Mecademic Meca500 User manual

User Manual
Original instructions
Meca500 (R3)
Robot Firmware: 7.0.6
Document Revision: F
November 12, 2018

The information contained herein is the property of Mecademic Inc. and shall not be
reproduced in whole or in part without prior written approval of Mecademic Inc. The
information herein is subject to change without notice and should not be construed as a
commitment by Mecademic Inc. This manual will be periodically reviewed and revised.
Mecademic Inc. assumes no responsibility for any errors or omissions in this document.
Copyright c
2018 by Mecademic Inc.

Contents
1 Introduction 1
2 Warning messages, notes and emphases 1
3 What's inside the box 2
4 Safety 4
4.1 Power supply and stopping functions
................... 5
4.2 Disabling the brakes of the robot
..................... 5
4.3 Functioning of the brakes
.......................... 6
5 Technical specications 7
6 Installing the Meca500 9
7 Installing an end-eector 13
8 Operating the robot 14
8.1 The web interface
............................... 14
8.1.1 Overview ................................. 14
8.1.2 Connection and disconnection . . . . . . . . . . . . . . . . . . . . . . 15
8.1.3 The programming panel . . . . . . . . . . . . . . . . . . . . . . . . . 16
8.1.4 Thelogpanel............................... 17
8.1.5 The CAD models import panel . . . . . . . . . . . . . . . . . . . . . 18
8.2 Power-up procedure
.............................. 19
8.2.1 Poweringtherobot............................ 19
8.2.2 Connecting to the robot . . . . . . . . . . . . . . . . . . . . . . . . . 19
8.2.3 Activating the robot . . . . . . . . . . . . . . . . . . . . . . . . . . . 19
8.2.4 Homingtherobot............................. 20
8.3 Moving the robot
............................... 20
8.4 Power-o procedure
.............................. 22
8.4.1 Zeroing the robot (optional) . . . . . . . . . . . . . . . . . . . . . . . 22
8.4.2 Deactivating the robot . . . . . . . . . . . . . . . . . . . . . . . . . . 22
8.4.3 Disconnecting the robot . . . . . . . . . . . . . . . . . . . . . . . . . 22
8.4.4 Removingpower ............................. 23
8.5 Oine mode
................................... 23
8.5.1 Saving the program via the web client interface . . . . . . . . . . . . 23
8.5.2 Running the oine program . . . . . . . . . . . . . . . . . . . . . . . 23
i

8.6 Robot control panel
.............................. 24
8.6.1 LEDs ................................... 24
8.6.2 Buttons .................................. 25
9 Operating the intelligent power supply 27
9.1 LEDs
....................................... 28
9.2 External connections
............................. 28
10 Examples 32
10.1 Draw a square
................................. 32
11 Troubleshooting 33
12 Storing the robot in its shipping box 34
13 EC Declaration of Incorporation (original) 35
ii

User Manual
1 Introduction
There are two manuals that come with the Meca500 (R3): this one and the programming
manual. This manual will guide you through the steps required for setting up your Meca500
and for using it in a safe manner. You must read this user manual thoroughly before even
unpacking your rst Meca500.
The Meca500 is a six-axis industrial robot arm that is relatively easy to use, robust and
lightweight. The robot is, however, a precision device with rapidly moving parts. This
robot should therefore be used only by technical personnel who have read and understood
every part of this user manual, in order to avoid damages to the robot, its end-eector, the
workpiece and adjacent equipment, and, most importantly, in order to avoid injuries.
2 Warning messages, notes and emphases
Particular attention must be paid to the warning messages in this manual. There are only
two types of warning messages, as shown bellow:
B
WARNING:
This presents instructions that must be followed in order to prevent injuries
and possibly damage to your robot cell (robot arm, power supply, end-eector,
workpiece and/or adjacent equipment).
B
CAUTION:
This presents instructions that must be followed in order to prevent damage
to your robot cell (robot arm, power supply, end-eector, workpiece and/or
adjacent equipment).
In addition, important notes and denitions are formatted as follows:
NOTICE:
This highlights important suggestions or denitions, the purpose of which is to
improve the understanding of this manual and of how the robot works.
Finally, occasionally, small portions of the text in this manual that are particularly important
are underlined (as already done in the previous section).
Copyright c
2018 by Mecademic Inc.
Page 1 of 35

User Manual
3 What's inside the box
Your shipping box contains a Meca500 robot arm (Fig. 1a), a 24 V DC intelligent power
supply with an integrated safety module (Fig. 1b) and a D-SUB 15-position dongle (Fig. 1c),
a 2-meter M12 D-Code to RJ45 Ethernet cable (Fig. 1d), and a 2-meter M12 Circular male
to M12 Circular female DC power cable (Fig. 1e).
Your box may also contain the MEGP 25 electric gripper and accessories. Remove all
items carefully and do not discard your shipping box. If your order contained a gripper,
do not open its package immediately. You must read the MEGP 25 user manual prior to
installing the gripper.
Note, that you must provide your own AC power cord, with three-prong IEC C13 con-
nector on one end, and your own country's power plug on the other. You must also provide
M6 screws of proper length for xing the robot's base and the power supply.
(a) The Meca500 robot arm
(b) D-SUB dongle
(c) Power supply
(d) Ethernet cable
(e) DC power cable
Figure 1: The main contents of your shipping box (optional items not shown)
Page 2 of 35
Copyright c
2018 by Mecademic Inc.

