Penn A421 Series User manual

A421 Series Electronic Temperature Controls
with Cycle Timer Installation Guide
Applications
Important: Use this A421 Series Electronic
Temperature Control only as an operating control.
Where failure or malfunction of the A421 Control
could lead to personal injury or property damage
to the controlled equipment or other property,
additional precautions must be designed into the
control system. Incorporate and maintain other
devices, such as supervisory or alarm systems or
safety or limit controls, intended to warn of or
protect against failure or malfunction of the A421
Control.
Important: Utiliser ce A421 Series Electronic
Temperature Control uniquement en tant que
dispositif de régulation. Lorsqu'une défaillance
ou un dysfonctionnement du A421 Control risque
de provoquer des blessures ou d'endommager
l'équipement contrôlé ou un autre équipement, la
conception du système de contrôle doit intégrer des
dispositifs de protection supplémentaires. Veiller
dans ce cas à intégrer de façon permanente d'autres
dispositifs, tels que des systèmes de supervision
ou d'alarme, ou des dispositifs de sécurité ou de
limitation, ayant une fonction d'avertissement
ou de protection en cas de défaillance ou de
dysfonctionnement du A421 Control.
The A421 Series Electronic Temperature Controls are
single-stage, electronic temperature controls with a single-
pole, double-throw (SPDT) output relay.
A421 Controls feature a backlit LCD with adjustable
brightness and three-button touchpad interface that can
be set up to restrict user adjustments. An LED indicates
the output relay's on and off status.
A421 Control with Cycle Timer also provides sensor
offset capability and restricted user adjustment. The
temperature control range is -40°F to 212°F or -40°C to
100°C.
The A421 Controls are available either in Type 1 (NEMA),
IP20 (CE), high-impact plastic enclosures suitable for
surface or DIN rail mounting (Figure 1) or in Type 4X
(NEMA), IP66 (CE) watertight, corrosion resistant surface
mount enclosures (Figure 2).
The control housing base on the Type 4X/IP66 models can
be easily rotated 180º relative to the control housing cover
and LCD, allowing you to bring the electrical connection to
either the top or bottom of the mounted control. Do not
twist the wiring harness between the housing base and
cover more than 180º.
Dimensions
Figure 1: A421ABT Control with Type 1 (NEMA), IP20
enclosure; dimensions, in. (mm)
Figure 2: A421AET Control with Type 4X (NEMA), IP66
enclosure; dimensions, in. (mm)
Part No. 24-7664-3043 Rev. C
2018-11-13
A421ABT, A421AET

A421 Control with Cycle Timer
The A421 Control with Cycle Timer is a free-cooling, duty-
cycle ventilation control. This control provides timed-
ventilation and over-cooling protection.
The A421 equipped with Cycle Timer is used in agricultural
and related applications where free-cooling and
ventilation can be used.
Parts included
Each A421 Control includes a Johnson Controls® or
PENN® A99 Series temperature sensor. See A99 Series
Temperature Sensors, Wiring, and Technical specifications
for more information about A99 sensors.
A99 Series Temperature Sensors
The A421 Controls require an A99 sensor, and each A421
Control includes an A99 sensor. Any A99 Series sensor
works with the A421 Series Controls. Do not replace an
A99 Series sensor with any other brand, series, or type
of temperature sensor. See Ordering information for
available A99 Series sensor models.
You can extend the sensor leads in the field. See Table 1
for recommended wire sizes and lengths. On long sensor
cable runs, use shielded cable to reduce electromagnetic
interference (EMI). Observe EMI best practices when
routing sensor leads.
Do not immerse the A99 Series sensors in water or any
other liquid. The A99 sensors are moisture tolerant and
splash resistant but if you immerse the sensor, liquid can
enter the sensor probe where the steel tube meets the
wire cable and result in sensor failure, which voids any
warranty.
In applications where the sensor may be exposed to a lot
of moisture, splashing, or rain, we recommend mounting
the sensor in a vertical position with the cable at the
bottom routed downward so that moisture can drain away
from the steel probe. Use a suitable bulb well for complete
fluid immersion applications. See Ordering information for
information about bulb wells.
The A99 Series sensors are positive temperature
coefficient (PTC) sensors. To test an A99 sensor,
disconnect the sensor from the control and measure the
resistance between the sensor leads.
• When the temperature at the sensor is 77°F (25°C), the
resistance should be 1,035 ohms.
• When the temperature at the sensor is 32°F (0°C), the
resistance should be 855 ohms.
See Troubleshooting for more information.
When an A99 sensor is connected to a standard A421
Control, the control restricts the range of usable values
from -40°F to 212°F or -40°C to 100°C.
See Wiring, Technical specifications, and refer to the
A99B Series Temperature Sensors Product/Technical Bulletin
(LIT-125186) for more information regarding A99 Series
sensors.
Mounting
Observe the following guidelines when locating and
mounting an A421 Control:
• Make sure that the mounting surface can support the
control, DIN rail, mounting hardware, and any user-
supplied panel or enclosure.
• Mount the control in a vertical, upright orientation
wherever possible. It is best practice to use DIN rail
mounting for type 1 controls.
• In direct-mount applications, mount the control on a
flat and even surface.
• Mount the control in a location free of corrosive vapors
and observe the ambient operating conditions listed
in Technical specifications for the A421 Control and the
A99 sensor.
• Allow sufficient space for connecting and routing wires,
viewing the LCD, and using the touchpad.
• Do not mount the control on surfaces that are prone
to vibration or in a location where high-voltage relays,
motor starters, other sources of electromagnetic
emissions, or strong radio frequency may cause
interference.
• Do not install the control in an airtight enclosure.
• Do not install heat generating devices with the
control in an enclosure that may cause the ambient
temperature to exceed 150°F (66°C).
Mounting a Type 1/IP20 control on DIN rail
1. Provide a section of 35 mm DIN rail that is longer
than the control width. Mount the DIN rail in a
suitable location and use appropriate mounting
hardware.
2. Clip the control module on the rail, position the
module’s upper DIN rail clips on the top rail, and
gently snap the lower clips on to the bottom of the
rail.
Direct-mounting a Type 1/IP20 control to
a wall or other flat surface using the four
keyhole slots
1. Disconnect the power and remove the enclosure
cover. Place the control vertically against the wall
surface in a suitable location, and mark the keyhole
slot locations on the mounting surface.
2. Install appropriate screws or fasteners and leave the
screw heads approximately one or two turns away
from flush to the mounting surface.
3. Position the control mounting slots over the screw
heads, and then tighten the mounting screws to
secure the control to the surface.
Note: When you mount the control on an
uneven surface, use shims to mount the control
evenly.
A421 Series Electronic Temperature Controls with Cycle Timer Installation Guide2

