KLINGER KVN Series Service manual














Other manuals for KVN Series
1
This manual suits for next models
3
Other KLINGER Control Unit manuals
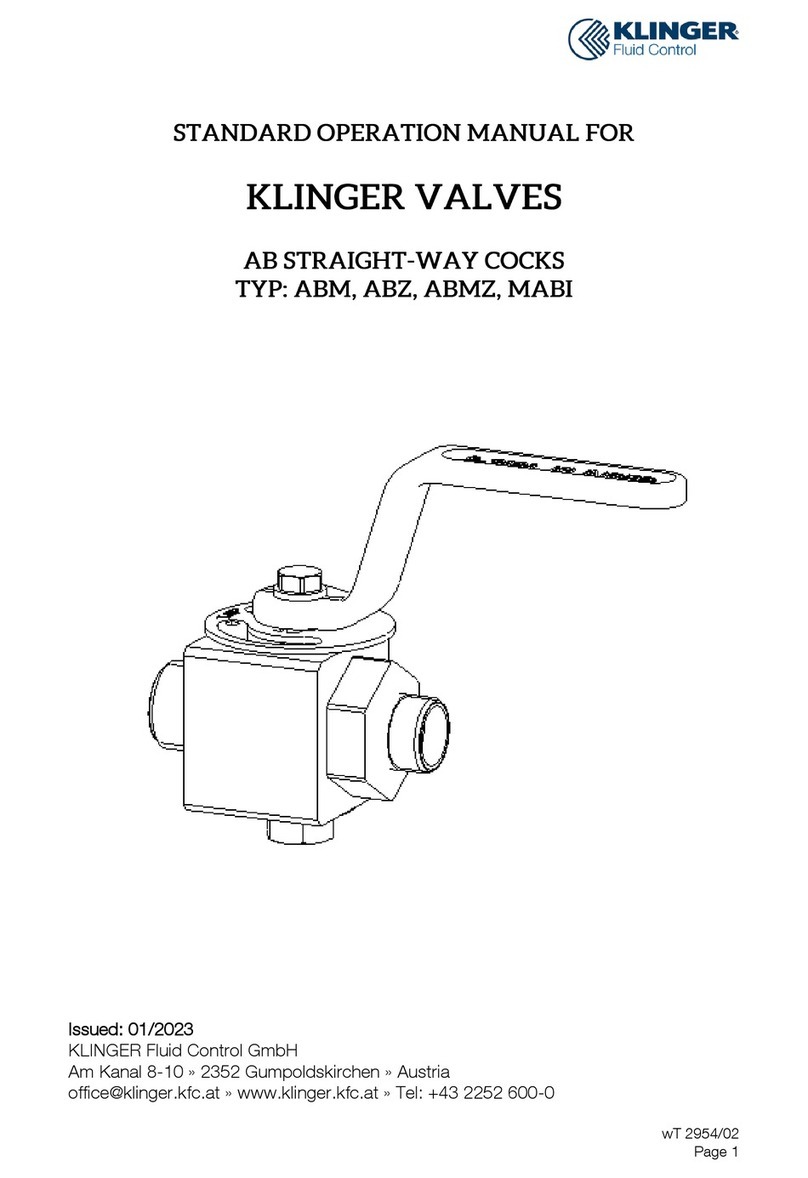
KLINGER
KLINGER ABM User manual
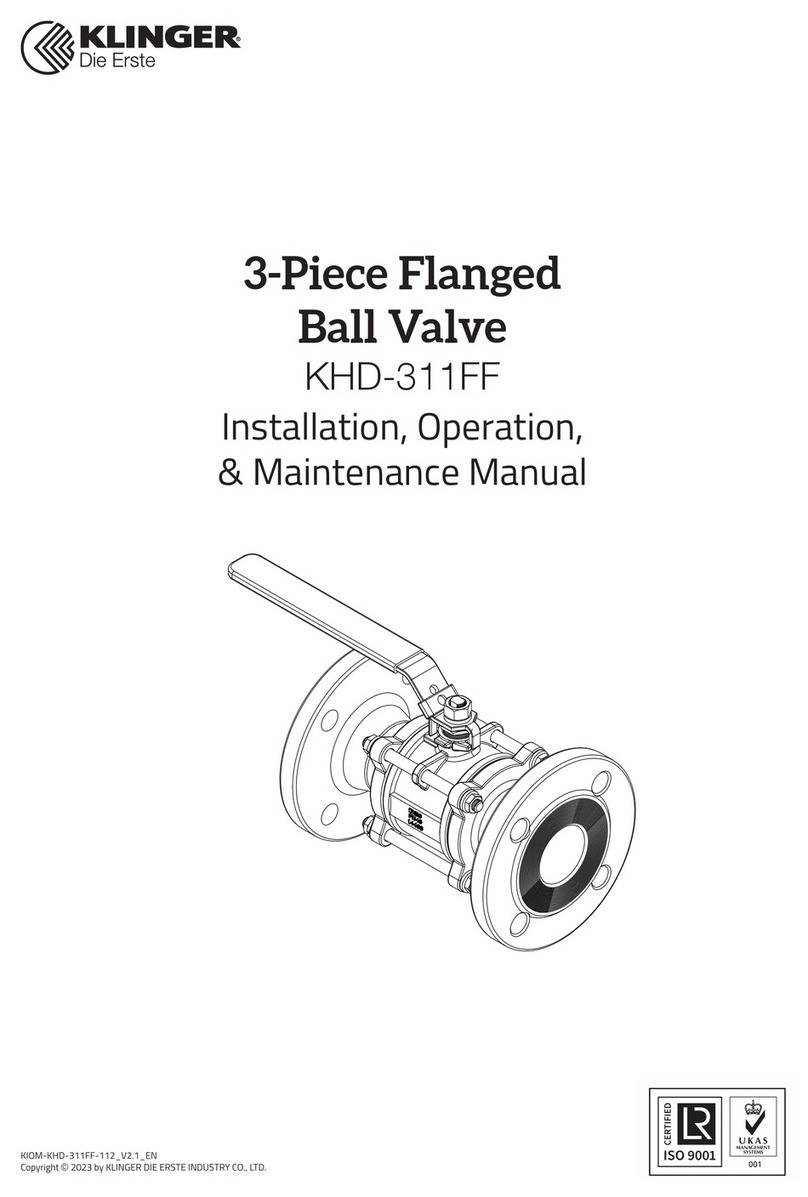
