NXP Semiconductors LPC845 User manual

LPC845 Capacitive Touch Kit
User Manual
User Manual for LPC845 Development Kit
Rev. 1.0 — 27 November 2017 User Manual
Document information
Info Content
Keywords LPC845, OM40004, LPC845, LPC844, UM11080
Abstract LPC845 Capacitive Touch Kit User Manual

UM11080 All information provided in this document is subject to legal disclaimers. © NXP B.V. 2017. All rights reserved.
User Manual Rev. 1.0 — 27 November 2017 2 of 12
Contact information
For more information, please visit: http://www.nxp.com
NXP Semiconductors LPC845 Capacitive Touch Kit
User Manual
Revision history
Rev Date Description
1.0 20171115 First draft

UM11080 All information provided in this document is subject to legal disclaimers. © NXP B.V. 2017. All rights reserved.
User Manual Rev. 1.0 — 27 November 2017 3 of 12
NXP Semiconductors LPC845 Capacitive Touch Kit
User Manual
1. Introduction
The LPC845 Capacitive Touch Kit enables easy evaluation of the capacitive touch
features of the LPC84x family of devices. The Kit can be used with a range of
development tools, including the MCUXpresso IDE, IAR EWARM and Keil MDK.
The LPC845 Capacitive Touch Kit board includes the following features:
•Compatible with MCUXpresso IDE and other popular toolchains (incl. IAR and Keil)
•On-board CMSIS-DAP (debug probe) with VCOM port, based on LPC11U35 MCU
•LPC845 Main Processor (MP) Board, compatible with LPCXpresso845MAX board
(for common features), for easy code porting/sharing
•Rotary wheel and slider (RWS) sensor board
•9 button matrix (BM) sensor board
•Debug connector to allow debug of target MCU using an external probe
•LEDs on sensor boards for each capacitive touch pad
•Target ISP and User/Wake buttons
•Target Reset button
•DAC output via speaker driver and speaker
2. Board Layout
Figure 2 below shows the layout of the MP board, indicating location of jumpers, buttons,
connectors/expansion options and MCU devices.
Fig 1. LPC845 Capacitive Touch Kit boards

UM11080 All information provided in this document is subject to legal disclaimers. © NXP B.V. 2017. All rights reserved.
User Manual Rev. 1.0 — 27 November 2017 4 of 12
NXP Semiconductors LPC845 Capacitive Touch Kit
User Manual
Table 1 below shows the layout of the MP board, indicating location of jumpers, buttons,
connectors/expansion options and MCU devices.
Fig 2. MP board layout (top silkscreen)
P10
P1
P3 P2
P11
P8
P7
P5
J3
P6
P9
S2
WAKE
S3
ISP
D1
D9
D10
D8
S1
RESET
P4
J4
Table 1. Jumpers and connectors
Circuit reference Description Reference section
J3 External SWD debug connector for LPC845 [4.1]
J4 USB connector for debug probe / board power [4]
J5 External SWD debug connector for LPC11U35 (not installed, would be
mounted on underside of PCB.)
[4]
P1 P1 is not normally installed during production. After removing R6 (which is
a zero ohm resistor in parallel with P1), the VDD supply to the LPC845
can be isolated from that to other devices on the board.
n/a

UM11080 All information provided in this document is subject to legal disclaimers. © NXP B.V. 2017. All rights reserved.
User Manual Rev. 1.0 — 27 November 2017 5 of 12
NXP Semiconductors LPC845 Capacitive Touch Kit
User Manual
P2 Power measurement point. Connect a voltmeter across P2 to measure
voltage drop across a 2.43 ohm resistor connected in-line with the supply
to the LPC845 device.
[6]
P4 External supply voltage connection. An external power supply may be
used by connecting it to P4; pin 1 should be connected to pin 1 and
ground to pin 2. A 5V nominal supply should be used.
n/a
P5 LPC11U35 Device Firmware Update (DFU) mode enable. Install P5
before powering up the board via USB in order to place the LPC11U35 in
DFU mode (thus enabling software update via drag and drop
programming on a host computer.)