Additional guidelines for mounting Type
4X/IP66 controls
You can mount the Type 4X models to flat vertical surfaces
using the four holes at the enclosure corners. Place the
control against a flat wall surface in a suitable location,
and mark the mounting screw hole locations on the
mounting surface. Use appropriate screws and shims to
mount the control evenly on the surface.
On Type 4X models, select the knockout for removal. Place
a screwdriver blade on the knockout near the edge. Apply
a sharp blow to the screwdriver handle to loosen the
knockout. Be careful not to damage the control’s interior
components.
You need an additional low-voltage, two-wire cable to
operate the A421 (optional) manual override feature.
On Type 4X/IP66 enclosures, you must install a suitable
watertight fitting in an available knockout to pass the two-
wire cable through the enclosure wall.
You can rotate the control enclosure base on the Type 4X/
IP66 models 180º relative to the control enclosure cover
and LCD, to bring the electrical connection to the top or
bottom of the mounted control.
Note: Do not twist the wiring harness between the
enclosure base and cover more than 180º.
Wiring
Observe the following guidelines:
WARNING
Risk of Electric Shock
Disconnect or isolate all power supplies before mak-
ing electrical connections. More than one disconnec-
tion or isolation may be required to completely de-en-
ergize equipment. Contact with components carrying
hazardous voltage can cause electric shock and may
result in severe personal injury or death.
AVERTISSEMENT
Risque de décharge électrique
Débrancher ou isoler toute alimentation avant de
réaliser un raccordement électrique. Plusieurs iso-
lations et débranchements sont peut-être néces-
saires pour -couper entièrement l'alimentation de
l'équipement. Tout contact avec des composants por-
teurs de tensions dangereuses risque d'entraîner une
décharge électrique et de provoquer des blessures
graves, voire mortelles.
Important: Use copper conductors only. Make
all wiring in accordance with local, national, and
regional regulations. Do not exceed the A421
Control's electrical ratings.
Important: Do not exceed the A421 Control’s
electrical ratings. Exceeding the electrical ratings can
result in permanent damage to the control and void
any warranty.
Important: Run all low-voltage wiring and cables
separate from all high-voltage wiring. It is best
practice to use shielded cable for input (sensor)
cables that are exposed to high electromagnetic or
radio frequency noise.
Important: Make all wiring connections in
accordance with the National Electrical Code and
local regulations. Use proper Electrostatic Discharge
(ESD) precautions during installation and servicing
to avoid damaging the electronic circuits of the A421
Control.
Important: Do not connect supply power to the
A421 Controls before checking all wire connections.
Short circuits or improperly connected wires can
result in damage to the modules and void any
warranty.
Important: When you connect an A99 sensor with a
shielded cable to an A421 Control, connect the cable
shield drain lead to the common (COM) terminal on
the sensor and binary input terminal block (TB3).
Do not connect the shield at any other point along
the cable, and isolate and insulate the shield along
the entire length of the sensor cable. If you connect
a cable shield at more than one point, transient
currents can flow through the sensor cable shield
and cause erratic control operation.
Observe the wire size restrictions listed in Table 2 and the
Electrical Ratings listed in Technical specifications.
Observe the following guidelines, procedures, and
illustrations when you wire an A421 Series control and A99
Series sensor.
• Select the appropriate A99 sensors for the ambient
operating range that the A421 Control monitors
and controls, as shown in Table 6. See Technical
specifications for more information.
• Keep the sensor leads as short as possible in your
application. The additional resistance in long
sensor cables creates an offset between the actual
temperature and the displayed temperature. See Table
1 when extending sensor leads.
• A99 sensors are not polarity specific. You can connect
either lead to the SEN or COM terminals.
• It is best practice to use 22 AWG, stranded, twisted-pair
cable with a shield to extend sensor cable runs.
Table 1: Maximum sensor cable lengths and wire sizes
Wire
gauge
1Maximum Sensor cable length1
16 AWG 500 ft (150 m)
18 AWG 300 ft (100 m)
20 AWG 200 ft (60 m)
A421 Series Electronic Temperature Controls with Cycle Timer Installation Guide 3

Table 1: Maximum sensor cable lengths and wire sizes
Wire
gauge
1Maximum Sensor cable length1
22 AWG 125 ft (40 m)
1 At the listed maximum cable lengths, there is less than 1Fº
(0.6Cº) error between the temperature sensed at the A99
sensor and the temperature displayed on the LCD.
TB2 Terminal Block and SPDT relay output
The terminals LC, LNO, and LNC on the TB2 terminal block
connect to an SPDT dry-contact relay in the A421 Control
(Figure 3). The control does not provide any internal
power to the TB2 terminals or relay contacts. The A421
Control energizes and de-energizes the relay to open
and close the contacts based on the On/Off temperature
values.
• Relay De-energized (Off) = LC open to LNO as shown in
Figure 3, and the relay status LED is off
• Relay Energized (On) = LC closed to LNO and the relay
status LED is on
Figure 4 shows how to wire the A421 Control to use the
same power source that powers the controlled equipment
to also power the A421 Control.
Figure 3: TB2 Terminal Block showing connections to
the internal SPDT relay
You can also provide an independent power source for the
A421 Control on the TB1 terminals and then wire the TB2
relay terminals to a separate power source to switch and
power the controlled equipment circuit.
Figure 4: Wiring the A421 Series Controls using the
same power source to power the control operation and
power the controlled equipment
Table 2: A421 Control Wiring Terminals and wire size
information
Terminal
block
Label Description, function, and
requirements
Wire sizes
LN Line-voltage power source
(common): Connect the neutral
wire for 120 VAC supply power
applications. Connect the L1 supply
power lead for all 208/240 VAC
supply power applications.
120V Line-voltage 120 VAC control power
(hot): Connect the 120 VAC supply
power (hot) for 120 VAC supply
power applications (using jumper
from LC in Figure 4).
TB1
120/240
VAC
Models
240V Line-voltage 240 VAC control
power (L2) terminal: Connect
the L2 supply power connection
for 208/240 VAC supply power
applications (using jumper from LC
in Figure 4).
28 AWG to
12 AWG
0.08 mm² to
4.0 mm²
LC Line-voltage SPDT relay common
contact: Connect power supply to
power the controlled load.
Connect 120 VAC (hot) for 120 VAC
applications.
Connect L2 for 208/240 VAC
applications.
LNO Line-voltage SPDT relay normally
open contact: Connects controlled
equipment to the line-voltage
normally open (LNO) contact on
the SPDT relay. When LC is closed
to LNO, the relay is energized
and the green LED is on. The
LNO terminal typically provides
power to the controlled equipment
in both cooling and heating
applications.
TB2
LNC Line-voltage SPDT relay normally
closed contact: Connects controlled
equipment to the line-voltage
normally closed (LNC) contact on
the SPDT relay. When LC is closed
to LNC, the relay is de-energized
and the green LED is off. The LNC
terminal is not typically wired to
the controlled equipment.
28 AWG to
12 AWG
0.08 mm² to
4.0 mm²
BIN Detects a switch closure between
the BIN and COM terminals and
overrides the control to turn the
fan on. Normal control resumes
after this switch is opened again.
COM Connects the low-voltage common
from the sensor and binary input.
TB3
SEN Connects the low-voltage input
signal wire from control sensors.
22 AWG
(0.34 mm²)
stranded,
shielded
cable
A421 Series Electronic Temperature Controls with Cycle Timer Installation Guide4