KLINGER
KLINGER KHD-311FF Instruction manual
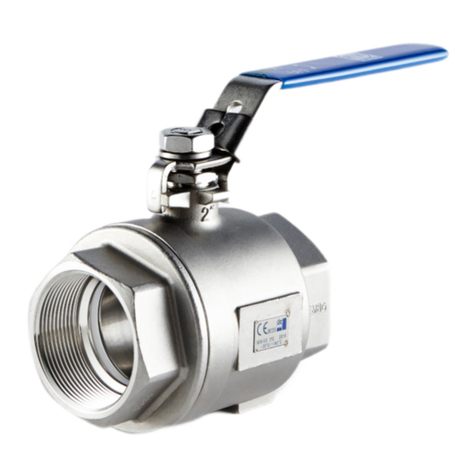
KLINGER
KLINGER KHD-21E Instruction manual
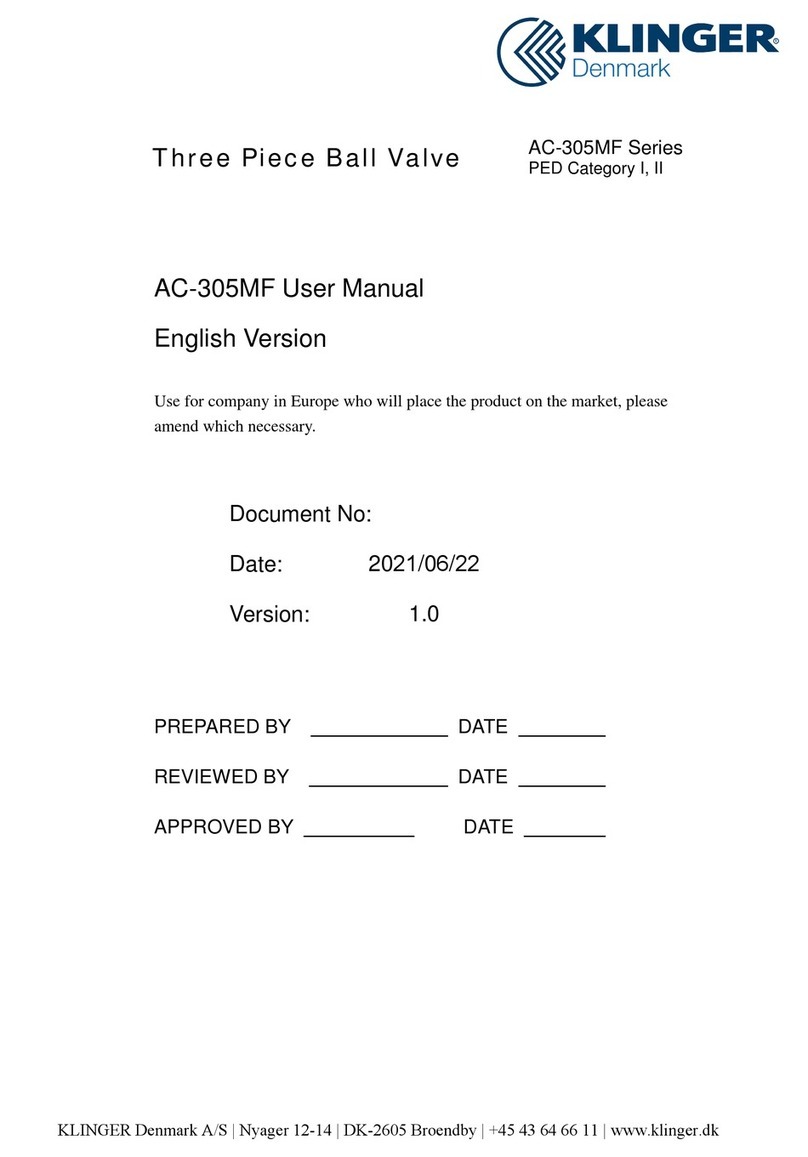
KLINGER
KLINGER AC-305MF User manual
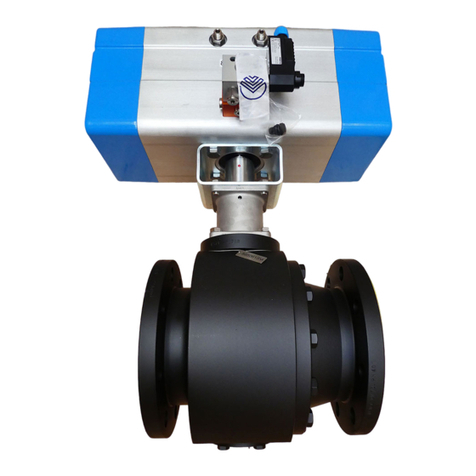
KLINGER