[3.1]
P6 Inserting a jumper on JP1 holds the LPC11U35 debug probe in reset.
Install JP1 when using an external debug probe.
[4.1]
P7 Once R35 has been removed, P7 can be used to connect/disconnect the
LPC845 UART TX from the LPC11U35 debug probe (VCOMM
connection).
n/a
P8 Once R39 has been removed, P6 can be used to connect/disconnect the
LPC845 UART RX from the LPC11U35 debug probe (VCOMM
connection).
n/a
P9 Sensor board connector. The RWS, BM or other custom sensor board
connect to the MP via this connector.
[5]
P10 Connects CAPT_YH signal (PIO1_9) to the comparator input 5
(PIO0_30). Should be installed for normal use.
n/a
P11 Ammeter connection. After removal of R53, an ammeter can be installed
between the pins of JP2 to measure current flow to the LPC845. Once
R53 has been removed, P11 must either be installed or an ammeter in
place in order for the LPC845 to be powered.
[6]
Table 1. Jumpers and connectors
Circuit reference Description Reference section

UM11080 All information provided in this document is subject to legal disclaimers. © NXP B.V. 2017. All rights reserved.
User Manual Rev. 1.0 — 27 November 2017 6 of 12
NXP Semiconductors LPC845 Capacitive Touch Kit
User Manual
3. Getting Started
The firmware for the on-board debug probe and Windows 7/8 driver for the virtual com
(VCOM) port are available from http://nxp.com/demoboard/om40004 under the Software
and Tools tab (look under “Software” download types). If using Window 7 or 8, you will
need to install the VCOM driver by running the installer program (see installation notes
included in the package.)
The MP board is pre-programmed with a simple program to demonstrate use of the BM
and MP boards together. Connect a micro USB cable from connector J4 to a host
computer or power supply to power up the board and run this program. When the program
is running, firmly press a button on the BM board to light the associated LED (i.e. X0 to
light D0, X1 for D1, etc.)
The rest of this section describes how to set up your board for use with MCUXpresso IDE
and/or third party tools.
3.1 Driver installation and (optional) debugger firmware update
The MP board comes pre-programmed with a CMSIS-DAP firmware image; it is not
necessary to update the debugger firmware image, but this can be done by following the
steps below.
1. With the board unpowered, install jumper P5.
2. Power the board. Using File Explorer (or equivalent on Mac/Linux platforms), look at
the available drives on your system. A device called CRP_DISABLED will appear.
3. Delete the firmware.bin file on the CRP_DISABLED drive.
4. Drag and drop the firmware.bin file you downloaded from nxp.com on to the
CRP_DISABLED drive.
5. Remove P5, unplug then repower the board.
6. The board should now enumerate on your system - allow 20-30 seconds for this to
complete.
3.2 Using the board with MCUXpresso IDE
To use the board during a debug session in MCUXpresso IDE, connect to the host
computer then follow the steps below.
Note that MCUXpresso IDE has built-in knowledge of the LPC84x part family, so does not
require any SDK installation steps. Follow the steps below to build and run a simple
example from the LPC84x Code Bundles provided by NXP.
1. Download the latest LPC84x Code Bundle from nxp.com:
http://www.nxp.com/products/software-and-tools/software-development-tools/softwar
e-tools/lpc800-code-bundles:LPC800-Code-Bundles.
2. Open a new workspace in the IDE.
3. In the Quickstart panel of the IDE, click in “Import a new project from the file system”

UM11080 All information provided in this document is subject to legal disclaimers. © NXP B.V. 2017. All rights reserved.
User Manual Rev. 1.0 — 27 November 2017 7 of 12
NXP Semiconductors LPC845 Capacitive Touch Kit
User Manual
4. In the “Import project(s) from file system...” dialog box that opens, click “Browse...” in
the Project Archive (from zip) section, and select the LPC84x Code Bundle zip file
downloaded in step (1). Click “Next >” on the “Import project(s) from file system...”
dialog to continue.
5. You will see several projects listed in the Code Bundle; click “Finish” to import them
all.
