microSYST MS6026 User manual

COMPETENCE IN
MEASUREMENT
Process Meter
with Tricolor Bargraph and Universal Input
MS 02 & MS 12
v 2.2
USER MANUAL
PLOVDIV 2015
Document revision 2015-03-20

Programming by keyboard or by RS485
1. Sensor and input signal selection:
Variant 1 – RTD or TC selection with line riz tion in the device.
Line riz tion is up to 9th st ge in 4 sub-r nges. In RTD it is necess ry its connection to be selected
In TC it is necess ry the utom tic correction of the cold end to be en bled or dis bled. The
dimension h ve to be set - º C or º F.
The sensor r nge is set by p r meters.
Variant 2 – The input sign l is line r current or volt ge.
The tr nsmitter r nge is set by p r meters
Variant 3 – The sensor is non-st nd rd nonline r – it c n be line rized by request or by the user by
RS485, MODBUS RTU protocol, by entering polynomi l up to degree three coefficients.
Variant 4 - At sensor/tr nsmitters with unknown tr nsmission ch r cteristics it is possible to be set
line r by two points by physic l ch nge of the technologic l qu ntity nd setting of two limit v lues
in the device.
2. Setting of decimal point and lower and upper limit of the range, set-points parameters, alarms,
bargraph etc.
3. Selection of analogue output and range setting – if it is available / ordered /.
4. System setting of analogue inputs – if it is necessary.
5. System setting of analogue outputs – if it is necessary.
. Setting of communication parameters – if RS485 is available.
* It is possible to begin with this procedure
To restore the f ctory settings – p ge 20
After ch nging the decim l point ll the p r meters rel ted with PV – process v ri ble,
influencing on the r nge, b rgr ph, set-points etc. h ve to be ch nged
For controller programming Microsyst offers:
•USB / RS485 Convertor
•Base software for setting for operating systems Windows
MOST COMMONLY USED ABBREVIATIONS:
RTD - resist nce temper ture detector
TC - thermocouple
ATC - utom tic temper ture correction
PV - process v ri ble
SP - set point – set point for regul ting of the me sured process v ri ble
OFFSET- offsetting the indic tion of input or output v lue
Aout - n log output
Document revision 2015-03-20
2

CONTENT
I. ORDER CODE 3
II. TECHNICAL DATA 4
III. FEATURES 6
IV. ADVANTAGES 6
V. DESIGNATION 6
VI. FRONT PANEL AND TERMINALS 7
VII. ELECTRICAL CONNECTION OF INPUTS AND OUTPUTS 8
VIII.
OPERATING MODE
EDIT OF THE SET-POINTS (SP)
LOCK / UNLOCK THE KEYPAD
BARGRAPH – PRINCIPLE OF OPERATION
10
10
10
11
IX.
PARAMETERS
SYSTEM PARAMETERS
HIDDEN SYSTEM PARAMETERS
SERVICE PARAMETERS
12
12
14
16
X. USER SETTING OF THE ANALOG INPUT OFFSET 18
XI. RECOMMENDATIONS AGAINST INTERFERENCE 19
XII.
ANALOG INPUTS SETTING
SERVICE SETTING
LINEAR INPUT SETTING BY TWO REFERENCE POINTS
SETTING OF NON-STANDARD INPUT
19
19
20
20
XIII. RESTORING OF DEFAULT SETTINGS 21
XIV. MODBUS RTU RS485 COMMUNICATION 21
I. ORDER CODE
MS 02 и MS 12 differ only in: housing, number and type of relay
outputs and bargraph - type and number of LEDs.
See. TECHNICAL DATA
Document revision 2015-03-20
3
MS6026 - K1-K2-K3-K4-K5 . . Aout RS485
RS485: 0 - No, 1 - Yes
An log outputs:
0 - No, 1 - Yes
Digit l outputs:
0 - tr nsistor OC- 500mA/30 VDC
1 - Rel y NO-250V / 5A AC
N me
MS6026 - K1-K2-K3- . . Aout RS485

II. TECHNICAL DATA
Analog input (universal, user selectable) Resolution - 16bits
Current
Volt ge 0 ÷ 20 mA DC; 4 ÷ 20 mA DC
0 ÷ 1V; 0 ÷ 10 V DC
Resist nce temper ture detector -
RTD
Current through RTD sensor
Pt385-10,50,100,200,500,1000;
Pt391-100, Pt392-100; Cu482-100; Ni617-100; Ni672-120
420µA for 2 wire nd 4 wire connection; 210 µA for 3 wire
Thermocouple – TC
TC-compens tion of the cold end R nge ±73,125 mV.......J, K, S, B, T, E, N, R, C, ХК(L) GOST
Pt100 Cl.B: EN 60751
User progr mm ble inputs in r nges
0 ÷ 400 Ω nd 0 ÷ 4 kΩ
±73,125 mV for thermocouple with ATC
0 ÷ 20 mA DC
0 ÷ 1 V DC nd 0 ÷ 10 V DC
Temper ture drift < 10 ppm / °C
Me surement time 0.5 sec;
Auxili ry power supply nsulated 24 VDC ± 3 %; 40 mA m x
Digital outputs for MS6026 - 5 pcs; for MS6126 – 3 pcs
For MS6026 K1÷К5 Rel y SPDT NO & NC 5A /250V AC or OC- 500 mA/30 VDC
For MS6126 K1÷К3 Rel y SPST NO 5A /250V AC or OC- 500 mA/30 VDC
Analogue output 2 Resolution - 10bits
Me surement ccur cy 0. 1 % from r nge for 0 ÷ 10V DC nd 0 ÷ 20 mA
Time to refresh 0.5 sec
Lower nd upper limit -
NAMUR level detection -1,56% ÷ +105,4% from the r nge
i.e. for 4÷20 mA – огр. 3,75÷20,86 mA
Auxili ry power supply nsulated 21 ÷ 24 VDC ; 40 mA m x
Indication and keypad
Displ y
Displ y r nge
Displ y form t
Keyp d
4 LED seven-segment indic tors with h = 14mm
-1999 ÷ 9999
X■XXX XX■XX XXX■X XXXX
Foil membr ne with buttons
Bargraph
for MS6026 / 6126 32 / 24 броя LED - Trocolor - green, red or or nge
64 / 48 броя LED - Monochrome – red or green
Power supply
Power supply 90 ÷ 250 VAC, 9VA m x
Communication (option)
RS485 – insulated RS485 2WIRE MODBUS RTU SLAVE
9600, 19200bps; p rity – NONE, EVEN ; 1 , 2 stop bit
Environment
Temper ture nd rel tive humidity
without condens tion Working : 0 ÷ 50 °C / 10 ÷ 85 % rh
Stor ge : -10 ÷ 70 °C / 20 ÷ 90 % rh
Dimensions-for MS 02 ; MS 12
Over ll dimensions (WxHxL), mm
Mounting (WxH), mm According to DIN IEC 61554 - 96x 96 x 128; 96 x 48 x 128
P nel in hole - 92 x 92; 90 x 40
Weight – for MS 02 ; MS 12 m x 370g ; 280 g
The version of the device is visible when exiting menu ‘PARAMETERS’
Document revision 2015-03-20
4

