Palax KS 50s User manual

OPERATING INSTRUCTIONS
PALAX KS 50s
powered by tractor
powered by electricity
swing conveyor of 4.0-metres with hydraulic
motor
SERIAL NUMBER
_______________________
YEAR OF MANUFACTURE
_______________________
Palax
Lahdentie 9
FI-61400 Ylistaro, FINLAND
Tel. +358 6 4745100
Fax. +358 6 4740790
www.palax.fi

Palax KS50s Translation 1-2012
II

Palax KS50s Translation 1-2012
III
CONTENTS
1 Basic specifications and responsibilities...................................................................1
1.1 Foreword...........................................................................................................1
1.2 EU Declaration of Conformity..........................................................................2
1.3 Intended use of the machine..............................................................................4
1.4 Warning signs ...................................................................................................4
1.5 Instruction signs................................................................................................4
1.6 Signs for operating controls..............................................................................5
1.7 Type markings...................................................................................................6
1.8 The main dimensions and models of the machine............................................7
1.9 Safety instructions.............................................................................................7
1.10 Noise emission and vibration............................................................................8
1.11 Responsibilities of the operator.........................................................................8
1.12 Operating conditions.........................................................................................8
1.13 Terms of warranty.............................................................................................9
2 Taking delivery and assembly of the machine..........................................................9
2.1 State of delivery and acceptance control...........................................................9
2.2 Main parts of the machine, Figs. 2.1, 2.2, 2.3 and 2.4....................................10
2.3 Installing the winch, Figure 2.5 ......................................................................12
2.4 Topping up hydraulic oil, Fig. 2.6...................................................................12
2.5 Checking and topping up the saw-chain oil, Fig. 2.7......................................12
2.6 Bringing the discharge conveyor into the work position, Figures 2.8-2.10....13
2.7 Bringing the conveyor into the transport position ..........................................14
2.8 Bringing the in-feed conveyor to the work position, Fig. 2.1.........................14
2.9 Changing the splitting wedge, Fig. 2.11 .........................................................14
2.10 Lifting and moving the machine, Figures 2.12, 2.13, 2.14.............................15
3 Driving power .........................................................................................................15
3.1 Powered by a tractor........................................................................................15
3.2 Selecting the operating mode: powered by tractor or electricity (Figures 3.1
and 3.2) ..........................................................................................................16
3.3 Electric drive, start and emergency stop.........................................................16
3.4 Starting ..........................................................................................................17
3.5 Emergency stop of an electric-motor-powered machine ................................17
3.6 Starting the electric motor in frost ..................................................................17
4 Using the firewood processor, description of operation .........................................18
4.1 Operating controls, Fig. 4.1 and 4.2................................................................18
4.2 Setting up the machine for operation..............................................................18
4.3 Adjusting the log length, Fig. 4.2....................................................................19
4.4 How the safety devices affect the operation of the machine, Figure 4.4........19
5 Use of the firewood processor, crosscut operation .................................................20
5.1 During the operation .......................................................................................20
5.2 Placing the wood on the deck .........................................................................20

