KRAL OMP Series User manual

www.kral.at
Operating Instructions
KRAL Flowmeter.
OMP Series
OIO 23en
Edition 10/2017
Original instructions

2 OIO 23en Edition 10/2017 Operating Instructions
Table of contents
KRAL Flowmeter – OMP Series
About this document
□General information 3
□Target groups 3
□Symbols 3
□Danger levels 4
□Associated documents 4
Safety
□Proper use 5
□Safety information 5
Identification
□Type code 6
□Rating plate 7
Technical data
□Operating limits 8
▪Load due to pressure pulsation 8
▪Maximum values 8
▪Substitute operating data 9
□Sound pressure level 9
□Heating system 9
▪Trace heating system 9
□Dimensions and weights 10
▪OMP with pipe thread (BSPP thread) 10
▪OMP with DIN flange 11
▪OMP with ANSI flange 12
▪OMP with JIS flange 13
□Load-bearing capacity 14
▪Load-bearing capacity OMP 13 14
▪Load-bearing capacity OMP 20 15
▪Load-bearing capacity OMP 32 16
▪Load-bearing capacity OMP 52 17
Function description
□Description 18
□Rolling bearings 18
□Signal generation 19
□Linearization 19
□Temperature compensation 19
□Flow direction detection 19
□Junction box 19
Transportation, storage and disposal
□Unpacking and checking the state of delivery 20
□Lifting the flowmeter 20
□Storage 20
□Preservation 20
▪Preserving the flowmeter 20
▪Removing the preservation 21
□Disposal 21
Installation, removal and connection
□Safety instructions for installation and removal 22
□Installing the flowmeter 22
▪Installation types 22
▪Preferred installation variant 23
▪Recommendations for alternative installation
variants 23
▪Protect the flowmeter against soiling 24
▪Connecting the flowmeter to the pipe system 24
□Electrical installation 25
▪Safety instructions for electrical installation 25
▪Connection for the pick ups 25
□Removing the flowmeter 25
Operation
□Commissioning 27
▪Cleaning the pipe system 27
▪Checking the function 27
▪Commissioning the flowmeter 27
□Switching off the flowmeter 28
▪Safety instruction for switching off the
flowmeter 28
▪Switching off the flowmeter 28
□Recommissioning the flowmeter 28
Maintenance
□Safety instructions on repairs 29
□Required maintenance 29
□Re-calibration of the flowmeters 29
□Mounting instructions OMP 13 30
▪Removing seals and bearings 31
▪Installing seals and bearings 31
□Mounting instructions OMP 20/32 32
▪Removing seals and bearings 33
▪Installing seals and bearings 33
□Mounting instructions OMP 52 34
▪Removing seals and bearings 35
▪Installing seals and bearings 36
Troubleshooting
□Possible faults 37
□Troubleshooting 37
Appendix
□Spare parts 39
▪Maintenance kits 39
□Accessories 42
▪Junction box 42
▪Mounting the junction box 44
▪Connecting the junction box 45
▪Connecting the extension cable 46
□Tightening torques 47
□Contents of the EC Declaration of Conformity 47

Operating Instructions OIO 23en Edition 10/2017 3
General information
About this document
About this doc ument General information
The operating instructions form part of the KRAL flowmeter and must be kept for future reference.
Furthermore please observe the associated documents.
Target groups
Symbols
Target group Tasks
Operator-owner □Keep these instructions available at the system site for future
reference.
□Ensure that employees read and observe these instructions and the
associated documents, in particular the safety instructions and
warnings.
□Observe additional system-specific directives and regulations.
Specialist personnel, fitters □Read, observe and follow these instructions and the associated
documents, in particular the safety instructions and warnings.
Symbol Meaning
Warning personal injury
Notice
Procedures mechanical installation
Procedures electrical installation
Check or fault table
Request for action

4 OIO 23en Edition 10/2017 Operating Instructions
Danger levels
About this document
Danger levels
Associated documents
Warning Danger level Consequences of non-observances
Danger Immediate threat of danger Serious personal injury, death
Warning Possible threat of danger Serious personal injury, invalidity
Caution Potentially dangerous situation Slight personal injury
Caution Potentially dangerous situation Material damage
Calibration certificate
Declaration of conformity according to EU Directive 2006/42/EC
Declaration of conformity according to EU Directive 2014/34/EU
ATEX supplementary instructions for operation in potentially explosive areas
Manufacturer's declaration according to EU Directive 2014/68/EU
Corresponding operating instructions for pick up
Corresponding operating instructions for electronic equipment

Operating Instructions OIO 23en Edition 10/2017 5
Proper use
Safety
Safety Proper use
□Use flowmeters of the OMP series solely for flow measurement of lubricating liquids that are
chemically neutral and do not contain any gas or solids content.
□Flowmeters require the operation with clean liquids. If coarse soiling, solid particles in the liquid or
abrasive fine particles occur during operation, the flowmeter has to be protected additionally by a
correspondingly dimensioned operating filter in the pipe system, see "Cleaning the pipe system",
page 27.
□Only use flowmeters within the operational limits specified on the rating plate and in the "Technical
data" section. Deviating operating data can result in damage to the flowmeter. In the case of
operating data that does not agree with the specifications on the rating plate, please contact the
manufacturer.
□Strong changes to the flow rate (e.g. rapid shutdown, pulsations ...) cause marked pressure
differences on the flowmeter and can damage the measuring unit.
▪The pressure loss of the flowmeter must not exceed the values given in the chapter "Technical
data", see "Load-bearing capacity", page 14.
Safety information
The following safety instructions must be observed:
□No liability is accepted for damage arising through non-observance of the operating
instructions.
▪Read the operating instructions carefully and observe them.
▪The operator-owner is responsible for the observance of the operating instructions.
▪Installation, removal and installation work may only be carried out by specialist personnel.
□Flowmeters wear to different degrees depending on the respective operating conditions
(pulsations, temperature, …).
▪Do not continue to use flowmeters that are operated contrary to specifications or after damage.
▪Check the flowmeters regularly.
▪Shut down damaged flowmeters and replace worn flowmeters immediately.
□In order for the warranty to remain valid, corrective maintenance carried out during the
warranty period requires the express permission of the manufacturer.
□Observe the general regulations for the prevention of accidents as well as the local safety
and operating instructions.
□Observe the valid national and international standards and specifications of the installation
location.
□In case of systems with an increased potential of danger to humans and/or machines the
failure of a flowmeter may not lead to injuries or damage to property.
▪Always equip systems with an increased potential of danger with alarm equipment and/or
bypass.
▪Maintain and check the protective/alarm equipment regularly.
□The pumped liquids can be dangerous (e.g. hot, dangerous to health, poisonous,
combustible). Observe the safety conditions for handling dangerous materials.
□Pumped liquids can be subject to pressure and can cause damage and/or personal injury
should leaks occur.

