Orgapack H-2386 User manual

09.09/WE
OR-T 400
BATTERY-HAND TOOL FOR PLASTIC STRAPPING
Before using the tool,
read the operating
instructions carefully.
OPERATING INSTRUCTIONS
Patent angemeldet
Patent pending
Brevet en cours
H-2386
H-2386
1-800-295-5510

5
09.09/WE
ORGAPACK OR-T 400
TABLE OF CONTENTS
egaP
SHORT INSTRUCTIONS 2
7atadlacinhceT1
9noitamrofnilareneG2
2.1 Information on environmental protection 9
11snoitcurtsniytefaS3
31noitpircseD4
31noitcurtsnoC1.4
31lenapgnitarepO2.4
31noitcnuF3.4
51snoitcurtsnignitarepO5
51yrettabehtgnigrahC1.5
51lootehtgnitarepO2.5
91laesehtgnikcehC3.5
91egrahcyrettabgnikcehC4.5
5.5 Setting mode of operation 19
12noisnetpartsgnitteS6.5
12noisnettfosgnitteS7.5
12emitgnidlewgnitteS8.5
12htdiw
partsgnitteS9.5
32snoitcnuflaicepS6
6.1 Switch touch-pad lock on and off 23
32edompeelS2.6
32teserlooT3.6
7 Preventive and corrective maintenance 25
7.1 Cleaning/replacing tension wheel 25
7.2 Cleaning/replacing tooth plate 25
52efinkgnicalpeR3.7
72gnitoohselbuorT4.7
8 Wear parts / Recommended spare parts 28
8.1 Parts list 28
23gniwarddedolpxE
DECLARATION OF CONFORMITY
We take sole responsibility for declaring that the tool
OR-T 400 to which this declaration refers is in full
conformity with the current requirements of the
guidelines laid down by the council on 17th May 2006
(2006/42/ECC), “Machine Guidelines“.
Furthermore, electrical installations are in conformity
with the guideline laid down by the council on 12.
December 2006 (2006/95/EEC) “Low Voltage Guide-
lines“ and 15. December 2004 (2004/108/EEC)
“EMV Guidelines“.
Harmonised standards applied:
EN ISO 12100-1, EN ISO 12100-2, EN 349,
EN ISO 14121-1, EN 61000-6-1, EN 61000-6-3
EEC-Design certification: No 1201
Place of certification: NSBIV AG, SIBE CH
CH-8953 Dietikon, 04.09.2009
General Manager General Manager Prod.
Packaging Technology: Packaging Technology:
U. Schweizer M. Binder
H-2386
1-800-295-5510

7
09.09/WE
ORGAPACK OR-T 400
1TECHNICAL DATA
Weight 4.2 kg (9.3 lbs.)
)yrettab.lcni(
Dimensions Length 334 mm (13.1")
mm831htdiW (5.4")
mm841thgieH (5.8")
Strap tension (0) 1200–4000 N (264–882 lbs.)
).sbl353–88(N0061–004:tfoS
Tension speed 175 mm/s (6.9"/s)
Sealing Friction weld
Emission sound pressure
levels, measurement
type A (EN ISO 11202) LpA 79 dB (A)
Vibrations at handle
(EN ISO 8662-1) ah,w 2.2 ms-2
Working temperature –10 °C up to +40 °C
)F°401otpuF°41(
Relative humidity Up to 90 %
BATTERY CHARGER / BATTERY
Battery charger voltage 100 / 110 / 230 V
Battery charger type BOSCH AL 1860 CV
Charging time 20–45 minutes,
%07.xorppanim02retfa
yticapacgnigrahc
Strappings with
one battery charge 180 to 300 depending on
dnanoisnetparts,parts
egakcap
Battery 18 V / 2.6 Ah, Li-Ion
HCSOB
PLASTIC STRAP
Strap quality Polypropylene (PP)
)TEP(retseyloP
Strap width
adjustable to 15–16, 18–19 mm
( 5/8", 3/4")
Strap thickness 0.8–1.3 mm (.030"–.051")
TEP
)"930.–"030.(mm0.1–8.0
PP
H-2386
1-800-295-5510

