Kaufman & Robinson eHF 3005A User manual

Kaufman & Robinson, Inc.
1306 Blue Spruce Drive, Unit A
Fort Collins, CO 80524
Tel: 970-495-0187, Fax: 970-484-9350
Internet: www.ionsources.com
Copyright © 2011 by Kaufman & Robinson, Inc.
All rights reserved. No part of this publication
may be reproduced without written permission.
February 2011
VERSION 4
AUTOMATED CONTROLLER MANUAL
FOR
eH End-Hall Ion Source with
Filament Cathode
Models: eHF 3005A
eHF 30010A
eHF 15012A

CONTENTS I
_______________________________________________________________________
Copyright © 2010 by Kaufman & Robinson, Inc., 1306 Blue Spruce Drive, Unit A, Fort Collins, CO 80524
Tel: 970-495-0187, Fax: 970-484-9350, Internet: www.ionsources.com
CONTENTS
1. SAFETY . . . . . . . . . . . . . . . . . . . . . . . . . . . . . . . . . . . . . . . . . . . . . . . . . . . . . 1-1
2. GENERAL DESCRIPTION AND SPECIFICATIONS . . . . . . . . . . . . . . . . . . . .2-1
2.1. Auto Controller . . . . . . . . . . . . . . . . . . . . . . . . . . . . . . . . . . . . . . . . . . . . . .2-2
2.2. Filament Power Supply . . . . . . . . . . . . . . . . . . . . . . . . . . . . . . . . . . . . . . .2-2
2.3. Discharge Power Supply . . . . . . . . . . . . . . . . . . . . . . . . . . . . . . . . . . . . . . .2-2
2.4. Mass Flow Controllers . . . . . . . . . . . . . . . . . . . . . . . . . . . . . . . . . . . . . . . 2-3
3. INSTALLATION . . . . . . . . . . . . . . . . . . . . . . . . . . . . . . . . . . . . . . . . . . . . . . . .3-1
3.1 Unpack . . . . . . . . . . . . . . . . . . . . . . . . . . . . . . . . . . . . . . . . . . . . . . . . . . . .3-1
3.2 Install in Rack Mount Cabinet . . . . . . . . . . . . . . . . . . . . . . . . . . . . . . . . . . .3-2
3.3 Ground Connections . . . . . . . . . . . . . . . . . . . . . . . . . . . . . . . . . . . . . . . . . .3-2
3.4 Connections Between Controller Components . . . . . . . . . . . . . . . . . . . . . . 3-2
3.5 Connect Controller to Ion Source . . . . . . . . . . . . . . . . . . . . . . . . . . . . . . . . 3-5
4. INITIAL OPERATION . . . . . . . . . . . . . . . . . . . . . . . . . . . . . . . . . . . . . . . . . . . .4-1
4.1 Gas . . . . . . . . . . . . . . . . . . . . . . . . . . . . . . . . . . . . . . . . . . . . . . . . . . . . . . 4-1
4.2 Power On . . . . . . . . . . . . . . . . . . . . . . . . . . . . . . . . . . . . . . . . . . . . . . . . . . 4-1
4.3 Operating Mode . . . . . . . . . . . . . . . . . . . . . . . . . . . . . . . . . . . . . . . . . . . . . 4-1
4.3.1 Auto Gas Mode . . . . . . . . . . . . . . . . . . . . . . . . . . . . . . . . . . . . . . . . . . .4-1
4.3.1.1 Program Select . . . . . . . . . . . . . . . . . . . . . . . . . . . . . . . . . . . . . . . 4-2
4.3.1.2 Gas Setpoints . . . . . . . . . . . . . . . . . . . . . . . . . . . . . . . . . . . . . . . . .4-2
4.3.1.3 Emission Setpoint . . . . . . . . . . . . . . . . . . . . . . . . . . . . . . . . . . . . . 4-2
4.3.1.4 Discharge Parameters . . . . . . . . . . . . . . . . . . . . . . . . . . . . . . . . . . .4-3
4.3.1.5 Enable . . . . . . . . . . . . . . . . . . . . . . . . . . . . . . . . . . . . . . . . . . . . . .4-3
4.3.1.6 Standby . . . . . . . . . . . . . . . . . . . . . . . . . . . . . . . . . . . . . . . . . . . . 4-4
4.3.1.7 Setpoint Adjustment . . . . . . . . . . . . . . . . . . . . . . . . . . . . . . . . . . . . 4-4
4.3.1.8 Scratchpad . . . . . . . . . . . . . . . . . . . . . . . . . . . . . . . . . . . . . . . . . . 4-4
4.3.1.9 Saving a program . . . . . . . . . . . . . . . . . . . . . . . . . . . . . . . . . . . . . .4-5
4.3.2 Gas Only Mode . . . . . . . . . . . . . . . . . . . . . . . . . . . . . . . . . . . . . . . . . . .4-6
4.3.2.1 Constant Current Mode . . . . . . . . . . . . . . . . . . . . . . . . . . . . . . . . . .4-6
4.3.2.2 Constant Voltage Mode . . . . . . . . . . . . . . . . . . . . . . . . . . . . . . . . . 4-8
4.3.3 Manual Gas Mode . . . . . . . . . . . . . . . . . . . . . . . . . . . . . . . . . . . . . . . . . . 4-9
4.4 Remote Enable/Standby . . . . . . . . . . . . . . . . . . . . . . . . . . . . . . . . . . . . . . . . 4-10
4.5 Open Filament . . . . . . . . . . . . . . . . . . . . . . . . . . . . . . . . . . . . . . . . . . . . . 4-10
4.6 Discharge Power Limit . . . . . . . . . . . . . . . . . . . . . . . . . . . . . . . . . . . . . . . 4-11
5. GENERAL OPERATION . . . . . . . . . . . . . . . . . . . . . . . . . . . . . . . . . . . . . . . . . 5-1
5.1 Description of Ion-Source/Controller Components . . . . . . . . . . . . . . . . . . . . . 5-1

