LS Starvert-iG5A Operating manual

STARVERT - iG5A
MAINTENANCE GUIDE
- This guide contains safety information and basic troubleshooting and
maintenance guidance. For more detailed information, refer to the user manual
included with the product or contact your supplier.
- For your safety, carefully read the Maintenance Guide before you install and
use the product.
Safety information
▶Read and follow all safety instructions in this guide to understand the safe operating
conditions for the equipment and to avoid property damage and personal injury.
▶For your safety, Warning and Caution information is provided below.
Warning
Caution
Indicates an imminently hazardous situation which, if not
avoided, may result in severe injury or death.
Indicates a potentially hazardous situation which, if not
avoided, may result in injury or damage to property.
Do not open the inverter covers while it is energized or operating.
Doing so may cause the inverter to malfunction or result in electric shock.
Do not allow objects, such as metal filings or other debris inside the inverter.
Doing so may cause the inverter to malfunction or result in a fire.
Warning
Ensure that cables are correctly specified for the inverter’s rated voltage, cable entry,
and terminal arrangement. Ensure that all wiring connections are installed correctly.
Incorrect cable specifications and connections may cause the inverter to malfunction or result
in a fire.
Apply the correctly rated torque when tightening terminal screws.
Loose screws or over tightened screws may result in an electric shock or a fire.
Do not install the inverter near flammable objects.
Doing so may cause a fire.
Ensure that the inverter location or installation method is not affected by vibration.
Vibration may affect the inverter’s operation and result in an electric shock or fire.
Ensure that the inverter is not serviced or repaired by unauthorized persons.
Unauthorized work may result in an electric shock or a fire and void the warranty.
Ensure the inverter load does not exceed the product’s rated load and that the inverter is
installed in accordance with the environmental conditions specified in the User’s
Manual.
Exceeding the rated load or incorrectly installing the inverter may cause the inverter to
malfunction, overheat, or result in an electric shock or a fire.
Caution
- 1 - - 2 -

Selecting inverter capacity
Selecting the correct inverter capacity
1) Check that the required output for the load is within the inverter’s rated
output [KVA].
2) Check that the motor rating is within the inverter’s rated output [KVA].
3) Check that the current for the actual load is within the inverter’s rated
current [A].
When operating multiple motors with one inverter
1) Ensure the inverter ’s rated output is greater that or equal to the
combined rating of the motors.
2) Electronic Over-Current Relay (EOCR) protection is recommended.
(Note: Over-current protection for all motors supplied by the inverter
cannot
be provided. )
3) Not recommended for motors with large differences in ratings.
5cm 5cm
5cm
Area for measuring temperature
Safety information - Inverter installation
Installation conditions
1) The inverter must not vibrate and be installed on a wall that can
support the inverter's weight.
2) Since the inverter may overheat during operation, it must be installed
on a fire-resistant or flame-retardant surface and have adequate
clearance around it.
3) The ambient temperature of the inverter’s operational environment
must be within -10 –50℃.
Clearances around the inverter
A
A
B B A : >10cm
B : >5cm
Safety information –Inverter wiring
Things to check before wiring
1) Ensure the inverter is turned off before wiring.
2) After the inverter is turned off, ensure that the inverter’s charging
circuit is fully discharged. (Wait at least 10 minutes after the inverter is
turned off.)
Safety information for wiring
1) Do not allow objects, such as metal filings or cable off-cuts inside the
inverter. Doing so may damage the inverter or cause inverter
malfunction.
2) Apply the correctly rated torque when tightening screws. If screws are
loose or over tightened, the inverter may malfunction or cause a short
circuit.
3) If the forward command (Fx) is on, the motor should rotate
counterclockwise when viewed from the load side of the motor. If the
motor rotates in the reverse direction, switch the position of the U and
V connections at the inverter.
※Ensure the total cable length does not exceed 200 m.
※Use Shielded Twisted Pair (STP) cables for signal circuits used
with remotely located motors that are connected to the inverter. Do
not use 3 core cables.
