KLINGER Ballostar KHE Guide

wT 2575/11
Page 1
Mounting and treatment instructions for
KLINGER
BallostarKHE ball valves
Split body design, DN 15 – 200 and NPS ½“ – 8“
Edition: 06/2006
Rev.: 02/2008
Fluid Control GmbH
Am Kanal 8-10
A-2352 Gumpoldskirchen / AUSTRIA
Tel.: +43(0) 2252 / 600 0
Fax: +43(0) 2252 / 600 359
e-mail: [email protected]
Homepage: www.klinger.kfc.at
7 20 21 13
17
18
19
14
5
6 4 1 15 22 2 16
3
8
12
11
9
10
1 Body
2 Flanged end piece
3 Operating stem
4 Ball
5 Sealing element
6 Sealing ring
7 Stopper
8 Loading ring
9 Stuffing box
10 Slip ring
11 Antistatic disc
12 Fem. support ring
13 Hand lever
14 Secondary graphite sealing
15 Hex screw
16 Hex nut
17 Stuffing box nut
18 Belleville washer
19 Washer
20 Hex screw
21 Washer
22 Supporting ring

wT 2575/11
Page 2
Table of contents
Page 3 Functional principle
Page 4, 5, 6 Mode of operation
Page 7, 8 Instructions for treatment, tightening torques and wrench sizes
Page 8 Material code
Page 9 Designation of parts and materials
Page 10 Type overview
Page 11 Type overview sealing elements
Page 12 Type overview stuffing boxes
Page 13 Components of labyrinth stuffing box
Page 14, 15 Dismantling & assembling of valve
Page 16 Installation of valve, mounting of actuator
Page 17, 18 Operating torques
Page 19 Initiating operation and safety instructions

wT 2575/11
Page 3
FUNCTIONAL PRINCIPLE
Because of the ELASTIC SEALING SYSTEM, the KLINGER Ballostar®KHE ball valve is absolutely
leak tight at high, but also at extremely low pressures. The required contact forces between sealing ring
and ball are created by the differential pressure in the ball valve. For the FLOATING BALL sealing
principle it is important that the shut-off device is freely moveable. The sealing rings perform two
functions at the same time: They guide the ball and absorb bearing forces.
FORCE FLOW
The forces which are absorbed by the sealing rings increase with larger nominal diameters (DN, NPS).
Therefore the floating ball design is only used for small sized ball valves. To achieve a high service life
and to reduce the operating torques for pivot movements, the floating ball design is only used for sizes
up to DN 125. For larger sizes lower costs in production face the significant higher costs for increasing
the moment of force to surmount the high operating torques. The increased amount of friction caused by
high loading pressures additionally leads to a low service life and a poor number of shifting cycles.

wT 2575/11
Page 4
MODE OF OPERATION
The sealing system of the bore consists of:
-A pre-stressed elastic sealing element made of stainless and acid resistant steel with a
KFC-sealing ring (Standard) and a U-Sleeve made of K-Flon located at the pitch of the body
and the flange end piece.
-An inelastic sealing ring located in a chambered groove in the body
-The ball between sealing element and sealing ring
Basically KLINGER Ballostar®KHE ball valves can be pressurized in both directions. In consequence of
the different design of the two sealing components two operating conditions depending on the mounting
direction are possible:
1.) The elastic sealing element respective the flange end piece is mounted upstream:
The fluid pressure presses the ball against the downstream located sealing ring. At the same time, the
upstream located sealing element is pressed against the ball. Because of the elasticity of the KLINGER
sealing system two sealing areas are permanently available in the bore.
For standard applications KLINGER recommends this situation of installation as preferred mounting
direction. This recommended direction is additionally marked with an arrow on the valve body.
Occurring forces:
F1…Fluid force acting on ball
F2…Fluid force acting on
sealing element
Fv…Spring force of sealing
element
F1+F2+Fv…Total force, which
acts onto the sealing ring

wT 2575/11
Page 5
2.) Inelastic sealing ring respective body flange is mounted upstream:
The fluid pressure acts against the preloading force of the elastic sealing element located
downstream.
If the force of the fluid pressure is higher than the preloading force, the ball lifts from the sealing
ring and only the downstream located sealing element performs the primary sealing function.
Due to the fact that this condition occurs at high differential pressures the surface pressure
between sealing element and ball is high enough to enable an effective sealing.
At high differential pressures the preloading force of the elastic sealing element is high enough
to press the ball against the upstream located sealing ring. A second primary sealing area is
created, which enables an outstanding effective sealing!
High differential pressures: FV-F1 < F1 …ball lifts from upstream located sealing ring
Low differential pressures: FV-F1 > F1 …upstream located sealing ring is in full function
KLINGER Ballostar®KHE ball valves are basically maintenance free and can be pressurized in both
flow directions. The U-sleeve which is drawn onto the supporting ring is completely chambered and
seals the pitch flange against the outside. Additionally ball valves of type KHE have secondary graphite
sealing between body and flange end piece.
Occurring forces:
F1…Fluid force acting on ball
Fv…Spring force of sealing
element
Fv-F1…Total force, which acts
onto the sealing ring and
against fluid pressure

wT 2575/11
Page 6
THE EXTERNAL SEALING SYSTEM
The sealing of the shifting shaft (operating stem) is carried out by a belleville washer supported stuffing
box.
This type of sealing is almost maintenance free and has just little set-off behaviour. Only small
tightening forces are required for leak tightness.
The arrangement of the belleville washer ensures that a constant contact pressure acts against the
stuffing box to compensate alternating temperature- and pressure changes.
WELT OF SEALING RING
The grove in the body prevents floating of the sealing ring in radial direction (1) against the back side (2)
and the bore (3). The ball presses against the sealing ring (4). Therefore the sealing ring can not set
down or flow, because it is surrounded on each side.

wT 2575/11
Page 7
INSTRUCTIONS FOR TREATMENT
KLINGER Ballostarball valves are delivered in OPEN position. To protect them against dirt
contamination and damage the flange ends are covered with plastic caps. We recommend removing the
caps not until you want to install the valve. KLINGER valves should be stored in closed rooms with non-
aggressive ambient atmosphere and where they are protected from moisture and dirt. Furthermore the
maximum temperatures and pressures, specified in the P/T-diagrams, should not be exceeded during
operation. Just under these specified conditions mentioned before our warranty for the determined
duration is valid. Please notice, this warranty does not include valve components that are subjected to
corrosion, erosion and wear during operation
If cover- or shrink foils are used, you have to have to make sure, that the atmosphere within the foil is
free of condensation. For storage in dusty rooms appropriate protective measures are recommended.
To avoid confusion we suggest to name and store parts according to their shipping documents.
The temperature in the storage areas should range between -20° C and +50° C. Fast changes of
temperature should be avoided (creation of condensation- and perspiration water).
Instructions for treatment and application are part of the shipment and should therefore be stored next to
the goods. This makes sure that all necessary information and documentation are passed on.
Changes in documentation which belong to the storage of KLINGER products are timely forwarded by
circular letters.
Damages which can result from inappropriate storage absolve KLINGER from obligations deriving from
guarantee, warranty and product liability.