II CONTENTS
_______________________________________________________________________
Copyright © 2010 by Kaufman & Robinson, Inc., 1306 Blue Spruce Drive, Unit A, Fort Collins, CO 80524
Tel: 970-495-0187, Fax: 970-484-9350, Internet: www.ionsources.com
6. REMOTE/AUTOMATED CONTROL . . . . . . . . . . . . . . . . . . . . . . . . . . . . . . . .6-1
6.1 Remote Control using the DB-25 Connector . . . . . . . . . . . . . . . . . . . . . . . . . . 6-1
6.1.1 Remote enable of the four stored programs using the
DB-25 Connector . . . . . . . . . . . . . . . . . . . . . . . . . . . . . . . . . . . . . . . . . 6-1
6.1.2 Remote Analog Setpoint Option on the DB-25 Connector . . . . . . . . . . 6-1
6.2 Remote Control Using the DB-37 Connector . . . . . . . . . . . . . . . . . . . . . . .6-4
6.2.1 Remote enable of the four stored programs using the
DB-37 Connector . . . . . . . . . . . . . . . . . . . . . . . . . . . . . . . . . . . . . . . . . .6-4
6.2.2 Remote Gas Channel Setpoint Description for the DB-37 Connector . 6-4
6.2.3 Remote Analog Setpoint Option on the DB-37 Connector . . . . . . . . . .6-5
6.2.4 Analog Outputs for the DB-37 Connector . . . . . . . . . . . . . . . . . . . . . . .6-6
6.2.5 Run Fault and Beam Good on the DB-37 Connector . . . . . . . . . . . . . .6-7
6.2.6 Description of the DB-37 pins . . . . . . . . . . . . . . . . . . . . . . . . . . . . . . . .6-8
6.3 Interlock . . . . . . . . . . . . . . . . . . . . . . . . . . . . . . . . . . . . . . . . . . . . . . . . . . . 6-11
6.4 RS-232 Serial Interface . . . . . . . . . . . . . . . . . . . . . . . . . . . . . . . . . . . . . . . . . .6-12
6.4.1 Interface cable . . . . . . . . . . . . . . . . . . . . . . . . . . . . . . . . . . . . . . . . . . . 6-11
6.4.2 Communication settings . . . . . . . . . . . . . . . . . . . . . . . . . . . . . . . . . . . 6-11
6.4.3 Communication overview . . . . . . . . . . . . . . . . . . . . . . . . . . . . . . . . . . 6-11
6.4.4 Commands, queries and responses . . . . . . . . . . . . . . . . . . . . . . . . . . 6-12
6.4.4.1 VRB - Verbose Command . . . . . . . . . . . . . . . . . . . . . . . . . . . . . 6-13
6.4.4.2 COM - Enable RS-232 Command or Status Query . . . . . . . . . . 6-14
6.4.4.3 *IDN? - Unit Identification Query . . . . . . . . . . . . . . . . . . . . . . . . 6-15
6.4.4.4 *RST – Reset Command . . . . . . . . . . . . . . . . . . . . . . . . . . . . . . 6-16
6.4.4.5 *TST? – Self Test Query . . . . . . . . . . . . . . . . . . . . . . . . . . . . . . 6-16
6.4.4.6 OUT - System Level Output Control Command or
Status Query . . . . . . . . . . . . . . . . . . . . . . . . . . . . . . . . . . . . . . . 6-16
6.4.4.7 MDE - Mode Set Command or Mode Query . . . . . . . . . . . . . . . 6-17
6.4.4.8 BEAM - Beam Good Query . . . . . . . . . . . . . . . . . . . . . . . . . . . . 6-18
6.4.4.9 P - Program Value Read/Write Command . . . . . . . . . . . . . . . . . 6-18
6.4.4.10 R - Monitor Command for Reading the Actual
Feedback Values . . . . . . . . . . . . . . . . . . . . . . . . . . . . . . . . . . .6-23
6.4.4.11 CFG? – Query current system configuration . . . . . . . . . . . . . . 6-23
6.4.4.12 LRN – Learn Command or Learn Query . . . . . . . . . . . . . . . . . .6-24
7. DIAGNOSTICS . . . . . . . . . . . . . . . . . . . . . . . . . . . . . . . . . . . . . . . . . . . . . . . . . . .7-1
7.1 Auto Controller . . . . . . . . . . . . . . . . . . . . . . . . . . . . . . . . . . . . . . . . . . . . . . .7-1
7.2 Filament Power Supply . . . . . . . . . . . . . . . . . . . . . . . . . . . . . . . . . . . . . . . . . . .7-5
7.3 Discharge Power Supply . . . . . . . . . . . . . . . . . . . . . . . . . . . . . . . . . . . . . . . . .7-6
8. LIMITED WARRANTY . . . . . . . . . . . . . . . . . . . . . . . . . . . . . . . . . . . . . . . . . . .9-1
9 SERVICE AND TECHNICAL INFORMATION . . . . . . . . . . . . . . . . . . . . . . . . 10-1

