LG MODBUS-RTU User manual

MODBUS-RTU
Option Board for
SV-iS5 Series
Read this manual carefully before using the MODBUS-RTU Option board
and follow the instructions exactly.
After reading this manual, keep it at handy for future reference.
LG Industrial Systems


Thank you for purchase of LG Modbus-RTU Option Board!
SAFETY PRECAUTIONS
Always follow safety precautions to prevent accidents and potential hazards from occurring.
Safety precautions are classified into “WARNING” and “CAUTION” in this manual.
WARNING
CAUTION
Throughout this manual we use the following two illustrations to make you aware of safety
considerations:
Identifies potential hazards.
Read the message and follow the instructions carefully.
Identifies shock hazards.
Particular attention should be directed because dangerous voltage may be present.
Keep this manual at handy for quick reference.
CAUTION
Do not touch the CMOS components unless the board is grounded.
ESD can cause break down of CMOS components.
Do not change the communication cable with the inverter power is turned on.
Otherwise, there is a danger of connecting error and damage to the board.
Make sure to precisely insert the connector of inverter and option board
Otherwise, there is a danger of connecting error and damage to the board.
Indicates a potentially hazardous situation which, if not avoided, can
result in serious injury or death.
Indicates a potentially hazardous situation which, if not avoided, can
result in minor to moderate injury, or serious damage to the product.

Check the parameter unit when setting the parameters.
Otherwise, there is a danger of connecting error and damage to the board.
modbus-rtu iS5 manual.doc 2

INTRODUCTION
By using a MODBUS-RTU Option board, SV-iS5 inverter can be connected to a MODBUS-RTU network.
1.1.
When you use the MODBUS-RTU Option Card …
Inverter can be controlled and monitored by the sequence program of the PLC or other master module. The
card provides a terminal block for an RS-485 interface. Up to 32 drives or other Modbus slave devices may
be connected in a multi-drop fashion on the RS-485 Modbus network and may be monitored or controlled by
a single PLC or PC.
1.1.1 Interfacing type of RTU Reference:
- Allows the drive to communicate with any other computers.
- Allows connection of up to 31 drives with multi-drop link system.
- Ensure noise-resistant interface.
Users can use any kind of RS232-485 converters. However a converter that has built-in ‘automatic RTS
control’ is highly recommended. The specifications of converters depend on the manufacturers. Refer to the
converter manual for detailed converter specifications.
1.1.2 Before Installation
Before installation and operation, this manual should be read thoroughly. If not, it can cause personal injury
or damage other equipment.
SPECIFICATION
2.1.
Performance specification
Items Specifications
Communication method RS485
Transmission form Bus method Multi-drop Link System
Applicable inverter IS5 series drive
Number of drives Maximum 31 drives connectable
Transmission distance Max. 1200m (Less than 700 m recommended)
1
modbus-rtu iS5 manual.doc

Converter RS232-485, Use PC with RS232 card embedded
2.2.
Hardware Specifications
Installation CN2 connector on the inverter control board
Power
Supply
Control B/D From inverter power supply
Comm. B/D From control board (insulated)
modbus-rtu iS5 manual.doc 2

2.3.
Communication Specification
Communication speed 1200 /2400/4800/9600/19200 bps Selectable
Control procedure Asynchronous communication system
Communication system Half duplex system
Character system Binary (8 bit)
Start/Stop bit 1 bit
Error check (CRC16) 2 byte
Parity check None
PRODUCT DETAIL
3.1.
Layout and detail
Name Description
Connector CN2, Connector to inverter main PCB
Signal
connection
terminal
Communication
signal connection
terminal
P 485 signal - high
N 485 signal – low
G 485 Ground
S Shield
T1
T2
Short T1 and T2 to connect a
termination resistor
3
modbus-rtu iS5 manual.doc

Figure 1. Layout
3.2.
Status LED
CPU LED Indicates normal operation of the board when blinking once per second.
RXD LED Receiving 485 signal
TXD LED Responding to 485 signal
ERR LED
On and Off intermittently Wrong DATA received (Normal
operating)
Blinking with CPU LED at the same
time
DPRAM communication fault
Blinking with CPU LED in an
opposite way
Network Connection TimeOut <I/O-49>
elapsed
INSTALLATION
1. Connect the option board to the inverter control board using each connector on the board (See the
Figure 1).
modbus-rtu iS5 manual.doc 4

