OPW Petro Vend FSC3000 User manual

Part Number: M1700, Rev. 14
Issue Date: 8/10/2021
Supersedes: 7/8/2020
M1700 - FSC3000™
FSC3000
IOM

NOTE: Before you use this manual, make sure you have the most recent revision. Look at the
revision of this document to make sure it agrees with the most current revision found at
http://www.opwglobal.com/opw-fms/tech-support/manuals-how-to-videos. Download the
latest revision if necessary.
OPW Fuel Management Systems is a part of Dover Fueling Solutions.
Copyright Information
© 2021 Dover Fueling Solutions. All rights reserved. DOVER, the DOVER D Design, DOVER FUELING
SOLUTIONS, and other trademarks referenced herein are trademarks of Delaware Capital Formation.
Inc./Dover Corporation, Dover Fueling Solutions UK Ltd. and their affiliated entities.
Contact OPW Fuel Management Systems
Visit us at https://www.doverfuelingsolutions.com/, or contact us at:
Call 1-877-OPW-TECH (877-679-8324)
For calls outside US and Canada, call +1-708-485-4200
Monday through Friday, 7 a.m. to 6 p.m., US CST
For technician registration, see
http://www.opwglobal.com/opw-fms/tech-support/technician-registration
For in-depth training through OPW University, see
http://www.opwglobal.com/opw-fms/tech-support/training-certification
Compliance Information
Software is compliant with Visa U.S.A. Payment Application Best Practices (PABP) /Payment Card Industry
Payment Application Data Security Standard (PCI PA-DSS) guidelines by restricting user access to sensitive
cardholder data.
Specific to networks that process bankcards (i.e., Visa, MasterCard, T-Chek™, Comdata, American
Express, Discover and JCB) using the dual-serial port convertor and connecting the inbound port to the
Doc. No.: M1700 Rev.: 14
Page 2 of 75

FSC3000™ Fuel Site Controller direct-connect serial port (Port 1) conflicts with the guidelines described in
the “M030001_PA1-PA-DSS-Implementation-Guide” provided with your FSC3000™ Fuel Site Controller.
Please review the “M030001_PA1-PA-DSS-Implementation-Guide.pdf” for more information on maintaining
your PCI-DSS compliance.
For installation wiring reference, fuel control field wiring diagrams for the equipment that follows that includes
Bennett, Fill-Rite, Wayne and other products, go to the OPWGlobal.com website (technician login required).
Scan or click the QR code below or go to http://www.opwglobal.com/opw-fms/tech-support/technicians-
portal/fuel-control-field-wiring-diagrams-for-dispensing-equipment.
NOTE: A Technician login is required to access the Technician Portal. For technician
registration, go to the Technician Registration page at http://www.opwglobal.com/opw-
fms/tech-support/technician-registration.
l Bennett 3800 Duo-2
l Bennett 3800 Single
l Bennett Mechanical
l Fill-Rite
l Gasboy 9100 Dispenser
l Gasboy 9100 Duo-1 Pump
l Gasboy 9100 Duo-2 Pump
l Gasboy 9800 Dispenser
l Gasboy Pump
l Gasboy 9850KX
l Wayne Reliance Dual Dispenser
l Wayne Reliance Duo-2
l Wayne Reliance Single Dispenser
l Wayne Reliance Single Pump
l Wayne Select Dual
l Wayne Select Duo-2
l Wayne Select Single Duo-1 Pump
l Wayne Select Single
Doc. No.: M1700 Rev.: 14
Page 3 of 75

Table of Contents
Section 1 Important Safety Information 7
1.1 Safety Warnings 8
1.2 Information Panels 8
1.3 Installer Safety 10
1.4 Electrostatic Sensitive Devices (ESD) 11
1.5 FCC Compliance 12
1.6 Applicable Warnings, Battery Safety 13
1.6.1 Internal Coin Cell Battery Safety 13
Section 2 FSC3000 Controller 14
2.1 Technical Specifications 15
2.1.1 Remote vs. Integrated FSC3000 15
2.2 Components & Diagrams 16
2.2.1 Main Board Components 16
2.2.2 Parts Listings & Accessories Exploded View 16
2.2.3 System Wiring Schematics 18
2.3 Ports 20
2.3.1 USB Key 20
2.3.2 Ethernet 21
2.3.3 Phone Line 22
2.3.4 RS-485 23
2.3.5 RS-232 24
2.4 Installation 34
2.4.1 Integrated FSC3000 Communication Conduit 34
2.4.2 Remote FSC3000 34
2.4.3 SIMM Activation 35
Doc. No.: M1700 Rev.: 14
Page 4 of 75

