Ketterer Drive System 3062 User manual

3062.72-01 Rev. A
Assembly instructions
„Drive System 3062“
3062.00-V01XXX
3062.00-XXXX
Origin l ssembly instructions
3062.72-01
for p rtly completed m chines According to m chinery directive 2006/42/EG
Att chment VI
04/2022

3062.72-01 Rev. A
B. Ketterer Söhne GmbH & Co. KG
Bahnhofstra e 20
78120 Furtwangen
Phone: +49(0)77 23 / 6569-10
Internet: www.ketterer.de
© 2022 B. Ketterer Söhne GmbH & Co. KG • 78120 Furtwangen
All rights reserved, in particular the right of reproduction, distribution and translation. No part of this
manual may be reproduced in any form or saved, processed, duplicated or distributed using electronic
systems without the written consent of B. Ketterer Söhne GmbH & Co. KG.
Subject to modifications.

3062.72-01 Rev. A
1
Introduction ............................................................................................................................................. 1
1.1
Content .................................................................................................................................................. 1
1.2
Scope ..................................................................................................................................................... 1
1.3
St nd rds nd directives ...................................................................................................................... 1
1.4
Warnings and symbols used .................................................................................................................. 2
1.4.1
Structure of the section-specific warnings ........................................................................................ 4
1.4.2
Structure of the embedded warnings ............................................................................................... 4
2
S fety Instructions ................................................................................................................................... 5
2.1
Personnel - Qualification und obligations ............................................................................................. 5
2.2
Obligations of the operator ................................................................................................................... 6
2.3
Use ......................................................................................................................................................... 6
2.3.1
Intended use ..................................................................................................................................... 6
2.3.2
Foreseeable misuse ........................................................................................................................... 7
2.4
Residual risks ......................................................................................................................................... 8
3
Product description ................................................................................................................................. 9
3.1
Description of the drive system ............................................................................................................. 9
3.2
Standard scope of delivery .................................................................................................................... 9
3.2.1
Scope of delivery 3062.00-0010 ........................................................................................................ 9
3.2.2
Scope of delivery 3062.00-0011 ...................................................................................................... 10
3.2.3
Scope of delivery 3062.00-V01XXX ................................................................................................. 10
3.3
Dimension ............................................................................................................................................ 11
3.3.1
Dimension 3062.00-0010 ................................................................................................................ 11
3.3.2
Dimension 3062.00-0011 ................................................................................................................ 12
3.3.3
Dimension 3062.00-V01XXX ............................................................................................................ 13
3.4
Technical data / operating conditions ................................................................................................. 14
4
P cking / Tr nsport / Unp cking / Stor ge ............................................................................................ 15
4.1
Packing / Transport.............................................................................................................................. 15
4.2
Unpacking ............................................................................................................................................ 15
4.3
Storage................................................................................................................................................. 15
5
Assembly ............................................................................................................................................... 16
5.1
Mechanical mounting instructions ...................................................................................................... 16
5.2
Connecting a spindle unit with the drive system ................................................................................ 16
5.3
Mounting the drive system in your application................................................................................... 17
5.4
Installation instructions for the qualified electrician........................................................................... 19
5.4.1
Circuit diagram: ............................................................................................................................... 21
6
St rt-up ................................................................................................................................................. 22
6.1
Teaching-in / deleting a radio remote control .................................................................................... 23
6.2
Setting the end positions ..................................................................................................................... 25
7
Oper tion .............................................................................................................................................. 26
7.1
Operation with a wind sensor ............................................................................................................. 29
8
M inten nce .......................................................................................................................................... 30
9
Dispos l ................................................................................................................................................. 30
10
Rep ir .................................................................................................................................................... 30
11
Self-help nd di gnosis in c se of m lfunction ....................................................................................... 31
EC - Decl r tion of Incorpor tion ................................................................................................................... 32