9
09.09/WE
ORGAPACK OR-T 400
2GENERAL INFROMATION
These operating instructions are intended to simplify fa-
miliarisation with the strapping tool and its proper use for
the intended purpose. The operating instructions contain
important information concerning the safe, proper and
efficient use of the strapping tool.
The operating instructions must always be available at
the place of operation of the strapping tool. They must be
read and observed by all persons working with or on the
strapping tool.
In addition to the operating instructions and the regula-
tions for accident prevention effective in the country of
use and place of operation, the recognised technical
regulations for safety and proper operation must also be
observed.
CAUTION!
Used where there is danger to life and health.
WARNING!
Used for danger which can cause material damage.
NOTE!
Used for general information and information which, if
not followed can cause faults in the operating sequence.
2.1 INFORMATION ON DISPOSAL AND
ENVIRONMENTAL PROTECTION
This tool is manufactured without any physical or chemi-
cal substances which could be dangerous to health.
The legal prescriptions for disposal of all the parts must
be observed. The electrical assemblies should be dis-
mantled so that the mechanical, electro-mechanical and
electronic components can be disposed of separately.
Charger and batteries should be sorted for environ-
mental-friendly recycling.
•Do not open the battery.
•Do not throw the used battery into household waste,
fire or water.
Defective or used batteries undergo a complete recycling
process.
H-2386
1-800-295-5510

arning:
arning:
11
09.09/WE
ORGAPACK OR-T 400
3SAFETY INSTRUCTIONS
Inform yourself!
Read the operating instructions carefull y.
Preventive and corrective maintenance on the tool may
only be carried out by trained personnel.
Protect yourself!
When operating the tool, wear eye, face, hand protection
(cut-proof gloves) and safety shoes.
Power source!
Before starting preventive or corrective maintenance, re-
move battery from the tool. Always inspect the electrical
plug and cable before use. If damaged, they must be
replaced by qualified personnel.
W
Strap will snap forward!
When cutting the strap, hold the upper portion and stand
safely away from the strap.
Caution:
The lower strap will snap forward.
W
Strap could break!
Do not stand in line with the strap while it is tensioned.
The strap could break!
Caution:
Only strap packed goods!
Do not put hands or other parts of the body between the
strap and the package during the strapping process.
Caution:
Danger of crushing!
Do not put your fingers into the tension wheel area.
Do not use water!
Do not use water or steam to clean the tool.
Only original ORGAPACK spare parts may be used!
Using non-original spare parts will void the warranty and
any liability.
Use for the intended purpose
This tool is designed for strapping packages, pallet loads
and the like.
The tool is designed for use with plastic straps (poly-
propylene and polyester).
Possible misuse
The use of steel straps is not possible.
H-2386
1-800-295-5510
ORGAPACK
Original

13
09.09/WE
ORGAPACK OR-T 400
4DESCRIPTION
4.1 CONSTRUCTION
1 Operating panel
2 Tension button “Strap tensioning/welding” (Fully-Auto)
3 Handle
4 Battery, 18 V
5 Rocker lever
6 Welding button “Welding/cutting” (manual)
7 Welding/Cutting
8 Tensioning
9 Battery charger
For detailed information, refer to the operating instruc-
tions for the battery and battery charger.
4.2 OPERATING PANEL
1 LED indicator “Battery charge”
2 Push button “Strap tension”
3 Push button “Function”
4 Push button “Mode of operation”
5 Push button “Welding time”
6 LED indicator “Soft tension”
7 LED indicator “Manual strapping” (continuous
green light)
8 LED indicator for:
– Semi-Automatic strapping (continuous green light)
– Full-Automatic strapping (flashing green light)
9 Digital display for:
– Strap tension (1–9)
– Welding time (1–7)
– Cooling time (count down 3,2,1)
– Fault indication
For detailed information/adjustments, refer to
chapter 5 and 6.
4.3 FUNCTION
– Clamping of the straps by tooth plate on rocker
(3/1).
– Tensioning by feed wheel (3/2) counter clockwise.
– Friction welding (3/3) of the straps.
– Upper strap is cut by knife (3/4).
H-2386
1-800-295-5510
AUTO
MAN.
SOFT AUTO
MAN.
SOFT
+/ -
+/ -
AUTO
MAN.
SOFT AUTO
MAN.
SOFT
+ / -
+ / -
Fig. 1
1 2 3
4
5
6
7
8
9
Fig. 2
Fig. 3
123
4
1
2
3
4
5
6
7
8
9

