Micronor MR380-0 User manual

© COPYRIGHT 2016-2019, MICRONOR INC.
CAMARILLO, CALIFORNIA
UNITED STATES OF AMERICA
MR380-0
Fiber Optic Signaling
OEM PCB Controller
Instruction Manual
DOC: 98-0380-300
Revision B3 dated 9/27/2019
MICRONOR INC.
900 Calle Plano, Suite K
Camarillo, CA 93012 USA
T (805) 389-6600
F (805) 389-6605
sales@MICRONOR.com
www.MICRONOR.com
For Support in Europe:
MICRONOR AG
Pumpwerkstrasse 32
CH-8105 Regensdorf
Switzerland
T +41-44-843-4020
F +41-44-843-4039
sales@MICRONOR.ch
www.MICRONOR.com
Notice of Proprietary Rights
The design concepts and engineering details embodied in this manual, which are the property of MICRONOR INC.,
are to be maintained in strict confidence; no element or detail of this manual is to be spuriously used, nor disclosed,
without the express written permission of MICRONOR INC. All rights are reserved. No part of this publication may
be reproduced, stored in a retrieval system, or transmitted in any form or by any means, electronic, mechanical,
photocopying, recording, or otherwise, without prior written permission from MICRONOR INC.

MR380-0 PCB Signaling OEM Controller Manual
Page 2 of 19
Revision History
REV
Date
Notes
A
2/10/2016
Initial Release
B
8/1/2016
Update for New Terminal Plug
B1
10/20/2016
Added Explosive Atmosphere specification
B2
3/7/2017
Added Extended Temperature model MR380-0-1E
B3
9/27/2019
Added Updated MR380 Declaration of Conformity

MR380-0 PCB Signaling OEM Controller Manual
Page 3 of 19
Table of Contents
1. Product Description .......................................................................................................... 4
1.1 Fiber Optic Switch Sensor Controller Board ............................................................... 4
1.2 Fiber Optic Controller Board ...................................................................................... 5
1.3 Part Numbering .......................................................................................................... 5
1.4 Functional Description ................................................................................................ 6
2. Initial Preparation .............................................................................................................. 7
2.1 Unpacking and Inspection .......................................................................................... 7
2.2 Damage in Shipment .................................................................................................. 7
2.3 Standard Contents...................................................................................................... 7
3. Installation and Operation................................................................................................. 8
3.1 Mounting the Sensor Unit........................................................................................... 8
3.2 Mounting the MR380-0 Controller PCB ...................................................................... 8
3.3 Optical Connections to the MR380-0 Controller......................................................... 9
3.4 Electrical Connections To MR380-0 Controller ......................................................... 10
3.5 Interfacing with an external Relay ............................................................................. 11
4. Warranty Information....................................................................................................... 12
5. Specifications .................................................................................................................. 13
5.1 MR380-0 OEM Signaling Controller.......................................................................... 13
6. Reference Documents..................................................................................................... 15
6.1 MR380-0 OEM Controller Reference Drawing .......................................................... 15
6.2 MR386 Switch Reference Drawing ............................................................................ 15
6.3 MR380 Declaration of Conformity............................................................................. 15
Figures
Figure 1. MR380 Fiber Optic Signaling Devices........................................................... 5
Figure 2. Block-Diagram MR380-0 Controller Board.................................................... 6
Figure 3. Keep LC Duplex connector ends protected when not in use ....................... 8
Figure 4. Dimensions of MR380-0 Controller PCB ...................................................... 8
Figure 5. Make optical connection using LC-Duplex optical connector ....................... 9
Figure 6. Layout of MR380-1 PCB.............................................................................. 10
Figure 7. External Relay Connection .......................................................................... 11

