Metabo SMG ISO Series User manual













This manual suits for next models
4
Other Metabo Tools manuals
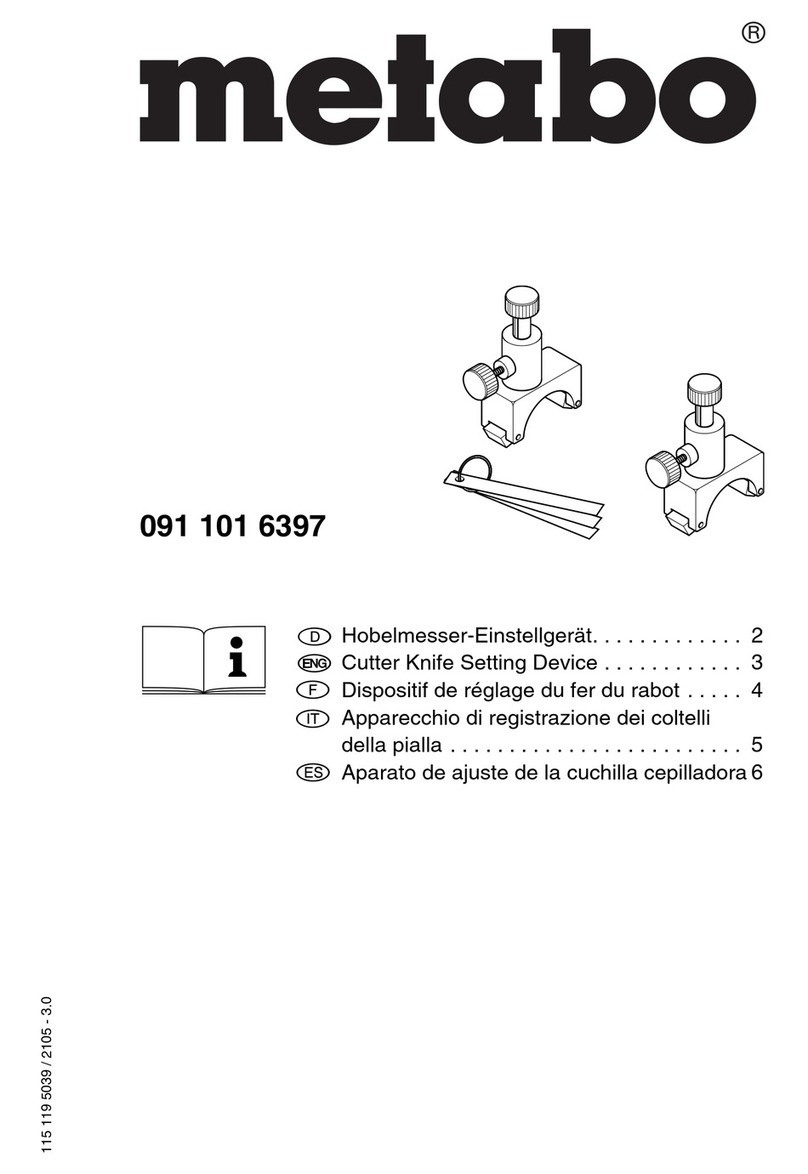
Metabo
Metabo Cutter Knife Setting Device 091 101 6397 User manual
