molitor MAD User manual

Instruction manual
MAD with EDS-2
Table of contents Page
1. Safety Precautions 2
2. General / Mode of Operation 4
3. Installation and Mounting 5
4. Wiring and Connections 6
5. Keys and Display 9
6. Display Functions and Initial Settings 11
7. Operating Indicators / menu / Startup 12
8. Trip history monitor 13
9. Expert mode 16
10. Clear presentation of the menu structure MA 18
11. Customer Settings 18
12. Technical execution, terminal diagram, schematic of the respective controller
Pump controller
!1
Pump-Controller :
Pressure regulation System for Pumps
MAD-EDS-2 Software version 2012......

1. Safety Precautions
Before installing and commissioning of the pump controller, please read the product manual carefully and
observe all warnings and safety instructions. Keep this manual is always easily accessible in the vicinity of
the frequency converter controller.
Definition of Information
Warning!
In disregard of the safety instructions may lead to serious and life-threatening bodily injury
or property damage occur, a significant!
Caution!
Failure to observe these instructions may lead to serious and life-threatening bodily injury
or property damage occur, a significant!
Notice!
Failure to observe these instructions may lead to malfunction of the plant!
Warning!
The frequency inverter controller generates dangerous electrical voltages and controls
potentially dangerous rotating mechanical parts.
Warning!
The installation, Initial Settings and maintenance of these drives can only be by qualified
personnel who are familiar with the operation, carried out.
Warning !
Give special care when automatic restart is enabled. To prevent injuries caused by any
inadvertent restart of inverter controller after a power failure, turn off in case of doubt the
automatic restart. For repair and maintenance work at the plant, you notice that the system
can not be turned on by other again!
Warning!
The frequency inverter controllers have the lead after the mains off dangerously high
voltage. Wait, therefore, after switching off the mains for at least 5 minutes before you work
on the device. It is important to ensure that no live parts are touched, or when voltage is
applied between the capacitors are charged. Do not work on the wiring and make sure no
signals when voltage is applied.
Caution!
All pump controllers are tested for dielectric strength and insulation resistance. Be
disconnected before the isolation measurement on the pump unit, for example, as part of the
inspection, the frequency control!
Pump controller
!2
Warning!
Caution!
Notice!
Warning!
Caution!
Warning!
Warning!

Warning!
The drive - controller has a leakage current. Ground the frequency -
Controller at the designated ports.
The customer's RCCB must be an in-MAH, MAS2, MAK, MAE - dial to pole sensitive /
selective RCCB tripping with type B be 300 mA.
The customer's RCCB must be a the MAI, MAD, MAG - dial to pole sensitive RCCB type B
with his tripping 30 mA. It is recommended to secure the separate frequency - control.
Observe the regional regulations for electrical installation!
Warning!
Make sure that the input voltage corresponds to the nameplate voltage registered.
Caution!
Environmental conditions such as high temperatures, high humidity should be avoided as well
as dust, dirt and corrosive gases. The installation should be a well-ventilated and not exposed
to direct sunlight location.
Caution!
Do they no mains power to the sensor terminals or to the control terminals.
Caution!
Enter the operating signals START / STOP button on the control panel on or about the
triggering of the external contacts and not by turning on and off a mains or motor contactor.
Caution!
It is strongly recommended that all electrical equipment conforms to the National Electrical
Codes and local regulations. Only qualified personnel should perform installation, alignment
and maintenance. The manufacturer reserves the right to alter the technical data in order to
make improvements or update information.
Notice!
The technical data and descriptions in this guide are correct to the best knowledge and belief.
Technical improvements have been continuously carried out - that's why the manufacturer
reserves the right, without prior notice to carry out such changes.
The manufacturer can not be held liable for errors in the manual.
Warranty is within Germany and within the
incorporated statutory warranty period and applies only to the product itself and
not for any consequential loss or damage or costs associated with the occurrence of a
Warranty claim arise at other plants or plant parts. The operator
shall, in each case to ensure that a failure or defect in the product
can not lead to further damage.
Pump controller
!3
Warning!
Caution!
Notice!
Warning!
Caution!
Caution!

2. General / Mode of Operation
2.1 MA .... Pressure Control System
Congratulations on purchasing this high-quality pump control. This product complies with the latest
technology and is continually developed and improved. The device was subjected to the production of an
extensive examination and therefore functions properly. To read to ensure optimal function and observe these
operating instructions.
This frequency inverter controller operates as an automatic pressure regulator, tested.
The speed of the pump (s) will be adjusted continuously. The actual pressure in the system is determined by
pressure transducer (sensor). A PI controller regulates the pressure by analogy.
The pressure regulator is programmable and can be adapted to the respective operating conditions. The
parameters are displayed on the display in plain text. Commissioning is menu driven. During
commissioning, some data must be entered to ensure the smooth operation of the pumping plant. An
adjustment of specific parameters (expert mode) requires special knowledge of pump technology. This
should be done by a competent person or the manufacturer.
2.2 Benefits of speed control:
- almost constant pressure
- Continuous adjustment of pump power to the changing operating conditions
- Energy saving
- a speed-double unit replaces a four-fold pressure switch system
- low mechanical wear of the pumps
- Maintenance
2.3 Principles of pressure control
To operate a speed control can be accurately and effectively, the following points to consider:
-the pump (s) must be construed in accordance with the plant / Requirement
-the pump (s) shall have power reserves available (80. .90%) = system reserve capacity at rating
-with submersible pumps must be based on an output reduction of about 5. .10%
2.4 Construction of a pressure control system
Non-return valve preventer is imperative and must be in the pressure behind the
Pump will be installed! The expansion tank is to be fitted if required.
1 Flow direction 2 Controller
3 Motor 4 Pump
5 Non-return valve 6 Pressure Transducer
7 Pressure vessel
Example 1 pump System Example 2 pumps System
Pump controller
!4
Caution!