6. The dialog box will close, and you will see the imported projects in the Project tab at
the upper left window of the IDE. Click on CapTouch_9Sensor_Button to select it,
then select Build from the Quickstart panel. You will see the build processing in the
Console window to the right of the Quickstart panel. The projects are set up to include
dependency checking, so the build process will automatically build the utility and
peripheral libraries as well as the example program.
7. Ensuring the MP is connected to the host computer, click Debug in the Quickstart
panel. The IDE will search for available debug probes. Select the debug probe that
appears for your board, then click OK. Note that the IDE will remember your selection
for the next time you debug this project, so will not prompt for this again, unless it
cannot find the board.
8. The code will execute to main. Press F8 to resume and run the program. You will now
see the same demonstration program for the BM board running. Note that the Code
Bundle includes similar examples for the Slider (“CapTouch_3Sensor_Slider”) and
Rotary Wheel (“CapTouch_6Sensor_Wheel”) sensors of the RWS board.
3.3 Using MP with 3rd Party IDEs
Once the board debugger firmware has been installed (as described in Section 3.2), to
use the board during a debug session in MCUXpresso IDE, it can be used with 3rd party
development tools. Set up will vary between Development Tools, but the board debug
probe should supported as a CMSIS-DAP probe in all cases).
Code Bundles, including sample projects for Keil MDK and IAR EWARM, are available
from NXP’s website at
http://www.nxp.com/products/software-and-tools/software-development-tools/software-to
ols/lpc800-code-bundles:LPC800-Code-Bundles. Refer to the readme files provided with
each code bundle in order to build/debug.
When using Keil MDK, install the Device Pack for the LPC84x (version 1.5 or later) before
attempting to use the board.
When using IAR EWARM, ensure that you have version 8.12.2 or later in order to have
LPC84x device family support.
4. Debug Probe
The on-board LPC11U35 provides CMSIS-DAP debug probe functionality, plus a virtual
comm port (VCOM) capability via PIO1_16 and PIO1_17 of the LPC845 target. This
functionality bridges the LPC845 serial port via USB, so that PC applications such as the
FreeMASTER utility (used to tune capacitive touch board designs) can communicate
directly with the target. (See the notes included with the Code Bundle examples for how to
use FreeMaster with this Kit.)

UM11080 All information provided in this document is subject to legal disclaimers. © NXP B.V. 2017. All rights reserved.
User Manual Rev. 1.0 — 27 November 2017 8 of 12
NXP Semiconductors LPC845 Capacitive Touch Kit
User Manual
The CMSIS, DISK and COMM LEDs are connected to the LPC11U35 device. The
behavior of the LEDs will vary depending on firmware used, typically the CMSIS LED will
blink when debug communication is occurring, and the COMM LED will blink when data is
being transferred over the VCOMM port.
The board design includes pads for an external debug probe to be connected to the
LPC11U35 (connector J5). This connector is not installed, and is not intended for
customer use.
4.1 Using an external debug probe
An external debug probe that supports ARM’s SWD interface, such as a SEGGER J-Link
or PE Micro probe, can be used with the MP board. The external probe must be
connected to header J3. When an external debug probe is used, the on-board probe must
be held in reset by placing a jumper on P6. It is recommended that P6 is fitted before
powering the board.
5. Sensor Board Connection
The BM and RWS board connect to the MP board via a 2 x 13 right-angled connector
(circuit reference P9 on the MP board.) This connector provides all the capacitive touch
signals plus power, ground and GPIO signals to drive the LEDs. It is recommended that
power be removed before connecting / disconnecting the boards.
Custom designed sensor boards may be used with the MP board. Refer to the LPC84x
User Manual and the application note AN12083. for further information on sensor design
and associated software development. The pin connections for P9 are shown in Figure 3
below.

UM11080 All information provided in this document is subject to legal disclaimers. © NXP B.V. 2017. All rights reserved.
User Manual Rev. 1.0 — 27 November 2017 9 of 12
NXP Semiconductors LPC845 Capacitive Touch Kit
User Manual
6. Power measurement
P2 is provided to enable supply current to the LPC845 to be measured by placing an
ammeter in line with P2 pins. By default this jumper is bypassed by a resistor (R5) which
needs to be removed in order to use an ammeter. Header P1 may be installed to measure
supply power to the LPC845 by measuring voltage drop across a 2.43 ohm resistor on the
board.
