Nicotra AT Manual

Nicotra S.p.A.- Via C.Cantù,1 – 20121 Milano – Italy
Factory.: Via Modena, 18 – Ciserano Loc. Zingonia (BG)– Italy
Factory.: Strada di Ronchis, 5 – Remanzacco (UD) - Italy
Cod. 985719 – 00 / Jan 2004
INSTALLATION AND MAINTENANCE
MANUAL
CENTRIFUGAL FANS
AT-AS-ASH-RSH-ADH-RDH
In accordance with ATEX directive
In issuing this guide-book maximum attention has been paid to ensure correct information. Nicotra S.p.A. does not accept any
responsibility for eventual errors or omissions.

Cod. 985719 – 00 / July 2004 2
SUMMARY
1. GENERAL INFORMATION.................................................................................. 4
1.1. ATEX VERSIONS..................................................................................................................... 4
2. RECEIVING AND INSPECTING THE PRODUCT................................................ 4
2.1. DATA ON THE RATING PLATE.............................................................................................. 5
2.2. WEIGHTS OF THE PRODUCTS.............................................................................................. 6
2.3. HANDLING AND LIFTING THE FAN ...................................................................................... 7
2.4. STORAGE ................................................................................................................................ 8
3. FUNCTION AND DESIGN OF THE FAN ............................................................ 8
3.1. OPERATING CONDITIONS..................................................................................................... 8
3.2. OPERATING LIMITS................................................................................................................ 8
3.2.1. Max installed power 8
3.2.2. Maximum speed 8
3.2.3. Operating temperature 9
3.3. BALANCING ............................................................................................................................ 9
3.4. BEARINGS ............................................................................................................................... 9
3.4.1. Bearing life 9
3.5. SHAFTS.................................................................................................................................... 9
4. INSTALLATION ................................................................................................... 9
4.1. FIXING THE FAN ..................................................................................................................... 9
4.2. INSTALLING THE DRIVE SYSTEM ...................................................................................... 11
4.2.1. Problems due to a too low belt tension 11
4.2.2. Problems due to a too high belt tension 11
4.2.3. Belt tension 12
4.3. SAFETY ACCESSORIES....................................................................................................... 13
4.3.1. Protection of moving components 13
4.3.2. Electrical insulation 13
4.4. INSPECTION AFTER INSTALLATION ................................................................................. 13
4.5. STARTING THE FAN ............................................................................................................. 13
5. MAINTENANCE ................................................................................................. 14

Cod. 985719 – 00 / July 2004 3
5.1. ORDINARY MAINTENANCE ................................................................................................. 14
5.1.1. ATEX version 15
5.1.2. Drive 15
5.1.3. Bearings 15
5.1.4. Bearings lubrication 15
5.2. REPLACING INSTRUCTIONSFOR BEARINGS .................................................................. 17
5.2.1. Dismantling the bearing with eccentric locking collar 17
5.2.2. Mounting the bearing with eccentric locking collar 17
5.2.3. Dismantling the plummer block with ball bearing and eccentric locking collar 18
5.2.4. Mounting the plummer block with ball bearing and eccentric locking collar 18
5.2.5. Dismantling the plummer block with ball bearing and adapter sleeve 18
5.2.6. Mounting the plummer block with ball bearing and adapter sleeve 18
5.2.7. Dismantling the SNL plummer block with self-aligning ball bearing and adapter sleeve 19
5.2.8. Mounting the SNL plummer block with self-aligning ball bearing and adapter sleeve 19
5.2.9. Dismantling ConCentra roller bearing 22
5.2.10. Mounting ConCentra roller bearing 23
6. ATEX – DECLARATION OF CONFORMITY ..................................................... 26
ADH ATEX - OPERATING LIMITS…………………………………………………..27
RDH ATEX - OPERATING LIMITS ..………………………………………………..28
AT ATEX - OPERATING LIMITS …..……………………………………………….29
ASH ATEX - OPERATING LIMITS ..………………………………………………..30
RSH ATEX - OPERATING LIMITS …..……………………………………………..31

Cod. 985719 – 00 / July 2004 4
1. GENERAL INFORMATION
The scope of this manual is to provide information about the correct installation, use and maintenance of the fans listed in
the title.
The safety recommendations contained herein are of general level and can be applied to several models of Nicotra
range.
To know the specific characteristics of each model, please refer to the relevant catalogues.
It is customer’s responsibility to verify that all the operations on the ventilation equipment are carried out by professional
staff, who must apply all the safety recommendations required by the laws, rules and standards of the country where the
fans are installed.
The information contained in this manual must be read in conjunction with the contents of the catalogues of each model
and the selection program “Ventil”.
These recommendations cannot represent totally the methods or procedures required for safe operation. Care should
always be taken when working in close proximity to equipment or moving parts. Total safety depends on acquired skill,
experience and reasonable care in all operations.
1.1. ATEX VERSIONS
In this manual are listed specific information for fans intended for use in potentially explosive atmospheres for ATEX
“Group II”, “Categories 2G-2D-3G-3D” according to the directive 94/9/CE.
Design of fans is in accordance with the following standards: EN 1127-1, EN 13463-1, prEN 13463-5.
The information contained in this manual for ATEX fans, must be integrated with the contents of the catalogues of each
model and the selection program “Ventil”.
2. RECEIVING AND INSPECTING THE PRODUCT
All Nicotra products are carefully checked before delivery to assure the best standard quality.
It is customer responsibility to control that the received units are in accordance with the order and have not been
damaged during the transport.
If you discover any damage, please contact immediately the Forwarder Agent and start the damage notification
procedure.
After having accepted the goods, Nicotra will guarantee only what stated in the commercial agreement.

