Onan MDJA User manual

Service
Manual
MDJA
MDJB
MDJC
MDJE
MDJF
MarineDiesel
GenSet
Engines
974-0750
12-85
Printed
in
USA

Safety
Precautions
Itis recommendedthatyou readyour engine manualand be-
come thoroughlyacquaintedwith your equipment beforeyou
startthe engine.
[awnR"cl
This symbol is used throughout this
manual to warn
of
possibleseriouspersonalinjury.
-1
This symbol refers
to
possible equip-
mentdamage.
Fuels,electricalequipment,batteries,exhaustgasesandmov-
ingpartspresentpotentialhazardsthatcould resultinserious,
personalinjury.Takecareinfollowingtheserecommendedpro-
cedures.
Safety Codes
All
local, stateandfederalcodesshouldbeconsultedand
compliedwith.
Thisengineisnotdesignedor intendedforuse inaircraft.
Any such use is at theowner's sole risk.
General
Provideappropriatefire extinguishersand installthem in
convenientlocations. Usean extinguisherratedABC by
N
FPA.
Makesurethatallfastenersontheenginearesecureand
accurately torqued. Keep guards in position over fans,
drivingbelts, etc.
If
it
isnecessaryto makeadjustmentswhiletheengineis
running, useextremecautionwhenclose
to
hotexhausts,
movingparts, etc.
ProtectAgainst Moving Parts
0
Do
notwear looseclothinginthevicinityof movingparts,
such as PTO shafts, flywheels, blowers, couplings,fans,
belts,etc.
Keepyour handsaway from movingparts.
Batteries
Beforestartingwork ontheengine, disconnect batteries
to
preventinadvertentstartingof theengine.
DONOTSMOKEwhileservicingbatteries.Leadacidbat-
teriesgive
off
a highlyexplosivehydrogengaswhichcan
be ignitedby flame, electrical arcingor by smoking.
0
Verify battery polarity before connecting battery cables.
Connectnegativecable last.
FuelSystem
DO
NOT
fill
fueltanks while engine isrunning.
DO
NOTsmokeor usean openflame inthevicinityof the
engine or fueltank. Internalcombustionenginefuels are
highlyflammable.
Fuel lines must be of steel piping, adequately secured,
and freefrom leaks. Pipingat the engine should be ap-
provedflexible line.
Do
not usecopper pipingforflexible
lines as copper will work harden and become brittle
enoughto break.
Besure allfuelsupplies have
a
positive
shutoff
valve.
#
ExhaustSystem
0
Exhaustproductsof any internalcombustion engine are
toxic andcan causeinjury, or deathif inhaled.Allengine
applications, especially those within a confined area,
shouldbeequippedwithan exhaustsystem
to
discharge
gasesto the outsideatmosphere.
0
DO
NOT use exhaustgasesto heat
a
compartment.
0
Makesurethatyour exhaustsystemisfreeof leaks. En-
sure that exhaust manifolds are secure and are not
warpedby bolts unevenlytorqued.
ExhaustGas
Is
Deadly!
Exhaustgasescontaincarbonmonoxide,apoisonousgasthat
mightcause unconsciousnessanddeath. Itisan odorlessand
colorlessgas formed during combustionof hydrocarbonfuels.
Symptomsof carbon monoxidepoisoningare:
Dizziness
0
Vomiting
0
Headache
0
MuscularTwitching
0
Weaknessand Sleepiness
Ifyouexperienceany of thesesymptoms,get out intofreshair
immediately,shutdowntheunitanddonotuseuntilithasbeen
inspected.
The best protection against carbon monoxide inhalation is
properinstallationandregular,frequentinspectionsofthecom-
pleteexhaustsystem.
If
younoticeachangeinthesoundorap-
pearance of exhaust system, shut the unit down immediately
andhave
it
inspectedandrepairedatoncebyacompetentme-
chanic.
Cooling System
0
ThrobbinginTemples
0
Coolantsunderpressurehaveahigherboilingpointthan
water. DONOTopen a radiatorpressurecapwhen cool-
anttemperatureisabove
212
degreesF
(1
00
degrees C)
orwhile engine
is
running.
KeepThe UnitAndSurroundingArea Clean
0
Makesurethatoilyragsare notlefton
or
neartheengine.
Removeallunnecessarygreaseandoilfromtheunit.Ac-
cumulated grease and oil can cause overheating and
subsequentengine damage and presenta potentialfire
hazard.
Redistribution or publication of this document,
by any means, is strictly prohibited.

Table
of
Contents
TITLE
General Information
....................................................
2
Specifications
.........................................................
3
Dimensionsand Clearances
.............................................
4
Assembly Torques andSpecial
Tools
....................................
6
Serviceand Maintenance
...............................................
8
CoolingSystem
.......................................................
16
FuelSystem
..........................................................
36
GovernorSystem
.....................................................
60
EngineTroubleshooting
................................................
7
ExhaustSystem
.......................................................
14
OilSystem
...........................................................
62
StartingSystem
.......................................................
68
EngineDisassembly
...................................................
75
INCORRECT SERVICE
OR
REPLACEMENT
OF
PARTS MIGHT RESULT IN
SEVERE PERSONAL INJURY AND/OR EQUIPMENT DAMAGE
.
SERVICE
PERSONNELMUST BE QUALIFIEDTOPERFORMELECTRICALAND/OR
MECHANICALSERVICE
.
.
1
Redistribution or publication of this document,
by any means, is strictly prohibited.

General Information
INTRODUCTION
Thismanualdealswithspecificmechanicalandelec-
trical information needed by engine mechanics for
troubleshooting,servicing, repairing,or overhauling
the engine.
Usethetableof contentsfor aquick referencetothe
separateenginesystem sections.
Use the separate Parts Catalogs available at the
dealerlevel,for parts identificationandfor establish-
ingtheir proper locationon assemblies.
The
TROUBLESHOOTlNG
GUlDE
provides
a
quick
referencefor locatingandcorrectingenginetrouble.
The illustrations and procedures presented in each
sectionapplyto theengineslistedonthecover.The
flywheel end of the engine isthe front end,
so
right
and left sidesare determined by viewing the engine
from the front.
The disassembly section contains major overhaul
procedures for step by step removal, disassembly,
inspection, repair and assembly of the engine
components.
Ifamajorrepairoranoverhaulisnecessary,acompe-
tent mechanicshould either do thejob or supervise
and checkthe work of the mechanicassignedtodo
thejob toensurethat alldimensions,clearancesand
torquevalues arewithin the specifiedtolerances.
Thewiringdiagramshowshowtheelectricalcompo-
nentsare interconnected.
Apartscatalog(availableatthedealerlevel)contains
detailed exploded views of each assembly and the
individualpiecepartnurnbersandtheirpropernames
for orderingreplacementparts.
Useonly GenuineOnan replacementpartstoensure
quality and the best possible repair and overhaul
results. When ordering parts, always use
the
com-
pleteModelandSpecnumber
in
additiontotheSerial
numbershownonthe nameplate.
ENGINEMODEL REFERENCE
Identifyyour model by referring to the MODEL and
SPEC (specification)
NO.
as shown on the unit
nameplate. Always use this number and the engine
serialnumberwhenmakingreferencetoyourengine.
HowtointerpretMODELandSPEC
NO.
ongenerator
set engines.
1.
2.
3.
4.
12.OiDJC
-
f
/
7
f
1
2
34
Factorycodefor generalidentificationpurposes.
SpecificTYPE, as follows.
R
-
REMOTE type. Electric starting. Optional
accessoryequipmentcan beconnectedfor
2
wire remotecontrol
of
startingand stopping
E
-
ELECTRIC starttype. Electricstarting at
the
plantonly.
Factory code for specific optional equipment
supplied.
Specification (Spec Letter). Advances with fac-
tory productionmodifications.
2
Redistribution or publication of this document,
by any means, is strictly prohibited.

Specifications
All
dimensionsin
U.S.
customary units
of
measure(metric in parentheses) unless otherwisespecified.
~~
UNIT
OF
SPECIFICATION MEASURE MDJA MDJB MDJC MDJE MDJF
Numberof Cylinders
1
2
4
2
4
DieselFuel ASTM2-D ASTM2-D ASTM2-D ASTM2-D ASTM2-D
Bore in 3.25 3.25 3.25 3.50 3.50
(mm) (82.55) (82.55) (82.55) (88.9) (88.9)
Stroke
in
3.625 3.625 3.625 3.625 3.625
(mm)
(92.07) (92.07) (92.07) (92.07) (92.07)
Displacement cu in 30 60 120 70
140
litre
(0.5)
(0.98) (1-9)
(1
-2) (2.3)
CompressionRatio 19to
1
19
to
1 19to1 19to1 19to1
Firing Order 1-2-4-3 1-2-4-3
CrankshaftRotation
Governor VariableSpeed Mechanical Variable Speed Mechanical
Valve Clearance(Cold)
Spec
A-C
Begin
Spec
D
*
Intake in 0.020 0.010 0.01
5
0.01
1 0.017 0.017
(mm)
(0.51)
(0.25) (0.38) (0.28)
(0.43)
(0.43)
Exhaust
in
0.020
0.010
0.01
3
0.01
6 0.017 0.017
(mm)
(0.51)
(0.25) (0.33) (0.41)
(0.43)
(0.43j
.
OilFilter Full
Flow
FullFlow FullFlow Full Flow FullFlow
CrankcaseCapacity qt
3
3.5
.
6.5 3.5 6.5
(viewedfromflywheel) Clockwise Clockwise Clockwise Clockwise Clockwise
with filter change (I
i
tre) (2.8) (3.3) (6.2) (3.3) (6.2)
3
Redistribution or publication of this document,
by any means, is strictly prohibited.