2. Double check the board is firmly installed to the board and then apply the inverter power.
3. When power ON, CPU LED is blinking per second after all LEDs blink one after another.
4. If “CPU LED” is not blinking, turn off the inverter power swiftly (if not, inverter and the board may
get damaged.) and check for the proper installation of the board. If the problem persists, contact
LG distributor.
5. Check ModBus-RTU is displayed in <COM-01>.
6. Set the parameters as below when the above steps are all done.
Parameter code Display Setting Value
< COM-01 > Opt B/D MODBUS displayed automatically
< COM-02 > Opt mode Set the Command controlled via
communication
< I/O- 46 > Inv. number 1~31
(Verify the assigned number is not duplicated)
< I/O- 47 > Baud-rate 9600 bps (Factory default)
< I/O- 48 > Lost command (Note1) User setting
< I/O- 49> TimeOut (Note 1) 0.1 sec (Factory default)
Note 1) it is used for Emergency Stop when communication between inverter and master is not done
properly. It is activated when communication is not done even once for the set time. It means remote
controlling of inverter is not done. Set this value for safety
7. Turn off the inverter power for the connection of the Converter when step 6 is finished.
8. if the inverter is to be placed at the end of the network trunk line, install a jumper at JP1 on the
Modbus card to enable the termination resistor.
TROUBLE SHOOTING
If communications cannot be established with the drive, there are four LEDs on the Modbus card to aid in
troubleshooting. The CPU LED should blink once per second to indicate that the modbus card is interfacing
with the inverter main PCB properly. The RXD LED should blink each time a properly formed Modbus
message is received that is addressed to the inverter. The RXD LED will not blink when messages are
received that are addressed to other inverters or devices. The TXD LED should blink each time the inverter
responds to a Modbus message. The ERR LED indicates either an invalid request was received or there is
a problem with the Modbus card itself. The ERR LED should never light.
5
modbus-rtu iS5 manual.doc

CPU LED
State Indicates Corrective measures
Blinking Card is installed properly and working
normally
Off Card is not installed properly Verify that the card is installed
properly
Inverter is not operating normally Verify that the inverter has power
RXD and TXD LEDs
State Indicates Corrective measures
Blinking Card is functioning normally and receiving
and sending messages
modbus-rtu iS5 manual.doc 6

Off Incorrect Modbus connection to the card Verify that the Low signal is
connected to terminal N and the
High signal is connected to
terminal P
Master is not polling
Verify that the master (PLC or
PC) is polling the inverter.
Incorrect baud rate setting
Verify that the baud rate (I/O47) is
set to match the baud rate of the
inverter.
Incorrect byte format
The inverter communicates using
8 data bits, 1 stop bit and no
parity bits. Verify that the master
is set to the same.
7
modbus-rtu iS5 manual.doc

ERR LED
State Indicates Corrective measures
On/off from
time to time
The card is receiving invalid data such
as noise.
Normal
Blinking with
CPU LED at the
same time
Trouble with the Modbus card Cycle the Inverter power. If the
problem persists, contact LG
Blinking after
CPU LED one
after another
Network communication is not done
during TimeOut (I/O 49) setting.
Verify that the master is
specifying valid register
addresses and valid data.
Off The card is functioning normally and
receiving and sending messages
*See COM group for Frequency/Run command setting.
modbus-rtu iS5 manual.doc 8

