Maguire Products Weigh Scale Blender WSB Manual

MAGUIRE PRODUCTS INC.
Weigh Scale Blender
®
For the Maguire Touchscreen Controller
Touch Screen Controller
WEIGH SCALE BLENDER®
TWELVE COMPONENT SOFTWARE
INSTALLATION •OPERATION •MAINTENANCE
Copyright ©Maguire Products, Inc. 2014

MAGUIRE PRODUCTS, INC.
Edition: August 6, 2014
2
W
EIGH SCALE BLENDER®

MAGUIRE PRODUCTS, INC.
Edition: August 5, 2014
3
W
EIGH SCALE BLENDER®
Copyright
©2014 Maguire Products Inc.
To every person concerned with use and maintenance of the Maguire Weigh Scale Blender it is
recommended to read thoroughly these operating instructions. Maguire Products Inc. accepts no
responsibility or liability for damage or malfunction of the equipment arising from non-observance of
these operating instructions.
To avoid errors and to ensure trouble-free operation, it is essential that these operating instructions
are read and understood by all personnel who are to use the equipment.
Should you have problems or difficulties with the equipment, please contact Maguire Products Inc.
or your local Maguire distributor.
These operating instructions only apply to the equipment described within this manual.
Manufacturer’s Contact Information
Maguire Products Inc.
11 Crozerville Road
Aston, PA. 19014
Phone: 610.459.4300
Fax: 610.459.2700
Website: http://www.maguire.com
Email: [email protected]

MAGUIRE PRODUCTS, INC.
Edition: August 6, 2014
4
W
EIGH SCALE BLENDER®
Maguire Weigh Scale Blender
12 Software Operation & Maintenance Manual
Table of Contents
Table of Contents_________________________________________________________________ 4
EC Declaration of Conformity_______________________________________________________ 6
SECTION 1 – BLENDER STARTUP_____________________________________________ 7
Getting Started – Read this page! ___________________________________________________ 7
Safety Hazards ___________________________________________________________________ 8
Safety Features __________________________________________________________________ 8
Blender Parts Key _______________________________________________________________ 10
Controller Parts Key _____________________________________________________________ 11
Assembly and Installation Instructions ______________________________________________ 12
Wiring Considerations____________________________________________________________ 16
Check Out Procedure ____________________________________________________________ 17
Check Out Procedure Diagnostics__________________________________________________ 19
Selecting the Correct Model _______________________________________________________ 20
Retrofit Touchscreen Controller Setup Instructions ___________________________________ 21
Communications ________________________________________________________________ 23
SECTION 2 - OPERATION ___________________________________________________ 24
Load Cell Calibration_____________________________________________________________ 24
Turning on Material Type Outputs __________________________________________________ 25
Material Type Definitions__________________________________________________________ 25
Setting Material Types____________________________________________________________ 26
Examples of Making Settings ______________________________________________________ 27
Materials Rate Calibration_________________________________________________________ 29
Entering Materials Settings________________________________________________________ 30
Special Instructions for Selected Models ____________________________________________ 31
Instructions for Normal Operation__________________________________________________ 32
Normal Operating Sequence - Each Cycle ___________________________________________ 34
Special Features_________________________________________________________________ 34
Touch Screen Controller Main Screen_______________________________________________ 36
Menu Map – Brief Explanation _____________________________________________________ 37
Menu Map – Full Explanation ______________________________________________________ 38
Parameters Introduction __________________________________________________________ 45
Navigating Parameters ___________________________________________________________ 45
General Parameters______________________________________________________________ 46

MAGUIRE PRODUCTS, INC.
Edition: August 5, 2014
5
W
EIGH SCALE BLENDER®
Component Parameters __________________________________________________________ 48
Saving Parameters in the User Backup Settings ______________________________________ 63
SECTION 3 - PRINTED OUTPUTS_____________________________________________ 64
Monitoring System Accuracy ______________________________________________________ 64
Cycle Printout Information ________________________________________________________ 64
Interpreting the Cycle Printout _____________________________________________________ 65
Troubleshooting with the Printout __________________________________________________ 66
Parameter Settings Printout _______________________________________________________ 69
Load Cell Calibration - Printout Verification __________________________________________ 69
Special Tests - Printout Verification ________________________________________________ 70
Material Usage Printout___________________________________________________________ 70
SECTION 4: TROUBLESHOOTING ____________________________________________ 72
What To Do_____________________________________________________________________ 72
Typical Problems ________________________________________________________________ 72
Mix Problems ___________________________________________________________________ 74
Increasing Throughput ___________________________________________________________ 75
Normal Operating Sequence_______________________________________________________ 76
Load Cell Raw Signal Readout _____________________________________________________ 78
Backup, Restore, Factory Reset ___________________________________________________ 79
Updating Controller Firmware _____________________________________________________ 80
SECTION 5 - HARDWARE MAINTENANCE _____________________________________ 81
Hardware Adjustments ___________________________________________________________ 81
Load Cell Recalibration___________________________________________________________ 82
Disclaimers_____________________________________________________________________ 97
Accuracy of this Manual __________________________________________________________ 97
Warranty _______________________________________________________________________ 97