15
09.09/WE
ORGAPACK OR-T 400
5ORERATING INSTRUCTIONS
5.1 CHARGING THE BATTERY
– Connect battery charger AL 1860 CV (4/2) to mains
supply.
– Insert battery 18 V (4/1) into battery charger slot.
The charging process and error functions are indicated
by a green (4/3) and a red light (4/4).
For detailed information, refer to the operating instruc-
tions for the battery and battery charger.
Charging times:
– First charging of a new battery, min. 5 hr.
– Recharging of empty battery:
approx. 20 to 45 minutes
Continuous lighting of the green LED (4/3)
indicates that the battery is fully charged.
The maximum charging current flows when the tempe-
rature of the battery is between 15–40°C (59–104°F).
Avoid charging the battery at temperatures below 0°C
(32°F) and above 40°C (104°F). Battery can be charged
at any time regardless of charging status!
If the battery is not to be used for a longer
period (several days), it should be remo-
ved from the tool and charged/stored in the battery
charger.
To remove battery from tool, depress button on battery
and at the same time pull out battery.
+
5.2 OPERATING THE TOOL
This description assumes that the
mode of operation is adjusted to
“Semi-Auto” (refer to chapter 5.5).
– Insert charged battery (5/1) into strapping tool.
– Place strap round goods to be packaged, so that the
straps lie one above the other on top of package. The
start of the strap is underneath. Hold the straps with
the left hand so that the strap start projects approxima-
tely 20 cm (8") out of the hand.
AUTO
MAN.+
The operator is responsible for safe strapping and the
correct strap selection for the package, depending on its
dimensions, weight, edges and stability and the way it
will be transported and stored.
Only the strap dimensions specified for the tool type
(page 7) should be used. The tool should be adjusted ap-
propriately for the strap used and the package (chapters
5.6/ 5.8/ 5.9). The operator is responsible for the correct
tool settings.
H-2386
1-800-295-5510
12
34
Fig. 4
Fig. 5
1

16 09.09/WE
ORGAPACK OR-T 400
Fig. 6
1
AUTO
MAN.
SOFT AUTO
MAN.
SOFT
+ / -
+ / -
1
Fig. 8
Fig. 7
1
H-2386
1-800-295-5510
– Take the tool in the right hand and lift the rocker lever
(6/1) towards the handle.
– Slide the straps, one on top of the other, into the tool
up to the stop.
The strap lead is now approximately 5 cm (2“)
beyond the tool.
– Release the rocker lever.
– Press the tension button (7/1) until the preselected
strap tension is reached. The tool switches over
automatically as soon as the strap tension has
been reached. The straps are welded and the
upper strap cut off.
– The tensioning process can be stopped at any time
and continued again. In order to release the strap
tension after the tensioning process, lift the rocker
lever (6/1) towards the handle.
– The strap tension can be adjusted on the operating
panel (see Chapter 5.6).
Tensioning – welding:
To perform welding before the strap has been tensioned,
first switch to operating mode „Manual“. However, the
tensioning button must be pressed once before welding.
– The digital display (8/1) indicates the cooling time of
the sealing. After finishing the friction welding, the
digital display counts backwards (3,2,1). Do not
remove the tool during this time!
Audible signal sounds once:
The sealing cycle is finished.
– After the audible signal sounds, raise the rocker lever
up to the handle.
– Swing the tool away from the strapping backwards and
to the right. If the tool is removed too early, the
audible signal will sound several times.
– Check the seal (refer to chapter 5.3).
Never transport or move packaged goods
with incorrectly welded seals.
If the tool is used in a dirty environment, it is
recommended that it should be cleaned daily. In
particular the tension wheel and the tooth plate should be
checked for damage and kept clean. This is best perfor-
med by blasting with compressed air (wear goggles).