Dimensions and Clearances
All
clearances given
at
room temperature
of
70°F
(21
"C)
.
All
dimensions
in
inches (millimeters
in
parentheses)unless otherwise specified
.
CAMSHAFT
BearingJournal Diameter. Front
.............................................
2.2500-2.2505(57.150-57.163)
BearingJournal Diameter.Center
(4
cylinder)
.................................
1.2580-1.2582(31-953-31.958)
BearingJournal Diameter. Rear
.............................................
1.1
875-1.1880(30.163-30.175)
BearingClearanceLimit(Original)
..................................................
.0015-.0030 (-038-.076)
BearingClearanceLimit(Replacement)
.............................................
.0012.. 0049 (.030-.123)
End Play
..............................................................................
.007.. 039 (0.2-1.0)
Cam Tappet Diameter(Priorto Spec P)
.........................................
.7475.7480 (18.987-18.999)
CamTappet Hole Diameter(Priorto Spec P)
...................................
.7507.. 7515 (19.068-19.088)
Cam Tappet Diameter(BeginSpec
P)
..........................................
.8725.. 8730 (22.162-22.174)
Cam Tappet HoleDiameter (EeginSpec P)
.....................
:
...............
.8755.. 8765 (22.238-22.263)
Large BoreDiameter
.....................................................
2.1 871-2.1876 (55.5523-55.5650)
Small Bore Diameter
........................................................
1.043-1.045(26.4922-26.543)
LargeBearingBoreto Small BearingBore
(Center-to-Center)
.....................................................
5.998-6.002
(1
52.3492-152.4508)
ConnectingRod End Play
.............................................................
.002.. 016 (.05-.41)
Bore Honed Diameter(MDJA. MDJB. MDJC)
.................................
3.2495-3.2505(82.537-82.563)
Bore Honed Diameter(MDJE. MDJF)
........................................
3.4995-3.5005(88.887-88.913)
MaximumAllowableTaper
.................................................................
0.005
(0.127)
MaximumAllowableOut-of-Round
..........................................................
0.001 (0.025)
Main BearingJournal Diameter
(1
&
2
cylinder)
.................................
2.2437-2.2445(56.99-57.01)
Main BearingJournal Diameter
(4
cylinder)...................................
2.2427-2.2435(56.965-56.985)
Center Main BearingClearance
(4
cylinder)
.........................................
.0024.. 0052 (.061-.132)
Frontand Rear MainBearingClearance(Original)
(4
cylinder)
.........................
.0030.. 0043 (.076-.109)
Main BearingClearance(Original)
(1
&
2
cylinder)
....................................
.002.. 0033 (.051-.084)
ConnectingRodJournalDiameter
...........................................
2.0597-2.0605(52.316-52.337)
Rod
BearingClearance
............................................................
.001.. 0033(.025-.084)
EndPlay
...........................................................................
.010.. 015 (.254-.381)
CONNECTING
RODS
CY
Ll
NDER
CRANKSHAFT
Frontand Rear MainBearingClearance(Replacement)
(4
cylinder)
......................
.0024-.0062(.06-.16)
Main BearingClearance(Replacement)
(1
&
2
cylinder)
.................................
.0014-.0052 (.04-.13)
PISTONSAND
RINGS
ClearanceinCylinder
Measure
90'
to pin.just below oil ring
RingGrooveWidth
(Priorto Spec
P).
...............................................................
.0050..
0070 (.127-.178)
(BeginSpec
P)
.................................................................
.0055-.
0075(.140-.191)
TOP
.........................................................................
.0970.. 0980 (2.464-2.489)
NO
.
2
........................................................................
.0965.. 0975 (2.451-2.477)
NO
.
3
........................................................................
.0965-.0975 (2.451-2.477)
NO
.
4
........................................................................
.1880.. 1897(4.775-4.818)
RingGap
............................................................................
.010.. 020
(.25-51)
Clearancein Piston
.....................................................................
Thumb-push Fit
ConnectingRod BushingClearance
................................................
.0002.. 0007 (.005-.018)
Rotation
.............................................................................
Counterclockwise
PinionClearance
to
PinionStop(SolenoidPlungerBottomed)
...........................
.070.. 120(1.78-3.05)
Armature End Play
..................................................................
.005..
030(.030-.760)
PISTONPIN
STARTING
MOTOR
(prestolite)
4
Redistribution or publication of this document,
by any means, is strictly prohibited.

.
VALVE-INTAKE
Stem Diameter(Stemistapered)
Center
..
..
..
.
..
..
.
.
.
.
.
.
.
.
.
.
.
.
.
..
.
...
...
.
.
.
.
.
.
..
.
.
.
..
..
..
.
.
..
.
.
.
.
.
..
.
.
.
....
.
-3401-.3411 (8.639-8.664)
**Face.
.
.
..
.
.
..
..
..
.
.
.
.
.
.
.
.
.
.
.
.
.
.
...
.
.
.
.
.
.
..
.
.
.
.
..
..
...
.
.
..
.
.
.
.
.
.
.
.
.
.
.
.
.
..
.
.
.
.3386-.3396(8.601-8.626)
Valve Face..
..
..
.
.
..
.
.
.
.
.
.
.
.
.
.
.
.
..
.
.
.
..
.
.
..
.
...
.
.
.
.
.......
.
..
.
...
.
.
..
.
.
..
.
.
.
..
.
..
.
...
..
.
.
.
..
.
.
.
..
42"
GuideClearance
.
...
.
.
.
.
.
..
..
.
.
.
.
.
.
.
..
..
.
.
.
..
..
.
.
.
.
.
.
.
....
.
..
.
..
..
.
.
.
.
.
..
.
.
.
.
.
.
.
.0015-.003(.038-.076)
Stem
D
iameter .
.
.
..
.
.
..
.
.
..
.
.
.
..
.
.
.
.
.
.
.
.
.
.
.
..
.
.
.
.
.
..
.
.
.
.
.
.
.
..
.
.....
.
.
.
.
.
.
.
.
.
.
.3405-.3415(8.649-8.674)
GuideClearance
.
.
.
..
.
..
.
..
..
.
...
.
.
.
..
.
.
.
..
..
.
..
.
.
..
.
.
.
..
..
.
.
.
.
.
..
.
.
.
.
.
.
.
.
.
.
.
.
.
-0030-.0050(.076-.127)
Valve Face
.......................................................................................
45"
Length .
.
.
..
.
.
.
.
.
.
.
...
..
.
.
.
..
.
.
.
.
.
..
.
.
.
.
.
.
.
.
.....
.
...
.
.......
.
...
.
.
.
...
.
.
.
..
.
.
.
..
.
.
.
.
1.781 2 (45.2424)
OutsideDiameter
.
.
.
.
.
.
.
..
.
..
.
.
.
..
.
.
.
.
.
.
.
.
.
.
.
.
..
..
.
..
..
.
..
.
..
.
.
...
.
.
.
.
.
.
.4690-.4695(11.91 26-11.9253)
InsideDiameter(after reaming)
Exhaust ..
..
.
.
.
.
..
.
.
.
......
.
.
.
.
.
.
.
.
.
.
..
.
.
..
.
.
.
..
.
.....
.
..
.
.
.
.
..
.
.
.
.
.
..
..
.
.
.
.3445-.3455(8.750-8.776)
Intake
.
.
.
.
...
..
.
.
.
.
.
.
..
..
..
.
...
.
...
.
.
..
.
.
....
.
.
..
..
.
.
.
..
..
.
.
.
..
..
.
.
..
.
.
.
.
.
.
.3425--3435(8.700-8.725)
Cylinder Block Bore Diameter..
.
.
..
..
.
.
,
.
.
.
.
.
.
..
.
.
..
.
.
.
.
...
.
.
.
.
.
.
.
..
.
.
.
..
.
.
.
.467-.468(11.8618-11.8872)
Valve Seat Bore(Diameter)
VALVE-EXH AUST
VALVE GUIDE
VALVE SEATS
Intake
.
..
.
.
..
..
.
.
.
.
.
.
..
.
..
.
.
.
.
..
.
..
.
.
.
.
.
.
...
..
.
.
....
..
.
.
...
.
.
..
..
.
.
.
.
.
..
.
.
1
S47-.1.548(39.29-39.32)
Exhaust .
..
.
.
.
.
.
..
.
.
.
.
.
.
.
.
..
.
.
..
.
.
.
..
.
.
.
.
.
..
..
.
..
..
.
.
.
.
....
.
.
.
.
.
.
.
.
..
.
..
.
1.361-1.362(34.570-34.595)
Depth(fromCylinderHead Face) .
..
.
.
..
.
.
..
.
.
.
.
.
..
.
.
.
.
.
.
.
.
..
.
.
.
...
.
.
.
..
.
.
.
.
.
.
.
43--439(10.99-11.15)
Exhaust
.
..
.
.
.
..
.
..
.
.
..
..
.
.
.
..
.
.
.
.
..
..
.
.
.
.
.
..
..
.
..
.
.
.
..
.
.
.
.
....
.
.
..
...
.
1.364-1.365(34.6456-34.6710)
Intake
.
.
..
.
..
.
.
.
.
.
.
.
..
.
.
.
.
..
.
.
..
..:.
.
.
.
.
..
.
.
..
.
.
.
.
.
.
..
.
.
...
.
.
.
..
.
.
.
.
..
..
.
.
.
1
-550-1-551(39.37-39.39)
Seat Width..
.
.
.
.
.
.
.
..
.
.
.
.
..
.
..
.
.
.
.
..
.
.
.
..
.
.
.
.
...
.
..
..
.
..
.
.
..
..
.
.
..
.
.
..
.
...
.
.
....
.
.047-.062(1.19-1.57)
Angle
.............................................................................................
45"
Available InsertOversizes....
..
.
.
.
....
.
.
..
.
.
.
..
.
.
...
..
.
.
.
..
.
....
.
.
.
.
.
..
.
.
..
.
.
.
..
.
.
...
.
..
..
.
,002(.0508)
.005
(.127)
-010
(.254)
.025(.635)
Load-Valve Closed
.
..
.
..
..
.
.
.
..
..
..
.
.
.
.
..
.
.
.
.
.
..
..
.
.
.
.
.
.
.
.
....
.
..
.
.
..
.
.
.
.
.
.
.
.
,
.
45-49
Ib
(200-218
N*)
Load-Valve Open (Prior toSpec P) .
..
..
.
..
.
.
.
.
..
.
..
.
..
.
.
...
..
.
....
.
.
...
.
.
.
.
.
.
.
.
.
83-93
Ib
(369-414
N*)
Load-Valve Open (BeginSpec P). ...
.
.
..
.
.
.
...
.
.
.
.
.
.
.
.
..
.
.
.
...
.
.
.
.
..
.
.
.
.
.
.
.
...
.
.
87-97
Ib
(388-432
N*)
Seat Outside Diameter
VALVE
SPRINGS
'Newton
-
Base unit
of
force.
"Measure intakevalve
stem
at
points
indicated.
Valve Stem Diameter
(intake)
(75.2
mm)
1.18
IN
(30.0
mm)
5
Redistribution or publication of this document,
by any means, is strictly prohibited.

