Omega HE-XT103 User manual

omega.com
e-mail: [email protected]
For latest product manuals:
omegamanual.info
User’s Guide
Shop online at
MADE IN
HE-XT103
12 Digital DC Inputs,
12 Digital Outputs,
2 Analog Inputs
(Medium Resolution)
HE-XT104
24 Digital DC Inputs,
16 Digital Outputs,
2 Analog Inputs
(Medium Resolution)

Servicing North America:
U.S.A.: Omega Engineering, Inc., One Omega Drive, P.O. Box 4047
ISO 9001 Certified Stamford, CT 06907-0047 USA
Toll Free: 1-800-826-6342 TEL: (203) 359-1660
Canada: 976 Bergar
Laval (Quebec), Canada H7L 5A1
Toll-Free: 1-800-826-6342 TEL: (514) 856-6928
For immediate technical or application assistance:
U.S.A. and Canada: Sales Service: 1-800-826-6342/1-800-TC-OMEGA®
Customer Service: 1-800-622-2378/1-800-622-BEST®
Engineering Service: 1-800-872-9436/1-800-USA-WHEN®
Mexico: En Español: 001 (203) 359-7803 FAX: (001) 203-359-7807
Servicing Europe:
Benelux: Managed by the United Kingdom Office
Toll-Free: 0800 099 3344 TEL: +31 20 347 21 21
Czech Republic: Frystatska 184
733 01 Karviná, Czech Republic
Toll-Free: 0800-1-66342 TEL: +420-59-6311899
France: Managed by the United Kingdom Office
Toll-Free: 0800 466 342 TEL: +33 (0) 161 37 29 00
Germany/Austria: Daimlerstrasse 26
D-75392 Deckenpfronn, Germany
Toll-Free: 0 800 6397678 TEL: +49 (0) 7059 9398-0
United Kingdom: OMEGA Engineering Ltd.
ISO 9001 Certified One Omega Drive, River Bend Technology Centre, Northbank
Irlam, Manchester M44 5BD England
Toll-Free: 0800-488-488 TEL: +44 (0)161 777-6611
OMEGAnet®Online Service Internet e-mail
omega.com [email protected]
It is the policy of OMEGA Engineering, Inc. to comply with all worldwide safety and EMC/EMI
regulations that apply. OMEGA is constantly pursuing certification of its products to the European New
Approach Directives. OMEGA will add the CE mark to every appropriate device upon certification.
The information contained in this document is believed to be correct, but OMEGA accepts no liability for any
errors it contains, and reserves the right to alter specifications without notice.
WARNING: These products are not designed for use in, and should not be used for, human applications.

__________________________________________________________________________________________________________________________________________________________________
Page 1 of 4
1 Specifications
Specifications
Digital DC Inputs XLT103 XLT104 Digital DC
Outputs XLT103 XLT104
Inputs per Module
12 including 4
configurable
HSC inputs
24 including
4
configurable
HSC inputs
Outputs per
Module
12 including
2
configurable
PWM
outputs
16 including
2
configurable
PWM
outputs
Commons per
Module 1 Commons per
Module 1
Input Voltage
Range 12 VDC / 24 VDC Output Type Sourcing / 10 K Pull-Down
Absolute Max.
Voltage 35 VDC Max. Absolute Max.
Voltage 28 VDC Max.
Input Impedance 10 kΩOutput
Protection Short Circuit
Input Current
Positive
Logic Negative Logic
Max. Output
Current per
point
0.5 A
Upper Threshold 0.8 mA -1.6 mA Max. Total
Current 4 A Continuous
Lower Threshold 0.3 mA -2.1 mA Max. Output
Supply Voltage 30 VDC
Max Upper
Threshold 8 VDC Minimum Output
Supply Voltage 10 VDC
Min Lower
Threshold 3 VDC
Max. Voltage
Drop at Rated
Current
0.25 VDC
OFF to ON
Response 1 ms Max. Inrush
Current 650 mA per channel
ON to OFF
Response 1 ms Min. Load None
HSC Max.
Switching Rate
10 kHz Totalizer/Pulse,Edges
5 kHz Frequency/Pulse,Width
2.5 kHz Quadrature
OFF to ON
Response 1 ms
Analog Inputs,
Medium
Resolution
XLT103 XLT104
ON to OFF
Response 1 ms
Number of
Channels 2 2 Output
Characteristics Current Sourcing (Pos logic)
General Specifications
Input Ranges
Safe input voltage
range
Input Impedance
(Clamped @ -0.5
VDC to 12 VDC)
0 - 10 VDC
0 – 20 mA
4 – 20 mA
-0.5 V to +12V
Current Mode:
100 Ω
Voltage Mode:
500 k Ω
Required Power
(Steady State) 130 mA @ 24 VDC
Required Power
(Inrush)
30 A for 1 ms @ 24 VDC
Nominal Resolution
%AI full scale
Max. Over-Current
10 Bits
32,000 counts
35 mA Primary Power
Range
10 – 30 VDC
Conversion Speed All channels converted once
per ladder scan Relative Humidity 5 to 95% Non-
condensing
Max. Error at 25°C
(excluding zero)
4-20 mA 1.00%
0-20 mA 1.00%
0-10 VDC 0.50%
Operating
Temperature -10°C to +60°C
Terminal Type Screw Type,5 mm
Removable
Additional error for
temperatures other
than 25°C
TBD
CE
UL
Filtering
160 Hz hash (noise) filter
1-128 scan digital running
average filter Weight 12.5 oz. (354.36 g)
ycaruccAkcolC +/- Seven
Minutes/Month at 20C
Note: Highest usable frequency for PWM output is 65 KHz
2 Panel Cut-Out and Dimensions
Note: Max. panel thickness: 5 mm.