18 09.09/WE
ORGAPACK OR-T 400
1
23
Fig. 9
12
Fig. 11
MAN.
AUTO
MAN.
SOFT
blinkend /flashing /
clignote
AUTO
MAN.
SOFT
AUTO
MAN.
SOFT
AUTO
MAN.
SOFT
1.
2.
AUTO MAN.
+
AUT
O
3 4
5
6
Fig. 10
1
3
2
H-2386
1-800-295-5510
5.3 CHECKING THE SEAL
– Check appearance of seal (see fig. 9) regularly. If the
straps are poorly welded, check the welding time
setting (refer to chapter 5.8).
1 Good seal (the complete surface is cleanly welded
without excess material being forced out sideways).
2 Poorly welded seal (not welded over the complete
surface), welding time too short.
3 Poorly welded seal (excess material is forced out
sideways), welding time too long.
5.5 SETTING MODE OF OPERATION
– Press „Function“ button (11/1) briefly. The digital
display will show „F“ (Function). The present mode of
operation is shown.
– Then press the „Mode of operation“ button (11/2)
briefly until the desired mode of operation is shown.
Semi-Auto strapping (Standard):
Strapping is performed by pressing the tensioning button.
When the strap tension is reached, welding and cutting is
performed automatically.
– Press the „Mode of operation“ button (11/2). When the
„AUTO“ (11/3) and „MAN“ (11/4) LED indicators light
continuous green „Semi-Auto“ mode of operation is
selected.
Fully-Auto strapping:
Strapping is performed by tapping tensioning button.
Tensioning, welding and cutting are performed fully-
automatically.
– Press the „Mode of operation“ button (11/2). When the
„AUTO“ LED indicator (11/5) flashes green „Fully-
Auto“ mode of operation is selected.
Stop of Fully-Auto sequence:
By pressing tension- /welding button or raising rocker
lever.
Manual strapping (manual welding):
Strapping is performed by first pressing the tensioning
button (1.). When the tension is reached, press the
welding button (2.).
– Press the “Mode of operation” button (11/2). When the
“MAN” LED indicator (11/6) lights continous green
“Manual” mode of operation is selected.
5.4 CHECKING BATTERY CHARGE
– Read off battery charge on LED indicator (Fig. 10):
1 = Green indicator: maximum battery charge
2 = Green indicator: good battery charge
3 = Red indicator: empty battery
(Battery must be charged)