Assembly Torques
and
Special Tools
The assembly torques given herewill assureproper
tightness without danger of stripping threads. If a
torquewrenchisnotavailable,estimatethedegreeof
tightness necessary
for
the stud, nut, or screw. Be
carefulnottostripthreads.Useonly reasonableforce
and awrench of normallength.
Speciallydesignedplaceboltsdo notrequirea lock-
washer orgasket.
Do
notattempttouse
a
lockwasher
withthesebolts;itwill defeattheir purpose.Checkall
studs, nuts, andscrewsoften andtightenas needed
to keep them from working loose.
SPECIAL
TOOLS
Thesetoolsare availablefrom Onanto aidserviceand
repairwork.
DieselNozzleTester
.
.
.
.
.
.
.
.....
.
.
..
.
..
.
.420-0184
DieselPintleNozzleCleaning
Tool
Set
(includesinjectionnozzle
centeringtool) .
..
.
.
..
....
.
.
..
.
..
..
.
.
.
.
.420-0208
Driver, Center CamshaftBearing
(RDJFonly) .
..
.
.
.
.
.
.
.
.
..
..
..
.
..
..
.
...
.420-0254
Driver,Valve Seat .
.
.
.
.
.
.
.
..
.
.
.
...
.
.
.
...
.
.420-0270
OilSeal Guide and Driver.. ..
...
...
.
.
.
.
,
.
.420-0456
Nozzle Centering Sleeve. .
.
...
.
....
.
.
.
.
.
.
.420-0321
DeliveryValve Test Fixture..
.
.
..
.
.
.
.
.
..
.
.
.420-0322
Combination Mainand Cam
Bearing Driver......
.
.
..
.
.
.
...
.
.
..
.
..
.
.420-0326
DieselCompressionTester .....
.
.
.
.
.
.
.
.
.
.420-0283
Valve SpringCompressor Tool
.
.
.
..
.
.
.
..
.
.420-0119
Valve Seat Remover.
..
.
.
.
.
.
.
...
.
.
.
.
.
.
..
.
.420-0311
RECESS
UNDER
HEAD
A749
TORQUE
SPECIFICATIONS Ft.-Lb.
Nom
Center mainbolt
(4
cylinder) ...
97-102 (131-138)
Connectingrod bolt.. ..
..
.
.
.
..
.
27-29 (37-39)
Rocker-Box cover.
.
.
.
..
..
.
..
..
.
8-1
0
(1
1-1
4)
Cylinderhead bolt
..
.
.
.
..
.
..
.
.
.
44-46 (60-62)
Exhaust manifoldnuts..
.
.
.
.
..
.
.
13-15* (18-20)
Flywheelmountingscrew.. .
.
.
.
.
65-70 (88-95)
Fuelpump mountingscrews
.
.
.
.
15-20 (20-27)
Gear case cover
.
..
.
.
..
.
.
..
.
.
.
.
18-20 (24-27)
Injection nozzle mounting
screws .
.
..
.
..
.
...
.
..
..
..
.
.
.
.
20-21 (27-28)
Injectionpumpmounting
screws .
.
..
.
.
.
..
.
.
.
..
.
.
..
.
.
.
.
15-1
6 (20-22)
Intakemanifold.
.
.
.
.
..
.
..
..
.
.
.
.
13-15 (18-20)
Oil base mountingscrews ..
.
...
45-50 (61-68)
Oilfilter
..
.
.
.
.
..
..
. Handtight plus
114
to
1/2
turn
Oil
pump mountingscrews .
.
.
.
.
15-20
(20-27)
Rear bearingplate .
.
..
.
...
.
.
.
..
40-45 (54-61)
Rockerarm nut .....
..
..
.
.
.
.
..
.
4-lo** (5-13)
Rockerarmstud .
.
..
.
.
.
..
.
.
.
..
.
35-40 (48-54)
Glowplug .
.
..
..
.
...
.
.
.
.
.
.
.
..
.
.
10-15 (18-20)
-
Exhaust nutsmust betightened evenly.
FlywheelPuller
.
..
..
....
.
.
.
..
..
.
.
.
..
.
..
.
.420-0100
Crankshaft Gear Puller
.
.
.
.
.
.
...
.
..
.
.
.
...
.420-0072
Crankshaft Gear PullingRing .
.
.
.
.
.
.
.
.
.
.
.420-0248
Tool
Catalog
.
..
.
.
...
.
.
.
....
.
..
.
.
..
.
.
.
.
.
.900-0019
*'
-This torque
is
dueto friction betwenthethreads only and
locksthenuts
in
place. Usethe rockerarmnut
to
adjustvalve
lash.
Redistribution or publication of this document,
by any means, is strictly prohibited.

Service and Maintenance
PRE-STARTING
Preparationsforthe initial andeachadditionalstart-
ingoperationshouldincludecarefulchecksoftheoil,
fuel, cooling, and electricalsystems.
Beforeengine is put inoperation, check all compo-
nentsfor mechanicalsecurity. Ifanabnormalcondi-
tion, defectivepart,oroperatingdifficultyisdetected,
repair or serviceas required.The engine should be
keptfree of dust, dirt, and spilled oil or fuel. Besure
properoperating procedureis followed.
Crankcase
Oil
Multi-gradeoils (such as 5W-30) are recommended
for service in ambient temperatures of 32OF and
colder. OnOnan
J
Dieselliquidcooledengines,
SAE
15W-40or20W-40 oils (CD/SEServiceDesignation)
maybeused
in
anambienttemperaturerangeof
15OF
(-10°C)
through
90°F
(32OC). Refer to the oil chart
belowfor recommendedviscosity grades at various
temperatureambients.
Useoilwithan
API
classificationofCD/SE (allviscos-
ity grades) or
CC/SE
(grades
1OW-30,
1OW-40,
or
5W-30
only).
When addingoilbetweenoilchanges,
it
ispreferable
to usethesame brand, as various brandsof oil may
not be compatible. Refer
to
MaintenanceSchedule
for recommended
oil
change intervals and pro-
cedures.
Crankcasepressure couldblow out
hot
oll
and causeseflous,burns.
Do
NOT
check oil while the engine
is
operating.
Recommended
Fuel
Use
ASTM
2-D or 1-D fuel with a minimum Cetane
number of
45*.
Number2 diesel fuel gives the best
economy for most operating conditions; however,
use
ASTM
1-D
fuel during the following conditions:
1.
When ambient temperatures are below 32"
F
2. During long periods of light engine load; or no
(OOC);
load.
*NOTE
FuelswithCetanenumbershigherthan45maybeneeded
inhigher altitudes or when extremely low ambient temperatures
are encounteredto preventmisfires.
Use low sulfur content fuel having a pour point
(ability to filter) of at least
10°F
below the lowest
expectedtemperature. Keep thefuel clean and pro-
tected from adverse weather. Leave some room for
expansionwhen filling the fuel tank.
Duetotheprecisetolerancesofdie-
sel injectionsystems,it
is
extremely
important the fuel be kept clean.
Dirt
in the system
cancausesevere damage to both theinjectionpump
and the injectionnozzles.
WORK TRANSFERPUMP
PRIMINGLEVER UNTIL
FUEL FLOWS FROM
RETURN
LINEFITTING
OF INJECTION
PUMP.
FIGURE
1.
BLEED
FUEL
SYSTEM
If
the camshaft pumplobeisup, crank engine one revolution
to
permithandpriming.When finished, returnpriming leverinward
(disengaged position)
to
permitnormalpumpoperation.
8
Redistribution or publication of this document,
by any means, is strictly prohibited.

Bleeding
Fuel
System
Bleedairfromfuelsystemasfollows: Disconnectfuel
return
line,
Figure
1.
Operatehandpriming lever on
fueltransfer pumpuntilfuelflowingfrom fuel return
line is free of air bubbles. Then reconnect the fuel
returnline.
Preheating for
60
seconds
is
recommended on all
DJ-Series Diesels at 55°F
(13°C)
or lower, and
30
seconds
for
temperaturesabove
55°F
(13OC).
Refer
to
Onan
Diesel
Starting
Guide,
foradditionalstarting
guidelines. Inhalation of exhaust gases might
result in seriouspersonal injury or
death. Be sure deadly exhaustgas
is
piped outside
and away from windows, doors, or other inlets to
building. Use of ether as a sfarfing aidmight
i
cause an explosion resulting in
severe personal injury and engine damage.
Do
not
use ether as a starting aid; heat or compressionor
heat
from
theglowplugsmaycauseasuddenignition
of theether vapor.
1.
Engage PREHEAT switch for the time period
4
PRE-HEATING AND STARTING
b
p
WnRNlNGI
recommendedbelow:
30
seconds if above
55"
F
(13"C)
-
60
seconds if below
55°F
(13°C).
2.
EngageSTARTswitchwhilecontinuing preheat.
3.
If engine fails to start in
15-20
seconds, repeat
Hold
untilenginecomes upto speed.
To
START
4.
5.
1,
n
PREHEATCOLDENGINEPUSH PREHEATSWITCHAND HOLD-
*
30
SECONDS IFABOVE
55OF
(13°C);
60
SECONDS
IF
BELOW
55OF
(13'C).
NEVER PREHEATMORE THAN
60
SECONDS.
steps
1
&
2.
Absence
of
blue
exhaust
smoke
dur-
ing cranking indicates
no
fuel being delivered.
Determinecause.
In
extremecold
it
may
benecessarytomaintain
preheatingupto
2
minutesaftertheenginestarts
to obtain firing
or
to smooth
out
all cylinders,
especiallyat no load
or
light loads.
Do
not
exceed the one minute
preheatperiodstoprevent heat-
er burn
out
and conserve the battery. Longer
preheatingtimeprior
to
crankingtheenginecan
ruinthemanifoldheaterandglowplugsbecause
fhere
is
no
incomingair flow
io
coolthem. Addi-
tional operation
of
the preheaters for a few
seconds during cranking in cold weather may
help
to
preheattheincomingcombustionairand
preventmisfiresas theengine
starts
running.
Verifythatoilpressuregaugereadsatleast
20
psi
afterenginereachesspeed (pressurereliefvalve
is
notadjustable).
Do
not
applyovervoltage
to
the
starting circuit at any
time.
Overvoltagewill destroy theglow plugs and air
heater.
If
jt becomes necessary
to
use an addi-
tionalsourceof power
to
start the set, usea
72
voltbaffery connectedinparallel.
STOPPING
Pushfuel solenoidswitch40
Stop
position.
L.
Releaseswitchwhensetstops.
If
stopcircuitfails,
close fuel valve.
ONAN DIESELSTARTING GUIDE
-
INDUSTRIALENGINES
BEFORE
STARTING: CHECK FUEL SUPPLY.
BE SURE SHUTOFF VALVES ARE OPEN.
I
1
PRIMEFUELSYSTEMIFFUELFILTERSWEREDRAlNED
OR
CHANGED.
SYSTEM WAS JUST INSTALLED. FUEL TANK RAN
DRY.
1
1
i
1
-AIR HEATER
1
ELEMENT INMANIFOL
TO PRIMEFUEL
SYSTEM
MOVEPRIMINGLEVERUP JECTION NOZZLE
AND
DOWN UNTIL FUEL
FLOWS STEADILY
FROM
RETURN
LINE (DISCON- LOW PLUG
NECTED). INJECTIONPUMP
FUEL TRANSFER
PUMP
PRIMING
LEVER
-
FUEL FILTERS
FUEL RETURNLINE
-
I
~ ~~~
IFENGINEFIRESBUTDOESNOTSTART.REPEATABOVEPROCEDURES,INCLUDING
PREHEAT. LIMIT CRANKING TO
15
TO
20
SECONDS TO CONSERVEBATTERY. IF
r
ENGINESTILLDOESNOTSTART.SEEYFENGINEFAILS
TO
START"INFORMATION.
9
Redistribution or publication of this document,
by any means, is strictly prohibited.