3 Ports / Connectors / Cables
Note: The case of the XLt is black, but for clarity, it is shown in a
lighter gray color.
3
.
6
2
2
[
9
2
m
m
]
3.622 [92mm]
001XLE002
To Remove Back Cover:
Unscrew 4 screws located on
the back of the unit and remove
back cover.
CAUTION: Do not over tighten
screws when replacing the back
cover.
001ACC009
Power Connector
Power Up:
Connect to Earth Ground.
Apply 10 – 30 VDC.
Screen lights up.
Torque rating 4.5 - 7 Lb-In
(0.50 – 0.78 N-m)
CAN Connector
Use the CAN Connector
when using CsCAN network.
Torque rating 4.5 – 7 Lb-In
(0.50 – 0.78 N-m)
I/O Jumpers (Not Shown): I/O Jumpers (JP) are located
internally. To access, remove back cover of unit.
Wiring Connectors (J1 – J4), I/O Jumpers (JP1-3), and
External Jumpers (RS-485) are described in the Wiring and
Jumpers section of this document.
MJ1
(RS-232 / RS-485)
MJ2
(RS-232 / RS-485)
J1
I/O
Jumper
Memory Slot
001XLE029-R2
J2
I/O
Jumper
NET 1
(CsCAN)
Power
DIP
Switch
If you require a Compliance Table:
1-888-556-6342

__________________________________________________________________________________________________________________________________________________________________
Page 2 of 4
Section 3 continued
4 Wiring and Jumpers
•
•
•
•
Wire according to the type of inputs / outputs used and select
the appropriate jumper option. Use Copper Conductors
in Field Wiring Only, 60/75°C
4.1 I/O Jumpers Settings (JP1 – JP3)
4.2 External DIP Switch Settings (or Jumpers Settings)
4.3 Wiring Examples
J1
Orange
XT103 / XT104
Name
I1 IN1
I2 IN2
I3 IN3
I4 IN4
I5 IN5
I6 IN6
I7 IN7
I8 IN8
H1 HSC1 / IN9
H2 HSC2 / IN10
H3 HSC3 / IN11
H4 HSC4 / IN12
A1 Analog IN1
A2 Analog IN2
0V Ground
J2
Black XT103 XT104
0V Ground
V+ V+ *
NC No
Connect
OUT13
Q12 OUT12
Q11 OUT11
Q10 OUT10
Q9 OUT9
Q8 OUT8
Q7 OUT7
Q6 OUT6
Q5 OUT5
Q4 OUT4
Q3 OUT3
Q2 OUT2 / PWM2
Q1 OUT1 / PWM1
V+* Supply for Sourcing Outputs
J3
Orange XT104
I13 IN13
I14 IN14
I15 IN15
I16 IN16
I17 IN17
I18 IN18
I19 IN19
I20 IN20
I21 IN21
I22 IN22
I23 IN23
I24 IN24
0V Ground
8
1
Pin MJ1 Pins MJ2 Pins
8
TXD OUT TXD OUT
7
RXD IN RXD IN
6
0 V Ground 0 V Ground
5*
+5
60mA OUT +5
60mA OUT
4
RTS OUT TX- OUT
3
CTS IN TX+ OUT
2
RX- /
TX-
IN /
OUT RX- IN
1
RX+ /
TX+
IN /
OUT RX+ IN
Note: The Cscape Module Setup configuration must match
the selected I/O (JP) jumper settings.
I1
0V
001XLE036
12-24VDC
I1
0V
Positive Logic In Negative Logic In
Positive Logic vs. Negative Logic Wiring
The XLt can be wired for Positive Logic inputs or
Negative Logic inputs.
DIPSW3:
FACTORY USE
ONLY (tiny bootloader firmware
downloading). NOT TO BE
USED FOR NORMAL OCS
OPERATION.
DIPSW2: MJ2 Termination
(default – none)
DIPSW1: MJ1 Termination
(default – none)
As seen when looking at the top of the XLt unit:
Memory Slot:
Uses Removable Memory for data logging, screen
captures, program loading and recipes.