MAGUIRE PRODUCTS, INC.
Edition: August 6, 2014
6
W
EIGH SCALE BLENDER®
EC Declaration of Conformity
Manufacturer: Maguire Products Inc.
Address: 11, Crozerville Road, Media, Pennsylvania, 19014, USA
Declares the following range of equipment described;
Make: Maguire Weigh Scale Blender
Model: WSB
Conforms to the following CE directives;
EEC 89/392 Machinery Directive
EEC 89/336 Electromagnetic Compatibility
Using the following CE standard references:
CEI EN 50081-1/2 CEI EN 55022
CEI EN 55082-2 CEI EN 61000-4-2
CEI EN 61000-4-3 CEI EN 61000-4-4
CEI EN 61000-4-5 CEI EN 61000-4-6
CEI EN 60204-1
And complies with the relevant Health and Safety requirements.
Responsible Person: Steve Maguire
President, Maguire Products, Inc.
Please Note: All Maguire blenders shipped within Europe have a CE Certificate with the shipping
documentation, which is specific to the model and serial number of the Maguire WSB blender
shipped. Please refer to your shipping documentation for further information.

MAGUIRE PRODUCTS, INC.
Edition: August 5, 2014
7
W
EIGH SCALE BLENDER®
SECTION 1 – BLENDER STARTUP
Getting Started – Read this page!
THE NEXT SECTIONS OF THIS MANUAL WILL GUIDE YOU, STEP BY STEP, TO A
SUCCESSFUL STARTUP.
IT WON'T TAKE LONG; SO.... PLEASE, DON'T SKIP AHEAD.
HERE ARE THE STEPS YOU WILL FOLLOW:
SAFETY HAZARDS - Page 8 ……………………….. TWO HAZARDS exist on this unit: MIX BLADES and SLIDE VALVES. Read
this short sensible page so no one gets hurt.
ASSEMBLY INSTRUCTIONS - Page 12 ……………. Very little assembly is required. But you might as well get it right the first
time. ALSO: Pay attention to the section on WIRING.
CHECK OUT PROCEDURE - Page 17 ……………. This is to see if you did it right. It also will tell if anything was damaged in
shipping.
LOAD CELL CALIBRATION - Page 22 …………… We already did this. But shipping or rough handling during assembly
sometimes creates load cell problems. If weight readings are not correct,
you MUST recalibrate the load cells.
SETUP OUTPUTS & MATERIAL TYPES - Page 22.. To "TURN ON" a component, it must be designated as to TYPE, either
REGRIND, NATURAL, or ADDITIVE. Each is handled differently by the
MATH routines. The controller MUST know the material TYPE to know what
the setting means. This is IMPORTANT. Be SURE you UNDERSTAND this
section before trying to operate your system.
RATE CALIBRATION - Page 27 …………………… This is NOT really necessary. But if your system uses non-standard
equipment, you MAY want to do this.
SETTINGS & NORMAL OPERATION - Page 28 … From this point forward, operating your system is a snap. This section tells
you just how simple it is and exactly what to expect under normal operating
conditions.
SPECIAL FEATURES - Page 29 …………………... Your system can do much more then you may know. This page reviews
briefly some of the added features that are available to you and where in this
manual you can find them.
PROCEED TO: SAFETY HAZARDS NEXT PAGE