IF
ENGINE
FAILS
TO START=
IMPORTANT!
KEEP ENTIREFUELSYSTEMCLEAN AND FREE
FROM
WATER
DIESEL INJECTIONPUMPS WILL FAIL
IF
SYSTEMCLEANLINESS
IS
NEGLECTED
INJECTION PUMPSAND NOZZLESARE NOT FIELD REPAIRABLE
TEMPERATURES BELOW
32
F
(0
C): USE NUMBER
1
DIESEL FUEL. USECORRECTVISCOSITY OIL.
KEEP BATTERIES FULLY CHARGED. DO NOT USE ETHER STARTING AID.
I
OBSERVE ENGINE EXHAUST”SM0KE SIGNALS”:
-
r
I
1
LUE-WHITEEXHAUST SMOKE LITTLE
OR
NO
EXHAUST
SMOKE
ENGINE
IS
NOT GETTING FUEL.
PRIMEFUELSYSTEM, OBSERVE FUELFLOW FROM RETURN LINE.
ENGINE
IS
GETTINGFUEL
CHECK PREHEATSYSTEM:
1.
OBSERVE AIR HEATER
THRU AIR INLET.
2.
ENGAGEPREHEAT.
3. IFHEATERELEMENTDOE:
NOT GLOW RED WITHIN
30
SECONDS. CHECK AIR
HEATERANDGLOW PLUG
WIRING.
CONNECTIONSTIGHT?
FREEFROMCORROSION?
~
8-79
98-4006
I
FUELFLOWS STEADILY
I
LITTLE OR NO FUEL FLOW
I
I
SOLENOID ROD SHOULD
PULLINAND THROTTLEARM
FOLLOW (AS SHOWN) WHEN
START SWITCH
IS
TURNED
ON. IFNOT. CHECK FOR
G LINKAGE
OR
BROKENWIRES
LENOID
ROD
THROTTLE
ARM
I
CHECK FUEL SUPPLY
SYSTEM:
FUEL TANK EMPTY?
SHUTOFF VALVES
FUEL LINESKINKED?
LOOSECONNECTIONS?
CLOGGED FUELFILTERS?
CLOSED?
1
I
I I
IFENGINE
IS
STILL NOT GETTINGFUEL. CHECK TRANSFER PUMP
1.
CRANK ENGINEAND OBSERVEFUELFLOW FROM RETURN LINE.
2.
IFFUEL DOES NOT SPURT OUT, PUMP
MAY
BEDEFECTIVE.
IFENGINESTILL DOES NOT START. CONTACTAUTHORIZED ONANSERVICEREPRESENTATIVE
AUTOMATIC STARTINGAND STOPPING
Optional controls may be used for automatic start
andstop, but mustprovideenginepreheating.
Theautomaticcontrolshouldhaveatimedelayrelay
to preheatglow plugsand the manifoldheater for at
least
20
seconds before cranking occurs. The time
delay relay prevents immediate engagementof the
starterincasetheloadisreappliedbeforetheengine
stops.
APPLYING LOAD
If practicable,allow engine to warm up beforecon-
nectingaheavyload.Continuousoverloadingcauses
high operating temperatures that can damage
the
engine.Theexhaustsystemmayformcarbondepos-
its during operation at light loads; apply full load
occasionally beforeshut-down to preventexcessive
carbonaccumulations.
Try to apply the load in steps insteadof full load at
onetime.
BREAK-IN
PROCEDURE
The unitshouldbe run inthefollowing sequence:
1.
One half hourat 112 load.
2. Onehalf hourat
3/4
load.
3.
Full load.
Continuousrunning under one half load during the
firstfew hundredhoursmay resultinpoorpistonring
seating,causinghigherthannormaloilconsumption
and blowby.
Drainandreplacethe crankcaseoilafter
first
50
hours
of
opera-
tion; drainwhiletheengine
is
still hot.
INSPECTION
Check for alignment of engine and load. Misalign-
mentwillcauseexcessivevibrationandbearingwear.
Makeavisual inspectionof the entire installation.
Contact with rofafing rnachlnery
mighf causeserious personal injury
or
death. Stay clear
of
rofafing componenfs and
ensurefhafprofecfiveshieldsandguardsareinplace
andsecured before operafing machinery.
10
Redistribution or publication of this document,
by any means, is strictly prohibited.

VENTlLATlON
Goodventilationis neededtocooltheengineandto
support combustion.
Avoid
recirculation
of ventilat-
ingair.
lnhalafion
of
exhausf gases might
i
resulf in seriouspersonal injury
or
death.
Do
not use exhaust heat to warm a
room,
compartmentor storagearea.
HOURS
OF
OPERATION
8
.
50
(moreoften
in
dusty
conditions)
100
200
500
600
2000
3000
5000
EXHAUST
Pipeexhaustgas outsideanyenclosure:exhaustgas
ispoisonous. Exhaustpipesmustnotterminatenear
inletvents. Avoidsharpbends. Usesweeping,large-
radius elbows. Use a section of seamless, flexible
tubing betweentheengineand any rigidpipetores-
trictvibration.
MAINTENANCETASK
Inspect exhaustsystem
Inspectengine
Checkfuel
supply,
seeNote
1
Check oil level. SeeFigure
2.
Check aircleaner.
Clean governor linkage
Changecrankcaseoil
Drain fuel condensationtraps
in
lines and filters,
seeNote
1
Replace oil
filter
Check battery condition
Clean breatherstandpipes
0
Check start-disconnectcircuit
Check valve clearances
Changeprimary fuel filter
Grind
valves
(if
required)
Clean holes
in
rocker box
Check nozzlespraypattern,
Changesecondaryfuel filter
General overhaul
(if
required)
oil line orifices
seeNote
2
see Note
3
BATTERIES
Check the condition
of
thestartingbatteriesat least
everytwoweeks. Seethatconnectionsarecleanand
tight.
A
light coating of non-conductive grease will
retardcorrosionatterminals.Keeptheelectrolyteat
the proper levelabove the platesby addingdistilled
water. Check specific gravity; recharge if below
1.260.
DUST AND DIRT
1.
Keep inletscreen free of dirt, etc.
2. Serviceair cleaneras frequentlyas necessary.
3.
Change crankcaseoil every
50
operating hours.
4.
Keep oilandfuel indust-tight containers.
5.
Keep governor linkageclean.
HIGH
ALTITUDE
Maximum power will be reduced approximately
4
percentfor each
1000
feet (310 m) abovesea level,
afterthe first 1000feet (310
m).
1.
2.
3.
4.
LOW TEMPERATURES
Use correct SAE
No.
oil for temperature condi-
tions.
Change
oil
onlywhen engine
is
warm. Ifan
unexpected temperature drop causes
an emer-
gency, moveenginetoawarm location or apply
heatedair (never useopenflame) externallyuntil
oil
flows
freely.
Usefreshfuel. Protectagainstmoistureconden-
sation.
.
Keep fuel system clean, and batteries in a well
chargedcondition.
Useadditionalpreheatcyclesduringcoldstarts.
Do
not exceed one minute preheat
periods; longerperiodscan
ruin
the
heater elements.
OPERATORAND SERVICEMAINTENANCESCHEDULE
NOTE
1.
Water orforeign material
in
fuel can
ruin
the injection
system.
If
daily inspection shows water
or
excessive
dirt
in
sedimentbowl fuel,handling and storingfacili-
ties should
be
checked and situationcorrected. Prirn-
ary and secondaryfuelfiltersmust
be
replaced follow-
ing
correction of fuel contamination problem.
2.
Thisservice
must
beconductedby traineddiesel injec-
tion equipment personnel with suitabletest facilities.
Omit thisserviceuntil these conditionscan be met.
3.
Tighten head boltsandadjustvalve clearanceafterfirst
50
hours on an overhauled engine.
'
11
Redistribution or publication of this document,
by any means, is strictly prohibited.

OIL FILTER CHANGE
Place pan under old filter and remove by turning
counterclockwise.Cleanfilter mountingarea. Lubri-
cate gasket on new filter with oil and screw filter on
clockwiseuntil gasket touches mountingbase, then
tighten
1/2
turn.
OIL DRAINEXTENSION
Forserviceconvenience,installashort(lessthan
10
inches
[254
mrn]) oil drain extension made from
standardpipeandfittings, inthe1/2-inch
(12.70
mm)
pipe-tapped
oil
drain'hole inthe base.
Crankcasepressure
could
blow
out
hot oil
and
causeserious burns.
Do
NOT
check
oil
while fhe engine
is
operating.
CRANKCASE
BREATHER
PIPE
INSERTA
SOFT
WIRE THROUGH
BREATHER PIPE
TO
CLEAN
BREATHER
SYSTEM
OIL LEVEL INDICATOR
FUEL
PUMP
FUEL TRANSFER
PUMP
BALL JOINT
DUAL FUEL FILTER SYSTEM
FIGURE
2.
MAINTENANCE PROCEDURES
12
Redistribution or publication of this document,
by any means, is strictly prohibited.

