Patton EQUALIZER User manual

PATTON DIVIDER BLOCK SYSTEMS
Pro-Tecting “Your” Compressor
All trademark names are the property of their respective companies and not associated with Patton Lubricator Products
1.888.788.4402
www.pattonlube.com
Patton Divider Block Systems
1004-B South Midkiff Rd.
Midland Texas 79701
BUILT TANK TOUGH
2-Year Factory Warranty
ALL DIVIDER BLOCK SYSTEMS ARE COMPROMISED AND
ARE NOT INJECTING THE CALCULATED QUANTITY OF OIL!
SAFEGUARD YOUR COMPRESSOR RINGS, RODS & PACKING
BY INSTALLING EQUALIZERS ON ALL DIVIDER BLOCK OUTLETS!
"Ensures divider block pistons 1.
move fluidly and dispense the calculated
volume of oil to rings, rods, packing &
cylinders!"
"Reduces problems associated with 2.
divider block lock up, and blown
rupture discs!"
"Increases the longevity and 3.
reliability of all divider block systems!"
"Increases the runtime, reliability and 4.
longevity of compressor wear
components!"
FOUR (4) CRITICAL REASONS THE WORKING
PRESSURE OF ALL DIVIDER BLOCK SYSTEMS
SHOULD BE EQUALIZED WITHIN 200 PSI!
"THE EQUALIZER"
Adds Reliability and Longevity to
Cylinders, Rings, Rods & Packing, Plus
Extends The Life of Divider Block Systems
Part#
PLP-EQLZ
PRESSURE BALANCING VALVE
FOR HIGH PRESSURE DIVIDER BLOCK SYSTEMS
CORRECTS THE COMPROMISED LUBRICANT OUTPUT
OF DIVIDER BLOCK SYSTEMS
"EQUALIZER"
Pro-Tecting “Your” Compressor
PATTON
DIVIDER BLOCK SYSTEMS
R
INTELLECTUAL PROPERTY
US PATENT PENDING
1/4" Tube Fittings For
Quick & Easy Installation
in Tubing Lines
Lock Nut Secures Set
Pressure
Easy to Adjust or
Change Opening
Pressure Settings
Stainless Steel
Construction
*5 Year Warranty

What Causes Differential Pressure Short Stroking (DPSS)?
When the working pressure of all divider block outlets are not equalized within 200 PSI, the differential pressure
between the injection points will cause the pistons in the block to short stroke. The shortened travel of the pistons
seriously reduces the volume of oil that was calculated to lubricate the pistons, rings, rods and packing.
NOTE: The only proven method to prevent the short stroking of divider block pistons, and ensure the correct volume of
oil is injected into the lubrication points, is to equalize the pressure on all tubing lines serviced by the divider block!
Consequences of Differential Pressure on Divider Blocks:
A. Divider blocks operating with differential pressures exceeding 200 PSI can cause the internal pistons in the valve to
hit the end plugs of the block causing the pistons to bounce out of sync, locking up the divider block assembly.
B. When the discharge pressure of divider block systems are not equalized within 200 PSI, the slap action of the piston
can also cause damage and cause spring failure in lube no-flow devices and proximity switches, which in turn will cause
the compressor to shutdown on lube no-flow.
Field and laboratory testing have proven ALL compressor divider block systems ARE NOT lubricating the rings,
rods, packing and cylinders with the quantity of oil as designed. The lack of proper lubrication has been causing
premature wear and failure of compressor cylinder wear components for decades. Through the years, contract
compression companies and compressor owner/operators have come to accept premature wear or failure of
components as “what is to be expected after specific run time hours” and roll these expenses into their annual
operational costs.
After discovering the phenomenon of D.P.S.S., “Normal wear and failure of the compressor components is no
longer considered Normal.......it is Abnormal” and can be prevented by installing the "EQUALIZER!"
DIVIDER BLOCK SYSTEMS OPERATING WITH OVER 200 PSI DIFFERENTIAL PRESSURE
BETWEEN LUBE POINTS ARE COMPROMISED, AND DO NOT DISTRIBUTE
THE CORRECT VOLUME OF OIL, DUE TO SHORT STROKING OF INTERNAL PISTONS!
THE RESULTS OF DIFFERENTIAL PRESSURE SHORT STROKING OF ALL DIVIDER BLOCKS IS SHOCKING!