wT 2575/11
Page 8
KLINGER ball valves are basically MAINTENANCE FREE!
During long periods of non-operating, the valves have to be drained. In case of leakage the screws of
the body have to be retightened. Please check table No.1 for the required torque values!
KLINGER recommends operating the valve minimum six times a year to increase the service life!
Table 1: Tightening torques and wrench sizes (SW)
Tolerances for tightening torques of stuffing box nut: + 10 %
Tolerances for tightening torques of body screws: ±10 %
Screw thread lubricated with special grease paste: MOLYKOTE 1000
Material codes of KLINGER BallostarKHE ball valves
The material codes (m.c.) characterise the materials of body and flange end piece.
Used Materials:
DIN ANSI
Carbon steel: GS – C25N 1.0619 WCB
Stainless steel: G-X 6Cr NiMo 1810 1.4408 CF8M
1) Approval in cryogenic temperature range acc. to pressure-/temperature-diagram wT 2455/2 (13.05.96)
(Application limits acc. to AD-Merkblatt W 10 – technical sheet for the acceptance of facilities)
Size
DN
NPS
15
½”
20
¾”
25
1”
32
40
1 ½”
50
2”
65
2 ½”
80
3”
100
4”
125
-
150
6”
200
8”
Tightening torque of
stuffing box nut 5 15 15 25 25 20 20 40 40 40 o.r. o.r.
Tightening torque of
body screws 9 20 20 40 60 60 80 110 120 o.r. o.r.
SW of stopper screws 8 10 10 13 13 13 13 19 19 19 o.r. o.r.
SW of body screws 10 13 13 17 19 22 19 24 24 24 o.r. o.r.
SW of stuffing box nut:
DIN-version
ANSI-version
16
5/8”
22
7/8”
22
7/8
24
15/16”
24
15/16”
36
1 7/16”
36
1 7/16”
46
1 13/16”
46
1 13/16”
50
-
50
2”
65
2 9/16”
SW of operating stem 8 11 11 14 14 17 17 22 22 27 27 36
o.r. = on request
Symbol Body/end piece Internal parts Colour/surface treatment
VIII Carbon steel Without copper alloy black - phosphated
Xc Stainless steel Stainless steel blanc - pickled

wT 2575/11
Page 9
DESIGNATION OF PARTS AND MATERIALS
Materials
Pos. Parts of the standard version m.c. VIII m.c. Xc
1 Body 1.0619 (WCB) * 1.4408 (CF8M) **
2 Flange end piece 1.0619 (WCB) * 1.4408 (CF8M) **
3 Operating stem 1.4104 1.4571
4 Ball 1.4401(316)****
5 Sealing element *** Xc - KFC
6 Sealing ring *** KFC
7 Stopper 1.4301
8 Fem. support ring 1.4404
9 Labyrinth stuffing box* K – Flon / 4401 / Graphite
10 Slip ring KFC-25
11 Antistatic disc 1.4401
12 Loading ring 1.4404 plasma-nitrated
13 Hand lever 1.4006/Vinyl blue
14 Hexagon screw 8.8-A2L A4-70
15 Hexagon nut 8-A2L A4
16 Stuffing box nut 1.4404
17 Belleville washer 1.4310
18 Washer A4
19 Hexagon screw A4-70
20 Supporting ring Sint D10/Sint C39 1.4404 (316L)
21 Secondary body sealing Graphite
22 Socket head screw A4-70
23 Hexagon nut A4
19
18
7
16
12
17
8
11
9
13
22
23
14 1 10 3 6 4 20 5 21 15 2
* Zn/Fe phosphated
** pickled
*** Standard design
**** beginning with DN65: 1.4408
(CF8M)

wT 2575/11
Page 10
TYPE OVERVIEW
There are three different types of KHE ball valves available: KHE-FK, KHE-FL and KHE-CL
The valves are differed by:
- Overall length (EN 558-1 or ANSI 16.10 and basic series)
- Type of flange connection: a) KHE-FK and KHE-FL ball valves are delivered with flanges
acc. to EN 1092-1
b) KHE-CL ball valves are equipped with flanges acc. to ANSI B 16.5
- Pressure range (PN16, PN40 or Class 150, Class 300)
KHE-FL, long overall length acc. to EN 558-1, basic series 1 (DIN 3202-1F1)
KHE-FK, short overall length acc. to EN 558-1, basic series 27 (DIN 3202-1F4)
KHE-CL, short pattern acc. to ANSI B 16.10
Further information, as product features, dimensions, equipment and fields of application can be
gathered from the product catalogue.

wT 2575/11
Page 11
TYPE OVERVIEW SEALING ELEMENTS
Due to the modular system of construction the sealing system of KHE ball valves can be adapted easily
for special applications. The sealing elements of the valves are suited for many kinds of applications,
operating conditions and fluids. There are 4 types of different sealing elements/rings combinations
available:
1. KFC-25 (Standard = Fire Safe)
U-sleeve (K-Flon)
Used for standard applications and as spare part
Elastic sealing element
(stainless steel)
Sealing ring (KFC-25)
2. PTFE
U-sleeve (K-Flon)
Gas and vacuum applications
Elastic sealing element
(stainless steel)
Sealing ring (PTFE)
3. Metal
U-sleeve (K-Flon)
Used for abrasive fluids Graphite
Elastic sealing element
(stainless steel)
Graphite gasket
Stelite plated
Sealing ring
4. Single-Part Sealing Element
Used for applications with
high temperature changes
Sealing ring
(KFC-25
Single part sealing element
U-Sleeve
(K-Flon)
U-Sleeve
(K-Flon)
4.1 Single Part Sealing Element with release hole
used for heavy expanding liquids
and high temperature changes
Single part sealing element
Sealing ring
(KFC-25)
release-
hole

wT 2575/11
Page 12
TYPE OVERVIEW STUFFING BOXES
Labyrinth stuffing box
(PTFE)
Graphite stuffin
g
box
O
-rin
g
Stuffin
g
box
(
Viton
)
Fields of application:
Vacuum and gases
Fields of application:
High temperature
Fields of application:
This is the standard type of
stuffing box.