MR380-0 PCB Signaling OEM Controller Manual
Page 4 of 19
1. Product Description
1.1 Fiber Optic Switch Sensor Controller Board
A fiber optic switch works on the basis of interrupting a light beam when a certain event occurs
and the switch is activated. Although switches take on various forms such as, Toggle, E-STOP,
Push-Button and so on, the principle of sensing the switch state remains the same via
interruption of the optical beam. MICRONOR has implemented the concept by using a transmit
fiber and a receive fiber. The transmitter sends a constant light level via the transmit fiber and
the receive fiber guides the light back. When the switch is not activated, most of the light is
guided back to the receiver. When the switch is activated, little or no light is coupled back to
the receiver.
The MICRONOR Fiber Optic switches are immune to EMI/RFI and can be deployed at great
distances from the electrical controller. Applications include:
•MRI machines operate under an extremely strong electromagnetic field. Special switches
are manufactured to be entirely free of metallic materials and, thus, will not interfere with
the MRI imaging process.
•Pipe and tube welding produces extreme interference while the welding process is
active
•Surgical robots must perform 100% reliably
•Oil & Gas since there is no sparking
•Aerospace actuators operating in and around other noise generating avionics
•Aerial Tramways, Gondolas, Skilifts etc, because immunity to lightening.
An all-optical, non-electronic passive solution, such as the fiber optic switch, provides complete
immunity to such interferences.

MR380-0 PCB Signaling OEM Controller Manual
Page 5 of 19
1.2 Fiber Optic Controller Board
The MR380-0 Controller Board is intended for the OEM user in support of deployment of the
various Fiber Optic Signaling products. The OEM PCB contains a stabilized transmitter and a
sensitive optical receiver. There are two digital outputs
a.) 5V logic Level signals a High when optical power is received.
b.) Open-collect output for activating an external relay (or other electrical load) when
sufficieant optical power is received.
This universal PCB may be used in conjunction with many of the MICRONOR signaling devices.
The MR380-0 is intended for OEM applications where the PCB can be mounted into a suitable
enclosure and where it is sufficiently protected from the environment such as water and dust or
similar influences. Optically the interface board is compatible with OM1 (62.5µm/125µm) and
OM3 (50µm/125µm) fiber cabling.
1.3 Part Numbering
The part number is MR380-0-1. The last digit (1) defines the operating wavelength as 850nm.
Figure 1. MR380 Fiber Optic Signaling Devices

MR380-0 PCB Signaling OEM Controller Manual
Page 6 of 19
1.4 Functional Description
The controller board sends a steady stream of optical pulses at approx. 150kHz to 300kHz
frequency. The returned optical signal strength determines wether the electrical output is
activated. When sufficient light is received, the outputs are activated.
The optical power is internally monitored and held at a constant level over the full operating
temperature range. The factory set level is -9dBm coupled into a OM1 fiber (62.5/125µm) and
typically -11dBm is coupled into am OM3 fiber (50/125µm).
The receiver sensitivity is set at -25dBm.
For system planning the dynamic range for OM1 fiber is 15dB and for OM3 fiber it is -13dB.
Figure 2. Block-Diagram MR380-0 Controller Board

MR380-0 PCB Signaling OEM Controller Manual
Page 7 of 19
2. Initial Preparation
2.1 Unpacking and Inspection
The unit was carefully inspected mechanically and electrically before shipment. When received,
the shipping carton should contain the following items listed below. Account for and inspect
each item before the carton is discarded.
The PCB is an electronic Assembly and susceptible to ESD. Please use appropriate
grounding and caution when handling the PCB.
In the event of a damaged product, write or call your nearest MICRONOR sales office.
Please retain the shipping container in case re-shipment is required for any reason.
2.2 Damage in Shipment
If you receive a damaged product you should:
1) Report the damage to your shipper immediately.
2) Inform MICRONOR
3) Save all shipping cartons.
Failure to follow this procedure may affect your claim for compensation.
2.3 Standard Contents
MR380-0 OEM Controller Board:
•PCB board with built-in Duplex LC interface and 3.5mm contact strip.
•CamdenBoss P/N CTB1301/6A
6C, Screw-Type Terminal Plug, 5mm Contact Spacing
Note: The Terminal plug may be excluded for customers with special contract
agreements.
•Instruction Sheet
This Instruction Manual can be downloaded from www.micronor.com