※When using long cable lengths, decrease the carrier frequency and
install a micro surge filter or sine wave filter.
Distance between inverter and motor
<
50 m
<
100 m
>
100 m
Allowed carrier frequency
<
15 kHz
<
5 kHz
<
2.5 kHz
- 3 -
- 4 -
If an inverter’s capacity is incorrect it may cause trip faults and also cause the
inverter and connected motors to malfunction.
Caution
- 4 -
Ensure the input terminals (R,S,T) and output terminals (U,V,W)are connected
correctly.
Transposing the input and output connections may damage the inverter.
Do not short-circuit the B1 and B2 terminals. This may damage the inverter.
Warning
When installing phase advance condensers, surge killer, or electronic noise
filters on the output side of the inverter, the inverter protection function may
perform or the surge killer may be damaged.
Caution

Peripherals and optional device configuration
Cautions for peripherals and optional device configuration
※Ensure optional devices are correctly connected to the inverter and
correctly configured for the system. Incorrect connections and
configurations may affect the product’s lifespan and reliability and
cause serious damage to the product.
Ideal operating conditions
-10 ℃~ 50 ℃(ice free conditions)
< 90 % rH (condensation free conditions)
No exposure to corrosives, flammable gases, oil
residue, or dust.
< 1,000 m above sea level
< 0.6 G, 5.9 m/s2
Ambient temperature
Ambient humidity
Environmental factors
Altitude
Vibration
DescriptionItem
Inverter operating conditions
- 5 - - 6 -
MCCB
MC
AC Input
Reactor
EMC Filter
DC Output Reactor
(Use for the inverter with 11 kW and higher)
Braking Resistor
Micro Surge Filter
Motor
RS-485 (PLC)
RS-485 (PC)
P1(+) B1
R S
+ T
U
V
W
S+
S-
SG
AC Power Supply
B1 B2
Name Description
AC Power
(
Power source
)
-
Connect the inverter to the specified input power
supply. (Phase to phase voltage: within 15 %
below - 10 % over, nominal supply voltage.)
MCCB
(Circuit
breaker
/Current
leakage
breaker)
-
Protects the power system from a short-circuit
faults.
-
High levels of in-rush current occur when the
power is on, so select correctly rated MCCBs.
(Contact the manufacturer for further information.)
M/C
(Magnetic
contactor)
-
Avoid starting and stopping the inverter
unnecessarily. It may impact the lifespan and
reliability of the product and cause switching noise
.
-
Select correctly rated M/Cs.
(Contact the manufacturer for further information.)
Reactor
(AC and DC
reactors)
-
Protects the inverter when a high load is
connected, suppresses high frequency and
improves power factor.
-
Use a maximum cable length of 10 m.
-
Select correctly rated reactors.
(Contact the manufacturer for further information.)
-
Use an inverter rated at 11 kW or higher.
EMC Filter
-
Reduces electro-magnetic interference.
-
Use a maximum cable length of 10 m.
-
Select correctly rated filters.
(Contact the manufacturer for further information.)
Braking
Resistor
-
Used when the inverter requires electrical braking
for vertical loads, or to shorten the deceleration
time. It absorbs the regenerative energy at braking
by turning it into heat.
-
Ensure that B1 and B2 are not short-circuited
when wiring.
-
The rated capacity must be based on the amount
of regenerated energy.
-
Select correctly rated resistors.
(Contact the manufacturer for further information.)
Micro Surge
Filter
-
Reduces noise occurring at the input and output
sides of cables and components that can affect
inverter operation.
-
Use a maximum cable length of 10 m.
-
Select correctly rated filters.
(Contact the manufacturer for further information.)

Over current2
(Arm short)
IGBT phase to phase fault.
There is a short circuit in
the wiring on the output
side.
Motor oput cables are too
long.
Surge voltages occur at
the output terminals.