MEASUREMENT RANGE AND ACCURACY
Sensor Standard Range Accuracy Drift,
µV / °C
TC - °C µV without ATC °C with ATC
J EN 60584 -210 ÷ 1200 -8095÷ 69553 0.3 1
K EN 60584 -200 ÷ 1372 -6458÷ 54886 0.4 1
S EN 60584 -50 ÷ 1768 -236 ÷ 18693 0.5 1
B EN 60584 44 ÷ 1820 0 ÷ 13820 0.5 1
T EN 60584 -200 ÷ 400 -5603 ÷ 20872 0.4 1
E EN 60584 -200 ÷ 1000 -8825 ÷ 76373 * 0.3 1
N EN 60584 -200 ÷ 1300 -3990÷47513 0.4 1
R EN 60584 39 ÷ 1768 226 ÷ 21103 0.5 1
C EN 60584 0 ÷ 2320 0 ÷ 37107 0.5 1
XK – GOST – L GOST P.585-2001 -200 ÷ 800 -9488 ÷ 66466 0.3 1
RTD - °C Ω °C mΩ /°C
Pt10_385 EN 60751 -200 ÷ 850 1,852÷39,048Ω 0.7 0.04
Pt50_385 EN 60751 -200 ÷ 850 9,26÷195,24Ω 0.3 0.04
Pt100_385 EN 60751 -200 ÷ 850 18,52÷390,48Ω 0.15 0.04
Pt200_385 EN 60751 -200 ÷ 850 37,04÷780,96Ω 0.15 0.04
Pt500_385 EN 60751 -200 ÷ 850 92,6÷1950,24Ω 0.15 0.04
Pt1000_385 EN 60751 -200 ÷ 850 185,2÷3904,8Ω 0.15 0.04
Pt100_391 GOST -200 ÷ 850 17,24 ÷ 395,16Ω 0.15 0.04
Pt100_392 JIS C1604-81 -200 ÷ 660 17,08 ÷337,03Ω 0.15 0.04
Cu100_482 GOST -180 ÷ 260 20,53 ÷ 185,6Ω 0.15 0.04
Ni100_617 DIN 43760 -70 ÷ 180 69,29 ÷ 223,21Ω 0.15 0.04
Ni120_672 Edison Curve -80 ÷ 260 66,60 ÷ 380,31Ω 0.15 0.04
TC non-standard User Curve - ±73,125 mV - 1 µV / °C
Current input -mA DC Limits, mA % ppm/°C
0.000 ÷ 20.000 - 0.000 ÷ 20.000 0.000 ÷ 20.860 mA 0.01 10
4.000 ÷ 20.000 - 4.000 ÷ 20.000 3.750 ÷ 20.860 mA 0.01 10
Voltage input -V DC V DC % ppm/°C
0.000 ÷ 10.000 V - 0.000 ÷ 10.000 0.01 10
0.000 ÷ 1.000 V - 0.000 ÷ 1.000 0.01 10
Resistance input - Ω Ω % ppm/°C
0 ÷ 400 Ω - 0 ÷ 400 0.1 ÷ 400 0.01 10
0 ÷ 4000 Ω - 0 ÷ 4000 0.1 ÷ 4000 0.01 10
T ble v lue. In the cold end temper ture 25°C the upper limit for TC - E type is 950°C.
Accur cy is defined electric lly s % from the r nge nd without influence of sensors nd their connection.
Document revision 2015-03-20
5

III. FEATURES
In the device is embedded line riz tion for 11 RTDs nd 10 thermocouples, four line r inputs -
0÷20mA, 4 ÷20 mA, 0 ÷ 1 V nd 0 ÷ 10 V for connection of tr nsmitters.
The device llows line riz tion with polynomi ls up to degree three, which c n be set vi RS485
with MODBUS RTU protocol, of nother 6 types of sensors. To do this you h ve to select n
ppropri te non-st nd rd for the device sensor.
The correction of the cold end temper ture of ll thermocouples is performed utom tic lly by
built-in to termin ls thermoresistor Pt100, Cl ss B. It is possible this function to be dis bled.
The device me sures electric l resist nce up to 4kΩ, DC volt ge in three subr nges -
± 73 mV, 1 V nd 10V, direct current in one r nge up to 26mA.
The n logue output tr nsmits the input line rized sign l in the r nge limits
Progr mming is on 3 levels - System p r meters, Hidden system p r meters nd Service P r meters.
The b rgr ph is configured s tricolor, monochrome green nd monochrome red.
The me surement ccur cy of the input electric l sign ls is better th n 0.01% from r nge, while th t
of the n log output is 0.1% from the r nge of the output sign l.
The device llows two communic tion speeds - 9600 or 19200 bps
IV. ADVANTAGES
High me surement ccur cy – 0.01%. Temper ture st bility - drift < 10 ppm/°C
Univers l input with 31 types of sensors, 6 of which customer djust ble
Univers l power supply 90 ÷ 250 VAC
Tricolor b rgr ph – 7 zones th t c n be configured by the customer s levels nd color –
green, red or or nge
Five digit l outputs th t c n be controlled with individu l set-points
Simult neously output g lv nic lly isol ted current nd volt ge outputs
Simult neously output ctive nd p ssive current output
G lv nic lly isol ted communic tion port - RS485 MODBUS RTU
Precise temper ture correction of the cold end of thermocouples - Pt100, Cl. B
Progr mm ble exponenti l low frequency filter
Progr mm ble filter for pe ks in the me surement circuit
Deep filter for noise rejection from power supply NMRR 80dB t 50Hz or NMRR 65dB for use t
50/60Hz – univers l power supply
V. DESIGNATION
MS6026 nd MS8126 re designed for mesurement nd control of different process p r meters. The
me sured v lue is displ yed on LED displ y nd LED b rgr ph.
The device supports MODBUS RTU protocol by isol ted RS485 seri l ch nnel. The n logue output
is tr nsmitting nd g lv nic lly isol ted from the other ch nnels.
The presence of a programmable by color and range bargraph ensures easy and rapid
differentiation of normal, warning or critical situations.
The device is pplic ble s:
–St ge ON/OFF controller – up to 4 st ges nd one l rm output
–Process meter with b rgr ph nd five digit l outputs
–Converter of technologic l qu ntity in unified n logue sign l or its tr nsmition by seri l
MODBUS RTU protocol
Document revision 2015-03-20
6

VI. FRONT PANEL AND TERMINALS
MS 202
Document revision 2015-03-20
7

MS 212
VII. ELECTRICAL CONNECTION OF INPUTS AND OUTPUTS
POWER SUPPLY Terminals – 14 и 15
DIGITAL OUTPUTS
Designation
Model ----> MS 02 MS 12
Contacts ----> NO NO COM NC
Outputs
and
Terminals
К1 3 4 4 5 6
К2 5 6 7 8 9
K3 7 8 10 11 12
K4 9 10 - - -
K5 11 12 - - -
Document revision 2015-03-20
8