wT 2575/11
Page 13
COMPONENTS OF LABYRINTH STUFFING BOX
Nominal
Diameter
Pos.1 Pos.2 Pos.3 Pos.4 Pos.5 Pos.6
15 10/14x0,5 10 (10/14x0,4) 10,1/14x0,5 10,5x14,2 x0,1 10/14x2 10/14x1,5
20, 25 16/21x0,7 16 (16/21x0,5) 16/21x0,5 16,5/21,2x0,1 16/21x2 16/21x1
32, 40 20/26x1,0 20 (20/26x0,5) 20/26x0,7 20,5/26,2x0,1 20/26x2 20/26x2
50, 65 25/33x1,0 25 (25/33x1,0) 25/33x0,7 25,5/33,2x0,1 25/33x2 25/33x1
80, 100 30/40x1,5 30 (30/40x1,0) 30,1/40x1,0 30,5/40,3x0,1 30/40x2 30/40x2
125 34/34x1,5 34 (34/45x1,0) 34/45x1,0 34,5/45,3x0,1 34/45x2 34/45x2
Nominal Diameter 15 20,25 32,40 50,65 80,100 125
Quantity of Pos.1 3 4 4 4 4 6
Quantity of Pos.2 3 4 4 4 4 6
Quantity of Pos.3 1 1 1 1 1 1
Quantity of Pos.4 1 1 1 1 1 1
Quantity of Pos.5 1 2 2 3 3 5
Quantity of Pos.6 1 1 1 1 1 1
Pos. 1 Stuffing box lamella K-Flon
Pos. 2 Disc 1.4401
Pos. 3 Slip ring KFC-25
Pos. 4 Antistatic disc 1.4401
Pos. 5 Washer Graphite
Pos. 6 Washer Graphite
6
2
5
3
4
1

wT 2575/11
Page 14
ASSEMBLING AND DISMANTLING
a) Remove valve from line
b
)
Turn hand lever in
„
OPEN
“
-
p
osition
c) Loosen hexagon screw
d) Remove hand lever
and stop
e) Loosen hexagon screw
f) Take off flange end piece
g) Secure ball against
twisting and loosen
stuffing box nut
h) Turn to “CLOSED”- Position
Re-assembling: Do NOT insert
supporting rings
It is not necessary, if a single-
piece sealing element is used.
i) Remove graphite sealing,
sealing element, supporting
ring and ball
2
1
3
2

wT 2575/11
Page 15
j) Remove stuffing box nut
Clamp on these surfaces.
Warning: Use protectors
Stuffing box nut secured
with LOCTITE 620
Loading ring
Belleville washer
Fem. supporting ring
Antistatic disc
Labyrinth stuffing box
4
3
k) Carefully remove
operating stem and slip
ring from the body
5
6
Assembly is done in reversed sequence (6-5-4-3-2-1)
Please Remember: Screw bolts have to be tightened crosswise!
Check the table 1 (page 7) to get the correct
torque values and wrench sizes.

wT 2575/11
Page 16
INSTALLATION OF VALVE
Although KHE ball valves can be pressurised in both flow directions, KLINGER recommends a preferred
mounting direction. The correct mounting direction is marked with an arrow on the valve body. This
ensures that the flange end piece (respective the elastic sealing element) of the ball valve is positioned
upstream.
ATTENTION: Make sure, that you use the metal part of the hand lever and not the plastic cover to bear
or lift the valve.
MOUNTING OF ACTUATOR
Preparation:
Type and Dimension of the actuator is determined by the required torque for operating the ball valve.
The torque values of valve and actuator can be taken from the torque tables. Attention should be paid to
the operating conditions.
A type plate is not standard
Direct mounting of actuators (as shown on the picture above) is only recommended for temperatures
beneath 80°C. KLINGER recommends to use mounting kits with bracket and coupling, if the
connection-holes of actuator and valve do not match or high operating temperatures occur.
Installation:
•Turn both valve and actuator into “OPEN”-position.
•Install actuator in the correct position (ATTENTION: valve closes with counter clock wise rotation).
Make sure, that the 90° rotation precisely complies with the end positions “OPEN” respective
“CLOSE”.
•Perform an operational test
Take notice of the actuator position!
(Remember: the actuator has to
be in “OPEN”-position during the
assembly)
Mounting situation
acc. to ISO 5211,
DIN 3337
(except DN 10 and 1S)

wT 2575/11
Page 17
OPERATING TORQUES
Operating torques [Nm], sealing element KFC-25
Differential pressure [bar]
NPS DN 0 5 10 16
Class
150 25 30 40
Class
300
1/2" 15 6 6,2 6,4 6,6 6,8 7 7,2 7,6 8
3/4" 20 12 12,4 12,7 13,1 13,4 13,8 14,1 14,8 15,5
1" 25 14 15 16,1 17,3 18,1 19,2 20,2 22,3 24,3
1 1/4"
32 17 18,4 19,9 21,6 22,7 24,1 25,6 28,4 31,3
1 1/2"
40 25 27,8 30,6 33,9 36,1 38,9 41,7 47,2 52,8
2" 50 37 40,6 44,3 48,6 51,5 55,1 58,8 66 80
2 1/2"
65 60 66,3 72,5 80 85 91,3 97,5 110 200
3" 80 96 114 132 153,6 168 186 204 240 300
4" 100 160 183,8 207,5 236 255,0 278,8 302,5 350 420
Size
5" 125 270 317,5 365 422 460 507,5 555 650 720
Orpeational torques [Nm], sealing element PTFE
Differential pressure [bar]
NPS DN 0 5 10 16
Class
150 25 30 40
Class
300
1/2" 15 5,4 5,6 5,8 6 6,1 6,3 6,5 6,8 7,2
3/4" 20 10,8 11,1 11,4 11,8 12,1 12,4 12,7 13,3 14
1" 25 12,6 13,5 14,5 15,6 16,3 17,2 18,2 20 21,9
1 1/4"
32 15,3 16,6 17,9 19,4 20,4 21,7 23 25,6 28,2
1 1/2"
40 21,3 23,6 26 28,8 30,7 33,1 35,4 40,1 44,9
2" 50 30,3 33,3 36,3 39,9 42,2 45,2 48,2 54,1 75
2 1/2"
65 51 56,3 61,6 68 72,3 77,6 82,9 93,5 180
3" 80 72 85,5 99 115,2 126 139,5 153 180 250
4" 100 120 137,8 155,6 177 191,3 209,1 226,9 262,5 350
Size
5" 125 202,5 238,1 273,8 316,5 345 380,6 416,3 487,5 600