Cod. 985719 – 00 / July 2004 5
In particular we suggest to check the following points:
•The goods quantity, type and design must fit what was stated in the order and listed in the transport bill
•Make sure that there are not damaged or missing parts
•Verify if the housing or the flange have dents
•Check if some parts are not correctly fixed
•The wheel must rotate easily, without touching other parts; make sure that the wheel is still balanced and fixed
correctly on the shaft
•Verify the correct tightening of the screws
•Make sure that the inner ring of the bearings is locked on the shaft
•Check if shafts and frames have been bent during transport
•Couplings between the shafts must be aligned
•Atex fans must be accompanied by the following documents: “ Maintenance and Installation Manual”, “Atex
Certificate” and rating plate fixed on the housing
Note: for any other information, please refer always to the relevant drawing, catalogue or contact our Technical
Department.
2.1. DATA ON THE RATING PLATE
MOD: product description
COD: Nicotra code
SERIAL: serial number
COD. CLI: customer code (optional)
WATT MAX: max admissible power
RPM MAX: max admissible speed
MAX BEARING LOAD: max admissible radial load on bearing
Prod. Date: production date
Instr. Code: “Maintenance and Installation Manual” code
II 2 G: Atex Group II, Cat.1, Gas (only Atex version)
ctype of protection against ignition risk (only Atex version)
T5: max surface temperature class (only Atex version)

Cod. 985719 – 00 / July 2004 6
2.2. WEIGHTS OF THE PRODUCTS
Approximate weights (±10%) of the standard fans, excluding the packaging, are listed in the table below. The exact
weight of the fans is specified in the relevant drawing.
AT 7/7 9/7 9/9 10/8 10/10 12/9 12/12 15/11 15/15 18/13 18/18
Skg 5,0 6,5 8,0 8,5 9,5 13 15 18 21 27 33
SC kg 6,0 8,5 9,5 10 11 16 18 21 25 33 38
AR kg -13,5 15 15,5 17 28 30 35 39 48 55
G2L kg 11,7 14,9 18 19 21 28 34 40 45 58 71
SC2 kg 13,7 18 22 22 24 35 40 46 53 70 82
G2C kg -24 27 27 31 46 51 57 68 91 106
G3C kg -----70 81 90 108 118 137
AT 20/15 20/20 22/15 22/22 25/20 25/25 28/20 28/28 30/20 30/28
TIC kg 71 78 73 82,5 93 120 127 131 138
G2C kg 137 150 141 165 195 202 210 235 245 302
G2C-C2 kg 144 158 148 173 202 210 218 244 253 310
G3C kg 315 355 340 425 432 480 474 539 505 577
G3C-C2 kg 319 359 347 438 436 484 478 543 509 581
RDH 180 200 225 250 280 315 355 400 450 500 560 630 710 800 900 1000
Lkg 5,2 6,5 7,7 13,3 17,8 21,2 29 36 50 62 79 104,1 148,7 - - -
Rkg 7,1 8,5 9,9 15,7 21,3 25 34 42 57 70 92 119,1 165,4 - - -
Kkg - 11,8 13,6 20,6 28 32 46 57 73 90 141,1 173,5 220 270,1 342,5 414,7
K1 kg - - - - - 34 47 58 75 92 148 180,4 240 296,8 355,4 -
K2 kg - - - - - - - - - 110 152,6 185,1 249,7 305,3 374,8 450,3
G2L kg 11,3 14 17 27 36 43 59 77 102 131 - - - - - -
G2R kg 15,5 19 22 33 44 53 74 91 121 152 203 - - - - -
G2K kg - - - 44,5 59,3 68,5 103,1 125,3 159,9 197 301 370 436 565 685 953
G2K2 kg - - - 42 56 66 93 114 144 183 289 359 443 572 692 960
ADH 160 180 200 225 250 280 315 355 400 450 500 560 630 710 800 900 1000
Lkg 5 6 7,1 8,5 10,5 14,2 17,8 23 31 42 57 72 91 118 - - -
Rkg 6,67,89,110,71318222938506586106135- - -
Kkg - - 12,6 14,5 18 24 29 41 52 66 85 134 170 201 249 306 333
K1 kg ------3042536786142175208261316-
K2 kg ----------105150180225278320360
G2L kg 10,512,61518223038496690120------
G2R kg 14,51720242939486382107140185230----
G2K kg ----38506084108135176268342532665801894
G2K2 kg ----44597398133159221319393537670806899

Cod. 985719 – 00 / July 2004 7
2.3. HANDLING AND LIFTING THE FAN
The fans must be handled by experienced and fully trained staff. A wrong handling or lifting could damage the fans. The
most frequent are the following:
•shifting of the wheel on the shaft due to loosening of the hub set screws
•bending or misalignment of the shaft
•bending of the frames
•dents on the housing
•damage of the bearings; in particular a wrong tightening of the locking system
The fans are supplied in a carton box, pallets or cages.
The lifting equipments must be chosen according to weight and type of the goods.
The fan fitted with side frames should be lifted by its lifting lugs (holes or slots) in four points.
The fans without frames may be lifted with a rope secured to the shaft ends.
Do not bend or misalign frames and shaft when lifting the twin and triple fans. We suggest to fix them on a pallet larger
than the dimension of the fan base.
The fans supplied in a carton box, must be handled with equipment which avoids damaging the packaging.
The units on pallet must be lifted by a forklift truck.