Introduction
3062.72-01 Rev. A
S e i t e | 1
1 Introduction
1.1 Content
This documentation is intended to help you work safely on and
with the "Drive system 3062", hereinafter called "drive system".
It contains safety instructions that must be followed for all work
performed on and with the drive system.
The documentation must be made accessible to all persons who
work on and with the drive system. They must have understood
the documentation and follow the specifications and
instructions relevant to them.
The documentation must be always complete and in a clearly
readable condition.
Ple se re d these instructions c refully nd follow the s fety
instructions ex ctly!
Depending on the design or modific tion st tus of the product,
there
m y be differences from these instructions. The user
must check this before use nd observe the differences if
necess ry.
1.2 Scope
These instructions are valid for the incomplete machine with
article number 3062.00-V01XXX and 3062.00-XXXX only.
1.3 St nd rds nd directives
The conformity assessment procedure was carried out in
accordance with the Machinery Directive (MRL) 2006/42/EC.
This drive system is a "partly completed machine" according to
Article 2, Paragraph g), MRL 2006/42/EC.
A declaration of incorporation according to Annex II, Part 1,
Section B, MRL 2006/42/EC is provided in this document.
The drive system is designed according to compliance with the
directives 2011/65/EU (RoHs), 2014/30/EU (EMC) and
2014/53/EU (radio equipment).
Based on the MRL, the manufacturer of the overall system in
which the drive system is installed has the responsibility to
verify and ensure compliance with the essential requirements
of the MRL. This must be done before the complete machine is
placed on the market.

Introduction
3062.72-01 Rev. A
S e i t e | 2
1.4 W rnings nd symbols used
The safety sign visually represents a source of hazard. The safety
signs in these assembly instructions comply with DIN EN ISO
7010.
The following pictograms and signal words are used in this
documentation to indicate hazards and important information:
Pictogr m
Description
W rning of gener l h z rd
This warning sign is placed in front of activities where several
causes can lead to hazards.
Hot surf ce w rning
This warning sign stands in front of activities where there is a
hazard from hot surfaces which can lead to burns.
W rning of electric shock
This warning sign stands in front of activities where there is a
risk of electric shock, possibly with lethal consequences.
W rning g inst pointed object / sh rp edges
This warning sign stands in front of activities where injuries can
occur due to pointed and or sharp edges and corners.
W rning of crushing h z rd
This warning sign stands in front of activities where hazards
exist due to crushing and shearing points which can lead to
crushing injuries.
Follow instructions
Inform tion

Introduction
3062.72-01 Rev. A
S e i t e | 3
In these assembly instructions, the following danger levels are
used to indicate potentially hazardous situations and important
safety instructions:
H z rd level Description
Indicates a hazardous situation which, if not avoided, will
result in death or serious irreversible injury.
DANGER
!
Indicates a hazardous situation which, if not avoided, could
result in death or serious irreversible injury.
WARNING
!
Indicates a hazardous situation which, if not avoided, could
result in minor or moderate injury.
CAUTION!
Indicates a potentially hazardous situation. If not avoided, the
equipment or something in its environment may be
damaged.
INFORMATION!

Introduction
3062.72-01 Rev. A
S e i t e | 4
1.4.1 Structure of the section-specific w rnings
The section-specific warnings apply not only to one specific
action, but to several actions within a chapter. The hazard
symbols used indicate either a general or specific hazard.
The warning is structured as follows:
SIGNAL WORD!
N ture of the h z rd nd its source.
Possible Consequence(s) of disregard.
►
Action(s) to avoid the hazard.
1.4.2 Structure of the embedded w rnings
The embedded warnings are directly integrated into the action
before the dangerous action step.
The embedded warning is structured as follows:
SIGNAL WORD! Nature of the hazard and its source.
Possible Consequence(s) of disregard.
Action(s) to avoid the hazard.

