Matrix JF72553B User manual

Art.-Nr.: 59695035
JF72553B
Traduction de la notice originale
Banc de scie 10 po
F
Original instructions
10" Table Saw
GB

2
E
K
R
M
N
FIG.2
FIG.1
HI J
C
F
G
L
P
B
AD
O
Q

3
FIG.10
FIG.9
FIG.8FIG.7
FIG.6FIG.5
FIG.4
FIG.3
45
45
2
7
6
2
1
3
1
2
A
C
D
E
E
D
B
B
C
1
2
3
4
U
X
U
Y

4
FIG.18
FIG.17
FIG.16FIG.15
FIG.14FIG.13
FIG.12
FIG.11
LOCK
KNOB
MITRE
GAUGE
FRONT
RAIL
LOCKING
HANDLE
BLADE
RIP
FENCE
2i n.
MARK
SCALE
SCALE
INDICATOR
2i n.
REAR LIP
RIPF ENCE
SAW TABLE
RIPF ENCE
LEVER
BEVEL
INDICATOR SCREW
SCREWDRIVER
TO LOCKT O UNLOCK
BEVEL LOCK
LEVER
SWITCH ON SWITCH OFF
SWITCH KEY REMOVED
1
8
9
11
10
2
CREUX

5
FIG.26
FIG.25
FIG.24
90° POSITIVE
STOP
ADJUSTMENT
SCREW
45° POSITIVE
STOP
ADJUSTMENT
SCREW
LOCKING
HANDLE
CLAMP
SCREW
RIP FENCE
SAW
BLADE
RIP
FENCE
SCREWS
FIG.23
N
JUU
FIG.22
UU
FIG.21
N
FIG.20
FIG.19

6
2
3
4
1
6
11
10
13
12
14 15
8
5
7
9

7
WARNING! Read and understand
all instructions. Failure to follow all
instructions listed below may result in
serious personal injury.
WARNING! When using electric tools,
machines or equipment, basic safety
precautions should always be followed to
reduce the risk of re, electric shock, and
personal injury. Completely read the
manual before proceeding to use this
tool. KEEP THESE INSTRUCTIONS.
IMPORTANT SAFETY INSTRUCTIONS
WORK AREA
1. Keep your work area clean and well lit.
Cluttered benches and dark areas invite
accidents.
2. Do not operate power tools in explosive
atmospheres, such as in the presence of
ammable liquids, gases, or dust. Power tools
create sparks which may ignite the dust or fumes.
3. Keep bystanders, children, and visitors away
while operating a power tool. Distractions can
cause you to lose control. Protect others in the
work area from debris such as chips and sparks.
Provide barriers or shields as needed.
ELECTRICAL SAFETY
4. Grounded tools must be plugged into an
outlet that is properly installed and grounded.
Grounding provides a low-resistance path
to carry electricity to ground away from the
operator, should th e tool malfunction electrically.
Do not remove the grounding prong from the
plug nor alter the plug in any way.
If in doubt as to whether the outlet is properly
grounded according to code, check with a
qualied electrician.
5. Avoid body contact with grounded
surfaces such as pipes, heaters, ranges and
refrigerators. The risk of electric shock is
increased if your body is grounded.
6. Don’t expose power tools to rain or wet
conditions. Water entering a power tool
will increase the risk of electric shock.
7. Handle the cord carefully.Never use the
cord to carry the tools or pull the plug from an
outlet. Keep cord away from heat, oil, sharp
edges or moving parts. Replace damaged
cords immediately. Damaged cords increase the
risk of electric shock.
8. When operating a power tool outside, use
outdoor extensions cord marked “W-A” or “W”.
These cords are rated for outdoor use and reduce
the risk of electric shock.
PERSONAL SAFETY
9. Stay alert, watch what you are doing, and
use common sense when operating a power
tool. Do not use tool while tired or under the
inuence of drugs, alcohol, or medication. A
moment of inattention while operating power
tools may result in serious personal injury.
10. Dress properly. Do not wear loose clothing
or jewelry. Contain long hair. Keep your hair,
clothing,and gloves away from moving parts.
Loose clothes, jewelry, or long hair can be caught
in moving parts.
11. Avoid accidental starting. Be sure switch is
o before plugging in. Carrying tools with your
nger on the switch or plugging in tools with the
switch on invites accidents.
12. Remove adjusting keys before turning the
tool on. A wrench or a key that is left attached to
a rotating part of the tool may result in personal
injury.
13. Do not overreach. Keep proper footing and
balance at all times. Proper footing and balance
GB

8
enables better control of the tool in unexpected
situations.
14. Use safety equipment. Always wear eye
protection. Dust mask, non-skid safety shoes,
hard hat, or hearing protection must be used for
appropriate conditions.
TOOL USE AND CARE
15. Use clamps or other practical way to
secure and support the work piece to a stable
platform. Holding the work by hand or against
your body is unstable and may lead to loss of
control.
16. Do not force tool. Use the correct tool for
your application. The correct tool will do the
job better and safer at the rate for which it is
designed.
17. Do not use tool if switch does not turn it on
or o. Any tool that cannot be controlled with
the switch is dangerous and must be repaired.
18. Disconnect the plug from the power source
before making any adjustments, changing
accessories, or storing the tool. Such preventive
safety measures reduce the risk of starting the
tool accidentally.
19. Store idle tools out of reach of children and
other untrained persons. Tools are dangerous
in the hands of untrained users.
20. Maintain tools with care. Keep cutting tools
sharp and clean. Properly maintained tools with
sharp cutting edges are less likely to bind and are
easier to control. Do not use a damaged tool.Tag
damaged tools“Do not use”until repaired.
21. Check for misalignment or binding of
moving parts, breakage of parts,and any
other condition that may aect the tool’s
operation. If damaged,have the tool serviced
before using. Many accidents are caused by
poorly maintained tools.
22. Use only accessories that are
recommended by the manufacturer for your
model. Accessories that may be suitable for
one tool may become hazardous when used on
another tool.
SERVICE
23. Tool service must be performed only by
qualied repair personnel. Service
or maintenance performed by unqualied
personnel could result in a risk of injury.
24. When servicing a tool, ask that only
identical replacement parts be used.
Use of unauthorized parts or failure to follow
Maintenance instructions may create
a risk of electric shock or injury.
∙ HANDLE THE CORD CAREFULLY. Never
carry your tool by the cord or pull on the cord
to unplug it. Protect the cord from potential
sources of damage: heat, oil & solvents, sharp
edges, or moving parts. Replace damaged cords
immediately.
∙ WHEN WORKING OUTDOORS, USE AN
OUTDOOR-RATED EXTENSION CORD. An
extension cord rated for outdoor use must be
marked “W-A” or“W”.
∙ DO NOT EXPOSE ELECTRICAL POWER TOOLS
TO MOISTURE. Rain or wet conditions can cause
water to enter the tool and lead to electric shock.
∙ STORE IDLE EQUIPMENT. Store equipment in a
dry area to inhibit rust.
Equipment also should be in a high location or
locked up to keep out of reach of children.
∙ MAINTAIN TOOLS WITH CARE. Keep tools
sharp and clean for better and safer performance.
Follow instructions for lubricating and changing
accessories. Keep handles dry clean and free from
oil and grease.
∙ AVOID UNINTENTIONAL STARTING. Be sure