Horner Part No.: HE-MC1
Serial Communications:
MJ1: (RS-232 / RS-485) Use for Cscape programming and
Application-Defined Communications.
MJ2: (RS-232 / RS-485) Use for Application-Defined
Communications.
Location of I/O jumpers (JP)
and wiring connectors
(J1 – J4).
Wiring Specifications
For I/O wiring (discrete), use the
following wire type or equivalent:
Belden 9918, 18 AWG (0.8 mm
2
)
or larger.
For shielded Analog I/O wiring,
use the following wire type or
equivalent: Belden 8441, 18
AWG (0.8 mm
2
) or larger.
For CAN wiring, use the
following wire type or equivalent:
Belden 3084, 24 AWG (0.2 mm
2
)
or larger.
The External DIP Switches are used for termination of
the RS-485 ports. The XLt is shipped un-terminated.
To terminate, select one of the jumpers shipped with
the product and insert it based upon the option that is
desired or, select the switch (as shown in the
illustration) and configure based upon the option that
is desired.
Negative Logic
Positive Logic
JP1 Digital DC Inputs
Default
I1
I2
I3
I4
0V
I5
I6
I7
I8
H1
001XLE046
12-24VDC
LOOP
PWR
20mA
0-10VDC
A1
A2
H2
H3
H4
XT103 / 104 J1 Orange
Positive Logic
Digital In
Q1
Q2
Q3
Q4
Q9
Q10
Q11
Q12
Q5
Q6
Q7
Q8
V+
0V
LOAD
LOAD
LOAD
LOAD
LOAD
LOAD
LOAD
LOAD
LOAD
LOAD
LOAD
LOAD
10 - 30VDC
Q13
001XLE024
LOAD
XT103 / 104 J2 Black
Positive Logic
Digital Out
Note: The wiring examples show
Positive Logic input wiring.
I13
I14
I15
I16
I22
I23
I24
0V
I17
I18
I19
I20
I21
001XLE047
12-24VDC
XT104 J3 Orange
Positive Logic
Digital In
J4
Orange XT104
Q16 OUT16
Q15 OUT15
Q14 OUT14
XT104 J4 Orange
Positive Logic
Digital Out
Q14
Q15
V+
0V
LOAD
LOAD
10 - 30VDC
Q16
LOAD
J2
J4
Note:
When using JP3 (A1-A2),
each channel can be
independently configured.
Note:
Loop Power requirements
are determined by the
transmitter specification.
J1 J2
J3
JP3
JP1
001XLE005-R1
J4
20mA 10VDC
JP3
CURRENT OR VOLTAGE INPUTS
001XLE043-R1
A1
A2
A1
A2
11 22
33 44
001XLE037-R1
*+5Vdc 60mA Max

__________________________________________________________________________________________________________________________________________________________________
Page 3 of 4
5 Filter
Filter Constant sets the level of digital filtering according to the
following chart.
Digital Filtering. The illustration above demonstrates the
effect of digital filtering (set with Filter
Constant) on module response to a
temperature change.
6 I/O Register Map
Registers Description
%I1 to %I24 Digital Inputs
%I32 Output Fault
%I25 to %I31 Reserved
%Q1 to %Q16 Digital outputs
%Q17 Clear HSC1 accumulator to 0
%Q18
Totalizer: Clear HSC2
Quadrature 1-2: Accumulator 1
Reset to max – 1
%Q19 Clear HSC3 Accumulator to 0
%Q20
Totalizer: Clear HSC4
Quadrature 3-4: Accumulator 3
Reset to max – 1
%Q21 to %Q32 Reserved
%AI1 to %AI4 Analog inputs
%AI5, %AI6 HSC1 Accumulator
%AI7, %AI8 HSC2 Accumulator
%AI9, %AI10 HSC3 Accumulator
%AI11, %AI12 HSC4 Accumulator
%AQ1, %AQ2 PWM1 Duty Cycle
%AQ3, %AQ4 PWM2 Duty Cycle
%AQ5, %AQ6 PWM Prescale
%AQ7, %AQ8 PWM Period
%AQ9 to %AQ14 Analog outputs
Note: Not all XLt units contain the I/O listed in this table.