S fety Instructions
3062.72-01 Rev. A
S e i t e | 5
2 S fety Instructions
Re d the s fety instructions nd inform tion on
s fe oper tion
provided in these ssembly instructions c refully before
st rting work. Become f mili r with ll functions. Keep these
ssembly instructions in s fe pl ce nd p ss them on to
others if necess ry.
It is very import nt for your s fety th t
you underst nd nd
follow ll s fety inform tion cont ined in this document.
Non-compliance may result in danger to the life and health of
persons and / or extensive damage to property.
Compliance with the safety instructions helps to avoid hazards.
Always keep the assembly instructions available in a readable
condition.
2.1 Personnel - Qu lific tion und oblig tions
Inform tion
All activities on and with the drive system
must only be
performed by authorized personnel.
The uthorized personnel must...
…know and be able to apply the general accident prevention
regulations and safety instructions.
...be appropriately qualified for electrical work (qualified
electrician).
...have been trained and instructed in accordance with the rules
of behaviour in the event of a malfunction.
...have the physical and mental capabilities to carry out his
responsibilities, tasks and activities on the drive system.
...have been trained and instructed in accordance with his
responsibilities, tasks and activities at the drive system.
...have understood the technical documentation relating to his
responsibilities, tasks and activities at the drive system and be
able to implement it in practice.

S fety Instructions
3062.72-01 Rev. A
S e i t e | 6
2.2 Oblig tions of the oper tor
Every person who works with the drive system has a
responsibility to ensure safety and health protection. They must
be trained in the use of the drive system.
A safety-related condition and use of the drive system is a
requirement for safe operation. Therefore, the operator has the
responsibility to ensure that the following points are complied
with:
Ensure that the drive system is only operated by trained and
authorized personnel!
Prohibit safety-endangering and dangerous working methods!
Check the actions of the personnel!
Always keep this document in a complete and readable
condition!
Obligate the operating and maintenance personnel to report
occurring and recognizable safety defects immediately to their
superiors!
During start-up and operation, the operator must ensure that there
are no persons in the danger zone. The danger zone depends on
the function and dimensions of the end product in which the
drive system is installed.
2.3 Use
2.3.1 Intended use
This product is an electromotive drive system consisting of a
tubular motor with integrated control, radio module and multi-
tooth output shaft for connecting a spindle.
The drive system is designed to be integrated into an application
and to transmit the rotary motion of the motor to the
application via a spindle system.
The drive system is controlled via the supplied 1-channel
handheld radio transmitter.
The drive system may only be put into operation after
conformity with all relevant directives and standards has been
established by the integrator.
Observe the following notes on the intended use of the available
versions of the drive system.

S fety Instructions
3062.72-01 Rev. A
S e i t e | 7
The drive system is available in two versions:
Version with emergency h nd cr nk
3062.00-V01XXX (v ri ble ge r di meter)
3062.00-0011 (ge r di meter 53 mm)
The versions with item numbers 3062.00-V01XXX and 3062.00-
0011 has been specially designed for integration into the mast
tube of an umbrella. This version has a gear input and an
emergency hand crank for manual closing of the umbrella in
case of emergency situations. Please note the specific
instructions for this version.
Version without emergency h nd cr nk
3062.00-0010 (ge r di meter 53 mm)
This version of the drive system does not have a gear input for
manual operation. This must be taken into account when
integrating it into the application. In emergency situations, this
version cannot be operated manually. The integrator or
operator of the application must provide sufficient safety in
emergency situations.
The spindle system must be individually configured with
Ketterer depending on the application.
2.3.2 Foresee ble misuse
In the case of misuse, Ketterer is not responsible for any injuries
caused, property damage or any subsequent damage that may
occur.
Misuses are:
Operation in the range outside the operating data specified in
these assembly instructions (see chapter 3.4 “Technical data /
operating conditions").
Mechanical and electrical assembly in non-compliance with the
instructions given in these assembly instructions.
Operation different from the application approved by Ketterer.
Operation without suitable protection against the intrusion of
water.
Interference with the components or the system during
operation.
Changes to the drive system which have not been approved by
Ketterer.