MAGUIRE PRODUCTS, INC.
Edition: August 6, 2014
8
W
EIGH SCALE BLENDER®
Safety Hazards
MIX BLADE HAZARD
Mix Blades are driven with substantial Torque.
Never place your hand in the Mix Chamber while the blades are turning.
SERIOUS INJURY WILL RESULT
ADDITIONAL MIX BLADE HAZARD
Over time, Mix Blades may become RAZOR SHARP.
ALWAYS be careful when TOUCHING or CLEANING these blades.
Check for Sharp Edges frequently
Replace Blades if a Hazard exists.
SLIDE VALVES
Slide valves in hoppers SLAM CLOSED without warning.
They WILL injure your fingers.
ALWAYS keep fingers clear of slide gate openings.
NEVER use your fingers to clear an obstruction.
NEVER use your fingers to move a sticking slide gate.
Safety Features
SAFETY INTERLOCK SWITCH
The ACCESS DOOR is equipped with a safety interlock
switch that prevents the mix motor from running and the slide valves from opening.
DO NOT defeat this safety switch.
HOPPER FINGER GUARDS
Finger Guards are fitted into each Material Hopper compartment.
DO NOT reach through these Guards.
DO NOT use your fingers to clear an obstruction below these Guards.
DO NOT remove these Guards.

MAGUIRE PRODUCTS, INC.
Edition: August 5, 2014
9
W
EIGH SCALE BLENDER®

MAGUIRE PRODUCTS, INC.
Edition: August 6, 2014
10
W
EIGH SCALE BLENDER®
Blender Parts Key
1. Auger Feeder – Screw Feeder for feeding in small percentage materials such as Colors and Additives
2. Fixed Material Hopper – Material Hopper for main materials to be dosed by the slide gates
3. Removable Hopper – Removable Material hopper for small percentage materials such as Colors and
Additives
4. Hopper Access Door – Door to access inside of hopper for quick cleaning and materials changes
5. Sight Glass – Means to view current material level inside the hopper
6. Vertical Valve – Dispense Device mounted inside removable hopper for small percentages up to 10%
7. Slide Gate – Dispense Device mounted below fixed hoppers to dispense large percentages
8. Auger Screw – Dispense Device mounted inside removable hopper for small percentages up to 10%
9. Air Assembly & Solenoids – Pneumatic assembly for activating pneumatic parts automatically and manually
10. Controller – Central Controller for all settings on the blender
11. Cleaning Airline – Airline for quick and easy cleaning of blender during materials changes
12. Load Cells – Load Cells monitor continuously the weight in the Weigh Bin
13. Load Cell Bracket – Load Cell Bracket for mounting Weigh Bin onto the Load Cells
14. Safety Interlock – Pneumatic and Electrical Safety interlock – stops blender operating if door is opened
15. Weigh Bin – Weigh Bin holds materials as materials are dispensed during a batch and weighed
16. Dump Valve – Pneumatic Valve and Flap to release materials from Weigh Bin when a batch is complete
17. Mix Chamber – Area where materials are blended together after being weighed
18. Mix Blades – Removable Mix Blades to fold the materials together to achieve an effective blend
19. Power and Circuitry Box – Central box for power and support circuitry for controller.
20. Mix Chamber Insert – Stainless Steel removable insert to assist in quick materials cleaning and changes
21. Level Sensor – Sensor to monitor material level in the Mix Chamber, pauses blender when covered and mix
chamber is full, once uncovered signals Controller to begin a new batch of material.
22. Mix Motor – Electric Motor to drive Mix Blades – Note on WSB MB and WSB 100 Series blenders this
motor is a pneumatic Mix Motor
23.
Flow Control Valve – (Optional) – Additional pneumatic slide gate with finger guards to be used when blender
is not mounted directly on the throat of a machine but instead a stand or surge hopper. The Flow Control Valve
ensures material remains inside the Mix Chamber long enough to be mixed efficiently. Automatically controlled
by the blender Controller.

MAGUIRE PRODUCTS, INC.
Edition: August 5, 2014
11
W
EIGH SCALE BLENDER®
Touchscreen Controller and Power Box Parts Key
1. Touch Screen Controller
1.1 Touchscreen
1.2 USB Printer / Software Update Port
1.3 Ethernet Port (RJ-45)
1.4 Power Cord (back panel)
2. Power Box
Left Side Panel
2.1 Alarm Light
2.2 Solenoid Manifold
2.3 Feeder Output (Optional)
2.4 Filter / Regulator
2.5 Touchscreen Interface Connector
2.6 Feeder Output (Optional)
2.7 Blow Off Hose
Right Side Panel
2.8 On / Off Main Power Switch
2.9 Fuse (10 amp)
2.10 Feeder Output (Standard Component 6)
2.11 Feeder Output (Standard Component 5)
2.12 Main Power Cord
Bottom Panel
2.13 24 Volt DC Interlock
2.14 Sensor Cable
2.15 Load Cell Connector
2.16 Mix Motor Output
2.17 AC Output Interlock
Maguire Touchscreen Retrofit Controllers
Also Available from Maguire is the Touchscreen Controller
Retrofit for older Maguire Weigh Scale Blenders. This
controller has all of the features of the Maguire Touchscreen
Controller without the remote power box and easily installs
on existing Weigh Scale Blenders. It is idea for customers
who would like the Touchscreen functionality but already
have the Weigh Scale Blender. This manual also covers the
Touchscreen Retrofit Controller.
For Retrofit Controller specific instructions see page 21.