20 09.09/WE
ORGAPACK OR-T 400
+ / -
+ / -
Fig. 12
123
=
Fig. 14
123
=
Fig. 15
12 3 4
AUTO
MAN.
SOFT
Fig. 13
12
3
=
AUTO
MAN.
SOFT
AUTO
MAN.
SOFT
AUTO
MAN.
SOFT
A)
1 2 3 4 5 6 7 8 9
1200 1550 1900 2250 2600 2950 3300 3650 4000 N
264 341 418 496 573 650 727 804 882 lbs.
B)
1 2 3 4 5 6 7 8 9
400 550 700 850 1000 1150 1300 1450 1600 N
88 121 154 187 220 253 286 319 353 lbs.
H-2386
1-800-295-5510
5.6 SETTING STRAP TENSION
– Press the „Function“ button (12/1) briefly.
– Press the „Strap tension“ button (12/2) until the
flashing digital display (12/3) shows the required strap
tension. Wait two seconds until the new setting is
saved.
1 = min. strap tension approx. 400/1200 N*
(88/264 lbs.) (PP)
9 = max. strap tension approx. 1600/4000 N*
(353/882 lbs) (PET)
* refer to Chapter 5.7
5.8 SETTING WELDING TIME
– Press the „Function“ button (14/1) briefly.
– Press the „Welding time“ button (14/2) until the
flashing digital display (14/3) shows the required
welding time. Wait two seconds until the new setting is
saved.
1 = minimum welding time
7 = maximum welding time
5.7 SETTING SOFT TENSION
The following two strap tension ranges can
be set on the tool:
A = 1200–4000 N (308–880 lbs.)
standard, PET straps
B = 400–1600 N (88–335 lbs.)
Soft tension*, PP straps
* Soft tension: tension wheel starts slowly. Prevents
excessive dirt on PP straps.
Setting soft tension:
– Press the „Function“ button (13/1) briefly.
– Press the „Mode of operation“ button (13/2) several
times until the green „SOFT“ LED indicator (13/3)
lights up together with the desired mode of operation
(refer to chapter 5.5).
5.9 SETTING STRAP WIDTH
The tool can be used with two different strap
widths:
– 15–16 mm (5/8“)
– 18–19 mm (3/4“)
a) Change strap width from 15–16 mm to 18–19 mm
– Remove battery from tool.
– Release sunk screw (15/2) and remove strap stop
16 mm (15/1).
– Lift the rocker lever towards the handle, release
sunk screw (15/4) and remove strap guide 16 mm
(15/3).
Continuation page 23

22 09.09/WE
ORGAPACK OR-T 400
Fig. 16
12
3
4
5
7
6
AUTO
MAN.
SOFT
2
=
Fig. 18
1
blinkend /flashing /
clignote
AUT
O
Fig. 17
1
+ =
2 3
H 2386
1-800-295-5510
– Remove three cylinder screws (16/2).
– Lift the rocker lever towards the handle, remove cylin-
der screw (16/4) together with the strap stop rear
16 mm (16/3).
– Remove cover (16/1).
– Remove oval head screw (16/7) and remove strap
guide rear 16 mm (16/6) from lever.
– Install cover (16/1).
– Mount strap stop rear 19 mm (16/5).
b) Change strap width from 18–19 mm to 15–16 mm
– Mount 16 mm strap stop (15/1) and secure sunk
screw (15/2) with Loctite 222.
– Mount 16 mm strap guide (15/3) and secure sunk
screw (15/4) with Loctite 222.
– Remove strap stop rear 19 mm (16/5).
– Remove three cylinder screws (16/2) and remove
cover (16/1).
– Mount strap guide rear 16 mm (16/6).
– Install cover (16/1).
– Mount strap stop rear 16 mm (16/3).
6.1 SWITCH TOUCH-PAD LOCK ON AND OFF
The touch-pad lock can be activated to prevent acciden-
tal changes to the settings.
– Press and hold the “Function“ button (17/1) and press
the tension button (17/2) at the same time. The audible
signal sounds and the keypad is blocked. If any key is
pressed, the digital display will show „L“ (Lock) (17/3).
– The keypad block is released in the same way as it is
activated.
6SPECIAL FUNCTIONS
6.3 TOOL RESET
The tool reset may be used only if the rocker lever is
blocked:
– Change to mode of operation „Fully-Auto strapping“
(refer to Chapter 5.5).
– Press and hold welding button (18/1) and press
tension button (18/2). Tool reset starts (approx.
0.5 sec. welding).
If the tool reset could not successfully carried out,
please contact the Service Centre!
6.2 SLEEP MODE
In order to avoid unnecessary battery consumption, the
tool changes after approx. 5 min. to sleep mode, if no
key is pressed.
– The digital display and the LED indicator are switched
off.
Sleep mode is switched off by touching any operating
panel element.