Palax KS50s Translation 1-2012
IV
5.3 Crosscut operation...........................................................................................21
5.4 Disturbances during crosscut operation and their remedy..............................21
6 Use of the firewood processor, splitting operation .................................................22
6.1 Splitting speed and force.................................................................................22
6.2 Splitting wedges..............................................................................................22
6.3 Flap, Fig. 6.1 ...................................................................................................22
6.4 Disturbances during the splitting operation and their remedy........................23
6.5 Re-splitting the logs safely..............................................................................23
7 Operation of the splitting mechanism.....................................................................23
7.1 Automatic start, Fig. 7.1..................................................................................24
7.2 Manual start.....................................................................................................24
7.3 Parts of the splitting valve, Figure 7.2 ............................................................24
8 Maintenance of the machine ...................................................................................24
8.1 Crosscut saw-blade..........................................................................................24
8.1.1 Changing and tightening the saw-chain, Figures 22 and 23..............24
8.1.2 Servicing the saw-chain.....................................................................25
8.1.3 Servicing the saw-bar.........................................................................26
8.2 Changing the angular gear oil, Fig. 8.2...........................................................26
8.3 Lubricating the machine..................................................................................26
8.4 Coupling for electric motor, Fig. 28 ...............................................................26
8.5 Oil change .......................................................................................................27
8.6 Maintenance of the valve................................................................................27
8.7 Detent end of valve .........................................................................................27
8.8 Lubricating the spool shifter ...........................................................................28
8.9 Structure of the detent end and the correct order of the parts, Fig. 8.7...........28
8.10 Basic settings of the splitting valve.................................................................29
8.11 Adjusting the end stopper for the launch rod..................................................30
8.12 Adjusting the launch lever pusher gap............................................................30
8.13 Adjusting the start moment of splitting...........................................................30
8.14 Adjusting the safety devices ...........................................................................31
8.14.1 Adjusting the safety wedge and the safety shaft................................31
8.14.2 Adjusting the safety rod for the saw-shaft.........................................31
8.14.3 Centring lever for the splitting valve.................................................32
8.15 Discharge conveyor.........................................................................................33
8.16 Adjusting the pusher clearance .......................................................................33
8.17 Cleaning the machine......................................................................................33
8.18 Washing the machine......................................................................................34
8.19 Storing the machine.........................................................................................34
9 Maintenance schedule.............................................................................................35
10 Malfunctions and their remedy...............................................................................35
11 Electric diagrams.....................................................................................................38

Palax KS50s Translation 1-2012
1
1 BASIC SPECIFICATIONS AND
RESPONSIBILITIES
1.1 Foreword
This Instruction Manual is intended for a professional operator of the machine.
The operator must have usual general knowledge and skills. For example, the
buyer of a tractor-powered machine is expected to master the use of power
take-off shaft transmission.
Before the installation and operation, the operator of the machine must become
thoroughly familiar with the contents of the manual. The operator is also obliged
to gain familiarity with the operating controls of the machine and the emergency
stop mechanism.
NOTE! Keep this manual with the machine at all times.

Palax KS50s Translation 1-2012
2
1.2 EU Declaration of Conformity
Directive 2006/42/EC
Manufacturer: Ylistaron Terästakomo Oy
www.palax.fi
Lahdentie 9
FI-61400 Ylistaro
Finland
+358 6 474 5100
Product: Palax KS 50s Firewood Processor with discharge conveyor
of 4 m.
Powered by: Tractor PTO. or electric motor
Models: TR Powered by tractor equipped with own
hydraulic system
TR/SM Powered either by tractor or electric motor
SERIAL NUMBER _______________________
We hereby certify that the machine meets the requirements of the Government
Decree 12.6.2008/400 on safety of machinery through which the Machine
Directive 2006/42/EC has been put into effect, and that during the
manufacturing process the following harmonized standards have been applied.
SFS-HANDBOOK 93-series, SFS-EN 349-1+A1, SFS-EN 609-1+A1,
SFS-EN 618, SFS-EN 620, SFS-EN 953+A1, SFS-EN 954-1, SFS-EN
982+A1, SFS-EN 4254-1, SFS-EN 11684, SFS-EN 12100-1+A1, SFS-
EN 12100-2, SFS-EN 13850, SFS-EN 13857, SFS-EN 14121-1, SFS-EN
14121-2 SFS-EN 60204-1+A1.
Ylistaron Terästakomo Oy
29.12.2009

Palax KS50s Translation 1-2012
3
Martti Vaurio
Managing Director

Palax KS50s Translation 1-2012
4
1.3 Intended use of the machine
This Firewood Processor with Conveyor is intended for the purpose of
producing firewood primarily of round timber, but of logs as well.
Use of the machine for any other purposes is prohibited.
Note! Max. capacity of the machine
For cutting, the maximum diameter of the tree is about 48 cm.
The maximum length of the log to be processed is 4–5 metres. If the logs
are longer than this, a log-deck shall be used
1.4 Warning signs
Read the
instruction
manual
Beware of
the crosscut
saw-bar
Wear
clothes,
which do
not hang
loosely
Always use
eye guards
and hearing
protectors
Wear safety
shoes
Risk of
getting
squeezed
Beware of power take
-
off shaft
Disconnect the
machine from the
electric supply before
taking to any service
measures