KLINGER INTEC K210-FS Setup guide
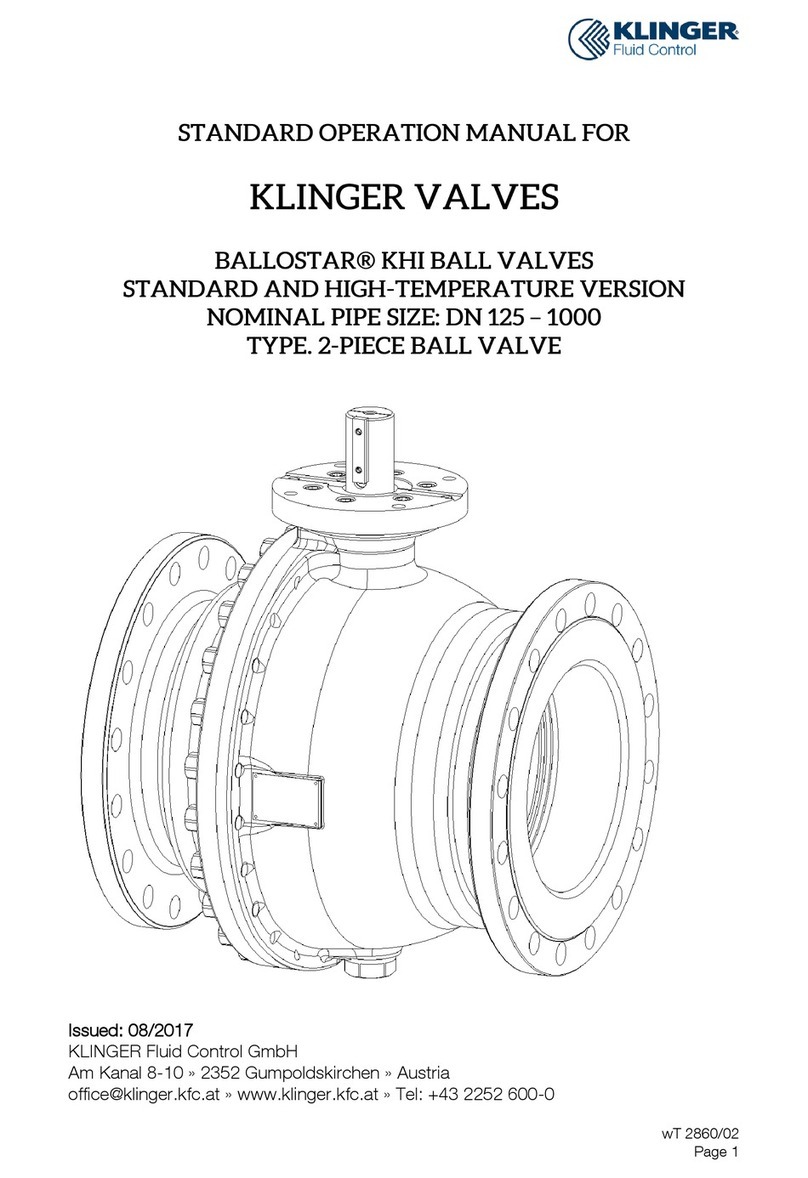
KLINGER
KLINGER BALLOSTAR KHI User manual
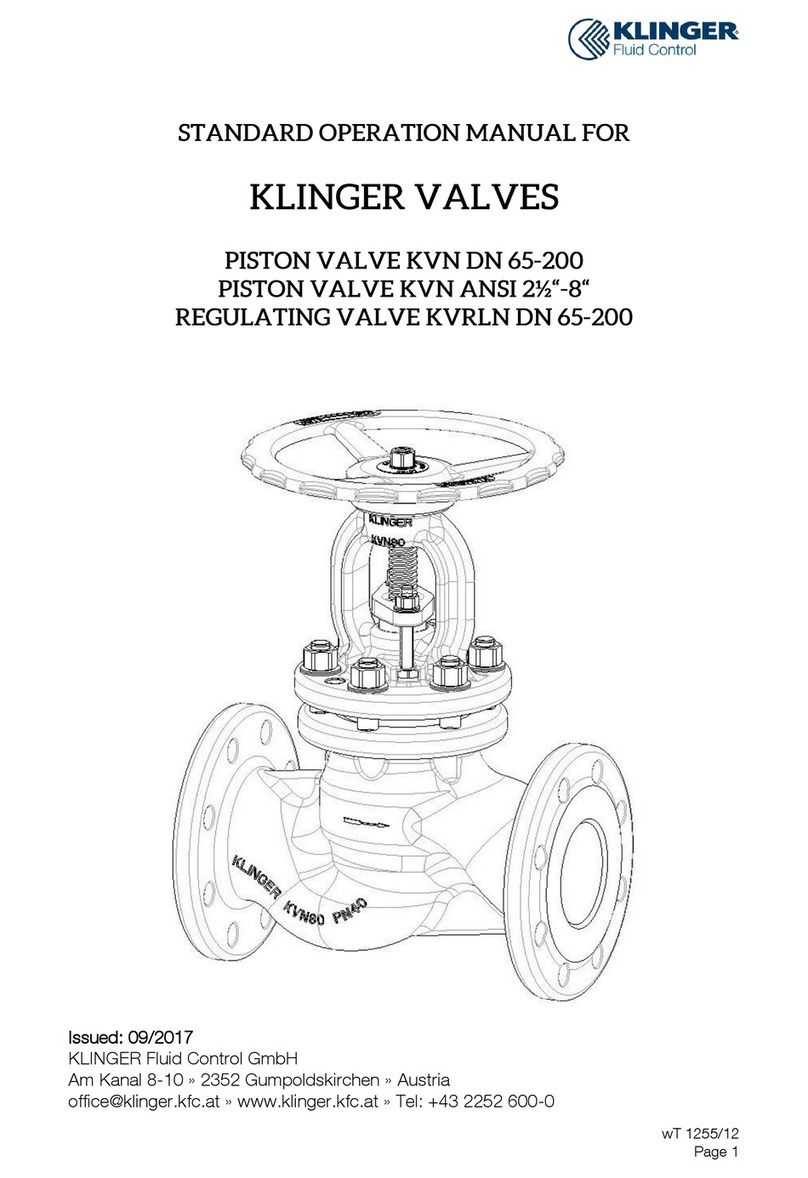
KLINGER
KLINGER KVN Series User manual
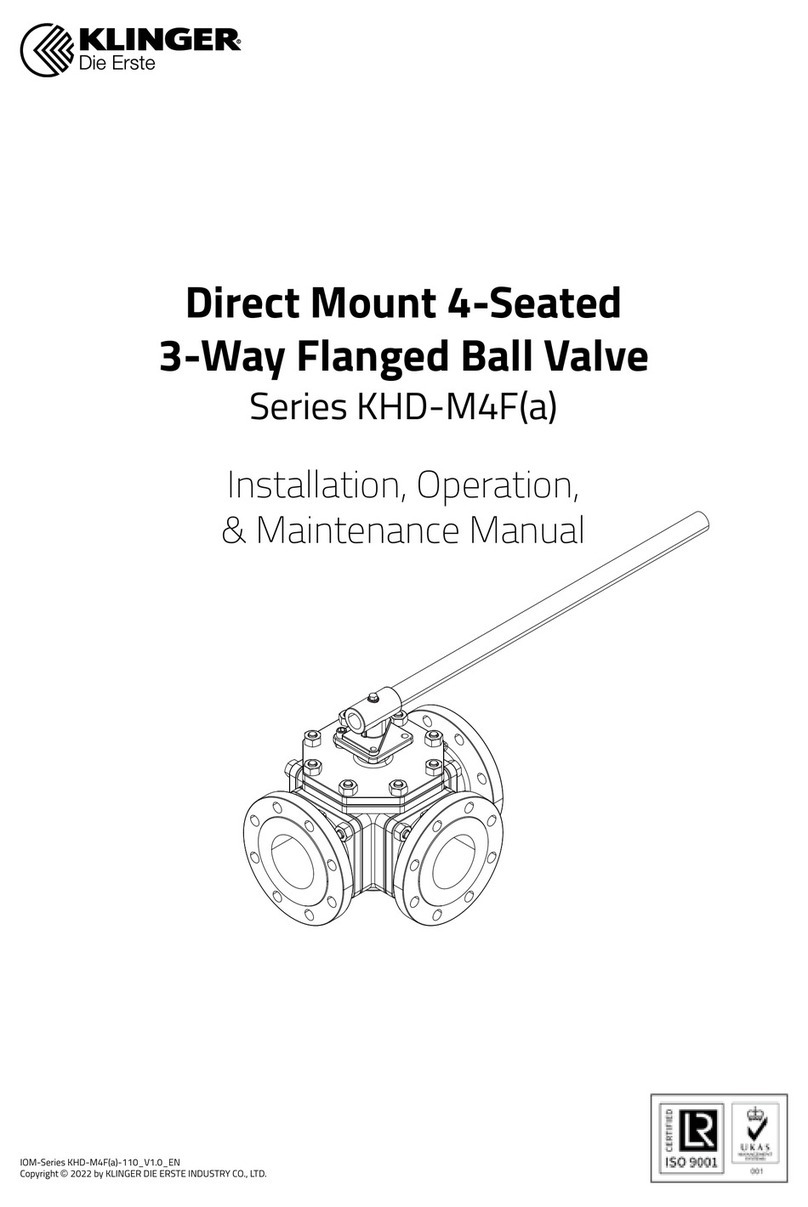
KLINGER