9
the switch is in the OFF position before plugging
in.
∙ DISCONNNECT THE PLUG FROM POWER
BEFORE MAKING ANY ADJUSTMENTS.
Changing attachments or accessories can be
dangerous if the tool could accidentally start.
∙ DO NOT USE THE TOOL IF IT CANNOT BE
SWITCHED ON OR OFF. Have
your tool repaired before using it.
∙ STAY ALERT. Watch what you are doing & use
common sense. Don’t operate
any tool when you are tired, or under the
inuence of alcohol, drugs or medications
that cause drowsiness.
∙ CHECK FOR DAMAGED PARTS. Before using
this tool, any part that is damaged should be
carefully checked to determine that it will operate
properly and perform its intended function.
Check for alignment of moving parts, binding
of moving parts, breakage of parts, mountings,
and other conditions that may aect its
operation. Inspect screws and tighten any ones
that are loose. Any part that is damaged should
be properly repaired or replaced by an authorized
service center unless otherwise indicated
elsewhere in the instruction manual.
Have defective switches replaced by an
authorized service center. Don’t use the
tool if switch does not turn it on and o properly.
∙ REPLACEMENT PARTS. When servicing, use
only identical replacement parts.
∙ SERVICE AND REPAIRS should be made by
qualied repair technicians at an
authorized repair centre. Improperly repaired
tools could cause serious shock or
injury.
SPECIFIC SAFETY INSTRUCTIONS FOR
TABLE SAWS
1. DO NOT OPERATE table saw until it has
been assembled and installed according to the
“assembly” instructions of this manual.
2. KEEP THE SAW TABLE free of tool and debris.
3. USE AN AUXILIARY WORK SUPPORT when
sawing long or wide work pieces to assure rm
control of the work piece at all times.
4. USE THE BLADE GUARD, spreader and anti-
kickback device whenever possible. Use the
guard on all operations where the saw blade cuts
through the thickness of the work piece.
5. THE BLADE SHOULD PROJECT ONLY A
MINIMAL DISTANCE ABOVE THE CUT: 1/8" to
1/4" (3-6 mm) for most operations.
6. NEVER REACH over or behind the blade with
the table saw operating.
7. WHEN USING THE TABLE SAW for dadoing,
grooving or shaping, use a push
block to keep your ands and ngers well away
from the saw blade in case of
kickback or other unexpected event.
8. CHECK OFTEN to assure that guards return to
their normal position quickly. If
a guard seems slow to return or “hangs up,”repair
or adjust it immediately.
9. DO NOT CUT FREEHAND (cutting without the
use of a mitre gauge or rip fence).
10. WHEN CROSSCUTTING, use the mitre gauge
to assure a straight cut, not the
rip fence. The cut o piece can bind between the
fence and blade, causing
kickback and possible injury.
11. WHEN RIPPING, always use the rip fence to

10
assure a straight cut.
12. MAKE SURE THE BLADE AND FENCE ARE
PARALLEL to each other.
Pressure to feed the work piece (stock) should be
against the direction of blade
rotation and between the blade and the fence.
Use a push stick to keep your
ngers away from the saw blade.
13. USE A FEATHER BOARD to rmly hold the
work piece against the fence and table when
ripping narrow stock.
14. KEEP YOUR TOOL BLADES SHARP. Dull
blades can cause binding, possible kick-back and
injury.
15. USE THE CORRECT BLADE for the job you
are doing. Watch for overly heated or vibrating
blades. Correct the condition before continuing.
16. MAKE SURE THE BLADE IS INSTALLED TO
ROTATE IN THE PROPER DIRECTION. Do not use
grinding wheels, wire brushes, or abrasive wheels
on a table saw.
17. ONLOOKERS SHOULD BE KEPT OUT of the
work areas. They distract the operator and make
him more accident prone. A kickback or a broken
carbide tip could send the stock or the tip ying
with unpredictable results.
18. TURN THE TOOL OFF after each completed
procedure.
19. THE SAW SHOULD ALWAYS BE TURNED OFF
and unplugged before making adjustments of
any kind.
20. TURN OFF, unplug when possible, and lock
the table saw after each use.
Remove and store the switch or lock key.
21. PREVENTING TABLE SAW KICKBACK.
Kickback is the ejection of the work
piece from the saw back towards the operator.
Tablesaw kickback may be caused by:
∙ The kerfs of the work piece closing up and
pinching the rear of the saw blade.
∙ Wedging of the work piece between the fence
and the rear of the saw blade (fence not parallel
with saw blade).
∙ A crooked cut which causes the work piece to
bind against the sides of the blade as it passes
through.
∙ Edge of a work piece against the fence not
straight. When binding, pinching, or wedging
occur the motion of the saw blade tends to
lift the wood and may hurl it back towards the
operator.
22. WOOD ONLY. This tool is designed for wood
cutting only.
23. DAMAGED OR WARPED SAW BLADES
should not be used. They are out of balance
and could cause further damage to the saw and
possible personal injury.
24. DO NOT OPERATE SAW WITHOUT GUARDS
IN PLACE. The guard protects you the operator
from cutting debris as well as from broken pieces
of the blade should it break in use.
25. REPLACE THE TABLE INSERT WHEN WORN.
Excessive tear-out increases the likelihood of
injury from ying debris. When setting the saw
at a new angle, check that due to some mis-
alignment, the blade does not cut into the table
insert or another part of your saw.
26. ALWAYS USE THE BLADE WRENCH to
tighten the saw blade onto the arbor.
27. USE A SAWBLADE SUITED TO THE CUTTING
JOB AND MATERIAL TO BE CUT.