ANALOG OUTPUTS M rking Termin l
Active current output Positive termin l Iout ACT+ 22
Neg tive termin l Iout ACT- 21
Passive current output Positive termin l Iout PAS+ 21
Neg tive termin l Iout PAS- 20
Voltage output Positive termin l Uout+ 19
Neg tive termin l Uout- 20
ANALOG INPUTS – CURRENT AND VOLTAGE M rking Termin l
Power supply
for transmitters
Positive termin l 24 Vdc+ 26
Neg tive termin l 24 Vdc- 24
Current input
from 2-wire transmitter,
supplied from the device
Positive termin l Iin ACT+ 26
Neg tive termin l Iin ACT- 25
Current input Positive termin l Iin PAS+ 25
Neg tive termin l Iin PAS- 24
Voltage input
0.000 ÷ 10.000 V
Positive termin l U in + 23
Neg tive termin l U in - 24
Voltage input
0.000 ÷ 1.000 V
Positive termin l TC + 29
Neg tive termin l TC - 28
INPUT – RTD, Ω and kΩ M rking Termin ls
4-wire connection
Two wires, shorted to one end of the sensor
4W
27,28
Two wires, shorted in the other end of the
sensor 29,30
3-wire connection Two wires, shorted to one end of the sensor 3W 27,28
Connection between termin ls 29 nd 30 29
2-wire connection Connection between termin ls 27 nd 28 2W 28
Connection between termin ls 29 nd 30 29
INPUT – THERMOCOUPLE M rking Termin l
2-wire connection Positive termin l TC + 29
Neg tive termin l TC - 28
Document revision 2015-03-20
9

VIII. OPERATING MODE
MS6026 controls up to 4 /four/ digit l outputs with ON/OFF logic by independent set-points nd
hysteresis. When specifying neg tive set-point is inverted the control logic. Fifth digit l output is used for
l rm functions for lower nd upper level with progr mm ble del y nd time for ction.
MS6126 h s three outputs - two ON/OFF with hysteresis nd one l rm.
Softw re is the s me for both units. P r meters ssoci ted with discrete outputs K3 nd K4
re not import nt for MS6126. Al rm output K5 of MS6026 is identic l to K3 of MS6126.
Possible non-standard versions in which K3 of MS8126 to realized as a control with
hysteresis
SP3
SP2
SP1
K3
K2
K1
3 3
1 1
SP4
K4
4 4
.
1. EDIT OF THE SET-POINTS (SP)
[PV] → [SP1] → [SP2] → [SP3] → [SP4] → [PV].
By successively pressing – viewing nd editing of the set-points
or
V lue editing [SP1] [50] → [49] →[48] →[49]...
Adoption of the new v lue (this c n be done utom tic lly too, 5 sec. fter the
l st pressed button). [SP1] [49] → ок
2. LOCK / UNLOCK THE KEYPAD
When the keyp d is locked no possibility to ch nge the p r meters, only to view the
set-points. The v lues of the set-points do not blink.
+ [Loc] ↔ [UnLc]
Switch unlocked <=> locked st te
Document revision 2015-03-20
10

3. BARGRAPH – PRINCIPLE OF OPERATION
The b rgr ph indic tion is connected with p r meters bG0 ÷ bG7 or with rnGL,AL,SP1 ÷ SP4,AH
nd rnGH (r nge, l rm levels nd set-points) . This c n be specified by Syst,GF p r meter. In both
c ses, in order to function properly the indic tion re given descending nd scending v lues. For
ex mple t Syst,GF=1 - bG0≤bG1≤bG2.... ≤bG7 / bG0≥bG1≥bG2.... ≥bG7. The device does not
check l yout. If necess ry points of AH nd AL re utom tic lly exch nged ( t rnGL> rnGH) in the
order shown in the figure.
For e ch zone between the set v lues c n be specified color by p r meter coL1 ÷ 7. It c n be color of
zone – there will be colorful view or color of column - s whole will ch nge its color
ccording to PV (p r meter Syst, GC).
By SySt.GP p r meter the mode 'lighting column' / 'lighting point' is determined.
When LED is between two color zones when ch nging PV it would ch nge its color, thereby
slightly exp nds one zone t the expense of the other. This c n be en bled / dis bled by SySt.G1.
Monochrome b rgr ph functions s color b rgr ph with two possible colors.
ConF, Gh=0 or Gh=1 from menu „OTHER SERVICE PARAMETERS“ indic tes color or
monochrome b rgr ph will be used.
The b rgr ph c n be switched off by bLEd=0 from menu „Service parameters“
The displ y is limited in the r nge -1999 ÷ +9999, beyond which blinks (┌ - - ┐ or └ - - ┘).
If the process v ri ble is within the me surement limits but is out of r nge (par. rnGL, rnGH)
v lues ltern te with ┌ - - ┐- over the r nge or └ - - ┘- below the r nge.
Document revision 2015-03-20
11
MEASURED VARIABLE (PV)
LED display
LED bargraph
3 colors
bG0
bG1
bG2
bG3
bG4
bG5
bG6
bG7
rnGL
AL
SP1
SP2
SP3
SP4
A
rnG
SYSt,GF=1 SYSt,GF=0
AOut
4-20mA

IX. PARAMETERS
Enter menu 'PARAMETERS SETTING' - Press nd hold the button (SP
ppe rs on the displ y) for 4 sec. while ProG ppe rs on the displ y.
Rele se this button in order to ccess menu „SYSTEM PARAMETERS”.
To ccess “HIDDEN” or „SERVICE PARAMETERS” without rele sing
button, press the button . COdE ppe rs on the displ y. Rele se the buttons.
0 ppe rs on the displ y. By buttons select the code of the desired
p r meters group. Through speci l codes here you c n ctiv te some controller
functions – setting of the input, offset nd others. Press button to confirm.
En bles ch nging the v lue, the displ y fl shes.
Ch nges the v lue of the selected p r meter.
Scroll in the p r meters list.
Confirms the v lue ch nge.
Exit from p r meters menu (should not be in v lue ch nge). Press nd hold this
button for 4 sec. while v1_5 ppe rs on the displ y.
V1_5 is the softw re version of the device.
●2 minutes after the last pressed button the de ice automatically returns in operating menu
SYSTEM PARAMETERS
Parame
ter Description Range of change
RS485
communication
HOLD REG
ADDRESS,
TYPE,
SCALE.Where
not specified the
sc le depends on
the decim l point
-dP
Def -
ult
v lue
* Parameters bG0÷7 and coL1÷7 are not included in the menu if the device is without bargraph
(bLEd=0).
●Zones of LED b rgr ph t Syst,GF=1.
●P r meters bG0÷7 re included only t
Syst,GF=1
-1999 ÷ 9999
(Dimension s PV)
bG0 Beginning of the LED l dder
at PV < bG0 – there is no lighting LED 43, Sint
bG1 Zone 1 44, Sint
bG2 Zone 2 45, Sint
bG3 Zone 3 46, Sint
bG4 Zone 4 47, Sint
bG5 Zone 5 48, Sint
bG Zone 6 49, Sint
bG7 End of the LED l dder 50, Sint
Document revision 2015-03-20
12