KLINGER KHD-M4F Series Instruction manual
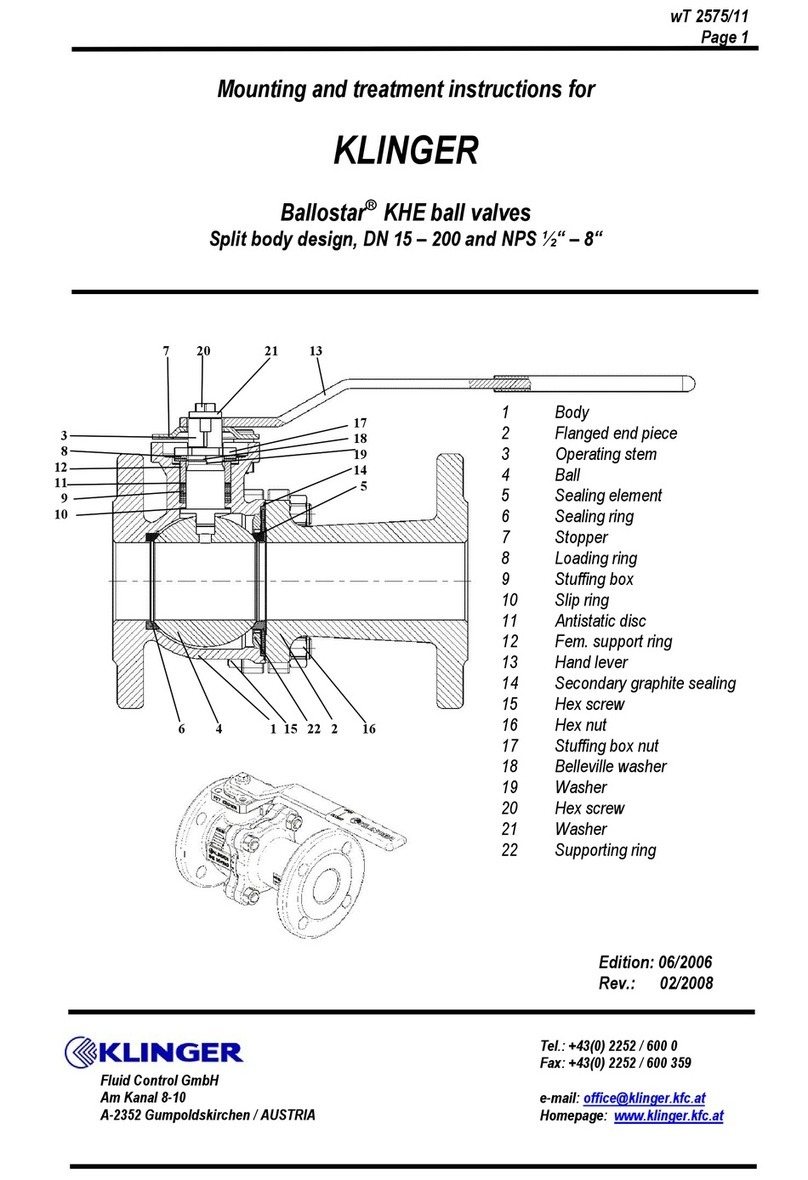
KLINGER
KLINGER Ballostar KHE Guide

KLINGER
KLINGER 3530 Owner's manual
Popular Control Unit manuals by other brands
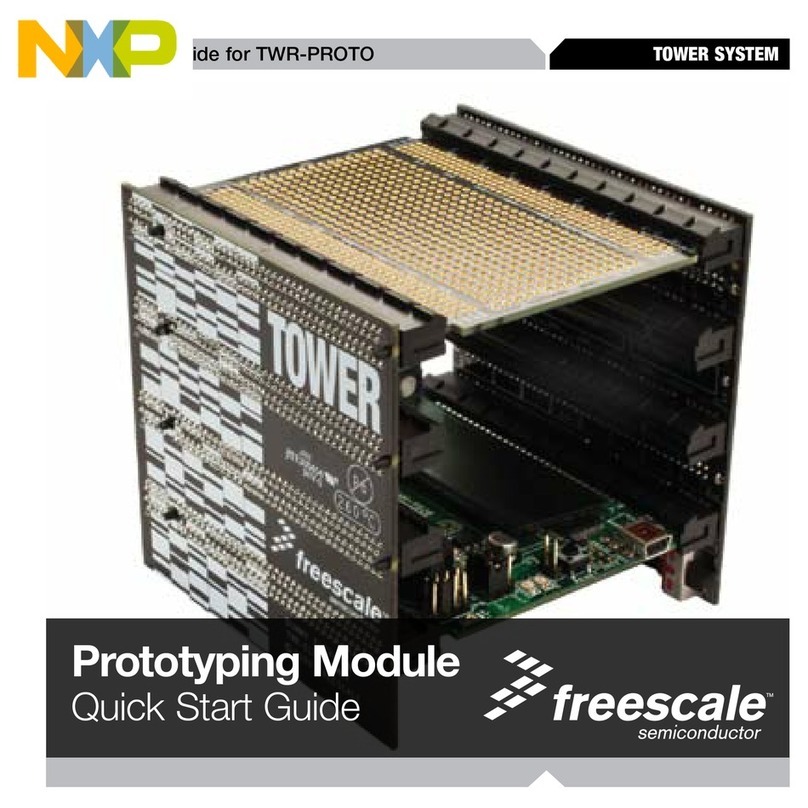
NXP Semiconductors