7. Other board features
This section describes other board features not detailed elsewhere in this document.
7.1 ISP booting and the ISP button
The LPC845 can be forced into ISP boot mode by holding down the ISP button (S3) and
then holding and releasing reset. The ISP button is connected via a 100 ohm resistor to
LPC845 pin PIO0_12, which is also routed to the LPCXpresso expansion connector (pin
45) and to the cathode of the red user LED. LPC845 pin PIO0_12 can be reconfigured by
software so that the button can be used by an application as a general purpose button
(refer to the LPC84x User Manual).
Fig 3. MP Sensor Board Connector (P9)
P1_1-CAPT_X2
1 2
3 4
5 6
7 8
910
11 12
13 14
15 16
17 18
19 20
21 22
23 24
25 26
P9
HEADER 2x13 RA
PIO0_15 PIO0_16
PIO0_18
PIO0_19 PIO0_20
PIO0_21 PIO0_22
PIO0_17
VCC VCC
PIO0_30/ACMP_I5
P1_8-CAPT_Y_LOWPIO1_9 / CAPT_YH
PIO0_23
P0_31-CAPT_X0P1_0-CAPT_X1
P1_2-CAPT_X3
P1_3-CAPT_X4P1_4-CAPT_X5
P1_5-CAPT_X6P1_6-CAPT_X7
P1_7-CAPT_X8

UM11080 All information provided in this document is subject to legal disclaimers. © NXP B.V. 2017. All rights reserved.
User Manual Rev. 1.0 — 27 November 2017 10 of 12
NXP Semiconductors LPC845 Capacitive Touch Kit
User Manual
7.2 Wake button
The Wake button (S2) is for general purpose use by LPC845 applications. It is connected
via a 100 ohm resistor to a 100K ohm pull-up to 3.3V, and to the LPC845 PIO0_4 pin. This
pin can wake the LPC845 from deep power-down.
7.3 User LEDs
Three users LEDs are provided on the board, one blue, one green and one red. The
anodes of the LEDs are connected together, then through solder jumper SJ1 to the 3.3V
regulator output. SJ1 can be opened to prevent leakage from the LPC845 pins through
the diodes if accurate power measurement measurements are being performed. The
LEDs are connected to the LPC845 as shown in the table below.
7.4 Speaker driver
The LPC845 DACOUT output PIO0_29 is route to an IS31AP4991 speaker driver (see
Integrated Silicon Solutions web site for datasheet). This device can drive 8 to 32 ohm
speakers; a 32 ohm speaker is supplied with the board and resistors have been selected
to provide a reasonable volume level for musical tones. If desired, a capacitor can be
added in parallel with the speaker driver feedback resistor, in order to reduce the speaker
circuit bandwidth and reject DAC output sampling artifacts. This capacitor can be added
using the through holes with circuit reference designator C24.
Table 2. LED connections
LED LPC845 pin Notes
Blue (D2) PIO1_15 Shared with LPCXpresso connector pin 44
Red (D3) PIO0_12 Shared with ISP pin and LPCXpresso connector pin 45
Green (D1) PIO0_0

UM11080 All information provided in this document is subject to legal disclaimers. © NXP B.V. 2017. All rights reserved.
User Manual Rev. 1.0 — 27 November 2017 11 of 12
NXP Semiconductors LPC845 Capacitive Touch Kit
User Manual
8. Legal information
8.1 Disclaimers
Limited warranty and liability — Information in this document is believed to be accurate and reliable. However, NXP
Semiconductors does not give any representations or warranties, expressed or implied, as to the accuracy or completeness of
such information and shall have no liability for the consequences of use of such information.
In no event shall NXP Semiconductors be liable for any indirect, incidental, punitive, special or consequential damages (including
- without limitation - lost profits, lost savings, business interruption, costs related to the removal or replacement of any products
or rework charges) whether or not such damages are based on tort (including negligence), warranty, breach of contract or any
other legal theory.