Registers PWM HSC Stepper
%AQ1 Start
Frequency
%AQ2
PWM1 Duty
Cycle
(32 bit)
HSC1
Preset
Value Run
Frequency
%AQ3
%AQ4
PWM2 Duty
Cycle
(32 bit)
HSC2
Preset
Value
Accel Count
(32 bit)
%AQ5
%AQ6
PWM Prescale
(32 bit)
Run Count
(32 bit)
%AQ7
%AQ8
PWM Period
(32 bit)
Decel Count
(32 bit)
%Q1 Run
%I30 Ready/Done
%I31 Error
7 MJ2 Pinouts in Full and Half Duplex Modes
60
20
100
40
80
20
0
10
100
90
80
70
60
50
40
30
Scans
0
1 2 3 4 5 60 7
%
C
o
m
p
l
e
t
e
[
]
Filter
Constant
Full Duplex Mode
Half Duplex Mode
Pin MJ2 Pins
Signal Direction
8
TXD OUT
7
RXD IN
6
0 V Ground
5*
+5 60mA OUT
4
TX- OUT
3
TX+ OUT
2
RX- IN
1
RX+ IN
1
8
*+5Vdc 60mA max
Pin MJ2 Pins
Signal Direction
8
TXD OUT
7
RXD IN
6
0 V Ground
5*
+5 60mA OUT
4
TX- OUT
3
TX+ OUT
2
TX-/RX- IN/OUT
1
TX+/RX+ IN/OUT
1
8
*+5Vdc 60mA Max

__________________________________________________________________________________________________________________________________________________________________
Page 4 of 4
8 Safety
When found on the product, the following symbols specify:
All applicable codes and standards need to be followed in the installation of this product.
Adhere to the following safety precautions whenever any type of connection is made to the module:
Connect the safety (earth) ground on the power connector first before making any other connections.
When connecting to electric circuits or pulse-initiating equipment, open their related breakers.
Do not make connections to live power lines.
Make connections to the module first; then connect to the circuit to be monitored.
Route power wires in a safe manner in accordance with good practice and local codes.
Wear proper personal protective equipment including safety glasses and insulated gloves when making connections to power circuits.
Ensure hands, shoes, and floor are dry before making any connection to a power line.
Make sure the unit is turned OFF before making connection to terminals.
Make sure all circuits are de-energized before making connections.
Before each use, inspect all cables for breaks or cracks in the insulation. Replace immediately if defective.
•
•
•
•
•
•
•
•
•
•
•
•
•
Use Copper Conductors in Field Wiring Only, 60/75° C
Warning: Consult
user documentation.
Warning: Electrical
Shock Hazard.
This equipment is suitable for use in Class I, Division 2, Groups A, B, C and D or Non-hazardous locations only
WARNING – EXPLOSION HAZARD – Substitution of components may impair suitability for Class I, Division 2
AVERTISSEMENT - RISQUE D'EXPLOSION - LA SUBSTITUTION DE COMPOSANTS PEUT RENDRE CE MATERIAL INACCEPTABLE POUR LES EMPLACEMENTS DE
CLASSE 1, DIVISION 2
WARNING – EXPLOSION HAZARD – Do not disconnect equipment unless power has been switched off or the area is known to be non-hazardous.
AVERTISSEMENT - RISQUE D'EXPLOSION - AVANT DE DECONNECTOR L'EQUIPMENT, COUPER LE COURANT OU S'ASSURER QUE L'EMPLACEMENT EST DESIGNE
NON DANGEREUX.
WARNING: To avoid the risk of electric shock or burns, always connect the safety (or earth) ground before making any other connections.
WARNING: To reduce the risk of fire, electrical shock, or physical injury it is strongly recommended to fuse the voltage measurement inputs. Be sure to locate fuses as close to the
source as possible.
WARNING: Replace fuse with the same type and rating to provide protection against risk of fire and shock hazards.
WARNING: In the event of repeated failure, do not replace the fuse again as a repeated failure indicates a defective condition that will not clear by replacing the fuse.
WARNING: Only qualified electrical personnel familiar with the construction and operation of this equipment and the hazards involved should install, adjust, operate, or service this
equipment. Read and understand this manual and other applicable manuals in their entirety before proceeding. Failure to observe this precaution could result in severe bodily injury
or loss of life.
This device complies with part 15 of the FCC Rules. Operation is subject to the following two conditions:
1. This device may not cause harmful interference.
2. This device must accept any interference received, including interference that may cause undesired operation.

WARRANTY/DISCLAIMER
OMEGA ENGINEERING, INC. warrants this unit to be free of defects in materials and workmanship for a
period of 13 months from date of purchase. OMEGA’s WARRANTY adds an additional one (1) month
grace period to the normal one (1) year product warranty to cover handling and shipping time. This
ensures that OMEGA’s customers receive maximum coverage on each product.
If the unit malfunctions, it must be returned to the factory for evaluation. OMEGA’s Customer Service
Department will issue an Authorized Return (AR) number immediately upon phone or written request.
Upon examination by OMEGA, if the unit is found to be defective, it will be repaired or replaced at no
charge. OMEGA’s WARRANTY does not apply to defects resulting from any action of the purchaser,
including but not limited to mishandling, improper interfacing, operation outside of design limits,
improper repair, or unauthorized modification. This WARRANTY is VOID if the unit shows evidence of
having been tampered with or shows evidence of having been damaged as a result of excessive corrosion;
or current, heat, moisture or vibration; improper specification; misapplication; misuse or other operating
conditions outside of OMEGA’s control. Components in which wear is not warranted, include but are not
limited to contact points, fuses, and triacs.
