Levitronix PuraLev i30SU User manual

User Manual for PuraLev®i30SU
www.levitronix.com
PL-4051-00, Rev03, DCO# 20-275
First Release: 01-May-2016
Last Update: 18-Dec-2020
PuraLev®i30SU
1.0 bar (14.5 psi)
7.7 liters/min (2.0 gallons/min)
USER MANUAL
This manual contains information necessary for the safe and proper use of the PuraLev®i30SU. Included
are specifications for the standard configurations of the flow control system and instructions regarding its
use, installation, operation, adjustment, inspection and maintenance. For special configurations of the
pump system refer to accompanying information. If the pump system must be configured for other
parameter settings, then the Levitronix®Service Software version V2.0.5.0 or higher (with relevant manual
Levitronix
Doc.# PL-4043-00) is necessary. Familiarize yourself with the contents of the manual to
ensure the safe and effective use of this product. After reading this manual, please store the manual
where the personnel responsible for operating the flow control system can readily refer to it at any time.

User Manual for PuraLev®i30SU
www.levitronix.com
PL-4051-00, Rev03, DCO# 20-275
2
Table of Contents
1SAFETY PRECAUTIONS...............................................................................................................................................................3
2SPECIFICATIONS..........................................................................................................................................................................4
2.1 Specification of Components.................................................................................................................................................4
2.2 System Overview and General Specification.........................................................................................................................6
2.3 General Environmental Conditions........................................................................................................................................9
2.4 Pressure-Flow Curves.........................................................................................................................................................10
2.5 Maximum Static Pressure for Pump Heads.........................................................................................................................10
2.6 Basic Dimensions of Main Components..............................................................................................................................11
3ENGINEERING INFORMATION...................................................................................................................................................14
3.1 Power Supply and Consumption.........................................................................................................................................14
3.2 Temperature Monitoring......................................................................................................................................................14
3.3 Thermal Management.........................................................................................................................................................15
3.4 Hydraulic Circuit Design......................................................................................................................................................17
4INSTALLATION ...........................................................................................................................................................................18
4.1 Electrical Installation of Stand-Alone Model.........................................................................................................................18
4.2 Electrical Installation of EasyConnect Model.......................................................................................................................21
4.3 Electrical Installation of OEM Model....................................................................................................................................26
4.4 Mechanical Installation –General Instructions.....................................................................................................................30
4.5 Mechanical Installation of Stand-Alone and EasyConnect Model ........................................................................................30
4.6 Mechanical Installation of OEM Model ................................................................................................................................30
5OPERATION................................................................................................................................................................................31
5.1 Operation of Stand-Alone Model.........................................................................................................................................31
5.2 Operation of EasyConnect and OEM Model........................................................................................................................34
5.3 Operation for ATEX / IECEx Application..............................................................................................................................36
6INSTRUCTIONS FOR USE OF PUMP HEAD ..............................................................................................................................37
6.1 Description and Preparation................................................................................................................................................37
6.2 General Warnings and Cautions .........................................................................................................................................37
6.3 Mounting of Pump Head......................................................................................................................................................38
6.4 Removal of Pump Head......................................................................................................................................................38
6.5 Assembly into Hydraulic Circuit...........................................................................................................................................38
7TROUBLESHOOTING .................................................................................................................................................................39
7.1 Trouble Shooting with Stand-Alone Model...........................................................................................................................39
7.2 Trouble Shooting with EasyConnect and OEM Models........................................................................................................39
8TECHNICAL SUPPORT...............................................................................................................................................................39
9APPENDIX...................................................................................................................................................................................40
9.1 Regulatory Status ...............................................................................................................................................................40
9.2 Symbols and Signal Words.................................................................................................................................................41

User Manual for PuraLev®i30SU
www.levitronix.com
PL-4051-00, Rev03, DCO# 20-275
3
1 Safety Precautions
The PuraLev®i30SU pump system is designed to be used in industrial production machines and laboratory
equipment containing hydraulic circuits. Typical applications are Single-Use Bioprocessing manufacturing
equipment. Installation shall be done by qualified personnel only. Following safety precautions and all
“CAUTION”, “WARNING” and “DANGER” indications in the relevant sections shall be followed.
CAUTION
Do not under any circumstances open the driver. Levitronix®does not assume
responsibility for any damage, which occurs under such circumstances.
CAUTION
High magnetic field strength of pump impeller.
The pump system contains a rotor magnet with high field strength. This may
alter or damage the calibration of sensitive electronic devices and measuring
instruments in the immediate surroundings. Keep at a safe distance from
computers, monitors and all magnetic data storage media (e.g. disks, credit
cards, audio and video tapes etc.)
!
WARNING
Hazardous voltage may be present.
In case of the usage of an inadequate AC/DC power supply, mains voltages
may be present (even if the system is designed for up to 24 VDC). The usage
of a galvanic separated power supply, which is certified by a 3rd party (UL or
CE), is highly recommended.
Do not under any circumstances open the powered driver.
!
WARNING
High magnetic field strength of pump impeller.
The pump system contains a rotor magnet with high field strength.
Pacemakers may be influenced and magnetic forces may lead to contusions.
Keep distance to pacemakers and handle impeller with care.
!
WARNING
TOXIC CHEMICALS may be present.
When using the system to pump chemicals skin contact and toxic gases may
be hazardous to your health. Wear safety gloves and other appropriate safety
equipment.
!
WARNING
Pump Driver for ATEX / IECEX applications.
Only specific types of integrated Pump Drivers are classified for the use in Ex
classified locations. Refer to the corresponding section in the manual.