Palax KS50s Translation 1-2012
4
Safe distance from the conveyor 5 m
Stay away from moving
parts
The machine may only be operated by one
person
1.5 Instruction signs
Lifting point, for a
forklift truck
Lifting point, hook
Direction of rotation of
the motor
Rotational speed of the
PTO-shaft
Saw
-
chain oil tank
Adjustment of oil flow
to the saw-chain

Palax KS50s Translation 1-2012
5
1.6 Signs for operating controls
Sideways adjustment of the
discharge conveyor
Height adjustment of the discharge
conveyor
Starting and stopping
the discharge
conveyor belt
Height adjustment of
the splitting wedge
Emergency stop, only
in machines powered
by electricity
Manual start of the
splitting cylinder
/
Reversing the
pusher
Stopping the splitting
/
Automatic splitting

Palax KS50s Translation 1-2012
6
Automatic splitting ON
OFF
Lifting the hydraulic
log-clamp
Controlling the in
-
feed conveyor and cutting
operation as well as automatic launch of the
splitting
Bringing the log onto
the in-feed rollers
using the hydraulic
log-deck
Flap not in use/Manual
use of the flap
Flap not in use
1.7 Type markings
Nameplate on the machine
The name and address of the manufacturer
Designation of the machine type
Serial number and year of manufacture
Total weight of the machine
The sign is located at the same end of the
machine as the in-feed conveyor.
Always mention the serial number and year
of manufacture when ordering spare parts.
Nameplates on the electric drive
3-phase motor
Voltage 230/380 V or 380/600 V, may vary depending on the country.
Output 15 kW, current 32A.

Palax KS50s Translation 1-2012
7
The sign is located in the connecting box of the electric motor.
1.8 The main dimensions and models of the machine
Item Powered by tractor TR /operated by
electricity
Output - 15 kW
Fuse size - 32 A
Weight 2,000 kg 2,100 kg
Height/width/length 2600 mm x 3300 mm x 1800 mm
Crosscut deck Length 2550 mm
Height of crosscut deck 1,040 mm
Saw-bar length 22”
Saw-chain Gauge 1,6 mm; pitch 0,404”; 75 links
Max. diameter of the tree 48 cm
Max. length of tree, splitting 660 mm
1.9 Safety instructions
General regulations and restrictions
The maximum length of the log to be cut is 4–5 metres. A log-deck shall be
used for longer logs.
The machine is exclusively intended for the production of firewood.
The machine is about 3.3 metres wide, which means its transport width is
slightly greater than that of the tractor.
The machine may only be operated by one person.
The danger zone around the conveyor is 5 metres to the sides and to the
rear.
Before transporting, always swing the extension table of the in-feed
conveyor into the upright position, and lock it there.
The three-point linkage of the tractor is of size-category two. If using a
tractor larger in size, check that there is sufficiently space for the PTO-shaft
and its protective guard.
Never use the machine indoors, risk of dust generation!
Never remove any safety-related devices from the machine.
The operator
Every person operating the machine, must thoroughly study the entire user
manual.
Always use eye guards and hearing protectors.
Always wear protective shoes.
Always wear work gloves.
Do not wear loosely-fitting clothing.
Before use
Make sure that all other people stay outside the operating range.
Always hitch the tractor-driven machine to the three-point linkage. Also
ensure that sufficient space is provided for the PTO-shaft and its guard.