S fety Instructions
3062.72-01 Rev. A
S e i t e | 8
2.4 Residu l risks
Despite all actions taken to integrate safety in the design, safety
provisions and additional protective actions, non-obvious
residual risks cannot be completely avoided. You can reduce
residual risks by carefully following the safety instructions and
the intended use. The identified residual risks are listed in Table
1.
Table 1: residual risks
Life ph se /
Activity
Residu l risk
Packing /
Transport /
Unpacking /
Assembly
Cutting injuries
Despite strict quality controls, parts of the drive system, as well as the
accessories and packaging, may have sharp edges and corners which can lead
to cuts. Make sure that you wear suitable protective gear whenever handling
the drive system.
Start-up /
Operation
Hot surf ces
Depending on the load and environmental temperature, the surfaces of the
drive system may reach temperatures of over 90 °C. Only perform necessary
activities directly with the drive system after it has cooled down completely.
However, wait at least 45 minutes after the last motor activity.
Assembly /
Start-up /
Operation
Electric l volt ge / residu l energy
Residual electrical energy may remain in lines, electrical components,
equipment and devices when the drive system is switched off. Only allow work
on the electrical supply to be carried out by qualified electrical personnel. Make
sure that all phases are voltage-free. There must be no residual voltage left in
the system, so wait at least 5 minutes after complete disconnection from the
power supply before carrying out the necessary work.
Start-up /
Operation
Uncontrolled movements
Incorrect programming of the radio remote control may cause one or more
applications to be activated unintentionally when several applications are
controlled. Follow the instructions for programming and deleting the radio
remote control.
Start-up /
Operation
Tr pping, dr wing in, gr bbing
Objects, items of clothing or body parts can be drawn in, trapped or grabbed by
the rotary motion of the motor, gear unit or spindle. Only operate the motor
when it is encapsulated.
Start-up /
Operation
Bre k ge
Overloading the drive system above the specified load limits can lead to a
defect in the drive system and thus to injury or damage to property. This also
includes overloading due to wind forces.

Product description
3062.72-01 Rev. A
S e i t e | 9
3 Product description
3.1 Description of the drive system
The 3062 drive system is an electromotive drive system
consisting of motor, control unit and radio remote control.
The drive is designed for large tensile and compressive forces
and moves the corresponding application at the push of a
button. The system is controlled via the radio remote control.
A wide range of applications can be realized by connecting a
spindle unit and spindle nut.
The version with gear input and emergency hand crank was
developed for use in umbrellas. The system can be integrated
into the mast tube of the umbrella and is therefore not visible
from the outside. The emergency hand crank allows to close the
umbrella manually in emergency situations such as storms.
The version without emergency hand crank can be used for
various applications.
In version 3062.00-V01XXX, the outer diameter of the gearbox
can be adapted to customer requirements (Ø > 53mm), see
chapter 3.3 “Dimensions”.
3.2 St nd rd scope of delivery
The scope of delivery depends on the corresponding version:
3.2.1 Scope of delivery 3062.00-0010
Pcs Description
1
Electric motor drive
consisting of motor with integrated control and
radio module, connection cable 230V with
open wires
1 1-channel radio remote control
1 Spindle unit SG25x4 RH incl. spindle nut

Product description
3062.72-01 Rev. A
S e i t e | 10
3.2.2 Scope of delivery 3062.00-0011
3.2.3 Scope of delivery 3062.00-V01XXX
NOTE!
Customized solutions of spindle nd spindle nut must be configured individu lly
with Ketterer nd ordered sep r tely.
Pcs Description
1
Electric motor drive
consisting of motor with integrated control and
radio module, connection cable 230V with
open wires
1 1-channel radio remote control
1 Emergency hand crank
with integrated ejection mechanism
1 Spindle unit SG25x4 RH incl. spindle nut
Pcs Description
1
Electric motor drive
consisting of motor with integrated control and
radio module, connection cable 230V with
open wires
1 1-channel radio remote control
1 Emergency hand crank
with integrated ejection mechanism
Spindle unit must be configured individually with
Ketterer

Product description
3062.72-01 Rev. A
S e i t e | 11
3.3 Dimension
The dimensions depend on the version:
3.3.1 Dimension 3062.00-0010
Figure 3-1: Dimensions of the drive system 3062.00-0010

Product description
3062.72-01 Rev. A
S e i t e | 12
3.3.2 Dimension 3062.00-0011
Figure 3-2: Dimensions of the drive system 3062.00-0011

Product description
3062.72-01 Rev. A
S e i t e | 13
3.3.3 Dimension 3062.00-V01XXX
Figure 3-3: Dimensions of the drive system 3062.00-V01XXX
Customer-specific d pt tion for 3062.00-V01XXX
Dimension of the gear housing can be realised between Square 73 mm und Ø = 53 mm.