2.5 Note for the operation of the system with Pressure vessel!
If the plant is operated with a pressure vessel, the vessel must be pre-pressed in normally state.
The pre-squeezing pressure should be checked regularly. The amount of pre-squeezing pressure is: Start
pressure bar minus 0.20.
e.g.: Nominal System Pressure: 4.00 bar
Vessel Air Pressure: 3.80 bar
2.6 Booster Sets
Booster units are ready plumbed and wired pump installations. For them, the installation cost
is minimal - connect to the existing network of pipes, mains and commissioning. The
regulator is factory set at these facilities.
This manual refers only to the electrical control of the system is therefore possibly the pump
consult the manual (s) note the / partition.
See manufacturers data sheet.
3. Installation and Mounting
Environmental conditions such as high temperatures, high humidity should be avoided as well as dust, dirt
and corrosive gases. The installation should be a well-ventilated and not exposed to direct
sunlight location.
Because of convection, the frequency control during installation of at least
Be installed 15 cm from side walls or other facilities.
The allowable temperature range of +5 ° C to +30 ° C must not be under-or exceeded.
Do not install the Inverter controller near heat-radiating bodies.
3.1 Mounting the MA.... Controller
Metal box:
In the rear contains holes for wall mounting of the cabinet.
The sole assembly recommended hung stud to the electrical cabinet.
Mounting Dimensions: See manufacturers data sheet MAD.
Pump controller
!5
Notice!
Caution!
Waning!

4. Wiring and Connections
Make sure that the input voltage corresponds to the nameplate voltage registered.
Be sure to supply voltage and terminal assignment instructions!
The installation, commissioning and maintenance of the actuators may be of
an expert who is familiar with the pump system will be implemented.
Shielded cable! Screen to the grounding clamps in the cabinet and connected to the pump!
For submersible pumps combine the screen with a ground potential in the vicinity of the
pump.
Do they no mains power to the sensor - or control terminals.
No manipulation of the sensor signal to make!
No other users connect to the 24V supply!
The used pressure sensor (0. .10 V) or (4. .20 mA),
is connected to the respective terminals!
The respective pin assignment, refer to the respective diagram.
In systems with several pumps are used again and 0. .10 V sensors.
Here you can optionally one or more sensors are connected.
The respective pin assignment, refer to the respective diagram.
Notice!
If the motor cable longer than 100 meters, it is advisable to install an motor reactor.
Caution!
Verify the correct connection of the network, sensor, and control lines.
4.1 Motor Protection
The MAD - EDS-2 has a monitoring role for the motor current.
The motor current is set on the motor protection relay or soft starter.
As a special version thermistor to monitor temperature can be used.
Contactor Soft Starter 3RW40
4.2 Connection of inputs / outputs
The lower part of the cubicle MAD is the terminal strip.
The line to the pump, the sensor line and the lines for the external contacts will be connected to appropriate
wires. Screening is not required.
Only with proper installation, trouble-free operation is guaranteed!
Pump controller
!6
Caution!
Warning!
Notice!
Warning!
Caution!

4.3 Wiring diagram EDS-2 module
1- pump unit 2- pumps unit
4.4 Terminals
When power supply, alarm relay, relay (option), external inputs (option), external outputs (option), sensor
(s), pump (s), they face each diagram or schematic or picture of each terminal controller: MAD, MAG on.
4.5 Power Supply
Clamp Function Description
PE Power Supply PE Ground
L1 L1 Phase
L2 400V AC L2 Phase
L3 L3 Phase
NN Neutral
or:
PE Power Supply PE Ground
L1 L1 Phase
N230V AC N Neutral
4.6 Port for the alarm relay
Function Description
Potential-free contact AL 1 (17)
Register relay contact AL 2 (18)
230V 1 A contact AL 3 (16)
4.7 Port for the Run relay
Function Description
Potential-free contact 4 (24)
Register relay contact 6 (26) Run Signal (Option)
Power Supply
(Option)
Register Relay
Pump controller
!7

