Lincat OD7007 User guide

IS433 ECN3592
User, Installation, Servicing and Conversion
Instructions
Opus 700 Dual Fuel Oven Ranges
OD7006 and OD7007

IS433 ECN3592
2
Dear Customer,
Thank you for purchasing this Lincat product.
This is just one of over 450 different items of catering equipment available
which is constantly being extended and improved. Details are available from
your local distributor or direct from us.
Used for the purposes for which it is intended, and with careful maintenance
as outlined in this User Guide, your Lincat product will give you years of
trouble free service.
For use in GB & IE
IMPORTANT INFORMATION
Please read all of the safety and operating instructions carefully before using this
product. Please pay particular attention to all sections of this User Guide that carry
warning symbols and notices.
WARNING!
This is a Warning symbol. This symbol is used throughout the user guide
whenever there is a risk of personal injury. Ensure that these warnings are
read and understood at all times.
CAUTION!
This is a Caution symbol. This symbol is used throughout the user guide whenever
there is a risk damaging your Lincat product. Ensure that these warnings are read
and understood at all times.
NOTE:
This is a Note symbol. This symbol is used throughout the user guide to provide additional
information, hints and tips.

IS433 ECN3592
3
CONTENTS
Contents Page
Customer Information………………………………………………………. 2
Warnings and Precautions………………………………………………… 4
Technical Data……………………………………………………………….. 5
Commissioning………………………………………………………………. 6
Check List of Enclosures…………………………………………………... 6
Installation…………………………………………………….……………… 7
Conversion of Gas Types………………………………………………….. 8-9
User…………………………………………………………………………….. 10-11
Servicing ……………………………………………………………………… 12
Component Replacement ………………………………………….……… 12-14
Spare Parts List……………………………………………………………… 15
Fault Finding…………………………………………………………………. 16
Wiring Diagrams…………………………………………………………….. 17
Service information………………………………………………………….. 18
Guarantee………………………………………………………….………….. 18

IS433 ECN3592
4
WARNINGS AND PRECAUTIONS
It is mandatory that all appliances are installed, commissioned and serviced by a qualified and
competent person as defined by the regulations in force in the country of installation.
Failure to comply will invalidate the warranty.
WARNING!
This appliance must be installed by a competent installation engineer in accordance with
the installation instructions, and should conform to the following requirements:
Gas Safety (Installation & Use)(Amendment) Regulations
BS 5440: Flues, Air Supply for gas appliances of input not exceeding 70kW
Institution of Gas Engineers Publications:IGE/UP/1, IGE/UP/2 and IG/UP/4
BS 6173: Code of Practice for Installation of Gas Catering Appliances
Local and National Building Regulations
Fire Precautions Act
Health & Safety At Work etc Act
BS EN60335-1 Safety of Household and Similar Electrical Appliances
BS EN 60335-2-42 Particular Requirements for Commercial Electric Forced
Convection Ovens, Steam Cookers and Steam-Convection Ovens
Do not obstruct or block the appliance flue.
Installation must include sufficient ventilation to prevent the occurrence of
unacceptable concentrations of substances harmful to health in the room in which they
are installed.
It is recommended that this appliance is sited under an extraction canopy for the
removal of combustion products
After operation, some parts of the appliance will remain hot for a period of time. Please
take care to avoid accidental burns.
CAUTION!
All equipment must be earthed to prevent shock.
Do not connect directly to any flue, ducting or mechanical extraction system.
Installation should allow for a sufficient flow of fresh air for gas combustion.
Parts which have been protected by the manufacturer or his agent must not be adjusted
by the installer or user.
A means of disconnection must be incorporated in the fixed wiring having a contact
separation of at least 3.0mm in all poles.
Supply cords shall be oil-resistant, sheathed flexible cable not lighter than ordinary
polychloroprene or equivalent synthetic elastomer-sheathed cord (code designation 30245
IEC 57)
Connection of the electrical supply cable is made at the rear of the unit. Remove the
protective cover and fit a suitable cable into the strain relief and then to the inlet terminal
block. The unit is supplied for connection to a three-phase supply. Connections are
provided to allow termination of all three-phase cables, although only two are used to
power the unit. If the unit is to be fed from a single-phase then the two supply terminals
will need to be connected together using a wire link.