wT 2575/11
Page 18
Operating torque [Nm], sealing element metal
Differential pressure [bar]
NPS DN 0 5 10 16
Class
150 25 30 40
Class
300
1/2" 15 7,5 7,8 8,2 8,5 8,8 9,1 9,5 10,1 10,8
3/4" 20 15 15,7 16,4 17,2 17,8 18,5 19,2 20,6 22
1" 25 18 19,4 20,9 22,6 23,7 25,1 26,6 29,4 32,3
1 1/4" 32 25 26,7 28,3 30,3 31,7 33,3 35 38,3 41,7
1 1/2" 40 40 44,8 49,5 55,2 59 63,8 68,6 78,1 87,6
2" 50 55 64,4 73,8 85 92,5 101,9 111,3 130 180
2 1/2" 65 85 101,9 118,8 139 152,5 169,4 186,3 220 300
3" 80 140 172,5 205 244 270 302,5 335 400 500
4" 100 250 293,8 337,5 390 425 468,8 512,5 600 750
Sizes
5" 125 450 580 710 866 970 1100
KLINGER recommends to use a safety-factor of 1,5 (= +5O%) for calculation
.

wT 2575/11
Page 19
INITIATING OPERATION
After installation and before initiating operation make sure to:
•Remove solid parts from the pipeline, which are not components of the fluid.
•Perform a functional test
•Perform a pressure test
Please notice that damages, which are caused by impurities or solid parts in the fluid/medium,
are excluded from warranty!
SAFETY INSTRUCTIONS
In general the usage and operation of these valves is without any risks. But remember yourself to act
with caution and care:
●Make sure, that you choose the correct type of ball valve which meets the requirements of your
application and operating conditions.
Take care of the safety instructions and pressure/temperature limits.
Use the product catalogue to select the best suitable material for your field of application
•Before installing and dismounting the valve the line is drained and not pressurized.
•Do not loose any screws on parts which are under pressure, unless this task is specified in the
mounting and treatment instructions.
•The assembling and service tasks should be performed only by qualified people.
•Make sure that all connections are duly tightened, after the dismantling process.
•Do not open any screws, bolts or nuts by force.
•ATTENTION when opening drain cocks – DANGER fluid is released.
•ATTENTION – take care of moving/movable parts! Especially if ball valves are equipped with
electric or pneumatic actuator.
This mounting and treatment instructions have to be referred to those employees who are
operating or maintaining these types of ball valves!
Table of contents
Other KLINGER Control Unit manuals