NXP Semiconductors TWR-PROTO quick start guide
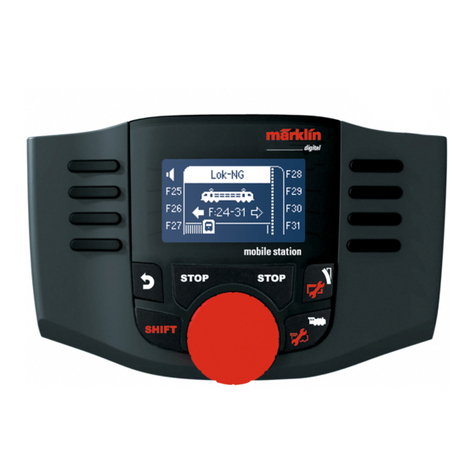
Marklin Digital
Marklin Digital 60653 Instruction
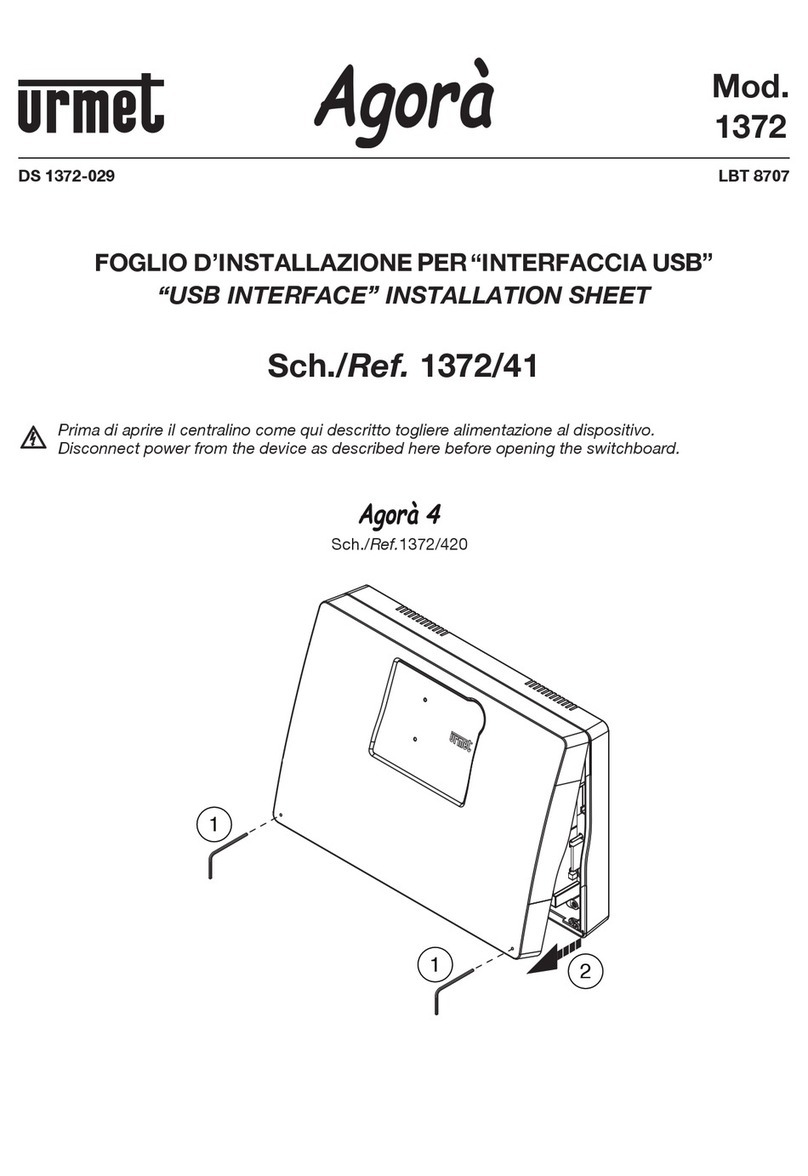
urmet domus
urmet domus Agora Installation sheet
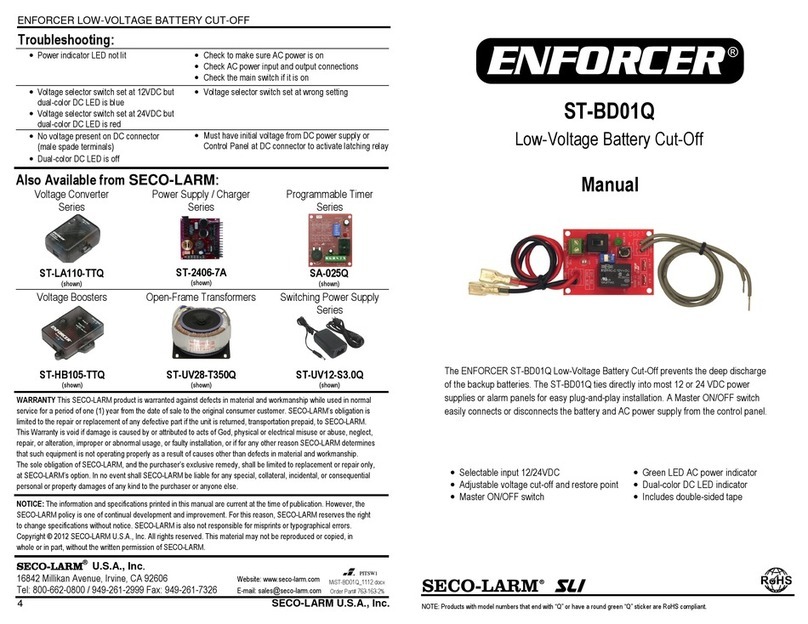
ENFORCER