User Manual for PuraLev®i30SU
www.levitronix.com
PL-4051-00, Rev03, DCO# 20-275
4
2 Specifications
2.1 Specification of Components
Figure 1: Pump systems with standard components
Figure 2: General standard accessories
Figure 3: Standard cables
7
8a
8b
9
10
12
C
A
C
B
4
6
5a
5b
5c
D
D
F
E
A
2a
2b
2c
3
1a
1e
2d
A
11
1b
B
B
C
C

User Manual for PuraLev®i30SU
www.levitronix.com
PL-4051-00, Rev03, DCO# 20-275
5
System Name
Article #
Pump Head Socket
Driver
Note
PLD-i30SU.1
PLD-i30SU.6
100-90955
100-91514
PHS-i30.1
PHS-i30.1
IPD-30.1-50-02
IPD-30.12-50-02
OEM - Driver, 5 m PVC cable with open wires, pump head socket
OEM - ATEX/IECEx - 5 m FEP cable with open wires, pump head socket.
PLD-i30SU.2
100-91025
PHS-i30.1
IPD-30.3-02 (MBP-i30.1 included)
EasyConnect - Driver with interface connectors, pump head socket.
PLD-i30SU.3
100-91026
PHS-i30.1
IPD-30.5-02 (MBP-i30.1 included)
Stand-Alone - Driver with integrated user panel, pump head socket.
Table 1: Standard driver system configurations
Pos.
Component
Article Name
Article #
Characteristics
Value / Feature
1a
1b
Single-Use (SU)
Pump Head
DCP-30.2 (Barb)
DCP-30.1 (Triclamp)
100-90968
100-90959
Material Impeller/Housing
Housing Sealing
In-/Outlet Fittings
Polypropylene (FDA, USP Class VI, BSE/TSE/Animal free)
Infrared welding
Max. Flow
Max. Diff.-Pressure
Max. Viscosity
Max. Liquid Temp.
7.7 liters/min / 2.0 gallons/min
1.0 bar / 14.5 psi
40 cP
60 °C / 140 °F
Wet Pump
Volume/Surface
7.7 ml / 55.9 cm2
Sterilization Methods
Gamma radiation up to 40kGy
1c
1d
Irradiated SU Pump
Head
DCP-30.2-G25 (Barb)
DCP-30.1-G25 (Tricl.)
100-91071
100-91170
Applied Gamma Dosage
≥ 25 kGy
1e
Irradiated SU Pump
Head
with Sterile Fittings
DCP-30.2-SF1-G25
100-91234
Pump Type (A) / Tubing (C)
Sterile Fittings (B)
Fitting Compatibility
Applied Gamma Dosage
DCP-30.2 (Barb) / Silicone
AseptiQuik
S from CPC
with part # AQS17006 3
Various sizes and types including autoclavable versions available at CPC®
2a
Integrated Pump Driver
(“OEM Model”)
IPD-30.1-50-02
100-10088
Voltage, Power
Housing / Cable
Interfaces
Standard Firmware
24 VDC ±10%, 35 W
Epoxy coated Alu., PP for bottom lid, IP651/ PVC jacket, open wires, cable 5 m
PLC and RS485 with Modbus protocol
H2.48
2b
Integrated Pump Driver
(“EasyConnect” Model)
IPD-30.3-02
(MBP-i30.1 included)
100-10097
Housing
Interfaces
Standard Firmware
Epoxy coated Aluminum, PP for bottom lid, IP65
2x Fieldbus RS485 with Modbus protocol, PLC and power supply
H2.48 2
2c
Integrated Pump Driver
(“Stand-Alone” Model)
IPD-30.5-02
(MBP-i30.1 included)
100-10098
Housing
Interfaces
Standard Firmware
Epoxy coated Aluminum, PP for bottom lid, IP65
User panel with 3 user buttons, PLC and power supply
H2.25
2d
Integrated Pump Driver
ATEX /IECEx
(“OEM Model” only)
IPD-30.12-50-02
100-10203
Housing / Cable
Interfaces
ATEX / IECEx Marking
Standard Firmware
ETFE coated Alu., IP651/ FEP jacket, open wires, cable length 5 m
PLC and RS485 with Modbus protocol
II 3G Ex ec h mc IIC T4 Gc / II 3D Ex h tc IIIC T90°C Dc
H2.48
3
Pump Head Socket
PHS-i30.1
100-90947
Mounting Type
Material
Assembly Screws
Bayonet type with locking pin
Anodized Aluminum
4 pcs M3 x 6 mm (Stainless Steel, INOX A4)
Table 2: Specification of standard components
Note 1: Designed and tested for IP67. Note 2: Special firmwarefor serial pumping as one unit (Figure 6) available on request. Note 3: CPC®and AseptiQuik®are registered marks of the Colder Product Company.
Pos.
Component
Article Name
Article #
Characteristics
Value / Feature
4
Mounting Base Plate
MBP-i30.1
190-10313
Material / Mounting
Screws
PP + 30% GF / 2 pieces, stainless steel FEP coated, M3 x 10 mm
5a
AC/DC Power Supply
TPC 055-124 (Traco)
100-40014
Voltage Output / Input
Basic Dimensions
Certification or Standards
24 VDC with 55 W / 85 264 VAC, 47-63 Hz
45 x 90 x 96.5 mm (mountable on DIN rail 35 mm)
UL, CSA, CB, Semi F47
5b
Desktop AC/DC Power
Supply
AC/DC Power Supply
VEC50US24 HR30
100-40015
Voltage Output / Input
Basic Dimensions
Safety Approvals
Note
24VDC, 50W / 90 264 VAC, 47-63 Hz
116 x 52 x 31 mm
IEC60950-1, EN60950-1, UL/cUL60950-1
Connector for direct connection to power supply of driver with 1.2m cable.
5c
AC Mains Cables
(for Desktop power supply 5b)
AMC-1.1 (2m)
AMC-1.2 (2.5m)
AMC-1.3 (2.5m)
AMC-1.4 (2.5m)
AMC-1.5 (2.5m)
190-10331
190-10332
190-10333
190-10334
190-10335
Approvals and Country
Approvals and Country
Approvals and Country
Approvals and Country
Approvals and Country
Cable Specifications
UL, cUL, US, Canada
CB, Germany, Denmark, Norway, Finland, Belg., Netherl., Sweden, Austria
PSE, Japan
Switzerland
CE, United Kingdom
Black color, ROHS
6
USB to RS485
Adaptor-TR Isolated
YN-485I-TR
100-30392
Structure/Design
USB connector (A) with termination resistor and cable (2m) with connector
pair (B and C) for external RS485 wire connection. Magnetically isolated.
Cable length is 2m. Included is a USB space saver cable (D).
Purpose
Communication over fieldbus of driver with PC
7
IPS Cable Power 3
Wires
ICP-1.1-50 (5 m)
190-10342
Cable Material / Wires
Connection In / Out
Main Purpose
PVC jacket / 3x 0.5 mm 2 (only 2 wires used, 1 is cut)
Open wires / Circular Hirose type to driver
Connection of -
8a
IPS Cable Signal 6
Wires
ICS-1.1-01 (0.1 m)
ICS-1.1-10 (1 m)
ICS-1.1-30 (3 m)
190-10343
190-10344
190-10345
Cable Material / Wires
Connection In / Out
Main Purpose
PVC jacket / 6x 0.08 mm2and shielding
Circular Hirose type / Circular Hirose type
-pump arrays)
8b
IPS Cable Signal 6
Wires
ICS-1.2-50 (5 m)
190-10346
Cable Material / Wires
Connection In / Out
Main Purpose
PVC jacket / 6x 0.08 mm2and shielding
Connector with screw type plug for open wire connection / Circular Hirose
type
-
9
IPS Cable Signal 12
Wires
ICS-2.1-50 (5 m)
190-10347
Cable Material / Wires
Connection In / Out
Main Purpose
PVC jacket / 12x 0.14 mm2and shielding
Connector with screw type plug for open wire connection / Circular Hirose type
10
Fieldbus Termination
Connector
FTC-1.1
190-10348
Materials
Main Purpose
PPS for connector housing and FPM for sealing.
Termination of fieldbus.
11
User Panel
LUI-B.1-01
100-30448
Interface / Housing Rating
Standard Firmware
RS485 / IP65
A3.00
12
ATEX Cable
Sealing System
ACS-A.1
(Roxtec)
100-90292
Sleeve (A) and Gasket (B)
Frame (C)
2x Cable Module (D)
Stainless Steel and EPDM
Roxylon (EPDM rubber)
Roxylon (EPDM rubber)
Note:
Lubricant (E) and measurement
plates (F) are included.
Table 3: Specification of accessories
Note 1: Designed and tested for IP67.

