Kentech Instruments J14080131 User manual

Kentech Instruments Ltd.
Two Channel Gated Optical Intensifier
Serial Number J14080131
Last Modified 5-2-15
PLEASE READ THIS MANUAL CAREFULLY BEFORE USING THE UNIT
Print in colour not in Black and White.
Hazard information is coloured RED
Kentech Instruments Ltd.,
Isis Building, Howbery Park, Wallingford, Oxfordshire, OX10 8BA, U.K.
Tel: +44 (0) 1491 82 1601

2
Kentech Instruments Ltd., Isis Building, Howbery Park, Wallingford, Oxfordshire, OX10 8BA, U.K.
Last Modied 5-2-15
Contents
1 DECLARATION OF CONFORMITY 5
2 DISCLAIMER 6
3 EMC CAUTION 6
4 MAGNETIC HAZARD 6
5 ABBREVIATIONS 7
6 INTRODUCTION 8
7 SPECIFICATIONS OF THE SYSTEM 8
7.1 TRIGGER MODULE .................................................................................................................... 8
7.2 DRIVER AND HEADS.................................................................................................................8
8 PRINCIPALS OF OPERATION 9
8.1 FAST AND MEDIUM MODES ....................................................................................................9
8.2 SLOW MODES .............................................................................................................................9
8.3 COHERENT LIGHT ILLUMINATION ....................................................................................... 9
9 POWER SUPPLY 9
10 CONNECTIONS AND MECHANICS 10
10.1 ATTACHING A HEAD TO THE CONTROL UNIT ..................................................................10
10.2 THE HEADS ............................................................................................................................... 12
10.3 ATTACHING EQUIPMENT TO A HEAD .................................................................................12
10.4 CONNECTING THE TRIGGER UNIT ...................................................................................... 13
10.5 POWERING UP THE SYSTEM .................................................................................................14
11 OPERATIONAL NOTES 14
11.1 TIMING .......................................................................................................................................14
11.2 DELAY ADJUSTMENT..............................................................................................................15
12 TESTS 15
12.1 STATIC TESTS. ..........................................................................................................................15
12.2 DYNAMIC TEST. ......................................................................................................................15
13 GOI SOFTWARE INTERFACE 18
13.1 REVISIONS.................................................................................................................................18
13.2 INTRODUCTION .......................................................................................................................18
13.3 DUAL CHANNEL SYSTEM......................................................................................................18
13.4 SYSTEM VARIABLES...............................................................................................................18
13.5 1.1 GOI MODES .........................................................................................................................18
13.5.1 INHIBIT MODE.................................................................................................................... 19
13.5.2 FAST MODE .........................................................................................................................19
13.5.3 SLOW MODE .......................................................................................................................19
13.5.4 DC MODE ............................................................................................................................. 20
13.6 TRIGGER ....................................................................................................................................20
13.7 OVERLOAD................................................................................................................................20
13.8 SELF TEST.................................................................................................................................. 20
13.9 DEFAULT SETTINGS ................................................................................................................21
13.10 ETHERNET INTERFACE ..........................................................................................................21
13.11 RS232 INTERFACE ....................................................................................................................24
13.11.1 THE PROTOCOL..................................................................................................................25
13.12 COMMANDS FOR CHANNEL 1 (A)........................................................................................ 26
13.13 COMMANDS FOR CHANNEL 2 (b).........................................................................................29

3
Kentech Instruments Ltd., Isis Building, Howbery Park, Wallingford, Oxfordshire, OX10 8BA, U.K.
Last Modied 5-2-15
13.14 COMMANDS WHICH ARE CHANNEL INDEPENDENT ...................................................... 32
13.15 EXAMPLE COMMS...................................................................................................................33
13.15.1 RANDOM EXAMPLES TO TRY FIRST............................................................................. 33
13.15.2 SETTING THE GOI UP IN DC MODE FROM A COLD START.......................................35
13.15.3 SETTING THE GOI UP IN FAST MODE FROM A COLD START.................................. 36
14 ELECTRICAL WAVE FORMS 37
15 OPTICAL GATE WAVEFORMS CHANNEL 1 (a) 39
16 OPTICAL GATE WAVEFORMS CHANNEL 2 (b) 45
17 TUBE DATA 51
Tables
Table 1 Tube data Channel 1/a.............................................................................................. 51
Table 2 Tube data Channel 2/b ............................................................................................. 53
Appendices
Appendix 1 Magnetic eld computed data and various limits .................................................... 56
Appendix 2 XML response.......................................................................................................... 57
Appendix 3 JSON response......................................................................................................... 61
Appendix 4 Operation without magnets in the head ................................................................... 62

4
Kentech Instruments Ltd., Isis Building, Howbery Park, Wallingford, Oxfordshire, OX10 8BA, U.K.
Last Modied 5-2-15
Figure Captions
Figure 1 Set up for testing the gating. .................................................................................... 15
Figure 2 Input window ........................................................................................................... 16
Figure 3 Output window......................................................................................................... 16
Figure 4 Example responses using POSTER with xml response........................................... 21
Figure 5 Example responses using POSTER with json response .......................................... 21
Figure 6 Changed variables XML .......................................................................................... 22
Figure 7 Changed Variables JSON......................................................................................... 22
Figure 8 Write to variables XML ........................................................................................... 23
Figure 9 Write to variables JSON........................................................................................... 23
Figure 10 Fast and medium gate waveforms............................................................................ 36
Figure 11 Medium gate waveforms.......................................................................................... 37
Figure 13 Ch1 Speed 0 Time right to left ~90 ps. ................................................................. 38
Figure 12 Ch1 Speed 1 Time right to left ~ 105ps ................................................................. 38
Figure 14 Ch1 Speed 2 Time right to left ~ 130ps ................................................................. 39
Figure 15 Ch1 Speed 3 Time right to left ~ 270ps ................................................................. 39
Figure 16 Ch1 Speed 4 Time right to left ~ 500ps. ................................................................ 40
Figure 17 Ch1 Speed 5 Time right to left ~ 1ns ..................................................................... 40
Figure 18 Ch1 Speed 6 Time right to left ~ 2ns. .................................................................... 41
Figure 19 Ch1 Speed 7 Time right to left ~3.5ns ................................................................... 41
Figure 20 Ch1 Speed 8 Time right to left ~ 4ns. .................................................................... 42
Figure 21 Ch1 Speed 9 Time right to left ~ 5ns ..................................................................... 42
Figure 22 Ch1 Slow gate Time right to left ~ 210ns. ............................................................. 43
Figure 23 Ch1 Shortest gate - digitised and normalised ......................................................... 43
Figure 24 Ch2 Speed 0 Time right to left ~90 ps. ................................................................. 44
Figure 25 Ch2 Speed 1 Time right to left ~90 ps. ................................................................. 44
Figure 26 Ch2 Speed 2 Time right to left ~90 ps. ................................................................. 45
Figure 27 Ch2 Speed 3 Time right to left ~90 ps. ................................................................. 45
Figure 28 Ch2 Speed 4 Time right to left ~90 ps. ................................................................. 46
Figure 29 Ch2 Speed 5 Time right to left ~90 ps. ................................................................. 46
Figure 31 Ch2 Speed 6 Time right to left ~90 ps. ................................................................. 47
Figure 32 Ch2 Speed 7 Time right to left ~90 ps. ................................................................. 47
Figure 33 Ch2 Speed 8 Time right to left ~90 ps. ................................................................. 48
Figure 34 Ch2 Speed 9 Time right to left ~90 ps. ................................................................. 48
Figure 35 Ch2 Slow gate Time right to left ~ 210ns. ............................................................. 49
Figure 36 Ch1 Shortest gate - digitised and normalised ......................................................... 49
Figure 37 Tube response........................................................................................................... 51
Figure 38 Tube response........................................................................................................... 53
Figure 39 Tube manufacturer’s instructions............................................................................. 54

