Kohzu Precision SC-021 User manual

Stepping Motor Controller
SC-021 RC-010
Pioneering the door to the future with a commitment to technology
KOHZU Precision Co., Ltd.
Introduction Manual
● Thank you for purchasing this product.
● Before operating this product, carefully review this Manual in its entirety
to ensure its proper and safe use. Always keep this Manual in a
convenient location, for future reference.
Ver. 1.00
N
ote: this version does not correspond with
the latest controller version.

Introduction
Greeting
Thank you for purchasing Kohzu’s Stepping Motor Controller, model SC-021 / RC-010. This
manual covers safe handling, operating procedures and precautions for the SC series
controller. For proper and safe use of this product, carefully review this manual in its
entirety.Always keep this manual in a convenient location, for future reference.
禁止
Avoid crushing, dropping, or any strong impact.
Do not use in an area subject to frequent
vibrations.
禁止
Avoid operating in an area where any liquids or
chemicals can spill on the unit. This can cause
series injury and/or product failure.
注意
100V
Use 100VAC (50/60Hz) as a power supply.
禁止
This product is an electronic, high-precision piece
of equipment. Avoid operating near large
machinery, high voltage equipment, or equipment
generating strong magnetism. Doing so can
results in product malfunction or failure.
禁止
Do not unnecessarily remove the fixed panel and
cover except in cases where adjustment or setting
of the integrated driver must be adjusted.
禁止
Never attempt to modify, rework or replace parts
yourself. This should only be done by a Kohzu
technician.
注意
?
Pay close attention when connecting the motor
driven stage or a motor other than those specified
by Kohzu.
To use safel
y
Prohibition
Prohibition
Caution
Prohibition
Prohibition
Prohibition
Caution

SC-021/RC-010 Introduction Manual / INDEX
i
INDEX ・・・ i
I. Basic Version ・・・ 1
0-0. Part Identification ・・・ 2
0-1. Status Display LED ・・・ 4
0-2. Connection Method ・・・ 5
0-3. Turning on Power and Starting Up ・・・ 6
1-0. ManuallyActuating a Stage ・・・ 7
1-1. Performing a Manual Scan Drive ・・・ 8
Scan Drive Operation ・・・ 8
Speed Setting ・・・ 9
1-2. Performing a Manual Origin Return ・・・ 10
Origin Return Operation ・・・ 10
Speed Setting ・・・ 11
1-3. Performing a ManualAbsolute Position Movement ・・・ 12
Absolute Position Movement Operation ・・・ 12
Setting of Movement Position ・・・ 13
Speed Setting ・・・ 13
1-4. Performing a Manual Relative Position Movement ・・・ 14
Relative Position Movement Operation ・・・ 14
Setting of Movement Position ・・・ 15
Speed Setting ・・・ 15
2-0. Manually Rewriting Present Position ・・・ 16
Setting of Rewriting Present Position ・・・ 16
INDEX

SC-021/RC-010 Introduction Manual / INDEX
ii
II. Practical Version ・・・ 17
0. Introduction to Detailed Setting Functions ・・・ 18
1. Accessing the System Setting Screen ・・・ 20
Setting the Item Code Values ・・・ 22
List of System Setting Items and Item Codes ・・・ 24
2. Manually Setting the Drive Speed ・・・ 26
Rewriting of Speed Tables 1 to 9 (SP1 to SP9) ・・・ 26
Rewriting of Speed Table 0 (SP0) ・・・ 28
Setting of Acceleration and Deceleration Mode ・・・ 30
Rewriting Acceleration and Deceleration Times for Speed Table 0 (SP0) ・・・ 32
3. Manually Setting Origin Return ・・・ 34
Setting Origin Return Mode ・・・ 34
Setting Preset Position ・・・ 36
4. Converting Pulse Number to Real Distance/Angle ・・・ 37
Setting Conversion Coefficient ・・・ 37
Setting Number of Digits for Displayed Data ・・・ 39
5. Converting Encoder Value to Real Distance/Angle ・・・ 40
Setting Conversion Coefficient ・・・ 40
Setting Number of Digits for Displayed Data ・・・ 42
Setting Encoder Pulse Multiplier ・・・ 43
6. Manually Performing Encoder Correction ・・・ 44
Setting Encoder Correction ・・・ 44
Solutions to Encoder Correction Conditions ・・・ 45
7. Manually Performing Backlash Correction ・・・ 48
Setting Backlash Correction Command ・・・ 48
Setting Number of Pulses for Backlash Correction ・・・ 49
8. Changing How Data is Displayed on LCD ・・・ 50
Changing First Data Line ・・・ 50
Changing Second Data Line ・・・ 52
9. Manually Setting Pulse Number in Scan Drive Operation ・・・ 53
Setting Number of Pulses in SCN Mode… Scan Drive Operation ・・・ 53