User Manual for PuraLev®i30SU
www.levitronix.com
PL-4051-00, Rev03, DCO# 20-275
6
2.2 System Overview and General Specification
2.2.1 System Configuration for Stand-Alone Model
Figure 4 illustrates the system configuration of the Stand-Alone model with integrated user panel and buttons
to set the speed manually. The driver also contains a PLC interface for remote speed control by analog and
digital signals. Various accessories are available like a desktop power supply with relevant power cable and
signal cables to connect to the PLC.
Figure 4: Standard system configuration for Stand-Alone model
2.2.2 System Configurations for EasyConnect Model
The EasyConnect model (see Figure 5 and Figure 6) with relevant cable accessories is designed to realize
various interface configurations with minimal setup effort. The PLC interface allows not only remote control
by analog/digital signals but also connections of external sensors hence enabling for example a precise flow
or pressure control (see notes below).
Figure 5: Standard system configuration for EasyConnect model
Integrated Pump Driver
Stand-Alone Model
Power Supply
Connector
Single-Use
Pump Head
Outlet
Inlet
PLC Connector
Option for Remote
Control with PLC Signals
Back-Side Display with
3 Button User Interface
for Speed Setting and Reading
IPS Cable Signal
Screw type connector for open-wires
connection included in cable package
Bayonet Socket
with Locking Pin Power Supply
Connector
Desktop
AC/DC
Power
Supply
AC Input
DC Output
AC Cable
(International Adaptors)
Integrated Pump Driver
EasyConnect Model
AC/DC
Power
Supply
(DIN-Rail)
AC InputDC Output
Power
Supply
PLC
Fieldbus
OUT
Fieldbus
IN
PC Connection:
- System configuration
- Firmware update
- Monitoring
IPS Cable Power
IPS Cable
Signal
Open Wires
Single-Use
Pump Head
Outlet
Inlet
Bayonet Socket
with Locking Pin
PLC Interface:
- Remote control with speed signal
- Flowcontrol with external sensor
- Pressure control with ext. sensor
- 24VDC supply for sensors included
IPS Cable Signal Screw type connector for
open-wires connection
included in cable package.
USB to RS485
Converter Cable
IPS Cable
Signal User Panel
1
3
2b
5a
7
1
3
8b
2c
5b
5c
8b
6
8a
9
As an option the desktop power
supply can be attached as shown
-
11

