NDT James Instruments Cementometer L User manual

1
T-C-20
Cementometer™ L
Operating Instructions
Original Instructions: Revision: May 2019

2
Table of Contents
T-C-20 General Overview .....................................................3
Fine Aggregate.............................................................5
Coarse Aggregate ........................................................7
Mixing your Sample .............................................................8
Menu Items .......................................................................11
Unit Operation.............................................................11
Type I..........................................................................11
Type III........................................................................11
Direct… ......................................................................12
User Program .............................................................12
Change User Program ................................................12
Upload Data................................................................13
Change Date...............................................................13
PC Software Functions.………………………………………..15
Least Squares Analysis...……………………………………...17
Warranty Information ..........................................................18
Repair Policy ......................................................................22

3
T-C-20 Cementometer™ L Instruction Manual
GENERAL OVERVIEW
The James®Instruments Cementometer™- L is a revolutionary
digital meter for low Water/Cement (or w/c) ration concrete. It allows
the user to measure the complex dielectric constant of the mixture of
water and material under investigation. As it has been shown in
many studies that the complex dielectric constant is directly related
to the amount of water present, the built-in microprocessor can
convert this value directly into the percentage of moisture.
The Cementometer™ L consists of a 100 MHZ probe and logging
unit that can process the data from the unit and can store it for later
retrieval.
The Cementometer™ L probe has 5 stainless steel prongs to insert
in the material to get a moisture content reading. Each prong is 3.5
inches in length with a diameter of 0.125 inches. They should be
inserted so that the entire prong is covered by the material under
investigation. The volume tested is that enclosed by the four outer
prongs of the sensor unit. The robust prongs have been designed to
be inserted into various materials. Most commonly used materials
are sand, aggregate, and gravel.
Proper cleaning and maintenance of probes is required for
accurate readings. Any contaminating material attached to the
probes can influence subsequent readings.
Stainless steel probes should be cleaned before and after testing
has been completed. The Cementometer™ L prongs cover a surface
depth of about 5 inches. Keep in mind that moisture always flows to
the bottom of these materials. The more moisture suspected in the
material, the deeper the depth you want your testing to be.
The unit comes from the factory with a variety of modes to assist
the user in determining the water/cement ratio. The unit comes
preprogrammed to analyze mixes of both Type I and Type III
cement. There is also a mode to read the output of the sensor
directly. The Cementometer™ L can also be programmed with up to
ten different user programs. These are correlation factors that
pertain to the direct material the user is dealing with and should be

4
used for the most accurate readings. There are also the capabilities
to upload the data stored in the unit to a P.C. for later analysis, as
well as a clock to help synchronize and differentiate the data.
Finally, the unit comes with our P.C. software which simplifies
uploading of data to a Windows Compatible P.C. and analyzing the
data for later programming of the unit. When required, the software
will automatically monitor the serial communication port specified by
the user. Once transmission of data from the Cementometer™ L unit
has occurred, this information will appear in the edit window in the
software. This data can then be analyzed by the built in software
of the program or with a common spread sheet. The built-in
software will take the user step by step through each record and
allow the user to enter the moisture percentage associated with each
reading. Once all the readings have an associated moisture
percentage, the data can be graphically displayed, and the optimal
correlation relationship determined. Coefficients representing this
relationship are displayed for subsequent loading into the
Cementometer™ L unit.
The Cementometer™ L is an easy and accurate way of
testing
for water / cement ratio in a controlled or uncontrolled environment.
Every effort has been made in providing a user friendly robust and
accurate system for the measurement of water / cement ratios in
fresh concrete. A robust sensor which responds to water content
has been created. This feeds into the main microprocessor unit of
the Cementometer™ L allowing the user an instantaneous direct
reading of the moisture under test.

5
Calibration Procedure
Preparation of Concrete Sample
Fine Aggregate (Sand)
We advise using ASTM C-128 & ASTM C-127 when preparing a
cement mix for calibration of a user mode for the Cementometer™
unit. A Saturated-Surface Dry (or SSD) condition is very important.
ASTM-C-128-15: Standard Test Method for Relative Density (Specific
Gravity) and Absorption of Fine Aggregate.
Step 1
Drying of the specimen is a very important step in this
procedure as values for absorption (SSD) may be higher for
aggregates not dried before soaking. This higher number could
lead to erroneous water/cement ratio reading when calibration
is in progress. Dry 1kg of fine aggregate in a suitable pan
at a temperature of 110 deg Celsius. Dry for 24 hours or until
sample stops losing water weight.
Step2
Remove sample from oven a let stand to cool to handling
temperature (approximately 50 deg C).
Step 3
Weigh and record the sample. Per ASTM C 128-15 8.1; which
states the following “…cover with water, either by immersion
or by the addition of at least 6% moisture to the fine
aggregate, and permit to stand for 24
± 4
hours…”.
Step 4
Remove excess water from sample but be careful not to
lose fine aggregate, now spread the sample on a flat non-
absorbent. Allow a warm breeze from a small table top fan
to flow through the sample. Stir the sample frequently to
allow homogeneous drying. This procedure should be done
until sample shows signs that it has reached SSD (step 6).