User Manual
B
CAUTION:
•
Handle the robot with care.
•
The Meca500 is equipped with brakes on the rst three joints (the ones close
to the base). When the robot is not activated, these brakes are automatically
applied. Do not force the brakes of the robot, unless there is an emergency!
•
Inspect the robot and the power supply for damages. If you think either of
them is damaged, do not use them and contact us immediately.
•
Do not modify or disassemble the robot arm or the power supply.
•
Do not use or store the Meca500 in a humid environment.
•
Do not operate the Meca500 at temperatures bellow
+5◦
C or above
+45◦
C.
•
Do not use any other power supply but the one provided.
•
Do not replace the Ethernet and DC power cables provided with longer ones,
without contacting us rst.
Copyright c
2018 by Mecademic Inc.
Page 3 of 35

User Manual
4 Safety
The Meca500 weighs less than 5 kg. It can, however, move fast and may cause injuries,
especially when certain end-eectors are attached to its ange (e.g., a sharp tool or a laser).
The robot also has pinch regions where two adjacent links of the robot can squeeze a nger
(Fig. 2).
It is imperative that you follow the guidelines of ISO 12100:2010 and ISO 10218-2:2011
and conduct a risk assessment of your complete robot cell, including the Meca500, its end-
eector and all adjacent equipment.
B
WARNING:
•
When the Meca500 is activated, stand away from it, wear safety goggles and
be attentive and alert.
•
If deemed necessary, place the robot in a safety enclosure.
•
In case of an emergency, press immediately the E-STOP button located on
the power supply.
Figure 2: When the Meca500 is activated, keep away from the zones labeled with the pinch-
point warning sign, to avoid injuries
Page 4 of 35
Copyright c
2018 by Mecademic Inc.

User Manual
4.1 Power supply and stopping functions
To power your Meca500 robot arm, you can only use the intelligent power supply provided
by Mecademic. If you use one of our older power supplies or your own 24 V DC source, the
robot would not function. Our new power supply has an integrated safety module, including
a button for emergency stop (Stop Category 1), a reset button, status LEDs, and a D-SUB
15-position interface for connecting an external emergency stop (Stop Category 1), a Stop
Category 1 protective stop, and a Stop Category 2 protective stop. The emergency stops
and the Stop Category 1 protective stop are designed as PL=d with Safety Category 3.
To start using your robot immediately, connect the dongle provided to the D-SUB 15-
position interface. This would deactivate the additional protective stops and emergency
stop. Read section 9.2 if you want to remove the dongle and install such additional stops.
Furthermore, to connect the power supply to the robot, you must use the DC power cable
provided and never modify it.
B
CAUTION:
Never install an emergency stop or any kind of on/o switch on the DC side of
the power supply.
When disconnecting the AC power, either by using the on/o switch on the power supply
or by unplugging the AC cord, the brakes on joints 1, 2 and 3 will be immediately applied
and the joints will be immobilized instantly. Therefore, to avoid premature use of the brakes,
do not disconnect the AC power when the robot is moving.
When disconnecting the AC power or activating the emergency stop or the external Stop
Category 1 protective and emergency stops, the wrist joints of the robot become free. This
minimizes the risks of pinning and pinching from the wrist and the end-eector. However,
beware that the end-eector might slowly move downwards under the eects of gravity.
Depending on the type of end-eector used, this residual motion might lead to an injury.
By denition, the Stop Category 2 protective stop does not cut power to the robot, so
after the robot stops all motors are active and maintain the position of all joints. The brakes
are not applied and there is no residual motion due to gravity.
4.2 Disabling the brakes of the robot
In case of a collision, you can disable the brakes of joints 1, 2 and 3. This can only be done
if the robot is powered AND not activated. How to activate and deactivate the robot is
explained later in this manual, but for now, it suces to say that the robot is deactivated
Copyright c
2018 by Mecademic Inc.
Page 5 of 35