User Manual for PuraLev®i30SU
www.levitronix.com
PL-4051-00, Rev03, DCO# 20-275
7
Two Fieldbus connectors (IN and OUT) allow to setup arrays of multiple pumps. Therefore serial pumping
configurations as shown in Figure 6 can be realized.
Figure 6: Multi-pump array for serial pumping with EasyConnect models
Note: Specific firmware for serial pumping as one unit available on request.
2.2.3 System Configurations for OEM Models
The OEM model, with one integrated cable only, is design for compact integration into an equipment. When
using the pump system in speed control mode, the speed can precisely be set via an analog input. Various
digital inputs and outputs allow controlling and monitoring of the system. A RS485 enables communication
with a PC with the Levitronix®Service Software. Hence parameterization, firmware updates and failure
analysis are possible. The RS485 can also be used as a fieldbus to implement more intelligent concepts of
pump control.
Figure 7: System configuration of OEM model for speed control
Integrated Pump Driver
EasyConnect Model
#1
Outlet
Inlet
Power
Supply PLC Fieldbus
OUT
Fieldbus
IN
IPS Cable Signal
Integrated Pump Driver
EasyConnect Model
#2
Power
Supply PLC Fieldbus
OUT
Fieldbus
IN
Integrated Pump Driver
EasyConnect Model
#3
Power
Supply PLC Fieldbus
OUT
Fieldbus
IN
IPS Cable Signal
24 VDC
Supply 24 VDC
Supply 24 VDC
Supply
IPS Cable Power
Remote Control of Array
over PLC or RS485
IPS Cable Signal
IPS Cable Signal
Fieldbus
Termination
Connector
Single-Use
Pump Head Single-Use
Pump Head Single-Use
Pump Head
Integrated Pump Driver
OEM Model
PLC Interface:
- Analog and digital IO s
- Remote control with speed signal
- Flowcontrol with external sensor
- Pressure control with ext. sensor
AC/DC
Power
Supply
(DIN-Rail)
AC InputDC Output
PC Connection:
- System configuration
- Firmware update
- Monitoring
Open
Wires
Screw type connector for
open-wires connection
included in converter cable
package.
Integrated
Driver Cable
Cable Bushing
DC Supply 24 V
Single-Use
Pump Head
Outlet
Inlet
Bayonet Socket
with Locking Pin
USB to RS485
Converter Cable
User Panel
24VDC
Fieldbus
RS485
2b
2b
2b
7
7
7
1
3
9
8b
8a
8a
10
6
5a
1
3
2a
8b
11
Pin Designation
LUI-B.1 Cable 8b:
1: RS485+ 2: RS485-
3: GND 4: NC
5: NC 6: +24VDC

User Manual for PuraLev®i30SU
www.levitronix.com
PL-4051-00, Rev03, DCO# 20-275
8
The PLC interface of the OEM model enables the implementation of precise closed loop flow or pressure
control in connection with either a flow or pressure sensor (see Figure 8). Precise ultrapure flow control
systems can be realized in combination with LEVIFLOW®flowmeters.
Figure 8: System configuration of OEM model for process control
(Pressure or flow control with external sensor, details in Section 4.3.1)
2.2.4 System Configuration for OEM ATEX / IECEx Models
Together with the defined pump heads an ATEX / IECEx certified pump driver allows installation of the pump
within an Ex classified area (see Figure 9 and Figure 10). One option to lead the driver cable outside of the
Ex area is to use an Ex certified cable sealing system as listed in Table 3.
Figure 9: System configuration of OEM Ex model for speed control
Integrated Pump Driver
OEM Model
Outlet
PLC Interface:
- Analog and Digital IO s
- Remote Control
AC/DC
Power
Supply
(24VDC, DIN-Rail)
AC InputDC Output
PC Connection:
- System configuration
- Firmware update
- Monitoring
Open
Wires
Screw type connector for
open-wires connection
included in converter cable
package.
Integrated
Driver Cable
Cable Bushing
Flow
or Pressure
Sensor
Sensor Feedback for
Flow or Pressure Control
Single-Use
Pump Head
Inlet
Bayonet Socket
with Locking Pin
USB to RS485
Converter Cable
User Panel
24VDC
Fieldbus
RS485
Integrated Ex Pump Driver
OEM Model
Outlet
Inlet
PLC Interface:
- Analog and Digital IO s
- Remote Control with Speed Signal
- Flowcontrol with external Sensor
- Pressure Control with ext. Sensor
AC/DC
Power
Supply
(DIN-Rail)
AC InputDC Output
PC Connection:
- System configuration
- Service and Firmware update
- Monitoring
Open Wires
Fieldbus Interface:
- Remote control with fieldbus
- Connection to PC
Screw type connector for
open-wires connection included in
converter cable package. Fieldbus
RS485 of Driver
Integrated Driver Cable
Cable Bushing
DC Supply 24 V
USB to RS485
Converter with Cable
Cabinet Boundary for
Ex classified Area
Ex conform cable
sealing system
Ex classified
Location
Single-Use
Pump Head
Bayonet Socket
with Locking Pin
1
2d
6
5a
12
5a
6
1
3
2a
8b
11

User Manual for PuraLev®i30SU
www.levitronix.com
PL-4051-00, Rev03, DCO# 20-275
9
Figure 10: System configuration of OEM Ex model for process control
(Pressure or flow control with external sensor.)
2.3 General Environmental Conditions
Usage
Indoor
Altitude
Up to 2000 m
Operating ambient temperature
0 to 40 °C
Storage ambient temperature
(Extremes for Transportation)
-20 to 80 °C
-20 to 70 °Cfor single-use pump head
Operating humidity range (relative humidity)
15 –95%(non-condensing)
Storage humidity range (relative humidity)
(Extremes for Transportation)
15 –95%(non-condensing)
Normal storage conditions
Ambient temp.: 20 to 30 °C
Relative humidity: 50% (non-condensing)
DC supply fluctuations
10% of nominal voltage
Transient over-voltages typically present on
the mains supply
Surge immunity according to EN 61000-4-5
(tested together with certified AC/DC power supply)
Pollution degree
2
Table 4: Environmental conditions for pump system
Integrated Ex Pump Driver
OEM Model
Outlet
Inlet
PLC Interface:
- Analog and Digital IO s
- Remote Control
AC/DC
Power
Supply
(24VDC, DIN-Rail)
AC InputDC Output
PC Connection:
- System configuration
- Service and Firmware update
- Monitoring
Open Wires
Fieldbus Interface:
- Remote control with fieldbus
- Connection to PC
Screw type connector for
open-wires connection included in
converter cable package. Fieldbus
RS485 of Driver
Integrated Driver Cable
Cable Bushing
Sensor Feedback for
Flow or Pressure Control
USB to RS485
Converter with Cable
Ex classified
Location
Cabinet Boundary for
Ex classified Area
Ex conform cable
sealing system
Flow
or Pressure
Sensor
Single-Use
Pump Head
Bayonet Socket
with Locking Pin
12
2d
1
6
5a

