Lutz Jesco C 2700-V User manual

Dosing
Conveying
Control
Liquids
Gases
Systems
Original Operating Instructions
© Lutz-Jesco GmbH 2016
BA-21210-02-V05
Vacuum Regulator for Chlorine Gas
C 2700-V
Operating Instructions
Read the Operating Instructions!
The user is responsible for installation and operation related mistakes!


3
© Lutz-Jesco GmbH 2016
Subject to technical changes.
160426
Vacuum Regulator for Chlorine Gas C 2700-V Operating Instructions
BA-21210-02-V05
Contents
1 Notes for the Reader ........................................................ 4
General non-discrimination .......................................................... 4
Explanation of the signal words .................................................... 4
Explanation of the warning signs .................................................. 4
Identification of warnings ............................................................. 4
Instruction for action identification ................................................ 4
2 Safety ............................................................................... 5
General warnings ......................................................................... 5
Information about chlorine............................................................ 5
Hazards due to non-compliance with the safety instructions......... 6
Working in a safety-conscious manner ......................................... 6
Personal protective equipment ..................................................... 6
Personnel qualification ................................................................. 6
3 Intended Use .................................................................... 7
Notes on product warranty ........................................................... 7
Intended purpose ......................................................................... 7
Device revision ............................................................................. 7
Prohibited dosing media ............................................................... 7
4 Product description ......................................................... 8
Scope of delivery .......................................................................... 8
Design and function ..................................................................... 8
Rating plate ................................................................................ 10
Technical data ........................................................................... 10
5Dimensions..................................................................... 11
Vacuum regulator with threaded connection ............................... 11
Vacuum regulator with flange connection ................................... 11
6 Installation ..................................................................... 12
Installation location .................................................................... 12
Mounting position.......................................................................12
Installing the device ...................................................................12
Completing the installation ......................................................... 15
Installation examples .................................................................. 16
7 Commissioning .............................................................. 18
Inspecting the pressure system .................................................. 18
Inspecting the vacuum system ...................................................19
Switching the system on ............................................................ 19
8Operation........................................................................ 20
Test intervals ............................................................................. 20
9Shutdown....................................................................... 21
Short-term shutdown .................................................................21
Long-term shutdown ..................................................................21
Disposal of the old device...........................................................21
10 Maintenance................................................................... 22
Maintenance intervals ................................................................22
Accessories for maintenance...................................................... 22
Preparing the system for maintenance ....................................... 22
Maintaining the inlet valve ..........................................................23
Maintaining the vacuum part ...................................................... 25
Conclusion of maintenance ........................................................27
11 Troubleshooting ............................................................. 28
12 Spare parts .................................................................... 29
Individual parts .......................................................................... 30
Complete assemblies ................................................................. 31
Maintenance sets ....................................................................... 31
13 Declaration of Incorporation ......................................... 32
14 Declaration of harmlessness ........................................ 33
15 Warranty application ..................................................... 35
16 Index .............................................................................. 37

Notes for the Reader
General non-discrimination
4
Vacuum Regulator for Chlorine Gas C 2700-V
© Lutz-Jesco GmbH 2016
Operating Instructions
BA-21210-02-V05
1 Notes for the Reader
This operating manual contains information and behaviour rules for the
safe and designated operation of the device.
Observe the following principles:
read the entire operating manual prior to commissioning the device.
ensure that everyone who works with or on the device has read the
operating manual and follows the instructions.
keep the operating manual throughout the service life of the device.
pass the operating manual on to any subsequent owner of the
device.
1.1 General non-discrimination
In these operating instructions, only the male gender is used where
grammar allows gender allocation. The purpose of this is to make the
text easy to read. Men and women are always referred to equally. We
would like to ask female readers for understanding of this text simplifi-
cation.
1.2 Explanation of the signal words
Different signal words in combination with warning signs are used in
this operating manual. Signal words illustrate the gravity of possible
injuries if the risk is ignored:
I
1.3 Explanation of the warning signs
Warning signs represent the type and source of a danger:
1.4 Identification of warnings
Warnings are intended to help you recognise risks and avoid negative
consequences.
This is how warnings are identified:
1.5 Instruction for action identification
This is how pre-conditions for action are identified:
Pre-condition for action which must be met before taking action.
This is how instructions for action are identified:
Separate step with no follow-up action.
1. First step in a series of steps.
2. Second step in a series of steps.
Result of the above action.
Action completed, aim achieved.
Signal word Meaning
DANGER Refers to imminent danger. Ignoring this sign may
lead to death or the most serious injuries.
WARNING Refers to a potentially hazardous situation. Failure
to follow this instruction may lead to death or
severe injuries.
CAUTION Refers to a potentially hazardous situation. Failure
to follow this instruction may lead to minor injury
or damage to property.
NOTICE Refers to a danger which, if ignored, may lead to
risk to the machine and its function.
Warning sign Type of danger
Danger to life from chlorine poisoning
General danger zone
Danger of damage to machine or functional
influences
Warning
sign SIGNAL WORD
Description of danger.
Consequences if ignored.
The arrow signals a safety precaution to be taken to eliminate
the danger.