6 OIO 23en Edition 10/2017 Operating Instructions
Type code
Identification
Identification Type code
1Series
2Size
3Sensor technology
4Function of sensor technology
5Material of bearing
6Material of seal
7Mechanical connection
8Electrical connection
9Version index
Fig. 1 Type code
Item Designation Description
1Series OMP: Universal
2Size Corresponds to the diameter of the measuring screw large in [mm]
3Sensor technology F: BEG 47
I: BEG 56
K: BEG 64
X: Special design
4Function of sensor
technology
A: Without flow direction detection
B: With flow direction detection
C: Without flow direction detection, with temperature compensation
D: With flow direction detection, with temperature compensation
X: Special design
5Material of bearing B: Hybrid
6Material of seal A: FPM (FKM)
B: FFPM
C: Low temperature FPM
D: EPDM
X: Special design
7Mechanical
connection
A: Pipe thread connection BSPP
B: Flange connection DIN
C: Pipe thread connection NPT
D: Flange connection ANSI
E: Flange connection JIS
X: Special design
8Electrical
connection
A: Loose cable head
B: Cable gland junction box
D: Mounting kit for electronic unit
X: Special design
9Version index For internal administration
OMP-020.FDBAAD.0001
3
4
5
2
7
68
9
1

Operating Instructions OIO 23en Edition 10/2017 7
Rating plate
Identification
Rating plate
1Serial number
2Year of construction
3K-factor
4Preferred flow direction
5Maximum temperature
6Type
7Maximum pressure
Fig. 2 Rating plate
R
123
4
5
6
7
®

8 OIO 23en Edition 10/2017 Operating Instructions
Operating limits
Technical data
Technic al data Operating limits
The values specified on the rating plate and the calibration certificate apply. The permissible operational
limits of individual values influence each other so that every application is checked individually by the
manufacturer when selecting the flowmeter.
If no operating data are provided by the orderer, standardized substitute operating data are used.
Load due to pressure pulsation
Maximum values
The following table shows the respective maximum values that, however, may not occur simultaneously.
In addition, the operational limits of the corresponding completion, of the sealing material and of the pick
up are to be observed.
Tab. 1 Maximum values
Strong pressure pulses in the system can reduce the lifetime of
the flowmeter.
Fig. 1 Pressure pulses
Unit OMP 13 OMP 20 OMP 32 OMP 52
Flow rate
Qmax [l/min] 15 45 150 525
Qnom 10 30 100 350
Qmin 0,1 0.3 1.0 3.5
Max. pressure [bar] 40
Temperature
min. – max. [°C] -20...+200
Viscosity
min. – max. [mm2/s] 1 – 1000000
Measuring chamber
volume [ml/U] 1,65 6.25 25.6 112.7
Rotation speed
n (Qmax)[min-1]9120 7200 5850 4658
n (Qnom)6060 4800 3900 3105
n (Qmin)61 48 39 31
Pole number 2 2 2 2
K-factor [P/l] 1214 321.0 78.0 17.73
Milliliters/pulse [ml/P] 0,824 3.12 12.8 56.4
Pulse frequency
f1 (Qmax)[Hz] 304 242 195 155
f1 (Qnom)202 161 130 104
f1 (Qmin)2,0 1.6 1.3 1.0
10 3020 40 t [ms]
30
10
20
0
p
[bar]

Operating Instructions OIO 23en Edition 10/2017 9
Sound pressure level
Technical data
Substitute operating data
The following table shows standardized values for the flow rate, temperature and viscosity. These
values can be used at the same time as maximum values without impairing the service life of the
flowmeter. In addition, the operational limits of the corresponding completion, of the sealing material of
the pick up and of the temperature sensor are to be observed.
Tab. 2 Substitute operating data
Sound pressure level
The sound pressure level of the flowmeter amounts to less than 70 dB(A).
Heating system
A heating system is not installed at the factory. The customer can optionally fit OMP-series KRAL
flowmeters with a trace heating system. The manufacturer recommends heating systems for high-
viscosity liquids that do not flow sufficiently if not heated, because bearing damage and destruction of
the device may otherwise result.
Trace heating system
Contact the manufacturer before installing a trace heating system.
Unit OMP 13 OMP 20 OMP 32 OMP 52
Flow rate
Qmax [l/min] 10 30 100 350
Qnom 10 30 100 350
Qmin 0,2 0.6 2.0 7.0
Max. pressure [bar] 40
Temperature
min. – max. [°C] -20...+125
Viscosity
min. – max. [mm2/s] 1–200
1Heat insulation
2Trace heating
3Pick up with
connecting cable
4Piping
5Temperature sensor
with connecting cable
6Junction box
7Flowmeter
XArea stringently without
heat insulation
Fig. 2 Flowmeter with trace heating system
5
1
2
1
4
4
3
6
7
X