IS433 ECN3592
5
TECHNICAL DATA
Model
OD7006
OD7007
Dimensions
Overall Height (mm)
950
950
Width (mm)
600
900
Depth (mm)
750
750
Weight (kg)
85
113
Hob Cooking Surface w x d (mm)
600 x 600
900 x 600
Usable Oven Capacity w x d x h (mm)
500 x 540 x 400
715 x 540 x 400
Oven Shelf Size (mm) w x d
480 x 530
770 x 530
Heat Input
Total Heat Input Natural (Gross)
24.4 kW
36.6 kW
Total Heat Input Propane (Gross)
22.8 kW
34.2 kW
Hob Rating, per Burner Natural (Gross)
6.1 kW
Hob Rating, per Burner Propane (Gross)
5.7 kW
Hob Low Rating, per Burner Natural
1.4 kW
Hob Low Rating, per Burner Propane
1.2 kW
Connection and Operating Pressures
Gas Inlet Connection
1/2” BSP Female
3/4” BSP Female
Supply Pressure - Natural
20mbar
Operating Pressure - Natural
20mbar
Supply Pressure - Propane
37mbar
Operating Pressure - Propane
37mbar
Gas Consumption
Total Gas Rate –Natural
2.32 m3h-1
3.48 m3h-1
Total Gas Rate –Propane
1.64 kg h-1
2.46 kg h-1
Hob Burner Gas Rate - Natural
0.58 m3h-1
Hob Burner Gas Rate - Propane
0.41 kg h-1
Electrical
Total Power Rating @230V single phase
4.032 kW
6.06 kW
Total Power Rating @ 400V three phase
Phase
1
2.032
kW
Phase
1
2.064
kW
Phase
2
2.0 kW
Phase
2
2.0 kW
Phase
3
N/A
Phase
3
2.0 kW

IS433 ECN3592
6
NOTE
COMMISSIONING
PREPARATION
Remove all packaging and protective coatings prior to installation.
Check that the burner caps have been fitted correctly to the burner body and the Pan Supports are
located.
VENTILATION
The area in which this equipment is to be installed should have sufficient fixed ventilation to comply
with local legislation requirements. It is recommended that a room, or internal space, be provided
with a minimum free area of 4.5cm2per kW (3,400Btu/hr) of total heat input.
OD7007 OD7006
CHECK LIST OF ENCLOSURES
Please ensure the following items are included with this piece of equipment:
Model
OD7006
OD7007
Tick
Wire Shelf
3
3
Ignitor Wand
1
1
Pan Supports
2
3
Warranty Card
1
1
User Instructions
1
1
SERIAL NUMBER
Each appliance manufactured at Lincat has a unique identifying number found in the top
right hand corner of the data plate attached at the rear of the appliance. Please record that
number in the space provided should it be required for future reference.
Serial Number
MARK OF CONFIDENCE
Every singe product that leaves our factory bears a serial plate showing the assembler’s
initials. It’s a mark of confidence we have in our people and our manufacturing process.

IS433 ECN3592
7
INSTALLATION
SITING
The installer must ensure that all regulations are met and that there is an unobstructed minimum
distance of 1000mm from the top of the flue to the ceiling, which must be of non-combustible
material.
The appliance should be installed on a level surface ensuring the unit is stable and firmly located.
Any partitions, walls or kitchen furniture in close proximity must be of non-combustible materials
and not be closer than 50mm from the sides and rear of the flue.
GAS SUPPLY AND CONNECTION
The gas inlet connection is at the rear of the appliance. The pipe work should be of adequate size but
not smaller than the gas inlet connection at the rear of the appliance, i.e. Rp ½” BSP (OD7006) &
Rp ¾” BSP (OD7007).
All joints made must be leak free. The gas supply hose or tubing should be periodically inspected
and replaced as necessary.
Final gas connection to the appliance and gas supply shall comply with local regulations.
When making the connection to the appliance an isolating cock should be fitted into the supply line
close to the unit, for emergency shutdown or servicing purposes.
SUPPLY PRESSURES
The appliance is connected directly to the gas supply where the gas supply pressure is controlled at
the source of inlet in the building or via the governor attached to the bottle gases. See Technical Data
for the supply pressures.
To gain access to the gas pressure test nipple the fascia panel requires removal. The test
nipple is situated in the centre of the manifold rail.
Remove the blanking screw and attach a pressure gauge to the boss of the test nipple.
Light the oven burner and set thermostat to the highest setting and check the pressure.
ELECTRICAL SUPPLY AND CONNECTION
Connection of the electrical supply cable is made at the rear of the unit. Remove the protective cover
and fit a suitable cable into the strain relief and then to the inlet terminal block. The unit is supplied
for connection to a three-phase supply. Connections are provided to allow termination of all three-
phase cables, although only two are used to power the unit. If the unit is to be fed from a single-phase
then the two supply terminals will need to be connected together using a wire link
LOCKING OF WHEELS
When the appliance has been installed in its intended position the front castors should be locked by
depressing the locking tabs on the castors.
Locks should only be released for the intention of moving the appliance for cleaning
purposes and or routine servicing of the appliance.