I. Basic Version

SC-021/RC-010 Introduction Manual/ Basic Version
2
0-0. Part Identification
Front
Rear
Model: SC-021
Power Switch
Power Connector Cooling Fan
Status Display LED Power indicator LED
RC-010 Connector
RS-232C Connector
Drive Connector 1
(PM1)
Drive Connector 2
(PM2)
Encoder Connector 1
Encoder Connector 2

SC-021/RC-010 Introduction Manual/ Basic Version
3
Md PE Ax Sp Val
S P 1 0 0
P 2 1 0
Model: RC-010
LCD Panel
Numeric Keypad
Dial-Key
SC-021 Connector
SET Button
ESC Button
CLR Button
LCD Panel Display Magnified View (Example)
1
4
3
5
2
3.Drive Axis No.
1/2
4.Drive Speed
0 to 9
5.Readout Numbers
1.Drive Operation
S: Scan
O: Origin Return
A: Absolute Position Movement
R: Relative Position Movement
2.Pulse/Encoder Display
P:Amount of Motor-Pulses
p: Conversion Data Relating to Motor-Pulses
E: Amount of Encoder-Pulses
e: Conversion Data Relating to Encoder

SC-021/RC-010 Introduction Manual/ Basic Version
4
0-1.Status Display LED
Status BUSY CW LMT
(CW Limit)
CCW LMT
(CCW Limit)
NORG
(NORG Sensor)
ORG
(ORG Sensor)
L
Li
ig
gh
ht
t
O
On
n
On driving ON ON ON ON
L
Li
ig
gh
ht
t
O
Of
ff
f
Waiting for
command OFF OFF OFF OFF
BUSY
CW LMT CCW LMT
NORG ORG
1
2

SC-021/RC-010 Introduction Manual/ Basic Version
5
0-2.Connection Method
RS-232C Cable
Power
Cable
Motor Cable
Encoder Cable
100V
SC-021 Front
SC-021 Rear
Cable connected to
RC-010
Encoder

SC-021/RC-010 Introduction Manual/ Basic Version
6
Display on screen after power is turned on
Md PE Ax Sp Val
K O H Z U P re c i s i o n
R C - 1 0 V e r . # . # #
Md PE Ax Sp Val
C o n t r o l l e r i s
S C - 0 2 0 V e r . # . # #
Md PE Ax Sp Val
D a t a L o a d i n g ! !
N O 1 # # / 1 0 0
Md PE Ax Sp Val
S P 1 0 0
P 2 0 0
Initial State
0-3.Turning on Power and Starting Up
Power Switch
Power On
Logo
RC-010 Version
SC-021 Version
Sequence of Events at Start-Up:
Power ON, Logo, Version, Controller Information, Message and
Initial State are displayed in this order.
(Once Initial Status is displayed, the initialization of SC Series is complete.)
SC-021 Front
Retrieving
last data
RC-010 LCD Panel
N
No
ot
te
e:
:
Kohzu SC series controller will always default to the last saved information. Therefore, the
initial state information may differ from what is shown above.

