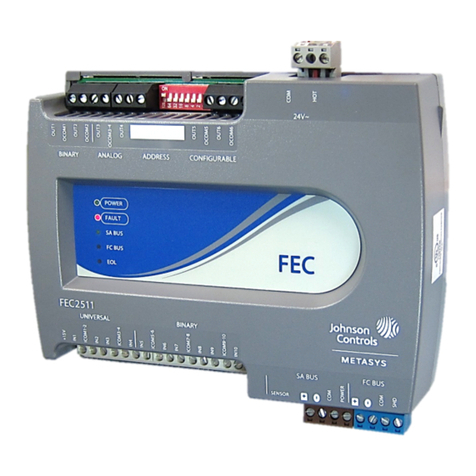
Johnson Controls
Johnson Controls FEC25 User manual
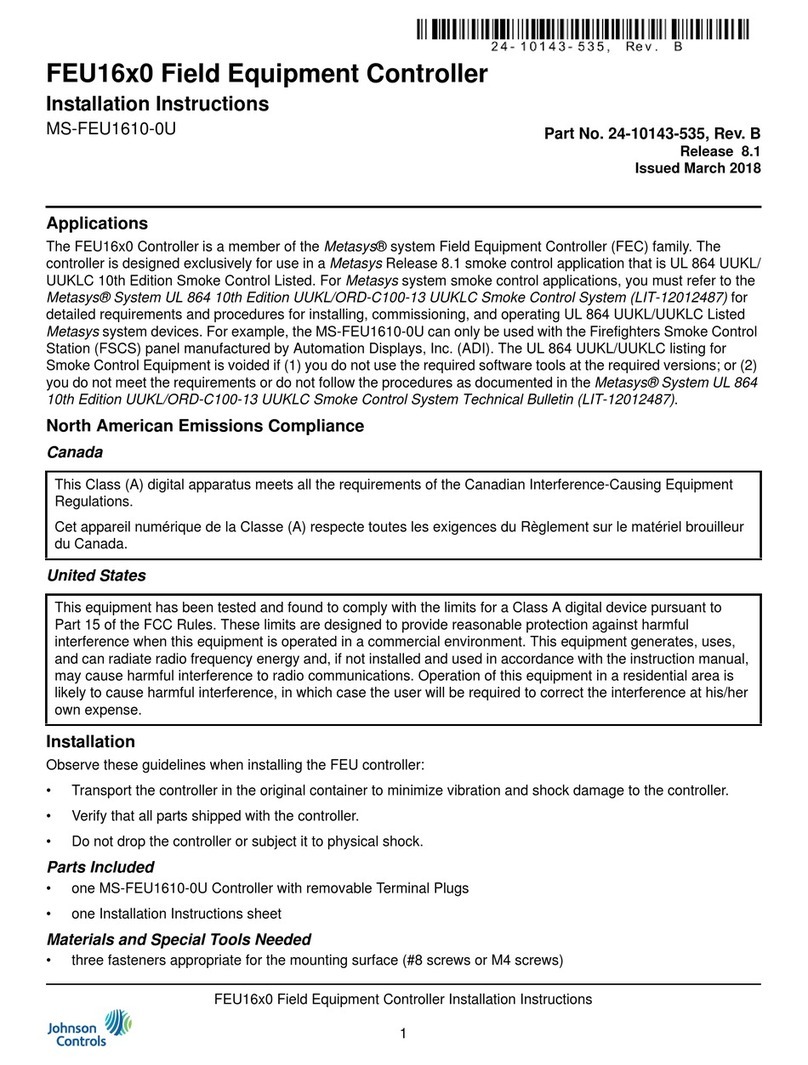
Johnson Controls
Johnson Controls Metasys MS-FEU1610-0U User manual
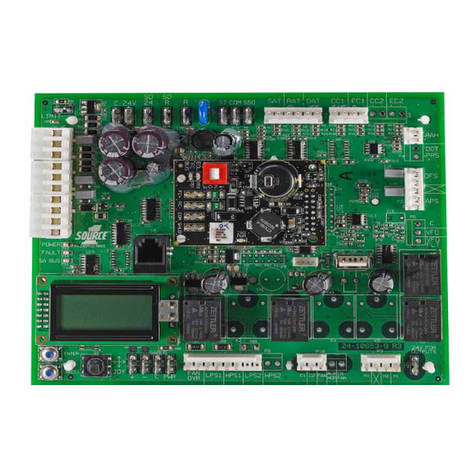
Johnson Controls
Johnson Controls SE-SPU101 Series User manual

Johnson Controls
Johnson Controls F4-CV Series User manual
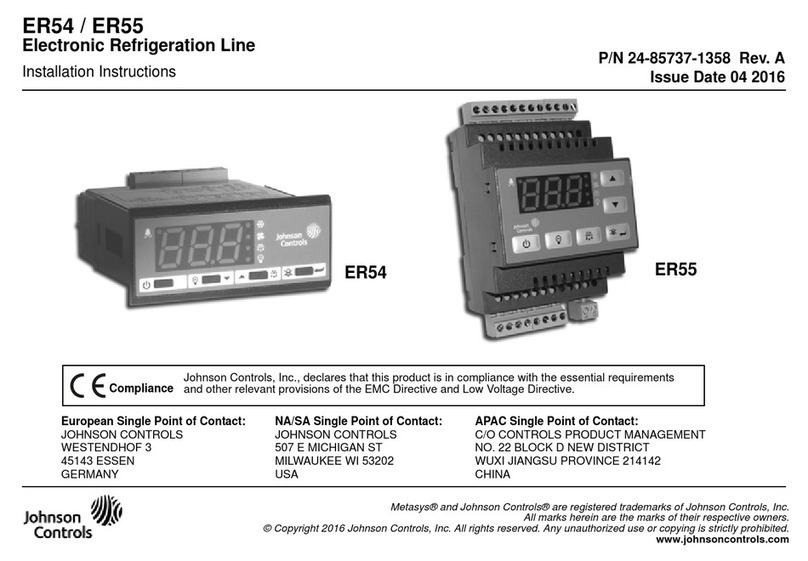