Safety
General warnings 5
© Lutz-Jesco GmbH 2016
Subject to technical changes.
160426
Vacuum Regulator for Chlorine Gas C 2700-V Operating Instructions
BA-21210-02-V05
2 Safety
2.1 General warnings
The following warnings are intended to help you to eliminate the
dangers that can arise while handling the device. Risk prevention meas-
ures always apply regardless of any specific action.
Safety instructions warning against risks arising from specific activities
or situations can be found in the respective sub-chapters.
2.2 Information about chlorine
Chlorine is a hazardous substance. The chemical element chlorine is a
greenish-yellow, toxic gas with a pungent odour, which can be detected
in the air at concentrations below 1 ppm (= 1 ml/m³).
Chlorine is 2.5 times heavier than air and accumulates at ground level.
Chlorine is extremely toxic for water organisms. The reason for the
toxicity of chlorine is its extraordinary reactivity. It reacts with animal
and vegetable tissue and thus destroys it.
Air with a chlorine gas content of 0.5 – 1% leads to a quick death in
mammals and humans as it attacks the respiratory tract and the pulmo-
nary alveolus (formation of hydrogen chloride or hydrochloride acid).
DANGER
Danger to life from chlorine poisoning!
Chlorine is poisonous. In severe cases, breathing in chlorine may
lead to death. It irritates the eyes, the respiratory system and the
skin.
Use sufficient personal protective equipment.
When carrying out any work on the system, use a respirator
mask with a Type B gas filter that complies with EN 14387.
Always comply with the accident prevention regulations that
apply at the place of use.
Get rid of leaks without delay. You must get rid of even very
minor leaks without delay. Together with the humidity, chlorine
forms hydrochloric acid and corrosion rapidly results in
increased leakage.
Only use chlorine-resistant seals.
Only use seals once. Reusing them leads to leaks.
DANGER
Danger to life from chlorine poisoning!
If chlorine gas escapes, a filter mask is ineffective, since it is not a
self-contained breathing apparatus.
If chlorine gas escapes, wear type 2 self-contained breathing
apparatus that complies with EN 137.
DANGER
Danger to life from chlorine poisoning!
Chlorinators without gas warning devices represent an increased
safety risk since escaping chlorine gas can either not be detected
at all or not in good time.
Install a gas warning device.
WARNING
Increased risk of accidents due to insufficient qualifica-
tion of personnel!
Chlorinators and their accessories must only be installed, operated
and maintained by personnel with sufficient qualifications. Insuffi-
cient qualification will increase the risk of accidents.
Ensure that all action is taken only by personnel with sufficient
and corresponding qualifications.
Prevent access to the system for unauthorised persons.
NOTICE
Damage to the system due to the formation of hydro-
chloric acid
Chlorine gas is highly hygroscopic. This means that humidity enters
the system at any open connection on devices or pipes, which
results in the formation of hydrochloric acid and contamination.
Damage to the devices is then inevitable.
Keep all the connections (in the vacuum system too) closed at all
times.
NOTICE
Faults due to insufficient chlorine quality
Impurities in the chlorine gas result in build-ups in devices and
valves and can chemically attack the components. This can cause
malfunctions.
Only use technically pure chlorine which satisfies the following
requirements:
- Chlorine mass content of at least 99.5%
- Max. chlorine water content of 20 mg/kg
Chlorine as per EN 937 satisfies these requirements.

Safety
Hazards due to non-compliance with the safety instructions
6
Vacuum Regulator for Chlorine Gas C 2700-V
© Lutz-Jesco GmbH 2016
Operating Instructions
BA-21210-02-V05
2.3 Hazards due to non-compliance with the safety
instructions
Failure to follow the safety instructions may endanger not only persons,
but also the environment and the device.
The specific consequences can be:
failure of major device and corresponding system functions,
failure of required maintenance and repair methods,
danger to persons,
danger to the environment caused by substances leaking from the
system.
2.4 Working in a safety-conscious manner
Besides the safety instructions specified in this operating manual,
further safety rules apply and must be followed:
accident prevention regulations
safety and operating provisions,
safety regulations on handling hazardous substances,
environmental protection provisions,
applicable standards and legislation.
2.5 Personal protective equipment
Depending on the type of work being performed, appropriate protective
equipment must be worn. Read the Accident Prevention Regulations and
the Safety Data Sheets on the dosing media to find out what protective
equipment is required.
As a minimum, the following protective equipment is recommended:
Mask Protective clothing Gloves Safety footwear
Corresponding protective equipment must be used during these tasks:
commissioning,
all work on gas-bearing sections of the system
changing the chlorine gas containers,
shutdown,
maintenance work,
disposal.
2.6 Personnel qualification
Any personnel who work with the device must have appropriate special
knowledge and skills.
Anybody who works with the device must meet the conditions below:
attendance at all the training courses offered by the owner,
personal suitability for the respective activity,
sufficient qualification for the respective activity,
training on the handling of the device.
knowledge of safety equipment and the way this equipment func-
tions,
knowledge of this operating manual, particularly of safety instruc-
tions and sections relevant for the activity,
knowledge of fundamental regulations regarding health and safety
and accident prevention.
All persons must generally have the following minimum qualification:
training as specialists to carry out work on the device unsupervised,
sufficient training that they can work on the device under the super-
vision and guidance of a trained specialist.
This operating manual distinguishes between these user groups:
2.6.1 Specialist staff
Specialist staff are able, thanks to their professional training, knowledge
and experience as well as knowledge of the respective provisions, to do
the job allocated to them and recognise and/or eliminate any possible
dangers by themselves.
2.6.2 Trained persons
Trained persons have been trained by the operator on the tasks they are
supposed to perform and on the dangers stemming from improper
behaviour.
Trained persons have attended all trainings offered by the operator.
2.6.3 Personnel tasks
In the table below you can check what qualifications are the pre-condi-
tion for the respective tasks. Only people with appropriate qualifications
are allowed to perform these tasks.
Qualification Activities
Specialist staff Assembly
Commissioning
Taking out of operation
Maintenance
Repairs
Disposal
Fault rectification
Trained persons Storage
Transportation
Operation

Intended Use
Notes on product warranty 7
© Lutz-Jesco GmbH 2016
Subject to technical changes.
160426
Vacuum Regulator for Chlorine Gas C 2700-V Operating Instructions
BA-21210-02-V05
3 Intended Use
3.1 Notes on product warranty
Any non-designated use of the device can compromise its function or
intended protection. This leads to invalidation of any warranty claims!
Please note that liability passes to the user in the following cases:
The device is operated in a manner which is not consistent with this
operating manual, particularly the safety instructions, handling
instructions and chapter Intended Use.
Information on the usage and ambient conditions (see "Technical
data" on page 10) is not observed.
If people operate the device who are not adequately qualified to
carry out their respective activities.
No original spare parts or accessories of Lutz-Jesco GmbH are used.
Unauthorised changes are made to the device.
The user uses different dosing media than those indicated in the
order.
Maintenance and inspection intervals are either not adhered to at all
or not as prescribed.
The device is commissioned before it or the corresponding system
has been correctly and completely installed.
Safety equipment has been bridged, removed or made inoperative in
any other way.
3.2 Intended purpose
The vacuum regulator is designated exclusively for chlorinators based
on the vacuum procedure. The vacuum regulator is only supplied with
gaseous chlorine. It reduces the existing underpressure from the chlo-
rine gas supply to a lower pressure than the atmospheric air pressure.
Only technically pure chlorine with a mass chlorine content of at least
99.5% may be used.
3.3 Device revision
This operating manual applies to the following devices:
The date of production is stated on the rating plate.
3.4 Prohibited dosing media
The device must not be used for the following media and substances:
Any gases except chlorine gas,
Liquid chlorine
Chlorine of insufficient quality.
Device Month / year of manufacture
Vacuum Regulator for Chlorine Gas
C 2700-V
07/2007 onwards