5
Kentech Instruments Ltd., Isis Building, Howbery Park, Wallingford, Oxfordshire, OX10 8BA, U.K.
Last Modied 5-2-15
1
Declaration of Conformity
We:- Kentech Instruments Ltd
The Isis Building
Howbery Park
Wallingford
Oxfordshire OX10 8BA, UK
Certify that this apparatus:
Kentech Instruments Ltd.
Serial no: J1408131
Conforms with the requirements of European Community Directives:
2006/95/EC Low Voltage Directive
2004/108/EC EMC Directive
768/2008/EC CE Marking Directive
The following harmonized standards have been applied:
BS EN55011:2009 +A1:2010 Radio-Frequency
disturbance characteristics. Industrial, Scientific, Medical
equipment
96/211711 DC Electromagnetic compatibility. Generic
Immunity Standard.
Part 2 Industrial environment (EN 50082-2)
BS EN 61010-1:2010 Safety Requirements for Electrical
Equipment for Measurement, Control, and Laboratory Use
The following documents contain additional relevant information:-
Kentech file reference J1408131
Name: Signature:
A.K.L. Dymoke-Bradshaw
On behalf of Kentech Instruments Ltd
Position: Issued:
Director 5th. February 2015

6
Kentech Instruments Ltd., Isis Building, Howbery Park, Wallingford, Oxfordshire, OX10 8BA, U.K.
Last Modied 5-2-15
2 DISCLAIMER
There are high voltage power supplies (6kV) present in this instrument when the unit is operating. Do
not remove any covers from the GOI or expose any part of its circuitry. In the event of malfunction,
the GOI must be returned to Kentech Instruments Ltd. or its appointed agent for repair.
The accessible terminals of this instrument are protected from hazardous voltages by basic insulation
and protective grounding via the IEC power input connector. It is essential that the ground terminal
of this connector is earthed via the power lead to maintain this protection.
Kentech Instruments Ltd. accepts no responsibility for any electric shock or injury arising from
use or misuse of this product. It is the responsibility of the user to exercise care and common sense
with this highly versatile equipment.
Image intensier tubes are very delicate and very expensive and must be handled with great care
both in use and in storage. Read this manual before unpacking and using the instrument. Kentech
Instruments Ltd. accepts no responsibility for any damage to the intensier arising from misuse,
we offer the manufacturer’s warranty only on this component.
If cleaning is necessary this should be performed with a soft dry cloth or tissue only.
3 EMC CAUTION
This equipment includes circuits intentionally designed to generate short high energy electromagnetic
pulses and the EM emissions will be sensitive to the details of the experimental set up, particularly
in proximity to the cathode.
The emissions from this equipment should not exceed the limits specied in EN55011 “Emissions
Specication for Industrial, Scientic and Medical equipment” with the cathode and phosphor
windows covered with a conductive screen.
In practice with the user’s equipment in place and the conductive screens removed from cathode
and phosphor windows emissions may exceed E55011 and the unit may cause interference with
other equipment in its immediate environment. It is therefore suitable for use only in a laboratory
or a sealed electromagnetic environment, unless it is used in a system that has been veried by
the system builder to comply with EC directive 89/336/EEC. Use of this apparatus outside the
laboratory or sealed electromagnetic environment invalidates conformity with the EMC Directive
and could lead to prosecution.
4 MAGNETIC HAZARD
Each intensier head contains two strong neodymium large magnets. All normal care when working
with strong magnets should be employed. In particular:
1. If wearing a pacemaker keep the head at least 1 foot from your chest. Ideally get
someone else to do the work.
2. Be aware that the head will attract magnetic items. Be particularly careful of
normal tools and screws. Stainless steel screws are normally only slightly magnetic.
“Non-sparking” tools are also nearly non-magnetic. Non magnetic allen keys and
screwdrivers are readily available.
3. Do not place the head in a dusty environment that may contain magnetic particles.
4. If shipping the head be aware of various shipping regulations, particularly if it is
necessary to use air freight.

7
Kentech Instruments Ltd., Isis Building, Howbery Park, Wallingford, Oxfordshire, OX10 8BA, U.K.
Last Modied 5-2-15
5. If operating the head on a magnetic optical table be very careful moving it around and
always clamp it rmly.
5 ABBREVIATIONS
ASCII American Standard Code for Information Interchange
ADC or adc Analogue to Digital Convertor
AF Across Flats
CCD Charge Coupled Device (camera)
cr carriage return
EEPROM Electrically programmable and erasable Read only memory, non-volatile
EHT or eht Extra High Tension (high voltage)
EMC Electromagentic Compatibility
FO Fibre Optic
GXD Gated X-ray Detector
IEC International Electrotechnical Commission
JSON JavaScript Object Notation
lf Line Feed
MCP Micro Channel Plate
ND Neutral Density
PC Photo Cathode
PRF Pulse Repetition Frequency
PSU or psu power supply unit
SD Standard Deviation
sw software
URL Uniform Resource Locator
w.r.t. With Respect To
XML Extensible Markup Language

8
Kentech Instruments Ltd., Isis Building, Howbery Park, Wallingford, Oxfordshire, OX10 8BA, U.K.
Last Modied 5-2-15
6 INTRODUCTION
This manual describes the operation and use of a dual channel gated optical intensier system. The
intensiers can be gated over the range ~80ps to DC, over an 18mm diameter cathode aperture.
The image intensiers used in this system is very sensitive to light when active and easily damaged.
Before turning the unit on always check that the light levels to be used are appropriate.
The unit has four modes of operation: DC on, slow gate (10ns - 10µs), medium gate (300ps to
5ns) and fast gate (<100ps to 250ps) and may thus be used as a fast camera or as an ungated image
intensier. The wafer type design gives a large number of pixels across the full 18mm diameter
cathodes. The resolution is typically 10 1pmm-1. The system has a maximum PRF of 100Hz so
sampling/scanning operation is possible.
The cathode responds to 840nm light which allows easy setup with a laser diode (not supplied).
7 SPECIFICATIONS OF THE SYSTEM
7.1 TRIGGER MODULE
Number of channels 4
Output ~500 volts into 50 Ω on each of 4 channels.
Jitter SD <20ps , typical gures <4ps
Trigger requirements 5V into 50Ω with <5ns rise.
Power requirements 110/240 VAC <100W.
PRF 100Hz.
Dimensions 1U, 19inch x 400mm
7.2 DRIVER AND HEADS
Number of channels 2
Intensier type Photonis XK2050JE
18mm micro channel plate intensied wafer genII
S20 cathode on quartz input window
P43 phosphor on bre optic output.
MCP (gain) 260 through 925 volts mapped linearly to gain settings
of 0 through 1000 in steps of 1.
Phosphor voltage 6kV w.r.t. MCP output,
i.e. the absolute value wrt ground = 6kV + MCP out.
Gating times ≤100ps to 1ms but see gate proles in section 15 on
page 39
Spatial resolution 10 1pmm-1 typical
Power requirements 110/240 VAC <100W.
PRF 100Hz.
Trigger delay (typical)
Fast mode speed 0 54ns
Medium mode speed 3 65ns
Slow mode 104ns
Jitter SD <20ps , typical gures <4ps
Trigger requirements 500V into 50Ω with <1ns rise.
Length of umbilical nominally 3m
Dimensions 3U, 19inch x 500mm