6
Step 5
For proper SSD determination a commercially bought cone
should be used, ASTM C 128-15, 6.4 specs the mold as
follows.
“6.4 Mold and Tamper for surface Moisture Test - The metal
mold shall be in the form of a frustum of a cone with
dimensions as follows: 40 ± 3 mm inside diameter at the top,
90 ± 3 mm inside diameter at the bottom, and 75 ± 3 mm in
height, with the metal having a minimum thickness of 0.8 mm.
The metal tamper shall have a mass of 340 ± 15 g and a flat
circular tamping face 25 ± 3 mm in diameter.”
Step 6
ASTM C-128-15, 8.3 “Test for Surface Moisture - Hold the mold
firmly on a smooth nonabsorbent surface with the large
diameter down. Place a portion of the partially dried fine
aggregate loosely in the mold by filling it to overflowing and
heaping additional material above the top of the mold by holding
it with the cupped fingers of the hand holding the mold. Lightly
tamp the fine aggregate into the mold with 25 lights drops of the
tamper. Start each drop approximately 5 mm above the top
surface of the fine aggregate. Permit the tamper to fall freely
under gravitational attraction on each drop. Adjust the starting
height to the new surface elevation after each drop and
distribute the drops over the surface. Remove loose sand from
the base and lift the mold vertically. If surface moisture is still
present, the fine aggregate will retain the molded shape. Slight
slumping or the molded fine aggregates indicates that it has
reached a surface-dry condition.”
Step 7
SSD (Saturated–Surface Dry) the fine aggregate.
Absorption, % = [(B - A) / A] x 100
A = mass of oven dry test sample in air, g.
B = mass of surface-saturated-dry test sample in air, g.
Note: Allow your coarse aggregate to SSD for 24 hours prior to
adding to your mixture. (See below for more information.)
(EQUATION SHALL BE ADDED, SO CUSTOMER CAN
DETERMINE THEIR SSD VALUE.)

7
Coarse Aggregate
The following procedure is used to determine the SSD of Coarse
Aggregate using ASTM C-127 standard. It is advised to use this
standard when preparing a cement mix for the calibration of a user
mode of the Cementometer™ L unit.
Step 1
Place the course aggregate sample in an oven safe tray
and dry the sample for 24 hr ± 4 hrs at 110 ± 5
deg
C.
Step 2
Remove the coarse aggregate from the oven and let cool
to room temperature for 1 to 3 hrs for samples of 3.7 mm.
(Note: Larger size aggregates may require a longer
cooling time.) Record the aggregate weight at this point.
Step 3
After cooling, immersion of the coarse aggregates is
necessary. A sample container is required.
See ASTM C-127-15, 6.2 to 6.3 which specifies the sample
container and water tank as follows.
“6.2 Sample Container- A wire basket of 3.35 mm (No.6) or finer
mesh, or a bucket of approximately equal breath and height,
with a capacity of 4 to 7 L for 37.5 mm (1 ½ in.) nominal
maximum size aggregate or smaller, and a larger container as
needed for testing larger maximum size aggregate. The
container shall be constructed so as to prevent trapping air
when the container is submerged.”
“6.3 Water Tank - A water tight tank into which the sample
container is placed while suspended below the balance.”
The course aggregate sample should be immersed in the water
tank for 24 hr ± 4 hrs. The purpose of the 24 hr immersion is to
allow the aggregate’s pores to essentially fill.
Step 4
Remove the coarse aggregate from the sample container and
roll in a towel to dry until all visible films of water are gone.
Record the weight of the aggregate sample at this point.