10 OIO 23en Edition 10/2017 Operating Instructions
Dimensions and weights
Technical data
► Ensure that pick up 3, temperature sensor 5, junction box 6 and corresponding cables are not heat
insulated. The area X has to be free of heat insulation, see Fig. 2, page 9.
Dimensions and weights
OMP with pipe thread (BSPP thread)
Tab. 3 Dimensions and weights – Pipe thread connection
CAUTION
Defective pick up, temperature sensor or cabling due to exceeding of the maximum temperature.
► Do not heat the pick up, temperature sensor, junction box and corresponding cables above the
temperature specified in the associated operating instructions.
G
M16x1/
M18x1
G1/4"
D
L1
L2
L3, L4
T
Pipe thread
Pick up hole/
Mounting connection
element
Temperature sensor
hole
Outer diameter
Total length
Flowmeter length
without connections
Flange thickness
Max. screw-in depth
Fig. 3 Dimensional drawing OMP with pipe thread
Unit OMP 13 OMP 20 OMP 32 OMP 52
G[inch] 1/2 3/4 11 1/2
Pressure
stage
[bar] 40 40 40 40
D[mm] 90 74 104 118
L1 [mm] 115 145 215 270
L2 [mm] 64 85 140 215
L3 [mm] 25,5 38.0 47.0 27.5
L4 [mm] 25,5 22.0 28.0 27.5
T[mm] 15 16 18 22
Weight [kg] 3,4 3.5 11.0 18.0
G
T T
G1/4" M16x1 /
M18x1
L2L3
L1
L4
D

Operating Instructions OIO 23en Edition 10/2017 11
Dimensions and weights
Technical data
OMP with DIN flange
Tab. 4 Dimensions and weights – DIN flange connection
DN
M16x1/
M18x1
G1/4"
D
L1
L2
L3, L4
TK
Nominal diameter
flange
Pick up hole/
Mounting connection
element
Temperature sensor
hole
Outer diameter
Total length
Flowmeter length
without connections
Flange thickness
Pitch circle
Fig. 4 Dimensional drawing OMP with DIN flange
Unit OMP 13 OMP 20 OMP 32 OMP 32 OMP 52
DN 15 20 25 32 40
Pressure
stage
[bar] 40 40 40 40 40
D[mm] 95 105 115 140 150
L1 [mm] 115 125 180 190 240
L2 [mm] 64 85.0 140.0 140.0 185.5
L3 [mm] 25,5 20 20 25 32
L4 [mm] 25,5 20.0 20.0 25.0 22.5
TK [mm] 65 75 85 100 110
Weight [kg] 3,7 5.0 11.2 13,5 19.2
DN
G1/4" M16x1 /
M18x1
L2 L4
L1
Tk
L3
D

12 OIO 23en Edition 10/2017 Operating Instructions
Dimensions and weights
Technical data
OMP with ANSI flange
Tab. 5 Dimensions and weights – ANSI flange connection
DN
M16x1/
M18x1
G1/4"
D
L1
L2
L3, L4
TK
Nominal diameter
flange
Pick up hole/
Mounting connection
element
Temperature sensor
hole
Outer diameter
Total length
Flowmeter length
without connections
Flange thickness
Pitch circle
Fig. 5 Dimensional drawing OMP with ANSI flange
Unit OMP 20 OMP 32 OMP 52
DN [inch] 3/4 11 1/2
Class 300 300 300
D[mm] 117.5 123.8 155.6
L1 [mm] 134 195 245
L2 [mm] 85.0 140.0 185.5
L3 [mm] 24.5 27.5 32.0
L4 [mm] 24.5 27.5 27.5
TK [mm] 82.5 88.9 114.3
Weight [kg] 6.0 12.5 19.6
DN
G1/4" M16x1 /
M18x1
L4
L1
L3
TK
DN
L2

Operating Instructions OIO 23en Edition 10/2017 13
Dimensions and weights
Technical data
OMP with JIS flange
Tab. 6 Dimensions and weights – JIS flange connection
DN
M16x1/
M18x1
G1/4"
D
L1
L2
L3, L4
TK
Nominal diameter
flange
Pick up hole/
Mounting connection
element
Temperature sensor
hole
Outer diameter
Total length
Flowmeter length
without connections
Flange thickness
Pitch circle
Fig. 6 Dimensional drawing OMP with JIS flange
Unit OMP 20 OMP 32 OMP 52
DN 20 25 40
Pressure
stage
16K 16K 16K
D[mm] 100 125 140
L1 [mm] 125 190 260
L2 [mm] 85 140 215
L3 [mm] 20.0 25.0 22.5
L4 [mm] 20.0 25.0 22.5
TK [mm] 75 90 105
Weight [kg] 4.5 12.2 19.0
DN
G1/4" M16x1 /
M18x1
L2 L4
TK
D
L3
L1

14 OIO 23en Edition 10/2017 Operating Instructions
Load-bearing capacity
Technical data
Load-bearing capacity
Load-bearing capacity OMP 13
The values apply for lubricating liquids at temperatures of up to 120 °C. Abrasive and aggressive liquids
reduce the durability.
AShort-time operation
BContinuous operation
CPressure loss
DFlow rate
EQnom
20
18
16
14
12
2
4
6
8
10
0
A
B
1000 h
30000 h
10000 h
5000 h
100000
5
10
50
200
500
1000
2000
5000
10000
50000
100
[mm2/s]
C
[bar]
[bar]
C2
3
0
1
100000
5000
10000
50000
5
10
50
200
500
1000
2000
100
[mm2/s]
234 109
8
7
65
0,1 115
14
13
12
11
E
D
[l/min]
10050 150
D
[l/min]
50
45
40
30
25
20
1510
51 35
3,52,5
1,50,5
0,1 4,5 5
1 2 3 4
[%] [%]
1