SC-021/RC-010 Introduction Manual/ Basic Version
7
1-0. Manually Actuating a Stage
This controller has four drive modes… Scan, Origin Return, Absolute Position Movement,
and Relative Position Movement.
When changing drive modes at drive setting status, navigate up or down using the dial-key.
Relative position movement (REL)
See page 14
Scan Drive (SCN)
See
p
a
g
e 8
Md PE Ax Sp Val
O P 1 0 0
P 2 0 0
Md PE Ax Sp Val
R P 1 0 0
P 2 0 0
Md PE Ax Sp Val
A P 1 0 0
P 2 0 0
Origin return (ORG)
See page 10
Md PE Ax Sp Val
S P 1 0 0
P 2 0 0
Chan
g
in
g
drive mode
Chan
g
in
g
drive mode
Chan
g
in
g
drive mode
Dial-key moving up or down
Dial-key moving up or down
Dial-key moving up or down
Dial-key moving up or down
Chan
g
in
g
drive mode
Absolute position movement (ABS)
See page 12

SC-021/RC-010 Introduction Manual/ Basic Version
8
SCN
1st axis, positive move 1st axis, negative move
2nd axis, negative move
2nd axis, positive move
1st axis, positive
2nd axis, negative move
1st axis, positive
2nd axis, positive move 1st axis, negative
2nd axis, positive move
1st axis, negative
2nd axis, negative move
Switch to Scan Drive mode at the Drive Setting Status screen by moving dial-key up or down.
To start scan, press and hold one of the directional keys on the key pad(see diagram below).
Md PE Ax Sp Val
S P 1 0 0
P 2 0 0
To stop scan, release the key. Note: Once a button is pressed, don’t press any other button until
completion of last movement. Pushing buttons in succession causes misleading pulses in system.
Pulse Scanning
While in the Setting Status screen, press #5 to switch to Pulse Drive. By default, pressing any button
repeatedly will drive only 1 pulse at a time. See page 53 to assign a set number of pulses.
Once the number of pulses is set, as with the Manual Scan Drive, press and hold the applicable
direction key to start. Release to stop.
When finished, return to Manual Scan Drive mode by pressing #5 button again.
Press #5
Md PE Ax Sp Val
sP 1 0 0
P 2 0 0
Md PE Ax Sp Val
S P 1 0 L # # # # # # # #
P 2 0 0
1-1. Performing a Manual Scan Drive
《Scan Drive Operation》
When either a CW or CCW limit is triggered, an “L” will automatically appear in display.

SC-021/RC-010 Introduction Manual/ Basic Version
9
Press “SET” button to drive in Manual High Speed (Default speed: #7 on Speed settings table below).
Press “CLR” button to drive in Manual Low Speed (Default speed: #1 on Speed setting table below).
Press “ESC” button to return to Normal speed (Default speed: #0 on Speed setting table below).
Press”ESC”
Press”CLR”
Press “SET”
Md PE Ax Sp Val
S P 1 1 0
P 2 1 0
Md PE Ax Sp Val
S P 1 0 0
P 2 0 0
Md PE Ax Sp Val
S P 1 7 0
P 2 7 0
Md PE Ax Sp Val
S P 1 0 0
P 2 0 0
Change to high speed
Change to low speed
Return to Normal speed setting
Note: For individual axes, see Section 1-2 “Performing a Manual Origin Return Operation “ on page 11.
You can also program additional speed settings within the default High and Low settings. See pages 20-21 for
more information.
《Using the Default Scan Speeds 》
<Speed settings>
Display on panel Top Speed Startup time Display on panel Top Speed Startup time
0 5000[pps]24[ms] 5 6000[pps]25[ms]
1 2000[
pp
s]21
[
ms
]
67000[
pp
s]26
[
ms
]
2 3000[
pp
s]22
[
ms
]
78000[
pp
s]27
[
ms
]
3 4000[
pp
s]23
[
ms
]
89000[
pp
s]28
[
ms
]
4 5000[
pp
s]24
[
ms
]
910000[
pp
s]29
[
ms
]
(The values above are default values. See page 26 for additional information.)
While in the Manual Scan Drive mode, you can quickly switch between the default High, Low and Normal speeds
Default Normal Setting

SC-021/RC-010 Introduction Manual/ Basic Version
10
《Origin Return Operation》ORG
Md PE Ax Sp Val
O P 1 0 0
P 2 0 0
Md PE Ax Sp Val
O P 1 0 L # # # # # # # #
P 2 0 0
When either a CW or CCW limit is triggered, an “L” will automatically appear in display.
Dual axis, origin return
1st axis, origin return
Dual axis, origin return 2nd axis, origin return
Stop
1st axis, origin return
2nd axis, origin return
Dual axis, origin return
Dual axis, origin return
To stop drive, press the same key or the “ESC” button.
1-2. Performing aManual Origin Return
Note: Operator has the option of using the Default Scan Mode Speeds, explained on page 9 of Section
1-1, or setting own default speed values, explained on page 11 of this section.
To start drive, press one of the directional keys on the keypad (see diagram below).
《
《N
No
ot
te
e》
》
The Origin Return Mode value is setting No.3 (Norg + Org) in the System Setting screen.
See
p
a
g
es 34 - 35 for additional information.
Switch to Origin Return mode at the Drive Setting Status screen by moving the dial-key up or down.