Setup and adjustments
The front panel of the A421 Series Electronic Temperature
Control has an LCD and a three-button UI as shown in the
following figure.
Figure 5: A421 Control front panel with LCD and three-
button UI
LCD
The A421 Series Control has a backlit LCD screen (Figure
5). You can adjust the LCD brightness. During normal
operation, the LCD displays the Main screen, which
provides following information:
• Temperature sensed at the A99 sensor
• Selected temperature units (°F or °C)
• Mode of operation (snowflake = cooling mode only)
• Binary Input status (BIN) when a user-supplied toggle
switch is connected and closed to manually override the
relay control.
During setup and adjustment, the LCD displays the
parameter code screens and the parameter value screens.
See the A421 Control parameter setup menus for more
information.
Three-button touchpad
The touchpad has three buttons for setup and adjustment
of the A421 Control (Figure 5). See Navigating the Basic
and Advanced menus for more information on using the
three-button touchpad.
Relay status LED
The green LED on the front panel illuminates when the
SPDT output relay is energized and the LC and LNO
contacts are closed. See Figure 5.
Parameter codes and modes of
operation
Relay Off temperature (OFF)
Select the temperature at which the output relay
de-energizes, the LC to LNO relay contacts open
(cutout), and the green LED goes off. The range
of usable temperature values is -40°F to 212°F or
-40°C to 100°C in 1° increments.
Relay On temperature (On)
Select the temperature at which the output relay
energizes, the LC to LNO relay contacts close (cut
in), and the green LED lights. The range of usable
temperature values is -40°F to 212°F or -40°C to
100°C in 1° increments.
The A421 Series Control with Cycle Timer functions
in Cooling Mode only.
Temperature Units (Un)
Select the preferred temperature scale for your
application. Select either the Fahrenheit (°F) or
Celsius (°C) temperature scale.
Note: After changing the value for the temperature
units (Un), confirm that the temperature values for
the other parameter codes are still correct for your
application.
Low Temperature Stop (LtS)
Select the lowest temperature value below
which the Low Temperature On-Time (Ltt) is
enforced. This parameter is also used when
control adjustment is restricted. See Restricting
user adjustment.
The range of usable temperature values is -40°F to
212°F or -40°C to 100°C in 1° increments.
High Temperature Stop (HtS)
Select the highest temperature value in which the
On/OFF control band can be adjusted when the
control adjustment is restricted. See Restricting
user adjustment.
The range of usable temperature values is -40°F to
212°F or -40°C to 100°C in 1° increments.
Restricted Adjustment mode
The HtS and LtS values define the restricted
adjustment temperature range and are enforced
only when the A421 Control is set to the restricted
adjustment mode (Figure 9). See Restricting user
adjustment.
Low Temperature On-Time (Ltt)
Select the minimum relay On-time whenever the
sensed temperature is less than the LtS. The range
of values are 0 seconds to 300 seconds.
A421 Series Electronic Temperature Controls with Cycle Timer Installation Guide 5

The purpose of this parameter is to prevent over-
cooling that could occur if a long Ont is used when
the outside air is very cold.
Note: If LtS is left at the default value (40°F), the Ltt
parameter has little or no impact.
Minimum Relay On-Time (Ont)
Select the minimum relay On-time per cycle period
(cP). Ont is used when the sensed temperature
is greater that the LtS. The range of values are 0
seconds to 300 seconds.
During any relay On-time (Ont or Ltt), Ont is
displayed followed by the remaining Ont seconds
and the sensed temperature in sequence. This
sequence of three screens continues until the Ont
seconds expire for the cP.
When the fan relay is On for a temperature (free-
cooling) ventilation cycle, the screen displays the
sensed temperature and a snowflake in the lower-
right corner of the screen to indicate the fan relay
is On for free-cooling.
Cycle Period (cP)
Select the Cycle Period for free-cooling and
ventilation control. The range of values are zero 0
minutes to 60 minutes.
Sensor Offset Adjustment (So)
Sensor offset allows you to compensate for any
difference between the displayed temperature
value and the temperature sensed at the A99
sensor. Select a temperature value to offset the
temperature displayed on the LCD from the
temperature sensed at the sensor. The sensor
offset adjustment range is from -5°F to 5°F or -3°C
to 3°C in 1° increments.
Sensor Failure mode (SF)
Select whether the control’s fan relay operates as
energized or de-energized in the event of a sensor
or sensor wiring failure. When the control detects
a sensor circuit failure, the fan relay operates in
the selected sensor failure mode. The LCD flashes
SF and OP if the sensor circuit is open or SF and SH
if the sensor circuit is shorted.
Backlight Brightness Level (bll)
The backlight brightness level feature allows
you to adjust the LCD backlight intensity. At level
0 the backlight is off. Level 10 is the brightest
backlight setting and the system default. The
selected backlight brightness level is applied
to the LCD during normal operation. When you
enter the programming menus to set up the
control or press any key, the LCD automatically
goes to the brightest level. If you do not press a
key for 30 seconds, the main screen is displayed
and the backlight setting returns to the selected
brightness level.
Switch-Activated Override (Ord)
When a switch is closed between BIN and COM
terminals of the TB3, the control is overridden, and
the fan relay remains on. The fan relay remains On
until the circuit (toggle switch) between BIN and
COM is open.
The relay remains energized regardless of the
sensor value, sensor fail state, or any timing
parameters (cP, Ont, Ltt). The control display
alternates between the main display and manual
override (Ord).
Table 3: Standard parameter setup codes, descriptions,
range of values, and default values
Parameter
code
Parameter
description (menu)
Range of
usable
values
1Factory
default
value1
Un Temperature Units
(Advanced only)
ºF or ºC ºF
LtS Low Temperature Stop
(Advanced only)
-40ºF to
212ºF
(-40ºC to
100ºC)
40ºF
HtS High Temperature Stop
(Advanced only)
-40ºF to
212ºF
(-40ºC to
100ºC)
212ºF
OFF Relay Off Temperature
(Basic, Advanced, and
Restricted)
-40ºF to
212ºF
(-40ºC to
100ºC)
70ºF
On Relay On Temperature
(Basic and Advanced)
-40ºF to
212ºF
(-40ºC to
100ºC)
75ºF
Ltt Low Temperature On-
Time (Advanced only)
0 seconds to
300 seconds
60 seconds
Ont Minimum Relay On-
Time (Advanced only)
0 seconds to
300 seconds
60 seconds
cP Cycle Period 0 minutes to
60 minutes
10 minutes
So Sensor Offset
Adjustment (Advanced)
-5ºF to 5ºF
(-3 to 3ºC)
0ºF
SF Sensor Failure Action
(Basic and Advanced)
0 = output
relay de-
energized
1 = output
relay
energized
1 output
relay
energized
bll LCD Backlight
Brightness Level
Adjustment (Advanced
only)
0 to 10; 0 =
backlight
off, 10 =
brightest
backlight
setting
10 (brightest
backlight)
1 The default values for general application models are shown.
OEM models may have different default values.
A421 Series Electronic Temperature Controls with Cycle Timer Installation Guide6

