Lambrecht 16131.5 Series User manual

Manual
16131.5 SERIES
First class pyranometers
with various outputs (and heater)

2
Safety instructions and Warranty
Putting more than 12 Volt across the sensor wiring of
00.16131.501000 can lead to permanent damage to the sensor.
Putting more than 30 Volt across the sensor wiring of the main power
supply can lead to permanent damage to the sensor.
For proper instrument grounding: use 16131.5 with its original factory-
made cable.
Using the same Modbus address for more than one device will lead to
irregular behaviour of the entire network.
Disconnect power while performing service or maintenance.
Keep the voltage on the RS-485 data wiring of 00.16131.501030
between -7 and +12 V to avoid permanent damage.
This system is designed according to the state-of-the-art accepted safety regulations. However,
please note the following rules:
1. Before putting into operation please read all respective manuals!
2. Please observe all internal and state-specific guidelines and/or rules for the prevention of
accidents. If necessary ask your responsible safety representative.
3. Use the system only as described in the manual.
4. Always have the manual at hand at the installation site.
5. Use the system within the specified operating condition. Eliminate influences, which might
impair the safety.
6. Prevent the ingress of unwanted liquids into the devices.
Please note the loss that unauthorised manipulation of the system shall result in the loss of
warranty and non-liability. Changes to system components require express written permission
from LAMBRECHT meteo GmbH. These activities must be performed by a qualified technician.
The warranty does not cover:
1. Mechanical damage caused by external impacts (e. g. icefall, rockfall, vandalism).
2. Impacts or damage caused by over-voltage or electromagnetic fields which are beyond the
standards and specifications of the device.
3. Damage caused by improper handling, e. g. by using the wrong tools, incorrect installation,
incorrect electrical installation (incorrect polarity) etc.
4. Damage caused by using the device outside the specified operation conditions.
Modbus®is a registered trademark of Schneider Electric, licensed to the Modbus Organization, Inc.

3
Contents
Safety instructions and Warranty 2
Contents 3
Introduction 4
1Ordering and checking at delivery 5
1.1 Ordering 16131.5 5
1.2 Included items 5
1.3 Quick instrument check 5
2Instrument schematic 6
3Specifications of 16131.5 8
3.1 Specifications of 16131.5 8
3.2 Dimensions of 16131.5 11
4Installation of 16131.5 12
4.1 Site selection and installation 12
4.2 Installation of the sun screen 13
4.3 Installation of pyranometer 14
4.4 Electrical connection of active 16131.5 series: wiring diagram 15
4.5 Electrical connection of passive 16131.5: wiring diagram 16
4.6 Grounding and use of the shield 16
4.7 Using heater of 00.16131.501030 and 00.16131.0501000 16
4.8 Using 00.16131.501040’s analogue 4 to 20 mA output 17
4.9 Data acquisition requirements for using 00.16131.501000’s millivolt output 18
4.10 Connecting to an RS-485 network 19
5Communication with 16131.5 20
5.1 Modbus-protocol 20
5.2 Data encoding 20
5.3 Device-address 20
5.4 Standard configuration - default 20
5.5 Modbus command set 21
5.6 Measured value and parameter register 21
5.7 Additional value registers (Service) 21
5.8 Sensor parameters / configuration-parameters 22
5.9 Network communication: getting started 23
5.10 Adapting the Modbus address and communication settings 23
6Maintenance and trouble shooting 24
6.1 Recommended maintenance and quality assurance 24
6.2 Trouble shooting 25
7Appendices 27
7.1 LAMBRECHT meteo – Auto-configuration 27
7.2 EU declaration of conformity 30

4
Introduction
16131.5 digital pyranometer series is a range of high-accuracy digital solar radiation sensors. It is “first
class” according to the WMO guide and ISO 9060:1990 standard and “Spectrally Flat Class B” in the
2018 revision. Version 00.16131.501030, equipped with an on-board heater, is compliant in its
standard configuration with the requirements for “Class B” PV monitoring systems of the IEC 61724-
1:2017 standard.
The 16131.5 measures the solar radiation received by a plane surface, in W/m2, from a 180° field of
view angle. Various outputs are available, both digital and analogue, for ease of integration.
•Version 00.16131.501030:
digital sensor with Modbus over RS-485 output and heater
•Version 00.16131.501040:
digital sensor with Modbus over TTL (on request) and analogue 4-20 mA output (without
heater)
•Version 00.16131.501000: passive sensor with analogue millivolt output and heater
Benefits of the 16131.5 series:
•best measurement accuracy in first class
•improved response time
•with 00.16131.501030’s on-board heater: compliant with IEC 61724-1 Class B in its standard
configuration
Using the analogue version 00.16131.501000 is easy: the pyranometer can be connected directly to
commonly used data logging systems. The irradiance in W/m2is calculated by dividing the signal output, a
small voltage, by the sensitivity. This sensitivity is provided with 00.16134.501000 on its calibration
certificate.
The central equation governing 00.16131.501000 is: E = U/S
U: Voltage output in V
S: Sensitivity in V/(W/m2)
E: Solar irradiance in W/m2
Suggested use
Suggested use for 16131.5:
•PV system performance monitoring
•general solar resource monitoring
•indoor simulated solar testing
•meteorological networks