OUT-OF-SERVICE
PROTECTION
The natural lubricating qualities of
No.
2
dieselfuel
should protect
a
diesel engine for at.least 30-days
when unit isnotinservice. To protectan enginethat
will beout
of
service
for
morethan
30
days, proceed
as follows: Derature.
Returning
a
Unitto Service
1.
Remove cover and all protectivewrapping.
Re-
move
plug
from
exhaust
outlet.
2.
Checkwarningtagon oil baseandverifythat oil
viscosityis
still correct
for
existingambienttem-
1.
2.
3.
4.
5.
6.
7.
8.
Runengineuntilthoroughlywarm; underatleast
50
percentload.
Shut down engine and drain oil base while still
warm. Refilland attach awarning tag indicating
viscosityof oil used.
Removeglow plugs. Pourl-ounceof rustinhibi-
tor (or
SAE
#10 oil) into each cylinder. Install
Crank engine by hand only to
distributeoilincylinder.Starter
cranking
is
toofast;oilorinhibitor fluidwillfireif
crankedwithstarteratnormalroomtemperature.
Serviceair cleaner per
Maintenance
Schedule.
Cleanthrottle and governor linkageand protect
bywrappingwith acleancloth.
Plugexhaustoutletstoprevententranceofmois-
ture, bugs, dirt, etc.
Cleanandwipeentireunit.Coatpartssusceptible
torustwith alightcoatof greaseor oil.
Disconnect battery and follow standard battery
storageprocedure.
glow plugs.
3.
Clean and check battery.Measurespecific grav-
ity(1.260at
77OF
[25O
C])
andverifylevelisatsplit
ring.Ifspecificgravityis
low,
chargeuntilcorrect
value
is
obtained. If level
is
low, add distilled
waterandchargeuntilspecific gravity iscorrect.
DO
NOT
OVERCHARGE.
lgnifion
of
explosive battery
gases might causesevere per-
sonal
injury.
Do
notsmokewhileSeNiCingbatter-
ies.
4.
Checkthatfuel injectorsandfuellinesaresecure
and correctlytorqued.
5.
Cleanheatexchanger.
6.
Connectbatteries.
7.
Verifythat noloadsare connectedto engine.
-1
Inhalation of exhaust gases
mightresult
in
seriouspersonal
iniury
or deafh. Be sure deadly exhaust gas is
pipedoutsideandaway fromwindows,doors,or
otherinlets
to
building.
8.
Startengine.
Afterengine
has
started,excessiveamount
of
bluesmokewill
beexhausteduntil the
rust
inhibitor
or
oil
has
burnedaway.
Accidental starting of the engine
might causesevere personal injury
or death. Disconnect
the
batterycablewhenrepairs
aremade
to
theengine, controls,orgenerator.
.
13
Redistribution or publication of this document,
by any means, is strictly prohibited.

Exhaust
System
'
Unitsof
Measurement
Inches
of
Water
Inches
of
Mercury
Ounces
GENERAL
Theexhaustsystemmustefficiently expelallengine
combustionproductsandmuff
le
exhaustnoiseswith
minimumbackpressure. Ifbackpressureistoohigh,
volumetric efficiency of the engine is reduced, fuel
economydrops,exhausttemperatureincreases, and
valve life isshortened.
Full
Load
27
2
15.6
02.
Back pressure must notexceed
27
inches
(686
mm)
of water column for the rated load when measured
with a manometerat the exhaust manifold, Figure3.
FIGURE
3.
BACK
PRESSURETEST WITH MANOMETER
EXHAUSTSMOKE
A
lightgrayorlightbluesmokemaybearesultof low
ambient temperature and light load. This smoke is
unburnedfuel (not harmfultotheengine) anddisap-
pearswhen moreloadisapplied.
Black smoke indicates overfueling (more fuel than
oxygen) and is usually caused by overloading. The
smoke or unburned fuel becomes carbon when
raisedto a hightemperature. Carbon contributesto
enginedamagebecauseitcontaminatestheiubricat-
ing
oil.
Inhalation of exhaust gases might
a
result
in
serious personal injury or
death.
Do
not use exhaust heat
to
warm a room,
compartment,
or
storage area.
WARNING
Ventexhaustgasesoutside. Useflexibletubing only
betweenthe engineexhaustoutlet and rigid piping.
Inhalation
of
exhausf gases might
result in serious personal injury or
death. Inspect exhaustsystem audibly and visually
for leaks dally. Repairany leaks immediately.
WATER
COOLED
EXHAUST
Marine exhaust systems are designed
so
that a
minimum mount of heat will be radiated from the
exhaustsystem components.Thisisdone
to
keepthe
heat b'uild-up
in
the engine compartmentto a min-
imum. Exhaust heat is dissipated by using a water
cooledexhaustmanifoldandawaterinjectedexhaust
pipe and muffler system. The exhaust manifold is
encased ina shell through which engine coolant or
sea water is circulated. Just beyond the exhaust
manifold,
a
special elbow (see Figure
4)
is fitted
which allows the output water from the sea water
system to be injected into the exhaust pipe. The
injectedsea water iscarriedoutthorughtheexhaust
system and discharged into
the
flotation water.
CONNECTED
TO
EXHAUST
MANIFOLD
.\
SEA
WATER
INPUT
EXHAUST
ELBOW
ASSEMBLY
APPLY
PIPE
TO
ALL
PIPE
TWO
HOSE
CLAMPS
HIGH
EXHAUST
TEMPERATURE
RUBBER
EXHAUST
SHUTDOWN
SWITCH
HOSE
EXS-1014
FIGURE
4.
EXHAUSTELBOW
14
Redistribution or publication of this document,
by any means, is strictly prohibited.

.
TypicalInstallations
All
water injectedexhaustsystems mustbedesigned
so
that
the
dischargewater
will
not
flow
back
into
the
engine.Thereare several methodsthat can be used
to
keep water out of the engine.
All
are based on
injecting the water at a point
a
few inchesapprox-
imately
4
inches
(102
rnm)
belowthe exhaust mani-
fold outlet and installing asharpdrop
in
theexhaust
line that water cannot normally flow over. These
methods are divided into two general categories:
above water lineand below water line installation.
Above
WaterLine:Theexhaustmanifoldmustbeone
foot
or moreabovetheloadwater lineandthewater
must be injected near the exhaust manifold. The
exhaust pipe is pitched downward
1/2
inch perfoot
(13
mm
per
305
mm)
to
allow draining in the line
'
whetherthe genertor set is running
or
stopped.
Below WaferLine: An OnanAqualift muffler may be
used for below the water line installationsif the lift
height is no greater than four feet (1220 mm).
A
siphon break is required when the water injection
elbowisbelowthewater line(seeFigure5)to prevent
waterfrom beingsiphonedintotheexhaustmanifold.
The siphonbreak will be mountedat least
12
inches
(305
mm) above
the
loadwater line.
Ifthe
lift
heightisgreaterthanfourfeet
(1220
mm), a
riser exhaust system will be used. The exhaust
system
will
run
in
a
loop above the water line to a
point
12
to
18
inches
(305
to457 mm)abovetheboat
loadwater line. A waterjacketenclosesthe loopand
thewater
is
injectedontheoutletsideatapointfour
inches
(102
mm)
above the bottom of the loop.
A
condensation
trap
is
usually
installed
atthe
bottom
of
thedryexhaustlineseciton.Drainthetrapat regular
intervals
to
removecondensation.
Generally, exhaust systems
should
be
as
short as
possible with a minimum number
of
bends. The
radiusof any bend inthe exhaust pipeshould beat
least
5
times the diameter
of
the pipe. The
dry
sectionsof exhaust lineshouldbeeitherinsulatedor
waterjacketed.
Be sure the slotted opening in
fbe
EEEEl
vacuumreiief valveisopentoatmos-
phericpressure. Thesiphonbreak wiiinotfunctionif
therelief valveslot
is
closedin any way.
11
Ik
HANGERSTRAPS
VACUUM
RELIEF
RUBBER
HOSE
ATER
OUTLET
HAUST
WATER
ECTION
ELBOW
EXHAUST
OUTLET
FIGURE 5.
SIPHON
BREAK
EXHAUST
GAS
1s
DEADLY!
Exhaust gases contain carbon monoxide, apoisonous gas that might cause
unconsciousnessanddeath.
it
isanodorlessandcoiorlessgas formedduring
combustion
of
hydrocarbonfuels. Symptoms
of
carbonmonoxidepoisoning
are:
Dizziness Vomiting
Headache
Weaknessand Sleepiness MuscularTwitching
'
ThrobbinginTemples
if you experienceany
of
thesesymptoms, get out into fresh air immediafeiy,
shutdown theunitand donot useunfll
if
has been lnspected.
Thebest protectionagainstcarbonmonoxide inhaiafionisproperinstallation
andregular,frequentinspectionsof thecompleteexhaustsystem.lfyounotice
a changein thesound or appearance
of
exhaustsysfem, shut
the
unlf down
immedlafeiy and have
It
inspected and repaired at once by a competent
mechanic.
15
Redistribution or publication of this document,
by any means, is strictly prohibited.

Cooling
System
INSPECTION
As a part of standard maintenanceprocedures, the
entire cooling system should be inspectedfor signs
of leakage and checked for worn components. In-
spectthewater pumpbearings,impeller(neoprene),
and seals for signs of wear, and check for correct
drivebelttension.Locatethesource
of
anyleaksand
correct as required.Inspect
the
zinc pencilson heat-
exchanger cooled engines, and notethe amount of
deterioration. Refer to the appropriate section for
recommendedservice procedures.
As afinal check, runthe engineatfull loadandverify
that the enginecan maintainan operatingtempera-
ture of approximately18OOF (82'C). An enginethat
operates significantly above
or
below this value
should be tested for malfunctions.
IMPORTANCE
OF
REGULAR
MAINTENANCE
The entire cooling system, including the block and
radiator, heat exchanger,
or
keel cooler should be
cleanedand flushed outat least once ayear. This is
especially important in cold weather conditions
or
when preparingthe unit for extendedstorage (over
30
days). The cooling system can work efficiently
only when it isclean.
A
build-up of rust and scale
in
the cooling systemwill slow down heat absorption
and restrictwaterflow.
PRESSURECAP
DRAIN
PLUG
DRAININGCOOLINGSYSTEM
Openalldrainsand hoseconnectionswhere coolant
may be trappedwhen changing
the
antifreezesolu-
tion
or
when preparinga unit for storageinfreezing
conditions. Open the fill vent valve when draining
heat-exhangercooled engines. The following drain
plugsand hoses must be removedto drainthe
cool-
ingsystem completely:
Contact with
hof
coolanf might
n
resultinseriousburns.
Do
not
bleed
hof,
pressurized coolant
from
a closed cooling
sysfem.
Engine
Block: J-Series-Remove drain plug on
left
front side of engine.
(See
Figure
6).
Wafer
Pumps
(All
Unifs);
Remove drain plug under
pump
or
loosenpump cover (Figure
6).
Exhaust Manifold:
Remove plug from underside of
exhaust manifold(Figure
6).
Expansion Tank:
Remove plug from front side of
expansiontank (Figure
6).
Heat Exchanger(DrainingRaw WaterorSea Wafer):
Removedrainplugfromunderside,loosenendcover,
or
loosenand removehosetodrain heatexchanger.
TankHeafer:
Loosenandremovelowerhosetodrain
tank heater.
AqualiffMuffler;
The Aqualift muffler
has
relatively
littlewaterinitduringnormaloperationanddoes not
haveto be drainedduringfreezingweather.
Replaceand tighten all plugs, fittings, and clamps
when draining isfinished.
t
L
DRAIN
BLOCK
HERE
(SOME
MODELS
HAVE
A
PIPE
PLUG)
EXHAUST
MANIFOLD
J-SERIES
BLOCK
FIGURE
6.
DRAININGCOOLING
SYSTEM
REMOVEPUMP
COVER
TO
DRAIN
WATER
PUMP
Redistribution or publication of this document,
by any means, is strictly prohibited.