11
SPECIFIC SAFETY PRECAUTIONS IN
PREVENTING KICKBACK
∙ Always use the rip fence to guide the work piece
in a straight line when ripping.
∙ Never freehand cut a work piece. Free-handing
causes crooked cuts and
potential kickback. Crooked edges on the stock
can also cause crooked cuts.
∙ Make sure the fence is parallel to the blade. If
the fence closes in towards the rear of the blade
it will tend to wedge the wood against the blade
and may cause kickback.
∙ Never tilt the blade or saw table such that the
work piece is trapped in the angle between the
blade and the fence. This is a condition which has
high potential of causing kickback. Use the fence
to the side of the blade that results in an angle
greater than 90 degrees between the blade and
the table.
∙ Keep the angle between the blade and fence
open so that the work piece is free to absorb any
misalignments.
∙ Avoid standing directly behind the work piece
when making a rip cut.
∙ Always use the mitre gauge when crosscutting,
and hold the work piece rmly against it to assure
a straight cut.
∙ A dull blade may cause a kickback. Keep blades
sharp.
∙ Make sure set tooth blades have adequate set.
Tooth set provides clearance between the plate
of the blade and the work piece, thus minimizing
the probability of binding. Some saw blades are
hollow or tapered ground to provide clearance.
∙ Keep saw blades clean. A buildup of pitch or
sap on the surface of the saw blade increases the
thickness of the blade and also increases friction
on the blade surface. These conditions cause an
increase in the potential of a kickback.
∙ Do not cut wet wood. It produces higher friction
against the blade. Also the blade tends to load
up with wet sawdust, eecting a much greater
probability of kickback.
∙ Be very careful of stock which is pitty, knotty or
warped. These are more likely to create pinching
conditions and possible kickback.
∙ Never use a bent, broken or warped saw
blade. The probability of binding and creating a
kickback is greatly increased.
∙ Overheating a saw blade can cause it to warp
and create a kickback. Buildup of sap on the
blades, insucient set, dullness, and unguided
cuts can all cause an overheated blade.
∙ Never use mitre gauge with the rip fence
simultaneously.
WARNING: The warnings, cautions, and
instructions detailed in this manual cannot cover
all possible conditions and situations that occur.
It must be understood by the operator that
COMMON SENSE AND CAUTION ARE FACTORS
that cannot be built into this product, but MUST
BE SUPPLIED BY THE OPERATOR.
GLOSSARY OF TERMS
BEVEL CUT
A cut made with the blade at any angle to the
table other than 90. This cut is
accomplished by tilting the saw blade.
COMPOUND CUT
A cut made with the blade at any angle to the
table (bevel angle) other than 90 and
with the workpiece at any angle to the blade
(mitre angle) other than 90.

12
CROSS CUT
A cut made across the grain of a board.
FEATHERBOARD
Pieces of wood with ngers used to hold material
against a fence and or down against the table on
power tools.
FENCE
A straight guide on a tool such as a table saw,
band saw or router table to keep the material a
set parallel distance from the blade or cutter.
FREE HAND
Performing a cut without the workpiece in
contact with and supported by the work table,
fence, or mitre gauge.
KERF
The slot or groove made by the saw blade during
a cut, usually concerning its width.
MITRE CUT
A cross cut made with the workpiece at any angle
to the blade other than 90.
MITRE GAUGE
A guide with an adjustable head that ts in a slot
and slides across a power tool
table to hold material at an angle.
PUSH STICK
A hand-held safety device used for pushing wood
past a cutter to keep the hands
away from the blade.
RIP CUT
A cut which runs through the length of a board,
parallel to the grain.
WORKPIECE
The item to which the cutting operation is being
applied.
PRODUCT SPECIFICATIONS
MOTOR
Type Universal
Amps 15
Voltage 120
Hz 60
RPM 4800
Overload Protection YES
SAW
Blade Size 10”(255 mm)
Maximum Cut Depth @ 90º 2-7/8" (73 mm)
Maximum Cut Depth @ 45º 2-23/64" (60 mm)
Table size (width x depth): 26" x 18-7/8" (660 x
480 mm)
UNPACKING AND CHECKING CONTENTS
WARNING: To avoid injury from unexpected
starting or electrical shock, do not plug the
power cord into a source of power. This cord must
remain unplugged whenever you are working on
the table saw.
Your table saw is shipped complete in one carton.
1. Unpacking and Checking Contents. Separate
all parts from packing materials
and check each one with the illus tration and the
parts list to make certain all
items are accounted for before discarding any
packing material.
WARNING: If any parts are missing, do not
attempt to assemble the table saw.
Do not plug in the power cord or turn on the
switch until the missing parts are
obtained and are installed correctly.
PARTS IN CARTON
1. Table Saw Assembly
2. Mitre gauge
3. Rip fence and handle
4. Blade elevation wheel handle