5
1 Ordering and checking at delivery
1.1 Ordering 16131.5
Id-No. for standard configurations 16131.5:
Version 00.16131.501030:
ISO 9060 first class pyranometer sensor with Modbus over RS-485 and heater
Version 00.16131.501040:
ISO 9060 first class pyranometer sensor with 4 to 20 mA output without heater
Version 00.16131.501000:
ISO 9060 first class pyranometer sensor with passive analogue millivolt output and heater
Common options / accessories are:
•cable 10 m, M12 plug connector, 5-pin Id-No. 32.14581.060000
•cable 15 m, M12 plug connector. 5-pin Id-No. 32.05005.001500
Suitable data loggers:
•met[LOG] Id-No. 00.95800.010000
•Ser[LOG] Id-No. 00.95770.000000
1.2 Included items
Arriving at the customer, the delivery should include:
•pyranometer 16131.5
•sun screen
•cable of the length as ordered
•product certificate matching the instrument serial number, including:
ocalibration certificate
•any other options as ordered
Please store the certificates in a safe place.
1.3 Quick instrument check
1. At power–ON the signal may have a temporary output level different from zero; an offset. Let
this offset settle down; it is a normal part of the power-ON procedure.
2. Check if the sensor reacts to light: expose the sensor to a strong light source, for instance a
100 W light bulb at 0.1 m distance. The signal should read > 100 W/m2now. Darken the
sensor either by putting something over it or switching off the light. The instrument irradiance
output should go down and within one minute approach 0 W/m2.
3. Inspect the instrument for any damage.
4. Check the instrument serial number as indicated by the label on the instrument against the
certificates provided with the instrument.

6
2 Instrument schematic
16131.5’s scientific name is pyranometer. A pyranometer measures the solar radiation received by a
plane surface from a 180° field of view angle. This quantity, expressed in W/m2, is called
“hemispherical” solar radiation.
The solar radiation spectrum extends roughly from 285 to 3000 x 10-9 m. By definition a pyranometer
should cover that spectral range with a spectral selectivity that is as “flat” as possible.
Figure 2.0.1 Overview of 16131.5:
(1) cable
(2) connector
(3) sun screen
(4) bubble level
(5) bubble level window
(6) outer dome
(7) inner dome
(8) thermal sensor with black coating
(9) quick release system of sun screen
(10) instrument body
(11) levelling feet
The 16131.5 pyranometer series employs a state-of-the-art thermopile sensor with black coated
surface, two domes and an anodised aluminium body.
Version 00.16131.501030 offers irradiance in W/m2as a digital output. It must be used in combination
with suitable power supply and a data acquisition system which uses the Modbus communication
protocol over RS-485. In order to reduce the effect of dew deposition and frost on the outer dome
surface, 00.16131.501030 has a built-in heater. The heater is coupled to the sensor body. Heating a
pyrometer can generate additional irradiance offset signals, therefore it is recommended to activate
12
3
67895
4
10
11

7
the heater only during night-time. Combining a heater with external ventilation makes these heating
offsets very low.
Version 00.16131.501040 offers irradiance in W/m2as a 4-20 mA output. It must be used in
combination with suitable power supply and a data acquisition system which is capable of handling a
4-20 mA current loop signal.
Version 00.16131.501000 offers irradiance in W/m2as an analogue millivolt output. It is a passive
sensor and does not need a power supply. It can be connected directly to commonly used data
logging systems. In order to reduce the effect of dew deposition and frost on the outer dome surface,
00.16131.501000 has a built-in heater. The heater is coupled to the sensor body. Heating a pyrometer
can generate additional irradiance offset signals, therefore it is recommended to activate the heater
only during night-time. Combining a heater with external ventilation makes these heating offsets very
low.
The irradiance in W/m2is calculated by dividing the 00.16131.501000 output, a small voltage, by the
sensitivity. This sensitivity is e.g. provided on its calibration certificate.
The central equation governing 00.16131.501000 is: E = U/S
U: Voltage output in V
S: Sensitivity in V/(W/m2)
E: Solar irradiance in W/m2