User Manual
after pressing the E-STOP button. Thus, in case of a collisionthough ideally prior to
thatyou must press the E-STOP button.
Then, to release the brakes of joints 1, 2 and 3, press one of the two 0G buttons on the
base of the robot continuously while holding the robot with your other hand. After 3 seconds,
you will hear the deactivation of the brakes. Continue holding the 0G button pressed and
move the robot as far as possible from obstacles. Finally, release the 0G button, and move
away from the robot. Note that there is a pair of commands to disable and re-enable the
brakes. These are described in the programming manual.
B
WARNING:
In case of an emergency, it is relatively easy to force the robot brakes and move
the robot's joint manually. However, forcing the brakes too often will damage
the robot.
4.3 Functioning of the brakes
It is extremely important to remember that the robot has brakes only on joints 1, 2 and 3.
Therefore, when the robot is deactivated or powered o, the robot's end-eector will slowly
go down under the eects of gravity.
In addition, it is important to remember that the brakes used on joints 1, 2 and 3 are
emergency brakes, not locking brakes. Therefore, if you you leave the robot in a conguration
where the robot's forearm is nearly horizontal, the robot will eventually fall down under the
eects of gravity (e.g., after several hours), especially if you have the maximum payload.
Therefore, always deactivate the robot when the forearm is as vertical as possible (i.e., try
to minimize the static torques on joints 1, 2 and 3).
Page 6 of 35
Copyright c
2018 by Mecademic Inc.

User Manual
5 Technical specications
Table 1 lists the main technical specications of the Meca500 robot arm. Note that the
maximum tool-center point (TCP) linear velocity is software limited to 500 mm/s when the
robot moves in Cartesian mode, regardless of the denition of the TCP with respect to the
robot's ange. However, if the robot is fully stretched and all joints move at maximum
speed, in joint mode, the linear velocity of the TCP can surpass 2,000 mm/s.
B
WARNING:
Note that in some special congurations, the robot's end-eector can move at
2,000 m/s or even faster. You must consider this fact in your risk assessment.
Table 1: Technical specications for the Meca500
Position repeatability 0.005 mm
Rated payload 0.5 kg
Max. payload 1.0 kg (under special conditions)
Weight of robot arm 4.5 kg
Range for joint 1
[−175◦,175◦]
Range for joint 2
[−70◦,90◦]
Range for joint 3
[−135◦,70◦]
Range for joint 4
[−170◦,170◦]
Range for joint 5
[−115◦,115◦]
Range for joint 6
[−36,000◦,36,000◦]
Max. speed for joint 1
150◦
/s
Max. speed for joint 2
150◦
/s
Max. speed for joint 3
180◦
/s
Max. speed for joint 4
300◦
/s
Max. speed for joint 5
300◦
/s
Max. speed for joint 6
500◦
/s
Max. TCP linear velocity in joint mode more than 2,000 mm/s
Max. TCP linear velocity in Cartesian mode 500 mm/s
Max. power consumption 200 W
Input voltage 24 VDC
Operating ambient temperature range [5
◦
C, 45
◦
C]
Operating ambient relative humidity range
[10%,80%]
(non-condensing)
IP rating IP 40
Copyright c
2018 by Mecademic Inc.
Page 7 of 35

User Manual
135 135 38
120 70
R260
boundary for
wrist center
units: mm
Figure 3: The dimensions of the Meca500
Figure 3 shows the main dimensions of the Meca500. Note that all joints are at zero
degrees in the conguration drawn in black line. Also note that the gray zone is the area
attainable by the center of the robot's wrist (the intersection point of the last three axes),
for a xed angle of joint 1. This area, or even the volume obtained by sweeping this area
about the axis of joint 1 is NOT the workspace of the robot. The workspace of the robot
is a six-dimensional entity depending on the denition of your tool reference frame. The
workspace is the set of attainable poses (positions and orientations) of the tool reference
frame with respect to the robot's base. Even for a specic choice of a tool reference frame,
it is impossible to represent this six-dimensional workspace (read this tutorial of ours).
If you need the CAD les of the Meca500 (in STEP format), please contact us directly.
Alternatively, you can use one of several robot simulation and oine programming software
packages that include a model of our Meca500, including Visual Components and RoboDK.
Finally, as already mentioned, the power supply provided has an IEC C14 connector that
accepts an AC power cord with three-prong IEC C13 connector on one end, and your own
country's power plug on the other. You can connect this power cord to any AC source that
supplies voltage between 90 V and 264 V at frequency between 50 Hz to 60 Hz.
Page 8 of 35
Copyright c
2018 by Mecademic Inc.

User Manual
6 Installing the Meca500
You are surely eager to start using your Meca500. It is, however, imperative that you x
solidly the base of your robot arm before activating the robot.
B
WARNING:
Fix securely the robot's base via the mounting holes (Fig. 4a) with four M6
screws, on any at surface of a rigid, stationary and steady body.
Note that the robot will automatically detect the angle between the axis of joint 1 and
the gravity vector. Also, note that you can mount the robot's base on a mobile body (e.g.,
on the carriage of a linear guide), but only if you do not intend to move the robot's joints,
while the robot's base is moving with respect to the ground.
Next, you must solidly attach the power supply using four M6 screws (Fig. 5), at a
location suciently close to the robot's base to allow connection with the 2-meter DC cable
provided. However, unless you are using an external emergency stop wired via the D-SUB
115
90
100
75
4X thru holes for M6
units: mm
(a) Dimensions
(b) Connectors (c) Connectors properly attached
Figure 4: The base of the Meca500
Copyright c
2018 by Mecademic Inc.
Page 9 of 35