Cod. 985719 – 00 / July 2004 8
Do not hook the units in the following points:
•inlet cone
•wheel cone
•blade
•single shaft end
•motor (for complete units)
•bearing or bearing support bar/bracket
•cut-off
2.4. STORAGE
All Nicotra fans are designed to be stored for a maximum period of six months under the following conditions:
•storage temperature range: -25°C ÷+65°C
•relative humidity: < 60%
•protect the fans against direct rain or snow
•store the fans in premises, which are adequately ventilated and heated so that no condensation will occur on the
units
•rotate the wheel at least once a week, to permit the redistribution of the grease inside the bearing and prevent
corrosion
•protect the units from external loads or vibrations
•avoid the exposure to direct sunshine and UV rays
•protect the fans from corrosive agents
3. FUNCTION AND DESIGN OF THE FAN
3.1. OPERATING CONDITIONS
The operating data for fans in standard version are listed in the specific catalogues.
In general fans are designed for use with “clean air”.
For particular operating conditions such as temperature different from the standard range, airflow with corrosive agents,
high humidity, special applications or use outside the standard limits, please contact our Technical Department.
The fans in ATEX version are designed to work under the specific conditions of the “group”, “category” and “temperature
class” stated in the rating plate.
The standard limits for ATEX fans are listed in the tables enclosed in this manual. The specific limits of a special fan
could be different from those of the standard version and are listed in its rating plate.
3.2. OPERATING LIMITS
3.2.1. Max installed power
In the tables enclosed in each catalogue are listed the power limits and the minimum diameter of the smallest
transmission pulley according to the applied power.
The belt tension must never exceed the values calculated in the selection program “Ventil”. The values for the first
tensioning are indicated in the chapter “Belt tension”.
3.2.2. Maximum speed
Maximum permissible speed is listed in the tables enclosed in the catalogues.

Cod. 985719 – 00 / July 2004 9
3.2.3. Operating temperature
The standard operating temperature is indicated in the catalogues. For short periods it is possible to use the fan at a
temperature lower than –20°C, but it is dangerous to start a fan which was standing at a temperature lower than –20°C.
For special application please contact our “Technical Department”.
For use at temperatures higher than those indicated in the catalogue, the limit is controlled by the bearing grease; in this
case please refer to the paragraph “Maintenance”.
The operating temperature (airflow, ambient temperature) and the temperature class for the fans in ATEX version are
indicated in the rating plate.
3.3. BALANCING
The fan impellers are statically and dynamically balanced with grade G4 according to ISO 1940.
3.4. BEARINGS
In the “Maintenance” chapter are listed the bearings used on each fan.
3.4.1. Bearing life
The Nicotra bearings have been selected to achieve a bearing life L10h of 40.000 hrs according to ISO 281. This value is
calculated with common pulley sizes (see also the chapter “Pulley selection”) and at maximum load. In more common
load conditions, the bearing life can easily exceed this value.
If the bearing life depends on the applied loads, these are due to many factors; the most important is the belt tension
which is function of the installed power, pulleys diameter and number of grooves.
In the catalogue tables are listed the minimum diameter of the pulleys and the maximum number of grooves suggested in
order to respect the maximum permissible loads.
The belt tension must never be higher than the values calculated in the selection program “Ventil”.
3.5. SHAFTS
Shafts diameters are selected to have a critical speed higher than the maximum permissible speed with a safety factor
≥1.2.
4. INSTALLATION
Correct installation of the fan will ensure correct operation and avoid problems in the future.
Atex fans, must never be installed in presence of an explosive atmosphere. If they are connected to other components or
machines, such as motors, drive elements (pulleys, belts, couplings…) etc, these must also be Atex compliant and not
change the mechanical characteristics of the fan in such a way that the fan can not remain Atex compliant according to
the standard described in the paragraph 1.1.
The fan must always be connected to an earth cable. Category 2 fans have an earth screw, while for category 3 fans it is
necessary to connect an earth cable to the housing.
The painted frames can not guarantee a superficial resistivity lower than 1 Giga-Ohm, so are not suitable as earth
connection elements.
4.1. FIXING THE FAN
Pay attention to the following points:
•the fan must be fixed to a base or to a rigid frame designed to avoid vibrations and resonance
•use all the fixing points and verify that the frame or the feet will rest on the whole surface

Cod. 985719 – 00 / July 2004 10
•when tightening the screws, do not bend frames, fixing feet and sideplates. Avoid overloads that can compromise
the correct functioning of the fan
•Fix the fan on a plane base. The shaft must always be in horizontal position to avoid axial loads on bearings and
anomalous vibrations. Do not use the fan with the shaft in vertical position
•We suggest the use of antivibration mountings to isolate the system motor-fan from the machine structure. Motor
and fan must be fixed on a common base to avoid relative displacement which can create misalignment between
the pulleys
•If the fan is to be connected to a duct, we suggest the use of a flexible connection flange to compensate
misalignment between the outlet and the duct and avoid vibrations
•Make sure that the duct is as closely aligned as possible with the fan outlet
•Use gaskets to avoid losses

Cod. 985719 – 00 / July 2004 11
4.2. INSTALLING THE DRIVE SYSTEM
We suggest to use the selection program “Ventil” to dimension correctly type and diameter of the pulleys, belt tension etc.
Pulleys should be statically and dynamically balanced with grade G4 according to ISO 1940. This is compulsory for ATEX
fans.
•Install the drive system with the following recommendations:
•mount the pulleys on the motor-fan shaft
•verify the alignment of pulleys and motor-fan shafts: a straight bar can be used to put on pulleys side plane
•grooves must be clean
•apply the belts, loosening the tensioning system to avoid a excessive extension of the belts and eventual damage
•tension the belts gradually
Belt tension depends on many factors: installed power, speed, type and dimension of pulleys etc.
It is very important to apply the correct tension which is one of the most important factors for a correct working of the fan.
Please refer to the data listed in the selection program “Ventil”.
4.2.1. Problems due to a too low belt tension
•Belts turn over in pulley grooves with excessive wear
•Excessive running noise
•Severe belt vibration
•Anomalous loads
4.2.2. Problems due to a too high belt tension
•Excessive loads on bearings, shaft and motor with a consequent decrease of their life
•Rise in loads on all the other components
•Increase in vibration and noise