A421 Control parameter setup menus
The A421 Temperature Controls have a Basic and
Advanced setup menu. You can use these menus to
scroll through the parameter setup codes, view and
edit parameter values, and set up your control for your
application requirement. The control also has a Restricted
adjustment menu. See Restricting user adjustment for
more information.
Note: The A421 Control retains a copy of the saved
parameter values in memory. When you change
and save a new value, the new value immediately
overwrites the previous value and saves to memory.
In the event of a power failure, brown out, or when
you disconnect power from the control, all of the
current parameter values in memory are retained.
Reconnecting power to the control restores all of the
saved values.
Navigating the Basic and Advanced
menus
The A421 Control buttons and display operate the same
way in the Basic and Advanced menus. The parameter
code flashes on and off in any parameter code screen.
1. To navigate through all of the parameter code
screens, press Down or Up.
2. To exit either menu and return to the Main screen,
press Down and Up simultaneously.
3. While in any parameter value screen, the parameter
value flashes on and off.
4. To scroll through all of the available parameter values
for the associated parameter code, press Down or
Up.
5. With the preferred parameter value displayed,
press MENU to save the value and go to the next
parameter code screen.
Note: If you do not press MENU to save a new
value, the control reverts to the last saved
value. After 30 seconds of inactivity, while in any
screen, the control reverts to the Main screen.
Basic menu
Use the Basic menu to quickly edit the On and OFF
temperature values, and the Sensor Failure Mode (SF).
See Parameter codes and modes of operation and Table 3
for more information regarding parameter codes, usable
parameter values, and default values.
Figure 6: Navigating the Basic menu
Viewing and changing values in the Basic
menu
In this task you access the Basic menu and view and
change the Basic parameter values.
1. On the Main screen, press MENU. The LCD displays
OFF, which is the first parameter code screen
displayed in the Basic menu.
2. To scroll through all of the basic parameter codes
and display the preferred code, press Down or Up.
3. With the preferred parameter code displayed, press
MENU to display the current parameter value for the
code.
4. With the current parameter value displayed, press
Down or Up to scroll through all of the parameter’s
usable values and display the preferred value.
5. With the preferred parameter value displayed, press
MENU to save the displayed value and go to the next
parameter code.
6. To exit the Basic menu and go to the Advanced menu,
simultaneously press and hold Down and Up for 5
seconds.
Advanced menu
The Advanced menu allows you to change the parameter
values in the Basic menu and the values for the following
advanced parameter codes:
• Temperature Units (Un)
• Low Temperature Stop (LtS)
• High Temperature Stop (HtS)
• Low Temperature On-Time (Ltt)
• Minimum Relay On-Time (Ont)
• Cycle Period (cP)
A421 Series Electronic Temperature Controls with Cycle Timer Installation Guide 7

• Sensor Offset Adjustment (So)
• Sensor Failure Option (SF)
• Backlight Brightness Level (bll)
See Parameter codes and modes of operation and Table 3
for more information regarding parameter codes, usable
parameter values, and default values.
Figure 7: Navigating the Advanced menu
Viewing and changing values in the
Advanced menu
In this task you access the Advanced menu and view and
change the parameter values.
1. On the Main screen, press and hold Down and Up
simultaneously for 5 seconds. Un displays on the LCD,
which is the first parameter code screen displayed in
the Advanced menu.
2. To scroll through all of the advanced parameter
codes and display the preferred code, press Down or
Up.
3. With the preferred parameter code displayed, press
MENU to display the current parameter value for the
code.
4. With the current parameter value displayed, press
Down or Up to scroll through all of the parameter
code’s usable values and display the preferred value.
5. With the preferred parameter value displayed, press
MENU to save the displayed value and go to the next
parameter code.
A421 Series Control with Free-Cooling
Ventilation
When the sensed temperature is warmer than the On
value, the relay remains On. See Figure 8.
Control behavior for preferred temperature
range
When the sensed temperature is in between the On and
OFF values, the following behavior is enforced:
• The fan relay is On for at least the Minimum Relay On-
Time (Ont) during a Cycle Period (cP). See Figure 8.
• The fan relay goes Off when the sensed temperature is
less than or equal to the OFF value.
• If the temperature based On-time (t1+t2) is less than
Ont, only the remaining Ont [Ont minus (t1+t2)] is
enforced at the end of the cP.
• The total On-time may exceed the Ont only when the
sensed temperature On-time (t1+t2) is greater than
Ont.
• If the fan relay is On due to the sensed temperature for
a time is greater than or equal to Ont (earlier in the cP),
then the fan relay remains OFF for the remainder of the
cP.
• The only condition that turns the fan relay On greater
than the Ont is when the sensed temperature rises to
the On value.
Control behavior for cooler than preferred
temperature range
The fan relay is On for at least the Ont (Minimum Relay
On-Time) during each Cycle Period (cP). See Figure 8.
Control behavior for extremely colder than
preferred temperature range
When the sensed temperature is less than or equal to the
Low Temperature Stop (LtS) value, the relay is On for the
Low Temperature On-Time (Ltt) each Cycle Period (cP). The
following behavior is enforced:
• The On-time is restricted to just the Ltt value whenever
the sensed temperature falls below the LtS value. See
Figure 8.
• The Ltt is the minimum time required to ventilate the
controlled space.
A421 Series Electronic Temperature Controls with Cycle Timer Installation Guide8

Setting Up the Control for Free-Cooling
and Ventiliation
1. Select the Low Temperature Stop (LtS). The LtS value
must be less than or equal to the OFF value enforced
at setup. See Figure 8.
2. Select the Relay Off Temperature (OFF).
3. Select the Relay On Temperature (On). The On value
must be greater than the OFF value. If you force the
OFF value above the selected On value, the On value
is adjusted to remain greater than the OFF value.
4. Select the Minimum Relay On-time (Ont) per cycle
period (cP) when the sensed temperature remains
greater than LtS.
5. Select the Low Temperature On-Time (Ltt). The Ltt
value must be always less than or equal to the Ont. If
you force the Ltt above the Ont value, the Ont value is
adjusted to remain equal to the Ltt. Adjusting the Ont
value down is limited by the Ltt setting.
Note: The Ltt parameter is enforced (and
the Ont is ignored) whenever the sensed
temperature falls below the LtS value (even
momentarily) during a given cycle period.
6. Select the Cycle Period (cP) for free-cooling and
ventilation control.
Figure 8: Cycle Timer behavior for free-cooling and
ventilation control
Restricting user adjustment
You can restrict user adjustment of the A421 Control to the
OFF value control band adjustment within a defined range
(Figure 9) or no user adjustment at all.
To set the A421 Control into the restricted adjustment
mode, position the P1 jumper located on the circuit board
next to the TB3 terminal block. See Setting the control to
Restricted Adjustment mode.
Note: Setting the A421 Control up in the Restricted
mode prevents casual users from over-adjusting the
control in your application, or from inadvertently
changing the mode of operation from cooling to
heating or heating to cooling (by over-adjusting the
On value or OFF value).
When the A421 Control is set up in the restricted
adjustment mode, the following behavior is enforced:
• The selected HtS and LtS values define the restricted
temperature adjustment range.
• The On and OFF values define the control band
differential, and the control band between On and OFF
remains fixed and not adjustable.
• Only the OFF value can be adjusted, the control band
remains fixed, and the On value automatically shifts
equal to the OFF value adjustment.
• The OFF value can only be adjusted to values that
maintain the entire control band within the restricted
temperature adjustment range defined by HtS and LtS.
See Figure 9.
• The basic and advanced menus are not available. Only
the Restricted Adjustment mode menu is available and
only the OFF value can be adjusted. See Figure 11.
Figure 9: Adjustment behavior in Restricted Adjustment
mode
Setting the control to Restricted
Adjustment mode
In this task you set up the restricted adjustment feature.
1. To make sure that the A421 is not in restricted mode,
position the jumper on both pins. See Figure 10.
2. Select the OFF and On values that define the
application’s required control band (Figure 9).
3. Change the HtS and LtS temperature values to define
the restricted adjustment range (Figure 9).
4. Disconnect power to the control and reposition the
jumper to one pin (Figure 10). Reconnect power.
Figure 10: Repositioning the jumper to restrict control
adjustment
A421 Series Electronic Temperature Controls with Cycle Timer Installation Guide 9