CONTENTS iiI
_______________________________________________________________________
Copyright © 2010 by Kaufman & Robinson, Inc., 1306 Blue Spruce Drive, Unit A, Fort Collins, CO 80524
Tel: 970-495-0187, Fax: 970-484-9350, Internet: www.ionsources.com
FIGURES
2-1 Front view of controller for End Hall ion source . . . . . . . . . . . . . . . . . . . . . .2-4
2-2 Rear view of controller for End Hall ion source . . . . . . . . . . . . . . . . . . . . . . 2-5
3-1 Front view of controller for End Hall ion source . . . . . . . . . . . . . . . . . . . . . . 3-6
3-2 Rear view of controller for End Hall ion source . . . . . . . . . . . . . . . . . . . . . . 3-7
5-1 Schematic block diagram of ion source and controller . . . . . . . . . . . . . . . . . 5-2
TABLES
2-1 Controller Specifications . . . . . . . . . . . . . . . . . . . . . . . . . . . . . . . . . . . . . . . .2-1
2-2 Controller Specifications . . . . . . . . . . . . . . . . . . . . . . . . . . . . . . . . . . . . . . . 2-3
3-1 Controller Inventory List . . . . . . . . . . . . . . . . . . . . . . . . . . . . . . . . . . . . . . . . 3-1
3-2 Input Power Requirements . . . . . . . . . . . . . . . . . . . . . . . . . . . . . . . . . . . . . 3-2
3-3 Pin descriptions for the rear panel DB-15 female MFC output connectors . .3-4
6-1 Pin descriptions for the female DB-25 connector on the Auto Controller . . . 6-2
6-2 Remote program selection using pins 16 and 34 on the DB-37 . . . . . . . . . . 6-4
6-3 Pin descriptions for the analog inputs on the DB-37 connector . . . . . . . . . . 6-6
6-4 Pin descriptions for the analog outputs on the DB-37 connector . . . . . . . . . .6-6
6-5 Run Fault and Beam Good pin descriptions . . . . . . . . . . . . . . . . . . . . . . . . . . . .6-7
6-6 Pin descriptions for the female DB-37 connector on the Auto Controller . . . 6-8
6-7 Interlock connections for the auto controller . . . . . . . . . . . . . . . . . . . . . . . . . . .6-11
7-1 Help codes and error messages for the auto controller . . . . . . . . . . . . . . . . 7-1
7-2 Help codes and error messages for the Filament Power Supply . . . . . . . . . 7-7
7-3 Help codes and error messages for the Discharge Power Supply . . . . . . . . 7-9

SAFETY 1-1
_______________________________________________________________________
Copyright © 2010 by Kaufman & Robinson, Inc., 1306 Blue Spruce Drive, Unit A, Fort Collins, CO 80524
Tel: 970-495-0187, Fax: 970-484-9350, Internet: www.ionsources.com
1 SAFETY
Caution: High Voltage. Only technically qualified personnel should install,
maintain, and troubleshoot the equipment described herein.
The Auto Controller and power supplies for the End Hall ion source must be
installed in a grounded 19-inch (483 mm) rack mount cabinet before opera-
tion.

GENERAL DESCRIPTION AND SPECIFICATIONS 2-1
_______________________________________________________________________
Copyright © 2010 by Kaufman & Robinson, Inc., 1306 Blue Spruce Drive, Unit A, Fort Collins, CO 80524
Tel: 970-495-0187, Fax: 970-484-9350, Internet: www.ionsources.com
2 GENERAL DESCRIPTION AND SPECIFICATIONS
The auto controller package combines modular power supplies and automatic con-
trol for operating an End-Hall ion source. The auto controller is designed for use in
a standard 19-inch (48 cm) rack mount cabinet. The Auto Controller, Filament Pow-
er Supply, Discharge Power Supply and Mass Flow Controller(s) are included in
the standard package along with the associated interconnection and power cables.
The operating specifications, weight and dimensions of each controller are outlined
in the following table.
This section gives a general overview of the Auto Controller package with more
detailed information in the later sections of this manual. Additional information on
each controller is given in the Appendix/Manual for each.
Table 2-1 Controller Specifications
Nominal
Input voltage
Maximum
Input
Current
Maximum
Output
Weight Height x
Depth
Auto
Controller
115 V, 1Φ, 50-60 Hz
208-230 V, 1Φ,
50-60 Hz
0.35 A
0.75 A
+/- 15 V,
500 mA DC
3.0 kg
(8 lbs)
4.4 x 53 cm
(1.75 x 21 in.)
Filament
Power
Supply
115 V, 1Φ, 50-60 Hz
208-230 V, 1Φ,
50-60 Hz
7.5 A
15 A
40 V,
25 A, AC
7.27 kg
(16 lbs)
4.5 x 53 cm
(1.75x 21in.)
Discharge
Power
Supply
115 V, 1Φ, 50-60 Hz
208-230 V, 1Φ,
50-60 Hz
15 A* ** 7.27 kg
(16 lbs)
4.5 x 53 cm
(1.75x 21in.)
* The discharge power supply output will be limited to 1500 watts when operation
with a nominal 115 volt ac input.
** The maximum output depends on the specific power supply ordered.

2-2 GENERAL DESCRIPTION AND SPECIFICATIONS
_______________________________________________________________________
Copyright © 2010 by Kaufman & Robinson, Inc., 1306 Blue Spruce Drive, Unit A, Fort Collins, CO 80524
Tel: 970-495-0187, Fax: 970-484-9350, Internet: www.ionsources.com
2.1 Auto Controller
The Auto Controller is designed to be installed in a standard 19 inch rack mount
cabinet and is shown in figures 2-1 and 2-2 along with the filament and dis-
charge power supplies. The controller communicates with the filament and dis-
charge power supplies through a RS-485 interface. A front panel switch allows
selection of either local or remote mode operation. The End Hall ion source can
be controlled from the front panels when local mode is selected. When remote
mode is selected, the End Hall ion source can be completely controlled via con-
nections to the rear panel. Alternately, programs selected from the front panel
can be enabled or disabled from the rear panel when remote mode is selected.
Sockets are installed on the rear panel for remote operation using either RS-
232 or an Analog interface.
The Auto Controller also interfaces with up to four mass flow controllers using
cables that connect to the rear panel. Four relay contacts are also available on
the rear panel if additional positive shut off valves are desired for the gas feed
system.
The Auto Controller is connected to the Filament Power Supply and the Dis-
charge Power supply through an RS 485 interface. When the RS-485 interface
is not connected the Auto Controller functions as a stand-alone power supply
and readout for four mass flow controllers.
2.2 Filament Power Supply
The Filament Power Supply is designed to be installed in a standard 19 inch
rack mount cabinet and is shown in figures 2-1 and 2-2 along with the Auto
Controller and Discharge Power Supply. The Filament Power Supply provides
voltage and current to the filament of the End-Hall ion source. This power sup-
ply communicates to the Auto Controller through a RS-485 interface.
Additional information can be found in the individual manual for the Filament
Power Supply.
2.3 Discharge Power Supply
The Discharge Power Supply is designed to be installed in a standard 19 inch
rack mount cabinet and is shown in figures 2-1 and 2-2 along with the Auto
Controller and Discharge Power Supply. The Discharge Power Supply pro-
vides voltage and current to the anode of the End-Hall ion source. This power
supply communicates to the Auto Controller through a RS-485 interface.