2 PARAMETER CODE (HEX)
<Common> : Area accessible regardless of inverter models (Note 3)
Paramet
er
Address
Parameter Name Unit Read/Write Data Value (Hex)
0x0000 Drive model - R 4: SV-iS5
0x0001 Drive capacity - R
0: 0.75 1:1.5 2:2.2 3: 3.7
4: 5.5 5: 7.5 6: 11 7: 15 8:
18.5 9: 22 A: 30 B:37 C:45
D: 55 E: 75 F: 90 10: 110
11: 132 12: 160 13: 200
14:220 15:280 16:375 (Unit
: kW)
0x0002 Drive Input Voltage - R 0: 220V 1: 440V
0x0003 S/W Version - R 0100: Ver. 1.00,
0101: Ver 1.01
0x0005 Frequency
Reference 0.01Hz R/W
0x0006 Run Command - R/W
Bit 0: Stop
Bit 1: Forward Run
Bit 2: Reverse Run
Bit 3: Fault Reset
Bit 4: Emergency Stop
0x0007 Acceleration Time 0.1 sec R/W
0x0008 Deceleration Time 0.1 sec R/W
0x0009 Output Current 0.1 A R
9
modbus-rtu iS5 manual.doc

Paramet
er
Address
Parameter Name Unit Read/Write Data Value (Hex)
0x000A Output Frequency 0.01 Hz R
0x000B Output Voltage 0.1 V R
0x000C DC Link Voltage 0.1 V R
0x000D Output Power 0.1 kW R
0x000E Sequence Monitor - R
BIT 0 : Stop
BIT 1 : Forward Run
BIT 2 : Reverse Run
BIT 3 : Fault (Trip)
BIT 4 : Accelerating
BIT 5 : Decelerating
BIT 6 : Output Frequency
Arrival
BIT 7 : DC Braking
BIT 8 : Stopping
BIT 9 :Not Available
BIT 10 : BrakeOpen
BIT11: Forward Run
Command
BIT 12 : Reverse Run
Command
0x000F Trip information - R
Bit 0:OCT1, Bit 1: OV, Bit 2:
EXT-A Bit 3: BX, Bit
4:OCT2, Bit 5: GF, Bit 6:
OH, Bit 7: ETH, Bit 8: OLT,
Bit 9: HW-diag, Bit10:EXT-
B, Bit11:FO Bit12:OPT,
Bit13:PO Bit,14:IOLT,
Bit15:LV
modbus-rtu iS5 manual.doc 10

Paramet
er
Address
Parameter Name Unit Read/Write Data Value (Hex)
0x0010 Input Terminal
Status - R
Bit 0: P1, Bit 1: P2, Bit 2: P3
Bit 3: P4, Bit 4: P5, Bit 5:
P6,
Bit 6: RST, Bit 7: BX, Bit 8:
JOG, Bit 9: FX, Bit 10: RX
0x0011 Output Terminal
Status - R
Bit 0: Q1 (OC1), Bit 1: Q2
(OC2) Bit 2: Q3 (OC3), Bit
3: AUX Bit 4: 30AC
0x0012 V1 - R 0 – FFC0
0x0013 V2 - R 0 – FFC0
0x0014 I - R 0 – FFC0
0x0015 RPM - R
(Note 3)
The changed value in Common affects the current setting but returns to the previous setting when
power is cycled or Inverter is reset. However, changing value is immediately reflected in other parameter groups
even in the case of Reset or Power On/Off.
< DRV Group >
Addre
ss NO. Description Default Maximu
mMinimum Unit
5100 DRV#00 Cmd. freq 0 MaxFre
q0 0.01Hz
5101 DRV#01 Acc. Time 100 6000 0 0.1sec
5102 DRV#02 Dec. Time 200 6000 0 0.1sec
11
modbus-rtu iS5 manual.doc

Addre
ss NO. Description Default Maximu
mMinimum Unit
5103 DRV#03 Drive mode 1 2 0
5104 DRV#04 Freq. mode 0 4 0
5105 DRV#05 Step freq - 1 1000 MaxFre
qstartFreq 0.01Hz
5106 DRV#06 Step freq - 2 2000 MaxFre
qstartFreq 0.01Hz
5107 DRV#07 Step freq - 3 3000 MaxFre
q
startFreq 0.01Hz
5108 DRV#08 Current - - - 0.1A
5109 DRV#09 Speed - - - 1rpm
510A DRV#10 DC Link Voltage - - V
< FU1 Group >
Addre
ss NO. Description Default Maximu
mMinimum Unit
5203 FU1 #03 Run prohibit 0 2 0
5205 FU1 #05 Acc. pattern 0 4 0
5206 FU1 #06 Dec. pattern 0 4 0
5207 FU1 #07 Stop mode 0 2 0
5208 FU1 #08 DcBr freq. 500 6000 startFreq 0.01Hz
modbus-rtu iS5 manual.doc 12