9
Kentech Instruments Ltd., Isis Building, Howbery Park, Wallingford, Oxfordshire, OX10 8BA, U.K.
Last Modied 5-2-15
8 PRINCIPALS OF OPERATION
The camera is very simple in operation. It consists of a micro channel plate intensier tube congured
for the fast application of high voltage gate pulses to the cathode with a high voltage supply for
the tube bias voltages.
The tube is biased off by means of a small positive potential applied to the cathode with respect to
the channel plate input. A short duration negative pulse is applied to the cathode in order to gate
the camera on. There are two different mechanisms to apply this pulse, which is used depends on
the selected gating mode.
8.1 FAST AND MEDIUM MODES
The gating pulse is applied to the relatively high capacitance load presented by the cathode via
a ring electrode which is capacitively coupled to the cathode. The cathode forms the centre plate
in a capacitive divider. The capacitive load seen by the pulser is reduced at the expense of pulse
amplitude. The high voltage available from our fast pulse generators allows the voltage division
ratio to be >10:1 with a 1/10 reduction in the load seen by the driver. This allows the very fast gating
which is available with the GOI. The gate time is adjustable from <100ps to 5ns.
8.2 SLOW MODES
The gating pulse is conventionally driven by a suitable pulse applied directly to the cathode. The
gate time is adjustable from 100ns to 1ms.
8.3 COHERENT LIGHT ILLUMINATION
The high resolution and large cathode area result in a very large number of pixels in the gated
image. The input aperture to the intensier tube is clear and coherent light may be imaged onto the
cathode without the production of interference fringes. Some units use a gating mesh and are not
suitable for coherent light. This unit has no mesh.
9 POWER SUPPLY
The electronic package which drives the intensiers in the GOI is housed in one box. The box
contains four sections.
These are:
1. Low voltage power supply
2. Micro processor
3. High voltage pulse generators and delaying circuits.
4. High voltage tube bias supply
The system can be controlled remotely using RS232 connection on the rear panel or via the front
panel Ethernet connection. In this case it is more suitable to use a Labview driver. Without the
Labview driver the Ethernet can be used with “POST” and “GET” functions.
The following is relevant to each channel separately. Apart from a few commands the two channels
are completely independent. There is a trigger indicator light which shows when a trigger has been
received. There is an adjustable delay circuit which provides a total of ~50ns timing adjustment
in the trigger circuit. There is a second adjustable delay generator that controls the timing of the
“OFF” edge of the gate pulse in medium mode. In fast mode the gate width is only controlled by
the reverse bias applied to the cathode.

10
Kentech Instruments Ltd., Isis Building, Howbery Park, Wallingford, Oxfordshire, OX10 8BA, U.K.
Last Modied 5-2-15
The high voltage tube bias supply provides the static potentials required for the intensier tube.
The channel plate voltage is variable to adjust the intensier gain.
In DC mode the cathode is biased at approximately -50 volts with respect to the channel plate input.
The DC mode is only maintained for 5 seconds. After this it will switch off to protect the tube. The
intensier must not be left for a long time with a bright and damaging image on the phosphor. In
the slow gate mode the cathode is normally biased at approximately +50Volts with respect to the
channel plate input. The intensier is off in this state. At the application of a trigger signal to the
supply the cathode is pulsed to -50Volts, with respect to the channel plate input, for 100ns to 1ms,
turning the intensier on for this period.
In fast mode a variable positive bias is applied to the cathode with respect to the channel plate
input. This bias is overcome when the fast gate signal from the pulser is applied to the imager. The
bias is varied automatically by the microprocessor to give the correct gate time. Gate duration can
be selected from ~100ps to~ 5ns with one of 10 durations, see section 15 on page 39. The trigger
delay is different between fast mode and medium/slow mode, but note that different pulse generator
circuits are used for these modes and there can be some variation in the respective delays of the
order of 10ps as the unit warms up after switching modes. Note speeds 0,1,2 use a different set of
electronics from speeds 3 through 9. If changing from one set to another allow a little while for
temperature stabilisation if timing is critical.
The electrical delay in the GOI between the arrival of a trigger pulse at the front panel and the arrival
of the gate pulse at the cathode is shown in the specication see section 7 on page 8.
10 CONNECTIONS AND MECHANICS
The unit is supplied with the detection heads disconnected from the control unit.
These need to be connected before use.
The driver should not be switched on without the heads connected and the rear plastic
cover secured in place.
10.1 ATTACHING A HEAD TO THE CONTROL UNIT
1. Make sure there is no power connected to the control unit.
2. Remove the rear white plastic cover of the control unit
This needs the removal of ve M2.5 allen head screws. Tool 2mm AF.
3. The head labelled as Channel 1 must be connected to the channel one connections
on the rear of the control unit and Channel 2 to the channel 2 connections. Although
the heads may well work ne if switched, the software knows the maximum voltage
ratings of each tube and is set up not to exceed this for each tube. Similarly if more
than one system is available the heads should not be mixed up. The tube serial
numbers as well as the channel numbers are labelled both on the heads and on the rear
panel of the driver.

11
Kentech Instruments Ltd., Isis Building, Howbery Park, Wallingford, Oxfordshire, OX10 8BA, U.K.
Last Modied 5-2-15
4. If it is necessary to mix and match heads and control units please contact us and we
will arrange to have the control unit suitably programmed for a specic head.
5. Attach the bracket of the umbilical from the head to the upper square array of holes
shown. The screws needed should be stored in the holes. This may require the anti-
rotation collar on the umbilical to be moved to access the mount screws. If necessary
move it out the way and x it back afterwards. There is a clamp screw in the brass
piece.
6. Attach the 4 pin Fischer connector. Be careful to mate it with the correct orientation.
There are “half moon” pieces inside the connector that stop it being mated wrongly
but it is important not to damage these by trying the wrong orientation. There is also a
red dot on each piece; these should be aligned when mated.
7. Attach the two SMA connectors. They can t either jack on the bracket but should
be connected to the indicated (upper or lower) socket for each channel. If they are
switch around between upper and lower the gate pulse width, particularly on the
shortest gate may be different. Tighten the SMA connectors with a spanner 8mm or
5/16 inches, to a torque of 0.3 to 0.6 Nm. This is a little more than nger tight. Ideally
use a torque wrench. The jacks are tted to the bracket through an anti-rotation slot. It
is also advisable to inspect and clean out loose debris from the internal surfaces with
compressed air or a gas duster can before mating.

12
Kentech Instruments Ltd., Isis Building, Howbery Park, Wallingford, Oxfordshire, OX10 8BA, U.K.
Last Modied 5-2-15
8. Ret the plastic cover.
10.2 THE HEADS
The heads contain the intensiers which are fragile, mechanically, electrically and optically.
Appropriate care must be taken. In addition the head contains a pair of strong magnets. These
can cause the head to become attracted to the environment. Do not allow the head to slam into a
magnetic object. Do not allow magnetic objects to get accelerated towards the head. See section 4
on page 6 for safety considerations.
Make sure the head is well clamped in position before use.
10.3 ATTACHING EQUIPMENT TO A HEAD
If it is necessary to attach equipment to a head, several screw holes can be used. We recommend using
stainless steel screws as these have low magnetic susceptibility. If a normal magnetic screwdriver
is used, support the shaft as well as holding the handle to stop it being dragged towards the magnet.
On the front face are 6 M3 tapped holes at positions shown above. Screws may only protrude into
the head by 9 mm into these holes.
On the rear face are four holes on a 68 mm square. They are tapped M3 and screws can protrude
into them by 12mm but only 7mm is tapped.

13
Kentech Instruments Ltd., Isis Building, Howbery Park, Wallingford, Oxfordshire, OX10 8BA, U.K.
Last Modied 5-2-15
Holes on the sides are also tapped M3 and are available to a depth of 5mm.
10.4 CONNECTING THE TRIGGER UNIT
This 2 channel unit has a separate 4 channel trigger unit. This supplies 4 synchronous high voltage
trigger pulses, one to each of up to 4 channels. By using high voltage trigger signals the channel
to channel jitter can be kept very low. Typical SD between channel down to <2ps can be achieved.
The trigger unit should be connected to the driver unit with suitable BNC cables, (four 1m cables
are supplied). The cables should not degrade the fast (sub ns rise time) trigger pulse that the trigger
unit delivers. If long cable runs are needed then the cable quality may need to be upgraded.