OMEGA is pleased to offer suggestions on the use of its various products. However,
OMEGA neither assumes responsibility for any omissions or errors nor assumes liability for any
damages that result from the use of its products in accordance with information provided by
OMEGA, either verbal or written. OMEGA warrants only that the parts manufactured by it will be
as specified and free of defects. OMEGA MAKES NO OTHER WARRANTIES OR
REPRESENTATIONS OF ANY KIND WHATSOEVER, EXPRESS OR IMPLIED, EXCEPT THAT OF TITLE,
AND ALL IMPLIED WARRANTIES INCLUDING ANY WARRANTY OF MERCHANTABILITY AND
FITNESS FOR A PARTICULAR PURPOSE ARE HEREBY DISCLAIMED. LIMITATION OF
LIABILITY: The remedies of purchaser set forth herein are exclusive, and the total liability of
OMEGA with respect to this order, whether based on contract, warranty, negligence,
indemnification, strict liability or otherwise, shall not exceed the purchase price of the
component upon which liability is based. In no event shall OMEGA be liable for
consequential, incidental or special damages.
CONDITIONS: Equipment sold by OMEGA is not intended to be used, nor shall it be used: (1) as a “Basic
Component” under 10 CFR 21 (NRC), used in or with any nuclear installation or activity; or (2) in medical
applications or used on humans. Should any Product(s) be used in or with any nuclear installation or