4.8 Port for the external inputs MAD/G
Clamp Function Description
7 / 13 low water / external On /Off Ext. 34
10 Start/Stop/Reset (only MAG) Ext. 25
10 Reset (only MAD) Ext. 25
81 Reference voltage P24 VDC +
87 Reference voltage OI VDC -
18 / 82 PTC (Option) Kaltleiter 1
38 / 82 PTC (Option) Kaltleiter 2
Caution!
Use shielded cable and connect it to the grounding clamps in the cabinet! The maximum length of the control
lines may not exceed 20 meters.
Ext. 34: Alarm external Input „Low water“.
Ext. 25: external input „Limit function“. (only MAG)
Ext. 25: external input „Reset“. (only MAD)
4.9 Port for the transducer
Funktion DescriptionReference voltage P24 VDC +
Reference voltage L VDC -
Transducer signal OI 4-20mA
Caution!
Use shielded cable and connected to the grounding clamps in the cabinet!
Note terminal assignment (see the sensor Type plate)!
4.10 Port for the motor / pump
Clamp Function Description
U3 phase motor U1
Vsee the V1
WType plate W1
Caution!
Motors must be connected corresponding the output voltage (230V or 400V): Star- or Delta- connection
(motor terminal board)! Output voltage = input voltage.
4.11 Port for the motor / pump: single Phase
Clamp Function Description
U3 phase motor U1
Vsee the V1
Caution!
Verify the correct connection of the network, transducer, and control lines.
Check before switching on the mains again all connections are correct!
4,12 Frequent installation failures
- Sensor is connected wrong
- Sensor is not installed in the pressure pipe behind the non-return valve
- Non-return valve is not installed or not installed in the right direction
- Pipes/pumps are not ventilated
- Wrong running direction
- Motor terminal board is connected wrong (output voltage! Star- or Delta- connection?)
For faults please the notes under 9.2. Troubleshooting note!
external
Input
(Option)
PTC
Motor
Motor
Pump controller
!8

5. Panel Description
5.1 Block rocker and rotary switches
(Rocker, which is above gray side is active!)
Rocker: 1+2 1-2
Rocker: Alarm OFF
Rocker: Test OFF
Rocker: DS DY
Rotary switch A: Target ON 0-10 bar / 25 bar
(depending Transducer)
Rotary switch B : Target OFF 0-10 bar / 25 bar
(depending Transducer)
Rotary switch T: Run On Time 0-30 sec. (5-30 sec.)
Lamp P1: Pump 1 on Run
Lamp P2: Pump 2 on Run
Lamp Alarm: Alarm active
Reset button: Alarm Reset
Relay K1: P1 pump switches, relay K2: P2 pump switches, alarm relay: switches at fault
5.2 Rocker: Mode 1 + 2 / 1-2
This switch sets the operating mode of the system
1+2: Operation of the system with a base load and peak load pump.
In this mode, the pump with rotary switch "A" one-
connected with rotary switch "B" off.
With the rotary switch "T" they set the delay time. The
Pump is changed after each run.
The second pump is switched on automatically as needed
1-2: Operation of the system with base-load pump.
In this mode, the base-load pump with rotary switch "A"
with rotary switch on and "B" switched off.
With the rotary switch "T" they set the delay time. The
Pump is changed after each run.
The second pump is not switched on. Automatic
Switchover in case of failure on the other pump.
5.3 Rocker: Alarm ON / OFF
This switch set the alarm mode. "Water shortage"
If the alarm is "ON" is switched to the alarm relays to "water shortage".
The pressure monitoring, which is active after the fill mode is,
50% of engaging and delayed by 3 minutes for the off!
Dry Run!
If the shift switch "dry run" is active, turn the power off whenever the system
pressure of 0.5 bar is not reached in 60 seconds.
Fill mode!
If the system is switched "power on" is the lack of water only active if the pumping
station has been turned off for the first time to the set pressure.
Caution!
Pump controller
!9

If the alarm is OFF, the alarm relays to "water shortage" is not turned off
The "OFF" is used in fire-fighting operation to prevent a shutdown of the pumps.
Alarm relay does not switch at fault..
Rocker: Alarm ON / OFF
This switch set the alarm mode. "Switching"
Fault switching!
The pump system is monitored for switching game! Each pump is designed for
switching up to 60 times per hour.
If the alarm is "ON" is switched to the alarm relays to "Fault switching".
The alarm relay switches when the fault
If the alarm is OFF, the alarm relays to "Fault switching" is not turned off.
The "OFF" is used in fire-fighting operation to prevent a shutdown of the pumps.
Alarm relay does not switch at fault..
5.4 Rocker: Test ON / OFF
This switch set the 24-hour test run.
This function is used to prevent the pump and one to prevent.
This function is set to fire-fighting operation.
5.5 Rocker: DS / DY
This switch sets the operating mode of the system
DS: Operation of the system with air tank ( pressure switch).
In this mode, the pump on the rotary switch "A" is turned on and to dial "B" switched off.
With the rotary switch "T" they set the Run on Time. The pressure vessel is in pre-pressed at 0.5 bar above
cut-in.
The pump is changed after each run. The second pump is automatically switched on as needed or switched at
fault.
DY: Operation of the facility without pressure vessels (Dynamic mode).
In this mode, the pump on the rotary switch "A" is turned on and off to turn "B" in promoting zero.
With the rotary switch "B" is the switch-off (0.1 - 1 bar).
With the rotary switch "T" they set the Run on Time.
The pump is changed after each run. The second pump is automatically switched on as needed or switched at
fault.
Caution!
Pump controller
!10