MR380-0 PCB Signaling OEM Controller Manual
Page 8 of 19
3. Installation and Operation
3.1 Mounting the Sensor Unit
When installing the sensor, be careful not to bend the fiber excessively. It is recommended to
keep the minimum bend radius 25mm (1”) or larger. Ensure that the fiber outlet at the switch is
protected from excessive pulling or bending.
Figure 3. Keep LC Duplex connector ends protected when not in use
Make sure that the fiber optic connector tips are always covered when not in use. Always clean
and inspect the connector ends before mating to interface.
Be sure to use proper fiber optic cleaming tools and procedures such as the
MICRONOR MR321C Cleaning Kit. Improper tools and/or processes may damage or
contaminate the optical interface.
3.2 Mounting the MR380-0 Controller PCB
The controller PCB should be mounted on 4 standoffs.
Clearance shall be available for access to the Fiber Optic Interface.
The mounting holes are suitable for #2-56 or M2.5 screws.
The mounting holes are electrically connected to GND.
Consult Reference Drawing 98-0380-15 for more information
Figure 4. Dimensions of MR380-0 Controller PCB

MR380-0 PCB Signaling OEM Controller Manual
Page 9 of 19
3.3 Optical Connections to the MR380-0 Controller
A duplex fiber optic cable is used to interconnect the sensor and controller. The sensor
incorporates a 1.5m optical pigtail (or as specified by customer). If a longer connection to the
controller is required, then a fiber optic extension cable may be used.
Remove the dust cap form both the cable connector and the optical port on the controller.
Insert the LC connector as shown. There should be a positive click when the connector is
engaged properly.
Do not force the Fiber Optic Connector!
Figure 5. Make optical connection using LC-Duplex optical connector

MR380-0 PCB Signaling OEM Controller Manual
Page 10 of 19
3.4 Electrical Connections To MR380-0 Controller
The may be unit is powered with any voltage between 5V and 24V DC.
Current consumption is typ. 8mA at 5V DC and +12mA at 24V DC excluding any external load.
NOTE: Mounting holes are internally connected to GND.
When all connections are made, than apply DC voltage in the range of +5V to max +24V.
If the sufficient optical power is received, then the onboard LED will light up. It is OFF when no
optical power is received.
CamdenBoss P/N CTB1301/6A (supplied)
6C, Screw-Type Terminal Plug, 5mm Spacing
PIN
Function
1
+5V to +24V DC Power
Supply
2
GND
3
+5V Logic Out
4
GND
5
DC Supply (Out)
6
Open Collector Out
Figure 6. Layout of MR380-1 PCB
1

MR380-0 PCB Signaling OEM Controller Manual
Page 11 of 19
3.5 Interfacing with an external Relay
An external relay may be connected to the open-collector terminal (6).
The maximum voltage allowed for this output is up to the power supply Voltage.
If the pull-up resistor R8 is removed, then voltages exceeding the V Supply up to 48V are
allowed.
The current load shall not exceed 180mA.
Figure 7. External Relay Connection
R18 may be removed

MR380-0 PCB Signaling OEM Controller Manual
Page 12 of 19
4. Warranty Information
Warranty
MICRONOR INC. warrants this product to be free from defects in material and workmanship for
a period of 1 (one) year from date of shipment. During the warranty period we will, at our option,
either repair or replace any product that proves to be defective.
Applying improper supply voltage (greater then 24VDC or reverse polarity) voids
the warranty.
To exercise this warranty, write or call your local MICRONOR INC. representative, or contact
MICRONOR INC. headquarters. You will be given prompt assistance and return instructions.
Send the product, transportation prepaid, to the indicated service facility. Repairs will be made
and the product returned transportation prepaid. Repaired products are warranted for the
balance of the original warranty period, or at least 90 days. MICRONOR INC. resreves the option
to either repair, or replace product.
Limitations of Warranty
This warranty does not apply to defects resulting from unauthorized modification or misuse of
any product or part. This warranty also does not apply to Fiber Optic Connector interfaces,
improper mouning of the PCB, fuses or AC line cords. This warranty is limited to the maximum
price paid by purchaser to MICRONOR INC, excluding any shipping, transportation or duties.
This warranty is in lieu of all other warranties, expressed or implied, including any implied
warranty of merchantability of fitness for a particular use. MICRONOR INC. shall not be liable
for any indirect, special or consequent damages.
Contact Information:
MICRONOR Inc. T +1-805-389-6600
900 Calle Plano, Suite K F +1-805-389-6605
Camarillo, CA 93012 Email sales@micronor.com
USA URL www.micronor.com
For Europe:
MICRONOR AG T +41-44-843-4020
Pumpwerkstrasse 32 F +41-44-843-4039
CH-8015 Regensdorf Email sales@micronor.ch
SWITZERLAND URL www.micronor.ch