Product description
3062.72-01 Rev. A
S e i t e | 14
3.4 Technic l d t / oper ting conditions
Table 1: Technical data / operating conditions
* In combination with spindle SG25x4
Technic l d t / oper ting conditions
Voltage
230 V~/50 Hz
Current
1 A
Starting current (factor)
x 1,2
Power output
ca. 60 W
Transmission frequency radio remote control
434 MHz
Nominal torque / peak torque
5 Nm / 7 Nm short term
idle speed
134 U/min
Nominal speed
120 U/min @ 5 Nm
Operating mode
S2 4 min
Operating ambient temperature / humidity
T =
-
10°C ... +60°C / H max.
90%
Environmental temperature / humidity Storage
T =
-
15°C ... +70°C / dry
Motor operating temperature
Overheating protection with switch
-
off
at 110°C
Protection class
IP 44
Gear ratio i
Drive train electric drive - spindle
1:1
Travel speed at nominal
load
8 mm/s*
Maximum load peaks Tensile / compressive forces
static
10.000
N

P cking / Tr nsport / Unp cking / Stor ge
3062.72-01 Rev. A
S e i t e | 15
4 P cking / Tr nsport / Unp cking / Stor ge
CAUTION!
D nger from sh rp edges on p rts of the housing!
When handling the drive system, cuts may occur due to sharp edges
and corners.
►
Wear appropriate personal protective gear depending on the
environmental conditions.
4.1 P cking / Tr nsport
During transport, the drive system must be protected against
dust and shocks.
During transport, the drive system must be protected
adequately from moisture (e.g. rainwater).
Observe the temperature ranges during the entire transport.
These must not be exceeded or underrun. These are: - 15°C to
+ 70°C.
4.2 Unp cking
Make sure that all packaging components are removed.
Dispose all packaging components, according to the disposal
regulations applicable in the country of use.
When removing the packaging, pay attention to the danger of
cutting.
4.3 Stor ge
Storage in dry, low-vibration environment without aggressive
atmosphere. The air humidity must not exceed the value of 70%.
Temperature ranges must not be exceeded or underrun. These
are: - 15°C to + 70°C.
Protect from dust and shocks.

Assembly
3062.72-01 Rev. A
S e i t e | 16
5 Assembly
5.1 Mech nic l mounting instructions
WARNING!
M lfunctions due to incorrect inst ll tion of the drive system!
Incorrect installation of the drive system can lead to malfunctions of
the application and thus to dangerous situations with risk of injury
and / or damage to material.
►
Install the drive system only in compliance with the installation
instructions specified in this document.
►
Have the installation work performed by qualified personnel
only.
CAUTION!
D nger from pointed or sh rp edges on p rts of the housing!
When handling the drive system, cuts may occur due to pointed or
sharp edges or corners.
►
Wear suitable personal protective equipment depending on the
environmental conditions.
Prep r tory ctivities:
Inspect the drive system for external mechanical damage before
starting the assembly.
Remove all packaging components before the assembly.
Make sure that the torque and speed of the drive system are
suitable for your application.
5.2 Connecting spindle unit with the drive system
CAUTION! Risk of malfunction of the drive system.
If an unsuitable spindle / spindle nut is used, there is a risk of malfunctions with serious
consequences. The spindle / spindle nut must be approved by Ketterer. The spindle must
not be operated without grease.
If you have purchased part number 3062.00-0010 or 3062.00-
0011, the aluminium spindle 25x4 and a suitable spindle nut are
included. For part number 3062.00-V01XXX a suitable spindle
and spindle nut must be configured with Ketterer and ordered
separately.