14
Kentech Instruments Ltd., Isis Building, Howbery Park, Wallingford, Oxfordshire, OX10 8BA, U.K.
Last Modied 5-2-15
10.5 POWERING UP THE SYSTEM
Do not apply power unless both heads and the rear plastic cover are in place.
Applying power and switching on the control unit will not turn on an intensier. An intensier can
only be turned on under software control via either the RS232 connection at the rear panel or the
Ethernet connection at the front panel.
Read section 13 on page 18 about how to control the system.
Before an intensier is powered up, the photocathode input should be shielded from any ambient
light. A large signal on an imager output phosphor will reduce the life of the imager and could even
result in permanent damage.
Set the gain control set to minimum before turning on an intensier. If a DC image is required for
setting up then it should be kept as dim as possible and the duration should be as short as possible.
The image should only be sufciently bright to see in a dimly lit room. The DC mode can only be
enabled for 5 seconds. After this it will be necessary to re-enable the mode. Start at minimum gain
and work up to a reasonable level. A safer alternative to using the DC mode is to use the slow gate
mode. The user may set a gate duration of 100ns to 1ms and apply gate pulses to the trigger input
at the rate of 100 Hz. Starting with the gain at minimum set the gate mode control to slow gate and
look for a pulsed image on the phosphor. In this mode the imager is much safer in the presence of
excessive illumination.
Ensure that no excessive force is applied to the phosphor breoptic as this may damage the tube.
If using a bre optic coupled device on the rear of the intensier, make sure it is lightly sprung onto
the output face. Do not clamp a FO device hard onto the output face. The output face may be slightly
at an angle to the tube axis, this is a tube manufacturing issue and sometimes cannot be avoided.
The imager is most conveniently characterised by the use of a laser diode pulser. The cathode will
respond to 840nm or shorter wavelength light, see gure Figure 37 on page 52. The user will require
a pulse generator, a delay unit and a short pulse laser diode pulser in addition to the standard
components supplied with the imager.
The imager may be triggered at up to 100Hz. The image may be seen by eye on the phosphor if a
sufciently powerful laser diode is used. As a guide a diode producing 100mW with a pulse width
of 80ps and a wavelength of <840nm is adequate to illuminate the whole of a cathode at a level
which can be observed on the phosphor in a dimly lit room. In normal operation the camera will
only be triggered once per image. The user will be able to see a single exposure in a darkened room
and this exposure level will be captured easily by a well coupled scientic CCD camera.
11 OPERATIONAL NOTES
11.1 TIMING
Timing the imager is particularly critical when a single shot exposure is required such as in a laser
produced plasma experiment. The rst requirement is a trigger signal of stable timing (to within less
than the gate window) and stable amplitude. Since the trigger circuits integrate the trigger signal
for the rst nanosecond or two a varying amplitude will cause a timing change.
A second requirement may be a stable delay generator, ideally a passive switched cable network,
to set the timing. The unit has a built in 50 ns system of this type. A further highly desirable aid is
an optical ducial signal of suitable wavelength.
The delay between initial trigger at the front panel and the gate pulse getting to the intensier is
shown in the specications, see section 7 on page 8. The camera could be triggered from the signal

15
Kentech Instruments Ltd., Isis Building, Howbery Park, Wallingford, Oxfordshire, OX10 8BA, U.K.
Last Modied 5-2-15
it is detecting if a suitable optical delay can be introduced after the trigger signal generator (which
is probably a photodiode). This could be accomplished by means of bre optics or by relaying the
image via several lenses over a suitable distance. Ensure that the cables take the most direct path
to the camera so that they do not contribute to the trigger delay.
This scheme would be most suitable if there is no reliable pre-trigger available (for example in an
electrical discharge machine).
There is no timing monitor output on this unit. A simple way to derive an accurate timing signal
is to place a scope probe near the input to the intensier. This will pick up the gate signal and is a
very accurate indicator of the gate timing.
11.2 DELAY ADJUSTMENT.
The delay adjustment gives approximately 50ns of adjustment in approximately 25ps steps.
THIS IS NOT A PRECISION DELAY AND SHOULD NOT BE USED AS A
CALIBRATED TIME REFERENCE
but it is a very stable delay as it is based on passive delay lines switched with relays. If a longer
inter-fame time is required then the cable between the trigger unit and the driver input can be
lengthened but make sure the pulse is not signicantly degraded.
12 TESTS
12.1 STATIC TESTS.
The gated imager should be set up with a target resolution grid imaged onto the cathode.Acontrolled
and uniform light source should be used to backlight the target. This may be a variable output
microscope lamp with a diffuser and ND lters over the front. All other light sources should be
excluded from the input by using a black tube.
A microscope should be set up to view the output. This can be an objective lens mounted close to
the output. Take care not to scratch the bre optic window. Fibre optic face windows are made of
soft glass and the surface is in the image plane so any surface defects will appear on the image.
Only use lens tissues or other lens cleaning materials to clean the input and output faces.
In a dimly lit room (i.e. just enough light to manoeuvre after ones eyes have adjusted to the low
light level) turn on the imager and set the gain set to 350V. Activate the DC mode and gradually turn
up the lamp until a dim image is seen. Then turn up the gain in steps of 10 until a relatively bright
image of the resolution mask is present on the output. Note that the DC mode only remains active
for 5 seconds from receipt of a DC mode command but it can be repeatedly enabled and can be
enabled before the previous 5 seconds has elapsed to maintain the DC mode. Be very careful if doing
this. The whole point of the 5 second limit is to protect the tube from accidental over illumination.
Ensure that the imager is able to resolve lines separated by at most 100µm. Turn the gated imager
off and remove the microscope. Set the imager to SLOW GATE mode with the slow gate duration
set to 10µs. While triggering the power supply at a ~ 100Hz turn up the gain until a pulsed image
is seen on the phosphor.
12.2 DYNAMIC TEST.
For this test a short pulse light source is required. A laser diode is most convenient although a single
pulse mode locked laser can be used. The source should have a wavelength >200nm to ≤ 840nm
and should produce ~ 108 photons per pulse. A >100mW peak power laser diode with a ≤ 60ps
pulse duration is suitable. In both cases a pre-trigger signal is required with a lead time ~50ns. It

16
Kentech Instruments Ltd., Isis Building, Howbery Park, Wallingford, Oxfordshire, OX10 8BA, U.K.
Last Modied 5-2-15
should satisfy the trigger requirements in the specication. A switched cable delay generator and
a ne delay will also be required. For ne delays one can move the light source w.r.t. the detector
(if the bean is collimated) or use a variable length transmission line on the trigger signal or some
other system such a sampling system. In some sampling systems the delay is measured after the
event and the position of the sample moved accordingly.
Be sure to use the appropriate laser safety goggles.
Connect up the pulser, trigger source and delay lines as shown.
Figure 1 Set up for testing the gating.
The camera should be removed from the imager. The light source ideally will run at a repetition rate
from single shot to 100Hz. Set up the source to run at 100Hz with the power level on the cathode
at a minimum.
The laser should be set up to illuminate uniformly the input with a resolution mask in place as in
the previous test. Take care that the power level is not so great as to burn the cathode. This is not a
danger when using a laser diode. All other light sources should be excluded from the input.
In a dimly lit room turn on the imager in DC mode with the MCP set to about 350V. Activate the
DC mode and turn up the source brightness until a dim image is seen. Increase the MCP voltage in
steps of 10 until a relatively bright image of the resolution mask should be present on the output.
This establishes a reasonable exposure level for the test.
Initially the longest gate pulse duration should be used. Set up the imager as shown. Check that
the pulser is being triggered. In a dimly lit room turn on the imager and pulser and with the source
intensity and gain setting as in the previous section and scan the delay until an image is present.
Observe the effect of increasing and decreasing the delay and nd a delay setting that positions the
light pulse at the start of the cathode gate prole. Once this setting has been established, the gate
width can be progressively reduced, but note the changes in trigger delay for the different modes.
The gate window may now be measured either by monitoring the output intensity with a CCD or
a photodiode. The most convenient way to obtain the gate time is with a photodiode monitoring
the output signal and plotting the output intensity while stepping the delay. The source and camera