Cod. 985719 – 00 / July 2004 12
4.2.3. Belt tension
If you do not have a specific instrument, such as a tension gauge, to measure the belt tension, you can apply the
following approximate method:
Proceed with the tensioning of the belts by gradual tensioning of the motor base. Correct running of the fan is
determined by the correct tensioning. To ensure correct tensioning it is necessary to measure the tensioning force of
each belt by means of a dynamometer. Measure in the middle of the free length 'T' a perpendicular force able to deflect
the belt of an arrow "f" of 1.5mm for each 100mm of "T". Then compare the result with the dynamometer values F' and F"
in the following table.
Belt section External diam.
Minor pulley (mm)
RPM minor
pulley Min. F’ Newton Max F’’ Newton
SPZ
50÷90
100÷150
155÷180
1200÷5000
900÷1800
600÷1200
10
20
25
15
30
35
SPA
90÷145
150195
200÷250
900÷1800
600÷1200
400÷900
25
30
35
35
45
50
SPB
170÷235
250÷320
330÷400
900÷1800
600÷1500
400÷900
35
40
45
45
60
65
SPC
250÷320
330÷400
440÷520
900÷1800
600÷1200
400÷900
70
80
90
100
115
130

Cod. 985719 – 00 / July 2004 13
Remarks:
1. If F< F', a higher belt tension is required. If F>F", the belts are too tight
2. During the running-in period of the fan belts an early decrease in tension takes place. It is therefore necessary at the
initial assembly to tension the belts 1,3 times higher than the "f" arrow shown in the tables. Belt tensions should be
checked regularly and always after the first eight working hours.
4.3. SAFETY ACCESSORIES
Some safety devices are already included in the equipment as standard components while some are offered as optional
items. It is customer’s care to control that the machine where the fan is installed is in accordance with the local safety
norms.
4.3.1. Protection of moving components
All fans have moving parts, and require protection against contact.
Centrifugal fans are usually connected to ductwork affording protection against contact with moving parts. In the case of
free inlet or discharge, protection must be provided by means of proper guards or grilles.
In addition to inlet and outlet protection, it is necessary to provide protection from the fan shaft, belts and pulleys and all
other external moving parts by means of suitable protection guards (REF. UNI 9219).
4.3.2. Electrical insulation
Each fan must be protected with a local isolator.
Many fans are automatically controlled or controlled by remote systems, and therefore to ensure complete safety it is
necessary to provide a power interlock close to the fan, in order to enable maintenance staff to isolate the fan
independently from the main control system.
4.4. INSPECTION AFTER INSTALLATION
Make sure that inside the housing or wheel there are no foreign objects which can be ejected during start up (for example
screws fallen during mounting etc).
•Check if the shaft is bent or misaligned (for fans with couplings)
•Rotate the shaft and verify that the impeller can move freely and that it does not come in contact with the inlet cone
•The screws must be tightened
•The bearings must be locked correctly
•The impeller must not move on the shaft. The set screw of the hub must be tightened
4.5. STARTING THE FAN
•Switch on the power
•verify that the impeller rotates in the direction of the arrow moulded on
the housing or indicated in the label
•check if vibration and noise are normal
•tension and absorbed power values must be in accordance with the
data of the fan/motor rating plate

Cod. 985719 – 00 / July 2004 14
5. MAINTENANCE
Maintenance of the fan equipment should only be carried out by skilled and adequately trained staff.
To ensure complete safety do not start any maintenance procedure or inspection without disconnecting the unit from the
power supply and before the fan and motor have completely stopped rotating.
Close any inlet or outlet damper to avoid a rotation of the impeller due to induced airflow.
For Atex fans, do not begin any maintenance operation in an explosive atmosphere.
During the first two working hours:
After the initial installation the fan should be observed during the following two hours to ensure no excessive vibrations,
abnormal noises, excessive absorbed power. If necessary, adjust belt tensioning to compensate the initial tension
decrease.
After the first 24 working hours:
Run the following operations:
•check and, if necessary, re-align the pulleys and re-tension the belts
•check the correct tightening of the screws (see the table below)
•check the locking of the bearings on the shaft
•check that the impeller can move freely and that it does not come in contact with the inlet cone, or that it doesn't
move along the shaft
In the first working hours, it is normal that a certain amount of grease could come out of the bearings.
Max tightening torque for screws (Nm)
Type
Size 8,8 10,9 12,9
M4 3,2 4,5 5,2
M5 68,511
M6 11 14,5 17,5
M8 25 36 43
M10 49 70 85
5.1. ORDINARY MAINTENANCE
To guarantee smooth operation, the fan must be serviced regularly.
As a general rule, complying with the operation limits and the standard working conditions, the most important
maintenance measures, to be made at least twice a year, are:
•checking vibration and sound level; anomalous values indicate a problem on the unit
•checking the presence of corrosion on the fan, especially on the rotating parts, to prevent breakings
•cleaning of the fan, in particular of the impeller, to avoid dust deposits which can create unbalance of the impeller
and reduction in bearing life, vibrations and noise
Some components or versions can require most frequent maintenance. In the following paragraphs are listed the
maintenance operations for these critical parts.