Addre
ss NO. Description Default Maximu
mMinimum Unit
5209 FU1 #09 DcBlk time 10 6000 0 0.01sec
520A FU1 #10 DcBr value 50 200 0 %
520B FU1 #11 DcBr time 10 600 0 0.1sec
520C FU1 #12 DcSt value 50 200 0 %
520D FU1 #13 DcSt time 0 600 0 0.1sec
5214 FU1 #20 Max freq. 6000 40000 4000 0.01Hz
5215 FU1 #21 Base freq. 6000 maxFre
q3000 0.01Hz
5216 FU1 #22 Start freq. 50 6000 1 0.01Hz
5217 FU1 #23 Freq limit 0 1 0
5218 FU1 #24 F-limit Lo. 50 highFre
qstartFreq 0.01Hz
5219 FU1 #25 F-limit Hi. 6000 maxFre
qlowFreq 0.01Hz
521A FU1 #26 Torque boost 0 1 0
521B FU1 #27 Fwd boost 20 150 0 0.1%
521C FU1 #28 Rev boost 20 150 0 0.1%
521D FU1 #29 V/F pattern 0 2 0
521E FU1 #30 User freq. 1 1500 maxFre
q0 0.01Hz
13
modbus-rtu iS5 manual.doc

Addre
ss NO. Description Default Maximu
mMinimum Unit
521F FU1 #31 User volt. 1 25 100 0 %
5220 FU1 #32 User freq. 2 3000 maxFre
q0 0.01Hz
5221 FU1 #33 User volt. 2 50 100 0 %
5222 FU1 #34 User freq. 3 4500 maxFre
q0 0.01Hz
5223 FU1 #35 User volt. 3 75 100 0 %
5224 FU1 #36 User freq. 4 6000 maxFre
q0 0.01Hz
5225 FU1 #37 User volt. 4 100 100 0 %
5226 FU1 #38 Volt control 1000 1100 400 0.1%
5227 FU1 #39 Energy save 0 30 0 %
5232 FU1 #50 ETH select 0 1 0
5233 FU1 #51 ETH 1min 180 200 ETH Cont %
5234 FU1 #52 ETH Cont 100 150 50 %
5235 FU1 #53 Motor type 0 1 0
5236 FU1 #54 OL level 150 150 30 %
5237 FU1 #55 OL time 100 300 0 0.1sec
5238 FU1 #56 OLT select 1 1 0
modbus-rtu iS5 manual.doc 14

Addre
ss NO. Description Default Maximu
mMinimum Unit
5239 FU1 #57 OLT level 180 200 30 %
523A FU1 #58 OLT time 600 600 0 0.1sec
523B FU1 #59 Stall prev. 0 7 0
523C FU1 #60 Stall level 180 250 30 %
< FU2 Group >
Addre
ss NO. Description Default Maximu
m
Minimu
mUnit
5307 FU2 #07 Dwell freq 500 maxFre
q
StartFre
q0.01Hz
5308 FU1 #08 Dwell time 0 100 0 0.1sec
530A FU2 #10 Jump freq 0 1 0
530B FU2 #11 jump lo 1 1000 jump Hi
1
StartFre
q0.01Hz
530C FU2#12 jump Hi 1 1500 maxFre
q
jump Lo
10.01Hz
530D FU2 #13 jump lo 2 2000
jump Hi
2
StartFre
q0.01Hz
530E FU2 #14 jump Hi 2 2500 maxFre
q
jump Lo
20.01Hz
530F FU2 #15 jump lo 3 3000 jump Hi
3
startFre
q0.01Hz
15
modbus-rtu iS5 manual.doc

