National Instruments FOUNDATION NI-FBUS Mounting instructions

FOUNDATIONTM Fieldbus
NI-FBUS Hardware and Software User Manual
NI-FBUS Hardware and Software User Manual
August 2011
371994G-01

Support
Worldwide Technical Support and Product Information
ni.com
Worldwide Offices
Visit ni.com/niglobal to access the branch office Web sites, which provide up-to-date contact information,
support phone numbers, email addresses, and current events.
National Instruments Corporate Headquarters
11500 North Mopac Expressway Austin, Texas 78759-3504 USA Tel: 512 683 0100
For further support information, refer to the Technical Support and Professional Services appendix. To comment
on National Instruments documentation, refer to the National Instruments Web site at ni.com/info and enter
the Info Code feedback.
©2006–2011 National Instruments Corporation. All rights reserved.

Important Information
Warranty
The NI-FBUS hardware is warranted against defects in materials and workmanship for a period of one year from the date of shipment, as
evidenced by receipts or other documentation. National Instruments will, at its option, repair or replace equipment that proves to be defective
during the warranty period. This warranty includes parts and labor.
The media on which you receive National Instruments software are warranted not to fail to execute programming instructions, due to defects in
materials and workmanship, for a period of 90 days from date of shipment, as evidenced by receipts or other documentation. National Instruments
will, at its option, repair or replace software media that do not execute programming instructions if National Instruments receives notice of such defects
during the warranty period. National Instruments does not warrant that the operation of the software shall be uninterrupted or error free.
A Return Material Authorization (RMA) number must be obtained from the factory and clearly marked on the outside of the package before any
equipment will be accepted for warranty work. National Instruments will pay the shipping costs of returning to the owner parts which are covered by
warranty.
National Instruments believes that the information in this document is accurate. The document has been carefully reviewed for technical accuracy. In
the event that technical or typographical errors exist, National Instruments reserves the right to make changes to subsequent editions of this document
without prior notice to holders of this edition. The reader should consult National Instruments if errors are suspected. In no event shall National
Instruments be liable for any damages arising out of or related to this document or the information contained in it.
EXCEPT AS SPECIFIED HEREIN, NATIONAL INSTRUMENTS MAKES NO WARRANTIES, EXPRESS OR IMPLIED, AND SPECIFICALLY DISCLAIMS ANY WARRANTY OF
MERCHANTABILITY OR FITNESS FOR APARTICULAR PURPOSE. CUSTOMER’SRIGHT TO RECOVER DAMAGES CAUSED BY FAULT OR NEGLIGENCE ON THE PART OF NATIONAL
INSTRUMENTS SHALL BE LIMITED TO THE AMOUNT THERETOFORE PAID BY THE CUSTOMER. NATIONAL INSTRUMENTS WILL NOT BE LIABLE FOR DAMAGES RESULTING
FROM LOSS OF DATA, PROFITS, USE OF PRODUCTS, OR INCIDENTAL OR CONSEQUENTIAL DAMAGES, EVEN IF ADVISED OF THE POSSIBILITY THEREOF. This limitation of
the liability of National Instruments will apply regardless of the form of action, whether in contract or tort, including negligence. Any action against
National Instruments must be brought within one year after the cause of action accrues. National Instruments shall not be liable for any delay in
performance due to causes beyond its reasonable control. The warranty provided herein does not cover damages, defects, malfunctions, or service
failures caused by owner’s failure to follow the National Instruments installation, operation, or maintenance instructions; owner’s modification of the
product; owner’s abuse, misuse, or negligent acts; and power failure or surges, fire, flood, accident, actions of third parties, or other events outside
reasonable control.
Copyright
Under the copyright laws, this publication may not be reproduced or transmitted in any form, electronic or mechanical, including photocopying,
recording, storing in an information retrieval system, or translating, in whole or in part, without the prior written consent of National
Instruments Corporation.
National Instruments respects the intellectual property of others, and we ask our users to do the same. NI software is protected by copyright and other
intellectual property laws. Where NI software may be used to reproduce software or other materials belonging to others, you may use NI software only
to reproduce materials that you may reproduce in accordance with the terms of any applicable license or other legal restriction.
Trademarks
LabVIEW, National Instruments, NI, ni.com, the National Instruments corporate logo, and the Eagle logo are trademarks of National
Instruments Corporation. Refer to the Trademark Information at ni.com/trademarks for other National Instruments trademarks.
Other product and company names mentioned herein are trademarks or trade names of their respective companies.
Members of the National Instruments Alliance Partner Program are business entities independent from National Instruments and have no agency,
partnership, or joint-venture relationship with National Instruments.
Patents
For patents covering National Instruments products/technology, refer to the appropriate location: Help»Patents in your software,
the patents.txt file on your media, or the National Instruments Patent Notice at ni.com/patents.
Export Compliance Information
Refer to the Export Compliance Information at ni.com/legal/export-compliance for the National Instruments global trade compliance
policy and how to obtain relevant HTS codes, ECCNs, and other import/export data.
WARNING REGARDING USE OF NATIONAL INSTRUMENTS PRODUCTS
(1) NATIONAL INSTRUMENTS PRODUCTS ARE NOT DESIGNED WITH COMPONENTS AND TESTING FOR A LEVEL OF
RELIABILITY SUITABLE FOR USE IN OR IN CONNECTION WITH SURGICAL IMPLANTS OR AS CRITICAL COMPONENTS IN
ANY LIFE SUPPORT SYSTEMS WHOSE FAILURE TO PERFORM CAN REASONABLY BE EXPECTED TO CAUSE SIGNIFICANT
INJURY TO A HUMAN.
(2) IN ANY APPLICATION, INCLUDING THE ABOVE, RELIABILITY OF OPERATION OF THE SOFTWARE PRODUCTS CAN BE
IMPAIRED BY ADVERSE FACTORS, INCLUDING BUT NOT LIMITED TO FLUCTUATIONS IN ELECTRICAL POWER SUPPLY,
COMPUTER HARDWARE MALFUNCTIONS, COMPUTER OPERATING SYSTEM SOFTWARE FITNESS, FITNESS OF COMPILERS
AND DEVELOPMENT SOFTWARE USED TO DEVELOP AN APPLICATION, INSTALLATION ERRORS, SOFTWARE AND HARDWARE
COMPATIBILITY PROBLEMS, MALFUNCTIONS OR FAILURES OF ELECTRONIC MONITORING OR CONTROL DEVICES,
TRANSIENT FAILURES OF ELECTRONIC SYSTEMS (HARDWARE AND/OR SOFTWARE), UNANTICIPATED USES OR MISUSES, OR
ERRORS ON THE PART OF THE USER OR APPLICATIONS DESIGNER (ADVERSE FACTORS SUCH AS THESE ARE HEREAFTER
COLLECTIVELY TERMED “SYSTEM FAILURES”). ANY APPLICATION WHERE A SYSTEM FAILURE WOULD CREATE A RISK OF
HARM TO PROPERTY OR PERSONS (INCLUDING THE RISK OF BODILY INJURY AND DEATH) SHOULD NOT BE RELIANT SOLELY
UPON ONE FORM OF ELECTRONIC SYSTEM DUE TO THE RISK OF SYSTEM FAILURE. TO AVOID DAMAGE, INJURY, OR DEATH,
THE USER OR APPLICATION DESIGNER MUST TAKE REASONABLY PRUDENT STEPS TO PROTECT AGAINST SYSTEM FAILURES,
INCLUDING BUT NOT LIMITED TO BACK-UP OR SHUT DOWN MECHANISMS. BECAUSE EACH END-USER SYSTEM IS
CUSTOMIZED AND DIFFERS FROM NATIONAL INSTRUMENTS' TESTING PLATFORMS AND BECAUSE A USER OR APPLICATION
DESIGNER MAY USE NATIONAL INSTRUMENTS PRODUCTS IN COMBINATION WITH OTHER PRODUCTS IN A MANNER NOT
EVALUATED OR CONTEMPLATED BY NATIONAL INSTRUMENTS, THE USER OR APPLICATION DESIGNER IS ULTIMATELY
RESPONSIBLE FOR VERIFYING AND VALIDATING THE SUITABILITY OF NATIONAL INSTRUMENTS PRODUCTS WHENEVER
NATIONAL INSTRUMENTS PRODUCTS ARE INCORPORATED IN A SYSTEM OR APPLICATION, INCLUDING, WITHOUT
LIMITATION, THE APPROPRIATE DESIGN, PROCESS AND SAFETY LEVEL OF SUCH SYSTEM OR APPLICATION.