17
Kentech Instruments Ltd., Isis Building, Howbery Park, Wallingford, Oxfordshire, OX10 8BA, U.K.
Last Modied 5-2-15
must be triggered at a sufcient rate that a quasi DC signal can be obtained by integrating the diode
output. This rate is typically 1kHz so some kind of averaging may be needed to do this at 100Hz. A
sampling time base may be used as a delay generator and the photodiode output displayed directly
on the scope. By this means a rapid record of the gate prole can be obtained.
It should be established that the imager is being reliably triggered. This is most readily achieved by
triggering the imager at a few hertz and looking to see if the image is stable. If there is jitter then the
brightness of the image will vary from shot to shot. This test is most sensitive if the timing is set such
that the image is approximately 50% of peak brightness, i.e. the source is changing most rapidly.
Figure 2 Input window
Figure 3 Output window

18
Kentech Instruments Ltd., Isis Building, Howbery Park, Wallingford, Oxfordshire, OX10 8BA, U.K.
Last Modied 5-2-15
13 GOI SOFTWARE INTERFACE
13.1 REVISIONS
0.0 21 Jan 2015
13.2 INTRODUCTION
This document describes the GOI software interface supplied.
The GOI has both an Ethernet and an RS232 interface. The instrument cab be controlled from either
of these interfaces. To prevent conict between them only one should be used for control, i.e. to
change the various parameters. It is possible to use the non control port to monitor the instrument.
13.3 DUAL CHANNEL SYSTEM
The following describes control of channel 2 (also called channel b). The commands all start with
the letter “b”. Commands for channel 1 (also called channel a) are identical except that the leading
“b” should be replaced with an “a”.
13.4 SYSTEM VARIABLES
The GOI is controlled and monitored by reading from and writing values to a set of system variables.
These variables are:-
Channel 1(a) variables:
a_fast_width
a_ovld_ag
a_trig_ag
a_slow_width
a_mcp_gain
a_fast_mode
a_goi_mode
a_trig_delay
a_dc_on
a_status
Channel 2(b) variables:
b_fast_width
b_ovld_ag
b_trig_ag
b_slow_width
b_mcp_gain
b_fast_mode
b_goi_mode
b_trig_delay
b_dc_on
b_status
13.5 1.1 GOI MODES
The GOI has 4 primary operating modes, INHIBIT, FAST, SLOW and DC. Note that the “medium”
mode is not distinguished in software.
The primary operating mode is determined by the value in the variable b_goi_mode.
0 = Inhibit

19
Kentech Instruments Ltd., Isis Building, Howbery Park, Wallingford, Oxfordshire, OX10 8BA, U.K.
Last Modied 5-2-15
1 = Fast
2 = Slow
3= DC
[Internally the unit splits the fast mode into fast and medium and this is displayed on the front panel.]
The current operating mode can be determined by reading [for channel 1(a)] a_goi_mode.
The operating mode can be changed by writing 0 through 3 to a_goi_mode.
The mode is also indicated by the front panel LEDs.
13.5.1 INHIBIT MODE
In INHIBIT mode the tube is not gated and there should be no image as the fast and slow pulsers
are disabled and the photocathode is reverse biased.
13.5.2 FAST MODE
In FAST mode the fast pulser is enabled and a high voltage pulse is capacitively coupled onto the
photocathode to give an optical gate in the range 80 ps to 5 ns. The slow pulser is disabled.
The length of the optical gate is determined by the value in [for channel 2(b)] b_fast_mode.
0 = 80 ps
1 = 100 ps
2 = 120 ps
3 = 250 ps
4 = 500 ps
5 =1000 ps
6 = 2000 ps
7 = 3000 ps
8 = 4000 ps
9 = 5000 ps
The current fast mode gate width can be read from b_fast_mode.
The fast mode gate width can be changed by writing 0 though 9 to b_fast_mode.
The nominal fast mode gate width in ps can be read from the variable b_fast_width.
Writing values to b_fast_width has no effect.
There are in fact two different pulsers used for fast mode. Fast mode settings 0 though 2 uses the
fastest pulser and the FAST led will be illuminated. Fast mode settings 3 though 9 use the longer
gate pulser and the MEDIUM led will be illuminated.
13.5.3 SLOW MODE
In SLOW mode the fast pulser is disabled and the slow pulser is enabled, driving the cathode directly
and producing gate widths in the range 100 ns to 1 ms.
The current slow gate width in ns can be read from [for channel 2(b)] b_slow_width.
The slow gate width can be changed by writing the desired gate width in ns to b_slow_width.
In SLOW mode the slow LED is illuminated.

