Makita Maktec MT912 Manual

Model No.
Description
MT912
Die Grinder L
H
W
Dimensions: mm (")
Width (W)
Height (H)
Length (L) 350 (13-3/4)
75 (2-15/16)
75 (2-15/16)
Wrench ..................................... 2
Collet cone 6mm or 1/4” .......... 1
Insulation cover ........................ 1 (for some countries only)
PRODUCT
CONCEPT AND MAIN APPLICATIONS
P 1/ 1
Specification
Standard equipment
Optional accessories
Note: The standard equipment for the tool shown above may vary by country.
Collet cones (3mm, 6mm, 1/8”, 1/4”)
Continuous Rating (W)
Voltage (V) Cycle (Hz) Input Output
140
Max. Output (W)
110
220
240
4.6
2.1
50/60
50/60
50/60
480
480
480
380
380
140 380120 4.2 50/60 ---
380
Current (A)
140
140
2.3
230 50/60 480 3801402.2
Model MT912 has been developed as the cosmetic change model of
maktec die grinder MT911.
Its main features are:
•Industrial performance and durability at less expense
•Anti-slip ribs on motor housing for higher maneuverability and
better control
Collet size*1
*1: 3mm and 1/8” shank collets can be used by changing Collet cone.
*2: Max wheel diameter for China is the same of 20mm (13/16”).
*3: with Collet nut, Collet cone
6mm or 1/4”
Max wheel diameter*2: mm (")
33,000
20 (13/16)
2.0 (6.6)
1.4 (3.1)
Weight according to
EPTA-Procedure 01/2003*3: kg (lbs)
Double insulationProtection against electric shock
No load speed: min.ˉ¹=rpm
Power supply cord: m (ft)
TECHNICAL INFORMATION

P /1
Repair
[1] NECESSARY REPAIRING TOOLS
CAUTION: Repair the machine in accordance with “Instruction manual” or “Safety instructions”.
Code No. Description Use for
1R031 Bearing setting pipe 28-20.2 mounting Ball bearing 6001ZZ to Barrel
1R045 Gear extractor (large) removing/mounting Ball bearing 6001ZZ from/to Spindle
1R291 Retaining ring S & R pliers removing/mounting Retaining ring S-12 from/to Spindle
1R232 Pipe 30 supporting Barrel when removing Spindle
1R247 Round bar for Arbor 20-100 removing Ball bearing 629ZZ from Barrel
1R250 Round bar for Arbor 26-100 mounting Ball bearing 629ZZ to Barrel
1R269 Bearing extractor removing Ball bearing 607ZZ from Armature
1R282 Round bar for Arbor 8-50 •attaching to 1R045 when mounting Ball bearing 6001ZZ to Spindle
•attaching to arbor press when removing Armature from Gear housing cover
784416-4 Socket bit 17-55 removing/mounting Coupling
[2] LUBRICATION
Apply Lubricant VG100 to the following portions designated with the black triangle to protect parts and product from
unusual abrasion.
Fig. 1
Item No.
4 Felt ring 17
17
4
17
O ring 26
Bearing retainer
Spindle
Barrel
Coupling
Ball bearing 629ZZ
Flat washer 22
Whole portion
Whole portion
enough to be absorbed
in Felt ring 17 entirely
a little
Description AmountPortion to lubricate

P /1
Repair
[3] DISASSEMBLY/ASSEMBLY
[3] -1. Barrel Section
DISASSEMBLING
(1) Remove Insulation cover from Barrel if the cover is used.
(2) Disassemble Coupling and Bearing retainer from Barrel as drawn in Fig. 2.
2. While holding Spindle with Wrench
13, remove Collet nut 6 with another
Wrench 13 by turning it counter-
clockwise.
1. Unscrew four 4x25 Tapping screws,
then separate Barrel section from
Motor housing.
Note: Flat washer 22 between
Gear housing cover and
Barrel may be removed
at this time. Do not lose it.
3. Remove Collet cone 6.0
from Spindle.
4. Remove Spacer from Coupling. And then
remove Flat washer 22 from Barrel if the
washer is still in Barrel.
5. While holding Spindle with Wrench 13, remove Coupling
from Barrel with Impact driver and 784416-4 by turning it
counterclockwise.
6. Fix Barrel in Vise. Then remove Bearing
retainer with Adjustable wrench by
turning it counterclockwise
7. Remove Felt ring 17 and Flat washer 18 from Barrel.
Wrench 13
Spindle
Collet nut 6
Collet cone
784416-4
Coupling
Barrel
Bearing
retainer
Wrench 13
Fig. 2
Flat washer 18
Felt ring 17
Vise
Note: Felt ring 17 may be removed
with Bearing retainer in the
previous step.
Barrel
Barrel
Barrel
Gear housing
cover
Spacer
Coupling
Flat washer 22
Adjustable
wrench