MAGUIRE PRODUCTS, INC.
Edition: August 6, 2014
12
W
EIGH SCALE BLENDER®
Assembly and Installation Instructions
CAUTION: LOAD CELLS ARE EASILY DAMAGED.
If the FRAME is dropped from TWO FEET, the load cells WILL BE DAMAGED.
THE WARRANTY DOES NOT COVER DAMAGED LOAD CELLS.
The following items have been shipped to you:
1. FRAME and HOPPER assembly: (bolted to skid)
2. CONTROLLER BOX: with the instruction manual.
3. FEEDER BOX: contains a COLOR or ADDITIVE feeder: optional.
4. FLOW CONTROL ASSEMBLY: optional
5. FLOOR STAND or VACUUM TAKEOFF ASSEMBLY: optional
RED INSTRUCTION STICKERS will assist you during assembly.
LIFT HANGERS are available to allow lifting the blender with a strap or chain. Contact Maguire if
you require them.
1A. If your unit is to be MACHINE mounted:
For WSB MB, 100, 200, and 400 series models:
Two ways to do this are suggested ON THE NEXT PAGE:
The LEFT diagram shows the FRAME and SLIDE GATE both drilled with the proper bolt pattern for your
machine and THROUGH BOLTED to your press.
The RIGHT diagram shows only the 10 x 10 steel slide-gate plate drilled for your bolt pattern and bolted to
your press. The FRAME is then bolted to it using the existing 8 x 8 inch bolt pattern holes and bolts
provided. With this method, bolt head clearance holes are required in the poly-pro slide gate plate. This
mounting works well on smaller machines.
For WSB 900 and 1800 series models:
An additional machine mount adaptor plate may be required. If you have ANY DOUBT about the
STABILITY of the unit when bolted directly to your machine throat, please call us for advice.
NOTE: When choosing proper orientation, be sure to retain access to the
controller and weigh chamber, clearance for hinged doors, and access to
removable feeder hoppers.
1B. If your unit is STAND mounted:
A stand is provided and your unit will bolt directly to it. An assembly DIAGRAM is provided on the
following pages.
An air operated FLOW CONTROL ASSEMBLY is provided for dispensing into a container. The purpose
of this unit is to allow time for mixing to occur after each dispense. This flow valve keeps the mix chamber
full to just below the sensor. This assembly bolts directly to the bottom of the Weigh Scale Blender frame.

MAGUIRE PRODUCTS, INC.
Edition: August 5, 2014
13
W
EIGH SCALE BLENDER®

MAGUIRE PRODUCTS, INC.
Edition: August 6, 2014
14
W
EIGH SCALE BLENDER®
"Vacuum Takeoff Assmbly"
With Optional VTA
WSB STANDS
37-1/4 [946]
51-1/4 [1302]
Barrel
VTA
WSB 100/200/400 10-1/8 [257]
AB DC 25-7/8 [657]36 [914] 39-7/8 [1012] 8-1/8 [206]
EF
Gaylord
WSB 900/1800
51-7/8 [1318]63-1/4 [1607] 56 [1422]
VTA
Barrel
Gaylord
36 [914] 8 [203]
8 [203]
43-1/4 [1099]
69-1/4 [1759]
57-1/4 [1454]
16-1/8 [410] 36 [914]
56 [1422]
36 [914] 15 [381]
15 [381]
15 [381]
STAND DIMENSIONS
NOTE:
WSB 100/200/400 VTA Stand shown to scale.
10-1/8 [257]
10-1/8 [257]
8 [203]
8-1/8 [206]
8-1/8 [206]
14-1/8 [359]
14-1/8 [359]
14-1/8 [359]51-7/8 [1318]
39-7/8 [1012]
25-7/8 [657]
16-1/8 [410]
16-1/8 [410]