20
Kentech Instruments Ltd., Isis Building, Howbery Park, Wallingford, Oxfordshire, OX10 8BA, U.K.
Last Modied 5-2-15
13.5.4 DC MODE
In DC mode, the GOI can be made to switch the intensier tube on to produce a DC image for
approximately 5 seconds. This is done by writing 1 or -1 to [for channel 1(a)] a_dc_on.
This has no effect if the GOI is not in DC mode.
Whether or not the intensier is on DC can be determined by reading a_dc_on.
1 = dc on
0 = off
The 5 seconds can be extended by re-writing to b_dc_on before the initial 5 seconds has expired.
This will cause the DC mode to be maintained by 5 seconds from the last write time.
13.6 TRIGGER
The trigger delay can be varied by up to 55 ns in 25 ps steps.
The current trigger delay in ps can be read from [for channel 2(b)] b_trig_delay.
The trigger delay can be changed by writing the desired delay in ps to b_trig_delay.
An incoming trigger edge will ash the triggered light on the front panel. It will also set the trigger
latch.
The state of the trigger latch can be read from b_trig_ag.
1 = triggered
0 = not triggered
The trigger latch can be reset by writing 0 to b_trig_ag.
13.7 OVERLOAD
A high level of phosphor current due to an overbright image or hardware fault will trip the overload
latch. This is indicated by the overload LED on the front panel. If the overload latch is tripped, the
MCP power supply is disabled and there will be no image.
The state of the overload latch can be read from [for channel 2(b)] b_ovld_ag
1 = overload