8
Having your aggregates at SSD when mixing is very important
and the following equation should be used to determine the
percentage of moisture required to SSD your aggregate.
Absorption, % = [(B - A) / A] x 100
A = mass of oven dry test sample in air, g.
B = mass of surface-saturated-dry test sample in air, g.
Allow your coarse aggregate to SSD (Saturated-Surface Dry)
for 24 hours ± 4 hours prior to adding to your mixture.
Mixing Your Sample
Proper mixing of your concrete sample is a very important
process for the calibration of a user mode in the
Cementometer™ unit. Your mixture should be that of 1 cubic
foot and it is suggested to start at the 0.20 W/C ratio.
Example mixture design
* Material needed for approx. 1 cubic foot of concrete:
2 cubic feet commercially available tilting mixer
59 lbs surface-saturated-dry fine aggregate
46 lbs surface-saturated-dry coarse aggregate
29 lbs cement paste
5.8 lbs of water
As stated in an earlier paragraph the material above equals a
1 cubic foot of 0.20 w/c concrete mix. The following order
should be followed to properly mix the concrete.
Step 1
Spray down inner dome of tilting mixer to moisten drum.
Step 2
Remove any excess water from the drum and start revolving the
mixer.
Step 3
Add 10 % of the water and coarse aggregate in to the
drum.

9
Step 4
Add 50 % of the fine aggregate and cement into the drum.
Step 5
Add 60 % of the coarse aggregate and the remaining water
until approximately 1/4 to 1/3 of the water is remaining in the
reservoir being used to contain water.
Step 6
Add the remaining fine aggregate and cement to the drum
followed by the remaining coarse aggregate and water.
Step 7
Let sample mix properly until a proper paste has been
achieved.
Again, this is a 0.20 w/c ratio mix. Remove enough the
fresh concrete from mixer and place in a nonconductive
bucket (1 gallon or more, 4 liters or more) for testing with
the Cementometer™.
Using up or down arrows, scroll through the menu selection
until Direct mode appears on the T-C-20 display. (It is
recommended to erase all prior data saved in the T-C-20).
Take 10 readings for this w/c mixture, store each reading by
pressing enter. Then the readings can be uploaded to the
PC. The readings can be recorded manually with the
corresponding w/c ratio.
Uploading can be done by connecting the instrument to the
P.C. using the supplied USB cable.
Step 8
Once the sample has been put back into the drum, start
rotating drum.

10
Step 9
For the mixture design presented in the example, add 1.45 lbs of
water to the mix, or the corresponding amount of water to increase
the w/c of your mix to 0.25 and let the drum rotate for 1 minute.
This is now 0.25 w/c ratio concrete mix, and it is ready for
testing with the Cementometer™. Repeat steps 7-9 until value
on Cementometer™ display reaches 409.5. This is the
saturation point of sensor probe.
* Materials used for research and development may vary
depending on aggregate types.
After the data has been collected, a correlation relationship
needs to be established. This is a linear relationship of the
form
w/c ratio = Gain * Direct Reading + Offset
Where:
W/C ratio – Final Value
Gain – Multiplier obtained from the Data
Direct Reading – Value obtained from the meter
Offset – additive factor from gathered data
From the data generated above a best fit line through data
can be generated. This can be accomplished either with a
spreadsheet, or with the accompanying software. When
inserting the moisture percentage with the software, the time
and date stamp field can be used to identify which tests were
associated with which moisture percentages.
The Gain and Offset parameters are the two values that need
to be programmed into the Cementometer™ to define the
User program (see Ch. User prog).
Once the analysis has been completed with the T-C-20 P.C.
Software, the Gain and Offset values will be displayed. Write
these values down for future reference; in the event they are ever
lost.
Return to the T-C-20 and enter a user program. (See T-C-20
manual “Change user program”)
Once the Gain and Offset values have been entered into the
T-C-20, the calibration has been completed.

11
Menu Items
1.
UNIT OPERATION
The Cementometer™ L was designed for simple operation. Upon
start up, the unit should show a brief (five second) display of our
company name and the software version. The unit will then
proceed directly to the menu item it was last on before it was
turned off. The menu structure is as follows:
* Type I
* Type II
* Direct
* User 1-10
* Ch. User Mat.
* Upload Data
* Change Date
You can scroll through the menu by pressing an arrow key. Either
Up or Down arrow key will allow you to scroll through the
memory. Type I, Type III, Direct, and User menu items will
each simply show the instantaneous reading of the sensor, menu
item selected, and the date/time. Pressing the “Enter” key while
in any of these modes will record the reading, the menu item
selected, and date/time that the reading was taken in the main
memory for later upload to a personal computer. The memory is
non–volatile and will not be erased by turning off the power.
2.
Type I
The Cementometer™ L has a factory calibration for Concrete
using Type I material. More accurate readings can be
obtained by pre-calibrating the unit to the specific mix being
tested.
3.
Type III
This is the general category for concrete using Type III cement. More
accurate readings can be obtained by pre-calibrating the unit to the
specific mix being tested.

