MMF VM23 User manual

Instruction Manual
Manfred Weber
Metra Mess- und Frequenztechnik in Radebeul e.K.
Meissner Str. 58 - D- 1445 Radebeul
Tel. +49-351 836 2191 Fax +49-351 836 294
Email: [email protected] Internet: www.MMF.de
Vibration Meter
VM23
Valid from firmware ver. xxx. 7

Published by:
Manfred Weber
Metra Mess- und Frequenztechnik in Radebeul e.K.
Meißner Str. 58
D-0 445 Radebeul
Tel. +49-35 -836 2 9
Fax +49-35 -836 2940
Email [email protected]e
Internet www.MMF.de
Note: The latest version of this manual can be found at http://www.mmf.de/prod-
uct_literature.htm
Specification subject to change.
© 20 6 Manfred Weber Metra Mess- und Frequenztechnik in Radebeul e.K.
Full or partial reproduction subject to prior written approval.
Jan/ 2

Contents
. Purpose.................................................................................................................3
2. Function................................................................................................................3
2. . The Sensor.....................................................................................................3
2.2. The Measuring Instrument............................................................................4
3. The Measurement Procedure................................................................................4
4. The Batteries.........................................................................................................6
4. . Inserting the Batteries....................................................................................6
4.2. Switching On and Off....................................................................................7
4.3. Battery Display and Battery Type.................................................................7
4.4. Shut-off Timer...............................................................................................8
5. Preparation of Measuring Points...........................................................................9
5. . General Information on Measurement Point Choice......................................9
5.2. ISO 208 6- Recommendations....................................................................9
5.3. VMID Measurement Point..........................................................................
5.3. . How the VMID Measurement Point Functions....................................
5.3.2. Mounting the VMID Measurement Point.............................................
6. Measurement...................................................................................................... 2
6. . Measurement Value Display........................................................................ 2
6.2. Measurement Point Detection...................................................................... 2
6.2. . Reading the VMID Data with the VM23............................................. 2
6.2.2. Entering the Measurement Point Text.................................................. 3
6.2.3. Deleting Measurement Point Data....................................................... 4
6.3. Saving Measurands...................................................................................... 4
7. Viewing Saved Measurement Data..................................................................... 5
7. . Graphical Trend Display............................................................................. 5
7.2. Viewing Saved Measurement Values.......................................................... 6
7.3. Deleting all Measurement Data................................................................... 6
8. Measurement Evaluation.................................................................................... 6
9. Setting the Date and Time.................................................................................. 9
0. Calibration........................................................................................................20
. Sensor Check....................................................................................................22
2. Reset Key..........................................................................................................22
3. Connection to a PC...........................................................................................23
3. . Device Driver............................................................................................23
3.2. Firmware Update.......................................................................................23
4. Technical Data..................................................................................................26
Appendix: Warranty
Declaration of CE Conformity

2
Figure : VM23 with sensor

Thank you for choosing a Metra Vibration Measurement Instrument!
1. Purpose
The VM23 has been developed, particularly, for the measurement and monitoring of
vibrations on rotating machines. In addition is is a useful tool for machines which
have the purpose of generating vibration, like vibration conveyors, vibrating screens
and separators.
Such measurements help to monitor the condition of the machine in order to avoid
unscheduled shut-down. Furthermore vibration measurement is carried out prior to
the distribution of new machinery and subsequently to repair with a view to quality
control and the issuing of product guarantees.
The basis for successful machine condition monitoring is the measurement of the vi-
bration severity over a longer period of time. Measurements are taken at regular in-
tervals of time and recorded.
The VM23 measures and records vibration velocity, also known as vibration sever-
ity. Its specification corresponds to the ISO 2954 regulations and is suitable for,
among other things, the measurement of machine vibrations on machines with a
nominal speed at or above 20 min- , in accordance with ISO 08 6. Additionally
the VM23 can measure vibration displacement and main frequency.
The VM23 includes different band filters for acceptance measurements according to
various standards, like ISO 208 6 or ISO 8528.
An external piezoelectric accelerometer is used as the sensor, and is provided to-
gether with the instrument. The VM23 is fitted with an electronic measurement
point detector (VMID) which enables it to take routine measurements of a large
number of measurement points very effectively. A software package for transferring
the measurement data to a PC is also available from Metra.
In the common hierarchy of condition monitoring the VM23 is equivalent to “Level
”. This represents the long term monitoring of parameters with low technical and
personnel requirements.
For fault detection (“Level 2”), as a further step, spectral diagnostic measurements
are taken, which require a large degree of expertise and sophisticated measurement
technology.
In the development of the VM23 value was placed on simple operation and mainte-
nance requirements, which enable trained personnel to operate the instrument with-
out the need of being specially qualified.
2. Function
2.1. The Sensor
The VM23 operates with a piezoceramic shear accelerometer. Piezoelectric vibra-
tion transducers are characterized by high precision and resolution with great ro-
bustness. The accelerometer of the VM23 has an integrated electronic circuit for im-
pedance conversion in accordance with the IEPE standard. At the base of the sensor
a magnet has been integrated for mounting to the measurement point. In the center
of the magnet there is a contact point from which the identification number can be
read. The measurement point ID is saved in the available VMID measurement
points.
The coupling surface is protected by a metal cap which attaches to the sensors mag-
netic base.
3