0 = normal
The overload latch can be reset by writing 0 to b_ovld_ag.
When the overload latch is reset the unit will restore the previous settings and be enabled. If the
fault has not been corrected the latch will be set again.
13.8 SELF TEST
On power up or reset the GOI performs a self test of the high voltage switching circuits. If this
test fails, the high voltage power supply will not be enabled and there will be no image. It is not
possible to clear the self test fail condition other than by rerunning the test by cycling the power.
The results of the self test can be read from [for channel 2(b)] b_status
0 = normal
non zero = self test fail
Table of contents
Other Kentech Instruments Inverter manuals
Popular Inverter manuals by other brands
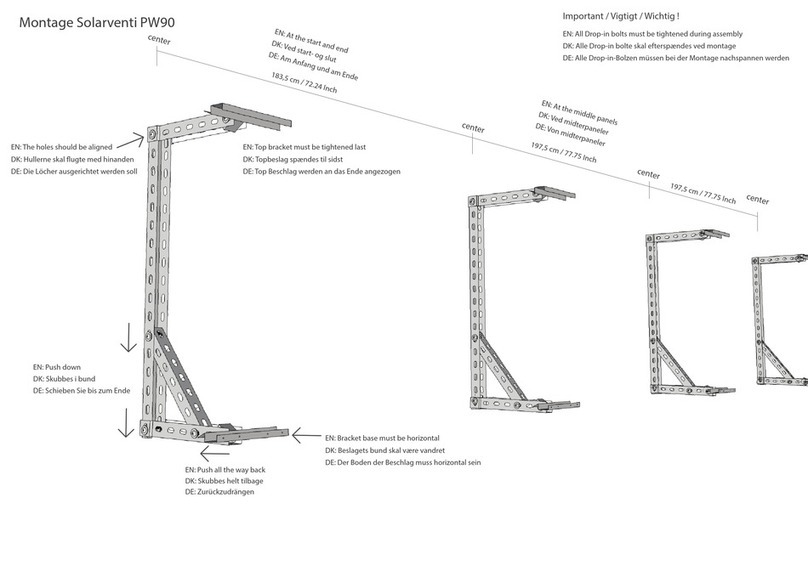
SolarVenti
SolarVenti PW90 Assembly instructions
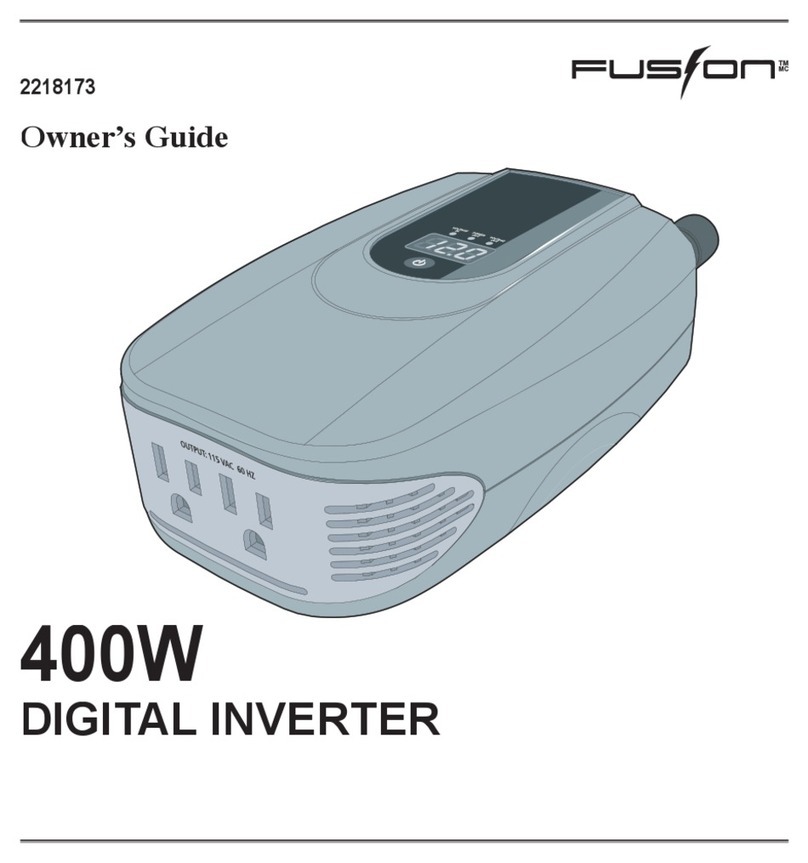
Fusion
Fusion 2218173 owner's guide
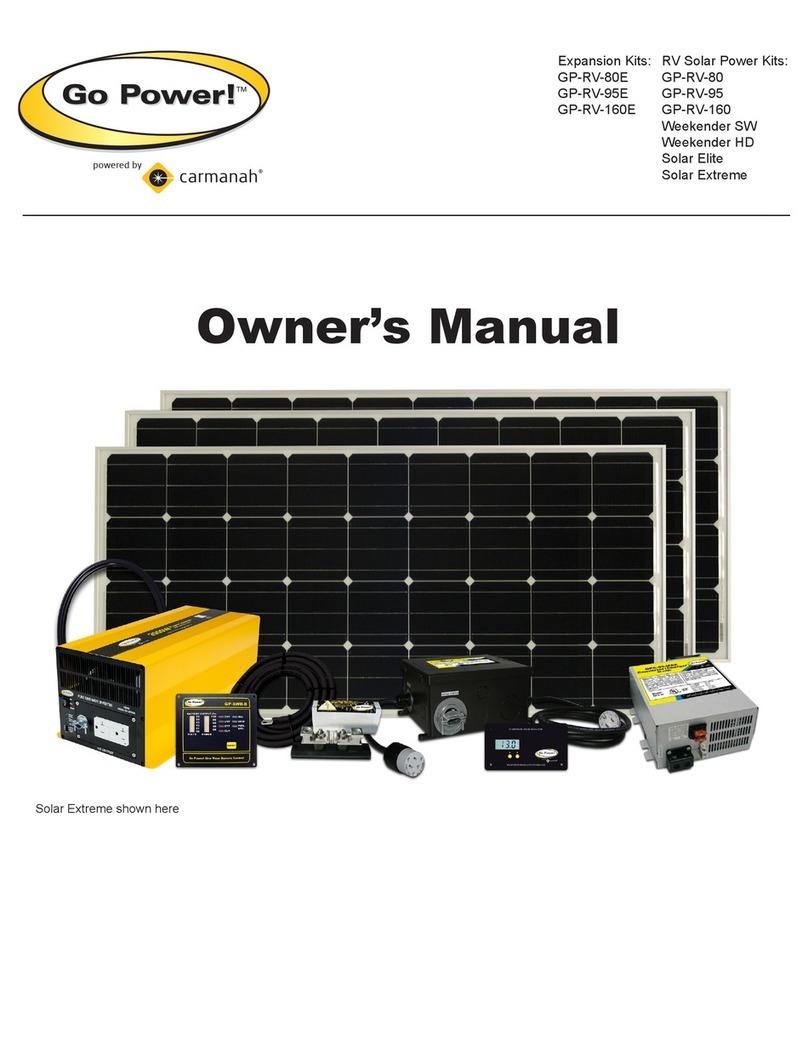
Carmanah
Carmanah Go Power! GP-RV-80E owner's manual
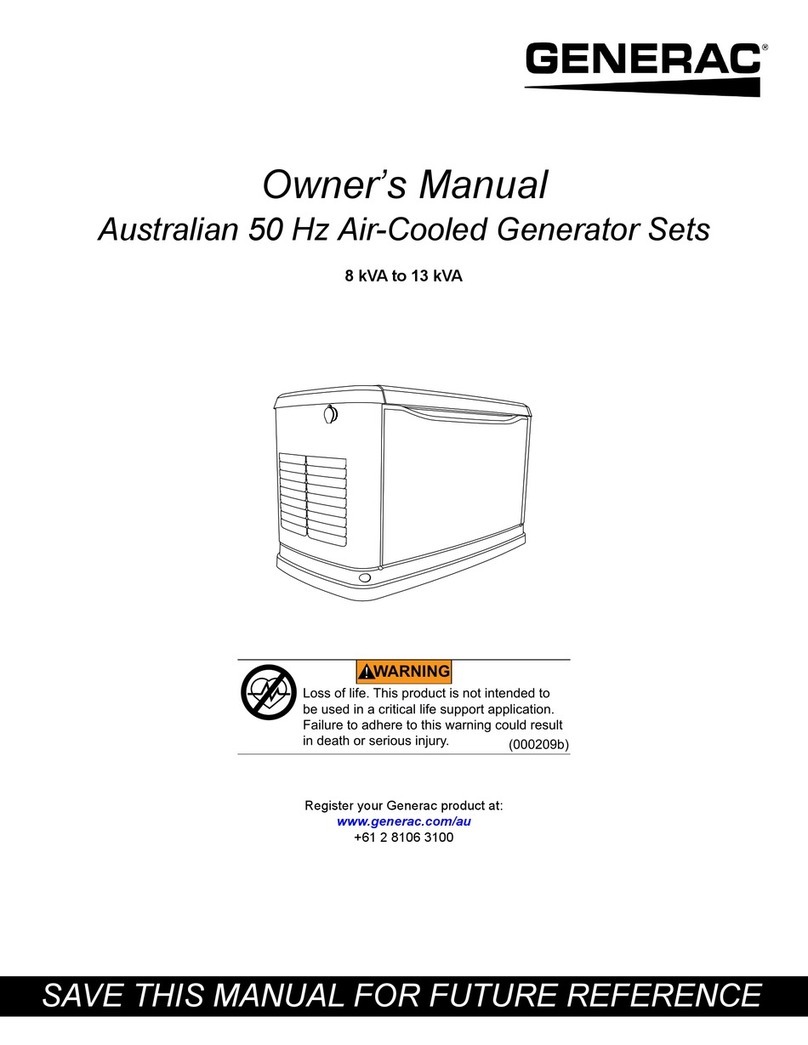
Generac Power Systems
Generac Power Systems 8 KVA owner's manual
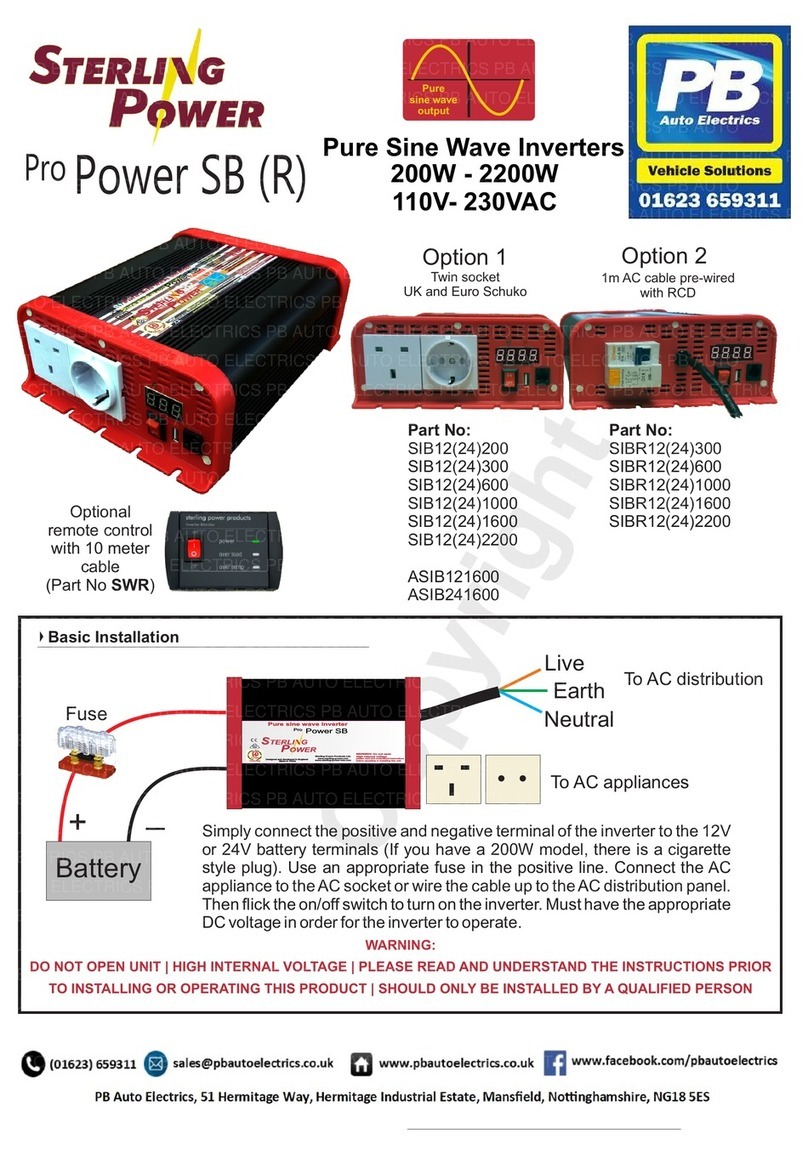
Sterling Power
Sterling Power Pro Power SB quick guide
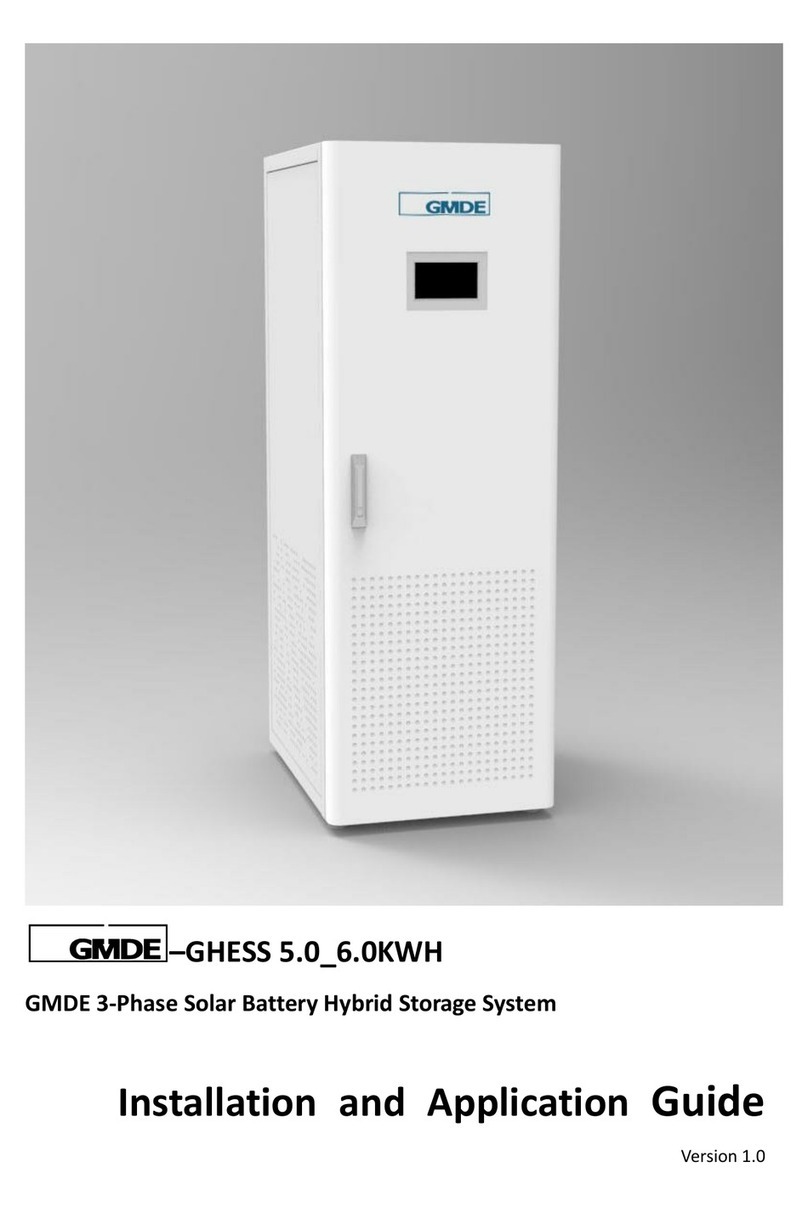
GMDE
GMDE GHESS 5.0_6.0KWH Installation and application manual
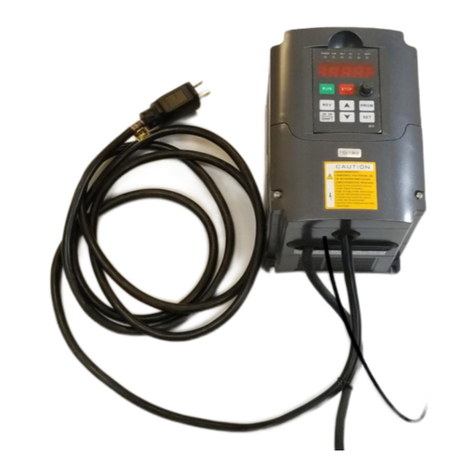
Next Wave CNC
Next Wave CNC SHARK manual
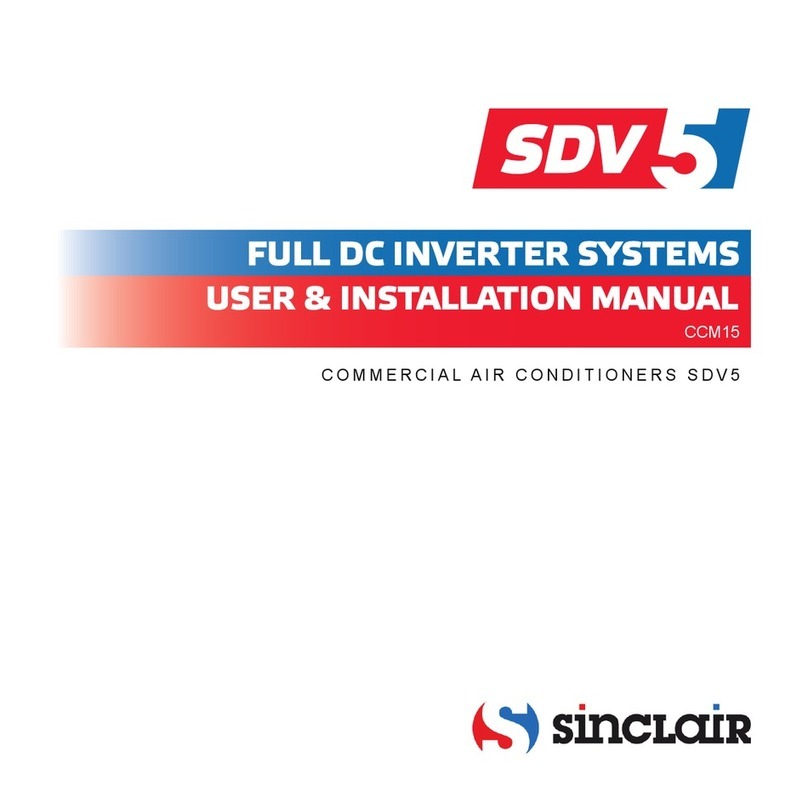
Sinclair
Sinclair SDV5 Series User & installation manual