Palax KS50s Translation 1-2012
8
Only use a fault-free power take-off drive shaft and attach the chain for the
shaft-guard. The rotational speed of the PTO-shaft is 450–500 r.p.m.
Only operate the machine on a sufficiently firm and level surface.
Only operate the machine in an adequately lit space.
Always check that all the covers are intact and properly fastened.
Always check that the crosscut saw-bar is intact.
Always ensure that the electric conductors are intact.
Always check that all the controls are operational.
Always check the oil level and that the hydraulic hoses and components are
undamaged.
Before starting the work, make sure that the machine is firmly in position.
During operation
Carelessness during the cut-off operation constitutes a major hazard.
During the cut-off operation, make sure that the log is always supported by
the cut-off deck at the cutting point. Danger of rolling over!
Exercise particular caution when cutting knotty or crooked logs, because, as
a result of faulty cutting, the log might roll over or twist the saw-bar with
enough force to break it.
Keep the working space clean and clear of foreign objects.
Always stop the machine before servicing.
Only cut one log at a time.
Danger! Stay away from moving parts.
1.10Noise emission and vibration
Equivalent continuous A-weighted sound-pressure level at the workstation is
89.5 dB (A) and the sound power level is 100.5 dB (A).
The vibration emission values do not exceed the limit 2.5m/s2.
1.11Responsibilities of the operator
All the safety-related devices are necessary to ensure a sufficient level of
safety.
The machine operator is responsible for the flawless operation of the safety-
related devices and for ensuring that the machine is serviced in a due
manner.
Modifying the construction of the machine is prohibited.
The machine may only be used to produce firewood.
The operator is responsible for ensuring that no one else is subjected to any
danger.
As the operator, remember that you are responsible for any injuries caused
if any safety-related devices have been removed from the machine or if its
operation has been modified in any way.
The KS 50s is a very safe machine provided that it is operated carefully
following the instructions and that it is serviced regularly.
1.12Operating conditions
Always place the machine on as level a surface as possible.

Palax KS50s Translation 1-2012
9
Prevent risks, such as slipping in winter, by organising the work sit–e in a
due manner.
Only operate the machine in an adequately lit space.
It is recommended that a suitable stand be purchased or made that enables
the trees to be processed where the logs are ready at the level of the in-feed
deck. Hence, unnecessary lifting may be avoided and the work can proceed
much faster.
The suitable temperature range for operation is approximately -20 to +30
degrees Centigrade. When starting the machine in severe frost, first allow it
to idle at low speed for about 5 to 10 minutes. This way, the oil warms up
and flows better, so risk of damage to the seals is reduced.
No restrictions concerning the weather apply.
Make sure that no other people, especially children, are present inside the
operating range.
Never use the machine indoors, risk of dust generation!
1.13Terms of warranty
The warranty period runs for 12 months from the date of purchase.
The warranty covers
Parts, damaged during normal operation of the machine due to defects in
material or workmanship.
The reasonable repair cost in accordance with the agreement between
the seller and the manufacturer or the buyer and the manufacturer.
A new part delivered as a replacement for the defective one.
The warranty does not cover
Defects due to normal wear, faulty operation or negligent maintenance.
The saw-bar, the saw-chain, the sprocket, the conveyor belts or oils.
Defects in the machine due to any modifications which the buyer has
made or ordered from a third party and which have affected the machine
in such a way that it can no longer be considered to correspond to its
original configuration.
Other possible expenses or financial demands due to the above-
mentioned measures.
Any indirect costs and/or travel expenses incurred from making repairs
under the guarantee.
The warranty for parts changed during the warranty period, expires at the
same time as the warranty period of the machine.
Consult your dealer about matters related to the warranty.
2 TAKING DELIVERY AND ASSEMBLY OF THE
MACHINE
2.1 State of delivery and acceptance control
❒
The machine is delivered almost ready-assembled, adjusted and test driven.

Palax KS50s Translation 1-2012
10
❒
Check the delivered goods without delay.
❒
If the product shows transport damage, contact the transport company and
your dealer immediately.
2.2 Main parts of the machine, Figs. 2.1, 2.2, 2.3 and 2.4
1 Discharge conveyor
2 Winch
3 Cover for splitting area
4 Blade cover
5 Control panel
6 Controls for the starting, stopping and emergency stopping of a machine
powered by electricity
7 In-feed conveyor
8 In-feed conveyor extension
9 Connectors for external hydraulic circuit (log-deck)

Palax KS50s Translation 1-2012
11
10 splitting wedge
11 Flap
12 Log-length limiter
13 Crosscut saw-blade
14 Log-clamp
15 Saw-chain oil tank
16 Log-stop
17 Hydraulic oil tank
18 Oil cooler (optional)
19 Adjustment of oil flow to the saw-chain
20 Exit opening for sawdust
21 Electric socket
22 PTO- shaft
23 Electric motor
24 Three-point linkage