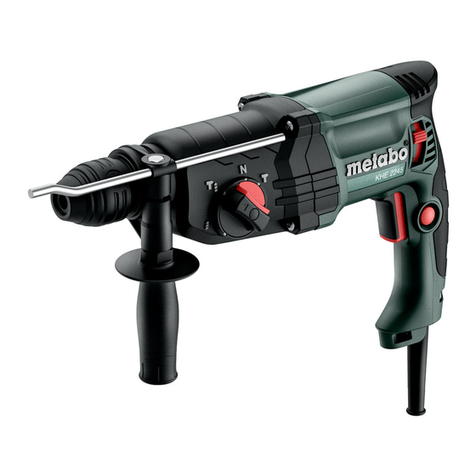
Metabo
Metabo KHE 2245 User manual
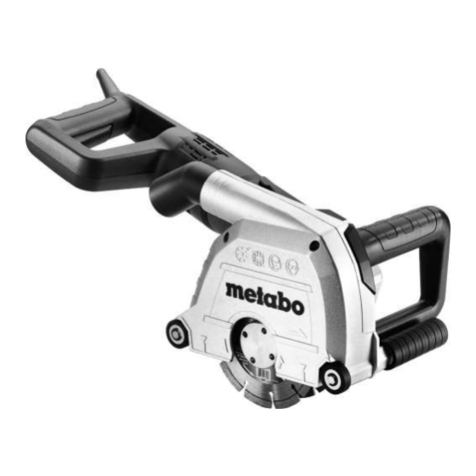
Metabo
Metabo MFE 40 User manual
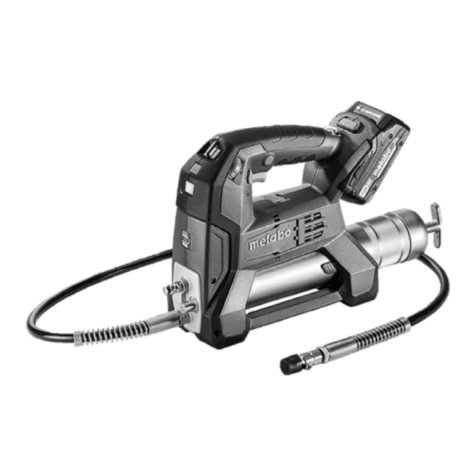
Metabo
Metabo FP 18 LTX User manual