SC-021/RC-010 Introduction Manual/ Basic Version
11
ⅰ) Press dial-key at the Drive Setting Status screen until the cursor reaches the 1st axis speed setting position.
ⅱ) Set the 1st axis speed by moving the dial-key up or down.
ⅲ) Press dial-key at the Drive Setting Status screen until the cursor reaches the 2nd axis speed setting position.
ⅳ) Set the 2nd axis speed by moving the dial-key up or down.
ⅴ) When finished, press the dial-key to return to the Drive Setting status.
<Speed Settings>
Display on panel Top Speed Startup time Display on panel Top Speed Startup time
0 5000[pps]24[ms] 5 6000[pps]25[ms]
1 2000[
pp
s]21
[
ms
]
67000[
pp
s]26
[
ms
]
2 3000[
pp
s]22
[
ms
]
78000[
pp
s]27
[
ms
]
3 4000[
pp
s]23
[
ms
]
89000[
pp
s]28
[
ms
]
4 5000[
pp
s]24
[
ms
]
910000[
pp
s]29
[
ms
]
(The values above are default values. See page 26 for additional information.)
Press Dial-key
All set
Press Dial-key
Press Dial-key
Md PE Ax Sp Val
O P 1 0 0
P 2 0 0
Md PE Ax Sp Val
O P 1 0 0
P 2 0 0
Md PE Ax Sp Val
O P 1 1 0
P 2 0 0
Md PE Ax Sp Val
O P 1 1 0
P 2 0 0
Md PE Ax Sp Val
O P 1 1 0
P 2
10
Md PE Ax Sp Val
O P 1 1 0
P 2 1 0
Cursor moving Change drive speed
Cursor moving Change drive speed
Back to drive setting status
Note: To set one speed for multiple axes, see Section 1-1 "Manually Actuating a Stage" on
page 9.
Dial-key moving up and down
Dial-key moving up and down
《Setting Your Own Default Drive Speeds for Individual Axes》

SC-021/RC-010 Introduction Manual/ Basic Version
12
ABS
To start drive, press one of the directional keys on the keypad (see diagram below).
Switch to Absolute Position mode at the Drive Setting Status screen by moving the dial-key up or down
Md PE Ax Sp Val
A P 1 0 0
P 2 0 0
Md PE Ax Sp Val
A P 1 0 L # # # # # # # #
P 2 0 0
When either a CW or CCW limit is triggered, an “L” will automatically appear in display.
1st axis, absolute move
Stop
1st axis, absolute move
2nd axis, absolute move
2nd axis, absolute move
Dual axis, absolute move
Dual axis, absolute move
Dual axis, absolute move
Dual axis, absolute move
To stop drive, press the same key or the “ESC” button.
《Absolute Position Movement Operation》
1-3. Performing a ManualAbsolute Position
Movement
Note: Operator has the option of using the Default Scan Mode Speeds, explained on page 9 of Section
1-1, or setting own default speed values, explained on page 11 of Section 1-2.