Assembly
3062.72-01 Rev. A
S e i t e | 17
Grease the entire length of the spindle with 60 grams
Castrol Optitemp LG2
The spindle is mounted with the enclosed screw DIN912-M8x40
and nut DIN985-M8-VZ via the bore provided in the output
shaft, see Figure 5-1.
Make sure that the tightening torque is 18 Nm ±2Nm.
Figure 5-1: Connection of a spindle
5.3 Mounting the drive system in your pplic tion
Fasten the drive system using the mounting points provided on
both sides in the housing and motor adapter, see Figure 5-2 and
Figure 5-3. If the drive system is only fixed on the housing and
not on the motor adapter, the motor can rotate freely and the
function in the application may be restricted.
The length of the screws depends on the mounting position in
the application and must be selected by taking the specified
thread length into account. The screw-in depth should be at
least 8 mm for M6 screws.
Fasten the spindle nut to the screw connection points provided
for this purpose.
Only use screws which are suitable for the forces occurring in
the application and for all tensile and compressive forces.
Make sure that the selected screws are tightened with a correct
torque value. Check that the screws are firmly seated. Use
appropriate tools to tighten the screws to ensure a secure seat
and to avoid damage to the screws.
If there is no protection against moving parts or heated housing
parts of the drive system, the system must be mounted at a
height of at least 2.5 m above floor level.
The drive system must not sit directly on the ground, but must
be positioned at least 10cm above ground level.
The drive system must be protected against intrusion of
moisture.
Table of contents
Popular DC Drive manuals by other brands