GENERAL DESCRIPTION AND SPECIFICATIONS 2-3
_______________________________________________________________________
Copyright © 2010 by Kaufman & Robinson, Inc., 1306 Blue Spruce Drive, Unit A, Fort Collins, CO 80524
Tel: 970-495-0187, Fax: 970-484-9350, Internet: www.ionsources.com
Additional information can be found in the individual manual for the Discharge
Power Supply.
2.4 Mass Flow Controller(s)
The mass flow controller or controllers are supplied when ordered as a com-
plete system. The controllers are connected to the gas feed for the ion sources
as close as possible to the gas feedthrough on the vacuum system. Up to four
mass flow controllers can be attached to the Auto Controller. The gas flows can
be set as a constant ratio or they can be set independently.
The Auto Controller can be used with a variety of mass flow controllers. How-
ever, the cables may vary depending on the mass flow controller provided in
the order. The pin descriptions for the female DB-15 connectors on the back of
the Auto Controller are given below in table 2-2.
Table 2-2. Pin descriptions for the DB-15 MFC connectors on the
Auto Controller.
Pin
number Description
1 Command Common. Return for 0-5 volt output to MFC on pin 8.
2 Mass flow read back from MFC. 0-5 volt signal from the MFC
referenced to pin 10.
3 No contact.
4 Valve off. Connected to common when MFC setpoint is set to
zero or when unit is in the standby mode, otherwise floated.
5 +15 volts DC for MFC supply voltage, referenced to pin 9.
6 - 15 volts DC for MFC supply voltage, referenced to pin 9.
7 No contact.
8 Setpoint out to MFC. 0-5 volts, referenced to pin 1.
9 Common for MFC supply voltages on pins 5 and 6.
10 Read back common. Reference for the 0-5 volt mass flow read-
back from the MFC on pin 2.
11 No contact.
12 No contact.
13 No contact.
14 Chassis ground
15 No contact.

GENERAL DESCRIPTION AND SPECIFICATIONS 2-4
2-4 GENERAL DESCRIPTION AND SPECIFICATIONS
_______________________________________________________________________
Copyright © 2010 by Kaufman & Robinson, Inc., 1306 Blue Spruce Drive, Unit A, Fort Collins, CO 80524
Tel: 970-495-0187, Fax: 970-484-9350, Internet: www.ionsources.com
Fig. 2-1. Front view of controller for End Hall ion source.

GENERAL DESCRIPTION AND SPECIFICATIONS 2-5
_______________________________________________________________________
Copyright © 2010 by Kaufman & Robinson, Inc., 1306 Blue Spruce Drive, Unit A, Fort Collins, CO 80524
Tel: 970-495-0187, Fax: 970-484-9350, Internet: www.ionsources.com
GENERAL DESCRIPTION AND SPECIFICATIONS 2-5
MFC
Cable
Auto
Controller Filament
Discharge
Operating
Cable Operating
Cable
Connections
RS-485
Cable
Input
Power
Ground
Connections
RS-232
Remote
iMII
Analog
Remote
KRI
Analog
Remote
Fig. 2-2. Rear view of controller for End Hall ion source.

INSTALLATION 3-1
_______________________________________________________________________
Copyright © 2010 by Kaufman & Robinson, Inc., 1306 Blue Spruce Drive, Unit A, Fort Collins, CO 80524
Tel: 970-495-0187, Fax: 970-484-9350, Internet: www.ionsources.com
3 INSTALLATION
This section describes how to install the Kaufman & Robinson, Inc., KRI® Control-
ler package for the filament cathode version of the End Hall Ion Source.
3.1 Unpack
Unpack the Controller package for the End Hall Ion Source. Prior to shipment,
the Controller was tested with the ion source to insure quality and verify the
standard range of operation. As soon as the Controller has been completely
removed from all packing materials, a visual inspection should be made to de-
termine if there has been any damage to the components during shipment. Use
the packing lists provided to confirm the completeness of order. If any damage
has occurred, contact Kaufman & Robinson, Inc., in addition to the shipping
company, to report the damage - see Section 8. Retain packaging materials for
any future shipments.
Table 3-1 is an inventory list for the controller package. The inventory list is for
the standard package so some items may or may not be included depending
on the particular order. For any questions or discrepancies concerning either
the inventory or shipping list, see Section 8 to contact Kaufman and Robinson,
Inc. Refer to Section 2 – General Description and Specifications for additional
information about the controller.
Table 3-1 Controller Inventory List
Quantity Description Part Number
1 Filament Power Supply FC 1000/Z or F 1006/Z
1 Power cable filament controller CBL-A07-PWR-HF-EH
1 Discharge Power Supply DC30010 or DC3005
1 Power cable, Discharge PS
6 m (20 ft) cable, 3 conductor
CBL-A08-PWR-DS-EH
(May vary)
1 Auto controller AC-01
1 Power cable, auto controller CBL-A01-PWR-GC
1 Mass flow controller MF-KRI-XXXX
(May vary)
1 Mass flow controller cable
6 m (20 ft) cable
CBL-BKS-GC
(May vary)
1 Operating cable,6 m (20 ft) cable CBL-A04-ATM-HF-EH
(May vary)
2 Interface cable, RS-485 (2 feet) CBL-IFC-485