Operating Instructions OIO 23en Edition 10/2017 15
Load-bearing capacity
Technical data
Load-bearing capacity OMP 20
The values apply for lubricating liquids at temperatures of up to 120 °C. Abrasive and aggressive liquids
reduce the durability.
AShort-time operation
BContinuous operation
CPressure loss
DFlow rate
EQnom
20
18
16
14
12
2
4
6
8
10
0
A
B
1000 h
30000 h
10000 h
5000 h
100000
5
10
50
200
500
1000
2000
5000
10000
50000
100
[mm2/s]
C
[bar]
[bar]
C
2
3
0
1
100000
5000
10000
50000
5
10
50
200
500
1000
2000
100
[mm2/s]
6912 3027
24
21
1815
0,3 345
42
39
36
33
E
D
[l/min]
10050 150
D
[l/min]
50
45
40
30
25
20
1510
51 35
10,57,5
4,51,5
0,3 13,5 15
3 6 9 12
[%] [%]
1

16 OIO 23en Edition 10/2017 Operating Instructions
Load-bearing capacity
Technical data
Load-bearing capacity OMP 32
The values apply for lubricating liquids at temperatures of up to 120 °C. Abrasive and aggressive liquids
reduce the durability.
AShort-time operation
BContinuous operation
CPressure loss
DFlow rate
EQnom
20
18
16
14
12
2
4
6
8
10
0
A
B
1000 h
30000 h
10000 h
5000 h
100000
5
10
50
200
500
1000
2000
5000
10000
50000
100
[mm2/s]
C
[bar]
[bar]
C
2
3
0
1
100000
5000
10000
50000
5
10
50
200
500
1000
2000
100
[mm2/s]
20 30 40 10090
80
70
6050
110 150
140
130
120
110
E
D
[l/min]
10050 150
D
[l/min]
50
45
40
30
25
20
1510
51 35
3525
155
1 45 50
10 20 30 40
[%] [%]
1

Operating Instructions OIO 23en Edition 10/2017 17
Load-bearing capacity
Technical data
Load-bearing capacity OMP 52
The values apply for lubricating liquids at temperatures of up to 120 °C. Abrasive and aggressive liquids
reduce the durability.
AShort-time operation
BContinuous operation
CPressure loss
DFlow rate
EQnom
20
18
16
14
12
2
4
6
8
10
0
A
B
1000 h
30000 h
10000 h
5000 h
100000
5
10
50
200
500
1000
2000
5000
10000
50000
100
[mm2/s]
C
[bar]
[bar]
C2
3
0
1
100000
5000
10000
50000
5
10
50
200
500
1000
2000
100
[mm2/s]
70 105 140 350315
280
245
210175
3,5 35 525
490
455
420
385
E
D
[l/min]
10050 150
D
[l/min]
50
45
40
30
25
20
1510
51 35
122,587,5
52,517,5
3,5 157,5 175
35 70 105 140
[%] [%]
1

18 OIO 23en Edition 10/2017 Operating Instructions
Description
Function description
Function descript ion Description
As screw meters flowmeters belong to the group of rotating displacement meters. The fluid current
makes the measuring unit rotate. The displacement effect results from the continuous filling, axial
displacement and discharge of the volumes that are formed by the measuring housing and measuring
unit. The measured liquid flows around and lubricates all the rotating parts. Thanks to the displacement
principle, the flowmeter does not require inlet and smoothing sections in its supply and discharge.
Depending on the customer requirements, the flowmeters can be equipped with suitable end
connections for connection to various flanges.
Rolling bearings
The measuring unit is maintained without contact and with a low degree of friction in the housing of the
flowmeter by means of precision rolling bearings. Depending on the respective size, the following
bearings are used:
□Single-row deep-groove ball bearings
□Paired angular-contact ball bearings
Fig. 1 Structure, flowmeter OMP series
1Connection
2* Bearing cover
3Temperature sensor hole
4Pick up hole
5Measuring housing
6Measuring screw small
7Ball bearing, floating bearing end
8Measuring screw large
9Ball bearing, fixed bearing end
* only for OMP 52
41 6 4 1
89
7
2* 2*3 5

Operating Instructions OIO 23en Edition 10/2017 19
Signal generation
Function description
Signal generation
A pick up samples the measuring pulses directly on the screw. The pick up generates a specific number
of pulses per flow volume unit – depending on the size and working point. This device-specific
characteristic is called the K-factor (unit: Pulse/Liter) and can be found on the rating plate and the
enclosed calibration certificate. Possible formats of the signals are:
□PNP
□NAMUR
The mounting method of the pick-up allows mounting without contact to the fluid to be measured. Two
different pick ups are employed, depending on the application (standard, or for use in areas where there
is an explosion hazard):
□Pick up based on the Hall effect
□Inductive pick up
Linearization
The calibration certificate contains a mean K-factor that has been determined for the flow range 10:1
and that can therefore be used across a wide flow range. However, the K-factor shows slightly different
values at different flow rates. These are also documented in the enclosed calibration certificate. If
highest measuring precision is required, it is therefore advisable, especially at strongly varying flow
rates, to take these different values into consideration by means of a "Linearization". The K-factors are
therefore fed into a suitable electronics unit across several interpolation values of the flow rate. The K-
factor relevant for the flow rate being measured is then determined by means of linear interpolation
between the two nearest interpolation values.
The viscosity dependence of the K-factors must also be taken into account. These are determined
during calibration at a viscosity of approximately 4.2 mm²/s. The influence of the flow rate on the K-factor
decreases at higher viscosities so that the mean K-factor can then also be used in a considerably larger
flow range without noteworthy errors.
Temperature compensation
If the flowmeter is additionally equipped with a temperature sensor, the current density of the flowing
liquid can be calculated from this measured value by means of a density table stored in the flow
management unit. A normalized volume measurement is then possible at which the displayed values
are converted to a reference temperature that can be selected freely. This ensures that measuring
errors caused by changes in the density due to temperature variations are avoided.
Flow direction detection
Systems with a changing flow direction as well as systems with pressure pulsations - that can also
cause a reversal of the flow direction - require the use of a second pick up. This additional signal (90°
phase-offset) and the incremental encoding inputs available in the KRAL electronic unit can be used to
determine the direction of flow and to take it into consideration when calculating the total values.
Junction box
The manufacturer offers a junction box that facilitates the electrical connection of the various sensors for
the flowmeters of the OMP series. For further information see "Accessories", page 42.