KLINGER
KLINGER 3530 Owner's manual
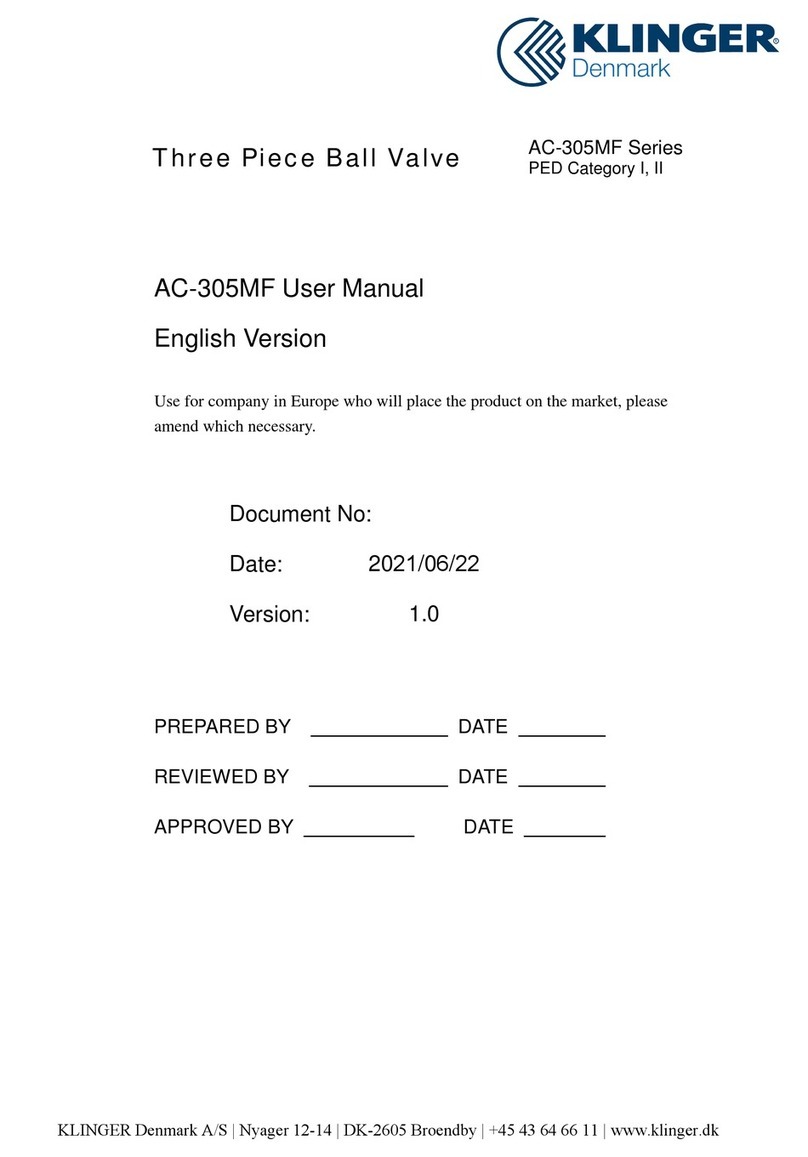
KLINGER
KLINGER AC-305MF User manual
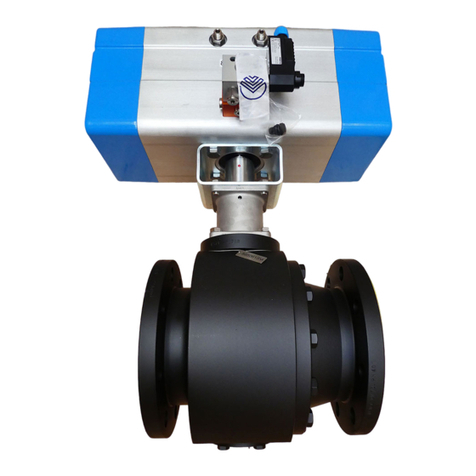
KLINGER
KLINGER INTEC K210-FS Setup guide
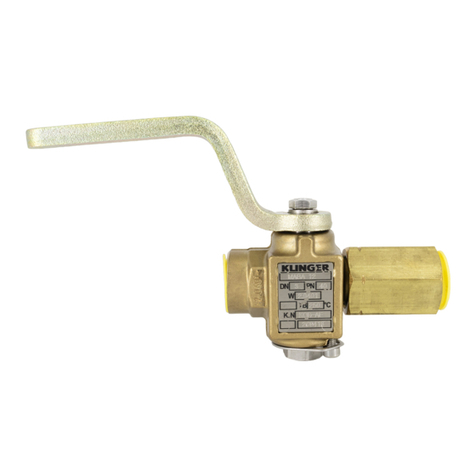
KLINGER
KLINGER MABA User manual
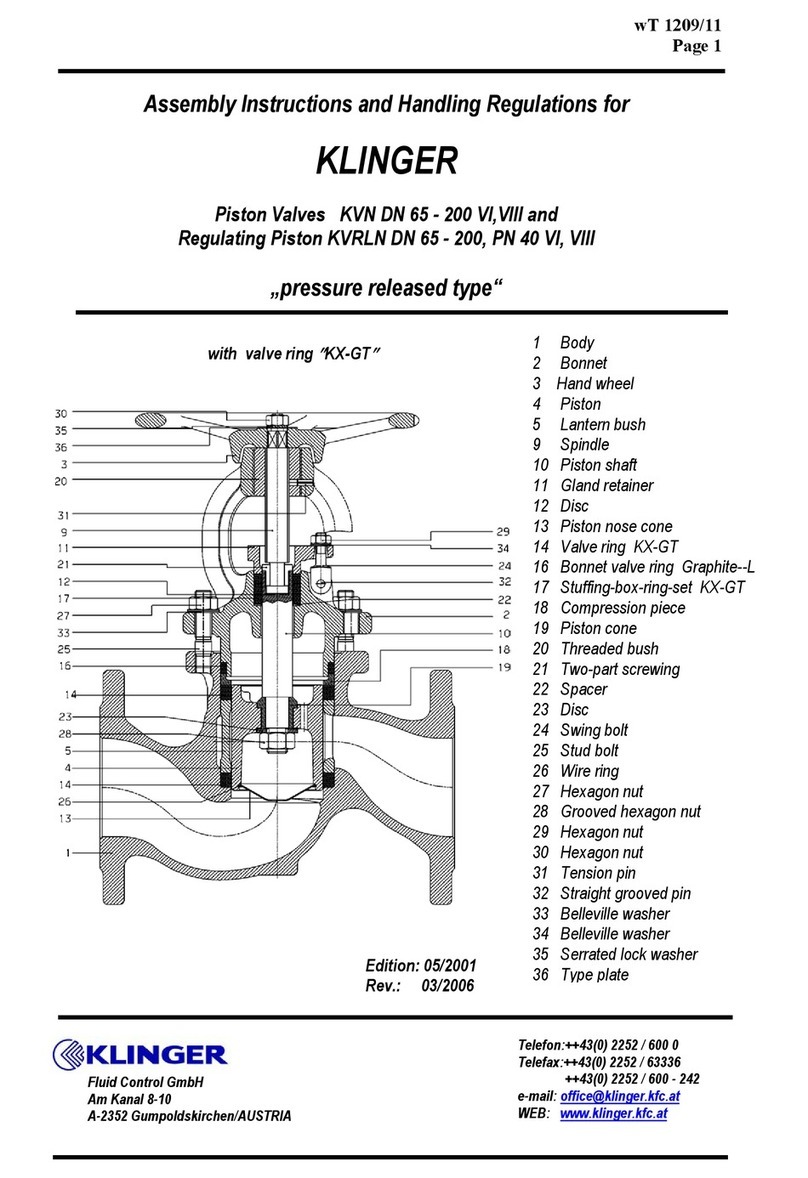
KLINGER
KLINGER KVN DN 65 User manual
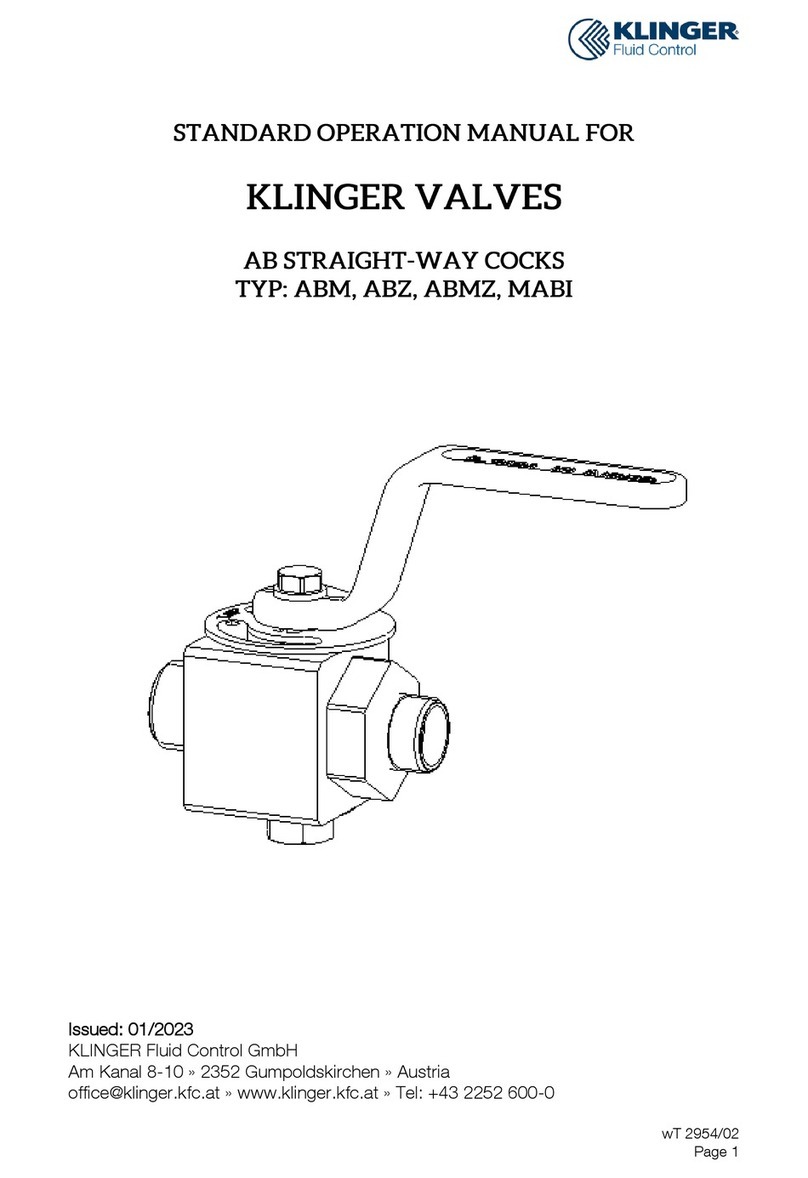
KLINGER
