ParTech ASLD 2200 Monitor User manual

INSTRUCTION MANUAL
ASLD 2200 Monitor
Sludge Blanket Level Monitor
Partech (Electronic ) Ltd
Charle town, St Au tell
Cornwall, PL25 3NN, UK
Phone: +44 (0) 1726 879800
Fax: +44 (0) 1726 879801
email: ale @partech.co.uk web ite: www.partech.co.uk

ASLD 2200 Monitor Instruction Manual Tel +44 (0)1726 879800
Contents
Introduction...................................................................................................................................3
Principle of Operation...................................................................................................................4
Sen or Selection............................................................................................................................5
Control and Setting ....................................................................................................................6
In tallation.....................................................................................................................................8
Configuration..............................................................................................................................10
Calibration...................................................................................................................................12
Scraper Clearance.......................................................................................................................13
Output ........................................................................................................................................14
Maintenance................................................................................................................................15
Fault Finding...............................................................................................................................16
Spare Part ..................................................................................................................................18
Technical Specification...............................................................................................................19
Technical Support.......................................................................................................................20
Declaration of Conformity..........................................................................................................21
Issue: 6 Docu ent Reference: 103370IM
Issue Date: 02/12/2008 Page 2

Introduction
General
The ASLD 2200 i de igned to monitor the po ition of a ludge blanket in a ettlement tank.
The y tem u e an infrared gap type en or to earch for and then track, the interface between
the ludge and the water.
Thi information i then provided via both an LED di play and a 4-20 mA output ignal.
Output Signal
The ASLD 2200 provide a 4-20 mA output ignal that i proportional to the location of the top
of the ludge blanket. With a normal etup the 4mA value relate to the bottom of the tank and
20 mA to the water urface.
Sensors
The ASLD 2200 Monitor can be u ed with the Soli-Tech 20 en or, minor modification will
allow u e with the older IR en or erie .
The function of the ASLD 2200 i identical for Soli-Tech 20 and IR Sen or . Reference to IR
en or are retained to allow thi manual to be compatible with older unit .
Manual Conventions
The manual ha been written on the ba i that the u er ha a ba ic knowledge of in trumentation
and an under tanding of the type of mea urement being made. Training in the u e of the ASLD
2200 Monitor can be provided by Partech, plea e contact ale for further information.
Introduction Page 3

Principle of Operation
The ASLD 2200 u e a Su pended Solid en or to detect the den ity of the ludge; the
in trument move the en or to a point that i ju t above the interface. The motor i then u ed to
keep the en or in that po ition when the interface move .
The u er i provided with information about the en or reading by the panel of LED’ on the
circuit board.
The output of the en or i divided a hown in the graph below:
The ‘motor’ LED’ will come on once the related en or LED ha been on for 5 econd and
the motor will activate.
The ‘limit ’ LED’ will be u ed when the y tem reache either 0 or 100%
The 3 digit LED di play will indicate the po ition of the ludge blanket a a percentage of the
depth of the tank. For example if the tank i 4 metre deep and the di play i howing 25%, the
ludge blanket i 1 metre from the bottom of the tank.
Controls and Settings Page 4
high
up
top
en or
motor
limit
low
down
bottom
Su pended Solid
Sen or
Output
Both
LED’ OFF
Sen or high LED
ON
Sen or Low
LED ON