activity, medical application, used on humans, or misused in any way, OMEGA assumes no responsibility
as set forth in our basic WARRANTY/ DISCLAIMER language, and, additionally, purchaser will indemnify
OMEGA and hold OMEGA harmless from any liability or damage whatsoever arising out of the use of the
Product(s) in such a manner.
RETURN REQUESTS/INQUIRIES
Direct all warranty and repair requests/inquiries to the OMEGA Customer Service Department. BEFORE
RETURNING ANY PRODUCT(S) TO OMEGA, PURCHASER MUST OBTAIN AN AUTHORIZED RETURN
(AR) NUMBER FROM OMEGA’S CUSTOMER SERVICE DEPARTMENT (IN ORDER TO AVOID
PROCESSING DELAYS). The assigned AR number should then be marked on the outside of the return
package and on any correspondence.
The purchaser is responsible for shipping charges, freight, insurance and proper packaging to prevent
breakage in transit.
FOR WARRANTY RETURNS, please have the
following information available BEFORE
contacting OMEGA:
1. Purchase Order number under which the product
was PURCHASED,
2. Model and serial number of the product under
warranty, and
3. Repair instructions and/or specific problems
relative to the product.
FOR NON-WARRANTY REPAIRS,
consult OMEGA
for current repair charges. Have the following
information available BEFORE contacting OMEGA:
1. Purchase Order number to cover the COST
of the repair,
2. Model and serial number of the product, and