Johnson Controls
Johnson Controls ER54 User manual
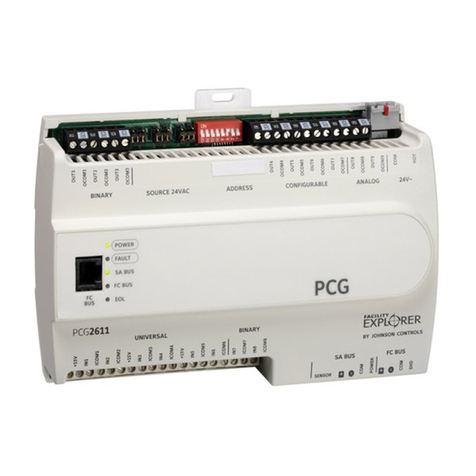
Johnson Controls
Johnson Controls FX-PCG26 User manual

Johnson Controls
Johnson Controls PENN P70 Series User manual
Popular Controllers manuals by other brands

Basler
Basler SSR 32-12 instruction manual
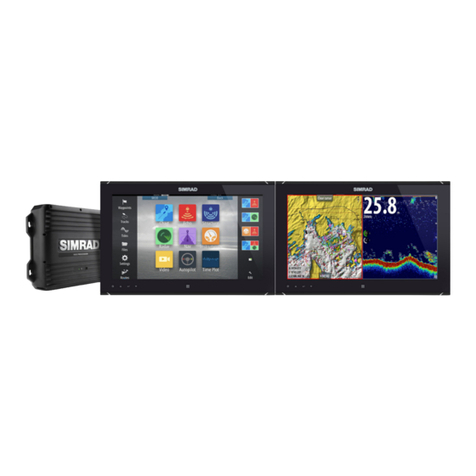
Simrad
Simrad NSO evo3S MPU installation manual