LIFAN Power USA
LIFAN Power USA Energy Storm ESI-860i-CA Operating instructions and owner's manual
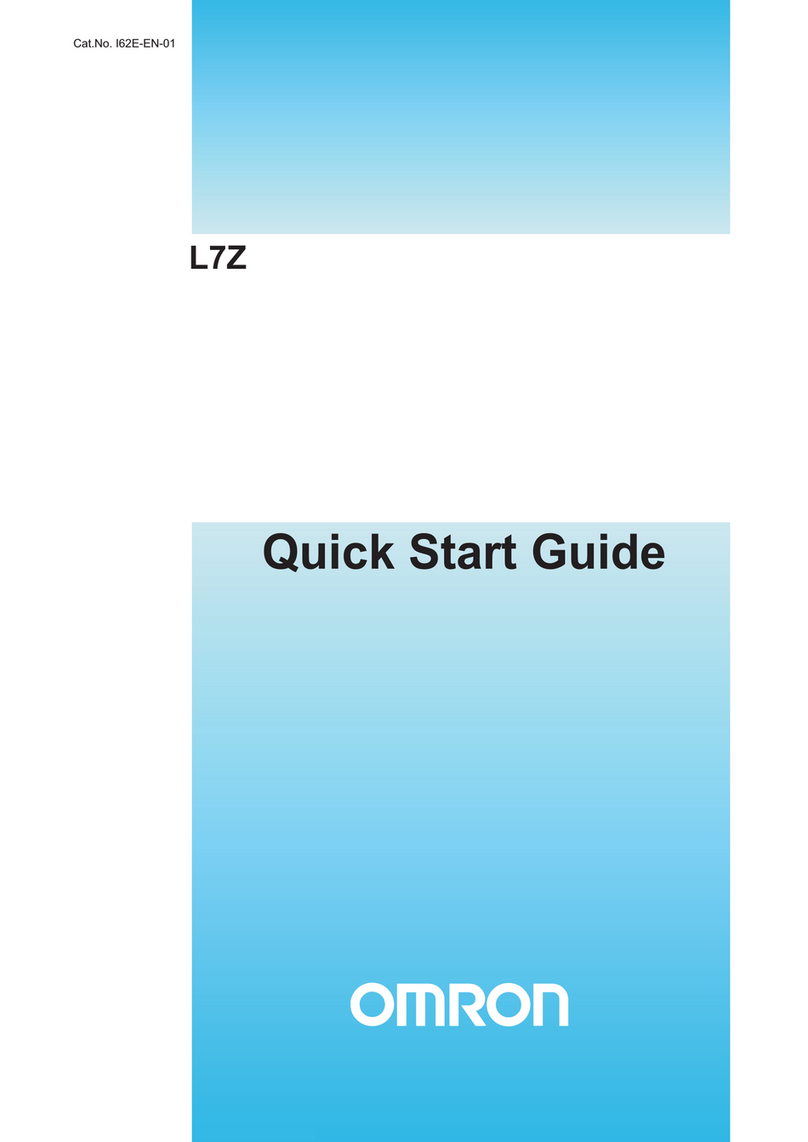
Omron
Omron L7Z - quick start guide
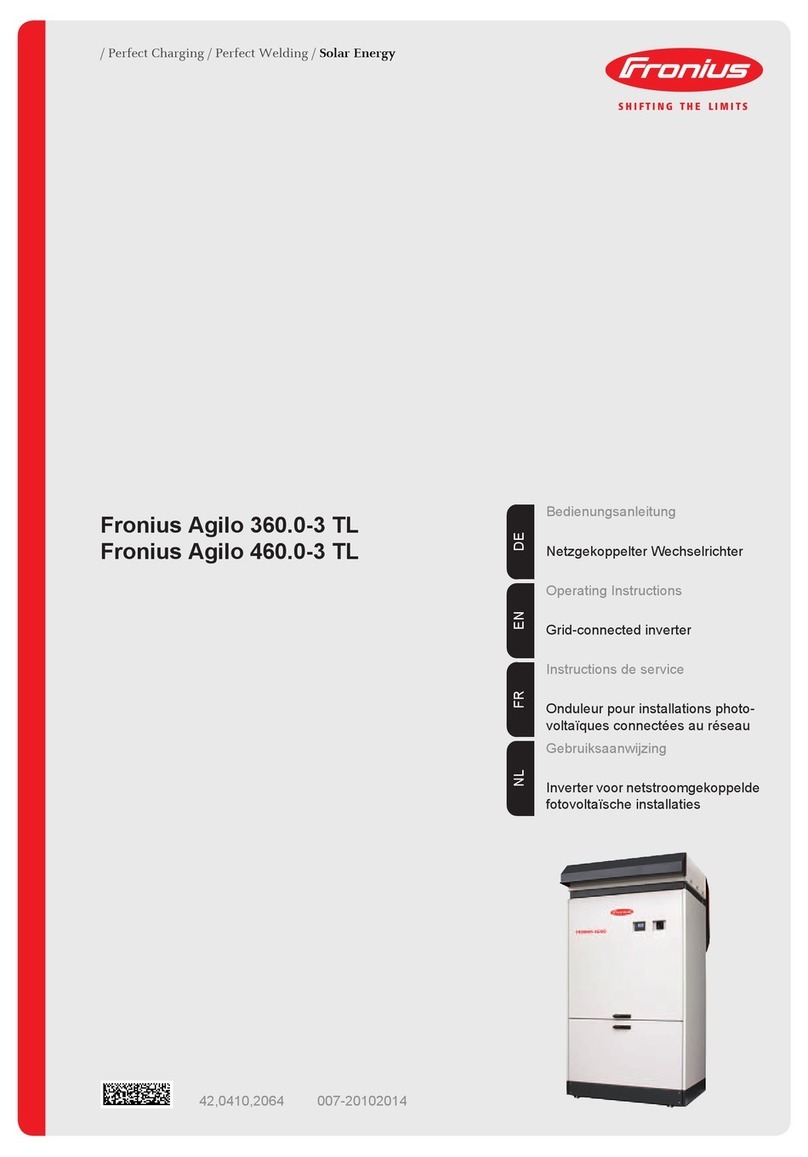
FRONIUS
FRONIUS Fronius Agilo 360.0-3 TL operating instructions
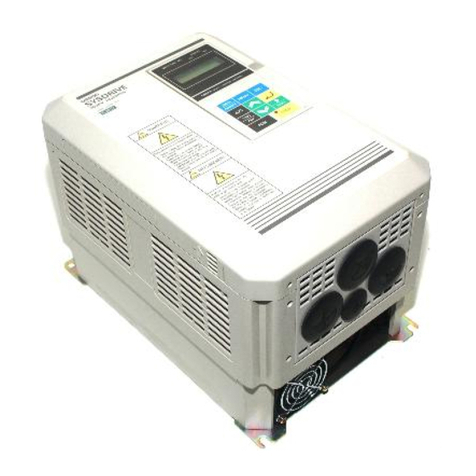
Omron
Omron SYSDRIVE 3G3FV CE Series installation manual