Notwithstanding any damages that customer might incur for any reason whatsoever, NXP Semiconductors’ aggregate and
cumulative liability towards customer for the products described herein shall be limited in accordance with the Terms and
conditions of commercial sale of NXP Semiconductors.
Right to make changes — NXP Semiconductors reserves the right to make changes to information published in this document,
including without limitation specifications and product descriptions, at any time and without notice. This document supersedes
and replaces all information supplied prior to the publication hereof.
Suitability for use — NXP Semiconductors products are not designed, authorized or warranted to be suitable for use in life
support, life-critical or safety-critical systems or equipment, nor in applications where failure or malfunction of an NXP
Semiconductors product can reasonably be expected to result in personal injury, death or severe property or environmental
damage. NXP Semiconductors accepts no liability for inclusion and/or use of NXP Semiconductors products in such equipment
or applications and therefore such inclusion and/or use is at the customer’s own risk.
Applications — Applications that are described herein for any of these products are for illustrative purposes only. NXP
Semiconductors makes no representation or warranty that such applications will be suitable for the specified use without further
testing or modification.
Customers are responsible for the design and operation of their applications and products using NXP Semiconductors products,
and NXP Semiconductors accepts no liability for any assistance with applications or customer product design. It is customer’s
sole responsibility to determine whether the NXP Semiconductors product is suitable and fit for the customer’s applications and
products planned, as well as for the planned application and use of customer’s third party customer(s). Customers should
provide appropriate design and operating safeguards to minimize the risks associated with their applications and products.
NXP Semiconductors does not accept any liability related to any default, damage, costs or problem which is based on any
weakness or default in the customer’s applications or products, or the application or use by customer’s third party customer(s).
Customer is responsible for doing all necessary testing for the customer’s applications and products using NXP Semiconductors
products in order to avoid a default of the applications and the products or of the application or use by customer’s third party
customer(s). NXP does not accept any liability in this respect.