Repair
DISASSEMBLING
(3) Spindle section is now removed from Barrel as drawn in Fig. 3.
3. Remove Retaining ring S-12 with 1R291 from Spindle. 4. Remove Ball bearing 6001ZZ with 1R045
from Spindle.
1. Put Barrel on 1R232. And then remove Spindle by pressing
1R282 with Arbor press.
2. Remove Ball bearing 629ZZ from Barrel
by pressing 1R247 with arbor press.
Fig. 3
1R232
Ball bearing
6001Z
Ball bearing 629Z
Spindle
1R282
Ball bearing
6001Z
Spindle
Retaining
ring S-12
Ball bearing
629Z
Barrel
1R247
[3] DISASSEMBLY/ASSEMBLY
[3] -1. Barrel Section (cont.)
1R291
1R045
P 4/11

1R250
P 5/11
Repair
ASSEMBLING
(1) Assemble Spindle section as drawn in Fig. 4.
(2) Assemble Ball bearing 629ZZ to Barrel, and then assemble the Spindle section to Barrel. (Fig. 5)
(3) Assemble Flat washer 18, Felt ring 17 and Bearing retainer to Barrel as drawn in Fig. 6.
Fig. 4
Fig. 5
Ball bearing
6001ZZ
Ball bearing
6001Z
1R045
Spindle
1. Insert 1R282 into the hole of Spindle. Then mount
Ball bearing 6001ZZ to Spindle with 1R045.
1. Assemble Ball bearing 629ZZ to Barrel
by press-fitting 1R250.
2. While supporting Ball bearing 629ZZ of Barrel with 1R250,
assemble Spindle section to Barrel by press-fitting with 1R031.
1R282 1R282
Retaining
ring S-12
2. Install Retaining ring S-12 to Spindle with 1R291
in order to secure Ball bearing 6001ZZ.
Ball bearing 629Z
1R250
Ball bearing
629ZZ
1R031
[3] DISASSEMBLY/ASSEMBLY
[3] -1. Barrel Section (cont.)
Fig. 6
Flat washer 18
3. Fix barrel with Vise, and then fasten Bearing retainer to
Barrel by turning it clockwise with Adjustable wrench.
Felt ring 17
Bearing retainer
2. Stuff Felt ring 17
into Bearing
retainer.
5. Mount Flat washer 22 to Barrel.
1. Mount Flat washer 18 to Barrel
by passing through Spindle.
Bearing
retainer
Spindle
Flat washer 22
784416-4
Wrench 13
4. While holding Spindle with Wrench 13, mount Coupling
with Impact driver and 784416-4 by turning it clockwise.
Coupling

P 6/11
Repair
ASSEMBLING
(4) Assemble Barrel to Motor housing. (Fig. 7)
Note in Assembling: When Barrel section is assembled to Motor housing, Rotation direction mark of Barrel
must be positioned on the same side of Switch knob.
(5) Mount Insulation cover to Barrel if the cover is used. (Fig. 8)
Spindle
Rotation direction mark
Motor housing
Switch knob
Barrel
Name plate
Fig. 7
[3] DISASSEMBLY/ASSEMBLY
[3] -1. Barrel Section (cont.)
Insulation coverConcave portion
Concave portion
Protrusion
Protrusion
While fitting the protrusion of Insulation cover to the concave portion on Barrel,
mount Insulation cover to Barrel.
Switch knob
Barrel
Fig. 8
[3] -2. Armature
DISASSEMBLING
1. Remove Brush holder caps
and Carbon brushes.
Brush holder caps
Carbon brushes
2. Separate Barrel section from
Motor housing.
3. Remove Armature together with Gear
housing cover from Motor housing.
4. Remove Spacer from
Coupling on Armature.
5. While holding Armature by hand, remove
Coupling with Impact driver and 784416-4
by turning it counterclockwise.
6. Disassemble Armature from Gear
housing cover by pressing Armature
shaft with 1R282 and Arbor press.
Spacer
Coupling
784416-4
1R282
Coupling
(1) Disassemble Armature as drawn in Fig. 9.
Fig. 9
Gear housing cover
Motor housing
Armature

P 7/ 11
Repair
[3] DISASSEMBLY/ASSEMBLY
[3] -2. Armature (cont.)
[3] -3. Field
DISASSEMBLING
DISASSEMBLING
1. Remove Labyrinth
rubber ring 19 by hand.
2. Remove Ball bearing 629ZZ with 1R269.
And then, remove Insulation washer.
Fig. 10
(1) Remove Brush holder caps and Carbon brushes. (Refer to Fig. 9)
(2) Disassemble Barrel section and Armature together with Gear housing cover. (Refer to Fig. 9)
(3) Disassemble Field from Motor housing as drawn in Fig. 11.
Fig. 11
Labyrinth
rubber ring 19
Ball bearing
629ZZ
1. Remove Baffle plate,
then unscrew two
4x70 Tapping screws.
2. Install two M4x25 Tapping screws in the holes on two diagonal corners of
Motor housing. Then, remove Field from Motor housing by alternately
tapping the screw heads.
Note: Do not tap the diagonal corners directly because the inlaid portion
near the corners is fragile.
Insulation
washer
1R269
M4x25 Tapping screws
4x70 Tapping
screws
Baffle plate
Field
(2) Disassemble Armature section. (Fig. 10)
Assemble Armature section by reversing the disassembly procedure. (Refer to Figs. 10 and 9)
Assemble Field by reversing the disassembly procedure. (Refer to Figs. 11 and 9)
ASSEMBLING
ASSEMBLING