Shihlin electric
Shihlin electric SDE-010A2U manual

Siemens
Siemens SINAMICS G120 CU230P-2 operating instructions
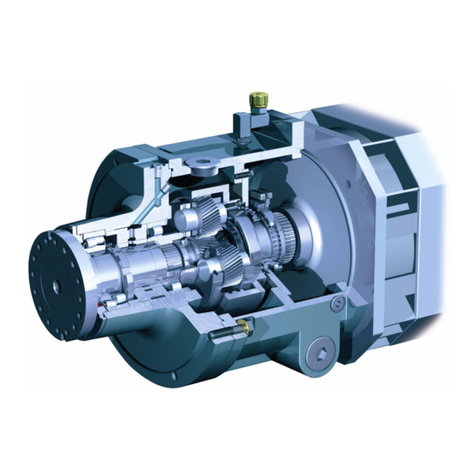
ZF-DUOPLAN
ZF-DUOPLAN 2K800 operating instructions
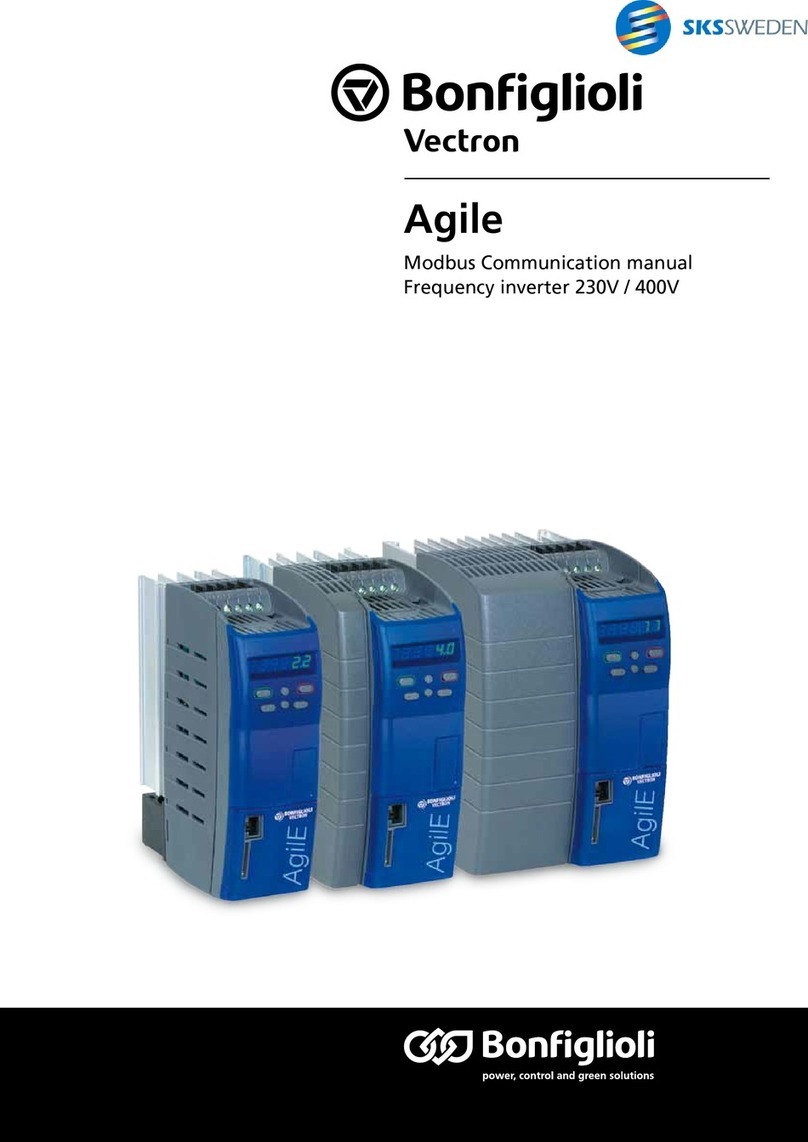
BONFIGLIOLI Vectron