Product description
Scope of delivery
8
Vacuum Regulator for Chlorine Gas C 2700-V
© Lutz-Jesco GmbH 2016
Operating Instructions
BA-21210-02-V05
4 Product description
4.1 Scope of delivery
Carefully check the delivery prior to installation and refer to the delivery
note to ensure the delivery is complete and to check for any transport
damage. Contact the supplier and/or carrier regarding any questions
concerning the delivery and/or transport damage. Do not operate defec-
tive devices.
The device is assembled ready-to-install. All the openings are closed by
transportation locks.
The scope of delivery includes:
Vacuum regulator with inlet valve and integrated safety valve.
Pressure gauge (optional)
Flange connection on chlorine gas input including screws and seal
(optional)
5-m tube with mounting material as blow-off line
Ammonia solution for leakage test
Operating manual
4.2 Design and function
4.2.1 Design of a vacuum chlorinator
Fig. 4-1: Design of a vacuum chlorinator
The chlorine gas is under overpressure when it comes from the chlorine
barrels. The vacuum regulator (1) only allows the chlorine to flow if
there is a suctioning vacuum at the device’s output. Therefore, if a line
behind the vacuum regulator breaks, there is no need to fear a chlorine
leak.
The dosing device comprises a flow meter (2) with manual control
valve, and also often an electrically actuated control valve (3) and a
pressure regulator (4).
The injector (6) creates the vacuum based on the Venturi effect and
mixes the chlorine gas in the motive water flow. If the water does not
move, chlorination is stopped immediately. Then the non-return valve
(5) prevents water from penetrating into the dosing devices.
4.2.2 Structure of the device
Fig. 4-2: Structure of the device
Cl
2
H
2
O
M
1
2
3
44
6
5
Item Description
1 Input
2 Pressure gauge (optional)
3 Safety valve output
4Plug
5 Output
2
5
1
4
3

Product description
Design and function 9
© Lutz-Jesco GmbH 2016
Subject to technical changes.
160426
Vacuum Regulator for Chlorine Gas C 2700-V Operating Instructions
BA-21210-02-V05
4.2.3 Function description
Fig. 4-3: Vacuum Regulator for Chlorine Gas C 2700-V - cross-sectional view
Pressurised chlorine gas flows from the chlorine barrel to the vacuum
regulator. The vacuum regulator comprises the inlet valve (1) and the
membrane chamber (3). In the inlet valve the chlorine gas is under
overpressure, in the membrane chamber there is a vacuum.
The PVC output of the vacuum regulator is connected to the injector. A
sufficient vacuum draws the diaphragm disc (4) upwards and pushes
the valve cone (2) downward against the spring force. The inlet valve (1)
opens and the amount of chlorine required flows into the membrane
chamber (3). If the vacuum is not sufficient, the spring closes the
system again. This results in a constant vacuum in the piping down-
stream of the vacuum regulator.
A constant vacuum ensures maximum system safety: In the event of a
leak, ambient air is drawn into the tube without enabling a dangerous
amount of chlorine gas to escape into the atmosphere.
If the valve cone (2) does not close properly due to heavy soiling, slight
overpressure builds up in the membrane chamber (3). In the event of
such faults, the safety valve (5) in the diaphragm disc opens and vents
the system vents to a neutralisation system, e.g., a chlorine eliminator
or an activated carbon cartridge.
Atmosphere
Chlorine (vacuum)
Chlorine (overpressure)
4
3
2
5
1

Product description
Rating plate
10
Vacuum Regulator for Chlorine Gas C 2700-V
© Lutz-Jesco GmbH 2016
Operating Instructions
BA-21210-02-V05
4.3 Rating plate
The rating plate contains information on the safety and functional
method of the product. The rating plate must be kept legible for the
duration of the service life of the product.
Fig. 4-4: Rating plate
4.4 Technical data
Item Meaning
1 Product designation
2 Part number
3 Serial number
4 Materials
5 Month of manufacture
6 Year of manufacture
Description Value
Throughput up to 200 kg/hr
Inlet pressure 1.5 – 16 bar
Operating vacuum -50 mbar
Response pressure of the safety valve 500 mbar
Pressure gauge (optional) 0 – 16 bar / Ø 63 mm
Materials Inlet valve Brass (chemically nickel-
plated), Monel, Hastelloy
Vacuum housing PVC
Seals FPM, PTFE
Weight with flange and pressure
gauge
approx. 8 kg
Ambient temperature 10 – 50°C
(no direct sunlight)
Lutz-Jesco GmbH 30900 Wedemark
Am Bostelberge 19 Germany
Chlorine Gas Vacuum Regulator C 2700-V
12/2008
P/N: 1234567890
S/N: 102A12345 Made in Germany
*102A12345678*
Material: PVC/FPM/Monel/Ms58
2
3
1
4 5 6

Dimensions
Vacuum regulator with threaded connection 11
© Lutz-Jesco GmbH 2016
Subject to technical changes.
160426
Vacuum Regulator for Chlorine Gas C 2700-V Operating Instructions
BA-21210-02-V05
5 Dimensions
All dimensions in mm
5.1 Vacuum regulator with threaded connection
Fig. 5-1: Dimensioned drawing of vacuum regulator with threaded connection
5.2 Vacuum regulator with flange connection
Fig. 5-2: Dimensioned drawing of vacuum regulator with flange connection
224Ø26
20
1" NPT
254~
37
ØD
A
8/12
224Ø26
20
266~
ØD
B
14Ø
85Ø
C
8/12
Flange DN25 / PN40 with groove
(form D) according to EN1092
Size Value
A 161
B 220
C59
ØD 50