Cod. 985719 – 00 / July 2004 15
5.1.1. ATEX version
Carry out, every month, the following operations:
•for category 2D and 3D fans, remove dust on all the components if the film is thicker than 2mm
•protect the bearings so that dust cannot contaminate the grease
•make sure that bearings temperature is not higher than the maximum surface temperature of the class listed in the
rating plate
5.1.2. Drive
We recommend to check the drive system at least every three months.
In particular:
•check belt tension and their integrity; in case of damage, replace the belts
•make sure that pulley grooves are clean
•check pulleys alignment
5.1.3. Bearings
Every maintenance operation must be carried out with suitable tools.
A first check of the bearing can be done simply by listening to it. A normal bearing generates a smooth and uniform
sound; while a damaged bearing generates a loud and irregular sound.
A low metallic noise, due to standard gap between the components, is normal, especially at low speed.
Excessive vibrations or temperature are often a sign of possible damages.
Check periodically seals integrity and the bearing locking system.
Make sure that there is not excessive leak of grease from the bearing. A leak of a little quantity of grease is normal,
expecially in the first working hours.
The bearings mounted on Nicotra fans are estimated to have a mechanical life (L10h) of 40,000 working hours when
selected within the operating limits and standard conditions mentioned in the catalogue or with an appropriately sized
drive.
The actual life of the grease contained inside the bearings may be shorter than the mechanical life of the bearing itself.
Bearings mounted with rubber shock absorbers or inside plummer blocks without grease nipples, are lubricated for life.
Bearings with re-lubricatable plummer blocks should be used for heavy duty applications. Periodical re-lubrication is
necessary to achieve the full mechanical life of bearings.
5.1.4. Bearings lubrication
Many factors can determine when re-lubrication of the bearings is required: the type and dimension of bearing, its
operating speed, the working temperature, pulleys dimension, installed motor power, type of grease and the working
environment. It is therefore only possible to give some indications based on statistical data available.
For these reasons the re-lubrication intervals tf( time period, at the end of which 99% of the bearings are still reliably
lubricated, and represent L1grease lives. The L10 grease lives are approximately 2,7 the L1 lives) can be obtained from
the attached figure taking into account the rotational speed and diameter. This figure is valid for bearings on horizontal
shafts with normal loads and for temperatures not higher than 70°C. For higher temperatures we suggest halving the
time between re-lubrication every 15°C increase in ambient temperature, without exceeding the maximum working
temperature stated in the catalogue.

Cod. 985719 – 00 / July 2004 16
For bearings on vertical shafts the intervals obtained from the diagram should be halved.
These values are not valid in presence of water, humidity or solid impurities (dust/air mixture for category 2D and 3D in
case of Atex fans), which can go inside the bearings. In this case we recommend to renew frequently the whole grease.
Never schedule relubrication intervals over of 30000 hours.
The grease quantity to be supplied can be obtained from the equation below for applications in standard conditions
(temperature not exceeding 70°C):
Where:
(g/h) = 0.005 x D x B g = grease quantity (g)
h = working hours
D = bearing outside diameter (mm)
B = total bearing width (mm)

Cod. 985719 – 00 / July 2004 17
To re-lubricate it is necessary to use the same grease as that employed at the initial lubrication.
Bearing type Grease type
YLithium soap grease with a mineral oil base according to DIN 51825-K3K-30
consistency NLGI 3
SNL-SYT Lithium soap grease with a mineral oil base - consistency NLGI 2
5.2. REPLACING INSTRUCTIONS FOR BEARINGS
5.2.1. Dismantling the bearing with eccentric locking collar
1) Unscrew the grub screw of the eccentric collar
2) Rotate the locking collar in the opposite direction to the direction
of shaft rotation
3) Measure and mark the position of the bearing on the shaft
4) Suspend the shaft between the bracket and the impeller
5) Remove the bearing bracket. For AT fans, the bearing can be
dismantled avoiding this operation
6) Remove with a file, the flash on the shaft produced by the grub
screw
7) Remove the bearing from the shaft with an extractor or tapping
the inner ring of the bearing with a hammer
8) Replace the bearing and the rubber damper
5.2.2. Mounting the bearing with eccentric
locking collar
1) Put the bearing into the rubber damper. Mount the bracket around the rubber. For AT fan it is possible to insert
bearing+rubber with bracket already assembled and mounted on the sideplate, after having greased the rubber to
insert it more easily
2) Carefully clean the shaft. If the shaft is not new, make sure that dimension and finishing are correct
3) Mount the bracket with bearing on the shaft in the marked position
4) Fix the bracket on the sideplate
5) Place the eccentric locking collar on the inner ring extension and tighten it in the direction of the shaft rotation
6) Tighten the grub screw without exceeding the maximum torque
Shaft diameter Hexagon key size Suggested tightening torque Maximum tightening torque
mm mm Nm Nm
20 3 4 6
25 3 4 6
30 4 7 10
35 5 17 25
40 5 17 25
45 5 17 25
50 5 17 25
60 5 17 25

Cod. 985719 – 00 / July 2004 18
5.2.3. Dismantling the plummer block with ball bearing and eccentric locking collar
1) Suspend the shaft between the bearing support bar and the impeller
2) unscrew the grub screw of the eccentric collar
3) Rotate the locking collar in the opposite direction to the direction of shaft rotation
4) Measure and mark the position of the bearing on the shaft
5) Unscrew the bolts of the plummer block
6) Remove with a file, the flash on the shaft produced by the grub screw
7) Remove the plummer block from the shaft with an extractor or tapping the inner ring of the bearing with a hammer
8) Replace the plummer block
5.2.4. Mounting the plummer block with ball bearing and eccentric locking collar
1) Carefully clean the shaft. If the shaft is not new, make sure that dimension and finishing are correct
2) Insert the bearing at the marked position on the shaft
3) Fully tighten the attachment bolts in the housing base
4) Place the eccentric locking collar on the inner ring extension and tighten it in the direction of rotation of the shaft
5) Tighten the grub screw without exceeding the maximum torque (see table in the paragraph above)
5.2.5. Dismantling the plummer block with ball bearing and adapter sleeve
1) Suspend the shaft between the bearing support bar and the impeller
2) Mark the position of the adapter sleeve on the shaft
3) Release the tap on the locking washer
4) Loosen the nut leaving it in position
5) Unscrew the attachment bolts of the housing base
6) Remove the plummer block from the shaft with an extractor or tapping the inner ring of the bearing with a hammer
7) Replace the plummer block
5.2.6. Mounting the plummer block with ball bearing and adapter sleeve
1) Carefully clean the shaft. If the shaft is not new, make sure that dimension and finishing are correct
2) Remove the nut and the locking washer from the adapter sleeve (fig.2)
3) Insert the sleeve at the marked position on the shaft (fig.1,3)
4) Slide the plummer block unit up on the adapter sleeve with the large end of the tapered bore leading
5) Insert the locking washer and screw the lock nut on to the adapter sleeve using the proper wrench according to the
tightening torque indicated in the table(fig.4)
6) Bend down a tap on the locking washer in one of the slots provided around the circumference of the nut (fig.5)
7) Align the two units and fully tighten the attachment bolts (fig.6)