ENFORCER ST-BD01Q manual
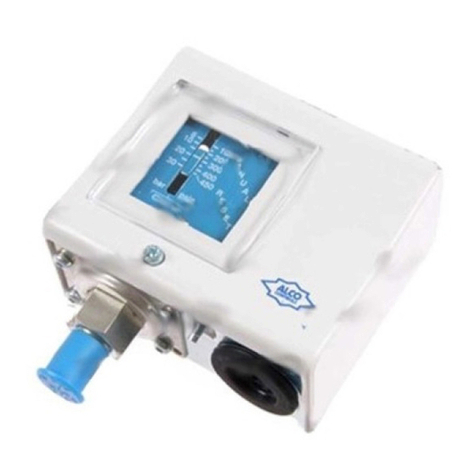
ALCO CONTROLS
ALCO CONTROLS PS1 Series operating instructions

Keysight Technologies
Keysight Technologies 11713B Operating and service manual
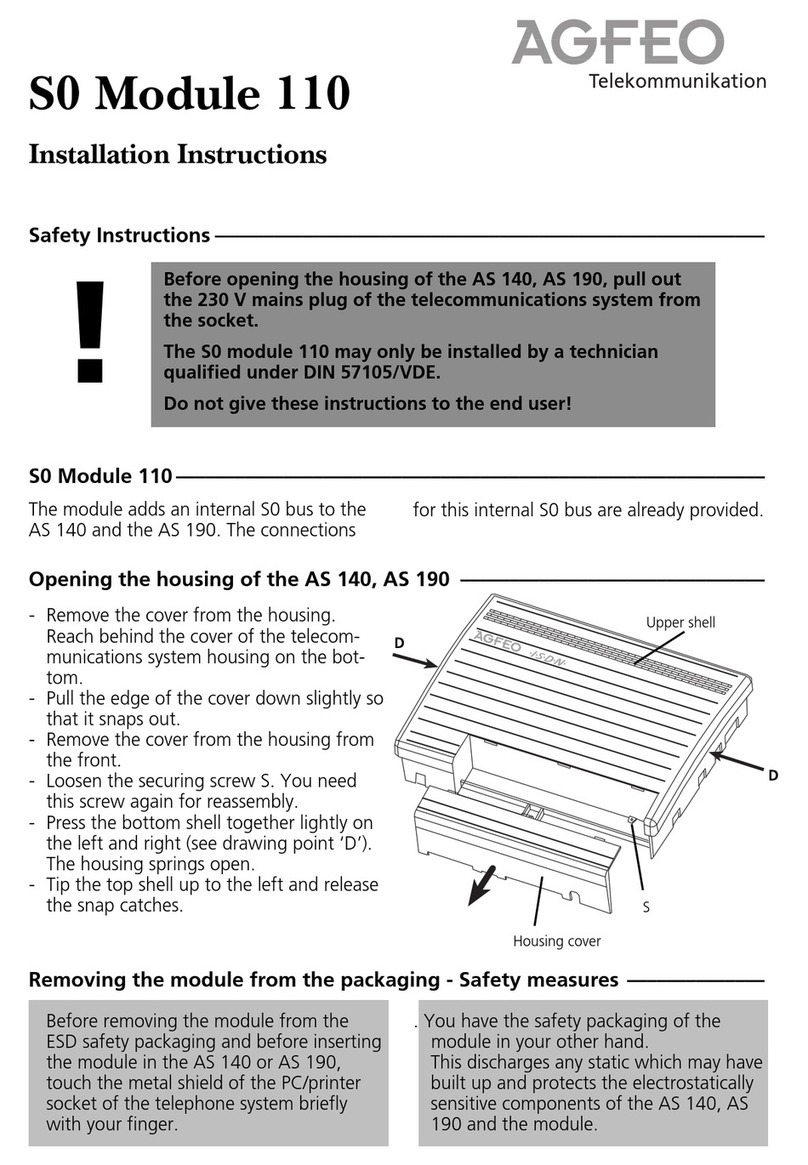
AGFEO