2.2. The Measuring Instrument
Figure 2 shows the block diagram. The VM23 supplies the IEPE Sensor with 2 mA
constant current. At the sensor output, a vibration acceleration proportional AC
voltage arises, which is amplified in the instrument to produce an optimum level.
The gain switch-over takes place automatically. The subsequent analog/digital con-
verter is a Sigma-Delta converter with 24 bit resolution.
Further signal processing, such as filtering, integration (for calculating velocity and
displacement from acceleration), RMS and peak-to-peak value calculation and fre-
quency analysis for main frequency detection, is carried out in the micro controller.
The micro controller also controls the graphic display, the USB communication and
the storing of measurements.
3. The Measurement Procedure
Measuring vibration velocity is a common procedure for assessing the running smooth-
ness of rotating machines. Vibration velocity, commonly known as vibration severity, is
a measurement of the energy expenditure of occurring vibrations. Vibrations are caused
by rotational imbalances, for example as a result of loose screws, bent parts, worn or
slack bearing clearance or dirt residues on fan blades. Often several factors have a mutu-
ally reinforcing effect. Besides rotary machines, the measurement procedure is also suit-
able for reciprocating machines.
The specifications of vibration velocity measuring instruments are described in
ISO 2954. In the ISO 2954 a band filter for the vibration velocity of 0 to 000 Hz is de-
fined. The VM23 has additional frequency ranges from 2 to 00 Hz and 2 to 000 Hz.
The corresponding frequency response graphs can be viewed in Figure 3.
The displayed values of the vibration severity are true RMS or true peak-peak.
For reasons of conformity with older instruments the VM23 also measures equivalent
peak-peak which is calculated by multiplying RMS with 2√2.
Note: Equivalent peak-peak measurements are only accurate for sine-wave oscillation.
In spite of this limitation equivalent peak-peak may be advantageous if true peak-peak
readings are very fluctuating. Higher stability is achieved by averaging over 2 seconds.
4
Figure 2: Block Diagram
IEPE
supply
Progr.
amplifier
A
D
Micro
controller
Display
Memory
Keys
Sensor
ID
USB
Power
supply

These settings are made in the main menu under “Measuring mode”.
For machines with the purpose of generating vibration, like vibration conveyors, vi-
brating screens and separators the VM23 can display the main vibration frequency.
At such machines the magnitude is usually measured as displacement.
Note: Displacement amplitudes at higher frequencies are very small due to double
integration of the accelerometer signal. Above approx. 300 Hz only the last digit of
the display changes. Therefore the diagram in Figure 4 shows ripple at the upper
end. Displacement measurements at higher frequencies should be avoided if possi-
ble since they are inaccurate. The ranges 2 to 000 Hz and 0 to 000 Hz are only
provided for reasons of compliance with some standards demanding such limits.
5
Figure 3: Frequency Response for vibration velocity
1 10 100 1000 10000
0,001
0,010
0,100
1,000
10,000 v: 2-100Hz
v: 10-1000Hz
v: 2-1000Hz
Hz
mm/s
Figure 4: Frequency Response for vibration displacement
1 10 100 1000
0,001
0,010
0,100
1,000
10,000 d: 3-60Hz
d: 3-200Hz
d: 2-300Hz
d: 2-1000Hz
d: 10-1000Hz
Hz
mm