H-2386
1-800-295-5510
24 09.09/WE
ORGAPACK OR-T 400
Fig. 19
1
34
2
5
Fig. 20
2
1
Fig. 21
3
2
1
6
4
5
7PREVENTIVE/CORRECTIVE MAINTENANCE
7.1 CLEANING/REPLACING TENSION WHEEL
Removal
– Remove battery from tool.
– Remove four cylinder screws (19/4) and remove strap
stop rear (19/5) and cover (19/3).
– Remove tension wheel (19/1) carefully. Remove ball
bearing (19/2) from tension wheel.
– Clean the tension wheel with compressed air (wear
goggles).
– If the tension wheel teeth are covered with heavy dirt,
they must be carefully cleaned with the wire brush
supplied.
– Check tension wheel for worn teeth. If a few teeth
are broken, replace tension wheel (observe rotating
direction, see arrow)
The tension wheel must not be cleaned
while it is rotating. There is a risk of
breaking teeth!
Installation
– Install the parts in reverse order.
– Grease gear teeth of tension wheel lightly with
Klüber grease GBU Y 131 (Microlube).
7.2 CLEANING/REPLACING TOOTH PLATE
Removal
– Remove battery from tool.
– Remove pan head screw (20/1). Lift the rocker lever
towards the handle and remove tooth plate (20/2).
– Clean tooth plate with compressed air (wear goggles).
– If the tooth plate teeth are covered with heavy dirt,
they must be carefully cleaned with the wire brush
supplied or a sharp tool.
– Check tooth plate for worn teeth, if necessary replace
tooth plate.
Installation
– Install the parts in reverse order.
– Secure pan head screw (20/1) with Loctite 222.
– The tooth plate (20/2) must be seated so it can move
freely in the rocker.
7.3 REPLACING KNIFE
Removal
– Remove battery from tool.
– Remove four cylinder screws (21/2) and remove strap
stop rear (21/3) and cover (21/1).
– Release panhead screw (21/4) and remove knife
(21/6) with flanged bushing (21/5). Replace knife.
Installation
– Install the parts in reverse order.
– Before installing knife, check that the compressing
spring on top of knife is still mounted.
– Secure panhead screw (21/4) with Loctite 222.