KLINGER ABM User manual
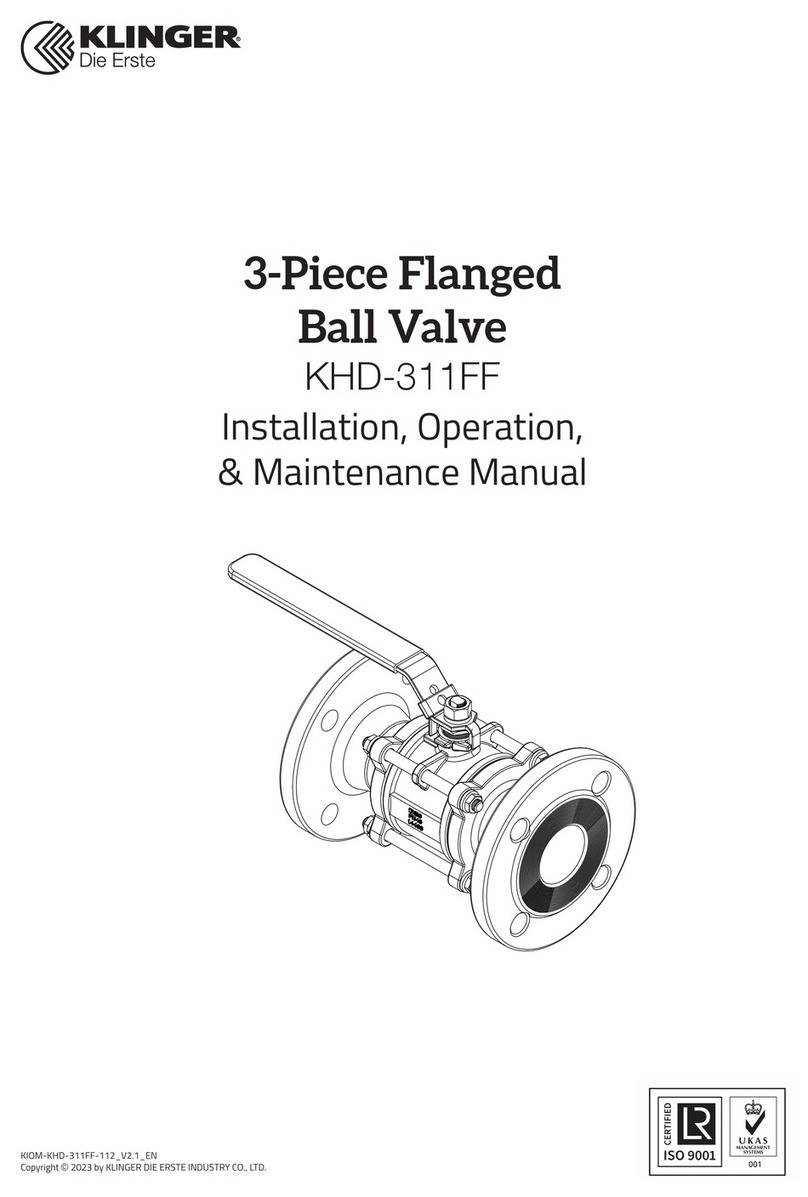
KLINGER
KLINGER KHD-311FF Instruction manual
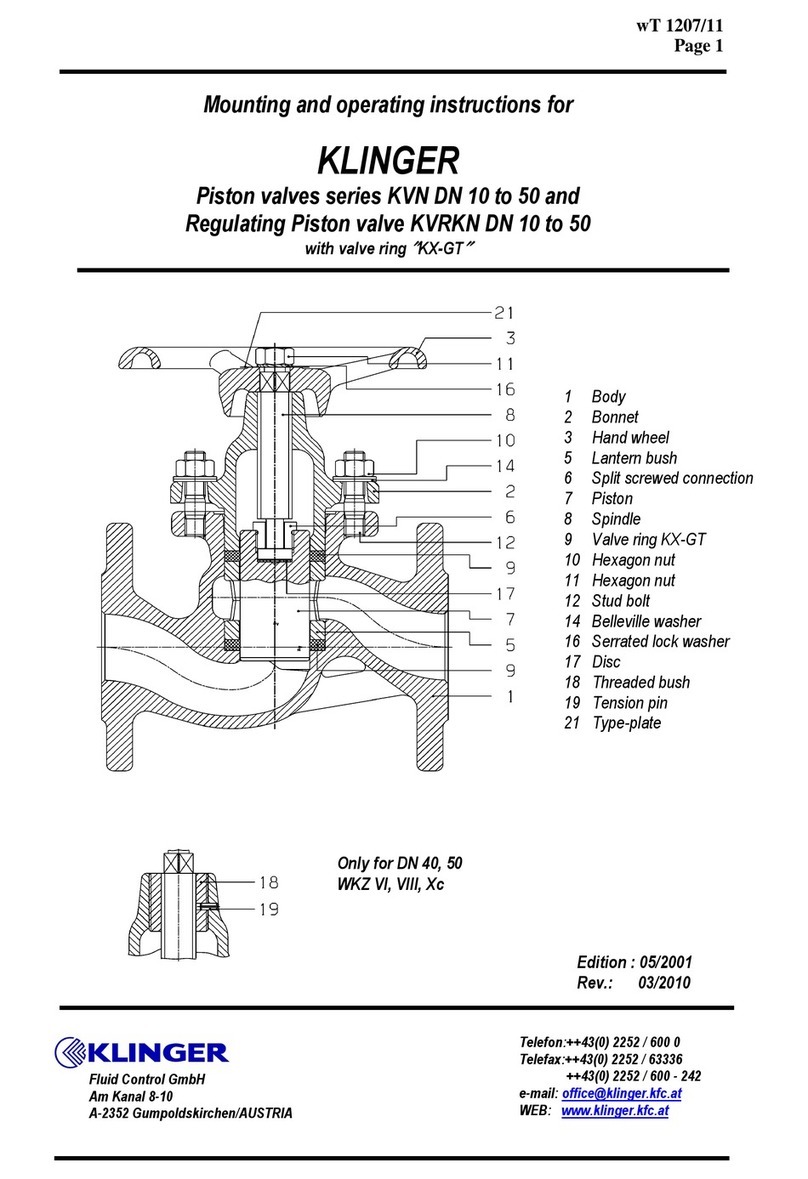
KLINGER
KLINGER KVN Series Service manual
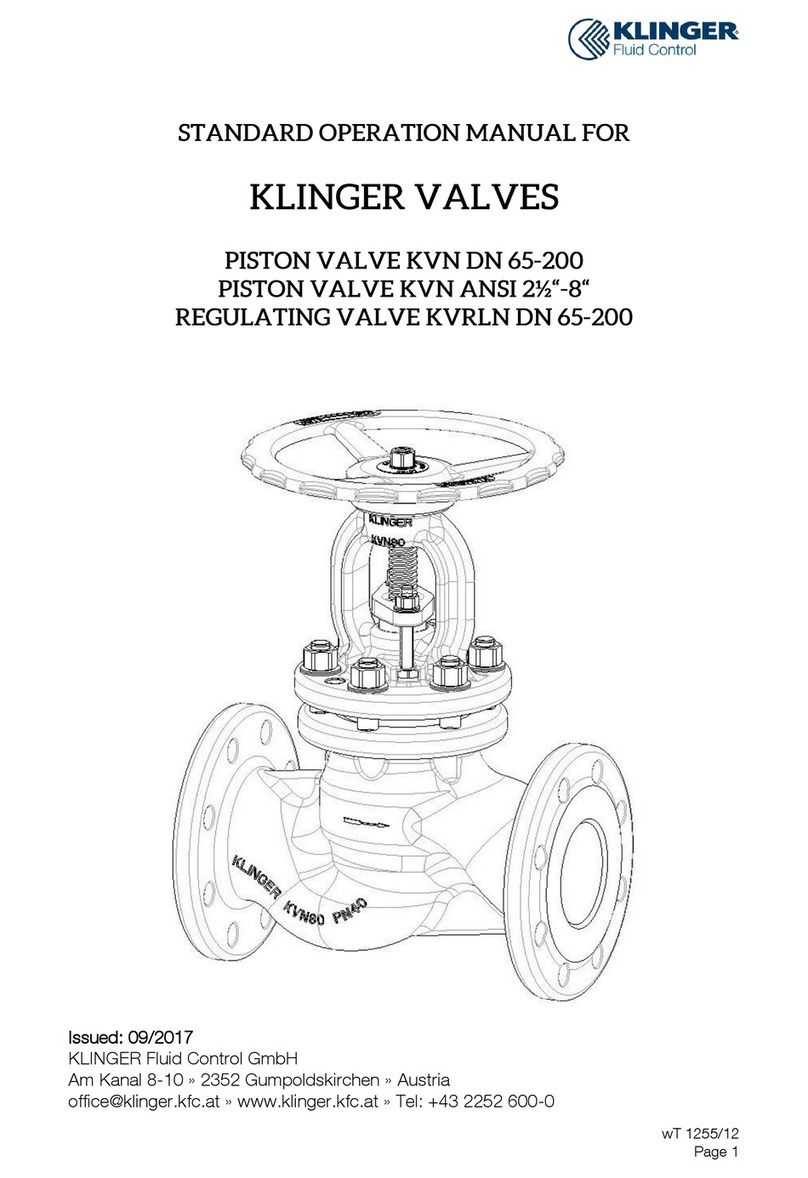
KLINGER
KLINGER KVN Series User manual
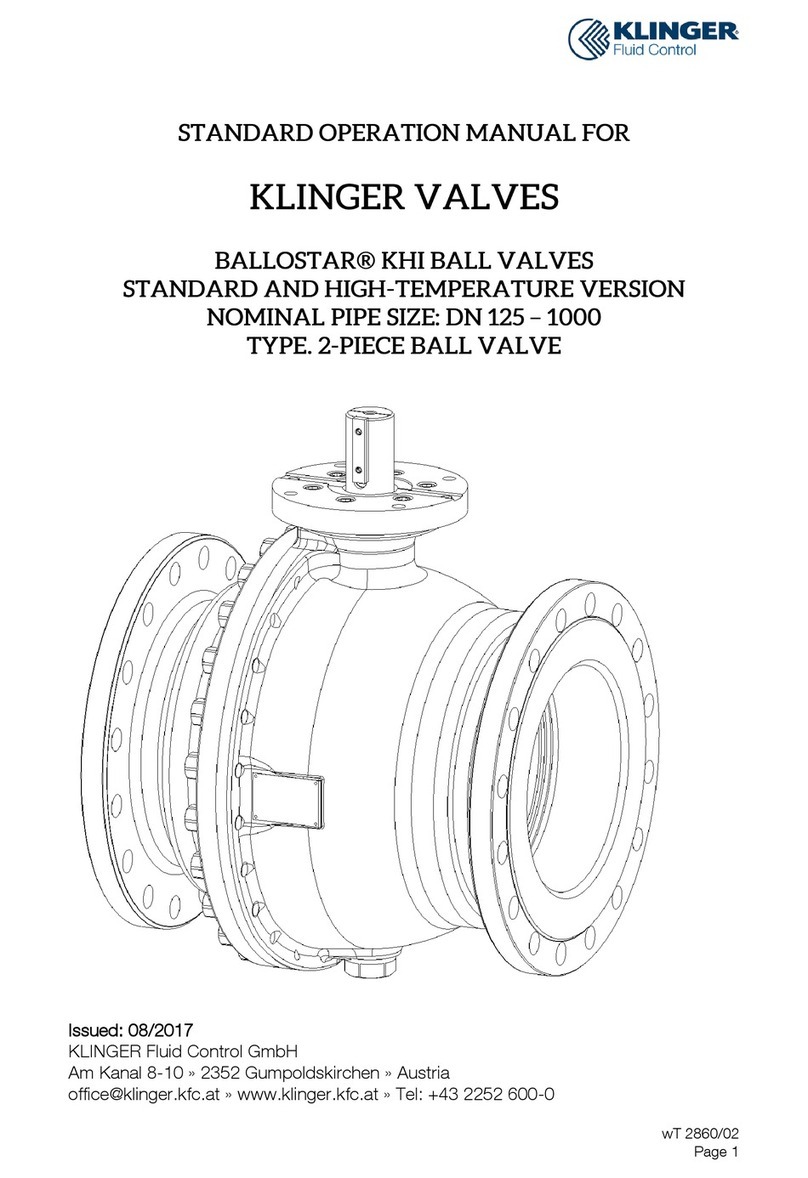
KLINGER
KLINGER BALLOSTAR KHI User manual
Popular Control Unit manuals by other brands