13
5. Blade guard assembly
6. Blade wrenches
7. Anti-Kickback Device
8. Table insert
9. Push stick
10. Long top plates
11. Short top plates
12. Long support plates
13. Short support plates
14. Legs
15. Rubber feet
16. Hardware kit (not shown)
ASSEMBLY TIME
The expected time to assemble and properly
adjust this saw is two hours.
FUNCTIONAL DESCRIPTION
A Overload Reset button
B On/O paddle switch
C Saw blade
D Blade elevation handwheel
E Sawdust port
F Rip fence scale
G Mitre gauge lock knob
H Mitre gauge
I Table
J Blade guard
K Anti-kickback pawls & splitter
L Kerf plate
M Mitre gauge storage
N Base
O Fence lock handle
P Blade tilt scale
Q Stand
R Rip fence
ASSEMBLY
WARNING: RISK OF PERSONAL INJURY. Always
disconnect tool from power source before
making any adjustments, installing or changing
accessories.
CAUTION: The tool must be assembled before
use. DO NOT plug unit into power source until
the unit has been completely assembled and all
guards are in place.
TOOLS NEEDED
The following tools are needed for assembly (not
included):
Adjustable crescent wrench
Phillips screwdriver
Combination square
5 mm Allen wrench
TO ASSEMBLE THE LEG STAND
See Figure 3.
WARNING: After completing adjustments,
securely tighten all fasteners. An
unstable stand may shift in use and cause serious
personal injury.
WARNING: The stamped rails may have sharp
edges. Be careful in handling the rails to prevent
being cut.
NOTE: Use the screws 1, washers 2, and lock nuts
3 supplied in the hardware kit
to attach the pieces of the leg stand together (Fig.
25). Do not tighten the
hardware completely until the leg stand is
completely assembled.
The following letters are stamped on pieces for
identication:
A - Legs (qty. 4).
B - Front and rear top plates (qty. 2).
C - Side top plates (qty. 2).
D - Side support plates (qty. 2).
E - Front and rear support plates (qty. 2).
1. Attach the side top plates C to the legs A.
2. Attach the side support plates D to the legs A.
3. Place the front and rear top plates B over the
side top plates C. and attach to the legs A.
4. Attach the front and rear support plates E to
the legs A.
5. Tap the four rubber feet 4 onto the bottom of
the legs A.

14
MOUNTING THE TABLE SAW ON THE STAND
See Figure 4.
Do not lift the saw without help. The saw base
weighs ap proximately 42 lbs.
Hold it close to your body. Keep your knees bent
and lift with your legs, not your back. Ignoring
these precautions can result in back injury.
∙ Take the following from a small hardware pack:
4 carriage bolts (M8X60)
4 hex nuts (M8)
NOTE: This hardware was in the pack with
hardware for assembling the leg stand and
leveling feet.
∙ Place the saw base on the leg stand. Align
the holes in the table with the holes in the end
braces.
∙ Place a bolt in each hole. Secure with a hex nut.
Hand tighten.
∙ Repeat for three remaining holes. Tighten all
hardware securely.
HANDWHEEL ASSEMBLY
1. (see g.5) Assemble handwheel (U) to shaft (X)
making sure the at on inside of handwheel lines
up with at on shaft.
2. (see g.6) Fasten handwheel (U) to shaft using
a M6 x 12 mm at head Phillips screw (Y).
ATTACHING THE SMART GUARD SYSTEM
POSITIONING THE RIVING KNIFE
1. Remove table insert using nger hole.
2. Raise the blade as high as it will go and set it
perpendicular to table (0° on bevel scale) (Fig. 7).
3. Rotate the riving knife release lever 1 clockwise,
so that it points upward (Fig. 7).
4. Pull riving knife 2 towards release lever to
disengage it from the pins 3.
5. Slide the riving knife 2 up to its highest
position, so that it is directly over
the center of the blade (Fig. 8).
6. Align holes in riving knife with pins 3 and lock
the release lever 1 by rotating it counterclockwise.
Push/pull riving knife to verify that it is locked
in place (Fig. 8).
7. Replace table insert (Fig. 9).
ATTACHING THE BLADE GUARD ASSEMBLY
8. With one hand, hold the front of the blade
guard assembly 4 by the metal
“fork”. With the other hand, hold the guard
release lever 5 up (Fig. 9).
9. Lower the rear of guard assembly and slip the
cross bar 6 into the rear
notch 7 on top of the riving knife 2 (Fig. 9).
10. Lower the front of the guard assembly 4 until
the metal“fork”is parallel
with the table (Fig.10).
11. Press down on the guard release lever 5 until
you feel and hear it snap
into the locking position. Check that the guard
assembly is securely
connected (Fig. 10).
ATTACHING THE ANTI-KICKBACK DEVICE
12. While pulling out the attachment pin 8, attach
the Anti-Kickback Device 9
into the at recessed area 10 of the riving knife 2
(Fig. 11).
13. Slide the Anti-Kickback Device down until it
drops into the recessed area
– then release the attachment pin such that the
Anti-Kickback Device locks onto the riving knife
immediately behind the guard assembly.
Check that the attachment pin is securely
connected into locking hole.
14. Carefully raise and lower the pawls 11 – when
letting go, the spring-loaded pawls must come
down and contact the table insert (Fig. 11).
Note: The two attachments are independent of
each other, so the Anti-Kickback Device can be
attached before the Blade Guard Assembly.
OPERATING PROCEDURES
WARNING: DO NOT OPERATE saw until it has
been assembled and installed according to the
instructions in “ASSEMBLY”. Read and follow all
safety rules within this Instruction Manual, failure
to do may result in electric shock and/or
serious personal injury.