Check for a phase to
phase short circuit at the
the IGBT.
Check the output cables.
Use the correct length for
motor cables.
Reduce the carrier
frequency.
Resolve the surging
voltage condition.
Display Cause Remedy
Over
current
Deceleration time is too
short.
The inverter output current
exceeds the rated
capacity.
The motor’s mechanical
brake is operating
improperly.
Over current occurs when
the inverter power is
turned on.
The actual current value is
different from the value
displayed.
Set the Acc/Dec time.
Decrease the load or
replace the inverter with a
higher-rated model.
Check the mechanical
brake.
Adjust the torque boost.
Contact the supplier.
Type Trip
Name
Function
Description
Current
OCT
Over
Current
Inverter output current exceeds 200 % of the
rated current.
OC2
Over
current
Inverter detects a IGBT Arm short circuit or an
output short circuit.
OLT
Over
load
The current value exceeds the motor’s rated
current. (Default value = 180 % of the motor’s
rated current)
GFT
Ground
trip
The sum of 3 phases current(Normal 0V) is
higher than the level which is set and flowing
through inverter output for the setting time.
IOLT
Inverter
over
load
The inverter is operating at 150 % of the rated
current for more than 60 sec or at 200 % of
the rated current for 10 sec (this feature has
inverse time characteristics).
ETH
Electronic
thermal
Stops the inverter operation to protect the
motor when a current exceeding the motor
rated current is supplied for a specific period
of time (Default value = 150 % of the motor’s
rated current detected for 60 sec. This feature
has inverse time characteristics).
The inverter output current exceeds the
motor’s rated current
Voltage
OVT
Over
voltage
The internal DC circuit voltage exceeds the
specified value.
200 V: 400 Vdc
400 V: 820 Vdc
LVT
Low
voltage
The internal DC circuit voltage is less than the
specified value.
200 V: 180 Vdc (Reset level: 230 Vdc)
400 V: 360 Vdc (Reset level: 460 Vdc)
-
Braking
operation
IGBT braking is turned on as DC voltage has
combined with regenerated voltage and
exceeds the specified voltage.
Turn On: 200 Vdc-390 Vdc , 400 Vdc-780 Vdc
Turn Off: 200 Vdc-380 Vdc , 400 Vdc-760 Vdc
Protective functions Fault trip troubleshooting
Over heat
Fan trip
Cooling system fault.
Cooling fan fault.
The ambient temperature
around the panel is too
high.
The carrier frequency is
too high.
Check that foreign objects
are obstructing the vent.
Replace the cooling fan.
Reduce the ambient
temperature to below 50
℃.
Reduce the carrier
frequency.
Note Cooling fan faults can be inspected by sound and
the exterior condition. If the fan is malfunctioning,
it may damage the inverter.
Ground trip
A ground fault has
occurred in the output side
of the inverter.
Phase to phase difference
of output voltage has
occurred.
The motor’s insulation is
damaged.
Check the output cables.
Check the voltages
between the phases are
balanced.
Check the motor’s
insulation resistance.
- 8 -- 7 -

Input phase
open
The magnetic contactor on
the input side has a
connection fault.
The input side wiring has
one or more phases in an
open circuit condition.
The capacitor inside the
inverter is broken due to
long-term use.
Check the magnetic
contactor.
Check the input cables.
Replace the capacitor.
Note The input phase open trip mode can be set by
adjusting the parameter.
Output
phase open
The magnetic contactor on
the output side has a
connection fault.
Output side wiring is faulty
,or the 3-phase inverter
output has one or more
phases in an open circuit
condition.
IGBT is faulty.
Check the magnetic
contactor.
Check the output cables.
Contact the supplier.
Note The output phase open trip mode can be set by adj
usting the parameter.
Keypad
display Cause Remedy
Over
voltage
Deceleration time is too
short for load inertia
(GD2).
Regenerative load is at the
inverter output.
Input voltage is too high.
Increase the acceleration
time.
Use the braking unit.