3-2 INSTALLATION
_______________________________________________________________________
Copyright © 2010 by Kaufman & Robinson, Inc., 1306 Blue Spruce Drive, Unit A, Fort Collins, CO 80524
Tel: 970-495-0187, Fax: 970-484-9350, Internet: www.ionsources.com
3.2 Install in Rack Mount Cabinet
The Controller is designed to be mounted in a standard 19-inch (48 cm) rack
mount cabinet. To assure that the power cable that came with each controller
is connected to that controller, the power cables can be connected as each
controller is installed in the cabinet. Do not connect to input power before the
installation is complete. The input power requirements are given below in table
3-2. Universal single phase 50-60 Hz input power of 85 to 275 volts can be
used, so no modification is required to use either a nominal 115 or 208-230 volt
input.
Table 3-2. Input power requirements.
Module Nominal Input Voltage Maximum Input Current
Auto Controller 115 V, 1Φ, 50-60 Hz
208-230 V, 1Φ, 50-60 Hz
0.75 A
0.35 A
Filament Power Supply 115 V, 1Φ, 50-60 Hz
208-230 V, 1Φ50-60 Hz
15 A
7.5 A
Discharge Power Supply 115 V, 1Φ, 50-60 Hz*
208-230 V, 1Φ, 50-60 Hz
15 A*
15 A
* The discharge power supply output will be limited to 1500 watts when operat-
ing with a nominal 115 volt ac input.
The Auto Controller, Filament Power Supply and Discharge Power Supply
should be mounted one above the other in the cabinet. See Fig. 3-1 for the
relative locations of the individual rack mounted units. The wiring and cables
may not reach all the controller connections if installed in a different order.
3.3 Ground Connections
An earth ground connection is required for both safety and correct operation.
Earth ground should be connected to the vacuum chamber in which the ion
source is to be operated as well as the cabinet in which the Controller is in-
stalled. Make sure that these ground connections are made by qualified techni-
cal personnel. These ground connections are independent of the ground con-
nections described below in section 3.4.
3.4 Connections Between Controller Components
The connections between Controller components are shown in Fig. 3-2, which
shows the rear panels of the Discharge, Filament power supplies and Auto

INSTALLATION 3-3
_______________________________________________________________________
Copyright © 2010 by Kaufman & Robinson, Inc., 1306 Blue Spruce Drive, Unit A, Fort Collins, CO 80524
Tel: 970-495-0187, Fax: 970-484-9350, Internet: www.ionsources.com
Controller. The individual connections required are given below:
• If the 6 meter (20 ft.) input power supply cables were not connected to the
individual power supplies when they were installed in the cabinet, connect
them now. Use plugs that will match the input power sources. Again, do
not connect to Input Power before the installation is complete.
• Attach the 8 pin (male) plug connector of the 6 meter (20 feet) operating ca-
ble to the “Ion Source” socket connection on the rear panel of the Filament
Power Supply, refer to Fig. 3-2. Connect the opposite end to the exposed
connector on the electrical feedthrough.
• Insert the end of the operating cable BLUE wire into one of the (+) positive
connectors located on the rear panel of the Discharge Power Supply and
tighten the screw above the appropriate connector.
• Insert the end of the operating cable BLACK wire into one of the (-) nega-
tive connectors located on the rear panel of the Discharge Power Supply
and tighten the screw above the appropriate connector.
• Attach the ground connections using the green striped Yellow wire with the
three ring terminals as follows; Connect the green striped Yellow wire to
the ground on the cabinet chassis. Connect the three ring terminals to the
three ground studs on the Discharge Power Supply rear panel, the Filament
Power Supply rear panel and the Auto Controller rear panel. Tighten the
nuts on the ground studs. Connect the remaining green striped yellow wire
to the chassis system ground that the power supplies are installed in.
• Attach the two RS-485 cables to the connector labeled “RS-485 X 4” lo-
cated on the back panel of the Auto Controller as shown in figure 3-2. The
RS-485 connectors are not device specific, so they can be plugged into any
of the RS-485 connectors.
• Attach the other ends of the two RS-485 cables to the connectors labeled
“RS-485” located on the back panel, one for the Discharge and one for Fila-
ment Power Supplies as shown in figure 3-2.
• Attach the MFC cable to the connector labeled “MFC 1” located on the back
panel of the Auto Controller. Attach the other end to the MFC connector.
The pin descriptions for the DB-15 Female connectors is shown below in
table 3-3.
• Attach any additional MFC cables to the connectors labeled “MFC 2”, “MFC

3-4 INSTALLATION
_______________________________________________________________________
Copyright © 2010 by Kaufman & Robinson, Inc., 1306 Blue Spruce Drive, Unit A, Fort Collins, CO 80524
Tel: 970-495-0187, Fax: 970-484-9350, Internet: www.ionsources.com
3” and “MFC 4” located on the back panel of the Auto Controller. Attach the
other ends of these cables to the corresponding MFC’s.
• The mass flow controller is defined by the ion-source application. The gas
flow controller should be mounted as close as possible to the vacuum
chamber. See the MFC manual.
• There is a two pin interlock connector located on the back of the Auto
Controller. The unit comes supplied with a jumper installed in the interlock
connector. The Auto Controller disables the output of the filament and dis-
charge power supplies if this contact is open. If a system interlock is used, a
separate isolated contact should be connected to each interlock connector.
• If remote control of the auto controller is used, that cable can be attached at
this time to either the female DB-25 connector, the female DB-37 connec-
tor or the female DB-9 connector. These remote interfaces require knowl-
edge of the ion source operation, which is given in the next two sections
of this manual. The detailed descriptions for remote control are Section 6
REMOTE/AUTOMATED CONTROL of this manual.
• The connections between the pressure regulators and the flow controller
valves should be made with clean (passivated or hydrocarbon free) stain-
less-steel tubing, with all fittings properly installed. Plastic tubing should
not be used to avoid contamination of the gas.
Table 3-3. Pin descriptions for the rear panel DB-15 female MFC output con-
nectors.
Pin
Number
Description
1 Common for 0-5 volt setpoint.
2 0-5 V flow read back signal from MFC, referenced to pin 10.
3 Not used.
4 Valve off. Connected to common when the setpoint flow is set to zero or
when the Auto Controller is in Standby, otherwise floated.
5 +15 V, referenced to pin 9.
6 -15 V, referenced to pin 9.
7 Not used.
8 0-5 V setpoint out to MFC, referenced to pin 1.
9 Power common for ± 15 V.
10 Common for read back signal.
11 Not used.