Color of each zone of the LED bargraph
Color Zone depending on a parameter
Syst,GF=1 Syst,GF=0
Color bargraph:
0-DOES NOT LIGHT;
1-RED;
2-GREEN; 3-ORANGE
Monochrome bargraph:
0-DOES NOT LIGHT;
1,2,3-LIGHT;
coL1 bG0 ÷ bG1 rnGL ÷ AL* 51, Uint, *1
coL2 bG1 ÷ bG2 AL* ÷ SP1 52, Uint, *1
coL3 bG2 ÷ bG3 SP1 ÷ SP2 53, Uint, *1
coL4 bG3 ÷ bG4 SP2 ÷ SP3 54, Uint, *1
coL5 bG4 ÷ bG5 SP3 ÷ SP4 55, Uint, *1
coL bG5 ÷ bG6 SP4 ÷ AH* 56, Uint, *1
coL7 bG6 ÷ bG7 AH* ÷ rnGH
* f it is necessary points of AH and AL
are automatically exchanged
(at rnGL>rnGH)
57, Uint, *1
Hysteresis at К1-К4 outputs operation
A negati e alue in erts the corresponding output
-1999 ÷ 9999
(Dimension s PV)
HST1 Hysteresis for К1 33, Sint
HST2 Hysteresis for К2 34, Sint
HST3 Hysteresis for К3 35, Sint
HST4 Hysteresis for К4 36, Sint
AL Lower limit of l rm
AH Upper limit of l rm
rnGL÷ rnGH
(Dimension nd decim l
point re ccording to
process v ri ble)
41, Sint
42, Sint
t0AL Time to ctiv te n l rm under AL 0 ÷ 100 Sec. 58, Uint, *1
t0AH Time to ctiv te n l rm bove AH 0 ÷ 100 Sec. 59, Uint, *1
Document revision 2015-03-20
13

HIDDEN SYSTEM PARAMETERS Accessible at CODE= 12
To change with extreme caution!
Improperly setting leads to incorrect operation of the de ice!
SCALE OF AN ANALOG OUTPUT AOut
Through the next 2 p r meters re set limits nd slope of the n log output.
OtrL PV, corresponding to the lower limit of
Аout. (for ex mple 0°C for 4mA) -1999 ÷ 9999
(Dimension s PV) 18, Sint
OtrH PV, corresponding to the upper limit of
Аout. (for ex mple 100°C for 20mA) -1999 ÷ 9999
(Dimension s PV) 19, Sint
MEASUREMENT RANGE
Limit the set-point nd l rm levels t bsolute l rm. Set rnGL < rnGH.
In TC / RTD c n be used s w rning levels but do not p rticip te in the me surement. When
me suring below rnGL- displ y ch nges in 1 sec. PV↔└ - - , bove rnGH - PV↔┌ -- ┐.
P r meters djust the me surement in line r r nges (if Syst,Et=0) 0-1V, 0-10V, 4-20mA nd 0-
20mA.
rnGL Me surement r nge – lower limit.
Indic tion for 0V/ 0mA/4mA,
if (Syst ,Et=0).
-1999 ÷ 9999
( Dimension s PV ) 20, Sint
rnGH Me surement r nge – upper limit
Indic tion for 1V/10V/20mA,
ако (Syst ,Et=0).
-1999 ÷ 9999
(Dimension s PV) 21, Sint
OTHER
dPnt
Decim l point
* After ch nge it is necess ry to be
checked / corrected ll p r meters with
the dimension of PV.
** For built-in temper ture sensors nd
line r inputs, when ch nging the dPnt,
PV utom tic lly switches in the selected
form t. For non-st nd rd inputs the point
is decor tive – Coefficients 'non-st nd rd
input' h ve to be sc led through RS485
0 ÷ 4
0-xxxx;
1-xxxx.;
2-xxx.x;
3-xx.xx;
4-x.xxx
(for RTD nd TC-st nd rd or
non-st nd rd, 0, 1 nd 2 re
possible)
29, Uint, *1
SOFTWARE FILTER
A db Filter zone of ADC 0 ÷ 9999
( Dimension s PV ) 24, Uint
Adbt Time to perception of v lue outside of
A db zone 0 ÷ 255 sec. 25, Uint, *1
FILt Filter coefficient 1 ÷ 100 26, Uint, *1
Document revision 2015-03-20
14

SYST - Configuration options
LED Bargraph:
The field GF determines to which p r meters group to
connect LED zones. Possible groups:
(0 - RnGL,AL,SP1,2,3,4,AH,RnGH) nd
(1 – LED zones G0,1,2,3,4,5,6,7)
Field GC: t GC=0 ll LED column will be with one color,
which will ch nge depending on zone in which is PV. At
GC=1, every zone will be with its own color. At b rgr ph
type 'lighting point' is irrеlev nt.
Field GP=0, b rgr ph type 'column';
or GP=1, b rgr ph type 'lighting point'.
Field G1=0, the l st lighting LED from b rgr ph c n ch nge
its color;
or G1 =1, the l st lighting LED from b rgr ph c n't ch nge
its color. It is bout situ tion where inside the LED zone
h s bound ry between two colors. If G1 = 1, the color does
not reflect ex ctly PV, but color zones visu l re with fixed
sizes. Otherwise m y v ry by 1 LED.
Analog output Aout – (proportion l to the input p r meter
PV).: The v lues th t correspond to the n log output r nge
re in p r meters OtrL, OtrH. Field ob (out band)
determines if this v lues refer to 0-100% current output or to
20-100% (it is used for e sy tr nsition from 0-20mA ↔ 4-
20mA).
Et –En bled function 'line r input setting by two reference
points'. If ch nged, the current setting will rem in v lid until
such new (Et = 1) or until r nge correction rnGL, rnGH
(Et = 0)
BackUp options:
For Input / Output settings, nd some p r meters (Note 2)
keep b ckup. By rE = 1 these settings nd p r meters
return def ult v lues nd lose current v lues.
OPTIONS ACCESS:
SYST → GF → GC →.... t1AL
OPTION CHANGE:
with or , for ex mple:GF=0 → GF=1
GF=0 – LED zones
RnGL,AL,SP1 ÷ SP4,AH,RnGH
GF=1 - LED zones
bG0 ÷ bG7
GC=0 – B rgr ph color - column
GC=1 – B rgr ph color – zone
GP=0 – B rgr ph - column
GP=1 – B rgr ph – lighting point
G1 Permitted color ch nge l st
lighting LED
G1=0 – YES; G1=1 – NO
ob=0 – Aout 0-100%
(for ex mple 0-20mA)
ob=1 – Aout 20-100%
(for ex mple 4-20mA)
Et=0-Forbidden setting of line r
input by two reference points. The
setting is by r nge rnGL ÷ rnGH t
prior known p r meters of the
connected tr nsmitter.
Et=1- R nge rnGL÷ rnGH is just
for w rning when me suring
outside these limits.
rE=1- Restores the def ult v lues
nd fter th t rE=0 utom tic lly.
Attention – current settings are
lost!
St=1 – Cre tes buckup of the
settings (the def ult copy is lost),
nd St=0 utom tic lly.
The option is visible on the displ y
only fter speci l service code in
COdE.
MODBUS HOLDING REGISTER
ADDRESS
(REG №= REG ADDRESS+1) 30,
Uint, *1 .
Document revision 2015-03-20
15