4. The Batteries
4.1. Inserting the Batteries
The VM23 is supplied by three alkaline standard cell type AAA (LR03) batteries.
NiMH batteries (HR03) may also be used. The minimum energy requirement of the
VM23 enables maximum utilization of the batteries.
Attention: Please switch the instrument off before changing the batteries. When
switched off, the contents of the memory are stored for a few minutes, without need
of the batteries, and the internal clock continues to run. If the batteries are removed
when the instrument is switched on or if they remain in the instrument until the bat-
teries have been completely discharged, the device will perform a new start once the
batteries have been changed. Following a 'new start' the date and time will need to
be newly set. Further settings as well as the saved measurands, are stored without
need of the batteries.
To insert the batteries, remove the two screws from the back cover of the device and
open the battery compartment (Figure 5). When inserting the batteries, please ensure
that their polarity is correct, (see the engraved markings inside the compartment).
Important:
•Always use three batteries of the same type and same date of manufacture.
•Remove old batteries from the instrument, and take out the batteries if the instru-
ment will not be used for a long period of time. Otherwise leaking battery acid
may cause severe damage to the instrument.
6
Figure 5: Battery Compartment

Please use your local collection point to dispose of batteries.
Batteries do not belong to the household waste.
4.2. S itching On and Off
The instrument is switched on by a short press of the ON-OFF button. A start screen
will be shown on the display for 3 seconds. (Figure 6).
This displays the hardware version number (the 3 digits before the point) and the
software version number (the 3 digits after the point) followed by the serial number
corresponding to the type label. The month and year of the last calibration are dis-
played (cf. Section 0) along with the memory capacity.
By pressing the ON-OFF button again the VM23 switches itself off. In addition, the
instrument has an automatic shut-off timer for saving the battery power (see cf.
Chapter 4.4).
4.3. Battery Display and Battery Type
In the upper left corner of the VM23 display there is a battery level indicator (Fig-
ure 7). When the green battery symbol is full, the battery is fully charged.
7
Figure 6: Start Screen
Figure 7: Battery indicator upper left Figure 8: Select battery type

While non-rechargeable batteries have a cell voltage of .5 V, NiMH rechargeable
batteries deliver only .2 V per cell. The VM23 battery indicator can be adjusted to
both voltages. To adjust the voltage remove the sensor from the VMID and press F2
to open the main menu. Here the battery type can be changed by pressing F to
scroll down to the menu option 'Instrument Settings' and then pressing OK. Within
the sub-menu select “Battery type” by following the same instructions as before
(Figure 8) and then by pressing F scroll between F “Alkaline” (non-rechargeable,
.5 V) or “NiMH Accu” (rechargeable, .2 V). Confirm your choice by pressing OK
and exit the menu by pressing F2 repeatedly.
If the power supply drops below 3.3 V when using alkaline batteries or below 3 V
with rechargeable batteries, the battery indicator becomes red. Further measure-
ments can be taken until the power supply reaches 2.8 V in keeping with the instru-
ment specifications. At this point the battery level indicator is completely empty and
the instrument switches itself off automatically.
If the VM23 is connected to a USB port, it will be supplied by the USB voltage in
order to spare the batteries. In this case, “External” is displayed on the screen in -
stead of the battery level indicator.
4.4. Shut-off Timer
The VM23 has a shut-off timer to help prolong the battery operating life. To set the
shut-off timer, remove the sensor from the VMID and press F2 to open the main
menu. From the main menu scroll down to the sub-menu option “Instrument Set-
tings” by pressing F and OK. Here the menu option “Shut-off timer” can be se-
lected by pressing F and the timer duration options of , 5, 5 and 60 minutes can
be selected, alternatively to deactivate the switch off timer select “none”. The auto-
matic switch off timer starts to run after the last press of a button. If a button is
pressed then the timer restarts and counts down again according to the duration se-
lected.
8
Figure 9: Shut down time