Control adjustment is now restricted to changing only
the OFF value, which shifts the On and OFF control band
within the restricted adjustment range defined by HtS and
LtS (Figure 9).
Note: To completely restrict and lockout all user
adjustment on the control, set the HtS value equal to
the On or OFF value and the LtS value equal to OFF or
On value. Then the (On to OFF) control band is equal
to the restricted adjustment range (LtS to HtS) and
the OFF value cannot be adjusted in the restricted
mode.
Adjusting the control in Restricted mode
In this task you adjust the OFF value and shift the On and
OFF control band within the restricted adjustment range,
when the control is in the restricted adjustment mode.
1. In the Main screen, press MENU to go to the
restricted adjustment mode menu and display the
OFF parameter code screen (Figure 11).
2. To go to the OFF value screen, press MENU.
3. In the OFF value screen, press Down or Up to change
the OFF value within the restricted adjustment range.
4. To save the selected OFF value and return to the OFF
code screen, press MENU.
5. To return to the Main screen, press Down and Up
simultaneously.
Figure 11: Adjusting temperature in the Restricted menu
Troubleshooting
A421 Series Controls display fault codes on the LCD as
described in Table 4.
Table 4: Fault Codes Defined
Fault code Definition System status Solution
SF flashing
alternately
with OP
Open
temperature
sensor or
sensor wiring
Output
functions
according to
the selected SF
mode
See Troubleshooting
procedure. Cycle
power to reset the
control.
SF flashing
alternately
with SH
Shorted
temperature
sensor or
sensor wiring
Output
functions
according to
the selected SF
mode
See Troubleshooting
procedure. Cycle
power to reset the
control.
EE Program
failure
Output is off To reset the control,
press MENU. If
problems persist,
replace the control.
Troubleshooting procedure
1. Check for proper voltage to the A421 Control.
a. To remove the cover, loosen the two captive cover
screws.
b. Use an AC voltmeter to check the voltage between
the COM and 120V or 240V terminals on line-
voltage models. See Figure 4.
Note: The voltage must be between:
- 102 VAC and 132 VAC for 120 VAC
applications
- 177 VAC and 264 VAC for 208/240 VAC
applications
c. If the voltage reading is not within the required
range, check the power source and input power
wires for problems.
2. Check for proper sensor operation.
a. Disconnect all power sources to control.
b. Using an accurate thermometer, take a
temperature reading at the sensor location.
c. Disconnect the sensor from the control.
d. Using an ohmmeter, measure the resistance
across the two sensor leads while the sensor is at
the temperature taken in Step 2b.
e. Consult Figure 12 to verify that the measured
temperature and resistance conform to
established temperature and resistance values.
f. If the measured values conform to the values in
Figure 12, proceed to Step 3.
g. If the sensor’s measured resistance value is
substantially different from the expected value
for that temperature, check the sensor wiring. If
sensor wiring is correct, replace the sensor.
A421 Series Electronic Temperature Controls with Cycle Timer Installation Guide10

Figure 12: Temperature versus sensor resistance
3. Check the A421 for proper operation.
Note: Perform Troubleshooting Steps 1 and 2
before performing this step.
a. Disconnect the load from the output relay
terminals.
b. Make sure that the Parameter Adjustments
jumper is installed so that you have unrestricted
access to adjust parameters.
c. Reconnect the sensor leads and supply power to
the control.
d. Replace the cover.
e. Check the control settings for proper values.
f. Press MENU until On appears. Press MENU again
to display the On value.
g. Press Down or Up to change the On temperature
above and below the sensor temperature until the
relay energizes and de-energizes.
h. If the output relay does not perform as expected,
replace the A421 Control.
i. If you verify proper operation of the A421 Control,
reconnect the load and consult the equipment
manufacturer’s instructions to troubleshoot the
controlled equipment.
Repair information
Do not attempt to repair or recalibrate the A421
Temperature Control. In case of a defective or
improperly functioning control, contact your nearest
authorized Johnson Controls/PENN distributor or sales
representative.
When contacting your Johnson Controls/PENN distributor,
have the model number of the control available. This
number can be found on the label inside the cover of the
control.
Ordering information
See Table 5 to order a standard A421 Series Electronic
Temperature Control. See Table 6 and Table 7 for
information about A99 sensors, mounting hardware, and
other accessories you use to install A421 Controls. Contact
your nearest Johnson Controls or PENN distributor or sales
representative to order these products.
Table 5: A421 Series Electronic Temperature Controls
with Cycle Timer selection chart
Product type Description
A421ABT-02C Line-voltage Type 1 Electronic Temperature
Control with Cycle Timer: Type 1 (NEMA), IP20
standard enclosure for DIN rail and surface-
mount applications. Rated for 120/240 VAC.
Includes timer for On/Off duty-cycle control.
Includes an A99BB-200C temperature sensor
with 6.6 ft (2.0 m) cable.
A421AET-01C Line-voltage Type 4X Electronic Temperature
Control with Cycle Timer: Type 4X (NEMA),
IP66 watertight enclosure for surface-mount
applications. Rated for 120/240 VAC. Includes
timer for On/Off duty-cycle control. Includes an
A99BB-25C temperature sensor with 9 7/8 in.
(0.25 m) cable.
Table 6: A99 Temperature Sensors selection chart
Product code1Description
A99BA-200C Positive temperature coefficient (PTC)
Temperature Sensor: Standard probe 2 in. (5.1
cm) with 6.6 ft (2.0 m) shielded polyvinyl chloride
(PVC) cable; ambient operating temperature
range: -40ºF to 212ºF (-40ºC to 100ºC)
A99BB-25C PTC Temperature Sensor: Standard probe 2
in. (5.1 cm) with 9 7/8 in. (0.25 m) PVC cable;
ambient operating temperature range: -40ºF to
212ºF (-40ºC to 100ºC)
A99BB-200C PTC Temperature Sensor: Standard probe 2 in.
(5.1 cm) with 6.6 ft (2.0 m) PVC cable; ambient
operating temperature range: -40ºF to 212ºF
(-40ºC to 100ºC)
A99BB-300C PTC Temperature Sensor: Standard probe 2 in.
(5.1 cm) with 9.8 ft (3.0 m) PVC cable; ambient
operating temperature range: -40ºF to 212ºF
(-40ºC to 100ºC)
A99BB-400C PTC Temperature Sensor: Standard probe 2 in.
(5.1 cm) with 13.1 ft (4.0 m) PVC cable; ambient
operating temperature range: -40ºF to 212ºF
(-40ºC to 100ºC)
A99BB-600C PTC Temperature Sensor: Standard probe 2 in.
(5.1 cm) with 19.7 ft (6.0 m) PVC cable; ambient
operating temperature range: -40ºF to 212ºF or
(-40ºC to 100ºC)
A99BC-25C1PTC Temperature Sensor: Standard probe 2 in.
(5.1 cm) with 9 7/8 in. (0.25 m) high-temperature
silicon cable; ambient operating temperature
range: -40ºF to 212ºF (-40ºC to 100ºC)
A99BC-100C11PTC Temperature Sensor: Standard probe 2 in.
(5.1 cm) with 3.3 ft (1.0 m) high-temperature
silicon cable; ambient operating temperature
range: -40ºF to 212ºF (-40ºC to 100ºC)
A421 Series Electronic Temperature Controls with Cycle Timer Installation Guide 11