8
3 Specifications of 16131.5
3.1 Specifications of 16131.5
16131.5 measures the solar radiation received by a plane surface from a 180° field of view angle. This
quantity, expressed in W/m2, is called “hemispherical” solar radiation.
The instrument is classified according to ISO 9060 and should be used in accordance with the
recommended practices of ISO, IEC, WMO and ASTM.
Table 3.1.1 Specifications of 16131.5
16131.5 MEASUREMENT SPECIFICATIONS:
ISO classification (ISO 9060:1990)
First class pyranometer
WMO performance level (WMO-No. 8,
seventh edition 2008)
good quality pyranometer
Response time (95 %)
< 10 s
Zero offset a (response to 200 W/m2net
thermal radiation)
5 W/m² unventilated
Zero offset b (response to 5 K/h change in
ambient temperature)
< 4 W/m2
Non-stability
< 1 % change per year
Non-linearity
< 1 % (100 to 1000 W/m2)
Directional response
< 20 W/m2
Spectral selectivity
< 3 % (0.35 to 1.5 x 10-6 m)
Temperature response
< 2 % (-30 to +50 °C)
Tilt response
< 2 % (0 to 90 ° at 1000 W/m2)
Measurement range
0 to 3000 W/m2
Zero offset steady state
< 1 W/m2(-40 to + 80 °C)
Spectral range
(20 % transmission points)
285 to 3000 x 10-9 m
Figure 3.1.1 Spectral response of the pyranometer compared to the solar spectrum. The
pyranometer only cuts off a negligible part of the total solar spectrum.
Measurand
hemispherical solar radiation
Measurand in SI radiometry units
irradiance in W/m2
Optional measurand
sunshine duration
Field of view angle
180 °
Output definition
running average over 4 measurements, refreshed every 0.1 s
Recommended data request interval
1 s, storing 60 s averages
Temperature range of application
-40 to + 80 °C
IEC 61724-1:2017 COMPLIANCE
IEC 61724-1:2017 compliance
meets Class B PV monitoring system requirements

9
16131.5 ADDITIONAL SPECIFICATIONS
Measurand
Sensor body temperature
Measurand in SI radiometry units
temperature in °C
Temperature sensor
solid state System on Chip (SoC) silicon bandgap temperature
sensor
Instrument body temperature accuracy
0.5 °C
Instrument body temperature resolution
3.9 x 10-3 °C
Levelling (see options)
bubble level and adjustable levelling feet are included
Levelling accuracy
< 0.1 ° bubble entirely in ring
Connector type
M12-A, 5-pole, IP67
Mounting
2 x M5 bolt at 46 mm distance on north-south axis
IP protection class
IP67
Net weight including 5m cable
0.65 kg
HEATING (00.16131.501030 and 00.16131.501000 only)
Heater operation
the heater is not necessarily switched on; recommended
operation is to activate the heater when the sun is below the
horizon
Heater voltage
12 VDC
Required heater power
1.5 W at 12 VDC (the heater is not necessarily active)
Heater resistance
95 Ω
Steady state zero offset caused by heating
0 to -8 W/m2
CALIBRATION
Calibration traceability
to WRR
Calibration hierarchy
from WRR through ISO 9846 and ISO 9847, applying a
correction to reference conditions
Calibration method
indoor calibration according to ISO 9847, Type IIc
Calibration uncertainty
< 1.8 % (k = 2)
Recommended recalibration interval
2 years
Reference conditions
20 °C, normal incidence solar radiation, horizontal mounting,
irradiance level 1000 W/m2
Validity of calibration
based on experience the instrument sensitivity will not change
during storage. During use under exposure to solar radiation
the instrument “non-stability” specification is applicable.
MEASUREMENT ACCURACY AND RESOLUTION
Uncertainty of the measurement
statements about the overall measurement uncertainty can
only be made on an individual basis.
WMO estimate on achievable accuracy for
daily sums
5 % (WMO-No. 8, seventh edition 2008)
WMO estimate on achievable accuracy for
hourly sums
8 % (WMO-No. 8, seventh edition 2008)
Irradiance resolution
0.01 W/m2
00.16131.501030 –
DIGITAL MODBUS RTU (RS-485)
Digital output
irradiance in W/m2
instrument body temperature in °C
Rated operating voltage range
5 to 30 VDC (recommended 12 VDC)
Power consumption
< 48 x 10-3 W at 12 VDC (unheated)
Heater
included
Communication protocol
Modbus over 2-wire RS-485
half duplex
RS-485 transceiver type
2-wire, non-isolated
Transmission mode
RTU