AGFEO S0 Module 110 installation instructions
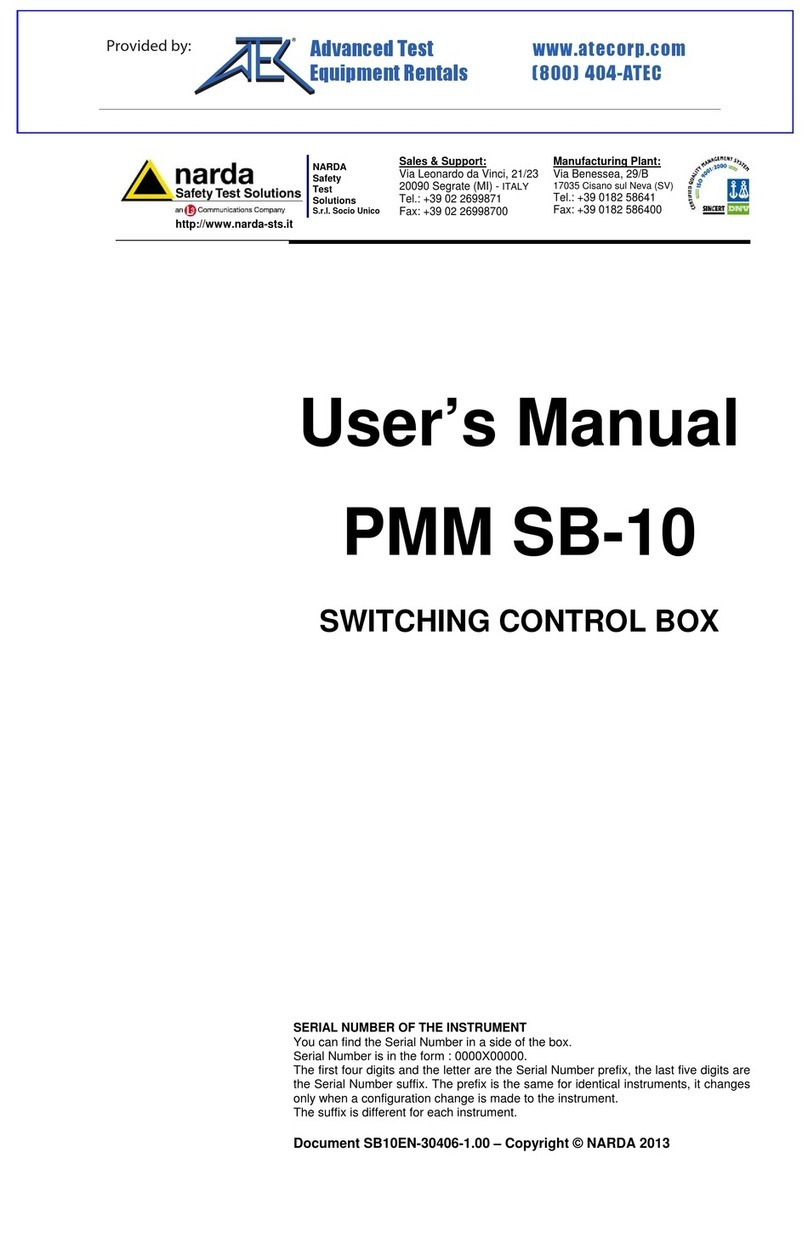
NARDA
NARDA PMM SB-10 user manual
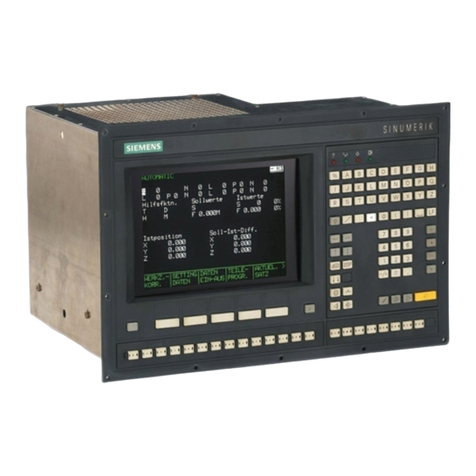
Siemens
Siemens SINUMERIK 880 SW 6 Planning guide
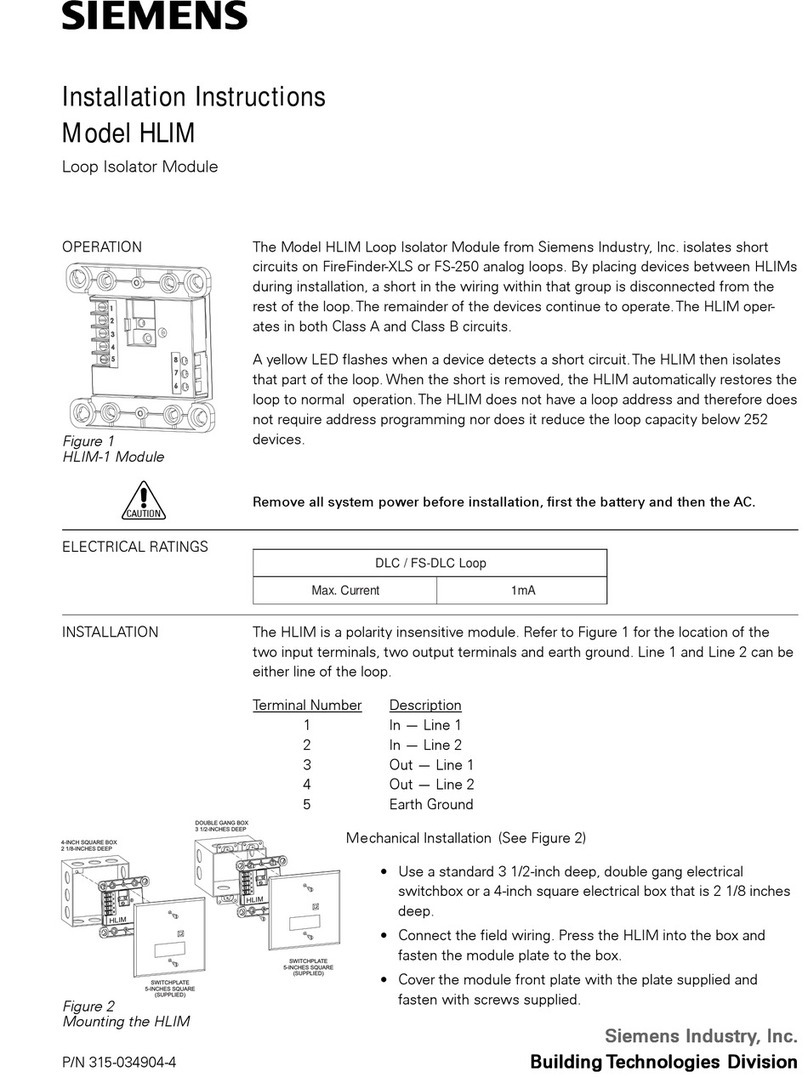
Siemens