2.4.4 Wireless Radio Modem Installation 35
2.4.5 Additional System Options 35
2.5 Physical Configuration 36
2.5.1 FSC3000 Access Connections – Baud Rate Setting 36
2.5.2 Direct-Connect Serial Communication to PC 36
2.5.3 PC Connection via Dial-In 36
2.5.4 PC Connection via Built-in Ethernet Adapter 37
2.6 Startup & Test 38
2.6.1 Cold-Start 38
2.6.2 Software Configuration 38
2.6.3 FSC3000 Ethernet Port Setup 39
Section 3 Pump Control 45
3.1 Direct Pump Control (DPC) 46
3.1.1 Wayne and Gilbarco 46
3.1.2 Gasboy 46
3.1.3 DPC Technical Specifications 46
3.1.4 DPC Installation 47
3.1.5 DPC Pump Control (Electronic Control) Conduit Requirements 47
3.1.6 DPC Interface in a Remote Enclosure (for Wayne and Gilbarco) 48
3.1.6.1 Wayne Data Distribution Box Connection to DPC Board 49
3.1.6.2 Gilbarco D-Box Connection to DPC Board 50
3.1.7 Install a DPC Interface in a Terminal Pedestal (for Wayne and Gilbarco) 51
3.1.7.1 20-4428 Board Plate Assembly Installation 51
3.1.7.2 Pedestal Mount DPC Kit Installation (FMS P/N 20-4419-DPC) 52
3.1.8 Install a DPC Interface for Gasboy® 55
3.1.8.1 Remote DPC Interface for Gasboy Installation 55
Doc. No.: M1700 Rev.: 14
Page 5 of 75

3.1.8.2 DPC Interface for Gasboy Pedestal Installation 56
3.1.9 Physical Configuration 58
3.1.9.1 DPC Interface Jumper Setup (for Wayne and Gilbarco) 58
3.1.10 Software Configuration 59
3.1.11 Testing 59
3.2 Dispenser Terminal Control (DTC) 60
3.2.1 Technical Specifications 60
3.2.2 Terminal Types 60
3.2.2.1 Wayne CAT (Card Authorization Terminal) 60
3.2.2.2 Gilbarco CRIND (Card Reader in Dispenser) 60
3.2.3 Diagrams 61
3.2.3.1 Wayne DTC 61
3.2.3.2 Gilbarco DTC 61
3.2.3.3 Gilbarco Secure Prompts DTC 62
3.2.4 DTC Installation 63
3.2.4.1 DTC Remote Enclosure Installation 63
3.2.5 Physical Configuration 64
3.2.5.1 Wayne CAT-specific 64
3.2.5.2 Gilbarco CRIND-specific 65
3.2.6 Software Configuration 66
Section 4 Maintenance & Troubleshooting 67
4.1 FSC3000 (Remote Only) Maintenance 67
4.2 Fuel Island Terminal Maintenance 67
4.3 Remote Enclosures 68
4.4 Journal Printer 68
Appendix A - Pump Control Test Checklist 69
Warranty 75
Doc. No.: M1700 Rev.: 14
Page 6 of 75

Section 1 Important Safety Information
You must read and understand all safety information in this manual.
IMPORTANT: ONLY APPROVED, TRAINED TECHNICIANS ARE PERMITTED TO
INSTALL OR DO SERVICING ON THE EQUIPMENT AND COMPONENTS SHOWN IN THE
PROCEDURES IN THIS MANUAL.
For your protection, obey all safety panels, warnings and instructions where they occur.
Read the safety and compliance information completely in the sections that follow before you begin
installation.
DANGER: To prevent the possibility of explosion or fire, do not use electrical
or battery operated power tools in or near the Hazardous Area! Only use
pneumatic or hand tools.
Doc. No.: M1700 Rev.: 14
Page 7 of 75