IS433 ECN3592
8
CONVERSION OF GAS TYPES
Conversion of Gas Type –Injector Changes
Model
Gas
Inlet Pressure
Injector
Mark
Part No.
OD7006
G20
20 mbar
GG
1.90
190
JE254 x 4
C
N/A
76
JE216 x 4
OD7007
G20
20 mbar
GG
1.90
190
JE254 x 6
C
N/A
76
JE216 x 6
OD7006
G31
37 mbar
GG
1.20
120
JE255 x 4
C
N/A
50
JE217 x 4
OD7007
G31
37 mbar
GG
1.20
120
JE255 x 6
C
N/A
50
JE217 x 6
Fascia Panel Removal
AA
FF
BB
CC
DD EE C
GG
LL
MM
Remove the three pan supports AA, together with the control knobs CC.
Remove the fascia panel BB fixing screws EE from the underside of the panel.

IS433 ECN3592
9
B
A
C
D
FF
HH
GG
KK
Hob Valve Bypass Injectors
Remove the bypass injectors C from each of the hob burner control valves B.
Replace the bypass injectors applicable to the required gas type. Screw fully home but do not
over tighten.
Hob Burner Injectors
Remove pan supports.
Lift off the burner cap FF together with the burner base HH.
Remove injector GG and fit replacement applicable to the required gas type.
Replace burner base and cap.
Repeat the procedure for remaining hob burners.
Hob Burner Components
Part
Description
FF
Burner Cap
GG
Injector
HH
Burner Base
KK
Injector Holder
Completion of Conversion
Remove the redundant data plate and gas type identification label and attach new
replacements corresponding to new gas type.
Test all previously dismantled joints for soundness.
Functionally operate the appliance to the new operating pressure as detailed in page 7.
Hob Tap Components
Part
Description
A
Manifold
B
Gas tap
C
Bypass injector
D
Clamp screw

IS433 ECN3592
10
USER INSTRUCTION
APPLIANCE USE
This appliance is only for professional use and should only be used by qualified personnel.
Ensure that the person responsible understands how to light, safely operate, clean and shut down the
appliance and is made aware of the position and operation of the gas isolating cock in the event of an
emergency. All users should know how to clean burner caps and to correctly locate the burner cap on
the burner body.
LIGHTING SEQUENCE –HOB BURNER
Ensure that all the burner caps and pan supports are in the correct positions.
MAINS POWER ON
OVEN THERMOSTAT
CONTROL KNOB
OVEN ELEMENT
POWER ON
HOB INDICATOR ON / OFF INDICATOR
LH REAR BURNER
LH FRONT BURNER
MIDDLE REAR BURNER
MIDDLE FRONT BURNER
RH REAR BURNER
RH FRONT BURNER
PAN SUPPORTS
Open the main gas cock.
Push in the control knob then rotate anti-clockwise to any position to allow gas through to the
burner. Manually light this burner using a taper or piezo ignitor wand.
On establishing a flame at the burner, keep the knob depressed for approximately 15 seconds
then release. The burner should remain lit.
OVEN SETTING
Check the green ‘power on’ neon on the control panel is illuminated.
Set the control knob to the desired temperature in degrees Celsius. The orange light will
illuminate indicating that power is being supplied to the elements.
The orange light will go out when the oven has achieved the set temperature. Periodically the
orange light will illuminate to indicate that the oven temperature has fallen and the elements
are turned on to top up the temperature.
SHUT DOWN
To shut down the appliance rotate all control knobs clockwise to the OFF position. The gas supply
stopcock or bottle valve should now be closed.
After operation, some parts of the appliance will remain hot for a period of time; care
should be taken to avoid risk of burns.