Addre
ss NO. Description Default Maximu
m
Minimu
mUnit
5310 FU2 #16 jump Hi 3 3500 maxFre
q
jump Lo
30.01Hz
5311 FU2 #17 Start Curve 40 100 1 %
5312 FU2 #18 End Curve 40 100 1 %
5313 FU2 #19 Trip select 0 3 0 BIT
5314 FU2 #20 Power-on run 0 1 0
5315 FU2 #21 RST restart 0 1 0
5316 FU2 #22 Speed Search 0 15 0 BIT
5317 FU2 #23 SS Sup-Curr 100 200 80
5318 FU2 #24 SS P-gain 100 9999 0
5319 FU2 #25 SS I-gain 1000 9999 0
531A FU2 #26 Retry number 0 10 0
531B FU2 #27 Retry delay 10 600 0 0.1sec
531E FU2#30 Motor select 0 9 0
531F FU2#31 Pole number 4 12 2
5320 FU2 #32 Rated-Slip (Note4) 1000 0 0.01Hz
5321 FU2 #33 Rated-Curr (Note4) 2000 10 0.1A
5322 FU2 #34 Noload-Curr (Note4) 2000 5 0.1A
5324 FU2 #36 Efficiency (Note4) 100 70 %
modbus-rtu iS5 manual.doc 16
Table of contents
Other LG Network Hardware manuals

LG
LG ETPFFRPP01 User manual
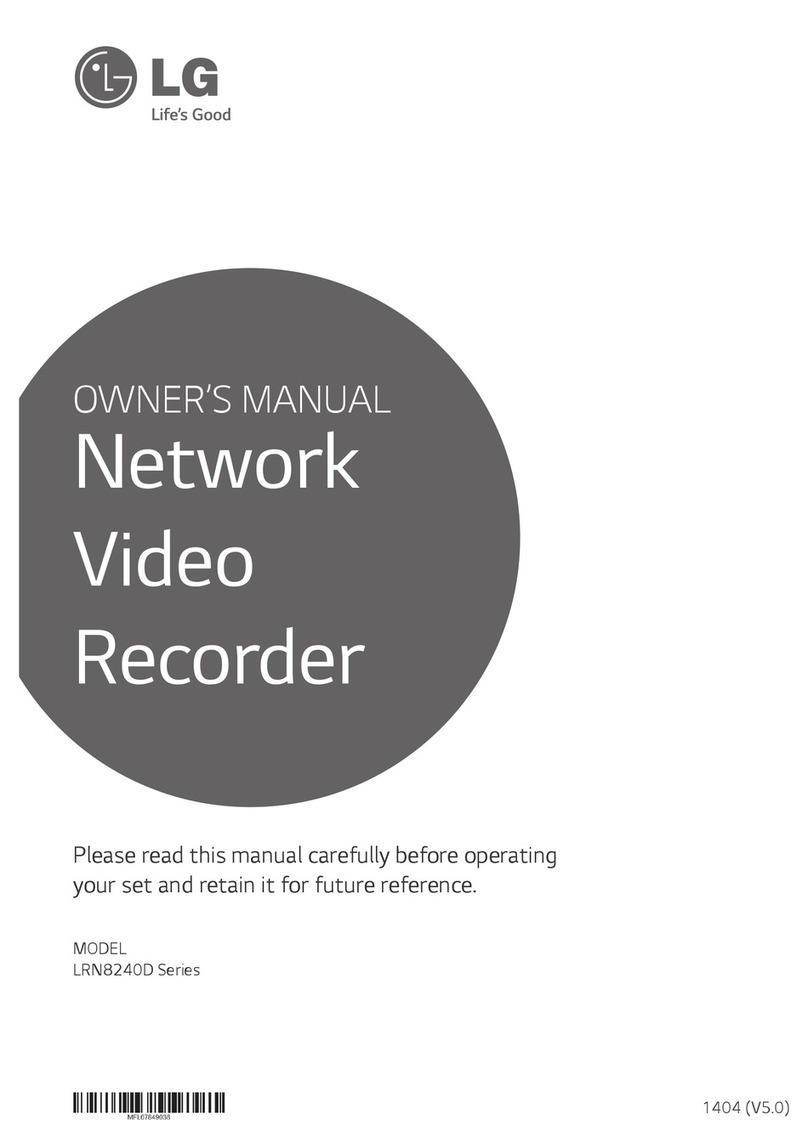
LG
LG LRN8240D Series User manual