12
4.
DIRECT
This mode is used when calibrating the unit directly to a user
material. This shows the raw mV reading coming to the A-D
converter of the unit from the sensor. By recording the value for a
range of moistures and correlating this value, the unit will then be
calibrated for the specific material being monitored by the
Cementometer™ L.
5.
USER PROGRAM
The Cementometer™ L can be programmed with up to ten
different user materials for subsequent testing.
These are labeled in the unit as 0 – 9 and are displayed in
sequential order. Their programming is performed in the “Ch.
User Mat.” section. The final value from the user generated
calibration function will be displayed instantaneously with
different outputs from the probe.
6.
CHANGE USER PROGRAM
To change the user program please follow these steps:
Use the plus and minus keys to select the menu item “Ch. User
Mat.?”
(Press Enter for Yes)
•
Pressing enter will bring up the following message:
User Pog.? X
(0-9)
Where: X is the user program number you wish to change to
(ranging from 0 to 9).
•
Use the plus and minus keys to change the value of X until you
have reached the user program # you are interested in.
•
Pressing Enter now brings the message: OFFSETsXX.XX
Where:
s is the sign either + or –, and X is the value
•
Pressing the plus or minus keys will increment this value.
Pressing and holding the plus or minus key will rapidly
increment this value.
•
Once the proper value has been reached, press the enter
key. The unit will display the following:
GAIN
x.xxx
Where:
x is the value to be entered.
•
Again pressing the plus or minus keys will increment this value.
Pressing and holding the plus or minus key will rapidly
increment this value.
•
Finally pressing the enter key enters these values into
memory and sets up the user program for subsequent use.

13
For further information regarding the meaning of the OFFSET
and GAIN parameters, please refer to the “General Notes on
the User Program.”
7.
UPLOAD DATA
Please follow the bottom steps in order to upload the data
stored in the unit to a P.C.
•
Connect the unit to a USB serial port on the P.C. using the
USB serial cable supplied with the unit.
•
Use the plus or minus keys until the following message is
displayed: Upload Data (Press “Enter” to begin.)
•
Pressing “Enter” will also display the following message:
Erase Data?
+ for Y (yes), – for N (no)
•
Pressing either the + or - button will commence the upload
process and will display the message: “Data Upload in
Process”
•
Once the process is complete, the following message will be
displayed for a few seconds: “
Upload Complete”!
For more information regarding uploading the data to a personal
computer please refer to the Software section or go to “Tools”.
8.
CHANGE DATE
To change date and time please follow these steps:
•
Press the + or – arrow key until you get to Change Date?
(press “Enter” for Yes)
•
Pressing “Enter” will display the date and time in the following
format:
hh:mm MM/DD/YY
Where:
hh - hour range 0 – 24
mm - minute range 1 – 60
MM - Month range 1 – 12
DD - Day range 1 – 31
YY - Year range 00 – 99
The cursor should be blinking over the two hour digits.

14
•
Pressing the plus or minus keys will increment the digits at the
cursor. Holding the plus or minus key will increment the value
rapidly.
•
Pressing the enter Key will store the value selected and move
the cursor to the next proper position.
•
Pressing the enter key at the year position will bring the
user to the “Change Date” menu screen describes above.
Power Key, Plus Key, Average Key, Minus Key & Enter Key
•
Power Key –
Momentarily push this key to turn ON the unit.
Pressing it again turns OFF the unit. The unit will power up
displaying the same menu selection as when it was
powered
down.
•
Average Key –
Depressing this key holds the current value
and an “A” appears next to this value on the dis
play. This
then displays a running average of readings entered by
pressing this key.
•
Enter Key –
This key can be used to store data points in the
units. Depressing this will display an “S” next to the value
being read for a few seconds. The reading will
then be
stored in the unit along with the type of material being used and
the date and time. This can subsequently uploaded to the P.C.
for later retrieval. It is also used in various ancillary functions
such as changing the date and the time, uploading the data to a
P.C., and programming the unit for user materials.
•
Plus Key –
This key is used to scroll through various settings.
•
Minus Key –
This key is used to scroll through various settings.
•
X – Menu item currently being used
•
n – Current moisture reading
•
A – auxiliary character used to show data being stored and
held
•
hh – Current hour
•
mm –Current time
•
MM – Current month
•
DD – Current day