5. Preparation of Measuring Points
5.1. General Information on Measurement Point Choice
When monitoring machines it is important to take measurements under the same op-
erating conditions, at the same measurement point. Choosing the suitable measure-
ment point is therefore decisive.
Where possible, qualified staff experienced in machine monitoring should be called
upon.
It is generally advisable to record machine vibrations near to their source. This helps
to reduce distortion of the measuring signal to a minimum when it is being carried
through transmission parts. Suitable measurement points include rigid machine
components such as bearing housings or gearboxes.
Light or mechanically flexible machine components such as cladding and casing are
unsuitable for the measurement of vibrations.
5.2. ISO 20816-1 Recommendations
The standard ISO 208 6- recommends bearing housings or their immediate sur-
roundings as preferred measuring location points for the measurement of machine
vibrations (Figures 0, , 2 and 3).
For the purpose of monitoring a rotating machine it is normally sufficient to take
measurements in only one direction, either vertically or horizontally.
On machines with horizontal shafts and rigid foundations the largest vibration am-
plitudes occur horizontally. With flexible foundations, strong vertical components
also arise.
For the purpose of acceptance tests, measurement values are to be taken from all
bearing point locations at the center of the bearing and in all three directions (verti-
cal, horizontal and axial).
The following illustrations give a few examples of suitable measurement point loca-
tions.
The Standard ISO 3373- also gives recommendations for measurement points on
various machine types.
9
Figure : Measuring points on flange
bearings
X
Y
Z
Figure 0: Measuring points on vertical
bearings
X
Y
Z

0
Figure 3: Measuring points on electric
motors
Z1 Z2
X2
Y1 Y2
X1
Figure 2: Measuring points on machines
with vertical rotors
Z
X1 Y1
X2 Y2
X3
X4
Y3
Y4

5.3. VMID Measurement Point
5.3.1. Ho the VMID Measurement Point Functions
The VM23 is equipped with an electronic measuring point detector. Metra offers a
type measurement point called VMID, which is made of magnetic stainless steel and
has an inbuilt memory with an individual serial number (Figure 4).
The serial number stored inside the measurement point is a unique 6-digit hexadec-
imal number, e.g. “000000FBC52B”.
Each measurand can be easily and reliably allocated to a specific measuring point.
To read the serial number, contact is made through the sensor's magnetic base.
The maximum permissible operating temperature for the VMID is 80 °C.
5.3.2. Mounting the VMID Measurement Point
A VMID measurement point is mounted onto the machine using two component
epoxy adhesive. For an accurate vibration transmission, Metra recommends the fol-
lowing adhesive:
•LOCTITE Hysol 3430 without filler for even surfaces
•LOCTITE Hysol 3450 with filler for uneven surfaces
Before applying the adhesive ensure that all residues of grease have been thor -
oughly removed from both contact surfaces. The two component adhesive can be
applied directly onto the chosen surface. The adhesive takes 5 minutes to harden
and after 5 minutes the first measurement can be taken.
For protection against dust and humidity according to IP67 please put the supplied
protective plastic cap on the VMID measurement points when no measurements are
taken.
Figure 4: VMID Measurement Point

6. Measurement
6.1. Measurement Value Display
In the top margin of the screen (Figure 5) the battery power is displayed. Next to
this the date and time are also indicated.
Below the measurand (d: 3-60Hz Peak-Peak) the currently measured vibration dis-
placement is displayed green in mm (or velocity in mm/s).
The blue line below shows the measurement point name if a VMID was detected.
6.2. Measurement Point Detection
6.2.1. Reading the VMID Data ith the VM23
The VMID measurement points are designed, so that the magnetic sensor base cen-
ters itself. To avoid mechanical shock do not let the sensor snap onto the measure-
ment point, instead, roll it slowly over the edge. To improve the vibration transmis-
sion the measuring point can be lightly lubricated.
When the Sensor base comes into contact with the measurement point for the first
time, the VM23 displays the VMID measurement point number (Figure 6).
2
Figure 6: Newly recognized VMID
Figure 5: Measurand display