LG
LG LRN3040N Series User manual
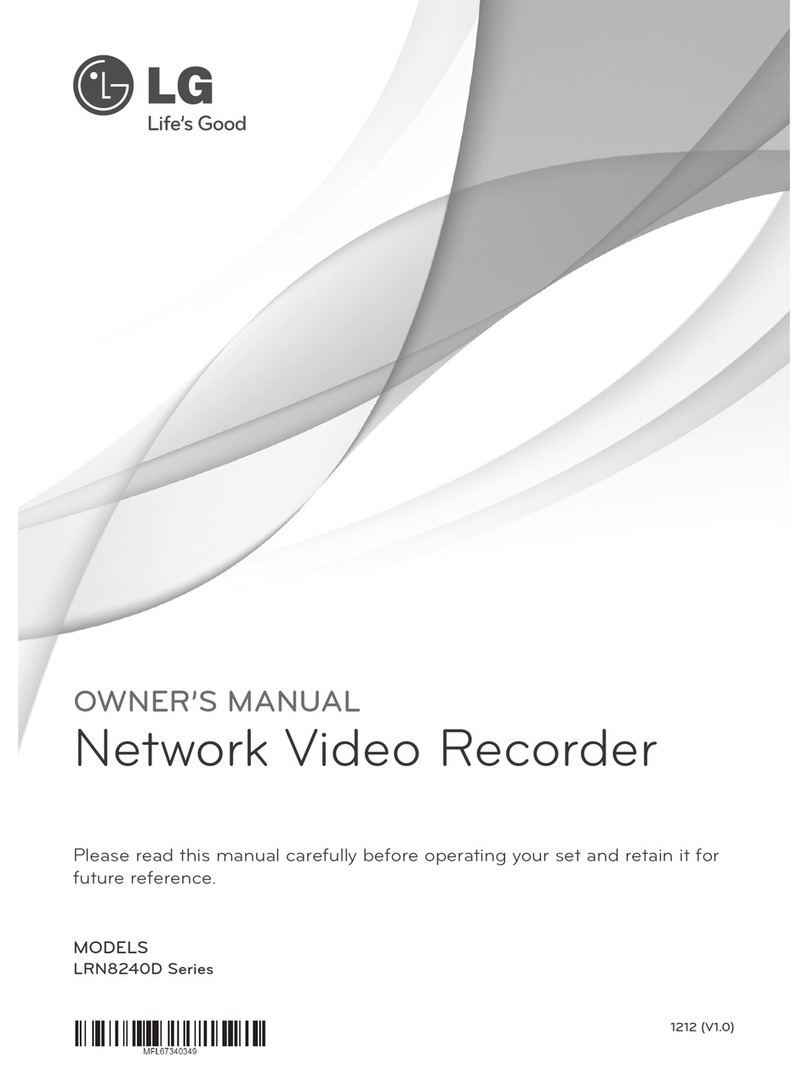
LG
LG LRN8240D Series User manual