FIELD DOCUMENTED DPSS
Percentages reflect the amount of oil being delivered from each block output at the cycle time recorded during testing.
Pressure for all lines were measured upstream of the injection point with the unit running at full speed and loaded.
FIELD DOCUMENTED DPSS
NOTE: Three compressors were tested yielding the same results. All divider block
system components were new and properly installed.
(Percentages of would indicate accurate delivery of oil)100%
PATTON DIVIDER BLOCK SYSTEMS
Pro-Tecting “Your” Compressor
What is The Definition of Differential Pressure?
Differential pressure is the difference between the lowest and highest pressure the divider block system is working against to
inject lubricant into the rings, rods, cylinders and packing glands of the compressor.
D.P.S.S. is the term Patton Lubricator Products uses to describe the forceful, erratic, and inconsistent travel of divider block
piston moving within its body. The distance traveled by the divider block piston is significantly affected by contrasting pressures
each individual piston is working against to inject a specific amount of oil to the rod packing and cylinder.
Individual Assessment of Each Lubrication point on a Two
Throw 3 Stage Compressor, With In-Board 3rd Stage
Cylinder, Proving Reduced lubrication Caused By D.P.S.S..
Assessment of Each Lubrication Point
After System Pressure on Each Injection
Point Was Equalized Within 200 PSI.

PRESET THE OPENING PRESSURE OF THE "EQUALIZER" BEFORE INSTALLATION
CAUTION: The opening pressure of the "EQUALIZER" should be preset with a purge gun (in the shop or field) prior
to installation on the divider block system. NOTE: To preset the Equalizer you must know the highest pressure
reading of the gauge on the discharge of the lubricator pump, with the compressor loaded.
Presetting the EQUALIZER: Adjust the pressure to open the EQUALIZER valve to a minimum of 300 PSI over the highest
pressure reading on the gauge at the discharge of the lubricator pump, with the compressor operating fully loaded.
After manually presetting the EQUALIZERS, install them in each tubing line of the divider block system.
NOTE: After installing the EQUALIZER, you can make minor adjustments to ensure the pressure gauge pointer is
moving fluidly with no more that 200 PSI differential, with the compressor operating at max discharge pressure.
NOTE: ADJUST AND SECURE THE OPENING PRESSURE OF THE EQUALIZER PRIOR TO INSTALLATION ON THE
COMPRESSOR:
Tools needed: Manual purge gun, crescent wrench and 5/8" open end wrench.
NOTE: The lock nut and adjusting nut on the EQUALIZER must be sealed with Torque Seal after adjusting the set pressure to
ensure the opening set pressure is secured and cannot be tampered with!
1. Connect purge gun to the EQUALIZER inlet and slowly pump oil through the unit. (see fig 2)
2. As you're pumping oil into the EQUALIZER notice the pointer on the pressure gauge on the purge gun to verify (see fig 1)
pressure needed to pump through the unit.
3. Loosen the lock nut with a 5/8" open end wrench and turn clockwise. (see fig 3)
4. Increase opening pressure by rotating the adjusting nut clockwise. (see fig 4)
5. Slowly pump oil through the EQUALIZER and continue visually checking the pressure on the purge gun gauge.
6. Continue turning adjusting nut clockwise until the desired pressure setting is shown on the purge gun pressure (see fig 4)
gauge.
7. Hand tighten the lock nut to the adjusting nut, then place a 5/8" open end wrench on the adjusting nut (see fig 3) (see fig 4)
for a backup. After opening pressure is set, Do Not allow the adjusting nut to rotate! If the adjusting nut is rotated, the pressure
desired settings will change. Tighten to the secure pressure setting. the lock nut securely with a 5/8" open end wrench (see fig
3 & 4)
8. After you've set the EQUALIZER to the desired opening pressure, spread Cross Check Torque Seal over the adjusting nut
and lock nut. If the torque seal has been broken at any time after the EQUALIZERS have been sealed. it's (see fig 3 & 4)
obvious someone has tampered with the set pressure.