MR380-0 PCB Signaling OEM Controller Manual
Page 13 of 19
5. Specifications
5.1 MR380-0 OEM Signaling Controller
Electrical Interface
Description
Specification
Connector
CamdenBoss P/N CTB1301/6A
6C, Screw-Type Terminal Plug, 5mm Contact Spacing
Logic Output
High: 4.5V min. (2k Ohm Load)
Low: 0.25V max.
Open Collector Output
Maximum Load Voltage 24V
Maximum Current 180mA Protected by resettable fuse)
Power Supply
Voltage
Current Consumption
+5VDC to +24V DC maximum
8mA max. at 5V DC, 12mA at +24V and R8 installed
Optical Interface
Specification
Connectior
LC Duplex, PC Polish
Fiber Type (Duplex)
62.5/125µm 0.275NA OM1 Multimode Fiber or
Or 50/125µm 0.22NA OM2/OM3 Multimode Fiber
Optical Output Power
OM1
OM3
-9dBm (0.11mW) average (850nm VCSEL diode)
-11dBm (0.080mW) average
Receiver Sensitivity
OM1
OM3
-25dBm or better
-25dBm or better
Switching Hysteresis
1.5dB typical
Optical Dynamic Range
Maximum Link Loss
OM1 = 15dB ; OM3 = 13dB
Link lengths up to 1.5km are typically achievable. Refer to
Application Note AN118 for more information on Link Loss.
Operating Wavelength
850nm
Optical Output Power
< -8dBm (0.158mW) average
Laser Safety Classification
Class 1
Explosive Atmospheres
Inherently Safe Optical Radiation
Ex Classification
Controller shall be installed in non-hazardous location Only
Power supply to Controll shall be current limited to 200mA
IECEx Test Report GB/CML/ExTR 16.0105.00/00
ATEX
EPL Mb/Gb/Gc/Db/Dc
IEC Ex
EPL Mb/Gb/Gc/Db/Dc
NEC
Exempt
Environmental
& Mechanical
Specification

MR380-0 PCB Signaling OEM Controller Manual
Page 14 of 19
Temperature
Standard (MR380-0-1): -10°C to +65°C
Extended (MR380-0-1E): -40°C to +70°C
Humidity
0% to 85% RH (non-condensing)
Ingress Protection
IP00 (none)
Vibration/Shock
Performance depends on mounting. Consult factory when
designing for high shock and vibration environment.
Mounting
4x #2-56 or M2.5 screws
Mounting pattern 1.60” x 2.60 inches
Size
5.08 x 7.62cm (2.00 x 3.00”)
Weight
25g (1oz)
Specifications subject to change without notice

MR380-0 PCB Signaling OEM Controller Manual
Page 15 of 19
6. Reference Documents
Documents appear on the following pages.
6.1 MR380-0 OEM Controller Reference Drawing
6.2 MR386 Switch Reference Drawing
6.3 MR380 Declaration of Conformity