SC-021/RC-010 Introduction Manual/ Basic Version
13
《Speed Setting》
To program Speed Settings, refer to page 11... Setting Your Own Default Drive Speeds for Individual
Axes, in Section 1-2.
All set
Md PE Ax Sp Val
A P 1 0 0
P 2 0 0
Md PE Ax Sp Val
A P 1 0 0
P 2 0 0
Md PE Ax Sp Val
A P 1 :A B S R e W r i t e
0 0 0 0 0 0 0 0 0 0 0
Md PE Ax Sp Val
A P 1 :A B S R e W r i t e
N N N N N N N N N N N
Md PE Ax Sp Val
A P 1 0 0
P 2 0 0
Cursor moving Displaying setting screen
Put numbers
Back to drive setting status
Move Dial-key down
Md PE Ax Sp Val
A P 1 :A B S R e W r i t e
- N N N N N N N N N N N
If necessary, put minus
ⅱ) Press the SET button to display the setting screen.
ⅲ) Set numbers using the keypad. Move the dial-key down to select a negative (-) number.
ⅳ) When finished, press the SET button again to return to the Drive Setting Status.
Press Dial-key
Press “SET”
Press “SET”
Put numbers
《Setting Movement Position – 1st Axis》
ⅰ) Press dial-key at the Drive Setting Status screen until the cursor reaches the 1st axis speed setting position.
ⅴ) To set the movement position for the 2nd axis, select the 2nd axis at step i and repeat steps ii - iv.

SC-021/RC-010 Introduction Manual/ Basic Version
14
REL
Md PE Ax Sp Val
R P 1 0 L # # # # # # # #
P 2 0 0
When either a CW or CCW limit is triggered, an “L” will automatically appear in display.
To start drive, press one of the directional keys on the keypad (see diagram below).
Switch to Absolute Position mode at the Drive Setting Status screen by moving the dial-key up or down
Md PE Ax Sp Val
R P 1 0 0
P 2 0 0
1-4. Performing a Manual Relative Position
Movement
《Relative Position Movement Operation》
1st axis, positive move 1st axis, negative move
2nd axis, negative move
2nd axis, positive move
1st axis, positive
2nd axis, negative move
1st axis, positive
2nd axis, positive move 1st axis, negative
2nd axis, positive move
1st axis, negative
2nd axis, negative move
Stop
To stop drive, press the same key or the “ESC” button.
Note: Operator has the option of using the Default Scan Mode Speeds, explained on page 9 of Section
1-1, or setting own default speed values, explained on page 11 of Section 1-2.

SC-021/RC-010 Introduction Manual/ Basic Version
15
All set
Press Dial-key
Press “SET”
Md PE Ax Sp Val
R P 1 0 0
P 2 0 0
Md PE Ax Sp Val
R P 1 0 0
P 2 0 0
Md PE Ax Sp Val
R P 1 :R E L R e W r i t e
0 0 0 0 0 0 0 1 0 0 0
Md PE Ax Sp Val
R P 1 :R E L R e W r i t e
N N N N N N N N N N N
Cursor moving Displaying setting
Move Dial-key down
Md PE Ax Sp Val
R P 1 0 0
P 2 0 0
Put numbers
Md PE Ax Sp Val
R P 1 :R E L R e W r i t e
- N N N N N N N N N N N
If necessary, put minus
Back to drive setting status Press “SET”
Put numbers
ⅱ) Press the SET button to display the setting screen.
ⅲ) Set numbers using the keypad. Move the dial-key down to select a negative (-) number.
ⅳ) When finished, press the SET button again to return to the Drive Setting Status.
《Setting Movement Position – 1st Axis》
ⅰ) Press dial-key at the Drive Setting Status screen until the cursor reaches the 1st axis speed setting position.
ⅴ) To set the movement position for the 2nd axis, select the 2nd axis at step i and repeat steps ii - iv.
《Speed Setting》
To program Speed Settings, refer to page 11... Setting Your Own Default Drive Speeds for Individual
Axes, in Section 1-2.