15
P.C. SOFTWARE Functions
•
Open
(Ctrl + O)
Opens previously saved files containing data.
•
Close
Closes currently open files
•
Save
•
Saves As
Saves uploaded data. Files are saved as *.TXT file for later
analysis via spreadsheet, or insertion into a word processor program.
•Exit
Terminates the program and returns to your operating
system.
TOOLS
•
Upload
(Ctrl + U)
This command is used to upload data from module to
the CPU.
For the proper upload of data to a P.C. please follow the steps
below:
•
Open the Cementometer™ L software (title of screen should read
Cementometer™ L Regression Analysis) on the P.C.
•
Connect P.C. and Cementometer™ L using the USB cable and
the serial port on the Cementometer™ L. Use the + or – arrow
keys on the unit until the “Upload Data screen appears on the
display.
•
Press Enter.
•
Go to the Cementometer™ L software (needs to be installed
on P.C.) click on the upload icon or press CTRL
+ U
•
Cementometer™ L software will ask you to “Please start
upload.”
•
At this moment, press the + arrow to erase data, or the – arrow
to save data after upload (The Cementometer™ L soft
ware will
wait 10 seconds for the upload information. If no data is received
after 10 seconds, a “No data received” sub screen will appear.)
•
Data will appear on the screen after the + or – arrow key
selection was made.
•
Save data in desired folder.

16
•
Analyze
(Ctrl + A)
Allows the user to view individual records, graph data, and
determine the correct coefficients for the user program. This key
should only be used when data is uploaded from the unit that was
saved in direct mode. It is then used to analyze the data and
generate a user program. This feature is not enabled until a data file
has been brought up on the screen.
This shows the record number, date the record was taken,
time the record was taken, value of the direct readout, and a
corresponding percentage moisture (w/c ratio) that needs to be
completed by the user in order to generate a correlation
curve.
Pressing the OK button updates the data in the file and brings up
the next record in the file. Pressing the cancel button cancels the
entire operation. Once the last data point has been entered, the
Finish button can be pressed to generate a correlation curve.
This will produce a display of the correlated data and the
appropriate OFFSET and GAIN parameters to be entered in the
Cementometer™ L.
•Ports
This command allows setting the correct (USB) Com
port. It can be
Com 1 through Com 20. The default setting is Com 1. (See your PC’s
Device Manager / Ports - to confirm what Comport is used for the
Cementometer™ L unit. This Comport setting will need to be set
whenever installing the program on a new computer. Once set, it does
not change for that PC.)

17
LEAST SQUARES ANALYSIS
OF A STRAIGHT-LINE FIT
For this method, we assume that there exists a linear relationship
between the output of the probe, and the amount of moisture in the
material to be tested. This relationship takes the following form:
w/c ratio = Gain * Direct Reading + Offset
(or y = a * x + b) (aka. the slope intercept formula)
What needs to be determined are the parameters for
Gain
&
Offset
(or a and b) from a given set of points determined by testing.
We can then define: (Note: S means “sum up”, or ∑.)
Sxx = x¡2 – (x¡)2/n
Syy = y¡2 – (y¡)2/n
Sxy = x¡y¡2 – (x¡ y¡)/n
Where x¡ and y¡ are individual pairs of values for x and y; each
defining the pairs of the
points to be plotted.
The quantity n is the number of points.
The
Gain
of the line, “a” is now simply: a = Sxy/Sxx
The
Offset
, “ b” can be calculated as: b = y¡/n – ax¡/n
This is performed automatically by the accompanying software
and is also available in
most spread sheet programs.