MAGUIRE PRODUCTS, INC.
Edition: August 5, 2014
15
W
EIGH SCALE BLENDER®
2. Slide the WEIGH BIN into position. It rests behind the clear-hinged access window.
Install with the air cylinder toward you. If bin is already in place, remove any shipping
materials, packing tape or string.
3. Hang the Color and Additive Feeders: (Optional)
a. Lift side latches and fully extend slide assembly. Remove the hopper. Leave slide
extended.
b. Tilting the entire slide assembly, motor end up, insert one corner of hanger cross bar behind
frame corner post.
c. Rotate assembly into place so both ends of cross bar are behind corner posts.
d. Lower into place, bottom edge resting on frame and cross bar properly positioned behind
corner posts.
e.
Re-install hopper. Slide motor forward until latches engage.
4. Connect the Touchscreen to the mounting wing and plug in Touchscreen cable
(7-pin connector).
5. Plug the power cord coming from the power box into a 110-volt power source
(220 volt outside USA). This cord MUST provide the ONLY power source for the
entire system, including the controller. See: WIRING CONSIDERATIONS, next page.
1800 series blenders also require a 240-volt power source for the mix motors.
6. Connect Compressed Air to the unit. About 80 psi (5.5 bar) is recommended (40 psi
for the Micro Blender). Lubricated air is NOT recommended.
NOTE: Micro Blenders should be set to 40 psi (2.7 bar). The
Vertical Valves used in removable hoppers on Micro Blenders
are more accurate at the lower 40 psi pressure setting.
7. Remove all protective paper from the plastic windows.

MAGUIRE PRODUCTS, INC.
Edition: August 6, 2014
16
W
EIGH SCALE BLENDER®
Wiring Considerations
The wiring of your blender is very important to its proper operation. Electronics are very
susceptible to voltage spikes and static charges, both of which are very common in plastics
factories. To MINIMIZE these things, consider the following.
¾The power supply should be solid; a strong supply, not limited by a "just adequate" control
transformer. A source of voltage that comes from a large transformer that supplies a large
portion of the plant is better then a small power supply transformer that is intended to
supply only this device. Power supplies, even though they may be "isolation" transformers,
will still pass all voltage spikes right through. Their small size limits their ability to dampen
RF (Radio Frequency) noise that is often induced into the system from outside sources.
This proves worse then connection to larger central transformers.
¾Avoid running the power supply line along side any heavy power lines. An unshielded power supply
in a raceway along side other heavy power lines will pick up induced RF noise and transfer it into
the WSB steel enclosure causing computer trouble.
¾Long extension cords should be avoided. They also reduce the ability to provide a dampening
effect on spikes and static. The further the equipment is from a substantial power source, the more
susceptible it is to spikes.
¾The CONTROLLER and the WSB frame MUST share the same GROUND PATH. This is why you
MUST plug the controller into the OUTLET that is provided ON THE FRAME.
¾REMOTE SYSTEMS. If you have your controller mounted in a remote location, you will have a
number of power and signal cords running between the frame and the controller. BE SURE that
the LOW VOLTAGE lines are NOT BUNDLED to the HIGH VOLTAGE lines and keep them away
from other nearby electrical lines.
LOW VOLTAGE lines are: Load Cell cable, Level Sensor cord,
Air Solenoid cable, and Printer and communication cables.
HIGH VOLTAGE lines are: Mixer motor cable, Feeder motors,
and MAIN POWER line.
Keep these sets of cables SEPARATED.
¾VACUUM LOADER CONVEYING LINES. Keep them away from all electrical lines, particularly the
Load Cell lines. Conveying plastic produces extreme static sources. A power supply line, even in
conduit, that runs next to a vacuum line, can introduce extreme static pulses into the processor.
Keep conveying lines SEPARATED from electrical supply lines.
¾
We use many internal tooth "STAR" washers in assembling the WSB to ensure good ground
between painted parts. Do not remove them.
PROCEED TO: CHECK OUT PROCEDURE NEXT PAGE