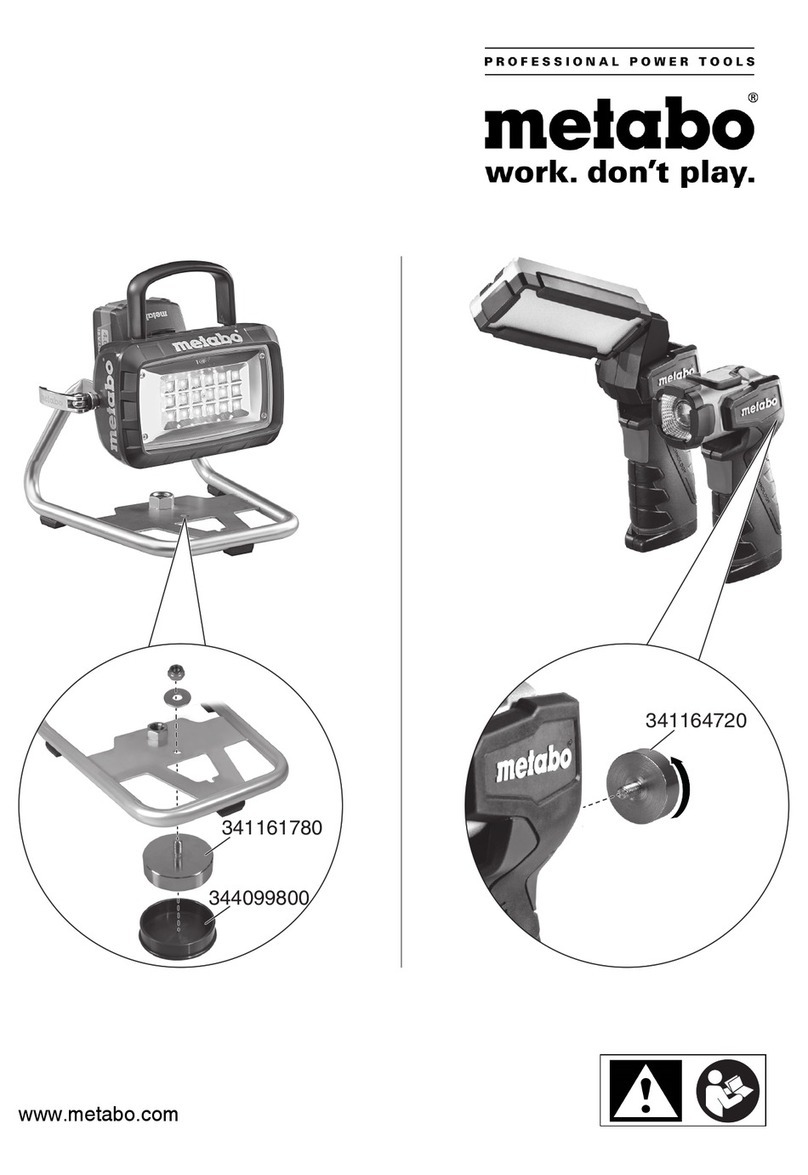
Metabo
Metabo 341161780 User manual
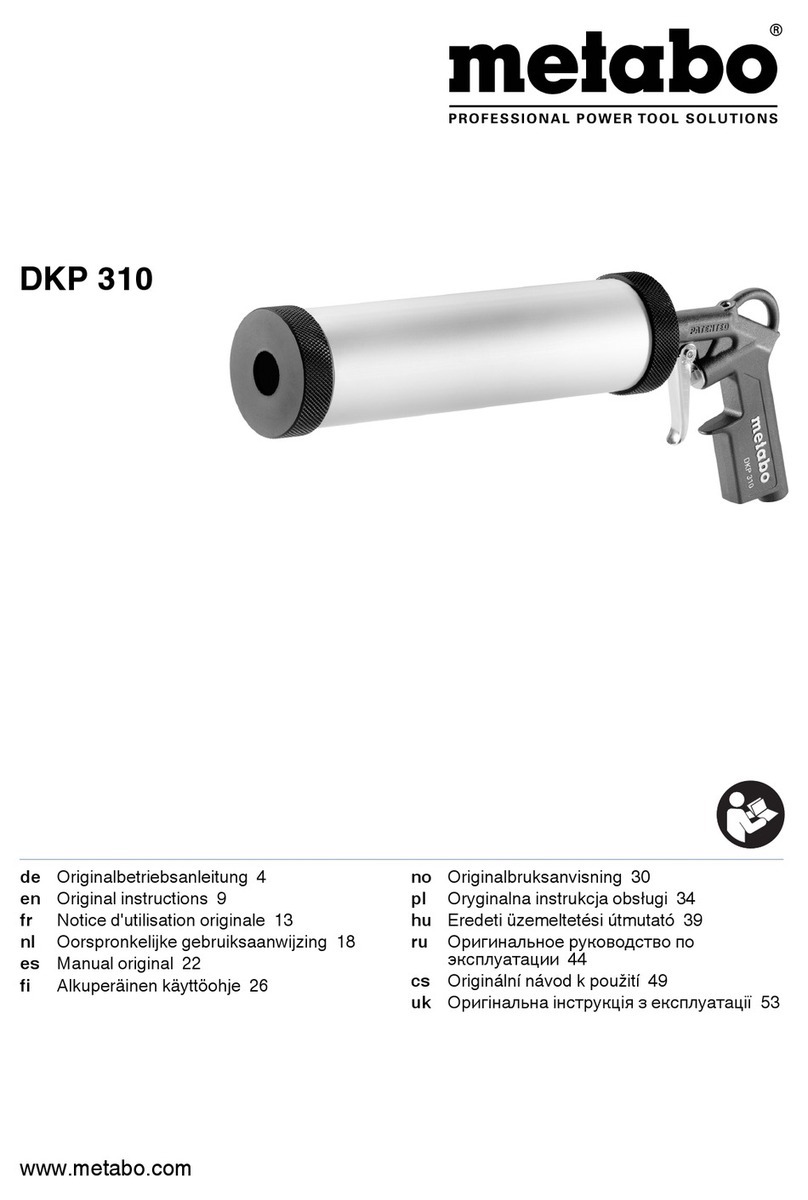
Metabo
Metabo DKP 310 User manual
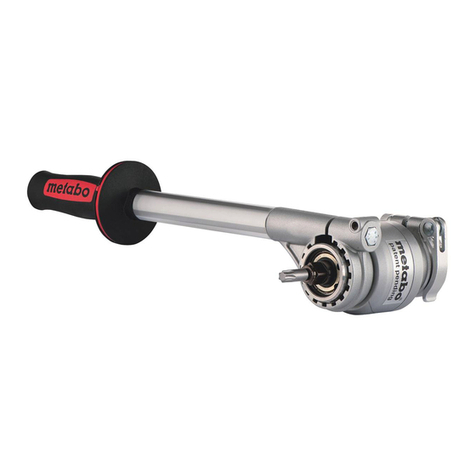
Metabo
Metabo PowerX3 User manual