18
Warranty Information
1. Contract
Unless otherwise stated all sales transactions are expressly subject to these
terms and conditions. Modification or additions will be recognized only if
accepted in writing by an authorized Officer of James® Instruments Inc.
(hereinafter referred to as “James®” or the “Company”), or an officially
designated representative. PROVISIONS OF BUYER'S PURCHASE ORDER
OR OTHER DOCUMENTS THAT ADD TO OR DIFFER FROM THESE TERMS
AND CONDITIONS ARE EXPRESSLY REJECTED. NO WAIVER OF THESE
TERMS AND CONDITIONS OR ACCEPTANCE OF OTHERS SHALL BE
CONSTRUED AS FAILURE OF THE COMPANY TO RAISE OBJECTIONS.
2. Warranties
The Company only warrants the equipment manufactured or supplied by the
Company as set forth herein. James® makes no other warranties, either
expressed or implied (including without limitation, warranties as to
merchantability or fitness for a particular purpose). In no event shall James® be
liable for any type of special, consequential, incidental, or penal damages,
whether such damages arise out of or are a result of breach of contract,
warranty, negligence, strict liability or otherwise. Warranty shall not apply where
the equipment manufactured or supplied has been subject to accident,
alteration, misuse, abuse, improper storage, packing, force majeure, improper
operation, installation, or servicing. In addition, the following shall constitute the
sole and exclusive remedies of Buyer for any breach by James® of its warranty
hereunder.
a. New Products
James® warrants the equipment manufactured or supplied by
James® as set forth herein. This limited warranty can only be
exercised by the original purchaser of the equipment from James® or
authorized James® Agent and is not transferable to any subsequent
owner or party. This limited warranty gives you specific legal rights,
and you may also have other rights which vary from case to case.
i. For James® Equipment
James® warrants that James®'s equipment will be free from
defects in materials and workmanship for a period of twenty-
four (24) months on the electronic portion and six (6) months
on the mechanical portion from the date of shipment of
equipment from James® to Buyer. Should any defects be
found and reported by the Buyer during the applicable
limited warranty period, the defect will be corrected upon
return of the item to James®. James® will, during the
applicable new equipment warranty period, provide the
necessary replacement parts and labor to correct the defect.
Excluded from the new equipment warranty are all
consumable and wear and tear items such as impact bodies,
penetrators, connection cables, etc. These items are subject

19
to usual wear and tear during usage. Refer to the
Consumable, Wear and Tear Items section of this warranty
document.
Option for Extended Limited Warranty Coverage
The original purchaser of any new equipment of James®
which have been identified or labeled by James® from time
to time in James®'s sole discretion as being eligible for
extended warranty coverage shall have the option to
purchase certain extensions of the applicable limited
warranty provided hereunder to the electronic portion of any
such items for either a twelve (12), twenty-four (24) or thirty-
six (36) month period (up to a possible maximum limited
warranty coverage period for the electronic portions of such
new James® equipment of sixty (60) months) by purchasing
any such twelve (12), twenty-four (24) or thirty-six (36)
month limited warranty extension period either all the time of
the purchase of any such item(s) or within ninety (90) days
from the date of delivery of the subject item(s) of the original
purchaser of such item(s). The price for each such extended
limited warranty coverage period shall be as determined by
the Company from time to time and all such purchases of
any extended warranty coverage periods shall only be
effective upon a completed purchase order and payment
directly between James® and the original purchaser of any
such item(s). The extended warranty coverage periods are
only valid with respect to the original purchaser of such
item(s) from the Company and such extended warranty
coverage is not transferable to subsequent owners of the
subject item(s) or any other parties. Upon the purchase of
any extended limited warranty coverage period, the
Company will issue a certificate to Buyer evidencing the
details of the applicable extended warranty coverage period
purchased by the Buyer.
ii. For Other Manufacturer's Products Supplied by
James®
Products of other manufacturers supplied as such by
James® are warranted by James® only to the extent of any
warranty provided by the original manufacturer, if any.
iii. For Parts and Sub-Assemblies
Parts or sub-assemblies purchased by the Buyer to perform
its own repair work etc. are warranted as provided
hereunder by James® for six (6) months from date of
shipment of material from James® to Buyer.
iv. For Consumables, Wear and Tear Items