Table 6: A99 Temperature Sensors selection chart
Product code1Description
A99BC-300C1PTC Temperature Sensor: Standard probe 2 in.
(5.1 cm) with 9.8 ft (3.0 m) high-temperature
silicon cable; ambient operating temperature
range: -40ºF to 248ºF (-40ºC to 120ºC)
A99BC-500C1PTC Temperature Sensor: Standard probe 2 in.
(5.1 cm) with 16.4 ft (5.0 m) high-temperature
silicon cable; ambient operating temperature
range: -40ºF to 248ºF (-40ºC to 120ºC)
A99BC-1500C1PTC Temperature Sensor: Standard probe 2 in.
(5.1 cm) with 49.2 ft (15.0 m) high-temperature
silicon cable; ambient operating temperature
range: -40ºF to 248ºF (-40ºC to 120ºC)
A99CB-200C PTC Temperature Sensor: Extended probe 6 in.
(15.2 cm) with 6.6 ft (2.0 m) PVC cable; ambient
operating temperature range: -40ºF to 212ºF
(-40ºC to 100ºC)
A99CB-600C PTC Temperature Sensor: Extended probe 6 in.
(15.2 cm) with 19.7 ft (6.0 m) PVC cable; ambient
operating temperature range: -40ºF to 212ºF
(-40ºC to 100ºC)
1 When any A99 Series Temperature Sensor is connected
to a standard A421 Control model, the range of displayed
temperature values is -40ºF to 212ºF or -40ºC to 100ºC.
Table 7: Accessories
Product code Description
BKT287-1R 12 in. (305 mm) long DIN rail section
BKT287-2R 36 in. (914 mm) long DIN rail section
PLT344-1R Two end clamps for DIN rail sections
A99-CLP-1 Surface mounting clip for A99B and A99C Series
Temperature Sensors
SHL10-603R Sun shield for A99B and A99C Series
Temperature Sensors
BOX10A-603R PVC enclosure for A99B and A99C Series
Temperature Sensors
WEL11A-601R Copper and brass immersion well for applying
sensor in fluid applications
TE-6300W-102 Stainless steel immersion well for applying
A99 sensors in fluid applications. (A99CB Type
sensors with extended probe are recommended
for use with this immersion well.)
Technical specifications
Table 8: A421 Series Electronic Temperature Controls
Technical Specifications
Specification Description
Power
consumption
1.8 VA maximum
Supply power 110/120 or 208/230/240 VAC, 50/60 Hz
Table 8: A421 Series Electronic Temperature Controls
Technical Specifications
Specification Description
Ambient
conditions
Operating: Type 1 models: -40°F to 150°F (-40°C
to 66°C), 0% to 95% RH noncondensing
Type 4X models: -40°F to 140°F (-40°C to 60°C),
0% to 95% RH noncondensing
Shipping and storage: All models: -40°F to 185°F
(-40°C to 85°C), 0% to 95% RH noncondensing
Temperature
control range
-40°F to 212°F or -40°C to 100°C
Input signal 1,035 ohm at 77°F (25°C) for A99 PTC
temperature sensors
Accuracy Combined accuracy of A421 Control and A99
sensor: ±2°F (±1°C) between 5°F and 167°F(-15°C
and 75°C); diverging to ±3°F (±2°C) at -40°F
(-40°C) and ±3°F (±2°C) at 212°F (100°C)
Sensor offset
range
±5ºF or ±3ºC
Enclosure
material
Type 1, IP20 high-impact thermoplastic or
Type 4X, IP66 watertight, corrosion-resistant,
high-impact thermoplastic
Note: To maintain type 4X / IP66 rating, tighten
enclosure screws to: 10 – 12 in·lb.
Compliance North America: cULus Listed; UL 60730, File
E27734, Vol. 1; FCC Compliant to CFR47, Part 15,
Subpart B, Class B
Industry Canada (IC) Compliant to Canadian
ICES-003, Class B limits
Europe: CE Mark – Johnson Controls declares
that this product is in compliance with the
essential requirements and other relevant
provisions of the EMC Directive; Low Voltage
Directive.
Australia and New Zealand: RCM, Australia/NZ
Emissions Compliant
Table 9: A421 Temperature Control Output Relay
Contacts electrical ratings
A421
Agency and file UL 60730 and EN 60730
Applied AC voltage at
50/60 Hz 120 VAC 208 VAC 240 VAC
Horsepower LC/LNO
(LC/LNC)
1 (0.25) 1 (0.3) 1 (0.5)
Full load amperes LC/
LNO (LC/LNC)
16 (5.8) 9.2 (4) 8 (4.9)
Locked rotor amperes
LC/LNO (LC/LNC)
96 (34.8) 55.2 (24) 48 (29.4)
Resistive amperes LC/
LNO (LC/LNC)
15 (10) 10 (10) 10 (10)
Pilot duty VA LC/LNO
(LC/LNC)
125 (125) 125 (125) 125 (125)
Table 10: UL conformity declaration information
Information Description
Purpose of control Sensing control / Operating control
A421 Series Electronic Temperature Controls with Cycle Timer Installation Guide12

Table 10: UL conformity declaration information
Information Description
Construction of control Electronic independently mounted
control
Number of cycles 30,000 cycles
Method of mounting
control
Mounting screws or DIN rail
Type 1 or type 2 action Type 1.B (Micro-disconnection)
External pollution
situation
All models: A421 [ ] B: Pollution degree 3
All models: A421 [ ] E: Pollution degree 4
Internal pollution
situation
Pollution degree 2
Heat and fire
resistance category
D
Rated impulse voltage 4,000 V
Ball pressure
temperature
128°C
Cover screw torque
requirements
instruction
All models: A421 [ ] E: To maintain type
4X / IP66 rating, tighten enclosure screws
to: 10–12 in·lb
Table 11: A99B Series Positive Temperature Coefficient
Sensors Technical Specifications
Specification Description
1Sensing range1Type A99BA and A99BB: -40°F to 212°F (-40 to
100°C)
Type A99BC: -40°F to 248°F (-40 to 120°C)
Reference
resistance
1,035 ohms at 77°F (25°C) and 855 ohms at
32°F (0°C)
Accuracy 0.9°F (0.5°C) between 5°F and 167°F
(-15°C and 57°C). Refer to the A99B Series
Temperature Sensors Product/Technical Bulletin
(LIT-125186) for accuracy rating outside of this
temperature range.
Table 11: A99B Series Positive Temperature Coefficient
Sensors Technical Specifications
Specification Description
Sensor
construction
Probe: Stainless steel
Sensor cable
sheath
Type A99BA: Shielded PVC cable
Type A99BB: PVC cable
Type A99BC: High temperature silicon cable
Wire gauge 22 AWG
Ambient
operating
conditions
Type A99BA and A99BB: -40°F to 212°F (-40°C
to 100°C); 0% to 100% RH, condensing
Type A99BC: -40°F to 248°F (-40°C to 120°C);
0% to 100% RH, condensing
Ambient storage
conditions
Type A99BA and A99BB: -40°F to 221°F (-40°C
to 105°C); 0% to 100% RH, condensing
Type A99BC: -40°F to 266°F (-40°C to 130°C);
0% to 100% RH, condensing
Shipping weight 1.4 oz (41 g) for 6 1/2 ft (2 m) sensor
Accessories See Table 7
1 When any A99 Series Temperature Sensor is connected
to a standard A421 Control model, the range of displayed
temperature values is -40ºF to 212ºF or -40ºC to 100ºC.
The performance specifications are nominal and conform to
acceptable industry standards. For application at conditions
beyond these specifications Johnson Controls shall not be
liable for damages resulting from misapplication or misuse of
its products.
North American emissions compliance
United States
This equipment has been tested and found to comply with the limits for a Class B digital device, pursuant to Part 15 of
the FCC Rules. These limits are designed to provide reasonable protection against harmful interference in a residential
installation. This equipment generates, uses and can radiate radio frequency energy and, if not installed and used
in accordance with the instructions, may cause harmful interference to radio communications. However, there is no
guarantee that interference will not occur in a particular installation. If this equipment does cause harmful interference
to radio or television reception, which can be determined by turning the equipment off and on, the user is encouraged to
try to correct the interference by one or more of the following measures:
• Reorient or relocate the receiving antenna.
• Increase the separation between the equipment and receiver.
• Connect the equipment into an outlet on a circuit different from that to which the receiver is connected.
• Consult the dealer or an experienced radio/TV technician for help.
Canada
This Class (B) digital apparatus meets all the requirements of the Canadian Interference-Causing Equipment Regulations.
Cet appareil numérique de la Classe (B) respecte toutes les exigences du Règlement sur le matériel brouilleur du Canada.
A421 Series Electronic Temperature Controls with Cycle Timer Installation Guide 13