Palax KS50s Translation 1-2012
12
2.3 Installing the winch, Figure 2.5
The machine is equipped with a winch for
changing the splitting wedge and manoeuvring the
in-feed conveyor extension.
The winch is delivered separately with the
machine.
Lower the peg at the lower end of the winch
support (1) into the socket (2) in the winch lug.
Fasten the winch support to the socket using the
screw and the washer (3) that were delivered with
the winch.
2.4 Topping up hydraulic oil, Fig. 2.6
The volume of hydraulic oil is 120 litres.
Oil type Univis 32, SHELL Tellus 32, NESTE
HYDRAULI 32 or equivalent.
Only use fresh, clean oil, because smooth
operation of the machine is highly dependent
on the purity of the oil.
Check the oil level regularly by means of the
dipstick 2.
2.5 Checking and topping up the saw-chain oil, Fig. 2.7
The oil tank for the saw-chain is located in the saw
housing at the rear of the machine.
Regularly check the level of the saw-chain oil in the
level hose 1.
Top up the oil, as necessary. The volume of the tank
is about 9 litres.

Palax KS50s Translation 1-2012
13
2.6 Bringing the discharge conveyor into the work position,
Figures 2.8-2.10
Bringing the conveyor into the work position, adjusting it while in the work
position or lifting it into the transport position shall be carried out in such a
manner that that neither the machine, nor the persons or the environment
will be exposed to danger or damage.
Never stand or walk under the conveyor while it is in the upper position!
1. Make sure that the control lever for the conveyor’s drive motor is in the
STOP-position, which means the conveyor belt is immovable.
2. Lower the conveyor using the control lever on the control panel.
3. Lift up the extension, point A, Fig. 2.8.
4. Lower the extension, point B, Fig. 2.8.
5. The holder (1) at the centre of the conveyor prevents the conveyor belt
from lowering of itself into the transport or storing position. Remove the
split cotter (2) that locks the holder while the conveyor is in the horizontal
position. Turn the holder parallel with the conveyor and lock it in position
using the split cotter.
6. Lift up the conveyor to an angle of about 45 degrees.
7. Lock the extension of the conveyor using the lock at the bottom of the
conveyor.
8. Start the discharge conveyor using the control lever on the control panel.

Palax KS50s Translation 1-2012
14
2.7 Bringing the conveyor into the transport position
1. Bringing the conveyor into the transport position is done in the same
manner as bringing it into the work position, but in reverse order.
2. NOTE! Only lift the conveyor when it has been swung to the centre
position! When it is lifted up, the conveyor must always be in the centre
position. If the conveyor is in a swung position while lifted up, it may hit
the surrounding structures and get damaged.
2.8 Bringing the in-feed conveyor to the work position, Fig. 2.1
1. Transfer the loop of the winch to the
hole in the plate of the conveyor's
extension part.
2. Keep the wire rope tight.
3. Release the lock bolt.
4. Lower the extension part by means
of the winch so that the holes in the
support leg pipe align with the holes
in the support legs.
5. Release the winch hook from the in-
feed conveyor.
6. Bringing the extension part of the
in-feed conveyor to the transport
position proceeds in the reverse
order.
2.9 Changing the splitting wedge, Fig. 2.11
As standard, the machine comes with a splitting wedge that splits in 8 ways.
In addition, splitting wedges that split in four, six, eight or twelve ways are
available as an option.
To change the splitting wedge, proceed as follows:
1. Undo the locking screw of the splitting wedge rail.
2. Bring the splitting wedge to its most extreme vertical position using the
height adjustment lever on the control panel.
3. Open the splitting cover completely: When
opening the cover, the gas spring thrusts the
cover to its normal open-position. After this,
open the cover completely with your hand so
that the cover turns away from over the
splitting wedge.
4. Twist an eye-bolt into the hole in the upper
surface of the splitting wedge.
5. Attach the wire rope of the winch to the loop
of the eye-bolt and lift away the splitting
wedge.
6. Lower the replacement splitting wedge onto
its rails by means of the winch. Make sure
that the splitting wedge is set in its upper
position.