INSTALLATION 3-5
_______________________________________________________________________
Copyright © 2010 by Kaufman & Robinson, Inc., 1306 Blue Spruce Drive, Unit A, Fort Collins, CO 80524
Tel: 970-495-0187, Fax: 970-484-9350, Internet: www.ionsources.com
Pin
Number
Description
12 Not used.
13 Not used.
14 Chassis Ground.
15 Not used.
3.5 Connect Controller to Ion Source
If the Ion Source has not been installed in the vacuum chamber, do so now,
using the Installation/Inspection description in the ion source manual. The ion
source installation procedures cover installation of the ion source, vacuum
cables, gas tubing inside the vacuum chamber, as well as electrical and gas
feedthroughs in the wall of the vacuum chamber. Once installed, connect the
operating cable to the electrical feedthrough.
• As the final installation step, turn off the front panel power switches on the
Auto Controller, Filament Power Supply and Discharge Power Supply and
then plug the power cables of the individual controllers into appropriate in-
put power sources. See table 3-1 above for input power requirements.

INSTALLATION 3-6
3-6 INSTALLATION
_______________________________________________________________________
Copyright © 2010 by Kaufman & Robinson, Inc., 1306 Blue Spruce Drive, Unit A, Fort Collins, CO 80524
Tel: 970-495-0187, Fax: 970-484-9350, Internet: www.ionsources.com
Fig. 3-1. Front view of controller for End-Hall ion source.

INSTALLATION 3-7
MFC
Cable
Auto
Controller Filament
Discharge
Operating
Cable Operating
Cable
Connections
RS-485
Cable
Input
Power
Ground
Connections
RS-232
Remote
iMII
Analog
Remote
KRI
Analog
Remote
INSTALLATION 3-7
_______________________________________________________________________
Copyright © 2010 by Kaufman & Robinson, Inc., 1306 Blue Spruce Drive, Unit A, Fort Collins, CO 80524
Tel: 970-495-0187, Fax: 970-484-9350, Internet: www.ionsources.com
Fig. 3-2. Rear view of controller for End-Hall ion source.

INITIAL OPERATION 4-1
_______________________________________________________________________
Copyright © 2010 by Kaufman & Robinson, Inc., 1306 Blue Spruce Drive, Unit A, Fort Collins, CO 80524
Tel: 970-495-0187, Fax: 970-484-9350, Internet: www.ionsources.com
4 INITIAL OPERATION
This initial operation is done locally from the front panel and serves to both demon-
strate and provide familiarization with operation. Make sure that the Auto controller
is switched to local mode. When using the gas only mode described below, the
filament and discharge power supplies must also be in the local mode. For a more
complete description refer to the Operation section, Section 5. The description in
this section assumes that the installation sequence described in Section 3 of this
manual and Section 2 in the ion source manual has been carried out.
4.1 Gas
High-purity (99.999+%) argon, oxygen or nitrogen gas can be used in the ion
source. For other process gases, please contact Kaufman & Robinson, Inc.
The bottle, regulator and mass flow controller(s) should be installed and gas
lines evacuated as described in Section 2.4.3 of the Ion Source manual.
4.2 Power On
Switch on the front panel power switches to the Discharge Supply, Filament
Supply, and the Auto Controller. These switches are the rocker type switches
located on the far left of the three panels.
4.3 Operating Mode
There are three selectable operating modes for the Auto Controller. These
three modes include Auto Gas, Manual Gas, and Gas Only. All three modes
can be selected using the white Operating Mode button on the front panel of
the auto controller. Auto Gas and Manual Gas modes are available only when
the Auto Controller has established communication with the filament and dis-
charge power supplies.
4.3.1 Auto Gas Mode
When using Auto Gas mode, the gas is automatically adjusted to maintain
constant discharge current and voltage once the ion source is running.
Check to see if the green Auto Gas LED indicator above the Operating
Mode button is on. If it is not, then continue to press and release the Oper-
ating Mode button until the green Auto Gas LED is on.

4-2 INITIAL OPERATION
_______________________________________________________________________
Copyright © 2010 by Kaufman & Robinson, Inc., 1306 Blue Spruce Drive, Unit A, Fort Collins, CO 80524
Tel: 970-495-0187, Fax: 970-484-9350, Internet: www.ionsources.com
4.3.1.1 Program Select
The Auto controller is shipped with four programs stored. Pressing and
releasing the white Program Select button will increment to the next
program as indicated by the numbered red LED’s on the left side of the
Program Select button. The program values will be displayed on the front
panels for each program. Program 1 may already be selected when the
unit is powered on, if it is not, then press and release the program select
button until the red LED for program 1 is on for the initial operation.
The other programs can still be viewed after the Auto Controller is
enabled with one of the programs running. When a program is running
and “Program Select” is pressed, the setpoint values of the next
program will be displayed for two seconds before switching to
that program. This gives time to review the programs before deciding
which one to run. Pressing again within two seconds moves to the next
program, etc. Cycling around to the program that’s currently running will
continue operation without change. Otherwise, the parameters will be
ramped to the newly selected program.
4.3.1.2 Gas Setpoints
There are four gas channels. Pressing and releasing the Gas Channel
Select button will increment to viewing the gas setpoint in sccm, for the
next gas channel for each program. In the Auto Gas mode, the gas is
automatically adjusted to maintain constant discharge current and
voltage once the ion source is running. The setpoints act as the starting
point from which the gas is adjusted. When more than one gas is blended
together, a constant ratio of the gas is adjusted based on the initial gas
setpoints to maintain the discharge voltage and current.
The gas flow may be adjusted by selecting the gas channel and turning
the knob on the front panel of the gas controller before the auto controller
is enabled. For the initial operation, leave the gas at the programmed
setpoint(s).
4.3.1.3 Emission Setpoint
The setpoint for the emission current in amps is shown in the display
labeled Emission Amps on the Filament Power supply. Notice that the
yellow setpoint LED below the display is on to indicate that the setpoint
is being viewed. Once the Auto Controller is enabled, the run value will
be displayed and the green run LED will be on.