Installation
Installation location
12
Vacuum Regulator for Chlorine Gas C 2700-V
© Lutz-Jesco GmbH 2016
Operating Instructions
BA-21210-02-V05
6 Installation
6.1 Installation location
Based on the chlorine direction of flow, the vacuum regulator is the final
device in the installation which is operated with overpressure. For this
reason, the vacuum regulator must be installed in the chlorine supply
room which is monitored by a gas warning device (see "Installation
examples" on page 16).
All the subsequent devices and lines in the direction of flow operate at
negative pressure compared to the atmosphere. These devices are
normally installed in the dosing device room.
The device must not be exposed to direct sunlight.
6.2 Mounting position
The device input must point downwards.
Fig. 6-1: Mounting position
6.3 Installing the device
6.3.1 Chlorine input (pressure line)
The vacuum regulator should be installed directly on the supply line. It
can be carried by the line and thus does not have to be fixed separately.
However, the line should be sufficiently secured.
The line from the chlorine barrel to the vacuum regulator must be laid
so as to ascend continuously.
A shut-off valve should be fitted upstream of every vacuum regulator.
Seamless pipes with a nominal diameter of DN25 (1") made of non-alloy
carbon steel are used as pressure lines. A larger pipe only has to be
used for very long distances or if several vacuum regulators are
connected to a joint supply line.
The following nominal diameters are recommended for the pressure line
(pressure drop of a maximum of 0.5 bar, max. speed of 20 m/s, calcu-
lated at 1.5 bar with 4x90° angles):
WARNING
Increased risk of accidents due to insufficient qualifica-
tion of personnel!
Chlorinators and their accessories must only be installed, operated
and maintained by personnel with sufficient qualifications. Insuffi-
cient qualification will increase the risk of accidents.
Ensure that all action is taken only by personnel with sufficient
and corresponding qualifications.
Prevent access to the system for unauthorised persons.
NOTICE
Damage to the system due to incorrect installation
Failure to comply with the installation instructions (e.g., use of
unsuitable tools, incorrect torques) can damage the system compo-
nents.
Only apply the appropriate amount of force to plastic compo-
nents! Plastic threads (especially PVC threads) can be tightened
and loosened more easily by applying a thin layer of silicone or
PTFE grease to them beforehand.
Observe the following torques:
NOTICE
Damage to the system due to liquid chlorine
The vacuum regulator is only suitable for gaseous chlorine. Liquid
chlorine destroys PVC components.
Install a chlorine evaporator upstream of the vacuum regulator
if liquid chlorine is used. An additional pressure-reducing valve
prevents condensation of the chlorine gas in the installation
downstream of the chlorine evaporator.
In the case of systems without pressure-reducing valves, the
highest temperature must be in the line directly before the
vacuum regulator. This is achieved by heating up the line
directly upstream of the inlet valve with a heating collar or by
equipping the entire pipe line with a heating belt. This prevents
the condensation of chlorine gas.
Install a moisture eliminator with a heating collar at the vacuum
regulator input to evaporate residual quantities of liquid chlorine.
Mass chlorine
flow
Length of pressure line
10 m 20 m 30 m 50 m 100 m 150 m
80 kg/hr DN25 DN25 DN25 DN25 DN25 DN25
120 kg/hr DN25 DN25 DN25 DN25 DN25 DN32
200 kg/hr DN25 DN25 DN25 DN32 DN32 DN32
400 kg/hr DN32 DN32 DN32 DN40 DN40 DN50
600 kg/hr DN40 DN40 DN40 DN40 DN50 DN50

Installation
Installing the device 13
© Lutz-Jesco GmbH 2016
Subject to technical changes.
160426
Vacuum Regulator for Chlorine Gas C 2700-V Operating Instructions
BA-21210-02-V05
Installing the connection with flange connection
Precondition for action:
The inside of the supply line is clean and dry.
The transport protection has been removed.
The sealing surfaces are free of contamination and damage.
The seals are clean, undamaged and dry.
The screws, nuts and washers are clean and undamaged.
Fig. 6-2: Installing the flange connection
Perform the following working steps:
1. Lubricate the sliding surfaces and threads of the screw, nuts and
discs using, for example, fitting or PTFE grease.
2. Place the flat gasket (2) onto the projecting tongue of the connec-
tion flange (1). Install the seal whilst dry.
3. Place the groove flange (3) of the vacuum regulator in position.
Make sure that the flat gasket does not slip.
4. Attach the screws (4), discs (5, 6) and nuts (7) by hand.
5. Tighten the screws evenly in three stages crosswise: 20 Nm, 35
Nm, 50 Nm. After this, retighten all the screws to the full target
tightening torque (50 Nm).
6. Setting the seal (adapting to the flange seal surface) can make it
necessary to retighten the screws). Thus the screws should be
retightened to a torque of 50 Nm after a few hours.
Installed chlorine input with flange connection.
Installing the connection with threaded connection
Precondition for action:
The inside of the supply line is clean and dry.
The transport protection has been removed.
The threads are bare metal.
Perform the following working steps:
1. Clean the threads with a degreasing cleaning agent, e.g., alcohol.
2. Allow the threads to dry completely.
3. Apply the thread sealant compound around the male thread at the
start of thread. Keep the first thread pitch clear. Press the thread
sealant compound into the thread groove to ensure the thread
flanks are well moistened.
Fig. 6-3: Seal the threads.
4. Guide the threaded pin into the internal thread and, in doing so,
apply a little adhesive to the internal thread. Screw the components
together by hand.
5. Tighten the connection using tools. When doing this, the tool must
only be used on the metal inlet valve and not on the PVC component
of the vacuum regulator. The thread size 1" NPT demands approx.
150 Nm
6. Remove any excess adhesive with a cloth.
Any screws, nuts and washers that are removed during
installation must be replaced with new ones if damaged.
Used screws, nuts and washers may only be installed if they
are in at least new condition.
i
2
3
1
4
5
6
7
DANGER
Danger to life from chlorine poisoning!
Use chlorine-resistant material for sealing pipe connections and fit-
tings in pressurised pipes. Inadequate sealants will react with chlo-
rine and cause leaks.
Use only sealants that resist contact with chlorine (e.g., anaero-
bic sealing compounds).
NOTICE
Leak due to incorrect installation
To correctly align the connection, it may be necessary to turn the
thread in an anticlockwise direction. When releasing the connec-
tion, bubbles form in the adhesive which can result in leaks.
Only turn the thread in a clockwise direction.
If, after tightening, the connection is not correctly aligned,
repeat steps 1 – 5.