10
00.16131.501040 –
ANALOGUE 4 TO 20 mA
4 to 20 mA output
irradiance in W/m2
Transmitted range
0 to 1600 W/m2
Output signal
4 to 20 x 10-3 A
Standard setting (see options)
4 x 10-3 A at 0 W/m2 and 20 x 10-3 A at 1600 W/m2
Principle of 4 to 20 mA output
2-wire current loop
Rated operating voltage range
5 to 30 VDC (recommended 12 VDC)
Recommended operating voltage
12 VDC
Power consumption
< 240 x 10-3 W at 12 VDC
Heating
not included
00.16131.501000 -
ANALOGUE mV
Millivolt (mV) output
irradiance in W/m2
Sensitivity range
7 to 15 x 10-6 V/(W/m2)
Sensitivity (nominal)
10 x 10-6 V/(W/m2)
Expected voltage output
application under natural solar radiation: -0.1 to +30 x 10-3 V
Measurement function / required programming
E = U/S
U: Voltage output in V
S: Sensitivity in V/(W/m2)
E: Solar irradiance in W/m2
Irradiance resolution
depends on readout equipment; 7 x 10-6V data logger
resolution is sufficient for 1 W/m2 resolution in irradiance
Required readout
1 differential voltage channel or 1 single ended
voltage channel, input resistance > 106Ω
Sensor resistance range
50 to 150 Ω

11
3.2 Dimensions of 16131.5
Figure 3.2.1 Dimensions of 16131.5 in x 10-3 m
95
Ø 92
M6
Ø 68
46
M5 (2x)

12
4 Installation of 16131.5
4.1 Site selection and installation
Table 4.1.1 Recommendations for installation of pyranometers
Location
The horizon should be as free from obstacles as possible.
Ideally, there should be no objects between the course of the
sun and the instrument.
Mechanical mounting / thermal insulation
Use connection by bolts to the bottom plate of the instrument.
A pyranometer is sensitive to thermal shocks. Do not mount
the instrument with the body in direct thermal contact to the
mounting plate (so always use the levelling feet also if the
mounting is not horizontal), do not mount the instrument on
objects that become very hot (black coated metal plates).
Instrument mounting with 2 bolts
2 x M5 bolt at 46 x 10-3 m centre to centre distance on north-
south axis, connection from below under the bottom plate of
the instrument.
Instrument mounting with one bolt
1 x M6 bolt at the centre of the instrument, connection from
below under the bottom plate of the instrument.
Performing a representative measurement
The pyranometer measures the solar radiation in the plane of
the sensor. Some installations require a tilted or inverted
position. The sensor bottom plate, parallel to the black sensor
surface, should be mounted parallel to the plane of interest.
In case a pyranometer is not mounted horizontally or in case
the horizon is obstructed, the representativeness of the
location becomes an important element of the measurement.
See the chapter on uncertainty evaluation.
Levelling
In case of horizontal mounting, use the bubble level and
levelling feet. The bubble level is visible and can be inspected
at all times.
Tilted installation
For tilted installation, the tilt sensor provides a sufficiently
accurate measurement. The register “tilt angle” can be used
when mounting and levelling the sensor.
Instrument orientation
By convention: with the cable exit pointing to the nearest pole,
so the cable exit should point north in the northern
hemisphere, south in the southern hemisphere.
Installation height
In case of inverted installation, WMO recommends a distance
of 1.5 m between soil surface and sensor (reducing the effect
of shadows and in order to obtain good spatial averaging).

13
4.2 Installation of the sun screen
The quick release system of 16131.5’s sun screen allows for easy and secure mounting of the sun
screen on the sensor. Installation and removal of the connector can be done after removal of the sun
screen.
Release sun screen: The system consists of a spring loaded lever opposite the bubble level window of
the 16131.5 sun screen. The bottom of the handle can be pulled out gently. Once the handle is pulled
out and fully released, as shown in the figure below, the sun screen can be lifted off manually for
removal.
Installing the sun screen: pull out the bottom of the quick release system handle so it is fully released,
place the screen on 16131.5 and, once it is positioned properly, press the handle of the quick release
system until it is locked.
Figure 4.2.1 16131.5’s sun screen with its quick release system and bubble level window
Figure 4.2.2 Installation of 16131.5’s sun screen