User Manual for PuraLev®i30SU
www.levitronix.com
PL-4051-00, Rev03, DCO# 20-275
10
2.4 Pressure-Flow Curves
Figure 11: Pressure/flow rate curves of DCP-30 pump head
2.5 Maximum Static Pressure for Pump Heads
Figure 12: Specification for maximum static pressure of pump head DCP-30
Note 1: Pressure limits only valid for pump head mounted on motor and do not account for tubing limits attached to the fittings.
Note 2: The above chart is also applicable to the DCP-30.2-SF1-G25 with sterile fittings.
0
2
4
6
8
10
12
14
16
0.0 0.5 1.0 1.5 2.0
0.0
0.2
0.4
0.6
0.8
1.0
0 1 2 3 4 5 6 7 8
[psi]
[gallons / min]
[bar]
[liters / min]
6000 rpm
13000 rpm
12000 rpm
11000 rpm
10000 rpm
8000 rpm
Specific gravity = 1g/cm3
Viscosity = 0.7cP
Liquid Temp.: 40C
9000 rpm
7000 rpm
5000 rpm
0
10
20
30
40
50
60
70
80
77 87 97 107 117 127 137
0
1
2
3
4
5
6
25 30 35 40 45 50 55 60
[psi]
[°F]
[bar]
Liquid Temperature in [°C]
Max. Static Pressure for DCP-30
Safety Factor = 1.3 (according to EN12162)
Note: Burst pressure is significantly higher.
Ambient Temp = 25 C
Note: Pressure limit only valid for pumphead mounted on motor. Values
only valid after Gamma radiation doses of < 40 kGy.

User Manual for PuraLev®i30SU
www.levitronix.com
PL-4051-00, Rev03, DCO# 20-275
11
2.6 Basic Dimensions of Main Components
Figure 13: Basic dimensions (in [mm] and [inch]) of Stand-Alone model
Note 1: Drawings with DCP-30.1 (Triclamp) and DCP-30.2-SF1 (Sterile Fittings) are available on request.
Figure 14: Basic dimensions (in [mm] and [inch]) of EasyConnect model
Note 1: Drawings with DCP-30.1 (Triclamp) and DCP-30.2-SF1 (sterile fittings) are available on request.
2c
1
Single-Use
Pump Head
DCP-30.2
Driver IPD-30.5
Protective Cover for PLC
Connector
(Included in driver Package).
Mounting Base Plate MBP-i30.1
(Included in driver Package).
4
Pump Head Inlet and Outlet Fitting:
3
Pump Head Socket
PHS-i30.1
Locking Pin
Note: Pump Head Socket can be
mounted and rotated in steps of 45° to
change pump outlet orientation.
2b
1
Single-Use
Pump Head
DCP-30.2
Driver IPD-30.3
Protective Cover Nut for
PLC and Fieldbus Connectors
(Included in driver package).
Pump Head Inlet and Outlet Fitting:
3
Pump Head Socket
PHS-i30.1
Locking Pin
Note: Pump Head Socket can be
mounted and rotated in steps of 45° to
change pump outlet orientation.
Mounting Base Plate MBP-i30.1
(Included in driver Package).
4

User Manual for PuraLev®i30SU
www.levitronix.com
PL-4051-00, Rev03, DCO# 20-275
12
Figure 15: Basic dimensions (in [mm] and [inch]) of OEM model
Note 1: Drawings with DCP-30.1 (Triclamp) and DCP-30.2-SF1 (sterile fittings) are available on request
Figure 16: Basic dimensions (in [mm] and [inch]) of OEM driver of mounting base plate MBP-i30
2a
Slot for Driver Mounting
with M4 screws
Driver IPD-30.1
Mounting Base Plate
MBP-i30.1
Material: PP+GF30
Countersunk Head Screws
M3 x 10mm, FEP coated
1a
Pump Head
DCP-30.2
Driver IPD-30.1
(Epoxy Coating)
Driver Cable
(PVC with Open Wires)
Multi-purpose screw
holes 4 pcs M3 x 4 mm
Multi-purpose screw holes
2 pcs M3 x 4 mm screws with
FKM O-ring for protection
Pump head inlet and outlet fitting:
3
Pump Head Socket
PHS-i30.1
Note: Pump head socket can be mounted
and rotated in steps of 45° to change
pump outlet orientation.
2d
Driver IPD-30.11
ATEX/IECEx
(ETFE Coating)
Driver Cable
FEP with Open Wires)

User Manual for PuraLev®i30SU
www.levitronix.com
PL-4051-00, Rev03, DCO# 20-275
13
IPS Cable Power ICP-1.1 (for EasyConnect and Stand-Alone drivers)
IPS Cable Signal ICS-1.1 (for EasyConnect drivers)
IPS Cable Signal ICS-1.2 (for EasyConnect and Stand-Alone drivers)
IPS Cable Signal ICS-2.1 (for EasyConnect drivers)
Figure 17: Basic dimensions and specifications of standard cables
Cable
Jacket
Cable
Diameter
Minimum Bending Radius
Permanent Installation
Minimum Bending Radius
Sometimes Moved
PVC
8.4 mm
7x Cable OD
15 x Cable OD
Table 5: Specifications for min. bending radius of cables
Note: If not mentioned explicitly all the cables are not suited for constant dynamic bending and movement!
to AC/DC Supply
to driver DC supply
7
to driver fieldbus IN
8a
to driver fieldbus OUT
8b
to external interface
EasyConnect driver: to field bus
Stand-Alone driver: to PLC
Screw type wire
connector
9
to external PLC
to driver PLC
Screw type wire
connector
Wire size: 0.5 mm2
Wire size: 0.08 mm2
Wire size: 0.08 mm2
Wire size: 0.14 mm2