MODBUS COIL ADDRESS IN
RS485 COMMUNICATION
(COIL №= COIL ADR+1)
St rE Et ob G1 G
PGC GF
4
9
5
4
9
4
4
9
3
4
9
2
4
9
1
4
9
0
4
8
9
4
8
8
t1AL Time for ction of l rm output fter its
switching on below the AL. When the time run,
the output is off, the LED AL is fl shing while
PV is below AL.
1÷100 sec.,
0-permanently on
MODBUS HOLD.REG. ADDRESS
60, Uint, *1
0
t1AH Time for ction of l rm output fter its
switching on bove the AH. When the time run,
the output is off, the LED AL is fl shing while
PV is bove AH.
1 ÷ 100 sec.,
0-permanently on
MODBUS HOLD.REG. ADDRESS
61, Uint, *1
0
SERVICE PARAMETERS Accessible at CODE=23
To change with extreme caution!
Improperly setting leads to incorrect operation of the de ice!
Para-
meter Description Values,
MODBUS HOLD. REG. ADR , TYPE ,
SCALE.
Default
value
SERVICE SETTING OF AN ANALOG OUTPUT.
The n log outputs re f ctory set !
This setting sc les the n log outputs to correspond to 0 ÷ 20 mA nd 0÷ 10 V. This requires n
reference mA meter or V-meter with ccur cy higher th n 0.1% to be connected to the respective
output.
n unsuccessful set up it is possible the factory settings to be restored by parameter Syst, rE=1
from menu “Hidden system parameters” .
When changing the value by buttons on front panel Aout enters in calibration mode which is
different from operating mode. This should be considered in connected control and
measurement equipment.
Settings re m de t Syst,ob=1, i.e. for points 4 ÷ 20 mA DC and 2 ÷ 10 VDC
In dv nce h ve to be specified which type of n log output ( volt ge or current ) is set by
p r meter AtYP
In need of user ch nge sc ling p r meters ОtrL/H h ve to be used.
PA0 Offset for Aout1. Adjust to indic tion
AOut1=4mA (current output)
-1999 ÷ 9999
MODBUS HOLD.REG. ADDRESS
I-23, U-123 Sint, *1
PA1 Slope for Aоut1. Adjust fter PA0 until
indic tion AOut1=20mA.
-1999 ÷ 9999
MODBUS HOLD.REG. ADDRESS
I-22, U-122 Sint, *1
Document revision 2015-03-20
16

OTHER SERVICE PARAMETERS
SenS Choice of sensor MODBUS HOLD.REG. ADDRESS 28, Uint, *1
№ input displ y № input displ y № input displ y
0 TC J tc J 10 4-20 mA line r 4-20 14 Pt10 385 Pt10
1 TC K tc ├ 11 0-20 mA line r 0-20 15 Pt50 385 Pt50
2 TC S tc S 12 0-1V line r 0-1v 16 Pt100 385 P100
3 TC B tc b 13 0-10 V line r 010v 17 Pt200 385 P200
4 TC T tc t 18 Pt500 385 P500
5 TC E tc E 25 TC non-st nd rd nStc 19 Pt1000 385 1000
6 TC N tc n 26 RTD_4KΩ non-
st nd rd nSr├ 20 Pt100 392 P392
7 TC R tc r 27 RTD 400Ω non-
st nd rd nSr0 21 Pt100 391 P391
8 TC C tc C 28 0-20mA non-st nd rd nS20 22 Cu100 482 C100
9TXK
(L) tc L 29 0-1V non-st nd rd nS01 23 Ni100 617 n100
30 0-10V non-st nd rd nS10 24 Ni120 672 n120
virE Connection RTD 3 / 4 wire
( ppe rs only for RTD sensor) 3÷ 4 MODBUS HOLD.REG.
ADDRESS 32, Uint, *1
nEtA MODBUS ddress of the device 1 ÷ 255 MODBUS HOLD.REG.
ADDRESS 127, Uint, *1 1
ConF System settings
Field 1u indic tes n log type used
(h rdw re rel ted)..
Field rr – Norm l Mode Rejection R tio
BAUDRATE, PARITY, STOP BIT re
communic tion p r meters in RS485
network.
Gh-service setting – b rgr ph type.
□F-°C/°F
It ffects only on built-in
temper ture sensors nd for
ATC(in Sens=nStc).
It does not ffect on line r or non-
st nd rd input.
ACCESS TO THE OPTIONS:
Conf → 1u → rr → ....
□F → bLEd
OPTION CHANGE:
by or
1u=0– Aout1 CURRENT;
1u=1- Aout1 VOLTAGE
rr=0– NMRR 80dB 50Hz;
rr=1- NMRR 65dB 50/60Hz;
br=0 BAUDRATE 9600 bps;
br=1-19200 bps
Pr=0 PARITY NONE;
Pr=1-EVEN
Sb=0 - 1 stop bit; =1 - 2stop bits
bC=0 Performing of BROADCAST queries
(queries to ddress of the device 0).
bC=1-Not perform BROADCAST queries
Gh=0-color b rgr ph Gh=1- monochrome
b rgr ph
□F=0 -°C
□F=1 -°F
MODBUS COIL ADDRESS
ПРИ RS485
°FGh bC Sb Pr br rr 1u-
4
4
7
4
4
4
4
5
4
4
4
4
4
3
4
4
2
4
4
1
4
4
0
MODBUS HOLDING REG ADDRESS
27, Uint, LSByte,*1
rr=0
Br=0,
Pr=0,
Sb=0,
bC=0
Document revision 2015-03-20
17