20 OIO 23en Edition 10/2017 Operating Instructions
Unpacking and checking the state of delivery
Transportation, storage and disposal
Transportation , storage and d isposal Unpacking and checking the state of delivery
1. Upon delivery unpack the flowmeter and check for transport damage.
2. Report damage during transportation immediately to the manufacturer.
3. Store the supplied pick up and temperature sensor for the installation.
4. Dispose of packing material in accordance with the locally applicable regulations.
Lifting the flowmeter
Storage
As a result of the calibration, the internal components of the flowmeter are wetted with calibration liquid
that has a preservative effect. In addition, a special anticorrosive agent is sprayed onto the interior of the
flowmeters before being dispatched. The connections of the flowmeter are fitted with protective caps.
Unless otherwise specified, the external components of the flowmeter are preserved with a single-coat
PU-based two-component paint. The preservation applied at the factory will protect the flowmeter for up
to six weeks, if it is stored in a dry and clean location. The manufacturer offers a long-term preservation
for storage times of up to 60 months. The flowmeter is additionally packed in hermetically sealing anti-
corrosion paper.
► Observe the chapters "Storage" and "Preservation".
Preservation
Preservation has to be carried out additionally under the following conditions:
Tab. 1 Check table for preservation
Preserving the flowmeter
1. Close a connection of the flowmeter with a blind flange.
2. Position the flowmeter vertically.
3. Fill non-corrosive and resin-free oil up to approx. 1 cm under the connection at the top, while turning
the measuring unit slowly, so that the measuring unit also comes into contact with it.
4. Close the upper connection with a blind flange.
5. Apply non-corrosive and resin-free oil to all the plain and unpainted parts of the outer housing.
WARNING
Risk of injury and/or damage to equipment should the flowmeter fall.
► Use intact and correctly dimensioned hoisting equipment in accordance with the total weight to be
transported.
► Select the attachment points for the hoisting equipment in accordance with the center of gravity
and the weight distribution.
► Use at least two load ropes.
► Do not stand under raised loads.
CAUTION
Damage to device through corrosion if stored improperly and during longer standstills.
► Protect the flowmeters against corrosion during long standstills.
Type of delivery Condition
Standard delivery □Storage time exceeding six weeks
□Unfavorable storage conditions such as high
humidity, salty air, etc.
Delivery with long-term preservation □Opened or damaged packaging
This manual suits for next models
4
Table of contents
Other KRAL Measuring Instrument manuals
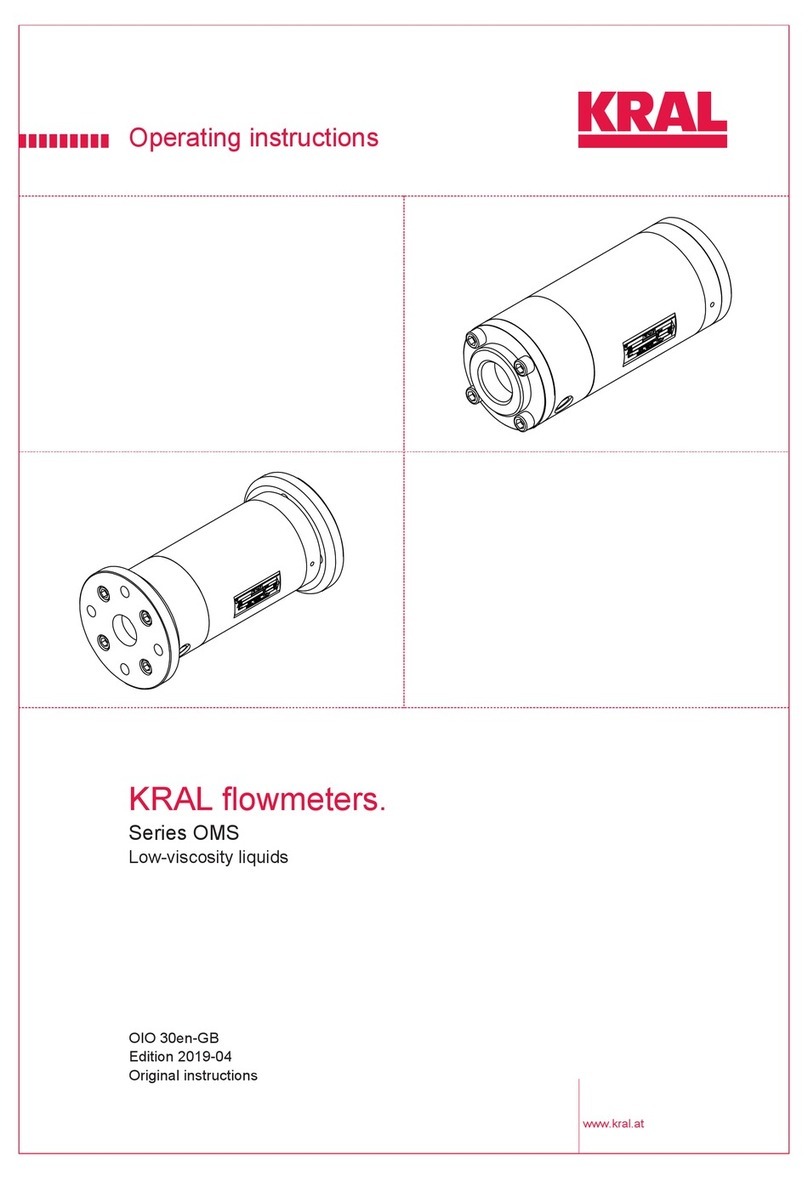
KRAL
KRAL OMS Series User manual