User Manual for PuraLev®i30SU
www.levitronix.com
PL-4051-00, Rev03, DCO# 20-275
14
3 Engineering Information
3.1 Power Supply and Consumption
3.1.1 Power Consumption
Figure 18: Electrical power consumption
(Measured on OEM model with DCP-30 pump head but also representative for EasyConnect and Stand-Alone models)
3.1.1 Inrush Current
When selecting a AC/DC power supply the inrush currents (currents during power-on) shown in Table 6 shall
be considered. If the specifications of the power supply are unclear a test with multiple power-on cycles is
recommended to assure proper operation.
Situation
I2tValue in [A2s]
Peak Value in [A]
Driver with 0.5m cable length
3.5
216
Driver with 5 m cable length
1.7
114
Table 6: Inrush currents of power supply driver during power on of driver
(Measured at 24 VDC + 10% on OEM model but also representative for EasyConnect and Stand-Alone models)
3.1.2 Evaluation of Power Supplies
If other power supplies than the standard specified ones are used, it is recommended to evaluate them
under demanding operating situations like fast braking from maximum speed and during power on and take-
off of the impeller.
3.2 Temperature Monitoring
To avoid overheating of the system, the controller and motor temperatures within the driver are monitored. If
one of both temperatures exceeds 80°C (176°F) for a period of more than 10 minutes, the system goes into
an error state and the pump stops. At 90°C (194°F), the system stops immediately.
If 65°C is exceeded a warning is given within the driver announcing to the user that the driver is running near
the thermal limit (see explanation in Section 3.3). For the EasyConnect and OEM models the warning signal
can be monitored with the Levitronix®Service Software or configured on one of the digital outputs. For the
Stand-Alone model the temperature can be monitored on the display.
0.0 0.5 1.0 1.5 2.0
0
5
10
15
20
25
30
0 1 2 3 4 5 6 7 8
[gallons/min]
[Watts]
[liters/min]
5000 rpm
13000 rpm 12000 rpm
11000 rpm
10000 rpm
9000 rpm
8000 rpm
7000 rpm
6000 rpm
Specific gravity = 1g/cm3
Viscosity = 0.7cP
Liquid Temp.: 40C

User Manual for PuraLev®i30SU
www.levitronix.com
PL-4051-00, Rev03, DCO# 20-275
15
3.3 Thermal Management
The driver temperature depends on the ambient and liquid temperature, as well as on the hydraulic operation
point. Figure 19 and Figure 20 illustrate the temperature characteristics of the motor depending on these
parameters.
Figure 19: Temperature curves for the IPD-30.1-50 driver @ 25°C liquid temperature
(Pumping with pump head DCP-30, temperature is measured inside of the integrated motor and controller,
contact temperature of surface is below this temperature)
Figure 20: Temperature curves for the IPD-30.1-50 driver @ 60°C liquid temperature
(Pumping with pump head DCP-30, temperature is measured inside of the integrated motor and controller,
contact temperature is below this temperature)
77
97
117
137
157
177
0.0 0.5 1.0 1.5 2.0
25
35
45
55
65
75
85
012345678
[°F]
[gallons/min]
[°C]
[liters/min]
Ambient Temp = 25C
Liquid Temp. = 25C
Specific gravity = 1g/cm3
Viscosity = 0.7cP
Temp. Time Constant = ~40min
Recommended Operational Limit
Absolute Thermal Limit
13000 rpm 12000 rpm 11000 rpm
10000 rpm
9000 rpm
8000 rpm
7000 rpm
6000 rpm
77
97
117
137
157
177
0.0 0.5 1.0 1.5 2.0
25
35
45
55
65
75
85
012345678
[°F]
[gallons/min]
[°C]
[liters/min]
Ambient Temp = 25C
Liquid Temp. = 60C
Specific gravity = 1g/cm3
Viscosity = 0.7cP
Temp. Time Constant = ~40min
Recommended Operational Limit
Absolute Thermal Limit
13000 rpm 12000 rpm 11000 rpm
10000 rpm
9000 rpm
8000 rpm
7000 rpm
6000 rpm

User Manual for PuraLev®i30SU
www.levitronix.com
PL-4051-00, Rev03, DCO# 20-275
16
The above curves are measurements of the motor temperature at certain liquid and ambient temperatures.
Equation (Eq. 1) shows how to calculate the motor temperature for other liquid and ambient temperatures
based on these curves.
(
(Eq. 1)
All above presented thermal data are typical values, which are partly based on measurements and partly on
interpolations with a simplified thermal model and are therefore only guideline values and are suitable for a
first layout of the basic thermal concept. It is recommended to check the thermal values with the motor
placed on the final location and under worst case performance conditions of the application.
In order to account for thermal variations (like ambient temperature, closed chemical cabinets or corners
without ventilations) and to not significantly reduce the MTBF of the motor it is recommended to keep about
15°C safety distance to the absolute thermal limit of the driver (80°C) when designing the thermal concept of
the pump system.
It is recommended to avoid thermal stagnation in the room or cabinet where the driver is placed. Any type of
circulation decreases the driver temperature significantly.

User Manual for PuraLev®i30SU
www.levitronix.com
PL-4051-00, Rev03, DCO# 20-275
17
3.4 Hydraulic Circuit Design
Following general design rules help to operate the pump system optimally considering efficiency, optimum
priming behavior and low shear forces:
1. The general rule for minimum shear forces and optimum priming behavior is to minimize the
pressure drop in the inlet circuit and avoid negative pressure at the inlet of the pump head.
2. Minimize tubing length at the inlet of the pump head and maximize the ID (not smaller than the
pump head inlet ID of 1/4” = 6.5 mm is recommended). This reduces the pressure drop and the
tendency of cavitation.
3. Avoid any restrictions, valves, elbows, bended tubing and sharp edges at the inlet circuit of the
pump head, which potentially cause cavitation resulting in higher shear forces and bubble
collection in the pump head with the danger of priming loss.
4. Place the pump at the lowest point of the hydraulic circuit. Optimum is as much as possible
below a tank or reservoir. This optimizes priming behavior and keeps the inlet pressure positive
for low shear forces.
5. Keep the liquid level in the reservoir tank or bag as high as possible, which increases the inlet
pressure of the pump head and minimized heat up of the liquid.
6. When horizontal mounting of the driver the optimum outlet angle of the pump head is 45 degree
(see Figure 28) hence allowing gas bubbles to leave the pump head and keep it primed.
7. To minimize heat up of the liquid the overall pressure drop in the hydraulic circuit shall be
reduced as much as possible.
8. It shall be avoided to pump longer times against a closed valve, which can cause heat-up of the
liquid and higher shear forces.
9. At higher liquid temperature rules mentioned above become more important due to higher
cavitation tendency of the liquid.
Contact the Levitronix®Technical Service department (see Section 8) for more detailed considerations and
support on the design of the hydraulic circuit.