INITIAL OPERATION 4-3
_______________________________________________________________________
Copyright © 2010 by Kaufman & Robinson, Inc., 1306 Blue Spruce Drive, Unit A, Fort Collins, CO 80524
Tel: 970-495-0187, Fax: 970-484-9350, Internet: www.ionsources.com
The emission setpoint can be adjusted by turning the Emission Adjust
knob on the front of the Filament Power Supply. This can only be
independently in the standby mode, but is also adjusted automatically
when adjusting the Discharge current. This maintains the same Emission
to Discharge current ratio. For the initial operation, leave the emission at
the program setpoint.
4.3.1.4 Discharge Parameters
The setpoints for the discharge voltage in volts and the discharge current
in amps are displayed on the front panel of the discharge power supply
in the displays labeled Discharge Volts and Discharge Amps. Notice
that the yellow setpoint LED below the display is on to indicate that the
setpoint is being viewed. Once the Auto Controller is enabled, the run
values will be displayed and the green run LED will be on.
The discharge voltage and current setpoints can be adjusted using the
Setpoint Adjust knob on the front of the discharge controller. These
adjustments can be made when the Auto Controller is in Standby or
Enable. The setpoint being adjusted by the knob is indicated by the
green LED’s on the front panel labeled Amps and Volts. These LED’s are
located above and below the white Select button on the front panel of the
discharge controller. Pressing and releasing the Select button will switch
the parameter being adjusted from Amps (discharge current) to Volts
(discharge voltage) or from Volts to Amps. For the initial operation, leave
the discharge voltage and current at the program setpoints.
4.3.1.5 Enable
Press and release the white Enable/Standby button on the front panel of
the Auto Controller. Notice that the yellow Standby LED under the button
turns off and the green Enable LED above the button turns on. The same
LED transition from Standby to enable also happens on the Filament
Power Supply and the Discharge Power Supply as the Auto Controller
sequences them on. Then the gas flow will be adjusted until the program
1 parameters are reached.
Note that the operating range of the ion source may be limited by the
vacuum facility pump speed or other process that take place while the
ion source is running.
This manual suits for next models
2
Table of contents
Popular Controllers manuals by other brands
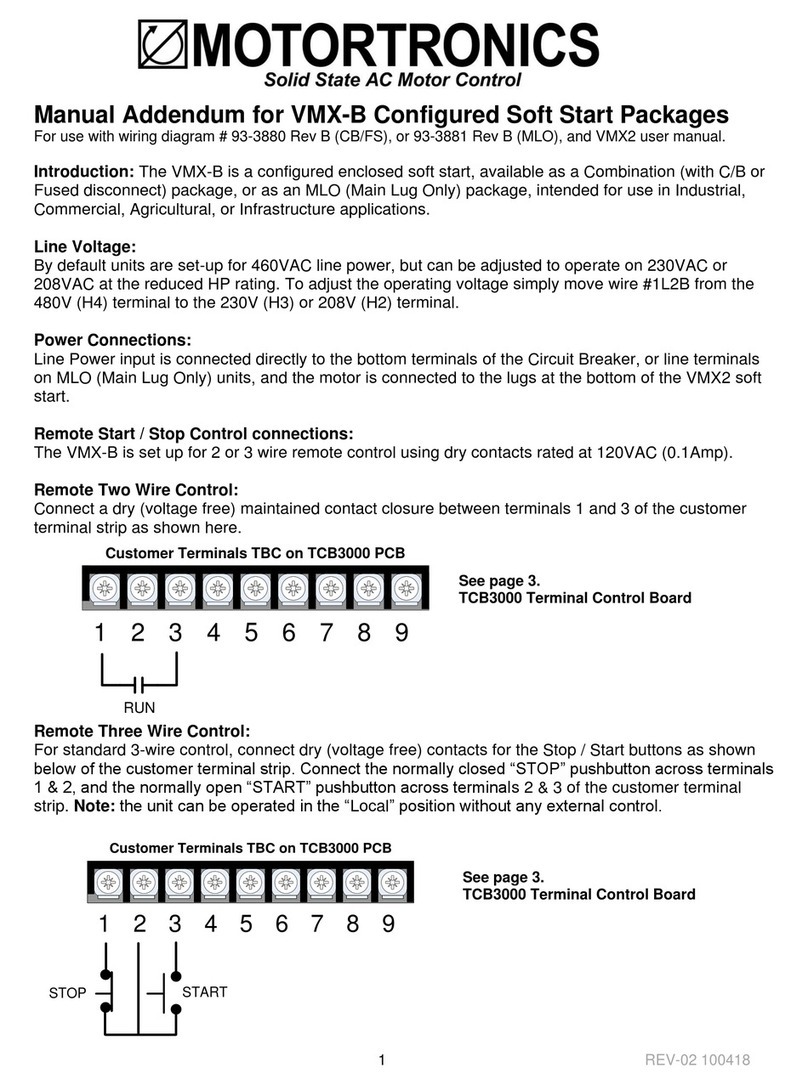
motortronics
motortronics VMX-B Soft Start Packages Manual addendum
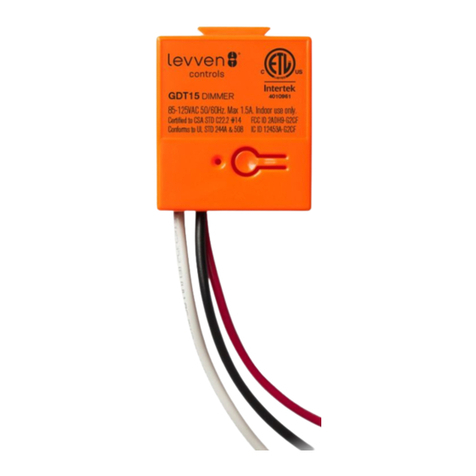
Levven
Levven GDT15 instruction sheet