6. Applications
Single pump system or a double pump system with expansion tank, alarm and test run
6.1 Pressure switch operation
Operating mode 1+2 1-2
Alarm Mode Select ON OFF
Test Run Enable ON OFF
DS – Stop operation DS -----
Rotary switch A: Target ON z.B. 2,5 bar
Rotary switch B: Target OFF z.B. 4,5 bar
Rotary switch T: Run on Time 0-30 sec. z.B. 3,0 sec.
Single pump system or a double pump system with no expansion tank, alarm and test run "OFF"
6.2 Dynamic switch Operation
Operating mode 1+2 1-2
Alarm Mode Select ON OFF
Test Run Enable ON OFF
DS – Stop operation ---- DY
Rotary switch A: Target ON z.B. 1,5 bar
Rotary switch B: Target OFF z.B. 0,3 bar
Rotary switch T: Run on Time 5-30 sec. z.B. 10,0 sec.
Lock off: The settings are adjustable
Bridge 30/31 (yellow) is open.
Lock on: The settings are not adjustable
Bridge 30/31 (yellow) is closed.
Pump controller
!11

7. Switching / operation / start messages
7.1 General operation of the EDS-2
The pump control MA .... EDS-2, by setting various functions and operational parameters in individual cases
can be optimally adapted to all possible operating conditions. The unit is preset at the time of delivery to
keep the cost of commissioning local minimum. To set the necessary data to any operating parameters, a
switch can be changed. The menu items are invoked as described above. For each parameter is a setting in
which either select an option or a value range can be adjusted.
7.2 Conditions for starting the MA .... Control
Before control is put into operation the following requirements must be met:
- System / pump suction and discharge side connected to the pipeline!
- Piping and pumps are filling!
- Electrical connection is made and checked!
7.3 First turn on the MAD-EDS-2
Caution!
When the alarm to "Off" are lack of water protection and
Switching cycle monitoring is not active! The protection system must be external!
Caution!
When the alarm to "on" position is the only active when water protection
the pump station for the first time has stopped in the pressure (fill mode)!
MAD-Switch EDS-2!
The EDS-2 reports for you! turning the main switch / line voltage
with the inset:
The following message appears on the display:
Custom text
Custom text
00000 RH 00000 RH
Version: 200XXXXX
Notice!
Pump controller
!12

8.Operation indicators / Commissioning
8.1 MAD-EDS2 into operation
The EDS2 logs after the startup screen! with the main picture:
The rotary switches A, B, T on the EDS-2 set.
ON:2,0
OFF : 3,5
TIME: 10s
Pumps Off
The pump / pump by switching on the "manual mode" to "turn" position.
ON:3,0
OFF : 5,5
TIME: 10s
Hand P1 Hand P2
Check direction of rotation!
If the wrong direction: switch network, replace two phases. Control!
If the rotational direction is correct, switch to "automatic mode" position.
ON:3,0
OFF : 5,5
TIME: 10s
Pressure mode on
ON:3,0
OFF : 4,4
TIME: 10s
Dynamic mode on
In automatic mode, the pumps - the pressure regulator automatically
according to the sensitivity. Important: check!
Caution! In manual mode, the pump runs continuously.
Caution! In manual mode, there is no protection!
Pump controller
!13
00,5
01,5
04,5
04,5
Caution!

8.2 Operation indicators on the display EDS-2
After the main switch / voltage of the operational data in the display appear:
Startup message for 20 sec.:
Custom text
Custom text
00000 RH 00000 RH
Version: 200XXXXX
Startup screen when you turn for 20sec.
Custom text
RH–(Run Hour) Operating hours for each pump
Software Version: Year, month, day
ON:2,0
OFF : 3,5
TIME: 10s
Pumps Off
The power supply is on.
No pump is on.
Mode is not known.
The current pressure is 0.5 bar.
ON:2,0
OFF : 3,5
TIME: 10s
Pressure mode on
The power supply is on.
Pump is turned on.
Pressure switch mode is selected..
The current pressure is 2.5 bar.
ON:2,8
OFF : 3,0
TIME: 10s
Dynamic mode on
The power supply is on.
Pump is turned on.
Dynamic switch mode is selected.
The current pressure is 2.5 bar.
ON:2,0
OFF : 3,5
TIME: 10s
Hand-P1 Hand-P2
The power supply is on.
Pump 1 or Pump 2
or both are turned on manually
The current pressure is 7.5 bar.
ON:2,0
OFF : 3,5
TIME: 10s
Extern Off
The power supply is on.
Pump or pumps are turned off externally.
Float switch is open or missing from pressure.
The current pressure is 0.5 bar.
Pump controller
!14
00,5
02,5
02,5
07,5
00,5