LG
LG N2B1DD1 - NAS Server Parts list manual
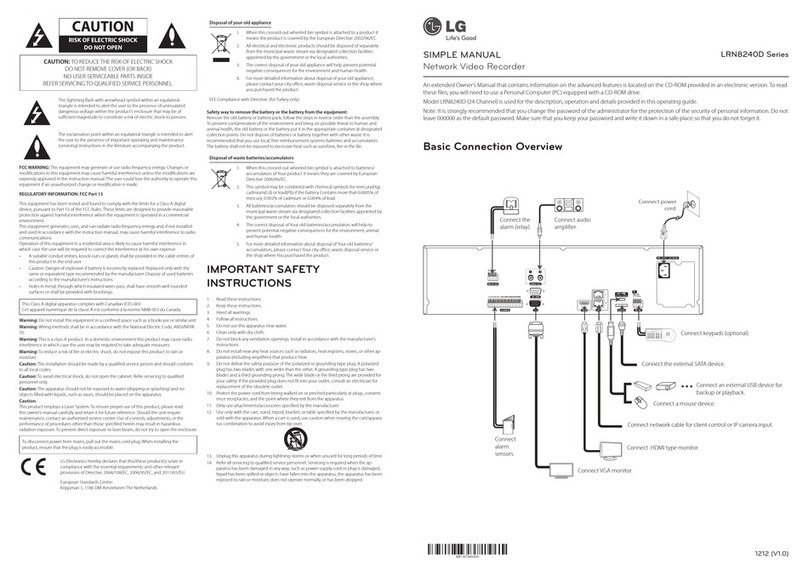
LG
LG LRN8240D Series Specification sheet
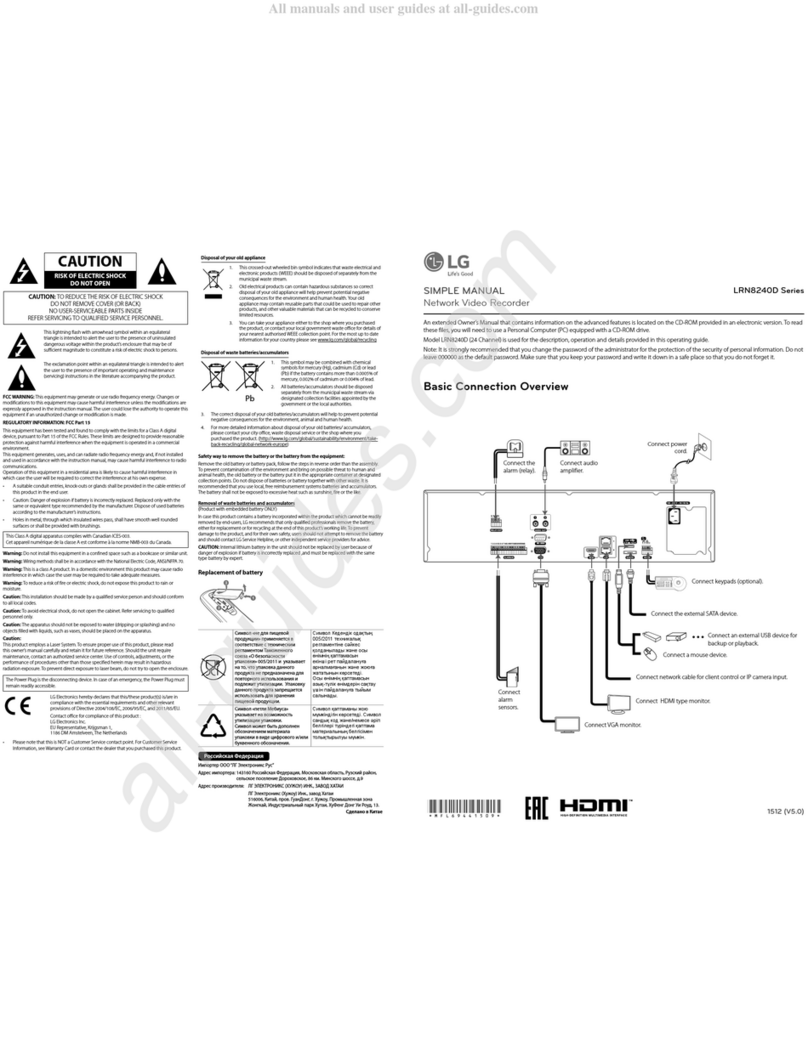
LG
LG LRN8240D Series Specification sheet

LG
LG N2A2DD2 Instruction Manual
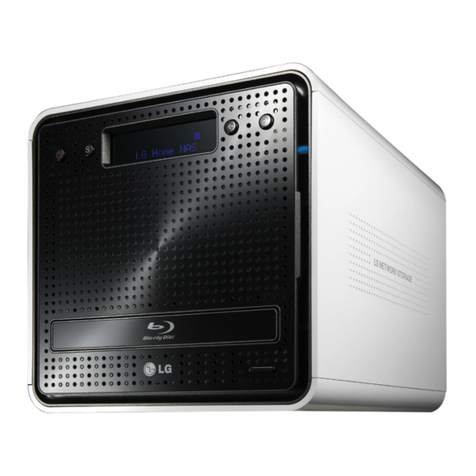
LG
LG N2R1D - NAS Server User manual

LG
LG N2A2DD2 User manual