Installation
Installing the device
14
Vacuum Regulator for Chlorine Gas C 2700-V
© Lutz-Jesco GmbH 2016
Operating Instructions
BA-21210-02-V05
7. Allow the adhesive to cure for at least 12 hours before carrying out
the leak test.
Installed chlorine input with threaded connection
6.3.2 Chlorine output (vacuum line)
Pipes made of PVC-U must be used for the vacuum lines. The pipe with
the nominal diameter of the vacuum connection should be chosen for
short distances. A larger pipe should be used for longer distances. If
several devices are connected to a line, the line must be calculated for
the entire chlorine flow.
The following nominal diameters are recommended for the vacuum line
(pressure drop of a maximum of 25 mbar, calculated at 0.9 bar with
4x90° angles):
If necessary, a greater nominal diameter can be installed for longer
distances and for shorter sections just in front of or after the devices a
connection with the nominal diameter of the devices can be selected:
Fig. 6-4: Long vacuum line
Installing the vacuum line
Precondition for action:
The chlorine input of the vacuum regulator is installed.
The vacuum line is secured with a sufficient number of pipe clamps
and meets with the output of the vacuum regulator without tension.
All the components are clean and dry.
The transport protection at the output of the vacuum regulator has
been removed.
Perform the following working steps:
1. Cut the PVC pipe at a right angle. Make a bevel on the outside of the
pipe (approx. 3 mm x 20°).
2. Clean the pipe and the sleeve with the cleaning agent recom-
mended by the manufacturer of the adhesive.
3. Glue the pipe in the connection. When doing so, follow the instruc-
tions for the PVC adhesive.
Fig. 6-5: Installing the chlorine output
4. Install the connection on the device. Make sure that the O-ring is
fitted.
5. Tighten the union nut by hand.
6. Allow the adhesive to cure for at least 3 hours before carrying out
the leak test.
Installed vacuum line.
If the pressure gauge on the inlet valve is pointing in the
wrong direction after installation of the chlorine supply, the
pressure gauge can be attached to the opposite side. For this,
exchange the pressure gauge and threaded plug. They are
installed with PTFE strips.
Mass chlorine
flow
Length of vacuum line
5 m 10 m 20 m 30 m 50 m 100 m
80 kg/hr DN32 DN32 DN40 DN40 DN40 DN50
120 kg/hr DN32 DN40 DN40 DN50 DN50 DN65
200 kg/hr DN40 DN50 DN50 DN65 DN65 DN65
Item Description
1 Vacuum regulator
2 Dosing device
LA
Line at the connection of the vacuum regulator
approx. 0.5 m in the nominal diameter of the connection
L Greater distance with a larger nominal diameter
LB
Line at the connection of the dosing device
approx. 0.5 m in the nominal diameter of the connection
i
M
L
L
A
L
B
1
2

Installation
Completing the installation 15
© Lutz-Jesco GmbH 2016
Subject to technical changes.
160426
Vacuum Regulator for Chlorine Gas C 2700-V Operating Instructions
BA-21210-02-V05
6.3.3 Safety valve
The blow-off line is a tube whose open end should be located in the
vicinity of the gas sensor. The installation of an activated carbon
cartridge is recommended at the open end of the tube which prevents
an alarm being issued in the event of system-related short shock pres-
sures.
Fig. 6-6: Blow-off line
Installing the blow-off line
Precondition for action:
The chlorine input of the vacuum regulator is installed.
The chlorine output of the vacuum regulator is installed.
The transport protection on the safety valve has been removed.
Fig. 6-7: Installing the tube connection
Perform the following working steps:
1. Cut the tube (1) at a right angle.
2. Push the union nut (2) onto the tube.
3. Push the end of the tube onto the cone of the tube connection (3).
4. Tighten the union nut by hand.
5. Secure the tube onto the wall.
6. If relevant, install the activated carbon cartridge at the open end of
the tube.
Installed blow-off line.
6.4 Completing the installation
After completing installation, you must check that all the connections
are leak-proof (see "Inspecting the pressure system" on page 18 and
"Inspecting the vacuum system" on page 19).
Item Description
1 Vacuum regulator
2 Blow-off line
3 Activated carbon cartridge
4 Gas sensor
A transparent PVC tube is ideal as a blow-off line. It becomes
milky in appearance when it comes into contact with chlorine
for the first time and thus allows faults to be detected early
on.
4
3
21
i
31
2
All the exposed bare metal surfaces must be painted as the
atmosphere in chlorine gas rooms is highly corrosive. A two-
part epoxy resin varnish yellow RAL1003 is suitable for
example. The surfaces must not be painted until after
successful completion of the leak test.
i

Installation
Installation examples
16
Vacuum Regulator for Chlorine Gas C 2700-V
© Lutz-Jesco GmbH 2016
Operating Instructions
BA-21210-02-V05
6.5 Installation examples
6.5.1 Installation without a chlorine evaporator
Fig. 6-8: Installation without a chlorine evaporator
M
A B
3
12
56
8
14
10
13
11
12
16
15
4
7
9
Item Description
A Room for the chlorine supply
B Dosing device room
1 Chlorine barrel
2 Chlorine barrel scale
3 Manifold
4 Changeover switch
5 Chlorine gas filter
6 Pressure reducing valve
7 Moisture eliminator with heating collar
8 Vacuum regulator
9 Activated carbon cartridge
10 Dosing device
11 Injector with non-return valve
12 Motive water pump
13 Gas warning device
14 Horn
15 Gas sensor
16 Entrance port of the chlorine eliminator

Installation
Installation examples 17
© Lutz-Jesco GmbH 2016
Subject to technical changes.
160426
Vacuum Regulator for Chlorine Gas C 2700-V Operating Instructions
BA-21210-02-V05
6.5.2 Installation with a chlorine evaporator
Fig. 6-9: Installation with a chlorine evaporator
M
M
AB
17
1
3
4
12
7
8
20
6
5
910
11
2
14
13
18
16
15
19
Item Description
A Room for the chlorine supply
B Dosing device room
1 Chlorine barrel
2 Chlorine barrel scale
3 Manifold
4 Rupture disk with expansion container
5 Changeover switch
6 Chlorine evaporator
7 Expansion system
8 Quick-action valve
9 Chlorine gas filter
10 Pressure reducing valve
11 Moisture eliminator with heating collar
12 Vacuum regulator
13 Activated carbon cartridge
14 Dosing device
15 Motive water pump
16 Injector with non-return valve
17 Gas warning device
18 Gas sensor
19 Horn
20 Entrance port of the chlorine eliminator