MAGUIRE PRODUCTS, INC.
Edition: August 5, 2014
17
W
EIGH SCALE BLENDER®
Check Out Procedure
As you go through this procedure, if WHAT SHOULD HAPPEN, doesn't happen, see next section,
DIAGNOSTICS, for what to check.
MB/100/200 series models (3K load cells), display all weights in 1/10 grams (xxxx.x).
400/900/1800 series models (10K load cells) display weights in FULL grams, NO decimal point
(xxxxx). On this page we show all weights with NO decimal point.
Start with NO MATERIAL in any hoppers.
Be sure an AIR SUPPLY is connected.
Turn POWER SWITCH OFF (on side of Power Box).
PROCEDURE: WHAT SHOULD HAPPEN:
1. POWER UP CONTROLLER / Blender
PLUG IN CONTROLLER Nothing should happen.
Air pressure should be holding ALL valves CLOSED.
This means all air cylinders are extended. If any slide gate or flap is
open, air lines are reversed.
If a FLOW CONTROL VALVE is installed, check it.
TURN POWER ON Display should briefly show a screen: POWER-ON SELF-TEST
This screen with display the following information:
Model, Serial Number (SN), Software,
Firmware, Time, Date.
Then the Screen will display the Main
Touchscreen view, which includes a
“Main Display” displaying the actual
weight of material in the bin. This
number should be zero, plus or minus
several grams ( 20) to (-20).
AT THIS POINT
Be sure the model number that displays matches your blender model
number. If this is not the case see two sections ahead, SELECTING
CORRECT MODEL.
TOUCH WEIGH BIN VERY LIGHTLY
Display should update the weight every second reflecting the light
pressure that you are exerting on the bin.
2. OPERATE DISPENSE DEVICES
PRESS
OPTIONS
Display will say ENTER PASSWORD
PRESS
then, press Enter button
This enters the PROGRAM mode. Display will show a menu of
options.
PRESS
MANUAL OPERATION
Display will say OPERATE DEVICES
PRESS
MAT 1
Device number 1 will operate.
Press "1" repeatedly to observe operation.
PRESS
MAT 2
Device number 2 will operate.
Press "2" repeatedly to observe operation.
REPEAT THIS SEQUENCE
For each dispense valve on your WEIGH SCALE BLENDER.
Up to 12 outputs are possible numbered MAT 1 through to MAT 12.
Only those connected to devices will operate.

MAGUIRE PRODUCTS, INC.
Edition: August 6, 2014
18
W
EIGH SCALE BLENDER®
3. NOTE HOPPER NUMBERS
AT THIS POINT
NOTE which component NUMBER is assigned to each hopper.
You will want to know each hopper's correct component number.
FOR WSB 940 & WSB
1840 SERIES: On 9000 and 18000 gram, FOUR hopper compartment systems, facing the
Controller side of the blender:
Device 1 is the NEAR hopper, 2 the FAR hopper, 3 the LEFT CENTER, and 4 the
RIGHT CENTER hopper.
FOR WSB 100, 200 &
400 SERIES:
On 1000, 2000, and 4000 gram, FOUR hopper systems facing the Controller side of
the blender:
Devices 1, 2, 3, and 4 are counter-clockwise starting with far left corner hopper.
FOR WSB 200, 400, 900
& 1800 SERIES: On 2000, 4000, 9000 and 18000 gram SIX hopper systems facing the Controller side
of the blender:
Devices 1, 2, 3, 4, 7, and 8 are counter-clockwise starting with far left corner hopper.
FOR WSB 100, 200,
400, 900 & 1800
SERIES:
On the blender Controller:
Device 5 is the LEFT Panel-front OUTLET.
Device 6 is the RIGHT Panel-front OUTLET.
4. OPERATE OTHER DEVICES
PRESS
DUMP
The weigh bin air solenoid will operate.
The weigh bin dump valve will open.
Press, "DUMP" repeatedly to observe operation.
PRESS
MIX
This key controls the mix motor outlet on the side of the controller.
The mixer motor will run.
Mix blade turns clockwise facing the motor shaft or 270º on Pneumatic Mix Motors.
Mixer switch must be down; timed position.
PRESS
HOLD
The Flow Control Valve will operate.
(Under the mix chamber - this device is optional)
PRESS
ALARM
The Strobe light and Beeper will operate.
Display will show ALARM: ON
PRESS
Press twice, to return to normal mode.
Verify normal mode by observing that the display is back to the Main Touchscreen
display.
If you have made it this far, congratulations. You have done well.
The load cells and controller are functioning properly.
LOAD CELL CALIBRATION – SKIP TO PAGE 27