CnF2
System settings 2
cd – en bled/dis bled utom tic
temper ture correction of the cool
end of the thermocouples
do – en ble/dis ble the indic tion of
v lue out of the r nge rnGL ÷ rnGH
ACCESS TO THE OPTIONS s
in the previous p r meter
cd = 0 –en bled temper ture correction of TC.
( PV = Т hotend + Т cold end )
cd = 1- dis bled temper ture correction of TC
( PV=Т hotend )
do = 0 – v lues out of r nge re displ yed.
The displ y blinks:
[NUMBER] ↔ [└ - - ┘or┌ -- ┐]
do =1- v lues out of r nge re not displ yed.
The displ y blinks [ ] ↔ [└ - - ┘or┌ -- ┐]
MODBUS HOLDING REG ADDRESS 27,
MSByte, *1
сd=0
do=0
bLEd Number of LEDs in b rgr ph
Service setting 0 ÷ 100
0 – the device is without bargraph
MODBUS HOLD.REG. ADDRESS
62, Uint, *1
Abbreviations: Uint – UNSIGNED INT, Sint – SIGNED INTEGER
X. OFFSET OF THE ANALOG INPUT – [CodE= 47]
In this mode c n be entered v lue which will be dded when me suring the input p r meter (offset),
if there is disp rity between the displ yed v lue nd me sured v lue with other reference equipment.
Enter CОdЕ= 47 (see ch pter IX. PARAMETERS). “OFSt” ppe rs on the displ y. Press
button. The current offset ppe rs on the displ y. By nd is set the desired offset. Press
button to confirm. (The device returns utom tic in m in menu 5 sec. fter the l st pressed button.
EXAMPLES FOR USER SETTING OFFSET
VII.Displ y indic tion: 129 Entered offset: 3.4
VIII.New displ y indic tion: 132 Entered offset: 0.6
IX. New displ y indic tion: 133 Entered offset: -1.0
X. New indic tion: 132
Document revision 2015-03-20
18
MODBUS CO L ADDRESS ПРИ RS485
-- - - - - do cd
4
3
9
4
3
8
4
3
7
4
3
6
4
3
5
4
3
4
4
3
3
4
3
2

XI.RECOMMENDATIONS AGAINST INTERFERENCE
1. Recommendations for use of connecting wires
Wires th t tr nsmit simil r type of sign ls c n be p cked together, but if the sign ls re different,
the wires must be sep r ted to prevent electrom gnetic inter ction.
When there h ve to be crossed wires with different sign l types this must be done t n ngle of 90
degrees nd long dist nce.
Wires, which c rry we k sign ls nd wires connecting the sensors to the controller must not be ne r
cont ctors, motors, gener tors, r dios nd wires, which c rry l rge currents.
2. Noise suppression using the built-in in the regulator filter
If the input p r meter fluctu tes nd is not st ble it is necess ry to reduce the filter coefficient FILt.
As less v lue, s he vier filter nd slowly ch nge the input p r meter.
If the input p r meter jumps periodic lly for short interv ls it is necess ry to incre se the p r meter
AdBt. By incre sing of this p r meter the device re cts slowly with sh rply ch nge of the input
p r meter, but ignores short disturb nces.
3. Programming of Normal-Mode Rejection Ratio (NMRR) filter
Depending on the frequency of the power supply it is desir ble to select ppropri te (NMRR) filter
for me surement by p r meter from “Service menu” - rr = 0 for NMRR 80dB 50Hz or rr = 1 for
NMRR 65dB 50/60Hz.
XII. SETTING OF ANALOG INPUTS
1. SERVICE SETTING - [CodE=81]
This service mode is allowed to be used only from competent for that purpose person.
The setting is made in production and it is not necessary to be done by the user.
When setting should be used reference calibrator of electrical resistance, direct current and direct
voltage with accuracy ≥ 0.01% .
n failure setting it is possible to restore the factory settings by parameter Syst, rE = 1 from menu
"Hidden system parameters"
C n be c libr ted only some of the inputs or n intern l c libr tion to be m de.
This does not ffect the others.
Step [Pt 3] sets the me surement of ll RTD (Pt, Ni, Cu) nd the cold end of TC.
If intern l c libr tion is done, it is done first.
For ccess enter [CodE=81] (see ch pter IX)→ → [Clbr End] ppe rs on the displ y, then you
h ve to continue long the t ble.
Document revision 2015-03-20
19

[CodE=81]
[Clbr End] Returning in the oper ting mode,
selecting of input Clbr End→ Clbr Intr → Pt 3 →10 v → 20 mA → Clbr End → ...
[Clbr Intr] Intern l c libr tion. Compens tion points of 3-wire
RTD re shorted (termin ls 27,28). After
confirm tion [Clbr U it] ppe rs on the displ y. W it
c libr tion to complete lone for ~ 10 s.
[Pt 3] Reference resist nce 3кΩ h ve to be connected,
4-wire.
[10 v] Reference volt ge 10V h ve to be connected
[20nA] Reference current sign l 20 mA h ve to be connected
Confirms the reference,
c libr tion is performed – [done]
ppe rs on the displ y. Tr nsition to
the next input.
Select the next input
without c libr tion
•For the input r nge 10 V fter setting is necess ry to t ke ccount of the v lue in
the bsence of input sign l or with short on input termin ls. Tthen the s me v lue,
but with opposite sign must be entered in the lower r nge limit - rnGL / bout
0.03% of the r nge.
•For the r nge 1 V the optimum settings re m de in r nge '0 -1V non - st nd rd'.
1. SETTING OF LINEAR INPUT BY TWO REFERENCE POINTS – [CodE=80]
This setting destroys the service setting
Restoring of factory setting is possible using the parameter Syst, rE=1 from menu “Hidden system
parameters”
The type of setting is common for r nges 0-1V, 0-10V, 4-20mA nd 0-20mA.
In order the function to be v il ble, the p r meter Syst,Et=1,
The r nge rnGL,rnGH does not set re dings, it is only w rming.
This type of setting is ppropri te when the p r meters of connected tr nsmitter re unknown nd
could not be entered in rnGL,rnGH.
For ccess Syst,Et=1, otherwise returns utom tic lly in oper ting mode.
Enter [CodE=80] → → [tun1] ppe rs on the displ y → → on input is fed first reference
v lue → → with buttons is entered the fed v lue → → [tun2] ppe rs on the
displ y → → second reference v lue is fed → → with buttons is entered the fed
v lue → → oper ting mode.
Document revision 2015-03-20
20
This manual suits for next models
1
Table of contents
Popular Measuring Instrument manuals by other brands
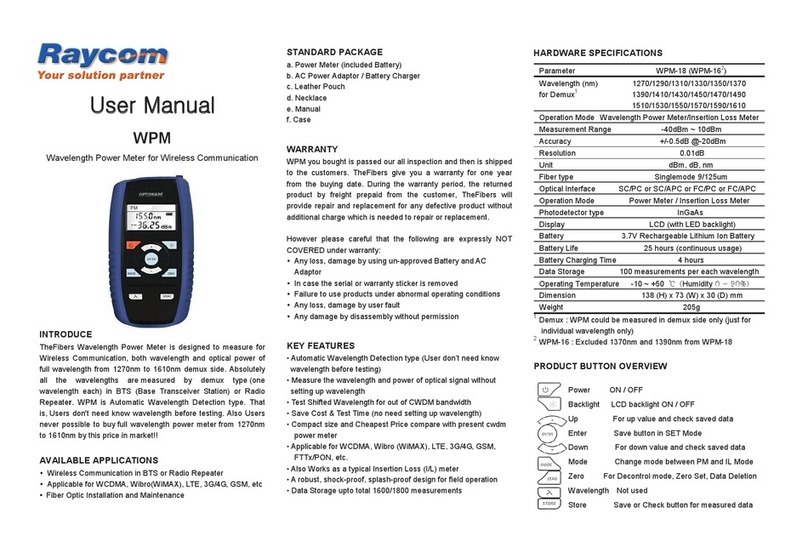
Raycom
Raycom WPM user manual