KRAL
KRAL BEM 100 User manual

KRAL
KRAL Volumeter OMG 13 User manual

KRAL
KRAL OMH Series User manual
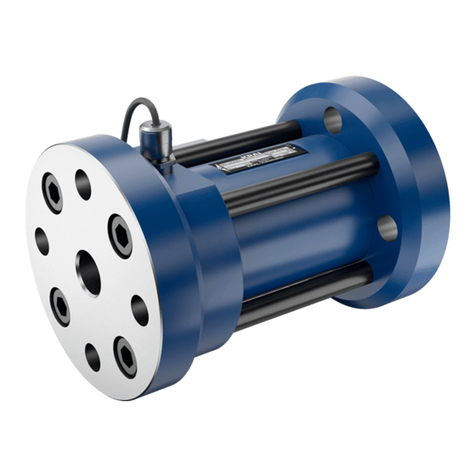
KRAL
KRAL OMG Series User manual
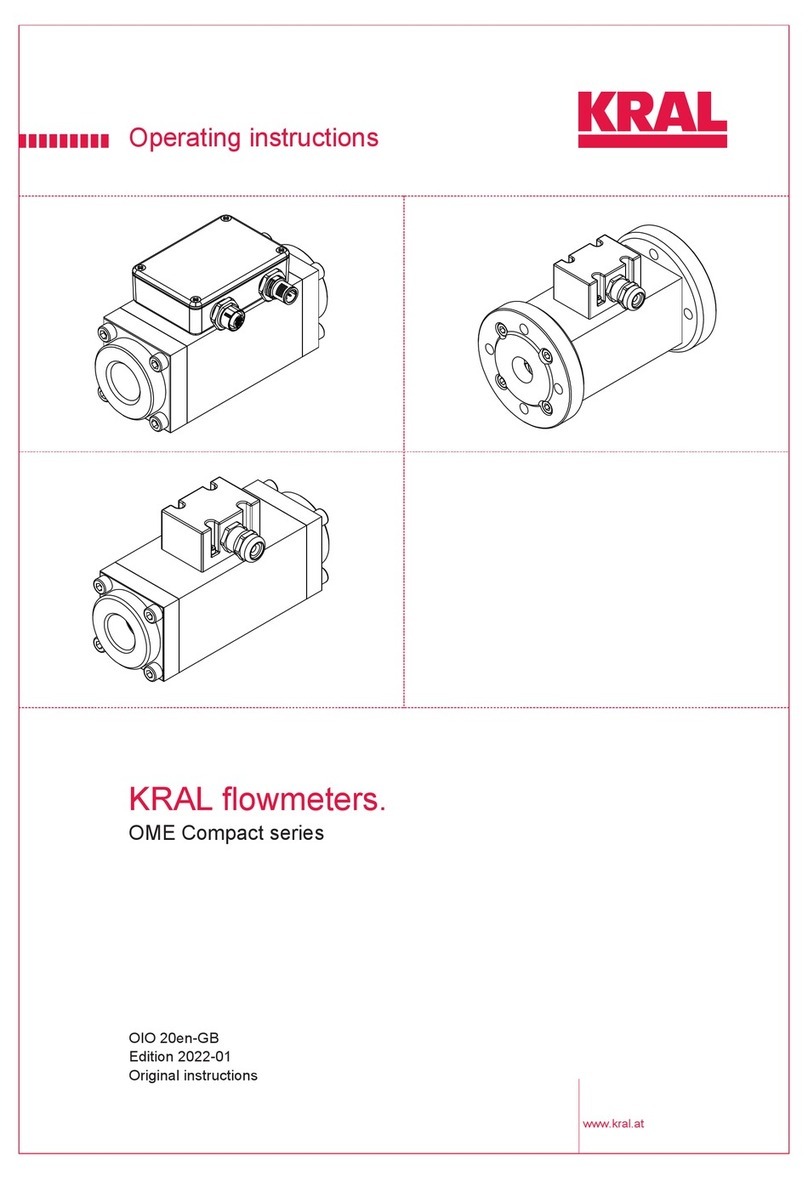
KRAL
KRAL OME Compact Series User manual