Sensor Selection
The ASLD 2200 i upplied with a Soli-Tech 20 en or; the correct en or hould have been
elected before purcha e. If you are in any doubt about the en or that ha been upplied plea e
contact Partech.
Sen or replacement in the field i ea y to carry out; the table below indicate the normal
application of the each of the four en or range .
Sensor Ranges
Soli-Tech 20 range 0-200
Thi en or i normally u ed for Su pended Solid mea urement and i not normally applied to
Sludge Blanket mea urement. The en or hould only be u ed if the ludge i very ‘light’ with
very clear upernatant.
Equivalent IR Serie Sen or: IR100
Soli-Tech 20 range 0-1500
Thi i the mo t commonly u ed en or and i uitable for u e on final ettlement tank in
ewage treatment application and clarifier in water treatment work .
Equivalent IR Serie Sen or: IR15
Soli-Tech 20 range 0-10000
Thi en or i al o regularly u ed for ludge blanket detection and i normally u ed for primary
ettlement in ewage treatment and ludge thickener in water treatment.
Equivalent IR Serie Sen or: IR15
Soli-Tech 20 range 0-30000
Thi en or hould only be applied on ludge thickener in ewage treatment plant .
Equivalent IR Serie Sen or: IR8
Controls and Settings Page 5

Controls and Settings
The principle control during operation i the rotary witch; thi allow the u er to elect the
following operation
In ‘automatic’ mode the in trument will continually monitor the u pended olid den ity and
will move the en or up and down to track the ludge blanket interface. The motor up/down and
top po ition are elf-explanatory and are only u ed during the etup of the in trument.
On the circuit board there are a number of other control , the function of the e control i
explained in later ection :
Circuit Board Ident Type of Control Use
Zero Pu h Button Calibration
Top Limit Potentiometer Calibration
Bridge Clearance Potentiometer Scraper Clearance
Motor Speed Control Potentiometer Factory etup
20 mA Adju tment Potentiometer Factory etup
4 mA Adju tment Potentiometer Factory etup
100% Potentiometer Factory etup
0% Potentiometer Factory etup
Up Pu h Button Calibration and maintenance
Down Pu h Button Calibration and maintenance
Link A Jumper Setup
Link B Jumper Setup
Link C Jumper Setup
Link D Jumper Setup
Voltage Selector Switch Setup
Controls and Settings Page 6
automatic
motor top
motor up
motor down

Up and Down Buttons
The ASLD 2200 ha 2 et of Up and Down button ; one et i on the out ide of the enclo ure
the other et i on the main circuit board. Both et have the ame function. The e button are
normally u ed to aid cleaning of the en or by bringing the en or to the urface.
Up and Stop
Thi button will cau e the en or to ri e to the 100% point at the higher peed.
Do n and Reset
Thi button will cau e the en or return to automatic mea urement.
Controls and Settings Page 7

Installation
Location
The ASLD 2200 i hou ed in an IP55 GRP outer enclo ure and i uitable for mounting on the
bridge of ettlement tank . The electronic for the monitor are hou ed within an inner IP65
enclo ure.
It i recommended that the monitor be mounted approximately half way between the centre and
the out ide wall of the tank, on the leading edge. Thi offer allow the y tem to monitor the
true ettled interface whil t minimi ing the effect of di turbance cau ed by incoming ludge and
by the tank craper.
It i normal for the 4-20 mA output ignal to be tran mitted via lip ring to the ite control
y tem, where thi i not po ible Partech are happy to offer a radio telemetry y tem for
tran mi ion directly to the de ired point.
Partech offer a mounting bracket hown below that allow ea y attachment to tank handrail .
The ASLD 2200 weigh 15 kg and can be difficult to handle, it i advi able to have a i tance
when in talling thi in trument. Do not lift the ASLD 2200 by it cable drum.
Controls and Settings Page 8

Electrical Connections
Number Function Colour of Internal Wiring
1 Remote Up Switch White/Black
2 Remote Down Switch Orange/Black
3 Remote Switch Common Yellow/Black
4 4-20 mA Hi (+)
5 4-20 mA Lo (-)
6 Regulated 12 VDC Output
7 0 VDC
8 Limit Relay, 0% and/or 100%
9 Limit Relay, 0% and/or 100%
10 0 VDC
11 Sen or Lo Blue
12 Sen or Hi Brown
13 5 VDC to Encoder Red
14 Input 1 from Encoder Blue
15 Input 2 from Encoder Yellow
16 O VDC to Encoder Black
17 Nominal 18 VDC to Motor (+ve) Green
18 Nominal 18 VDC to Motor (-ve) Red/Brown
19 Not U ed
20 Not U ed
21 To main i olator Red/Brown
22 To main i olator Red/Brown
23 Earth
24 No connection
25 Neutral
26 Live
The ASLD 2200 require a main power upply to operate thi can be either 115 or 230 VAC
which i field electable.
Unle pecifically advi ed to do o, do not make change to the internal wiring.
Controls and Settings Page 9