Circuit diagram
P 8/ 11
Color index of lead wires' sheath
Connect Brush holder's lead wire (black) from
Field lead wire (black) to Brush holder of
maktec logo side.
Switch
Terminal
block
Motor housing
Rear cover
maktec
logo side
Field Field
Noise suppressor is not used
for some countries.
Noise suppressor's lead wire is white in
case of that of two lead wire type is used.
(without grounding lead wire).
Correct Wrong
Spindle rotates in the inverse direction
to the indication on Barrel.
Fig. R Fig. F
Fig. D-1
maktec logo
maktec logo
Field Lead Wire (black) Field Lead Wire (white)
Brush Holder's
Lead Wire (black) Brush Holder's
Lead Wire (black)
Grounding terminal of
Noise suppressor
Black
White
Blue
Brown
Lead wire (white) is used
for some countries instead
of the lead wire (blue).
Lead wire (black) is used
for some countries instead
of the lead wire (brown).
Clear
Noise
suppressor
Motor housing Motor housing

Wiring diagram
P 9/ 11
Motor housing
Motor housing
Support
Field lead wire
(white) for connecting
to Switch
Field lead wire
(black) for connecting
to Terminal block
Support
Motor housing of Rear cover side
Noise suppressor
Grounding terminal of
Noise suppressor
Pass Field lead wires (black and white) through the holes of Motor housing.
Insert the grounding terminal of noise suppressor's lead wire deeply into the hole of Motor housing.
Install Noise suppressor to the space painted with gray color in Fig. D-2.
Pass Field lead wires (black and white) through the groove of Support while tightening them between
Motor housing and Support.
Groove of Support
Groove of
Support
Field lead wire (white)
Field lead wire
(black)
to Switch
to Terminal block
Tighten Field lead wires between
Motor housing and Support.
Fig. D-2
Fig. D-3

Wiring diagram
P 10/ 11
Support section
Fig. D-5
Left side view
Lead wire (blue or white)
of Power supply cord
Connecting terminal
Connect Connecting terminal to
Switch as follows.
* Screw hole side: Top
* Lead wire side: Bottom
Terminal block
Switch
Fig. D-4
Install Terminal block and Switch to Support. (Fig. D-4)
Switch
Terminal block
Support
Switch
Terminal block
Noise suppressor
Left
Top
Bottom
Lead wire (brown or black)
of Power supply cord

Wiring diagram
P 11/ 11
Switch
Switch
Terminal block
Terminal block
Lead wire holder
Field lead wire
(black)
Field lead wire
(white)
Noise
suppressor
Noise suppressor
Noise suppressor's
lead wire
(to Terminal block)
Noise suppressor's
lead wire
(to switch)
Top
Bottom
Right
Fig. D-6
Right side view
Connecting terminal
Connect Connecting terminal to
Switch as follows.
* Screw hole side: Top
* Lead wire side: Bottom
Fix the following lead wires
with Lead wire holder.
* Field lead wire (black)
* Noise suppressor's lead wire
for connecting to Terminal block
Support section
Table of contents
Other Makita Grinder manuals
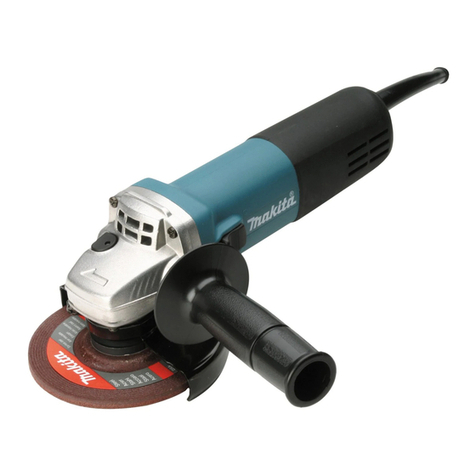
Makita
Makita 9556NB User manual

Makita
Makita DGA520 User manual

Makita
Makita 9557NB2 User manual

Makita
Makita GA4030K User manual

Makita
Makita MGA700 User manual
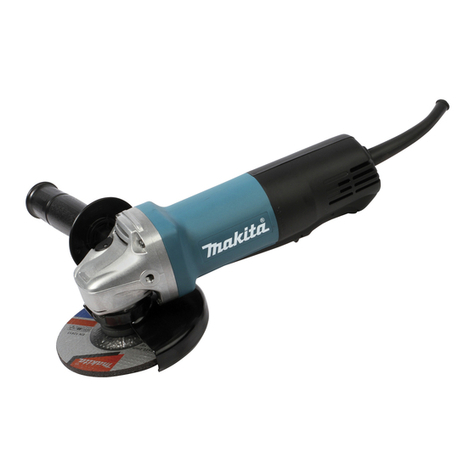
Makita
Makita 9558PBGYK User manual