Compliance
Electromagnetic Compatibility Information
This hardware has been tested and found to comply with the applicable regulatory requirements and limits for electromagnetic
compatibility (EMC) as indicated in the hardware’s Declaration of Conformity (DoC)1. These requirements and limits are
designed to provide reasonable protection against harmful interference when the hardware is operated in the intended
electromagnetic environment. In special cases, for example when either highly sensitive or noisy hardware is being used in close
proximity, additional mitigation measures may have to be employed to minimize the potential for electromagnetic interference.
While this hardware is compliant with the applicable regulatory EMC requirements, there is no guarantee that interference will
not occur in a particular installation. To minimize the potential for the hardware to cause interference to radio and television
reception or to experience unacceptable performance degradation, install and use this hardware in strict accordance with the
instructions in the hardware documentation and the DoC1.
If this hardware does cause interference with licensed radio communications services or other nearby electronics, which can be
determined by turning the hardware off and on, you are encouraged to try to correct the interference by one or more of the
following measures:
• Reorient the antenna of the receiver (the device suffering interference).
• Relocate the transmitter (the device generating interference) with respect to the receiver.
• Plug the transmitter into a different outlet so that the transmitter and the receiver are on different branch circuits.
Some hardware may require the use of a metal, shielded enclosure (windowless version) to meet the EMC requirements for
special EMC environments such as, for marine use or in heavy industrial areas. Refer to the hardware’s user documentation and
the DoC1for product installation requirements.
When the hardware is connected to a test object or to test leads, the system may become more sensitive to disturbances or may
cause interference in the local electromagnetic environment.
Operation of this hardware in a residential area is likely to cause harmful interference. Users are required to correct the
interference at their own expense or cease operation of the hardware.
Changes or modifications not expressly approved by National Instruments could void the user’s right to operate the hardware
under the local regulatory rules.
1 The Declaration of Conformity (DoC) contains important EMC compliance information and instructions for the user or
installer. To obtain the DoC for this product, visit ni.com/certification, search by model number or product line,
and click the appropriate link in the Certification column.