User Manual
Power
Status
Error
RESETE-STOP
Safety I/O
Port
Robot Power
24 VDC 8.34 A
AC Power
90-264 VAC
50-60 Hz
units: mm
4X thru counterbored holes for M6
120
90
75
100
48
68
Figure 5: Dimensions of the power supply
connector, you must x the power supply at a location that makes the integrated E-STOP
button readily accessible by an operator and outside the working range of the robot.
The following steps must then be executed before you can start using your Meca500:
1. Attach the circular connector of the Ethernet cable to the ETHERNET1 port on the
robot's base and connect the RJ-45 jack to your computer or router (Fig. 4b-c). The
two Ethernet ports on the robot's base act as a bridge, so you can daisy-chain several
Meca500 robots, or connect an Ethernet I/O module on the ETHERNET2 port.
2. Use the DC power cable provided to connect the unpowered power supply to the robot's
DC power connector (Fig. 4b-c). Make sure the connectors are completely screwed on
both sides, or else you may damage the robot controller. Then, connect the power
supply to your country-specic AC power cord (not provided by us). Only then, can
you connect the AC power cord to an AC outlet, and, if not already done, switch the
power supply on using its on/o button.
B
CAUTION:
•
Do not use any other power supply but the one provided, or else the warranty
will be voided and the CE certication no longer valid.
•
Always connect the DC power cable before connecting the power supply to
an AC outlet.
•
Always disconnect the power supply from the AC outlet (or switch it o)
before disconnecting the DC power cable.
•
Avoid un-plugging the DC power supply too often and always make sure both
connectors are completely screwed.
Page 10 of 35
Copyright c
2018 by Mecademic Inc.

User Manual
(a) Windows (b) Linux
Figure 6: Two examples of how to congure the IP address of your computer
4. The green LED on the power supply (next to Power) will be illuminate. Now, you
must provide power to the robot by pressing the RESET button on the power supply.
5. You will hear a clicking sound coming from the power supply, and the robot's LEDs
will start ashing for a few seconds while the robot's controller is booting. Once the
controller ready, the red LED on the robot's base will start ashing intermittently.
6. Depending on which of the two Ethernet ports was used in step 1, the Link/Act
IN (for ETHERNET1) or Link/Act OUT (for ETHERNET2) green LED should be
illuminated. If it is not, detach the Ethernet cable and repeat step 1.
7. Congure your computer with a static IP address. The way to do this diers from one
operating system to another. Figure 6 shows how to do this in Windows and in Linux.
8. Open a web browser, the latest version of either Google Chrome or Firefox only, and
type Meca500's default IP address
192.168.0.100
in the address bar.
9. Meca500's web interface should load instantaneously. If it doesn't, repeat the previous
step with a dierent browser.
It is also possible to change the robot's network conguration. This option is available
through the robot's web interface, which will be described in detail in Section 8. Here is the
procedure for doing so:
1. Click on the
Options
dropdown menu and then on
Settings
(Fig. 7).
2. Depending on your conguration, choose DHCP to automatically receive an address
from your router or Static to force a specic IP. You don't need to reboot the robot;
the new conguration will be applied as soon as you click on the
Save
button (Fig. 8).
Copyright c
2018 by Mecademic Inc.
Page 11 of 35

User Manual
7 Installing an end-eector
The Meca500 comes with a proprietary tool I/O (input/output) port located at the robot
extremity (Fig. 9a). However, this tool port is reserved uniquely for our electric gripper
MEGP 25. We do not share the pinout of this port or its custom-made communication
protocol. To install our gripper, refer to its user manual.
If you want to use any other end-eector with the Meca500, you will need to control it
independently from the Meca500. You can attach the cabling of your end-eector along the
robot arm using adhesive-backed tie mounts. Finally, you must x the end-eector to the
robot's ange (Fig. 9b) using four M3 screws and, optionally, one
3
locating pin, all of
properly selected length. The following rules should be respected:
B
WARNING:
•
Keep the robot un-powered while installing/removing a tool to its ange.
•
Do not overpass the robot payload (0.5 kg).
•
Securely fasten the tool to the robot ange.
Note that since joint 6 is multi-turn, there is no way of knowing the angle of joint 6 (even
approximately), unless the robot is activated and homed. Therefore, prior to mounting an
end-eector, it is important that you activate and home your robot, rotate joint 6 to its zero
position, and nally unpower the robot. However, if the screw on the ange of the robot
is not as in Fig. 9b when
θ6= 0◦
, then you need to follow the procedure described in the
subsection Homing of the programming manual.
(a) Closeup
Ø20
units: mm
Ø9 H6, É2.2
M3X0.5, É4
BCD 15.5
4X equally spaced
Ø3, É3.5
BCD 15.5
2X equally spaced
(b) Dimensions
Figure 9: The mechanical interface (ange) of the Meca500. The ange is the
20
disk,
inside the black isolation ring, and is the only one to rotate when joint 6 rotates.
Copyright c
2018 by Mecademic Inc.
Page 13 of 35