14
4.3 Installation of pyranometer
LAMBRECHT meteo provides several mounting set for the 16131.5 pyranometer.
Id-No. 32.14627.003010 Set for inclined mounting on traverse system 14627
Id-No. 32.14627.003000 Set for horizontal mounting on traverse system 14627
Id-No. 33.14627.012000 Set for wall mounting
The picture below shows the installation of the 16131.5 on the “Set for inclined mounting” as an
example. The whole pattern for mounting the 16131.5 is the same for all the sets mentioned above.
Figure 4.3.1 Mounting of 16131.5 on Set for inclined mounting on traverse system 14627
(1) 16131.5 pyranometer
(2 mounting plate for pyranometer*
(3) fixation for mounting on traverse system 14627*
(4) TORX M4 x 16 TX20 DIN 7985 TX A2
(5) washer 4.3 DIN 125 A A2
(6) washer 5.3 DIN 125 A A2
(7) hexagon screw M8 x 16 DIN 933 A2
(8) nut M5 DIN 934 A2
(9) nut M8 DIN 985 A2
(10) nut M4 DIN 985 A4
(11) setscrew M4 DIN 985 A4
* Parts of the “Set for inclined mounting on traverse system 14627”

15
4.4 Electrical connection of active 16131.5 series: wiring diagram
The instrument must be powered by an external power supply, providing an operating voltage in the
range from 8 to 30 VDC. This is the main power supply for the sensor, using the brown and white
wires.
Figure 4.4.1: Connector layout of 16131.5, indicating PIN numbers (viewed from cable side)
4.4.1 Wiring diagram 00.16131.501030 - Modbus RTU
Table 4.4.1.1 Wiring diagram of 00.16131.501030
PIN WIRE
00.16131.501030
Modbus over RS-485
1 Brown VDC [+]
2 White VDC [−] / heater [-]
3 Blue RS-485 B / B’ [+]
4 Black RS-485 A / A’[−]
5 Grey heater [+]
Shield mesh shield
Note 1: At the connector-end of the cable, the shield is connected to the connector housing.
Note 2: The heater is powered by applying a voltage to the grey wire, an operating voltage of 12 VDC
is used.
Note 3: Do not put more than 30 Volt across these wires, this will damage the sensor.
4.4.2 Wiring diagram 00.16131.501040 - Modbus RTU
Table 4.4.2.1 Wiring diagram of 00.16131.501040
PIN WIRE
00.16131.501040
Modbus over TTL
00.16131.501040
4 to 20 mA output
1 Brown
On request
VDC [+]
2 White not connected
3 Blue 4 to 20 mA output
4 Black not connected
5 Grey not connected
Shield mesh shield
Note 1: At the connector-end of the cable, the shield is connected to the connector housing.

16
4.5 Electrical connection of passive 16131.5: wiring diagram
16131.5 is a passive sensor that does not need any power. Cables generally act as a source of
distortion, by picking up capacitive noise. We recommend keeping the distance between a datalogger or
amplifier and the sensor as short as possible. For cable extension, see the appendix on this subject.
Table 4.5.1 Wiring diagram of 00.16131.501000
PIN WIRE
00.16131.501000
Analogue millivolt output
1 Brown heater
4 Black heater
3 Blue not connected
2 White signal [+]
5 Grey signal [-]
Shield mesh shield
Note 1: The heater is a resistive heater element
Note 2: At the connector-end of the cable, the shield is connected to the connector chassis and
thereby to the sensor housing
4.6 Grounding and use of the shield
Grounding and shield use are the responsibility of the user. The cable shield (called shield in the
wiring diagram) is connected to the aluminium instrument body via the connector. In most situations,
the instrument will be screwed on a mounting platform that is locally grounded. In these cases the
shield at the cable end should not be connected at all. When a ground connection is not obtained
through the instrument body, for instance in laboratory experiments, the shield should be connected to
the local ground at the cable end. This is typically the ground or low voltage of the power supply or the
common of the network. In exceptional cases, for instance when both the instrument and a datalogger
are connected to a small size mast, the local ground at the mounting platform is the same as the
network ground. In such cases ground connection may be made both to the instrument body and to
the shield at the cable end.
4.7 Using heater of 00.16131.501030 and 00.16131.0501000
00.16131.501030 and 00.16131.501000 have an on-board heater. Heating the sensor contributes to
the dependability and accuracy of the measurement, helping to prevent dew and frost deposition. The
heater is typically switched on at night-time only. During daytime it is recommended to switch off the
heater. Note that using the heater without any additional ventilation may cause zero offsets.
External ventilation can be used to reduce or eliminate the effect of heating. Note that when the heater
is not used, it has no impact on the instrument specifications.
The integrated heater is a resistive element with a constant resistance. This means that the generated
heating power increases with the applied voltage. When the heater resistance R, and voltage V, are
known, the generated heater power P, is given by:
P = V2/ R
A heating power of approximately 1.5 W is typically sufficient. With a heater resistance of 95 Ω, as
specified in the specifications table, 12 VDC is required to generate this power.