UNIT
MDJA
MDJB
MDJC
MDJE
MDJF
CLEANINGAND FLUSHINGTHE
COOLING
SYSTEM
To clean rustand scaledepositsfrom captivewater
systems, drainthesystem(as previouslydescribed),
and then fill with clean water and cleaner solution.
Usean approvedchemicalcleaner(suchasthetype
usedfor cleaningautomotivecooling systems), and
follow
the instructionsprovidedbythesupplier.
Chemical cleaners cannotbeused
with
directsea water cooled
marineengines.
WARNING
Cleaningsolutionsfypicallyconfain
i
strong chemicals that may cause
injury
if
used improperly. Read all warning labels
before using.
When cleaning
is
complete,drainthe cleaningsolu-
tionand flushthesystem.For bestresultstheengine
andheatexchangershouldbereverse-flushed.Allow
theenginetocoolas muchas possiblebeforeflush-
ingwith coldwater.
Never pour cold wafer info
a
hot
D
engine. Doing
so
may crack fhe
head or fhe cylinder block.
Do
not
operate engine
without
coolant
for
even a
few
minutes.
CAPACITY INQUARTS
ENGINE
AND
HEAT
EXCH.
4.5
(4.3
L)
9.5 (9
L)
4.5
(4.3
L)
9.5
(9
L)
2.3
(2
L)
Flush system if engine operation indicatesclogged
passages or overheating.
Toflush the engine:
1.
Drainheatexchanger,cylinderblockandexhaust
2,
3.
4.
5.
6.
To
1.
2.
3.
manifold.Removethermostats.
Remove the inlet and outlet hoses betweenthe
engineand heatexchanger.
Closealldrainplugsand attachtheflushing gun
nozzle to the water outlet, as near the exhaust
manifold as practical. Restrict the normal inlet
lineopeninguntilthesystemfillswithwater, then
applyair pressuregradually. Repeatthe process
untiltheflow of water from the cylinder block is
clean.
Removeflushinggun.
Reinstallthermostats,hoses, anddrainplugsand
refillthe system with the propercoolant.
When
flushing
is
completed, check the system
thoroughlyforanyleaksuncoveredbytheclean-
ingoperations.
flush heatexchanger:
Flushthe engine water jacket as previously dis-
cussed.
First remove water outlet hose between engine
waterjackettothe heat exchanger.
Flushbothfreshwatersideand rawwatersideof
heat exchanger.
4.
5.
6.
Remove
rubberimpellerpump covertoflush raw
waterside.
Flush
the
water-cooled exhaust manifold.
When flushing is.completed, check the system
thoroughly for leaks.
FILLINGCOOLINGSYSTEM
Allclosedorcaptivewatercoolingsystemsshouldbe
filled with
50/50
mixture of antifreeze and clean
water. This istheamountrecommendedforsatisfac-
tory corrosion protection and boil-over protection.
In extremely low temperatures
(-25OF
or lower),
it
may be necessary to increase the percentage of
antifreeze to provide adequate protection against
freezing. Followthe recommendationof thesupplier
todeterminetheamountof antifreezeneededforthe
lowesttemperatureexpected.Theantifreezesolution
mustbeabletoprotectthecoolingsystem duringthe
coldestwinterweather.Table
1
showsthecapacities
of the variouscooling systems.
TABLE
1.
COOLING
SYSTEM
CAPACTIES
Heat
Exchanger Filling
Improperfilling ofthe heatexchanger(Figure
7)
can
causeoverheatingof
the
engine-Topreventthispos-
sibility, follow these instructions whenever adding
coolanttotheheatexchanger:
1.
2.
3.
4.
5.
6.
7.
8.
9.
Removefillcap.
Openfillventvalve (turncounterclockwise).
Removevent plug (oldercitywater cooledunits
only).
Fillwith coolant untilvents beginto overflow.
Closefillventvalve (turnclockwise).
Replacevent plug (oldercitywater cooled units
only).
Replacefillcap (primepumpon marineunits).
Operate unit
10
minutes at full load; watch for
leaks.
Shutdown unit.
17
Redistribution or publication of this document,
by any means, is strictly prohibited.

Contact With hot coolant might
resultinseriousburns.
Do
notbleed
hot,
pressurized coolant
from
a
closed cooling
system.
10.
Slowlyopenpressurecapandcheckwater level.
11.
Fillsystemtotopwith coolant.
WATER
MANIFOLD FILL
VENT
VALVE
_,
I
t
8378
1
HEAT
EXCHANGER
FIGURE
7.
HEAT
EXCHANGER
FILLING
MARINE
COOLING
SYSTEMS
Threetypesof marinecoolingsystemsareingeneral
usetoday: direct seawater cooling, heat exchanger
cooling,and keel orskin cooling.
Direct sea water cooling systems use an engine
mounted pump to draw flotation water and pump
it
throughtheengineandout throughtheexhaustsys-
tem.Thefloatation orsea water comesindirectcon-
tact withtheenginewater jacket.
INLETFOR
COOLINGWATER
FLUSH
i
HULL
The heat exchanger and keelcooling systems were
developed to keep sea water, and the resulting
sediment deposits (salt, silt, etc.), from the engine
coolingjacket. Bothsystems haveafixedquantityof
captive water ina closedsystem to cooltheengine.
Sea water cools the captive water in the heat
exchanger or keel cooler. Sea water and captive
water are keptseparated,
so
theenginewater jacket
stays clean. Figure
8
shows a typical marine heat
exchanger.
Because marine generator sets operatetypically in
verysmallcompartments,
it
isimportantthattheheat
radiated from the exhaust system be keptto
a
min-
imum.
To
accomplish this, the heated sea water is
usually discharged through the exhaust system.
Special mufflers,pumps,andanti-siphon devicesare
required to avoid interferencewith the passage
of
exhaust gasesand to prevent entry of water into the
combustion chamber.
Direct
Cooling
System
Onan engine generator sets constructed for direct
sea water cooling are equipped with a sea water
pump and are normally installed with a water filter,
water inletvalve (seacock), and strainer.
A
through-the-hull flush-type fitting
is
used for a
water inlet. Heatedseawater flows past the thermo-
stat to the exhaust manifold (water cooled) and is
discharged through the exhaust system. The dis-
charged water
cools
the entireexhaust system and
greatly reduces the amount of heat that would
normally radiatefrom the mufflerand exhaust pipe
(see Figure
9).
Although this system isthe simplest
andhasthelowestinitialcost,
it
isnotrecommended
forsalt water or water that containssilt and debris.
WATER TO
EXHAUSTLINE
FLEXIBLE
SECTION
LINGWATER IN
Y
F STRAINER
--
PITCH
t
DOWN
TO
MUFFLER
FIGURE
8.
HEAT EXCHANGER FIGURE
9.
DIRECTSEA WATER COOLING
18
Redistribution or publication of this document,
by any means, is strictly prohibited.
This manual suits for next models
4
Table of contents
Other Onan Engine manuals
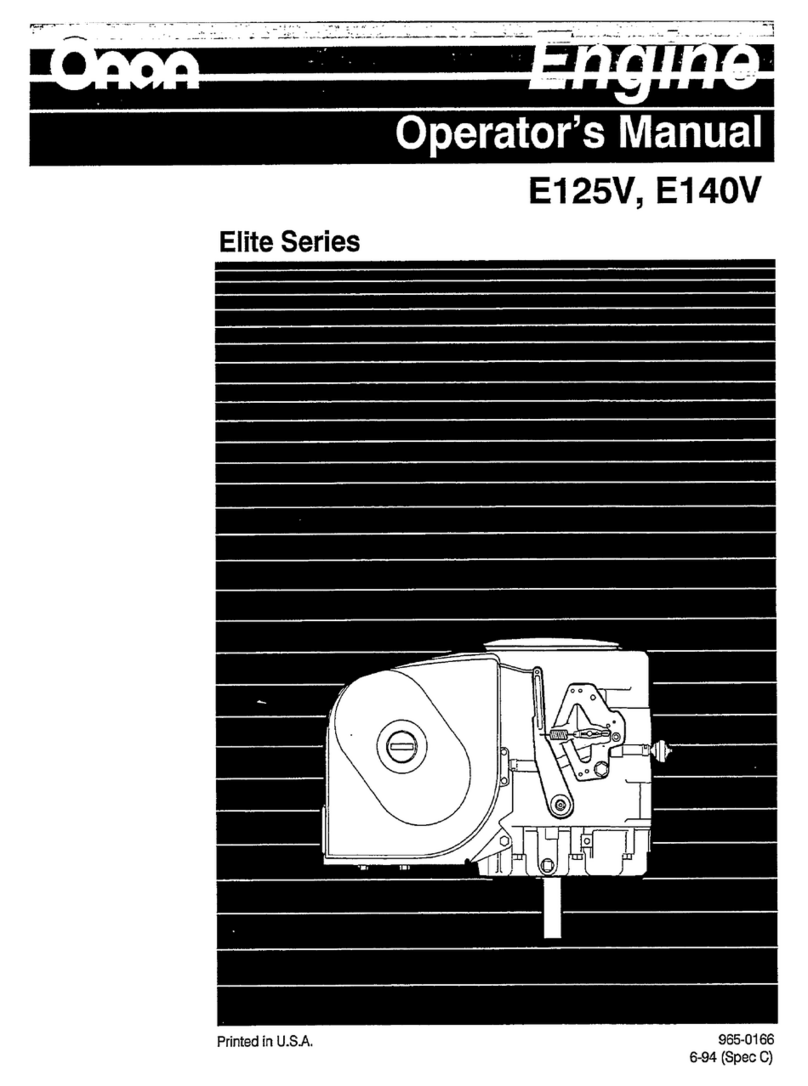
Onan
Onan Elite E125V User manual
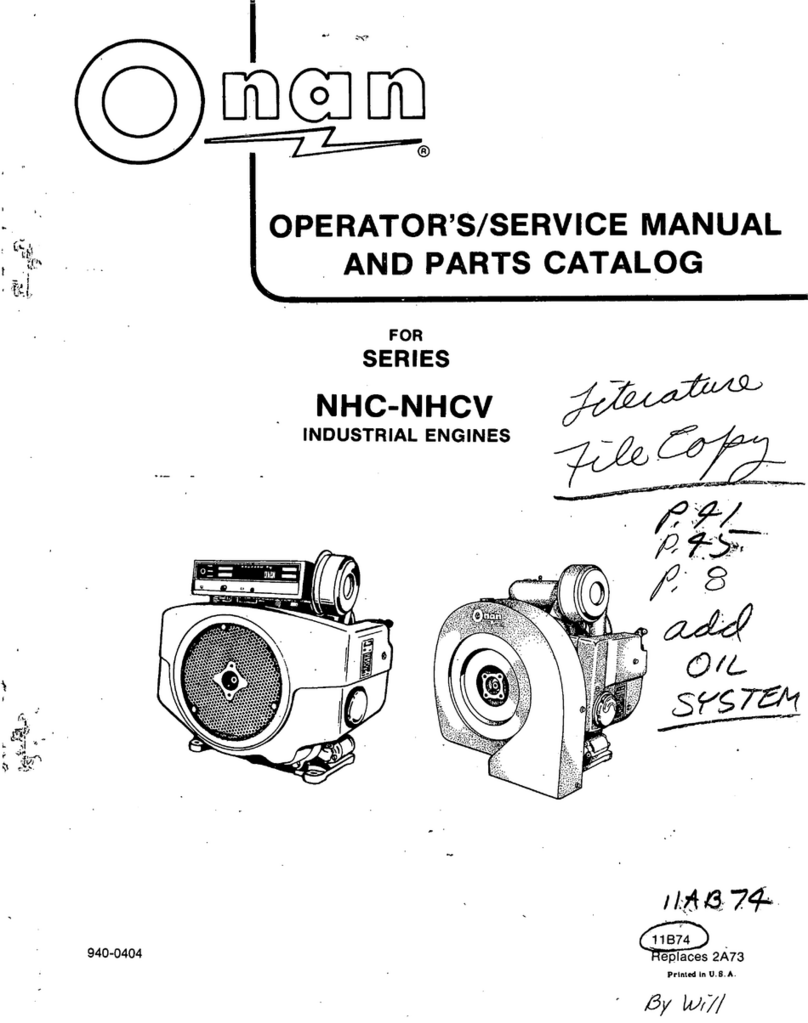
Onan
Onan NHC Series Instruction Manual
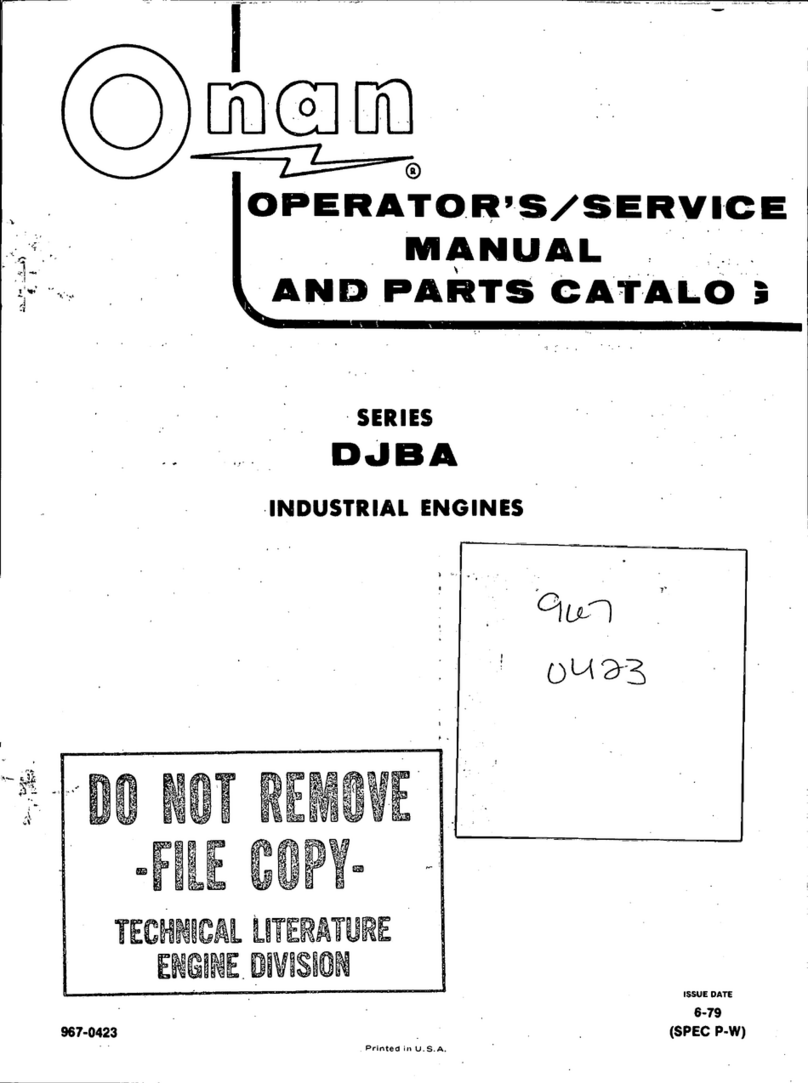
Onan
Onan DJBA Series Instruction Manual