Commissioning
Inspecting the pressure system
18
Vacuum Regulator for Chlorine Gas C 2700-V
© Lutz-Jesco GmbH 2016
Operating Instructions
BA-21210-02-V05
7 Commissioning
7.1 Inspecting the pressure system
Check the tightness of the pressure system from the chlorine container
to the vacuum regulator in two stages:
7.1.1 Carrying out the leak test with nitrogen
Precondition for action:
All the open connections of the pressure system were closed
correctly.
All the shut-off valves in the pipe system were opened.
A nitrogen cylinder was connected.
Perform the following working steps:
1. Slowly raise the system pressure on the nitrogen cylinder's pres-
sure reducing valve to 10 bar.
2. Close the nitrogen cylinder's valve.
3. Apply soap solution to all the potential leaks. Bubbles will appear at
leak locations.
4. Close the output on the nitrogen cylinder's pressure reducing valve
and observe the pressure gauge in the installation. The pressure
must not drop within one hour.
5. If necessary, repair leaks and repeat the leak test.
Leak test with nitrogen carried out.
7.1.2 Carrying out the leak test with chlorine
Precondition for action:
The leak test with nitrogen was carried out successfully.
All the open connections of the pressure system were closed
correctly.
A chlorine container was connected.
The injector is ready for operation.
Perform the following working steps:
1. Briefly open the chlorine container valve and close it again.
2. Carry out the ammonia test on the entire pressure system:
Ammonia steam with chlorine forms a white vapour and makes
even very small leaks visible. Hold an open bottle containing
ammonia solution close to the pipe and make slight pumping
motions with the plastic bottle.
Fig. 7-1: Leak test with ammonia
3. If you find leaks: Use the injector to suction off the chlorine immedi-
ately! Repair leaks and repeat the leak test.
4. If you do not find any leaks: Open the chlorine container valve and
leave it open.
DANGER
Chlorine gas can escape due to systems that are leaky
or not installed correctly!
Chlorinators represent an increased risk to safety if they have not
been installed properly, if adequate tightness tests have not been
performed or if the devices are not in a good condition.
Before commissioning the system, have an expert inspect that it
is tight and in the proper condition.
The condition of the installation must be checked for adequate
tightness on a regular basis.
Get rid of leaks without delay. You must get rid of even very
minor leaks without delay. Together with the humidity, chlorine
forms hydrochloric acid and corrosion rapidly results in
increased leakage.
You are strongly recommended to carry out this inspection
before carrying out the leak test with chlorine since it demon-
strates leaks in the pressure system without the risk of chlo-
rine escaping.
As an alternative, you can carry out the inspection using dry
compressed air.
i
DANGER
Danger to life from chlorine poisoning!
If you start the leak test with chlorine before the entire system has
been installed and the injectors are ready for operation, the chlorine
may not be extracted immediately in the case of a leak.
Make sure that all the components in the system are installed
correctly and the injectors are ready for operation before starting
the leak test with chlorine.
Put on protective clothing before carrying out the leak test with
chlorine.
NOTICE
Damage to the system by the ammonia solution
If the ammonia solution comes into contact with the system, this
leads to corrosion on the devices.
Make sure that you do not spill any ammonia.
NH3

Commissioning
Inspecting the vacuum system 19
© Lutz-Jesco GmbH 2016
Subject to technical changes.
160426
Vacuum Regulator for Chlorine Gas C 2700-V Operating Instructions
BA-21210-02-V05
5. Carry out the leak test again.
6. Close the chlorine container valve and suction off the chlorine using
the injector.
Leak test with chlorine carried out.
7.2 Inspecting the vacuum system
Tightness of the vacuum system is inspected together with the dosing
device.
7.2.1 Carry out the leak test on the vacuum system
Precondition for action:
The vacuum system is completely installed.
All the open connections of the vacuum system were closed.
The injector is ready for operation.
Perform the following working steps:
1. Connect the chlorine supply to, for example, the chlorine container
valves or to a valve in the vacuum regulator supply line.
2. Open the valves on the dosing device to adjust the dosing quantity.
3. Switch on the injector and wait until the vacuum meter on the
dosing device displays at least 0.5 bar underpressure.
4. Switch off the injector.
The vacuum must stay unchanged for at least five minutes.
5. If the vacuum collapses quickly, eliminate the leak (see 7.2.2
”Localising leakages in the vacuum system“) and repeat the check
on the vacuum system.
Vacuum system leak test carried out.
7.2.2 Localising leakages in the vacuum system
Leaks in the vacuum system are localised with the help of compressed
air or nitrogen at a slight positive pressure and a soap solution.
Precondition for action:
When checking the tightness of the vacuum system, a leak was
detected.
The vacuum system is fully assembled.
All the open connections of the vacuum system were closed
correctly.
The valves on the chlorine supply have been closed.
If the system was previously operated with chlorine, the residual
chlorine has been extracted with the injector and the system oper-
ated for approx. 5 minutes using nitrogen or dry compressed air.
The injector was switched off.
1. Close the water valves upstream and downstream of the injector.
2. Connect the supply of nitrogen or dry compressed air to the vacuum
system.
3. Slowly increase the system pressure to approx. 0.2 – 0.4 bar (at
significantly higher positive pressures, the safety valve in the
vacuum regulator will open).
4. Apply soap solution to all the potential leaks.
Bubbles will appear at leak locations.
Leakage in the vacuum system localised
7.3 Switching the system on
The vacuum regulator does not need to be operated separately. If there
is a sufficient vacuum and supply of chlorine, the device opens and, if
the vacuum is not sufficient, the device stops the flow of chlorine gas.
NOTICE
Operational disturbances due to leaks in the vacuum
system
In normal operation, you cannot detect minor leaks in the vacuum
system since no chlorine escapes. Humid air, however, enters the
system. Together with the chlorine, the humidity can cause build-
ups and operational disturbances.
With the injector switched off, there may be a slight chlorine smell.
Carry out a proper inspection of the vacuum system.
Ensure that all action is taken only by personnel with sufficient
and corresponding qualifications.
Some dosing devices feature a valve which protects the
injector from excessive vacuums. If, for example, this vacuum
is set to an underpressure of 0.4 bar, an underpressure of 0.5
bar cannot be reached during the leak test.
i
NOTICE
Damage to the plant due to excessive pressure
When using positive pressure to localise leaks, components in the
vacuum system, e.g. membranes or springs, may be mechanically
overloaded.
Use a maximum positive pressure of 0.5 bar.