3.00
2.600
.20
2.00
.200
1.600
4X
.096 THRU ALL
.60
.53
1.20
.60
.07
.43
5.0mm PITCH
PIN 1
CONNECTOR COVERS
2 WARNING: KEEP CONNECTOR COVERS IN
PLACE DURING STORAGE TO PROTECT
OPTICAL CONNECTOR
1 WARNING: AVOID SHARP BENDS IN FIBER
CABLING KEEP BEND RADIUS GREATER THAN
0.5 INCH [13MM].
NOTES: UNLESS OTHERWISE SPECIFIED
WAVELENGTH
1
MULTIMODE 850nm
PRODUCT
0
PCB CONTROLLER
PART NUMBER ORDERING CODE
MR380 -
X
- X
X
REVISIONS
REV.
DESCRIPTION
DATE
APPROVED
A
NEW RELEASE
8/4/2016
AD
CONTROLLER
OEM
A1
DO NOT SCALE DRAWING
MR380-0
SHEET 1 OF 1
4/28/16
A DU
UNLESS OTHERWISE SPECIFIED:
SCALE: 2:1
WEIGHT:
REV
DWG. NO.
C
SIZE
TITLE:
MICRONOR INC.
CAMARILLO, CA (805) 389-6600
NAME
DATE
COMMENTS:
Q.A.
MFG APPR.
ENG APPR.
CHECKED
DRAWN
FINISH
MATERIAL
INTERPRET GEOMETRIC
TOLERANCING PER:
DIMENSIONS ARE IN INCHES
TOLERANCES:
FRACTIONAL
ANGULAR: MACH
BEND
TWO PLACE DECIMAL
.01
THREE PLACE DECIMAL
.004
APPLICATION
USED ON
NEXT ASSY
PROPRIETARY AND CONFIDENTIAL
THE INFORMATION CONTAINED IN THIS
DRAWING IS THE SOLE PROPERTY OF
MICRONOR INC. ANY REPRODUCTION IN
PART OR AS A WHOLE WITHOUT THE
WRITTEN PERMISSION OF MICRONOR INC.
IS PROHIBITED.
Temperature Range
Blank
E
Standard, -10C to +65C
Extended, -40C to +70C
A1
DNH

Page 1of 18
Declaration of Conformity (EU)
We, the manufacturer,
Micronor Inc.
900 Calle Plano, Suite K, Camarillo, CA 93012, USA
Telephone +1-805-389-6600, Email sales@micronor.com
declare that this DoC is issued under our sole responsibility and belongs to the following
products:
•Fiber optic switch and signaling system, consisting of:
•MR380-0, MR380-1, MR380-2 or MR382-1, Controller
•MR380 series Sensor, MR381/MR382/MR383/MR384/MR385/MR386/MR387
That the equipment is in conformity with the following relevant European Union
harmonization legislation:
•Equipment for Potentially Explosive Atmospheres Directive (ATEX), 2014/34/EU
•Electromagnetic Compatibility Directive (EMC), 2014/30/EU
•Low Voltage Directive (LVD) 2014/35/EU
to which this declaration relates in conformity with the following standards or other
normative documents (latest version of EN or corresponding IEC document used per
Appendix C):
•
EN 60079-0:2018
•EN 60079-14:2014
•EN 60079-28:2015
•EN 60825-1:2014
•EN 61010-1:2010
•EN 61000-6-2:2005+AC:2005
•
EN 61000-6-4:2007+A1:2011
Certification Agency
•Certification Management Ltd, EU Notifying Body 2503, IEC Ex Certification Body
•CML Evaluation Report R1198C, GB/CML/ExTR 16.0130/00
Signed for and on behalf of:
Camarillo, CA 2019-09-27 Dennis Horwitz, VP
Ref: J:\Declaration of Conformity\MR340 Controller DOC\MICRONOR_98-0340-09_A_MR340 Declaration of Conformity_DRAFT_22-March-2019.docx