Outback Power Systems
Outback Power Systems MX60 Installation and user manual
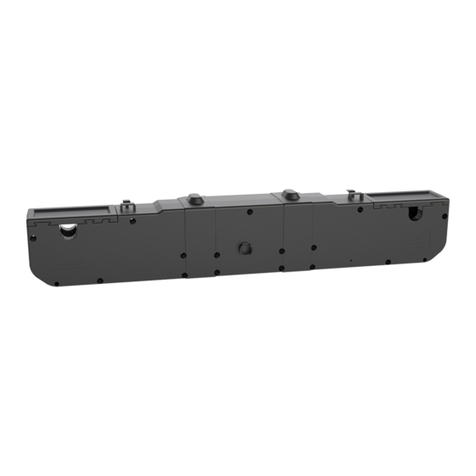
limoss
limoss MD200 Service instruction
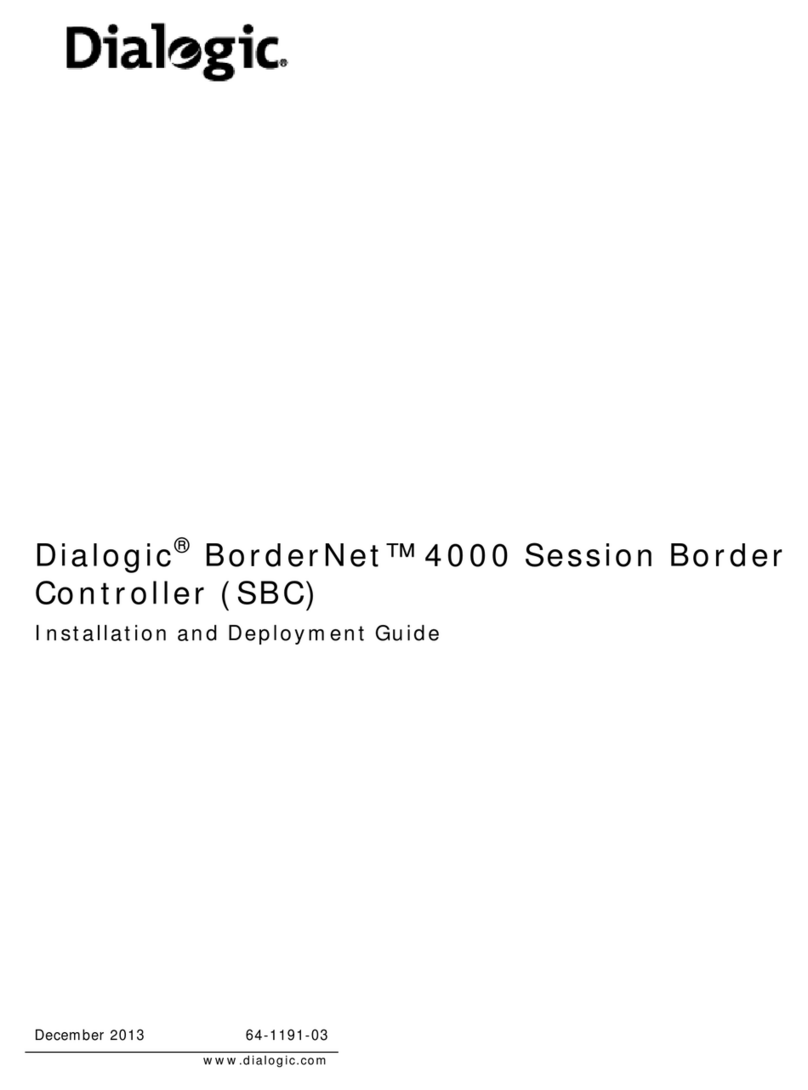
Dialogic
Dialogic 4000 Session installation guide
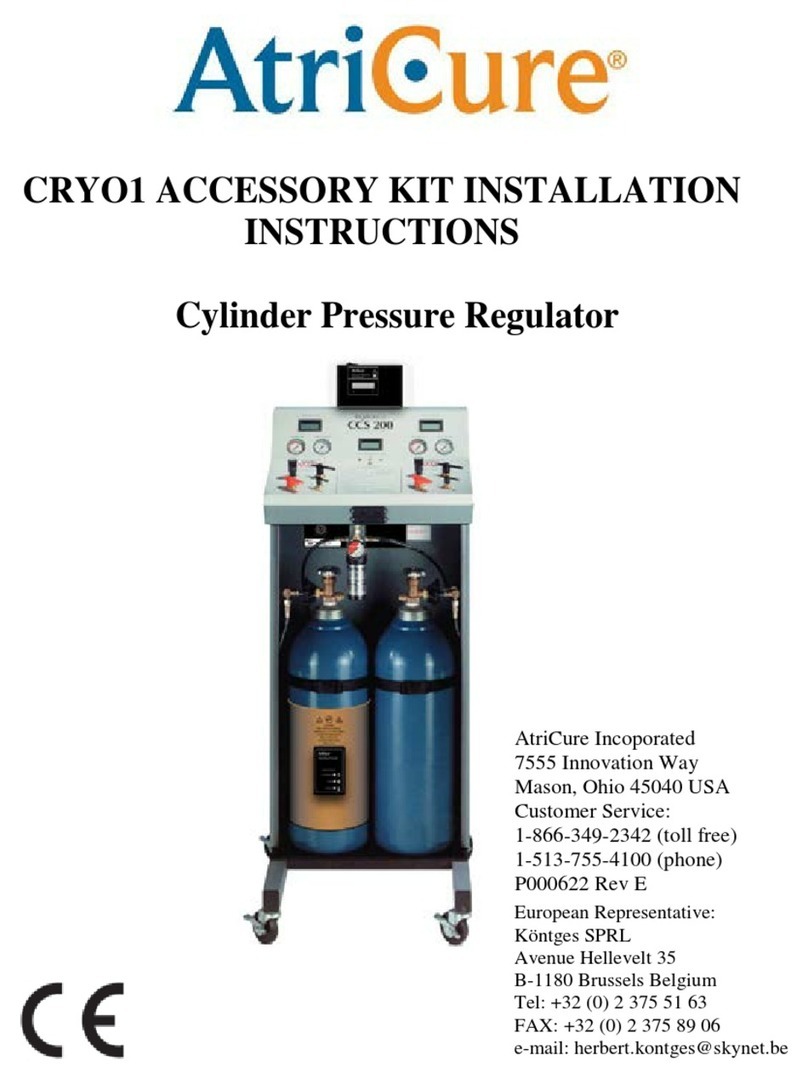
AtriCure
AtriCure CRYO1 installation instructions