1.1 Safety Warnings
This manual contains many important Safety Alerts. There can be a risk of injury or damage to property if you
do not obey these alerts. The panels below show the types of safety warnings that can be seen and how
each is specified.
DANGER: Indicates an immediately hazardous condition that, if not prevented, will
result in death or serious injury.
WARNING: Indicates a possibly hazardous condition that, if not prevented, could
result in death or serious injury.
CAUTION: Indicates a possibly hazardous situation that, if not prevented, could
result in minor or moderate injury.
NOTICE: Indicates important information not related to hazards. A condition that, if not
prevented, can result in property damage.
SAFETY INSTRUCTIONS: Indicates instructions and procedures related to safety or
gives the location of safety equipment
1.2 Information Panels
NOTE: This panel gives more information about an instruction or procedure.
IMPORTANT: This panel contains special information that is important and must be read and
obeyed.
Doc. No.: M1700 Rev.: 14
Page 8 of 75

REMINDER: This panel shows information that has been given before in the manual that is
important to show again.
TIP: A step or procedure that is recommended to make another step or procedure easier.
INFORMATION: This panel shows references to more information in other sources.
READ CAREFULLY: This panel points to information that must be fully read and understood
before doing the procedure(s) that comes after.
Doc. No.: M1700 Rev.: 14
Page 9 of 75

1.3 Installer Safety
CAUTION: Incorrect installation can cause a risk of injury to installers and
users of this equipment. Incorrect installation can result in environmental
contamination or equipment damage. Read these instructions carefully!
Refer to the National Electrical Code (NFPA No. 70) and the Motor Fuel Dispensing Facilities and Repair
Garages Code (NFPA No. 30A) to make sure your installation is correct.
Installers must obey the instructions in this document to complete a safe installation.
For installations outside the United States, make sure that the installation obeys all applicable local codes.
The installer must know and obey all applicable local codes in the country or county where this unit is
installed.
NOTE: Local codes can specify special installation requirements. Installation is subject to
approval by the local authority with jurisdiction at the site.
Doc. No.: M1700 Rev.: 14
Page 10 of 75

1.4 Electrostatic Sensitive Devices (ESD)
This product contains components that can be damaged by Electrostatic Discharge. See the instructions
below to work safely with these components.
ATTENTION: Electrostatic Sensitive Device - To prevent damage from electrostatic
discharge, obey the precautions below when it is necessary to move or touch electrostatic
sensitive devices.
l Use correct grounding methods.
l Use an ESD Field Service Kit with wrist strap, dissipative mat and grounding cord when possible.
l When possible, do not stand on carpeted surfaces while you do work with Electrostatic Discharge
Sensitive (ESDS) devices.
l Do not keep ESDS components/assemblies where there is a risk of damage.
l A new component should be kept in its anti-static package as long as possible before installation.
l Only touch ESDS components by the edges. Do not touch any of the circuitry.
Doc. No.: M1700 Rev.: 14
Page 11 of 75

1.5 FCC Compliance
This system complies with Part 15 of the Federal Communications Commission (FCC) Rules & Regulations.
Operation is applicable to these conditions:
l This device must not cause harmful interference.
l This device must accept interference received. This includes interference that can cause undesired
operation.
Doc. No.: M1700 Rev.: 14
Page 12 of 75

1.6 Applicable Warnings, Battery Safety
NOTE: Only certified OPW-FMS technicians are authorized to install and program this
system. This is necessary for warranty registration.
1.6.1 Internal Coin Cell Battery Safety
DANGER: The coin cell battery can explode if it is used incorrectly. Do not
recharge, disassemble or discard this battery in fire. Replace the SIMM coin
cell battery with Panasonic or Matsushita Electric Part Number CR-3032 or
equivalent ONLY. There can be a risk of fire or explosion if an incorrect battery
is used.
To avoid possible explosion or fire, do not replace the lithium battery with a
type that is not compatible.
The battery used in this device can present a risk of fire or chemical burn if
used incorrectly. Do not disassemble, heat above 100°C or incinerate.
Discard a used, replaced battery immediately. Keep away from children. Do
not disassemble and do not discard in fire.
The inside of the console contains high-voltage circuitry; ONLY certified
technicians should be permitted access to the console.
INFORMATION: For more safety information on the Panasonic CR-3032 coin cell Lithium
battery used in this device, refer to the Panasonic Product Safety Data Sheet.
Doc. No.: M1700 Rev.: 14
Page 13 of 75