KRAL
KRAL BEM 150 User manual
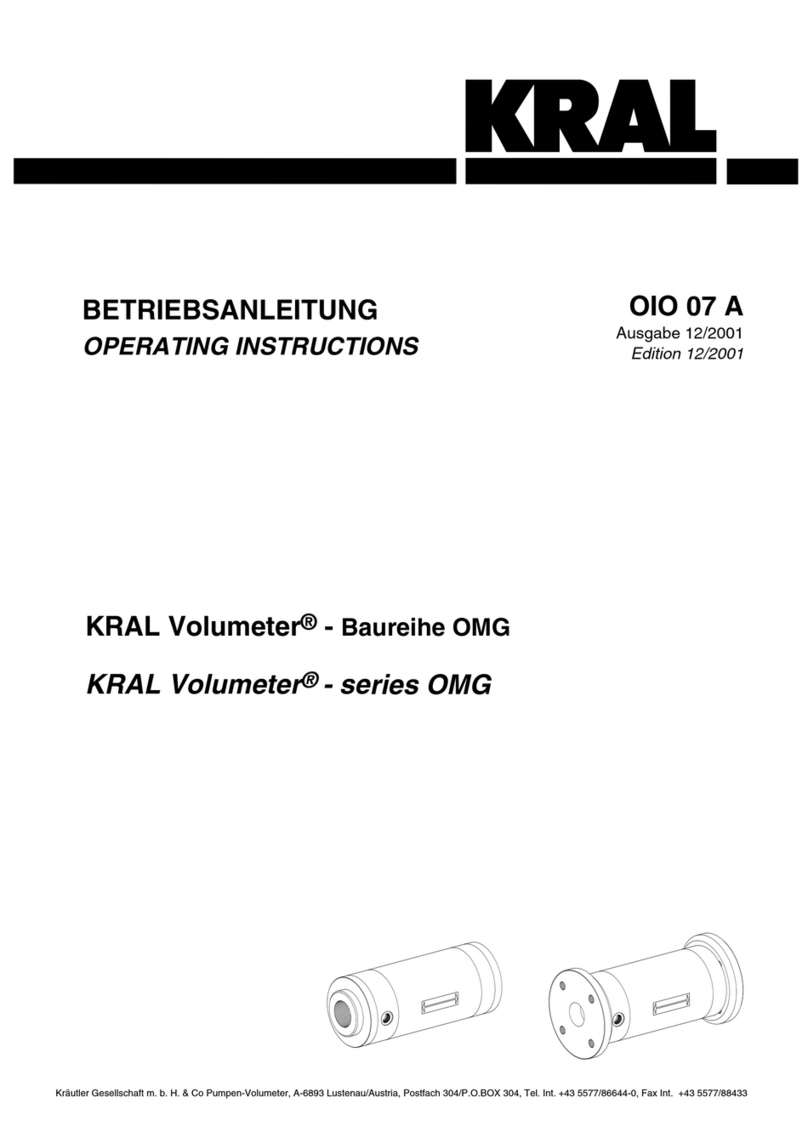
KRAL
KRAL Volumeter OMG Series User manual
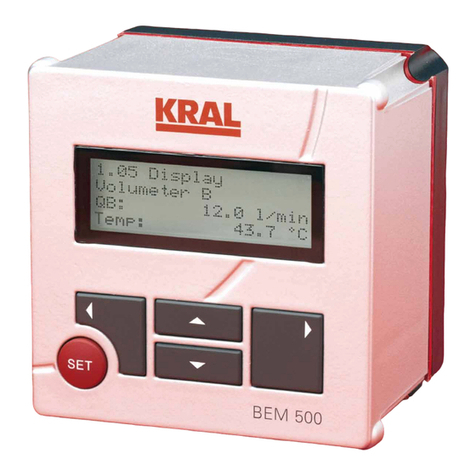
KRAL
KRAL BEM 500 Series User manual
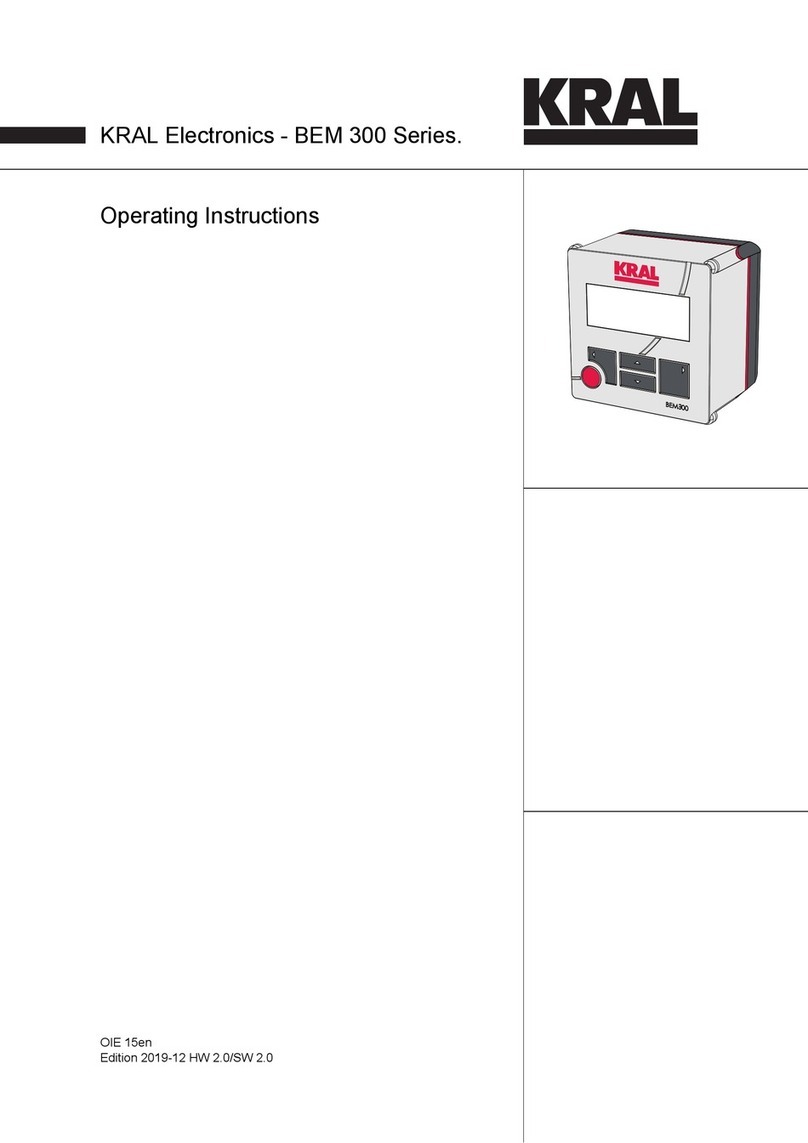
KRAL
KRAL BEM 300 Series User manual
Popular Measuring Instrument manuals by other brands
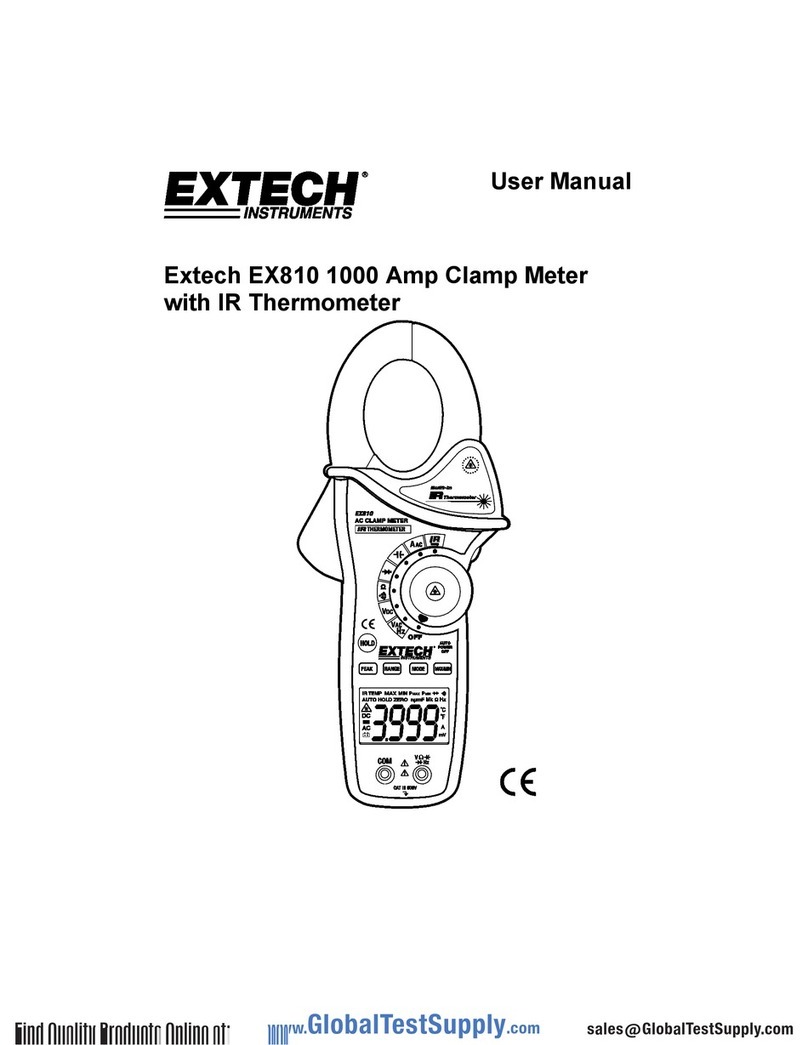
Extech Instruments
Extech Instruments EX810 user manual