Page 2 of 18
Declaration of Conformity (IECEx and North America)
We, the manufacturer,
Micronor Inc.
900 Calle Plano, Suite K, Camarillo, CA 93012, USA
Telephone +1-805-389-6600, Email sales@micronor.com
declare that this DoC is issued under our sole responsibility and belongs to the following
products:
•Fiber optic switch and signaling system, consisting of:
•MR380-0, MR380-1, MR380-2 or MR382-1, Controller
•MR380 series Sensor, MR381/MR382/MR383/MR384/MR385/MR386/MR387
That the equipment is in conformity with the following International (IEC) and North
American requirements:
•Explosive Atmospheres/Hazardous Locations, IEC Ex
•Electromagnetic Compatibility for Industrial Environments, IEC and FCC
•Electrical Safety, IEC and FDA/NEC
to which this declaration relates in conformity with the following standards or other
normative documents:
•
IEC 60079-0:2017, Edition 7.0
•IEC 60079-14:2013, Edition 5.0
•IEC 60079-28:2015: Edition 2.0
•IEC 60825-1: 2014, Edition 3.0
•IEC 61010-1:2010. Edition 3.0
•IEC 61000-6-2:2005, Edition 2.0
•IEC 61000-6-4:2006, Edition 2.0
+AMD1:2010 +ISH1:2011
•
US CFR, FDA, Title 21, Chapter 1,
Subchapter J, Parts 1000-1050
•US CFR, FCC, Title 47, Chapter 1,
Subchapter A, Part 15
•US NFPA 70, NEC, 2014
Certification Agency
•Certification Management Ltd, EU Notifying Body 2503, IEC Ex Certification Body
•CML Evaluation Report R1198C, GB/CML/ExTR 16.0130/00
Signed for and on behalf of:
Camarillo, CA 2019-09-27 Dennis Horwitz, VP

Page 3 of 18
Declaration of Conformity (EAEU)
We, the manufacturer,
Micronor Inc.
900 Calle Plano, Suite K, Camarillo, CA 93012, USA
Telephone +1-805-389-6600, Email sales@micronor.com
declare that this DoC is issued under our sole responsibility and belongs to the following
products:
•Fiber optic switch and signaling system, consisting of:
•MR380-0, MR380-1, MR380-2 or MR382-1, Controller
•MR380 series Sensor, MR381/MR382/MR383/MR384/MR385/MR386/MR387
That the equipment is in conformity with the following relevant EAEU harmonization
legislation:
•On safety of low-voltage equipment, TR-CU-004/2011
•On safety of equipment intended for use in explosive atmospheres, TP-TC-012/2011
•Electromagnetic Compatibility of Technical Products, CU-TR-020/2011
to which this declaration relates in conformity with the following standards or other
normative documents (latest version of corresponding IEC document used per Appendix D):
•
GOST 30804.6.2-2013
•GOST 30804.6.4-2013
•GOST 31610.28-2017
•GOST R IEC 60079-0-2011
•GOST IEC 60079-14-2013
•GOST IEC 60825-1-2013
•
GOST IEC 61010-1-2014
Certification Agency
•Certification Management Ltd, EU Notifying Body 2503, IEC Ex Certification Body
•CML Evaluation Report R1198C, GB/CML/ExTR 16.0130/00
Signed for and on behalf of:
Camarillo, CA 2019-09-27 Dennis Horwitz, VP
Table of contents
Other Micronor Controllers manuals
Popular Controllers manuals by other brands