User Manual
B
CAUTION:
•
Make sure that joint 6 is approximately at
0◦
before attaching an end-eector.
•
Do not over-tighten the M3 screws.
•
Attach the tool cabling in such a manner that it obstructs as little as possible
the motions of the robot.
•
Unless you plug the connector of our own gripper, keep the cover (screw cap,
not shown in Fig. 9a) of the tool I/O port in place at all times.
8 Operating the robot
8.1 The web interface
Meca500's web interface is more or less the equivalent of the teach pendant's interface of a
traditional industrial robot. The interface is essentially an HTML 5 web page with JavaScript
and WebGL code, the CAD models of the robot links, and potentially the end-eector and
the environment (in binary STL format). All of these les reside in the robot's controller,
so you do not need to install anything on your computer.
The interface basically translates your mouse clicks and keyboard entries into proprietary
commands that are sent to the robot's controller. These are the same commands described in
the programming manual that you will eventually start sending from your own application,
written in C++, Java, Python or any other modern programming language. In addition,
the web interface displays the feedback messages received from the robot and, generally, the
virtual model of the actual robot.
The web interface is intended mainly for testing and writing simple programs. You must
create your own software application or program if you intend to use the robot for complex
tasks, such as interacting with inputs and outputs (in which case you also need a third-party
I/O module).
8.1.1 Overview
Figure 10 shows the main elements of the web interface. These are:
1. The main menu
2. The programming panel
3. The robot log panel
4. The quick command panel
5. The real-time jogging panel
6. The real-time pose of the robot end-eector and joint
positions
7. The 3D view of the robot, which moves in real-time
Page 14 of 35
Copyright c
2018 by Mecademic Inc.

User Manual
Figure 10: Overview of Meca500's web interface
8.1.2 Connection and disconnection
Once the web interface is loaded, the rst step is to connect it to the robot. So far, you have
only established an HTTP connection with the robot, but not activated the socket messaging
which is the only communication channel for controlling the robot via the web interface. You
can connect to the robot by either selecting the
J
checkbox in the programming panel, or
by selecting the Connection menu item in the main menu.
Figure 11: Connect/disconnect windows
The windows displayed in each of these two cases are shown in Fig. 11. The elements of
these windows are:
1. IP address of the robot, which is automatically set
2. Connection type, which is either
Control
for sending commands to the robot or
Mon-
itoring
for getting a real-time view of the robot's motion
3. Connection button
4. Disconnect button
Copyright c
2018 by Mecademic Inc.
Page 15 of 35