©National Instruments Corporation vii NI-FBUS Hardware and Software User Manual
Contents
About This Manual
Conventions ...................................................................................................................xi
Related Documentation..................................................................................................xii
Chapter 1
Introduction
FF Overview ..................................................................................................................1-1
NI-FBUS Hardware Products ........................................................................................1-1
PCI, PCMCIA, and USB .................................................................................1-1
HSE..................................................................................................................1-2
NI-FBUS Software Products .........................................................................................1-2
Communications Manager...............................................................................1-2
Configurator ....................................................................................................1-2
Monitor ............................................................................................................1-3
Chapter 2
Installation and Configuration
Installing the Software ...................................................................................................2-1
Installing the Hardware..................................................................................................2-2
Install Your PCI-FBUS Card...........................................................................2-2
Install Your PCMCIA-FBUS Card .................................................................2-3
Install Your USB-8486....................................................................................2-5
Mount and Connect Your USB-8486................................................2-7
Install Your FBUS-HSE/H1 LD......................................................................2-12
Setting the Communication Parameters and Interface Name ........................................2-15
Testing the Installation...................................................................................................2-17
Changing or Deleting Existing Interface Information.....................................2-17
Importing Device Descriptions ......................................................................................2-18
Chapter 3
Connector and Cabling
PCI-FBUS/2...................................................................................................................3-1
Fieldbus Cable Connector Pinout....................................................................3-1
PCMCIA-FBUS.............................................................................................................3-2
Pinout Information...........................................................................................3-2
USB-8486 ......................................................................................................................3-4
9-Pin D-SUB (DB-9) Cable Information ........................................................3-4

Contents
NI-FBUS Hardware and Software User Manual viii ni.com
FBUS-HSE/H1 Linking Device .................................................................................... 3-5
Ethernet Cable Pinouts.................................................................................... 3-6
Fieldbus H1 Pinout Information ..................................................................... 3-7
Chapter 4
NI-FBUS CM Software
NI-FBUS Communications Manager Overview ........................................................... 4-1
Installing the OPC NI-FBUS Server ............................................................................. 4-2
NI-FBUS Functions Overview ...................................................................................... 4-2
Administrative Functions ................................................................................ 4-2
Example: Using Administrative Functions....................................... 4-3
Core Functions ................................................................................................ 4-3
Example: Using Core Functions....................................................... 4-4
Alert and Trend Functions .............................................................................. 4-4
Device Description Functions......................................................................... 4-5
Using the NI-FBUS Communications Manager Process................................ 4-6
Developing Your NI-FBUS Communications Manager Application ........................... 4-7
Choose Your Level of Communication .......................................................... 4-7
Choose to Access by Name or Index .............................................................. 4-7
Choose to Write Single-Thread or Multi-Thread Applications ...................... 4-8
Single-Thread Applications .............................................................. 4-8
Multi-Thread Applications ............................................................... 4-8
Access Object Dictionary Entries ................................................................... 4-9
Access Management Information Base (MIB) Parameters............................. 4-9
H1 Device MIB List Parameters ...................................................... 4-10
H1 Device MIB Parameters.............................................................. 4-10
HSE Device MIB List Parameters.................................................... 4-11
HSE Device MIB Parameters ........................................................... 4-11
Use the NI-FBUS Dialog Utility to Communicate with Devices ................... 4-11
Write Your Application .................................................................................. 4-12
Compile, Link, and Run Your Application..................................................... 4-13
Sample Programs........................................................................................................... 4-13
NI-FBUS Dialog Utility ................................................................................................ 4-14
NI-FBUS Dialog Examples........................................................................................... 4-14
Example 1. Get a Device List ......................................................................... 4-14
Example 2. Download a Schedule to an Interface .......................................... 4-15
Example 3. Read a Parameter Using TAG.PARAM Access............................ 4-16
Example 4. Wait for a Trend........................................................................... 4-16
Configuring the Link Active Schedule File................................................................... 4-17
Introduction to the Link Active Schedule File................................................ 4-17
Format of the Link Active Schedule File ......................................... 4-18

Contents
©National Instruments Corporation ix NI-FBUS Hardware and Software User Manual
Chapter 5
Developing The Application
LabVIEW.......................................................................................................................5-1
Visual C++.....................................................................................................................5-1
Visual Basic ...................................................................................................................5-2
.NET Class Libraries......................................................................................................5-2
OPC Server ....................................................................................................................5-3
OPC Data Type Mapping Rule........................................................................5-3
Chapter 6
NI-FBUS Function Reference
Administrative Functions...............................................................................................6-1
List of Administrative Functions.....................................................................6-1
Core Fieldbus Functions ................................................................................................6-26
List of Core Functions .....................................................................................6-26
Using Interface Macros..................................................................................................6-55
Alert and Trend Functions .............................................................................................6-56
Appendix A
Specifications
PCI-FBUS/2...................................................................................................................A-1
PCMCIA-FBUS.............................................................................................................A-4
USB-8486 ......................................................................................................................A-7
FBUS-HSE/H1 Linking Device.....................................................................................A-10
Appendix B
Troubleshooting and Common Questions
Interface Board—USB, PCI, and PCMCIA ..................................................................B-1
HSE Linking Device......................................................................................................B-8
NI-FBUS Software ........................................................................................................B-13
Appendix C
Technical Support and Professional Services
Glossary
Index