MAGUIRE PRODUCTS, INC.
Edition: August 5, 2014
19
W
EIGH SCALE BLENDER®
Check Out Procedure Diagnostics
If display fails to come on at all:
Check for power at outlet.
Check the 10 amp fuse located on the right side of the Power Box.
Possible model numbers are:
WMB, 140, 140R, 220, 240, 240R, 420, 440, 440R, 940, 1840, WSB 3000
If model number is not correct for you unit:
see the next page, SELECTING CORRECT MODEL.
If display shows randomly drifting numbers:
check to see load cells are plugged in.
If display shows about (- 1250.0) or ( -4500):
check that the weigh bin is in place properly.
If display is steady but not near zero:
An over stressed load cell will display a permanently high or low reading. Recalibrate load
cells; next section.
If there is no response from the display when the bin is touched:
check for damaged wires to load cells.
check that load cell plug screws are secure.
If response is not sensitive or does not return to its start point:
check for interference around weigh bin.
If pressing OPTIONS does not display ENTER PASSWORD screen:
you are not in the normal power-up mode or the touchscreen doesn't work. Normal mode
is indicated by the ABSENCE of MANUAL or PROGRAM at the lower right of the display.
If display says INVALID after entering the password number:
you pressed the wrong keys or the password number has been changed and it is no longer
22222. Call us for help.
If an air solenoid does not operate:
check the 10 amp fuse.
check solenoid cable connected properly and fully seated.
check mix chamber door closed, safety interlock engaged.
If a slide or dump valve does not open:
check the air supply and regulator adjustment:
80 psi (5.5 bar) recommended.
check for proper air line connection to cylinder.
If an auger feeder motor does not run:
check the 10 amp fuse.
check that the motor is plugged into the proper outlet.
check for faulty motor by plugging it into a known source of 110 volt A.C. power (240 volt
outside U.S.).