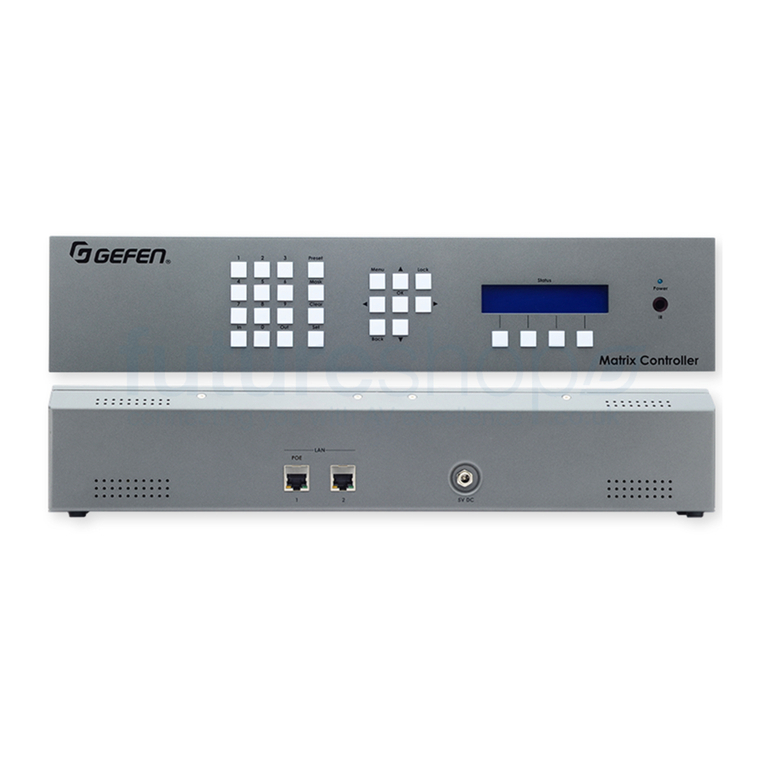
Gefen
Gefen EXT-CU-LAN user manual

Heatcraft Refrigeration Products
Heatcraft Refrigeration Products 25001501 Installation & operating instructions
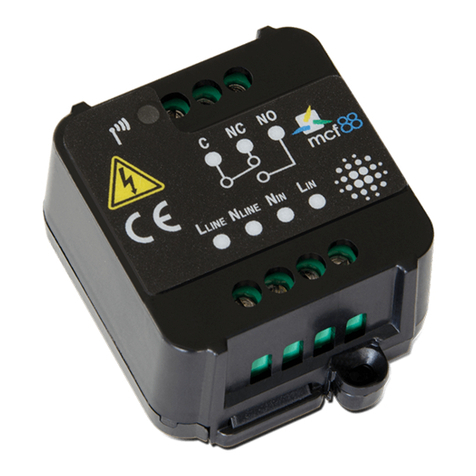
M2M
M2M enginko MCF-LW13IO operating manual
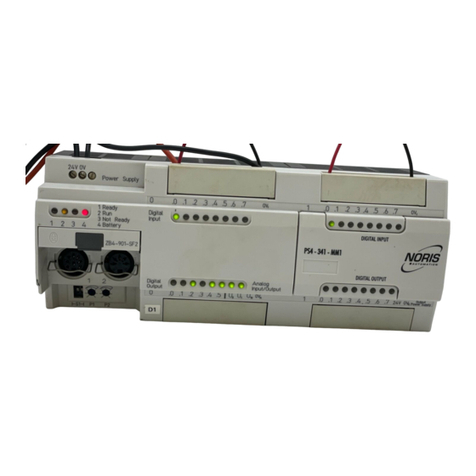
Moeller
Moeller PS 4-300 Series Hardware and engineering