9. Error messages
9.1 Error messages on the display of the EDS-2
In case of trouble off the pressure switch from module and the pump is running independently.
The error message is displayed in plain text display.
Fault can be reset by driving the external input "Reset".
Fault message, pressing the reset button to reset!
AutoP1
Auto P2
Error
Open Transducer
The power supply is on.
Pump or pumps are turned off.
The Transducer connection is open!
The current pressure is not known.
AutoP1
Auto P2
Error
Low Water
The power supply is on.
Pump or pumps are turned off.
Electronic low water protection is active!
The current pressure is 0.5 bar.
AutoP1
Auto P2
Error
Dry Run
The power supply is on.
Pump or pumps are turned off.
Electronic dry run protection is active!
The current pressure is 0.4 bar.
AutoP1
Auto P2
Error
Defect Transducer
The power supply is on.
Pump or pumps are turned off.
The Transducer is defective!
The current pressure is not known.
ON:2,0
OFF : 3,5
TIME: 10s
Trip-P1 Trip-P2
The power supply is on.
Pump or pumps are turned off.
The motor protection has tripped.
The current pressure is 0.5 bar.
AutoP1
Auto P2
Error
Error Switching
The power supply is on.
Pump or pumps are turned off.
Too many Switching (> 30 / 60) per hour.
The current pressure is 0.5 bar.
ON:5,0
OFF : 3,5
TIME: 10s
Wrong Setting
The power supply is on.
Pump or pumps are turned off.
The pressure "ON" is higher than the
pressure, "OFF ".
Pump controller
!15
00,0
00,5
10,5
00,5
00,5
00,5
00,4

9.2 Troubleshooting
Monitor is dark
Utility power and turned on?
If one or more fuses are broken?
Pump does not start
The start command is not!
Selector switch is on center position!
Fuses of the load circuit test!
Pump does not start, even though "Auto"signal appears on the display
Sensor is not connected? (Message: "Sensor Error")
The actual pressure is reached, or cut-out?
The pressure switch „On“ is set too small?
Pump does not stop
If the „Off“ pressure set too high (pump creating the pressure does not)?
If the off threshold is set too low?
If the pipeline of the system is not vented properly?
Back flow preventer installed not in the pressure line from the sensor?
If the check valve leaking?
In short, rigid piping, expansion tank installed in the discharge line downstream of the back flow preventer (check the
pre-press pressure: start pressure - 0.5 bar)!
Pressure monitor does not show the right pressure
Factor for “transducer type” is wrong (e.g., 10 bar - Sensor, 25 bar - sensor)?
Transducer plug is wet?
Transducer cable is faulty?
Soft starter is too warm
Check ambient temperature! If necessary. they cool!
Reduce switching frequency!
Pump switches on and off quickly
Reduce switching frequency!
Check the expansion tank air buffer
Display shows no data and pumps do not start
EDS-2 module is defective.
Control fuse in the EDS-2 check.
10. Expert mode
10.1 Dry run protection
If the internal slide switch set to "dry run", the pump (s) monitored at all times in automatic or hand mode
to "dry run". The pump (s) are stopped when the system pressure of 0.5 bar in 60 seconds is not reached.
10.2 Electronic low water protection
The electronic "water protection" is a pressure monitoring.You to monitor the system pressure in automatic
below. The pressure monitoring will be active after the fill mode. The fill mode is active again after every
interruption. The system pressure falls below the switch pressure „On“ by 50% for longer than 3 minutes,
off the system.
10.1 Pump change
Which of the pump first starts up, is not defined.To ensure smooth operation of the pumps, all operating
cycles or at least every 24 hours, the master / slave - changed operation. If a pump is stopped or fails due to a
defect, the master will switch status.
10.2 Forced pump change
Opening external release contact is changed, the master and slave. Now can be treated in the same way with
the new master.
Pump controller
!16

10.3 Dynamic Operation Mode (DY)
The mode "DY" provides for the safe shutdown output "0 " during operation of the pump system
without the expansion tank or a very small expansion tank..
In the mode "DY" turns the pump on the pressure (!) and off to output "0 "!
Using the rotary switches A, text "ON", set the starting pressure of 0-100%. You should adjust the pressure
„On“ switch as low as possible.
The rotary switch B, text "OFF", set the sensitivity (!) of the switch-off between 0-10%. The pressure-Off
with the switch-off form a mathematical combination.
The logic of the mathematical combination is:
Off pressure = measured pressure measurement cut-up time + - = Switch-off standby.
Off The pressure is calculated after each switching cycle On / Off "again (!).
The rotary switch T, text "TIME", set the delay time between 5 sec and 30 sec,
to the output "0" off point to reach safely.
The mode "DY" requires some experience in recruiting and detailed knowledge of the operation of the pump
controller. If the system working satisfactorily, please contact a dealer or manufacturer.
This setting trace across the display.
To set the switch-off knowledge is required!
10.4 Reset the operating hours
A reset operation hours for the customer not planned!
To reset the operating hours to 00000, the following procedure:
The reset button on the display. During the startup screen appears briefly put the clamp 28 on the EDS-2 to
ground terminal 36. Reset is done!
It appears this message on the display:
10.5 Self-test the EDS-2 module
A self-test of the EDS-2 module is not intended for the customer!
To test the EDS-2 module, the following procedure:
The terminal 28 to ground 36 firmly connect. Mains supply. The EDS-2 responds with: Start self-test. The
display changes to show self-test.The reset button on the Display button to cancel the self-test or end.
It appears this message on the display:
Notice!
ON:2,0
OFF : 5,5
TIME: 10s
Dynamic mode on
RESET
0 RH 0 RH
Self-test
aAbBcCdDeEfFgGhHiIhH
Pump controller
!17
05,6