Adjusting Nut
on "EQUALIZER"
Rotate to Increase
or Decrease Pressure
(fig 4)
LOCK NUT
(fig 3)
(fig 2)
INLET
PATTON "EQUALIZER"
500
0
1000
1500
2000
2500
3000
3500
4000
I
I
I
I
I
I
I
I
I
I
I
I
I
I
I
I
I
I
I
I
I
I
I
I
I
I
I
I
I
I
LUB R I C A TOR PRODUCTS
(fig 1)
PRESSURE
GAUGE
EQUALIZER
Step 1. Locate a convenient spot in the tubing between the divider block and the injection check valve. Cut out approximately
2 3/8" section of tubing. Deburr the tubing ends to ensure metal particles do not get in the oil supply!Caution:
Step 2. Confirm the EQUALIZER is oriented with the arrow indicating direction of flow from the divider block (see fig 1)
towards the injection check valve and install the EQUALIZER in the tubing line.
Step 3. Fully insert the tubing from the divider block into the inlet of the EQUALIZER until it rests firmly on the (see fig 2)
shoulder of the integral tube fitting. (see fig 3)
Step 4. Rotate the tubing cap (finger tight), then use a backup wrench on the hex end of the EQUALIZER and (see fig 5)
tighten each tubing cap one and one quarter turns to secure proper sealing at high pressure. (see fig 6)
Step 5. Repeat steps 4 & 5 for the outlet of the EQUALIZER, remember to fully insert the tubing to the shoulder of both tube
fittings. (see fig 7)
(fig 7)
SHOULDER
(inside fitting)
(fig 2)
1/4" SS TUBING
(fig 1)
Direction of Flow
(fig 5)
HEX NUT
(fig 3)
SHOULDER
(inside fitting)
Outlet to Injection
Check Valve
From
Divider Block
(fig 6)
TUBE FITTINGS
Installing The EQUALIZER In The Tubing Lines Of The Divider Block System
3.750"

Equalizing The Working Pressure of All Divider Block Outlets Ensures
Cylinders, Rings, Rods & Packing Are Receiving The Calculated Volume of Oil
NOTICE: The EQUALIZER should be manually adjusted to preset pressure before installation on the
divider block system. Locate any convenient section of tubing between the outlet of the divider block and the
injection check valve, remove approx 3" of tubing and install the EQUALIZER.
1) With the compressor operating at max RPM and discharge pressure, note the maximum pressure reading on the pressure
gauge installed on the discharge of the lubricator pump or inlet of the divider block. (see fig 1)
2) Loosen lock nut with a 5/8" open end wrench and slowly rotate clockwise to increase pressure while monitoring the pressure
gauge on the divider block or lube pump. Note: If needed a pressure gauge may be temporarily placed in the tubing line to simplify
making minor adjustments to the opening pressure on the EQUALIZER. (see fig 3)
3) Slowly increase pressure by rotating the adjusting nut on the EQUALIZER clockwise until you notice the pressure increasing
on the divider block system gauge. (see fig 4)
4) Continue monitoring the pressure gauge at the discharge of the lube pump (or inlet of the divider block) and slowly rotate the
adjusting nut clockwise until the pressure gauge begins to read approximately 300 PSI over the initial system pressure.
5) After installing and adjusting the EQUALIZER, the gauge should display pressure 300 PSI over the highest peak pressure of
the system BEFORE the EQUALIZER was adjusted. To secure the pressure setting, use an open end 5/8" wrench as backup
and tighten the lock nut against the adjusting nut. (see fig 3 & 4)
6) Continue installing and adjusting EQUALIZERS on all outlets of the divider block until the pressure gauge holds consistent
pressure with no more than 200 PSI rise and fall. As you install and adjust the other EQUALIZERS, the goal is never to NOTE:
increase the pressure reading on the gauge at the pump or divider block after adjusting the first EQUALIZER.
7) After adjusting all EQUALIZERS, the indicator needle on the pressure gauge at the lubricator pump or divider block should
fluctuate very little with fluid movement and no erratic pressure changes over 200 psi.
8) If the pressure gauge at the pump rises and falls erratically over 200 psi, re-adjust each EQUALIZER until the pressure gauge
shows less than 200 PSI differential with fluid movement.
NOTE: After you've set all EQUALIZERS to the desired opening pressure, spread Cross Check Torque Seal over the adjusting
nut and lock nut . If the torque seal is broken it's obvious someone has tampered with the set pressure.(see fig 2 & 3)
ADJUSTING NUT
on "EQUALIZER"
Rotate to Increase
or Decrease Pressure
PATTON
DIVIDER BLOCK SYSTEMS
12 T
15 T
06 T
(fig 4)
LOCK NUT
(fig 3)
Pressure Gauge
Discharge Of Pump
or Inlet of Divider Block
(fig 1)
1st Stage Cyl.