Palax KS50s Translation 1-2012
15
7. As soon as the splitting wedge has been lowered and is supported only
by the lifting mechanism, release the wire rope of the winch.
8. Lower the splitting wedge, and ensure that it is connected to the lifting
mechanism of the wedge.
9. Remove the eye-bolt from the upper part of the splitting wedge. The eye-
bolt and the splitting wedge may become damaged, if the log to be split
partly goes above the upper surface of the splitting wedge.
10.Redo the locking screw of the splitting wedge rail.
.
2.10Lifting and moving the machine, Figures 2.12, 2.13, 2.14
L
ifting the machine is allowed:
With a forklift truck, by the lifting points
A under the machine's frame.
By the lifting points B and C on the
upper part of the machine.
When moving the machine by tractor,
ensure that the transfer/lifting capacity
of the tractor is sufficient with respect
to the machine’s weight.
3 DRIVING POWER
The Palax KS 50s Firewood Processor can be driven both by tractor and by
electric motor.
3.1 Powered by a tractor
Always connect the machine to the tractor’s three-point linkage and ensure
that the space reserved for the PTO-shaft and its guard is sufficient.
Table of contents
Other Palax Log Splitter manuals
Popular Log Splitter manuals by other brands
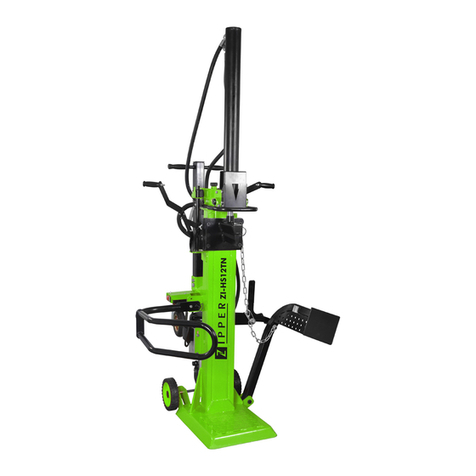
Zipper Mowers
Zipper Mowers ZI-HS10TN user manual
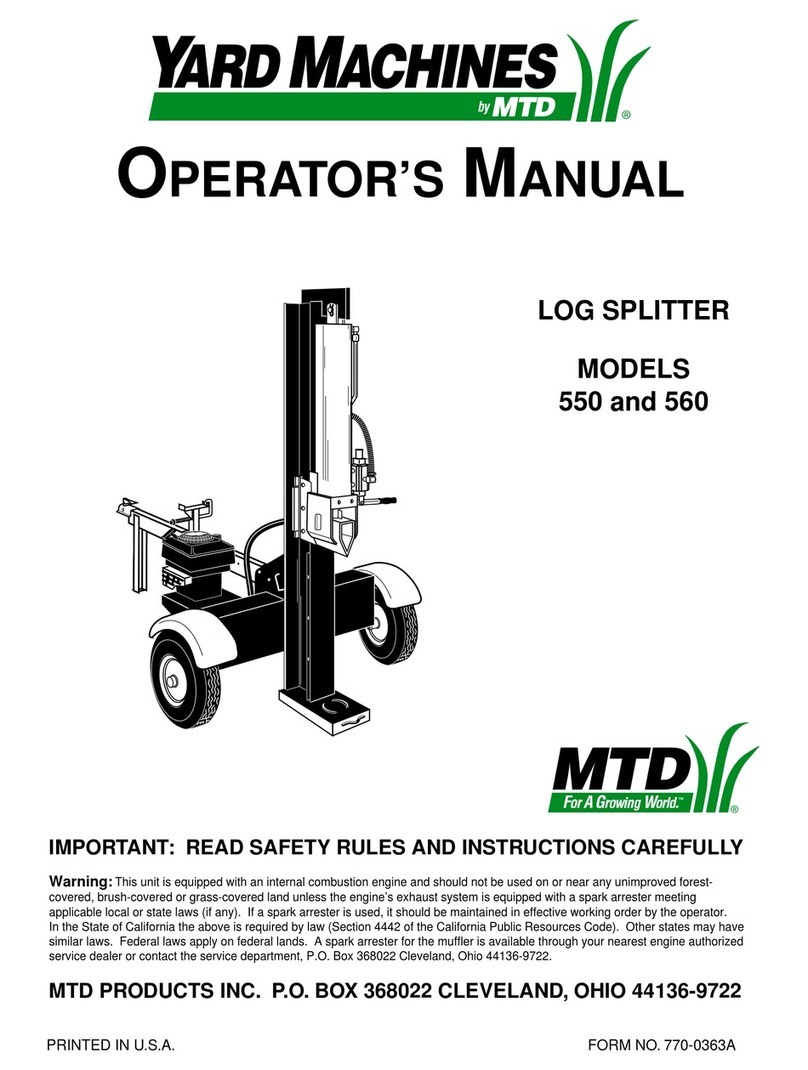
Yard Machines
Yard Machines 550 Operator's manual
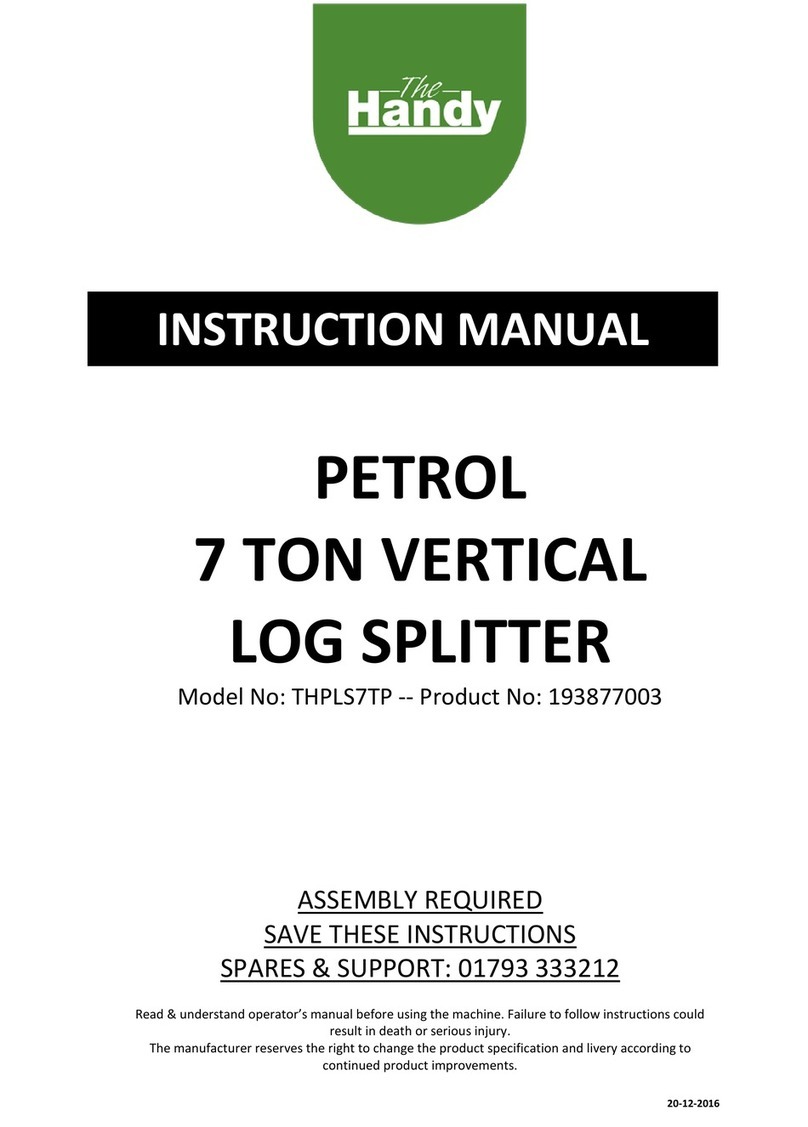
The Handy
The Handy THPLS7TP instruction manual
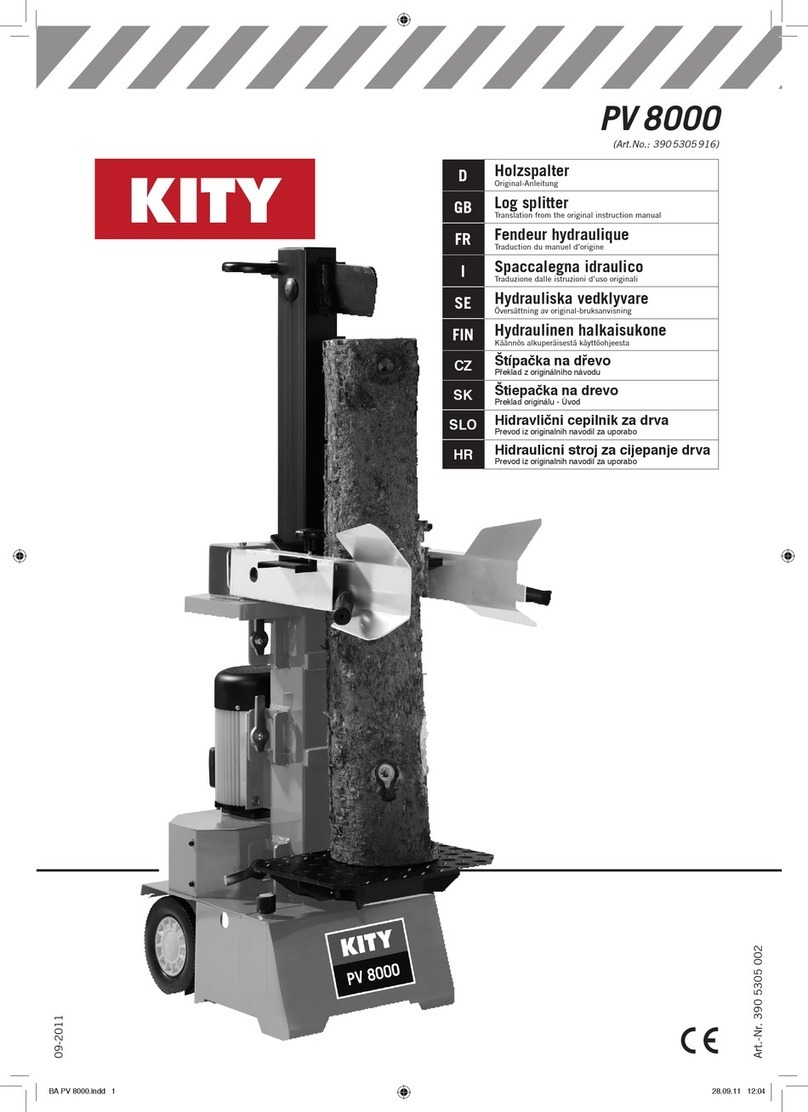
Kity
Kity PV 8000 Translation from the original instruction manual
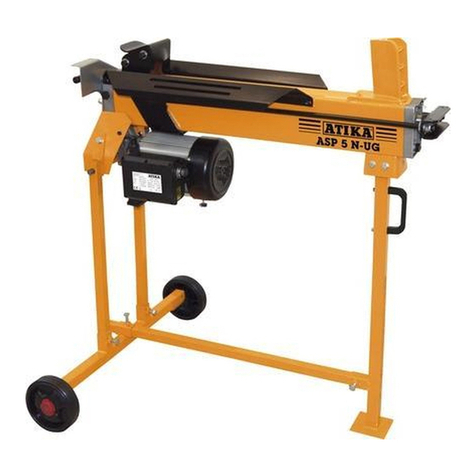
ATIKA
ATIKA ASP 5 N-UG Original instructions, safety instructions, spare parts
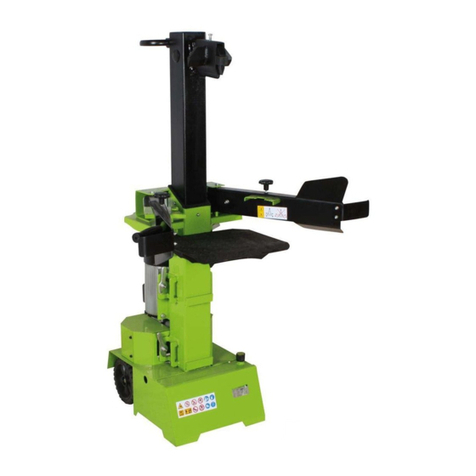
Zipper Mowers
Zipper Mowers ZI-HS8 manual