17
4.8 Using 00.16131.501040’s analogue 4 to 20 mA output
16131.5 gives users the option to use 4 to 20 mA output instead of its digital output. When using 4 to
20 mA output, please read this chapter first.
Using the 4 to 20 mA output provided by 00.16131.501040 is easy. The instrument can be connected
directly to commonly used data-logging systems.
The irradiance, E, in W/m2 is calculated by the formula:
E = 1600·(I - 4 x 10-3A)/(16 x 10-3A) I: Current output in A
E: Solar irradiance in W/m2
By convention 0 W/m2 irradiance corresponds with 4 x 10-3 A transmitter output current I. The
transmitted range, which is the irradiance at output current of 20 x 10-3 A, and is typically 1600 W/m2.
It is important to realise that the signal wires not only act to transmit the signal but also act as
power supply for the 4-20 mA current loop circuit!
Figure 4.8.1 Electrical diagram of the connection of 00.16131.501040 to a typical ampere meter or
datalogger with capability to measure current signals.
Usually a 100 Ω shunt resistor (R) is used to convert the current to a voltage (this will then be in the
0.4 – to 2 VDC range). This resistor must be put in series with the blue wire of the sensor.
00.16131.501040
brown [+] blue 4 to 20 mA output
A
ground
power supply 5 to 30 VDC
ampere meter
I = 4 to 20 mA
shield

18
Figure 4.8.2 Electrical diagram of the connection of 00.16131.501040 to a typical voltmeter or data-
logger with the capability to measure voltage signals.
4.9 Data acquisition requirements for using 00.16131.501000’s millivolt output
The selection and programming of data loggers is the responsibility of the user. The LAMBRECHT
meteo data logger Ser[LOG] Plus is ideally suited for solar irradiance measurement using a
pyranometer with millivolt output.
00.16131.501000 can usually be treated in the same way as other thermopile pyranometers.
Table 4.9.1 Requirements for data acquisition and amplification equipment for 00.16131.501000 in the
standard configuration
Capability to measure small voltage
signals
preferably: 5 x 10-6 V uncertainty
minimum requirement: 20 x 10-6 V uncertainty
(valid for the entire expected temperature range of the acquisition /
amplification equipment)
Capability for the data logger or the
software
to store data, and to perform division by the sensitivity to calculate the
solar irradiance.
E = U/S
Data acquisition input resistance
> 1 x 106Ω
Open circuit detection
(WARNING)
open-circuit detection should not be used, unless this is done
separately from the normal measurement by more than 5 times the
sensor response time and with a small current only. Thermopile
sensors are sensitive to the current that is used during open circuit
detection. The current will generate heat, which is measured and will
appear as an offset.
00.16131.501040
brown [+] blue 4 to 20 mA output
V
ground
power supply 5 to 30 VDC
voltmeter
I = 4 to 20 mA
shield
R I = U/R

19
4.10 Connecting to an RS-485 network
16131.5 is designed for a two-wire (half-duplex) RS-485 network. In such a network, 16131.5 acts as
a slave, receiving data requests from the master. An example of the connection to an RS-485 two-wire
network is shown in the figure below. 16131.5 is powered from 5 to 30 VDC. The power supply is not
shown in the figure. The VDC [-] power supply ground must be connected to the common line of the
network. [Modbus over serial line specification and implementation guide V1.02 (www.modbus.org).]
After the last nodes in the network, on both sides, line termination resistors (LT) are required to
eliminate reflections in the network. According to the RS-485 standard, these LT have a typical value
of 120 to 150 Ω. Never place more than two LT on the network and never place the LT on a derivation
cable. To minimise noise on the network when no transmission is occurring, a pull up and pull down
resistor are required. Typical values for both resistors are in the range from 650 to 850 Ω.
Figure 4.10.1 Connecting 16131.5 to a typical RS-485 network
[+] 12 VDC (heater)
[+] 5 to 30 VDC
[-
]5 to 30 VDC / [-] 12 VDC (heater)
common
[+] data
[-
]data, RS-485 A / A’
16131.5 wire
white
black
blue
grey
brown
,RS-485 B / B’
RS-485 network
shield
shield