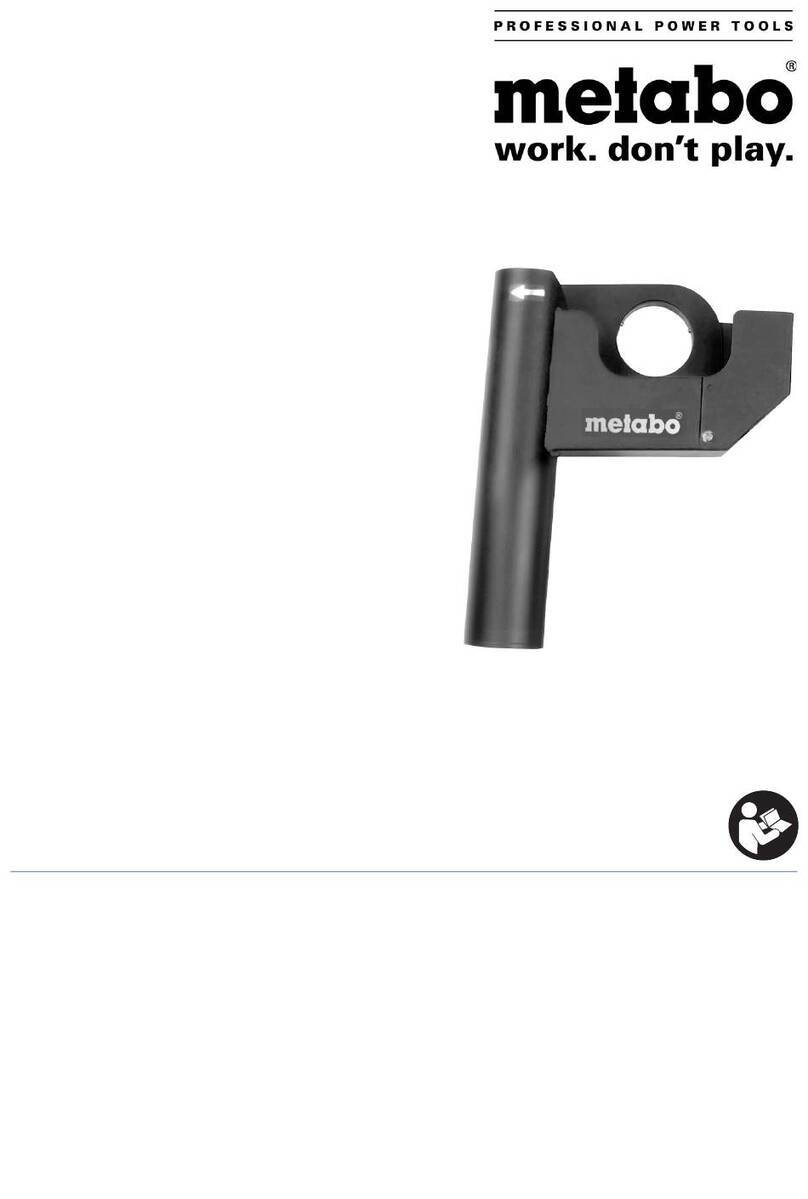
Metabo
Metabo 6.30845 User manual

Metabo
Metabo SR1250 K User manual

Metabo
Metabo KHEV 5-40 BL User manual

Metabo
Metabo MHS 5000 Set User manual

Metabo