Single point of contact
APAC Europe NA/SA
JOHNSON CONTROLS
C/O CONTROLS PRODUCT
MANAGEMENT
NO. 32 CHANGJIJANG RD NEW
DISTRICT
WUXI JIANGSU PROVINCE 214028
CHINA
JOHNSON CONTROLS
WESTENDHOF 3
45143 ESSEN
GERMANY
JOHNSON CONTROLS
507 E MICHIGAN ST
MILWAUKEE WI 53202
USA
For more contact information, refer to
www.johnsoncontrols.com/locations.
© 2019 Johnson Controls. All rights reserved. All specifications and other information shown were current as of document revision and
are subject to change without notice.
www.penncontrols.com
Other manuals for A421 Series
4
Table of contents
Other Penn Control System manuals

Penn
Penn P78 Series User manual
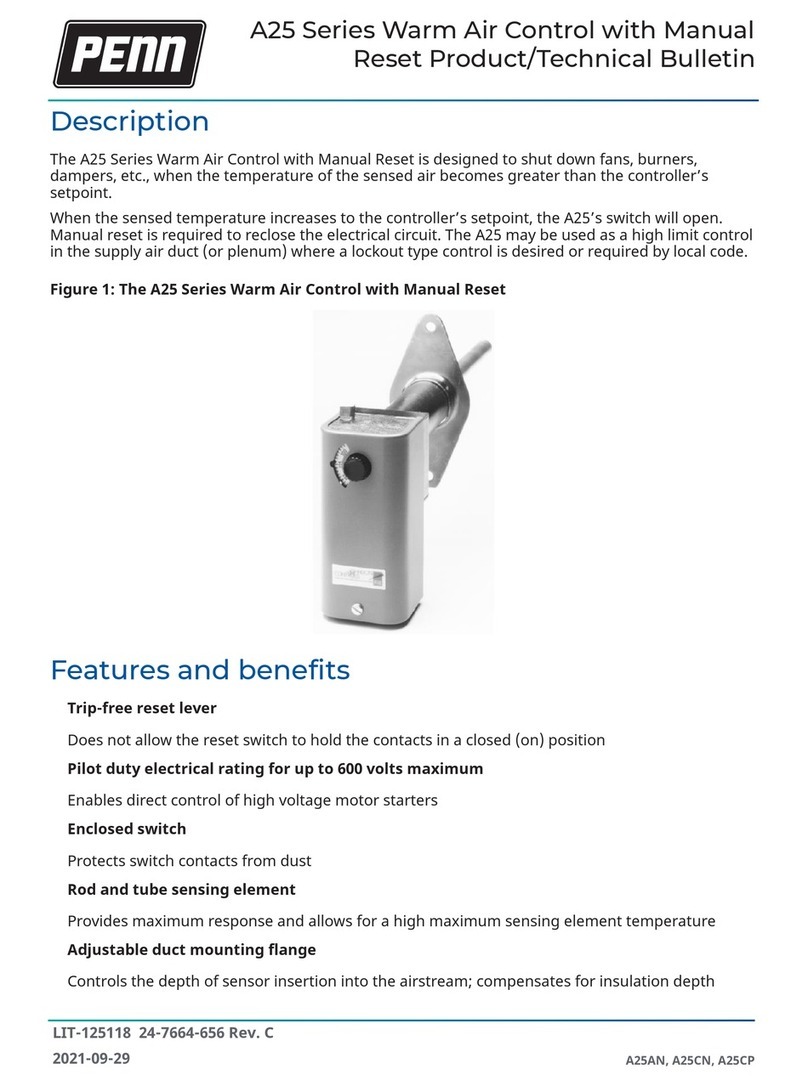
Penn
Penn A25 Series Service manual
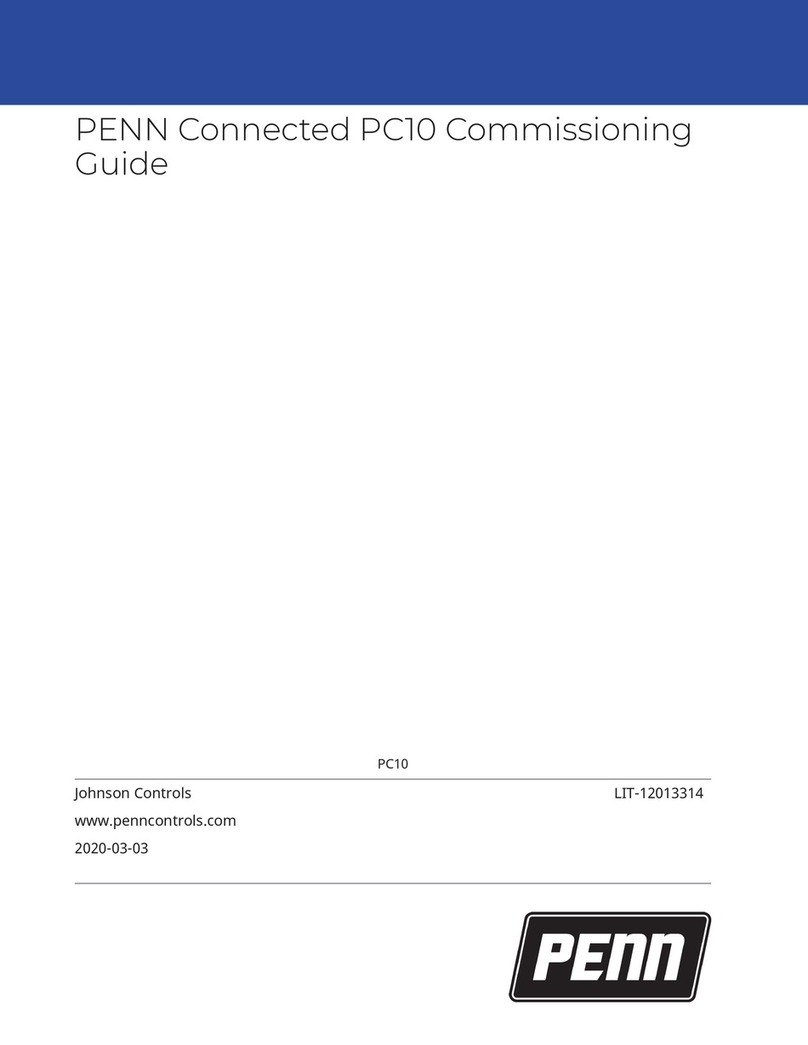
Penn
Penn Connected PC10 User manual