MAGUIRE PRODUCTS, INC.
Edition: August 6, 2014
20
W
EIGH SCALE BLENDER®
Selecting the Correct Model
Controllers are programmed to control all sizes of Weigh Scale Blenders.
The MODEL number that your unit is set for will be displayed in the top left of the Touchscreen.
The possible models are:
Blender Model Blender Display Code Batch Weight (Grams) Weigh Bin Dimensions Load Cell Rating
MB MB 400 5” x 5” x 5” High 1 @ 3Kg
140 / 140R 140 / 14R 1000 10” x 6” x 6” High 1 @ 3Kg
220 220 2000 10” x 10” x 7” High 2 @ 3 Kg
240 / 240R / 260 240/24R 2000 10” x 10” x 7” High 2 @ 3 Kg
420 420 4000 10” x 10” x 10” High 2 @ 10 Kg
440 / 440R / 460 440/44R 4000 10” x 10” x 10” High 2 @ 10 Kg
940 / 960 940 9000 16” x 16” x 12” High 2 @ 10 Kg
1840 / 1860 1840 18000 16” x 16” x 17” High 2 @ 20 Kg
“R” Models have 2 removable hoppers
The addition of feeders will change the last digit of the model number.
This digit can be ignored for selecting the correct Model.
400, 1000 and 2000 gram systems with 3 Kg load cells; weights are displayed in tenths of grams
(xxxx.x).
4000, 9000, and 18000 gram systems with 10 or 20 Kg load cells; weights are displayed in full
grams (xxxxx).
If your unit is NOT set correctly to match the hardware you have, you must change it. To do so:
Turn power on. From the NORMAL mode:
Model Setup Keypad Sequence:
Press
OPTIONS
Display will say: ENTER PASSWORD
Press
then, press Enter
Display will say:
MODEL SELECTION
Current Model: WSB 24R
Or whatever model it is currently set for.
Press The “Select Model”
Dropdown Menu Scroll through all model sizes.
When the model you want is displayed, then:
Press Your Model, then press the
“Select” button. Controller will reset and restart as the system you
have selected.
When switching models, all parameter table information is lost and the new "default" information
for this model is loaded from ROM. If you should be in any doubt as to which is the correct model
you should refer to the Blender Identification Plate located on the frame of the blender.
Table of contents
Other Maguire Products Controllers manuals
Popular Controllers manuals by other brands
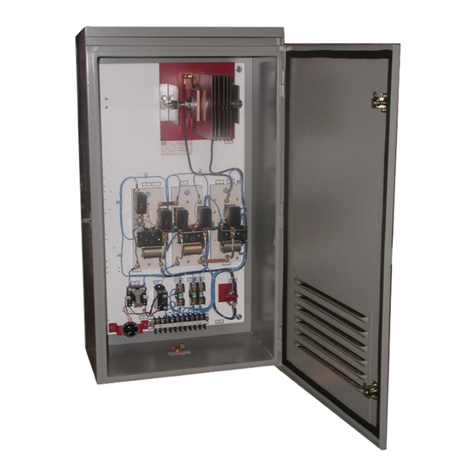
Hubbell
Hubbell Euclid Lifting Magnet Controller 4291 Specifications
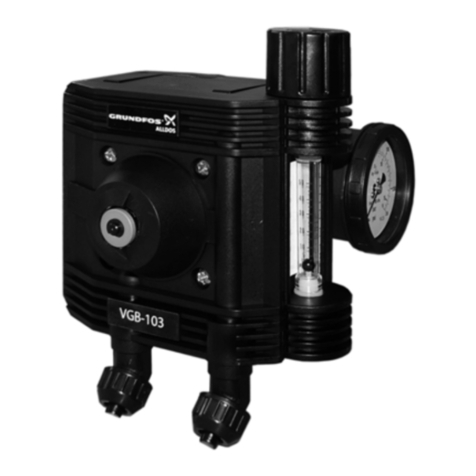
Grundfos
Grundfos Alldos Vaccuperm VGB-103 Installation and operating instructions
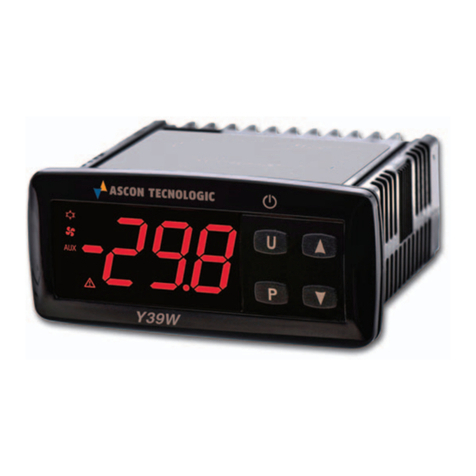
Ascon tecnologic
Ascon tecnologic Y39W operating instructions
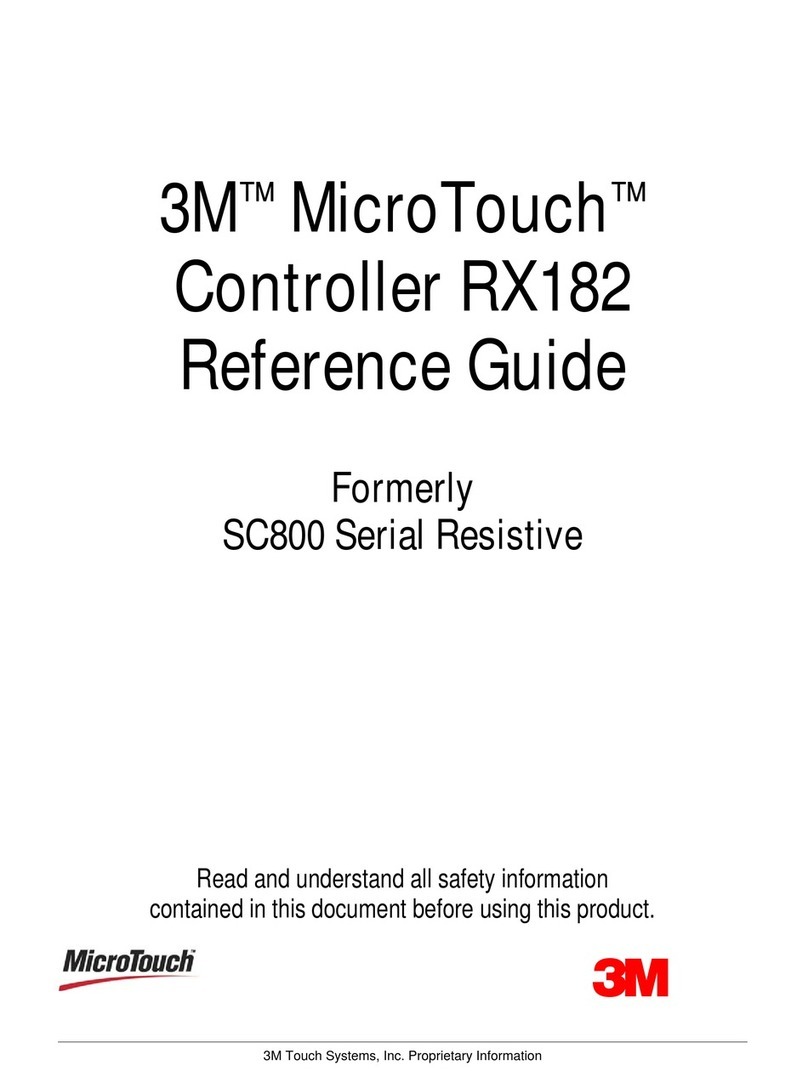
3M
3M Touch Screen Controller RX182 reference guide

Mitsubishi Electric
Mitsubishi Electric FX3S-30MT/ES-2AD Hardware manual

Arbor Technology
Arbor Technology ELIT-1270 user manual