Onan
Onan DJA Series Operating manual
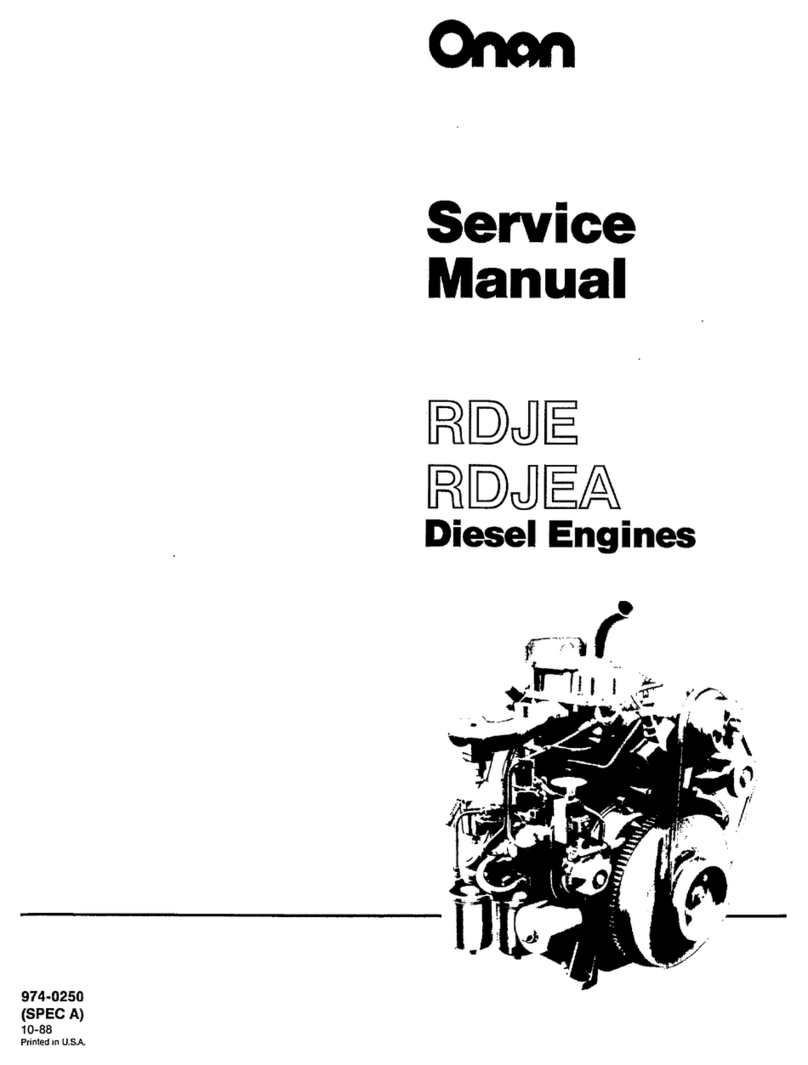
Onan
Onan RDJE User manual