Ensure the input voltage is
at the specified value.
Low voltage
Input voltage too low.
A load greater than the
power capacity is
connected to the inverter.
(e.g., a welder, direct
motor connection, etc.).
The magnetic contactor on
the input side has a
connection fault.
Ensure the input voltage is
at the specified value
Increase the power
capacity.
Replace the magnetic
contactor.
Parameter saving fault. Reconnect the loader
cables.
If the fault occurs
continuously, contact the
supplier.
Loader fault.
Communication error
between the loader and
inverter.
Contact the supplier.Hardware fault.
Insulated Gate Bipolar
Transistor (IGBT)
temperature sensor fault.
Fault trip troubleshooting Fault trip troubleshooting
- 9 - - 10 -
Keypad
display Cause Remedy
Inverter
over load
Over load
trip
The load is higher than the
inverter rating. Ensure the motor and the i
nverter are correctly rated.
Note The difference between OLT and IOLT is the
reference current (OLT-motor's rated current,
IOLT-inverter's rated current).

Type Cause Remedy
The
inverter is
not
responding
when power
is supplied
There is an input power
fault.
The inverter does not have
short circuit connectors at
P and B1 (11- 22 kW
models).
Loader fault and a loader
and inverter contact fault.
Switched-mode power
supply (SMPS) fault.
Ensure the input voltage is
correct. Check the
circuit breaker and
magnetic contactor (before
the input terminal).
Install short circuit
connectors.
Replace the loader.
Contact the supplier.
The motor
does not
rotate
Current is not supplied at
the inverter output(U, V,
W).
Motor cable fault or
peripheral device
connection fault.
Check the operation and
frequency commands.
If the inverter is not
operating, even if the Run
Lamp is on and the
frequency command is
correct, contact the
supplier.
Check the wiring and
peripheral devices.
The motor
does not
accelerate
or
decelerate
Operation and frequency
command values are
incorrect.
The load is too high and
an over-current control
condition exists.
The maximum frequency
or frequency limit is set.
Check the operation and
frequency commands.
Reduce the load or
increase the inverter
rating.
Adjust the parameter.
Type Cause Remedy
The motor
vibrates
severely, does
not rotate
normally, and
stalls.
There are large load
fluctuations.
The input voltage is
not stable.
The torque boost
value is too high.
Adjust the load to
the rated
value.
Ensure the input voltage is
correct
Adjust the torque boost
value.
The motor
is
overheating.
The motor has been
operating
continuously at low
speed.
The base frequency is
set incorrectly.
Adjust the operation speed
setting or install an extra
cooling system for the
motor.
Ensure the motor rating is
correct and set the base
frequency correctly.
The inverter
is
overheating
The charging resistor is
damaged. Check the input and output
cables, braking resistor,
and connections (ground
etc.).
Troubleshooting other faults Troubleshooting other faults
Name Replacement indications Recommended
replacement cycle
Cooling fan Check for fan noise and cooling
efficiency. 3 years
DC link
capacitor The top of the capacitor swells. 4 years
Relay
Check the relay operation sound
when power is supplied to the
inverter. LV trips occur when the
motor runs.
After inspection
Consumable parts
Maintenance
- 11 - - 12 -

The replacement cycle for parts varies depending on the operating
environment, including ambient temperature and ventilation efficiency.
It also depends on the use rate, load, and time operating under load.
Conditions that reduce the lifespan and affect reliability of the product
and its components are as follows:
1) The inverter is located in a space that is exposed to high and significant
changes in temperature and humidity.
2) The motors run and stop frequently.
3) The inverter is exposed to significant changes in power supply and load,
including changes in voltage, frequency, and waveform distortion.
4) The inverter is exposed to regular vibration.
5) The inverter is exposed to corrosive or flammable substances, oil residue, or
dust.
6) The inverter has been in storage for a long time or has been stored
incorrectly.