20
James® supplies consumable items and items subject to
wear and tear during normal usage of James® supplied
products. These items are not covered under warranty.
Buyer is to check for proper fit, form and function of such
items upon receipt of such items. In case of a defect
condition, Buyer can return the item to James® for
evaluation within thirty (30) days of the date of shipment to
the Buyer. James® reserves the exclusive right to issue full,
partial, or no credit to the Buyer based on the condition of
the returned item and circumstances related to the return.
Examples of items in this category: connection cables, test
blocks, impact bodies, penetrators, probes, extraction
liquids, calibration liquids, pins, recording paper, test plugs,
etc.
b. Calibration and Repair
i. For Calibration Services
James® does not warrant the calibration of any equipment.
James® does however warrant the equipment manufactured
by it, in proper working condition, to be capable of being
adjusted to meet James® printed specifications, if any, for
accuracy and performance as to the particular model type
during the period of warranty applicable as stated above.
ii. For Repair Services
James® warrants repair work performed under the direct
control and supervision of James® personnel for a period of
three (3) months from the date repairs are completed either
at James® or at the customer site. Should the defect for
which the repair work was performed reoccur within this
period, James® will supply the necessary parts and labor
(repair at James® facility) or parts (repair at Buyer facility)
required to repair the original equipment defect for which the
repair parts and labor were required. Additional repair
charges that may be incurred in conjunction with any repair
service warranty event will be invoiced at the James®
customer service rates and policies in effect at the time of
the event.
Excluded are all consumable and wear and tear items such
as impact bodies, probes, connection cables, etc. These
items are subject to usual wear and tear during usage. Refer
to the Consumable Wear and Tear Item section of this
warranty document.
This manual suits for next models
1
Table of contents
Other NDT James Instruments Measuring Instrument manuals
Popular Measuring Instrument manuals by other brands
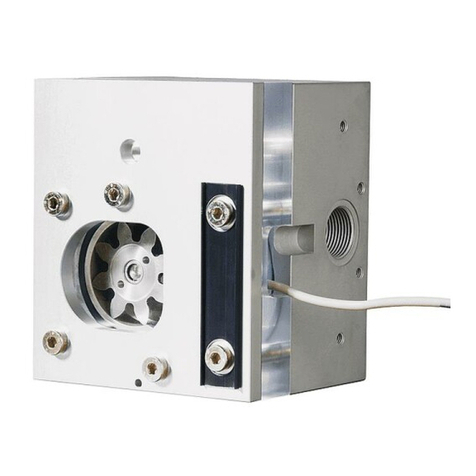
SKF
SKF SMD 1B Component Lifecycle Manual
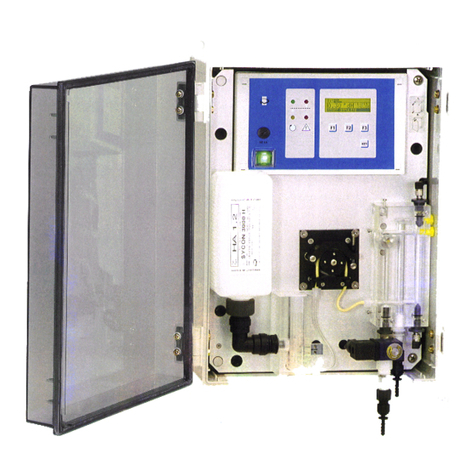
RLS Wacon
RLS Wacon SYCON 3000 C operating manual
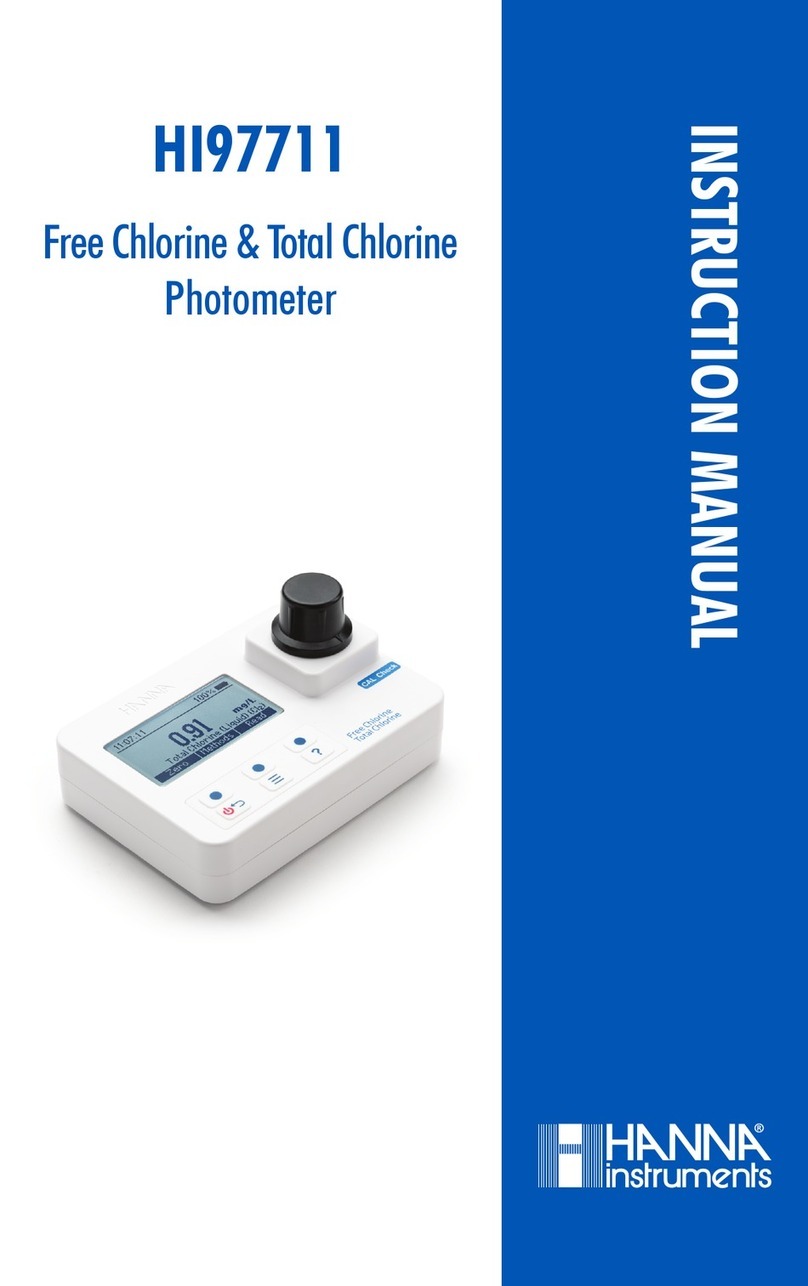
Hanna Instruments
Hanna Instruments HI97711 instruction manual