Makita
Makita 9005B User manual
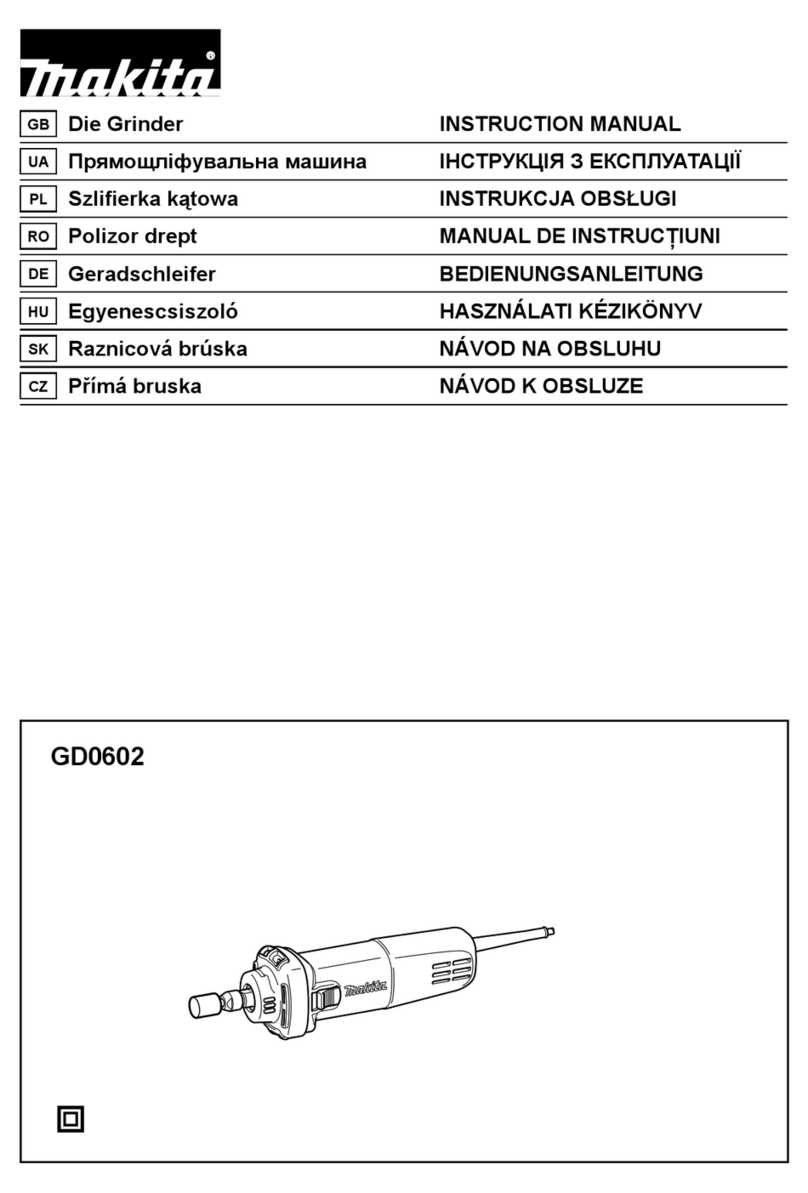
Makita
Makita GD0602 User manual
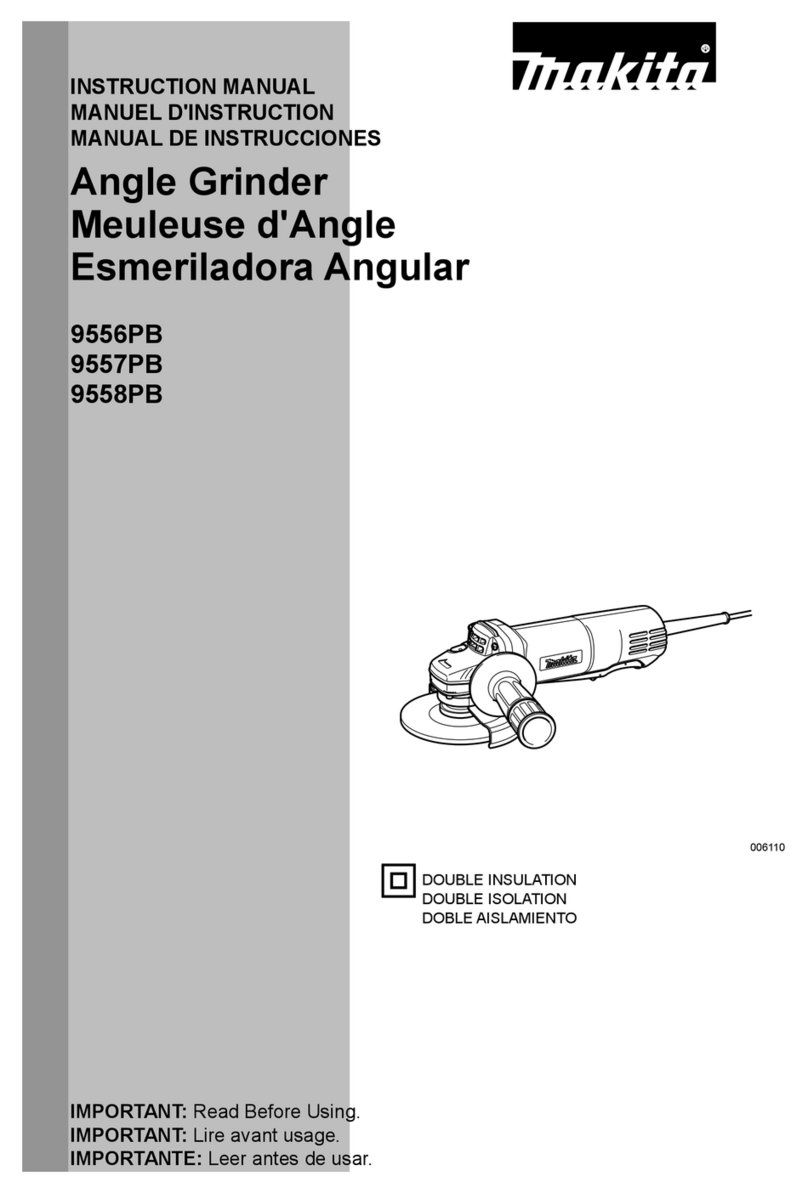
Makita
Makita 9556PB User manual
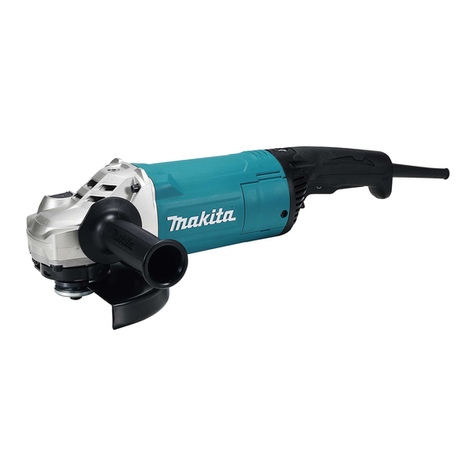
Makita
Makita GA7080 User manual