Rosemount
Rosemount 6888Xi Reference manual
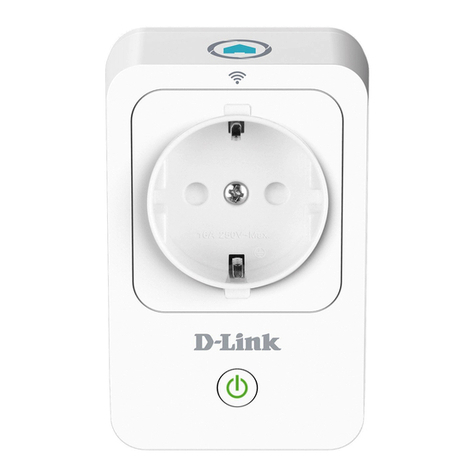
D-Link
D-Link mydlink DSP-W215 user manual
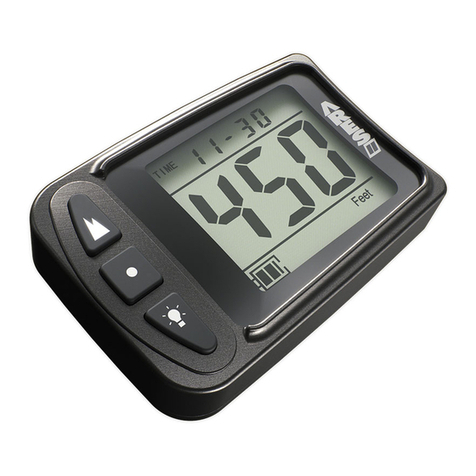
LB Altimeters
LB Altimeters ARES II manual

ProMinent
ProMinent DULCOMETER Installation and configuration manual
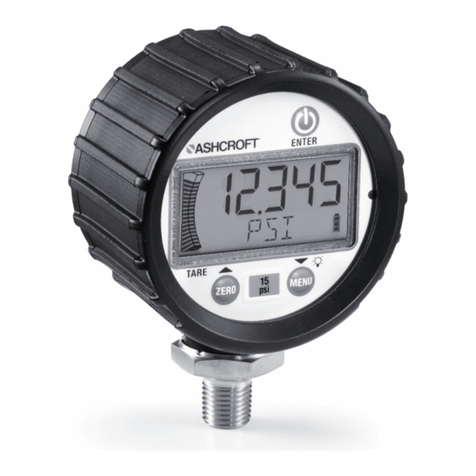
Ashcroft
Ashcroft DG25 Installation and operating instructions