Onan
Onan Performer Series User manual

Onan
Onan J Series Operating manual
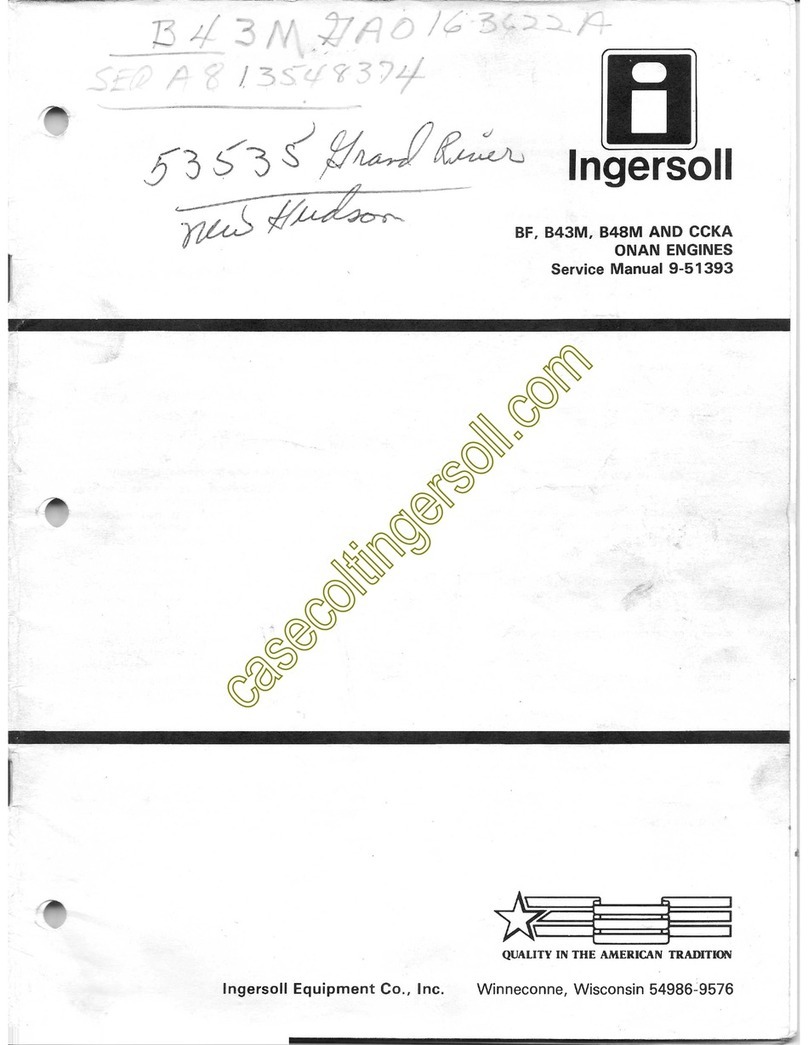
Onan
Onan B43M User manual
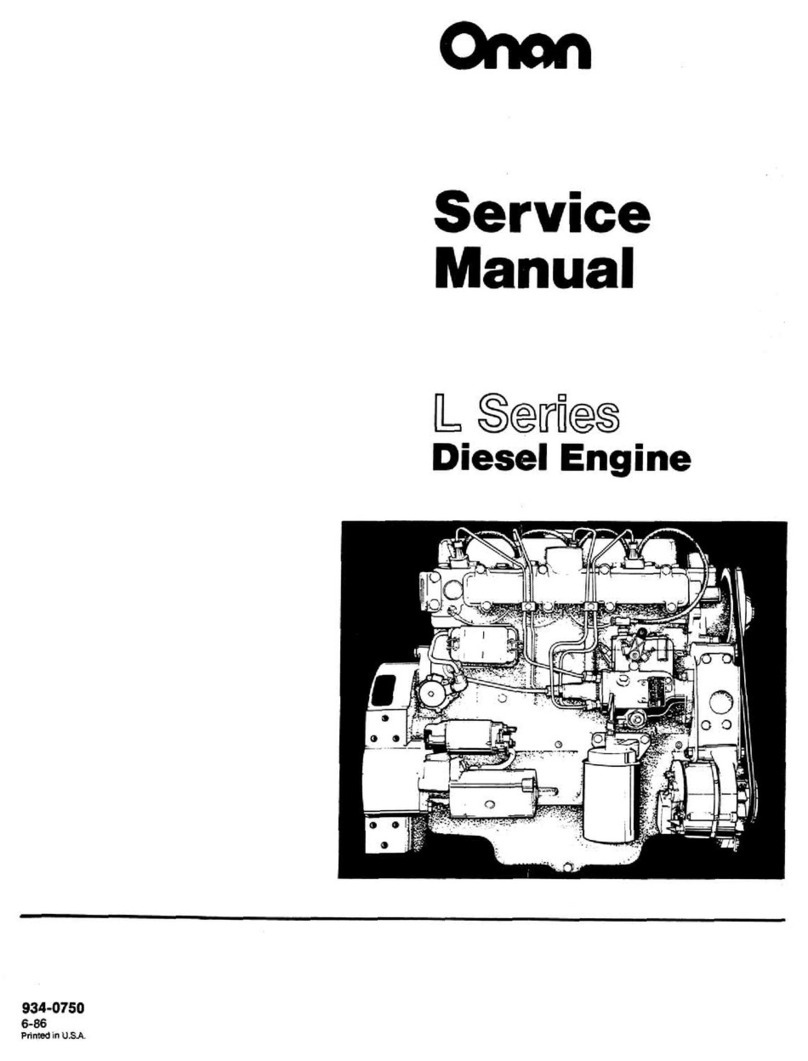
Onan
Onan L Series User manual
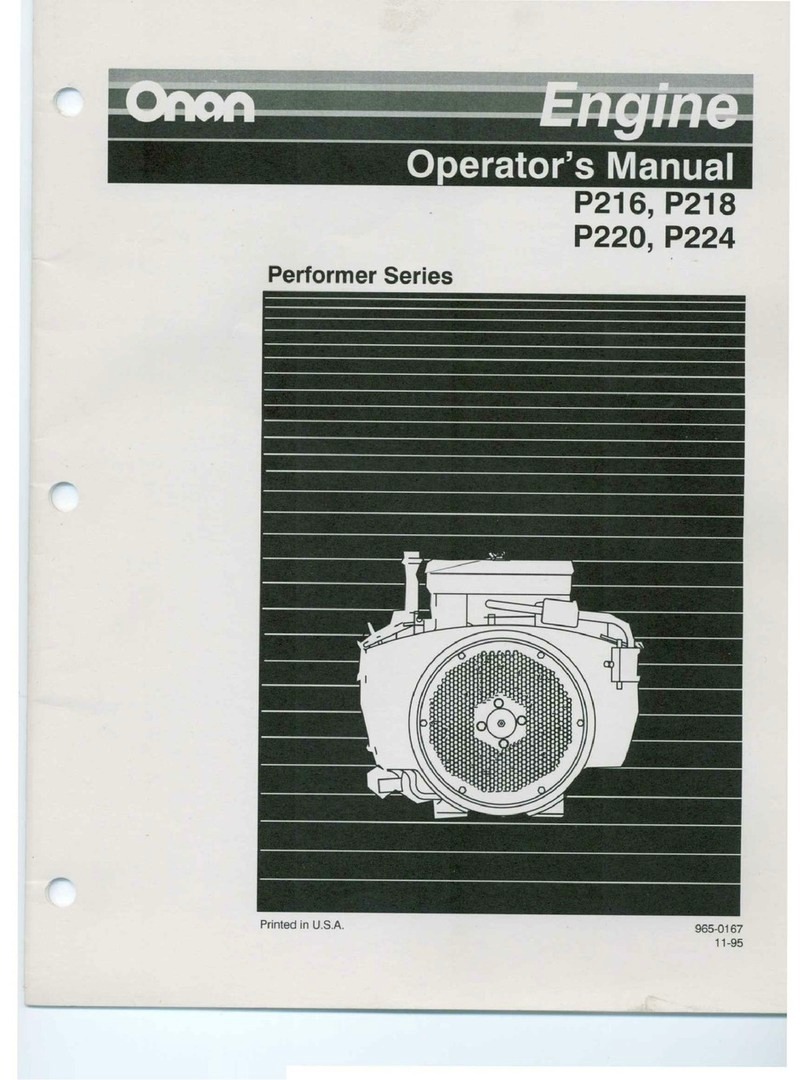
Onan
Onan Performer P216 User manual
Popular Engine manuals by other brands
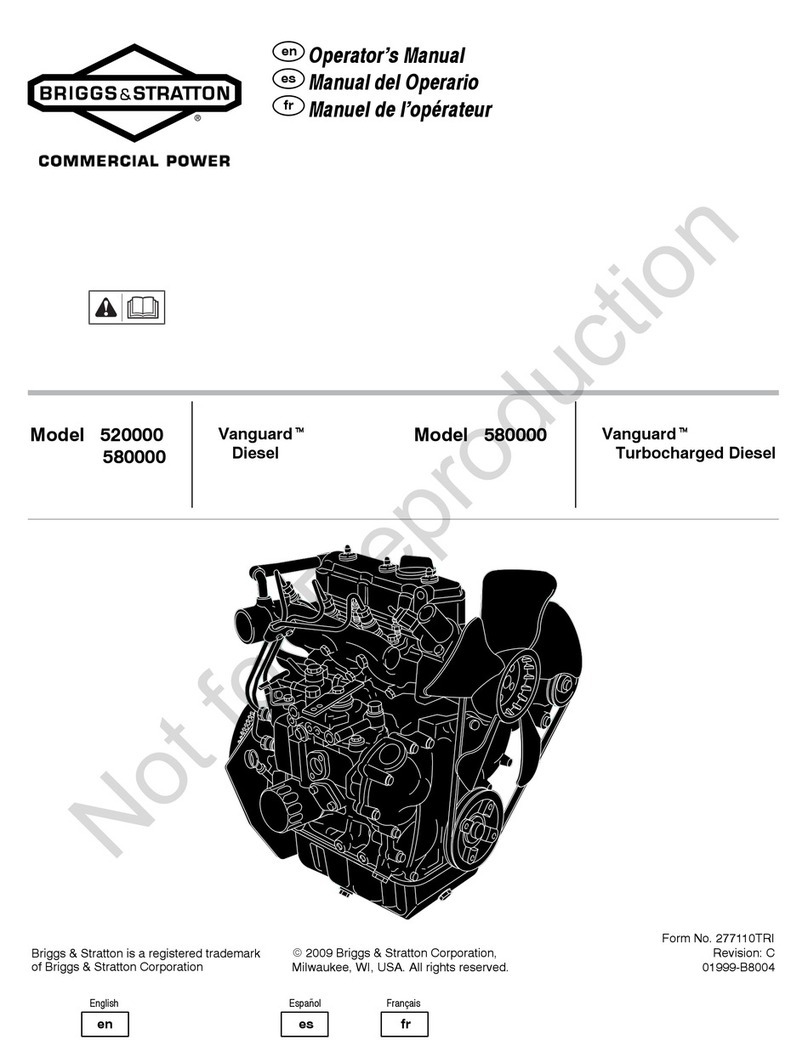
Briggs & Stratton
Briggs & Stratton 277110TRI Operator's manual
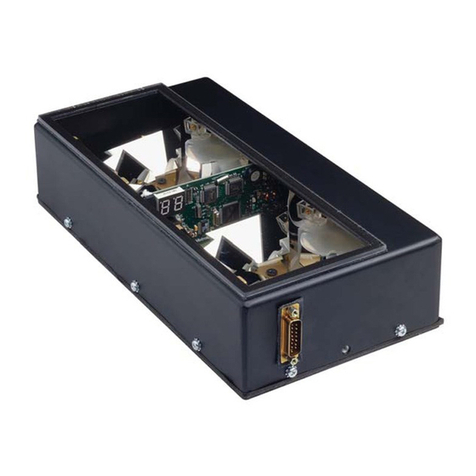
Honeywell
Honeywell IS220 user guide
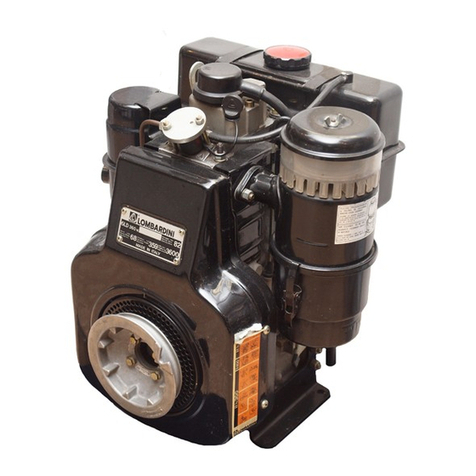
Kohler
Kohler Lombardini 6 LD 260 Use & maintenance

ZONGSHEN
ZONGSHEN 1P61F owner's manual

SOMFY
SOMFY MAESTRIA+ 50 io instructions

Ametek
Ametek dunkermotoren BG dCore Series Translation of the original manual