Makita
Makita 9560C User manual
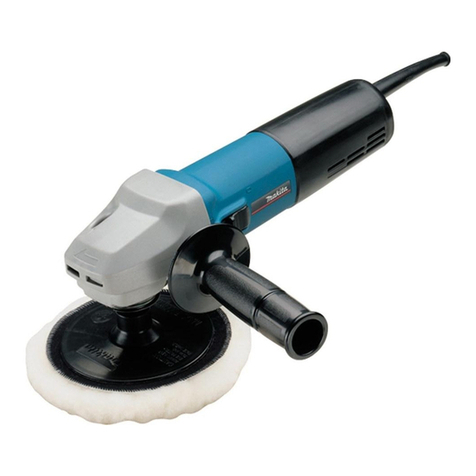
Makita
Makita 9565CLR User manual
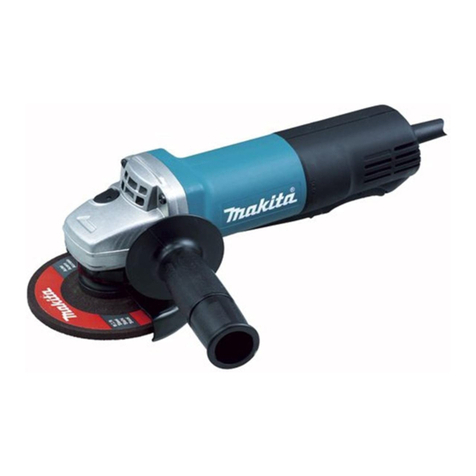
Makita
Makita 9557PBK User manual
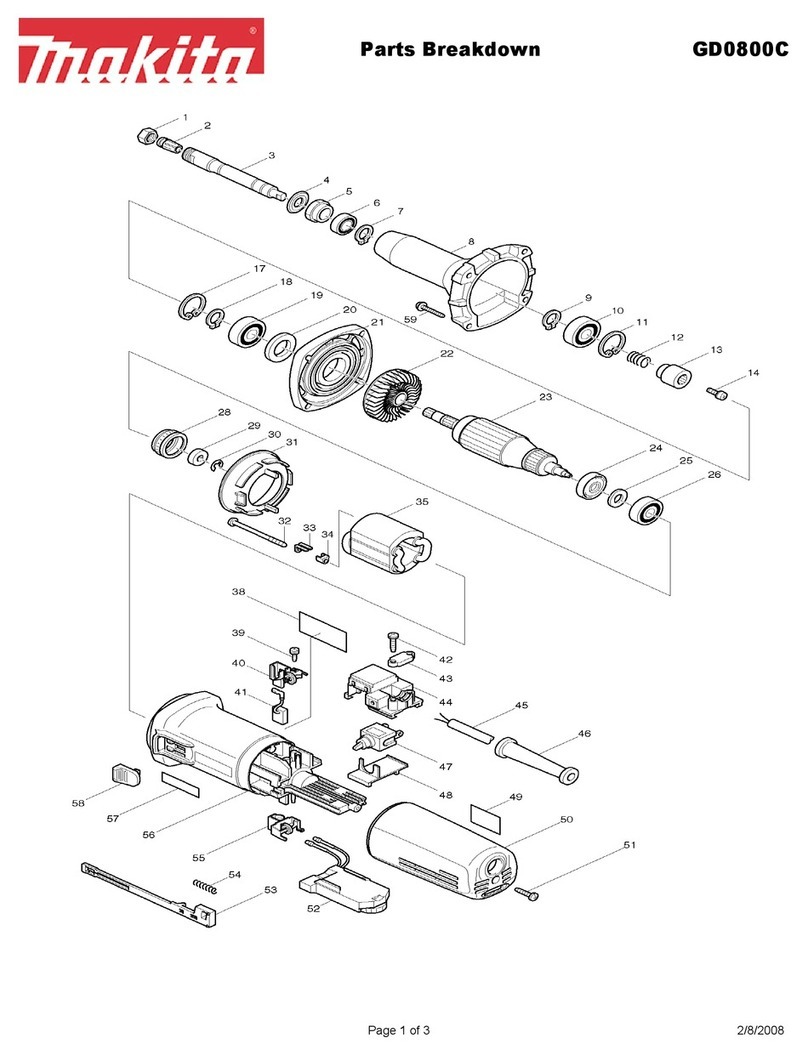
Makita