11. Technical data
11.1 Modes in the EDS-2 set:
After the opening of the EDS2 can be connected to the internal switch block set different operating
modes:
Switch block inside:
Transducer 10 bar / Transducer 25 bar
Limit Funktion Modus / pressure switch modus
English / Deutsch
Dry Run off / Dry Run on
11.2 Technical data EDS-2
Supply voltage 230 VAC, max. 5 W
Sensor connection UB: 24VDC, S: 4 to 20 mA, 70 mA max.
Relay 3 x floating 230VAC 1A (6A)
Pressure range: 0 .. 100% of sensor value, follow-up time: 0-100%
Ambient temperature +5 ... +40 ° C
View LCD text display illuminated
IP 54 (according to the cabinet design)
The cabinet dimensions are different depending on the version and need to be asked separately.
12. Customer Settings
Customer Settings from: ______________
Pressure On A ______________ bar
Pressure Off B ______________ bar
Run On Time T ______________ sec
Switch 1 ON / OFF 1+2 / 1-2 ______________
Switch 2 ON / OFF Alarm / OFF ______________
Switch 3 ON / OFF Test / OFF ______________
Switch 4 ON / OFF DS / DY ______________
Locking Yes / No ______________
Date: _______________________ from: _________________________
Pump controller
!18
This manual suits for next models
1
Table of contents
Popular Controllers manuals by other brands
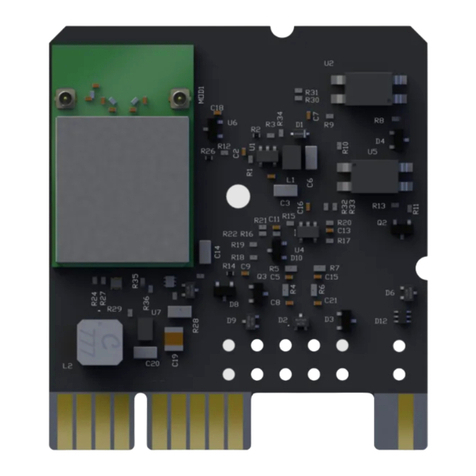
Synapse
Synapse DIM10-087-06 install guide
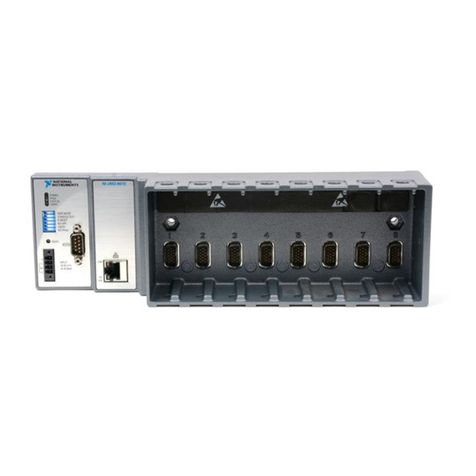
National Instruments
National Instruments CompactRIO cRIO-9072 User manual and specifications
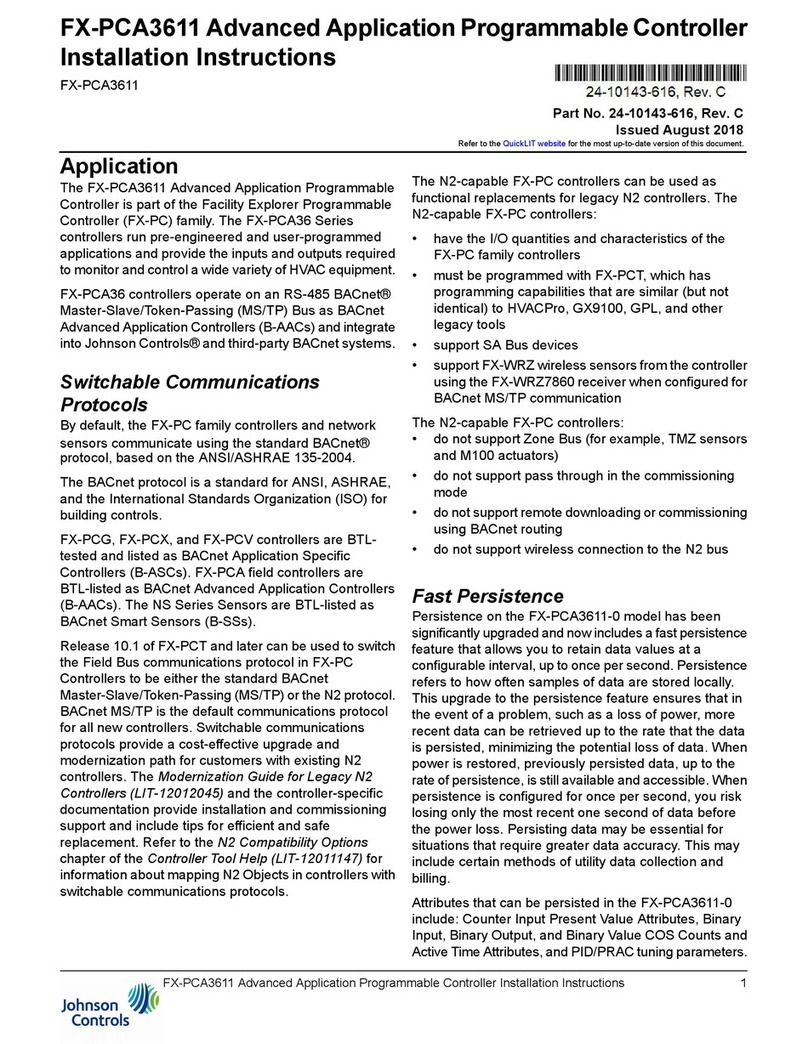
Johnson Controls
Johnson Controls FX-PCA3611 installation instructions