3. Repair instructions and/or specific problems
relative to the product.
OMEGA’s policy is to make running changes, not model changes, whenever an improvement is possible. This affords
our customers the latest in technology and engineering.
OMEGA is a registered trademark of OMEGA ENGINEERING, INC.
© Copyright 2009 OMEGA ENGINEERING, INC. All rights reserved. This document may not be copied, photocopied,
reproduced, translated, or reduced to any electronic medium or machine-readable form, in whole or in part, without the
prior written consent of OMEGA ENGINEERING, INC.

M4758/0109
OME0872-04-EN
Where Do I Find Everything I Need for
Process Measurement and Control?
OMEGA…Of Course!
Shop online at omega.com
sm
TEMPERATURE
䡺⻬ Thermocouple, RTD & Thermistor Probes, Connectors, Panels & Assemblies
䡺⻬ Wire: Thermocouple, RTD & Thermistor
䡺⻬ Calibrators & Ice Point References
䡺⻬ Recorders, Controllers & Process Monitors
䡺⻬ Infrared Pyrometers
PRESSURE, STRAIN AND FORCE
䡺⻬ Transducers & Strain Gages
䡺⻬ Load Cells & Pressure Gages
䡺⻬ Displacement Transducers
䡺⻬ Instrumentation & Accessories
FLOW/LEVEL
䡺⻬ Rotameters, Gas Mass Flowmeters & Flow Computers
䡺⻬ Air Velocity Indicators
䡺⻬ Turbine/Paddlewheel Systems
䡺⻬ Totalizers & Batch Controllers
pH/CONDUCTIVITY
䡺⻬ pH Electrodes, Testers & Accessories
䡺⻬ Benchtop/Laboratory Meters