IS433 ECN3592
11
CLEANING
Ensure the appliance is cool and the gas supply is isolated before commencing cleaning.
After use wash the unit down with a warm detergent solution.
Frequently check the burner cap ports for blockages. Clear as necessary.
Do not use abrasives on stainless steel or enamelled parts.
Do not use any products containing chlorine or hydrochloric acid to clean stainless steel
surfaces.
Do not clean the appliance using a water jet.
To remove shelf supports, lift shelf support up and out to disengage from retaining screws.
POTS AND PANS
The minimum recommended pan size should have a base diameter not less than 150mm.
The maximum recommended pan size per burner should not exceed a base diameter of 360mm.
Under no circumstances should multiple burners be covered by a single pan or
container.
OPENING OF THE OVEN DOOR
Care must be taken to avoid injury when opening the oven door, when the oven is in use as hot
air will rapidly escape.
Tilt shelf up at rear and pull to disengage

IS433 ECN3592
12
SERVICING
SERVICE ACCESS
To access and service the gas control valves
Remove the control knobs and fascia panel to gain access to the valves.
Remove the two screws securing the valve boss and carefully withdraw the spindle
from the valve.
Grease as necessary and refit parts. Carry out gas soundness check.
FASCIA PANEL REMOVAL
See page 8 for details
OPERATIONAL CHECK
Commissioning must include an operational check of all controls.
Check that each burner can be lit at both full rate and low rate.
Check that each burner will remain lit when turned to low rate.
Set the Oven thermostat at its lowest setting and check that on the oven attaining the set
temperature the amber light goes out.

IS433 ECN3592
13
COMPONENT REPLACEMENT
Access to Hob components can be more easily gained by removal of the the hob top (as shown
below) rather than removing the fascia.
HOB TOP
ACCESS PANEL
FASCIA
CONTROL KNOBHOOK HOB OVER
FASCIA BEFORE
FASTENING AT
REAR
HOB TOP
FIXING SCREWS
FASCIA FIXING
SCREWS
Hob Thermocouple
Remove the pan supports, burner caps, rear access panel and hob top as shown above.
Remove the thermocouple lock nut at the hob top.
Remove thermocouple nut from valve body B.
Withdraw the thermocouple.
Fit the new thermocouple and re-assemble in the reverse order.
Hob Valve
Remove the control knobs, pan supports, rear access panel and hob top as shown above.
Remove the nut from the gas output at the valve.
Remove the thermocouple nut from the valve.
Remove clamp screws D from the valve.
Free the valve from the manifold A.
Fit the new valve and re-assemble reverse order.
Perform gas soundness test of circuit prior to operation of appliance.
Hob Burner
Remove the pan supports, rear access panel and hob top as shown above.
Remove the burner cap FF and base HH.
Remove the burner body retaining screws.
Fit the new burner body and re-assemble parts.

IS433 ECN3592
14
Oven Fans
Ensure that the gas supply to this unit is turned off and the electrical supply is disconnected.
Remove the oven shelves.
Loosen the fan guard screws and lift off the keyhole slots.
Remove the hex head nut from the centre of the fan, this is a left-hand thread, and remove the
fan blade.
Working from the back of the unit, remove the rear cover panel.
Remove the electrical connections from the relevant motor.
Remove the three securing screws and extract the motor unit.
Refitting is the reversal of removal.
Check the unit for electrical safety.
Contactor
Ensure that the gas supply to this unit is turned off and the electrical supply is disconnected.
Working from the back of the unit, remove the rear cover.
Remove the electrical connections from the contactor.
Release the clip from the base of the contactor.
Refitting is the reversal of removal.
Check the unit for electrical safety.
Over Temperature Cut-Out Thermostat
Ensure that the gas supply to this unit is turned off and the electrical supply is disconnected.
Remove the thermostat bulb from the top of the oven.
Working from the back of the unit, remove the rear cover panel.
Remove the electrical connections from the thermostat housing.
Remove the front control panel.
Pull the thermostat bulb through the oven back.
Remove the two securing screws and remove the thermostat unit.
Refitting is the reversal of removal.
Check the unit for electrical safety.
Control Thermostat
Ensure that the gas supply to this unit is turned off and the electrical supply is disconnected.
Remove the thermostat bulb from the top of the oven.
Remove the control knobs from the front of the unit.
Remove the two screws holding the control thermostat to the control panel.
Remove the control panel as detailed previously.
Remove the electrical connections from the thermostat housing.
Remove the thermostat and capillary from the unit.
Refitting is the reversal of removal.
Check the unit for electrical safety.