Section 2 FSC3000 Controller
The Fuel Site Controller (FSC) contains the site configuration that manages card and pump processes to and
from the Fuel Island Terminals (FITs) and Pump Control Terminals (PCTs). The FSC communicates to the
FITs and PCT 24/7 through a two-wire RS485 communication circuit (i.e., Petro-Net™).
The FSC verifies the card data, collects all fuel transaction data and stores local proprietary card flies. The
FSC3000 is equipped with the released PCI (Payment Card Industry) Security Standards application
software (a requirement by most credit card and fleet card processors, which assures merchants and their
customers that the FSC3000 Multi-trucking System does not store sensitive credit card data).
Doc. No.: M1700 Rev.: 14
Page 14 of 75

2.1 Technical Specifications
The FSC3000 Fuel Site Controller can be contained in its own remote/desktop enclosure or installed inside a
FIT. See below for additional information of a remote FSC and an integrated FSC.
2.1.1 Remote vs. Integrated FSC3000
FSC3000 Remote Enclosure
FSC3000 Board (Integrated)
Remote vs. Integrated FSC3000 Specifications
Remote FSC3000 Integrated FSC3000
Cabinet Dimensions (H x W x D)
2.25” x 10” x 8.25”
(5.7 cm x 25.4 cm x 21 cm)
See specific FIT specifications
Power Requirements
85-240 VAC, 50/60 Hz;
25 watts maximum
See specific FIT specifications
Operating Temperature Range 32°F - 122°F (0°C – 50°C) See specific FIT specifications
One (1) DIN (RS-485) Petro-Net Max. Length 5,000' (1,524 m) 5,000' (1,524 m)
Doc. No.: M1700 Rev.: 14
Page 15 of 75

2.2 Components & Diagrams
2.2.1 Main Board Components
Components of the FSC3000 Main Board
The power supply supplies 12 VDC to the main board. This lets the main board run logic and
communication circuit devices. The main board contains all communication circuits for a back-office PC,
Petro-Net communication to the FITs and PCMs, and Ethernet communication. The main board also
manages fleet network host modem, journal printer, pass-thru port communications and USB key operation.
The SIMM card contains the application program for the operattion of all ordered options (i.e.,
card/transaction memory, fleet networks, DPC, etc.) The SIMM card also contains a backup battery to
maintain all data in memory in the event of a power loss. Remove the battery-insulating strip to activate a
SIMM memory module. Gently remove the yellow strip at this time. It is recommended that the SIMM module
be reseated.
2.2.2 Parts Listings & Accessories Exploded View
FSC3000 Parts List
Item No. Part Number Description
1 75-2037 FSC3000 Internal Modem
2 R20-0380 FSC3000 Main Board
3 R20-0381-03* FSC3000 SIMM Module (*requires configuration)
4 20-1517-05 FSC3000 Printer Cable
5 20-1613 RJ45 to RJ45 Ethernet Cable
6 20-1517-01 Network Modem Cable
7 20-1520-01 PC/CRT Cable
8 75-0108 USB Key
9 20-4089 Display Assy. External FSC3000
10 75-2059 Bluetooth M-7EM
Doc. No.: M1700 Rev.: 14
Page 16 of 75

FSC3000 Parts List
Item No. Part Number Description
11 20-4089-01 Internal FSC3000 Display
12 20-7073 Journal Printer with Cable
13 20-7078 Network Modem
14 75-2047 Indoor Wireless Modem
Doc. No.: M1700 Rev.: 14
Page 17 of 75

2.2.3 System Wiring Schematics
Typical System Installation Diagram with Electronic Pump Control
Doc. No.: M1700 Rev.: 14
Page 18 of 75

Typical System Installation Diagram with Mechanical Pump Control
Doc. No.: M1700 Rev.: 14
Page 19 of 75