©National Instruments Corporation xi NI-FBUS Hardware and Software User Manual
About This Manual
This manual contains information on the installation, configuration, and
use of National Instruments Fieldbus hardware and software.
Conventions
The following conventions appear in this manual:
»The »symbol leads you through nested menu items and dialog box options
to a final action. The sequence Options»Settings»General directs you to
pull down the Options menu, select the Settings item, and select General
from the last dialog box.
This icon denotes a note, which alerts you to important information.
This icon denotes a caution, which advises you of precautions to take to
avoid injury, data loss, or a system crash.
bold Bold text denotes items that you must select or click in the software, such
as menu items and dialog box options. Bold text also denotes parameter
names.
italic Italic text denotes variables, emphasis, a cross-reference, or an introduction
to a key concept. Italic text also denotes text that is a placeholder for a word
or value that you must supply.
monospace Text in this font denotes text or characters that you should enter from the
keyboard, sections of code, programming examples, and syntax examples.
This font is also used for the proper names of disk drives, paths, directories,
programs, subprograms, subroutines, device names, functions, operations,
variables, filenames, and extensions.
monospace bold Bold text in this font denotes the messages and responses that the computer
automatically prints to the screen. This font also emphasizes lines of code
that are different from the other examples.
monospace italic
Italic text in this font denotes text that is a placeholder for a word or value
that you must supply.

About This Manual
NI-FBUS Hardware and Software User Manual xii ni.com
Related Documentation
The following documents contain information that you may find helpful as
you read this manual:
• Fieldbus Standard for Use in Industrial Control Systems, Part 2,
ISA-S50.02.1992
•Wiring and Installation 31.25 kbit/s, Voltage Mode, Wire Medium
Application Guide, Fieldbus Foundation

©National Instruments Corporation 1-1 NI-FBUS Hardware and Software User Manual
1
Introduction
This chapter provides an introduction to the FOUNDATION™Fieldbus (FF)
and the National Instruments hardware and software products for FF.
FF Overview
FOUNDATION™Fieldbus is an all-digital, two-way, multi-drop
communication system that brings the control algorithms into
instrumentation. FOUNDATION™Fieldbus is a Local Area Network (LAN)
for FOUNDATION™Fieldbus devices including process control sensors,
actuators, and control devices. FOUNDATION™Fieldbus supports digital
encoding of data and many types of messages. Unlike many traditional
system which requires a set of wires for each device, multiple FOUNDATION™
Fieldbus devices can be connected to the same set of wires.
FOUNDATION™Fieldbus has two communication protocols: H1 and HSE.
The first, H1, transmits at 31.25 Kb/s and is used to connect the field
devices. The second protocol, High Speed Ethernet (HSE), uses 10 or
100 Mbps Ethernet as the physical later and provides a high-speed
backbone for the network.
Please refer to FOUNDATIONTM Fieldbus Overview document for more
information about FOUNDATION™Fieldbus technology.
NI-FBUS Hardware Products
PCI, PCMCIA, and USB
National Instruments provides interface devices for the PCI bus
(PCI-FBUS), PCMCIA (PCMCIA-FBUS), and USB (USB-8486). Each
National Instruments device connects FOUNDATION™Fieldbus devices
to standard desktop, industrial, and notebook personal computers.
PCMCIA-FBUS is available in 1- and 2-port configurations. PCI-FBUS
is available in a 2-port configuration. USB-8486 is available in a 1-port
configuration.

Chapter 1 Introduction
NI-FBUS Hardware and Software User Manual 1-2 ni.com
The PCI-FBUS/USB-8486 uses a standard DB-9 male D-SUB connector to
attach to the Fieldbus network. The PCMCIA-FBUS connects to the
fieldbus by using a cable that provides two connectors to attach to the
fieldbus network DB-9 male D-SUB connector and Combicon-style
pluggable screw terminals.
HSE
The National Instruments FBUS-HSE/H1 is a high-speed Ethernet (HSE)
linking device that couples a 10/100 Mb/s Ethernet network to two H1
FOUNDATION™Fieldbus segments. The linking device complies with
Class 42a-2 of the HSE profile and acts as the link-active scheduler (LAS)
for the H1 segments, as well as managing all fieldbus communications. It
provides connectivity to H1 devices through HSE networks and supports
function block configurations and scheduling on H1 segments. The
FBUS-HSE/H1 linking device, serving as link masters for 31.25-kbps
H1 segments connected to the HSE network running at 10 Mbps or higher,
is a crucial component in FOUNDATION™Fieldbus technology.
The combined H1/HSE solution allows for full integration of sensor,
process/discrete control, and hybrid/batch control subsystems with higher
level, supervisory applications. The HSE linking device is the key to
integrate H1 and HSE technology.
NI-FBUS Software Products
Communications Manager
The NI-FBUS Communications Manager implements a high-level
Application Program Interface (API) that lets you communicate with the
National Instruments FOUNDATION™Fieldbus communication stack and
hardware. It provides a high-level API advanced users can use to interface
with the National Instruments FOUNDATION™Fieldbus communication stack
and hardware.
Configurator
Most NI-FBUS users use the NI-FBUS Configurator. In addition to
providing the functionality of the NI-FBUS Communications Manager in a
graphical format, it includes additional functionality to allow you to
configure a Fieldbus network. It can automatically generate the schedule
for the network and configure field devices and hosts to transmit and
receive alarms and trends.

Chapter 1 Introduction
©National Instruments Corporation 1-3 NI-FBUS Hardware and Software User Manual
Monitor
The NI-FBUS Monitor helps you monitor and debug Fieldbus data traffic.
It symbolically decodes data packets from the Fieldbus, monitors the live
list, and performs statistical analysis of packets. You can use the NI-FBUS
Monitor to diagnose the communication of H1 network or debug the
development of device.
You can use FOUNDATION™Fieldbus products with National Instruments
HMI software packages, including Lookout and LabVIEW DSC. And you
can also use third-party HMI software through NI-FBUS OPC Server.