IS433 ECN3592
15
Part Number
Part Description
Used On
BU55
Door Bushes
All models
BU224
Burner Base
All models
BU225
Burner Injector Holder
All models
BU226
Burner Cap
All models
CO113
Copper Washer
All models
CA143
125mm Braked Swivel Castors
All models
CA145
125mm Un-Braked Swivel Castors
All models
CO214
Contactor
All models
DO73
Door Catch Assembly
All models
EL149
Element –4kW
OD7006
EL248
Element –3kW
OD7007
FA12
LHS Fan/Motor Assembly
OD7007
FA102
RHS Fan/Motor Assembly
All models
HA77
Door Handle
All models
JE254
Hob Burner Injector –Natural
All models
JE255
Hob Burner Injector –Propane
All models
JE216
Hob Valve Low Rate Jet - Natural
All models
JE217
Hob Valve Low Rate Jet –Propane
All models
KN228
Control Knob –Oven Thermostat
All models
KN256
Control Knob –Hob Burners
All models
LE37
Adjustable Leg - 150mm
All models
NE39
Green Neon
All models
NE40
Amber Neon
All models
PA122
Cast Pan Supports
All models
SE25
Door Seal
All models
SH112
Oven Shelf
OD7006
SH81
Oven Shelf
OD7007
SP56
Leg Spanner
All models
SR07
Side Rack
All models
SW58
Fan Switch
All models
TC34
Thermocouple 750mm
All models
TH46
Thermostat
All models
TH63
Safety Cut-Out Thermostat
All models
VA65
Hob Burner Valve
All models
WA08
Fibre Washer
All models
SPARE PARTS LIST

IS433 ECN3592
16
Is there gas at the burner?Yes No
Are thermocouple connections loose?
Is the thermocouple voltage less than 15mV?
Is the valve damaged?
Check injector for blockages
Tighten connections
Replace valve
Yes
Yes
Yes
No
No
No
Replace thermocouple
Recheck system
Burner/s will not light or stay lit.
Oven not heating.
FAULT FINDING
Is green neon lit?
Yes No
Check incoming
supplyis connected
and switched
correctly
Are the fans operating
when the oven control
switch is turned on?
Yes No
Check the over
temperature cutout
re-set switch at the
rear of the appliance
Faultyswitch or
wiring fault.

IS433 ECN3592
17
OD7006 Wiring (E356)
L1
L2
L3
N
12
3
4
5
6
7
8
9
13
14 16
18
4
CA36
200
TP- P
3
CA36
2000
TP- #
2
CA09
280
- - #
1
CA09
280
- - #
8
CA36
2000
P - #
7
6
CA36
2000
TP-P
5
CA36
200
P-TP
12
CA09
700
P - F
11
CA09
700
P - F
10
CA09
360
P - #
9
CA09
360
P - #
16
CA35
200
TP-TP
15
CA35
2000
P- #
14
CA10
280
- - P
13
CA36
2000
P - P
20
19
CA35
2000
P -P
18
N/A
N/A
N/A
17
CA35
200
TP- P
23
22
CA35
300
- - #
CA10
120
F- F
21
CA10
400
P-F
25 27
CA13
300
TP-SR
26
TE14
CO214
SW58
TH46
NE39
GREEN
NE40
AMBER
TH63
EL149
FA12
TO CHASSIS
23
28
CA13
SR-SR
E356
WIRING DIAGRAMFOR
OD7006/N/P/FL
300
I. Marshall
25/03/10
3394
25/03/10
CONTROL PANEL COMPONENTS
21
B
B
B
B
B
B
BB
B
B
B
B
B
B
B
USE OUTER PAIRS OF
TERMINALS ONLY NO
CONNECTIONS TO INNER
PAIR OF CONTACTS
B
24
CA13
TP-SR
200
NO
WIRES WITH A # TO BE STRIPPED 10mm
NOT STD 6mm
NO
L1 L3
L1 L2
T1 T2 T3
20
10
11
15
22
A1
NO
A2
19 24
12
OD7007 Wiring (E329)
L1 L2 L3
TE55
EARTH TAG
TE47
TERMINAL BLOCK
TH63
SAFETY THERMOSTAT
CO214
CONTACTOR
NE39
GREEN
NEON
NE40
AMBER
NEON
SW58
FAN
SWITCH
TH46
OVEN
THERMOSTAT
EL248
ELEMENT EL248
ELEMENT
FA12 FAN FA12 FAN
29
28
26
27
B B
1 2 3 134 5 6 714
89 10 11 12 16 17 18 19 20 21 22 23 24 25 26 27 28 29 OE7008 - A006
OD7007 - A006
OVEN WIRING
E329
CA09 CA09 CA09 CA36
CA09 CA09 CA09 CA09 CA36
CA09 CA09 CA09 CA09 CA09 CA36 CA36 CA36 CA36 CA10 CA10 CA35
400
P- #
400
P- #
400
P- #
1850
P- #
150
P- #
150
P-#
150
P- #
400
P- P
1850
P- #
400
P- P
400
P- P
550
P-P
550
P-P
550
P-P
700
P-P
1400
P-P
1850
P-#
1300
P-P P-P
600
P-P
600
P-P
120
332406.09
30
CA35
120
P-P
Connect to
inner
bulkhead
via
heat
deflector
screw
123
4
5
6
789
10
11
12
13
14
15
15
CA36
1850
P- P
16
17
18
19
N
CA35 CA35 CA35
P-#
400
P-#
1750
P-P
150
CA35
150
P-P
20
21
22
23
24 25
CA35
P-P
120
CA35
120
P-P
30
31
CA35
1750
P-P
32
WIRES WITH A # TO BE STRIPPED 10MM
NOT STD 6MM
Connect
to fascia