Makita GD0800C Quick start guide
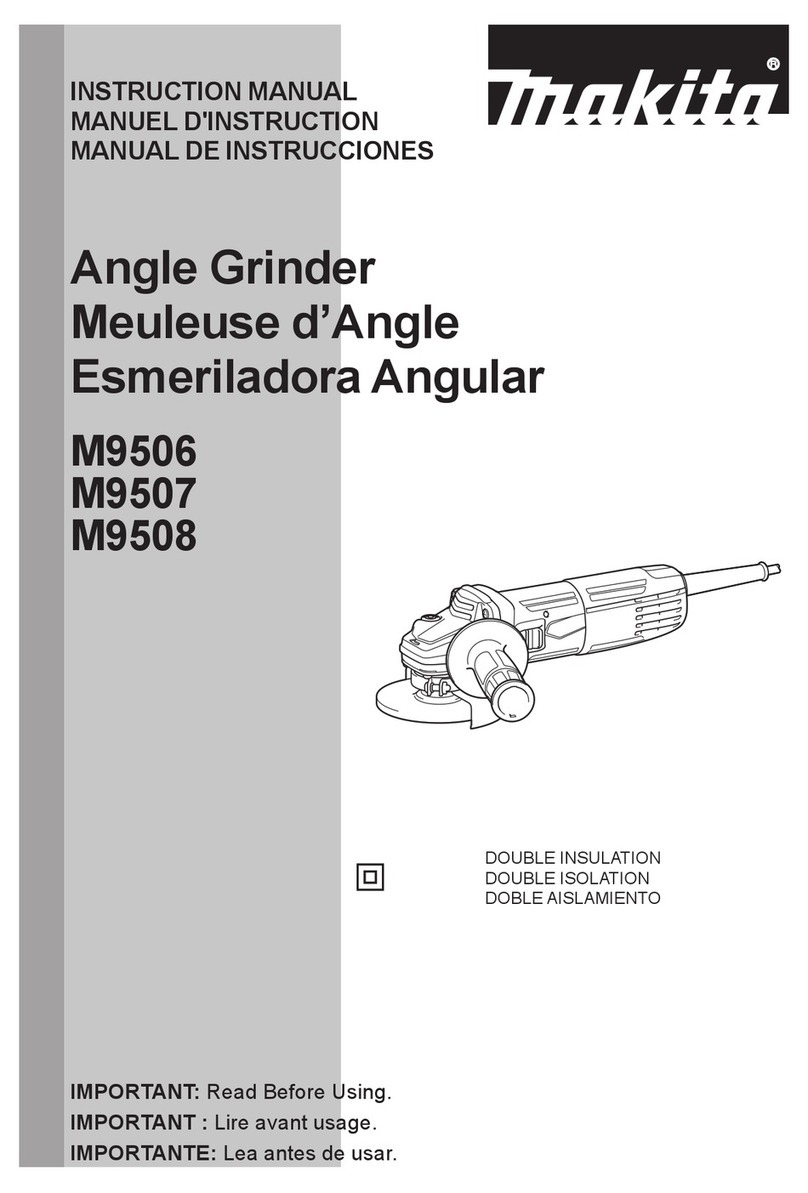
Makita
Makita M9508 User manual
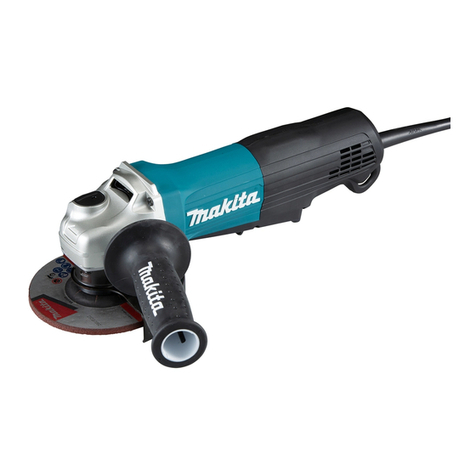
Makita
Makita GA4051R User manual
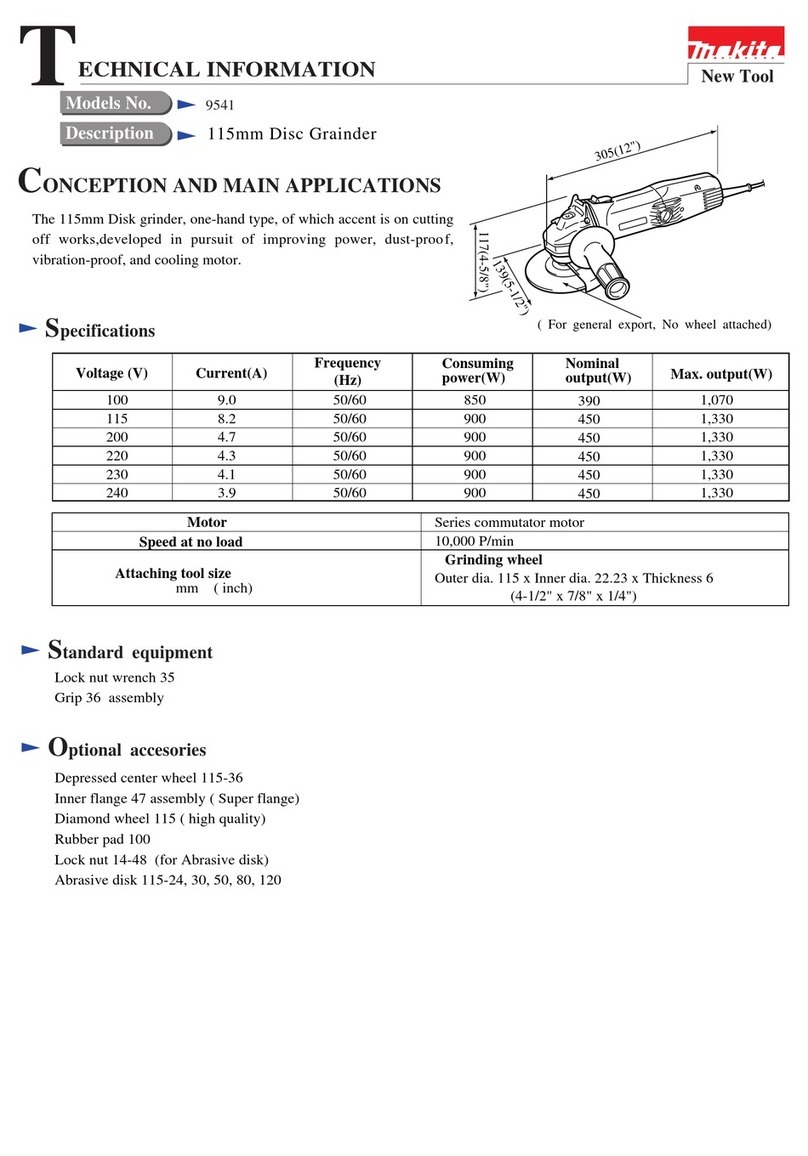
Makita
Makita 9541 User manual