15
POWER SWITCH
See Figure 12.
Your table saw is equipped with a power switch
that has a built-in locking
feature. This feature is intended to prevent
unauthorized and possible
hazardous use by children and others.
TO TURN YOUR SAW ON:
∙ With the switch key inserted into the switch, lift
the switch button to turn ON.
TO TURN YOUR SAW OFF:
∙ Press the switch button down to turn OFF.
TO LOCK YOUR SAW:
∙ With the saw turned OFF, pull the switch key
from the switch and store in a safe, secure
location.
Overload protection
WARNING: To prevent an accidental startup if
the overload reset switch
is pushed, the on/o switch should be in the OFF
position, and the plug
should be removed from the power source while
cool-down takes place.
Overheating may be caused by misaligned parts
or a dull blade. Inspect your saw for proper setup
before using it again.
This saw has an overload reset switch (1) that
will restart the motor after it shuts o due to
overloading or low voltage. If the motor stops
during operation:
1.Turn the ON/OFF switch to the OFF position.
2.Wait about ve minutes for the motor to cool.
3.Push in on the overload reset switch.
4.Turn the switch to the ON position.
TO CHANGE THE BLADE DEPTH
See Figure 13.
The blade depth should be set so that the outer
tips of the blade are higher
than the workpiece by approximately 1/8 in. to
1/4 in. but the lowest points
(gullets) are below the top surface. Raise the
blade by turning the blade adjusting
handle counterclockwise or lower it by turning
the handle clockwise.
TO CHANGE BEVEL ANGLE
See Figure 14.
A 90° cut has a 0° bevel and a 45° cut has a 45°
bevel.
∙ Unplug the saw.
∙ Loosen bevel control by turning bevel lock lever
all the way to the left. If it needs
to be further loosened, pull spring-loaded bevel
lock lever out and rotate it back to
the right. Release bevel locking lever and allow it
to seat (lock) in its original position.
Turn it to the left again until loose.
∙ Adjust the bevel angle by sliding the blade
adjusting handle left or right to the
desired angle.
∙ Tighten bevel control by turning bevel lock lever
to the right. If it needs to be
tightened more, pull the spring-loaded bevel lock
lever out and rotate it to the left.
Then release bevel lock lever and allow it to
return to its original position. Rotate to
the right again. Repeat this process until bevel
lock lever is securely tightened.
NOTE:
Before cutting, the bevel lock lever must be
securely locked as shown in
gure 16.
TO ADJUST THE BEVEL INDICATOR
See Figure 15.
If the bevel indicator is not at zero when the saw
blade is at 90°, adjust the indicator
by loosening the screw and setting it at 0° on the
bevel scale. Retighten the screw.
WARNING: To reduce the risk of injury,
alwaysmake sure the rip fence is parallel to
the blade before beginning any operation.
TO INSTALL THE RIP FENCE
See Figure 16.
∙ Place the rear lip on the rear of the saw table
and pull slightly toward the front of the unit.
∙ Lower the front end of the rip fence onto the

16
guide surfaces on top of the front
rail.
∙ Push the rip fence lever down to automatically
align and secure the fence. The
trigger lock must engage.
Check for a smooth gliding action. If adjustments
are needed, see To Check the Alignment of
the Rip Fence to the Blade in the Adjustment
section of this manual.
TO SET THE RIP FENCE SCALE INDICATOR TO
THE BLADE
See Figure 17.
Beginning with the blade at a 0° angle (straight
up), use the following steps to set
the rip fence scale indicator to the blade:
∙ Unplug the saw.
∙ Loosen the rip fence by depressing the trigger
lock and lifting the locking handle.
∙ Using a framing square, set the rip fence 2 in.
from the blade tip edge.
∙ Loosen the screw for the scale indicator and
align with the 2 in. mark as shown.
∙ Retighten the screw.
TO USE THE MITRE GAUGE
See Figure 18.
The mitre gauge provides greater accuracy in
angled cuts. For very close
tolerances, test cuts are recommended.
There are two mitre gauge channels, one on
either side of the blade. When making
a 90° cross cut, you can use either mitre gauge
channel. When making a beveled cross
cut (the blade tilted in relation to the table) the
mitre gauge should be located in the
slot on the right so that the blade is tilted away
from the mitre gauge and your hands.
The mitre gauge can be turned 60° to the right or
left.
∙ Loosen the lock knob.
∙ With the mitre gauge in the mitre gauge slot,
rotate the gauge until the desired
angle is reached on the scale.
∙ Retighten the lock knob.
CROSS-CUTTING
1. Cross-cutting requires the use of the mitre
gauge to position and guide the work. It is best
to set aside the rip fence when cross-cutting.
2. Place the work against the mitre gauge and
advance both the gauge and work towards the
saw blade ( see g.19).
3. The mitre gauge may be used in either table
slot.
4. When bevel cross-cutting (blade tilted), use the
mitre gauge in the right table slot only, where
the blade is tilted away from the mitre gauge and
your hands.
WARNING: The saw guard must always be used.
5. Start the cut slowly and hold the work rmly
against the mitre gauge and the table.
6. One of the rules in running a saw is that you
never hang onto or touch a free piece of work.
Hold the supported piece, not the free piece that
is cut o.
7. The feed in cross-cutting continues until the
work is cut in two, and the mitre gauge and work
are pulled back to the starting point. Before
pulling the work back it is good practice to give
the work a little sideways shift to move the work
slightly away from the saw blade.
8. Never pick up any short length of free work
from the table while the saw is running.
9. Never touch a cut-o piece while the saw is
running unless the piece is at least 30 cm (1 foot)
long.
WARNING: Never use the fence as a cut-o
gauge when cross-cutting.
10. For added safety and convenience the mitre
gauge can be tted with an auxiliary facing.
This auxiliary wood-facing can be fastened to
the front of the mitre gauge by using two wood
screws through the slots provided in the mitre
gauge body and into the wood facing.
RIPPING
Ripping is the operation of making a length-wise
cut through a board.
1. The rip fence (N, g.20) is used to position
and guide the work. One edge of the work rides
against the rip fence while the at side of the
board rests on the table.