Export control — This document as well as the item(s) described herein may be subject to export control regulations. Export
might require a prior authorization from national authorities.
8.2 Trademarks
Notice: All referenced brands, product names, service names and trademarks are the property of their respective owners.

UM11080 All information provided in this document is subject to legal disclaimers. © NXP B.V. 2017. All rights reserved.
User Manual Rev. 1.0 — 27 November 2017 12 of 12
NXP Semiconductors LPC845 Capacitive Touch Kit
User Manual
9. Contents
1 Introduction . . . . . . . . . . . . . . . . . . . . . . . . . . . . 3
2 Board Layout . . . . . . . . . . . . . . . . . . . . . . . . . . . 3
3 Getting Started . . . . . . . . . . . . . . . . . . . . . . . . . . 6
3.1 Driver installation and (optional) debugger
firmware update . . . . . . . . . . . . . . . . . . . . . . . . 6
3.2 Using the board with MCUXpresso IDE . . . . . . 6
3.3 Using MP with 3rd Party IDEs . . . . . . . . . . . . . 7
4 Debug Probe . . . . . . . . . . . . . . . . . . . . . . . . . . . 7
4.1 Using an external debug probe. . . . . . . . . . . . . 8
5 Sensor Board Connection. . . . . . . . . . . . . . . . . 8
6 Power measurement . . . . . . . . . . . . . . . . . . . . . 9
7 Other board features. . . . . . . . . . . . . . . . . . . . . 9