©National Instruments Corporation 2-1 NI-FBUS Hardware and Software User Manual
2
Installation and Configuration
This chapter contains installation and configuration instructions for
PCI-FBUS, PCMCIA-FBUS, USB-8486, and the FBUS-HSE/H1 linking
device.
Note Install the NI-FBUS software before you install the hardware.
Installing the Software
Complete the following steps to install the NI-FBUS software.
Caution If you are reinstalling the NI-FBUS software over a previous version, write down
your card configuration and any port configuration parameters you changed from their
defaults. Reinstalling the software may cause you to lose any existing card and port
configuration information.
1. Log in as Administrator or as a user that has Administrator
privileges.
2. Insert the NI-FBUS Software for Windows CD into the CD-ROM
drive.
If the installer does not launch automatically, navigate to the CD using
Windows Explorer and launch the autorun.exe file from the CD.
3. The interactive setup program guides you through the necessary steps
to install the NI-FBUS software. You may go back and change values
where appropriate by clicking Back. You can exit the setup where
appropriate by clicking Cancel.
4. Power down your computer when the setup is complete.
5. Continue to the Installing the Hardware section to configure and
install your hardware.

Chapter 2 Installation and Configuration
NI-FBUS Hardware and Software User Manual 2-2 ni.com
Installing the Hardware
This section describe how to install your PCI-FBUS, PCMCIA-FBUS,
USB-8486, and FBUS-HSE/H1 linking device.
Note Here, the term PCI-FBUS represents PCI-FBUS/2, and the term PCMCIA-FBUS
represents PCMCIA-FBUS, PCMCIA-FBUS/2, PCMCIA-FBUS Series 2, and
PCMCIA-FBUS/2 Series 2.
Install Your PCI-FBUS Card
Caution Before you remove the card from the package, touch the antistatic plastic package
to a metal part of the system chassis to discharge electrostatic energy, which can damage
several components on the PCI-FBUS card.
To install the PCI-FBUS card, complete the following steps.
1. Shut down and power off the computer. Keep the computer plugged in
so that it remains grounded while you install the PCI-FBUS card.
2. Remove the top cover or access port of the I/O channel.
3. Remove the expansion slot cover on the back panel of the computer.
4. As shown in Figure 2-1, insert the PCI-FBUS card into any unused PCI
slot with the Fieldbus connector protruding from the opening on the
back panel. Make sure all pins are inserted an equal depth into the
connector. Although it might be a tight fit, do not force the card into
place.

Chapter 2 Installation and Configuration
©National Instruments Corporation 2-3 NI-FBUS Hardware and Software User Manual
Figure 2-1. Installing the PCI-FBUS Card
5. Screw the mounting bracket of the PCI-FBUS card to the back panel
rail of the computer.
6. Keep the top cover or access port off until you have verified that the
hardware resources do not conflict.
7. Power on the computer.
8. Launch the Interface Configuration Utility. Make sure that the
PCI-FBUS card is listed and enabled.
9. Close the Interface Configuration Utility and start the NI-FBUS
Communications Manager or NI-FBUS Configurator.
Install Your PCMCIA-FBUS Card
Caution Before you remove the card from the package, touch the antistatic plastic package
to a metal part of the system chassis to discharge electrostatic energy, which can damage
several components on the PCMCIA-FBUS card.
Personal
Computer
PCI/ISA Slot
PCI-FBUS

Chapter 2 Installation and Configuration
NI-FBUS Hardware and Software User Manual 2-4 ni.com
To install the PCMCIA-FBUS card, complete the following steps.
1. Power on the computer and allow the operating system to boot.
2. Insert the card into a free PCMCIA (or Cardbus) socket. The card has
no jumpers or switches to set. Figure 2-2 shows how to insert the
PCMCIA-FBUS and how to connect the PCMCIA-FBUS cable
and connector to the PCMCIA-FBUS card. However, the
PCMCIA-FBUS/2 card has two connectors. Refer to Chapter 3,
Connector and Cabling, for more information about these
two connectors.
Figure 2-2. Inserting the PCMCIA-FBUS Card
3. Connect the PCMCIA-FBUS to the Fieldbus network.
Your kit contains a PCMCIA-FBUS cable. Refer to Chapter 3,
Connector and Cabling, if you need a longer cable than the
PCMCIA-FBUS cable provided.
1Portable Computer 2 PCMCIA Socket 3 PCMCIA-FBUSCable
1
2
3
3

Chapter 2 Installation and Configuration
©National Instruments Corporation 2-5 NI-FBUS Hardware and Software User Manual
Install Your USB-8486
Caution Operate the USB-8486 only as described in the operating instructions. Do not
unplug the USB-8486 when the NI-FBUS software is running.
The USB-8486 has the following two variants:
• USB-8486 without screw retention and mounting option
• USB-8486 with screw retention and mounting option
You can connect the USB-8486 without screw retention and mounting
option to a desktop PC or a laptop PC.
Figure 2-3. Connecting the USB-8486 to a Desktop PC
1Desktop PC 2USB-8486 3 DB-9 Connector
1
3
2

Chapter 2 Installation and Configuration
NI-FBUS Hardware and Software User Manual 2-6 ni.com
Figure 2-4. Connecting the USB-8486 to a Laptop PC
To install the USB-8486, complete the following steps.
1. Power on the computer and allow the operating system to boot.
2. Insert the USB-8486 into a free USB port, as shown in Figure 2-3 and
Figure 2-4.
3. Connect the USB-8486 to the Fieldbus network. Refer to the
USB-8486 section of Chapter 3, Connector and Cabling, for more
information about the connectors.
4. Launch the Interface Configuration Utility.
5. Right-click the USB-8486 to enable if it is disabled.
6. Close the Interface Configuration Utility and start the NI-FBUS
Communications Manager or NI-FBUS Configurator.
1Portable Computer 2USB Port 3USB-8486 4 DB-9 Connector
1
2
3
4