Cod. 985719 – 00 / July 2004 19
Unit Shaft
diameter Hook spanner Min. tightening torque Max. tightening torque
mm mm Nm Nm
SYJ 25 KF 20 HN5 13 17
SYJ 30 KF 25 HN6 22 28
SYJ 35 KF 30 HN7 27 33
SYJ 40 KF 35 HN8 35 45
SYJ 45 KF 40 HN9 45 55
SYJ 50 KF 45 HN10 55 65
SYJ 55 KF 50 HN11 65 85
SYJ 65 KF 60 HN13 110 150
5.2.7. Dismantling the plummer block SNL with self-aligning ball bearing and
adapter sleeve
1) Suspend the shaft between the bearing support bar and the impeller
2) Unscrew the bolts and remove the upper part of the housing
3) Remove the shaft with bearing from the housing
4) A hammer can be used to remove the bearing from the shaft
5) Mark the position of the sleeve on the shaft. Release the tap on the locking washer
6) Unscrew the nut leaving it in position
7) Remove the nut, lock washer and the bearing from the shaft
5.2.8. Mounting the plummer block SNL with self-aligning ball bearing and adapter
sleeve
If the bearing is mounted on an adapter sleeve, determine the position of the housing. The grease nipple arranged at one
side of the housing cap (for improved lubrication) should be always positioned at the side opposite to the sleeve nut.
Where housings are mounted at shaft ends, grease should be applied at the end cover side. It is necessary to consider
the complete housing as the base and cap will only fit together as supplied.

Cod. 985719 – 00 / July 2004 20
1Position the housing on the support surface
2 Fit the attachment bolts but do not tighten them
3
Insert one seal half in each of the grooves in the housing base and fill with
grease the space between the two lips
4
Wipe the preservative from the bore, outside diameter of the bearing and
surfaces of the sleeve
5
Lightly oil the bore of the bearing with a thin mineral oil. Open the adapter
sleeve by inserting a screwdriver or other suitable tool in the slit and slide
the sleeve along the shaft to the correct position
6
Place the bearing on the sleeve
7
Screw on the nut with its chamfer facing the bearing but do not mount the
locking washer
8
Tighten the nut by hand just enough to achieve proper contact between
bearing, sleeve and shaft
9
If a sleeve with metric thread is used, tighten the nut through the angle 75°
using a hook spanner
10
Re-position the spanner at 180° to its original position and tighten the
spanner a few degrees more by tapping the spanner handle lightly with a
hammer. This will straighten up the bearing if it has become skewed on the
shaft
This manual suits for next models
5
Table of contents
Other Nicotra Fan manuals
Popular Fan manuals by other brands