17
2. Since the work is pushed along the fence, it
must have a straight edge and
make solid contact with the table.
WARNING: The saw guard must always be used.
The guard has anti-kickback
ngers to help prevent kickback and a splitter to
prevent the saw kerf from closing and binding
the blade.
3. Start the motor and advance the work, holding
it down against the fence.
4. Never stand in the line of the saw cut when
ripping.
5. Hold the work with both hands and push it
along the fence and into the saw blade.
6. When the work piece is fully on the table, it
can then be fed through the saw blade with one
hand.
7. When the work is beyond the saw blade and
anti-kickback ngers, the feed can continue to
the end of the table, after which the work is lifted
and brought back along the outside edge of the
fence.
8. The cut-o stock remains on the table or tilts
up slightly and is caught by the rear end of the
guard or slides o the table to the oor.
9. If the cut-o stock remains on the table, it is
not touched with the hands until the saw blade
is stopped, unless it is a large piece allowing safe
removal.
10. If the ripped work is less than 4" (10 cm) wide,
a push stick, as supplied (UU, ), or made out of
scrap wood, should always be used to
complete the feed as shown in g.22.
11. Use feather boards for all non “thru-sawing”
operations where the guard and spreader
assembly must be removed. Feather boards are
used to keep the work in contact with the fence
and table and help prevent kickbacks. Clamp the
feather boards to the fence and table so that the
leading edge of the feather boards will support
the work piece until the cut is completed.
12. Always replace the guard and spreader
assembly when the non thru-sawing operation is
completed.
ADJUSTMENTS
WARNING: Before performing any adjustment,
make sure the tool is unplugged from
the power supply and the switch is in the OFF
position. Failure to follow this warning
could result in serious personal injury.
To avoid unnecessary setups and adjustments, a
good practice is to check your
setups carefully with a framing square and make
practice cuts in scrap wood before
making nish cuts in good workpieces. Do not
start any adjustments until you have
checked with a square and made test cuts to be
sure adjustments are needed.
TO CHECK THE ALIGNMENT OF THE RIP FENCE
TO THE BLADE
See Figure 23.
WARNING: To reduce the risk of injury,
alwaysmake sure the rip fence is parallel to
the blade before beginning any operation.
∙ Unplug the saw then remove the blade guard
assembly.
∙ Unlock the rip fence by depressing the trigger
lock and lifting the locking handle.
∙ Place a framing square beside the blade and
move the rip fence up to the square.
Take the dimension on the rip scale.
∙ Move the rip fence back and turn the framing
square 180° to check the other side.
∙ If the two dimensions are not the same, loosen
the two screws on the fence and align it.
∙ Retighten the two screws.
∙ Make two or three test cuts on scrap wood. If
the cuts are not true, repeat the process.
NOTE: The rip fence must be secure when the
locking handle is engaged. The
clamp screw on the rear of the rip fence is
tightened by turning clockwise to
increase tightness of the rear of the rip fence.
TO SET THE 90° POSITIVE STOP
See Figure 24.

18
Make sure the saw is unplugged from the
power source. Raise the blade to the maximum
height by turning the blade adjusting handle
counterclockwise.
Unlock the bevel locking lever.
If the blade angle is less than 90°, turn the 90°
positive stop adjustment screw
counterclockwise one turn. Rotate blade
adjusting handle counterclockwise
until it stops. Recheck the blade position.
Continue this process until the
blade is at 90°. Relock the bevel locking lever.
If the blade angle is greater than 90°, use the
framing square to position
the blade to 90°. Turn the 90° positive stop
adjustment screw clockwise
until it stops. Relock the bevel locking lever.
Reset the bevel indicator to 0° by loosening the
screw holding the indicator.
Line up the red line on the indicator with the 0°
mark on the bevel scale.
TO SET THE 45° POSITIVE STOP
See Figure 25.
Make sure the saw is unplugged from the
power source. Raise the blade to the maximum
height by turning the blade adjusting handle
counterclockwise.
Turn the bevel locking lever to the left to loosen
the bevel.
If the blade angle is greater than 45°, turn the
45° positive stop adjustment screw
counterclockwise 1 turn and rotate the bevel
adjusting handle counterclockwise
until it stops. Recheck the blade position.
Continue this process until the blade
is at 45°. Tighten the bevel locking lever.
If the blade angle is less than 45°, use the
combination square or triangle to
position the blade at 45°. Turn the 45° positive
stop adjustment screw
clockwise until it stops. Tighten the bevel locking
lever.
Reset the bevel indicator to 45° by loosening the
screw holding the indicator.
Line up the red line on the indicator with the 45°
mark on the bevel scale.
MAINTENANCE
CHANGING THE SAW BLADE
WARNING: Disconnect machine from power
source.
WARNING: Use only 10” (254 mm) diameter saw
blades rated for 5000 RPM or
higher with 5/8”arbor holes, or with 25 mm arbor
holes and a bushing to 5/8”.
See Figure 26.
1. Raise the saw blade to its maximum height.
2. Remove the table insert kerf plate.
3. Using one supplied open end blade wrench
place open end of wrench on ats
of the outside blade ange to keep the saw arbor
from rotating.
4. Remove arbor nut with other supplied open
end blade wrench counterclockwise to remove.
5. Remove outside blade ange.
6. Remove saw blade.
7. Assemble new blade, marking certain teeth of
blade are pointing down at the front of the saw
table.
8. Assemble the outside blade ange and arbor
nut.
9. Tighten nut with wrench by turning nut
clockwise while holding arbor steady
with other wrench.
10. Replace table insert kerf plate.
GENERAL MAINTENANCE
WARNING: Prior to inspection or saw
maintenance, turn o power switch and
disconnect plug from power source.
WARNING: RISK OF PERSONAL INJURY. Always
disconnect tool from power

19
source before making any adjustments, installing
or changing accessories.
CAUTION: Tool service must be preformed only
by qualied repair personnel.
Service or maintenance performed by unqualied
personnel could result in a risk
of injur y. When servicing a tool, use only identical
replacement parts. Follow
instructions in the Maintenance section of this
service manual. Use of unauthorized
parts or failure to follow Maintenance Instructions
may create a risk of electrical
shock or injury.
∙ Inspect the cord regularly and have it replaced
by an authorized repair facility if it is damaged
∙ Clean the tool housing, motor vents and blade
after each use. This will help prevent possible
electrical shorts and ensure proper cooling.
∙ Keep the tool dry, clean and free from oil and
grease.
∙ Store the tool on a safe and dry place, out of
reach of children.
∙ Do not use cleaning agents or solvents that
could attach the plastic parts of the tool.
∙ Turn the tool o immediately and do not
operate, until repaired, if tool begins to make
abnormal noise, vibrations, produces smoke or
burning odour.
∙ Keep tools sharp and clean for best and safest
performance. Follow instructions for lubricating
and changing accessories. that involve
isassembling the saw.
∙ An authorized repair centre should do any
repairs, modication, or maintenance
that involve disassembling the saw
∙ Any damage to the tool should be corrected at
an authorized repair centre.
WARNING: Repairs should be made by an
authorized repair centre. Opening this
tool could invalidate your warranty.
WARNING: RISK OF PERSONAL INJURY. Use only
accessories that are
recommended by the manufacturer for your
model. Accessories that may be suitable
for one tool, may become hazardous when used
on another tool.