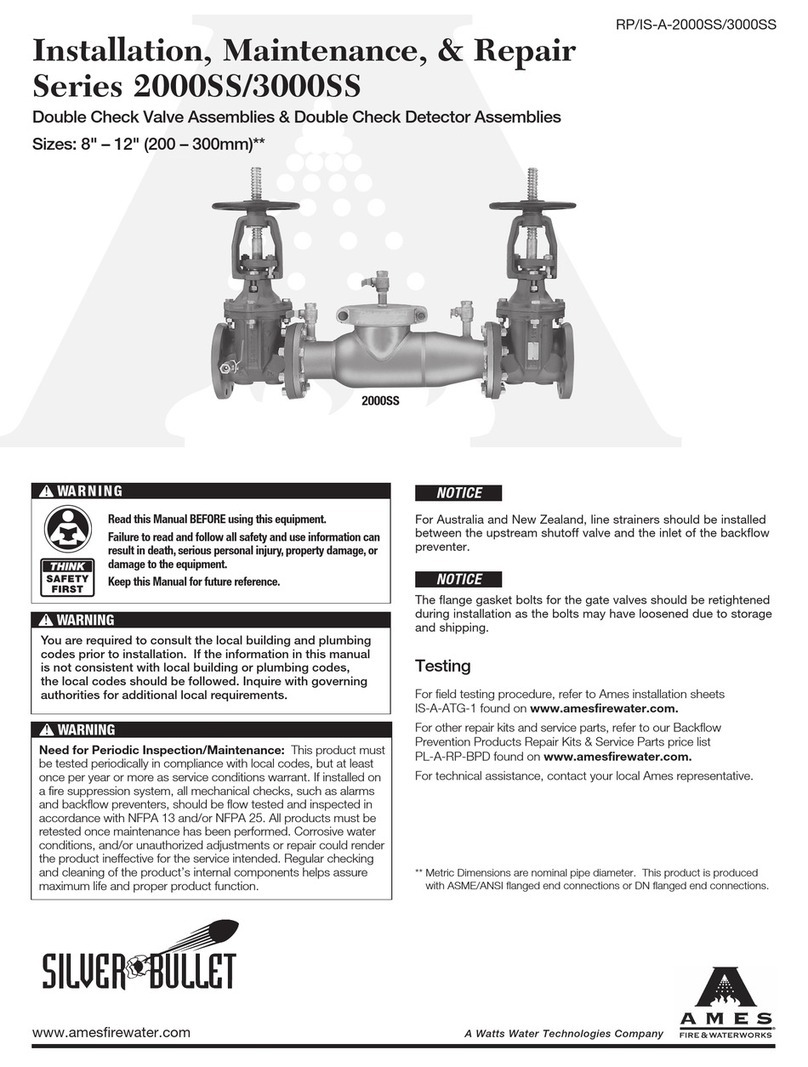
AMES
AMES 2000SS Series Installation, maintenance & repair
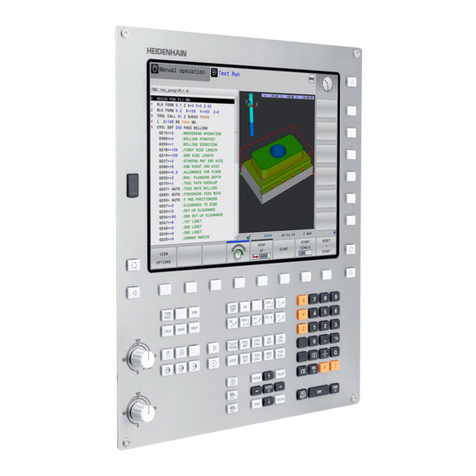
HEIDENHAIN
HEIDENHAIN TNC 320 Programming Station User's manual for cycle programming
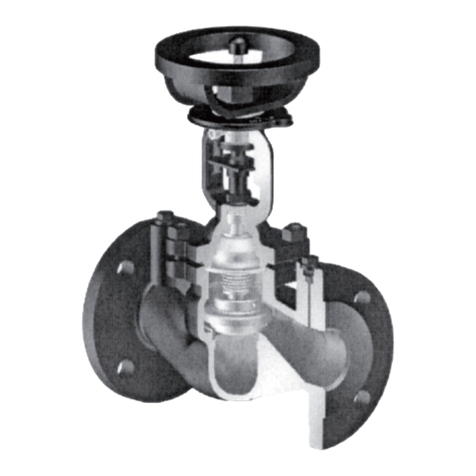
Danfoss
Danfoss MSV-F Plus DN 15 instructions
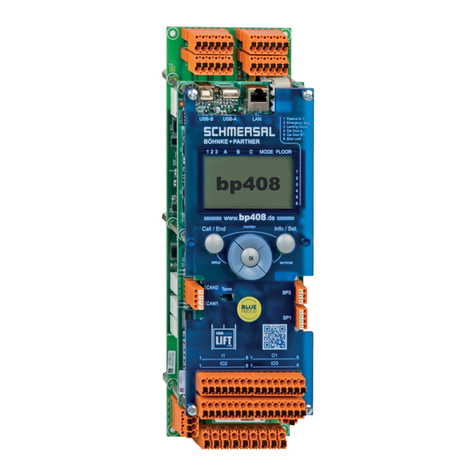
schmersal
schmersal bp408 installation manual