AKO
AKO 15440 instructions
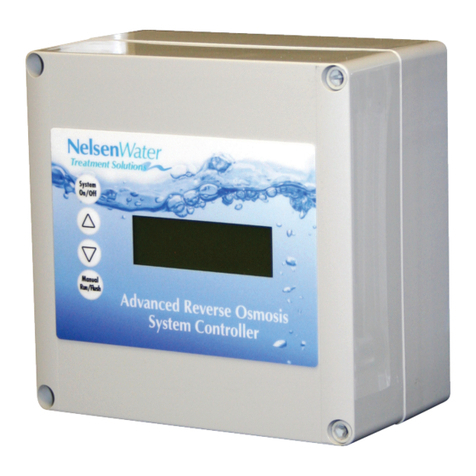
NELSEN WATER
NELSEN WATER NRO ROC-3HE manual
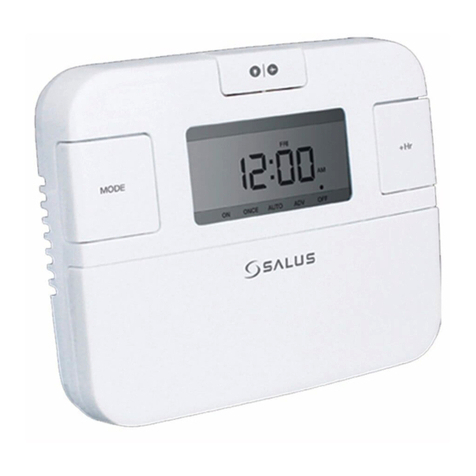
Salus
Salus EP110 Installer Manual and Quick Guide
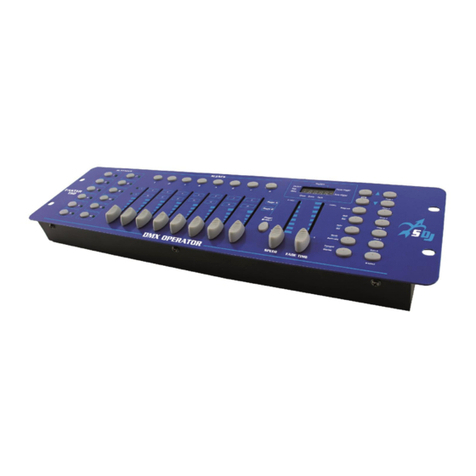
SDJ
SDJ SG FASTER192N user manual
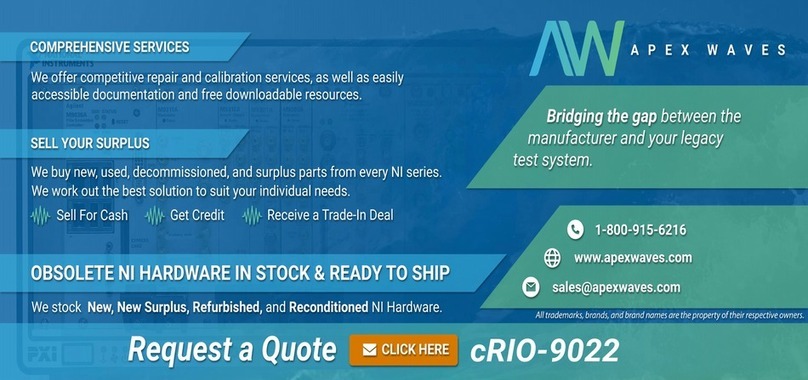
National Instruments
National Instruments NI cRIO-9022 User manual and specifications
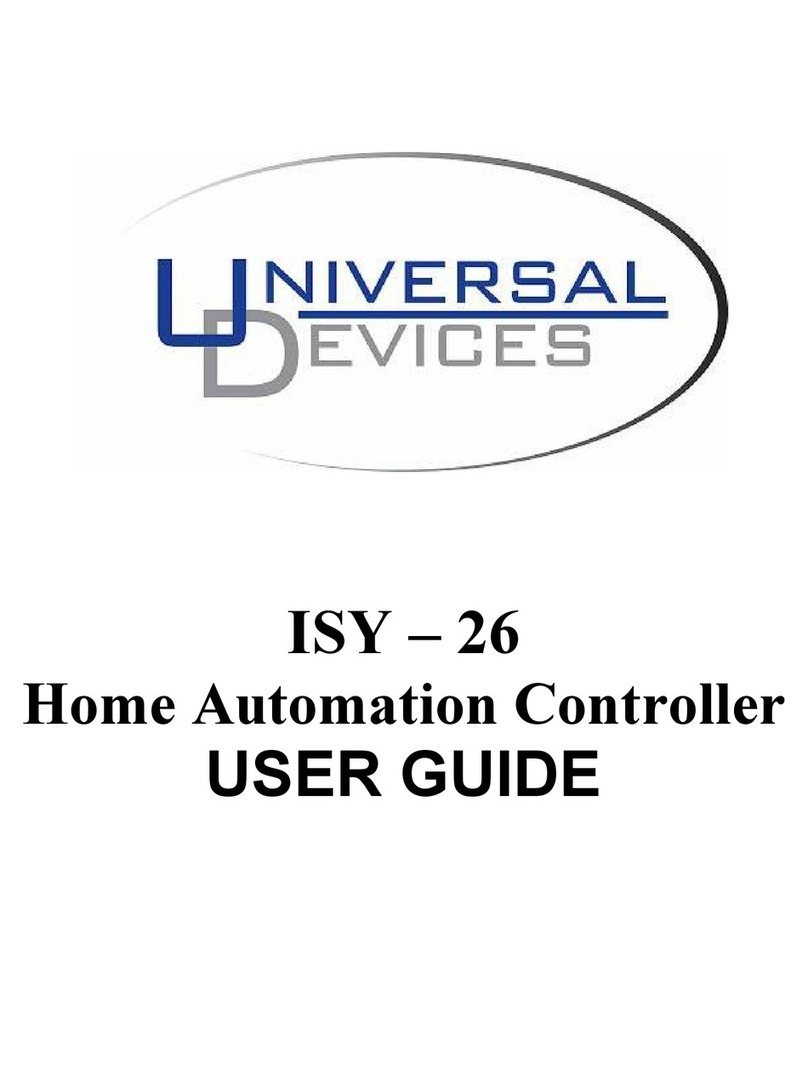
Universal Devices
Universal Devices ISY-26 user guide
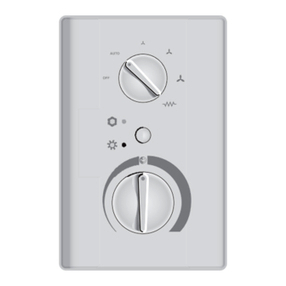
Daikin
Daikin ECFWEB6 Installation and operation manual