䡺⻬ Controllers, Calibrators, Simulators & Pumps
䡺⻬ Industrial pH & Conductivity Equipment
DATA ACQUISITION
䡺⻬ Data Acquisition & Engineering Software
䡺⻬ Communications-Based Acquisition Systems
䡺⻬ Plug-in Cards for Apple, IBM & Compatibles
䡺⻬ Data Logging Systems
䡺⻬ Recorders, Printers & Plotters
HEATERS
䡺⻬ Heating Cable
䡺⻬ Cartridge & Strip Heaters
䡺⻬ Immersion & Band Heaters
䡺⻬ Flexible Heaters
䡺⻬ Laboratory Heaters
ENVIRONMENTAL
MONITORING AND CONTROL
䡺⻬ Metering & Control Instrumentation
䡺⻬ Refractometers
䡺⻬ Pumps & Tubing
䡺⻬ Air, Soil & Water Monitors
䡺⻬ Industrial Water & Wastewater Treatment
䡺⻬ pH, Conductivity & Dissolved Oxygen Instruments
This manual suits for next models
1
Other Omega Switch manuals
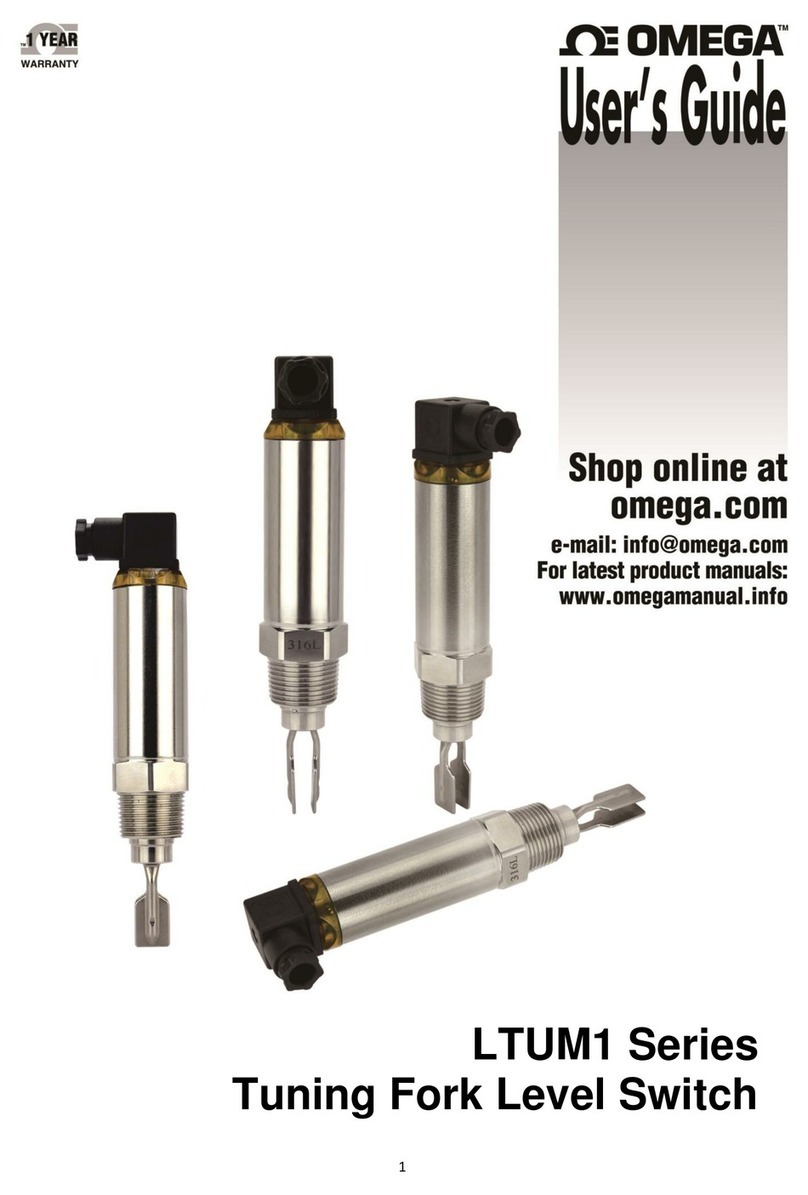
Omega
Omega LTUM1 Series User manual
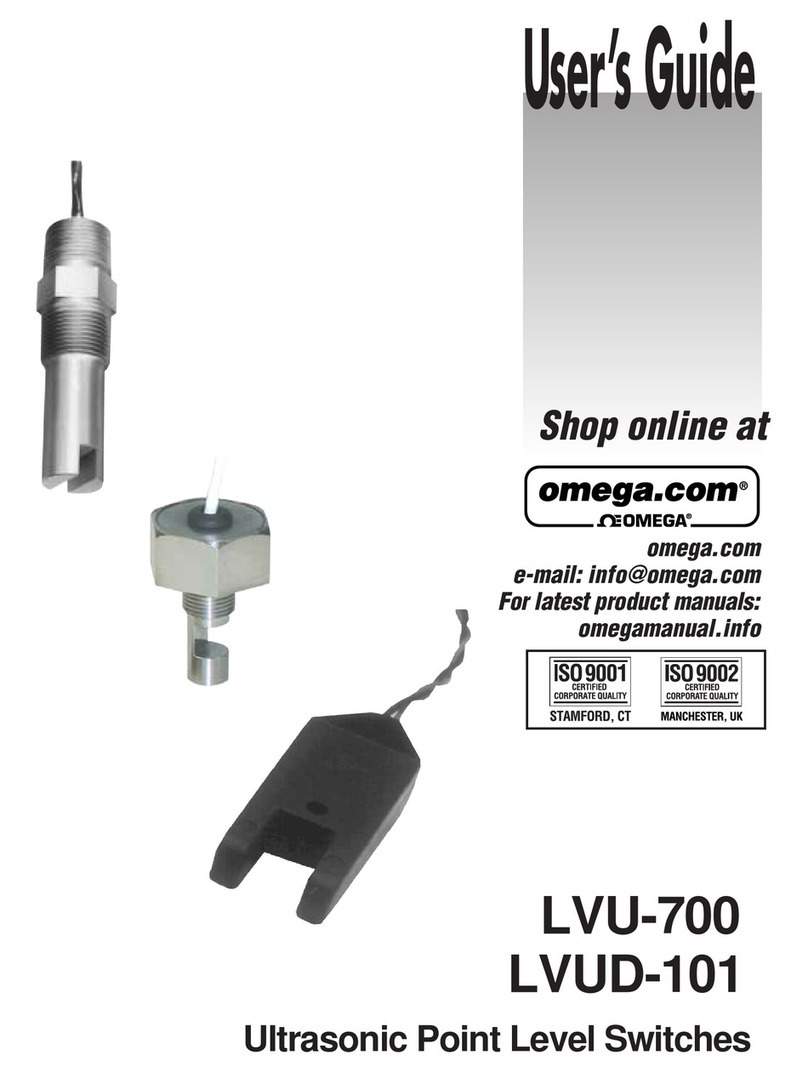
Omega
Omega LVU-700 User manual

Omega
Omega OM-ESW-105-POE User manual
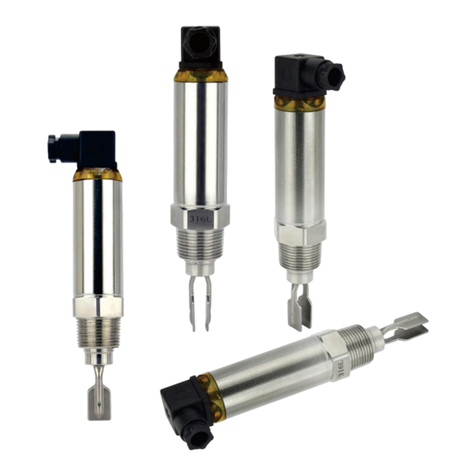
Omega
Omega TF280-N User manual
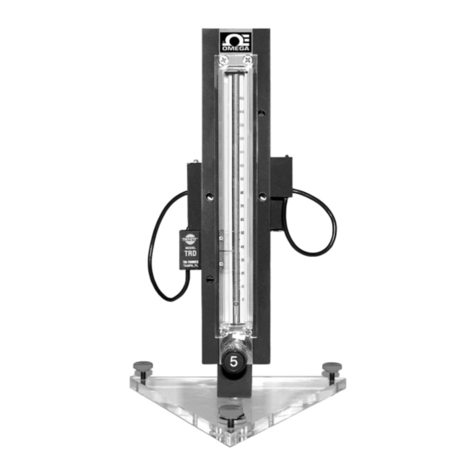
Omega
Omega FLSW3400 Series User manual

Omega
Omega OM-ESW-105-POE User manual
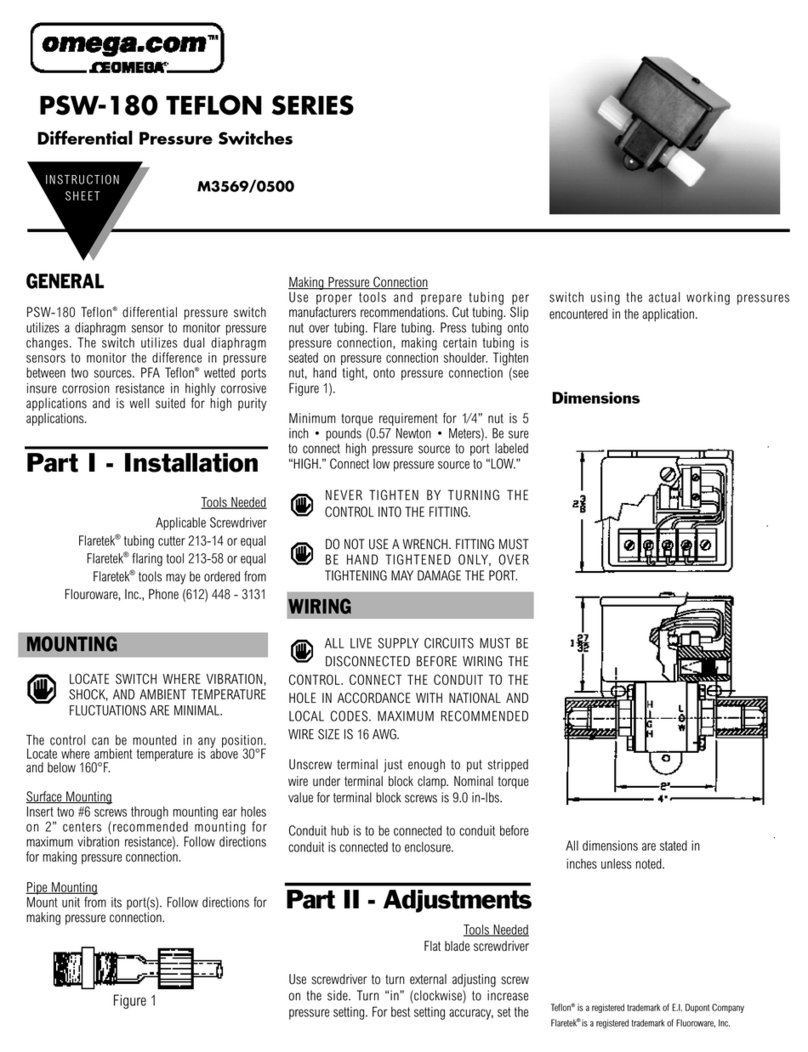
Omega
Omega TEFLON PSW-180 User manual
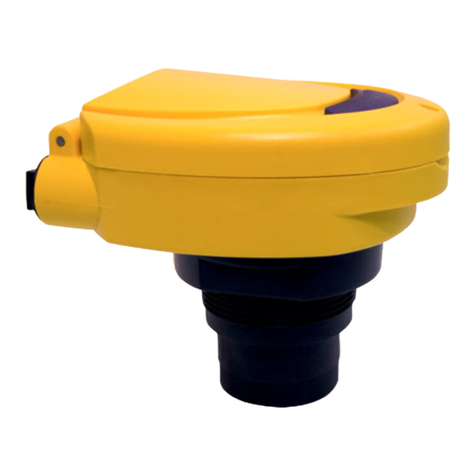
Omega
Omega LVCN700 Series User manual
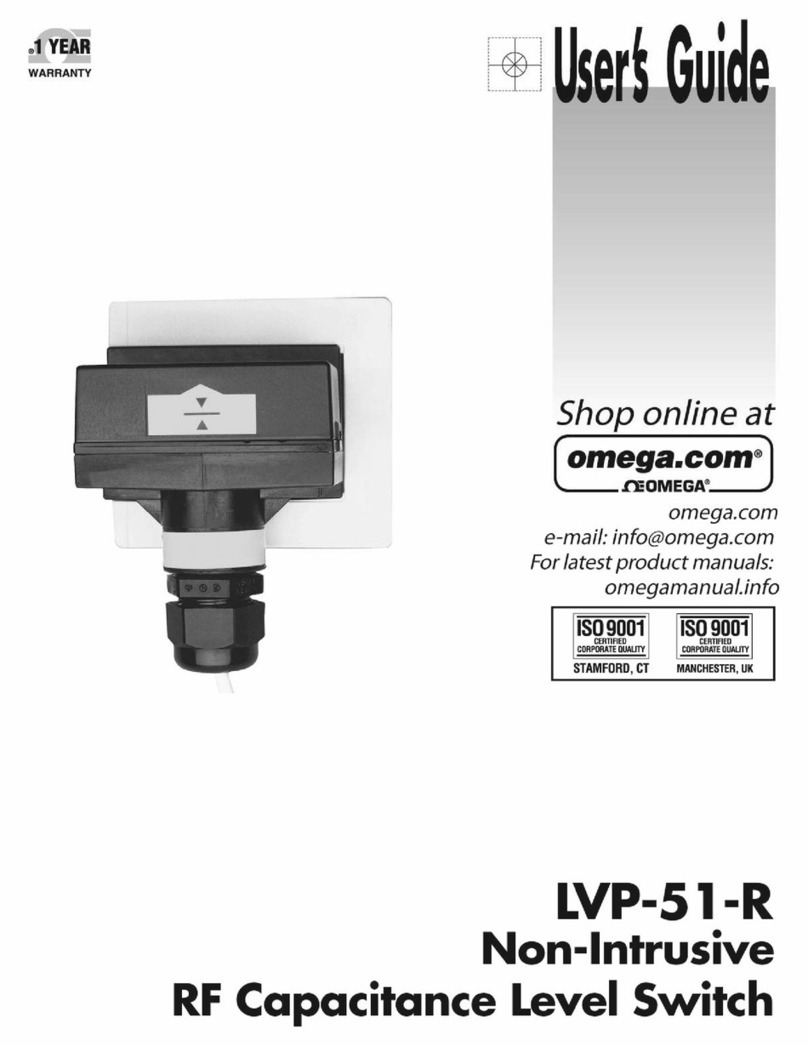
Omega
Omega LVP-51-R User manual

Omega
Omega LVF-210A Series User manual