User Manual
For now, leave the Control radio button in the Connect window selected. The Monitoring
option can be used to see in real-time the motion of the robot when another client (other
than the web interface, e.g., Matlab running on the same PC) is controlling the actual robot.
8.1.3 The programming panel
The programming panel is used mainly for writing and executing very simple programs,
i.e., for testing. These programs are sequences of the proprietary commands described in
the programming manual. The robot's command interface does not support conditionals,
loops, or other ow control statements. The robot only accepts request commands (to get
information from the robot) and motion commands (to tell the robot to perform an action).
The panel also supports comments in C/C++ style (e.g., // and /* */).
For complex tasks, you must write a program outside the web interface (e.g., in your
preferred integrated development environment) that parses the robot's feedback, controls
the robot, and handles all ow control logic. For this, you can use any language that
supports communication over TCP/IP (e.g., C/C++, C#, Python, Java or even Structured
Text, in the case of a PLC).
Figure 12: The programming panel
Figure 12 shows the programming panel. The dierent elements of this panel are enu-
merated bellow:
1. Connection/disconnection checkbox,
J
2. Activation/deactivation checkbox,
Page 16 of 35
Copyright c
2018 by Mecademic Inc.
Other manuals for Meca500
7
This manual suits for next models
1
Table of contents
Other Mecademic Robotics manuals
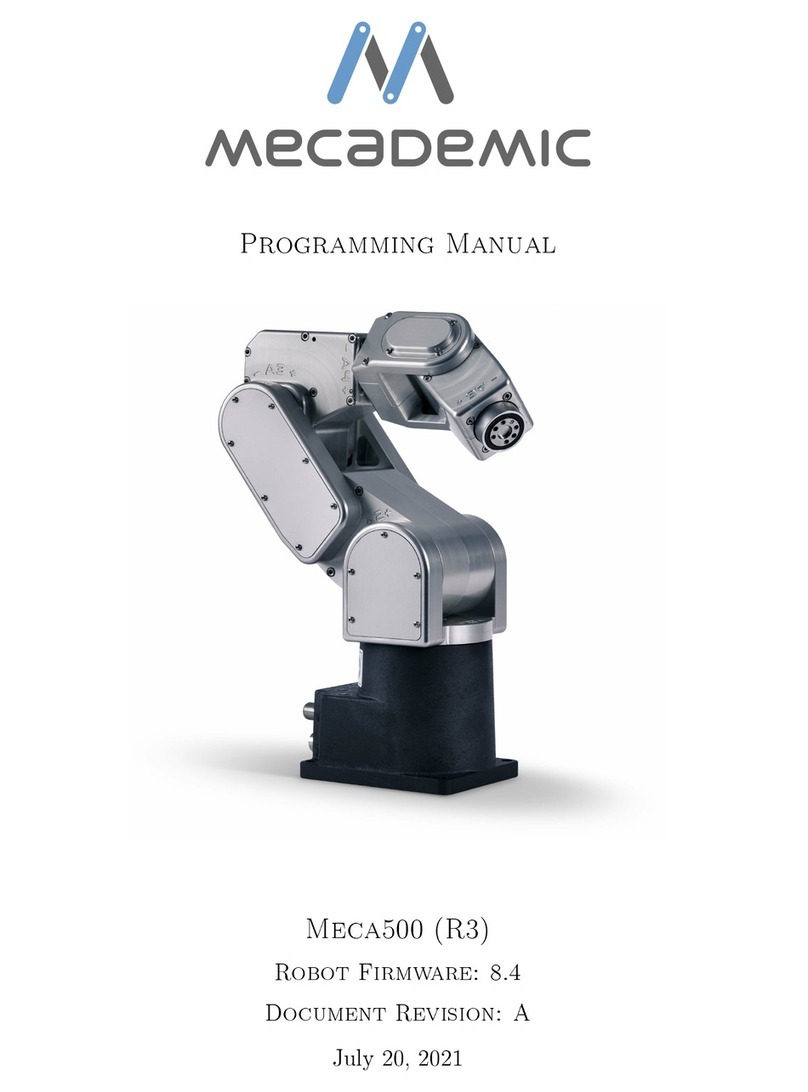
Mecademic
Mecademic Meca500 (R3) Owner's manual
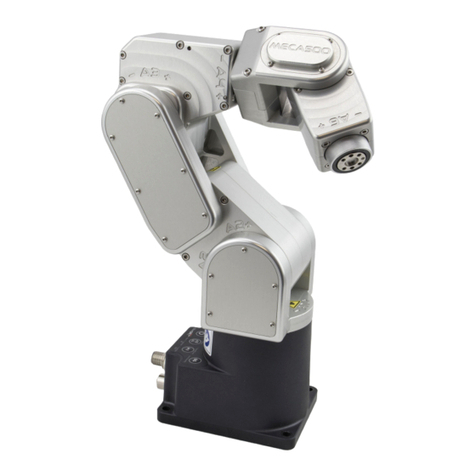
Mecademic
Mecademic Meca500 User manual
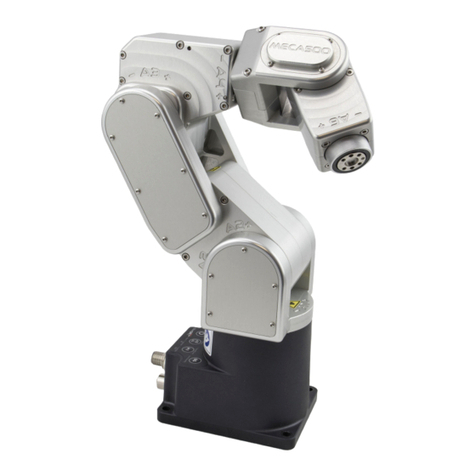
Mecademic
Mecademic Meca500 User manual
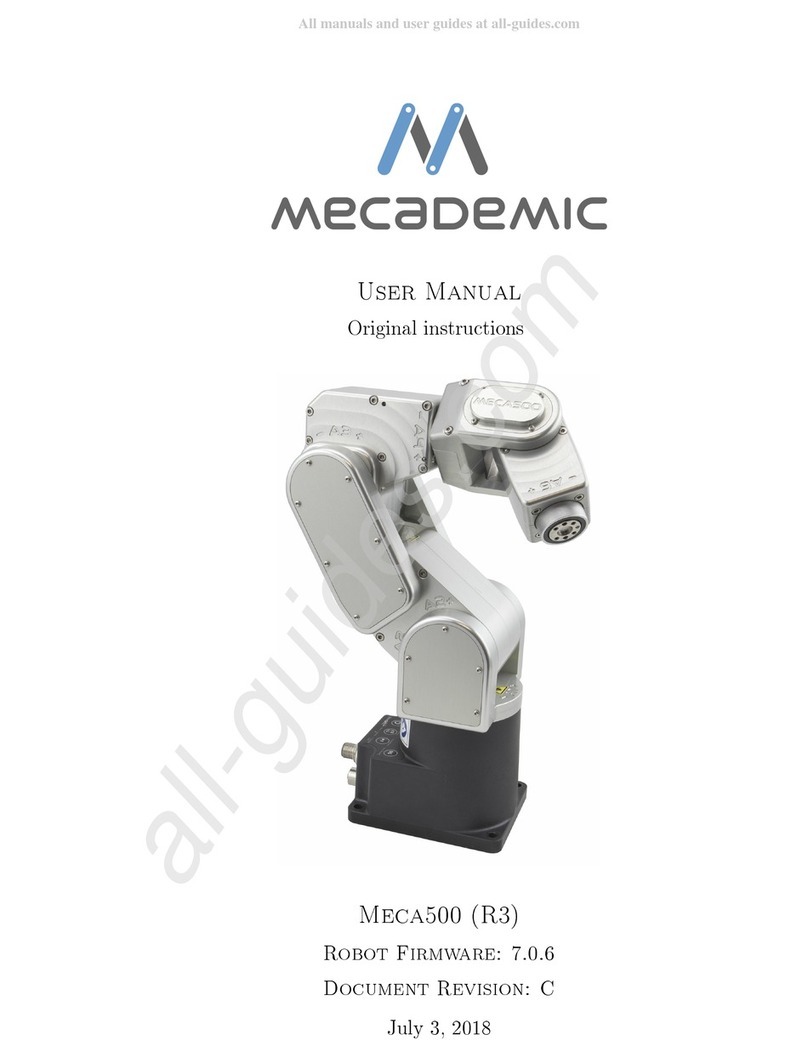
Mecademic
Mecademic Meca500 R3 User manual
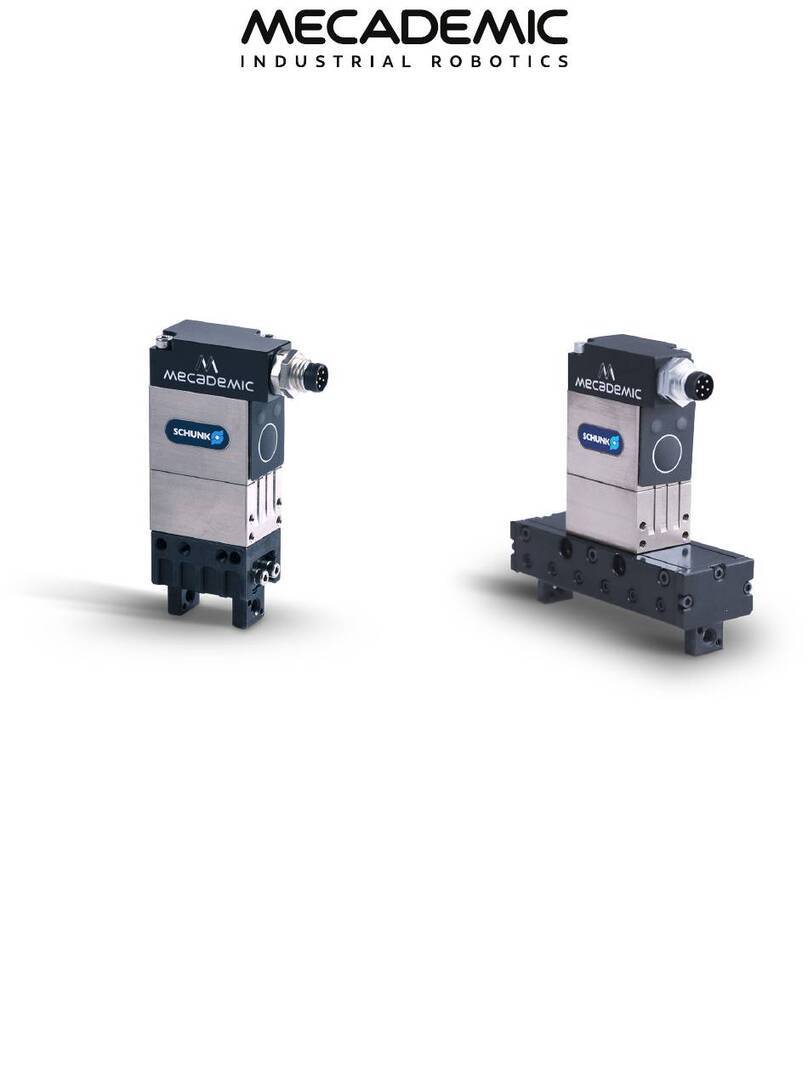
Mecademic
Mecademic MEGP 25E User manual
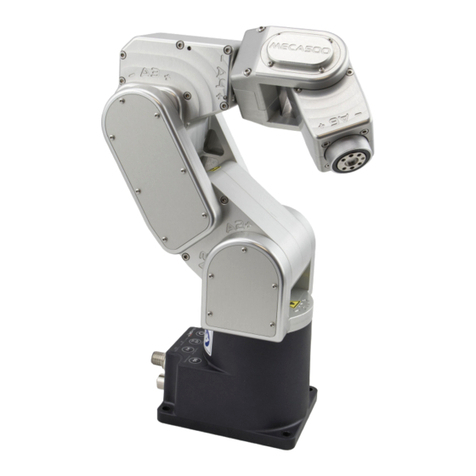
Mecademic
Mecademic Meca500 User manual