IS433 ECN3592
18
Gas catering equipment should be routinely serviced to ensure a long trouble free life. It is
recommended that this appliance is serviced every 6 months by a competent gas engineer.
For help regarding the installation, maintenance and use of your LINCAT equipment, please call:-
LINCAT SERVICE HELP DESK
+44 (0) 1522 875520
AUTHORISED SERVICE AGENTS
All service work, other than routine cleaning, to be carried out by our authorised agent.
We cannot accept responsibility for work carried out by other persons.
Please quote both the model and serial numbers from the data plate attached to the unit. Give brief
details of the service requirement.
If possible please quote the product code of the part number you require.
Work carried out under warranty will normally be undertaken only during normal working hours, i.e.
Monday to Friday, 8.30 a.m. - 5.00 p.m.
CONDITIONS OF GUARANTEE
The guarantee does not cover:-
1) Accidental breakage or damage
2) Operational misuse, wear and tear from normal usage, incorrect adjustment, or neglect.
3) Incorrect installation, maintenance, modification or unauthorised service work.
SERVICE INFORMATION
This manual suits for next models
2
Table of contents
Other Lincat Range manuals

Lincat
Lincat Opus 800 Series User manual
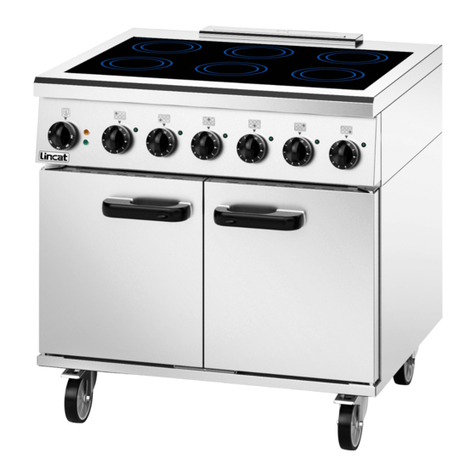
Lincat
Lincat Phoenix PHER01 Manual
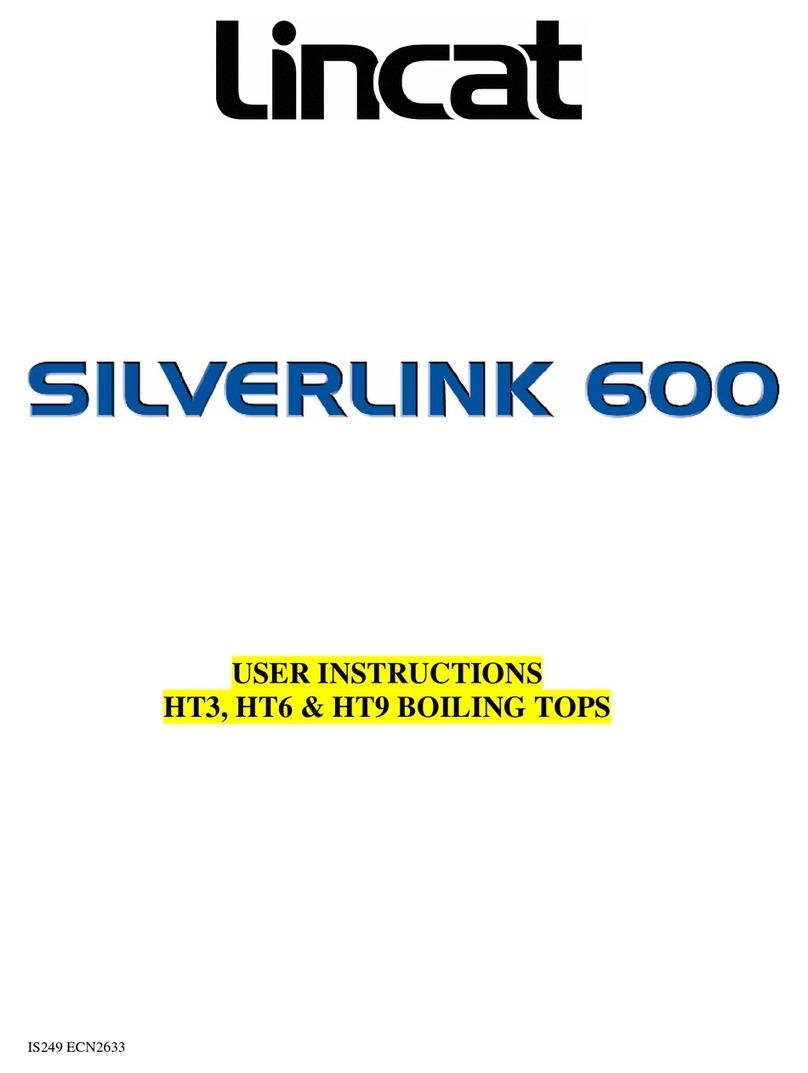
Lincat
Lincat Silverlink 600 HT3 User manual