SC-021/RC-010 Introduction Manual/ Basic Version
16
All set
Md PE Ax Sp Val
S P 1 0 0
P 2 0 0
Md PE Ax Sp Val
S P 1 0 0
P 2 0 0
Md PE Ax Sp Val
S P 1 :P O S R e W r i t e
0 0 0 0 0 0 0 0 0 0 0
Md PE Ax Sp Val
S P 1 :PO S R e W r i t e
N N N N N N N N N N N
Md PE Ax Sp Val
R P 1 0 0
P 2 0 0
Changing drive mode
Displaying setting
Cursor moving
ⅱ) Press dial-key at the Drive Setting Status screen until the cursor reaches the 1st axis speed setting position.
ⅲ) Press the SET button to display the setting screen.
ⅳ) Set numbers using the keypad. Move the dial-key down to select a negative (-) number.
ⅴ) When finished, press the SET button again to return to the Drive Setting Status.
ⅰ) Switch to Scan Drive mode at Drive Setting Status screen by moving dial-key up or down.
Md PE Ax Sp Val
R P 1 0 0
P 2 0 0
Back to drive setting status
Md PE Ax Sp Val
R P 1 :R E L R e W r i t e
- N N N N N N N N N N N
If necessary, put minus
Put current position
2-0. Manually Rewriting Present Position
Dial-key moving up and down
Press Dial-key
Press “SET”
Press “SET”
Move Dial-key down
Put current
position numbers
《Setting of Rewriting Present Position》
This manual suits for next models
1
Table of contents
Other Kohzu Precision Controllers manuals
Popular Controllers manuals by other brands
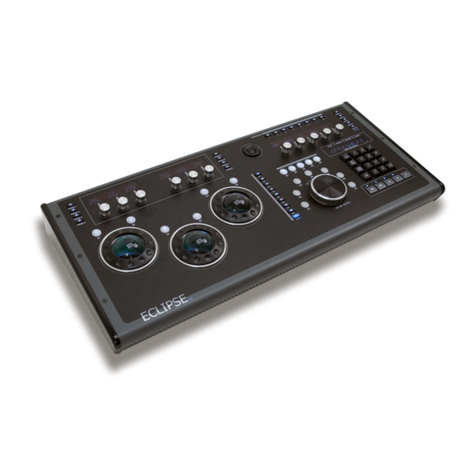
JLCooper Electronics
JLCooper Electronics EclipseCX Midnight user manual
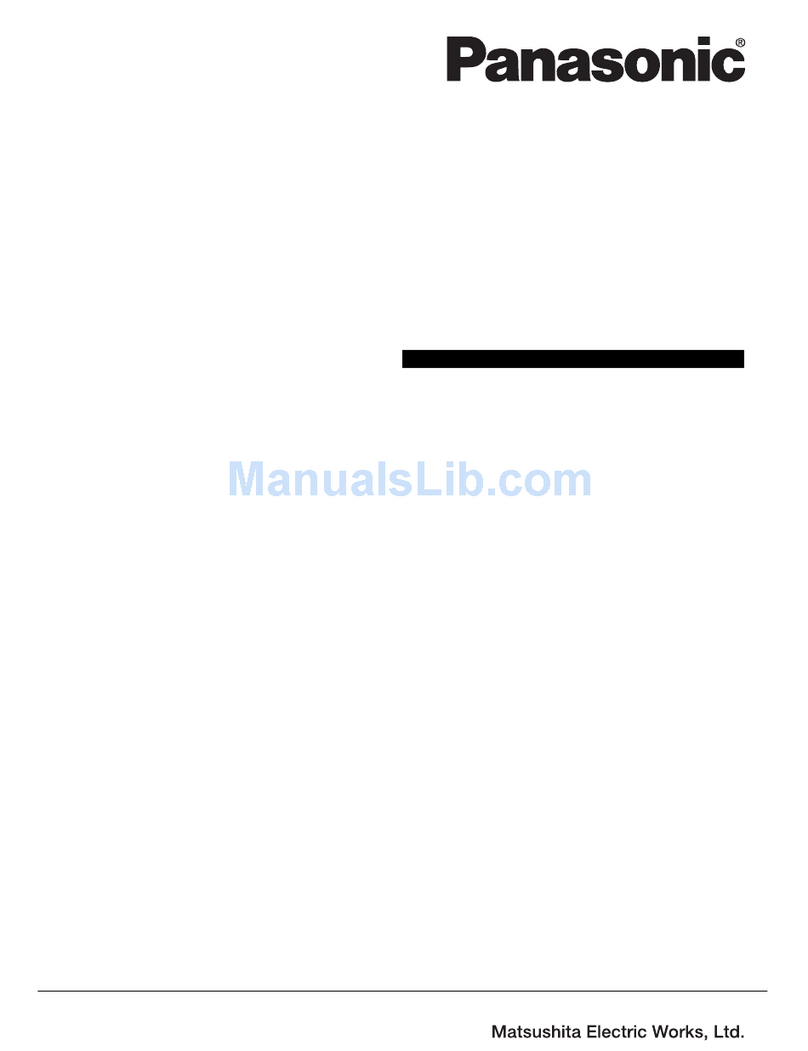
Panasonic
Panasonic FP3 Technical manual
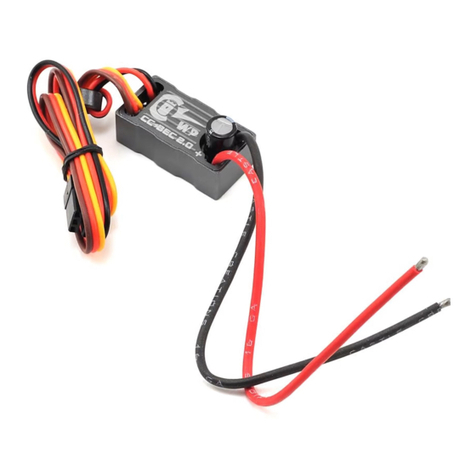
Castle Creations
Castle Creations CC BEC 2.0 quick start guide
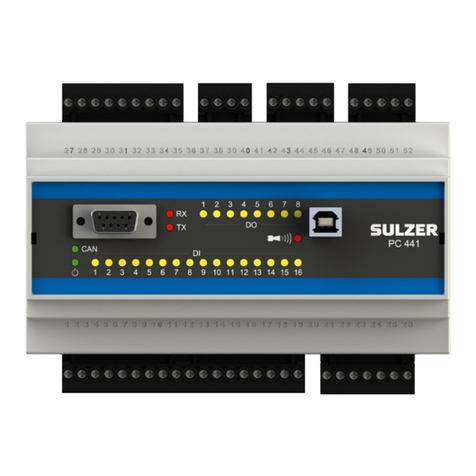
Sulzer
Sulzer ABS PC 441 installation guide
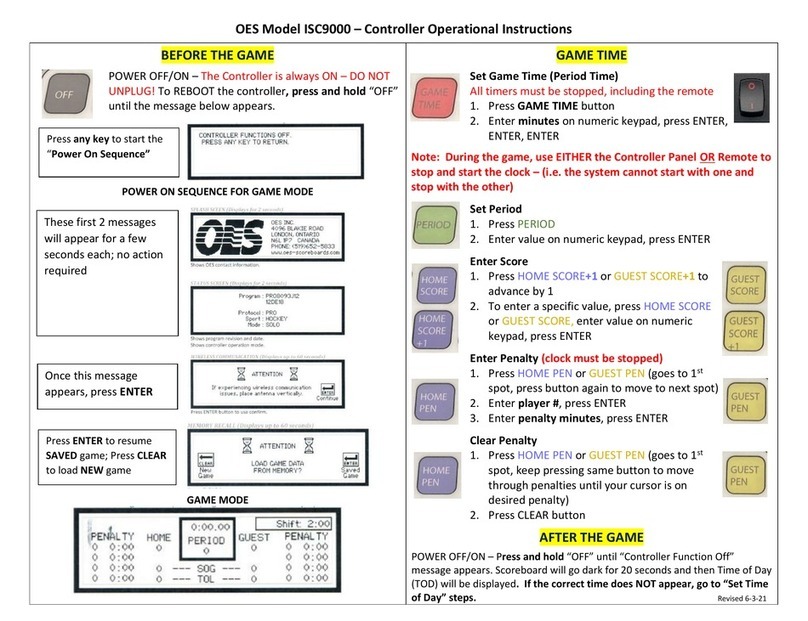
OES
OES ISC-9000 Operational instructions
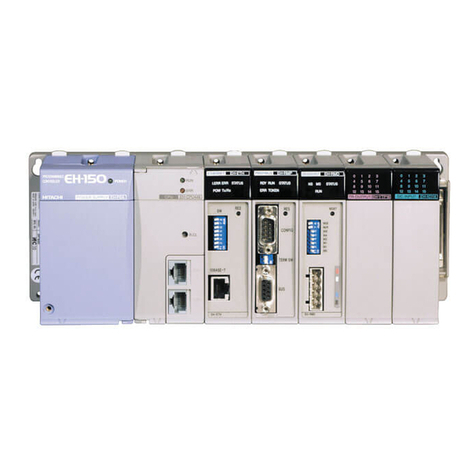
Hitachi
Hitachi HIDIC EH-150 Applications manual