Configuration
The ASLD 2200 require very little configuration, the u er mu t check the following detail
before u e. If you find that the incorrect en or or encoder di c ha been purcha ed contact
Partech to arrange a replacement.
Sensor Selection
The Soli-Tech 20 en or i available in four range ; which are hown below along with typical
application .
Part Number De cription Typical Application
179100 Soli-Tech 20, range 0-200
IR100, range 0-200
Water Treatment Clarifier
179120 Soli-Tech 20, range 0-1500
IR40, range 0-1500
Sewage Treatment Final Settlement
Water Treatment Primary
179140 Soli-Tech 20, range 0-10000
IR15, range 0-10000
Sewage Treatment Primary
Water Treatment Thickener
179160 Soli-Tech 20, range 0-30000
IR8, range, 0-30000
Sewage Treatment Thickener
Dept Range Selection
The depth range depend on the encoder di c that ha been fitted to the in trument, thi can be
found near the motor a embly.
Motor A embly Ver ion 1
(Thin tainle teel ide plate )
Motor A embly Ver ion 2
(Thick aluminium ide plate )
No of Blade Minimum Range
(metre )
Maximum Range
(metre )
Minimum Range
(metre )
Maximum Range
(metre )
1 5.6 13.8 11.0 20.0
2 2.8 6.9 5.5 11.0
4 1.4 3.4 3.0 6.0
6 1.0 2.2 2.0 4.0
8 0.8 1.6 1.5 2.5
The in trument will have been fitted with one of the e encoder di c , and will have been
elected prior to order placement. The encoder di c can be changed in the field if required, ee
the rear of the manual for part number .
Controls and Settings Page 10

Links
The circuit board ha four et of link that need to be et in the correct po ition for the
application.
Link Group A
When a jumper i placed acro thi link the limit relay will activate when the bottom limit
LED i on – di play i reading 0%.
The factory default i for thi jumper to be in place.
Link Group B
When a jumper i placed acro thi link the limit relay will activate when the top limit LED i
on – di play i reading 100%.
The factory default i for thi jumper to be in place.
Link Groups C and D
The e link work a a pair and both mu t either be to the left or to the right. The e only effect
operation with the rotary witch on ‘automatic’. Other etting of the rotary witch will override
thi feature.
The factory etting i both to the left.
Both to left
On power up, either during commi ioning or after a power failure the en or with immediately
tart to earch for the ludge blanket.
Both to the right
On power up, either during commi ioning or after a power failure the en or will lift to the top
limit. It will then wait for the down button to be pre ed.
Controls and Settings Page 11
Link A
Link B
Link C
Link D

Calibration
Calibration i carried out in 2 tage ; fir tly et the zero point, then the 100% value. A the
en or i going to be lowered to the bottom of the tank it i important that attention i paid to
any hazard uch a moving craper below the urface of the tank.
Set Zero
Set the rotary witch to ‘motor top’ and take the en or down to the bottom of the tank by
taking loop of cable off the drum. Once the cable i clo e to the bottom of the tank gently rai e
and lower the en or and it will be po ible to ‘feel’ the bottom of the tank. U e the ‘motor up’
po ition of the rotary witch to move the en or uch that it i approximately 25 mm from the
bottom of the tank. Pre the Red Zero pu h button to et the zero point, it i ometime
nece ary to pre thi button a few time to en ure a correct zero etting.
It i important that the zero point i et above the bottom of the tank, if the en or i allowed to
drag on the floor of the tank damage can occur and there i a danger that the en or can become
entangled in the craper mechani m.
Set Span
Now u e the ‘motor up’ po ition to bring the en or to the water urface. It i normally
advi able to leave the bottom part of the en or (approximately 50 mm) under the urface.
Set the rotary witch to ‘motor top’ and u e the Top Limit control to et the 3 digit LED
di play to 100.
It i advi able to run the in trument back down to 0 to confirm that the calibration ha been
performed ati factorily.
Controls and Settings Page 12