BONFIGLIOLI Vectron Agile Communications manual
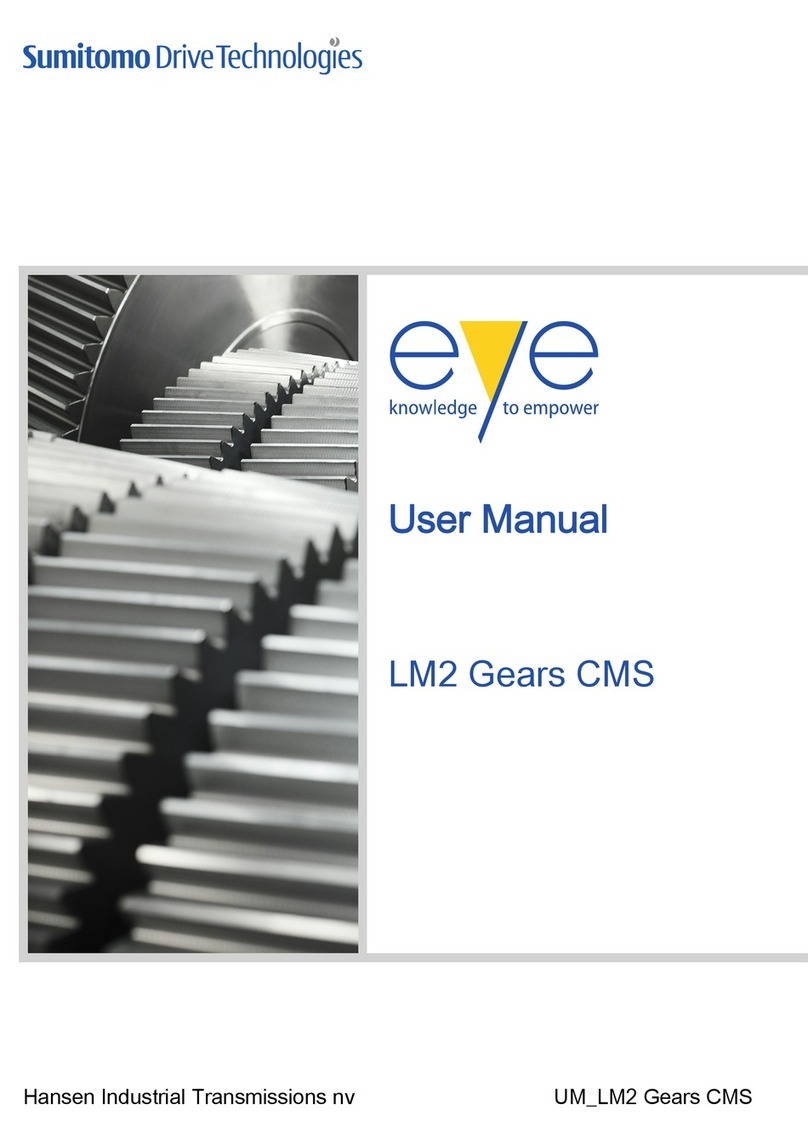
Sumitomo Drive Technologies
Sumitomo Drive Technologies eye LM2 Gears CMS user manual
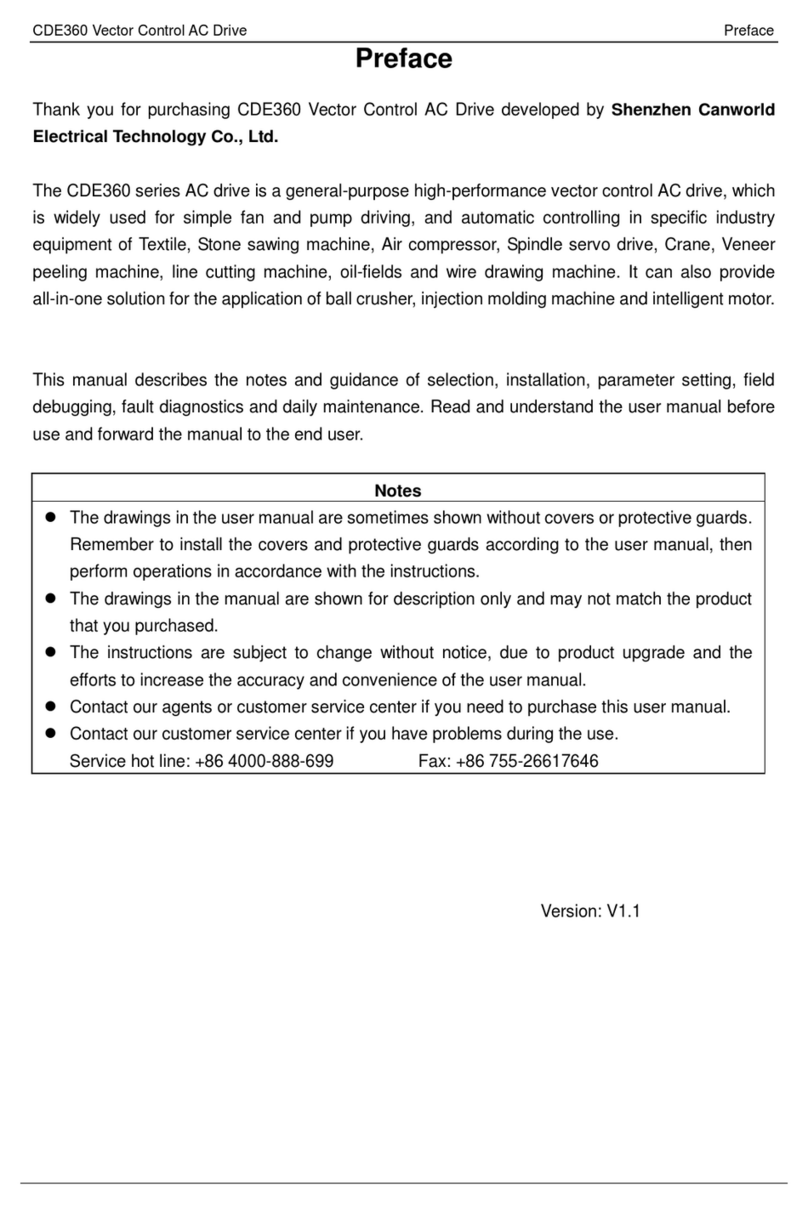
Canworld
Canworld CDE360 Series manual