20
5 Communication with 16131.5
5.1 Modbus-protocol
The Lambrecht meteo Modbus sensors and the met[LOG] follow the specification of the Modbus
organization: "MODBUS APPLICATION PROTOCOL SPECIFICATION V1.1b3"
(see www.modbus.org).
5.2 Data encoding
MODBUS uses the "big-endian" format for addresses and data. This means that if a value is
transmitted with a number format that is larger than a single byte, the "most significant byte" is sent
first. For values that go beyond one register (e.g. 32 bit) this is not clearly specified for the Modbus. In
these cases (32 bit or 64 bit) the LAMBRECHT Modbus sensors follow the big-endian number format.
Example Big-Endian:
Register size value
16 - Bits 0x1234 is transmitted in the order: 0x12 0x34.
Example big-endian (32bit or 64bit):
Register size value
32 - Bits 0x12345678 is transmitted in the order: 0x12 0x34 0x56 0x78.
5.3 Device-address
The addresses 1...247 are permitted for Modbus.
Warning: Using the same Modbus address for more than one device will lead to irregular behaviour of
the entire network.
5.4 Standard configuration - default
Baud rate: 19200 Baud
Address: Each sensor type (or family) has its own default address.
Table 5.4.1 Default addresses of the LAMBRECHT sensors
Address
Sensor
1
Wind speed
2
Wind direction
3
Precipitation rain[e]
4
THP
5
EOLOS IND
6
com[b]
7
PREOS
8
ARCO
9
u[sonic]
10
Pyranometer 2nd Class
11
Secondary standard Pyranometer, First Class Pyranometer
12
PT100 to Modbus converter (temperature)
Byte frame according to MODBUS standard for RTU mode:
8E1 (1 start bit, 8 data bits, 1 parity bit (even parity), 1 stop bit)
Table of contents
Other Lambrecht Measuring Instrument manuals
Popular Measuring Instrument manuals by other brands
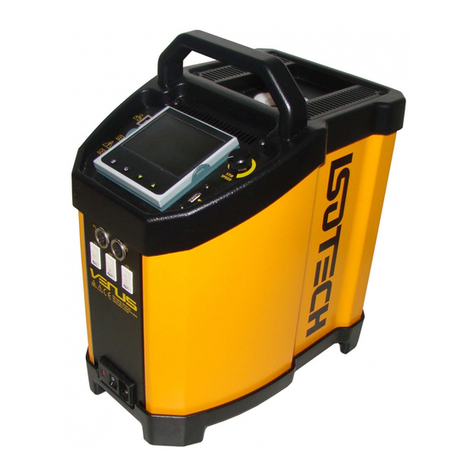
Isotech
Isotech VENUS 4951 BASIC Maintenance manual
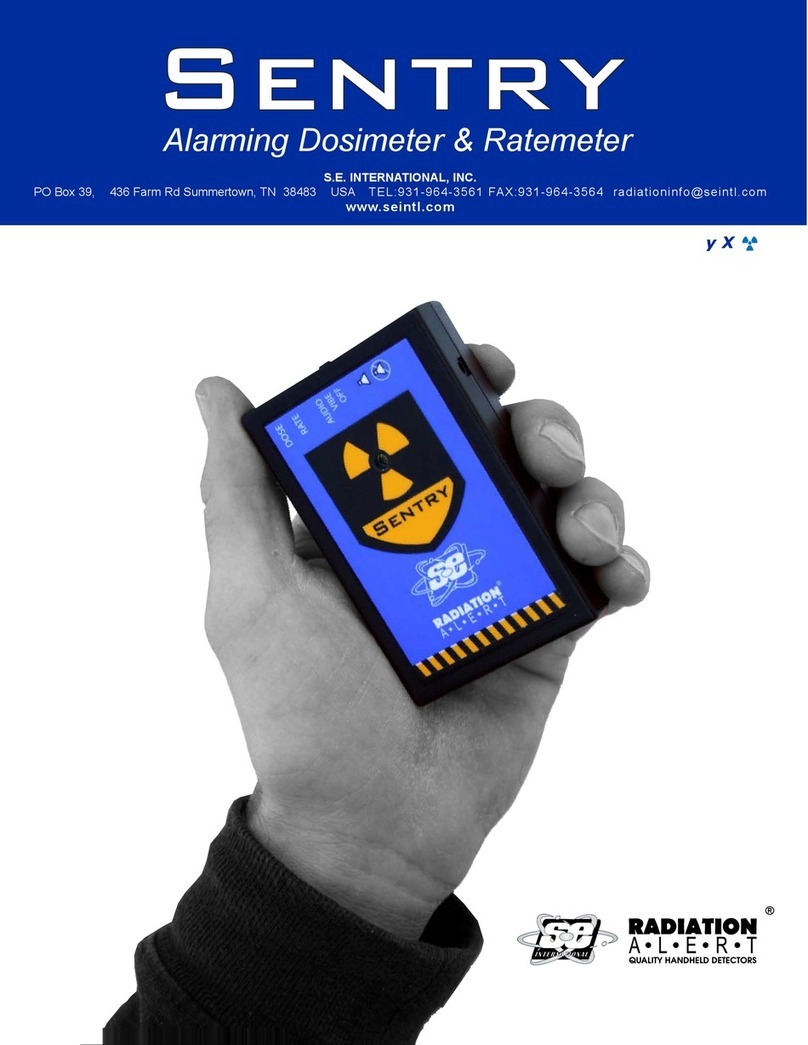
S.E. International
S.E. International Sentry user manual
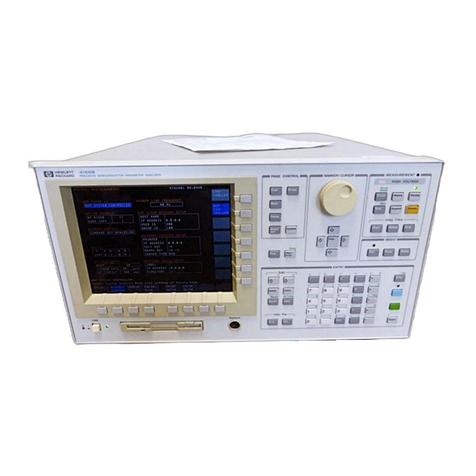
Agilent Technologies
Agilent Technologies 4156b user guide