MacroAir Technologies
MacroAir Technologies Controller 4 Operation manual
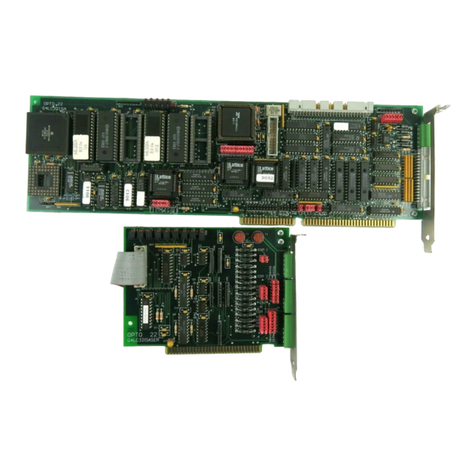
OPTO 22
OPTO 22 G4LC32ISA-LT user guide
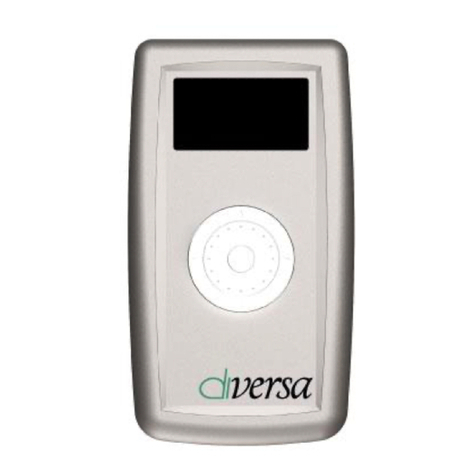
Douglas
Douglas WIR-3110 user manual
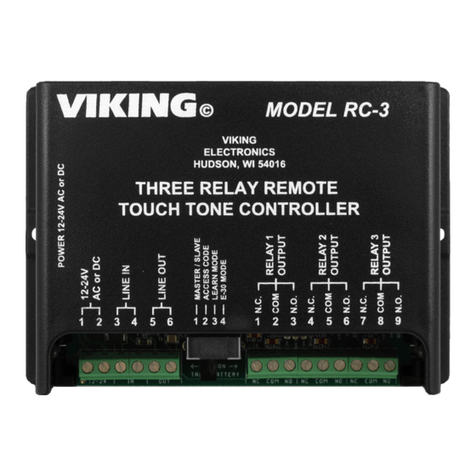
Viking
Viking RC-3 Technical practice
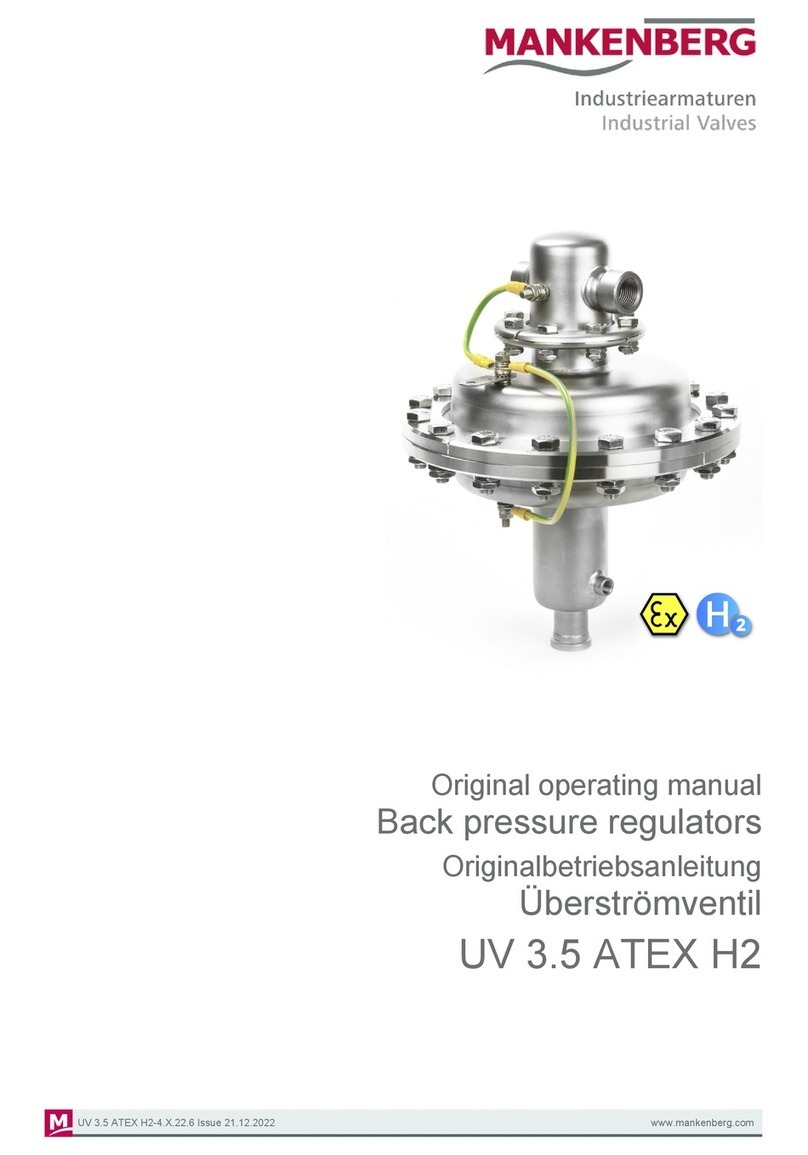
Mankenberg
Mankenberg UV 3.5 ATEX H2 Original operating manual

PIETRO FIORENTINI
PIETRO FIORENTINI REVAL 182 Use and maintenance instructions