Shaw
Shaw SDHmini Series instruction manual
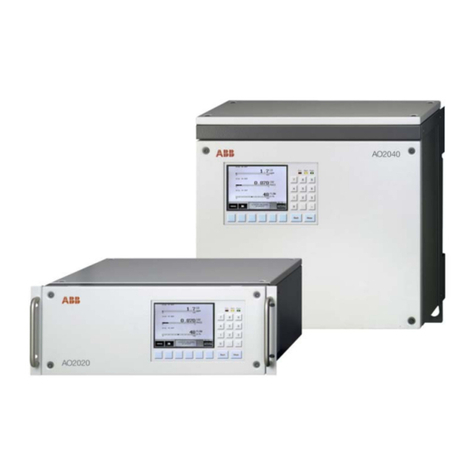
ABB
ABB Advance Optima magnos206 Operator's manual
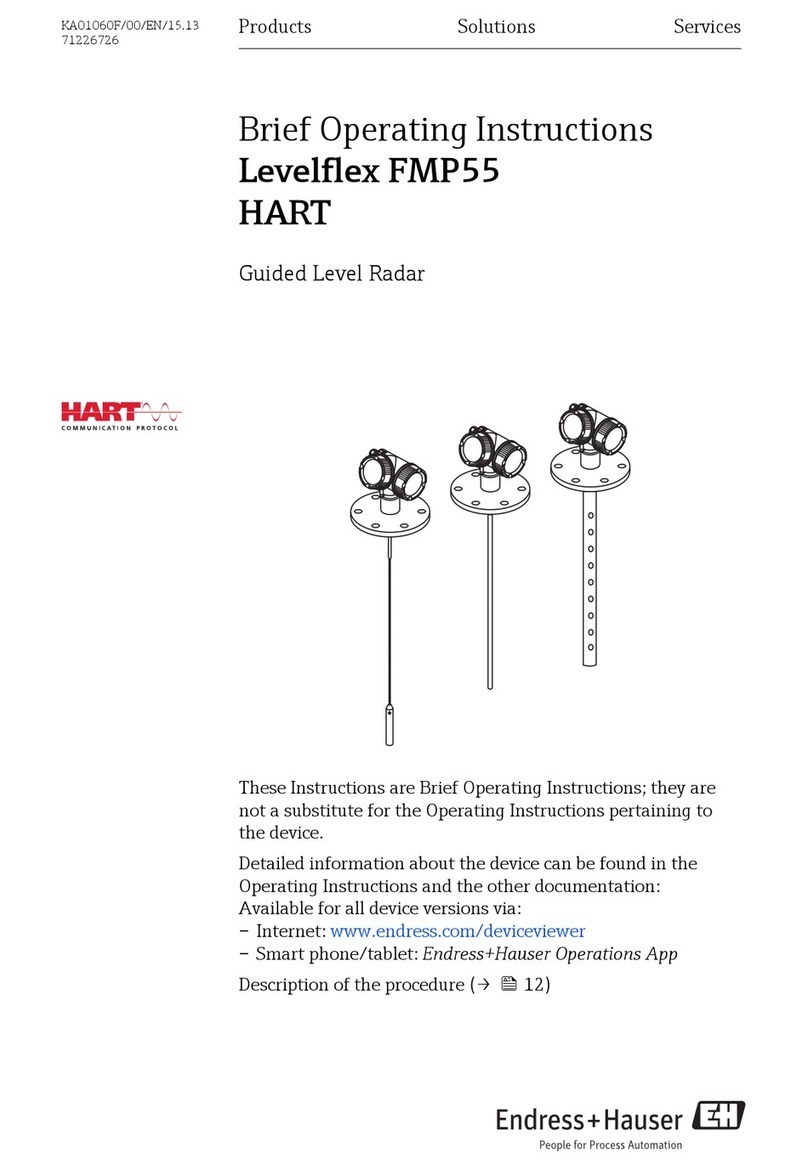
Endress+Hauser
Endress+Hauser Levelflex FMP55 Brief operating instructions
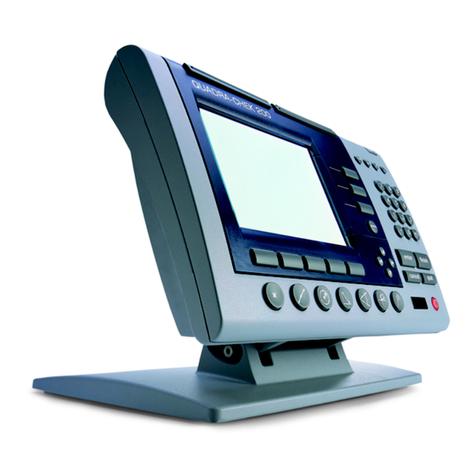
Metronics
Metronics Quadra-Chek 200 user guide
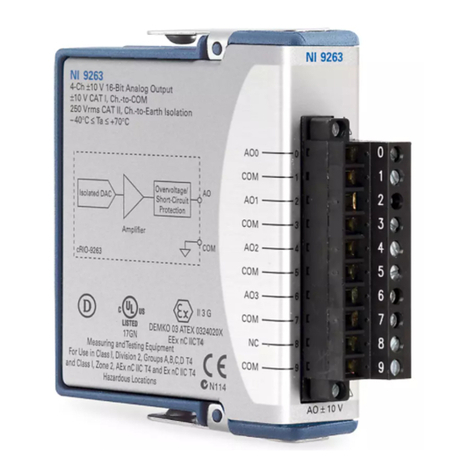
National Instruments
National Instruments NI 9263 operating instructions