Chapter 2 Installation and Configuration
©National Instruments Corporation 2-7 NI-FBUS Hardware and Software User Manual
Mount and Connect Your USB-8486
You can attach the USB-8486 with screw retention and mounting option to
a CompactRIO. This device provides the following mounting options:
• DIN mount using the unthreaded DIN rail mounting holes
• Panel mount using the panel mount notch and tab
DIN Rail Mounting
You can use the DIN-rail mounting kit to mount your USB-8486 to a
standard DIN rail, as shown in Figure 2-5.
Figure 2-5. Fastening a DIN Rail Clip to the USB-8486
1USB-8486 2 DIN Rail Clip 3Thread-Forming Screws
13
2

Chapter 2 Installation and Configuration
NI-FBUS Hardware and Software User Manual 2-8 ni.com
Complete the following steps to mount the device to a DIN rail vertically
by using the unthreaded mounting holes.
1. Fasten a DIN rail clip to the device using a #1 Phillips screwdriver and
four thread-forming screws included in the DIN-rail mounting kit.
Tighten the screws to a torque of 0.76 N · m (6.7 lb · in.). Figure 2-5
shows a DIN rail clip being attached to the device.
2. Clip the device onto the DIN rail as shown in Figure 2-6.
Note Using the thread-forming screws permanently affixes the DIN rail clip to the device.
Unscrewing and reinstalling the thread-forming screws produces a compromised
connection between the DIN rail and the device.
Figure 2-6. Clipping the USB-8486 to a DIN Rail
1 DIN Rail 2 DIN Rail Clip 3USB-8486