Scraper Clearance
In certain application uch a tho e where the ASLD 2200 i in talled on a fixed bridge above
a moving craper it i nece ary to bring the en or above the water urface to prevent damage
to the en or.
The ASLD 2200 allow the u er to in truct the en or to ri e to 100% to allow the craper to
pa and then return to the tank to continue mea urement.
It i recommended that the in taller con ult Partech before tarting in tallation to en ure that the
correct mea ure are taken to prevent damage to either in trument or to the craper mechani m.
Under normal circum tance it i po ible to place a detector ahead of the bridge that will
provide the ‘up’ command and another en or after the bridge that will provide the ‘down’
command.
The e external en or can be wired in parallel to the up and down button on the out ide of the
enclo ure u ing terminal 1 to 3.
Bridge Clearance Control
A ociated with the craper clearance function i the Bridge Clearance adju tment, thi allow
the en or to come clear of the water to allow the craper to pa . To adju t u e the following
tep :
Rai e the en or to the urface u ing the rotary witch.
Select ‘motor off’
Turn off power
Set Link C and D to the right hand po ition and witch on
Select ‘motor up’ and turn the bridge clearance control clockwi e until the en or i rai ed far
enough to allow the craper to pa . Thi can be et to a maximum of 110%.
Return the unit to ‘automatic’ and pre down to return to mea urement.
If power i temporarily lo t the en or will ri e to the urface on power up and remain there
until the craper pa e after which it will return to automatic mea urement.
Controls and Settings Page 13

Outputs
Analogue Output
The ASLD 2200 ha one analogue output that i directly proportional to the 0 to 100% digital
di play. Under normal circum tance thi relate to 4 mA with the en or at the bottom of the
tank and 20 mA with the en or at the water urface.
There i no need to make any field adju tment during commi ioning. If during maintenance it
i felt that the 4-20 mA ignal need calibration thi can be carried out u ing the 4 mA and 20
mA potentiometer adju tment .
To calibrate the analogue output connect a multimeter on it mA etting in erie with the output.
The ‘motor up’ and ‘motor down’ control can then be u ed to force the output to 4 mA and 20
mA a nece ary.
If the ‘Up’ button i pre ed at any time the 4-20 mA loop will go to 12 mA until the ‘Down’
button i pre ed and the ludge blanket i detected.
Limit Relay
The ASLD 2200 i equipped with a relay that i normally open; when either the top or bottom
limit i reached thi contact will clo e. Either or both top and bottom limit can cau e thi relay
to activate, link A and B are u ed to configure thi feature.
It hould be noted that the trip point i not adju table.
Controls and Settings Page 14

Maintenance
General Precautions
•Do not lift the unit by the drum
•Check that the unit i bolted firmly to the upport bracket
Warning: I olate the main upply before commencing any maintenance to the electronic
enclo ure; the external witch doe not i olate the electronic
Routine Maintenance
The en or will require routine cleaning; the frequency of cleaning i ite dependent and hould
be determined by ob ervation of the en or during the fir t few week of operation.
Typically the en or hould be cleaned once per fortnight, although on many ite once per
month i ufficient.
The en or can be cleaned u ing a oft cloth; no pecial cleaning material are required.
Care mu t be taken to en ure that no loop of cable are di placed during cleaning and the
en or hould be lowered carefully into the tank after cleaning.
C anging t e Circuit Board
1. I olate the main upply to the in trument; the external witch doe not i olate the
circuit board.
2. Open the main enclo ure and remove the tran parent cover from the inner enclo ure.
Undo the two crew retaining the front panel and remove it.
3. Pull out the four connector located toward the bottom of the PCB; the black
connector ha latche on the ide, which have to be relea ed.
4. Remove the crew from the heat ink, and then remove the four M5 crew , which can
be found at the corner of the PCB.
C anging t e Transformer
Perform the tage above to expo e the tran former
Remove the tran former by undoing the two M5 crew .
When replacing the tran former en ure that the green earth wire i fa tened ender one of the
crew .
Mentenance and Repair Page 15