Metabo NFR 18 LTX 90 BL User manual
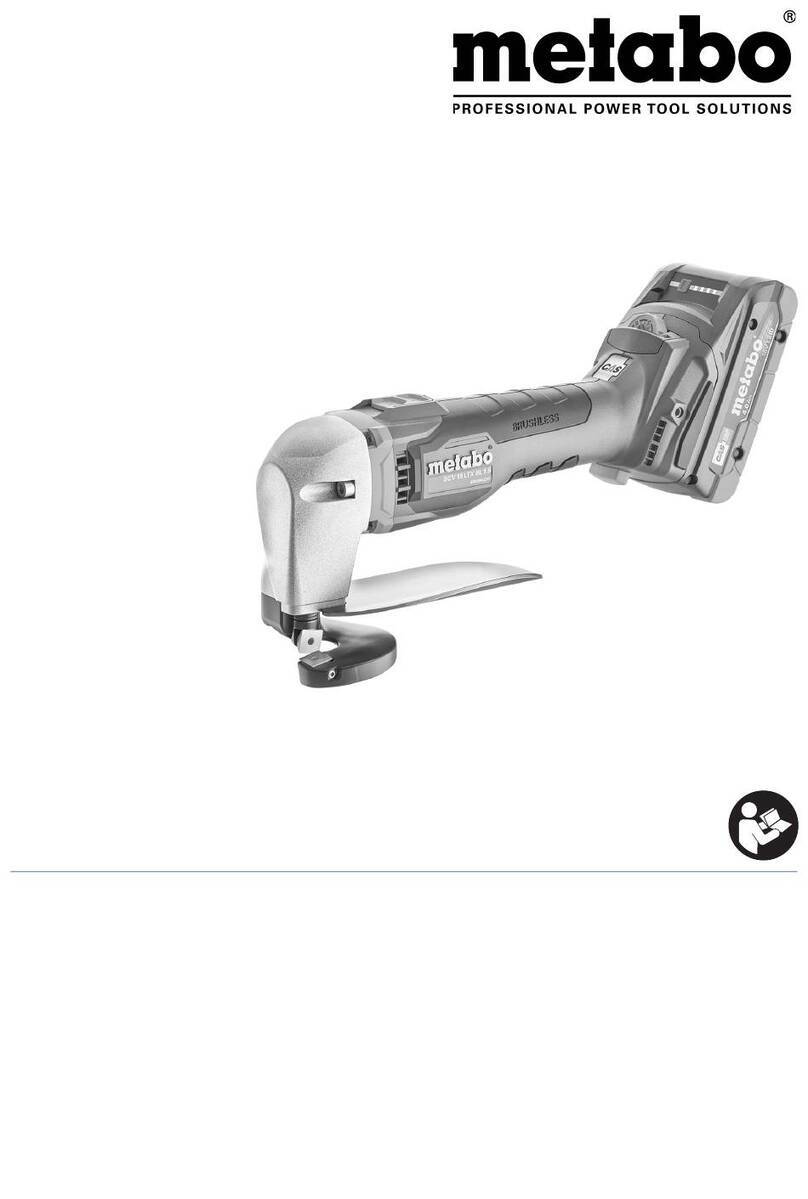
Metabo
Metabo NIV 18 LTX BL 1.6 User manual
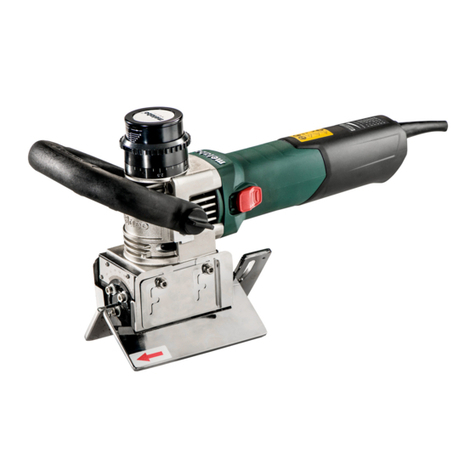
Metabo
Metabo KFM 15-10 F User manual
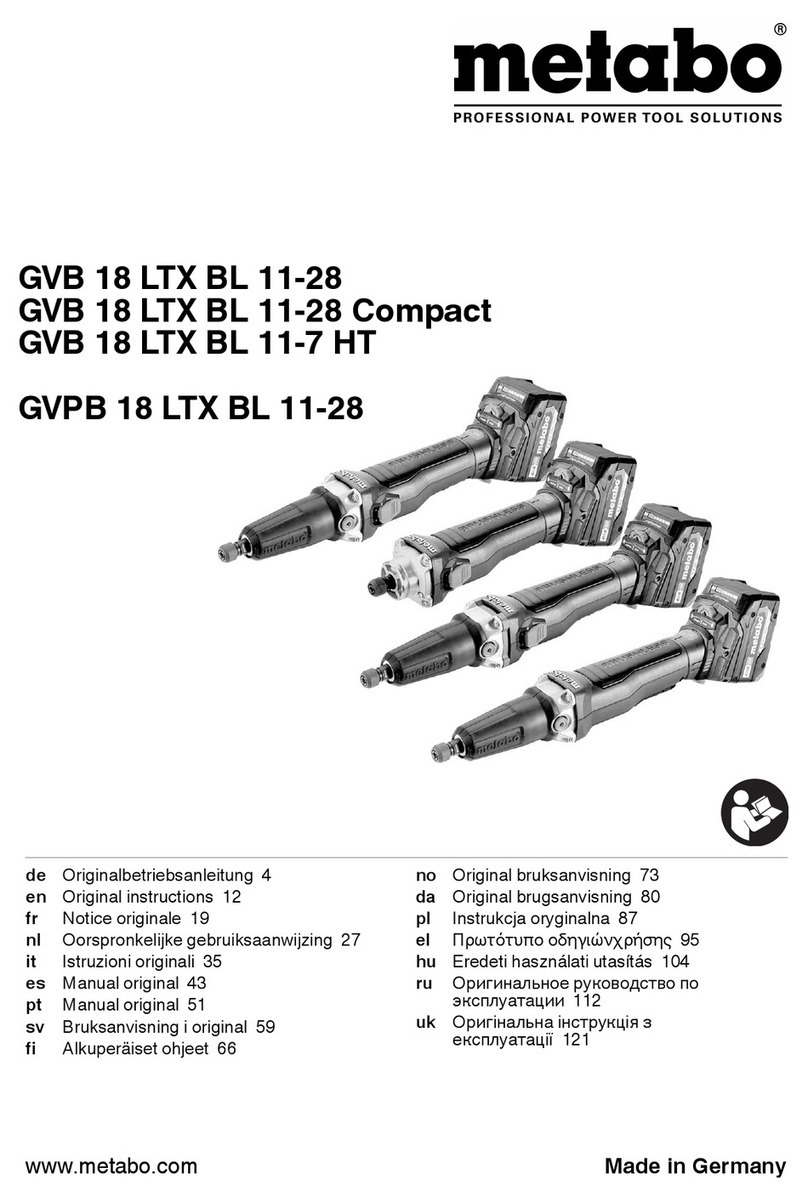