6.2.2. Entering the Measurement Point Text
If a measurement point has not yet been assigned a text, press F to reach the text-
edit menu (Figure 7).
A space of two rows consisting of 0 characters each is assigned for the measure-
ment point text. The text can be entered by pressing F and F2, F selects the char-
acter for editing and F2 the character position. Both capital letters (A to Z) and
numbers (0 to 9) can be used. To reach the second row press OK and then to exit the
menu press OK again. After entering the ID text you can set filtering and integration
and choose between RMS and peak-peak detection.
Once you have assigned the VMID serial number a text, the VM23 will display the
text continually upon identification of the measurement point. (Figure 8).
The measurement point text can also be changed later by following the instruction
for the initial entry. Remove the sensor from the measurement point, open the main
menu by pressing F2, scroll down to the sub menu “Point ID Memory” by pressing
F and OK to select. From within the Point ID Menu select “Edit Point ID”. Select
your chosen measurement point by pressing F and then OK to edit. The editing of
the ID text is achieved by following the instruction given for the initial entry.
Note: Changing the measuring point data also effects the display of saved measur-
ands (cf. Chapter 7). The current saved text of the respective VMID series number
is always displayed in the measurement data.
3
Figure 7: ID-Text Entry
Figure 8: ID Text Display

The measurement point data is saved in the instrument. If several instruments are
used at the same measurement point location, the measurement point data will need
to be saved within each instrument.
6.2.3. Deleting Measurement Point Data
Remove the sensor from the measurement point and open the main menu by press-
ing F2 and select the sub menu “Point ID memory” by pressing F and OK.
Within the menu option “Erase Point ID”, measurement point data records, each
consisting of a VMID serial number, text and operational mode, can be deleted one
by one. In the subsequent menu “Erase Point ID”, press or hold down F until the
record you wish to delete is shown, then press OK and confirm the warning by
pressing F once again. (Figure 9).
In the same way, the entire measurement point data can be deleted as a whole by se-
lecting “Erase all Point IDs” in the “ID Menu”.
The VM23 memory can store data for a maximum of 600 measurement points.
Note: Deleting measurement point data effects the display of saved measurements.
Instead of the measurement point series number and the measurement point text be-
ing shown, “none” is displayed. The measurement point data records can always be
newly generated, as described in 6.2.2
6.3. Saving Measurands
The currently displayed measurands and their measurement point numbers (if avail-
able), as well as the date and time can be saved by pressing the F key.
Note: If the sensor locates a measurement point which has not yet been assigned a
text (cf. Chapter 6.2.2), the F key can be used to enter the new measurement point
text.
4
Figure 9: Deleting measurement Point Records

7. Vie ing Saved Measurement Data
7.1. Graphical Trend Display
The purpose of measuring vibration according to ISO 08 6 and ISO 3373 is as
follows; To make assessments concerning the operating condition of a machine
based on changes in its vibration behavior. To achieve this it is imperative, that
measurements are taken at regular time intervals, from the same points and under
the same conditions.
To deliver the service staff on site a report about the periodic changes in vibration
severity and consequently the previous history of the measurement point concerned,
the VM23 provides a graphical trend display. The prerequisite for retrieving graphi-
cal trends is placing the sensor on the relevant VMID. The trend display is obtained
by pressing the F2 key. (Figure 20).
The vibration magnitude (RMS or peak-peak) is shown on the vertical axis and the
time on the horizontal axis. Both are scaled to their respective maximum value. The
time axis shows the interval between the first and last saved measurement. Below
the diagram there is a red marker. This can be moved horizontally to read the mag-
nitude, with the F and F2 keys. The marker only skips forward to time points
which have a measurand. At each data point the date and time of the measurement
as well as the measured RMS are displayed. Above the diagram the text assigned to
the measurement point is displayed. In order to be able to display trends, the points
are joined together by a line.
Press the OK key to exit the trend display.
If only one or zero measurands for a selected measurement point can be located in
the memory, the error message “Too few data for trending” will appear instead of
the trend graphic.
5
Figure 20: Trend Display