1
2
3
Table of contents
Other National Instruments Control System manuals
Popular Control System manuals by other brands
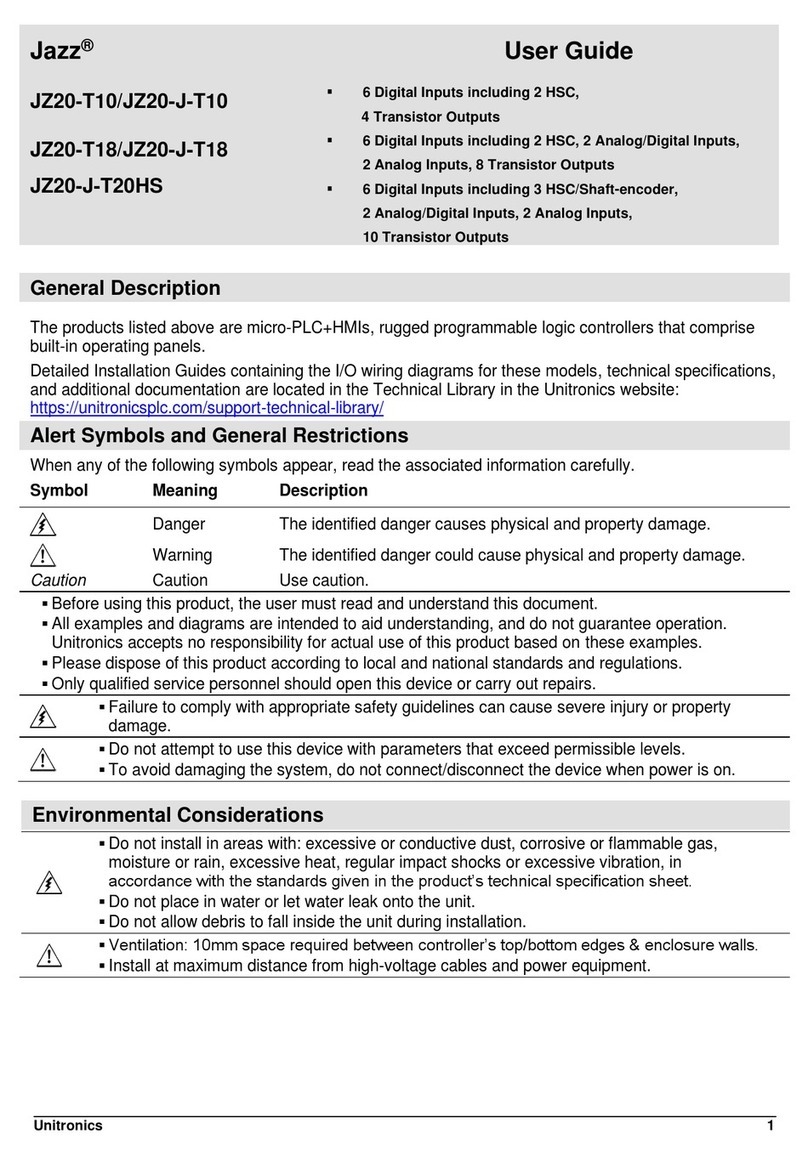
Jazz
Jazz JZ20-T10 user guide
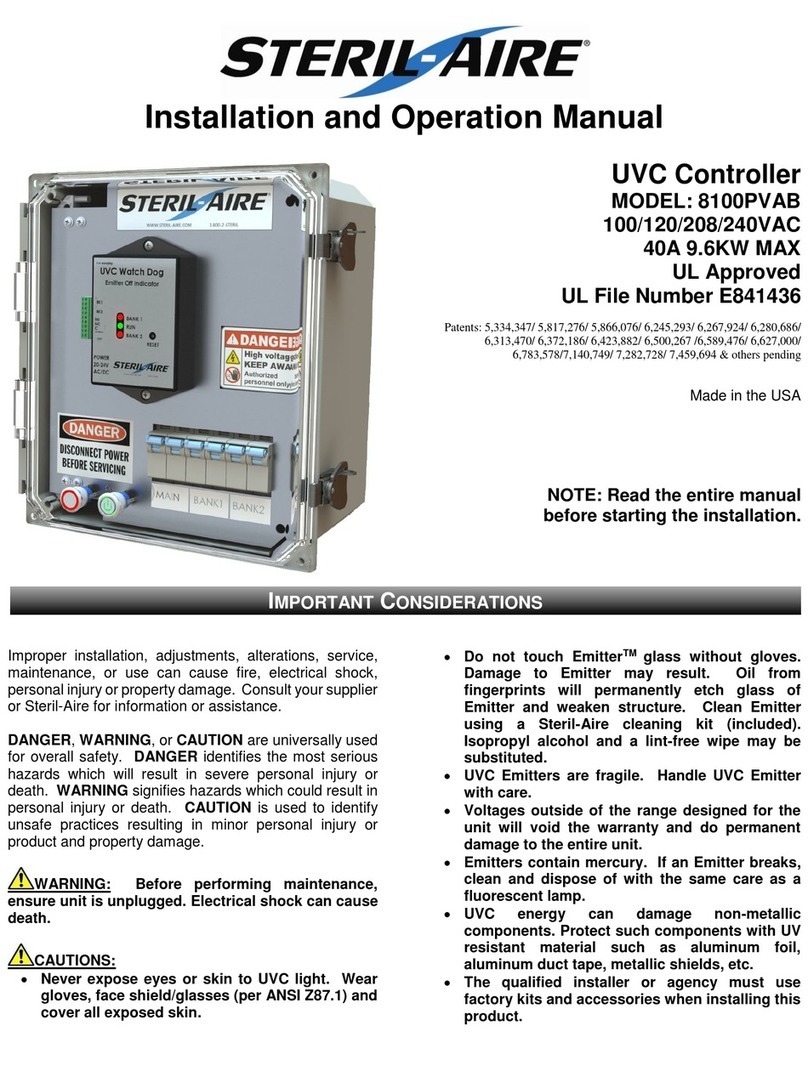
Steril-Aire
Steril-Aire 8100PVAB Installation and operation manual
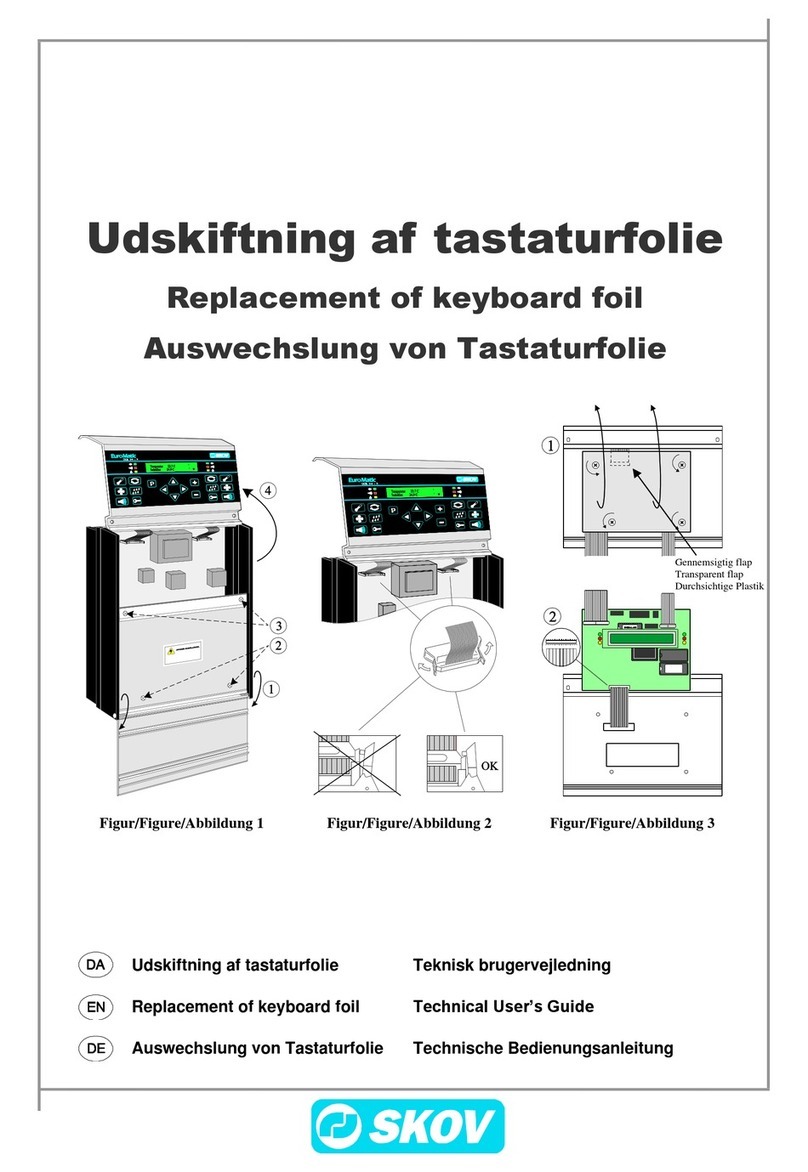
Skov
Skov DOL 34H Technical user guide
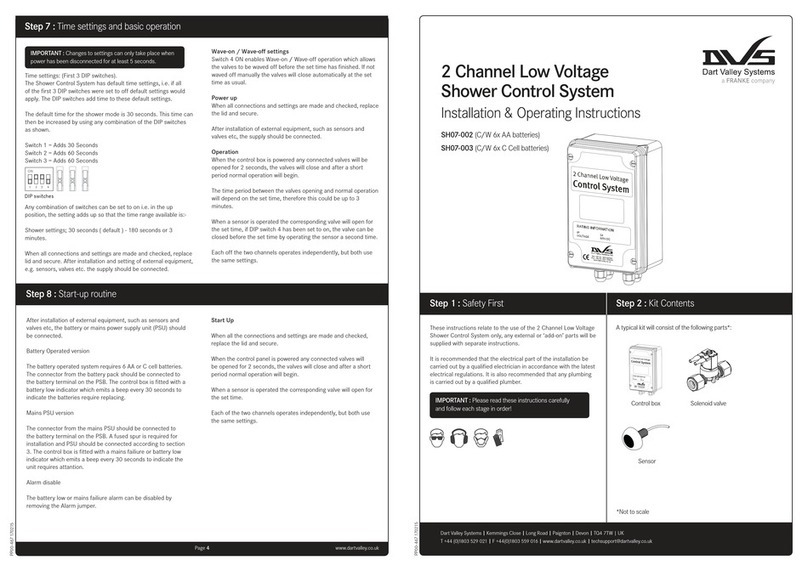
Franke
Franke DVS SH07-002 Installation & operating instructions
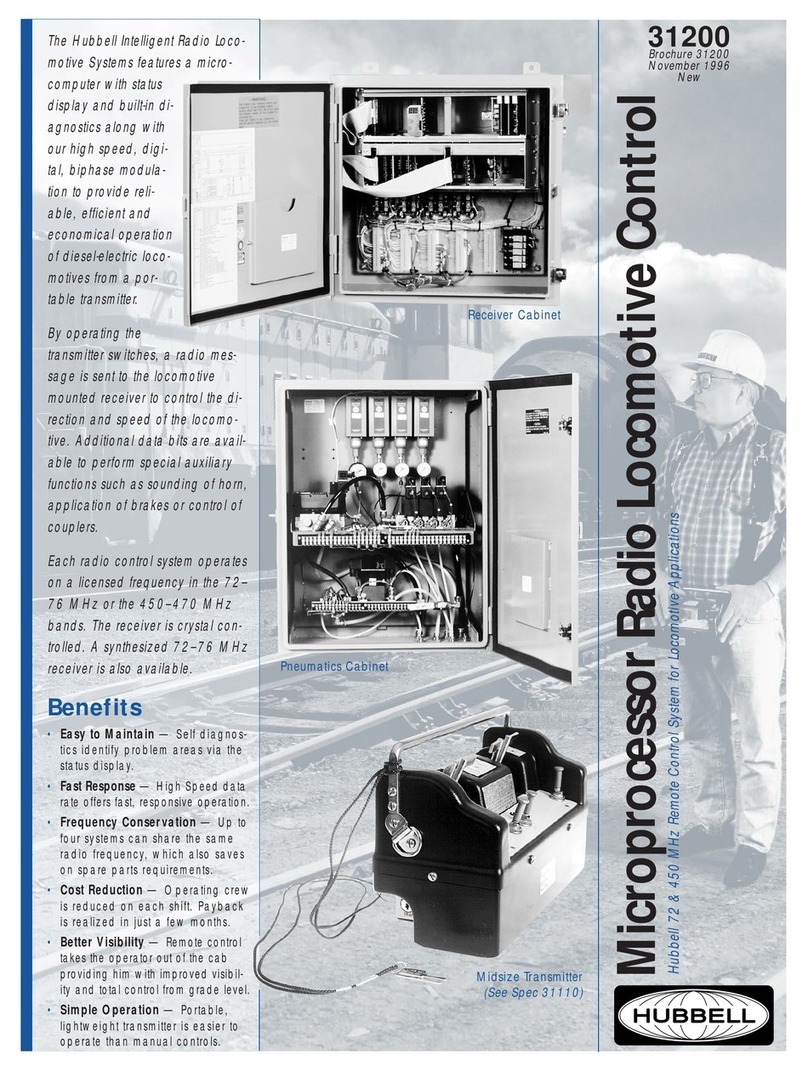
Hubbell
Hubbell Microprocessor Radio Locomotive Control... Brochure & specs
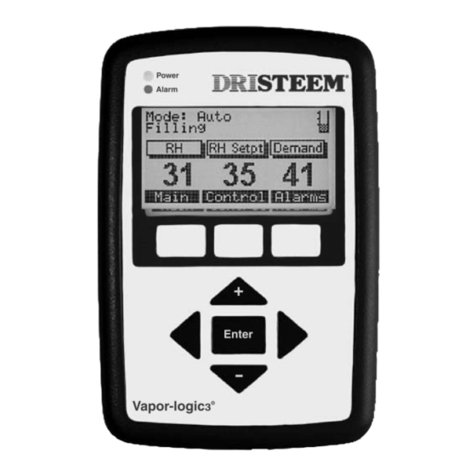
DriSteem
DriSteem Vapor-logic3 Installation and operation manual