Toto
Toto RENESSE TSKA Installation and owner's manual
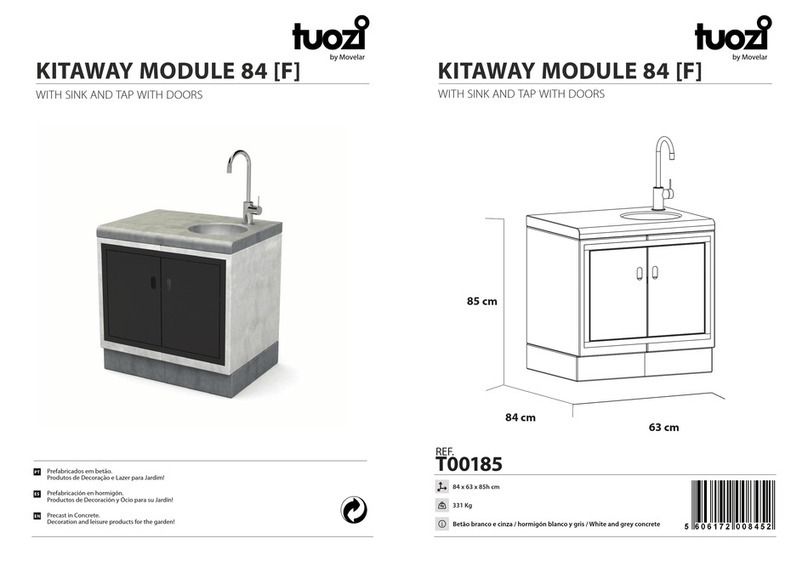
Movelar
Movelar tuozi KITAWAY MODULE 84 F manual