Operation
Test intervals
20
Vacuum Regulator for Chlorine Gas C 2700-V
© Lutz-Jesco GmbH 2016
Operating Instructions
BA-21210-02-V05
8 Operation
The vacuum regulator does not need to be operated separately. If there
is a sufficient vacuum and supply of chlorine, the device opens. If the
vacuum is interrupted, the device stops the flow of chlorine gas.
8.1 Test intervals
You must check the components of the chlorinator for leaks on a daily
basis and after maintenance or commissioning work.
DANGER
Chlorine gas can escape due to systems that are leaky
or not installed correctly!
Chlorinators represent an increased risk to safety if they have not
been installed properly, if adequate tightness tests have not been
performed or if the devices are not in a good condition.
Before commissioning the system, have an expert inspect that it
is tight and in the proper condition.
The condition of the installation must be checked for adequate
tightness on a regular basis.
Ensure that all action is taken only by personnel with sufficient
and corresponding qualifications.
In the event of an unfavourable combination of supply pres-
sure, pipe length and dosing amount, the vacuum regulator
may vibrate.
The vibrations can be remedied by adjusting the supply pres-
sure or by slightly restricting the stop valve ahead of the
vacuum regulator.
i
Table of contents
Other Lutz Controllers manuals
Popular Controllers manuals by other brands