Penn
Penn P77 Series User manual

Penn
Penn A28 Series User manual
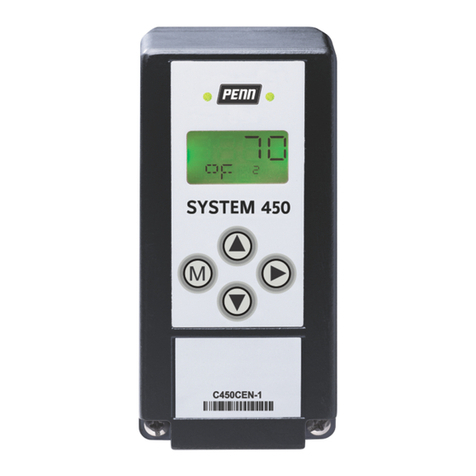
Penn
Penn System 450 Series User manual
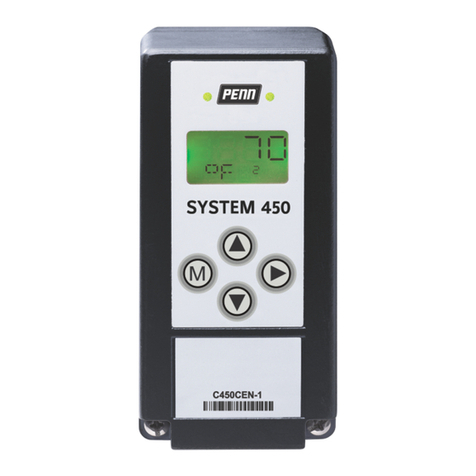
Penn
Penn System 450 Series Service manual
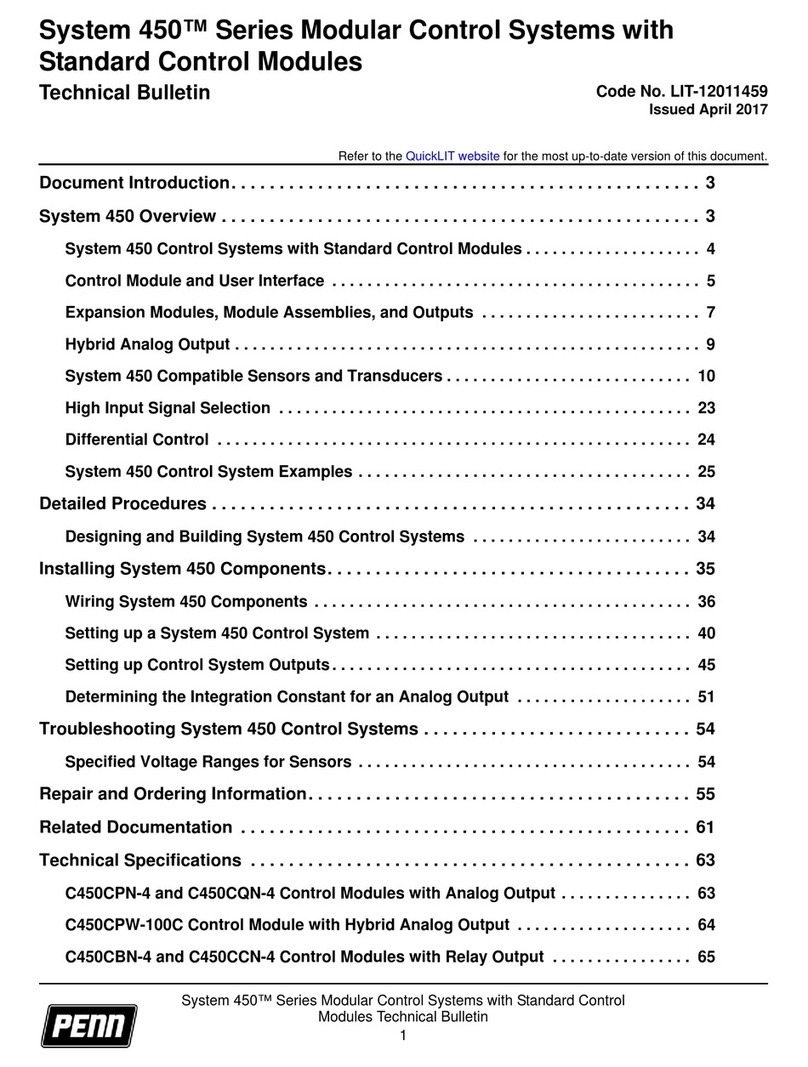
Penn
Penn System 450 Series Service manual

Penn
Penn A421 Series User manual
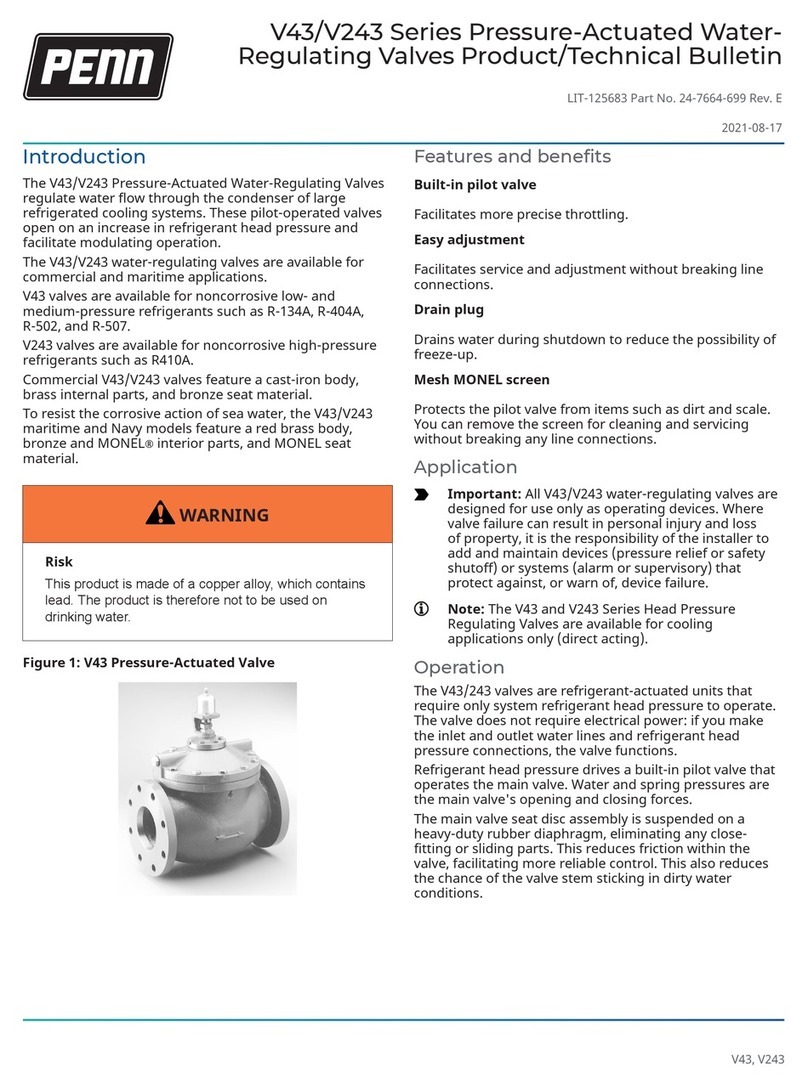
Penn
Penn V43 Series V243 Series Manual