26 09.09/WE
ORGAPACK OR-T 400
E +
E11
E20
E22
E23
E37
FAULT
H 2386
1-800-295-5510
7.4 TROUBLE SHOOTING
If a malfunction occurs, the digital display blinks and
displays error “E” followed by the error number.
FAULT:
Rocker lever was operated before the cooling-down
period had elapsed.
ACTION:
– Operate the rocker lever only when the cooling-down
period has elapsed..
FAULT:
The battery used is not the right type.
CAUSE:
– Wrong battery.
ACTION:
– Use the correct battery.
– Restart by removing/replacing the battery.
FAULT:
Battery too hot.
CAUSE:
– Battery temperature above 60°C.
ACTION:
– Let the battery cool down.
– Replace the battery.
FAULT:
Motor overload protection.
CAUSE:
– The motor was overloaded.
ACTION:
– Let the motor cool down.
FAULT:
Battery discharged.
CAUSE:
– The lowest charge limit of the battery has been
reached.
ACTION:
– Charge/replace the battery.
FAULT:
Rocker lever is blocked.
CAUSE:
– Tool blocks when welding.
ACTION:
– Refer to chapter 6.3 or by Service Centre.
For other error numbers not described here,
please contact the Service Centre.
Other Orgapack Tools manuals
Popular Tools manuals by other brands
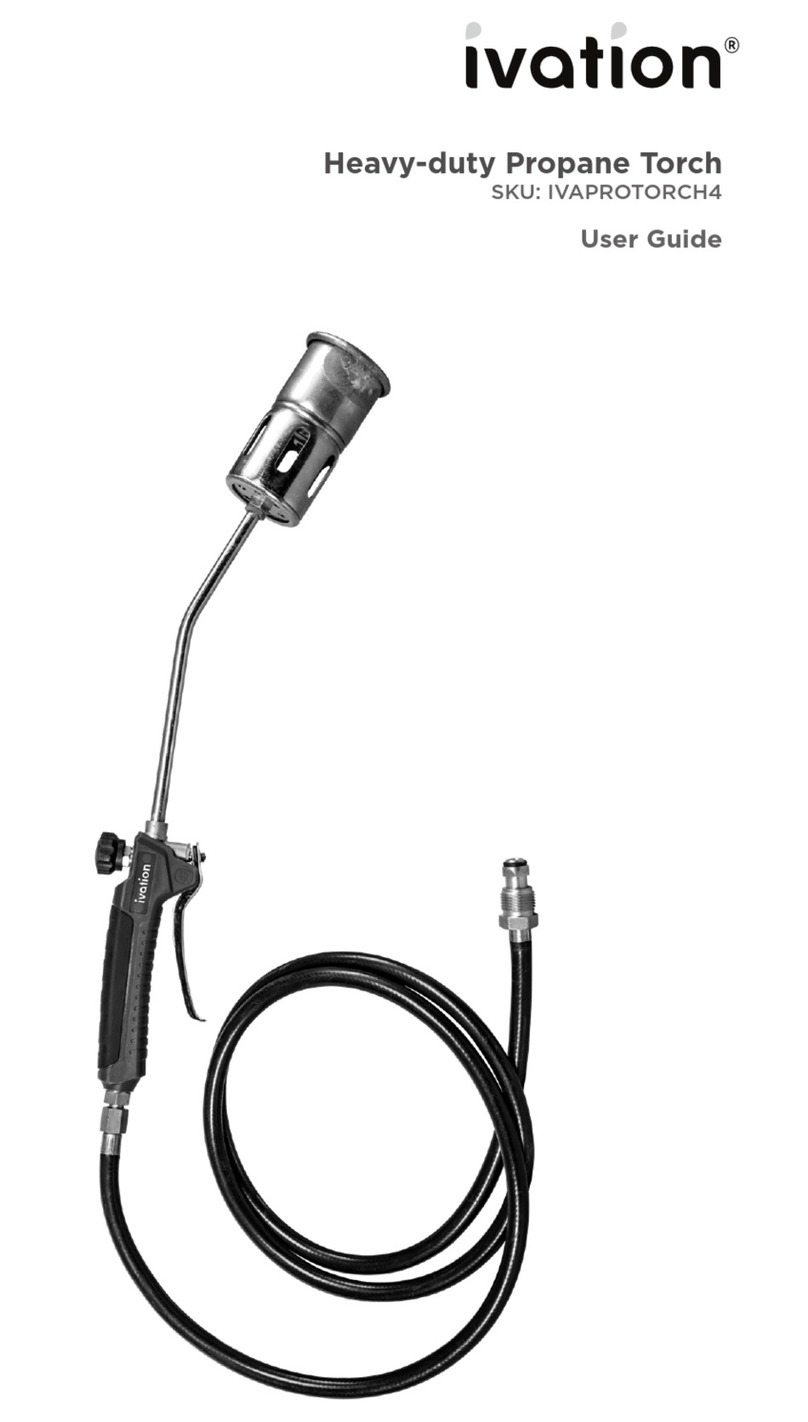
C&A IP Holdings
C&A IP Holdings Ivation IVAPROTORCH4 user guide