WAGNER
WAGNER RS 500 Translation of the original operating manual
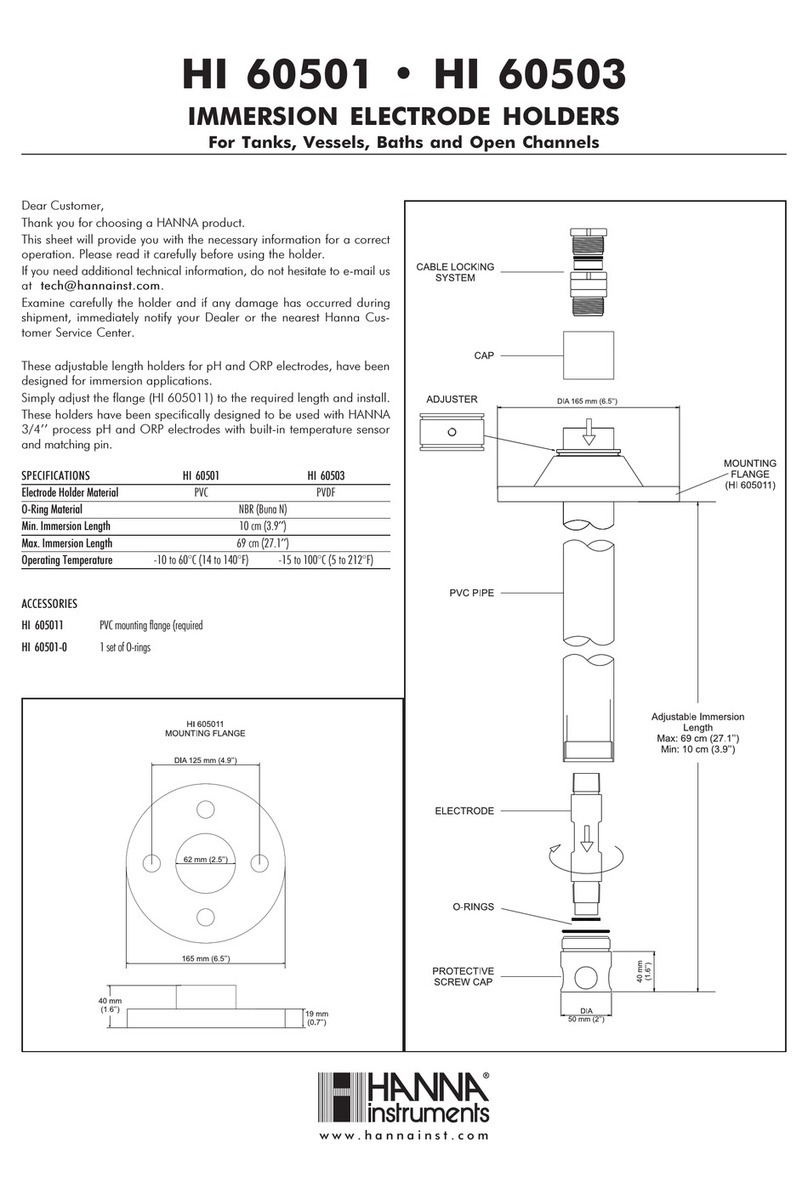
Hanna Instruments
Hanna Instruments HI 60503 instruction manual

Tru-Test
Tru-Test EC-20 user guide