7.1 ISP booting and the ISP button . . . . . . . . . . . . 9
7.2 Wake button . . . . . . . . . . . . . . . . . . . . . . . . . . 10
7.3 User LEDs . . . . . . . . . . . . . . . . . . . . . . . . . . . 10
7.4 Speaker driver . . . . . . . . . . . . . . . . . . . . . . . . 10
8 Legal information . . . . . . . . . . . . . . . . . . . . . . 11
8.1 Disclaimers. . . . . . . . . . . . . . . . . . . . . . . . . . . 11
8.2 Trademarks . . . . . . . . . . . . . . . . . . . . . . . . . . 11
9 Contents. . . . . . . . . . . . . . . . . . . . . . . . . . . . . . 12
Table of contents
Other NXP Semiconductors Network Hardware manuals

NXP Semiconductors
NXP Semiconductors PMSMLPC55S36EVK User manual
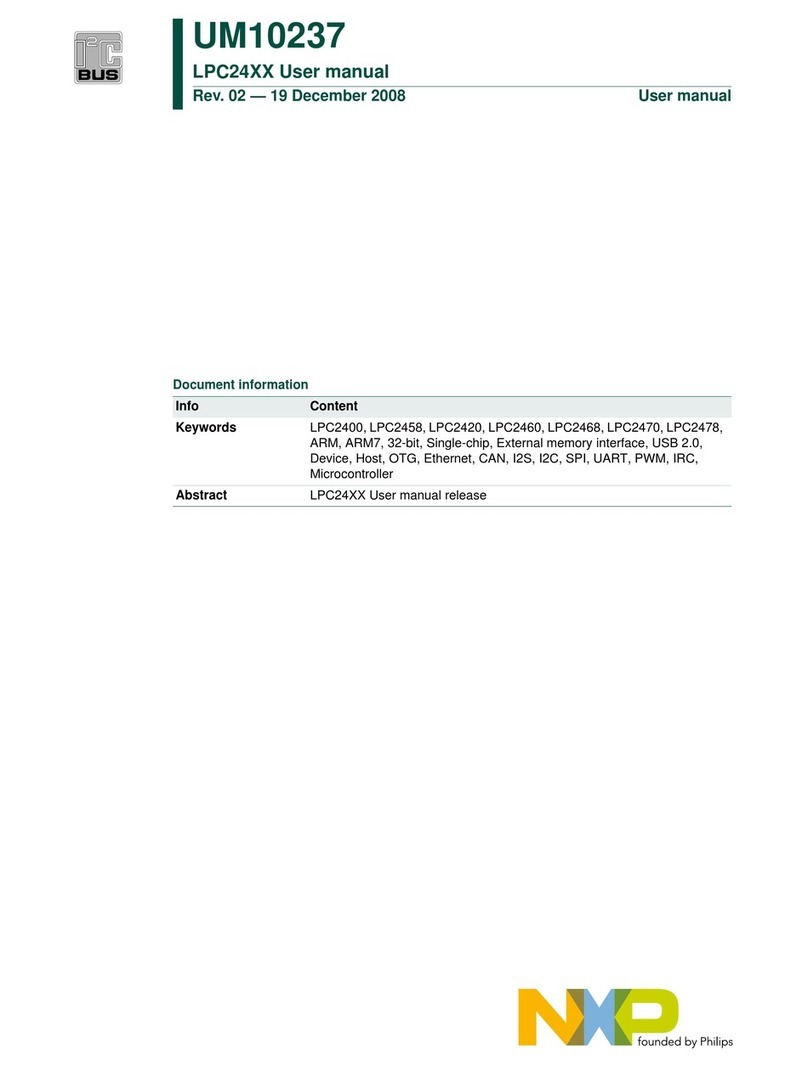
NXP Semiconductors
NXP Semiconductors LPC24XX UM10237 User manual
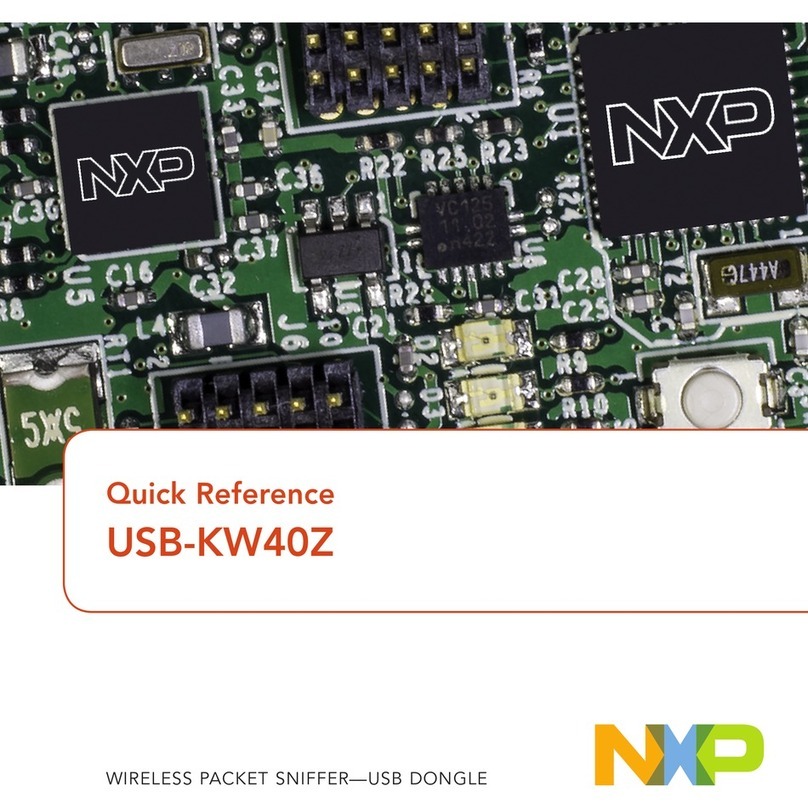
NXP Semiconductors
NXP Semiconductors USB-KW40Z User manual
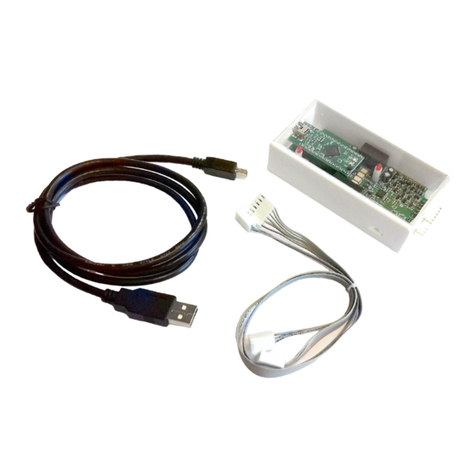
NXP Semiconductors
NXP Semiconductors UM11521 User manual
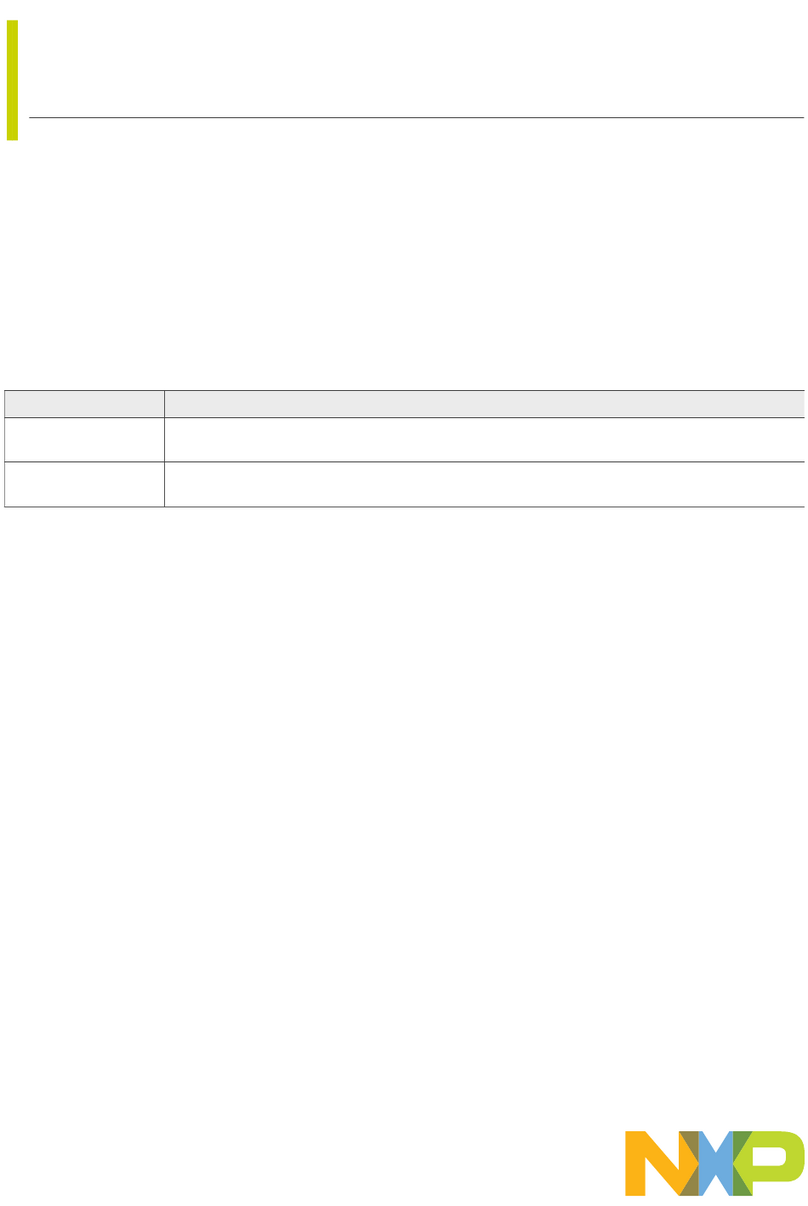
NXP Semiconductors
NXP Semiconductors PMSMRT1060C User manual
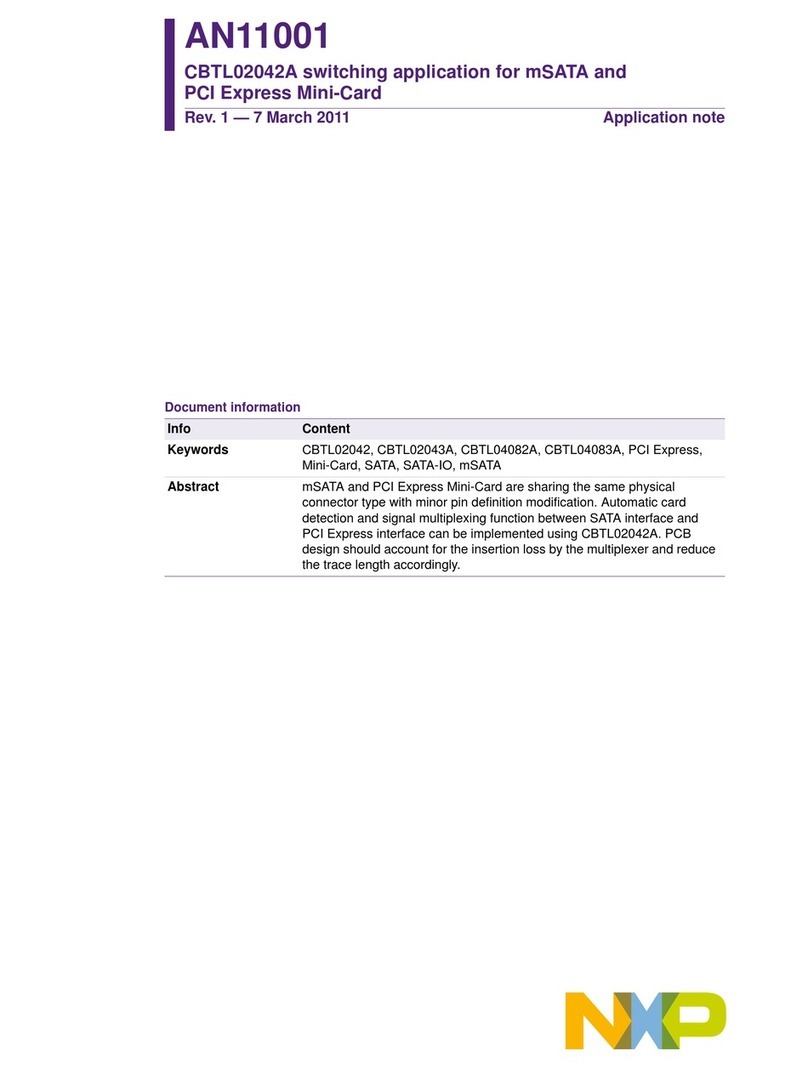
NXP Semiconductors
NXP Semiconductors AN11001 Installation and operating instructions

NXP Semiconductors
NXP Semiconductors AN13887 Installation and operating instructions