7.2. Vie ing Saved Measurement Values
In addition to the graphical trend readings for current measurement points, saved
measurement data can be viewed in text format. Remove the sensor from the mea-
surement point, open the main menu by pressing F2, select the sub-menu “Measure-
ment data memory” by pressing OK and within the sub-menu press OK to select
“View measurement data memory”. The first data record will now be displayed. At
the top, a consecutive number and the number of the data record within the memory
will be shown. Below these, the measuring point serial number and its assigned text
are displayed. The saved measurand is displayed underneath the date, time and filter
type in use (Figure 2 ).
With F you can scroll to the next measurand. The currently displayed measurands
can be deleted by pressing OK. Press F2 to exit the menu.
The VM23 memory can hold 6000 measurement values.
7.3. Deleting all Measurement Data
Select in the sub-menu “Measurement data memory” “Erase meas. data memory” in
order to delete all measuring data. After pressing OK a warning message will appear
showing the total number of records.
8. Measurement Evaluation
To be able to derive statements from the measured vibration velocity values about
the condition of a machine, experience is necessary. If experienced personnel are
not available, in many cases one can refer to the ISO 08 6 recommendations. In
this standard, the vibration severity zone limits for various machine types are de-
fined, which can provide an initial evaluation of a machines maintenance condition.
The four zone boundary limits characterize the machine in categories according to
vibration severity.
A: New condition
B: Good condition for unrestricted continuous operation
C: Poor condition - allows restricted continued operation only
D: Critical condition - Danger of damage to the machine
In the appendix of part , extended in 2009, general zone restrictions for machines
which are not separately dealt with in other parts of the standard are specified.
6
Figure 2 : Viewing Saved Measurement Values

veff 1 – 1 Hz
45 mm/s
28 mm/s
18 mm/s
14.7 mm/s Zone
C/D
4.5 – 14.7
mm/s
11.2 mm/s
9.3 mm/s Zone
B/C
1.8 – 9.3
mm/s
7.1 mm/s
4.5 mm/s Zone
A/B
0.71 – 4.5
mm/s
2.8 mm/s
1.8 mm/s
1.12 mm/s
.71 mm/s
.45 mm/s
.28 mm/s
D Risk of machine damage
C Restricted continued operation
B Unrestricted operation possible
A Newly operating machine
Table : Typical zone limit values for vibration severity according to ISO 08 6- .
In the standard it is pointed out that small machines, for example electric motors
with a power rating of up to 5 kW, tend to lie around the lower zone limits,
whereas large machines, for example motors with flexible foundations, lie around
the upper zone limits.
7

In part 3 of the ISO 08 6, revised in 2009, the zone borders for the vibration ve-
locity of machines with a power of 5 kW to 50 MW are specified (2).
Machine type
Large machines with 3
kW to 5 MW
Medium sized machines
with 15 to 3 kW
Electric motors with a
shaft height above 315
mm
Electric motors with a
shaft height between
16 and 315 mm
Foundation flexible rigid flexible rigid
veff 1 – 1 Hz
> 11 mm/s D D D D
> 7.1 mm/s C D D D
> 4.5 mm/s B C C D
> 3.5 mm/s B B B C
> 2.8 mm/s A B B C
> 2.3 mm/s A B B B
> 1.4 mm/s A A A B
< 1.4 mm/s A A A A
D Risk of machine damage
C Restricted operation
B Unrestricted long-term operation possible
A Newly commissioned
Table 2: Vibration velocity classification in accordance with ISO 08 6-3
8
Table of contents
Other MMF Measuring Instrument manuals
Popular Measuring Instrument manuals by other brands
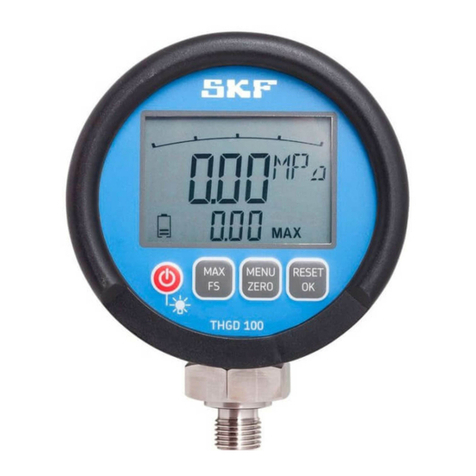
SKF
SKF THGD 100 Instructions for use