Domair
Domair FD-40M user manual

Black & Decker
Black & Decker FS1600R user manual

Minka Group
Minka Group minkaAire DECO Instruction manual warranty certificate

cecotec
cecotec ENERGYSILENCE 8090 SKYLINE instruction manual
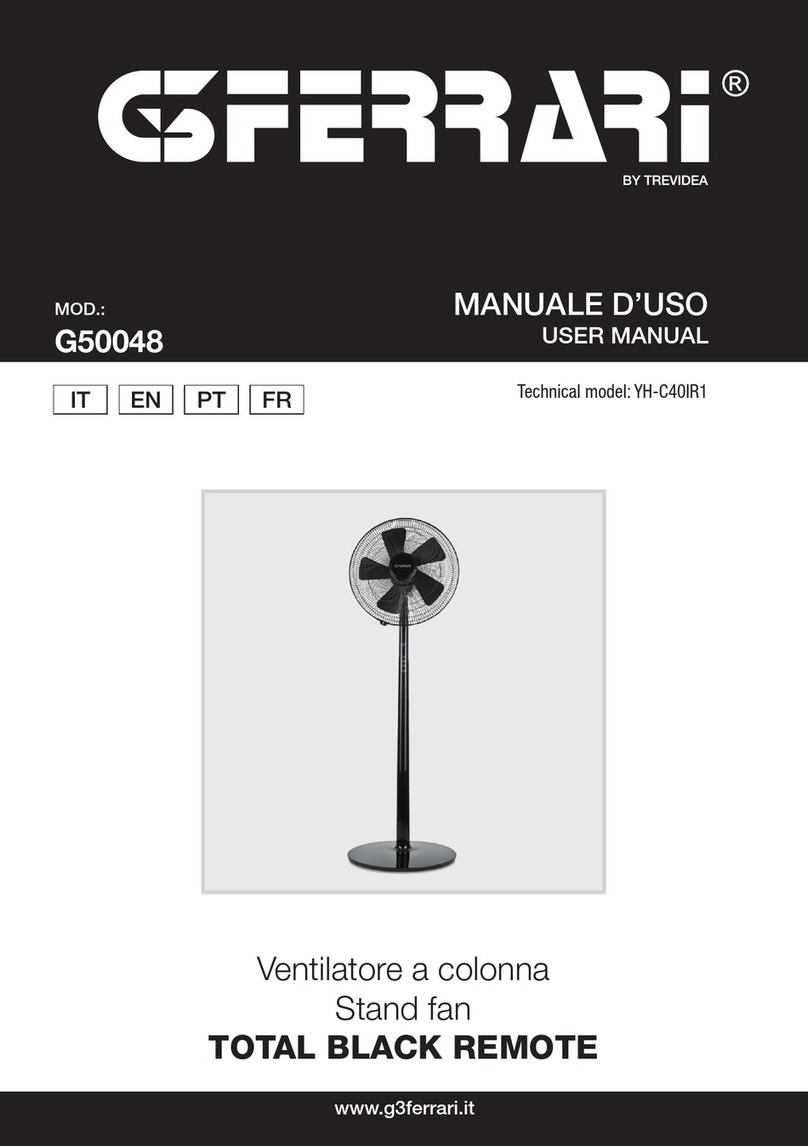
G3 Ferrari
G3 Ferrari TOTAL BLACK REMOTE user manual
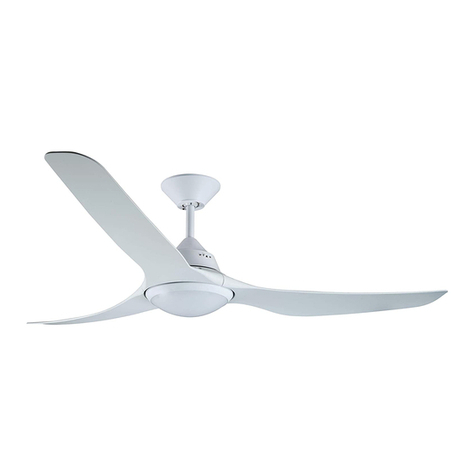
LUCCI Air
LUCCI Air AIRFUSION MARINER manual
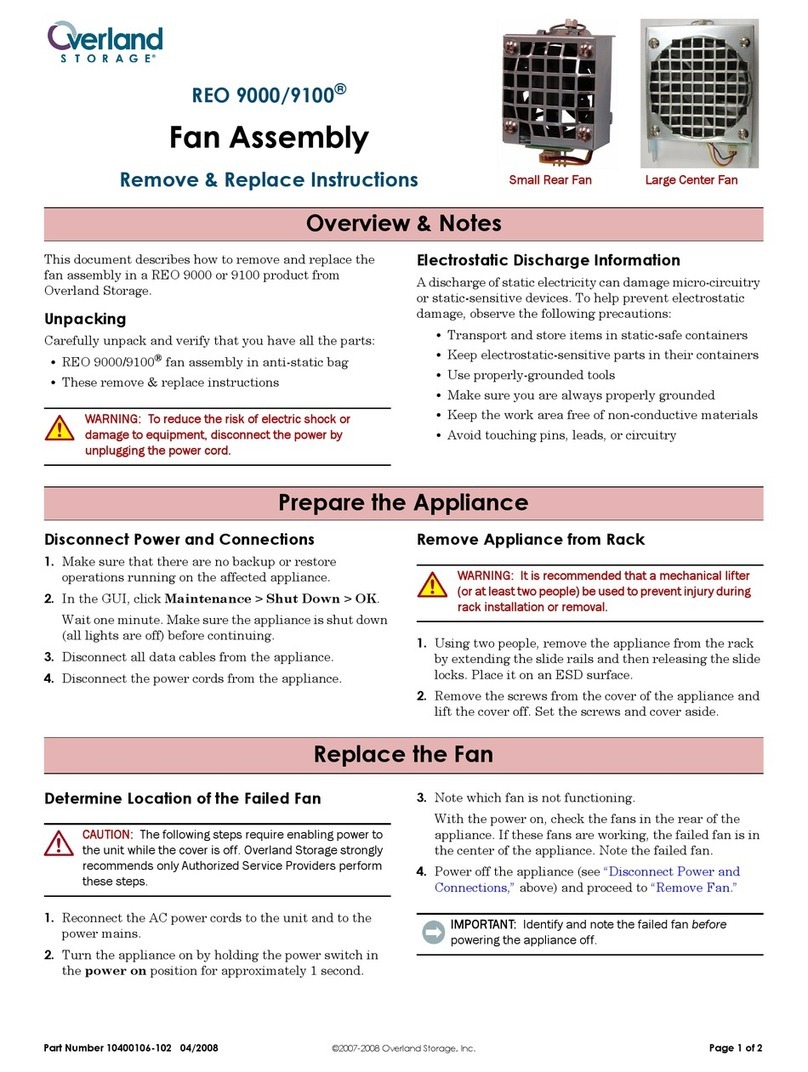
Overland Storage
Overland Storage REO 9000 Remove & Replace Instructions