7) The power capacity exceeds the inverter rating. (10 times greater)
Head Office LS Tower (South Korea)
•TAURUS (OR)
Tel : 1-503-692-9004
•E-MEC (NJ)
Tel : 1-201-816-1124
•K+S Service (MI)
Tel : 1-734-374-0400
Email : esyto@k-and-s.com
U.S.A
•HIGH-END (SP)
Tel : 55-19-9788-4426
BRAZIL
•VMC (Barcelona)
Tel : 34-935-747-017
SPAIN
•HEIGL (Rosbach)
Tel : 49-6003-3457
Email : t.heigl@heigl-antriebe.de
GERMANY
•PNEUMO (Saint-Petersburg)
Tel : 49-6003-3457
RUSSIA
•ANT (Istanbul)
Tel : 90-216-499-9111
TURKEY
•CECO (Calcutta)
Tel : 91-33-2248-5448
Email : akbasu@cecoelectronics.in
INDIA
•ICA (Hanoi)
Tel : 84-4-568-0582
•HAN MY VIET (HCM City)
Tel : 84-8-3821-6710
Email : sasbo@hcm.vnn.vn
VIETNAM
•PT SARANA (Jakarta)
Tel : 62-21-612-7535
INDONESIA
(Address) LS Tower, 127, LS-ro, Dongan-gu, Anyang-si, Gyeonggi-Do, 431-848
(Tel) INV : PLC/HMI :
Maintenance Service network
Part Description
Main capacitor
Increased motor noise.
Fault trips occur (OCT, OC2,GFT etc.,).
Inverter malfunction due to SMPS damage and long
term use of SMPS.
Cooling fan
Decreased fan speed and increased fan noise.
Fan over current condition occurs due to fan
malfunctions.
Reduced fan efficiency and fan speed cause an
OHT trip and result in deterioration of internal parts
due to the high temperature conditions inside the
inverter.