inVENTer
inVENTer sMove S4 Long instructions
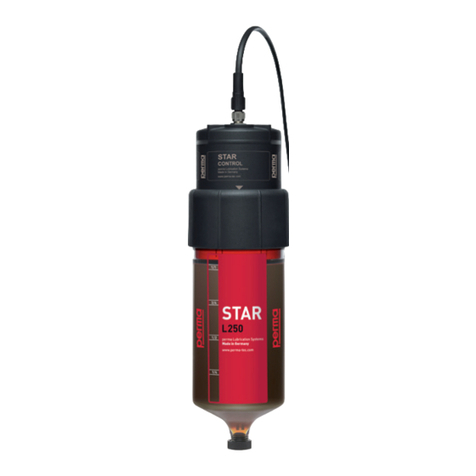
Perma
Perma star control series operating instructions
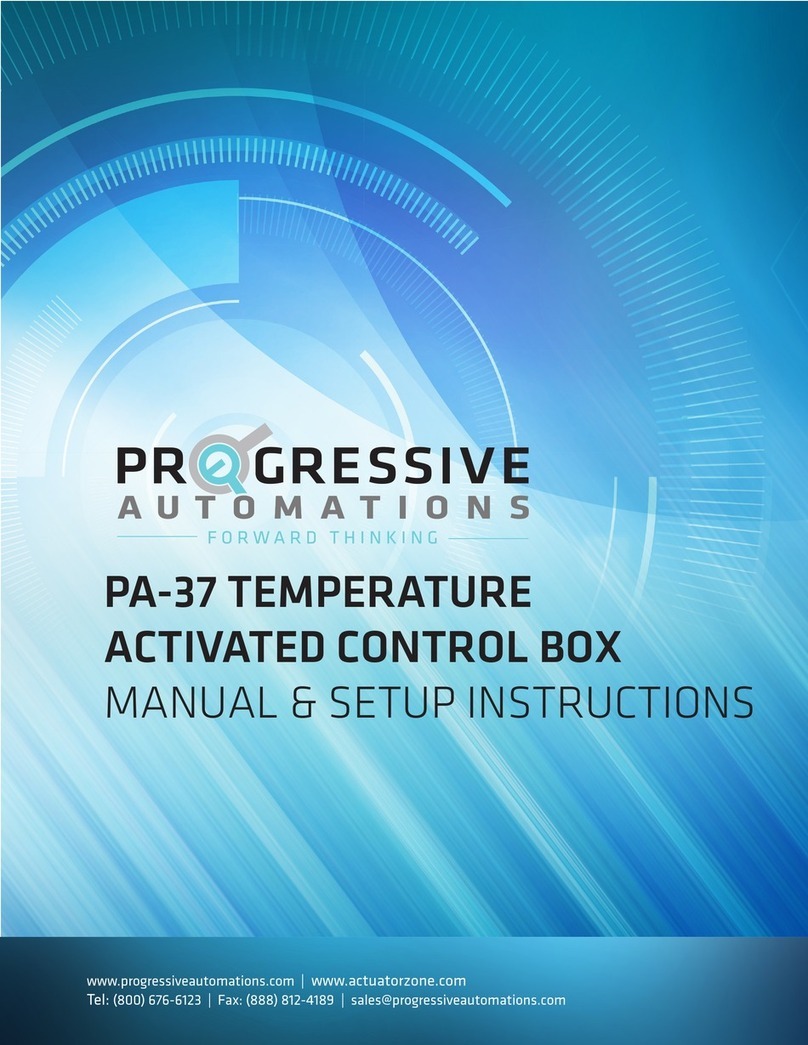
progressive automations
progressive automations PA-37 User's manual and setup instructions
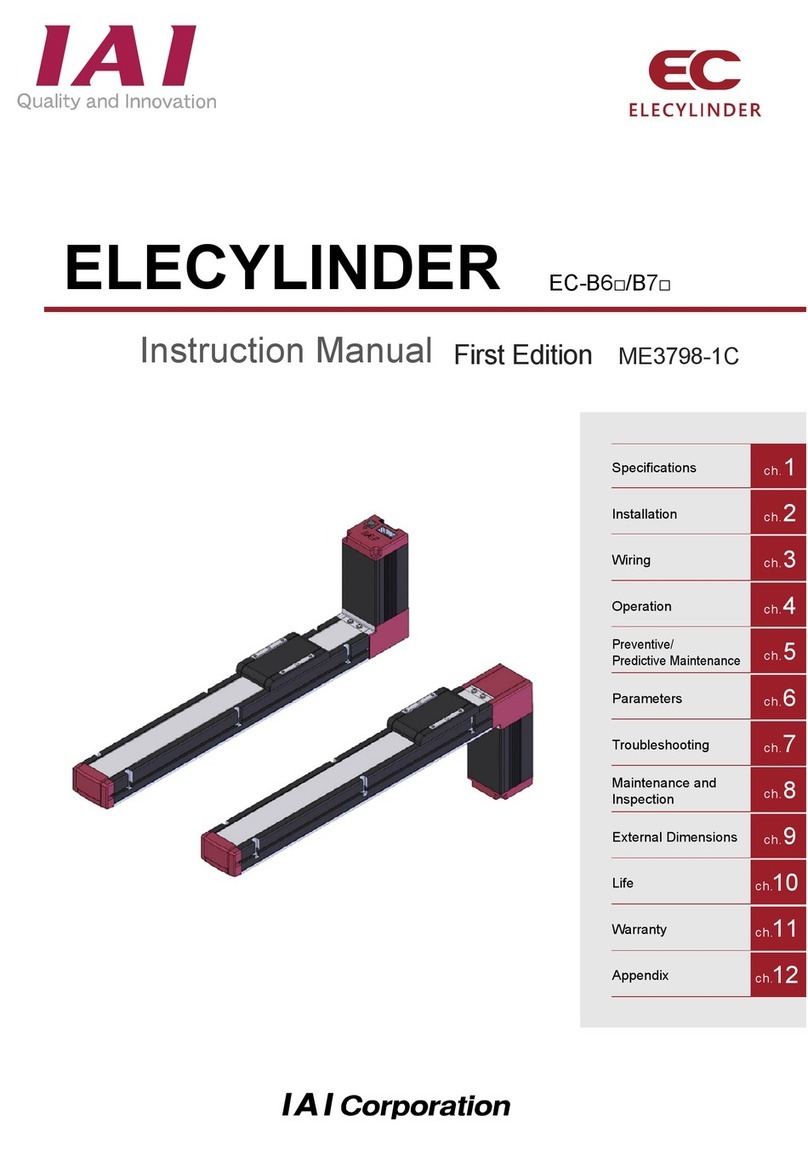
IAI
IAI EYECYLINDER EC-B6 Series instruction manual
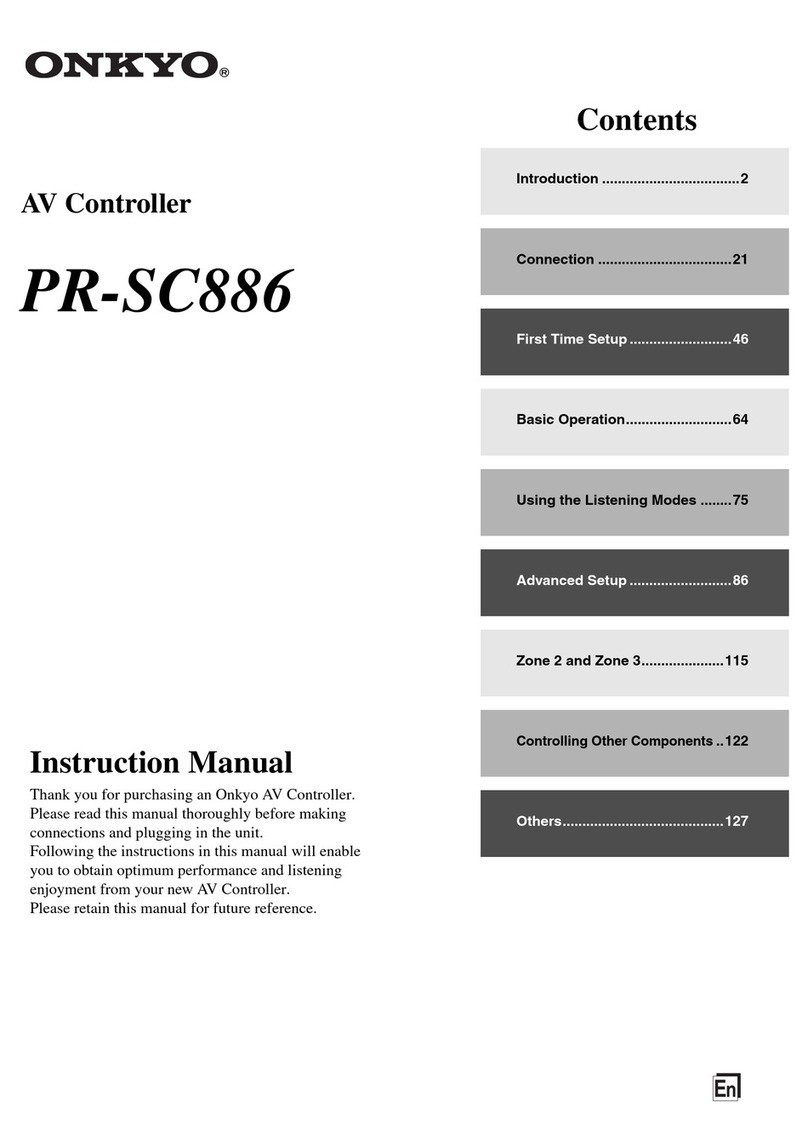
Onkyo
Onkyo SC886 - PR Preamplifier / Processor instruction manual
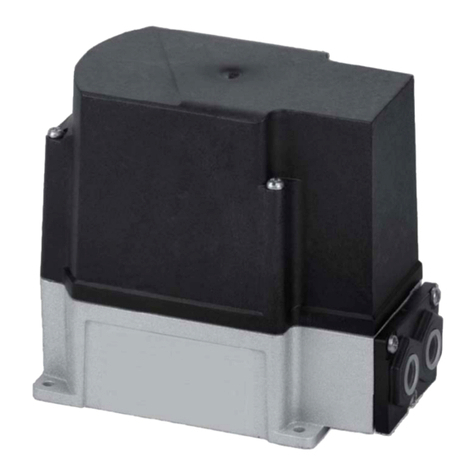
Eclipse
Eclipse TRILOGY T500 Series instruction manual