2.3 Ports
2.3.1 USB Key
l The USB Key port will allow fuel transactions to be written to the supplied USB key.
l Ideal for using with integrated systems that do not have a PC connection to the FSC for retrieving
transaction data. The USB key can then be removed from the FSC3000 and plugged into a PC. The
stored transaction data could then be imported into the optional Phoenix software package used to
generate reports.
l Also, if the FSC3000 has the optional card update feature, card updates can also be transferred
through the USB key.
Doc. No.: M1700 Rev.: 14
Page 20 of 75
Table of contents
Other OPW Controllers manuals
Popular Controllers manuals by other brands
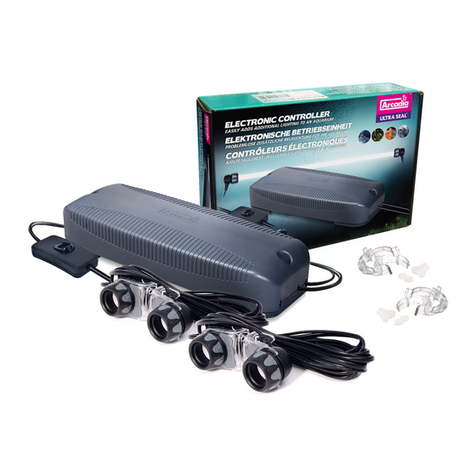
Arcadia
Arcadia REPTILE CONTROLLER RACRE Installation and maintenance instructions
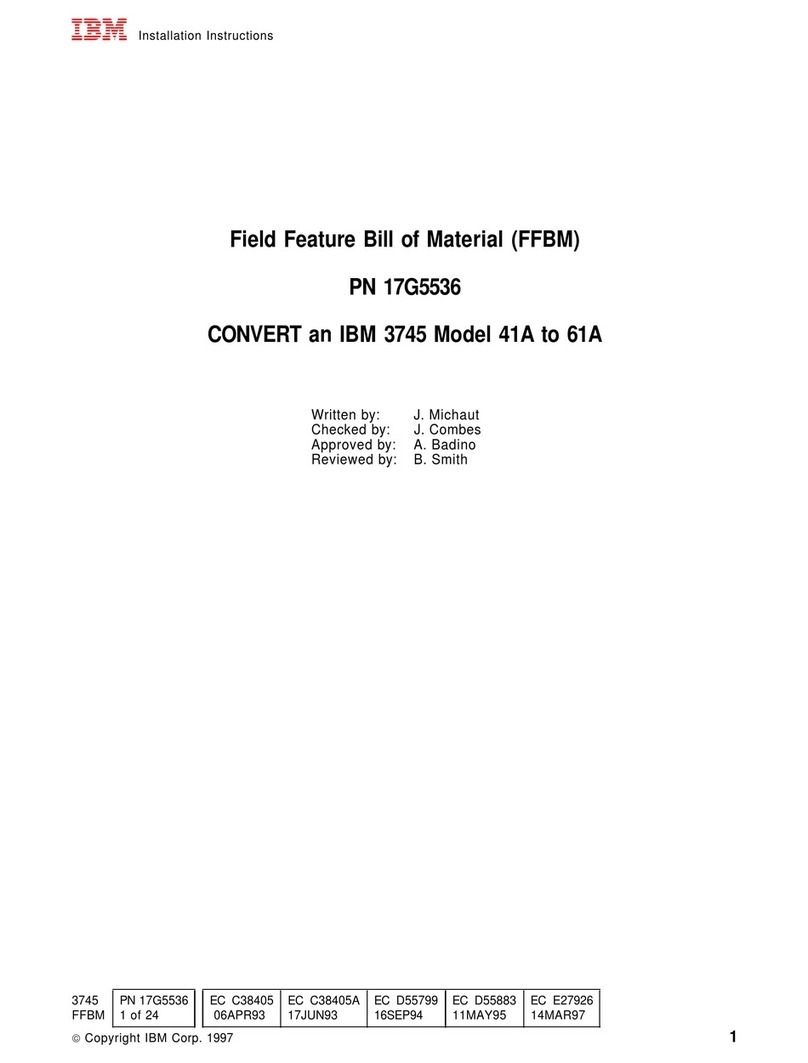
IBM
IBM 3745 Series installation instructions
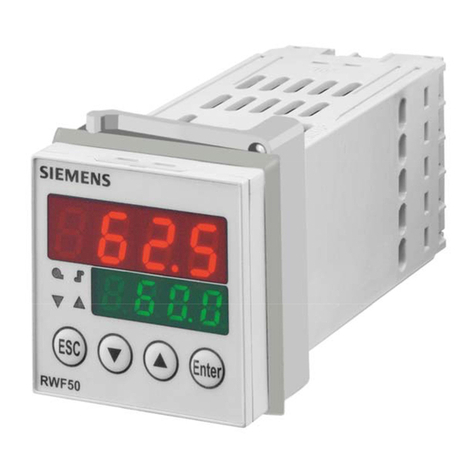
Siemens
Siemens RWF 50.2 Installation, use and maintenance instructions
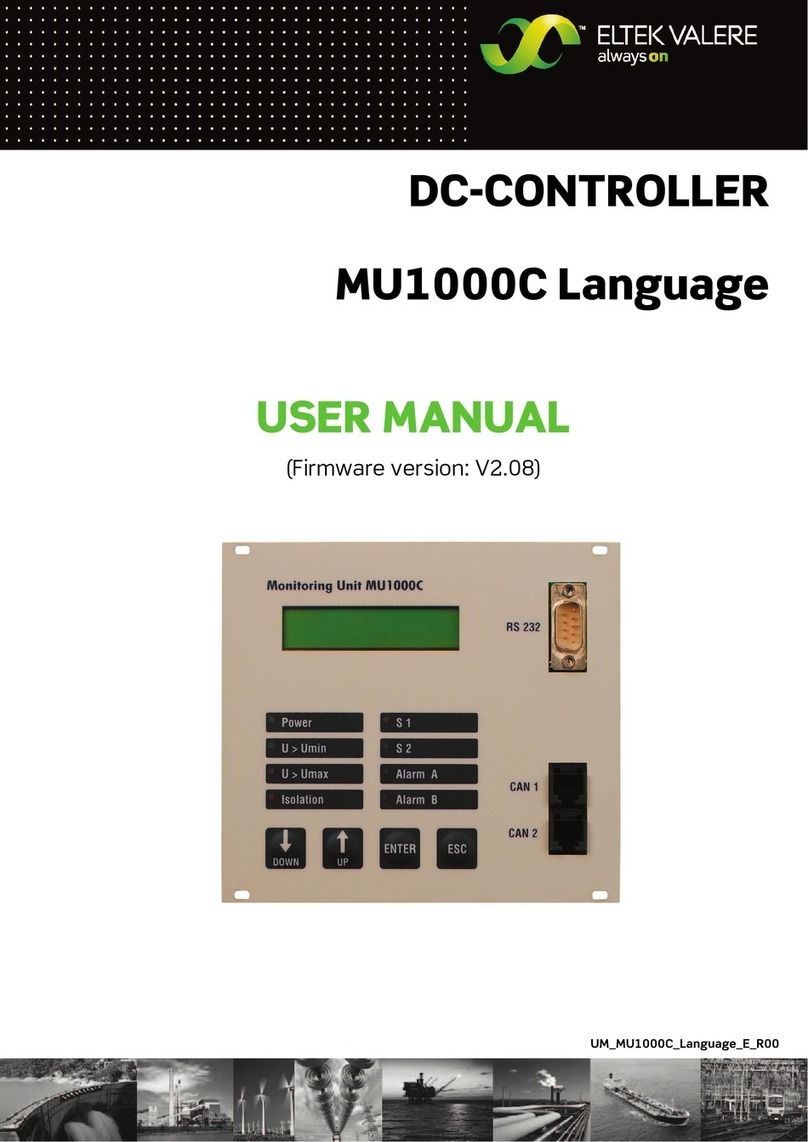
Eltek Valere
Eltek Valere MU1000C user manual
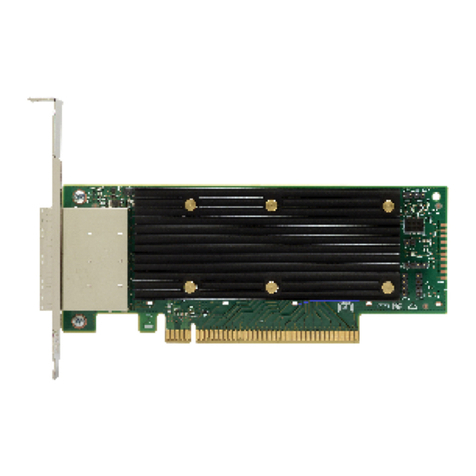
Broadcom
Broadcom HBA 9405W-16e Quick installation guide
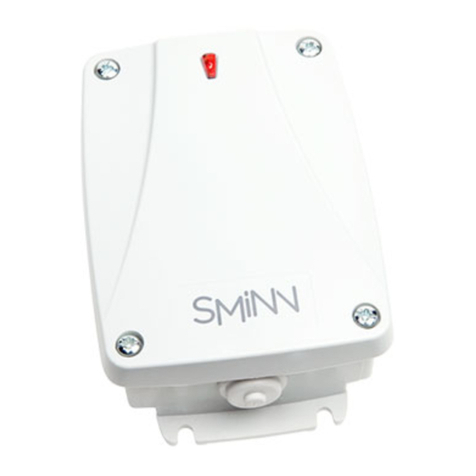
Sminn
Sminn BOX S 220 instruction manual