Water I.D.
Water I.D. PoolLAB 1.0 user manual
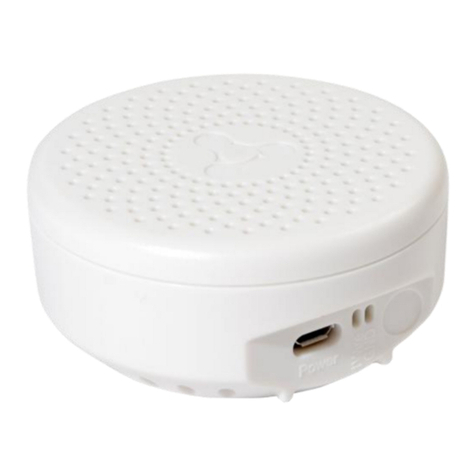
ELTEX
ELTEX Zwave PLUS SZ-AIR-HTQ01 user manual
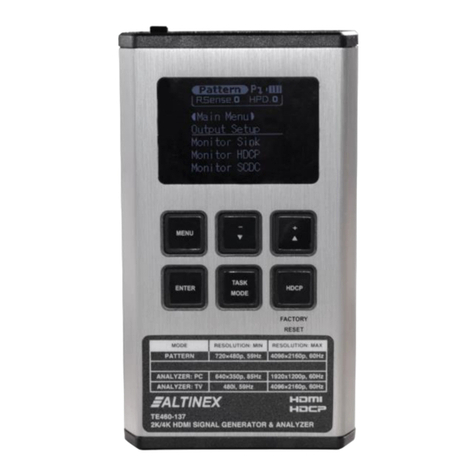
Altinex
Altinex SIGNAL MANAGEMENT SOLUTIONS TE460-137 user guide
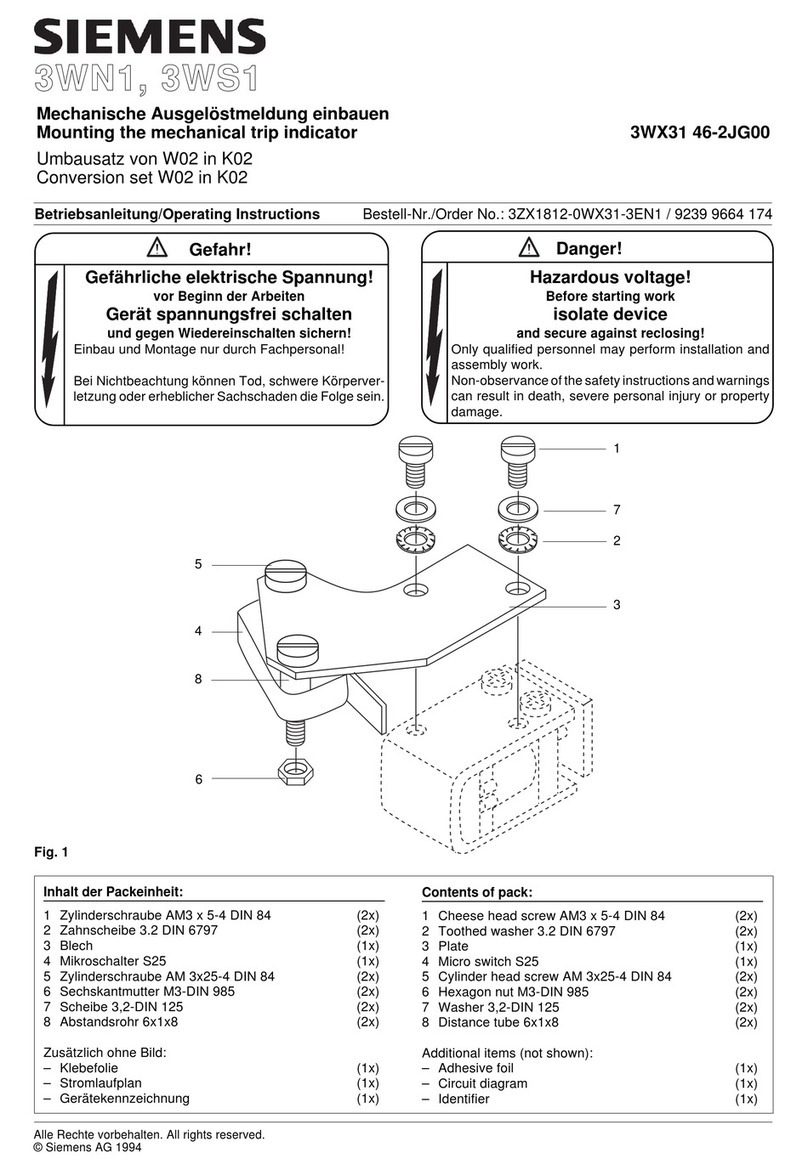
Siemens
Siemens 3WN1 Mounting

Bosch
Bosch GRL 250 HV Original instructions
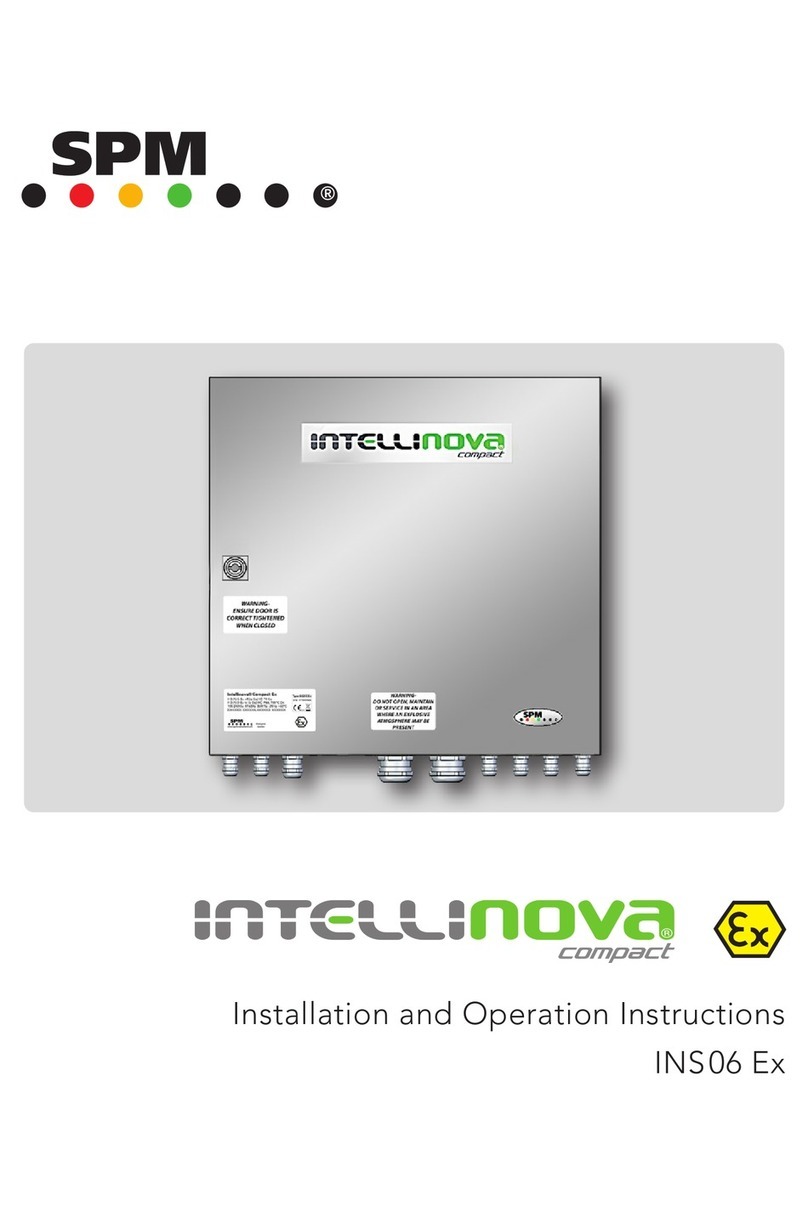
SPM
SPM intellinova compact INS06 Ex Assembly, installation and operation instructions