Fault Finding
Li ted below are ome of the common problem found on the ASLD 2200, the li t i not
comprehen ive and if you are in any doubt plea e contact your local di tributor or Partech.
Symptom
Digital di play change but doe not relate correctly to the en or po ition
Fault
Encoder incorrectly po itioned
Corrective Action
Adju t the po ition of the encoder o that the blade pa e centrally through the gap, it i al o
advi able to check that the encoder i free from du t.
Symptom
Di play doe not corre pond to the en or po ition; en or u ually de cend to the tank bottom
Fault
Slipping or broken drive belt
Corrective Action
If the belt i worn replace it, if the belt i undamaged then the belt can be reten ioned u ing the
adju tment hown.
Mentenance and Repair Page 16

Symptom
The en or drive to the top limit.
Fault
It i likely that the en or i fouled, if the problem per i t after en or cleaning then the en or
i likely to have failed.
Corrective Action
Clean the en or, if the problem per i t contact Partech.
Symptom
The motor doe not re pond to change in the ludge blanket level, but the en or i working
correctly.
Fault
The motor drive circuit ha failed, look for heat damage to the area hown.
Corrective Action
Return the main circuit board to Partech for repair.
Mentenance and Repair Page 17

Spare Parts
The part li ted below are available for the ASLD 2200; it i advi able to contact your local
di tributor or Partech’ technical upport team before purcha ing the e part to en ure that the
correct item are purcha ed.
Sensor
Part No Description
179120 Soli-Tech 20 Sen or, Range 0-1,500 for ASLD 2200
179140 Soli-Tech 20 Sen or, Range 0-10,000 for ASLD 2200
179160 Soli-Tech 20 Sen or, Range 0-30,000 for ASLD 2200
102201 IR100 Sen or for ASLD 2200
101901 IR40 Sen or for ASLD 2200
101601 IR15 Sen or for ASLD 2200
148121 IR8 Sen or for ASLD 2200
General
Part No Description
101170 Mounting Bracket for ASLD 2200
103370 In truction Manual for ASLD 2200
Repair
Part No Description
101480 1A Anti Surge Fu e (20 mm) located in fu e holder
103040 5A Anti Surge Fu e (20 mm) located on main CCA
101660 Drive Belt ASLD 2200 Motor A embly Ver ion 1
154110 Tran former Sub-A embly for ASLD 2200
117150 Encoder Di c 1 Bladed for ASLD 2200
117160 Encoder Di c 2 Bladed for ASLD 2200
117170 Encoder Di c 4 Bladed for ASLD 2200
121950 Encoder Di c 6 Bladed for ASLD 2200
121960 Encoder Di c 8 Bladed for ASLD 2200
222326 ASLD2200 Motor A embly Ver ion 2
222341 Drive Belt ASLD2200 Motor A embly Ver ion 2
Spare Partrs Page 18