Mecademic
Mecademic Meca500 User manual
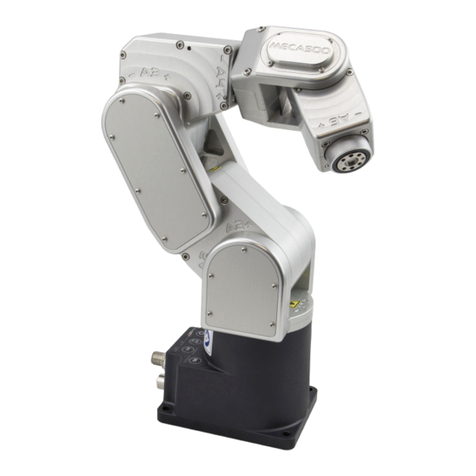
Mecademic
Mecademic Meca500 User manual
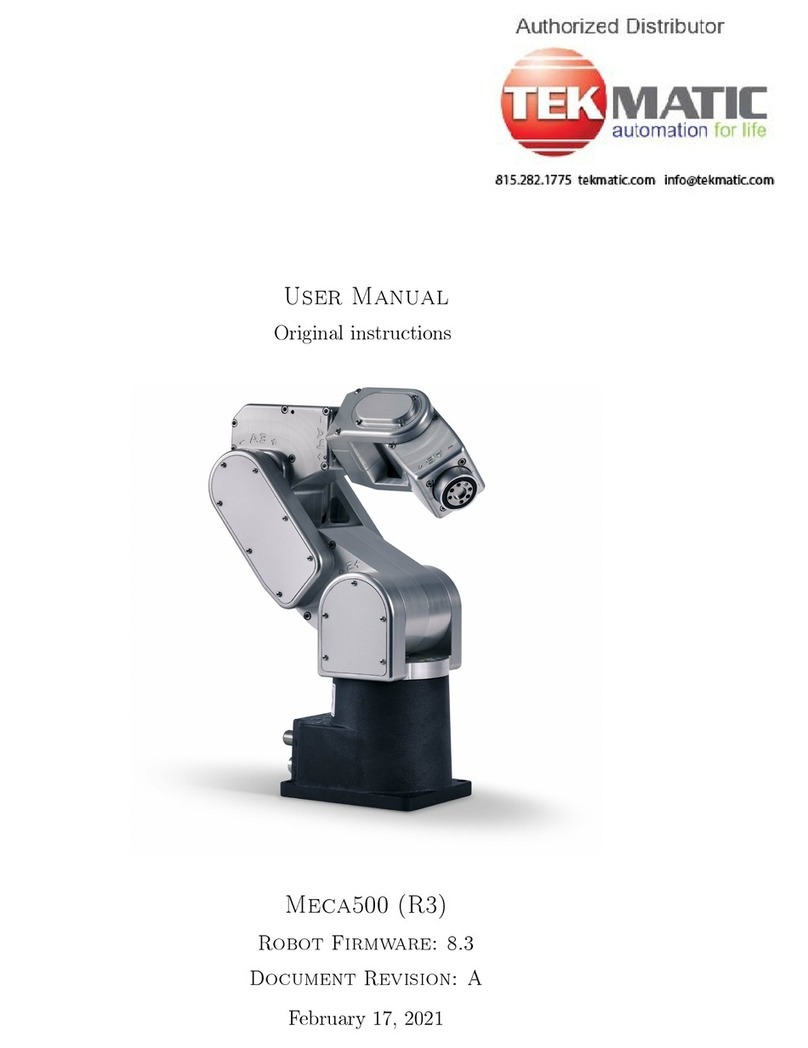
Mecademic
Mecademic Meca500 R3 User manual
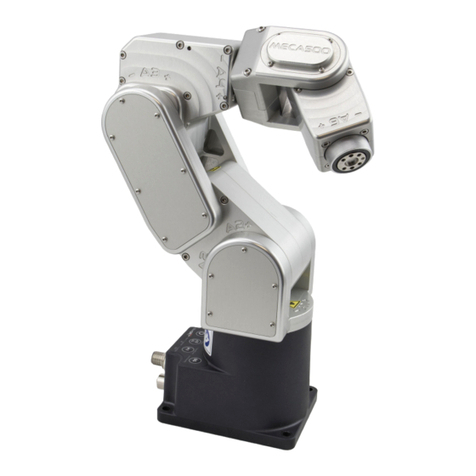
Mecademic
Mecademic Meca500 User manual