Metabo
Metabo GVB 18 LTX BL 11-28 User manual
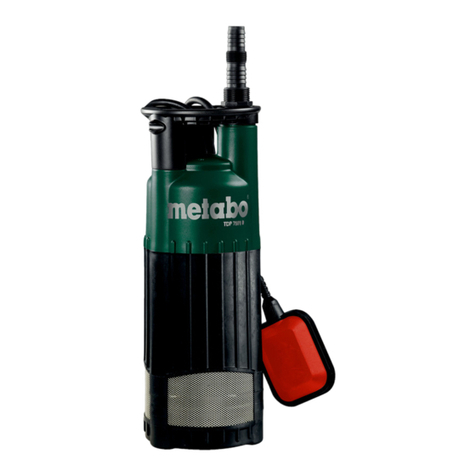
Metabo
Metabo TDP 7501 S User manual
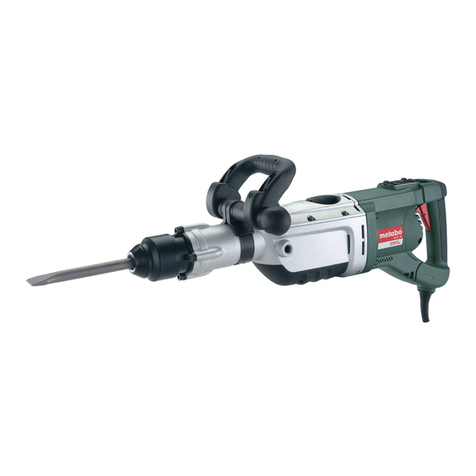
Metabo
Metabo MHE 96 User manual