Makita
Makita 9561CR User manual
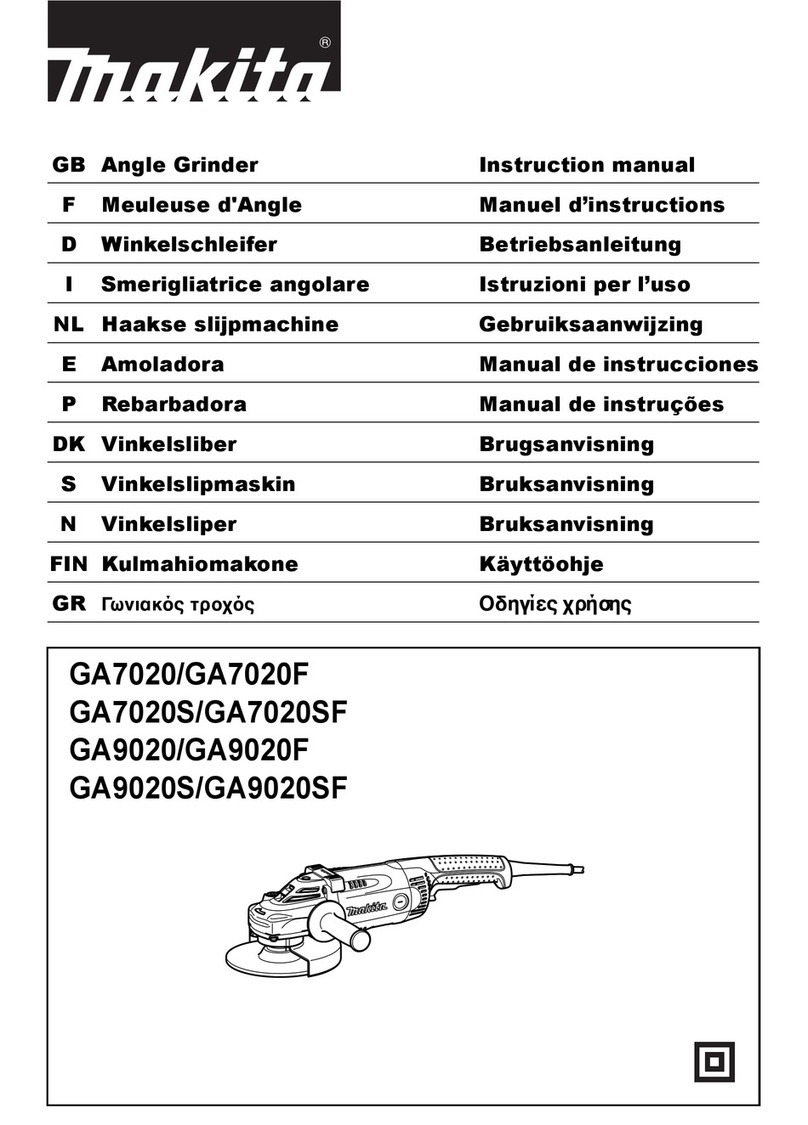
Makita
Makita GA7020 User manual
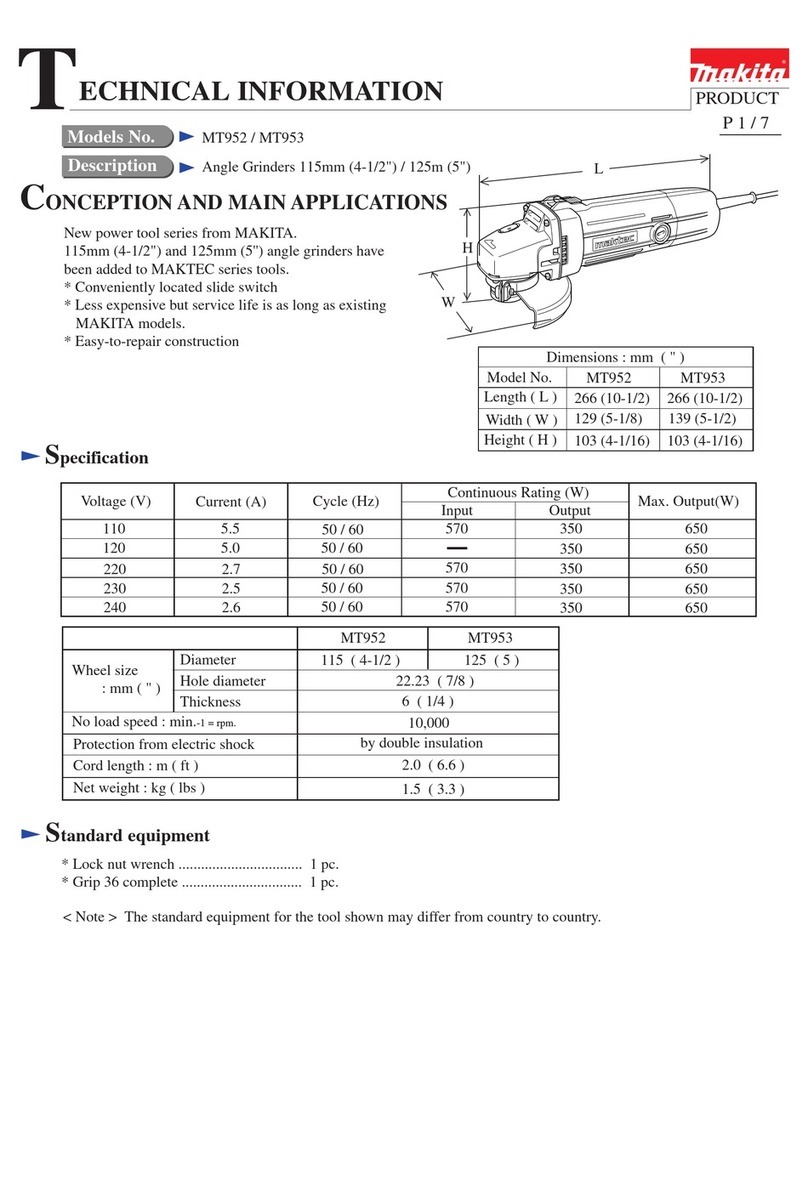
Makita
Makita MT952 Manual