20
I.D Description Qte
1. Switch 1
2. Panel 1
3. Ø4 at washer 15
4. St4.2x14 screw 16
5. Overload switch 1
6. Cushion 1
7. Switch box 1
8. Label 1
9. Rubber feet 4
10. M6x25 screw 4
11. Ø6 washer 6
12. Housing 1
13. Spring piece 2
14. Block 2
15. Dustproof cover 1
16. Plug 1
17. Cable sleeve 1
18. Cable clamp 1
19. M4x10 screw 1
20. Ø4 spring washer 1
21. Spring steel clip 1
22. Block 1
23. M4 net 1
24. M4x12 screw 9
25. Dead plate 1
26. M4 net 9
27. Dead gear 1
28. M8x65 screw 1
29. Up down adjust handle 1
30. M8 net 8
31. Label 1
32. Up down adjust handwheel 1
33. Spring 1
34. Ø2.5x22 pin 1
35. Adjust bar 1
36. Ø12 spring washer 9
37. M6 net 2
38. Bracket base 1
39. Limited plate 1
40. Angle limited plate 1
41. M5x12 screw 1
42. Ø5 spring washer 5
43. Ø5 at washer 9
44. M6x85 screw 2
45. Ø6 at washer 12
46. Connecting sleeve 3
47. M6 lock net 15
48. M5x14 screw 1
49. Magnier 1
50. M8 net 2
51. Connecting hook 1
52. M8x16 screw 1
53. Lock net 1
54. Ø6 washer 1
55. Lock sleeve 1
56. M6x net 23
57. M6x30 screw 1
58. Rotary board 2
59. M6 T screw 2
60. Up down adjust bar 1
61. Bracket base 1
62. M8 T screw 2
63. Ø8 at washer 7
64. Bracket 1
65. M6x16 screw 3
66. Ø6 spring washer 9
PARTS LIST
10’’TABLE SAW
WARNING
Any attempt to repair or replace electrical parts on this Table Saw may create a HAZARD unless repair is
done by a qualied service technician. Repair service is available at your nearest Service Centre.
This manual suits for next models
1
Table of contents
Languages:
Other Matrix Saw manuals
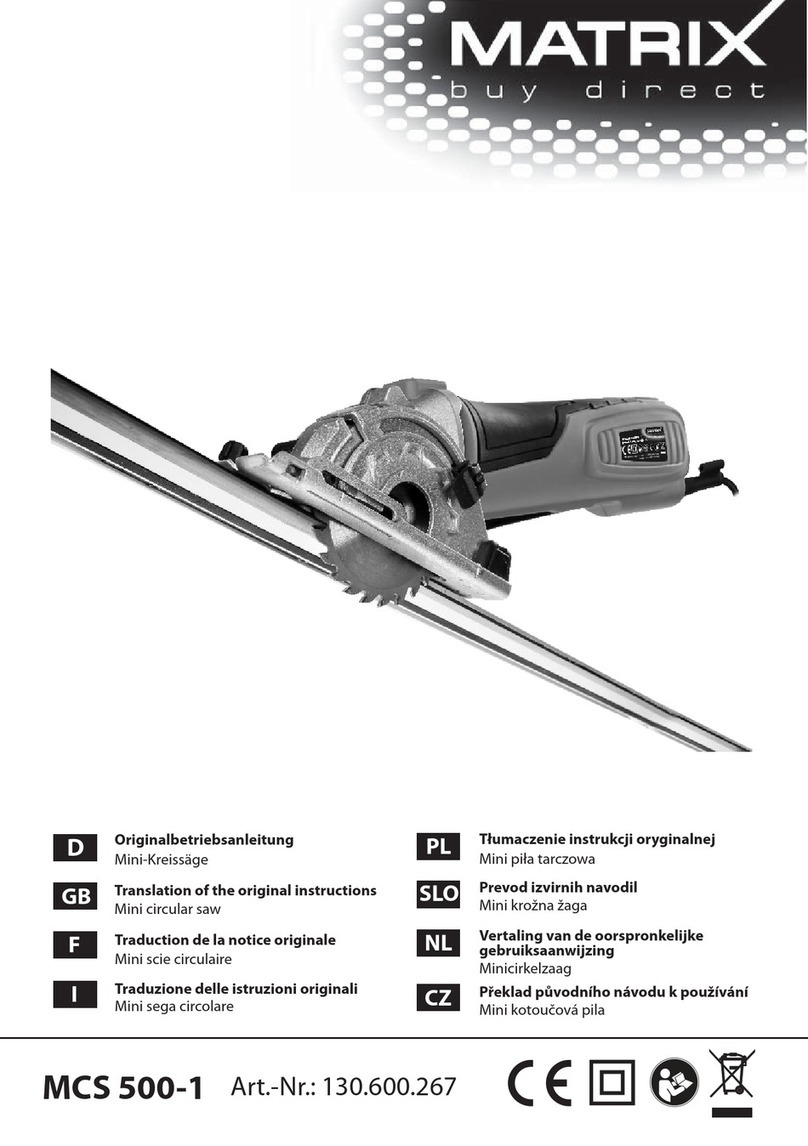
Matrix
Matrix MCS 500-1 User manual
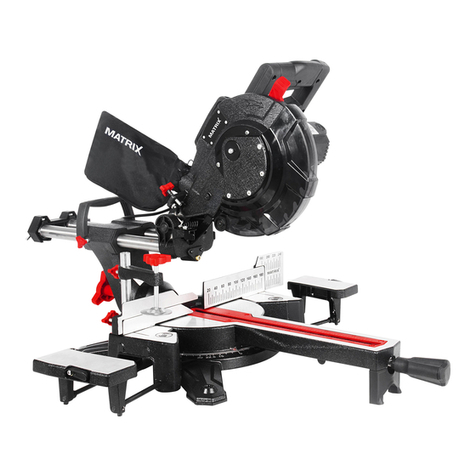
Matrix
Matrix SMS 2200-340 LL-2 Quick start guide