Büttner Elektronik
Büttner Elektronik Dometic MT iQ Basic Pro Installation and operating manual
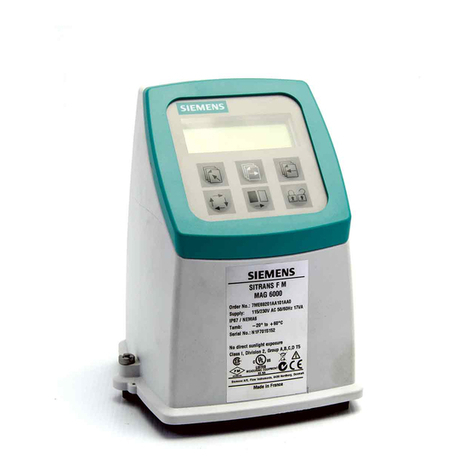
Siemens
Siemens SITRANS F M MAG 5000 operating instructions

Sper scientific
Sper scientific 840065 instruction manual

NeurOptics
NeurOptics NPi-300 Instructions for use
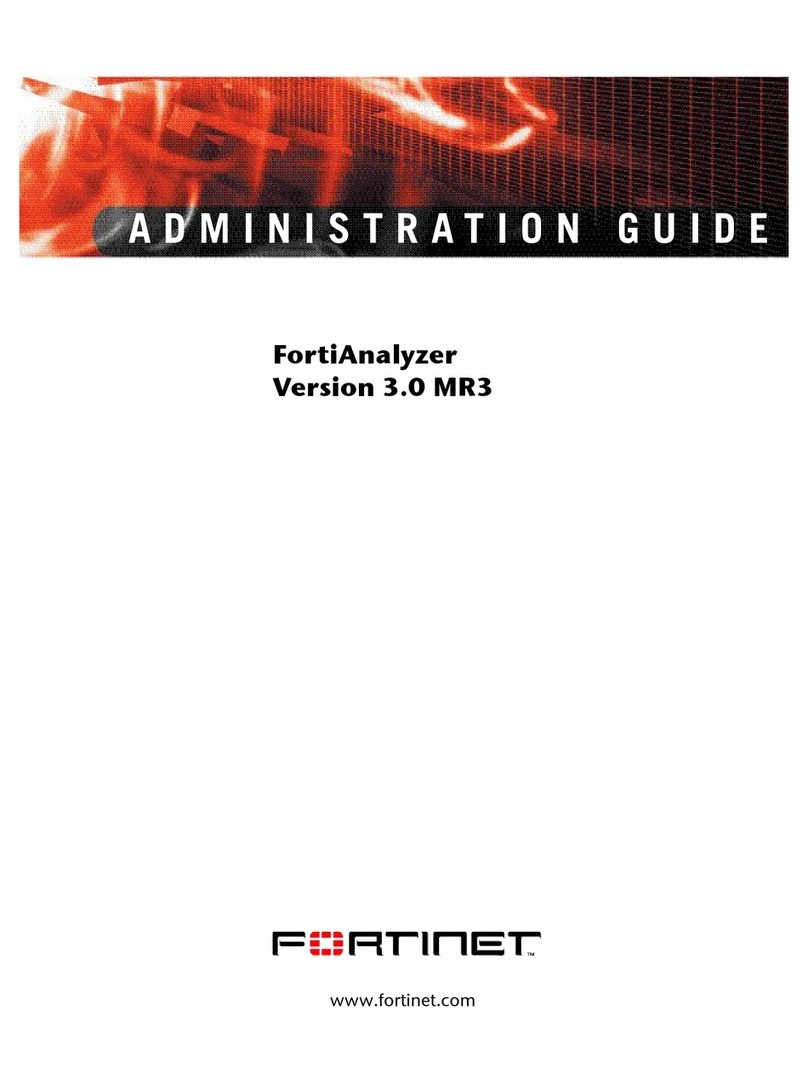
Fortinet
Fortinet FortiAnalyzer-100A Administration guide