wagner solar
wagner solar EURO 20/22 installation instructions

Oneida Air Systems
Oneida Air Systems AHR000025 instruction manual

Axminster
Axminster Woodturning Deluxe Pen Press instructions
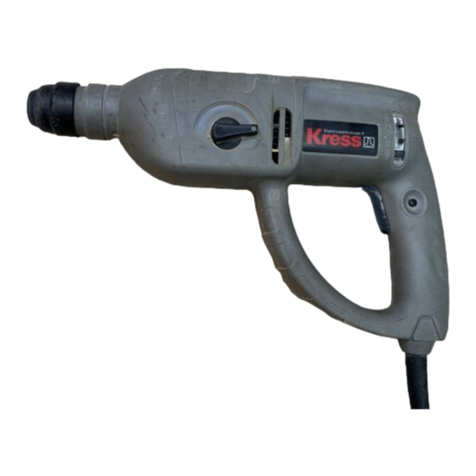
KRESS
KRESS PK 450 HM operating instructions
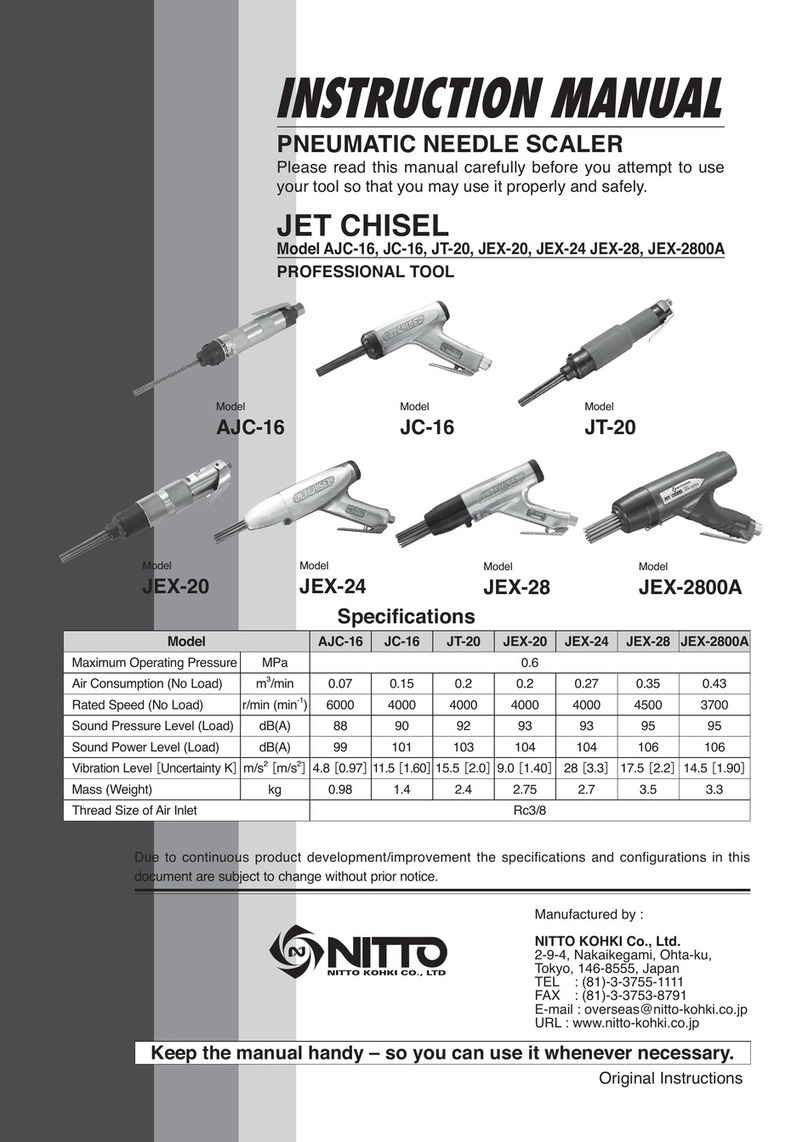
Nitto Kohki
Nitto Kohki JET CHISEL AJC-16 instruction manual