Matrix
Matrix 92109B User manual
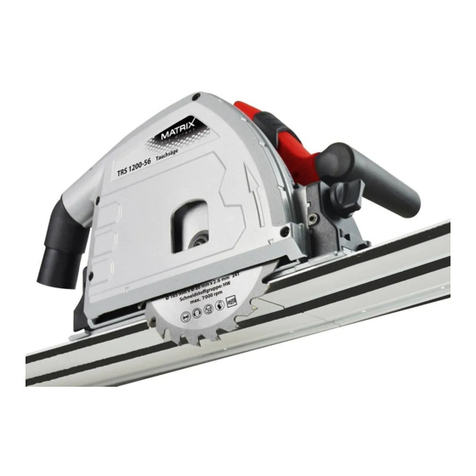
Matrix
Matrix TRS 1200-56 User manual
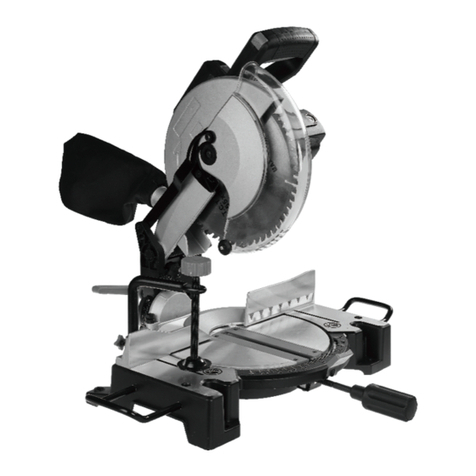
Matrix
Matrix 92552 User manual
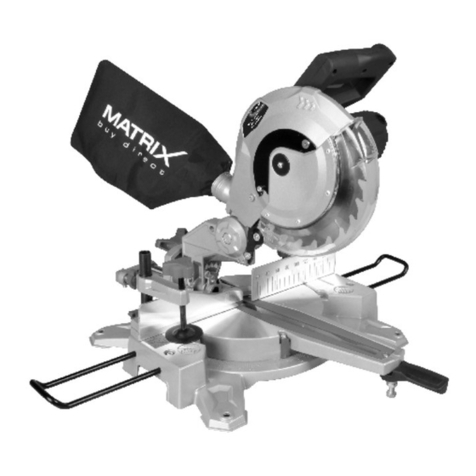
Matrix
Matrix M1YL-LZ-210 User manual
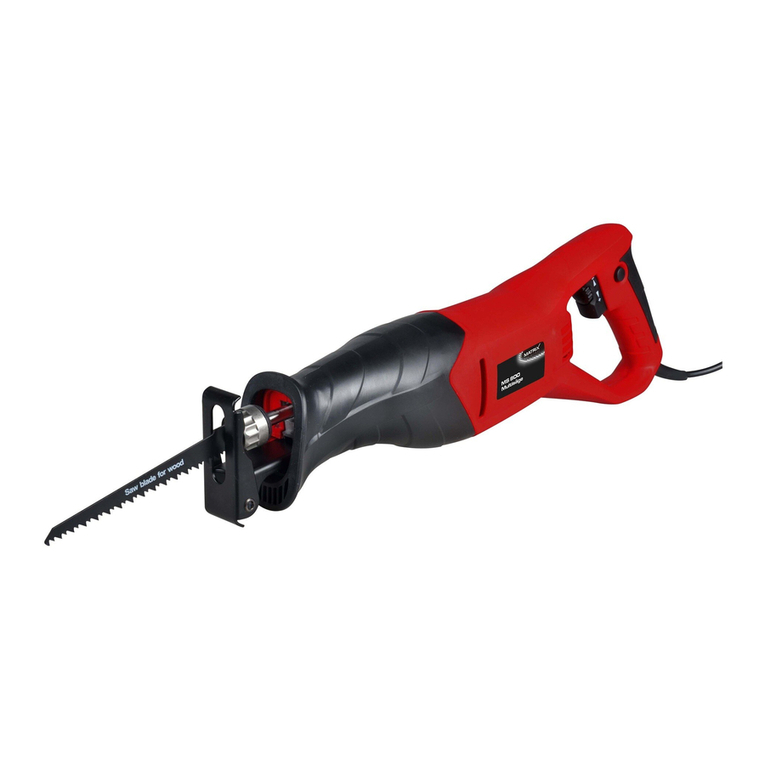
Matrix
Matrix MS 800 User manual

Matrix
Matrix MTS 2050-216 Duo User manual
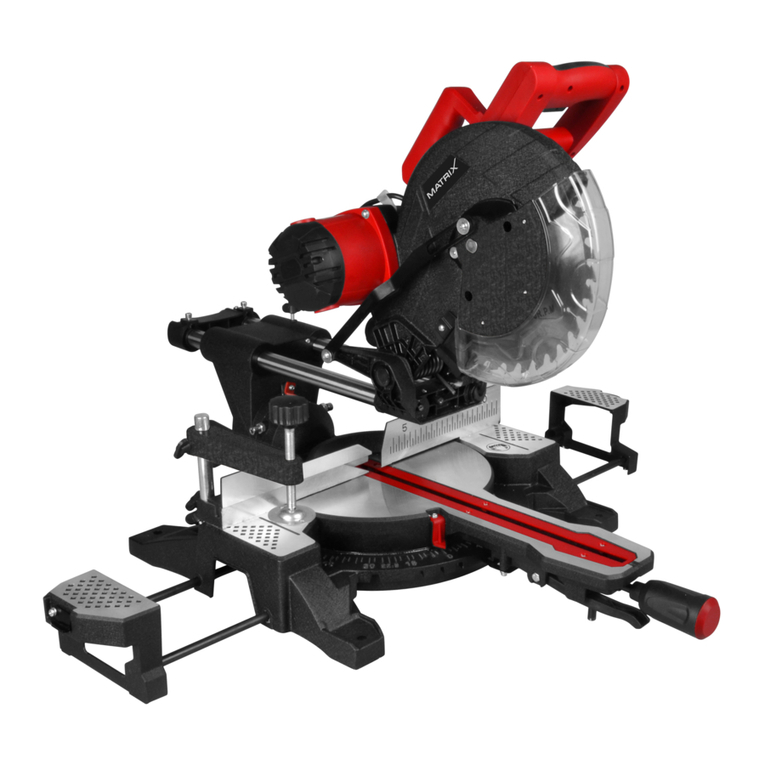
Matrix
Matrix HM1028R User manual

Matrix
Matrix CS 1200-185 User manual