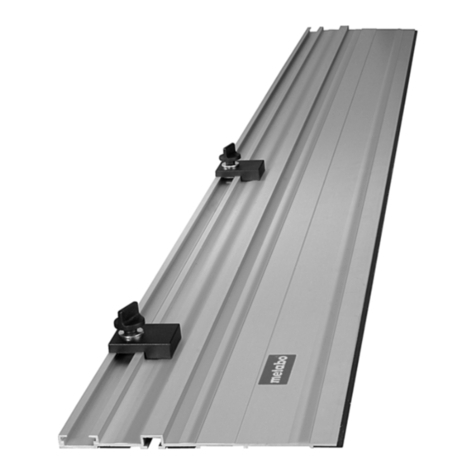
Metabo
Metabo 6.31213 User manual
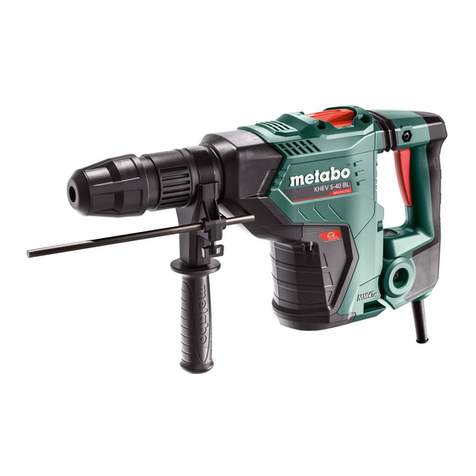
Metabo
Metabo KHEV Series User manual
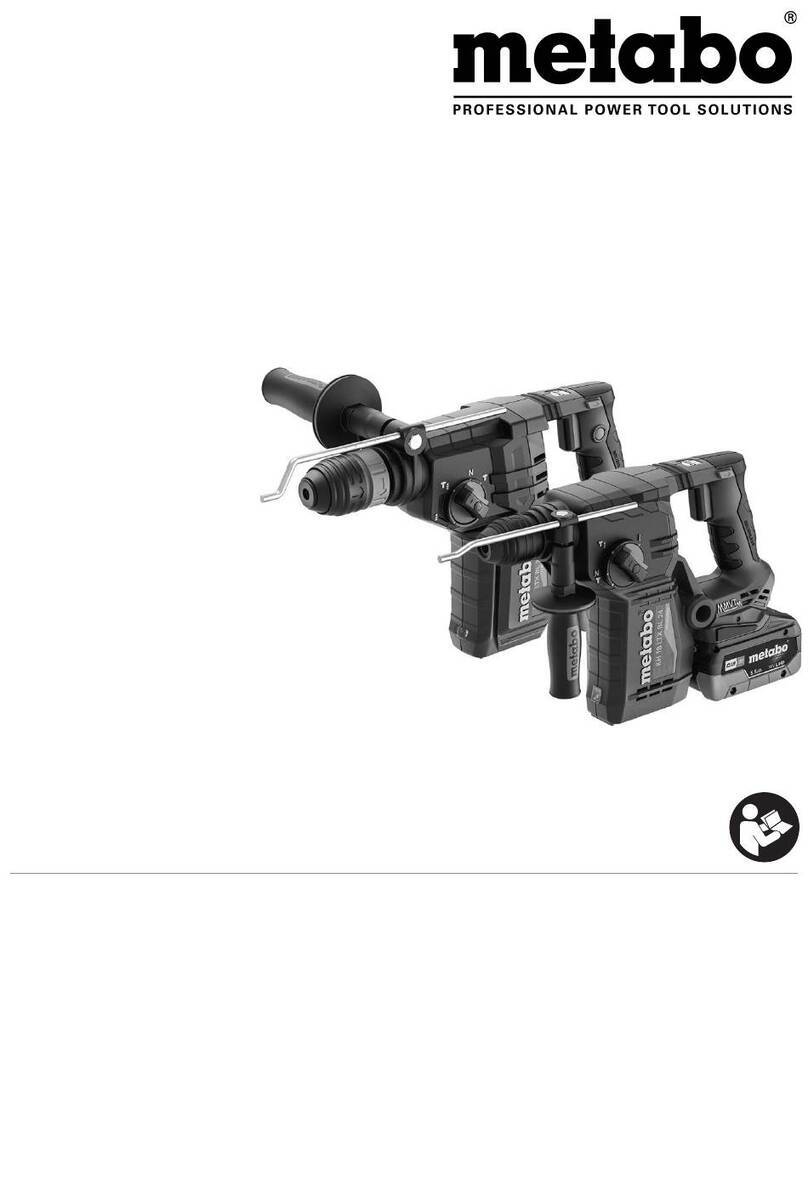
Metabo
Metabo KH 18 LTX BL 24 User manual