User Manual for PuraLev®i30SU
www.levitronix.com
PL-4051-00, Rev03, DCO# 20-275
18
4 Installation
4.1 Electrical Installation of Stand-Alone Model
4.1.1 Overview of Connections and Designations
Figure 21: Electrical connections to Stand-Alone driver IPD-30.5
Pin #
Pin
Name
Wire
Color 1
Description
Standard
Designation 2
Specifications
Typical Levels
Note
2
P +
red
+ 24 VDC
Power Supply
Voltage: 24 VDC ±10%
Power: 35 W
“P -“ shall be connected to earth
1
P -
black
Ground/Earth
3
NC
white
Not connected
--
Wire of compatible cables is cut.
Wire of compatible cables is cut.
Table 7: Power supply connector of Stand-Alone driver model
1: Wire colors of compatible cables: ICP-1.1-xx. 2: Designations for standard firmware. For other firmware refer to relevant documentation.
Pin #
Pin
Name
Wire
Color 1
Description
Standard
Designation 2
Typical Levels
Note
6
Ain1
pink
Analog Input
Remote
Speed
4..20 mA = 0..16000 rpm
-> Speed limit = 13000rpm
-> Cut-off (min.) speed = 0 rpm
450 Ohm shunt input, no galvanic isolation.
blue
5
Ain_GND
red
Analog Input
Ground
--
--
Reference to Ain1.
1
Dout1
white
Digital Output
Status
Closed circuit active, system on
Open circuit not active, system off
Open drain, max. 24V, 100mA
This signal indicates the state of the pump
system.
3
GND
brown
Ground
--
--
Reference to Dout1
black
Shield
2
Din1
yellow
Digital Input
PLC Enable
Edge triggered:
0 V 5-24 V Enable
5-24 V 0 V Disable
For enabling of the system with external signal.
Galvanic separation with optocoupler and
2.2 kinput resistance.
4
Din_COM
grey
Common
Digital Input
--
--
Reference to Din1.
Table 8: PLC connector of Stand-Alone driver model
1: Wires of compatible cables: ICS-1.1-xx and ICS-1.2-xx.
2: Designations for standard firmware H2.25. For other firmware refer to relevant documentation.
Power Supply
Connector
PLC Connector

User Manual for PuraLev®i30SU
www.levitronix.com
PL-4051-00, Rev03, DCO# 20-275
19
4.1.2 Overview Electrical Schematics of Driver Interface
Figure 22: Electrical schematics of interfacing for Stand-Alone driver model
Levitronix Driver
Interface Circuit Example of User
Interface Circuit
450
2.2 k
Pin 1: Digital Output
Pin 4: Common Digital Input
Pin 2: Digital Input
Pin 5: Analog Input Ground
Pin 6: Analog Input
Pin 3: Ground (GND)
Pin 3: Cable Shield
Analog inputs are not galvanic isolated.
Max. pin voltage to GND = 10 V
Max. 24 V / 100 mA
Open
Drain R > 240
Relais
AC/DC Supply
24 VDC
Pin 2: Power 24 VDC
Pin 1: Power Ground/Earth
30 V
5..24 V
4..20 mA
GND
GND
24 V
5 A
PLC 6 Interface
Power Supply