Tec nical Specification
General
Supply Voltage ...............................115/230 VAC, 50/60 Hz, +10/-15% (Voltage Selector
Power Consumption.......................25 VA
Supply Fuse....................................1A Anti Surge 20 mm (Fitted to fuse holder
........................................................5 A Anti Surge 20mm (Fitted to circuit board
Operating Temperature..................0 to 50°C
Storage Temperature......................-20 to 70°C
Display ...........................................3 Digit LED
Sensing Speed.................................1 metre per minute
Manual Operation Speed................5 metres per minute
Accuracy.........................................Dependent on depth of tank typically +/- 5%*
Resolution.......................................+/- 100 mm*
Terminals:.......................................Max conductor cross section 2.5 mm2
Alarm Output
Number of Output...........................1 Contact Closure
Alarm Types....................................Zero and/or 100% fixed
Relay Rating...................................0.5 A @ 100 VDC
Analogue Output
Type:...............................................4-20 mA
Resolution:......................................Better than 1%
4-20mA Maximum Output Load:....500 Ohms
EMC
EMC:..............................................EN 50081-1 (1992 , EN 50082-1 (1994
P ysical Features
Dimensions:....................................350 x 490 x 382 mm (w
×
h
×
d
Weight:............................................15 Kg
Enviromental Rating:.....................IP55 Outer Enclosure
........................................................IP65 Electronics Housing
Material:.........................................GRP
Cable Entry:...................................3
×
PG11
Mounting Legs................................10 mm holes
* Accuracy and re olution are dependent on the ettling characteri itc of the ludge and will
vary from ite to ite and with ite condition .
Technical Specification Page 19

Tec nical Support
Technical Support i available by phone, fax, or email, the detail of which are hown below.
Phone: +44 (0) 1726 879800
Fax: +44 (0) 1726 879801
Email: ale @partech.co.uk
Web ite: www.partech.co.uk
To enable u to provide quick and accurate technical upport plea e have the following
information ready when you contact our Technical Support Engineer:
Monitor type, and erial number.
Sen or type, and erial number.
Application detail .
De cription of fault.
Returning Instruments for Repair
If equipment need to be returned to Partech for repair or ervice the following addre hould
be u ed:
SERVICE DEPT.
PARTECH (ELECTRONICS) LTD
CHARLESTOWN
ST AUSTELL
CORNWALL
PL25 3NN
UNITED KINGDOM
Plea e include the following information with the returned equipment. Al o en ure that en or
are adequately protected for tran portation (Advice on packing can be provided by our ervice
department).
Contact name and phone number.
Return addre for equipment.
De cription of fault or ervice required.
Any pecial afety precaution becau e of nature of application.
Technical Support Page 20
Table of contents
Other ParTech Measuring Instrument manuals
Popular Measuring Instrument manuals by other brands
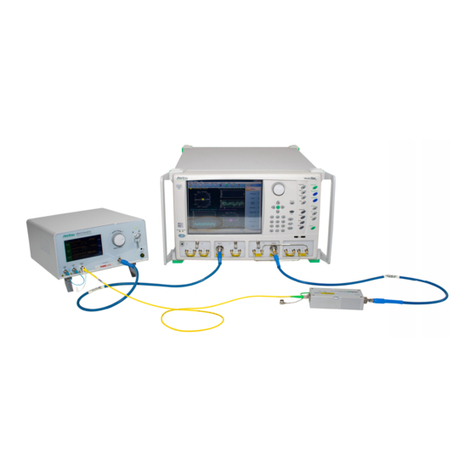
Anritsu
Anritsu VectorStar ME7848A Series Maintenance manual
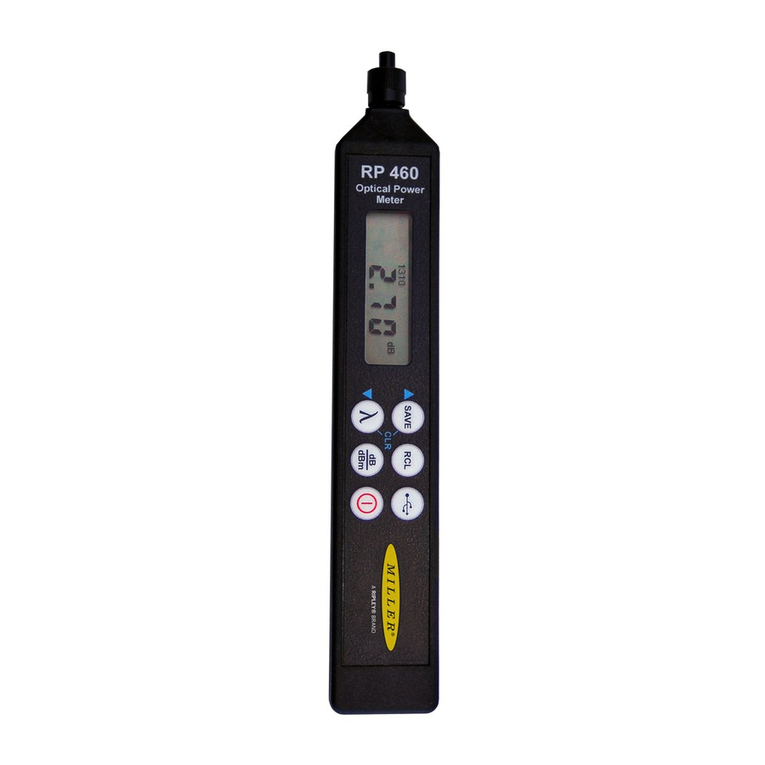
Ripley
Ripley ODM RP 460 quick start guide
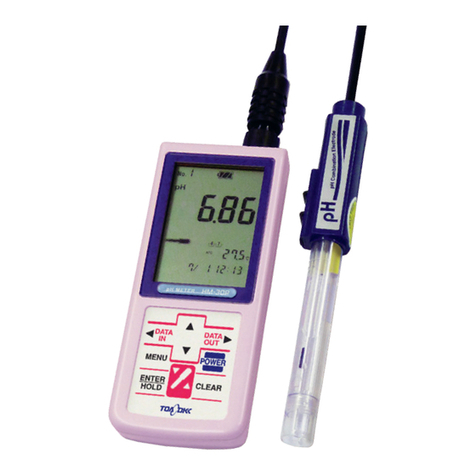
TOA-DKK
TOA-DKK HM-30P instruction manual