Lincat
Lincat Phoenix PHER01-A002 Manual
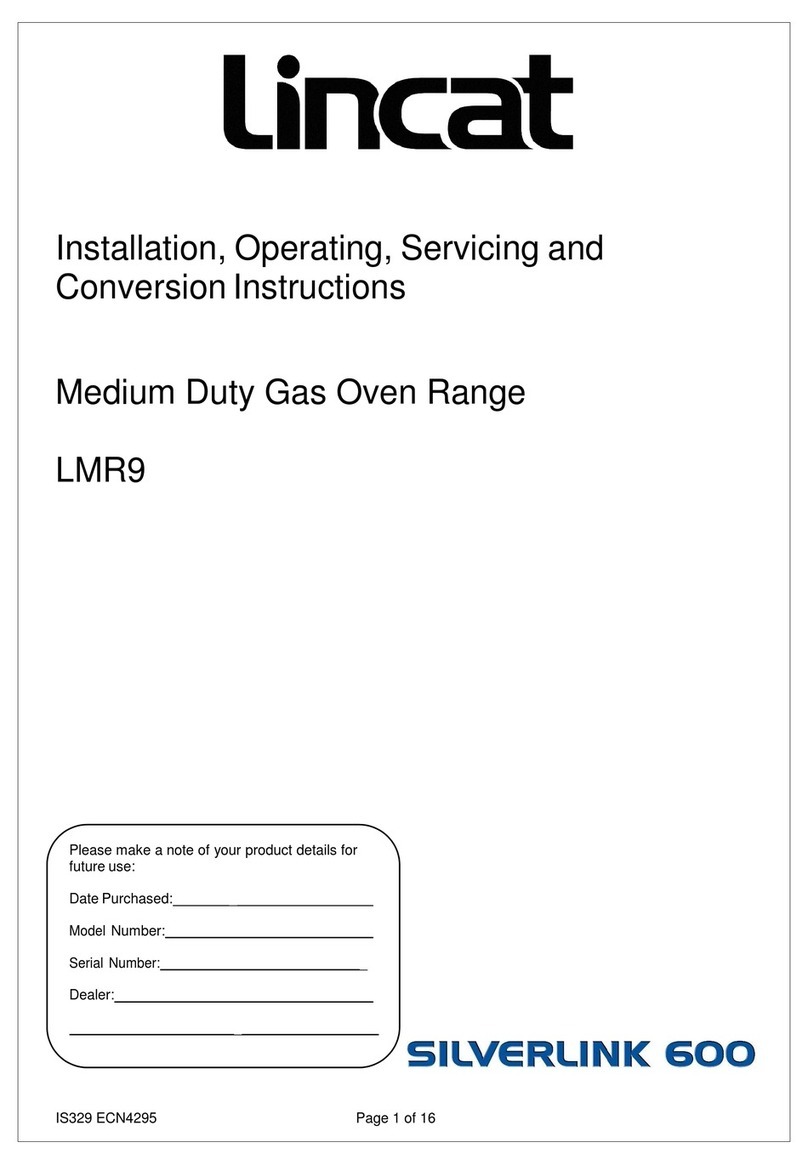
Lincat
Lincat Silverlink 600 User manual
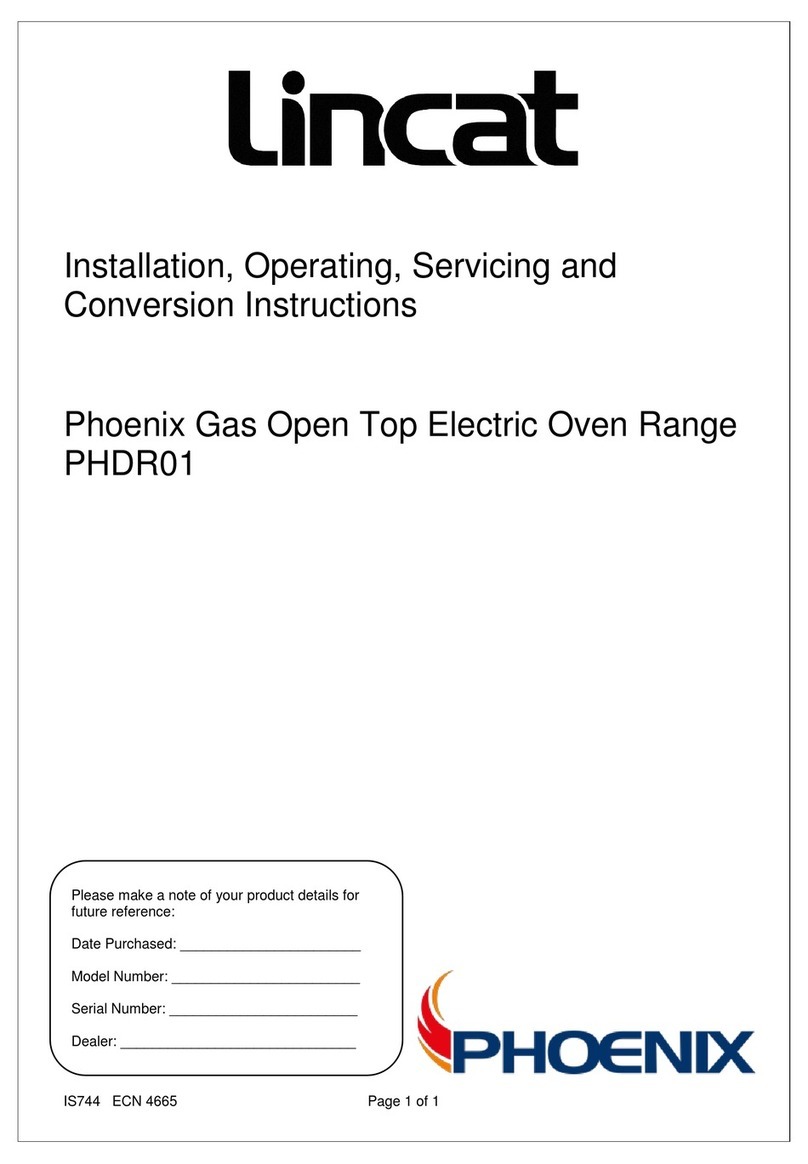
Lincat
Lincat Phoenix Series User manual

Lincat
Lincat OG7001 User guide

Lincat
Lincat Opus 800 Series Owner's manual

Lincat
Lincat SILVGRLINK 600 User guide

Lincat
Lincat Opus 700 OE7008 Manual