@ 300 PSI
2nd Stage Cyl.
@ 800 PSI
2nd Stage Pkg.
@ 400 PSI
1st Stage Cyl.
@ 300 PSI
1st Stage Pkg.
@ 200 PSI
2nd Stage Cyl.
@ 800 PSI
500
0
1000
1500
2000
2500
3000
3500
4000
I
I
I
I
I
I
I
I
I
I
I
I
I
I
I
I
I
I
I
I
I
I
I
I
I
I
I
I
I
I
LU B RIC ATO R PRO DUC TS
PATTON
DIVIDER BLOCK SYSTEMS
(fig 2)
INLET
(fig 5)
OUTLET
Minor Adjustment Of The "EQUALIZER"
After Installation In The Tubing Line of The Divider Block System
EQUALIZER
500
0
1000
1500
2000
2500
3000
3500
4000
I
I
I
I
I
I
I
I
I
I
I
I
I
I
I
I
I
I
I
I
I
I
I
I
I
I
I
I
I
I
L U B R I C A T O R P R O D U C T S
This manual suits for next models
1
Popular Lubrication System manuals by other brands

Lincoln industrial
Lincoln industrial QLS 301 Installation and operation instruction

DLS
DLS FlexxPump 250 B quick start
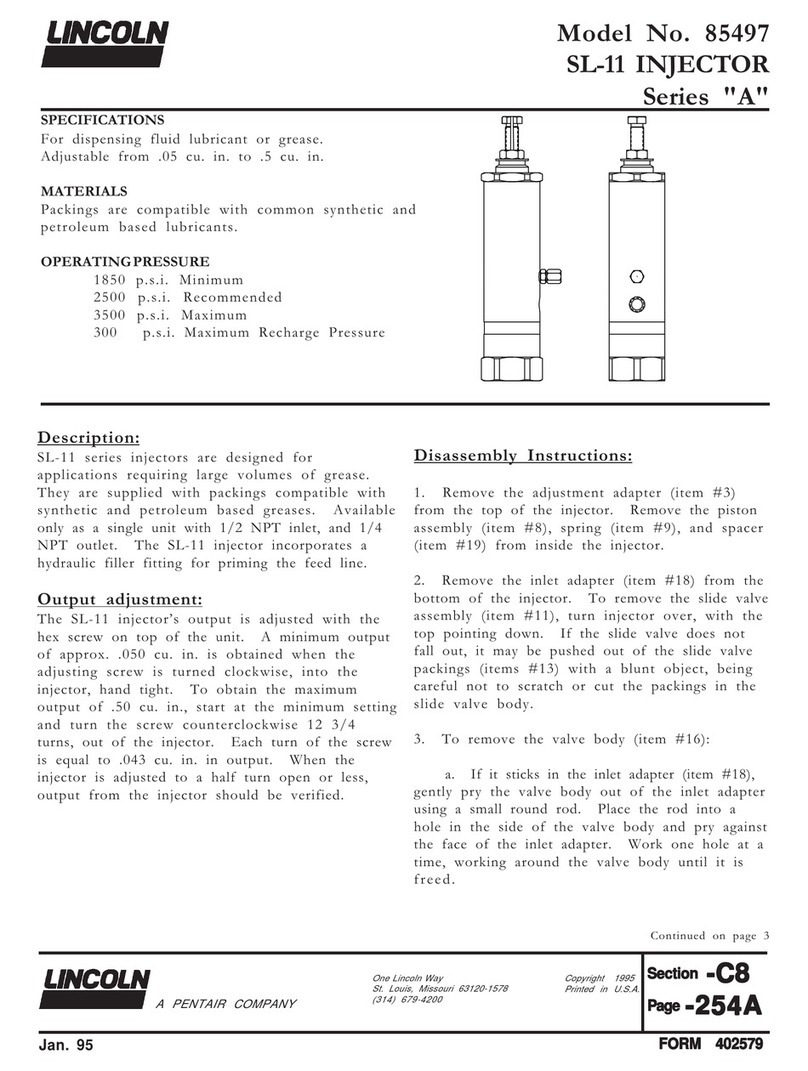
Lincoln
Lincoln SL-11 Series instruction manual
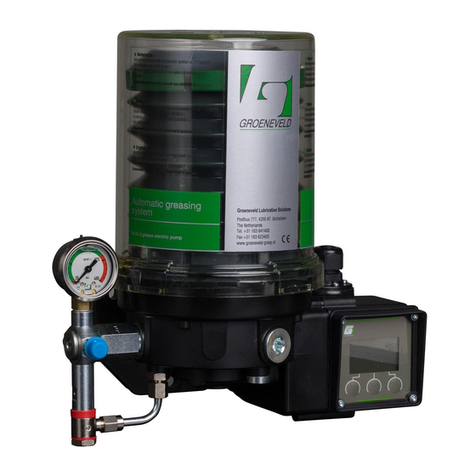
Groeneveld
Groeneveld EcoPlus User instruction
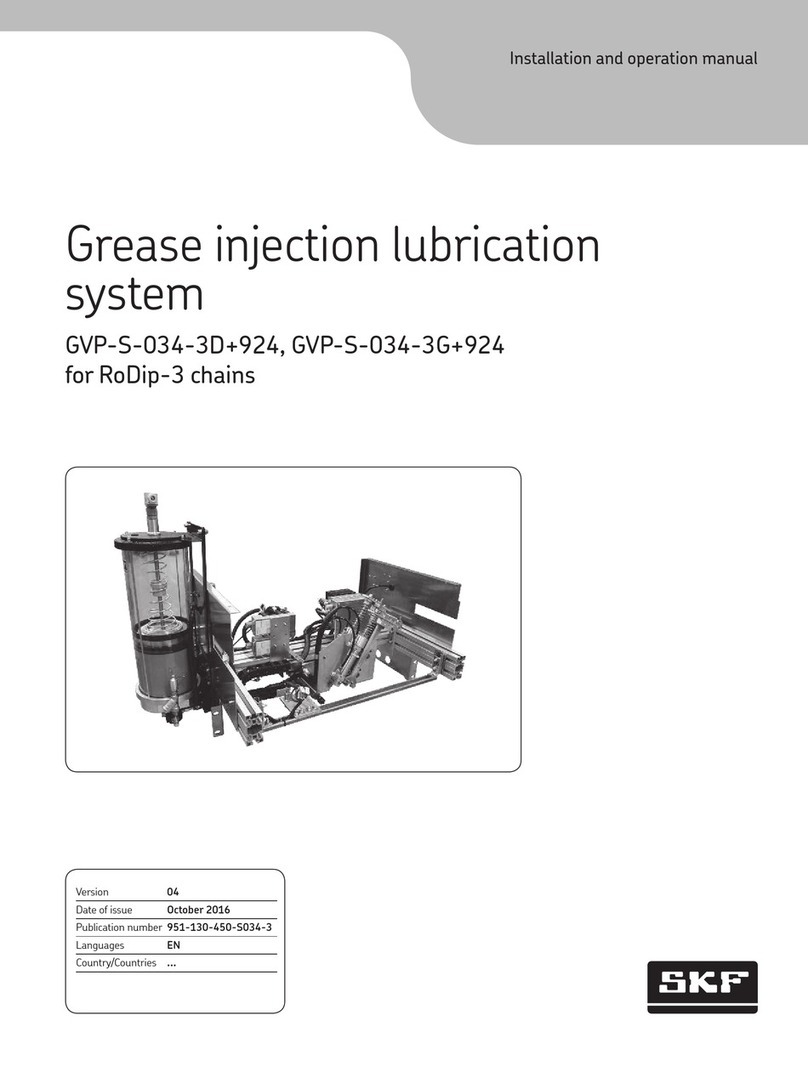
SKF
SKF GVP-S-034-3D+924 Installation and operation manual
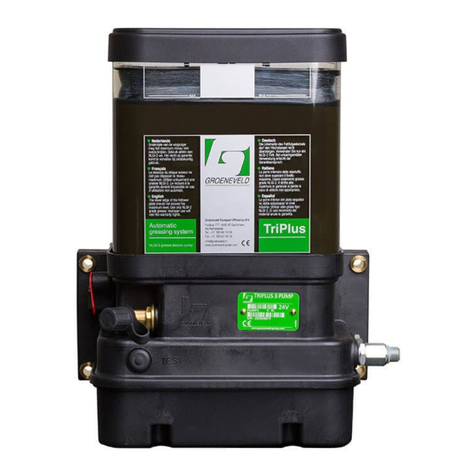
Groeneveld
Groeneveld TriPlus Truck-3 User instruction