Over current at the fan causes SMPS damage.
- 13 - - 14 -
Indications for part replacement after long term use)
Table of contents
Other LS Inverter manuals
Popular Inverter manuals by other brands
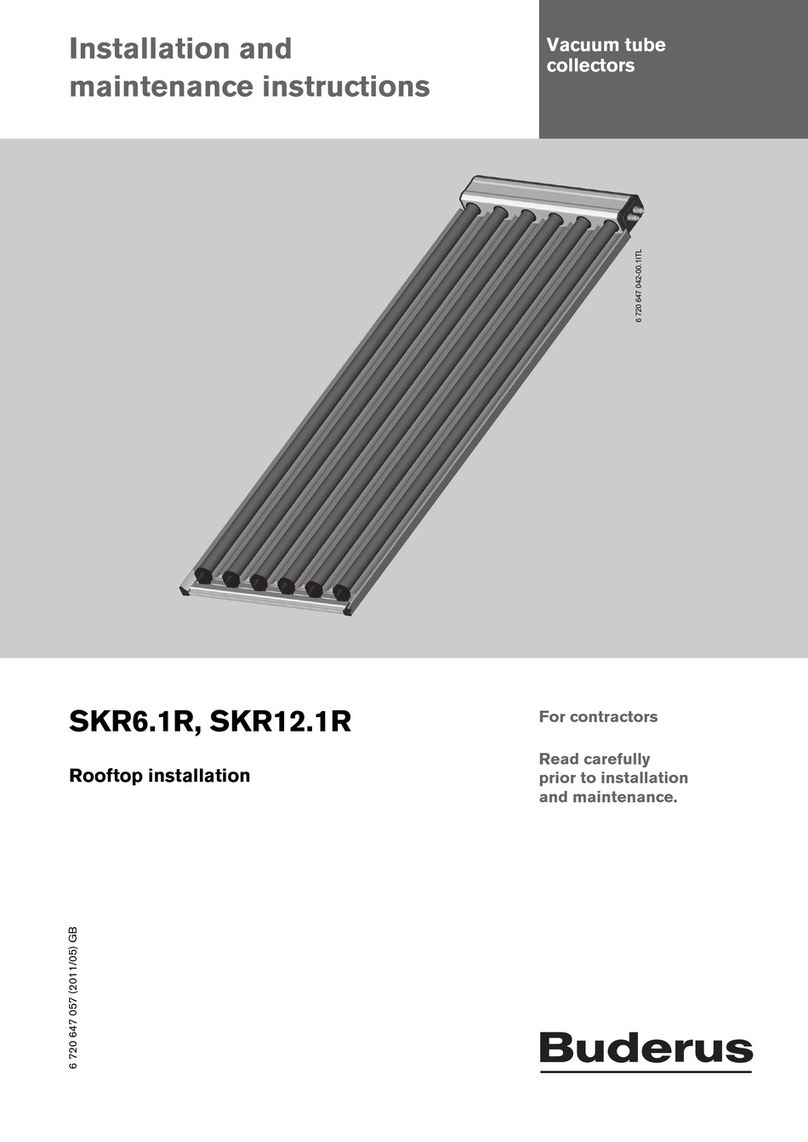
Buderus
Buderus SKR6.1R Installation and maintenance instructions
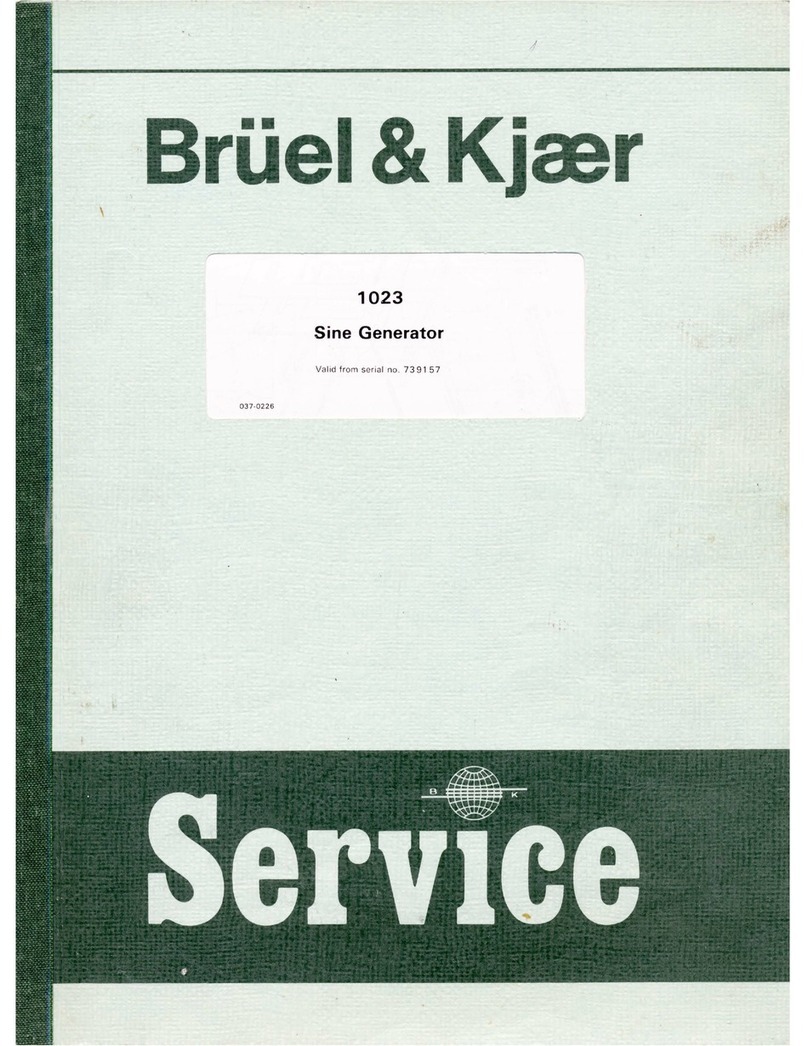
BRUEL & KJAER
BRUEL & KJAER 1023 Service manual

B.A. International
B.A. International SuPreme S5 operating instructions
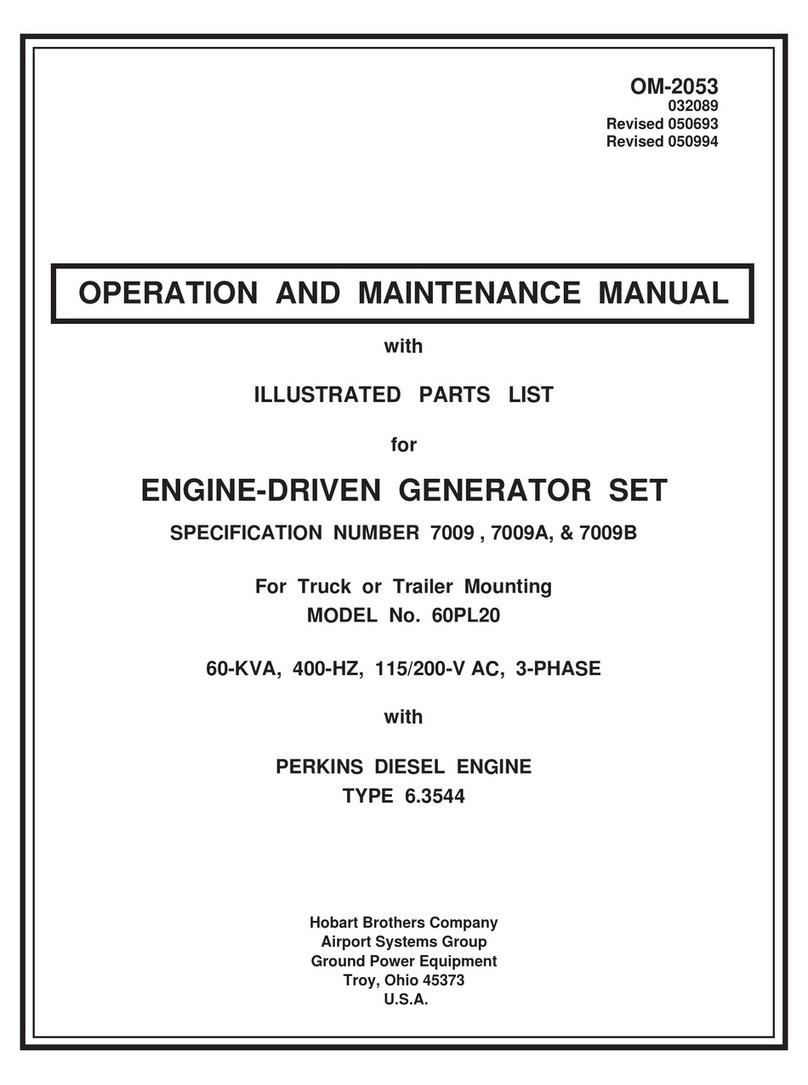
Hobart
Hobart 60PL20 Operation and maintenance manual
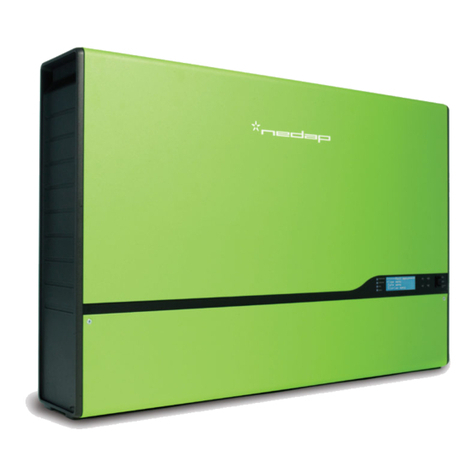
Nedap
Nedap PowerRouter installation manual

Goodwe
Goodwe EM Series user manual