ABQINDUSTRIAL
ABQINDUSTRIAL Dakota Ultrasonics ZX-2 instruction manual
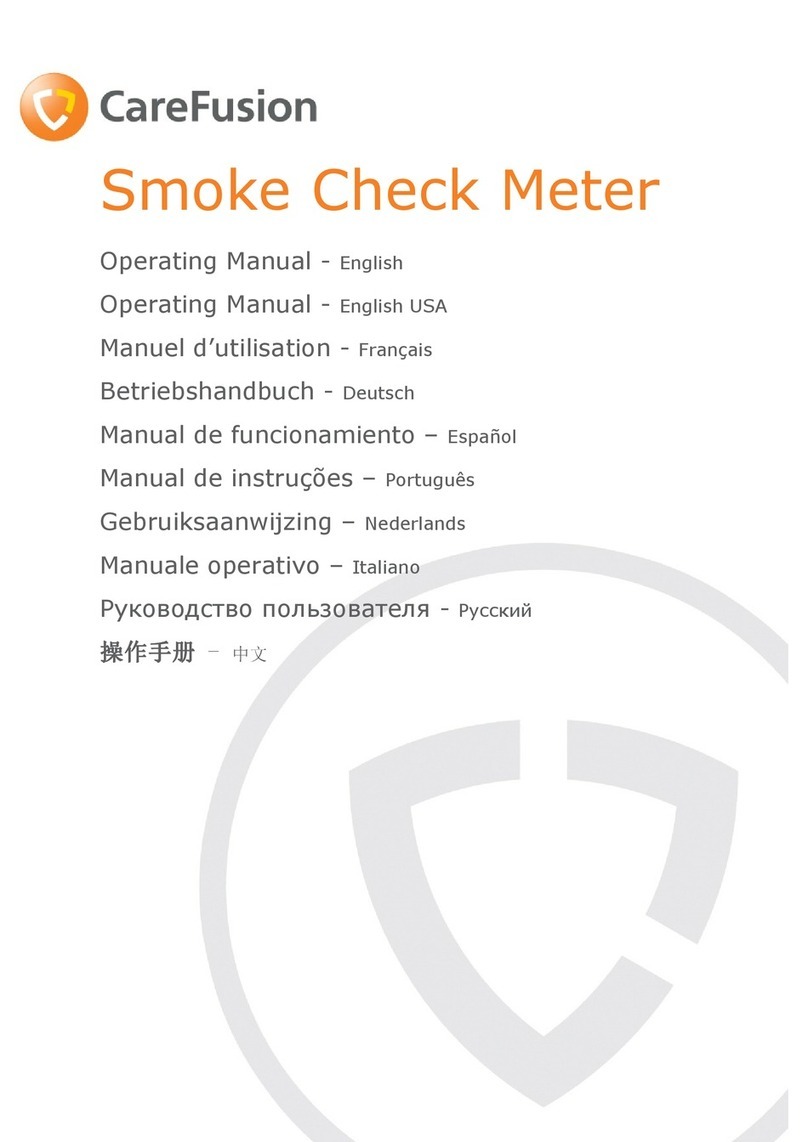
Care Fusion
Care Fusion SC01 operating manual

red lion
red lion PAX Lite Series manual