Siemens HLIM Installation instructions manual
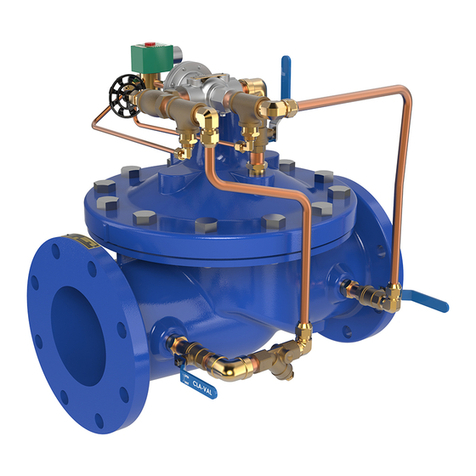
CLA-VAL
CLA-VAL 600 Series Installation operation & maintenance
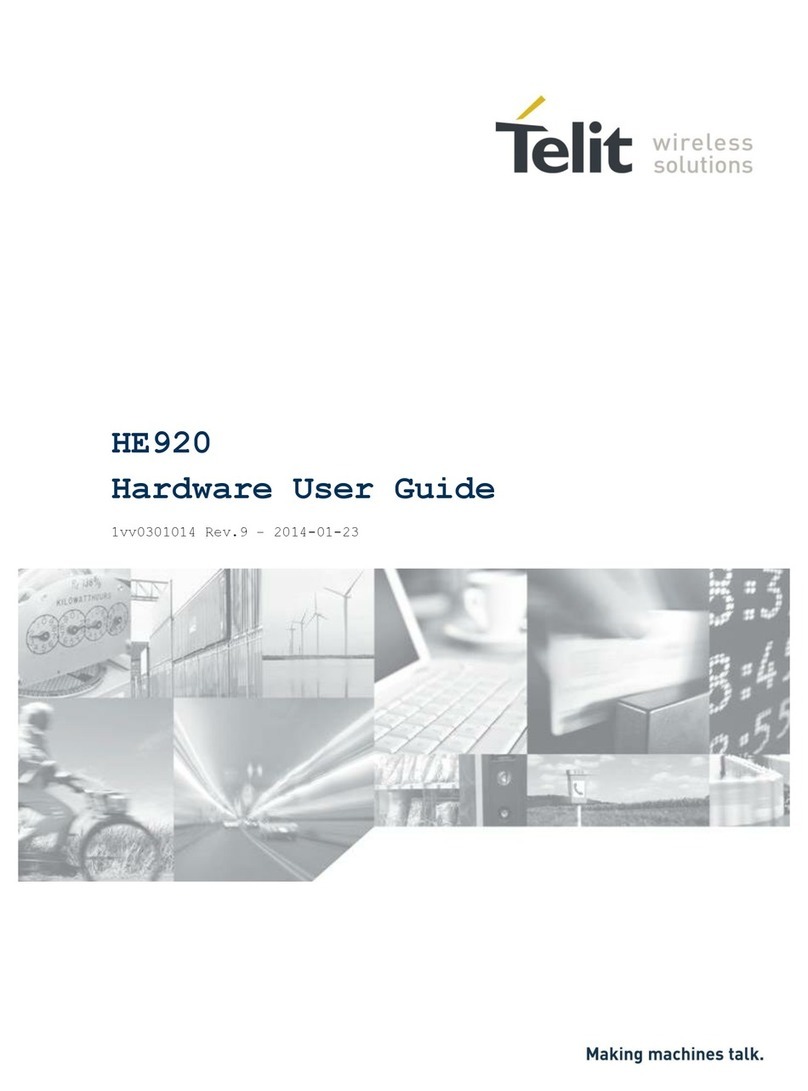
Telit Wireless Solutions
Telit Wireless Solutions HE920-NA Hardware user's guide