Controlli
Controlli SH 2 Series manual
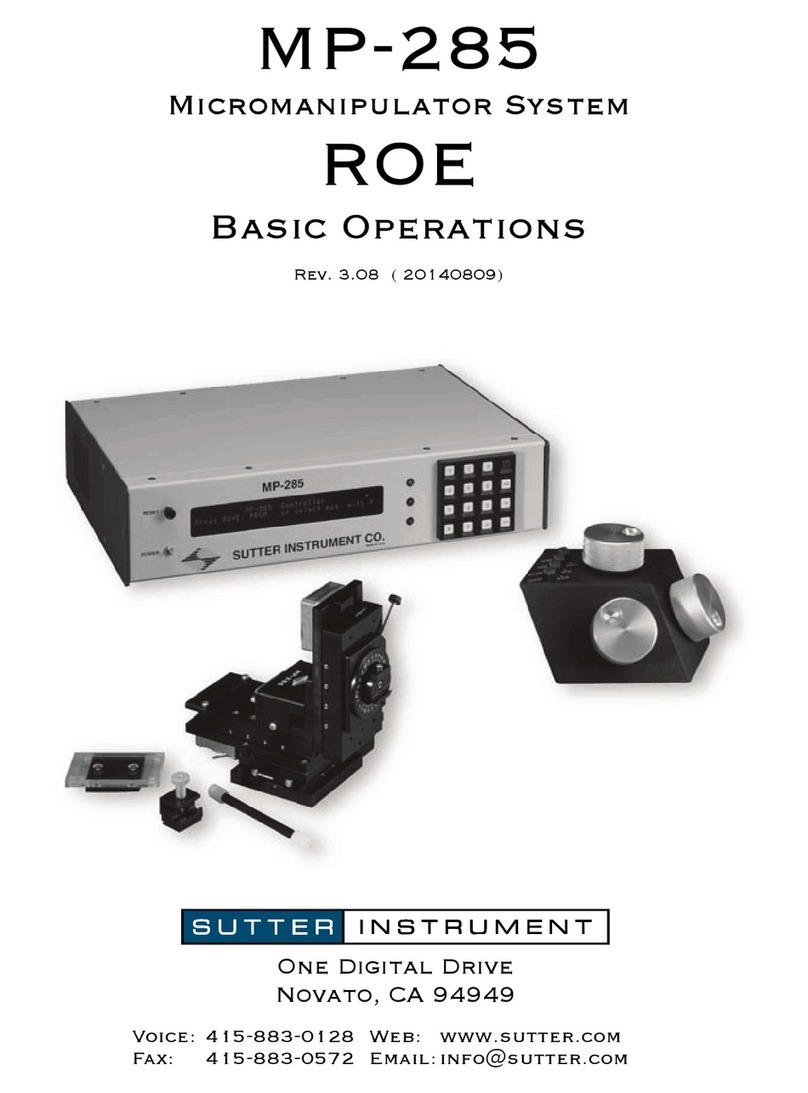
Sutter Instrument
Sutter Instrument MP-285 Basic operations