Hunter
Hunter Crown Canyon II installation manual
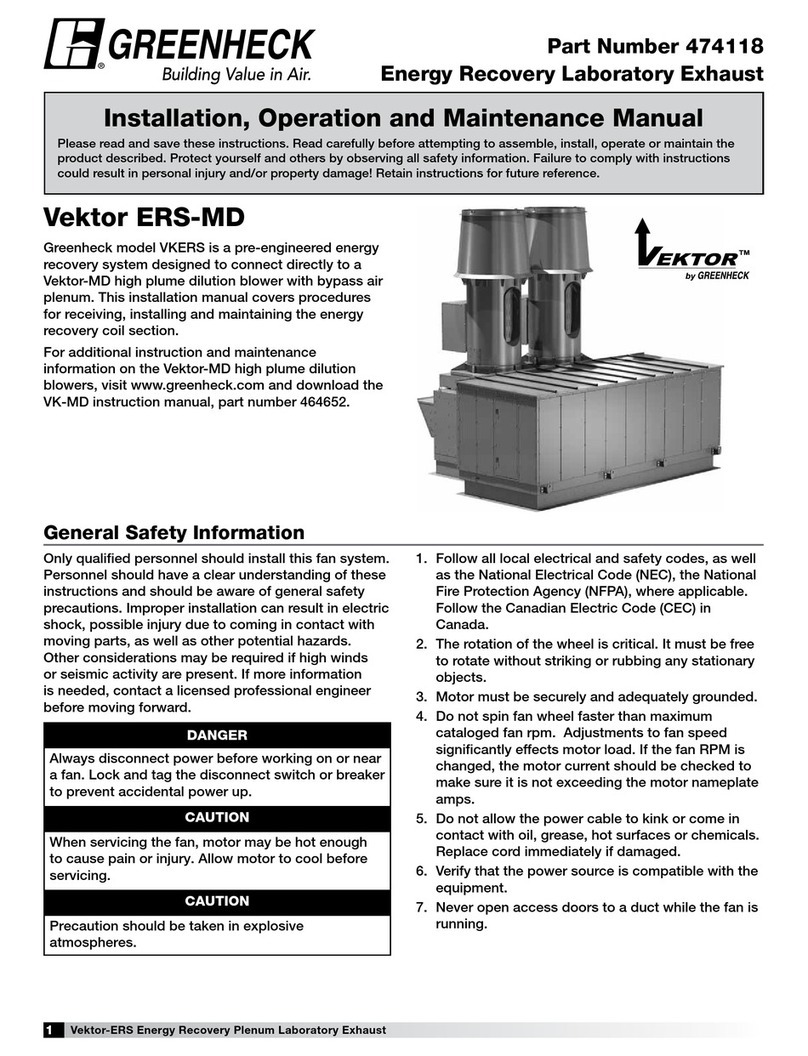
Greenheck
Greenheck ERS-MD Installation, operation and maintenance manual
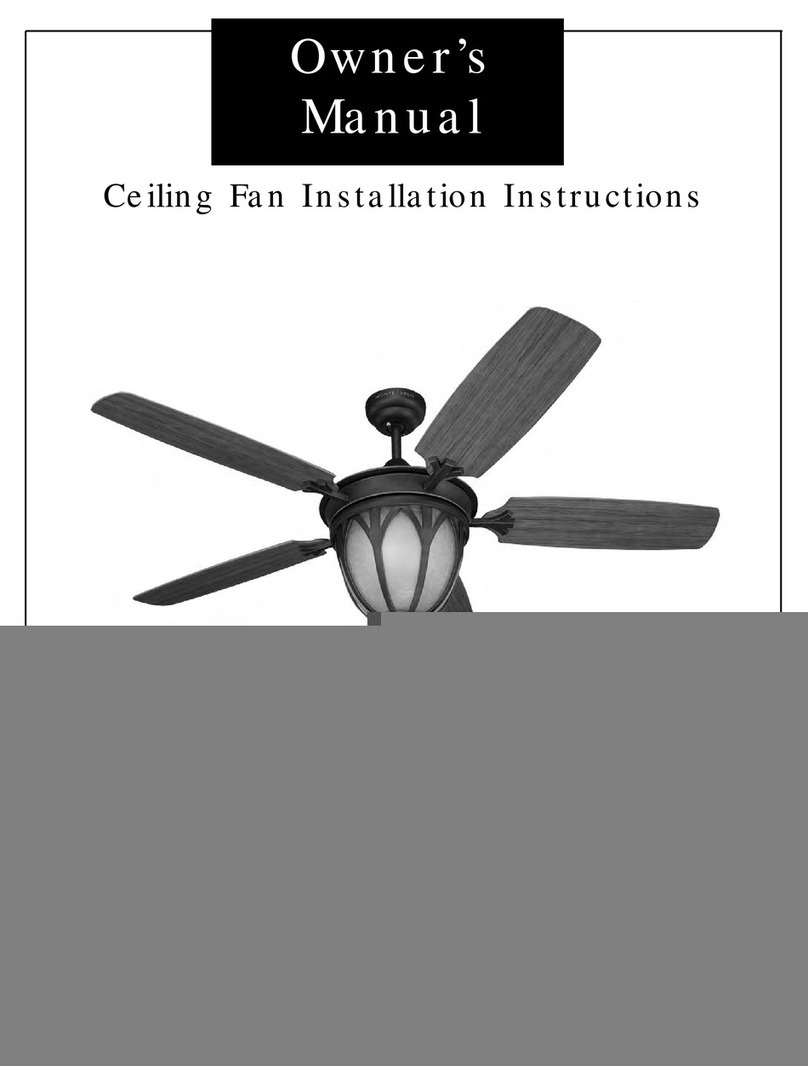
Monte Carlo Fan Company
Monte Carlo Fan Company 5GIR54XXD Series owner's manual
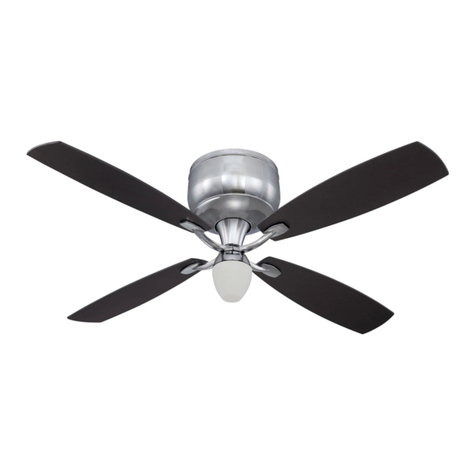
Craftmade
Craftmade DE52CH4 installation guide

Noaton
Noaton CALLISTO Instructions for use