Endress+Hauser
Endress+Hauser Proline Promag H 300 technical information
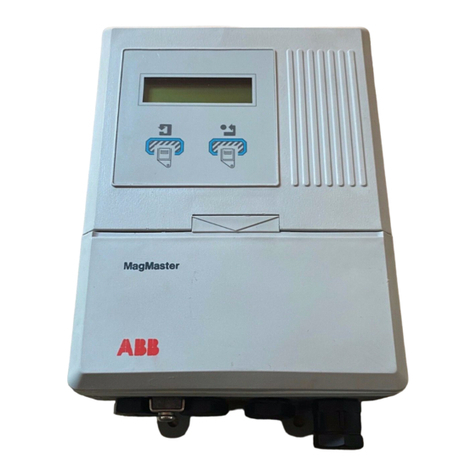
ABB
ABB MagMaster Quick reference guide
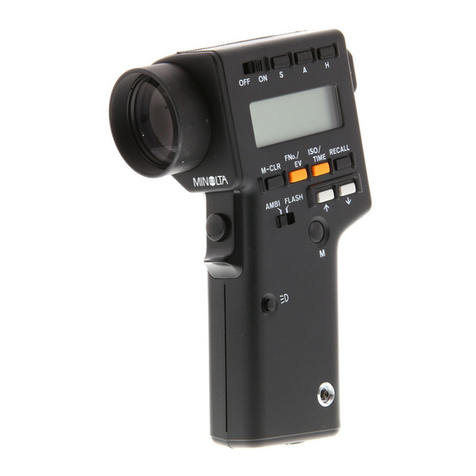
Minolta
Minolta SPOTMETER F - IR REMOTE CONTRO LRC-3 manual