User Manual for PuraLev®i30SU
www.levitronix.com
PL-4051-00, Rev03, DCO# 20-275
20
4.1.3 Installation Instructions for Power Supply
!
WARNING
Hazardous voltage may be present.
Always isolate the electrical power supply before making or changing
connections to the unit.
In case of the usage of an inadequate AC/DC power supply, mains
voltages may be present (even if the system is designed for 24 VDC).
The usage of a galvanic separated power supply, which is certified by
a 3rd party (UL or CE), is highly recommended.
1. A certified and tested desktop power supply with a specific connector is available as an
accessory (see Error! Reference source not found.), which allows simple direct connection to t
he driver.
2. For other power supplies an open wire power cable for connection to the driver is specified in
Table 3 (cable type ICP-1.1). Depending on the required hydraulic operational point (see Figure
11), the pump system requires 24V with a maximum power of 35 W. At a lower performance
power supplies with smaller power or bigger supplies to supply several pump systems
simultaneously may be used. Consult Figure 18 to get the power consumption depending on the
flow. If other power supplies are used, than the one recommended by Levitronix®, it is highly
recommended to test these under dynamic conditions (acceleration and braking of the pump
rotor speed).
3. Make sure that the polarity is correct and that AC/DC power supply is off.
4.1.4 Installation PLC Interface Signals
To operate the pump system with a PLC the analog input can be used to set the speed. The digital output
can be used to monitor the pump status and operating parameters (see Table 8).
CAUTION
The analog is not galvanically isolated from the controller
electronics. To avoid ground loops and malfunctions, use
floating analog signals.
1. Power off the system.
2. A signal cable with driver connector is available to simplify PLC wire connections (see Table 3
cable type ICS-1.2). Connect the designated PLC wires according to Table 8.
3. Follow Figure 22 as reference for hardware configuration of the PLC in/outputs.
4. Protect the un-used wires against short-circuit to each other
Table of contents
Other Levitronix Measuring Instrument manuals
Popular Measuring Instrument manuals by other brands
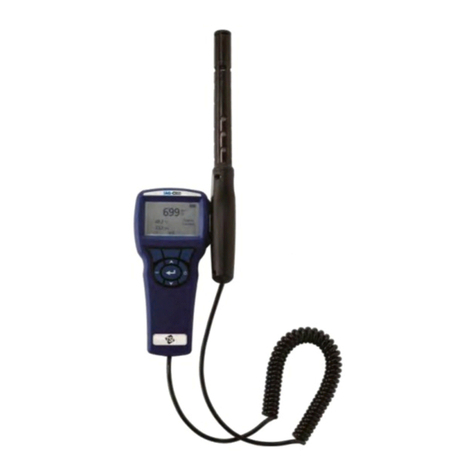
TSI Incorporated
TSI Incorporated IAQ-CALC 7515 Operation and service manual
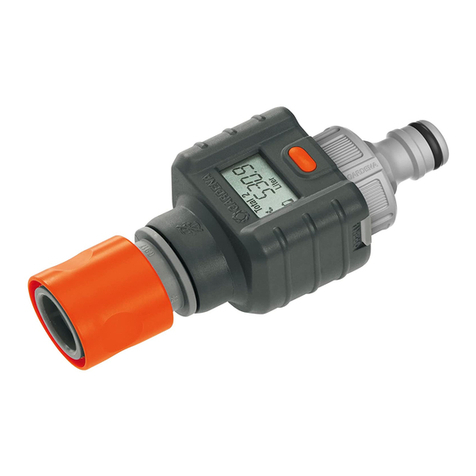
Gardena
Gardena 8188 operating instructions
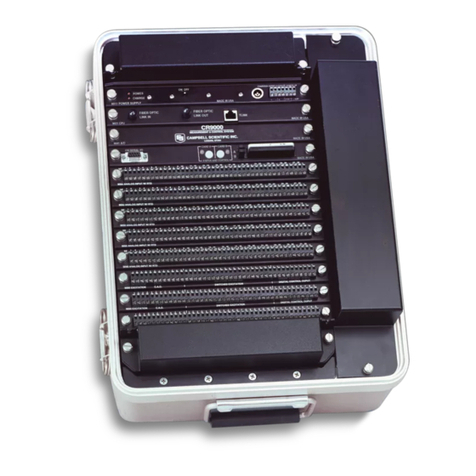
Campbell
Campbell CR9000 instruction manual
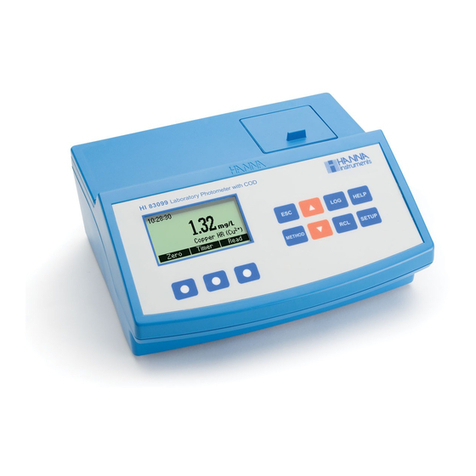
Hanna Instruments
Hanna Instruments HI 83099 instruction manual

SICK
SICK DUSTHUNTER SP100 Ex-3K operating instructions
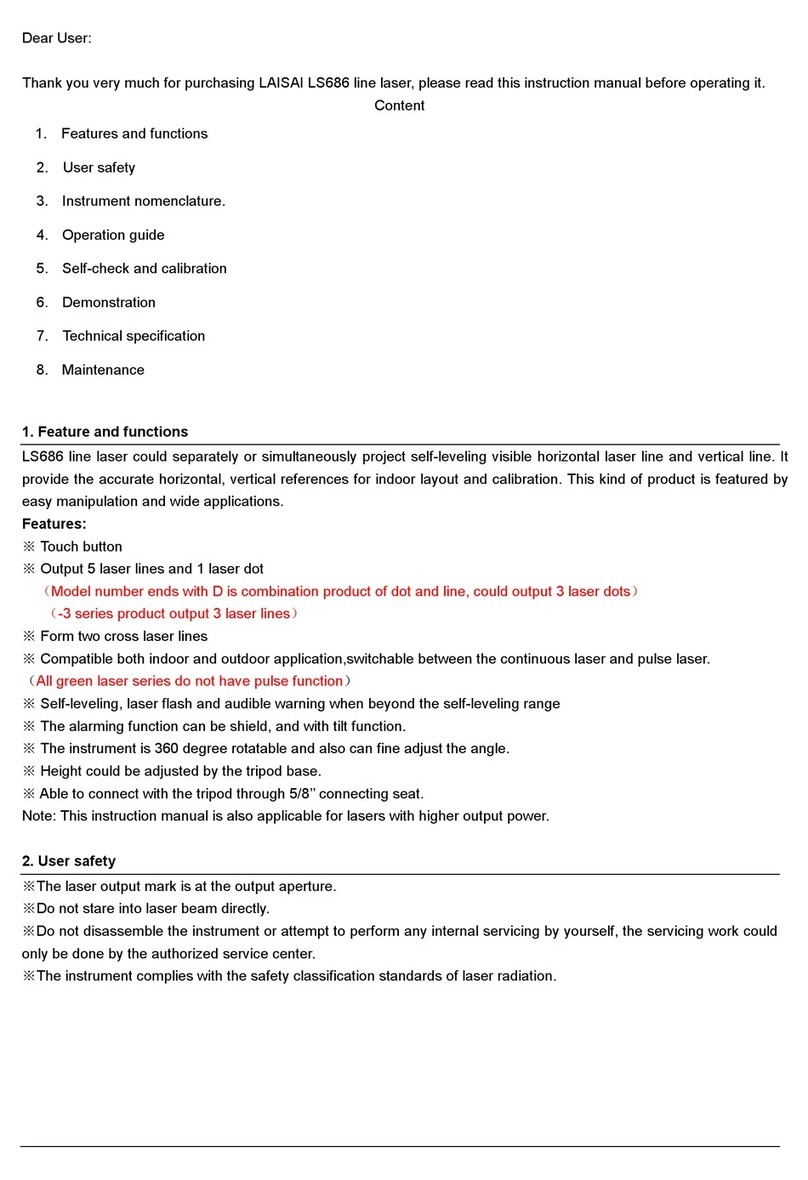
LAISAI
LAISAI LS686 user guide